磷化培训PPT资料
磷化培训资料

针对不同原因采取相应的措施,如延长磷化时间、调整磷化 温度、调整游离酸度、调整金属离子含量、更换合适的磷化 剂等。
磷化后表面出现锈蚀
原因
磷化后表面出现锈蚀可能是由于磷化膜质量差、磷化后清洗不干净、磷化液 中杂质的腐蚀、磷化后未进行钝化处理等因素造成的。
解决方案
针对不同原因采取相应的措施,如提高磷化膜质量、加强磷化后清洗、降低 磷化液中杂质含量、加强磷化后钝化处理等。
磷化质量的影响因素与控制措施
磷化质量的影响因素
温度、时间、浓度、酸碱度、表面活性剂等。
控制措施
严格控制磷化处理的温度、时间、浓度、酸碱度等参数,同时加入适量的表面活 性剂,以保证磷化处理的效果和稳定性。
05
磷化常见问题与解决方案
磷化膜质量差
原因
磷化膜质量差可能是由于磷化处理时间过短、温度过低、游 离酸度过低、金属离子含量过高或过低、磷化剂选择不当等 因素造成的。
处理剂的配方和性能。
结合新型磷化处理剂的应用特 点,开发与之相适应的设备和
工艺流程。
节能减排和环保的磷化技术发展趋势
开发和推广节能减排的磷化技术,如低温磷化、常温磷化及无渣磷化等。 加强环保型磷化技术的研发和应用,减少对环境的污染和危害。
针对磷化废液的处理和回收利用,研究和开发出更为环保和高效的处理技术。
解决方案
针对不同原因采取相应的措施,如提高磷化温度和延长磷化 时间以增加磷化膜厚度、选用适当的磷化剂和金属离子含量 以提高磷化膜质量、加强基体金属表面处理等。
06
磷化技术的未来发展
新型磷化处理剂的研究与应用
针对不同金属材质和不同环境 条件,研究开发出新型、高效
、环保的磷化处理剂。
针对新型磷化处理剂的应用效 果,开展深入研究,不断优化
磷化实用技术讲座

磷化实用技术讲座磷化(I)——基本原理及分类磷化是一种化学与电化学反应形成磷酸盐化学转化膜的过程,所形成的磷酸盐转化膜称之为磷化膜。
磷化的目的主要是:给基体金属提供保护,在一定程度上防止金属被腐蚀;用于涂漆前打底,提高漆膜层的附着力与防腐蚀能力;在金属冷加工工艺中起减摩润滑使用。
1 基本原理磷化过程包括化学与电化学反应。
不同磷化体系、不同其材的磷化反应机理比较复杂。
虽然科学家在这方面已做过大量的研究,但至今未完全弄清楚。
在很早以前,曾以一个化学反应方程式简单表述磷化成膜机理:8Fe+5Me(H2PO4)2+8H2O+H3PO4 Me2Fe(PO4)2·4H2O(膜)+Me3(PO4)·4H2O(膜)+7FeHPO4(沉渣)+8H↑Me为Mn、Zn 等,Machu等认为,钢铁在含有磷酸及磷酸二氢盐的高温溶液中浸泡,将形成以磷酸盐沉淀物组成的晶粒状磷化膜,并产生磷酸一氢铁沉渣和氢气。
这个机理解释比较粗糙,不能完整地解释成膜过程。
随着对磷化研究逐步深入,当今,各学者比较赞同的观点是磷化成膜过程主要是由如下4个步聚组成:① 酸的浸蚀使基体金属表面H+浓度降低Fe – 2e→ Fe2+2H2-+2e→2[H] (1)H2② 促进剂(氧化剂)加速[O]+[H] → [R]+H2OFe2++[O] → Fe3++[R]式中[O]为促进剂(氧化剂),[R]为还原产物,由于促进剂氧化掉第一步反应所产生的氢原子,加快了反应(1)的速度,进一步导致金属表面H+浓度急剧下降。
同时也将溶液中的Fe2+氧化成为Fe3+。
③ 磷酸根的多级离解H3PO4 H2PO4-+H+ HPO42-+2H+ PO43-+3H- (3)由于金属表面的H+浓度急剧下降,导致磷酸根各级离解平衡向右移动,最终为PO43-。
④ 磷酸盐沉淀结晶成为磷化膜当金属表面离解出的PO43-与溶液中(金属界面)的金属离子(如Zn2+、Mn2+、Ca2+、Fe2+)达到溶度积常数Ksp时,就会形成磷酸盐沉淀Zn2++Fe2++PO43-+H2O→Zn2Fe(PO4)2·4H2O↓ (4)3Zn2++2PO43-+4H2O=Zn3(PO4)2·4H2O↓ (5)磷酸盐沉淀与水分子一起形成磷化晶核,晶核继续长大成为磷化晶粒,无数个晶粒紧密堆集形而上学成磷化膜。
