铸件毛坯的质量要求
铸件质量检查标准

一、目的:为了确保外协标准铸件、成品铸件质量符合工艺、技术要求,为了满足产品特性,结合相关文件特制定本标准。
二、适用范围:本办法适用于我公司产品外协、采购、装配过程中、全部铸件质量检查标准。
三、检查标准:3.1、铸件结构要符合设计要求或加工工艺要求。
无特殊要求时按铸件通用标准执行。
通用标准等级分为:交货验收技术条件标准;铸件质量分等通则(合格品、一等品、优等品)材质、检验方法;工艺和材料规格等一般性规则。
3.2、铸件成品检验。
铸件成品检验包括:相关技术条件的检验、表面质量检验、几何尺寸检验等项内容。
①相关技术条件的检验。
包括铸件化学成分、机械性能等检验内容。
机械性能检验和金相及化学成分检验等技术条件的检验,均必须按相关国家标准执行检验(此处略)。
②表面质量检验。
机械加工生产一线人员在工艺过程中对铸造毛坯的检查主要是对其外观铸造缺陷(如有无沙眼、沙孔、疏松、有无浇不足、铸造裂纹等)的检验;以及毛坯加工余量是否满足加工要求的检验。
表3-1铸件外观质量检验项目(GB6060.1—1985)表3-2 铸件表面粗糙度(R a 值μm)(GB6414—1986)③铸件成品几何尺寸检验。
主要一种是采用划线法检查毛坯的加工余量是否足够。
另一种方法是:用毛坯的参考基准面(也称工艺基准面)作为毛坯的检验基准面的相对测量法(需要测量相对基准面的尺寸及进行简单换算)。
表3-3 铸件尺寸公差数值(mm)(GB6414—1986)注:铸件基本尺寸≤10mm 时,其公差等级提高3 级;大于10mm 至等于15mm 时,其公差等级提高2级;大于16mm 至25mm 时,其公差等级提高1 级。
附表:铸件质量检验与缺陷处理实用技术。
压铸件毛坯质量检验标准
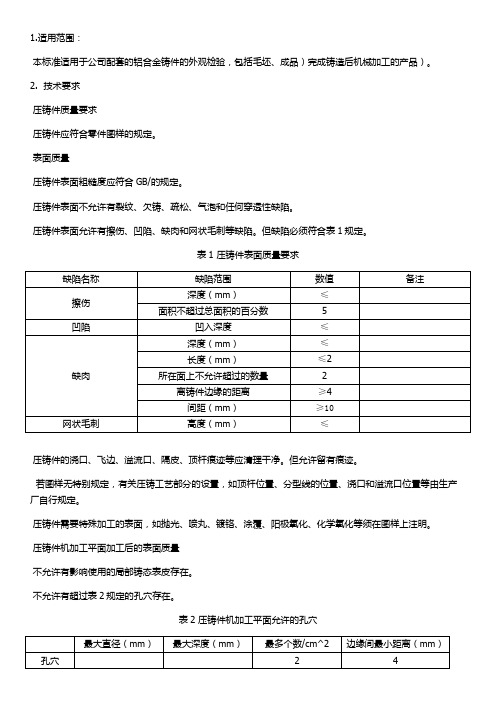
1.适用范围:本标准适用于公司配套的铝合金铸件的外观检验,包括毛坯、成品)完成铸造后机械加工的产品)。
2. 技术要求压铸件质量要求压铸件应符合零件图样的规定。
表面质量压铸件表面粗糙度应符合GB/的规定。
压铸件表面不允许有裂纹、欠铸、疏松、气泡和任何穿透性缺陷。
压铸件表面允许有擦伤、凹陷、缺肉和网状毛刺等缺陷。
但缺陷必须符合表1规定。
表1 压铸件表面质量要求压铸件的浇口、飞边、溢流口、隔皮、顶杆痕迹等应清理干净。
但允许留有痕迹。
若图样无特别规定,有关压铸工艺部分的设置,如顶杆位置、分型线的位置、浇口和溢流口位置等由生产厂自行规定。
压铸件需要特殊加工的表面,如抛光、喷丸、镀铬、涂覆、阳极氧化、化学氧化等须在图样上注明。
压铸件机加工平面加工后的表面质量不允许有影响使用的局部铸态表皮存在。
不允许有超过表2规定的孔穴存在。
表2 压铸件机加工平面允许的孔穴压铸件机械加工螺纹的表面质量压铸件机械加工螺纹的头两扣不允许有任何缺陷,其余部分螺纹不允许有表3所规定的孔穴缺陷。
表3 机械加工螺纹规定的孔穴缺陷范围压铸件不底孔加工后的螺纹表面质量见表4的规定表4 不铸底孔加工后的螺纹表面质量压铸件机械加工孔加工后表面的孔穴规定范围见表5。
表5 机械加工孔表面的孔穴规定范围压铸件内部质量压铸件若能满足其使用性能要求,则压铸件本质缺陷不作为报废的依据。
压铸件内部不允许有冷隔缺陷。
压铸件内部允许有气孔、疏孔、夹杂等缺陷,但孔穴缺陷最大直径不超过壁厚的1/8,孔穴数量在任何剖面上不超过2个/cm2 。
重要压铸件的受力部位须进行解剖检查,符合表6中的规定。
表6 压铸件指定解剖部位内部质量规定其它性能要求应符合GB/T15114的规定。
3 试验方法及检验规则化学成分铝合金化学成分的检验方法,检验规则和复检应符合GB/T15115的规定。
化学成分的试样也可取自压铸件,但必须符合GB/T15115的规定。
力学性能力学性能的检验方法,检验频率和检验规则应符合GB/T15115的规定。
QS GY-004-2014 模具外协毛坯铸件质量检验标准

模具外协毛坯铸件质量检验标准1 外观铸件表面应清理干净,修整飞边毛刺,去除补贴、粘砂、氧化铁皮及内腔残余物等。
应无影响使用的气孔、砂眼、夹渣、缩孔、缩松、裂纹、偏心、变形等缺陷。
毛坯如果出现缺陷,供应商应将缺陷的实际情况书面告知豪迈科技公司,由豪迈科技公司判定是否可以让步使用,工件毛坯面未经豪迈公司许可严禁焊补,详见“毛坯异常情况处理程序”。
2 外形尺寸有毛坯图的依据毛坯图进行检验。
有零件图的依据JB/T 5000.6-2007,检验余量大小。
3 硬度(HBS)将工作面磨去氧化皮得一光滑平坦表面后(粗糙度一般不低于Ra1.6um),检测硬度值,试验力作用方向应与试验面垂直。
