首末件管理办法
首末件管理规定

首末件管理规定1、编写目的为加强产品质量控制,预防产品在生产过程中出现批次质量事故,保证产品实物质量,促进产品顺利交付,特制定本管理办法。
2、使用范围本办法适用于公司所有生产工序首末件的确定及管理。
3、术语定义3.1首件:每个班次刚开始时或过程中条件发生改变,而后加工正常的第一或前几件产品,由生产人员确认后提交检验室做首件检验。
“首件”一般指正常批量生产前,经一定检验标准确认合格且适合用于评判生产产品品质的样品。
3.2末件:是指当批或当班生产的最后一个(组)产品。
3.3控制要求:3.3.1有下列情况之一的,需进行首件检验(首件首检触发条件):--重新开机时--换模、换料后--加工工艺重新调整后--工装、模具维修后--质量标准修订后--生产场地变更后3.3.2有下列情况之一的,需进行末件检验(末件检验触发条件):--该批次生产结束前--停机停产前4、职责划分4.1制造部的产品负责人需及时提交首末件到检验室进行首检、末检。
4.2质量异常时,制造部需组织人员对问题点进行分析、调整、改善。
4.3质量部检验室负责首末件的确认及过程检验。
4.4质量部检验室对不合格的首末件,要配合制造部进行分析,并有权提出停机要求改善。
5、作业程序5.1根据本办法第3.3.1条款,由制造部产品负责人提交首件产品到质量部检验室进行首件检验。
5.2检验结果不符合标准要求的,质量部检验室通报制造部重新调试;检验结果符合标准要求的,检验负责人应将检验后的产品按规定标识后,存档质量部,以供追溯模具状况所需。
5.2.1首件标识内容包含:产品图号、名称、送检日期、检验人员签名或签章。
5.2.2首件确认合格后,制造部方可开始生产。
5.3根据本办法第3.3.2条款,需要制作末件时,由制造部产品负责人提交首件产品到质量部检验室进行首件检验。
5.4末件检验合格,标识后转制造部进行保管并记录,以供追溯模具状况所需。
5.5末件标识内容包含:产品图号、名称、送检日期、检验人员签名或签章。
首末检管理规定
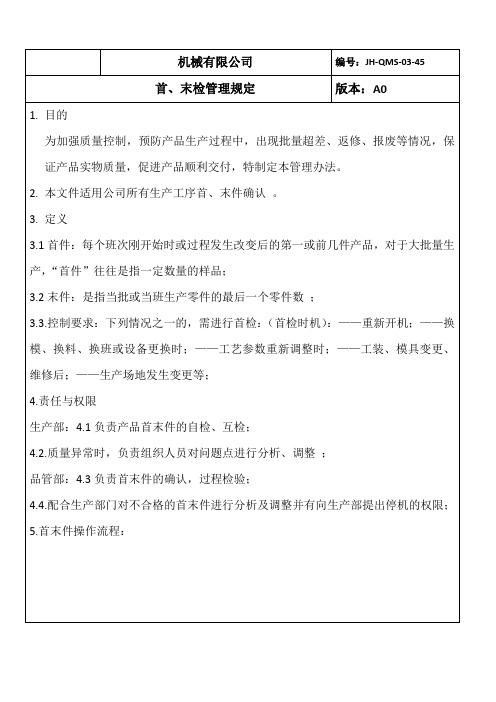
4.2.质量异常时,负责组织人员对问题点进行分析、调整 ;
品管部:4.3 负责首末件的确认,过程检验;
4.4.配合生产部门对不合格的首末件进行分析及调整并有向生产部提出停机的权限;
5.首末件操作流程:
流程图 产前准备
首件生产
NG
自检
OK NG
组长确认
机械有限公司
编号:JH-QMS-03-45
首件流程图
生产部
操作工对首件生产的产品进行检验,确认符 合技术要求和工序要求,填写《自检记录表》 并签名(尺寸需填写具体测量数值)
生产部
《自检记录表》
班组长确认操作工每个首件都有做检验,并 对操作工的首件检验结果做确认签字
生产部
《自检记录表》
OK OK
QC 确认
QC 对生产的《自检记录表》做确认,确认 车间有正常进行首件自检工作,并核对检验 结果后在《自检记录表》签字
版本:A0
说明
责任部门
相关记录
班、组长对操和工进行必须的岗前培训,准 备好生产所需的技术文件和工装治具,并确 认文件和治具正确性和适用后,派发给操作 工,作业前对人、机、料、法、环进行确认
生产部
《作业准备验证记录表》
经培训合格的员工允许上岗,并按照技术资 料和步骤,第个独立的作业单位首先生产第 一件产品
产,“首件”往往是指一定数量的样品;
3.2 末件:是指当批或当班生产零件的最后一个零件数 ;
3.3.控制要求:下列情况之一的,需进行首检:(首检时机):——重新开机;——换
模、换料、换班或设备更换时;——工艺参数重新调整时;——工装、模具变更、
维修后;——生产场地发生变更等;
4.责任与权限
生产部:4.1 负责产品首末件的自检、互检;
首末件管理办法

1 目的为了更好的控制产品的质量,预防产品在生产过程中的批量不良,在下次生产前处理好本次过程中的问题,确保使后续生产顺利进行,以达到降低成本、提高效率。
特制定本管理规定。
2 范围适用于本公司注塑车间首末件管理3 术语和定义首件:每次换模开始时或过程中条件发生变化时(包括:换机、换料、换色、修模、停机后、工艺发生变化较大时),由生产领班确认合格的产品后第15模报质检员做首件检验。
“首件”一般指正常批量生产前,依照检验标准确认合格的样品。
末件:是指当批次生产的最后一只产品制作的合格样品。
报废:为避免不合格品原有预期用途误用而对其所采取的措施。
废弃模:开机生产初期尺寸、外观不稳定的产品确认为不良品报废处理。
4 职责4.1 生产部负责首件自检,通报质检员做首末件,在质量异常时,负责组织人员对问题点进行分析和调整、改善。
4.2产生部门/车间负责组织对产品的评审工作及对生产现场产品的标识、隔离,并按评审结果进行处理及让步接受的申请。
4.3品质部负责对首末件的确认及过程检验,确保首末件产品的外观、尺寸、结构、性能等各方面满足客户的要求。
配合生产部门对改善品的检查,必要时组织相关部门参加评审。
4.4当出现批量不合格时,检验员有权要求停止生产;当外协辅料影响生产时检验员有权要求异常辅料隔离退换,有权要求对生产的产品进行追溯隔离,产品检查合格后方可放行。
4.5品质部负责首件产品品质记录的制作及保存,首件样品最长保存期限为三个月,末件产品最长保存期限为六个月4.6技术部负责返工返修指导书的编制;负责异常产品对顾客影响程度的评审。
