流态化技术
流态化原理
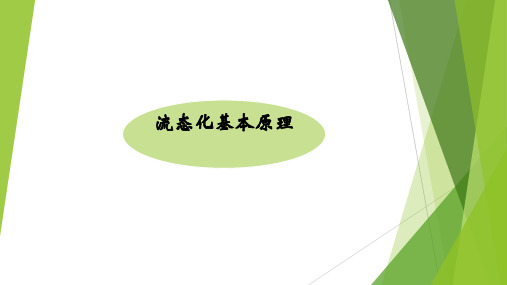
• 两相密度差小的 系统趋向散式流 化,大部分液固流化属于散式 流化
• 气-固流化系统 多属于聚式流化
自由沉降 • 自由沉降:是指单个颗粒在流体中的沉降过程。
干扰沉降
• 干扰沉降:若颗粒数量较多,相互间距离较近,则颗 粒沉降时相互间会干扰。
流态化技术的应用
流态化技术在强化某些单元操作和反 应过程以及开发新工艺方面,起着重 要作用,广泛应用于化学、石油、冶 金、原子能等工业的焙烧、干燥、吸 附、气化、催化反应和催化裂化等许 多过程中。
颗粒输送阶段 • u>ut
散式流化
• 流化床内固体颗 粒均匀分布在流 动流体中,并在 各个方向上作随 机运动,床层中 各部分密度几乎 相等,床层上界 面平稳而清晰, 这种现象被称为 散式流化。
聚式流化
特性
• 聚式流化也称鼓 泡流化,是床层 中出现组成不同 的两个相,即含 固体颗粒甚少的 不连续气泡相, 以及含固体颗粒 较多、分布较均 匀的连续乳化相, 乳化相内的液固 运动状况和空隙 率接近初始流化 状态
固定床阶段 流化床阶段
• u<ut • 颗粒基本静止不动
• 当流体速度增大到一定程度后,颗粒松动、 调整,床层膨胀,处于起始或临界流化态。 如果流体的流升高到使全部颗粒刚好悬浮 于向上流动的流体中而能做随机运动,此 时流体与颗粒之间的摩擦阻力恰好与其净 重力相平衡。此后,床层高度L将随流速 提高而升高,这种床层成为流化床。
流态化基本原理
流化态现象
三种情况
• 固定床阶 段
• 流化床阶 段
• 颗粒输送 阶段
两种形式
• 散式流化 •• 实际状态
两种不正常现象
• 腾涌 • 沟流
流态化
流态化一般指固体流态化,简称流化,它是利用流动流体的 作用,将固体颗粒群悬浮起来,从而使固体颗粒具有某些流 体表观特征,利用这种流体与固体间的接触方式实现生产过 程的操作,称为流态化技术,属于粉体工程的研究范畴。
流态化基础知识和流型分类

流态化技术自20世纪初被发现以来, 经历了从实验室研究到工业应用的漫 长过程,现已广泛应用于化工、能源 、环保等领域。
颗粒床层特性与流动状态
颗粒床层特性
颗粒床层是由固体颗粒堆积而成,具 有多孔性、可压缩性和渗透性等特性 。
流动状态
颗粒床层在气体或液体作用下可表现 为固定床、流化床和输送床等不同的 流动状态。
影响因素
流体速度、固体颗粒性质(如粒径、密度、形状等)、床层高度、温度、压力等都会对床层流型产生影响。
03
颗粒性质对流型影响研究
颗粒形状、大小及分布规律探讨
颗粒形状对流型的影响
球形颗粒在流化床中易于形成均匀流化,而非球形颗粒( 如片状、纤维状)可能导致流化不均匀或产生沟流现象。
颗粒大小对流型的影响
摩擦力对流型的影响
摩擦力使颗粒间相互摩擦产生热量和磨损, 影响床层的稳定性和流动行为。高摩擦力可 能导致床层内局部温度升高和颗粒磨损加剧 ,进而影响整体流型。
04
气体参数对流型影响研究
气体速度、压力变化规律探讨
气体速度对流型的影响
随着气体速度的增加,流型从固定床逐渐过渡到流化床,床层膨胀度增加,颗粒间的相 互作用力减弱,流型变得更加均匀。
物料循环和排放控制
根据生产需求控制物料的循环量和排放量;在操作过程中 密切关注物料循环和排放情况,及时调整相关参数以保持 稳定的物料平衡。
提高设备性能,降低能耗措施
设备结构优化
操作参数优化
通过改进设备结构,如采用高效分布板、 优化旋风分离器结构等,提高设备的流化 效率和分离效率,降低能耗。
通过调整操作参数,如气体速度、温度和 压力等,使设备在最佳状态下运行,提高 设备性能并降低能耗。
第三章 固体流态化技术

沟流对反应过程的影响:沟流现象发生时,大部分气体没有 与固体颗粒很好接触就通过了床层,这在催化反应时会引起催 化反应的转化率降低。由于部分颗粒没有流化或流化不好,造 成床层温度不均匀,从而引起催化剂的烧结,降低催化剂的寿 命和效率。
4、恒定的压降
流化床的重要优点
流化床床层压降 =(重量-浮力)/单位床截面积
固定床阶段 床层不动 u1 ut
流化床阶段 u1 ut开始悬浮
颗粒输送阶段 u1 ut 颗粒带走
u ,u1 ,u1 ut
(a)固定床
(b)流化床
(c)气力输送
此时流体的真正速 度 u < 颗粒的沉降 速度u0
此时u= u0 颗粒悬浮于流体中,床层 有一个明显的上界面,与 沸腾水的表面相似
流化阶段,压降与气速无关,始终保持定值
固定床 流化床 C ΔP B A ¢ u 带出开始
m P ( p ) g Ap
起始流化速度
表观速度 流体通过颗粒床层的压降
D( 带出速度 )
推导:
流化床阶段,近似认为颗粒处于动态平衡。
即:总曳力 总重力 总浮力
p f A Fg Fb AL(1 )(s ) g
此时u> u0