4 理化分析4.1中国GB标准:一般工程用铸造碳钢件[GB/T 11352—2009]4.2中国GB标准:焊接结构用碳素钢铸件[GB/T 7659--2010]4.3中国GB标准:一般工程与结构用低合金铸钢件[GB/T14408—1993]4.4中国JB标准:大型低合金钢铸件[JB/T 6402-2006]4.5中国GB标准:球墨铸铁件[GB/T 1348-2009]4.6中国JB标准:重型机械通用技术条件(第6部分:铸钢件)[JB/T 5000.6-2007]5产品内部缺陷检验5.1铸件内部应无影响使用的气孔、砂眼、夹渣、缩孔、缩松等缺陷。
5.2中国JB标准:重型机械通用技术条件(第14部分:铸钢件无损探伤)[JB/T 5000.14-2007]6 拉伸试验与冲击试验6.1供应商发货时,提供与工件规格数量相对应的质量证明。
6.2在一般(无特殊要求说明)情况下,每炉次号提供1件随件Y形试块,以备检测时使用,注意将试样标识清楚。
另在毛坯采购时,特殊标明需要试棒的,按采购单提供试棒。
6.3在设计科特殊要求或重要零件难于控制质量的情况下,随工件提供“附铸试块”。
在“材料采购报表”中注明“附铸试块”字样。
7 标志与质量证明书7.1供应商锻坯供货标识应按豪迈公司指定方式进行。
铸造毛坯件检验规范
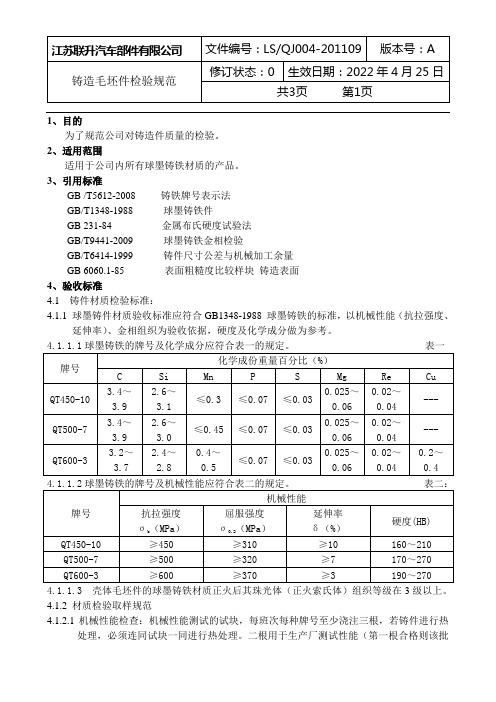
1、目的为了规范公司对铸造件质量的检验。
2、适用范围适用于公司内所有球墨铸铁材质的产品。
3、引用标准GB /T5612-2008 铸铁牌号表示法GB/T1348-1988 球墨铸铁件GB 231-84 金属布氏硬度试验法GB/T9441-2009 球墨铸铁金相检验GB/T6414-1999 铸件尺寸公差与机械加工余量GB 6060.1-85 表面粗糙度比较样块铸造表面4、验收标准4.1 铸件材质检验标准:4.1.1 球墨铸件材质验收标准应符合GB1348-1988 球墨铸铁的标准,以机械性能(抗拉强度、延伸率)、金相组织为验收依据,硬度及化学成分做为参考。
4.1.1.3 壳体毛坯件的球墨铸铁材质正火后其珠光体(正火索氏体)组织等级在3级以上。
4.1.2 材质检验取样规范4.1.2.1机械性能检查:机械性能测试的试块,每班次每种牌号至少浇注三根,若铸件进行热处理,必须连同试块一同进行热处理。
二根用于生产厂测试性能(第一根合格则该批次合格,余下试块(留有生产日期、包次标识)留存。
若第一根试块不合格,测试剩余二根,若第二根不合格则该批次产品全部报废,若第二根合格,应加试第三根,合格则判定该炉产品合格,若第三根不合格则该批次产品全部报废)。
材质检验报告(原档)保存期为5年。
4.1.2.2金相组织检查:球铁铸件从每包铁水的最后一型附铸金相试块或铸件本体进行金相检验,依次往前直到合格(或本包铁水所浇铸件检验完)为止。
附铸试块应能代表本体。
若试块不好,应对铸件本体破件进行检验。
若金相检验由问题,加倍抽查。
金相本体试块应按天分类以月为单位保存,保存期为6个月,检验报告保存期5年。
球化等级要求在3级以上,石墨大小要求为5~7级。
4.1.2.3化学成分检查:每天必须分析每炉铁水(炉前)及至少两炉铸件(炉后)的化学成分。
炉前主要化验C、Si和S,炉后所有元素全部化验。
每天第一炉溶清后必须检测C、Si、Mn、P和S,之后C、Si每炉化验检测。
铸造毛坯件质量检验规范
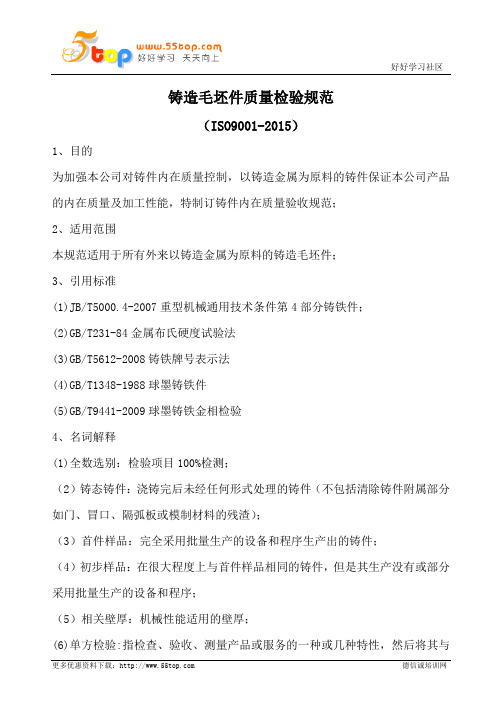
铸造毛坯件质量检验规范(ISO9001-2015)1、目的为加强本公司对铸件内在质量控制,以铸造金属为原料的铸件保证本公司产品的内在质量及加工性能,特制订铸件内在质量验收规范;2、适用范围本规范适用于所有外来以铸造金属为原料的铸造毛坯件;3、引用标准(1)JB/T5000.4-2007重型机械通用技术条件第4部分铸铁件;(2)GB/T231-84金属布氏硬度试验法(3)GB/T5612-2008铸铁牌号表示法(4)GB/T1348-1988球墨铸铁件(5)GB/T9441-2009球墨铸铁金相检验4、名词解释(1)全数选别:检验项目100%检测;(2)铸态铸件:浇铸完后未经任何形式处理的铸件(不包括清除铸件附属部分如门、冒口、隔弧板或模制材料的残渣);(3)首件样品:完全采用批量生产的设备和程序生产出的铸件;(4)初步样品:在很大程度上与首件样品相同的铸件,但是其生产没有或部分采用批量生产的设备和程序;(5)相关壁厚:机械性能适用的壁厚;(6)单方检验:指检查、验收、测量产品或服务的一种或几种特性,然后将其与指定要求相比较以确定产品是否合格的行为;(7)连续检验:指对生产一段时间后的大量相同规格的铸件的特性和/或生产参数进行定期检验;(8)跳跃检验:指对生产一段时间后的大量相同规格的铸件的特性和/或生产参数进行间断性检验;(9)试件:样品的一部分,有特定的尺寸,经过机械加工也可能没有经过机械加工,并严格遵守所要求的试验条件;5、铸件内在质量验收总则球墨