大规格锯齿螺纹铣削宏程序
?邹军:大螺距锯齿型螺纹的编程方案
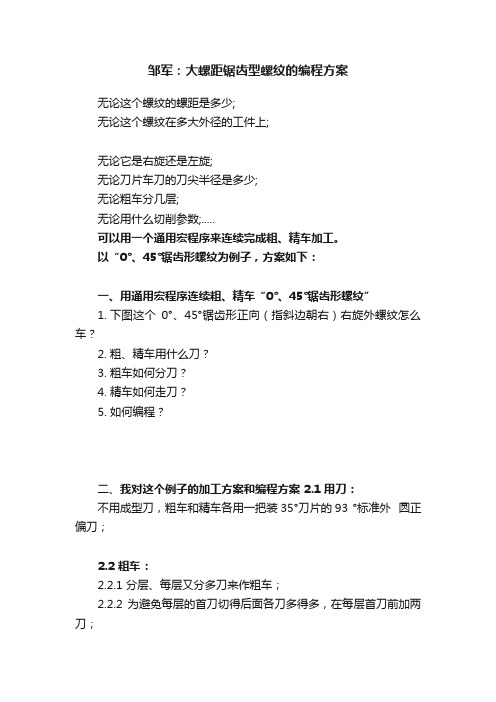
邹军:大螺距锯齿型螺纹的编程方案无论这个螺纹的螺距是多少;无论这个螺纹在多大外径的工件上;无论它是右旋还是左旋;无论刀片车刀的刀尖半径是多少;无论粗车分几层;无论用什么切削参数;.....可以用一个通用宏程序来连续完成粗、精车加工。
以“0°、45°锯齿形螺纹为例子,方案如下:一、用通用宏程序连续粗、精车“0°、45°锯齿形螺纹”1.下图这个0°、45°锯齿形正向(指斜边朝右)右旋外螺纹怎么车?2.粗、精车用什么刀?3.粗车如何分刀?4.精车如何走刀?5.如何编程?二、我对这个例子的加工方案和编程方案 2.1 用刀:不用成型刀,粗车和精车各用一把装35°刀片的93 °标准外圆正偏刀;2.2 粗车:2.2.1 分层、每层又分多刀来作粗车;2.2.2 为避免每层的首刀切得后面各刀多得多,在每层首刀前加两刀;2.3 精车:2.3.1 在斜边与外圆相交处安排一个圆倒角(把这个圆倒角的R设为0就是不要圆倒角);2.3.2 先车圆倒角、斜边和底圆右半,后车45°倒角、直边和底圆左半; 2.3.3 两边用不同的刀补号,以便能用刀补来调节槽宽;2.4 编一个把加工方案都包含进去的宏程序:2.4.1 这个宏程序应非常通用;2.4.2 执行这个宏程序应能连续把粗、精车都加工完成。
三、.粗车这个例子分层、每层分多刀和各层首刀前加两刀的示意图四、.关于0°、45°锯齿形螺纹的名称、用途和有关标准4.1 0°、45°锯齿形螺纹在我国只有(重型机械) 行业标准。
最早的标准是JB2071-1984 《水压机45°锯齿形螺纹》,后来被 JB/T2001.73-1999 《水系统45°锯齿形螺纹》替代,最新的标准是JB/ZQ4723-2006《液压机用45°锯齿形螺纹》。
4.2 0°、45°锯齿形螺纹的用途很广,不但水、液压机用,而且在需要承受巨大轴向力的传动件和固紧件中都用得着。
螺旋铣削宏程序
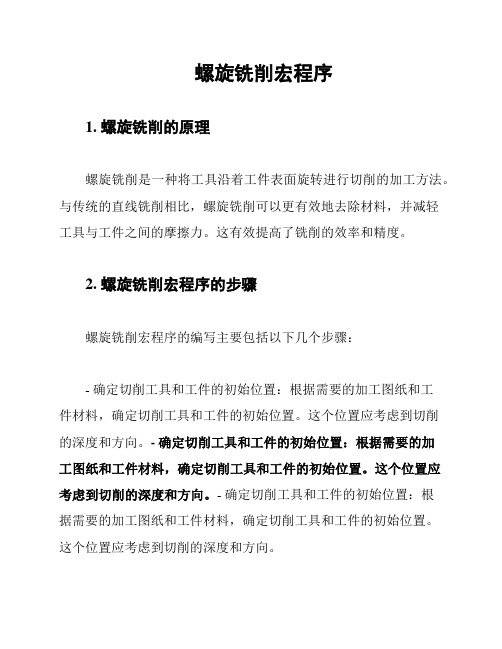
螺旋铣削宏程序1. 螺旋铣削的原理螺旋铣削是一种将工具沿着工件表面旋转进行切削的加工方法。
与传统的直线铣削相比,螺旋铣削可以更有效地去除材料,并减轻工具与工件之间的摩擦力。
这有效提高了铣削的效率和精度。
2. 螺旋铣削宏程序的步骤螺旋铣削宏程序的编写主要包括以下几个步骤:- 确定切削工具和工件的初始位置:根据需要的加工图纸和工件材料,确定切削工具和工件的初始位置。
这个位置应考虑到切削的深度和方向。
- 确定切削工具和工件的初始位置:根据需要的加工图纸和工件材料,确定切削工具和工件的初始位置。
这个位置应考虑到切削的深度和方向。
- 确定切削工具和工件的初始位置:根据需要的加工图纸和工件材料,确定切削工具和工件的初始位置。
这个位置应考虑到切削的深度和方向。
- 设置切削参数:根据需要的加工质量和效率,设置切削参数,如切削速度、进给速度和切削深度等。
这些参数应根据工具和工件的特性进行调整。
- 设置切削参数:根据需要的加工质量和效率,设置切削参数,如切削速度、进给速度和切削深度等。
这些参数应根据工具和工件的特性进行调整。
- 设置切削参数:根据需要的加工质量和效率,设置切削参数,如切削速度、进给速度和切削深度等。
这些参数应根据工具和工件的特性进行调整。
- 编写切削路径:根据加工图纸和要求,编写切削路径。
螺旋铣削的路径应沿着工件表面形成螺旋状的轨迹,以保证整个加工过程的稳定性和精度。
- 编写切削路径:根据加工图纸和要求,编写切削路径。
螺旋铣削的路径应沿着工件表面形成螺旋状的轨迹,以保证整个加工过程的稳定性和精度。
- 编写切削路径:根据加工图纸和要求,编写切削路径。
螺旋铣削的路径应沿着工件表面形成螺旋状的轨迹,以保证整个加工过程的稳定性和精度。
- 编写切削程序:根据切削路径,编写切削程序。
切削程序主要包括控制切削工具移动和设置相应的切削参数。
这些程序应根据具体的机床和控制系统进行编写。
- 编写切削程序:根据切削路径,编写切削程序。
螺 纹 铣 削 程 序(宏程序)
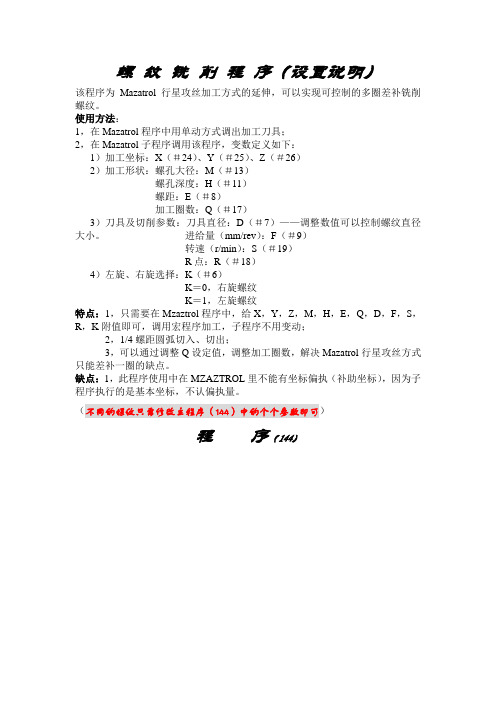
螺纹铣削程序(设置说明)该程序为Mazatrol行星攻丝加工方式的延伸,可以实现可控制的多圈差补铣削螺纹。
使用方法:1,在Mazatrol程序中用单动方式调出加工刀具;2,在Mazatrol子程序调用该程序,变数定义如下:1)加工坐标:X(#24)、Y(#25)、Z(#26)2)加工形状:螺孔大径:M(#13)螺孔深度:H(#11)螺距:E(#8)加工圈数:Q(#17)3)刀具及切削参数:刀具直径:D(#7)——调整数值可以控制螺纹直径大小。
进给量(mm/rev):F(#9)转速(r/min):S(#19)R点:R(#18)4)左旋、右旋选择:K(#6)K=0,右旋螺纹K=1,左旋螺纹特点:1,只需要在Mzaztrol程序中,给X,Y,Z,M,H,E,Q,D,F,S,R,K附值即可,调用宏程序加工,子程序不用变动;2,1/4螺距圆弧切入、切出;3,可以通过调整Q设定值,调整加工圈数,解决Mazatrol行星攻丝方式只能差补一圈的缺点。
缺点:1,此程序使用中在MZAZTROL里不能有坐标偏执(补助坐标),因为子程序执行的是基本坐标,不认偏执量。
(不同的螺纹只需修改主程序(144)中的个个参数即可)程序(144)子程序(145)O00000005(HELICAL TAP CYCLE) (EIA HELICAL TAP)O00000005IF[#13EQ0]GOTO100IF[#11EQ0]GOTO200IF[#8EQ0]GOTO300IF[#17EQ0]GOTO400IF[#7EQ0]GOTO500IF[#19EQ0]GOTO600IF[#18EQ0]GOTO700IF[[#13-#7]LT0]GOTO800(MAIN PROGRAM)G91G28Z0.G90G00G95X#24Y#25G43Z50.G90G00Z#18Z#26S#19M03#3=#9*4#21=#11-0.5G91G01Z-#21F#3Z-0.5F0.1#1=[#13-#7]/2#2=#17*#8#3=#9*0.4#4=[#13-#7]/4#5=#8/4IF[#6EQ1] GOTO 20(RIGHT TAP)N10 G17G03X-#1Y0.Z#5R#4F#3G17G03X0.Y0.Z#2I#1P#17F#9G17G03X#1Y0.Z#5R#4F#3GOTO 30(LEFT TAP)N20 G17G02X-#1Y0.Z#5R#4F#3G17G02X0.Y0.Z#2I#1P#17F#9G17G02X#1Y0.Z#5R#4F#3N30 G90G00Z#18G91G28Z0.M99N100 #3000=21(=M--ERROR)N200 #3000=22(=H--ERROR)N300 #3000=23(=E--ERROR)N400 #3000=24(=Q--ERROR)N500 #3000=25(=TOOL-D-ERROR) N600 #3000=26(=S-ERROR)N700 #3000=27(=POINT-R-ERROR) N800 #3000=28(=M-D--ERROR)M30。
《用宏程序实现在数控车床上加工锯齿形螺纹》
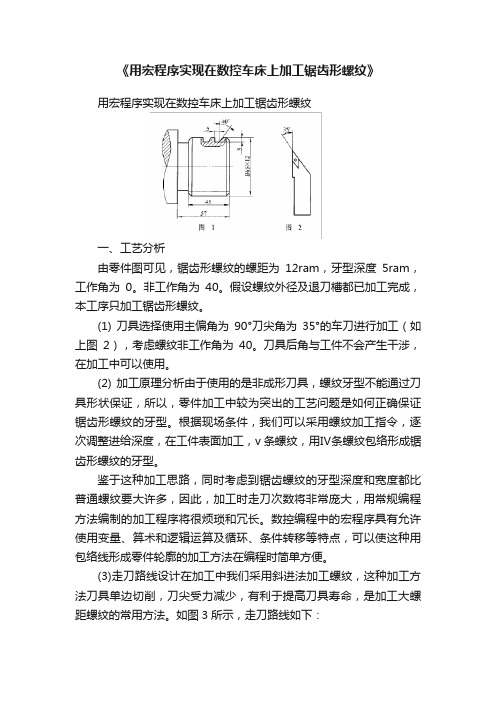
《用宏程序实现在数控车床上加工锯齿形螺纹》用宏程序实现在数控车床上加工锯齿形螺纹一、工艺分析由零件图可见,锯齿形螺纹的螺距为12ram,牙型深度5ram,工作角为0。