固体流态化运用在粉粒状物料的输送、混合、加热或冷 却、干燥、吸附、煅烧和气固反应等过程中。
3、流化床存在的基础—大量颗粒群居 颗粒能在相当宽范围内悬而不走,离开群体的个别颗粒上 升后, 速度将减小,则会回落。
浮力
曳力 u1(实际速度) 重力
u(表观速度)
二、实际流化现象
流态化按其性状的不同,可以分成两类, 即散式流态化和聚式流态化。
主要用途:
流态化技术基础及应用
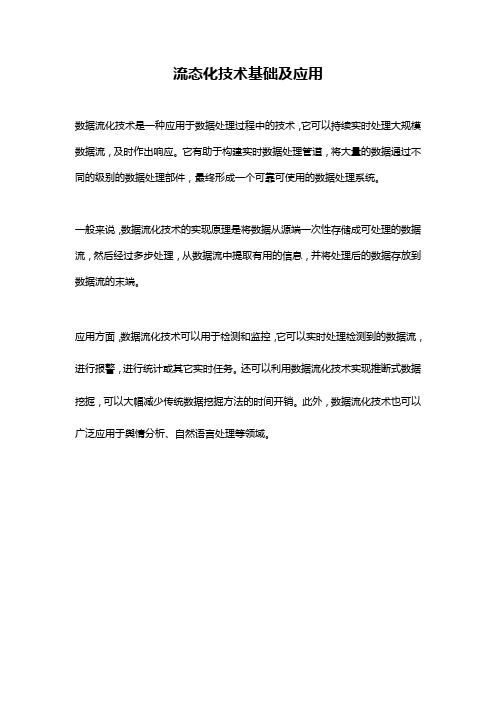
流态化技术基础及应用
数据流化技术是一种应用于数据处理过程中的技术,它可以持续实时处理大规模数据流,及时作出响应。
它有助于构建实时数据处理管道,将大量的数据通过不同的级别的数据处理部件,最终形成一个可靠可使用的数据处理系统。
一般来说,数据流化技术的实现原理是将数据从源端一次性存储成可处理的数据流,然后经过多步处理,从数据流中提取有用的信息,并将处理后的数据存放到数据流的末端。
应用方面,数据流化技术可以用于检测和监控,它可以实时处理检测到的数据流,进行报警,进行统计或其它实时任务。
还可以利用数据流化技术实现推断式数据挖掘,可以大幅减少传统数据挖掘方法的时间开销。
此外,数据流化技术也可以广泛应用于舆情分析、自然语言处理等领域。
《固体流态化技术》课件
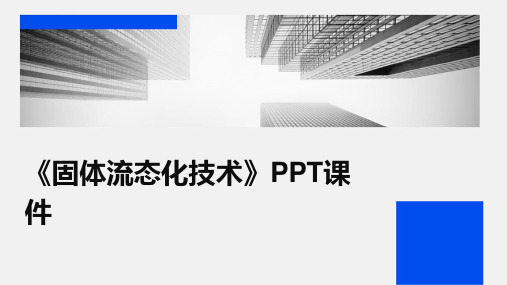
新型流态化技术的研发
随着科技的不断发展,新型流态化技术也不断涌现,如气固 流态化技术、液固流态化技术等,这些新型流态化技术具有 更高的效率和更好的应用前景。
新型流态化技术的研发需要不断探索和尝试,通过实验和模 拟等方式,不断优化和完善技术参数和工艺条件,提高技术 的应用效果和可靠性。
智能化与自动化的提升
进一步拓展。
技术局限
颗粒大小限制
固体流态化技术对固体颗粒的大小有 一定要求,过小的颗粒可能导致技术 效果不佳。
操作参数敏感
该技术的操作参数较为敏感,需要精 确控制以获得最佳效果。
高成本
固体流态化技术的设备成本较高,增 加了应用成本。
稳定性问题
在某些情况下,固体流态化技术的稳 定性有待提高。
技术挑战与前景
01
化工
用于反应、分离、混合等工艺过 程,如石油化工、化学反应工程 等。
02
03
能源
环保
用于煤炭、生物质等固体燃料的 燃烧、气化、热解等过程,提高 能源利用效率。
用于固体废弃物的处理、处置和 资源化利用,如城市垃圾焚烧、 工业废弃物处理等。
02
固体流态化技术的原 理
基本原理
固体流态化技术的基本原理是利用流 体对固体颗粒进行作用,使固体颗粒 呈现出流体的某些特性,从而实现固 体颗粒的流动和运输。
04
固体流态化技术的优 缺点
技术优势
高效性
固体流态化技术能够实现连续 、大规模的物质处理,提高了
生产效率。
节能环保
该技术能够降低能耗,减少环 境污染,符合绿色发展理念。
灵活性
固体流态化技术适用于多种不 同性质的固体颗粒,应用范围 广泛。
可扩展性
流态化工程原理

流态化工程原理流态化工程原理是指通过控制流体的运动状态和物理特性来实现特定的工艺目标或应用需求的一种技术。
它在化工、石油、能源、环保等领域中广泛应用,为工业生产提供了重要的技术支持和创新方向。
流态化工程原理的基本概念是将固体颗粒悬浮于气体或液体介质中,通过调节流体的速度和流态化剂的添加来改变固体颗粒的运动状态。
在流态化状态下,固体颗粒的运动呈现出流体的特性,具有类似于液体的流动性和类似于气体的均匀性。
这种特性使得流态化工程成为一种高效的物料搬运和反应控制技术。
流态化工程原理的核心是流体的运动和相互作用。
在流态化过程中,流体中的颗粒受到气体或液体的作用力,呈现出不同的运动状态,如床层流动、颗粒间的碰撞和混合等。
这些运动状态对于实现特定的工艺目标至关重要,如颗粒的分离、搬运和反应等。
流态化工程原理的应用范围非常广泛。
在化工领域,流态化工程可以用于固体颗粒的分离、干燥、反应和催化等过程。
例如,在石化工业中,流态化工程可以用于催化剂的制备和石油的加工。
在环保领域,流态化工程可以用于废气和废水的处理和净化。
在能源领域,流态化工程可以用于燃煤和生物质的燃烧,以及核能的利用等。
流态化工程原理的核心是控制流体的运动和相互作用。
通过调节流体的速度和流态化剂的添加,可以改变固体颗粒的运动状态,从而实现特定的工艺目标。
流态化工程既有理论研究,又有实际应用。
在理论研究方面,流态化工程涉及流体力学、热力学和物质传递等多个学科的知识。
在实际应用方面,流态化工程需要考虑工艺流程、设备设计和操作控制等多个方面的问题。
流态化工程原理的研究和应用对于推动工业生产的发展具有重要意义。
它可以提高物料搬运和反应过程的效率,减少能源和原材料的消耗,降低环境污染和废物排放。
同时,流态化工程也为新材料的研发和应用提供了技术支持和创新思路。
通过研究流态化工程原理,我们可以更好地理解和掌握流体的运动规律和相互作用机制,为工业生产的可持续发展做出贡献。
