5s整改方案车间图片doc
100张工厂车间5S改善案例图

100张工厂车间5S改善案例图,张张经典!
现在很多企业在推进5s相关工作,过程中产生了很多优秀的5s改善的案例,这
些案例对于其他也是很有很有借鉴意义所有整理出很不错 5s图片供给大家学习和
借鉴。
希望对大家的5s工作有很大的帮助。
6s管理
在5s活动的基础上,有的人提出了6s管理活动,记在“整理、整顿、清扫、清洁、素养”的基础上增加了“自检”,即每日下班前作自我反省与检讨,目的是1.总结经
验与不足 2.判定一至两种改进措施 3.培养自觉性、韧性和耐心,加强员工安全教育,每时每刻都有安全第一观念,防范于未然。
8S管理
8S就是整理(SEIRI)、整顿(SEITON)、清扫(SEISO)、清洁(SETKETSU)、素养(SHITSUKE)、安全(SAFETY)、节约(SAVE)、学习(STUDY)八个项目,因其古罗马发音均以“S”开头,简称为8S。
8s管理法的目的,是使企业在现场
管理的基础上,通过创建学习型组织不断提升企业文化的素养,消除安全隐患、节约成本和时间。
使企业在激烈的竞争中,永远立于不败之地。
13S管理
随着管理的不断完善和精细,5S管理的内容也不断地被扩充,已经逐步发展到
13S,即在5S的基础上增加安全、节约、服务、满意、坚持、共享、效率、学习。
其实,无论怎么变化,5S其实是一种管理思想和文化。
1
“定位划线“ good case
2
“定位划线“ good case
3
“生产区域“ good case
4
“办公区域“ good case
“仓库区域“ good case
5
“其他区域“ good case
=。
5S改善案例(经典作品)

检验区和作业区分开,慎防混料
文件未加以分类定置,易丢失
有了位置线,放错也不容易
车间规划清晰,一尘不染
物料置于车间通道,阻碍物流,影响效率
在制物料未标示清楚,易使产线弄错
整洁车间现场一览
车间整洁,员工战斗力高
流动红旗简单有效,你也可试
2019/3/22
26/46
2019/3/22
态度 习惯
2019/3/22
行为 人格
命运
45/46
想改变自己命运的时候,就从态度开始。
谢谢大家!
2019/3/22
46/46
27/46
2019/3/22
28/46
2019/3/22
29/46
222
31/46
2019/3/22
32/46
2019/3/22
33/46
2019/3/22
34/46
2019/3/22
35/46
2019/3/22
36/46
不好
2019/3/22
37/46
好
◎形迹定位管理 自 己 制 作
2019/3/22
38/46
2019/3/22
39/46
2019/3/22
40/46
2019/3/22
41/46
2019/3/22
42/46
2019/3/22
43/46
2019/3/22
44/46
安冈正笃
名言-----日本汉学大师
心态变则态度变; 态度变则习惯跟着变; 习惯变则人格随之变; 人格一变则人生也就变。