非工作角为40。
假设螺纹外径及退刀槽都已加工完成,本工序只加工锯齿形螺纹。
(1) 刀具选择使用主偏角为90°刀尖角为35°的车刀进行加工(如上图2),考虑螺纹非工作角为40。
刀具后角与工件不会产生干涉,在加工中可以使用。
(2) 加工原理分析由于使用的是非成形刀具,螺纹牙型不能通过刀具形状保证,所以,零件加工中较为突出的工艺问题是如何正确保证锯齿形螺纹的牙型。
根据现场条件,我们可以采用螺纹加工指令,逐次调整进给深度,在工件表面加工,v条螺纹,用Ⅳ条螺纹包络形成锯齿形螺纹的牙型。
鉴于这种加工思路,同时考虑到锯齿螺纹的牙型深度和宽度都比普通螺纹要大许多,因此,加工时走刀次数将非常庞大,用常规编程方法编制的加工程序将很烦琐和冗长。
数控编程中的宏程序具有允许使用变量、算术和逻辑运算及循环、条件转移等特点,可以使这种用包络线形成零件轮廓的加工方法在编程时简单方便。
(3)走刀路线设计在加工中我们采用斜进法加工螺纹,这种加工方法刀具单边切削,刀尖受力减少,有利于提高刀具寿命,是加工大螺距螺纹的常用方法。
如图3所示,走刀路线如下:其中图3a是z向循环,递增进给,沿右边界向进给一次。
图3b 是沿右边界向循环进给,z向嵌套循环递增进给。
1、刀具在工件外,沿锯齿形螺纹的40。
斜边进给一定的深度。
2、进行螺距12ram的螺纹加工,完成后刀具返回前一螺纹加工起点。
3、向坐标不变,刀具自右向左沿z向进给一定深度。
4、进行螺距12ram的螺纹加工,完成后刀具返回前一螺纹加工起点。
5、向坐标不变,刀具继续自右向左沿z向进给,然后同 4 加工;如此循环,直到z坐标到达牙型左侧轮廓线,则该深度牙型余量依次全部被切除。
6、刀具依据①的螺纹起点,继续沿锯齿形螺纹的40。
车铣加工中心铣螺纹宏程序的应用

车铣加工中心铣螺纹宏程序的应用车铣加工中心是一种集车削和铣削功能于一体的加工中心设备,可以完成复杂零件的加工。
在车铣加工中心中,铣割是一项重要的加工工艺之一,而铣螺纹则是其中的一种常见的加工操作,通过宏程序的应用,可以有效地实现铣螺纹的加工。
铣螺纹是指在工件表面加工出螺旋状凹凸纹路的工艺,常用于制造零部件的连接结构,如螺钉、螺母等。
在车铣加工中心中,铣螺纹通常使用宏程序来实现,宏程序是一种由一系列预设的指令组成的程序,通过它可以实现一系列复杂的加工操作,极大地提高了加工的效率和精度。
车铣加工中心铣螺纹宏程序的应用可以大大提高生产效率。
传统的铣螺纹加工是通过手动操作来完成的,需要操作员不断地调整刀具和工件的位置,操作繁琐,效率低下。
而通过宏程序,可以预先设定螺纹的参数和工艺路径,然后由数控系统自动执行,整个加工过程无需人工干预,大大提高了加工效率,减少了人力成本。
铣螺纹宏程序的应用可以提高加工的精度和稳定性。
由于宏程序是由预设的指令组成,所以在加工过程中可以保持加工参数的一致性,避免了人为的误差,从而保证了加工零件的尺寸精度和表面质量。
宏程序可以实现自动刀具更换和自动补偿功能,及时修正加工中的误差,保证了加工的稳定性和一致性。
铣螺纹宏程序的应用还可以降低操作员的技能要求。
传统的手动操作方式需要操作员具备较高的操作技能和经验,才能熟练地完成铣螺纹的加工。
而通过宏程序,加工操作可以由数控系统自动执行,操作员只需进行简单的参数设置和监控,减轻了操作员的工作负担,降低了技能要求,提高了生产的稳定性。
车铣加工中心铣螺纹宏程序的应用具有诸多优点,可以极大地提高生产效率,提高加工的精度和稳定性,降低操作员的技能要求,是一种非常有效的加工方法。
在实际的生产中,加工厂可以根据具体的零件需求和加工要求,充分利用宏程序的功能,制定合理的加工工艺,有效地提高生产效率和产品质量,降低生产成本,提升市场竞争力。
值得注意的是,在使用铣螺纹宏程序时,操作人员应该熟悉它的操作步骤和注意事项,掌握其使用技巧,确保加工安全和稳定性。
Fanuc螺旋铣螺纹与宏程序铣螺纹教程

Fanuc系统铣螺纹编程(宏程序和螺旋插补)举例:如下图铣削5-M30*1.5-深15mm的细牙右旋螺纹。
刀具选择如下:(用废旧的钨钢刀柄磨的单刃螺纹铣刀,适合切削1.5螺距的螺纹)工艺分析:三轴联动铣削螺纹,实质是XY平面加工整圆同时,Z轴每加工一个整圆下降一个螺纹,加工时是以螺纹孔的中心轴线作为编程参考点,所以铣削单个螺纹孔时,通常将坐标系原点建立在孔中心,若要铣削多个螺孔,就要试着将坐标系偏移至孔的中心。
这题要铣削5个孔,中间的孔直接可以铣削,R50圆周上的4个等分螺孔,可以借助坐标偏移(fanuc系统用G52)来实现。
M30*1.5的螺纹,事先将螺纹底孔加工到28.5mm,螺纹齿高H=0.974刀具直径经检测,直径为8mm,有效加工孔深为22mm,程序如下:1、宏程序铣削螺纹单个螺纹孔铣削程序G54 G90 G17 坐标系原点建立在孔的中心,底孔事先加工好M03 S3500 (单刃切削,高转速,小吃刀,快进给)G00 Z50.G00 X0 Y0G00 Z3. (安全高度,定位值是螺距的整倍数)#1=0.3 齿高切深赋值N10 #2=10.25+#1 (28.5的孔,单边14.25,刀半径4,刀具往内偏移到10.25定位)G02 X#2 Y0 I [ #2/2 ] J0 F300. 以半圆形式切入#3=1.5 螺距PN20 G02 X#2 Y0 Z#3 I-#2 J0 F3000. 插补螺纹,到Z1.5的高度#3= #3 - 1.5IF [ #3 GE - 15.1 ] GOTO20 螺纹切削孔深15mmG02 X0 Y0 I-[ #2/2 ] J0 F300. 半圆形式切出,刀具到中心G00 Z3. 抬刀到安全高度,前后一致#1 = #1 + 0.2 切削齿高,往X方向增大IF [ #1 LE 0.91 ] GOTO10 加工到齿高G01 X0 Y0 F300. 退刀G00 Z100. 抬刀M30本题5-M30*1.5-15的程序主程序:G54 G90 G17 坐标系原点建立在孔的中心,底孔事先加工好M03 S3500 (单刃切削,高转速,小吃刀,快进给)G00 Z50.G00 X0 Y0M98 P1000 调用铣床螺纹的子程序#4 = 0 角度初始赋值N30 #5 = 50 * COS [ #4 ] X坐标#6 = 50 * SIN [ #4 ] Y坐标G52 X#5 Y#6 坐标偏移G00 X0 Y0 到偏移之后的原点定位M98 P1000 调用铣螺纹的子程序#4 = #4 + 90 角度增加IF [ #4 LE 271 ] GOTO30加工剩余3个孔,要是写360,第一个孔要再加工一次G00 Z100.G52 X0 Y0G54 G00 X100. Y100.M30子程序:O1000;G00 X0 Y0G00 Z3. (安全高度,定位值是螺距的整倍数)#1=0.3 齿高切深赋值N10 #2=10.25+#1 (28.5的孔,单边14.25,刀半径4,刀具往内偏移到10.25定位)G02 X#2 Y0 I [ #2/2 ] J0 F300. 以半圆形式切入#3=1.5 螺距PN20 G02 X#2 Y0 Z#3 I-#2 J0 F3000. 插补螺纹,到Z1.5的高度#3= #3 - 1.5IF [ #3 GE - 15.1 ] GOTO20 螺纹切削孔深15mmG02 X0 Y0 I-[ #2/2 ] J0 F300. 半圆形式切出,刀具到中心G00 Z3. 抬刀到安全高度,前后一致#1 = #1 + 0.2 切削齿高,往X方向增大IF [ #1 LE 0.91 ] GOTO10 加工到齿高G01 X0 Y0 F300. 