漏加工,错混料的8D
异常矫正措施-8D手法
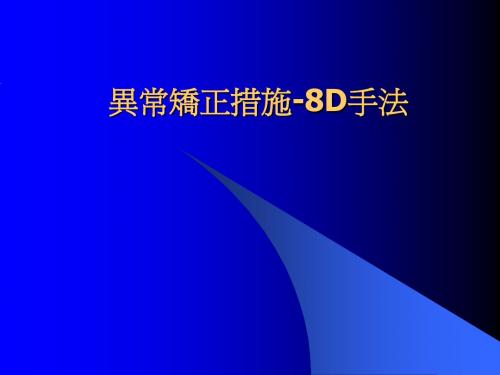
D7. 防止再發的改善措施
总结
– 解释防止问题再次发生的重要性。 – 用重复的‘为什么’技术确定根本原因的 根本原因。 – 解释怎样确定系统改进并确定和执行系统 预防建议。
D8. 效果確認
由品保稽核人員做針對改善結果最終效果確認.
•关闭 –为了关闭小组的的过程,在D教训 •完成提交领导的最后介绍 •表达对小组成员的抱怨和遗憾 •表达对小组成员的感谢
其它的不良問題產生.
2. 異常流出
1>. 解決此不良問題的永久性防止流出對策.
2>. 估計每種對策對此不良問題的貢獻度 3>. 在抽樣的基礎上確認改善對策的有效性,并確保不會因此行動 有其它的不良問題產生.
D6. 執行永久的改善措施
5W1H具體化提出的改善對策
從提出到導入為14天,最長不 可超過一個月,依實際狀況決定
D2. 問題點描述
問題點描述一般包括: 1. 問題點陳述(Problem Statement).
2. 詳細描述(Problem Description).
陳述指客戶抱怨或下流程反餽時對此異常的簡單描述. 詳細描述指小組成員針對異常的詳細敘述.
1>. What 問題點的名稱.
2>. Where 發現問題的地點. 3>. When 4>. How 5>. Big 6>. D/C 7> P/N 發現問題的具體時間. 如何發現問題(方法工具等). 不良的比例(必須包括總批量,抽檢數量,不良數量). 可追溯的標記. 客戶料號及廠內料號.
異常矯正措施-8D手法
何為8D
8D是一個系統化流程以發覺真因及解決問題 的手法. 跨功能改善小組(團隊作業) 問題點描述 緊急圍堵措施 原因分析 提出永久的改善對策 執行永久的改善對策 預防再發的改善對策 效果確認
8D详解,质量工程师都要看
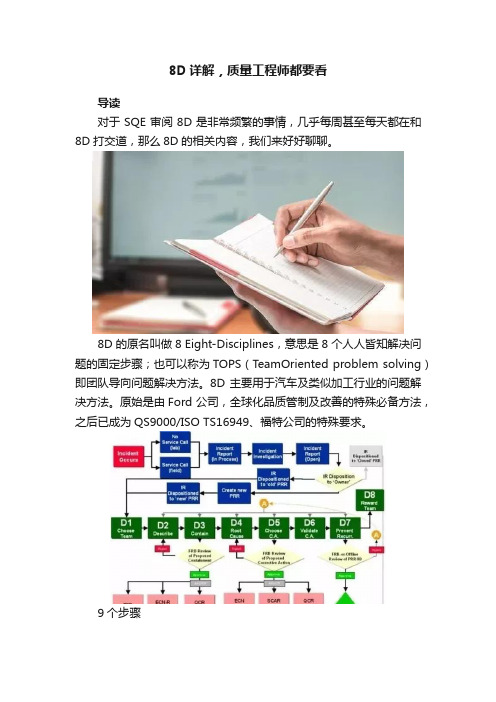
8D详解,质量工程师都要看导读对于SQE审阅8D是非常频繁的事情,几乎每周甚至每天都在和8D打交道,那么8D的相关内容,我们来好好聊聊。
8D 的原名叫做 8 Eight-Disciplines,意思是8 个人人皆知解决问题的固定步骤;也可以称为TOPS(T eamOriented problem solving)即团队导向问题解决方法。
8D主要用于汽车及类似加工行业的问题解决方法。
原始是由Ford 公司,全球化品质管制及改善的特殊必备方法,之后已成为QS9000/ISO TS16949、福特公司的特殊要求。
9个步骤8D是解决问题的8条基本准则或称8个工作步骤,但在实际应用中却有9个步骤:1.D0:征兆紧急反应措施2.D1:小组成立3.D2:问题说明4.D3:实施并验证临时措施5.D4:确定并验证根本原因6.D5:选择和验证永久纠正措施7.D6:实施永久纠正措施8.D7:预防再发生9.D8:小组祝贺3个问题SQE在给供应商做8D报告的培训的时候,必须跟供应商讲清楚,作为供应商在撰写8D报告的时候,务必要保证下面的问题被清楚准确有理有据地回答:1.D2-问题是什么?2.D3~D6-问题如何解决?3.D7-将来该问题如何预防?7个问题然而作为SQE在审阅供应商的8D报告的时候,也务必保证以下的问题被如实回答:1.对零件的知识进行了充分的论证2.完全确定了根本原因并聚焦于该原因3.遗漏点已经被识别4.确定与根本相匹配的纠正措施5.纠正措施计划的验证已经被确定6.包括了实施纠正措施的时间计划7.有证据显示供方将把纠正措施纳入整个系统。
质量工具8D的实施过程可能用到的质量工具总结如下:可靠性/设计验证DV/产品和过程确认/潜在失效模式及后果分析FMEA/控制计划CP/PPAP文件/SPC/DOE/QC7大工具D0:征兆紧急反应措施目的:主要是为了看此类问题是否需要用8D来解决,如果问题太小,或是不适合用8D来解决的问题,例如价格,经费等等,这一步是针对问题发生时候的紧急反应。
8D解决问题的方法
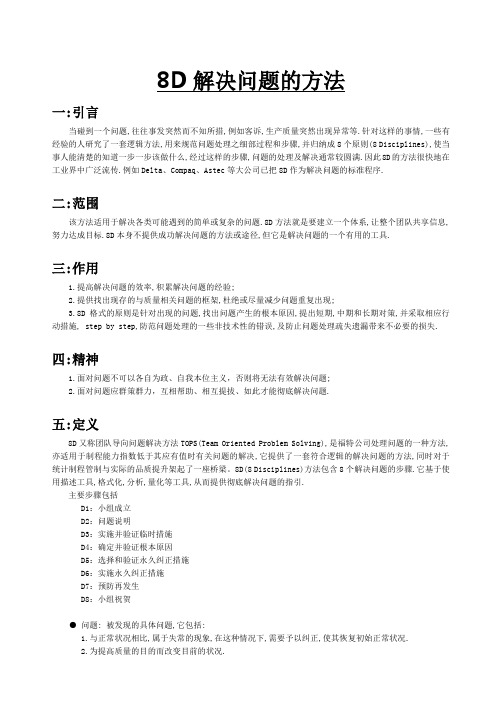
8D解决问题的方法一:引言当碰到一个问题,往往事发突然而不知所措,例如客诉,生产质量突然出现异常等.针对这样的事情,一些有经验的人研究了一套逻辑方法,用来规范问题处理之细部过程和步骤,并归纳成8个原则(8 Disciplines),使当事人能清楚的知道一步一步该做什么,经过这样的步骤,问题的处理及解决通常较圆满.因此8D的方法很快地在工业界中广泛流传.例如Delta、Compaq、Astec等大公司已把8D作为解决问题的标准程序.二:范围该方法适用于解决各类可能遇到的简单或复杂的问题.8D方法就是要建立一个体系,让整个团队共享信息,努力达成目标.8D本身不提供成功解决问题的方法或途径,但它是解决问题的一个有用的工具.三:作用1.提高解决问题的效率,积累解决问题的经验;2.提供找出现存的与质量相关问题的框架,杜绝或尽量减少问题重复出现;3.8D格式的原则是针对出现的问题,找出问题产生的根本原因,提出短期,中期和长期对策,并采取相应行动措施, step by step,防范问题处理的一些非技术性的错误,及防止问题处理疏失遗漏带来不必要的损失.四:精神1.面对问题不可以各自为政、自我本位主义,否则将无法有效解决问题;2.面对问题应群策群力,互相帮助、相互提拔、如此才能彻底解决问题.五:定义8D又称团队导向问题解决方法TOPS(Team Oriented Problem Solving),是福特公司处理问题的一种方法,亦适用于制程能力指数低于其应有值时有关问题的解决,它提供了一套符合逻辑的解决问题的方法,同时对于统计制程管制与实际的品质提升架起了一座桥梁。