5S的实例图片
2019/3/22
1/46
干部自已未遵守,怎能要求员工遵守
5S整理整顿标准(图例)

页脚内容15S 整理整顿标准制造中心5S 专项工作实施过程中发现各分厂在整理整顿存在不同的标准,不利于工厂统一标准,现根据工厂实际,特制定5S 整理整顿标准,如下所示:一、 划线标准1.主通道2. 物料暂存区3. 通道转弯处倒角m②①4.工装架或周转车定位工装架或周转车放置必须在定位线以内(定位角或定位框),横平竖直,不能歪斜。
(1)定位角5c(2) 定位框页脚内容2页脚内容3风扇、花盆,焊枪工装使用圆型标识5. 不合格物料区,欠产尾数区(1)总装线根据实际情况设置不合格物料区及欠产尾数区,区域使用红色警戒色,欠产尾数半成品及物料只能在区隔内放置,并做好标识。
黄色1CM5cm(2)不合格物料必须有明确的放置位置,并及时清退,不能随便摆放。
6.设备、消防设施使用警戒线页脚内容47.生产区与线边物料区必须使用黄线分割区分。
二、物料存放标准1.物料必须定位置(物料位置便于员工拿取,避免弯腰,180°转身)使用工装(周转箱)或周转车存放,不得把物料或周转箱直接堆放在地板上。
2.岗位上只允许放置当前作业的物料,上一单作业的物料必须清理出生产区置于欠产尾数区标识存放。
3.转机时必须采用双箱的方法将多余物料清走;页脚内容5页脚内容64、有物料就必须有标识,同一种容器不允许装有两种以上物料。
4. 总装线根据实际设置螺钉架分类标识存放螺钉。
转产标识小件物料每车一作业5.海绵件需要制作海绵存放架,按作业号分类标识,小单海绵件使用胶箱存放。
6.损坏的工具,快速接头要放到待维修胶箱标识。
三、工具存放标准工具柜及返修线的工具必须定位,不能随意摆放;页脚内容7页脚内容8四、 工装架存放标准1、参观路线周围物料摆放整齐有序,道路通畅,地面干净整洁;2、工位架上返回处不能放置满箱物料,只能存放空胶箱;页脚内容93、工装物料摆放整齐,通道边工装物料摆放不压黄线,摆成一条直线。
4、垃圾桶统一标准,边缘上无牛皮癣,有工装必有定位并按定位摆放。
一车间现场5S改善报告(汇报)ppt课件
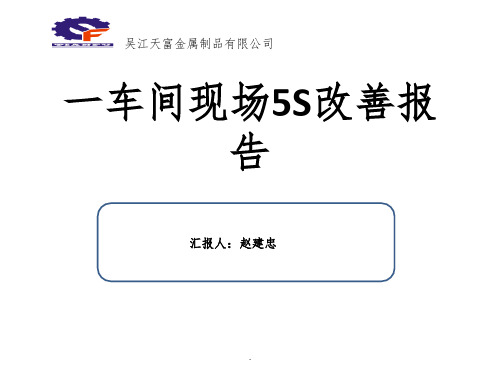
识 负责任。 3、清理现场的呆滞物料、闲置模具。------腾出了多余的空间。 4、对车间的工位器具标记、标识。 5、对一车间的成品和半成品、物料周转区域划分标记、标识。 6、对车间的共用器具划定区域,并标识。 7、确保通道畅通无阻。
、
.
吴江天富金属制品有限公司
一车间现状改善前和改善后对比
改善前:散乱,没有标记、标识
2、摆放的物料与标识牌一致。
3、物料摆放整齐。
4、合格品与不合格品区分,且有标识。
现场标识
1、标签、标识牌与被示物品、区域. 一致。
2、标识清楚完整、无破损。
吴江天富金属制品有限公司
谢谢!!
.
生产现场改善后的状况
.
吴江天富金属制品有限公司
生产现场改善后的状况
.
