来料异常通知单
供应商来料品质改善通知单

*******************有限公司
供应商来料问题改善通知单
TO(致):DATE(日期):
ATTN(收件人):FROM(由):
1.****填写:
机型:品名:收料单号:
来料日期:来料数量:检验报告NO.:
问题描述:
专案人:
主管:
2.供应商回复:
1. 是否有仓存:□没有,□有,数量pcs.,处理方法
2. 是否正在生产中:□不是,□是,数量pcs.,处理方法
3. 是否有货品在送货途中没有,有数量件
4.0 是否需要派代表来访华露芬
如需要请填写
姓名职位:来访日期:
带回坏品数量负责人签名:
4.1 坏品原因分析
属哪种问题
设计问题生产工艺问题原材料供应商问题其它4.2 为什么坏品可通过贵厂IPQC和QA检验?
4.3 改善对策及可执行日期?
表单编号: VB/BD-7.5-16。
MRB作业指引(基础性通用)-干货

MRB作业指引文件编号:版本:A/0 MRB作业指引制定部门: ****部制订日期: ***年**月**日正文页数: 4页附件页数: 2页文件修订履历1.目的:根据《不合格品处理程序》的定义,针对重大异常/或者涉及到需要过程评估、相关部门评审的不符合事件/或者涉及到PMC紧急需求的事件而成立MRB小组,并定义MRB小组会议方式对相关事件进行及时、有效的处理,使做出合理的、可行的、不影响客户需求的最佳决定。
2.范围:可适用于原材料来料、仓库物料/半成品/成品、客户投诉/反馈事件/售后事件的处理,以及其他整个生产运营过程涉及到需要各相关部门共同评估、评审的事件。
3.定义:3.1 MRB: Material Review Board 材料审查委员会3.2 8D: 8Discipline Working Sheet 8D Report3.3 MRB小组成员组成:由PMC、采购、业务、生产、工程、品质、研发、仓储组成,并由组织者负责召集相关部门进行MRB会议。
4.职责:4.1.IQC: 负责原材料进料抽样检查和品质标准判定,标识隔离不符合品;物料重大异常/或涉及到过程评估、各部门评审的异常事件的提报;4.2.SQE: 负责供应商原材料质量问题的处理推进,反馈成效追踪及必要时对厂商稽查;供应商原材料质量问题导致产线额外工时的确认,并最终确认工时的正确性,并附上工时记录表于MRB报告/或者来料物料异常通知单,进而跟进工时转嫁和妥当处理;组织生产过程因物料质量问题导致的重大异常的MRB会议召集,协助PQE推进受影响产品的应急围堵处理;4.3.IPQC:负责制程中原材料/半成品/成品异常CAR处理推进和标识隔离不符合品,反馈成效追踪;搜集详细信息并提报过程重大异常/或涉及到过程评估、各部门评审的异常事件于组长及以上;4.4.FQC/OQC: 负责成品抽样检查和品质标准判定工作过程异常品的CAR和标识隔离不符合品,成效追踪和反馈,搜集详细信息并提报FQC/OQC处重大异常/或涉及到过程评估、各部门评审的异常事件于组长及以上;4.5.PQE:负责过程中重大异常/或涉及到过程评估、各部门评审的异常事件的处理推进,主导非原材料质量问题导致的MRB会议,并协助因原材料质量问题导致的MRB会议的正常进行和妥善处理;对于异常成品出货部分,协同工程/研发进行成品可靠性、风险评估等工作;督促MRB的有效执行;4.6.CQE:负责客户投诉/反馈事件/售后事件的MRB召开,具体处理根据客诉流程执行(ER-QP-04 客户投诉处理程序);4.7.PE:负责重大异常/或者涉及到需要过程评估、相关部门评审的不符合事件的过程评估(工艺角度进行评估),并协助研发进行产品可靠性评估;对于异常成品出货部分,协同品质/研发进行成品可靠性、风险评估等工作;主导应急围堵措施、纠正和预防措施的制定;当锁定并明确为原材料问题时,转交给到SQE;由SQE推进供应商处理,并反馈供应商8D结果;4.8.