数控车中的切槽方法探讨
数控车精品课程切槽加工

THANKS
感谢观看
材料。焊接式切槽刀易于更换刀片,适应不同槽宽的加工需求。
02
整体硬质合金切槽刀
整体硬质合金刀具有较好的耐磨性、硬度高,刀片为直条形,刚性好,
适合于大进给量切削。
03
陶瓷结合剂金刚石砂轮修整器
陶瓷结合剂金刚石砂轮具有磨削效率高、磨削成本低、使用寿命长等优
点,适用于精密磨削、超精磨削等高精度加工。
切槽刀具的几何参数
切削液浓度
根据切削液种类和浓度要求,调整好切削液 的浓度。
切削液更换
定期更换切削液,以保证切削液的质量和效 果。
05ห้องสมุดไป่ตู้
切槽加工的质量控制
Chapter
切槽加工的质量标准
尺寸精度
表面粗糙度
切槽加工后的尺寸精度应符合加工要求, 如槽宽、槽深等参数应符合设计标准。
切槽加工后的表面粗糙度应尽可能低,以 减小对工件耐磨性和使用寿命的影响。
切槽刀具的选用原则
01
根据工件材料选择 合适的切槽刀具种 类和材质。
02
根据加工要求选择 合适的切槽刀具几 何参数,如前角、 后角、刃倾角等。
03
根据槽宽选择合适 的切槽刀具直径和 刃长,以保证加工 质量和效率。
04
根据生产批量选择 合适的切槽刀具寿 命和精度等级,以 降低生产成本。
03
切槽加工的程序编制
02
切槽加工的主要刀具有切槽刀、尖刀和成型刀等,根据不同的加工需求选择不同 的刀具。
切槽加工的工艺特点
切槽加工具有以下工艺特点
可以根据需要选择不同的刀具和切削参数,以达到所需 的加工精度和表面粗糙度。
可以加工各种形状的槽类零件,如方形、圆形、梯形等 。
槽加工
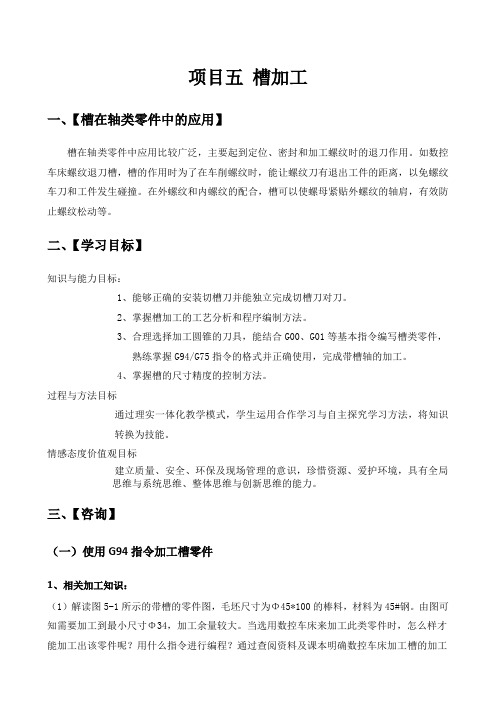
项目五槽加工一、【槽在轴类零件中的应用】槽在轴类零件中应用比较广泛,主要起到定位、密封和加工螺纹时的退刀作用。
如数控车床螺纹退刀槽,槽的作用时为了在车削螺纹时,能让螺纹刀有退出工件的距离,以免螺纹车刀和工件发生碰撞。
在外螺纹和内螺纹的配合,槽可以使螺母紧贴外螺纹的轴肩,有效防止螺纹松动等。
二、【学习目标】知识与能力目标:1、能够正确的安装切槽刀并能独立完成切槽刀对刀。
2、掌握槽加工的工艺分析和程序编制方法。
3、合理选择加工圆锥的刀具,能结合G00、G01等基本指令编写槽类零件,熟练掌握G94/G75指令的格式并正确使用,完成带槽轴的加工。
4、掌握槽的尺寸精度的控制方法。
过程与方法目标通过理实一体化教学模式,学生运用合作学习与自主探究学习方法,将知识转换为技能。
情感态度价值观目标建立质量、安全、环保及现场管理的意识,珍惜资源、爱护环境,具有全局思维与系统思维、整体思维与创新思维的能力。
三、【咨询】(一)使用G94指令加工槽零件1、相关加工知识:(1)解读图5-1所示的带槽的零件图,毛坯尺寸为Φ45*100的棒料,材料为45#钢。
由图可知需要加工到最小尺寸Φ34,加工余量较大。
当选用数控车床来加工此类零件时,怎么样才能加工出该零件呢?用什么指令进行编程?通过查阅资料及课本明确数控车床加工槽的加工方法及指令的应用;叙述数控车床加工槽工件的全过程。
(2)任务分析解读图5-1所示的槽零件,所用的毛坯为棒料,加工余量大,要得到图纸标注尺寸,需要一层层切削。
如果使用G00、G01等指令分层切削编程,编程将会很繁琐,采用外圆粗车循环 G71指令及精车循环G70指令以及G94端面切削循环指令编程则可简化编程。
本任务为带槽圆柱轴的车削,在编程与加工之前,应先了解槽零件的工艺分析方法及车削加工路线等相关知识。
图5-1槽加工零件图(3)刀具卡(见表5-1)表5-1 槽加工刀具卡(4)检测方法(见表5-2)2、制定加工工艺:(1)加工路线:粗车所有外圆尺寸,精车所有外圆尺寸,切槽。
数控——教学案例三车槽和车断

令了解沟槽的种类和作用。
令掌握矩形槽和圆弧形槽的车削方法和测量方法。
令理解车沟槽时可能产生的问题和防止方法。