吴江天富金属制品有限公司
生产现场改善后的状况
5S整理整顿标准(图例)

5S 整理整顿标准
现根据公司实际,特制定5S 整理整顿标准,如下所示: 一、 划线标准
1. 主通道
2. 物料暂存区
3. 通道转弯处倒角
②
①
4. 工具架或周转车定位
工具架或周转车放置必须在定位线以内(定位角或定位框),横平竖直,不能歪斜。
(1)定位角
(2) 定位框
风扇、花盆,焊枪工装使用圆型标识
更换下来的废品物料区(损坏的工具
)
间隙
1CM
5. 设备、消防设施使用警戒线
二、 工具存放标准
工具柜的工具必须定位,不能随意摆放;
垃圾桶统一标准,边缘上无牛皮癣,有工装必有定位并按定位摆放。
茶杯架整洁干净,无杂物,茶杯摆放整齐并标识清楚。
5S现场管理标准图
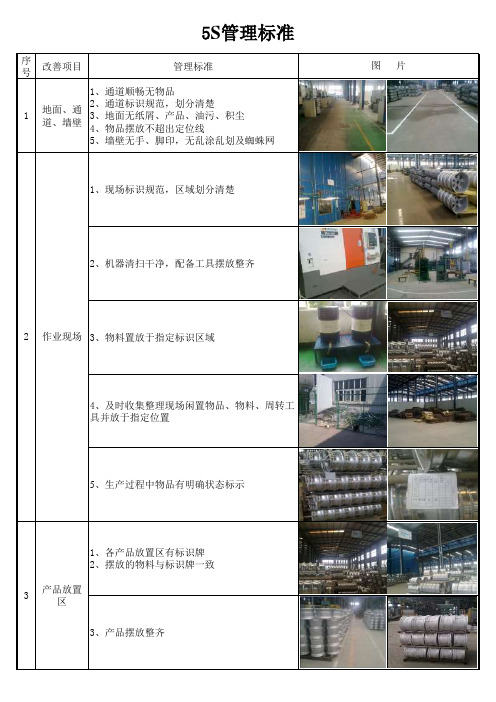
编 制:
审核:
批 准:
5S管理标准
序 号
改善项目
管理标准
1、通道顺畅道标识规范,划分清楚 3、地面无纸屑、产品、油污、积尘 4、物品摆放不超出定位线
5、墙壁无手、脚印,无乱涂乱划及蜘蛛网
1、现场标识规范,区域划分清楚
2、机器清扫干净,配备工具摆放整齐
2 作业现场 3、物料置放于指定标识区域
4、仓库有按原材料、包材、成品、不合格、待 检品等进行规划
9 其 它 1、茶杯放置整齐
图片
序 号
改善项目
5S管理标准
管理标准
2、易燃、有毒物品放置在特定场所,专人负责 管理
3、清洁工具放于规定位置 4、垃圾摆放整齐、定期清理
9 其 它 5、生产车间有“5S”责任区域划分
图片
6、液压叉车使用完毕后放于规定位置整齐放置
3、机器设备零件擦拭干净并按时点检与保养
4
机器、设备 配备、工具
4、机器设备标明保养责任人
5、机台上无杂物、无锈蚀等
1、消防器材随时保持使用状态,并标识显明 2、定期检验维护,专人负责管理 3、灭火器材前方无障碍物
5
安全与消 防设施
4、危险之场所有警告标示
6标
识
1、标签、标识牌与被示物品、区域一致 2、标识清楚完整、无破损
图片
5S管理标准
序 号
改善项目
管理标准
1、穿着规定厂服,保持仪容清爽 2、工作认真,不闲谈、不怠慢、不打瞌睡工作 认真专心 3、谈吐礼貌
7 人 员 4、按规定作业程序、标准作业
5、生产时有戴手套或防护安全工具操作
8
1、仓库有平面标识图及物品存放区域位置标示
2、存放的物品与区域及标示牌一致 仓库
整理5s标准化管理图片车间
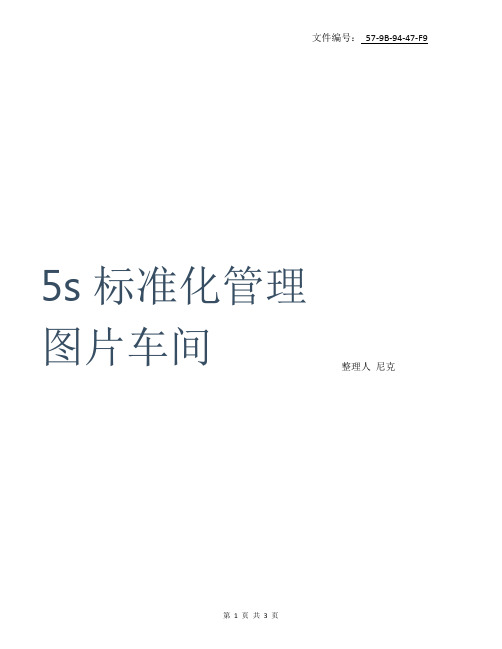
5s标准化管理
图片车间
整理人尼克
5S现场管理
整理
(区分要与不要的物品,现场只保留必需的物品)
整顿
(必需品依规定定位、定方法摆放整齐有序,明确标示)
清扫
(清除现场内的脏污、清除作业区域的物料垃圾)
清洁
(将整理、整顿、清扫实施的做法制度化、规范化,维持其成果)
素养
(人人按章操作、依规行事,养成良好的习惯,成为有教养的人)