磷化培训资料讲解

金属基体的腐蚀
▪ 酸的浸蚀使基体金属表面H+浓度降低 : ▪ Fe – 2e→ Fe2+
2H++2e→2[H]
▪ Fe+2H+→Fe2++H2 (1)
氧化去氢
▪ 第一步产生的氢原子吸附在金属基体会对磷化反应
造成不良影响,因此需要氧化去除。
磷化培训资料
诚星化工技术部编制 2009年10月
磷化的定义
▪ 什么是磷化
磷化是指将金属工件(如钢铁、锌、铝)浸入 (或喷淋或涂刷)含有磷酸、磷酸盐和其 他化学物质的微酸性溶液中,发生化学反 应而在金属工件表面生成一层主要为不溶 或难溶的磷酸盐膜层的一种化学处理方法, 该磷酸盐膜称为磷化膜。
磷化的作用
总酸度
▪ 总酸度过高,磷化膜结晶粗糙,表面易产生浮
粉,磷化沉渣增加,可加水调整。
▪ 总酸度过低,磷化速度缓慢,磷化膜生成困难,
磷化膜结晶粗糙疏松,磷化膜变薄,耐蚀性也 差,可加磷化剂调整 。
酸比
▪ 酸比越高,磷化膜越细、越薄,过高不易成
膜、渣多。
▪ 酸比过小,磷化膜结晶粗大,疏松。 ▪ 常温磷化的酸比一般在20-30左右。
磷化的分类
▪ 按磷化膜种类分:锌系、铁系、锌钙系、锌锰系、锰系、非
晶相铁系六大类
▪ 按磷化方式分:浸渍磷化、喷淋磷化、刷涂磷化 ▪ 按磷化温度高低分 :高温磷化、中温磷化、 常温磷化 ▪ 按磷化膜单位面积膜层质量分(附用途):
A、次轻量级 膜重0.2-1.0g/㎡( 用作耐蚀性要求较低的涂装
底层)
磷化的成膜机理
▪ 磷化工作液的主要组成为酸式磷酸盐,在
线材磷化线作业培训

2,工艺介质准备及使用要求、控制
• 1,酸洗槽: 本公司酸洗使用的是工业盐酸,新建酸槽为工业浓盐酸原液。 酸洗槽的建槽:本公司盐酸槽在建槽时按照2~3Kg/槽的量添加酸洗抑雾剂 可以在充入盐酸前或充入盐酸后添加酸洗抑雾剂。 酸洗槽的使用:1),使用过程中,对于浓盐酸槽,如酸液表面覆盖的气泡 覆盖面积接近或不足一半面积时,需按照1Kg/次的量添加酸洗抑雾剂。2),对 于作为稀盐酸使用的盐酸槽,可以由操作工视酸雾挥发量决定是否添加酸洗抑 雾剂;3),本公司酸洗过程使用两槽法酸洗,一般在稀盐酸槽内酸洗15~25分钟 再转入浓盐酸槽内酸洗2~5分钟;4),污染、氧化程度差异大的材料或产品,应 分别处理,防止酸洗速度不一致导致的过酸或清洗不干净;5),酸洗槽的加热: 在气温低于25°C的情况下,稀盐酸槽允许加热到45°C以下;在气温低于5°C 的情况下,浓盐酸槽允许加热到30°C以下;6),酸洗过程中,操作工应根据酸 洗时间、反应产生气泡的翻滚程度,合理安排酸洗进度检查。 酸洗槽的翻槽:当盐酸槽浓度过低时,必须须重新配置酸洗槽。配槽前, 应清理槽内残液和残渣。
2,工艺介质准备及使用要求、控制
• 3,磷化槽(续): 磷化槽液酸度/酸比的测算: 使用量杯取槽液约50ml。 总酸度的测定:使用小号移液管(5ml),移取5ml槽液到另一量杯, 滴入3~4滴酚酞指示剂,摇匀;使用大号移液管(10ml),移取0.1N的 NaOH(氢氧化钠)10ml槽液,边摇晃边滴入添加了槽液和酚酞指示剂的 量杯,直至颜色稳定变红,读取滴入NaOH的毫升数,乘以2,即为槽液的 总酸度;(总酸度要求在35~65范围内,添加补给剂可以提高总酸度) 游离酸度的测定:使用小号移液管(5ml),移取5ml槽液到另一量杯, 滴入3~4滴溴酚蓝指示剂,摇匀;使用大号移液管(10ml),移取0.1N的 NaOH(氢氧化钠)10ml槽液,边摇晃边滴入添加了槽液和溴酚蓝指示剂 的量杯,直至颜色稳定蓝,读取滴入NaOH的毫升数,乘以2,即为槽液的 游离酸度;(游离酸度要求在5~8范围内,添加补给剂可以提高游离酸度) 酸比的计算:酸比=总酸度/游离酸度。(酸比要求在5~8范围内)
钢铁的磷化PPT课件
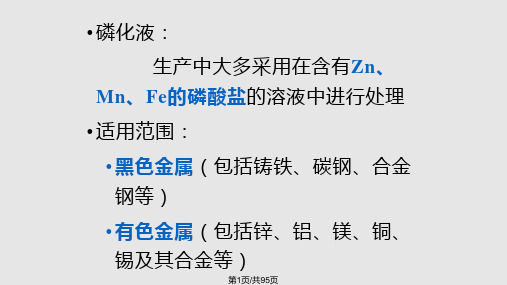
• 伪转化型磷化:膜中主要阳离子(锌、锰、铬)由溶液提供的磷化