研发:负责重大异常/或者涉及到需要过程评估、相关部门评审的不符合事件的产品评估(可靠性、风险性角度进行评估)。
不合格和纠正措施程序(含表格)

不合格和纠正措施管理程序(ISO9001-2015)1.目的:确保不合格发生后能及时调查原因,采取有效纠正措施,防止再发生同样的问题。
2.范围:本公司所采取的纠正措施及改善统计技术的运用。
3.权责:当以下情况发生时按下表执行纠正措施:4.定义:(无)5.作业流程5.1.1以上质量异常发生时,应由以上表中规定的部门填写适合表单送相关部门。
5.1.2供方的纠正措施:若供方来料不良,则由IQC填写《进料异常通知单》,采购部联络供方,由其分析原因并完成纠正措施;品质部应予以跟踪、确认。
5.1.3 本厂内部的纠正措施:a)本厂内部制程出现严重不良/不良连续发生或成品抽检不合格时,,由品质部开出《巡回检查异常联络书》或《品质异常处理单》交责任部门分析原因并采取纠正措施,品质部应予以跟踪、确认。
b)当质量/环境目标或环境绩效出现不符合时,管理部发出《纠正措施报告》,并由管理部进行跟踪确认直至问题改善。
c)内审发现不符合项依《内部审核控制程序》执行。
d)管理评审决议事项依《管理评审控制程序》执行。
e)客户满意度测量发现客户不满意时依《客户满意度测量控制程序》执行。
5.1.4客户投诉、退货之纠正状况:a)客户投诉/退货之纠正,由品质部负责组织相关部门填写《客户投诉处理单》,相关责任部门采取纠正措施直至问题改善,待品质部验证合格后将完成情况回复客户以取得客户满意。
具体参照《客户投诉控制程序》执行。
5.1.7 改善效果与确认:a)由(表一)所列权责部门依责任部门拟订措施及预估完成日期追踪。
b)若未改善,应要求重新分析原因及拟订对策,直到完全纠正。
5.1.5需要时,更新策划期间确定的风险和机遇,具体参见《风险管理程序》。
5.1.6如有必要,经确认有效的纠正措施应修订于相关的体系文件之中,具体的修订作业遵照《文件控制程序》执行。
5.1.7品质部或管理部应将所有纠正措施汇总登记在《纠正措施一览表》。
纠正措施实施情况应提交管理评审会议予以效果检讨、确认其合理性与有效性。
来料检验规范

(1)包装、标签、数量、型号等相目的核对;
(2)产品规格(外观、结构、装配、电气性能、安全规定)作选择性或必要性之检验。
备注:
1.若客户有特殊要求,则按客户要求检验;
2.若产品出货到有ROHS要求的国家或地区,其来料产品要求能满足ROHS要求
E) 料件不要忘记做试装检验。
附:
IQC作业流程图:参考来讲检验控制程序
用到表格:《特采申请单》
《来料送检通知单》
《来料品质异常联络单》
《Байду номын сангаас料检验记录》
2. 品质部门(IQC)依据抽样计划,予以检验判定,并将检测数据记录在《来料检验记录》表上,当物料判定不合格时送部门主管人员审核裁定。