铸件材质验收标准应符合GB1348-1988球墨铸铁的标准,以机械性能(抗拉强度、屈服强度、延伸率)、金相组织、硬度及化学成分为验收判定依据;5.1铸件化学成分(1)如果未在图纸或询价单或订单或者质保协议中另行规定,对于铸造材料的化学组成,应采用相关材料标准的要求;(2)如果未在图纸或询价单或订单或者质保协议中另行规定,铸造材料化学组成的有关数据应特指液体金属,即球化后浇筑前的(炉前)浇包分析;(3)如果相关材料标准和订单或询价单等都不含有铸造材料化学组成的任何有关数据,如只规定了材料的机械性能,则制造商可以自行选择适当的化学组成,但必须符合铸件使用地(毛坯或半成品或者成品的最终使用地点)的环保等法律法规要求;(5)化学组成在要求对某一铸件进行化学分析时,化学元素允许偏差要符合材料标准给出的偏差或符合采购方与制造商之间通过协议确定的偏差。
资料│球铁铸件验收标准

资料│球铁铸件验收标准一、引用标准GB9441-88 球墨铸铁金相检验GB6060.1-85 表面粗糙度比较样块铸造表面 GB321-81 硬度试验二、技术要求三、机械性能机械性能为铸态毛坯本体试块测试值。
1、金相组织按GB9441-88《球墨铸铁金相检验》2、石墨铸件毛坯本体的球化率在60%以上,球化级别80%为1-3级,最差部位不低于5级,球径为5-7级。
3、基体(参考)铸件本体的基础组织为:铁素体80%以上,碳化物含量小于2%。
4、几何形状与尺寸铸件应符合相应的毛坯图尺寸规定。
铸件错型≤0.5mm,砂芯歪斜量≤0.8mm。
5、表面质量①铸件毛坯表面应无粘砂、氧化皮等缺陷,铸件毛坯表面的浇冒口、出气孔、多肉、飞边、毛刺等清除干净。
②铸件毛坯不允许有裂纹、缩孔、疏松、冷隔等影响使用性能的铸造缺陷。
③铸造毛坯非加工表面粗糙度R a≤100粗糙度评定按GB6060.1-85的规定进行。
④铸造毛坯不允许有锈蚀。
⑤铸件外表气孔和渣孔加工部位:直径≤Φ3mm,最大深度≤1.5mm,Φ2mm以上气孔数量每侧面不多于4个,Φ2mm以下气孔数量每侧面不多于7个。
非加工部位:直径≤Φ2mm,最大深度≤1.5mm,Φ2mm以上气孔数量不多于2个,Φ2mm以下气孔数量不多于5个。
6、铸件上的缺陷不允许修补。
7、批次的标识铸件毛坯必须在其本体的表面铸出永久性炉次标志即炉号。
炉号用六位组成。
第一位表示年号,取年号尾数,第二、三位表示月号,第四、五位为H号,第六位为流水号(当一炉铁水分作多包球化浇注时)× ×× ×× ×年号尾数月号日号流水号四、检验方法1、在提供最处样件时,铸件必须经解剖检测,X射线检测或Y射线检测无缩孔、缩松、裂纹等缺陷;在正常生产时,为确保质量稳定,要定期进行上述方式检测。
并且抽1‰铸件进行解剖检测。
生产设备改变、材料改变、更换模具、更改工艺或更换操作者时,铸件必须经以上解剖与检测。
铸件毛坯

铸造毛坯件的技术要求TT630-357(不适用于轮毂,下环和叶片毛坯)1.0应用范围这些技术要求应适应水轮机铸钢毛配件,并且与毛配件图纸要求提供的铸造毛配件的钢材相一致,初加工的20Л, 25Л, 35Л, 20ГСЛ, 08ГДНФЛ, 10Х12НДЛ, 06Х12Н3ДЛ, 08Х15Н4ДМЛ, 08Х13Н4ДМЛ等级钢。
2.0 一般要求3.1对于表1中材料的指定的化学成分允许的元素含量偏差列在表格2(Table2)。
3.2硫和磷的总含量不能超过0,050%.4.0热处理4.1热处理根据同购方协商一致的热处理规范4.2允许进行两次完全的重复热处理,回火次数不限。
5.0机械性能要求5.1最终热处理后(包括修复缺陷后回火)的毛坯件材料的机械性能和硬度应满足图表3要求图表3 ,5.2机械性能试验样本应从分离的铸件测试样本上取得,或者在铸件的测试带上取得。
对于铸件机械性能测定要求的测试带在毛坯图纸中被指出。
5.2.1. 单独的铸件试验样本从一组铸件中取样,这些铸件由相同的材料浇注并经过共同的热处理。
试验样本尺寸满足所有必要试验的需要包括重复试验需要的双倍数量试验样本。
对于1000Kg及以上的每个铸件应做为一个取样对象。
5.2.2. 在开始制造前,除非试验样本的尺寸在毛坯件图纸中没有被指出,否则试验样本在铸件上的位置和尺寸对于制造商和买方应是一样的并且和买方要求的一致。
试验样本在从铸件上取下前,制造商应在铸件上进行标记并且伴随铸件制造的全过程。
试验样本的尺寸应满足所有试验的需要,包括重复试验所需要的双倍数量样本。
制造商应提交给买方一份样本,这份样本需是已经过全部热处理,其中包括通过焊接进行缺陷处理后的回火处理。
5.3机械性能测试样本应按如下从测试样本上取样:如果壁厚至56mm,样本轴线应从表面深入14mm取样。
如果壁厚超过56mm,样本深度为样本厚度从表面算起的1/4深。
5.4机械性能测试的样本数量:1-拉伸试验,3-冲击试验或冲击弹性试验。