退刀G00 Z10. 抬刀G52 X0 Y0 取消坐标偏移M99 返回主程序2、利用螺旋插补加工螺纹单个螺纹孔铣削程序G54 G90 G17 坐标系原点建立在孔的中心,底孔事先加工好M03 S3500 (单刃切削,高转速,小吃刀,快进给)G00 Z50.G00 X0 Y0G00 Z3. (安全高度,定位值是螺距的整倍数)#1=0.3 齿高切深赋值N10 #2=10.25+#1 (28.5的孔,单边14.25,刀半径4,刀具往内偏移到10.25定位)G02 X#2 Y0 I [ #2/2 ] J0 F300. 以半圆形式切入G91 G02 X0 Y0 Z-1.5 I-#2 J0 L11 F3000. 每次1.5,重复11次G90 G02 X0 Y0 I-[ #2/2 ] J0 F300. 半圆形式切出,刀具到中心G00 Z3. 抬刀到安全高度,前后一致#1 = #1 + 0.2 切削齿高,往X方向增大IF [ #1 LE 0.91 ] GOTO10 加工到齿高G01 X0 Y0 F300. 退刀G00 Z100. 抬刀M30本题5-M30*1.5-15的程序主程序:G54 G90 G17 坐标系原点建立在孔的中心,底孔事先加工好M03 S3500 (单刃切削,高转速,小吃刀,快进给)G00 Z50.G00 X0 Y0M98 P1000 调用铣床螺纹的子程序#4 = 0 角度初始赋值N30 #5 = 50 * COS [ #4 ] X坐标#6 = 50 * SIN [ #4 ] Y坐标G52 X#5 Y#6 坐标偏移G00 X0 Y0 到偏移之后的原点定位M98 P1000 调用铣螺纹的子程序#4 = #4 + 90 角度增加IF [ #4 LE 271 ] GOTO30加工剩余3个孔,要是写360,第一个孔要再加工一次G00 Z100.G52 X0 Y0G54 G00 X100. Y100.M30子程序:O1000;G00 X0 Y0G00 Z3. (安全高度,定位值是螺距的整倍数)#1=0.3 齿高切深赋值N10 #2=10.25+#1 (28.5的孔,单边14.25,刀半径4,刀具往内偏移到10.25定位)G02 X#2 Y0 I [ #2/2 ] J0 F300. 以半圆形式切入G91 G02 X0 Y0 Z-1.5 I-#2 J0 L11 F3000. 每次1.5,重复11次G90 G02 X0 Y0 I-[ #2/2 ] J0 F300. 半圆形式切出,刀具到中心G00 Z3. 抬刀到安全高度,前后一致#1 = #1 + 0.2 切削齿高,往X方向增大IF [ #1 LE 0.91 ] GOTO10 加工到齿高G90 G01 X0 Y0 F300. 退刀G00 Z10. 抬刀G52 X0 Y0 取消坐标偏移M99 返回主程序。
Fanuc螺旋铣螺纹与宏程序铣螺纹教程

Fanuc系统铣螺纹编程(宏程序与螺旋插补)举例:如下图铣削5—M30*1、5—深15mm得细牙右旋螺纹.刀具选择如下:(用废旧得钨钢刀柄磨得单刃螺纹铣刀,适合切削1、5螺距得螺纹)工艺分析:三轴联动铣削螺纹,实质就是XY平面加工整圆同时,Z轴每加工一个整圆下降一个螺纹,加工时就是以螺纹孔得中心轴线作为编程参考点,所以铣削单个螺纹孔时,通常将坐标系原点建立在孔中心,若要铣削多个螺孔,就要试着将坐标系偏移至孔得中心。
这题要铣削5个孔,中间得孔直接可以铣削,R50圆周上得4个等分螺孔,可以借助坐标偏移(fanuc系统用G52)来实现。
M30*1、5得螺纹,事先将螺纹底孔加工到28、5mm,螺纹齿高H=0、974刀具直径经检测,直径为8mm,有效加工孔深为22mm,程序如下:1、宏程序铣削螺纹单个螺纹孔铣削程序G54G90G17 坐标系原点建立在孔得中心,底孔事先加工好M03 S3500(单刃切削,高转速,小吃刀,快进给)G00Z50、G00 X0 Y0G00Z3、(安全高度,定位值就是螺距得整倍数)#1=0、3 齿高切深赋值N10#2=10、25+#1 (28、5得孔,单边14、25,刀半径4,刀具往内偏移到10、25定位)G02 X#2 Y0 I [#2/2 ]J0 F300、以半圆形式切入#3=1、5螺距PN20G02X#2Y0 Z#3I-#2 J0F3000、插补螺纹,到Z1、5得高度#3=#3 —1、5IF[#3GE -15、1 ] GOTO20 螺纹切削孔深15mmG02X0Y0 I—[ #2/2]J0F300、半圆形式切出,刀具到中心G00Z3、抬刀到安全高度,前后一致#1= #1 +0、2切削齿高,往X方向增大IF [ #1 LE 0、91]GOTO10 加工到齿高G01 X0 Y0 F300、退刀G00Z100、抬刀M30本题5-M30*1、5—15得程序主程序:G54 G90G17 坐标系原点建立在孔得中心,底孔事先加工好M03S3500 (单刃切削,高转速,小吃刀,快进给)G00 Z50、G00 X0 Y0M98 P1000调用铣床螺纹得子程序#4 = 0 角度初始赋值N30#5=50*COS [ #4 ]X坐标#6= 50*SIN[#4 ] Y坐标G52X#5Y#6 坐标偏移G00X0 Y0 到偏移之后得原点定位M98 P1000调用铣螺纹得子程序#4=#4 +90 角度增加IF [#4LE271]GOTO30加工剩余3个孔,要就是写360,第一个孔要再加工一次G00 Z100、G52 X0 Y0G54 G00 X100、Y100、M30子程序:O1000;G00X0 Y0G00Z3、(安全高度,定位值就是螺距得整倍数)#1=0、3 齿高切深赋值N10 #2=10、25+#1 (28、5得孔,单边14、25,刀半径4,刀具往内偏移到10、25定位)G02X#2 Y0 I [#2/2 ]J0 F300、以半圆形式切入#3=1、5螺距PN20G02X#2Y0Z#3I—#2 J0F3000、插补螺纹,到Z1、5得高度#3=#3 —1、5IF[#3 GE—15、1 ]GOTO20螺纹切削孔深15mmG02X0 Y0 I-[#2/2] J0F300、半圆形式切出,刀具到中心G00 Z3、抬刀到安全高度,前后一致#1 = #1 + 0、2切削齿高,往X方向增大IF [#1LE 0、91]GOTO10加工到齿高G01X0Y0 F300、退刀G00 Z10、抬刀G52 X0Y0 取消坐标偏移M99 返回主程序2、利用螺旋插补加工螺纹单个螺纹孔铣削程序G54 G90G17 坐标系原点建立在孔得中心,底孔事先加工好M03 S3500(单刃切削,高转速,小吃刀,快进给)G00 Z50、G00 X0Y0G00 Z3、(安全高度,定位值就是螺距得整倍数)#1=0、3 齿高切深赋值N10 #2=10、25+#1(28、5得孔,单边14、25,刀半径4,刀具往内偏移到10、25定位)G02X#2 Y0I [ #2/2]J0 F300、以半圆形式切入G91G02 X0 Y0Z-1、5I—#2 J0 L11F3000、每次1、5,重复11次G90G02 X0 Y0I—[#2/2 ]J0 F300、半圆形式切出,刀具到中心G00 Z3、抬刀到安全高度,前后一致#1 =#1 + 0、2切削齿高,往X 方向增大IF [#1 LE0、91 ]GOTO10加工到齿高G01X0Y0F300、退刀G00 Z100、抬刀M30本题5-M30*1、5-15得程序主程序:G54G90 G17坐标系原点建立在孔得中心,底孔事先加工好M03 S3500(单刃切削,高转速,小吃刀,快进给)G00Z50、G00 X0 Y0M98P1000调用铣床螺纹得子程序#4 = 0角度初始赋值N30#5= 50 *COS[#4] X坐标#6 =50 * SIN [#4 ]Y坐标G52 X#5 Y#6坐标偏移G00 X0Y0 到偏移之后得原点定位M98P1000调用铣螺纹得子程序#4=#4 + 90 角度增加IF[#4 LE271 ]GOTO30加工剩余3个孔,要就是写360,第一个孔要再加工一次G00Z100、G52X0Y0G54 G00 X100、Y100、M30子程序:O1000;G00X0 Y0G00Z3、(安全高度,定位值就是螺距得整倍数)#1=0、3 齿高切深赋值N10 #2=10、25+#1 (28、5得孔,单边14、25,刀半径4,刀具往内偏移到10、25定位)G02 X#2 Y0 I[#2/2 ]J0 F300、以半圆形式切入G91G02 X0Y0 Z-1、5 I—#2 J0 L11 F3000、每次1、5,重复11次G90 G02 X0 Y0 I-[ #2/2] J0F300、半圆形式切出,刀具到中心G00Z3、抬刀到安全高度,前后一致#1= #1+ 0、2 切削齿高,往X方向增大IF[#1 LE 0、91 ] GOTO10加工到齿高G90 G01 X0Y0 F300、退刀G00 Z10、抬刀G52X0Y0 取消坐标偏移M99返回主程序。
高效加工大螺距锯齿型螺纹的方法

高效加工大螺距锯齿型螺纹的方法摘要:锯齿形螺纹在数控车床上的加工,因其程序设计比较复杂,在实际应用时还有诸多难点,尤其在细长轴上加工大螺距锯齿螺纹,由于工件刚性差,加工过程中容易颤动,常导致刀具崩刃或损坏。
本文以某产品大型螺杆为例,对加工过程遇到的加工难点进行了深入剖析,从设备选型,刀具及工艺装备的选择,宏程序的编制等方面进行了深入探讨,形成了一套完整的工艺规程,保证了产品质量,提高了加工效率。
关键词锯齿螺纹宏程序加工工艺引言近年来,随着航天产品质量要求的持续增高,大螺距、大牙深的螺纹加工零件不断增多,零件形位公差,尺寸公差、表面粗糙度等要求也越来越严,致使加工难度进一步增大。
以螺杆为例,其为某产品支撑臂中的关键受力部件,螺距大、牙型深、螺纹长,同时,整体的形位公差,尺寸公差及粗糙度要求较高,因此零件的加工难度较大,质量不易保证。
其工件材料为40Cr,总长1096mm,锯齿螺纹:B300*24-7e,牙深21mm,螺距为24mm,螺纹长度450mm。
该产品过去使用普通车床CW6180加工,刀具选用高速钢成型刀具,刀具切削量大,容易引起振动,极易崩刃,影响工件的加工质量,且工人的劳动强度大,效率低下。
本文从数控加工角度,对刀具,加工方法,工艺过程进行革新,解决了此类零件的加工难点。
螺杆及牙型示意图(如图1.1、1.2所示)图1.1 螺杆图1.2 锯齿型螺纹牙型1.工艺设计方案1.1.设备的选择选择数控设备时,其主轴、中心架及尾座的同轴度应小于0.03mm,机床的定位精度、重复定位精度要求小于0.003,由于牙侧壁表面粗糙度要求为Ra1.6,因此,机床的刚性、稳定性要好,轴向及径向跳动应小于0.003。
1.1.刀具的选择由于工件硬度较高,为HRC25-32。
按照传统方法加工时,选用高速钢成型车刀,刀具的硬度低,刚性差,易磨损。
现选择硬质合金涂层切槽刀具。
在选择槽刀具时,刀头长度应稍大于18mm,刀片宽度4mm,R角应稍大于0.4mm(以保证精加工时牙侧壁的粗糙度),并同时准备两把,一把用于粗加工,另一把则用于精加工。
加工中心铣加工螺纹通用宏程序

工作原理加工中心通用铳螺纹宏程序工作原理:编程原理:G02 Z-2.5 13.Z-2.5等于螺距为2.5mm优势假设刀具半径为5mm则加工M16的右旋螺纹使用了三轴联动数控铳床或加工中心进行加工螺纹,相对于传统螺纹加工1、如螺距为2的螺纹铳刀可以加工各种公称直径,螺距为2mm的内外螺纹2、采用铳削方式加工螺纹,螺纹的质量比传统方式加工质量高3、采用机夹式刀片刀具,寿命长4、多齿螺纹铳刀加工时,加工速度远超攻丝5、首件通止规检测后,后面的零件加工质量稳定使用方法G65 P1999 X_ Y_ Z_ R_ A_ B_ C_ S_ F_XY螺纹孔或外螺纹的中心位置X=#24 Y=#25Z螺纹加工到底部,Z轴的位置(绝对坐标)Z=#26R 快速定位(安全高度)开始切削螺纹的位置R=#18A 螺纹螺距A=#1B 螺纹公称直径B=#2C螺纹铳刀的刀具半径C=#3内螺纹为负数外螺纹加工为正数S 主轴转速F 进给速度,主要用于控制刀具的每齿吃刀量如:G65 p1999 X30 Y30 Z-10 R2 A2 B16 C-5 S2000 F150; 在X30y30 的位置加工M16 螺距2 深10 的右旋螺纹加工时主轴转速为2000 转进给进度为150mm/min 宏程序代码O1999;G90G94G17G40;G0X#24Y#25; 快速定位至螺纹中心的X、Y 坐标M3S#19; 主轴以设定的速度正转#31=#2*0.5+#3; 计算出刀具偏移量#32=#18-#1; 刀具走螺旋线时,第一次下刀的位置#33=#24-#31; 计算出刀具移动到螺纹起点的位置G0Z#18; 刀具快速定位至R 点G1X#33F#9; 刀具直线插补至螺旋线的起点,起点位于X 的负方向N20 G02Z-#32I#31; 以偏移量作为半径,以螺距作为螺旋线Z 向下刀量(绝对坐标)IF[#32LE#26]GOTO30; 当前Z 向位置大于等于设定Z 向底位时,进行跳转#32=#32-#1; Z 向的下个螺旋深度目标位置(绝对坐标)GOTO20;N30;IF[#3GT0]THEN #6=#33-#1; 外螺纹,退刀时刀具往X 负方向退一个螺距量IF[#3LT0]]THEN #6=#24; 内螺纹,退刀时刀具移动到螺纹中心位置G0X#6G90G0Z#18; 提刀至安全高度M99;。
螺纹铣削宏程序
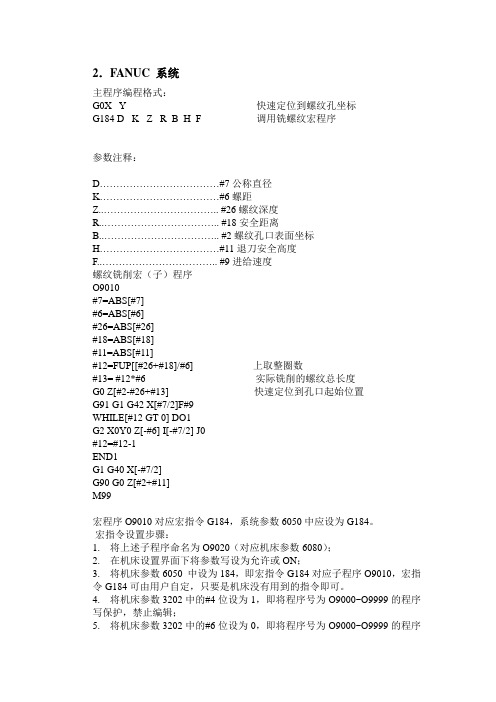
2.FANUC 系统主程序编程格式:G0X_ Y_ 快速定位到螺纹孔坐标G184 D_ K_ Z_ R_B_H_F_ 调用铣螺纹宏程序参数注释:D………………………………#7公称直径K………………………………#6螺距Z..…………………………….. #26螺纹深度R..…………………………….. #18安全距离B..…………………………….. #2螺纹孔口表面坐标H………………………………#11退刀安全高度F..…………………………….. #9进给速度螺纹铣削宏(子)程序O9010#7=ABS[#7]#6=ABS[#6]#26=ABS[#26]#18=ABS[#18]#11=ABS[#11]#12=FUP[[#26+#18]/#6] 上取整圈数#13= #12*#6 实际铣削的螺纹总长度G0 Z[#2-#26+#13] 快速定位到孔口起始位置G91 G1 G42 X[#7/2]F#9WHILE[#12 GT 0] DO1G2 X0Y0 Z[-#6] I[-#7/2] J0#12=#12-1END1G1 G40 X[-#7/2]G90 G0 Z[#2+#11]M99宏程序O9010对应宏指令G184,系统参数6050中应设为G184。
宏指令设置步骤:1.将上述子程序命名为O9020(对应机床参数6080);2.在机床设置界面下将参数写设为允许或ON;3.将机床参数6050 中设为184,即宏指令G184对应子程序O9010,宏指令G184可由用户自定,只要是机床没有用到的指令即可。
4.将机床参数3202中的#4位设为1,即将程序号为O9000~O9999的程序写保护,禁止编辑;5.将机床参数3202中的#6位设为0,即将程序号为O9000~O9999的程序隐藏;6.将参数写设为不允许或OFF。