流态化
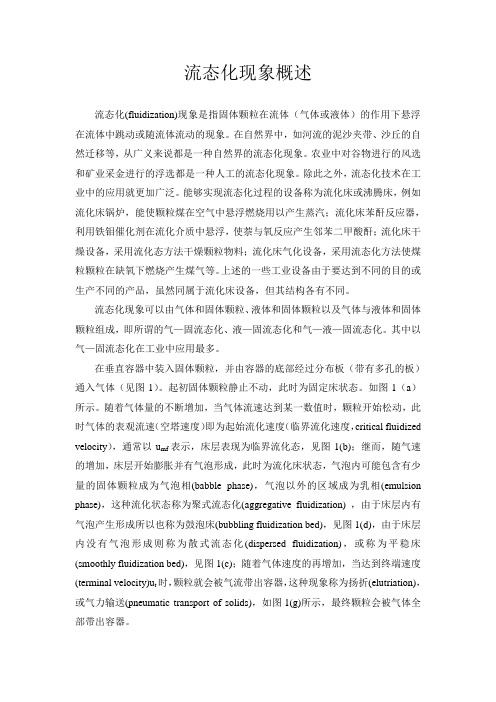
流态化现象概述流态化(fluidization)现象是指固体颗粒在流体(气体或液体)的作用下悬浮在流体中跳动或随流体流动的现象。
在自然界中,如河流的泥沙夹带、沙丘的自然迁移等,从广义来说都是一种自然界的流态化现象。
农业中对谷物进行的风选和矿业采金进行的浮选都是一种人工的流态化现象。
除此之外,流态化技术在工业中的应用就更加广泛。
能够实现流态化过程的设备称为流化床或沸腾床,例如流化床锅炉,能使颗粒煤在空气中悬浮燃烧用以产生蒸汽;流化床苯酐反应器,利用铁钼催化剂在流化介质中悬浮,使萘与氧反应产生邻苯二甲酸酐;流化床干燥设备,采用流化态方法干燥颗粒物料;流化床气化设备,采用流态化方法使煤粒颗粒在缺氧下燃烧产生煤气等。
上述的一些工业设备由于要达到不同的目的或生产不同的产品,虽然同属于流化床设备,但其结构各有不同。
流态化现象可以由气体和固体颗粒、液体和固体颗粒以及气体与液体和固体颗粒组成,即所谓的气—固流态化、液—固流态化和气—液—固流态化。
其中以气—固流态化在工业中应用最多。
在垂直容器中装入固体颗粒,并由容器的底部经过分布板(带有多孔的板)通入气体(见图1)。
起初固体颗粒静止不动,此时为固定床状态。
如图1(a)所示。
随着气体量的不断增加,当气体流速达到某一数值时,颗粒开始松动,此时气体的表观流速(空塔速度)即为起始流化速度(临界流化速度,critical fluidized velocity),通常以u mf表示,床层表现为临界流化态,见图1(b);继而,随气速的增加,床层开始膨胀并有气泡形成,此时为流化床状态,气泡内可能包含有少量的固体颗粒成为气泡相(babble phase),气泡以外的区域成为乳相(emulsion phase),这种流化状态称为聚式流态化(aggregative fluidization) ,由于床层内有气泡产生形成所以也称为鼓泡床(bubbling fluidization bed),见图1(d),由于床层内没有气泡形成则称为散式流态化(dispersed fluidization),或称为平稳床(smoothly fluidization bed),见图1(c);随着气体速度的再增加,当达到终端速度(terminal velocity)u t时,颗粒就会被气流带出容器,这种现象称为扬折(elutriation),或气力输送(pneumatic transport of solids),如图1(g)所示,最终颗粒会被气体全部带出容器。
流态化原理
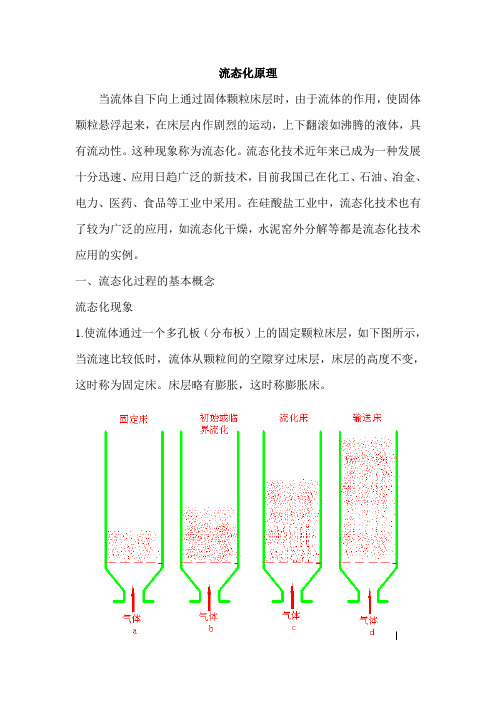
流态化原理当流体自下向上通过固体颗粒床层时,由于流体的作用,使固体颗粒悬浮起来,在床层内作剧烈的运动,上下翻滚如沸腾的液体,具有流动性。
这种现象称为流态化。
流态化技术近年来已成为一种发展十分迅速、应用日趋广泛的新技术,目前我国已在化工、石油、冶金、电力、医药、食品等工业中采用。
在硅酸盐工业中,流态化技术也有了较为广泛的应用,如流态化干燥,水泥窑外分解等都是流态化技术应用的实例。
一、流态化过程的基本概念流态化现象1.使流体通过一个多孔板(分布板)上的固定颗粒床层,如下图所示,当流速比较低时,流体从颗粒间的空隙穿过床层,床层的高度不变,这时称为固定床。
床层略有膨胀,这时称膨胀床。
流速增加到一定数值时,颗粒之间失去接触关系而悬浮于流体中,床层显著膨胀,这时称为初始流化或临界流化。
临界流化是固体床向流化床的转折点。
继续增加流速,床层进一步膨胀,但有明显的上界面,床层中颗粒运动加剧,整个床层具有类似液态的性质,这时称为流态化或流化床。
在更高的流速下,一部分固体颗粒被气流带出,流速增大,带出增多,上界面消失,颗粒间的孔隙加大,密度减小,固体颗粒在流体中形成旋风状态的稀相,并随气体一起被吹送出去,这时称为气力输送,亦称稀相输送床。
图1-332.流化床类似液体的性质气-固系统流化床非常像沸腾的液体,并在许多方面表现出类似液体的性质。
如图1-33所示,一个大而轻的物体可以很容易地被推入床层,去掉外力它就上浮在床层表面上;容器倾斜时,它们在床面也和液体一样自找水平;此外,床层中任一不同高度两点间的压强差,能满足流体力学的静力学方程式;气、固流化床也具有像液体一样的流动性,固体颗粒可以从小孔喷出,并像液体那样从一个容器流入另一个容器。
流态化实验报告
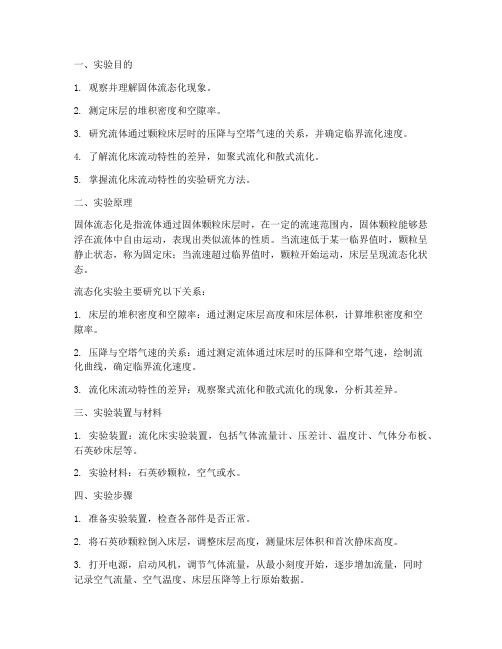
一、实验目的1. 观察并理解固体流态化现象。
2. 测定床层的堆积密度和空隙率。
3. 研究流体通过颗粒床层时的压降与空塔气速的关系,并确定临界流化速度。
4. 了解流化床流动特性的差异,如聚式流化和散式流化。