令掌握切断的方法。
令掌握车削沟槽零件加工的方法。
令掌握车削沟槽零件的检测。
令掌握切断时的注意事项。
槽轴,如图3- 1 所示,毛坯尺寸 50 150 mm,材料为45 号钢,分析零件加工工艺。
图3- 1 槽轴1.本任务车削矩形槽和圆形槽,并切断(4mm 处),毛坯材料为45 钢。
2.掉头,用一夹一顶加工。
3.根据尺寸公差.表面粗糙度的要求,采用先粗后精的加工方法。
切断与车槽是车工的基本操作技能之一,能否掌握好,关键在于刀具的刃磨。
⑴刃磨左侧副后刀面:两手握刀,车刀前刀面向上,同时磨出左侧副后角和副偏角。
⑵刃磨右侧副后刀面:两手握刀,车刀前刀面向上,同时磨出右侧副后角和副偏角。
⑶刃磨主后刀面:同时磨出主后角。
⑷刃磨前刀面和前角:车刀前刀面对着砂轮磨削表面。
⑴切断刀的卷屑槽不宜磨得太深,普通为0.75-1.5mm。
⑵刃磨切断刀和车槽刀的两侧副后角时,应以车刀的底面为基准,用钢尺或者直角尺检查。
⑶刃磨切断刀和车槽刀的副偏角时,要防止下列情况产生:副偏角太大,刀头强度变差,容易折断;副偏角为负值,不能用直进法切削;副切削刃不平直,不能用直进法切削;车刀左侧磨去太多,不能切割有高台阶的工件。
在零件上加工各种形状的槽的操作,叫做切沟槽。
常用的外沟槽有外圆沟槽.45 外沟槽.外圆端面沟槽和圆弧沟槽等。
车槽刀装夹是否正确,对车槽的质量有直接影响。
如矩形车槽刀的装夹,要求垂直工件轴心线,否则车出的槽壁不会平直。
⑴车精度不高.宽度较窄的矩形沟槽,可以用刀宽等于槽宽的车槽刀,采用直进法一次进给车出。
精度要求较高的沟槽,普通采用二次进给车成。
即第一次进给车沟槽时,槽壁两侧留精车余量,第二次进给时用等宽刀修整。
⑵车较宽的沟槽,可以采用多次直进法切割。
并在槽壁两侧留一定的精车余量,然后根据槽深. 槽宽精车至尺寸。
⑶车较小的圆弧形槽,普通用成型刀车削。
数控车床上螺旋槽加工
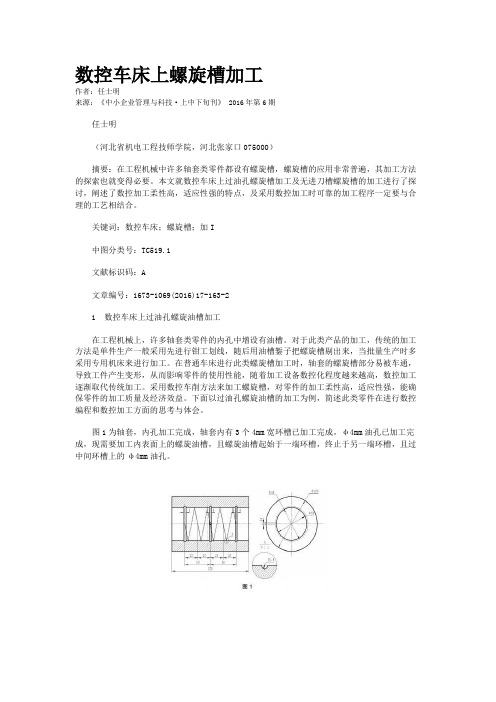
数控车床上螺旋槽加工作者:任士明来源:《中小企业管理与科技·上中下旬刊》 2016年第6期任士明(河北省机电工程技师学院,河北张家口075000)摘要:在工程机械中许多轴套类零件都设有螺旋槽,螺旋槽的应用非常普遍,其加工方法的探索也就变得必要。
本文就数控车床上过油孔螺旋槽加工及无进刀槽螺旋槽的加工进行了探讨,阐述了数控加工柔性高,适应性强的特点,及采用数控加工时可靠的加工程序一定要与合理的工艺相结合。
关键词:数控车床;螺旋槽;加I中图分类号:TC519.1文献标识码:A文章编号:1673-1069(2016)17-163-21 数控车床上过油孔螺旋油槽加工在工程机械上,许多轴套类零件的内孔中增设有油槽。
对于此类产品的加工,传统的加工方法是单件生产一般采用先进行钳工划线,随后用油槽錾子把螺旋槽剔出来,当批量生产时多采用专用机床来进行加工。
在普通车床进行此类螺旋槽加工时,轴套的螺旋槽部分易被车通,导致工件产生变形,从而影响零件的使用性能,随着加工设备数控化程度越来越高,数控加工逐渐取代传统加工。
采用数控车削方法来加工螺旋槽,对零件的加工柔性高,适应性强,能确保零件的加工质量及经济效益。
下面以过油孔螺旋油槽的加工为例,简述此类零件在进行数控编程和数控加工方面的思考与体会。
图1为轴套,内孔加工完成,轴套内有3个4mm宽环槽已加工完成,φ4mm油孔已加工完成,现需要加工内表面上的螺旋油槽,且螺旋油槽起始于一端环槽,终止于另一端环槽,且过中间环槽上的φ4mm油孔。
以最后一刀精加工编程阐述螺旋油槽的加工方法为例:首先,准备一把R1.5的半圆头内螺纹车刀,装刀后进行对刀操作(X向刀具补偿值放在“形状补偿”页面内。
其次,工件坐标系零点设在工件右端面中心,刀位点选在刀头圆心位置。
螺旋油槽起于右端环槽,止于左端环槽,其程序如下:……G00 X55.;Z-25.;G01 X60. F ;G32 Z-125. F25.;G00 X55.;Z5.;……至此螺旋线已经加工完成。