螺纹铣削的宏程序加工

价 可低廉 。 只能加 T 刀片相 同齿形螺 要采用 G 0 2 / G 0 3圆弧插 补指令 。一次
只 能产牛 一条 3 6 0 度 的螺 旋线 即 一个螺
在X K 5 0 4 0数控 铣 床 上 ( 南 京 笫 二
距 的螺旋 线 。 要加 T 7 2 0度 或更 大角 机 床厂 生产 , 眦置 F A N U C 0 i 数 控 系统 )
体 式两类 机 央式 又可分 为单 齿 机央 和 T右旋 外螺纹 刀具从 f 至 下 ,加 T : 左
多 机央 两类
旋外 螺纹刀 具从下 至
与 一 般 轮廓
单齿 机火 : 结 构像 内螺纹牟 刀。 只有 的数控 铣 削相 同 ,螺 纹铣 削开始 进刀
一
个 螺纹 加 r 齿 。一个螺 旋运 动 只能加 时也采 用切 向的切人 和切 } J I 。 并上 土 , 为
T螺纹 长度 的铣刀 。 3 、 螺 纹铣 削的程 序编 制
个 螺纹 , 加T效 高 。 刀片更换 力 便 且 距 的刀 片 , 以称 为定螺距 螺纹铣 刀 。 整体 式 : 刃上也有 多个 螺 纹加
对 于数控 铣床来 说,铣 削螺 纹主 图 2 加工左 旋外 螺纹时 刀具 运动 示意
所示 上件 的 内螺纹 ,选用 齿 齿, 也是一 种定螺 距螺纹 铣刀 。 具 整 度 的螺 旋 线叫‘ ,就要 币复 编下 了 螺旋插 补 加 上 图 3 而日 . 还需要 大量 的运 算 , 造 成 了时 机 夹 式 铣 。螺 纹 相关 参 数 为 : M 2 0 X 体 硬质合 金制 成 , 刚性 好 , 能有 较 高的切 指令 ,
上 一 齿 。效率底 。n 加 r 相 M齿彤 , 任 意 保 证铣 旋 转 一周 H 『 J 完 成 螺纹 J J I I J 二 。 螺距 的螺 纹。
螺纹的宏程序铣削加工分析
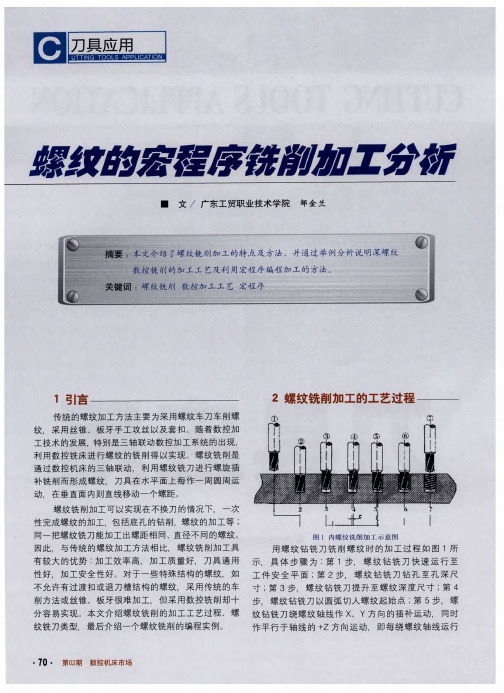
合 适的螺纹底 孔对于螺纹加工是十分重要的。一 个尺 寸稍 大的螺纹底孔能 有效降低攻丝过程 中产 生的
3螺 纹铣 削轨 迹
切 削热和 切削力。但 它也会减 小螺纹的接触率。 国家
螺 纹 铣 削运 动 轨 迹 为 一螺 旋 线 ,可 通过 数 控机 床 标 准 和技 术 委 员会 规 定 : 深 孔 中, 允 许 在 孔 壁 上 只 在 的三轴联动来 实现 。图 2为左旋 和右旋外螺纹 的铣削 攻 出螺纹 全高 的 5 %。这一 点在 对特 殊材 料 和难加 O
%
1 1 .2 = 69 2 1 = 8
‘ 螺纹底孔半径 。 螺纹公称半径 。 螺纹长度
长 度 L 2 mm: =5 螺距 := mr: P 2 整体 圆柱 螺纹 铣刀直 # = 5 n 32 径 : 2 1 mm, D =4 切削刃长 为 3 mm: 削方式 : 4 铣 顺铣。 42 = 切 削速度 :0 5 mm/ n m_1每齿进给量 f0 1 = .mm。 ()参数计算 1
的螺纹 时,这种情况通 常称 为深孔攻丝。 加工 一个深 孔螺纹,意味 着刀具 与工件之间需长
时要 求丝锥后 角为 4 。 0 。在 加工钛金 属时,在丝锥 上 磨 出大的后角,有利于排 屑。另外,全磨制 丝锥和刃 背铲磨 的丝锥也有利于攻丝。
D、冷 却 液
时间的接触。 同时,在加工过程 中会产生更 多的切 削
42深螺纹加工实例 .
现结合 M3 x2右旋 内螺纹铣削加工实例说 明螺 6 纹铣 削的编程 方法。工 件材料 :5钢 , 4 调质 : 螺纹底 孔 直 径 : i3 .4 D= 38 mm: 纹 直 径 : 0 3 mm: 纹 螺 D=6 螺
西门子宏程序G代码人机对话铣螺纹教程

西门子宏程序G代码人机对话铣螺纹教程引言:铣螺纹是数控铣床的一种常见工作方式。
传统的铣螺纹方法需要通过机械传动来实现,但使用数控铣床可以更加方便快捷地完成该任务。
本教程将介绍使用西门子宏程序、G代码和人机对话方式铣螺纹的具体步骤。
一、西门子宏程序:2.调用宏程序:在主程序中通过M指令调用宏程序。
例如,使用M98指令调用宏程序O9001,可以在主程序中加入“M98P9001”来调用宏程序。
3.参数传递:在调用宏程序时可以传递参数,用于设置螺纹的参数值。
例如,在主程序中可以设置螺纹的直径、螺距、转速等参数,并在宏程序中使用这些参数进行计算。
二、G代码:G代码是数控机床上的一种控制语言,用于告诉机床如何进行运动和加工。
下面以数控铣床为例,介绍使用G代码铣螺纹的步骤。
1.选择加工方式:在G代码中,首先需要选择螺纹的加工方式。
可以使用G33指令进行螺纹攻丝,或使用G76指令进行螺纹插补。
3.编写螺纹指令:编写螺纹相关的G代码指令。
例如,在G33方式下,使用G33XxZzRrPpFf来指定螺纹的参数和加工方式。
在G76方式下,使用G76XxZzQqPpKk,分别指定螺纹的参数和加工方式。
三、人机对话:人机对话是通过数控系统的图形界面进行交互,以完成螺纹加工的设置和操作。
下面以西门子840D数控系统为例,介绍使用人机对话方式铣螺纹的步骤。
1.进入对话界面:在数控系统的主菜单中选择相应的加工功能,进入螺纹加工的对话界面。
可以选择螺纹的类型、规格和参数,以及加工方式等。
2.设置参数:在对话界面中,可以设置螺纹的直径、螺距、起始位置和加工速度等参数。
通过对话界面中的输入框和选项来设置这些参数。
3.开始加工:设置完参数后,点击界面上的“开始”按钮,数控铣床将自动进行螺纹加工。
在加工过程中,可以随时监控加工状态,并根据需要进行调整。
总结:通过本教程,我们介绍了使用西门子宏程序、G代码和人机对话方式铣螺纹的具体步骤。
无论是选择宏程序、G代码还是人机对话,都可以根据实际需求选择最适合的方式。
大规格锯齿螺纹铣削宏程序

图1 锯齿螺纹牙型图
要有两个:①没有标准的螺纹铣刀,只能就地取 材,使用形状相近的刀具。②螺纹的去除余量太 大,要多次分层铣削。靠编程轨迹保证螺纹两侧的 牙型角度。软件编程肯定不行,宏程序也有一定难 度。 (1)自制螺纹铣刀 35°菱形刀片是一种常用
1. 加工方案
S220×25.4-L H属非标螺纹,螺距大,牙槽 深,很难找到合适的刀具,专门定做,价格贵不 说,还要等很长时间,即使做成了刀片,按照传统 的直进方法铣削螺纹,刀片与牙型完全吻合后,切
图2 加工示意图
achine Tools Automation
刀尖中心为刀位点,不使用刀具半径补偿,直接对 螺旋线半径编程。螺纹起点选择在工件以外的安全 高度,螺纹终点有比较宽松的退刀槽空间,起始点 均采用直线进刀和退刀。 (1)粗铣 去除大部分余量。变量设置:
#24=97-30 螺纹最小编程半径 (螺纹牙顶半径-刀具半径) #14=110-30 螺纹最大编程半径 (螺纹牙底半径-刀具半径) #4 =13/4 #9=25.4 #11=127 螺纹半径方向分层进给切入值 螺旋线Z 向距离 螺纹编程长度 (按螺距倍数圆整处理)
M机床自动化
achine Tools Automation
大规格锯齿螺纹铣削宏程序
德州联合石油机械有限公司 (山东 253034) 侯祖刚
锯齿螺纹,一般用于单向受力的传动部件,牙 型为不等腰梯形,前面的一个角度用来承受载荷, 后面的一个角度用来增加牙根强度。大规格的锯齿 螺纹多用于矿山机械,本文以图1为例,介绍35° 菱形刀片分层铣削锯齿螺纹的加工方法和短小精悍 的宏程序模式。
LHYSET(90,-1,90);(建立G54时测量机床Y 值用立头,测量