3. 品质部门(IQC)依据抽样计划判定合格时,需在物料外包装的适当位置放上合格标识牌,在《检验、入库单》上签字,由仓管人员办理入库手续。
4. 品质部门(IQC)依据抽样计划判定不合格时,须填写《来料品质异常联络单》,交品管主管审核裁定。
B) 由本公司委托外部检验机构进行检验,费用由供应商承担或依双方约定分摊。
C) 本公司视同合格物料之接受,所导致之任何损失或影响均由该物料之供应商承担。
12. 其他规定:
A) IQC应规定每月汇总进料检验记录,做成月报。
B)品质部IQC做成月报除品质了解、自存外,应送采购部了解,必要时应上报总经理。
4.3抽样计划:
4.3.1依据GB/T2828采用正常检查一次抽样方案
4.3.2检验水平:特殊检查水平S-4
合格质量水平(AQL):A=1.5B=0.4 C=0.65;
4.4检验判定条件:
来料检验规范

来料检验规范
1 检验员接到来料,根据《采购通知单》清点核对供应商编号、物料名称、规格及数量后,物料
移至待检区域。
2 根据品质抽样标准,正常检验:参见具体的检验标准(特殊情况以客户的确认检验标准为准),
按照作业指导书的要求对来料进行检验,并记录于“检验报告”内。
如果有特殊要求的进料,执行全检。
3 检验合格,盖合格章,办理入仓手续;
4 检验不合格马上通知采购,采购根据物料急需程度,协调相关部门共同讨论处理,具体方式有:
A.挑选(品质部提供标准样品,挑选后再检,直至合格);
B.特采;
C.加工;
D.拒收。
来料检验记录
1、检验员须及时认真填写“检验报告”,经品质部主管审核后交采购存档。
2、对于检验结果不合格并判定为挑选时,执行者需记录挑选的结果。
3、来料检验不合格时,检验员及时督促采购通知供应商要求改善,同时在品质记录中作
相应记录,并按《不合格品处理程序》执行。
4、检验员每月应对各供应商供货合格率、以及不良原因进行分析总结,并以书面报告形
式提交给采购以作为对供应商进行评估的依据,具体参照“供应商管理程序”。
5、紧急放行
若有因生产急需来不及验证的物料:
a)由生产部主管提出书面申请,经总经理/管理者代表批准。
b)申请原因须写明清楚,包括具体的放行数量、交货期、生产日期、供应商编码。
c)紧急放行的物料须作相应标识,当发现不符合规定要求时,能立即追回或更换。
模具异常处理单
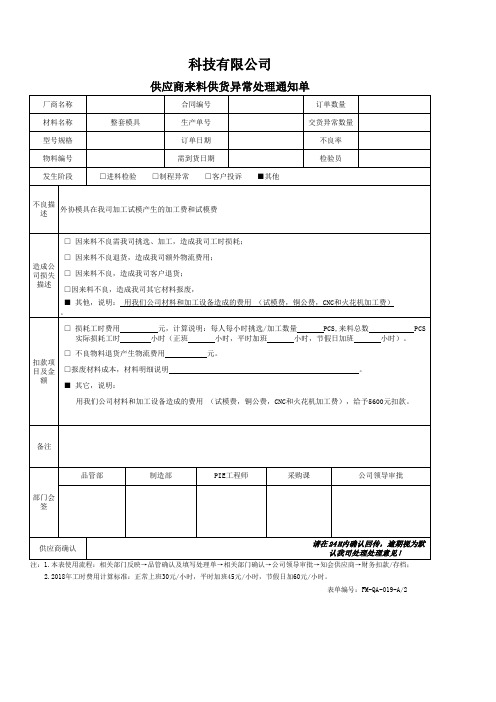
厂商名称 材料名称 型号规格 物料编号 发生阶段
科技有限公司
供应商来料供货异常处理通知单
合同编号
订单数量
整套模具
生产单号
交货异常数量
订单日期
不良率
需到货日期
检验员
□进料检验 □制程异常 □客户投诉 ■其他
不良描 述
外协模具在我司加工试模产生的加工费和试模费
□ 因来料不良需我司挑选、加工,造成我司工时损耗;
PCS,来料总数
PCS
小时(正班
小时,平时加班
小时,节假日加班
小时)。
□ 不良物料退货产生物流费用
元。
扣款项
目及金 □报废材料成本,材料明细说明 Nhomakorabea。
额 ■ 其它,说明:
用我们公司材料和加工设备造成的费用 (试模费,铜公费,CNC和火花机加工费),给予5600元扣款。
备注
部门会 签
品管部
制造部
PIE工程师
采购课
公司领导审批
供应商确认
请在 24 H内确认回传,逾期视为默 认我司处理处理意见!