数控车精品课程-切槽加工

02
切槽加工的技术要点
切槽刀具的选择
切槽刀具的材料
切槽刀具的规格
选择具有高硬度、高耐磨性和高耐热 性的刀具材料,如硬质合金和陶瓷等。
根据切槽的宽度和深度选择合适的切 槽刀具,以确保切削过程中的刚性和 安全性。
数控车精品课程-切槽加工
目录 Contents
• 切槽加工的基本概念 • 切槽加工的技术要点 • 切槽加工的工艺流程 • 切槽加工的常见问题及解决方案 • 切槽加工的案例分析
01
切槽加工的基本概念
切槽加工的定义
切槽加工是指在金属切削加工过程中 ,利用数控车床的切削刀具对工件上 的槽进行切削,以达到预设的槽宽、 槽深和槽型的过程。
切削振动问题
总结词
切削振动会降低切槽加工的表面质量和加工精度,同时可能加剧刀具磨损。
详细描述
切削振动的原因可能是机床刚性不足、刀具设计不合理或切削参数设置不合适。 为了解决这个问题,可以提高机床的刚性和稳定性,优化刀具设计,选择合适的 切削参数。同时,加强切削液的供给和使用也可以有效减小切削振动。
05
切槽加工的案例分析
案例一:不锈钢切槽加工
总结词
难度适中,刀具选择要求高
详细描述
不锈钢切槽加工对刀具的硬度和耐磨性要求较高,同时需要合理选择切削参数, 以避免刀具过快磨损和工件表面质量下降。在加工过程中,还需注意控制切削 温度,防止刀具和工件产生热变形。
案例二:铝合金切槽加工
总结词
加工效率高,切削参数范围广
切槽加工后的检测与修正
切槽尺寸检测
使用测量工具对切槽尺 寸进行检测,确保符合
《切断与切槽》数控车床编程格式与编程方法要点

《切断与切槽》数控车床编程格式与编程方法要点第9讲切断与切槽·学习目的和要求1、掌握在数控车床上切断工件与切沟槽的基本方法2、掌握切断刀的安装、调整以及对刀操作3、掌握切槽切断指令的编程格式与编程方法4、掌握内切槽、外切槽、典型槽的加工方法5、掌握切断与沟槽加工的加工工艺·重点内容1、数控车床上切断工件与切沟槽的基本方法2、切断刀的安装、调整以及对刀操作3、切槽切断循环指令的编程格式4、内切槽、外切槽、典型槽的加工方法5、掌握切断与沟槽加工的加工工艺·难点内容1、工件切断与沟槽的加工工艺路线2、切断与沟槽的加工方法·实训任务1、要求每组学生必须完成一个实训项目。
2、要求每个学生必须独立完成实习报告。
·教学准备·课时分配:4H·教学方法先讲解知识内容,再进行加工操作练习。
·教学过程1、强调上课纪律,考勤记录。
2、讲解本节课主题,内容简要概括。
3、讲解安全操作规程4、上课准备5、教学分配(分组,工具配发)6、知识内容讲解7、本节课点评总结一、切槽/切断方法1、槽的类型在工件表面上车沟槽的方法叫切槽,槽的形状有外槽、内槽和端面槽。
2、切槽的方法(1)加工外槽时用外切槽刀,且沿着工件中心方向切削;加工内槽时用内切槽刀,且沿着工件大径方向切削;加工端面槽时可用外切槽刀、内切槽刀或自磨刀具。
(2)车削精度不高的和宽度较窄的矩形沟槽:可以用刀宽(主切削刃宽度)等于槽宽的切槽刀,直接采用G01直进法横向走刀一次将槽切出。
(3)车削精度要求较高的和宽度较宽的沟槽:主切削刃宽度小于槽宽,分几次直进法横向走刀,并在槽的两侧、槽底留一定的精车余量。
切出槽宽后,然后根据槽深、槽宽,最后一刀纵向走刀精车至槽底尺寸。
当切削到槽底时一般应暂停一段时间以光顺槽底。
(4)加工宽槽和多槽时:可用移位法、调用子程序、宏程序或G75切槽复合循环指令编程。
(5)车削较小的圆弧形槽,一般用成形车刀车削,或改变主偏角与副偏角的角度。
基于宏程序华中数控车切槽循环指令开发
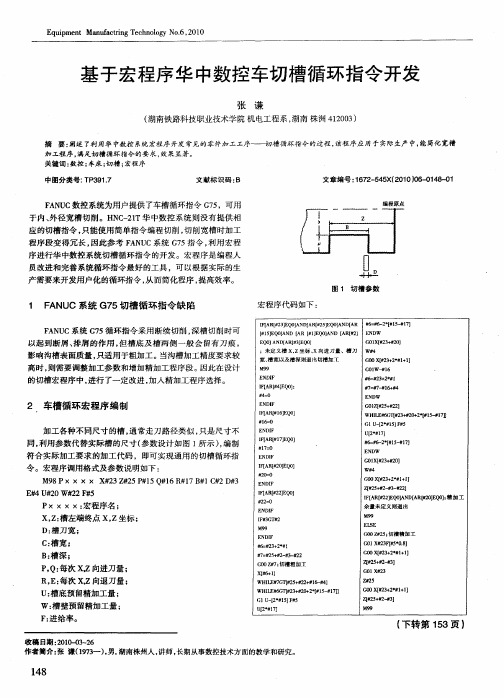
加 工程序 , 满足切槽循 环指令 的要 求, 效果显著。 关键词 : 数控 ; 车床 ; 切槽 ; 宏程序 中图分类号: 3 17 TP 9 . 文献标识码 : B