5. 掌握流化床流动特性的实验研究方法。
二、实验原理固体流态化是指流体通过固体颗粒床层时,在一定的流速范围内,固体颗粒能够悬浮在流体中自由运动,表现出类似流体的性质。
当流速低于某一临界值时,颗粒呈静止状态,称为固定床;当流速超过临界值时,颗粒开始运动,床层呈现流态化状态。
流态化实验主要研究以下关系:1. 床层的堆积密度和空隙率:通过测定床层高度和床层体积,计算堆积密度和空隙率。
2. 压降与空塔气速的关系:通过测定流体通过床层时的压降和空塔气速,绘制流化曲线,确定临界流化速度。
3. 流化床流动特性的差异:观察聚式流化和散式流化的现象,分析其差异。
三、实验装置与材料1. 实验装置:流化床实验装置,包括气体流量计、压差计、温度计、气体分布板、石英砂床层等。
2. 实验材料:石英砂颗粒,空气或水。
四、实验步骤1. 准备实验装置,检查各部件是否正常。
2. 将石英砂颗粒倒入床层,调整床层高度,测量床层体积和首次静床高度。
3. 打开电源,启动风机,调节气体流量,从最小刻度开始,逐步增加流量,同时记录空气流量、空气温度、床层压降等上行原始数据。
4. 继续调节气体流量,从上行的最大流量开始,逐步减少流量,直至最小流量,记录相应的下行原始数据。
5. 测量结束后,关闭电源,再次测量经过流化后的静床高度,比较两次静床高度的变化。
6. 重复以上步骤,进行多次实验,确保数据的准确性。
五、实验结果与分析1. 床层的堆积密度和空隙率:通过测量床层体积和首次静床高度,计算堆积密度和空隙率。
结果显示,床层的堆积密度约为1.5 g/cm³,空隙率约为0.45。
2. 压降与空塔气速的关系:通过绘制流化曲线,确定临界流化速度。
结果显示,临界流化速度约为0.6 m/s。
流态化

流态化-正文简称流化,利用流动流体的作用,将固体颗粒群悬浮起来,从而使固体颗粒具有某些流体表观特征,利用这种流体与固体间的接触方式实现生产过程的操作,称为流态化技术,属于粉体工程的研究范畴。
流态化技术在强化某些单元操作和反应过程以及开发新工艺方面,起着重要作用。
它已在化工、炼油、冶金、轻工和环保等部门得到广泛应用。
流态化现象将一批固体颗粒堆放在多孔的分布板上形成床层(图1),使流体自下而上通过床层。
由于流体的流动及其与颗粒表面的摩擦,造成流体通过床层的压力降。
当流体通过床层的表观流速(按床层截面计算的流速)不大时,颗粒之间仍保持静止和互相接触,这种床层称为固定床。
当表观流速增大至起始流化速度时,床层压力降等于单位分布板面积上的颗粒浮重(颗粒的重力减去同体积流体的重力),这时颗粒不再相互支撑,并开始悬浮在流体之中。
进一步提高表观流速,床层随之膨胀,床层压力降近乎不变,但床层中颗粒的运动加剧。
这时的床层称为流化床。
当表观流速增加到等于颗粒的自由沉降速度时,所有颗粒都被流体带走,而流态化过程进入输送阶段。
(见彩图)流态化散式流态化和聚式流态化这两种流态化现象,是根据流化床内颗粒和流体的运动状况来区分的。
在散式流态化时,颗粒均匀分布在流体中,并在各方向上作随机运动,床层表面平稳且清晰,床层随流体表观流速的增加而均匀膨胀。
在聚式流态化时,床层内出现组成不同的两个相,即含颗粒甚少的不连续气泡相,以及含颗粒较多的连续乳化相。
乳化相的气固运动状况和空隙率,与起始流化状态相近。
通过床层的流体,部分从乳化相的颗粒间通过,其余以气泡形式通过床层。
增加流体流量时,通过乳化相的气量基本不变,而气泡量相应增加。
气泡在分布板上生成,在上升过程中长大;小气泡会合并成大气泡;大气泡也会破裂成小气泡。
气泡上升至床面时破裂,使床面频繁地波动起伏,同时将一部分固体颗粒抛撒到界面以上,形成一个含固体颗粒较少的稀相区;与此相对应,床面以下的床层称为浓相区。
化工原理第八章固体流态化
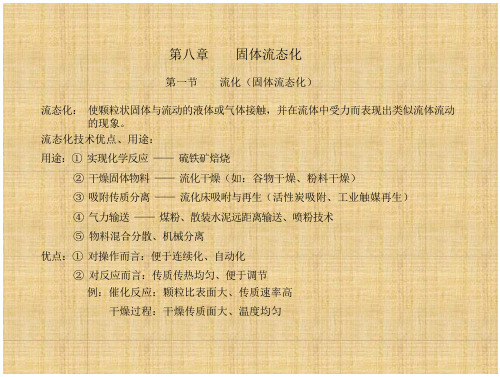
或
式中: u0 —ξ—= Cd分2 布阻板力小系孔数气(速当开孔率≤10 % 查图 6-12 P334)
为了增大△P干, 工业上常在开孔率一定下(0.4~1.4 %), 采用小孔布 气
2. 内部构件: 3. 型式: 挡网、档板 4. 作用: ① 抑制气泡成长和产生大气泡(“腾涌流化”) 5. ② 减小返混程度 6. ③ 增强两相接触 7. 粒度分布: 8. 主要影响临界流化速度umf及操作弹性比ut /umf,床层膨胀比L /Lmf及床层压降△P 9. 因此: 工业中常用小直径且粒径分布较宽的颗粒进行流化作业,粉粒可在其中起“润滑”
, ut , dp表示事出颗粒最小粒 径
3. 操作范围: (ut/umf)—— 亦可称操作弹性 比对于微细颗粒: 当 Rep<1 时,
对于大颗粒: 当 Re>1000 时,ξ = 0.44
1-4. 流化过程的主要影响因素 1. 分布板结构形式(开孔率、孔径等)作用: ① 支承颗粒、防止漏料 ② 使气体均匀分布 ③ 分散气流,形成小气泡 要求: 分布板的干板压降足够大(≥3.5Kpa)以保障气体的均布(或△P干 / △P总≥10 %)