第24页/共95页
基本组成: • 碱金属或重金属磷酸二氢盐 Me(H2PO4)2 (Me为Zn2+、Mn2+、Fe2+ 、Ca2+等) • 氧化性促进剂 • 游离磷酸
第25页/共95页
• 微阳极区反应: Fe - 2e- → Fe2+ Fe+ 2ZnPO4 - → FeZn2(PO4)2↓ +2e- ( Zn(H2PO4)2 ⇌ ZnPO4— +2H+ ) • 微阴极区反应: 2H+ + 2e → H2↑
• 避免H+浓度太高 • 避免促进剂氧化能力过强
第35页/共95页
条件: →
• 基体材料 • 工件的表面状态 • 磷化液组成 • 工艺条件
磷化膜:
• 种类 • 厚度 • 表面密度 • 结构 • 颜色
第36页/共95页
分类 锌系 锌钙系
磷化液主要 成分
磷化膜主要组成
Zn(H2PO4)2
Zn3(PO4)2·4H2O Zn2Fe(PO4)2·4H2O
第26页/共95页
Edward Ghali Laval University Canada
磷化膜成膜的电位-时间曲线示意图
Crrosion Science, 1972, 12 (7): 583-594
第27页/共95页
• A段:开始的瞬间,电势快速负移,对 应基体金属的溶解 Me + 2H3PO4→Me(H2PO4)2 + H2↑
• 精密钢管拉拔,磷化膜的质量为 4~10 g/m2
• 钢铁工件冷挤压成型,磷化膜的质
第212页/共95页
表面处理(磷化)工艺培训ppt课件
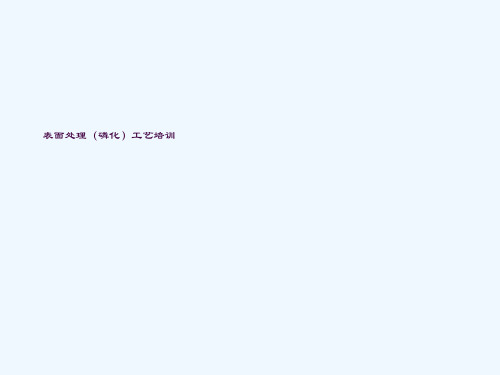
符号 P(不能理解为元素符号磷)
O Ec Ph A C C1A C1B (漂白型)常用 C2C (彩虹型)常用 C2D C2D
1.4 金属镀覆表示方法示例:
第一章:简述通用表面处理标注
例1. Fe/Ep.CuN15bCy0.3mc. (钢材,电镀铜10μm,光亮镍15μm,微裂纹铬0.3μm)
例2. Fe/Ep.Zn7.C2C (钢材。电镀锌7μm,彩虹铬酸盐处理2级C型)(彩虹型)
第三章:磷化处理工艺
氢气的去极化 防止在工件表面形成阻碍磷化膜生成的氢气泡,使磷化膜均匀,致密。
Fe2+的氧化 Fe2+被氧化成Fe3+,然后形成磷化渣被除去。
备注: 一般使用的促进剂:亚硝酸钠、氯酸盐、硝酸盐、过氧化氢、过氧化物、有机硝基
化合物、溴酸盐、碘酸盐
第三章:磷化处理工艺
目的: 封闭磷化膜孔隙,提高磷化膜耐蚀性,特别是提高漆膜的整体附 着力和耐腐蚀性
槽液主要成分
磷化膜主体
Zn2+、H2PO3-NO3-、 H3PO4、促进剂
Zn3(PO4)2•4H2O Zn2Fe(PO4)2•4H2O
锌钙系 锌锰系 锰系
Zn2+、Ca 2+、 H2PO3、NO3-H3PO4、促进 剂 Zn2+、Mn 2+、 H2PO3- 、NO3-、 H3PO4、促进剂
Mn2+、H2PO3-NO3-、 H3PO4、促进剂
Zn2Fe(PO4)2•4H2O Zn2Ca(PO4)2•4H2O Zn3(PO4)2•4H2O
Zn2Fe(PO4)2•4H2O Zn3(PO4)2•4H2O (Mn, Fe)5(PO4)4•4H2O (Mn, Fe)5(PO4)4•4H2O
磷化表面处理 PPT课件
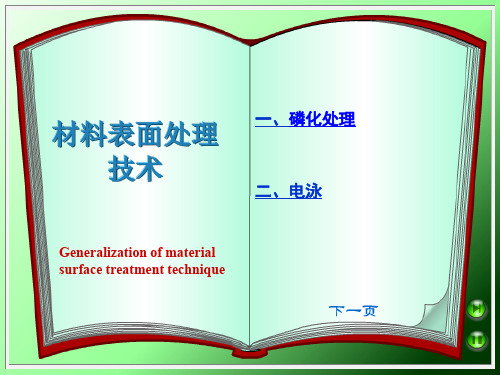
磷化处理
电化学机理:认为是一种微电池作用的结果
阴极反应:2H-+2e=H2 阳极反应:Fe-2e=Fe2+
Fe2+ +2H2PO4-=Fe(H2PO4)2
Fe(H2PO4)2= FeHPO4+ H3PO4
3FeHPO4= Fe3(PO4)2↓+ H3PO4
阴极反应:2H-+2e=H2
材料表面处理 技术
一、磷化处理 二、电泳
Generalization of material surface treatment technique
汽车涂装工艺