文 章 编 号 :6 2 5 5 ( 0 0)6 0 4 _ 1 1 7— 4 X 2 1 0- 1 8o
F N C数控系统为用户提供了车槽循 环指令 G 5 AU 7 ,可用
员改进和完善系统循环指令最好 的工具 ,可以根据实际 的生 产需要来开发用户化的循环指令 , 从而简化程序 , 提高效率 。
图 1 切槽参数
1 F NU A C系统 G7 5切 槽 循环 指令 缺 陷
F N C系统 C 5 环指令采用断续切削 , AU 7循 深槽切削时可 以起到断屑 、 排屑 的作 用 , 但槽底 及槽两侧 一般 会留有刀痕 , 影响沟槽表 面质量 , 只适 用于粗加工。当沟槽加工精度要求较 高时 , 则需要调整加工参 数和增加 精加工程序段 。因此在设计 的切槽宏程序 中, 进行 了一定 改进 , 加人精加工程序选择 。
#1 = 70
# = 6 2 1 4 l】 6 #- 5 7
ENDW
符合实际加工要求的加工代码 ,即可实 现通 用的切槽循环指
令 。宏程序调用格式及参数说 明如下 :
M9 8P× X × X # 3Z 2 # 5Q 1 # 7B 1 # # X 2 #5P 1 # 6R 1 # 2D 3 C
宏程序代码如下:
I[ [ 3 Q ]NDA [2 】Q ] N [ R FAR舵 ] OA [ R # 5 0A D A E E : 6 2 1- 1】 # — 5 # 7 Z] Q 】N 【 R 1 Q ] D 【R # 】 E D SE OA D A ] 0AN A [ N W E 2 E 0 AN [ R #I Q ] Q ] D A [3 o E C I [2 + 0 , X#3# 】 O 2
数控车床沟槽件加工工艺设计与实践

数控车床沟槽件加工工艺设计与实践沈国祥【摘要】Grooving part machining is often met with in NC lathe.There are various methods for groove machining,but the machining workmanship,cutting parameter and programming are different.The workmanship of groove machining is more important,and the accuracy of parts depends on the programming.This paper analyes and studies the machining workmanship and the problems commonly met with during the process of production.%沟槽零件是数控车床加工中经常碰到的,不同类型沟槽的加工方法是有差别的,其各自的加工工艺、切削参数、编程方法也截然不同.沟槽零件的制造其生产工艺是关键,零件精度好坏取决于工艺编制的品质.对沟槽件的加工工艺设计、生产制造中常遇到相关问题进行分析与研究.【期刊名称】《机械制造与自动化》【年(卷),期】2013(042)003【总页数】4页(P63-66)【关键词】数控车床;沟槽零件;工艺设计;生产制造【作者】沈国祥【作者单位】南京工业职业技术学院,江苏南京210046【正文语种】中文【中图分类】TG519.10 引言数控车床在生产加工过程中,常会遇到轴肩部分的沟槽加工、内孔台阶的沟槽加工:常见的有矩形内外沟槽、梯形内外沟槽、端面沟槽、内外圆弧沟槽等。
沟槽零件的设计是根据它在整机中所处位置的机械性能的要求而程序成形的,各种槽其功能也各不相同,它们在整机中各自承担着自己的使命。
槽的加工(切槽固定循环指令)
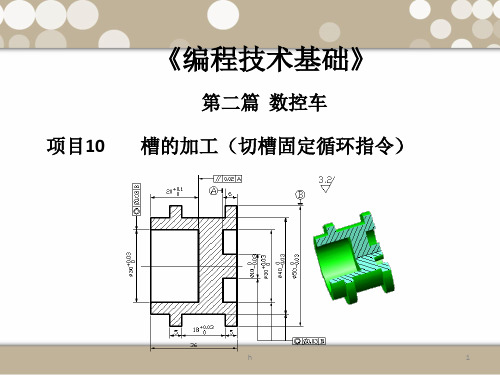
G74 X10 Z-6 P2500 Q3000 F60;
G28 U0 W0;