……;(加工内容) L01(270) G54 LHY ATRANS Z=$TC_DP21[$P_TOOLNO,$P_TOOL] G90 M3 S600 F30 D1 ……;(加工内容) M05 M30
西门子宏程序铣螺纹教程
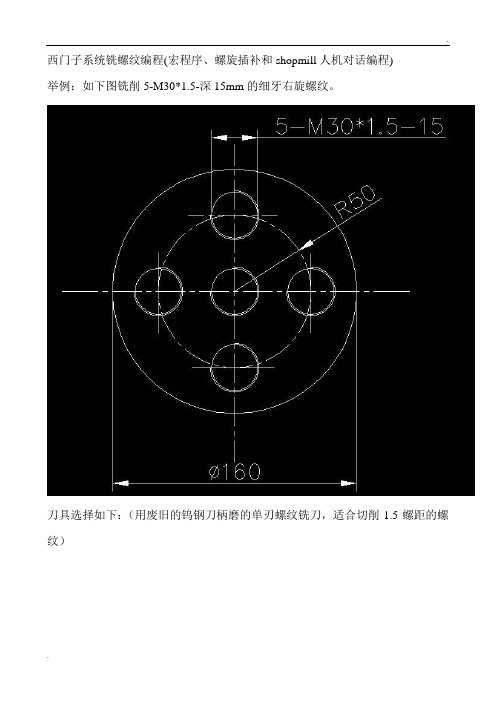
西门子系统铣螺纹编程(宏程序、螺旋插补和shopmill人机对话编程)举例:如下图铣削5-M30*1.5-深15mm的细牙右旋螺纹。
刀具选择如下:(用废旧的钨钢刀柄磨的单刃螺纹铣刀,适合切削1.5螺距的螺纹)工艺分析:三轴联动铣削螺纹,实质是XY平面加工整圆同时,Z轴每加工一个整圆下降一个螺纹,加工时是以螺纹孔的中心轴线作为编程参考点,所以铣削单个螺纹孔时,通常将坐标系原点建立在孔中心,若要铣削多个螺孔,就要试着将坐标系偏移至孔的中心。
这题要铣削5个孔,中间的孔直接可以铣削,R50圆周上的4个等分螺孔,可以借助坐标偏移(西门子系统用TRANS)实现。
M30*1.5的螺纹,事先将螺纹底孔加工到28.5mm,螺纹齿高H=0.974刀具直径经检测,直径为8mm,有效加工孔深为22mm,程序如下:1、宏程序铣削螺纹单个螺纹孔铣削程序G54 G90 G17 G64 坐标系原点建立在孔的中心,底孔事先加工好M03 S3500 (单刃切削,高转速,小吃刀,快进给)G00 Z50.G00 X0 Y0G00 Z3. (安全高度,定位值是螺距的整倍数)R1=0.3 齿高切深赋值NN1: R2=10.25 + R1 (单边14.25,刀半径4,刀具往内偏移到10.25定位)G02 X=R2 Y0 I =R2/2 J0 F300. 以半圆形式切入R3=1.5 螺距PNN2: G02 X=R2 Y0 Z=R3 I= - R2 J0 F3000. 插补螺纹,到Z1.5的高度R3 = R3 - 1.5IF R3 >= - 15.1 GOTOB NN2 螺纹切削孔深15mmG02 X0 Y0 I = - R2/2 J0 F300. 半圆形式切出,刀具到中心G00 Z3. 抬刀到安全高度,前后一致R1 = R1 + 0.2 切削齿高,往X方向增大IF R1 <= 0.91 GOTOB NN1 加工到齿高G01 X0 Y0 F300. 退刀G00 Z100. 抬刀M30本题5-M30*1.5-15的程序主程序:G54 G90 G17 G64 坐标系原点建立在孔的中心,底孔事先加工好M03 S3500 (单刃切削,高转速,小吃刀,快进给)G00 Z50.G00 X0 Y0L1000 P1 调用铣床螺纹的子程序R4 = 0 角度初始赋值NN3: R5 = 50 * COS ( R4 ) X坐标R6 = 50 * SIN ( R4) Y坐标TRANS X=R5 Y=R6 坐标偏移G00 X0 Y0 到偏移之后的原点定位L1000 P1 调用铣螺纹的子程序R4 = R4 + 90 角度增加IF R4 <= 271 GOTOB NN3 加工剩余3孔,要是写360,第一个孔要再加工一次G00 Z100.TRANS 后面不跟任何数值,单独占一段,取消偏移G54 G00 X100. Y100.M30子程序:L1000;G00 X0 Y0G00 Z3. (安全高度,定位值是螺距的整倍数)R1=0.3 齿高切深赋值NN1: R2 =10.25 + R1 (单边14.25,刀半径4,刀具往内偏移到10.25定位)G02 X=R2 Y0 I =R2/2 J0 F300. 以半圆形式切入R3=1.5 螺距PNN2: G02 X=R2 Y0 Z=R3 I= - R2 J0 F3000. 插补螺纹,到Z1.5的高度R3 = R3 - 1.5IF R3 >= - 15.1 GOTOB NN2 螺纹切削孔深15mmG02 X0 Y0 I = - R2/2 J0 F300. 半圆形式切出,刀具到中心G00 Z3. 抬刀到安全高度,前后一致R1 = R1 + 0.2 切削齿高,往X方向增大IF R1 <= 0.91 GOTOB NN1 加工到齿高G01 X0 Y0 F300. 退刀G00 Z10. 抬刀TRANS 后面不跟任何数值,单独占一段,取消偏移M17 返回主程序2、利用螺旋插补加工螺纹单个螺纹孔铣削程序G54 G90 G17 坐标系原点建立在孔的中心,底孔事先加工好M03 S3500 (单刃切削,高转速,小吃刀,快进给)G00 Z50.G00 X0 Y0G00 Z3. (安全高度,定位值是螺距的整倍数)R1=0.3 齿高切深赋值NN1: R2= 10.25 + R1 (单边14.25,刀半径4,刀具往内偏移到10.25定位)G02 X=R2 Y0 I = R2/2 J0 F300. 以半圆形式切入G02 X0 Y0 Z-15 I = - R2 J0 TRUN=11 F3000. 每次1.5,重复11次G02 X0 Y0 I = - R2/2 J0 F300. 半圆形式切出,刀具到中心G00 Z3. 抬刀到安全高度,前后一致R1 = R1 + 0.2 切削齿高,往X方向增大IF R1 <= 0.91 GOTOB NN1 加工到齿高G01 X0 Y0 F300. 退刀G00 Z100. 抬刀M30本题5-M30*1.5-15的程序主程序:G54 G90 G17 坐标系原点建立在孔的中心,底孔事先加工好M03 S3500 (单刃切削,高转速,小吃刀,快进给)G00 Z50.G00 X0 Y0L1000 P1 调用铣床螺纹的子程序R4 = 0 角度初始赋值NN3: R5 = 50 * COS ( R4 ) X坐标R6 = 50 * SIN ( R4 ) Y坐标TRANS X=R5 Y=R6 坐标偏移G00 X0 Y0 到偏移之后的原点定位L1000 P1 调用铣螺纹的子程序R4 = R4 + 90 角度增加IF R4 <= 271 GOTOB NN3加工剩余3个孔,要是写360,第一个孔要再加工一次G00 Z100.TRANS 后面不跟任何数值,单独占一段,取消偏移G54 G00 X100. Y100.M30子程序:L1000;G00 X0 Y0G00 Z3. (安全高度,定位值是螺距的整倍数)R1=0.3 齿高切深赋值NN1: R2 = 10.25 + R1 (单边14.25,刀半径4,刀具往内偏移到10.25定位)G02 X=R2 Y0 I = R2/2 J0 F300. 以半圆形式切入G02 X0 Y0 Z-15 I = - R2 J0 TRUN=11 F3000. 每次1.5,重复11次G90 G02 X0 Y0 I = - R2/2 J0 F300. 半圆形式切出,刀具到中心G00 Z3. 抬刀到安全高度,前后一致R1 = R1 + 0.2 切削齿高,往X方向增大IF R1 <= 0.91 GOTOB NN1 加工到齿高G01 X0 Y0 F300. 退刀G00 Z10. 抬刀TRANS 后面不跟任何数值,单独占一段,取消偏移M17 返回主程序3、利用shopmill人机对话编程ShopMill ——内螺纹铣削说明:abs—绝对值inc—相对值select—选择/切换按“help”(帮助)可以切换视图。
螺纹铣削的宏程序编程加工
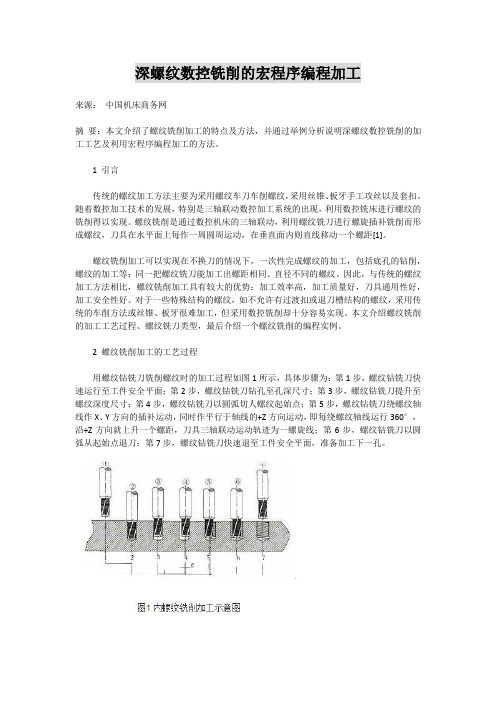
深螺纹数控铣削的宏程序编程加工来源:中国机床商务网摘要:本文介绍了螺纹铣削加工的特点及方法,并通过举例分析说明深螺纹数控铣削的加工工艺及利用宏程序编程加工的方法。
1 引言传统的螺纹加工方法主要为采用螺纹车刀车削螺纹,采用丝锥、板牙手工攻丝以及套扣。