关系: 气体的放(吸)热 = 固体颗粒吸(放) 热
在微分床层高度dH内: 故:
即: 以
对H作图, 由斜率
G —— 质量流速 Kg/m2·s at —— 单位体积床层颗粒比表面
可求得α值
b.非定态法 假定: ① 任一时刻床层中气体温度等于其离开床层时温度(Tf离 = Tf1)
② 床层中任一时刻τ的颗粒温度Ts分布均匀,但随时间变化。 ③ 无热损失。(床层表面不散失热量)
第八章 固体流态化
第一节 流化(固体流态化)
02-第1章-流态化基础知识

《洁净燃烧技术》课程讲义-循环流化床燃烧技术 洁净燃烧技术》课程讲义-
循环流化床
在循环流化床锅炉中,循环流化床状态 包括 湍流床、快速流化床和密相气力输送 ;
《洁净燃烧技术》课程讲义-循环流化床燃烧技术 洁净燃烧技术》课程讲义-
湍流床
当床内达到鼓泡流化状态后,随着流化 风速继续增大,气泡产生、合并和破裂都相 应增大,床内呈现较强烈的气固运动,气固 接触良好;床层表面有大量的气泡破裂,床 层的压力降快速地脉动,大量床料颗粒被抛 入床层上方的悬浮空间,床层仍有表面但已 相当弥散,这种床层称之为湍流流化床。 湍流床的运行风速会高于细颗粒的终端 沉降速度,而低于粗颗粒的终端沉降速度。
《洁净燃烧技术》课程讲义-循环流化床燃烧技术 洁净燃烧技术》课程讲义-
固定床(移动床) 固定床(移动床)的特征
固体物料基本不随气体运动(极个别细粉除 外),固体颗粒之间没有相对运动。 当气体流经固体颗粒时,会产生压力损失。 且压力损失随流体速度增大而增加。 在移动床中,床层固体颗粒整体相对于器壁 产生移动,但床层颗粒之间没有相对运动。 立管(料脚)中颗粒的流动状态,就属于移 动床状态。
《洁净燃烧技术》课程讲义-循环流化床燃烧技术 洁净燃烧技术》课程讲义-
鼓泡流化床
其特征是超过临界流化风 速的空气以气泡形式流过床层, 床内存在明显的密相界面。气 泡从布风板处产生,在上升过 程中不断与其它气泡合并或分 裂,到达床面后气泡破裂并飞 溅,同时将少量床料颗粒抛向 床层上方的悬浮空间。类似于 沸腾着的开水。 这是工业应用中常见的一 种流化现象,也叫聚式流化床。
冷态流化特性曲线
三个重要的特性 参数: 1-临界流化速度 2-床层压降 3-终端沉降速度
《洁净燃烧技术》课程讲义-循环流化床燃烧技术 洁净燃烧技术》课程讲义-
流态化原理与及应用
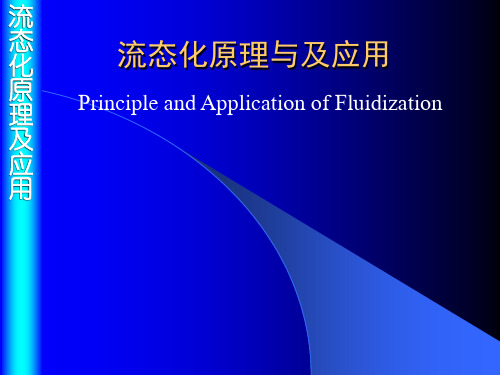
流 态
1.2、 气固流态化的形成
化 1.2.1 流态化过程
原
理
及
应
用
气力输送 Pneumatic Transport
ln Δp /ln H
( ) ( )
19:35:30
固定床 Fixed Bed
流化床 Fluidized Bed
umf
lnu
流 态
1.2、
气固流态化的形成
化 流态化形成的三个阶段:
往称这种全风帽式沸腾燃烧炉为“第一代沸腾炉”。
1975年,原西德鲁奇Lurgi)公司在第一代风幅式全沸腾炉
(也称鼓泡床燃烧炉)的燃烧装置中引入炉外分离装置,使
燃烧效率大大提高,这就是第二代沸腾炉一循环床沸腾
燃烧锅炉。设置的分离装置可较好地实现气、固分离,
使未燃尽的固体颗粒得以重新回到沪内燃烧.因而燃烧
流 态
1.2、 气固流态化的形成
化 1.2.3 流态床的基本结构
原 (1)风室
理
作用:就是使气体介质压力均匀稳定,实现气体介
南京化学工业公司采用流态化技术焙烧黄铁矿生产SO2 并制造H2SO4。
19:35:30
流
态 1.1.2 流态化的发展历史(续)
化
原 理
1957年:我国在辽宁葫芦岛采用流态化装置培烧精锌矿以生 产ZnO和SO2,获得成功。
及 50年代中期,采用新型的全沸腾风帽式流态化技术用于固
应 用
体煤颗粒的燃烧,获得良好的效果。在燃烧技术领域,往
化 1.2.2 流态化实现要素及特点
原 2、特点
理
主要优点
及
主要缺点
应 ① 气固接触比表面积大,物理 与化学过程速率高;
流态化工程原理

流态化工程原理介绍如下:流态化工程原理是指利用流态化技术进行的化学反应工程和化学工艺流程的研究。
流态化是固体颗粒在高速气流的振动作用下,呈现出类似于流体的状态,具有多孔、均匀、高效的特点。
以下是流态化工程原理的介绍。
一、流态化工程的基本原理流态化化学反应器是利用流态化技术进行化学反应的装置,其外形和固定床反应器相似。
流态床反应器依靠流化床内的气固两相混合来增加反应物质之间的接触次数,从而提高反应效率。
可以通过对流化床内的粒子尺寸、颗粒形状、气流速度等参数进行调节,实现对反应性能的优化和控制。
二、流态化工程的应用1.清洁能源领域。
流态化技术可用于生物质能的去除和提取,煤炭气化等领域,是一种清洁、高效的生产方式。