整理丨尼克
本文档信息来自于网络,如您发现内容不准确或不完善,欢迎您联系我修正;如您发现内容涉嫌侵权,请与我们联系,我们将按照相关法律规定及时处理。
1、5S改善图片1
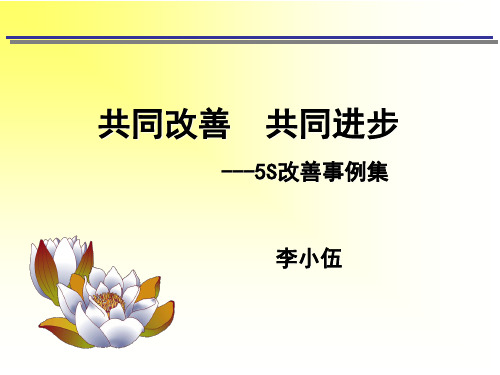
5改善事例
事例⑤:水管保护的改善
改善前 改善后
改善前: 1、气管(水管?)表面护棉脏、 破,影响美观且存在安全。
2、容易被推送物品的推车,叉车
碰撞。 改善后: 1、重行更换新的保护棉 2、使用铁栏将该区域围起来,防 止推车、叉车碰撞。
<效果>
保护棉美观维持管理可
事例⑥:小刀的改善
改善前 改善后
改善前: 小刀使用作业者名进行管理,因 人员更换频率高,管理困难。 改善后: 使用成形机编号管理 <效果> 管理简单化
整顿事例—治· 工具
P5
工具凌乱、堆积摆放,使用时查找 困难,影响功工作效率,不能判断 工具的正常· 异常。
对工具车实施整理、整顿。能一 眼判断工具数量、放置状态的正 常· 异常。
整顿事例—治· 工具
P6
工具随意放置,无数量、定位管理。 不能判断工具的正常· 异常。
对工具实施形迹整顿。能一眼判 断工具数量、放置状态的正常。
5改善事例
事例⑩:油柜的改善 改善前 第一次改善
问题概述:油类标识不清晰,油瓶没盖,摆放混乱,无法区分适 用的油瓶
油品标识及油瓶已用颜色或形状区分,但油瓶无量的管理
第二次改善
方便拿取和管理
5改善事例
各种改善事例
改善前
改善后
手套回收改善
作业台小刀放置改善
作业台简化改善
手套回收基准明确改善
作业台垃圾桶放置改善
作业区域包材限高改善及定位改善
5改善事例
各种改善事例
扳手形状定位改善
工具柜物品放置标示改善
垃圾分类改善
安全帽3定管理
安全管理规定明确
成品放置标示改善
防止架子移动的对策
车间5S改善计划PPT课件

2、其他收益:
项目
改善前
测样员工工作量减半 测样员要到处找样品
新员工工作时不会出错, 培训新人要花费很大
也有助于新人的学习
的人力,时力,
员工有个好的工作环境
材料不洒落出来没有 那么大的气味
改善后
直接可以去样品架子拿样品
我们的标识可以让新员工很快 的记住所有的管道用途
车间不会整体都是化学物பைடு நூலகம்的 味道,为员工的身心健康有了
很大的帮助
改善效果
良好 好
较好
5
四、推进计划
项目名称
开始时 间
结束时 间
状态
难度分 自评
难度分 上级评
分
难度系 数
性质
负责人
车间5S改 善
7月
7月 已完成 4
3
1
绩效 刘志向
6
五、改善效果确认
7
• 自7月份5S改善计划实施以来,我们部门保安发现问题,经 理发现问题,主任发现问题都有了明显的下降,都同比下 降43%
改善后
改善前问题:
1、之前处理固化剂需要两个人才能完成 2、易洒落,影响车间生产环境
改善后效果:
1、现在每次处理固化剂只需要一个人就可以轻松完 成 2、而且不会洒落,省时省力
3
二、改善方案
方案:二