退刀
M30;
程序结束
h
12
h
4
G75的循环轨迹如图所示,刀具从循环起点A点开始,沿径向进刀Δi并到达C点, 然后退刀e(断屑)到D点,再继续按循环递进切削至径向终点的X坐标处,然后 快速退刀到径向起刀点,完成一次切削循环;接着沿轴向偏移Δk至F点,进行第 二次切削循环;依次循环直至刀具切削至程序终点坐标处(B点),径向退刀至 起刀点(G点),再轴向退刀至起刀点(A点),完成整个切槽循环动作。
其中, e为退刀量,其值为模态值; X(U)_Z(W)_为切槽终点处坐标; Δi为X方向的每次切深量,用不带符号的半径量表示,单位:μm; Δk为刀具完成一次径向切削后,在Z方向的偏移量,用不带符号的值表 示,单位:μm; Δd为刀具在切削底部的Z向退刀量,无要求时可省略; F为径向切削时的进给速度。 最后一次切深量和最后一次Z向偏移量均由系统自行计算。
(2)由于Δi和Δk为无符号值,所以刀具切深完成后的偏移方向由系 统根据刀具起刀点及切槽终点的坐标自动判断。
(3)切槽过程中,刀具或工件受较大的单方向切削力,容易在切削 过程中产生振动,因此,切槽过程中进给速度F的取值应略小,特别是 在端面切削时,通常取50~100mm/min。
h
11
【本项目参考程序】
h
6
例题:按如图所示尺寸切断零件。
解:
T0101;
M03 S600;
G00 X45 Z-40;
G75 R1;
G75 X-1 P5000 F50;
M05;
M30;
h
7
2、端面切槽循环指令G74
车削加工外圆弧类表面(切槽)

教学过程程序(环节)教学内容教师活动学生活动方法及提示1.新课引入(10分钟)1.复习G00、G01指令格式2.提出本节课的任务:⑴窄槽、宽槽、深槽的加工方法提出任务,激发学生学习兴趣⑴回答老师的提问。
⑵看投影仪,明确本节课的任务直接提出本节课任务。
2.必备知识(30分钟)一、槽的种类1.窄槽和宽槽:沟槽的宽度不大,采用切槽刀宽度等于槽宽的车刀,一次车出的沟槽称为窄槽。
沟槽宽度大于切槽刀头宽的槽称为宽槽。
2.浅槽和深槽:浅槽和深槽是相对而言,若槽深小于槽宽则可视为浅槽,槽深大于槽宽则可视为深槽。
二、槽的加工1.窄槽的加工窄槽加工时选用切槽刀宽等于槽宽的车刀,用G01指令进行直线切削。
精度要求较高时,用G04指令使刀具在槽底停留几秒,以光整槽底。
2.深槽的加工为了避免切槽过程中由于排屑不畅,使刀具前部压力过大出现扎刀和折断刀具的现象,应采用分次进刀的方式,刀具在切入工件一定深度后,停止进刀并回退一段距离,达到断屑和排屑的目的,注意应尽量选择强度较高的刀具。
3.宽槽的加工宽槽的宽度、深度的精度要求及表面质量相对较高。
在切削宽槽时常采用排刀的方式进行粗切,然后用精切槽刀沿槽的一侧切至槽底,精加工槽底至槽的另一侧,再沿侧面退出。
三、刀具刀位点的确定切槽刀有左右两个刀尖及切削中利用简洁语言配合课件进行讲解认真聆听,记录重要知识点。
抓住重点和难点进行讲解心处三个刀位点,加工径向槽进行对刀和编程时一般常用刀位点1。
四、切槽编程中应注意的问题1.在加工同类型槽的过程中采用同一个刀位点。
2.注意合理安排切槽后的退刀路线,避免刀具与零件的碰撞,造成车刀及零件的损坏。
3.切槽时,刀刃宽度、切削速度和进给量都不宜太大。
五、G代码指令1.暂停(延时)指令G04指令执行后,进行暂停至指定时间,暂停时间过后,继续执行下一段程序。
格式:G04 X(P);说明:X(P)表示暂停时间,X单位是秒,P单位是毫秒。
例如G04 X5表示暂停5秒;G04 P5表示暂停5毫秒。
数控车床编程与操作(机工版)教案:7.6 外圆、内孔切槽循环(G75).doc
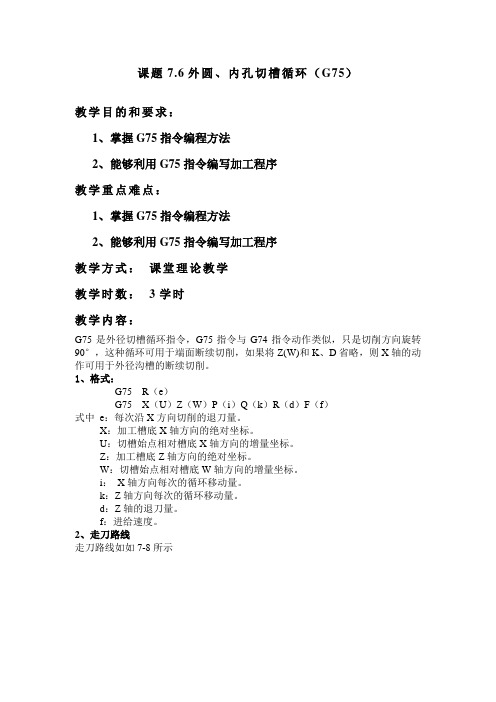