铸件质量检验标准

—
—
—
—
—
—
—
—
0.64
0.72
0.80
0.9
1.0
1.1
1.2
1.4
1.6
1.8
2.0
2.2
2.6
2.8
3.2
3.6
4.0
4.6
5
6
7
7
8
9
10
11
13
1600
2500
4000
6300
2500
4000
6300
10000
—
—
—
—
—
—
—
—
—
—
—
—
—
—
—
0.24
0.26
0.28
0.32
0.36
0.40
0.46
0.50
0.56
0.64
0.70
0.78
0.9
1.0
1.1
1.3
1.4
1.6
1.8
2.0
2.2
2.6
2.8
CF3M
ASTM
A351
0.03 1.5 1.5 17~21 0.04 0.04 9~13 2~3
CF8M
ASTM
A351
0.08 1.5 1.5 18~21 0.04 0.04 9~12 2~3
CG3M
ASTM
A351
0.03 1.0 2.0 18~20 0.035 0.03 11~15 3~4
铸铜件制作技术要求

铸铜件制作技术要求
一、总则
1、本技术要求所提出的是最低标准的技术要求,并未对一切技术细节做出规定,也未充分引述有关标准和规范的条文,乙方应保证提供符合有关标准和技术文件的优质产品。
2、乙方的产品质量必须是质量可靠,能够确保使用要求。
3、甲乙双方共同遵守国家和地方有关安全生产的法律、法规和规定,认真执行国家、行业、企业安全技术标准。
二、工程概况
工程名称:铸铜件制作
企业资质要求:乙方必须是独立法人企业,有相应营业执照,并有从事相应工作的业绩合同。
三、施工要求
1铸铜件外委分为毛坯和产品两列。
毛坯要求铸造后粗加工,单边留量2-3mm,成品严格按照图纸尺寸加工,并且确保表面无气孔、砂眼、裂纹等缺陷。
2.甲方提出的技术参数、质量要求具体以需要制作的图纸技术参数、质量要求为依据,同时甲方以图纸的技术参数、质量要求作为验收标准,按标准组织验收。
3.乙方保证备件的制造、验收应遵照备件图纸和技术协议要求。
依据甲方提供的图纸要求进行加工制造,同时加工完成后的产品应当满足图纸要求。
4.乙方未严格按照合同约定标准、技术要求以及图纸要求进行加工制作,达不到双方约定质量要求的,乙方应当无条件进行维修或更换,直至达到甲方正常使用要求。
5.乙方在依照甲方要求进行产品制作期间,发现甲方提供图纸的技术参数、质量要求不合理的,应当于接到图纸3日内日书面通知甲方修改,超过期限没有提出异议的,视为同意甲方提出的技术参数、质量要求及验收标准。
6、如因乙方制造原因不能按甲方要求解决质量问题,经甲乙双方共同确认后甲方有权寻求第三方解决,费用由乙方承担。
铸件表面质量验收标准

铸铁件验收项目及标准铸件的表面质量主要包括铸件的表面缺陷、尺寸精度、形状偏差、表面粗糙度、表面清理质量等;1、铸件表面缺陷的检验1.1表面缺陷检验的一般要求1.1.1 铸件非加工表面上的浇冒口必须清理得与铸件表面同样平整,加工面上的浇冒口残留量应符合技术要求,若无要求,则按表8执行;1.1.2 在铸件上不允许有裂纹、通孔、穿透性的冷隔和穿透性的缩松、夹渣等机械加工不能去除的缺陷;1.1.3 铸件非加工表面的毛刺、披缝、型砂、砂芯等应清理干净;1.1.4 铸件一般待加工表面,允许有不超过加工余量范围内的任何缺陷存在;重要加工面允许有不超过加工余量2/3的缺陷存在,但裂纹缺陷应予清除;加工后的表面允许存在直径*长度*深度小于等于2*2*2的非连片孔洞的铸造缺陷;1.1.5 作为加工基准面(孔)和测量基准的铸件表面,平整度小于等于2.0毫米、粗糙度Ra50以内;1.1.6 铸件表面气孔、砂眼、夹渣面积不大,但比较分散或者有连片麻点的表面不予接收;1.1.7 除技术要求特别注明的铸件外,对于表面有气孔、缩孔、砂眼等缺陷的铸钢件允许补焊,但铸铁件未经允许不得焊补(铸铁件实行一案一判的原则)但补焊面积不允许超过铸件面积的10%,焊接质量应符合JB/T 5000.7-2007标准要求,补焊后必须退火、机械性能达到图纸要求,且不得有渗漏及影响外观的缺陷;1.2铸件外观质量等级表1 铸件外观质量等级2、铸件尺寸的检验2.1铸件毛坯尺寸公差铸件尺寸公差应按毛坯图或技术条件规定的尺寸公差等级执行,当技术文件未规定尺寸公差时,则应以GB6414-1999为依据,并按照表2选定公差值(粗线框内为推荐使用公差等级);(单位:mm)表2铸件尺寸公差2.2铸件分型面处最大错型值应不得超过表2所示公差值,当需进一步限制错型量时,应从表3中选取;表3 错型值(GB6414-1999)2.3铸件加工余量应符合表4的规定,有特殊要求的表面应在技术要求中单独标注加工余量;表4 加工余量(单位:mm)3、表面粗糙度检测表面粗糙度总体检测原则依据图纸要求,当图纸无要求是执行国标GB/T15056-1994;3.1一般情况下,表面粗糙度要求 Ra50,铸件难以清理的部位,局部允许Ra100,待加工表面允许降低1级;3.2.