注:1.本表使用流程:相关部门反映→品管确认及填写处理单→相关部门确认→公司领导审批→知会供应商→财务扣款/存档;
2.2018年工时费用计算标准:正常上班30元/小时,平时加班45元/小时,节假日加60元/小时。
表单编号:FM-QA-019-A/2
造成公 司损失
描述
□ 因来料不良退货,造成我司额外物流费用; □ 因来料不良,造成我司客户退货; □因来料不良,造成我司其它材料报废,
■ 其他,说明: 用我们公司材料和加工设备造成的费用 (试模费,铜公费,CNC和火花机加工费) 。
□ 损耗工时费用 实际损耗工时
不合格品控制程序
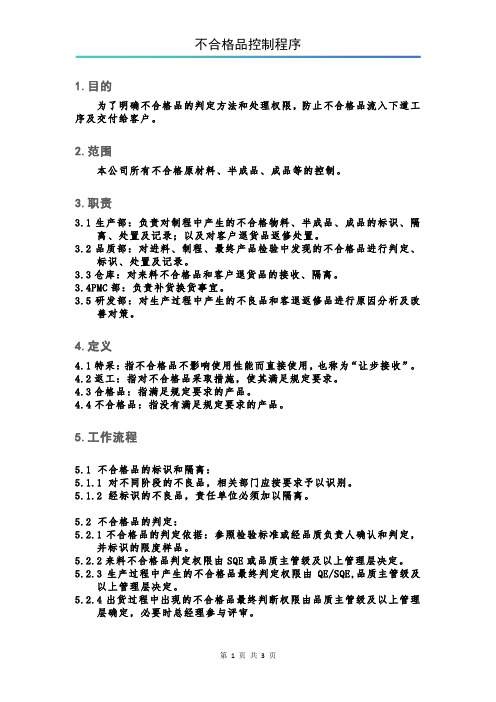
1.目的为了明确不合格品的判定方法和处理权限,防止不合格品流入下道工序及交付给客户。
2.范围本公司所有不合格原材料、半成品、成品等的控制。
3.职责3.1生产部:负责对制程中产生的不合格物料、半成品、成品的标识、隔离、处置及记录;以及对客户退货品返修处置。
3.2品质部:对进料、制程、最终产品检验中发现的不合格品进行判定、标识、处置及记录。
3.3仓库:对来料不合格品和客户退货品的接收、隔离。
3.4PMC部:负责补货换货事宜。
3.5研发部:对生产过程中产生的不良品和客退返修品进行原因分析及改善对策。
4.定义4.1特采:指不合格品不影响使用性能而直接使用,也称为“让步接收”。
4.2返工:指对不合格品采取措施,使其满足规定要求。
4.3合格品:指满足规定要求的产品。
4.4不合格品:指没有满足规定要求的产品。
5.工作流程5.1 不合格品的标识和隔离:5.1.1 对不同阶段的不良品,相关部门应按要求予以识别。
5.1.2 经标识的不良品,责任单位必须加以隔离。
5.2 不合格品的判定:5.2.1不合格品的判定依据:参照检验标准或经品质负责人确认和判定,并标识的限度样品。
5.2.2来料不合格品判定权限由SQE或品质主管级及以上管理层决定。
5.2.3生产过程中产生的不合格品最终判定权限由QE/SQE,品质主管级及以上管理层决定。
5.2.4出货过程中出现的不合格品最终判断权限由品质主管级及以上管理层确定,必要时总经理参与评审。
5.3不合格品的处理方式:A.批退B.加工使用C.挑选使用D.特采使用E.报废F.其它5.4 来料不合格的处理5.4.1 IQC来料检验不合格品,依《来料检验不良流程》进行处理;填写好《IQC来料验收单》及时通知SQE或品质主管进行处理。
5.4.2 SQE或品质主管判定拒收后将来料异常情况通知计划,计划可根据生产需求提出特采,交由研发部、品质部等相关部门评审,最终由工厂负责人根据评审结果决定是否特采使用;IQC在接到特采通知后须把物料上贴上“特采”标签,必要时注明特采原因及处理方式;若最终确定批退,由仓库填写《退货单》,并通知相应供货商来公司退货处理。
品质异常通知单(来料)

FROM:
供应商 Supplier 来料日期 Received date 来料数量 Received QTY. 不良率 Defective
rate
Байду номын сангаас
检查日期
Inspection date IQC Line 批准Approved 批准Approved by
退货 无 No
报废
特采 回答日期Reply date:
批准approved 批准approved by
暂定对策 Temporary action:
编制Prepare 编制Prepare by
发生原因分析occurrence cause:
永久对策permanent action:
批准approved 批准approved by