8D(8 Disciplines)方法包含8个解决问题的步骤.它基于使用描述工具,格式化,分析,量化等工具,从而提供彻底解决问题的指引.主要步骤包括D1:小组成立D2:问题说明D3:实施并验证临时措施D4:确定并验证根本原因D5:选择和验证永久纠正措施D6:实施永久纠正措施D7:预防再发生D8:小组祝贺●问题: 被发现的具体问题,它包括:1.与正常状况相比,属于失常的现象,在这种情况下,需要予以纠正,使其恢复初始正常状况.2.为提高质量的目的而改变目前的状况.●纠正措施:(按ISO8402标准定义)针对现存的不合格项或缺陷所采取的纠正措施,并杜绝或尽量减少重复问题出现.●预防措施:(按ISO8402标准定义)针对潜在的不合格项或缺陷所采取的纠正措施,并杜绝或尽量减少重复问题出现.六:在下列情形中须提交8D报告1.当客户在工厂现场的稽核中发现不合格项或缺陷时,对于严重不良,主要不良及重复发生的次要不良须提交8D报告;2.OQC发现严重不良,主要不良及重复发生的次要不良须提交8D报告;3.当市场上发现有重复发生的产品缺陷时须提交8D报告;4.当ORT(持續性壽命測試)测试过程中发现缺陷时须提交8D报告;5.IPQC在同一生产现场连续发现三个位置相同不良现象或三个原因相同不良现象;6.要对那些需要长期纠正措施来解决的缺陷采取行动时,须提交8D报告;7.相关程序文件明确要求提交8D报告时.七:提交报告时间要求1.在发现问题的24小时内,提交包含所采取的暂时措施描述的8D报告;2.在发现问题的72小时内,提交包含问题发生原因的初步分析的报告.八:结论8D格式用于监控解决问题的过程,它不是一个详尽的报告或复杂的分析,描述工具,而是一个包含了解决问题的每个步骤的集合,因而可从其中找到经提炼的基本信息.九:8D流程十:8D步骤e Team ApproachEstablish a small group of people with the knowledge, time, authority and skill to solve the problemand implement corrective actions. The group must select a team leader.1.建立解决问题的团队选择一群有相关知识, 时间, 权力, 和相关技能的人组成一个小组, 来解决问题和执行对策. 从该小组中选出一个组长说明:成立一个小组,小组成员具备工艺/产品的知识,有配给的时间并授予了权限,同时应具有所要求的能解决问题和实施纠正措施的技术素质。
质量管理之8D改善

质量管理之8D改善在进行企业质量改善辅导过程中,针对一般性的质量问题,我们会推荐8D改善方法。
8D 问题解决法的处理方式是先找到根本原因、采取行动消除根本原因,并实施永久对策,此作法是有效的,而且也可以找出系统会允许此错误出现的原因。
漏失点(escapepoints)的研究就是为了提升系统侦测错误的能力,即使错误再度发生,也有能力可以检测出来。
一、什么是8D8D是福特公司以及福特供应商必须要用的解决质量问题的工具,现已成为全球化品质管理及其它领域改善的必备方法。
8D(Eight-Disciplines),意思是8个解决问题的固定步骤;也可以称为TOPS (TeamOrientedproblemsolving)即团队导向问题解决方法。
由一个准备过程和8个标准步骤组成,这些步骤用来客观地确定、定义和解决问题并防止相似问题的再次发生。
8个步骤分别为:D1:成立小组D2:问题的描述D3:实施并验证临时措施D4:确定和验证根本原因D5:选择并验证永久纠正措施D6:实施永久纠正措施D7:防止再发生D8:承认小组及个人的贡献二、为何需要8D①对于企业:当标准与实际产生差距时,由以前的责备转化成由8D的方法来解决问题通过建立小组,采用团队合作的模式进行解决问题,以助于消除部门间壁垒,提高团队合作精神小组成员来源于不同的部门,有助于提供问题有效的解决方法。
通过8D的标准步骤,可以防止相同或类似的问题重复发生。
通过建立小组训练内部合作的技巧推进有效的问题解决和预防技术改进供方整体质量、生产率、成本等防止相同或类似问题的再发生,提高顾客满意度③对于顾客增强对供方的产品和过程的信心促进供应链能力的提升使过程运营更加稳定与供方互利的关系④对于个人形成逻辑的思维能力:问题发现—问题分析—问题解决—预防再发生熟知8D的相关工具(5WHY、FMEA、控制计划、七大质量工具、SPC等)学习其他部门的相关知识培养团队意识。
三、何时使用8D针对过程中偶然发生的问题重复发生,一直没有解决的问题问题出现后,异常原因未知比较重大的问题,个人无法解决客户要求回复的质量投诉问题存在一定的改进空间四、8D的实施步骤如何制作?以一个生活中的案例来进行解答,将一步步带你进入8D改善的殿堂。
零件错装8d报告案例

零件错装8d报告案例在包装时由于经常装错和漏装零配件,给成包带来很大的隐患和麻烦,包装生产受环境制约以及不规范性的包装作业操作,错放,漏放配件仍是当前、后续长期需要控制的重点项目。
仍需从包装流程控制、QA成品检验处加严管控才是。
我想解决的是在较常见的车间环境下如何实现包装步骤的简化法:一、首件法:每批次的产品生产组装完成后,拉倒另外的地方,集中隔离进行单独包装作业。
在每一个批量包装前,先包装一件样板,由专门负责的QA检验人员对其进行全方位的测试,并作出测试报告,也叫首件报告。
后面的包装作业以此为参照。
保证了产品出厂后在商业,质量,数量,配件,备件等多方面要求的完整性,符合客户的订单要求,减少投诉和退货。
二、称重法:对于较重的产品,容易称重的产品,因其对重量敏感,采用称重法控制。
建议测试成品箱的样板重量,然后再设定一个公差值,每生产一箱成品就过一次称重,这样就可以预防减少装错,漏装的现象。
三、数控法:1、十件法,(看具体的产量,或者是每个箱子里的数量,所有的附件都是一样的数量,配套,如果最后少了,或者不配套,就能及时处理这一小批包装产品。
2、利用软件控制,把附件能够贴标签的,然后扫描。
3、制作零配件清单,放了后做点检,关键是每个工序必须留下证据,员工才有责任心,增加员工的责任感,然后有目标地对员工进行教育培训。
4、设计数控自动控制装置用来计数,每通过一次,装置就自动计数一次。
5、专门定人取东西入包装袋如果每个包装袋成在的数量有出入即不相等,就得找原因。
6、小集合包装,小零件的打包工作,比如螺钉,垫片等小的零件,不超过3种集合在一起,做成一小包。
7、最终包装工作的标准可视化,三个部分组成,每部分为约3个零件的组合。
工作的这样分下来,每个操作工简化为只针对3个元件分配,消除了复杂程度,也能提高效率。
防止漏放配件应该从多个方面去管控。
8、发料及领料数量的管控,仓库发料时应一个个的点数及称重比较核对,当然对于大批量的物料可以分批发放(比如:500或1000为一个单位进行)。
人为因素,如何回复客户8D报告
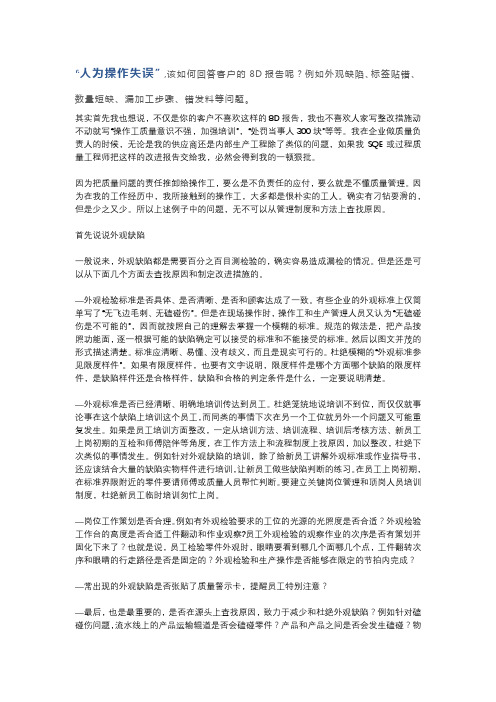
“人为操作失误”,该如何回答客户的8D报告呢?例如外观缺陷、标签贴错、数量短缺、漏加工步骤、错发料等问题。
其实首先我也想说,不仅是你的客户不喜欢这样的8D报告,我也不喜欢人家写整改措施动不动就写“操作工质量意识不强,加强培训”,“处罚当事人300块”等等。
我在企业做质量负责人的时候,无论是我的供应商还是内部生产工程除了类似的问题,如果我SQE或过程质量工程师把这样的改进报告交给我,必然会得到我的一顿狠批。