2.化学工业领域。
流态化系统可以广泛应用于化学反应、化学工艺、化学储能以及制药、农药等领域。
3.环保领域。
通过流态化技术,可以进行废物处理和节能减排,具有环保经济的双重优势。
三、流态化工程的特点1.动力学响应快。
流态化床反应器的反应介质在实际操作时,可以快速地达到热平衡和化学平衡,反应效果明显。
2.传质速率高。
在流态化床内,气体相和固体相交替运动,传质速度显著提高,有效缩短反应时间。
3.反应效率高。
随着颗粒粒径的减小,反应面积增大,从而使得反应剂互相接触的概率增加,反应速率提高。
4.易于操作和维护。
流态化床内无静止部位,床粉剧烈流动可减小床粉结块的发生,设备布局也比传统的反应器更加紧凑。
综上所述,流态化工程原理是一种有效的化学反应技术。
通过调整流化床内的气流速度、粒径分布、反应温度等参数,可以实现反应过程中多种反应物的混合,从而实现反应效果的快速优化和控制。
3.2.5高速流态化技术.
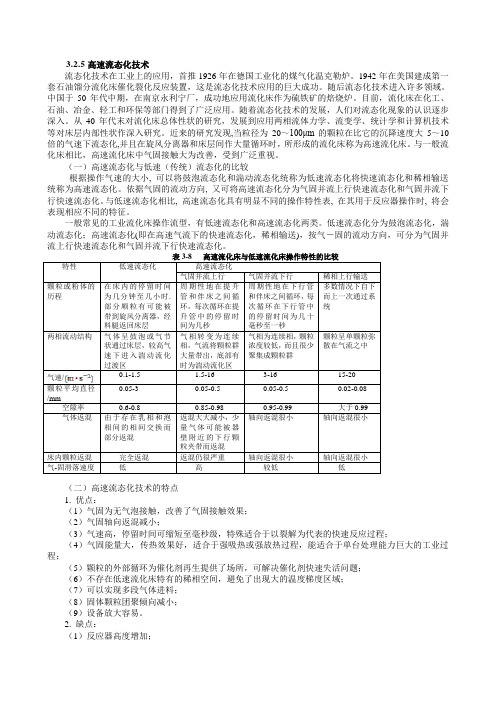
3.2.5高速流态化技术流态化技术在工业上的应用,首推1926年在德国工业化的煤气化温克勒炉。
1942年在美国建成第一套石油馏分流化床催化裂化反应装置,这是流态化技术应用的巨大成功。
随后流态化技术进入许多领域。
中国于50年代中期,在南京永利宁厂,成功地应用流化床作为硫铁矿的焙烧炉。
目前,流化床在化工、石油、冶金、轻工和环保等部门得到了广泛应用。
随着流态化技术的发展,人们对流态化现象的认识逐步深入。
从40年代末对流化床总体性状的研究,发展到应用两相流体力学、流变学、统计学和计算机技术等对床层内部性状作深入研究。
近来的研究发现,当粒径为20~100μm的颗粒在比它的沉降速度大5~10倍的气速下流态化,并且在旋风分离器和床层间作大量循环时,所形成的流化床称为高速流化床。
与一般流化床相比,高速流化床中气固接触大为改善,受到广泛重视。
(一)高速流态化与低速(传统)流态化的比较根据操作气速的大小, 可以将鼓泡流态化和湍动流态化统称为低速流态化将快速流态化和稀相输送统称为高速流态化。
依据气固的流动方向, 又可将高速流态化分为气固并流上行快速流态化和气固并流下行快速流态化。
与低速流态化相比, 高速流态化具有明显不同的操作特性表, 在其用于反应器操作时, 将会表现相应不同的特征。
一般常见的工业流化床操作流型,有低速流态化和高速流态化两类。
低速流态化分为鼓泡流态化,湍动流态化;高速流态化(即在高速气流下的快速流态化,稀相输送),按气-固的流动方向,可分为气固并流上行快速流态化和气固并流下行快速流态化。
(二)高速流态化技术的特点1. 优点:(1)气固为无气泡接触,改善了气固接触效果;(2)气固轴向返混减小;(3)气速高,停留时间可缩短至毫秒级,特殊适合于以裂解为代表的快速反应过程;(4)气固能量大,传热效果好,适合于强吸热或强放热过程,能适合于单台处理能力巨大的工业过程;(5)颗粒的外部循环为催化剂再生提供了场所,可解决催化剂快速失活问题;(6)不存在低速流化床特有的稀相空间,避免了出现大的温度梯度区域;(7)可以实现多段气体进料;(8)固体颗粒团聚倾向减小;(9)设备放大容易。
第五章 流态化与气力输送
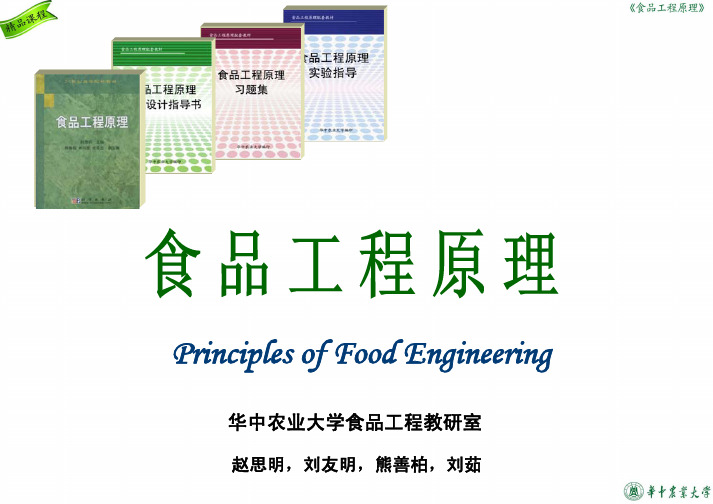
p L mf (1 mf )( s f ) g ( N / m 2 )
2.2 临界流化速度
流体流经固定床的压力降公式(层流):
p 200 f (1 0 ) 2 L0 u
2 s 30 d 2 p
200 f (1 mf ) 2 L mf
s
0.065
1.0 0.9 0.8 0.7 0.6 0.5 0.4 0.3 0.2 0.1 0.0 0.1 1 10 Re pt 100 1000
流化数(fluidization number)K: K u
流化床操作速度u必须保持在umf和ut之间;
u mf
计算umf时,须用床层中实际颗粒粒度分布的平均直径; 计算ut时,须用具有相当数量的最小颗粒粒度; ut/umf 反映了流化操作的机动灵活性; 大颗粒的ut/umf值较小,说明其操作灵活性较小颗粒差; u/umf的值常在10:1和90:1之间。
C mf 0 .0007 Re pmf
u mf 0 .00923 dp
1 .82
得Cmf 与Repmf的关系: 则:
① 当Repmf<5时: ② 当Repmf>5时:
0 .063
( s f ) 0.94
0 .88
f
f
0 .06
(m / s)
u mf ' FG u mf
对细颗粒,Rep<0.4: 对大颗粒,Rep>1000:
ut 91.6 u mf
ut 8.72 u mf
工业上常用的操作速度为0.2~1.0m/s。
提高设备生产能力的措施:
采用尽可能高的操作速度; 增加床层高度; 在床层中设置挡板或挡网; 改进粉尘回收系统; ……