5首末件检查时机5.1 每日每班到岗上班,某机台开始生产时,某机台转换产品颜色或材料时,某工序变更生产工艺后,生产异常改善后再生产时,模具生产机台及周边设备异常修复后,其它特殊情况导致生产机台不能正常生产停止生产后再继续生产时,应执行首件检查5.2 每批次生产的最后1个零件执行末件检查,末件随模具流转或者放置在固定的机台位置6首件检验6.1 IPQC接到生产部的首件样品后,依据《检验作业指导书》、“OK样品”、“限度样件”及外观标准、规格尺寸、性能需求及其它特殊要求对产品外观、尺寸、结构、性能等方面进行综合判定并做好相关记录。
产品首末件管理制度

产品首末件管理制度一、背景介绍在产品生产的过程中,首末件管理是一个非常重要的环节。
首末件是指每一批产品的第一件和最后一件,对于产品质量的控制和生产效率的提高起着关键作用。
因此,建立科学的首末件管理制度对于企业来说至关重要。
二、首末件管理的意义首末件管理是产品生产过程中的一个重要环节,其意义主要有以下几个方面:1.保证产品质量首件是产品生产过程中的第一件产品,其质量直接影响到后续产品的质量。
通过对首件进行严格的检测和控制,可以及时发现问题并及时进行调整,从而确保产品质量的稳定。
2.提高生产效率通过对末件进行检测和评估,可以及时发现生产过程中存在的问题和瓶颈,从而及时采取措施解决,提高生产效率。
3.降低生产成本通过对首末件进行管理,可以及时发现生产过程中存在的问题,避免不合格品的生产,降低二次加工成本,提高生产效率。
4.改善生产环境通过对首末件进行管理,可以及时发现生产环境中存在的问题,及时进行整改,改善生产环境,提高工作效率。
三、建立首末件管理制度的必要性建立首末件管理制度对于企业来说是非常必要的,其主要原因有以下几点:1.规范生产流程通过建立首末件管理制度,可以规范生产流程,建立起严谨的产品生产管理体系,提高生产效率。
2.提高产品质量通过对首末件进行严格管理,可以及时发现存在的问题并及时解决,从而提高产品质量。
3.降低生产成本通过对首末件进行管理,可以降低不合格品的生产,减少二次加工成本,提高生产效率。
4.改善生产环境通过对首末件进行管理,可以及时发现生产环境中存在的问题,及时进行整改,改善生产环境,提高工作效率。
四、建立首末件管理制度的具体措施为了建立一个科学、规范的首末件管理制度,需要采取以下具体措施:1.明确首末件的定义和标准首末件管理的第一步是明确首末件的定义和标准,确定首末件的检测方法和要求,从而为后续的管理和控制奠定基础。
2.建立责任制建立明确的首末件管理责任制,明确各个环节的责任人和责任范围,确保每个环节都能够按照规定的要求进行操作。
首末件管理规定

首末件管理规定
1.目的
为防止正常生产时产生批量不合格,确保生产过程得到有效控制以及对产品标准中不能用文字表达或虽用文字表达,还不确切而又必须用实样来说明规定要求。
2.适用范围
适用于公司所有经客户认可、已批量供货的产品(包括半成品)。
3.职责
质量部归口管理。
4.名词解释
4.1首件:是换摸后调试后符合检验规范的第一个产品,此调试过程中产生的报废件不超过10个;
4.2末件:产品批次注塑结束前,正常生产状态时的产品。
5.程序
5.1在下列情况下需进行首件确认
5.1.1每批连续生产前;
5.1.2工艺更改后;
5.1.3原材料(油漆)更改后;
5.1.4生产流程更改后;
5.1.5设备或工装维修后;
5.1.6采用新的工装;
5.1.7其它能较大影响产品质量的情况。
5.2每班生产开始/批量生产开始由操作工检验,过程检验员参照生产样件和过程检验规范
对首件检验确认,并签字,做好首件产品检验记录。
5.3首件检验如出现不合格,生产部门应查明原因,采取纠正措施,然后重新进行首件确认,直到首件合格后才可批量生产。
5.4每班生产结束/批量生产结束前或批量生产意外中断,应做末件产品检验记录,具体操
作同首件检验;若末件产品合格,合格首件不加特别标识流入批量中。
5.5每班生产开始/批量生产开始或批量生产意外中断的再生产,若首件产品合格,合格末
件不加特别标识流入批量中。
5.6不合格末件由制造部保存,直到合格首件产生后进行其它处理。
6.相关文件
产品标识和可追溯规定
7.使用表单。
首(末)检管理制度 - 副本
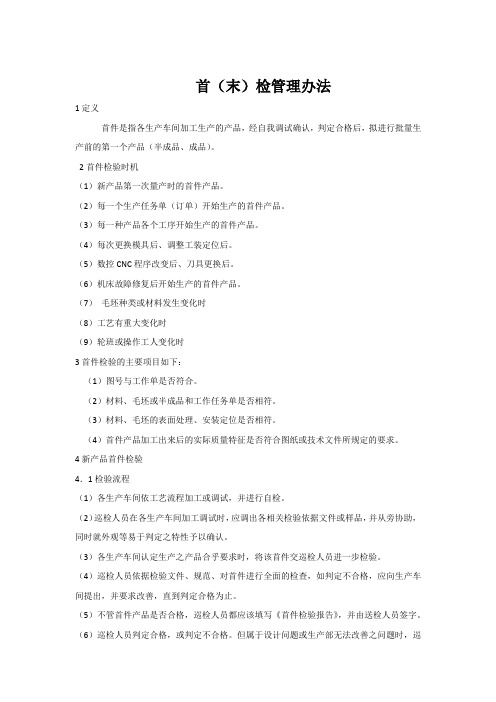
首(末)检管理办法1定义首件是指各生产车间加工生产的产品,经自我调试确认,判定合格后,拟进行批量生产前的第一个产品(半成品、成品)。
2首件检验时机(1)新产品第一次量产时的首件产品。
(2)每一个生产任务单(订单)开始生产的首件产品。
(3)每一种产品各个工序开始生产的首件产品。
(4)每次更换模具后、调整工装定位后。
(5)数控CNC程序改变后、刀具更换后。
(6)机床故障修复后开始生产的首件产品。
(7)毛坯种类或材料发生变化时(8)工艺有重大变化时(9)轮班或操作工人变化时3首件检验的主要项目如下:(1)图号与工作单是否符合。
(2)材料、毛坯或半成品和工作任务单是否相符。
(3)材料、毛坯的表面处理、安装定位是否相符。
(4)首件产品加工出来后的实际质量特征是否符合图纸或技术文件所规定的要求。