使用面积法作为验收依据面积法常用的比较样块评定铸件表面粗糙度;方法如下:3.2.1 铸造表面粗糙度比较样块应符合GB6060.1-1997标准;3.2.2 按照国标BWZ001-88评定铸件表面粗糙度的等级;3.2.3 铸件的浇道、冒口、修补的残余表面及铸造表面缺陷(如粘砂、结疤等)不列为被检表面;3.2.4 以铸造表面粗糙度比较样块为对照标准,对被检铸件的铸造表面用视觉或触觉的方法进行对比;3.2.5 用样块对比时,应选用适于铸造合金材料和工艺方法的样块进行对比;3.2.6 被检的铸造表面必须清理干净,样块表面和被检表面均不得有锈蚀处;3.2.7 用样块对比时,砂型铸造表面被检点数应符合表7的规定;特种铸造表面被检点数应按表8的规定加倍;被检点应平均分布,每点的被检面积不得小于与之对比面的面积;表7 被检铸造表面最低检测数3.2.8 当被检铸造表面的粗糙度介于比较样块两级参数值之间者,所确定的被检铸造表面的粗糙度等级为粗的一级;3.2.9 对被检铸造表面,以其80%的表面所达到的最粗表面粗糙度等级,为该铸造表面粗糙度等级;3.3铸件表面清理检测3.3.1 铸件几何形状必须完整,非加工面上的清理损伤不应大于该处的尺寸偏差,加工面上的损伤不应大于该处加工余量的1/2;3.3.2允许铸件表面有少量的局部低凹或打磨痕迹,在直径不大于 8mm,并能保证铸件规定的最小的壁厚;3.3.3为去除铸造缺陷而打磨后的铸件表面粗糙度应与一般铸件表面粗糙度基本一致;3.3.4除特殊情况外,铸件表面允许残留的浇冒口、毛刺,多肉残余量应按表8的要求进行;表8 浇冒口、毛刺、多肉等允许残留量值3.3.5铸件表面须经过防锈处理,保证在铸件进入面加工时不得有任何的锈蚀;3.3.6铸件表面如有油漆要求的,必须按有关涂装规定执行;4、铸件重量检测对于没有特殊要求的铸件,重量偏差可以不作为验收依据;如果技术条件有要求,供需双方协商后,铸件的重量偏差也应作为验收依据,一般应符合表6的规定;表6 铸件重量偏差。
铸铁件质量标准(YBJQ101.1.88)
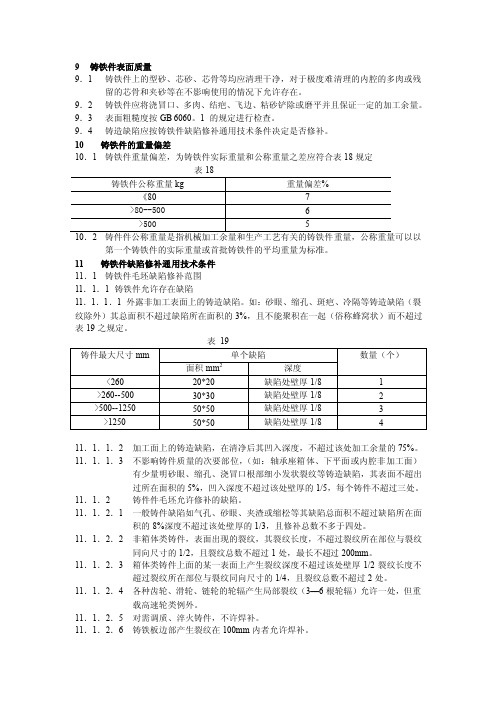
9铸铁件表面质量9.1铸铁件上的型砂、芯砂、芯骨等均应清理干净,对于极度难清理的内腔的多肉或残留的芯骨和夹砂等在不影响使用的情况下允许存在。
9.2铸铁件应将浇冒口、多肉、结疤、飞边、粘砂铲除或磨平并且保证一定的加工余量。
9.3表面粗糙度按GB 6060。
1 的规定进行检查。
9.4铸造缺陷应按铸铁件缺陷修补通用技术条件决定是否修补。
10铸铁件的重量偏差10.1铸铁件重量偏差,为铸铁件实际重量和公称重量之差应符合表18规定第一个铸铁件的实际重量或首批铸铁件的平均重量为标准。
11铸铁件缺陷修补通用技术条件11.1铸铁件毛坯缺陷修补范围11.1.1 铸铁件允许存在缺陷11.1.1.1 外露非加工表面上的铸造缺陷。
如:砂眼、缩孔、斑疤、冷隔等铸造缺陷(裂纹除外)其总面积不超过缺陷所在面积的3%,且不能聚积在一起(俗称蜂窝状)而不超过表19之规定。
表1911.1.1.2加工面上的铸造缺陷,在清净后其凹入深度,不超过该处加工余量的75%。
11.1.1.3不影响铸件质量的次要部位,(如:轴承座箱体、下平面或内腔非加工面)有少量明砂眼、缩孔、浇冒口根部细小发状裂纹等铸造缺陷,其表面不超出过所在面积的5%,凹入深度不超过该处壁厚的1/5,每个铸件不超过三处。
11.1.2铸件件毛坯允许修补的缺陷。
11.1.2.1一般铸件缺陷如气孔、砂眼、夹渣或缩松等其缺陷总面积不超过缺陷所在面积的8%深度不超过该处壁厚的1/3,且修补总数不多于四处。
11.1.2.2非箱体类铸件,表面出现的裂纹,其裂纹长度,不超过裂纹所在部位与裂纹同向尺寸的1/2,且裂纹总数不超过1处,最长不超过200mm。
11.1.2.3箱体类铸件上面的某一表面上产生裂纹深度不超过该处壁厚1/2裂纹长度不超过裂纹所在部位与裂纹同向尺寸的1/4,且裂纹总数不超过2处。
11.1.2.4各种齿轮、滑轮、链轮的轮辐产生局部裂纹(3—6根轮辐)允许一处,但重载高速轮类例外。
压铸件毛坯质量检验标准
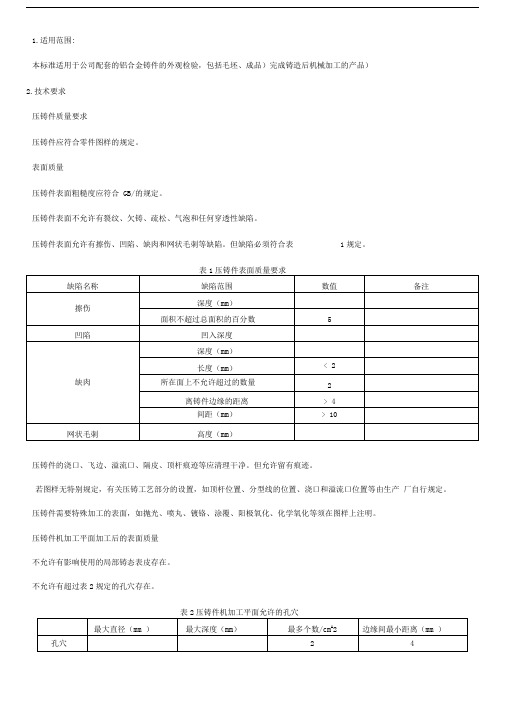
1.适用范围:本标准适用于公司配套的铝合金铸件的外观检验,包括毛坯、成品)完成铸造后机械加工的产品)2.技术要求压铸件质量要求压铸件应符合零件图样的规定。
表面质量压铸件表面粗糙度应符合 GB/的规定。
压铸件表面不允许有裂纹、欠铸、疏松、气泡和任何穿透性缺陷。
压铸件表面允许有擦伤、凹陷、缺肉和网状毛刺等缺陷。
但缺陷必须符合表1规定。
压铸件的浇口、飞边、溢流口、隔皮、顶杆痕迹等应清理干净。