汽车涂装工艺,一般可分为两大部分:一是涂装 前金属的表面处理,也叫前处理技术;二是涂装的 施工工艺。表面处理主要包括清除工件表面的油污、 尘土、锈蚀、以及进行修补作业时旧涂料层的清除 等,以改善工件的表面状态。包括根据各种具体情 况对工件表面进行机械加工和化学处理,如磷化、 氧化和钝化处理。
磷化方法:浸渍法(耐腐蚀性能较好)和喷淋法
22:43:09
22:43:09
22:43:09
磷化后处理
为了提高磷化膜的防护能力,磷化后应对磷化
膜进行填充和封闭处理。填充处理的工艺是:
重铬酸钾 30~50 g/L
碳酸钠 2~4 g/L
温度 90~98 ℃
时间 5~10 min
填充后,可以根据需要在锭子油、防锈油或润
M(H2PO4)2 → MHPO4↓ + H3PO4 MHPO4 → M3(PO4)2↓ + H3PO4 可溶性的磷酸二氢盐水解生成不溶性的磷酸氢盐和磷酸 盐。
3Fe +2H3PO4 =Fe3(PO4)2 +3 H2 ↑ 反应生成的不溶于水磷酸盐在金属表面沉积成为磷酸盐 保护膜。
磷化培训
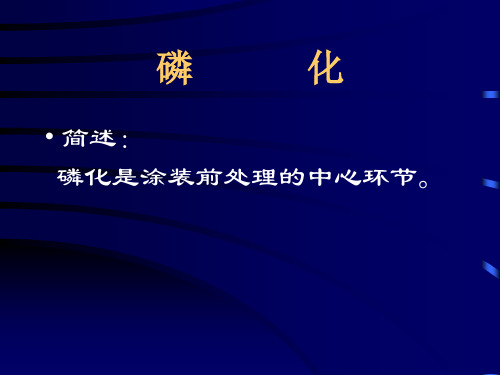
磷
化
5、铁系磷化液(如GBKH/1磷化液 实样) 铁系磷化只能生成磷酸铁和三氧化二铁, 且随着氧化剂种类和使用量的不同,磷 化膜中的磷酸铁和三氧化二铁的比例亦 不同,磷化膜呈不同颜色; ——典型产品参数示例(GB KH/1 磷化液) FA(60g/L,10ml):5.3+0.4; TA( 60g/L,10ml ):17.4+2.0
磷
化
三、常用磷化液分类及各类磷化液简介 1、锌系薄膜磷化液(GB101 磷化液实样) —— 锌系薄膜磷化液参数示例(GB101 磷化 液)及参数简介: FA(60g/L,10ml):7.5+0.2; TA( 60g/L,10ml ):39.3+1.2; GSF( 60g/L,10ml ):22.7+0.7; 密度:1.655+0.010; S:0.34+0.02;
磷
化
• 简述: 磷化是涂装前处理的中心环节。
磷
化
一、磷化的定义 ——磷化是指金属工件(如钢铁、锌、铝) 浸入(或喷淋或涂刷)含有磷酸、磷 酸盐和其他化学物质的微酸性溶液中, 发生化学反应而在金属工件表面生成 一层主要为不溶或难溶的磷酸盐膜层 的一种化学处理方法; ——该磷酸盐膜称为磷化膜;
磷
化
二、磷化的目的与作用 ——提供清洁表面 磷化膜只有在无油污和锈层的金属工 件上生成,因此经过磷化处理的金属 工件可以提供清洁、均匀、无油脂、 无锈层的表面;
磷
化
——铁系磷化液的主要成份 磷酸、氢氟酸、氧化剂、硝酸钠、 磷酸二氢钠 ——典型产品操作指导书简单介绍 (GB KH/1 磷化液) 用于冷轧钢、铝材、镀锌钢表面的磷化 处理; 用于喷淋;
磷
化
磷化膜重0.5g/m2左右; 磷化温度在40~50 °C; 磷化时间约为3分钟; 配槽浓度约为2%左右; 有极少量的磷化渣生成; 6、简单介绍GB24 磷化液
涂装前处理基础知识(磷化)

沈阳帕卡濑精有限总公司
序论
1934年,德国人Frits Singer提出磷化处理用于金属冷变形加工的专利(BP455077), 年 德国人 提出磷化处理用于金属冷变形加工的专利( 提出磷化处理用于金属冷变形加工的专利 ), 极大地提高了冷变形加工的劳动生产率, 极大地提高了冷变形加工的劳动生产率,从而结束了磷化膜只作为金属防蚀膜和油漆 底层的历史,打开了磷化膜在拔丝、拉管、冷挤压加工领域里应用的大门。 底层的历史,打开了磷化膜在拔丝、拉管、冷挤压加工领域里应用的大门。 (3)磷化处理技术进一步发展和完善时期(1937年以后) 磷化处理技术进一步发展和完善时期( 年以后) 磷化处理技术进一步发展和完善时期 年以后 技术上很少有突破,在金属冷变形加工工业应用广泛,磷化技术传播到其他国家。 技术上很少有突破,在金属冷变形加工工业应用广泛,磷化技术传播到其他国家。 主要改进有:低温磷化液,各种控制磷化膜膜重的方法,连续钢带高速磷化处理工艺。 主要改进有:低温磷化液,各种控制磷化膜膜重的方法,连续钢带高速磷化处理工艺。 胶体钛盐和磷酸锰悬浮液的应用,对细化磷化膜起特别重要的作用。 胶体钛盐和磷酸锰悬浮液的应用,对细化磷化膜起特别重要的作用。 美国还发明出专门处理铝的磷化液,以传统的磷酸锌系统为基础,添加氟化物。 美国还发明出专门处理铝的磷化液,以传统的磷酸锌系统为基础,添加氟化物。