4新产品首件检验4.1检验流程(1)各生产车间依工艺流程加工或调试,并进行自检。
(2)巡检人员在各生产车间加工调试时,应调出各相关检验依据文件或样品,并从旁协助,同时就外观等易于判定之特性予以确认。
(3)各生产车间认定生产之产品合乎要求时,将该首件交巡检人员进一步检验。
(4)巡检人员依据检验文件、规范、对首件进行全面的检查,如判定不合格,应向生产车间提出,并要求改善,直到判定合格为止。
(5)不管首件产品是否合格,巡检人员都应该填写《首件检验报告》,并由送检人员签字。
(6)巡检人员判定合格,或判定不合格。
但属于设计问题或生产部无法改善之问题时,巡检人员填写《首件检验报告》,呈质检部主管审核。
(7)经品质部主管审核之《首件检验报告》及首件产品后,由巡检人员直接送往技术部,交具体负责该产品之技术人员作检验。
(8)技术部技术人员经检验后,做出合格或不合格的判定,并填入《首件检验报告》中。
(9)技术部、品质部均判定合格后,《首件检验报告》由质检部保留,巡检员在《生产流程卡》“首检一栏”签字确认,并通知生产车间可以正式量产。
(10)技术部、品质部判定不合格时,如属生产原因时,应由生产部/车间改善、调试直到合格为止;如属于设计原因时,应停止生产,由技术部负责拟出对策加以改善后,方可恢复生产,并需重新作首件确认。
首尾件样品管理规定

首、尾件样品管理规定一、目的为了加强和规范公司对首/尾件样品的保管和品质的管理,使样品保持其有效性、统一性,样品因其对日后再生产的数据具有参考性和重要性,特制定此规定。
二、适用范围适用于本公司品管科、生产科和工程科等对样品的存档和领用。
三、职责1、品管科负责样品的收集、管理分类工作;2、生产科负责保证所需存档样品的真实、准确及完整性;3、工程科负责对领用样品的维护工作(指首、尾件样品),并及时归还;四、样品的保存公司的实物样品存放于公司样品室,由品管科统一采集、管理和处置。
五、样品的采集时机在公司模具首次试产成功时、修模、设计变更时、产品材质变更时、大批量生产产品之首、尾件产品;由成型科对符合公司各项外观判定标准和相关行业标准的两整模新产品送样至品管处,品管科按照正常的检验流程对产品进行检测并将一整模样品采集。
采集后的样品实物存放于样品室(尾数仓库)内,样品上依次注明产品的品名(型号)、产品的生产指令单号、订单数量、生产日期、班别、原材料规格、原材料批号等。
将产品的相应尺寸数据信息存于品管电脑产品尺寸检测表内。
六、样品的保存期限1)样品的分类实物存档一般BOBBIN规格依CORE规而定,例:EE.EI.EF.EFD.ETD.ER.EER.EEL.EPC.ERL.RM.UU.ET.ETD.PQ.POT.UI.BASE……等等.按形状:一般分为七大类,轮轴.卧式.立式.抽屉式.SMD.BASE.CASE.按照材质、制作工艺又可分为热固性、热塑性两大类型。
样品采集时机新模首次试产修模、设变产品材质变更首检检查尾件检查样品保存期限长期保存设变产品长期保存客户量产合格,下批量产前下批订单量产前下批订单生产前或模具维修经判定OK后备注/将设变前产品清理干净/ / /品管科在接到修模通知单后,根据要求及时准备所需样品,须经质检部负责人审核后方可提供样品。
注:如模具在生产过程中出现异常需完单后修模的由成型科直接提供样品交给工程科、品管科。
多模腔首末件管理制度
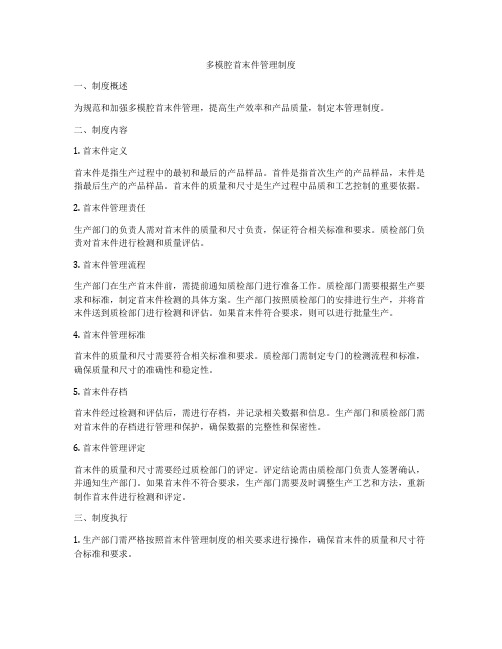
多模腔首末件管理制度一、制度概述为规范和加强多模腔首末件管理,提高生产效率和产品质量,制定本管理制度。
二、制度内容1. 首末件定义首末件是指生产过程中的最初和最后的产品样品。
首件是指首次生产的产品样品,末件是指最后生产的产品样品。
首末件的质量和尺寸是生产过程中品质和工艺控制的重要依据。
2. 首末件管理责任生产部门的负责人需对首末件的质量和尺寸负责,保证符合相关标准和要求。
质检部门负责对首末件进行检测和质量评估。
3. 首末件管理流程生产部门在生产首末件前,需提前通知质检部门进行准备工作。
质检部门需要根据生产要求和标准,制定首末件检测的具体方案。
生产部门按照质检部门的安排进行生产,并将首末件送到质检部门进行检测和评估。
如果首末件符合要求,则可以进行批量生产。
4. 首末件管理标准首末件的质量和尺寸需要符合相关标准和要求。
质检部门需制定专门的检测流程和标准,确保质量和尺寸的准确性和稳定性。
5. 首末件存档首末件经过检测和评估后,需进行存档,并记录相关数据和信息。
生产部门和质检部门需对首末件的存档进行管理和保护,确保数据的完整性和保密性。
6. 首末件管理评定首末件的质量和尺寸需要经过质检部门的评定。
评定结论需由质检部门负责人签署确认,并通知生产部门。
如果首末件不符合要求,生产部门需要及时调整生产工艺和方法,重新制作首末件进行检测和评定。
三、制度执行1. 生产部门需严格按照首末件管理制度的相关要求进行操作,确保首末件的质量和尺寸符合标准和要求。
2. 质检部门需严格按照首末件管理制度的相关要求进行检测和评定,确保数据的准确性和可靠性。
3. 生产部门和质检部门需密切合作,共同制定和执行首末件管理的具体流程和方案,确保首末件管理的有效性和高效性。
4. 首末件管理制度的执行情况需定期进行检查和评估,发现问题及时进行整改,并完善相关管理制度和流程。