因为把质量问题的责任推卸给操作工,要么是不负责任的应付,要么就是不懂质量管理。
因为在我的工作经历中,我所接触到的操作工,大多都是很朴实的工人。
确实有刁钻耍滑的,但是少之又少。
所以上述例子中的问题,无不可以从管理制度和方法上查找原因。
首先说说外观缺陷一般说来,外观缺陷都是需要百分之百目测检验的,确实容易造成漏检的情况。
但是还是可以从下面几个方面去查找原因和制定改进措施的。
—外观检验标准是否具体、是否清晰、是否和顾客达成了一致。
有些企业的外观标准上仅简单写了“无飞边毛刺、无磕碰伤”。
但是在现场操作时,操作工和生产管理人员又认为“无磕碰伤是不可能的”,因而就按照自己的理解去掌握一个模糊的标准。
规范的做法是,把产品按照功能面,逐一根据可能的缺陷确定可以接受的标准和不能接受的标准。
然后以图文并茂的形式描述清楚。
标准应清晰、易懂、没有歧义,而且是现实可行的。
杜绝模糊的“外观标准参见限度样件”。
如果有限度样件,也要有文字说明,限度样件是哪个方面哪个缺陷的限度样件,是缺陷样件还是合格样件,缺陷和合格的判定条件是什么,一定要说明清楚。
—外观标准是否已经清晰、明确地培训传达到员工。
杜绝笼统地说培训不到位,而仅仅就事论事在这个缺陷上培训这个员工,而同类的事情下次在另一个工位就另外一个问题又可能重复发生。
如果是员工培训方面整改,一定从培训方法、培训流程、培训后考核方法、新员工上岗初期的互检和师傅陪伴等角度,在工作方法上和流程制度上找原因,加以整改,杜绝下次类似的事情发生。
漏加工,错混料的8D
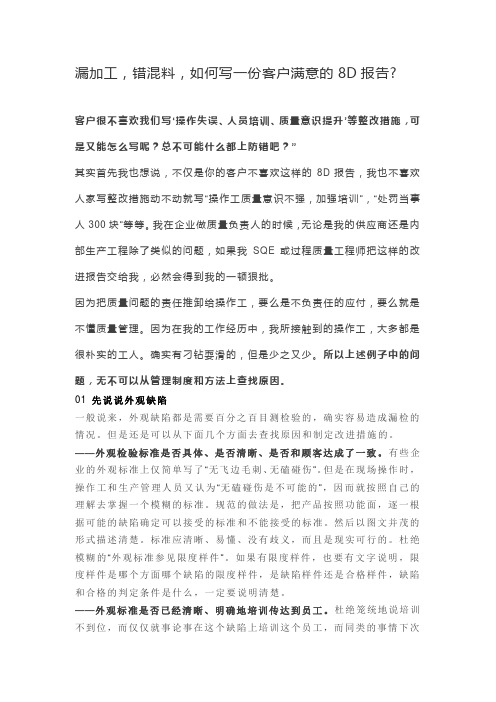
漏加工,错混料,如何写一份客户满意的8D报告?客户很不喜欢我们写‘操作失误、人员培训、质量意识提升’等整改措施,可是又能怎么写呢?总不可能什么都上防错吧?”其实首先我也想说,不仅是你的客户不喜欢这样的8D报告,我也不喜欢人家写整改措施动不动就写“操作工质量意识不强,加强培训”,“处罚当事人300块”等等。
我在企业做质量负责人的时候,无论是我的供应商还是内部生产工程除了类似的问题,如果我SQE或过程质量工程师把这样的改进报告交给我,必然会得到我的一顿狠批。
因为把质量问题的责任推卸给操作工,要么是不负责任的应付,要么就是不懂质量管理。
因为在我的工作经历中,我所接触到的操作工,大多都是很朴实的工人。
确实有刁钻耍滑的,但是少之又少。
所以上述例子中的问题,无不可以从管理制度和方法上查找原因。
01先说说外观缺陷一般说来,外观缺陷都是需要百分之百目测检验的,确实容易造成漏检的情况。
但是还是可以从下面几个方面去查找原因和制定改进措施的。
——外观检验标准是否具体、是否清晰、是否和顾客达成了一致。
有些企业的外观标准上仅简单写了“无飞边毛刺、无磕碰伤”。
但是在现场操作时,操作工和生产管理人员又认为“无磕碰伤是不可能的”,因而就按照自己的理解去掌握一个模糊的标准。
规范的做法是,把产品按照功能面,逐一根据可能的缺陷确定可以接受的标准和不能接受的标准。
然后以图文并茂的形式描述清楚。
标准应清晰、易懂、没有歧义,而且是现实可行的。
杜绝模糊的“外观标准参见限度样件”。
如果有限度样件,也要有文字说明,限度样件是哪个方面哪个缺陷的限度样件,是缺陷样件还是合格样件,缺陷和合格的判定条件是什么,一定要说明清楚。
——外观标准是否已经清晰、明确地培训传达到员工。
杜绝笼统地说培训不到位,而仅仅就事论事在这个缺陷上培训这个员工,而同类的事情下次在另一个工位就另外一个问题又可能重复发生。
如果是员工培训方面整改,一定从培训方法、培训流程、培训后考核方法、新员工上岗初期的互检和师傅陪伴等角度,在工作方法上和流程制度上找原因,加以整改,杜绝下次类似的事情发生。
漏打螺钉不良分析8D报告

编号:2013-09-03-1发生日期:2013.09.03 完成日期:2013.09.06步骤1:问题描述不合格类别归属客验RMA原件S1516L*1PCS时发现1PCS产品一侧漏打螺钉。
SN: 219801A05P9126Q01307□来料□制程□体系□成品■客验□客诉□其它: 现场稽核问题步骤2:改善小组成员执行人日期组长:张占良组员:韦礼科、黎鹏、陈春艳、赵伯贤陈春艳2013-09-03 步骤3:主要原因执行人日期原因调查、分析:1.RMA品8月底在维修部建立专线处理,在维修后直接由专人负责组装、测试、包装、检验。
但是由于是第一批生产,人员是产线上调过来的包装人员,组装部分不是很熟练,培训时虽有一对一进行,但未能完全避免问题流出。
申请时人员时提报的是3人,其中需一人检验,但是由于维修品数量两个人就可以完成,全检人员未申请到,由现有的两位人员互检,由于之前不是专职的检验人员,对异常问题敏感度低,加上人员操作方法上的变更,导致异常流出。
2.RMA返修时有提出让品质IPQC全程跟踪,但IPQC人员紧缺,未能全程跟踪。
3.OQC检验人员检验漏失,未能将问题发现出来。
韦礼科/赵伯贤/黎鹏2013-09-03步骤4:紧急对策拟定人日期1.RMA品全检外观时重点检验有无类似情况,无库存。
2.维修负责人到现场确认异常情况,将异常情况反馈给操作人员,注意此类问题。
3.OQC人员检验RMA品时特别关注外观检验。
4.不良品退回维修返工处理。
韦礼科/赵伯贤2013.9.3步骤5:永久性纠正对策拟定人日期1.定义检验内容的先后顺序。
加强培训检验标准。
2.RMA品专职负责人员记录不良案例,关注异常的发生集中性与问题容易发生的节点,同时设定不良指标进行考核。
3. 螺钉漏打给OQC警示,再发生检验过后螺钉漏打流出对责任人进行处罚。
4.后续维修必须要求IPQC跟踪,并抽检产品。
5.历史不良样品图例打印出来,给操作人员培训,并贴在作业的醒目位置。
产品混料如何写8d报告
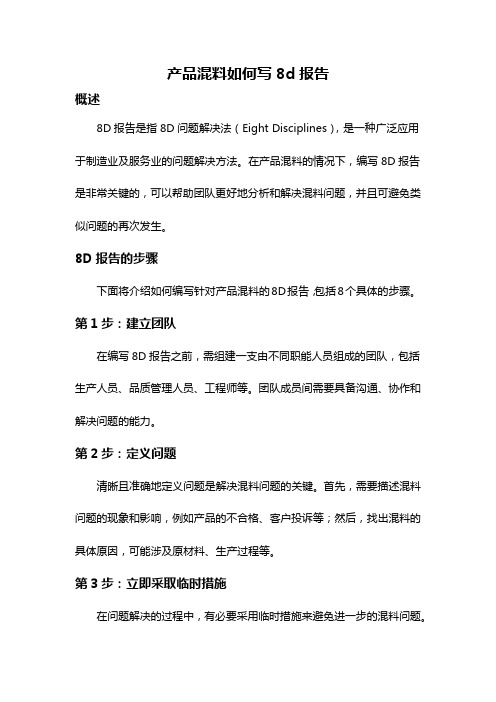
产品混料如何写8d报告概述8D报告是指8D问题解决法(Eight Disciplines),是一种广泛应用于制造业及服务业的问题解决方法。
在产品混料的情况下,编写8D报告是非常关键的,可以帮助团队更好地分析和解决混料问题,并且可避免类似问题的再次发生。
8D报告的步骤下面将介绍如何编写针对产品混料的8D报告,包括8个具体的步骤。
第1步:建立团队在编写8D报告之前,需组建一支由不同职能人员组成的团队,包括生产人员、品质管理人员、工程师等。
团队成员间需要具备沟通、协作和解决问题的能力。
第2步:定义问题清晰且准确地定义问题是解决混料问题的关键。