- 1、下载文档前请自行甄别文档内容的完整性,平台不提供额外的编辑、内容补充、找答案等附加服务。
- 2、"仅部分预览"的文档,不可在线预览部分如存在完整性等问题,可反馈申请退款(可完整预览的文档不适用该条件!)。
- 3、如文档侵犯您的权益,请联系客服反馈,我们会尽快为您处理(人工客服工作时间:9:00-18:30)。
流态化技术第一章定义:流态化是一种使固体颗粒通过与气体或液体(流体)接触而转变成类似流体状态的操作。
一、流态化形成的过程1.固定床阶段气流对颗粒的曳力 + 气流对颗粒的浮力 < 颗粒受到的重力床层体积固体颗粒总体积床层体积空隙率-=ε2.流态化床阶段气流对颗粒的浮力 = 颗粒受到的重力 压降△P = 单位截面积上床层物料的重量 不变不变,但P L L U ∆∴-↑↑→↑→)1(εε3.气力输送阶段 (气流床)气流对颗粒的曳力 + 气流对颗粒的浮力 > 颗粒受到的重力Umf ——临界流化速度,是指刚刚能够使固体颗粒流化起来的气体空床流化速度,也称最小流化速度。
Ut ——带出速度,当气体速度超过这一数值时,固体颗粒就不能沉降下来,而被气流带走,此带出速度也称最大流化速度。
操作速度、表观流速(U )——是指假想流体通过流化床整个截面(不考虑堆积固体粒子)时的截面平均流速(也称空塔速度或空管速度),用U 表示。
注意P2图1.2两条线不重合的原因:该页第四段(非自然堆积)二、形成流态化的条件1.有固体颗粒存在2.有流体介质存在3.固体与流体介质在特定条件下发生作用三、流态化过程具有的特点1.类似液体的特性(物性参数)2.固体颗粒的剧烈运动与迅速混合3. 强烈的碰撞与摩擦4.颗粒比表面积大5.气体与颗粒的接触时间不均匀四、流态化过程中的不正常现象1.沟流2.腾涌 3.分层 4.气泡五、气-固流化床的一般性评价1.良好的床层均温性 2.较高的传热传质速率 3.输送能力大4.可利用或加工粉末状物料流态化可以分为聚式流化态和散式流化态。
气泡相:就是内部几乎没有固体颗粒,仅在其边壁或 外表面 有固体颗粒环绕的运动空间乳化相:指的是固体颗粒与气体介质的混合区域第二章A 类: 细 大多数工业流化床反应使用的催化剂属于此类。
B 类: 粗 鼓泡床大都用此颗粒C 类: 极细 在气固催化反应中很少采用,但同相加工中采用较多,如明矾综合利用。
D 类:极粗 只适用于喷动床中,如谷物干燥和煤粒燃烧均属于此类书上图2.4分析理想与实际的区别(1)存在一个“驼峰”BCD ,原因:初始时颗粒排列紧密(2)DE 线右端向上倾斜,原因:颗粒间碰撞和颗粒与器壁摩擦引起的损失(3)有波动(气固系统),原因:气泡运动、破裂积相等球体体积与实际颗粒体颗粒的表面积球体的表面积)(=s φ 算术平均粒径最大 几何平均粒径次之 调和平均粒径最小 (会选择公式) 通常求临界流化速度的两种方法:实验和计算P19例题已知催化剂颗粒的平均直径为98um ,在20℃ 和0.1MPa (1atm )下用空气进行流化。
有关物性参数如下:4.0,.1078.1/001204.0,1,/1533=⨯====-mf f s s s pa cm g cm g εμρφρ试求在此条件下的临界流化速度。
解:假定Re<20,按式 ()g d U mf mf f s p s mf ⎪⎪⎭⎫⎝⎛--=εεμρρφ115032()sm U mf /1076.38.94.014.01078.110)001204.01(150108.91335326---⨯=⨯⎪⎪⎭⎫ ⎝⎛-⨯⨯-⨯⨯= 20025.01078.1108.9204.11076.3Re Re 553<=⨯⨯⨯⨯⨯==---μρp f mf d U ,验证 所以假定成立浮重力与摩擦阻力相等时所对应的颗粒速度即为颗粒的终端速度t U 会求雷诺数μρu d e p =R在流态化技术中,通常将操作气流速度U 与起始流态化速度mf U 之比称为流化数N 。
第三章简单两相理论定义:高于临界流态化所需的气体流量为超流量。
两相理论是以假设超流量以气泡形式流经床层为基础的。
最早的两相理论假定乳化相维持初临界化状态,即空隙率仍为εmf ,其空截面气速仍为Umf ,超流量(U-Umf )Ab 全部以气泡的形式流经床层修正后:乳化相中气流速度仍为Umf ,从通过流化床层中的总流量UAb 中减去流经乳化相的气体量 UmfAb (1-b ε)(b ε为气泡滞留量),气泡相的总流量应为Ab [U-U mf(1-b ε)] 。
气泡上升速度仅与气泡的直径有关。
气泡周围被这一循环气体所渗透的区域称为气泡晕流化床中气泡运动引起的混合现象 :1.固体颗粒的混合2.气体的混合 将膨胀高度与起始流化时的床高之比定义为膨胀比b mfmf mf fL L R ρρεε=--==11气泡相模型:1. 戴维森模型(简洁)2.国井-列文斯皮尔模型(着眼于整个流化床)床中只存在U>Ut 的小颗粒,这段允许大颗粒从气流中得到分离的高度称为分离高度TDH(F)第四章流化床层与容器壁面,为什么传热速率比较高?答:由于硫化床层中的气体与固体颗粒的激烈搅拌与混合,造成气-固两项之间接触面积很大,杰出效果良好,对两相之间的床层温度与湿度,都非常均匀。