四、制度改进根据首末件管理的实际情况和发展需求,需要不断进行制度的改进和完善,确保首末件管理制度符合当前行业标准和规范,提高管理的科学性和有效性。
首末件管理制度
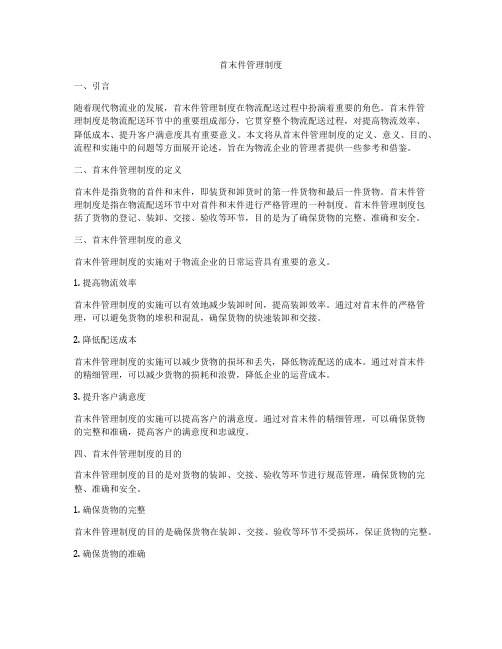
首末件管理制度一、引言随着现代物流业的发展,首末件管理制度在物流配送过程中扮演着重要的角色。
首末件管理制度是物流配送环节中的重要组成部分,它贯穿整个物流配送过程,对提高物流效率、降低成本、提升客户满意度具有重要意义。
本文将从首末件管理制度的定义、意义、目的、流程和实施中的问题等方面展开论述,旨在为物流企业的管理者提供一些参考和借鉴。
二、首末件管理制度的定义首末件是指货物的首件和末件,即装货和卸货时的第一件货物和最后一件货物。
首末件管理制度是指在物流配送环节中对首件和末件进行严格管理的一种制度。
首末件管理制度包括了货物的登记、装卸、交接、验收等环节,目的是为了确保货物的完整、准确和安全。
三、首末件管理制度的意义首末件管理制度的实施对于物流企业的日常运营具有重要的意义。
1. 提高物流效率首末件管理制度的实施可以有效地减少装卸时间,提高装卸效率。
通过对首末件的严格管理,可以避免货物的堆积和混乱,确保货物的快速装卸和交接。
2. 降低配送成本首末件管理制度的实施可以减少货物的损坏和丢失,降低物流配送的成本。
通过对首末件的精细管理,可以减少货物的损耗和浪费,降低企业的运营成本。
3. 提升客户满意度首末件管理制度的实施可以提高客户的满意度。
通过对首末件的精细管理,可以确保货物的完整和准确,提高客户的满意度和忠诚度。
四、首末件管理制度的目的首末件管理制度的目的是对货物的装卸、交接、验收等环节进行规范管理,确保货物的完整、准确和安全。
1. 确保货物的完整首末件管理制度的目的是确保货物在装卸、交接、验收等环节不受损坏,保证货物的完整。
2. 确保货物的准确首末件管理制度的目的是确保货物在装卸、交接、验收等环节不发生错装、错运等错误,保证货物的准确。
3. 确保货物的安全首末件管理制度的目的是确保货物在装卸、交接、验收等环节不发生丢失、盗窃等情况,保证货物的安全。
五、首末件管理制度的流程首末件管理制度的流程包括了货物的登记、装卸、交接、验收等环节。
首末件管理规定
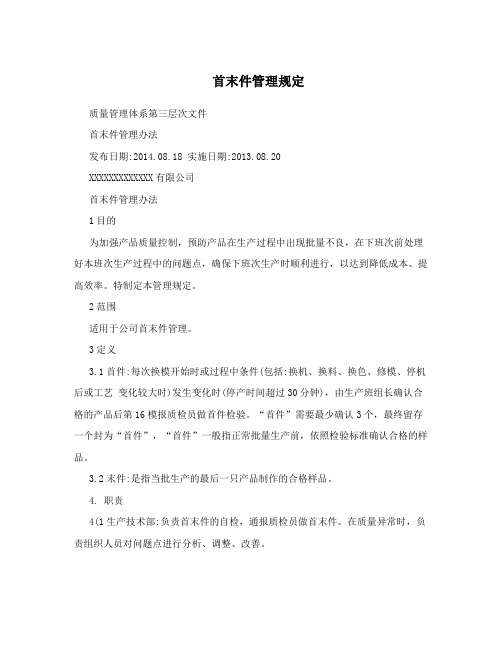
首末件管理规定质量管理体系第三层次文件首末件管理办法发布日期:2014.08.18 实施日期:2013.08.20XXXXXXXXXXXXX有限公司首末件管理办法1目的为加强产品质量控制,预防产品在生产过程中出现批量不良,在下班次前处理好本班次生产过程中的问题点,确保下班次生产时顺利进行,以达到降低成本、提高效率。
特制定本管理规定。
2范围适用于公司首末件管理。
3定义3.1首件:每次换模开始时或过程中条件(包括:换机、换料、换色、修模、停机后或工艺变化较大时)发生变化时(停产时间超过30分钟),由生产班组长确认合格的产品后第16模报质检员做首件检验。
“首件”需要最少确认3个,最终留存一个封为“首件”,“首件”一般指正常批量生产前,依照检验标准确认合格的样品。
3.2末件:是指当批生产的最后一只产品制作的合格样品。
4. 职责4(1生产技术部:负责首末件的自检,通报质检员做首末件。
在质量异常时,负责组织人员对问题点进行分析、调整、改善。
4(2质量保证部:负责首末件的确认及过程检验。
配合生产技术部门对不合格的首末件进行分析,并有权提出停机要求及改善要求。
5. 控制流程开机生产NG追溯首件检验OK末件留样首批OK 件量留生NG 样产检验生产结束6. 流程说明6(1生产开始时根据本规定的第3.1条款,需要制作首件时,由生产技术部班组长提供产品通报当班质检员进行首件检验。
6.1.1当班质检员接到生产技术部班长通知后,根据《生产计划单》和《检验指导书》对该机台的产品进行检验判定。
6.1.2质检员需在10分内做出外观判定,20分钟内做出最终判定,判定中包含原材料确认。
6.1.3若检验结果符合要求的要及时做好首件样品(样品包括:日期、时间、质检员签名)和加工样品并挂于相应的机台上,检验结果不符合标准要求的,质检员需立即通报生产班组长重新调试,重新报检。
6.2首件再确认:当首件确认合格后生产了1.6-2小时时,质检员要对生产中的产品进行一次再确认。
冲压首末件管理规定

冲压首末件管理规定第一篇:冲压首末件管理规定冲压首末件管理规定目的加强质量控制,预防产品生产过程中出现批量不良,确保制件质量状态可追溯。
2 适用范围冲压车间生产班组首末件管理。
3 引用标准《SJ/T 10726-1996 冲压件一般检验原则》 4 术语:⌝首件:在冲压生产活动中,在以下情况下生产的第一个或几个冲压零件。
1)变换产品;2)变换材料;3)修、换模后;4)设备调整后;5)操作者接班后。
⌝末件:在冲压生产活动中,在以下情况下生产的最后一个或几个冲压零件。
1)变换产品;2)变换材料;3)修、换模后;4)设备调整后;5)操作者接班后。
⌝首件检查:对首件进行的检查的活动。
⌝末件检查:对末件进行的检查的活动。
5 职责:在线抽检工位:1)负责产品首末件抽取、检查及存放;2)质量异常时,问题上报当班班长;生产班长:1)负责当班首末件的确认;2)质量异常时组织模修、返修、工艺、质量等人员对问题进行分析、整改;3)有权提出停机、改善要求。