(磷化渣)
Zn3(PO4)2.4 H2O + 4 H3PO4------------------------ (4)
(磷化膜.Hopeite)
Fe + 2Zn(H2PO4)2
H2O [O]
Zn2Fe(PO4)2.4H2O + 2 H3PO4 (磷化膜.Phosphophyllite)
磷化培训PPT
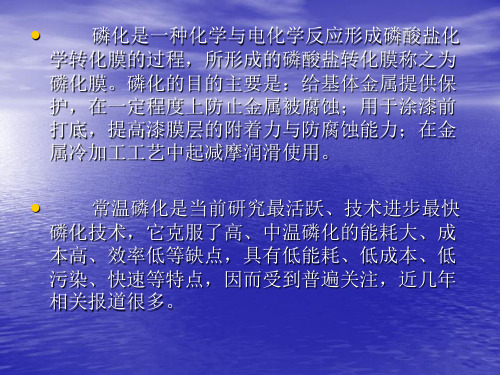
• 所谓“伪转化型磷化膜”则不同,膜中主要阳离子的成分
• 结晶型磷化膜(伪转化型磷化膜):在这种磷
化槽中不仅含有磷酸根、加速剂阴离子, 而且含有重金属阳离子直接参与成膜。 • 无定型磷化膜(转化型磷化膜):在磷化过程 中,基体金属是膜中阳离子的来源,形成 无定型膜(在钢铁上),这种膜是在磷酸或聚 磷酸的碱金属或铵盐溶液中形成的。不过 应该指出,磷酸钙膜是第三种变化形态, 因为它是伪转化无定型膜。
• 1.2 酸性清洗剂清洗
酸性清洗剂除油脂是一种应用非常广泛的方法。 它利用表面活性剂的乳化、润湿、渗透原理,并 借助于酸腐蚀金属产生氢气的机械剥离作用,达 到除油脂的目的。酸性清洗剂可在低温和中温下 使用。低温一般只能除掉液态油,中温就可除掉 油和脂,一般只适合于浸泡处理方式。酸性清洗 剂主要由表面活性剂(如OP类非离子型活性剂、 阴离子磺酸钠型)、普通无机酸、缓蚀剂三大部 分组成。由于它兼备有除锈与除油脂双重功能, 人们习惯称之为“二合一”处理液。
2、按磷化液及磷化膜的成分分类
• 按磷化液及磷化膜的成分,可分为铁系膜、
锌系膜、锌钙系膜、锌锰系膜、钙系膜等。 注意,此分法并不十分确切,因为任何磷 化膜中,只要是在铁基体上,都含有一定 量的铁成分。
3、按磷化膜结晶形状分类• 来自磷化膜的结晶形状可分成两类:第一为
结晶型磷化膜,如磷酸锌膜、磷酸锌锰膜、 磷酸铁膜、磷酸锌镍膜等;第二为无定型 (非结晶)磷化膜,主要是铁系磷化膜,单一 磷酸钙膜也是无定型膜,知识应用不多。 用途最广的是第一种。
1.2 磷化膜的作用
• 关于磷化膜的作用,阐述如下:
(1)磷化能把金属基材表面的活性转化到最小的程度,把以 后的腐蚀反应降到最低限度; (2)磷化膜能给金属提供一个“粗糙面”,给油漆或其他有 机膜提供一个很好的咬合力,增强其附着力; (3)由于磷化过程除去了工件表面的各种无机污染物,如金 属屑,轻微氧化物以及其他污物等,减少了影响附着力的 内在不利因素; (4) 磷化膜作为一种屏障,终止了有机层与基体金属之间 的化学反应,如皂化等; (5)磷化膜给金属表面各处提供一个同等的电化学电位,抑 制了任何局部的阴极和阳极的“点腐蚀”,从而消除了电 化学腐蚀区,减少了电化学腐蚀;同时也抑制了漆膜或其 他有机膜下面的腐蚀扩张,这应归于磷化膜的绝缘性。
磷化与金属前处理PPT课件

主要内容
• 磷化的基本原理 • 金属基材 • 汽车磷化技术 • 工艺参数对磷化工艺的影响 • 复合金属的磷化 • 磷化膜的性能检测 • 前处理技术的发展趋势
磷化的基本原理
发展历史、定义、分类及原理
涂装前处理的目的
• 除去表面污物,必要时进行表面化学转换,使被处 理件具有一定的粗糙度,平整度,增强金属抗腐蚀 能力及漆膜对金属基底的附着力
Z Z
n n
2 2
Fe(PO4)2·4H2O, Ca(PO4)2·2H2O
•改善表面摩擦学性能以 促进其滑动 •充当电绝缘层
涂装前磷化的目的
提高涂料附着力 减小涂膜下的腐蚀电流 磷化层形成抗水和氧扩散的屏障 一旦涂膜破裂可使漆膜裂纹处的腐蚀延迟
锌系磷化机理
• 正磷酸离解: K1=0.71×10-2 K2=7.99×10-8 K3=4.80×10-13