首先,需要描述混料问题的现象和影响,例如产品的不合格、客户投诉等;然后,找出混料的具体原因,可能涉及原材料、生产过程等。
第3步:立即采取临时措施在问题解决的过程中,有必要采用临时措施来避免进一步的混料问题。
例如,可以暂停生产线、更换原材料供应商等。
这些措施的目的是尽快降低混料问题的发生率。
第4步:确认根本原因在这一步骤中,团队需要使用质量工具(如5W1H分析、鱼骨图等)来分析混料问题的根本原因。
确定根本原因后,就可以制定针对性的解决方案。
第5步:设计纠正措施在这一步中,团队需要连同质量管理人员和工程师一起制定纠正措施。
这些纠正措施可能包括更改生产工艺、改进质量检测方法、提升员工培训能力等。
第6步:实施纠正措施在纠正措施设计好后,团队需要分配任务并确保措施的及时实施。
同时,需要确保纠正措施的有效性,可以通过进行样本检验或实地观察来验证措施的有效性。
第7步:预防措施为了避免类似问题再次发生,团队需要制定预防措施。
这可能需要改进生产流程、加强供应链管理、建立更严格的质量控制标准等。
同时,还需要对员工进行培训,提高他们的质量意识。
第8步:固化经验在解决混料问题后,团队需要总结经验教训,将解决方案进行文档化,以供未来参考。
这有助于组织积累经验,提升问题解决能力。
结论通过遵循上述步骤编写8D报告,可以帮助团队更好地解决产品混料问题,提升产品质量和客户满意度。
漏加工,错混料的8D

漏加工,错混料,如何写一份客户满意的8D报告客户很不喜欢我们写‘操作失误、人员培训、质量意识提升’等整改措施,可是又能怎么写呢总不可能什么都上防错吧”其实首先我也想说,不仅是你的客户不喜欢这样的8D报告,我也不喜欢人家写整改措施动不动就写“操作工质量意识不强,加强培训”,“处罚当事人300块”等等。
我在企业做质量负责人的时候,无论是我的供应商还是内部生产工程除了类似的问题,如果我SQE或过程质量工程师把这样的改进报告交给我,必然会得到我的一顿狠批。
因为把质量问题的责任推卸给操作工,要么是不负责任的应付,要么就是不懂质量管理。
因为在我的工作经历中,我所接触到的操作工,大多都是很朴实的工人。
确实有刁钻耍滑的,但是少之又少。
所以上述例子中的问题,无不可以从管理制度和方法上查找原因。
01先说说外观缺陷一般说来,外观缺陷都是需要百分之百目测检验的,确实容易造成漏检的情况。
但是还是可以从下面几个方面去查找原因和制定改进措施的。
——外观检验标准是否具体、是否清晰、是否和顾客达成了一致。
有些企业的外观标准上仅简单写了“无飞边毛刺、无磕碰伤”。
但是在现场操作时,操作工和生产管理人员又认为“无磕碰伤是不可能的”,因而就按照自己的理解去掌握一个模糊的标准。
规范的做法是,把产品按照功能面,逐一根据可能的缺陷确定可以接受的标准和不能接受的标准。
然后以图文并茂的形式描述清楚。
标准应清晰、易懂、没有歧义,而且是现实可行的。
杜绝模糊的“外观标准参见限度样件”。
如果有限度样件,也要有文字说明,限度样件是哪个方面哪个缺陷的限度样件,是缺陷样件还是合格样件,缺陷和合格的判定条件是什么,一定要说明清楚。
——外观标准是否已经清晰、明确地培训传达到员工。
杜绝笼统地说培训不到位,而仅仅就事论事在这个缺陷上培训这个员工,而同类的事情下次在另一个工位就另外一个问题又可能重复发生。
如果是员工培训方面整改,一定从培训方法、培训流程、培训后考核方法、新员工上岗初期的互检和师傅陪伴等角度,在工作方法上和流程制度上找原因,加以整改,杜绝下次类似的事情发生。
手把手教你写客户满意的人为操作失误8D报告

其实首先我也想说,不仅就是您得客户不喜欢这样得8D报告,我也不喜欢人家写整改措施动不动就写“操作工质量意识不强,加强培训”,“处罚当事人300块”等等。
我在企业做质量负责人得时候,无论就是我得供应商还就是内部生产工程除了类似得问题,如果我SQE或过程质量工程师把这样得改进报告交给我,必然会得到我得一顿狠批。
因为把质量问题得责任推卸给操作工,要么就是不负责任得应付,要么就就是不懂质量管理。
因为在我得工作经历中,我所接触到得操作工,大多都就是很朴实得工人。
确实有刁钻耍滑得,但就是少之又少。
所以上述例子中得问题,无不可以从管理制度与方法上查找原因。
首先说说外观缺陷一般说来,外观缺陷都就是需要百分之百目测检验得,确实容易造成漏检得情况。
但就是还就是可以从下面几个方面去查找原因与制定改进措施得。
—-外观检验标准就是否具体、就是否清晰、就是否与顾客达成了一致。
有些企业得外观标准上仅简单写了“无飞边毛刺、无磕碰伤”。
但就是在现场操作时,操作工与生产管理人员又认为“无磕碰伤就是不可能得",因而就按照自己得理解去掌握一个模糊得标准、规范得做法就是,把产品按照功能面,逐一根据可能得缺陷确定可以接受得标准与不能接受得标准、然后以图文并茂得形式描述清楚。
标准应清晰、易懂、没有歧义,而且就是现实可行得。
杜绝模糊得“外观标准参见限度样件”。
如果有限度样件,也要有文字说明,限度样件就是哪个方面哪个缺陷得限度样件,就是缺陷样件还就是合格样件,缺陷与合格得判定条件就是什么,一定要说明清楚。
——外观标准就是否已经清晰、明确地培训传达到员工。
杜绝笼统地说培训不到位,而仅仅就事论事在这个缺陷上培训这个员工,而同类得事情下次在另一个工位就另外一个问题又可能重复发生。
如果就是员工培训方面整改,一定从培训方法、培训流程、培训后考核方法、新员工上岗初期得互检与师傅陪伴等角度,在工作方法上与流程制度上找原因,加以整改,杜绝下次类似得事情发生、例如针对外观缺陷得培训,除了给新员工讲解外观标准或作业指导书,还应该结合大量得缺陷实物样件进行培训,让新员工做些缺陷判断得练习、在员工上岗初期,在标准界限附近得零件要请师傅或质量人员帮忙判断。
锣板未锣穿漏锣等异常8D报告格式 (2)
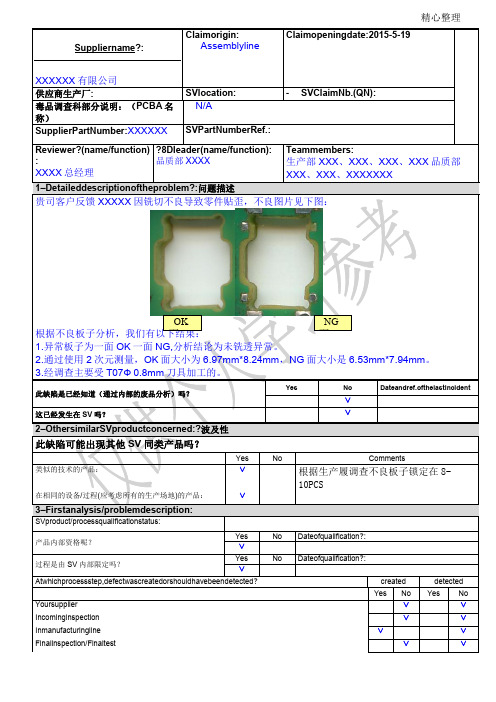
Claimorigin: Assemblyline
精心整理 Claimopeningdate:2015-5-19
XXXXXX 有限公司 供应商生产厂: 毒品调查科部分说明:(PCBA 名 称)
SupplierPartNumber:XXXXXX
SVlocation: N/A
∨
类似的技术的产品: 在相同的设备/过程(应考虑所有的生产场地)的产品:
Yes
No
Comments
∨
根据生产履调查不良板子锁定在 8-
10PCS
∨
3–Firstanalysis/problemdescription:
SVproduct/processqualificationstatus:
产品内部资格呢?