6规定:6.1制作留存规定:冲压首末件管理规定⌝当批生产的首件及末件进行检查后留存;⌝顶盖生产涉及到品种转换时,分别制作并留存有天窗及无天窗产品首末件;⌝当批生产未完成,出现临时换模生产或设备维修等情况时,继续生产后产生的首末件替换当批之前件;⌝操作者接班后,设备重新启动生产的首件替换当批之前件;⌝当批生产过程中若包含实验料,分别制作各材料首末件;⌝当批生产需要多垛板料,每垛料分别制作首末件。
6.2存放规定:⌝当批首末件:装入首末件工位器具,替换上批次的首末件。
⌝上批次首末件:装入当批生产成品件工位器具中。
⌝试验料首末件:装入试验料成品件工位器具中。
⌝料剁更换产生的首末件:如无其他情况,第一垛板料的首件及最后一垛板料的末件作为当批生产首末件。
生产过程中产生的其它首末件按抽检件存放到相应工位器具中。
6.3签字要求:⌝签字位置:在制件的里侧面醒目位置。
⌝签字内容:包括生产日期、操作者、班长签名等内容,并且标注○首或○末。
首末件及制程检验管理办法

1.目的让生产制造过程在受控状态下进行;提早发现不良品,避免不良品产生,并且杜绝不良品流出。
2.适用范围公司内所有制程,包括压铸,后加工,精加工,包装及返工返修。
3.职责品管部巡检负责首末件检验确认和过程巡检确认。
车间员工负责首末件自检和过程自检品质工程师负责审核相关记录3.内容3.1首件下列情景之一视为首件:a 调机的第一件合格品, b 接班第一件合格产品,c 设备维修或异常停机后第一件合格产品,d 工艺参数调整后第一件合格产品,e 工装维修后第一件合格产品,f 刀具调整第一件合格产品,g 人员调换后第一件合格产品。
(多工位的按一模)3.1.1首件产品经操作工自检合格,并填写自检记录《产品质量记录单》;3.1.2操作工把首件产品和记录交给当班检验员确认;3.1.3检验员接到首件后,依照检验工艺标准,进行检测和确认并填写《巡检记录表》;3.1.4首件须用三坐标检测的,检验员将产品送至计量检测中心工作台待测量;3.1.5三坐标检测人员检测依据:全尺寸依图纸,修改模产品依修模改模通知单,其他产品依工艺或检验指导书;3.1.6检测中心只提供检测报告,结论由检验员进行判定,确认合格后,通知操作工正常生产(人员调换后的首件,可以通过边生产边确认方式)。
批量生产的产品员工自检合格后可以先进行生产。
3.2制程3.2.1检验员依据检验指导书规定的管制项目和检验频率进行制程品质确认;3.2.2检验员检测产品并填写巡检记录(产品质量记录单或压铸机工艺参数现场检验记录表);3.2.3检验合格的项目,在巡检记录表上做好记录,如有不合格项目,在巡检记录表上做好记录,并立即通知操作工停止生产并向上级主管和生产部门报告。
检验员应对前面加工的产品进行追踪复核,对不良产品进标识隔离,并开据不合格品评审《不合格品控制程序》执行,备注一栏可填上开出的不合格评审单号;3.2.4如有特殊检查项目或为返工返修,可在检验记录表空格内填上须检查项目,执行巡检;3.3末件3.3.1操作工把末件产品交给检验员;检验员接到末件产品后,依照检验指导书,进行检测和确认,并填写记录;3.3.2末件检验不合格时,检验员应对前面加工的产品进行追踪复核,对不良产品进标识隔离,开出不合格品评审单按评审结果进行处置。
首末件管理办法

1.目的
为首末件检验管理有一定的程序遵循,使品质达到标准,确保产品品质,特订定此办法。
2.适用范围
适用于本公司生产现场品质的管理。
3.定义
首件建立的时机:
3.1每班或休息后开机或开工时;
3.2突发性停电后重新开机或开工时;
3.3机器故障修复后重新开机或开工时;
3.4品质问题点对策后生产时;
3.5生产作业人员变更后的首件。
4.职责
4.1本办法由品保课制订,各相关部门实施之。
4.2作业员:依检查重点略图及相关样件进行自检及生产。
4.3制程组长:针对作业员建立之首末件及生产过程中之产品品质进行巡检确认。
4.4制程品管:针对作业员建立、制程组长确认之首末件进行最终品质确认,确保量产
品质。
5.作业程序
6.相关文件
6.1记录管理程序FT-QP-003
7.使用相关表单
7.1首件检查合格QR-028-02-A0 7.2制程全检记录表PR-020-02-A0 7.3制程巡检记录表QR-040-06-A1。
首末件检验管理规定

首末件检验管理规定首末件检验管理规定1.检验流程2.首末件检验是指对生产过程中的首件和末件产品进行严格的检验和测试,以确保产品质量符合相关标准和规范。
以下是首末件检验的流程和步骤:3. a. 制定检验计划:根据生产计划和产品要求,制定首末件检验的计划和方案。
4. b. 确定检验项目:明确需要检验的部位、尺寸、质量、外观等项目,并准备好相应的检验工具。
5. c. 进行抽样检查:按照规定的抽样方案,从生产批次中抽取首件和末件产品进行检查。
6. d. 执行检验:根据检验计划和项目,对首件和末件产品进行严格的质量检验和测试。
7. e. 记录检验结果:将检验过程中发现的问题和数据记录下来,并填写相应的检验报告。
8. f. 分析检验结果:对检验结果进行分析,评估产品质量状况,提出改进措施。
9.g. 储存检验记录:将检验报告和相关数据资料进行存档,以备后续查阅和处理。