改善前
改善后
改善前问题:
1、所有的管道,台面都没有标识 2、材料随意乱放,
改善后效果:
1、改善后所有的管道都知道其作用,员工的工作效 率大大提高 2、车间里面整洁美观
项目改善前改善后改善效果测样员工工作量减半测样员要到处找样品直接可以去样品架子拿样品良好新员工工作时不会出错也有助于新人的学习培训新人要花费很大的人力时力我们的标识可以让新员工很快的记住所有的管道用途员工有个好的工作环境材料不洒落出来没有那么大的气味车间不会整体都是化学物品的味道为员工的身心健康有了很大的帮助较好四推进计划项目名称开始时状态难度分难度分上级评性质负责人车间5s改绩效刘志向自7月份5s改善计划实施以来我们部门保安发现问题经理发现问题主任发现问题都有了明显的下降都同比下降43员工看到车间工作环境的改变工作的积极性也有了很大的提高
5S现场管理整改前后对比图
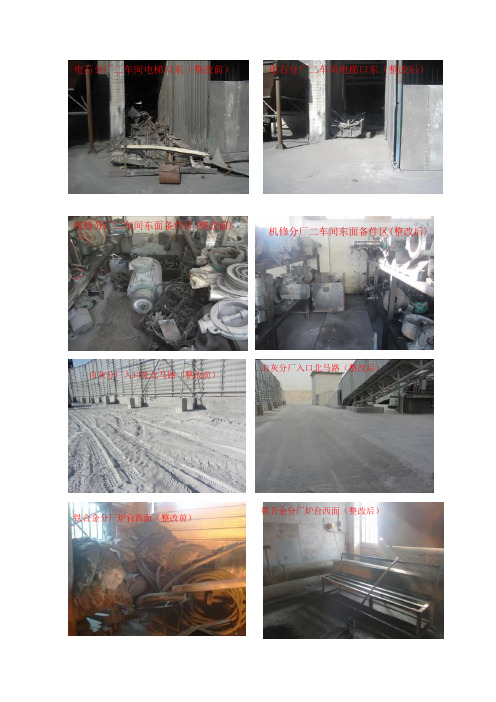
机修分厂二车间东面备件区(整改前)
机修分厂二车间东面备件区(整改后)白灰分厂入口处北马路(整改前)
白灰分厂入口北马路(整改后)
铁合金分厂炉台西面(整改前)铁合金分厂炉台西面(整改后)
电石分厂二车间电梯口东(整改前)电石分厂二车间电梯口东(整改后)
电石分厂原料车间煤泥池西侧(整改前)电石分厂原料车间煤泥池西侧(整改后)
电石分厂三车间西侧(整改前)
电石分厂三车间西侧(已整改)
电石二车间成品库周围(整改前)电石分厂二车间成品库周围(整改后)电石分厂一车间后小院。
- 1、下载文档前请自行甄别文档内容的完整性,平台不提供额外的编辑、内容补充、找答案等附加服务。
- 2、"仅部分预览"的文档,不可在线预览部分如存在完整性等问题,可反馈申请退款(可完整预览的文档不适用该条件!)。
- 3、如文档侵犯您的权益,请联系客服反馈,我们会尽快为您处理(人工客服工作时间:9:00-18:30)。
5s整改方案车间图片
篇一:5S整理整顿标准(图例)
5S整理整顿标准
制造中心5S专项工作实施过程中发现各分厂在整理整顿存在不同的标准,不利于工厂统一标准,现根据工厂实际,特制定5S整理整顿标准,如下所示:一、划线标准
1. 主通道
2. 物料暂存区
3. 通道转弯处倒角
4. 工装架或周转车定位
工装架或周转车放置必须在定位线以内(定位角或定位框),横平竖直,不能歪斜。
(1)定位角
(2) 定位框
风扇、花盆,焊枪工装使用圆型标识
隙
5. 不合格物料区,欠产尾数区
(1)总装线根据实际情况设置不合格物料区及欠产尾数区,区域使用红色警戒色,欠产尾数半成品及物料只能在区隔内放置,并做好标识。
(2)不合格物料必须有明确的放置位置,并及时清退,不能随便摆放。
6. 设备、消防设施使用警戒线
7. 生产区与线边物料区必须使用黄线分割区分。
二、物料存放标准
1. 物料必须定位置(物料位置便于员工拿取,避免弯腰,180°转身)使用工装(周转箱)
或周转车存放,不得把物料或周转箱直接堆放在地板上。