但允许留有痕迹。
若图样无特别规定,有关压铸工艺部分的设置,如顶杆位置、分型线的位置、浇口和溢流口位置等由生产厂自行规定。
压铸件需要特殊加工的表面,如抛光、喷丸、镀铬、涂覆、阳极氧化、化学氧化等须在图样上注明。
压铸件机加工平面加工后的表面质量不允许有影响使用的局部铸态表皮存在。
不允许有超过表2规定的孔穴存在。
压铸件机械加工螺纹的表面质量压铸件机械加工螺纹的头两扣不允许有任何缺陷,其余部分螺纹不允许有表3所规定的孔穴缺陷压铸件若能满足其使用性能要求,则压铸件本质缺陷不作为报废的依据。
压铸件内部不允许有冷隔缺陷。
压铸件内部允许有气孔、疏孔、夹杂等缺陷,但孔穴缺陷最大直径不超过壁厚的1/8,孔穴数量在任何剖面上不超过2个/cm2。
重要压铸件的受力部位须进行解剖检查,符合表6中的规定。
3试验方法及检验规则化学成分铝合金化学成分的检验方法,检验规则和复检应符合GB/T15115的规定。
化学成分的试样也可取自压铸件, 但必须符合 GB/T15115的规定。
力学性能力学性能的检验方法,检验频率和检验规则应符合 GB/T15115 的规定。
采用压铸件本体为试样时,切取部位的尺寸、测试形式由供需双方商定。
压铸件几何尺寸的检验可按检验批量抽检或按GB2828 、GB2829 的规定进行,检验结果应符合本标准的规定。
压铸件表面质量的出厂检验应逐件检查,检验结果应符合本标准的规定。
压铸件表面粗糙度按 GB/的规定执行。
压铸件需抛光加工的表面按 GB/T 的规定执行。
铸造毛坯检验规定
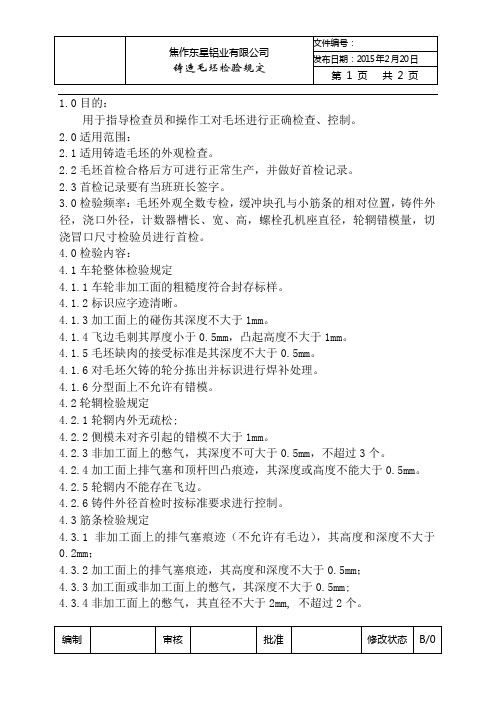
1.0目的:用于指导检查员和操作工对毛坯进行正确检查、控制。
2.0适用范围:2.1适用铸造毛坯的外观检查。
2.2毛坯首检合格后方可进行正常生产,并做好首检记录。
2.3首检记录要有当班班长签字。
3.0检验频率:毛坯外观全数专检,缓冲块孔与小筋条的相对位置,铸件外径,浇口外径,计数器槽长、宽、高,螺栓孔机座直径,轮辋错模量,切浇冒口尺寸检验员进行首检。
4.0检验内容:4.1车轮整体检验规定4.1.1车轮非加工面的粗糙度符合封存标样。
4.1.2标识应字迹清晰。
4.1.3加工面上的碰伤其深度不大于1mm。
4.1.4飞边毛刺其厚度小于0.5mm,凸起高度不大于1mm。
4.1.5毛坯缺肉的接受标准是其深度不大于0.5mm。
4.1.6对毛坯欠铸的轮分拣出并标识进行焊补处理。
4.1.6分型面上不允许有错模。
4.2轮辋检验规定4.2.1轮辋内外无疏松;4.2.2侧模未对齐引起的错模不大于1mm。
4.2.3非加工面上的憋气,其深度不可大于0.5mm,不超过3个。
4.2.4加工面上排气塞和顶杆凹凸痕迹,其深度或高度不能大于0.5mm。
4.2.5轮辋内不能存在飞边。
4.2.6铸件外径首检时按标准要求进行控制。
4.3筋条检验规定4.3.1非加工面上的排气塞痕迹(不允许有毛边),其高度和深度不大于0.2mm;4.3.2加工面上的排气塞痕迹,其高度和深度不大于0.5mm;4.3.3加工面或非加工面上的憋气,其深度不大于0.5mm;4.3.4非加工面上的憋气,其直径不大于2mm, 不超过2个。
4.3.5筋条上不能有疏松;4.3.6飞边、毛刺其厚度小于0.5mm,凸起高度不大于1mm。
4.3.7与轮辋交接处不允许有裂纹、缩松。
4.3.8筋条非加工面不允许有涂料脱落、凹凸不平等缺陷。
4.4轮鼓部位检验规定4.4.1轮鼓内各交接处无裂纹;4.4.2排气塞痕迹其深度不大于0.5mm,高度不大于0.3mm。
4.4.3轮鼓内的顶杆痕迹其高度和深度不大于1mm。
铸件表面质量验收标准

铸铁件验收项目及标准铸件的表面质量主要包括铸件的表面缺陷、尺寸精度、形状偏差、表面粗糙度、表面清理质量等;1、铸件表面缺陷的检验1.1表面缺陷检验的一般要求1.1.1铸件非加工表面上的浇冒口必须清理得与铸件表面同样平整,加工面上的浇冒口残留量应符合技术要求,若无要求,则按表8执行;1.1.2在铸件上不允许有裂纹、通孔、穿透性的冷隔和穿透性的缩松、夹渣等机械加工不能去除的缺陷;1.1.3铸件非加工表面的毛刺、披缝、型砂、砂芯等应清理干净;1.1.4铸件一般待加工表面,允许有不超过加工余量范围内的任何缺陷存在;重要加工面允许有不超过加工余量2/3的缺陷存在,但裂纹缺陷应予清除;加工后的表面允许存在直径*长度*深度小于等于2*2*2的非连片孔洞的铸造缺陷;1.1.5作为加工基准面(孔)和测量基准的铸件表面,平整度小于等于2.0 毫米、粗糙度Ra50以内;1.1.6铸件表面气孔、砂眼、夹渣面积不大,但比较分散或者有连片麻点的表面不予接收;1.1.7除技术要求特别注明的铸件外,对于表面有气孔、缩孔、砂眼等缺陷的铸钢件允许补焊,但铸铁件未经允许不得焊补(铸铁件实行一案一判的原则)但补焊面积不允许超过铸件面积的10%,焊接质量应符合JB/T 