10.责任与职责11.在首末件检验过程中,各个岗位和人员需要明确自己的责任和职责,以确保检验工作的顺利进行和质量问题的及时处理。
以下是相关岗位和人员的职责:12. a. 生产人员:负责按照生产计划进行生产,关注生产过程中的异常情况,并及时处理或上报。
13. b. 质检人员:负责制定首末件检验计划和方案,执行检验操作,分析检验结果,提出改进措施。
14. c. 技术人员:负责协助质检人员制定检验方案,提供技术支持和指导,解决检验过程中出现的技术问题。
15. d. 仓库管理人员:负责配合质检人员进行产品入库前的质量检查,确保产品数量和质量符合要求。
16. e. 上级管理人员:负责对首末件检验工作进行监督和考核,确保检验质量和效率得到保障。
17.首件检验标准18.首件检验是对生产过程中的首件产品进行严格的检查和测试,以确保后续产品的质量稳定和符合相关标准。
以下是首件检验的标准和要求:19. a. 外观完好:产品外观应无破损、划痕、变形等质量问题。
20. b. 尺寸符合:产品的尺寸应符合图纸和工艺要求,误差在允许范围内。
食品首末件管理制度

食品首末件管理制度食品生产环节是食品首末件管理制度中最重要的环节之一。
在食品生产过程中,首要件即是食品原料。
食品原料的质量和来源直接影响着食品的品质和安全。
因此,食品生产企业必须建立完善的原料采购管理制度,确保购进的原料符合相关标准,并进行质量检测。
对于不合格原料,必须及时淘汰,确保不会影响到食品生产的质量和安全。
在食品加工环节中,首要件是食品加工设备。
食品企业需要对加工设备进行定期检查和维护,确保设备运转良好,不会对食品生产过程造成任何问题。
此外,食品生产过程中的人员必须接受相关的培训和考核,确保操作技能和卫生意识达到标准要求,保证加工过程的卫生和安全。
在食品储存环节中,首要件是储存条件。
食品必须在适宜的温度和湿度条件下进行储存,以防止食品变质或者受到细菌的侵害。
因此,食品企业必须建立相应的储存管理制度,对储存条件进行定期检查和记录,确保储存环境符合要求,不会对食品的质量和安全产生负面影响。
在食品运输环节中,首要件是运输温度和时间。
食品在运输过程中必须保持适宜的温度,以防止食品变质或者受到细菌的侵害。
同时,食品的运输时间也必须控制在合理范围内,避免食品过长时间的运输导致食品变质。
因此,食品运输企业必须严格执行运输管理制度,对运输车辆和人员进行检查和记录,确保食品的安全和质量。
在食品销售环节中,首要件是销售环境和条件。
食品销售点必须对销售环境进行定期清洁和消毒,确保销售环境卫生。
同时,食品销售点也必须对食品的质量和保质期进行管理,避免销售过期或者劣质食品。
因此,食品销售点必须执行销售管理制度,对销售环境和食品质量进行定期检查和记录,确保食品销售的安全和可靠。
食品首末件管理制度是保障食品安全的一个重要环节。
只有每一个环节都能够严格执行管理制度,确保食品的质量和安全,才能够保障消费者的身体健康和利益。
因此,食品生产企业必须高度重视食品首末件管理制度的执行,建立完善的管理机制,确保食品生产过程中的每一个环节都处于受控状态,不会产生任何问题。
生产中的首末件管理方法

9、烧录首件 ① 首次量产 烧录完成后先将芯片植球并压合在PCB板上进行功能测试。(提前制作治具) 首次量产的烧录软件首件,和试产末件 + 量产变更点进行功能比对。 软件烧录,要将烧录的软件导出来,进行确认。
保留末件样机困难的,也可以采用图片或者视频的方式保留末件信息,以便和首件进行对比。 要将整机外观(各个侧面)、PCBA外观(两个侧面)、开机过程、显示内容、按键灯光颜色等等拍成图片 或者视频,保存留用。
首件检查的注意事项: a、首件检查的风险识别: 假定前道工序的各种错误。然后分析验证在首件检查或者首件测试的哪个环节可以识别到这些错误。 b、将过往批量不良(市场和工程内)进行汇总,确认当前的首件检查过程是否可以拦截住当初的不良。
6、SMT日常首件的首件管理 SMT日常首件由生产部门制作完成、自检合格之后,IPQC接收SMT首件,并进行首件检查与测试。 1)SMT首件确认:确认SMT首件生产的生产过程,包括:设备参数,工艺参数。和末件一致。 2)SMT首件检查: ① 检查生产部门提交的SMT首件检查单,是否填写完整,是否正确。 ② 将SMT首件与上次的末件,目视进行对比检查。 3)SMT首件测试 安排测试工位对SMT首件进行一般功能、性能测试。(频次高,风险低,要节省工时)
② 日常烧录 日常烧录首件,没有任何变更信息的,烧录完成后比对校验和。 (可以节省芯片植球、测试动作。)
③ 变更烧录 烧录完成后需将芯片植球并压合在PCB板上进行功能测试。(提前制作治具) 变更后的烧录软件首件,和上次末件 + 变更点进行功能比对。 软件烧录,要将烧录的软件导出来,进行确认。
首末件管理办法

编制日期
批准生效日期
目的
为加强质量控制,预防产品生过程中,出现批量超差、返修、报废等情况,保证产品实物质量,促进产品顺利交付,特制定本管理办法.范围本文件适用源自司所有生产工序首末件确认;定义
3.1.首件:每个班次刚开始时或过程发生改变后加工的第一或前几件产品,对于大批量生产,“首件”往往是指一定数量的样品。
4.2.质量异常时,负责组织人员对问题点进行分析、调整;
品质部:4.3.负责首末件的确认,过程检验;