课题7.6外圆、内孔切槽循环(G75)教学目的和要求:1、掌握G75指令编程方法2、能够利用G75指令编写加工程序教学重点难点:1、掌握G75指令编程方法2、能够利用G75指令编写加工程序教学方式:课堂理论教学教学时数:3学时教学内容:G75是外径切槽循环指令,G75指令与G74指令动作类似,只是切削方向旋转90°,这种循环可用于端面断续切削,如果将Z(W)和K、D省略,则X轴的动作可用于外径沟槽的断续切削。
1、格式:G75 R(e)G75 X(U)Z(W)P(i)Q(k)R(d)F(f)式中e:每次沿X方向切削的退刀量。
X:加工槽底X轴方向的绝对坐标。
U:切槽始点相对槽底X轴方向的增量坐标。
Z:加工槽底Z轴方向的绝对坐标。
W:切槽始点相对槽底W轴方向的增量坐标。
i:X轴方向每次的循环移动量。
k:Z轴方向每次的循环移动量。
d:Z轴的退刀量。
f:进给速度。
2、走刀路线走刀路线如如7-8所示图7-8 G75走刀路线3、编程实例编程实例:图7-9是用G75外径切槽循环指令加工槽的实例,刀具宽度为4mm,X方向分四次加工,Z方向分两次加工.图7-9其程序为:O0006N10 G50 X90.0 Z125.0:建立工件坐系N20 G00 X41.0 Z41.0 S600;刀具快速趋近N30 G75 X20.0 Z25.0 I2.5 K10 F2.5;用G75指令切槽N40 X90.0 Z125.0;刀具快速退至参考点【小结】:本课题主要是介绍G75的格式及应用,要注意G75指令的使用方法及注意事项,能够用G75编制中等复杂轴类零件的外圆、内圆切槽数控加工程序。
【课外作业】:用G75指令完成P227页图(51)、(52)的深孔加工。
圆球十字槽在数控车削中的加工方法
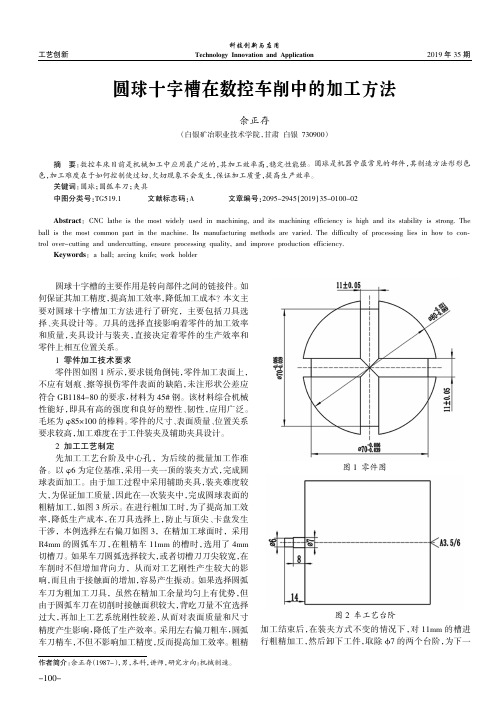
2019年35期工艺创新科技创新与应用Technology Innovation and Application圆球十字槽在数控车削中的加工方法余正存(白银矿冶职业技术学院,甘肃白银730900)圆球十字槽的主要作用是转向部件之间的链接件。
如何保证其加工精度,提高加工效率,降低加工成本?本文主要对圆球十字槽加工方法进行了研究,主要包括刀具选择、夹具设计等。
刀具的选择直接影响着零件的加工效率和质量,夹具设计与装夹,直接决定着零件的生产效率和零件上相互位置关系。
1零件加工技术要求零件图如图1所示,要求锐角倒钝,零件加工表面上,不应有划痕、擦等损伤零件表面的缺陷,未注形状公差应符合GB1184-80的要求,材料为45#钢。
该材料综合机械性能好,即具有高的强度和良好的塑性、韧性,应用广泛。
毛坯为φ85×100的棒料。
零件的尺寸、表面质量、位置关系要求较高,加工难度在于工件装夹及辅助夹具设计。
2加工工艺制定先加工工艺台阶及中心孔,为后续的批量加工作准备。
以φ6为定位基准,采用一夹一顶的装夹方式,完成圆球表面加工。
由于加工过程中采用辅助夹具,装夹难度较大,为保证加工质量,因此在一次装夹中,完成圆球表面的粗精加工,如图3所示。
在进行粗加工时,为了提高加工效率,降低生产成本,在刀具选择上,防止与顶尖、卡盘发生干涉,本例选择左右偏刀如图3,在精加工球面时,采用R4mm 的圆弧车刀,在粗精车11mm 的槽时,选用了4mm 切槽刀。
如果车刀圆弧选择较大,或者切槽刀刀尖较宽,在车削时不但增加背向力,从而对工艺刚性产生较大的影响,而且由于接触面的增加,容易产生振动。
如果选择圆弧车刀为粗加工刀具,虽然在精加工余量均匀上有优势,但由于圆弧车刀在切削时接触面积较大,背吃刀量不宜选择过大,再加上工艺系统刚性较差,从而对表面质量和尺寸精度产生影响,降低了生产效率。
采用左右偏刀粗车,圆弧车刀精车,不但不影响加工精度,反而提高加工效率。
利用CAXA数控车切槽的精加工编程方法
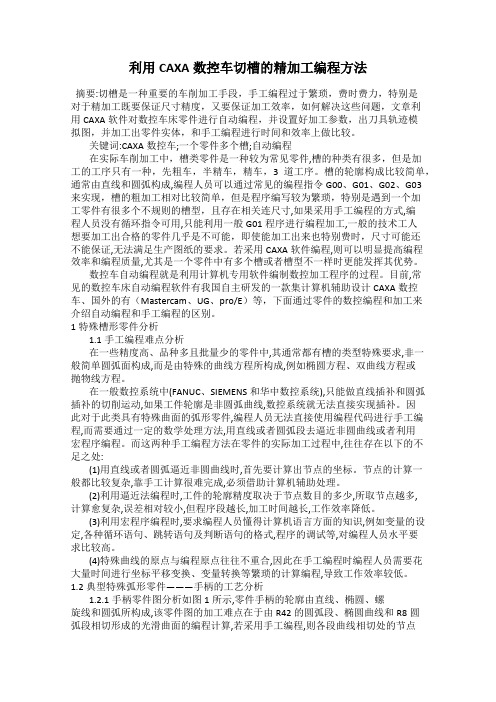