随着数控加工技术的发展,特别是三轴联动数控加工系统的出现,利用数控铣床进行螺纹的铣削得以实现。
螺纹铣削是通过数控机床的三轴联动,利用螺纹铣刀进行螺旋插补铣削而形成螺纹,刀具在水平面上每作一周圆周运动,在垂直面内则直线移动一个螺距[1]。
螺纹铣削加工可以实现在不换刀的情况下,一次性完成螺纹的加工,包括底孔的钻削,螺纹的加工等;同一把螺纹铣刀能加工出螺距相同、直径不同的螺纹。
因此,与传统的螺纹加工方法相比,螺纹铣削加工具有较大的优势:加工效率高,加工质量好,刀具通用性好,加工安全性好。
对于一些特殊结构的螺纹,如不允许有过渡扣或退刀槽结构的螺纹,采用传统的车削方法或丝锥、板牙很难加工,但采用数控铣削却十分容易实现。
本文介绍螺纹铣削的加工工艺过程、螺纹铣刀类型,最后介绍一个螺纹铣削的编程实例。
2 螺纹铣削加工的工艺过程用螺纹钻铣刀铣削螺纹时的加工过程如图1所示,具体步骤为:第1步,螺纹钻铣刀快速运行至工件安全平面;第2步,螺纹钻铣刀钻孔至孔深尺寸;第3步,螺纹钻铣刀提升至螺纹深度尺寸;第4步,螺纹钻铣刀以圆弧切人螺纹起始点;第5步,螺纹钻铣刀绕螺纹轴线作X、Y方向的插补运动,同时作平行于轴线的+Z方向运动,即每绕螺纹轴线运行360°,沿+Z方向就上升一个螺距,刀具三轴联动运动轨迹为一螺旋线;第6步,螺纹钻铣刀以圆弧从起始点退刀;第7步,螺纹钻铣刀快速退至工件安全平面,准备加工下一孔。
3 螺纹铣削轨迹螺纹铣削运动轨迹为一螺旋线,可通过数控机床的三轴联动来实现。
图2为左旋和右旋外螺纹的铣削运动示意图。
与一般轮廓的铣削运动一样,螺纹铣削开始进刀时也可采用1/4圆弧切入或直线切入。
车铣加工中心铣螺纹宏程序的应用

车铣加工中心铣螺纹宏程序的应用
车铣加工中心在加工工件时可以通过编写宏程序来实现一些特殊的功能或加工工艺,
其中包括铣螺纹。
铣螺纹宏程序的应用主要分为两个方面:一是用于加工螺纹孔,即在工件内部加工出
螺纹;二是用于加工螺纹沟,即在工件表面加工出螺纹。
对于加工螺纹孔来说,一般是通过铣攻的方式实现的。
铣攻可分为两种方式:一种是
通过敲击的方式将刀具与工件接触,以产生切削力,从而进行螺纹的加工;另一种是通过
旋转的方式将刀具与工件接触,并沿着螺纹轴向进行移动,以产生切削力,从而进行螺纹
的加工。
在编写螺纹宏程序时,首先需要确定螺纹的参数,包括螺纹的尺寸、螺距、螺旋角等。
然后需要确定螺纹刀具的类型和尺寸,包括螺纹攻和螺纹铣刀。
根据这些参数编写宏程序,实现螺纹的加工。
车铣加工中心铣螺纹宏程序的应用可以实现螺纹孔和螺纹沟的加工,提高加工效率和
质量。
它适用于批量生产和高精度要求的工件加工。
通过编写宏程序,可以减少操作人员
的操作和干预,提高生产自动化水平。
它也提高了对刀具和设备的使用寿命和效率,降低
了加工成本和成品率。
加工中心铣加工螺纹通用宏程序

加工中心通用铣螺纹宏程序之吉白夕凡创作工作原理: 编程原理:G02 Z-2.5 I3.Z-2.5等于螺距为2.5mm优势假设刀具半径为5mm则加工M16的右旋螺纹使用了三轴联动数控铣床或加工中心进行加工螺纹,相对于传统螺纹加工1、如螺距为2的螺纹铣刀可以加工各种公称直径,螺距为2mm的内外螺纹2、采取铣削方式加工螺纹,螺纹的质量比传统方式加工质量高3、采取机夹式刀片刀具,寿命长4、多齿螺纹铣刀加工时,加工速度远超攻丝5、首件通止规检测后,后面的零件加工质量稳定使用方法G65 P1999 X_ Y_ Z_ R_ A_ B_ C_ S_ F_XY 螺纹孔或外螺纹的中心位置X=#24 Y=#25Z 螺纹加工到底部,Z轴的位置(绝对坐标) Z=#26R 快速定位(平安高度)开始切削螺纹的位置 R=#18A 螺纹螺距A=#1B 螺纹公称直径B=#2C 螺纹铣刀的刀具半径C=#3 内螺纹为负数外螺纹加工为正数S 主轴转速F 进给速度,主要用于控制刀具的每齿吃刀量如: G65 p1999 X30 Y30 Z-10 R2 A2 B16 C-5 S2000 F150;在X30y30的位置加工 M16 螺距2 深10的右旋螺纹加工时主轴转速为2000转进给进度为150mm/min宏程序代码O1999;G90G94G17G40;G0X#24Y#25; 快速定位至螺纹中心的X、Y坐标M3S#19; 主轴以设定的速度正转#31=#2*0.5+#3; 计算出刀具偏移量#32=#18-#1; 刀具走螺旋线时,第一次下刀的位置#33=#24-#31; 计算出刀具移动到螺纹起点的位置G0Z#18;刀具快速定位至R点G1X#33F#9; 刀具直线插补至螺旋线的起点,起点位于X的负方向N20 G02Z-#32I#31;以偏移量作为半径,以螺距作为螺旋线Z向下刀量(绝对坐标)IF[#32LE#26]GOTO30; 当前Z向位置大于等于设定Z向底位时,进行跳转#32=#32-#1; Z向的下个螺旋深度目标位置(绝对坐标)GOTO20;N30;IF[#3GT0]THEN #6=#33-#1; 外螺纹,退刀时刀具往X负方向退一个螺距量IF[#3LT0]]THEN #6=#24; 内螺纹,退刀时刀具移动到螺纹中心位置G0X#6G90G0Z#18; 提刀至平安高度M99;。
谈利用宏程序对大螺距螺纹的加工

谈利用宏程序对大螺距螺纹的加工作者:王俊辉来源:《职业·下旬》2012年第01期摘要:在机械中,许多零件都具有大螺距螺纹。
传统加工方法很难保证加工精度和效率,而数控机床宏程序加工,不仅能高速度、高质量地完成加工,而且有能力分析和解决在螺纹车削中出现的各种质量问题。
关键词:数控车床高效率宏程序大螺纹数控编程是数控机床进行零件加工的必要前提,而程序的编写方法直接决定数控加工的效率。
一些典型的零件,依靠传统的指令格式进行编程,已经不能体现出数控加工的优点。
笔者主要介绍螺纹加工指令在应用时,如何与宏程序配合进行使用,解决加工中的一些突出问题。
它们的应用,使一些典型工件高效率的加工变成了现实。
一、大螺距螺纹的加工难点螺纹升角的大小决定了螺距的大小,大螺纹的升角将造成与走刀方向同侧的侧后刀面和工件之间的剧烈摩擦,出现让刀的情况,从而使工件精度达不到要求。
随着螺距增大,加工深度也增大,会出现夹刀现象,造成闷车、断刀等危险情况。
所以,要考虑刀具切削力的大小及刀具的承受能力。
二、传统加工方法用直进法进刀,使切屑垂直于螺纹轴线方向,有利于排出铁屑,而左右切削法因车刀只有一条刀刃参加切削,减小刀具和工件的接触面积,避免多刃同时切削,造成扎刀。
综合而言,就是直进法进刀,然后利用左右借刀,扩大加工面积,保证螺纹牙底和牙顶的尺寸,达到精度合格。
G92螺纹指令的进刀方法为直进法,走刀路线四方循环,左右借刀无法有指令完成,且程序内容过多,编写困难,加工到一定深度容易造成夹刀,轻者刀具损坏,重者工件报废。
G76代码可加工带螺纹退尾的直螺纹和锥螺纹,通过多次螺纹粗车、螺纹精车,完成规定牙高(总切深)的螺纹加工,可实现单侧刀刃螺纹切削,吃刀量逐渐减小,有利于保护刀具,提高螺纹精度。
进刀方法是斜进法。
但是左右借刀量无法控制,加工过程中一旦出现问题,很难控制尺寸,且指令参数较多,如果选择不合适,就会造成加工精度不合格,零件报废。
基于宏程序的多头锯齿形螺纹加工程序应用(完整版)

基于宏程序的多头锯齿形螺纹加工程序应用段树军游娜唐霄姜然王兰(宝鸡石油机械有限责任公司,陕西宝鸡 721002)【摘要】普通的多头锯齿形螺纹加工程序较为冗杂,因其牙型特殊,编制时工作量大,牙深度和宽度都比普通螺纹大很多,所以检查程序繁琐易出错。
根据宏程序的特点,通过对锯齿形螺纹牙型、公差的分析及原理应用,设计出许多简单易行的多头螺纹加工程序。