4.4.配合制造部门对不合格的首末件进行分析及调整并有向制造部提出停机的权限;
5 首末件操作流程
编制: 审核: 批准:
过程名称:
? 首末件检验
发放范围:
? 品质管理总部、装饰件分公司、欧美部品分公司、内饰件分公司、翔星分公司
概要:
版本
日期
拟订
变更内容
A/0
2012-4-17
新版作成
编审批签名:
编制
审核
批准
部门:
品质管理总部
姓名:
签名:
品质管理总部
装饰件分公司
欧美分公司
内饰件分公司
部门:品质中心
姓名:胡剑
职务:总监
签名:
3.2.末件:是指当批或当班生产零件的最后一个零件;
3.3.控制要求:下列情况之一的,需进行首检:(首检时机)
----重新开机; ----换模、换料、换班或设备更换时;
----工艺参数重新调整时; ----工装、模具变更换维修后; ----生产场地发生变更;
4 责任与权限
制造部:4.1.负责产品首末件的自检,互检;
食品生产首未件管理制度

食品生产首未件管理制度食品生产首件管理制度是指由食品生产企业制定的一套用于统一管理首件产品的流程和程序的规定,旨在确保首件产品的质量和安全,保障消费者的健康权益。
下面我将从制度的范围、制度的内容、制度的执行以及制度的评估四个方面来介绍食品生产首件管理制度。
制度的范围包括食品生产企业内所有生产首件产品的环节,涵盖从原材料采购、生产加工、包装、储存、运输等全过程。
制度适用于所有食品生产企业,无论其规模大小,无论其产品种类。
制度的内容主要包括以下几个方面:1.首件产品的定义和标准:明确首件产品的定义和标准,确保每一批次的产品都符合质量和安全要求。
包括对原材料的要求、生产工艺的规定、产品包装的要求等。
2.首件产品的抽样检验:针对每一批次的首件产品进行抽样检验,包括物理性状、化学成分、微生物指标等多个方面的检测,确保产品质量符合标准。
3.记录和存档:制定完善的记录制度,对首件产品的原材料、生产过程、检验结果等进行详细记录并存档。
确保数据真实可靠,以备查证。
4.问题处理:对于任何出现的问题,制度要求及时采取措施进行处理,追溯问题的原因,并对不合格产品实施处置措施,避免不合格产品流入市场。
制度的执行是保障制度有效性和实施效果的关键。
食品生产企业应对制度进行全员培训,确保每个员工都了解制度要求,并有能力执行。
同时,企业要建立健全的内部监督机制,通过内审、互查等方式监督制度的执行情况。
制度的评估是为了不断完善和提升制度的管理水平。
食品生产企业应定期进行制度的评估和审查,确定制度的有效性和实施效果,并根据评估结果进行调整和改进。
同时,还可以邀请第三方机构对企业的首件管理制度进行审查和评估,确保制度符合相关法律法规和行业标准。
总而言之,食品生产首件管理制度是保障食品质量和安全的重要措施,通过明确首件产品的标准、实施抽样检验、建立记录和存档制度、及时处理问题等方面的规定,确保产品质量符合标准,并保障消费者的健康权益。
企业应重视制度的执行和评估,不断完善和提升首件管理水平,以确保食品安全和质量。
ISO9001-2015首末件管理程序A0

首末件管理程序(ISO9001:2015)1.目地:为确保各阶段制程能在管制状态执行,确保质量稳定,提高产能,降低成本达到客户及系统需求,而建立该作业程序。
2.范围适用于本公司所有的在制品(制造之半成品,成品,成型射出品,冲压品)组装,成型,冲压。
3.术语:首件:每台机每批材料上线或开线,都要做全面检测并留样记录保存;末件:每批材料/每款产品之完成或停线都要留样并全面检测并记录保存,以保证以前之生产品之质量,并便于追溯。
4.权责:品保单位:负责首件样品的量测和功能试做;生产单位:负责确认后首件送样动作。
5.流程图:略6.作业内容:6.1注塑做首件时机:6.1.1注塑在每次换料、换模、修模(限尺寸、功能类)及设计变更后开机需送首件至IPQC确认;6.1.2注塑修模(外观类)后需送样品至IPQC确认,但IPQC不需要做首件,确认修模后的状况,记录于《PQC巡回检验记录表(注塑)》中;6.1.3注塑在停机前一小时需送末件至IPQC确认;6.1.4IPQC接到首、末件后依据《产品检验规范》、《工程图面》、《QIP检验记录表》在一个半小时内完成首件样品的外观,尺寸,功能的确认动作,并将结果记录于《QIP检验记录表》首件报表中,首件OK后正式生产;6.1.5首件试做部分:如因无材料或组装停线或机台设备维修等原因造成无法试做的首件部份,IPQC需量测好尺寸,如尺寸NG停机修模,后重新送首件,如尺寸量测OK需通知到生产部门主管及品管部门主管由其评估风险决定是否停机待首件试做结果。
6.2冲压做首件时机:6.2.1正常情况下:白班接班时做首件,夜班接班时做末件;6.2.2冲压在每次换模、修模(限尺寸、功能类)及设计变更后开机需送首件至IPQC确认;6.2.3冲压在停机前一小时需送末件至IPQC确认;6.2.4冲压修模(外观类)后需送样品至IPQC确认,但IPQC不需要做首件,确认修模后的状况,记录于《PQC巡回检验记录表(冲压)》中;6.2.5IPQC接到首、末件后依据《产品检验规范》、《工程图面》、《QIP检验记录表》在一个半小时内完成首件样品的外观,尺寸,功能的确认动作,并将结果记录于《QIP检验记录表》首件报表中,首件OK后正式生产;6.3组装在制程中有换线、换机种、换料、换设备及工程变更等情况需提前一小时首件给IPQC须对首5PCS成品进行首件检验(含外观﹑尺寸﹑功能)﹐检验项目参照《质量工程图》、《产品检验规范》、《工程图面》进行,并将结果记录于《首(末)件试做报告》及《QIP检验记录表》中。