N/A
5–Finalanalysis/validatedrootcause?:最终原因
验证整个过程的根源:执行分析:5 米/何人、何事,哪里时,为何,如何/5 为什么/制造或生产位置,更改/不合格过程、培训、维护
通过减少影响的经过验证的根本原因
Rootcause %
负责人进行验证
Serviceorfunction
OK
偏短 由于作业员未按照要求作业,本应对每支上机前的刀具 需测量长度、直径,而作业员只是测量了直径,忽略了 长度测量,因此加上 4#铣切设备侦器下测深度设置太 深,而对于刀具偏短无法检测出。(请参考下面的照 片)
测刀器未测刀 时状态。
测刀状态,下 测深度设置太 深,引起刀具 偏短检测不 到。 在这个时候,机器会判断为刀具长度是正常的,就接着 开始加工,从而产生了不良。 6–Finalcorrectiveactionplan:改善 对所有的根本原因,在第 5 章中得到验证的行动。 Pilot
漏检分析改善8d报告ppt
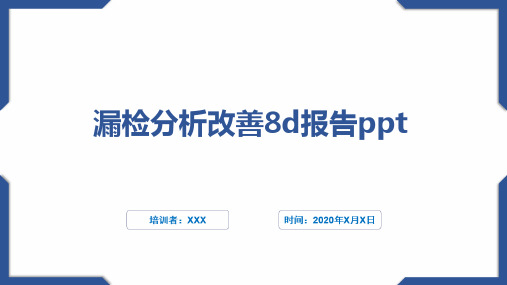
8D问题解决法是在汽车产业、组装及其他产业中, 利用团队方式结构性彻底解决问题时的标准作法。
指定团队成员人员,明 确分工,建立目标建立 规则制度,建立时间表
指定一个Champion和团队 Leader定义团队角色,开 始团队建设活动
掌握8D实施的步骤
用一个简短的说明描述对象和它的缺陷或问题
领导太多,角色没有正确定义时 间限制,缺乏足够的沟通 缺少管理层的支持,聚焦在错误 的伪命题,缺乏领导力
阳光灿烂,然而这次在阳光下,我们的心中却有着别样
品质不良回复 的感动,我们长大了。在领导们的发言结束后,依旧是
掌声雷动,这掌声是献给领导们的,更是献给我们自己
的!在这六天里,也许有过因训练强度过大而产生的埋
怨,也许有过因想念家人而彻夜未眠,也许品有质过因不饭菜良 回 复 报 告 培 训
不和胃口而
汇报人:XXX
漏检分析改善8d报告ppt
每每喊完,我们总能看到教官或是老师脸上那浅浅的微
笑,而这时,我们的心也是无比的舒畅,原来尊重他人,
赢得微笑自己也会感到快乐。......六天的时光悄然过去,
激动人心的是离开前的阅兵式。在三次紧张的彩排后,
8D 阅兵式正式开始了。伴随着激昂的进行曲,和着教官那
有力的口号声,我们踏着整齐的步伐,喊着响亮的方号, 一个个昂首挺胸,目光闪烁着从未有过的坚定。依旧是
目录 的军训生活那些我们一起军训的日子郯城一中2012级
22班杜礼贝初秋的阳光依旧像盛夏时那般热情,巨大的 火球高高地挂在我们头顶上,风无力的从我们脸颊掠过, 我们承受着这股热情,双眼被它刺激地无精打采地眯着,
CZ574220漏加工8D报告
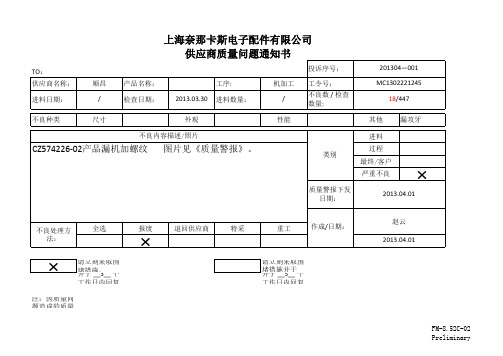
赵云 2013.04.01
FM-8.52C-02 Preliminary
CZ574226-02产品漏机加螺纹 图片见《质量警报》。
类别
质量警报下发 日期:
进料
过程
最终/客户
严重不良
×
Hale Waihona Puke 2013.04.01不良处理方
全选
报废
法:
×
×
请立刻采取围 堵并措于施__。3__ 个
工作日内回复
注:因质量问 题造成的质量
退回供应商
特采
重工
作成/日期:
请立刻采取围 堵并措于施__并5_于_ 个 工作日内回复
上海奈那卡斯电子配件有限公司 供应商质量问题通知书
TO: 供应商名称:
进料日期:
顺昌 /
产品名称: 检查日期:
工序: 2013.03.30 进料数量:
机加工 /
投诉序号:
工令号: 不良数 / 检查 数量:
201304—001 MC1302221245
18/447
不良种类
尺寸
外观
性能
其他 漏攻牙
不良内容描述/照片
8D分析-不合格品控制的8D方法

D3: 开发临时纠正措施
应考虑的问题
所有可疑地点的库存是否清查? 供方现场、仓库、分供方现场、顾客现场、下一个顾 客现场、其他遏制的有效性是多少? 遏制的有效性是否满意? 遏制措施的日期列出了吗? 筛选结果列出已筛选数,发现缺陷了吗? 筛选的方法提到了吗? 筛选的方法是否满意? 遏制措施是否单独包括审核? 短期纠正措施列出了吗?
2017/8/3
继续8D过程
注: 这些描述只代表理想的问题解决方式,实际
上,真实情况并非和在此描述的一样,努力获取
供方和顾客之间的积极联系将有助于发生问题得 到快速和容易的改进。
2017/8/3
完成8D过程
一般地,顾客会要求应在一定期限内完成8D过程。 例子:在福特,该期限是30天。对于某些问题,30天可能不够。当存 在要求超过30天的状况时,供方应向福特提供最新 为什么根本原因没有被确定和验证? 书面文件指出:
2017/8/3
D3: 开发临时纠正措施
常见性错误
筛选材料的检验是一个不令人满意的遏制措施。 所有可疑地
点的库存没有清查,不合格品重新进入生产 SPC数据
FMEA
。
2017/8/3
S公司的临时纠正措施如下
1.所有库存之H00651A50产品在收到顾客8D要进行了检查,结 果如下:
质量问题已经被定义了吗?? 质量问题已经被定量化了吗? ERA的需求是否已经评估? 如果采取ERA,验证了吗? 如果采取ERA,确认了吗?
质量工具
趋势图 排列图 Paynter图
2017/8/3
D1: 成立小组
关注的问题
任命领导者了吗? 小组中有分供方吗? 小组中有顾客吗? 小组中有其他相关人员吗?