利用CAXA数控车切槽的精加工编程方法摘要:切槽是一种重要的车削加工手段,手工编程过于繁琐,费时费力,特别是对于精加工既要保证尺寸精度,又要保证加工效率,如何解决这些问题,文章利用CAXA软件对数控车床零件进行自动编程,并设置好加工参数,出刀具轨迹模拟图,并加工出零件实体,和手工编程进行时间和效率上做比较。
关键词:CAXA数控车;一个零件多个槽;自动编程在实际车削加工中,槽类零件是一种较为常见零件,槽的种类有很多,但是加工的工序只有一种,先粗车,半精车,精车,3道工序。
槽的轮廓构成比较简单,通常由直线和圆弧构成,编程人员可以通过常见的编程指令G00、G01、G02、G03来实现,槽的粗加工相对比较简单,但是程序编写较为繁琐,特别是遇到一个加工零件有很多个不规则的槽型,且存在相关连尺寸,如果采用手工编程的方式,编程人员没有循环指令可用,只能利用一般G01程序进行编程加工,一般的技术工人想要加工出合格的零件几乎是不可能,即使能加工出来也特别费时,尺寸可能还不能保证,无法满足生产图纸的要求。
若采用CAXA软件编程,则可以明显提高编程效率和编程质量,尤其是一个零件中有多个槽或者槽型不一样时更能发挥其优势。
数控车自动编程就是利用计算机专用软件编制数控加工程序的过程。
目前,常见的数控车床自动编程软件有我国自主研发的一款集计算机辅助设计CAXA数控车、国外的有(Mastercam、UG、pro/E)等,下面通过零件的数控编程和加工来介绍自动编程和手工编程的区别。
1特殊槽形零件分析1.1手工编程难点分析在一些精度高、品种多且批量少的零件中,其通常都有槽的类型特殊要求,非一般简单圆弧面构成,而是由特殊的曲线方程所构成,例如椭圆方程、双曲线方程或抛物线方程。
在一般数控系统中(FANUC、SIEMENS和华中数控系统),只能做直线插补和圆弧插补的切削运动,如果工件轮廓是非圆弧曲线,数控系统就无法直接实现插补。
因此对于此类具有特殊曲面的弧形零件,编程人员无法直接使用编程代码进行手工编程,而需要通过一定的数学处理方法,用直线或者圆弧段去逼近非圆曲线或者利用宏程序编程。
数控车床切槽加工中的子程序应用

Oxxxx;(子程序号) …… …… …… M99; M99指令为子程序结束并返回主程序,M98 P△△△xxxx 的下一程序段,继续执行主程序。子程序重复执行过程中, 刀具的运动轨迹一般是有规律地变化的,所以一般采用相对 坐标编程。
三、子程序的应用
1.如图2所示 已知:毛坯直径Φ30mm,一号刀为外圆车刀,三号刀为 切槽刀(宽度为2mm),工件原点建立在工件右端面上,切 刀左刀尖对刀。 分析:各槽的尺寸完全相同,当把刀具的起点放在X32 Z0处,可使在加工各槽时,刀具的轴向和径向的运动规律完 全相同,适合用子程序编程,从而简化主程序。 加工程序如下: O0001 (主程序)
图3
Z8; M98 P20004(调用子程序两次,切右端两槽) G00 X32 Z-28;(左端槽切削起始点) M98 P0004; (调用子程序,切左端槽) G00 X100; Z100; M30; O0004 (子程序) G00 W-22;(相对左移22) G01 U-12 F0.1;(切削至槽底直径Φ20) U12; (相对退刀至绝对X32处) G00 W3; (相对右移3) M99; 图3所示的零件,第一次调用子程序,刀具定位在绝对 坐标Z8处,在子程序Z方向相对位移22,即为绝对坐标Z=14 切第一槽。切至槽底直径Φ20mm,刀具X方向相对退刀U12 至绝对坐标X32处,刀具相对位移W3。第二次调用子程序, 再相对左移22,正是切中间槽的Z方向起点。同理,第三次 调用子程序时,要使刀具刀位点在Z方向与左端槽左侧槽壁 相距22,则需在主程序Z方向切削起点定位至Z-28,再左移 22,即绝对坐标Z=-50处。 综述以上两例,四(三)个槽沿轴向偏移,注意此时U向累 加和为零,W向累加和为偏移量。编制子程序时,编程者要对刀 具在相对坐标与绝对坐标转换过程中所处位置有清晰的界定。