可以通过改变螺纹参数的变量值,加工出不同直径和螺距的锯齿形螺纹,其灵活性较强也较为方便。
关键词宏程序;锯齿形螺纹加工;多头螺纹锯齿形螺纹是一种非标准螺纹,通常采用成形车刀在卧式车床上进行加工,一般用于承受单向载荷。
螺纹工作面的牙型角较小,非工作面的角度较大,有利于提高螺纹的抗疲劳强度。
目前我国所使用的三菱等数控车床中,对于简单编程的普通螺纹加工来说,可操作性强,但用于复杂的多头锯齿形螺纹加工时,程序编制量大,检查也极其不易,容易造成错误。
而在数控车床加工中,我们可以根据宏程序编程的特点,使用变量、算术和逻辑运算及循环、条件转移等来完成对多头锯齿形螺纹的加工。
1 宏程序简介及锯齿形螺纹的牙型分析1.1 宏程序简介在编程工作中,我们经常把能完成某一功能的一系列指令像子程序那样存入存储器,用一个总指令来代表他们,使用时只需给出这个总指令就能执行其功能。
所存入的这一系列指令称作用户宏程序本体,简称宏程序。
这个总指令称作用户宏程序调用指令。
在编程时,编程员只要记住宏程序而不必记住宏程序。
用户宏程序与普通程序的区别在于:在用户宏程序本体中,能使用变量;可以给变量赋值;变量间可以运算;程序可以跳转。
而普通程序中,只能指定常量,常量之间不能运算,程序只能顺序执行,不能跳转,因此功能只固定的,不能变化。
用户宏功能是用户提高数控机床性能的一种特殊功能。
宏程序本体既可以由机床生产厂提供,也可以由机床用户自己编制。
使用时,先将用户宏主体像子程序一样存入到内存里,然后用子程序调用指令调用。
- 1、下载文档前请自行甄别文档内容的完整性,平台不提供额外的编辑、内容补充、找答案等附加服务。
- 2、"仅部分预览"的文档,不可在线预览部分如存在完整性等问题,可反馈申请退款(可完整预览的文档不适用该条件!)。
- 3、如文档侵犯您的权益,请联系客服反馈,我们会尽快为您处理(人工客服工作时间:9:00-18:30)。
如此,改进后的补偿程序完成。 (收稿日期:20130102)
#26=25.4-1-0.2 45°牙型面一侧分层进给下刀点Z 向坐 标值 (1为1/2刀尖宽度,0.2为精加工余量) #6= TAN45×#4 45°牙型面一侧分层进给下刀点Z 向偏移值 #25=5.4+1+0.2 7°牙型面一侧分层进给结束点Z 向坐标值 (1为1/2刀尖宽度,0.2为精加工余量) #5=TAN7×#4 7°牙型面一侧分层进给结束点-Z 向偏移值 #7=1 N10 #26=#26-#6 #25=#25+#5 #24=#24+#4 #16=#26 N20 #9=25.4 G0X0Y0 Z#16 G01X#24 F1000 N30 G03X#24 Y0 Z[#16-#9] I-#24 J0 F300 #9=#9+#9 IF[#9 LE #11] GOTO 30 IF[#16 EQ #25 ]GOTO 40 #16=#16-#7 IF[#16 LE #25] THEN #16=#25 GOTO20 N40 IF[#24 LE #14] GOTO 10 G0 X0 Y0 Z200 M30 分层切入后的Z 向平移值 G90G54G40S300M03
削面积太大。机床难免会产生强烈的振动,总结数 控车床分层车削大螺距螺纹的经验,能否用同样的 方法铣削螺纹,答案是可以的。数控车床有专门的 螺纹循环指令,进刀和退刀由系统自动控制,分层 车削只要控制好螺纹直径和起始点坐标就可以了。 相比之下,分层铣削就要复杂得多,首先要编程螺 纹的运动轨迹,保证每一圈螺旋线都能够顺滑过 渡,然后一层一层地切入,一步一步的平移,像挖 梯田一样,最终达到螺纹的加工要求。 铣削螺纹有很多先例,螺纹铣刀的规格和型号 也越来越多,但毕竟都是螺距较小的标准螺纹,如 此大的锯齿螺纹,还是第一次遇到,联系了机床厂 家和刀具商,都没有好的方案。摆在面前的问题主
图2 加工示意图
achine Tools Automation
刀尖中心为刀位点,不使用刀具半径补偿,直接对 螺旋线半径编程。螺纹起点选择在工件以外的安全 高度,螺纹终点有比较宽松的退刀槽空间,起始点 均采用直线进刀和退刀。 (1)粗铣 去除大部分余量。变量设置:
#24=97-30 螺纹最小编程半径 (螺纹牙顶半径-刀具半径) #14=110-30 螺纹最大编程半径 (螺纹牙底半径-刀具半径) #4 =13/4 #9=25.4 #11=127 螺纹半径方向分层进给切入值 螺旋线Z 向距离 螺纹编程长度 (按螺距倍数圆整处理)
M机床自动化
achine Tools Automation
大规格锯齿螺纹铣削宏程序
刚
锯齿螺纹,一般用于单向受力的传动部件,牙 型为不等腰梯形,前面的一个角度用来承受载荷, 后面的一个角度用来增加牙根强度。大规格的锯齿 螺纹多用于矿山机械,本文以图1为例,介绍35° 菱形刀片分层铣削锯齿螺纹的加工方法和短小精悍 的宏程序模式。
图1 锯齿螺纹牙型图
要有两个:①没有标准的螺纹铣刀,只能就地取 材,使用形状相近的刀具。②螺纹的去除余量太 大,要多次分层铣削。靠编程轨迹保证螺纹两侧的 牙型角度。软件编程肯定不行,宏程序也有一定难 度。 (1)自制螺纹铣刀 35°菱形刀片是一种常用
1. 加工方案
S220×25.4-L H属非标螺纹,螺距大,牙槽 深,很难找到合适的刀具,专门定做,价格贵不 说,还要等很长时间,即使做成了刀片,按照传统 的直进方法铣削螺纹,刀片与牙型完全吻合后,切
54
2013年 第6期
冷加工
M机床自动化
数控刀片,既可用于车削,也可用于铣削,有人曾 在数控车床上用其进行梯形螺纹的粗加工,并获得 了成功。以此为借鉴,能否用35°菱形刀片铣削 锯齿螺纹呢?带着这个疑问,我们选择强度高、耐 冲击性好的山特维克35°镗刀杆和(VBMT160412 M M1025)菱形刀片,来做一个大胆的试验。从 理论上讲,刀片的安装角度是一侧37°,一侧是 -2°,小于锯齿扣两侧牙型角,R 1.2mm的刀尖圆弧 也明显小于牙底槽宽,两侧切削刃下面的 3°后角, 大于锯齿螺纹的螺旋升角,上述特点,决定了35° 菱形刀片铣削螺纹时不会发生过切和干涉,自己动 手,将直径60mm的35°镗刀杆安装在数控铣床的强 力刀柄上,一把简易的螺纹铣刀就制作完成了。 (2)编程思路 相对于其他刀具路径,螺纹铣 削路线没有太多的选择,本例中的左旋螺纹,适用 自上而下顺铣加工,即主轴正转,刀具沿逆时针 方向做螺旋线插补。编程的焦点是用菱形刀片的 35°刀尖角保证螺纹两侧的7°/45°牙型角(见图 2),粗铣采用分层铣削的方法,考虑到螺纹牙深 13m m,分4层铣削,一次切入3.25m m,刀尖紧贴 45°牙型面一侧进刀至第一层螺纹半径,沿螺旋线 铣削至螺纹长度后,快速返回起始点,半径方向数 值不变,轴向平移进刀,继续执行螺旋线插补,直 到接近7°牙型面,再返回45°牙型面一侧进刀至 第二层螺纹半径,如此循环4次,快速去除大部分 余量,粗铣后,螺纹两侧面已基本接近牙型轮廓, 精铣仍然采用分层铣削的方法,与粗铣不同的是, 精铣只加工螺纹两侧面,以每层0.2m m的深度进 刀,此时可适当提高 主轴转速和进给量, 确保螺纹的牙型角度 和表面粗糙度。程序 的核心在于建立进刀 深度和牙型误差的关 联方程,通过不停地 改变螺旋线的半径值 和起始点位置,来达 到铣削两侧牙型面的目的。
LHYSET(90,-1,90);(建立G54时测量机床Y 值用立头,测量
……;(加工内容) L01(270) G54 LHY ATRANS Z=$TC_DP21[$P_TOOLNO,$P_TOOL] G90 M3 S600 F30 D1 ……;(加工内容) M05 M30
X 和Z 用卧头转到90°)