混料8d报告
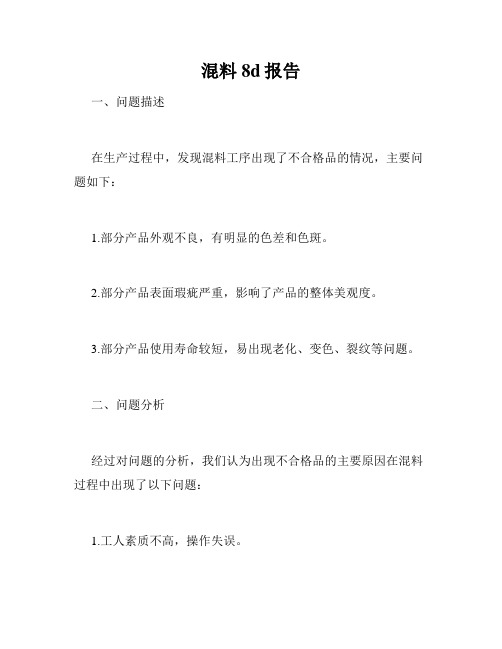
混料8d报告
一、问题描述
在生产过程中,发现混料工序出现了不合格品的情况,主要问题如下:
1.部分产品外观不良,有明显的色差和色斑。
2.部分产品表面瑕疵严重,影响了产品的整体美观度。
3.部分产品使用寿命较短,易出现老化、变色、裂纹等问题。
二、问题分析
经过对问题的分析,我们认为出现不合格品的主要原因在混料过程中出现了以下问题:
1.工人素质不高,操作失误。
2.混料机的质量存在一定的问题,容易导致混料不均匀。
3.原料的质量不稳定,存在一定的色差和异物。
三、解决方案
1.提高工人素质,加强培训,严格执行操作规程,减少操作失误。
2.购买新的混料机,并定期维护保养,确保混料的均匀性。
3.对于原料质量不稳定的问题,我们将与供应商沟通,要求提供更加稳定的原料,并加强原料的检验工作。
四、措施效果
经过以上的改进和措施,我们取得了一定的成效。
1.产品的外观得到了进一步的改善,色差和色斑问题得到了显著的改善。
2.产品的表面质量得到了一定的提升,瑕疵问题得到了部分缓解,整体美观度得到了一定的改善。
3.产品的使用寿命得到了一定的延长,老化、变色、裂纹等问题也得到了初步的解决。
五、结论
通过我们的努力,混料工序的问题得到了较为有效的解决,产品质量得到了较大的改善,我们将继续加强管理和控制,确保生产过程中各个环节的质量得到有效的保障,为用户提供更加优质可靠的产品。
注塑件料头漏处理8d的工艺流程详解

注塑件料头漏处理8d的工艺流程详解下载提示:该文档是本店铺精心编制而成的,希望大家下载后,能够帮助大家解决实际问题。
文档下载后可定制修改,请根据实际需要进行调整和使用,谢谢!本店铺为大家提供各种类型的实用资料,如教育随笔、日记赏析、句子摘抄、古诗大全、经典美文、话题作文、工作总结、词语解析、文案摘录、其他资料等等,想了解不同资料格式和写法,敬请关注!Download tips: This document is carefully compiled by this editor. I hope that after you download it, it can help you solve practical problems. The document can be customized and modified after downloading, please adjust and use it according to actual needs, thank you! In addition, this shop provides you with various types of practical materials, such as educational essays, diary appreciation, sentence excerpts, ancient poems, classic articles, topic composition, work summary, word parsing, copy excerpts, other materials and so on, want to know different data formats and writing methods, please pay attention!注塑件料头漏处理8D的工艺流程详解一、问题描述1.1 问题现象:注塑件料头出现漏料现象,严重影响产品质量和生产效率。
8D解决问题的方法
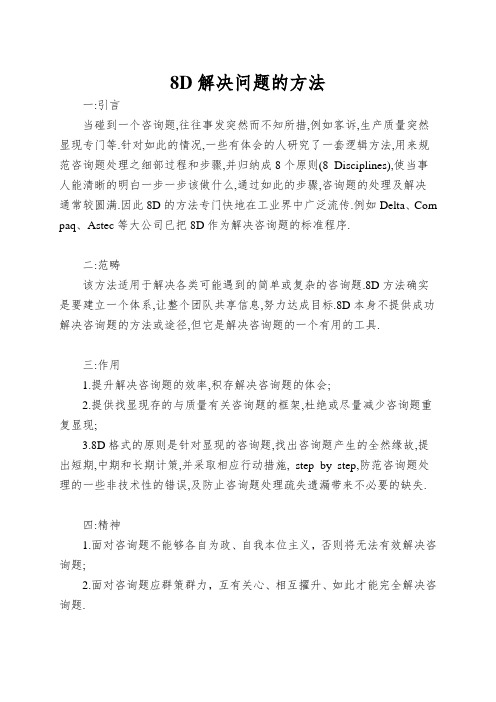
8D解决问题的方法一:引言当碰到一个咨询题,往往事发突然而不知所措,例如客诉,生产质量突然显现专门等.针对如此的情况,一些有体会的人研究了一套逻辑方法,用来规范咨询题处理之细部过程和步骤,并归纳成8个原则(8 Disciplines),使当事人能清晰的明白一步一步该做什么,通过如此的步骤,咨询题的处理及解决通常较圆满.因此8D的方法专门快地在工业界中广泛流传.例如Delta、Com paq、Astec等大公司已把8D作为解决咨询题的标准程序.二:范畴该方法适用于解决各类可能遇到的简单或复杂的咨询题.8D方法确实是要建立一个体系,让整个团队共享信息,努力达成目标.8D本身不提供成功解决咨询题的方法或途径,但它是解决咨询题的一个有用的工具.三:作用1.提升解决咨询题的效率,积存解决咨询题的体会;2.提供找显现存的与质量有关咨询题的框架,杜绝或尽量减少咨询题重复显现;3.8D格式的原则是针对显现的咨询题,找出咨询题产生的全然缘故,提出短期,中期和长期计策,并采取相应行动措施, step by step,防范咨询题处理的一些非技术性的错误,及防止咨询题处理疏失遗漏带来不必要的缺失.四:精神1.面对咨询题不能够各自为政、自我本位主义,否则将无法有效解决咨询题;2.面对咨询题应群策群力,互有关心、相互擢升、如此才能完全解决咨询题.五:定义8D又称团队导向咨询题解决方法TOPS(Team Oriented Problem Solvi ng),是福特公司处理咨询题的一种方法,亦适用于制程能力指数低于其应有值时有关咨询题的解决,它提供了一套符合逻辑的解决咨询题的方法,同时关于统计制程管制与实际的品质提升架起了一座桥梁。
8D(8 Disciplines)方法包含8个解决咨询题的步骤.它基于使用描述工具,格式化,分析,量化等工具,从而提供完全解决咨询题的指引.要紧步骤包括D1:小组成立D2:咨询题讲明D3:实施并验证临时措施D4:确定并验证全然缘故D5:选择和验证永久纠正措施D6:实施永久纠正措施D7:预防再发生D8:小组祝贺●咨询题: 被发觉的具体咨询题,它包括:1.与正常状况相比,属于失常的现象,在这种情形下,需要予以纠正,使其复原初始正常状况.2.为提升质量的目的而改变目前的状况.●纠正措施:(按ISO8402标准定义)针对现存的不合格项或缺陷所采取的纠正措施,并杜绝或尽量减少重复咨询题显现.●预防措施:(按ISO8402标准定义)针对潜在的不合格项或缺陷所采取的纠正措施,并杜绝或尽量减少重复咨询题显现.六:在下列情形中须提交8D报告1.当客户在工厂现场的稽核中发觉不合格项或缺陷时,关于严峻不良,要紧不良及重复发生的次要不良须提交8D报告;2.OQC发觉严峻不良,要紧不良及重复发生的次要不良须提交8D报告;3.当市场上发觉有重复发生的产品缺陷时须提交8D报告;4.当ORT(持續性壽命測試)测试过程中发觉缺陷时须提交8D报告;5.IPQC在同一生产现场连续发觉三个位置相同不良现象或三个缘故相同不良现象;6.要对那些需要长期纠正措施来解决的缺陷采取行动时,须提交8D报告;7.有关程序文件明确要求提交8D报告时.七:提交报告时刻要求1.在发觉咨询题的24小时内,提交包含所采取的临时措施描述的8D报告;2.在发觉咨询题的72小时内,提交包含咨询题发生缘故的初步分析的报告.八:结论8D格式用于监控解决咨询题的过程,它不是一个详尽的报告或复杂的分析,描述工具,而是一个包含了解决咨询题的每个步骤的集合,因而可从其中找到经提炼的差不多信息.九:8D流程十:8D步骤e Team ApproachEstablish a small group of people with the knowledge, time, authority and skill to solve the problemand implement corrective actions. The group must select a team lead er.1.建立解决咨询题的团队选择一群有有关知识, 时刻, 权力, 和有关技能的人组成一个小组, 来解决咨询题和执行计策. 从该小组中选出一个组长讲明:成立一个小组,小组成员具备工艺/产品的知识,有配给的时刻并授予了权限,同时应具有所要求的能解决咨询题和实施纠正措施的技术素养。
SMT错料8D改善报告

吴朝建/杨小兰
2016/5/18
Corrective action(纠正行动)
Responsible(负责人)
Date Implemented (导入日期):
1、重新理顺物料员工作,要求写站位在线外完成并按上料表顺序摆
放,由物料员完成并确认是否有误,上线后第一个班次由班长安排对
写好的站位再次确认,如果有站位写错,将对物料员按错料处理。
Effectiveness(有效性)
(紧急应变行
动)
吴朝建
2016年5月17日 20:30分
Responsible(负责人) Date(日期):
1、1.经确认隔离1469PCS全部在返工.