金属基材
Carbon Steels
Low Carbon 0.08 - 0.35% carbon content
Medium Carbon 0.35 - 0.50% carbon content
High Carbon > 0.55 % carbon content
METAL SUBSTRATES
STAINLESS STEEL 不锈钢 • Is used to construct the tanks used in the
水溶
水不溶
Fe-2e -→ Fe 2+ 微阳极金属溶解
(4)
2H++2e → 2[H] 微阴极释放出氢气 (5) H3PO4 → H2PO4-+H+ → HPO42-+2H+ → PO43-+3H+ (6)
实习报告-磷化PPT课件
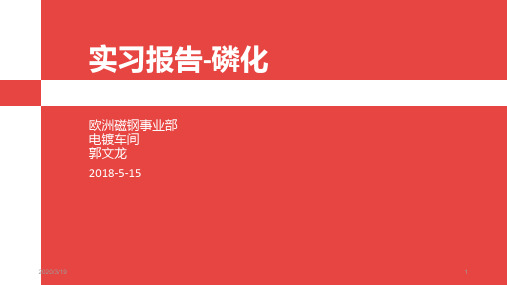
2020/3/19
4
4.磷化的作用和用途
磷化作 用
分类
特点
①涂装前磷 化的作用
A增强涂装膜层(如涂料涂层)与工件间结合力。 B提高涂装后工件表面涂层的耐蚀性。 C提高装饰性。
②非涂装磷 化的作用
A提高工件的耐磨性。 B令工件在机加工过程中具有润滑性。 C提高工件的耐蚀性。
b采用多级水洗,并控制最后清洗水的PH值接近中性
c时间:连续线上,由于链速已定,所以清洗时间不可能改变
a表调又称表面调整,通过调整,可以改善工件表面的微观状态,从而改善磷化膜外观,结晶 细小,均匀,致密,进而提高涂膜性能。
b现代表调基本上都是胶体钛盐表调,对已表调液也需严格控制总碱度(TAL)、温度、PH值、钛 含量,总碱度、PH值高易使磷化槽FA下降过快;温度过高,易产生工序间表干;钛含量过低表调 效果不好,钛含量太高,磷化膜不易生成,膜重不达标。
主要用途 钢铁磷化主要用于耐蚀防护和油漆用底膜。
分类
用途
磷化膜类型
磷化膜单位面积 质量
作用
磷化用 途
①耐蚀防护
2020/3/19
A防护用磷化 膜
B油漆底层用 磷化膜
用于钢铁件耐蚀 防护处理
增加漆膜与钢铁 工件附着力及防 护性
锌系、锰系
锌系或锌钙 系
10-40 g/㎡
0.2-1.0 g/㎡ 1-5 g/㎡ 5-10 g/㎡
3
三、磷化
1.磷化定义: 磷化是一种化学与电化学反应形成磷酸盐化学转化膜的过程,所形成的磷
酸盐转化膜称之为磷化膜。
2.磷化目的: 主要是:给基体金属提供保护,在一定程度上防止金属被腐蚀;用于涂漆前
磷化表面处理PPT课件

反应生成的不溶于水磷酸盐在金属表面沉积成为磷酸盐
保护膜。
2021/3/7
CHENLI
11
磷化处理
电化学机理:认为是一种微电池作用的结果
阴极反应:2H-+2e=H2 阳极反应:Fe-2e=Fe2+
Fe2+ +2H2PO4-=Fe(H2PO4)2 Fe(H2PO4)2= FeHPO4+ H3PO4 3FeHPO4= Fe3(PO4)2↓+ H3PO4 阴极反应:2H-+2e=H2 同 样 , 阳 极 反 应 生 成 物 还 有 Mn3(PO4)2 ﹑Zn3(PO4)2一起结晶,形成磷化膜。
2021/3/7
CHENLI
12
磷化处理
二、磷化膜的组成和结构
磷化液种类大致有锌型(以磷化锌为主盐)﹑ 锰型(以磷酸锰铁盐为主盐)。在同一型中,配 比又是多种多样的,所得到的晶粒大小不同。大 小有从几个微米到上百微米。晶粒愈大,膜层愈 厚。在磷化膜中应用最广的有磷酸铁膜﹑磷酸锌 膜﹑磷酸锰膜。
磷酸铁膜 用碱金属磷酸二氢盐为主要成分的 磷化液处理钢材表面时得到的非晶质膜是磷酸铁 膜。外观呈灰色﹑青色乃至黄色。磷化液中的添 加物也可共沉积于膜中,并影响膜的颜色。
2021/3/7
CHENLI
22
磷化处理
6 杂质的影响 除磷酸、硝酸和硼酸以外的酸,如硫酸根、氯离子以
及金属离子砷、铝、铬、铜都被认为是有害杂质,其中硫 酸根和氯离子的影响更为严重。硫酸根和氯离子会降低磷 化速度,并使磷化膜层疏松多孔易生锈。金属离子砷和铝 使膜层的耐蚀性下降,大量的铜离子会使磷化膜发红,耐 蚀性下降。