5000.7-2007标准要求,补焊后必须退火、机械性能达到图纸要求,且不得有渗漏及影响外观的缺陷;1.2铸件外观质量等级表1 铸件外观质量等级1、一般零部件采用B级精度,在检查过程中,如有一个或多个项目超出B级精度要求的零部件均判定为不合格;2、影响到零部件安全、性能的部位,外观质量采用A级精度,如果有一个或多个项目超出规定级精度要求的零部件均判定为不合格;2、铸件尺寸的检验2.1铸件毛坯尺寸公差铸件尺寸公差应按毛坯图或技术条件规定的尺寸公差等级执行,当技术文件未规定尺寸公差时,则应以GB6414-1999为依据,并按照表2选定公差值(粗线框内为推荐使用公差等级);表2铸件尺寸公差(单位:mm)2.2铸件分型面处最大错型值应不得超过表2所示公差值,当需进一步限制错型量时,应从表3中选取;表 3 错型值(GB6414-1999)2.3铸件加工余量应符合表4的规定,有特殊要求的表面应在技术要求中单独标注加工余量;表4加工余量(单位:mm)3、表面粗糙度检测表面粗糙度总体检测原则依据图纸要求,当图纸无要求是执行国标GB/T15056-1994;3.1一般情况下,表面粗糙度要求Ra50,铸件难以清理的部位,局部允许 Ra100,待加工表面允许降低1级;3.2.使用面积法作为验收依据面积法常用的比较样块评定铸件表面粗糙度;方法如下:3.2.1铸造表面粗糙度比较样块应符合GB6060.1-1997标准;3.2.2按照国标BWZ001-88评定铸件表面粗糙度的等级;3.2.3铸件的浇道、冒口、修补的残余表面及铸造表面缺陷(如粘砂、结疤等)不列为被检表面;3.2.4以铸造表面粗糙度比较样块为对照标准,对被检铸件的铸造表面用视觉或触觉的方法进行对比;3.2.5用样块对比时,应选用适于铸造合金材料和工艺方法的样块进行对比;3.2.6被检的铸造表面必须清理干净,样块表面和被检表面均不得有锈蚀处;3.2.7用样块对比时,砂型铸造表面被检点数应符合表7的规定;特种铸造表面被检点数应按表8的规定加倍;被检点应平均分布,每点的被检面积不得小于与之对比面的面积;表7 被检铸造表面最低检测数3.2.8当被检铸造表面的粗糙度介于比较样块两级参数值之间者,所确定的被检铸造表面的粗糙度等级为粗的一级;3.2.9对被检铸造表面,以其80%的表面所达到的最粗表面粗糙度等级,为该铸造表面粗糙度等级;3.3铸件表面清理检测3.3.1铸件几何形状必须完整,非加工面上的清理损伤不应大于该处的尺寸偏差,加工面上的损伤不应大于该处加工余量的1/2;3.3.2允许铸件表面有少量的局部低凹或打磨痕迹,在直径不大于8mm,并能保证铸件规定的最小的壁厚;3.3.3为去除铸造缺陷而打磨后的铸件表面粗糙度应与一般铸件表面粗糙度基本一致;3.3.4除特殊情况外,铸件表面允许残留的浇冒口、毛刺,多肉残余量应按表 8的要求进行;表8 浇冒口、毛刺、多肉等允许残留量值3.3.5铸件表面须经过防锈处理,保证在铸件进入面加工时不得有任何的锈蚀;3.3.6铸件表面如有油漆要求的,必须按有关涂装规定执行;4、铸件重量检测对于没有特殊要求的铸件,重量偏差可以不作为验收依据;如果技术条件有要求,供需双方协商后,铸件的重量偏差也应作为验收依据,一般应符合表6的规定;表6铸件重量偏差。
DKBA04000109[B]华为-铸件质量要求
![DKBA04000109[B]华为-铸件质量要求](https://img.taocdn.com/s3/m/bc48891114791711cc791764.png)
DKBA 华为技术有限公司内部技术规范DKBA0.400.0109 REV. B代替DKBA0.400.0109 REV.1.0铸件质量要求Specification for Casting Part’s Quality2009年6月20日发布 2009年6月30日实施华为技术有限公司Huawei Technologies Co., Ltd.版权所有侵权必究All rights reserved修订声明Revision declaration本规范拟制与解释部门:整机工程部本规范的相关系列规范或文件:无相关国际规范或文件一致性:无替代或作废的其它规范或文件:压铸件技术规范相关规范或文件的相互关系:无规范号主要起草部门专家主要评审部门专家修订情况DKBA0.400.0109 REV B 整机工程部:许志敏(00114402)、孟耐尔(00120639)整机工程部:周伟(00123276)、黄文源(00123114)、郑玲(00119690)、韦娟(37461)、肖春秀(53994)、魏华(00102167)、孟耐尔(00120639)、刘长林(00129646)、邓顺庆(61647)、鲍祥英(54845)、孙伟华(60798)TQC:吴貌貌(00113989)MQE:陈亮(68994)由于规范中增加了对金属型铸件的要求,将规范名称改为铸件质量要求;删除压铸件的表面分级,增加铸件的分类;铸件缺陷定义增加图片说明;删除公司未用到合金牌号;优化铸件表面质量、内部质量要求;增加检验项目;增加对回炉料的控制;增加铸件标识要求;将附录中内容移到正文中。