编制Parpare 编制Parpare by
对策开始Action started: 对策批复Action lot confirm:
对策批号Action lot No.:
对策批标记Action lot mark:
确认 confirmed by: JV-WI-QA-2-01-05A
来料品质异常联络单 料品质异常联络单
Incoming Material Abnormal Quality Communication
联络单号: Reference No. 发出日期 Issued date:
TO:
CC:
产品名称 Product name 产品批号 Lot No. 送货单号 Invoice No. 抽样数量
附不良样品
Defective sample attached:
品质异常处理管理规定

依相关检验标准进行判定,确定不良成立时,针对不合格物料标示“不合格”,并要求生产单位立即移至不良品区域。
于半小时内开立《品质异常联络单》、《返工通知单》并附不良样品,要求生产单位返工。
《品质异常联络单》、《返工通知单》及不良样品后,当天安排返工作业,并回复生产失效原因及改善措施,FQC负责跟踪返工及验证工作。
(注塑、移印、光刻、喷漆))5%时,IPQC应开出《生产异常通知单》待技术、品质、制造担当分析出原因找出责任单位后由责任单位进行对策,品质部监控对策实施有效性.。
3%时,IPQC应立即通知产线停线并召集工程、品质等单位对问题点进行分析,找出原因和对策,等问题点解决后,方可再开线生产。相关不合格品的控制见《不合格处理流程》。
负责对责任单位的改善结果进行追踪确认异常责任单位,并每月进行统计上报。
生产部:
负责品质异常的原因分析,提出临时措施及长期改善对策并执行。
负责品质异常的改善和预防措施的实施及验证改善措施的有效性;
其它相关单位:
在需要时进行异常改善的配合
出货品质异常:
品质部:
负责将品质异常通知各部门及确定责任部门;
负责异常改善后的跟踪确认;
品质异常处理管理规定
慈溪市精彩汽车零部件有限公司
品质异常处理管理办法
编号: JC/QA-PZ-11
使用部门: 品质部
受控状态:
版次
制定日期
修订内容
核 准
审 核
作 成
A/0
新制定
一、目的:
规范品质异常处理流程,提高品质异常处理的时效性,确保来料质量及产线的正常运转,同时满足顾客的质量要求。
二、范围:
适用于本公司来料、制程、出货品质异常的处理。
来料不合格品管理规定

来料不合格品管理规定1. 目的:确保不符合要求的产品得到识别和控制,以防止其非预期的使用和交付。
2. 适用范围:适应于DXC工厂内部不合格来料、生产线退料的管理。
各阶段检验测试作业之执行、评估、标识与隔离均适用,其它如工程试验、ECN等产生之不良依相关规定办理。
3. 定义:略4. 权责:略5.规定:5.1 不良品来源:5.1.1 物料承认为不合格的样品。
5.1.2 来料检验为不合格品。
5.1.3 制程批量不良物料。
5.1.4生产过程不良退料。
5.2 送样物料承认为不合格品:具体参照《新物料导入管理办法》(IC-ED-01)。
5.3 来料检验为不合格品:5.3.1当IQC检验或试验发现不合格时,应在不良品上粘贴红色箭头标签,并与良品明确区分。
5.3.1.1若检验符合允收水准,则由IQC检验人员分别在“来料检验单”(DXC-QDFM-30)上填不良品数和不良比例,由IQC判定此批来料合格。
5.3.1.2 若因不良数超出允收水准时,此批货判定为不合格,IQC在外箱贴上“待处理”标签及物品状态上盖红色“待处理”印章,并在其上清楚填写不良现象,并通知仓库立即将此不良货物移至不良品待处理区。