9 预处理的影响 预处理对磷化膜外观颜色和膜的质量有很大的影响。经喷砂处理的钢 铁表面粗糙,有利于形成大量晶核,获得致密的磷化膜。用有机溶剂清 洗过的金属表面,磷化后所获得的膜结晶细而致密,磷化过程进行的较 快。用强碱脱脂,磷化膜结晶粗大,磷化时间长。经强酸腐蚀的金属表 面,磷化膜结晶粗大,膜层重,金属基体侵蚀量大,磷化过程析氢较多。
- 1、下载文档前请自行甄别文档内容的完整性,平台不提供额外的编辑、内容补充、找答案等附加服务。
- 2、"仅部分预览"的文档,不可在线预览部分如存在完整性等问题,可反馈申请退款(可完整预览的文档不适用该条件!)。
- 3、如文档侵犯您的权益,请联系客服反馈,我们会尽快为您处理(人工客服工作时间:9:00-18:30)。
• 1.2 酸性清洗剂清洗
酸性清洗剂除油脂是一种应用非常广泛的方法。 它利用表面活性剂的乳化、润湿、渗透原理,并 借助于酸腐蚀金属产生氢气的机械剥离作用,达 到除油脂的目的。酸性清洗剂可在低温和中温下 使用。低温一般只能除掉液态油,中温就可除掉 油和脂,一般只适合于浸泡处理方式。酸性清洗 剂主要由表面活性剂(如OP类非离子型活性剂、 阴离子磺酸钠型)、普通无机酸、缓蚀剂三大部 分组成。由于它兼备有除锈与除油脂双重功能, 人们习惯称之为“二合一”处理液。
• (2)游离酸度(FA)
FA是指磷酸盐处理液中游离状态磷酸的浓度。用点数 表示FA的大小。FA对金属基体的溶解起决定性作用。适当 提高FA,对钢铁基体的溶解有利,弥补因磷化温度低金属 溶解慢的不足。 (3)磷化液的P比 P比=TA/FA,即总算度与游离酸度的比值。P比对成膜的 好坏起关键作用。一般控制P比在15~20:1左右。
•
磷化是一种化学与电化学反应形成磷酸盐化 学转化膜的过程,所形成的磷酸盐转化膜称之为 磷化膜。磷化的目的主要是:给基体金属提供保 护,在一定程度上防止金属被腐蚀;用于涂漆前 打底,提高漆膜层的附着力与防腐蚀能力;在金 属冷加工工艺中起减摩润滑使用。
常温磷化是当前研究最活跃、技术进步最快 磷化技术,它克服了高、中温磷化的能耗大、成 本高、效率低等缺点,具有低能耗、低成本、低 污染、快速等特点,因而受到普遍关注,近几年 相关报道很多。
4、按膜重和用途分类
• 所谓膜重是指膜层重量,按此可分为重量
级、中量级、轻量级,即厚膜、中等膜和 薄膜。厚膜的厚度在10~30g/m2,它主要 单独用作防护。作为防锈油、油脂、腊或 染色等的底基,不可用于涂漆及类似的有 机膜。厚度一般在10um左右,薄膜的厚度 在1~7g/m2,这种膜是在加速剂的槽中形 成的,处理时间短,膜薄,厚度一般在 1~5um,它多用作涂装处理。
•
一、 磷化机理
•
磷化过程包括化学与电化学反应。不 同磷化体系、不同其材的磷化反应机理比 较复杂。以一个化学反应方程式简单表述 磷酸锌磷化成膜机理:
Fe+5Zn(H2PO4)2+8H2O→6H3PO4 Zn2Fe(PO4)2· 4H2O+Zn3(PO4)2· 4H2O+2H2↑ 磷化膜是Zn2Fe(PO4)2· 4H2O+Zn3(PO4)2· 4H2O 的混合定型结晶。 我司代表产品:JH-31型低温锌系磷化液。
• 作为低温锌系磷化的副反应产物----磷化沉
渣。磷化沉渣主要是FePO4,要相减少沉渣 量就必须降低Fe3+的产生量,即通过两个方 法:降低磷化液的H+浓度(低游离酸度) 减少Fe2+氧化成为Fe3+。
1.1磷化中TA,FA及P比的含义
• (1)总酸度(TA)
TA的广义是指磷酸盐处理液中化合酸、 游离酸以及各种离子浓度的总和。反映磷 化工作液中内动力耳朵大小,决定了磷化 反应速度的快慢。同时又衡量浓缩磷化剂 浓度的重要参数。用点数表示TA的大小。
二、 磷化分类
• 1、按磷化膜的转化形式分类 • 根据磷化膜中金属离子的来源,所有的磷化膜都可归分为
转化型和伪转化型磷化膜。
• 所谓转化型的磷化膜,主要是溶液对金属基体的腐蚀,由