DKBA0.400.0109 REV1.0 结构造型设计部:欧阳华(60010597)、孟耐尔(外聘专家)结构造型设计部:盛辉(21628)、周伟(16271)、邓在明(10166)、佘旭凡(16523)删减了压铸件设计的内容;增加了压铸件的分类、分级及对质量的详细要求。
QT450-10铸造毛坯件检验规范

1、目的为了规范公司对铸造件质量的检验。
2、适用范围适用于公司内所有球墨铸铁材质的产品。
3、引用标准GB /T5612-2008 铸铁牌号表示法GB/T1348-1988 球墨铸铁件GB 231-84 金属布氏硬度试验法GB/T9441-2009 球墨铸铁金相检验GB/T6414-1999 铸件尺寸公差与机械加工余量GB 6060.1-85 表面粗糙度比较样块铸造表面4、验收标准4.1 铸件材质检验标准:4.1.1 球墨铸件材质验收标准应符合GB1348-1988 球墨铸铁的标准,以机械性能(抗拉强度、延伸率)、金相组织为验收依据,硬度及化学成分做为参考。
4.1.1.3 壳体毛坯件的球墨铸铁材质正火后其珠光体(正火索氏体)组织等级在3级以上。
4.1.2 材质检验取样规范4.1.2.1机械性能检查:机械性能测试的试块,每班次每种牌号至少浇注三根,若铸件进行热处理,必须连同试块一同进行热处理。
二根用于生产厂测试性能(第一根合格则该批次合格,余下试块(留有生产日期、包次标识)留存。
若第一根试块不合格,测试剩余二根,若第二根不合格则该批次产品全部报废,若第二根合格,应加试第三根,合格则判定该炉产品合格,若第三根不合格则该批次产品全部报废)。
材质检验报告(原档)保存期为5年。
4.1.2.2金相组织检查:球铁铸件从每包铁水的最后一型附铸金相试块或铸件本体进行金相检验,依次往前直到合格(或本包铁水所浇铸件检验完)为止。
附铸试块应能代表本体。
若试块不好,应对铸件本体破件进行检验。
若金相检验由问题,加倍抽查。
金相本体试块应按天分类以月为单位保存,保存期为6个月,检验报告保存期5年。
球化等级要求在3级以上,石墨大小要求为5~7级。
4.1.2.3化学成分检查:每天必须分析每炉铁水(炉前)及至少两炉铸件(炉后)的化学成分。
炉前主要化验C、Si和S,炉后所有元素全部化验。
每天第一炉溶清后必须检测C、Si、Mn、P和S,之后C、Si每炉化验检测。
铝合金压铸件毛坯检验规范
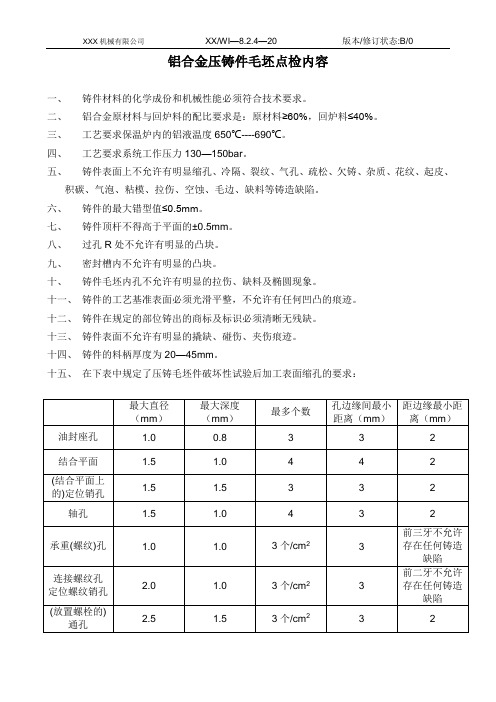
XXX机械有限公司XX/WI—8.2.4—20 版本/修订状态:B/0
铝合金压铸件毛坯点检内容
一、铸件材料的化学成份和机械性能必须符合技术要求。
二、铝合金原材料与回炉料的配比要求是:原材料≥60%,回炉料≤40%。
三、工艺要求保温炉内的铝液温度650℃----690℃。
四、工艺要求系统工作压力130—150bar。
五、铸件表面上不允许有明显缩孔、冷隔、裂纹、气孔、疏松、欠铸、杂质、花纹、起皮、
积碳、气泡、粘模、拉伤、空蚀、毛边、缺料等铸造缺陷。
六、铸件的最大错型值≤0.5mm。
七、铸件顶杆不得高于平面的±0.5mm。
八、过孔R处不允许有明显的凸块。
九、密封槽内不允许有明显的凸块。
十、铸件毛坯内孔不允许有明显的拉伤、缺料及椭圆现象。
十一、铸件的工艺基准表面必须光滑平整,不允许有任何凹凸的痕迹。
十二、铸件在规定的部位铸出的商标及标识必须清晰无残缺。
十三、铸件表面不允许有明显的撬缺、碰伤、夹伤痕迹。
十四、铸件的料柄厚度为20—45mm。
十五、在下表中规定了压铸毛坯件破坏性试验后加工表面缩孔的要求:。
- 1、下载文档前请自行甄别文档内容的完整性,平台不提供额外的编辑、内容补充、找答案等附加服务。
- 2、"仅部分预览"的文档,不可在线预览部分如存在完整性等问题,可反馈申请退款(可完整预览的文档不适用该条件!)。
- 3、如文档侵犯您的权益,请联系客服反馈,我们会尽快为您处理(人工客服工作时间:9:00-18:30)。
铸件毛坯的质量要求
目的:明确外协厂商铸造配件的来料质量要求,以保证产品加工过程中的正常加工。
范围:使用于所有本公司铸件加工产品的来料,使外协厂商确保铸件产品完好地供应到仓库。
要求
1.精度尺寸与材质请参照技术图纸的要求。
2.铸件毛坯不得有砂眼、气孔、缩松、夹砂、结疤、粘砂、裂纹
等铸造缺陷。
3.铸件毛坯要进行退火处理,以消除内应力,要经过530-560度
的炉冷处理。
4.提高铸件的外观质量和尺寸精度减少加工余量。
诚锋机械制造有限公司
质检部
2010-11-06。