2. 岗位上只允许放置当前作业的物料,上一单作业的物料必须清理出生产区置于欠产尾数区
标识存放。
3. 转机时必须采用双箱的方法将多余物料清走;
转产标识
小件物料每车一作业
4、有物料就必须有标识,同一种容器不允许装有两种以上物料。
4. 总装线根据实际设置螺钉架分类标识存放螺钉。
5. 海绵件需要制作海绵存放架,按作业号分类标识,小单海绵件使用胶箱存放。
6. 损坏的工具,快速接头要放到待维修胶箱标识。
三、工具存放标准
工具柜及返修线的工具必须定位,不能随意摆放;
篇二:生产现场管理整改报告
生产现场管理整改报告
一、现场“5S”改善方案及措施
1. 物料摆放
①从货仓到生产现场,不同机种的物料按机种归类分别存放,并在外包装箱上标识。
②生产每个机种之前将前一个机种的物料进行清理,(包括未成型物料、不良品、已加工物料)保证前一个机种的物料彻底清完后再生产另一个机种。
③对于二极管等小体积的物料经成型并经检验合格后按原包装的数量放回原包装盒。
④对于电容等体积稍大的元件经加工后用静电胶箱装好,并在外箱上贴上相对应的标识。
标识内容包括:机种、料号、插件位置、数量。
⑤插件拉生产过程中各种物料放置于静电胶盆中,保证拉台上没有散乱元件,不良品分类存放。
⑥生产过程中堆机用静电隔板单层摆放,超过三层高度时摆放于静电胶箱内,并贴上标识注明机种、状态、数量。
⑦剪脚工位将PCB板放置于玻璃罩内再进行作业,后焊拉整条产线定时清扫台面的脚渣。
⑧各工位操作过程中进行单拼板作业,保证不出现多拼板重叠一起作业。
二、仪器设备的保养与点检
①正在使用的各种设备注明其使用状态及保证其清
洁度。
②对于波峰焊及烙铁每天进行点检有效地控制其异常状态。
③加强防静电测试。
三、有效文件的应用及审核
①对每个生产机种的SOP要求与生产当中实际状况进行核对,不相符之处及时进行分析及更正。
②对每工位按照SOP要求进行培训,并严格遵照作业指导书作业。
四、重点工位的培训
① QC工位经过专业人员的培训合格后方能上岗作业,培训内容包括电子元件知识、BOM单核对、
PCBA的检验标准及规范。
②测试工位经过专业人员的培训合格后方能上岗作业,培训内容包括负载仪的使用、各机种的
测试参数要求、测试状态的确认。
五、修理工位的整理
①修理工位设置在专用的修理区域,负责修理与产线生产机种不同的机种。
②在线修理负责修理产线所生产的机种功能不良品。
③
修理工位物料按机种分类存放,不良品注明不良状态。
篇三:车间改善措施报告
车间整改改善措施报告
经过2天的车间生产实践及对日常对产品作业流程的观察,我本人初步总结出现在生产车间的问题点以及对车间后续规范化管理提出几点见解。
一问题点:
1. 产品生产工艺及流程比较混乱,几乎无人执行工艺规范及作业标准。
2. 作业人员大部分技术技能欠缺或技能单一,无工艺规范化常识。
3. 生产环节流通不顺利,较大影响生产作业效率,没有使整个现有车间的