- 1、下载文档前请自行甄别文档内容的完整性,平台不提供额外的编辑、内容补充、找答案等附加服务。
- 2、"仅部分预览"的文档,不可在线预览部分如存在完整性等问题,可反馈申请退款(可完整预览的文档不适用该条件!)。
- 3、如文档侵犯您的权益,请联系客服反馈,我们会尽快为您处理(人工客服工作时间:9:00-18:30)。
1 目的
为了更好的控制产品的质量,预防产品在生产过程中的批量不良,在下次生产前处理好本次过程中的问题,确保使后续生产顺利进行,以达到降低成本、提高效率。
特制定本管理规定。
2 范围
适用于本公司注塑车间首末件管理
3 术语和定义
首件:每次换模开始时或过程中条件发生变化时(包括:换机、换料、换色、修模、停机后、工艺发生变化较大时),由生产领班确认合格的产品后第15模报质检员做首件检验。
“首件”一般指正常批量生产前,依照检验标准确认合格的样品。
末件:是指当批次生产的最后一只产品制作的合格样品。
报废:为避免不合格品原有预期用途误用而对其所采取的措施。
废弃模:开机生产初期尺寸、外观不稳定的产品确认为不良品报废处理。
4 职责
4.1 生产部负责首件自检,通报质检员做首末件,在质量异常时,负责组织人员对问题点
进行分析和调整、改善。
4.2 产生部门/车间负责组织对产品的评审工作及对生产现场产品的标识、隔离,并按评审
结果进行处理及让步接受的申请。
4.3 品质部负责对首末件的确认及过程检验,确保首末件产品的外观、尺寸、结构、性能
等各方面满足客户的要求。
配合生产部门对改善品的检查,必要时组织相关部门参加评审。
4.4当出现批量不合格时,检验员有权要求停止生产;当外协辅料影响生产时检验员有权
要求异常辅料隔离退换,有权要求对生产的产品进行追溯隔离,产品检查合格后方可放行。
4.5品质部负责首件产品品质记录的制作及保存,首件样品最长保存期限为三个月,末件
产品最长保存期限为六个月
4.6技术部负责返工返修指导书的编制;负责异常产品对顾客影响程度的评审。
5首末件检查时机
5.1 每日每班到岗上班,某机台开始生产时,某机台转换产品颜色或材料时,某工序变更
生产工艺后,生产异常改善后再生产时,模具生产机台及周边设备异常修复后,其它特殊情况导致生产机台不能正常生产停止生产后再继续生产时,应执行首件检查
5.2 每批次生产的最后1个零件执行末件检查,末件随模具流转或者放置在固定的机台位
置
6首件检验
6.1 IPQC接到生产部的首件样品后,依据《检验作业指导书》、“OK样品”、“限度样件”
及外观标准、规格尺寸、性能需求及其它特殊要求对产品外观、尺寸、结构、性能等方面进行综合判定并做好相关记录。
6.2 IPQC判定完成,首件检验合格,需签首件样品标签(包含:产品名称、生产日期、
质检员签名),放置在对应的生产工位上;并立即通知正常生产。
6.3 连续生产中交接班的首件确认,本班首件替换上班末件,上一班次末件经检验符合或
处理后符合合格品标准,按合格品处理;不合格报废处理;连续生产中交接班的首件确认,可边生产边制作,但检查首件的时间跨度不得超过接班后1H
6.4 若首件检验不合格,IPQC应立即知会生产部门分析改善,改善完成后,继续送样直
到判定合格或条件认可为止。
如需要修模改善、返工返修、让步接收、报废处理的需要填写《过程不合格品处理单》由制造、品质、技术会签,按照会签处理意见实施;
不合格首件产品由生产部即时报废,相关记录保留存档;
7量产
7.1 首件合格后,生产部门立即安排生产。
8末件检验
8.1 根据本规定5.2条,制作末件,有生产班长提供最后一只产品通报当班IPQC进行末
件检验。
8.2 末件检查合格,标识(同首件标识)转生产部按照《模具管理制度》中的末件管理要
求进行检查保管及记录,用以追溯模具状态。
再次开机时本次末件当做参考样件使用,末件经检验能符合(或处理后能符合)合格品标准的,按照合格品处理;不合格的按照废品处理。
8.3 末件检查不合格,应通报当班作业员及班长,对本批次产品标识隔离,按照《可追溯
管理办法》清查所有异常产品,调查发生原因予以改善解决。
8.4 上/下模具时,如末件随模具流转时,模具管理人员要将末件一起发给注塑生产工位。
9. 首末件检查之持续改善
9.1 当生产完成时虽然产品的首末件都是合格的,但是因加工困难,需要返工返修、成本
高或劳动强度大时,生产部和品质部提出改善措施报告技术部(以修模改模为主)以便下次生产时达到降低成本、提高效率、持续改善的目的。
自主改善项目通知客户知悉并提供样件装配,合格后方可量产。
10工作流程图
11. 相关支持性文件
纠正和预防措施控制程序
产品标识和可追溯性控制程序(或生产过程控制程序)
顾客报怨控制程序
异常品流程图
红箱管理制度
返工作业指导书
检验规程
12.质量记录
R/QC.S11-01-01过程不合格品处理单
R/QC.S11-01-02质量问题处理单
R/QC.S11-01-04 返工/返修记录
本文档部分内容来源于网络,如有内容侵权请告知删除,感谢您的配合!。