5.3.2 来料检验不合格,需特采时,IQC将按《进料特采作业规定》(IC-IQC-03)进行作业。
5.3.3 来料判定不合格,需退料时,采购部/PMC应立即联络该供应商,要求其在2日内或要求的时间内至公司处理。
所有大陆供应商之供货,应在7日内退货完毕。
超出此期限者,每日应收取相应保管费用;若在30日内仍未办理退货,则以报废处理,不付供应商该款项。
5.3.4 当IQC判定之不合格品系因采购下错单或工程图错误所致,经采购与供应商协调无法退货,且无法协助加工或无法用于其它机种时,由采购申请变卖或报废,责任部门填写再发防止对策后,呈总经理核准。
5.4制程批量不良物料:5.4.1 生产过程中发现进料批量产生异常时(不良率大于5%),由发现单位速反馈IQC并开出“制程/品质异常处理单”(DXC-QDFM-30),同时保留不良品与不良品原包装标签(现品票)交IQC确认,若确定为来料不良时,立即由IQC予以处理。
补单流程规定
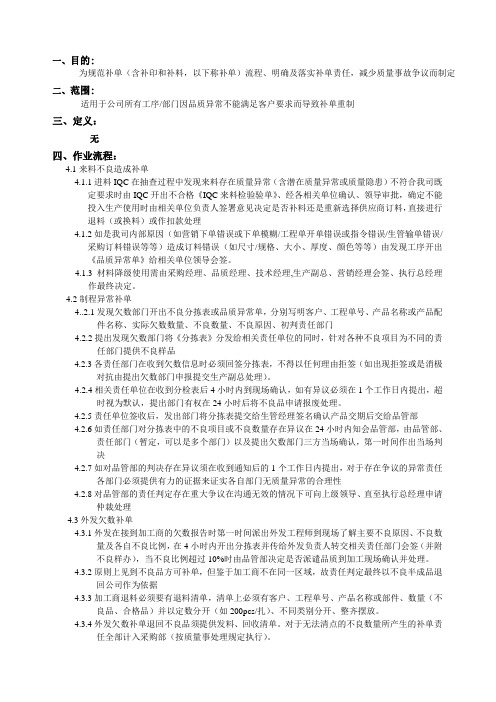
一、目的:为规范补单(含补印和补料,以下称补单)流程、明确及落实补单责任,减少质量事故争议而制定二、范围:适用于公司所有工序/部门因品质异常不能满足客户要求而导致补单重制三、定义:无四、作业流程:4.1来料不良造成补单4.1.1进料IQC在抽查过程中发现来料存在质量异常(含潜在质量异常或质量隐患)不符合我司既定要求时由IQC开出不合格《IQC来料检验验单》、经各相关单位确认、领导审批,确定不能投入生产使用时由相关单位负责人签署意见决定是否补料还是重新选择供应商订料,直接进行退料(或换料)或作扣款处理4.1.2如是我司内部原因(如营销下单错误或下单模糊/工程单开单错误或指令错误/生管输单错误/采购订料错误等等)造成订料错误(如尺寸/规格、大小、厚度、颜色等等)由发现工序开出《品质异常单》给相关单位领导会签。
4.1.3材料降级使用需由采购经理、品质经理、技术经理,生产副总、营销经理会签、执行总经理作最终决定。
4.2制程异常补单4..2.1发现欠数部门开出不良分拣表或品质异常单,分别写明客户、工程单号、产品名称或产品配件名称、实际欠数数量、不良数量、不良原因、初判责任部门4.2.2提出发现欠数部门将《分拣表》分发给相关责任单位的同时,针对各种不良项目为不同的责任部门提供不良样品4.2.3各责任部门在收到欠数信息时必须回签分拣表,不得以任何理由拒签(如出现拒签或是消极对抗由提出欠数部门申报提交生产副总处理)。
4.2.4相关责任单位在收到分检表后4小时内到现场确认,如有异议必须在1个工作日内提出,超时视为默认,提出部门有权在24小时后将不良品申请报废处理。
4.2.5责任单位签收后,发出部门将分拣表提交给生管经理签名确认产品交期后交给品管部4.2.6如责任部门对分拣表中的不良项目或不良数量存在异议在24小时内知会品管部,由品管部、责任部门(暂定,可以是多个部门)以及提出欠数部门三方当场确认,第一时间作出当场判决4.2.7如对品管部的判决存在异议须在收到通知后的1个工作日内提出,对于存在争议的异常责任各部门必须提供有力的证据来证实各自部门无质量异常的合理性4.2.8对品管部的责任判定存在重大争议在沟通无效的情况下可向上级领导、直至执行总经理申请仲裁处理4.3外发欠数补单4.3.1外发在接到加工商的欠数报告时第一时间派出外发工程师到现场了解主要不良原因、不良数量及各自不良比例,在4小时内开出分拣表并传给外发负责人转交相关责任部门会签(并附不良样办),当不良比例超过10%时由品管部决定是否派谴品质到加工现场确认并处理。
特采流程
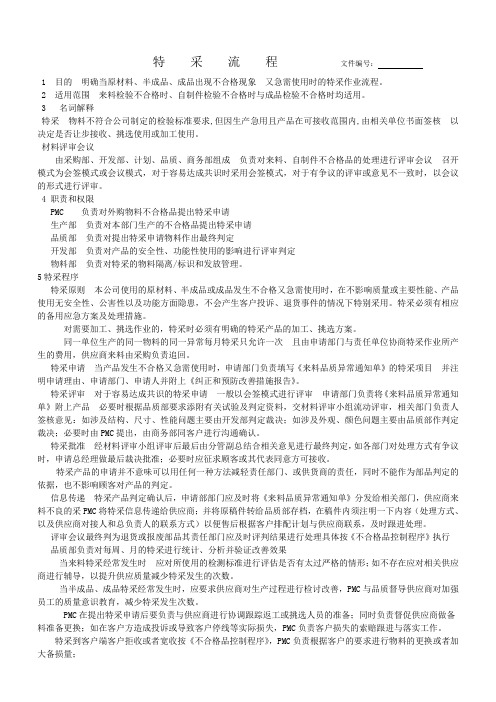