Escape cause investigation (流出原因分析)
Responsible(负责人) Date(日期):
CLOSE □再次发生,仍需解决 □多次改善无效果,建议成立专案小组处理 (问题关闭) □关闭,异常已解决
Responsible(负责人) Date(日期):
Responsible(负责人)
Date Implemented (导入日期):
PreparedBy/Date:
Approved By/ Date: 杨小兰
4、要求IT部全力配合完成IMS防错料功能的实现。今天开始培训。起
到系统作用,杜绝错料事故的发生。
吴朝建/杨小兰
2016/5/18
Preventive action(预防措施)
D6
Preventive Action (预防
措施)
G350错料培训记录 .docx
培训 写真
Responsible(负责人)
IPQC对料必须严格按流程作业,样品测值后必须核对与上料记录表上
8D分析法,工厂这样有效解决不良问题

8D分析法,工厂这样有效解决不良问题!8D(8 Disciplines)即问题解决8步法,最早是福特公司使用的经典质量问题分析手法,对于解决工厂中存在的问题是一个很有用的工具,尤其在面对重大不良时,它能建立一个体系,让整个团队共享信息,并引导团队提供解决问题的方法。
工作中,你有没有过这样的感触:1. XX现象已经反映了好几天了,怎么不见有人反馈呢?2. XX事件解决方法大家都知道,可是没有人愿意解决,我也一直推不动。
3. 这个不良现象到底是什么,为什么现在查到的和当时得知的不一样呢?4. 都已经让XX部门全检了,怎么又发现不良了呢?5. 这个不良一直反复发生,XX部门根本解决不掉!6. XX不良记得已经解决了呀,怎么还在发生呢?7. 原来XX SBU以前处理过这个问题,我们去看看他们怎么处理的。
8. 每天都在被各种各样的异常翻来覆去的折腾,根本没有时间好好整理报告!8D方法由8个步骤和1个准备步骤组成,客观地确定、定义和解决问题并防止相似问题的再次发生。
8D方法应用流程:01D1组建问题解决团队8D原名就是叫团队导向问题解决步骤,8D小组需要由具备产品及制程知识,能支配时间且拥有职权及技能的人士组成,必须指定一名8D团队组长。
不具备以上条件的8D是失败的8D,它没法在你需要资源解决问题时提供帮助。
若一个体系出现了质量异常,绝非单一部门职能失效,否则整个体系需要重新进行完善。
8D团队的角色构成:8D负责人:作为8D项目支持者的身份参与8D项目。
没有负责人的签字8D报告不能进行关闭审批。
8D组长:负责8D全过程的进行直至问题解决、8D项目关闭8D组员:在组长的协调下利用自身知识与技能参与8D 问题的解决确定团队成员应注意的问题:团队人数:4~10人组长的选择:部门经理指定本部门人员或亲自担任组员的选择原则:与问题相关且具备相关的资源、能力D1的常见性错误:选择的8D团队成员对涉及问题没有相关知识或认识;只有一两个人实施8D过程。
- 1、下载文档前请自行甄别文档内容的完整性,平台不提供额外的编辑、内容补充、找答案等附加服务。
- 2、"仅部分预览"的文档,不可在线预览部分如存在完整性等问题,可反馈申请退款(可完整预览的文档不适用该条件!)。
- 3、如文档侵犯您的权益,请联系客服反馈,我们会尽快为您处理(人工客服工作时间:9:00-18:30)。
漏加工,错混料,如何写一份客户满意的8D报告?客户很不喜欢我们写’操作失误、人员培训、质量意识提升’等整改措施,可是又能怎么写呢?总不可能什么都上防错吧?”其实首先我也想说,不仅是你的客户不喜欢这样的8D报告,我也不喜欢人家写整改措施动不动就写“操作工质量意识不强,加强培训”,“处罚当事人300块”等等。
我在企业做质量负责人的时候,无论是我的供应商还是内部生产工程除了类似的问题,如果我SQE或过程质量工程师把这样的改进报告交给我,必然会得到我的一顿狠批。
因为把质量问题的责任推卸给操作工,要么是不负责任的应付,要么就是不懂质量管理。
因为在我的工作经历中,我所接触到的操作工,大多都是很朴实的工人。
确实有刁钻耍滑的,但是少之又少。
所以上述例子中的问题,无不可以从管理制度和方法上查找原因。
01先说说外观缺陷一般说来,外观缺陷都是需要百分之百目测检验的,确实容易造成漏检的情况。
但是还是可以从下面几个方面去查找原因和制定改进措施的。
——外观检验标准是否具体、是否清晰、是否和顾客达成了一致。
有些企业的外观标准上仅简单写了“无飞边毛刺、无磕碰伤”。
但是在现场操作时,操作工和生产管理人员又认为“无磕碰伤是不可能的”,因而就按照自己的理解去掌握一个模糊的标准。
规范的做法是,把产品按照功能面,逐一根据可能的缺陷确定可以接受的标准和不能接受的标准。
然后以图文并茂的形式描述清楚。
标准应清晰、易懂、没有歧义,而且是现实可行的。
杜绝模糊的“外观标准参见限度样件”。
如果有限度样件,也要有文字说明,限度样件是哪个方面哪个缺陷的限度样件,是缺陷样件还是合格样件,缺陷和合格的判定条件是什么,一定要说明清楚。
——外观标准是否已经清晰、明确地培训传达到员工。
杜绝笼统地说培训不到位,而仅仅就事论事在这个缺陷上培训这个员工,而同类的事情下次在另一个工位就另外一个问题又可能重复发生。
如果是员工培训方面整改,一定从培训方法、培训流程、培训后考核方法、新员工上岗初期的互检和师傅陪伴等角度,在工作方法上和流程制度上找原因,加以整改,杜绝下次类似的事情发生。
例如针对外观缺陷的培训,除了给新员工讲解外观标准或作业指导书,还应该结合大量的缺陷实物样件进行培训,让新员工做些缺陷判断的练习。
在员工上岗初期,在标准界限附近的零件要请师傅或质量人员帮忙判断。
要建立关键岗位管理和顶岗人员培训制度,杜绝新员工临时培训匆忙上岗。
——岗位工作策划是否合理。
例如有外观检验要求的工位的光源的光照度是否合适?外观检验工作台的高度是否合适工件翻动和作业观察?员工外观检验的观察作业的次序是否有策划并固化下来了?也就是说,员工检验零件外观时,眼睛要看到哪几个面哪几个点,工件翻转次序和眼睛的行走路径是否是固定的?外观检验和生产操作是否能够在限定的节拍内完成?——常出现的外观缺陷是否张贴了质量警示卡,提醒员工特别注意?——最后,也是最重要的,是否在源头上查找原因,致力于减少和杜绝外观缺陷?例如针对磕碰伤问题,流水线上的产品运输辊道是否会磕碰零件?产品和产品之间是否会发生磕碰?物流周转工装是否合理?是否存在工件堆叠?员工操作过程、工件摆放过程是否存在磕碰风险?02 贴错标签标签贴错在很多主机厂客户来说,也是一个很严重的问题。
在有些客户那里如果发生标签贴错两次就可能直接导致受控发运。
标签贴错可以从如下几个角度考虑改进。
——现场打印,随用随打印,禁止事先打印标签。
一般来说要求严格的主机厂会要求供应商在生产线的包装工位设置标签打印机。
如果企业有多条生产线就应该在每条线边的下线包装工位设置独立的标签打印机。
杜绝在办公室里打印了一堆的标签。