人员配置效率达到较理想化。
4. 车间缺乏有效管理措施,未建立基本的人员管理办法及考核制度,作业
人员岗位职责概念模糊不清。
5. 车间环境亟待整理整顿,清除不必要的废弃物品,保持整个车间和生产
线的清洁,有利于保障产品的品质和提升生产效率。
6、生产车间原本会有目视管理看板,主要是监控生产动态效率提升和分析达成率等信息,但我们车间没有这样的
管理看板,有一些看板但没有及时
填写信息。
7、缺乏生产过程追溯机制,加工中的零部件半成品没有标示卡,品质对不合格品、特采品、合格品没有使用明确的标示卡来督导监督车间生产过程中的活动。
对不合格品没有进行有效的汇总进行分析,后推动责任部门进行有效的改进。
二改善计划及措施:
1. 大力推动公司生产运作流程,包括从生产订单下达,来料检验,仓库物
料管控措施,仓库根据订单配备所需物料,车间领取订单物料及管控措施,成品入仓流程等。
2. 生产车间务必要执行好现有产品生产规范工艺要求,不得私自更改,或
不按作业要求进行私自作业现象发生。
设置关键岗位工艺管控办法。
有利于对产品品质进行管控,以减少产品品质不良及客户投诉率,并可初步设定生产合格率目标,减少无谓的返工和人力浪费,从而提升产品品质及生产效率。
3. 人员岗位职责的明确化,建立责任机制和追踪机制,有利于岗位人员的
责任心的提升,并实施奖罚制度,不能做多做少一个样,
做好做坏一个样,做与不做一个样,提升员工的积极性和职责感。
还建议员工最好是固定一个工作岗位,不要轻易的改变工作岗位,让他们熟悉自己的岗位要求很重要,有利于保证质量的情况提升产能。
4. 可实现每日早会制度,管理人员总结前日生产时发现的品质,车间及生
产过程等发生问题,避免后续生产中再次发生,有利于对员工进行品质和责任教育。
明确当日生产计划任务和目标,使员工能分清轻重缓急,合理安排当日生产计划。
5. 制定车间5S(整理整顿清洁清扫素养)管理机制,管理人员实施推
动。
已达到整个车间物品摆放整齐,流水线物料摆放规范,拉线清洁干净等。
既能使作业人员有个舒适的生产环境,对公司有比较高的归属感,
从而使员工能安心工作,和公司一起发展。
又能有效减少产品不良率和提升生产效率。
试想一个物料摆放凌乱,现场无法分清好料和待料,流水线作业工具混乱摆放的车间,员工每次作业是都必须花大力气寻找和鉴别物料及工具,怎样能确保产品的品质,只能浪费更多的人力和物力。
由此可见5S制度的关键性和重要性。
6. 可根据实际情况初步划分产品生产作业区域,便于
整个生产流程的安全
管控,达到有利于安全生产的环境。
7. 车间需要制作印刷一批产品加工工序卡,以便追踪零部件加工完成状
况,品质部也需要印刷一批分为合格、不良品、特采标签
8. 为了有效管控品质质量,结合现实状况,公司需要在原有的基础上加大
品质巡检,半成品入仓检验的力度,这样可以确保批量合格率。
以上是本人在这2天的工作实践所发现及结合目前公司实际状况对后续车间管理的个人意见,仅请上级参考。
报告人:孙小槟。