- 1、下载文档前请自行甄别文档内容的完整性,平台不提供额外的编辑、内容补充、找答案等附加服务。
- 2、"仅部分预览"的文档,不可在线预览部分如存在完整性等问题,可反馈申请退款(可完整预览的文档不适用该条件!)。
- 3、如文档侵犯您的权益,请联系客服反馈,我们会尽快为您处理(人工客服工作时间:9:00-18:30)。
数控车中的切槽方法探讨
【摘要】在数控车的教学过程中,遇到各种切槽方法。
根据多年的教学经验积累,现将不同的加工指令给予综合,总结了一些编程技巧,供大家参考学习,共同提高。
【关键词】切槽;三种指令应用;起点坐标
以数控车削切槽为研究对象,在深入了解HNC-21/22T系统的宏编程处理方法后,通过对数控车削切槽循环的分析,以及在比较其他系统的基础上,提出以一个固定循环指令来实现切槽循环加工的方法。
通过介绍HNC-21/22T系统的宏编程指令功能扩展的二次开发技术,开发了数控车削切槽循环指令。
目前阶段得出的结果表明,该指令达到了预期的结果,简化了算法以及编程的过程,经实际验证效果良好。
数控车中的切槽方法课本讲的比较分散,课本上的例子不多,没有进行编程方法的比较,学生在学习过程中容易混淆。
我在授课过程中,将切槽方法给予总结,主要有三种方法进行编程,现总结如下。
一、当槽比较简单时,采用G01和G04指令进行联合编程的方法
如图一所示,槽宽等于4mm,采用4mm切槽刀,参考编程如下:
O0081;方法一O0082;方法二
T0303 G99;T0303 G99
M03S400;M03 S400
G00 X100.0 Z100.0;G00 X42.0 Z-29.0
G00 X32.0 Z-34.0;G75 R0.3
G01 Z21.0;G75 X32.0 Z-35.0 P1500 Q3000 F0.05
G04 X2.0;G00 X100.0 Z100.0
G01 X32.0;M05
G00 Z100.0 Z100.0;M30
M05;
方法一应该注意以下几个问题
1、起点坐标的X方向应大于最大直径,应取Φ32.0;
2、起点坐标的Z方向应考虑刀宽,所以Z方向的坐标应为Z-34.0;
3、切槽刀退出时,也必须采用G01指令,不能用G00指令。
方法二、采用G75复合切槽指令
如图二,直径为40的毛坯,我们只需要切出直径为32,宽度为10mm的槽即可。
采用槽宽为4mm的切槽刀,对刀时,采用左刀尖进行对刀。
注意事项:
1、起点坐标的X方向应大于最大直径,Z方向应考虑刀宽;
2、G75指令的起点坐标和终点坐标相同,这一点一定要明确;
3、采用G75指令时终点坐标一定要写正确,若用W值,要用槽宽减去刀宽,否则会出现错误。
方法三、采用调用子程序的方法进行编程(如图三)
O0083;(主程序) OO084;(子程序)
T0303 G99;G00 W-14.0 ;
M03 S400;G01 X20.0 F0.1
G00 X100.0 Z100.0;G04 X1.0;
G00 X32.0 Z0.0;G01 X32.0
M98 P20005;G00 W-10.0;
G00 X100.0 Z100.0 G01 X20.0 F0.1
M05; G04 X1.0;
M30;G01 X32.0
我们通过在教学中的不断积累,将切槽的几种方法给予总结,为以后的教学和工作打下良好基础。
结束语
切槽广泛应用在数控机床车削加工中,文章讲述了切槽与切断的刀具、加工及编程方法,并通过典型的加工实例,对其具体实现进行了描述,以供数控车削编程及操作人员参考。
参考文献
[1]马晓明,姚振强.锯齿形螺纹的通用宏程序设计及加工精度分析[J].机械设计与研究,2008年03期
[2]吴志光.基于FANUC Oi系统宏程序在二次曲面铣削加工中的应用研究
[D].合肥工业大学,2010年
[3]杨安,葛胜锦,潘长平,洪小锋.基于中望CAD平台的二次开发技术[A].中国公路学会计算机应用分会2010年学术年会论文集[C].2010年。