特采流程文件编号:1 目的明确当原材料、半成品、成品出现不合格现象又急需使用时的特采作业流程。
2 适用范围来料检验不合格时、自制件检验不合格时与成品检验不合格时均适用。
3 名词解释特采物料不符合公司制定的检验标准要求,但因生产急用且产品在可接收范围内,由相关单位书面签核以决定是否让步接收、挑选使用或加工使用。
材料评审会议由采购部、开发部、计划、品质、商务部组成负责对来料、自制件不合格品的处理进行评审会议召开模式为会签模式或会议模式,对于容易达成共识时采用会签模式,对于有争议的评审或意见不一致时,以会议的形式进行评审。
4 职责和权限PMC 负责对外购物料不合格品提出特采申请生产部负责对本部门生产的不合格品提出特采申请品质部负责对提出特采申请物料作出最终判定开发部负责对产品的安全性、功能性使用的影响进行评审判定物料部负责对特采的物料隔离/标识和发放管理。
5特采程序特采原则本公司使用的原材料、半成品或成品发生不合格又急需使用时,在不影响质量或主要性能、产品使用无安全性、公害性以及功能方面隐患,不会产生客户投诉、退货事件的情况下特别采用。
特采必须有相应的备用应急方案及处理措施。
对需要加工、挑选作业的,特采时必须有明确的特采产品的加工、挑选方案。
同一单位生产的同一物料的同一异常每月特采只允许一次且由申请部门与责任单位协商特采作业所产生的费用,供应商来料由采购负责追回。
特采申请当产品发生不合格又急需使用时,申请部门负责填写《来料品质异常通知单》的特采项目并注明申请理由、申请部门、申请人并附上《纠正和预防改善措施报告》。
特采评审对于容易达成共识的特采申请一般以会签模式进行评审申请部门负责将《来料品质异常通知单》附上产品必要时根据品质部要求添附有关试验及判定资料,交材料评审小组流动评审,相关部门负责人签核意见:如涉及结构、尺寸、性能问题主要由开发部判定裁决;如涉及外观、颜色问题主要由品质部作判定裁决;必要时由PMC提出,由商务部同客户进行沟通确认。
品质异常处理管理规定

d、不遵守作业标准或不遵守工艺卫生要求
e、机械发生故障或磨损
f、其他情形影响到产品质量时
3.3出货品质异常:
a、出货发现严重缺陷超过1%或轻缺陷超过3%;
b、客户投诉或抱怨;
四、职责
4.1来料品质异常:
品质部:
负责填写《来料检验报告》、《品质异常联络单》“异常显现描述”和“时效”
5.19如同一质量问题连续发起两次品质异常,验证结果无明显改善,则需采购部组织召开供应商评审,决定是否需要取消供应商资格。
5.2制程品质异常:
IP
5.2.3IPQC依相关检验标准进行判定,确认不良成立时,应开具《品质异常联络单》并要求生产部门暂停生产进行整改。
NO.往前追溯,直至良品。
5.2.5IPQC针对已追溯到的不良品标示“不合格”,并要求生产单位立即移至不良品区域,不良品如可以进行返工、返修达到合格要求,则由IPQC发出《返工通知单》,生产对不良品进行返工、返修,返工返修后需交付IPQC进行检验,合格品进行流入下一工序,不合格按照《不合格品处理流程》处理。
3%时,IPQC应立即通知产线停线并召集工程、品质等单位对问题点进行分析,找出原因和对策,等问题点解决后,方可再开线生产。相关不合格品的控制见《不合格处理流程》。
品质异常联络单》需生产部进行会签,生产部接到品质异常信息后半小时内需针对异常现象提出临时对策。
品质工程师针对责任单位回复内容进行确认,针对改善措施不合格部分予
4.3出货品质异常:
品质部:
负责将品质异常通知各部门及确定责任部门;
负责异常改善后的跟踪确认;
负责处理客户抱怨异常责任单位:
生产部:
负责品质异常的原因分析,提出临时措施及长实施及验证改善措施的有效性;