有些企业有各种不同产品的,也可能有不同批次的,喜欢在办公室统一打印一堆标签,然后一堆标签拿到生产线边,包装时再从一堆标签里翻找出来贴上。
或者先包装后,很多的包装箱堆叠在一起,然后一起贴标签。
甚至有的企业在包装后放置几天,发运前再贴标签。
这些不正确的做法,不出现问题才是不正常的。
——如果客户没有独立打印机的明确要求,而且企业一时还不能做到独立标签打印机,也可以采用换型防错的方法来保证标签正确。
换型防错的方法,我以后有机会再单独写文章介绍。
简单地说,就是在多种产品共线生产的情况下,当准备切换加工某一种型号产品时,把原材料、产成品、半成品、工装、刀具、工具、辅具、各种作业指导书、各种记录表、包装材料,包括设备里面调用的程序和工艺参数,当然也包括标签,统统切换成准备生产的产品型号相一致的。
而不一致的,确保从生产线上,从操作者可以拿到的范围内撤离或者封盖起来。
使得误拿误用成为不可能,这就叫换型防错。
在换型时,操作工利用《换型防错点检表》点检并记录所有的软硬件的切换得到了落实,班组长互检。
03 数量短缺问题我也不赞同增加人员互检,因为效率很低。
那么除了采用计数器之外,还可以从如下角度考虑改进:——如果是规则的产品,应该整齐摆放。
一个包装盒或者一个料箱固定几排几列几层,这样点检数量就转换成了对排列形状的外观检查,数量确认就变得很直观。
——如果同时在防护磕碰、挤压方面有要求,那就考虑定制成型吸塑盒、或带有分隔板的料盒来摆放产品,一个萝卜一个坑。
坑没填满,缺件了,就是数量不够。
——称重法。
但是在零件数量很多,每个件的重量又在一定范围内波动时,就可能导致称重判定数量时的不准确。
这时可以考虑在大包装内设置若干的小包装,而小包装的数量设置要考虑到总重量的波动范围的西格玛小于一个零件重量的六分之一。
04 漏加工除了设置连续的生产线,设置过程防错之外,还可以从以下方面考虑改进:——增加自检和互检,在每道序放行之前,操作者检验自行检验本道序加工的内容是否完成,检验后放行或者再放入料架料盒。
下道序在加工前检验上道序的加工或装配内容是否完成。
——定置管理,定位存放。
如果是单机作业,每个单机工位待加工件和已加工件一定要分开摆放,定置摆放。
一般地,左手边是待加工件,右手边是已加工件。
严禁混放,严禁待加工已加工件放置在同一料架或料盒。
在在制品周转区,整料箱的在制品也要各个不同工序状态的产品分区摆放,且做好明显标识。
——悬挂工序随行卡。
针对单机作业的生产线,料架或料车要悬挂随行卡,在随行卡上标明工序状态。
05 发错料最常见的错误是一个大包装多数正确的产品里面混进来一两只不同型号的产品。
一般是由下列原因造成的,把这些方面改掉了,也就基本杜绝了混料问题。
——针对这样的问题,最基本原因就是没有做好换型防错。
在生产工位、在生产线边存在不同型号的产成品、在制品同时存在的现象。
——或者在包装区、检验区,不同型号的产品同时存在,散放、混放。
所以定置管理、5S,还是最基本的要求,不是简单的干净整齐的而已。
除上述问题之外,还有一个被供应商常常使用的原因,就是“调试件被混在了合格件里报交”。
这也是被我和很多主机厂的SQE们所深恶痛绝的一个说法。
我们常常会追问,你怎么确定那个件就是调试件的?零件上有追溯号吗?调试件的检验记录和追溯号相对应吗?即使真的是调试件被混入合格品的话,企业也需要在不合格品定置摆放和标识、调试品定置摆放和标识、开机前检查确认、首件确认,等几个方面的管理方法加以原因分析和改进。
而不是简单地归结为认为操作失误。
8D 起源于福特公司处理质量问题的一种方法。
凡是福特公司的供应商遇到问题必须强制用这种方法。
后来这方法好,其他的非福特公司的供应商也引进这方法处理问题。
就这样家喻户晓,各行业通吃。
而且不仅仅解决工作问题,解决家庭生活问题也很有效。
在这里仅分享下8D 在处理质量问题上的应用。
1、D0 现象及应急反应活动根据现象评估8D 过程是否需要。
如果有必要,采取紧急反应行动(ERA)来保护顾客,并开始8D过程。
8D过程区别了症状和问题。
适用标准的大部分是症状。
没有症状,不会知道有问题。
症状是一个显示存在一个或多个问题的可测量的事件或结果。
这个事件的后果必须被一个或多个顾客经历;问题是指同期望有偏差或任何由未知原因引起的有害的后果;症状是问题的显示。
当收到投诉信息时,质量部门应尽量在客户投诉报告上确认以下信息以便展开调查:产品编号及品名客户名称,联系人及地址缺陷描述,不合格品数量追溯信息,如LOT NO ,发货单编号等索赔应尽量取得车型等信息如有,应从客户处得到样品,照片,标签及不合格率等必要的信息。
如是芯体泄露或严重投诉,收到投诉的人应立即通知质量经理及总经理。
QE 应在收到投诉一个工作日内与客户联系。
应就以下信息与客户沟通:跨部门小组及联系方式确认已得到的信息调查问题所必需的其他信息应急措施的进展应急措施及纠正措施的预期完成时间任何其它的客户要求,如,了解问题进展和期望的交货所有与客户之间的回复均应记录。
QE 根据得到信息,依据三现主义(现场,现物,现象)来确认不良状况;如果是可以目视的不良,尽量取得照片或样品(确认现物);对于不良发生场所状况尽量收集详细的情报(确认现场,现象)。
应急措施需要在24 小时内展开。
2、D1 建立8D 小组没有团队的8D是失败的8D。
其实8D原名就是叫团队导向问题解决步骤。
8D 小组需要由具备产品及制程知识,能支配时间,且拥有职权及技能的人士组成。
同时需指定一名8D 团队组长。
因为我们要做的是:建立一个由具备过程/成品知识的人员组成小组确定时间,职责和所需学科的技术确定小组负责人3、D2 问题描述通过确定可定量化的项谁,什么,何时,何地,为什么,如何,多少(5W2H),识别对象和缺陷(问“什么出现了什么问题”):“什么问题”是缺陷“什么出了问题”是对象问“什么出现了什么问题”能够帮助小组以问题陈述所需的两个基本要素为中心(对象和缺陷)。
收到客户不良样件操作流程:确认不良样件生产日期。
确认外观基本情况,拍照留下证据。
按正常生产流程确认不良样件是否能再现记录下确认数据,拍照或视频留下证据。
根据生产日期查找当时FTT 情况,确认当时是否有同样或类似不良。
根据生产日期确认人机料法环等有无变化点。
不再现时(NTF )按不再现操作流程进行4、D3 遏制措施ICA确定并实施遏制措施,隔离问题的后果与一切内/外部顾客,验证遏制措施的有效性。
ICA是保护顾客免受一个或多个问题的症状影响的任何行动:处理问题的症状在执行前验证有效性在执行过程中监控形成文件ICA 需要在3个工作日内确定并执行,围堵范围是客户处库存、在途品、厂内库存品数量并进行相关处理(退货、重工、报废等)。
5、D4 根本原因分析查找真正的原因,只有找到真因,方可有效解决问题。
如果仅仅只是糊弄糊弄应付了事,没有什么意义。
因此要找出一切潜在原因,对潜在原因逐个试验,隔离并验证根本原因,确定不同的纠正措施以消除根本原因;使用鱼骨图、FTA、头脑风暴等质量工具找出所有可能因素,并进行验证,最终找到根本发生原因和流出原因。