传热的动力是温差,传质的动力则是浓度差影响气体与颗粒间传热、传质过程的因素有:(1)气体与颗粒间的相对速度U0,这是一个很重要的参数,也是流化床的主要操作参数之一;(2)流体的物理性质,如ρ、λ、c 、μ(ν)等;(3)颗粒的平均直径dp 。
影响流化床中气体与固体颗粒间传热传质的主要因素:1流化速度 2气泡的直径3床截面积与布风板 4颗粒平均直径5气体的物性参数影响流态化床层与壁面之间换热的因素有:1.流化床的操作参数,如表观气速U 、ε等;2.物性参数dp 、 μ、λ、ρ、cp ;3.几何参数,如DT 、L 等。
流态化床层与壁面间的传热机理1.膜控制机理(边界层模型)2.乳化团传热机理3.固体颗粒传热+边界层传导机理第五章流化床燃烧特点:1. 燃料适应性广2.煤粒在流化床内有较长的停留时间3 清洁燃烧 4.负荷调节性能好 5.灰渣综合利用性能好6.流化床燃烧热强度大7.床内传热能力强煤粒的燃烧过程:(1)煤粒被加热和干燥;(2)挥发分的析出和燃烧;(3)煤粒膨胀和破裂(一级破碎);(4)焦炭燃烧和再次破裂(二级破碎)及炭粒磨损 煤在流化床内的燃烧过程大致可分为:挥发分析出燃烧和焦炭燃烧两个阶段 三个不同的燃烧区 1k k K k αα=>>时,当此时的燃烧状态称为扩散燃烧。
(k 为化学反应速度 2k K k k =<<时,当α燃烧状态称为动力燃烧。
k α为传质系数) 3在动力燃烧区与扩散燃烧区之间,叫做过渡燃烧区。
循环倍率:单位时间内送回床内的飞灰量与单位时间内加入床内的燃煤量之比。
影响脱硫效果的主要因素有流化速度、温度、Ca/S 摩尔比及脱硫剂特性等。
◆ NO 的生成机理:温度型NO 是指燃烧用空气中的氮气,在高温下氧化产生的氮氧化物◆ 快速温度型NO 是指碳化氢燃料过多时燃烧产生的氮的氧化物◆ 燃料型NO 是指燃料中含有氮的化合物,在燃烧过程中氧化而生成氮的氧化物降低NOX 的方法↓↑→↓→↓↓→→+↓↓↓→NO CO NO O N NO NH O NH NH NO CO T NO T x ααα燃烧)低(不超过,注意控制注射适量的或旋风分离器上部在循环流化床炉膛上部)注射(的还原对炉膛下部缺氧,有利于分段燃烧保证正常燃烧时的4%6~%5][,3)2()1(2333循环倍率:分离器循环灰量与给煤量之比(与之前意思相同)。
第六章流态化装置需要确定的内容 :床型 、床径、床高、换热系统和操作控制 、粉粒回收系统 、布风板和预分布器 、内部构件 、给料和排料系统。
◆ 影响流化质量的因素:固体颗粒的性质 包括:颗粒的粒度及其分布、颗粒密度ρs 、颗粒的形状系数φs 、颗粒的流动性、颗粒的特殊性质等。
◆ 流体的性质 ρf 、μ 、流体的平均操作速度和进床速度、方向和分布 ◆ 床高-直径比L0/DT◆ 内部构件流化床的操作速度P80(什么时候高?什么时候低?)1、布风板开孔率较大,超过一定值,可以发现,开始流化后总压降开始下降,然后再上升,如图ab线。
具有这种特性的布风板称为低压降布风板。
(不稳定)2、布风板开孔率较小,则总压降始终随流速增加而上升,如图中ac 线。
这种布风板称为高压降布风板。
(不经济)3、在高压降和低压降之间有一种特殊情况,如曲线ad ,即开始流化后,总压降为一定值保持不变,这时的布风板就称等压降布风板,而与此情况相应的开孔率即称为初始开孔率ak 。
布风板压降2212ga u P fρξ=∆(ξ阻力系数、u 流化速度、a 布风板的开孔率、f ρ流体密度、g 重力加速度)分布装置的作用有三:(1)它必须具有均匀分布流体的作用,同时其压降又最小。
这可以靠正确地选取布风板的开孔率或布风板压降与床层压降之比,以及选择适当的预分布手段来达到;(2)它必须使流化床有一个良好的起始流化状态,保证在布风板附件创造一个良好的气-固接触条件,使所有颗粒都动起来,从而排除形成“死床”的可能;(3)在长期操作过程中,布风板不被堵塞和磨蚀。
在操作过程中或在突然停止操作后,固体颗粒不流入布风板下面,以免造成恶劣后果。
风室的作用:具有气流分配的作用。
第七章流态化技术用作反应器的性能的优点:1、颗粒流动平稳,类似液体,其操作可连续自动控制,且易处理;2、固体颗粒混合迅速,反应器内易于处于等温状态,操作可以简单而可靠地加以控制;3、固体颗粒在两个流化床层之间循环,使得大型反应器中产生的或需供给的大量热量 有传递的可能;4、宜大规模操作;5、气体和固体颗粒之间的传热和传质速率较其它接触方式为高;6、流化床与浸没在床层中构件之间的传热速率较高,因此流化床中所需换热面积较少。