金属基体提供阳离子与溶液中的PO43-结合而形成的磷化膜, 磷化液的主要成分是由钠,钾,铵的磷酸二氢盐及加速剂 所组成。由这溶液形成的膜统称为铁系膜,膜中的铁成分 是从基体金属上转化来的。(如我司JH-42型磷化液) 来源于溶液,由溶液提供。如锌系磷化膜中的锌,锰系磷 化膜中的锰,铝及其合金上铬酸盐中的铬等都不是基体金 属铁或铝中直接转化而来,而是来源于预先加入到溶液中 的Zn(H2PO4)2、Mn(H2PO4)2等提供的。(如我司的JH31型、JH-311型锌系磷化液)
• 所谓“伪转化型磷化膜”则不同,膜中主要阳离子的成分
• 结晶型磷化膜(伪转化型磷化膜):在这种磷
化槽中不仅含有磷酸根、加速剂阴离子, 而且含有重金属阳离子直接参与成膜。 • 无定型磷化膜(转化型磷化膜):在磷化过程 中,基体金属是膜中阳离子的来源,形成 无定型膜(在钢铁上),这种膜是在磷酸或聚 磷酸的碱金属或铵盐溶液中形成的。不过 应该指出,磷酸钙膜是第三种变化形态, 因为它是伪转化无定型膜。
1.标准槽浸工艺:
A.工艺流程: 除油→水洗→水洗→除锈→水洗→中和→水洗→表调→ 磷化→水洗→钝化 B.药剂的选用: 除油:JH-04除油粉 除锈:盐酸+JH-21酸洗添加剂 中和:KD-C中和剂 表调:JH-68钛盐表调剂 磷化:JH-31常温锌系磷化液+YDM-2促进剂 钝化:JH-70钝化粉 C.槽浸线如图:
• 盐酸、硫酸酸基的清洗剂应用最为广泛,成本低,
效率较高。但酸洗残留的Cl-、SO42-对工件的后腐 蚀危害很大。而磷酸酸基没有腐蚀物残留的隐患, 但磷酸成本较高,清洗效率低些。 对于锌件,铝件一般不采用酸性清洗剂清洗, 特别锌件在酸中的腐蚀极快。
• 1.3强碱液清洗
强碱液除油脂是一种传统的有效方法。它是 利用强碱对植物油的皂化反应,形成溶于水的皂 化物达到除油脂的目的。纯粹的强碱液只能皂化 除掉植物油脂而不能除掉矿物油脂。因此人们通 过在强碱液中加入表面活性剂,一般是磺酸类阴 离子活性剂,利用表面活性剂的乳化作用达到除 矿物油的目的。强碱液除油脂的使用温度都较高, 通常〉80℃。 强碱液除油脂需要较高温度,能耗大,对设 备腐蚀性也大,并且材料成本并不算低,因此这 种方法的应用正逐步减少。
在PH值为6~8的脱脂液中进行脱脂。 通过乳化作用能降低工件油污的表面张力。 并通过强助洗剂使油污与工件分离,出去 固体污物。脱脂液中不含难以清洗的氢氧 化钠、硅酸盐和OP类乳化剂等,有的几乎 全部由表面活性剂组成。
• 2 酸洗
酸洗除锈、除氧化皮的方法是工业领域应用最为广 泛的方法。利用酸对氧化物溶解以及腐蚀产生氢气的机械 剥离作用达到除锈和除氧化皮的目的。酸洗中使用最为常 见的是盐酸、硫酸、磷酸。硝酸由于在酸洗时产生有毒的 二氧化氮气体,一般很少应用。盐酸酸洗适合在低温下使 用,不宜超过45℃,使用浓度10%~45%,还应加入适量 的酸雾抑制剂为宜。硫酸在低温下的酸洗速度很慢,宜在 中温使用,温度50~80℃,使用浓度10%~25%。磷酸 酸洗的优点是不会产生腐蚀性残留物(盐酸、硫酸酸洗后 或多或少会有少会有Cl-、SO42-残留),比较安全,但磷 酸的缺点是成本较高,酸洗速度较慢,一般使用浓度 10%~40%,处理温度可常温到80℃。在酸洗工艺中,采 用混合酸也是非常有效的方法,如盐酸-硫酸混合酸,磷 酸-柠檬酸混合酸。
三、磷化前的预处理工艺
• 一般情况下,磷化处理要求工件表面应是
洁净的金属表面。工件在磷化前必须进行 除油脂、锈蚀物、氧化皮以及表面调整等 预处理。特别是涂漆前打底用磷化还要求 作表面调整,使金属表面具备一定的“活 性”,才能获得均匀、细致、密实的磷化 膜,达到提高漆膜附着力和耐腐蚀性的要 求。因此,磷化前处理是获得高质量磷化 关于磷化膜的作用,阐述如下:
(1)磷化能把金属基材表面的活性转化到最小的程度,把以 后的腐蚀反应降到最低限度; (2)磷化膜能给金属提供一个“粗糙面”,给油漆或其他有 机膜提供一个很好的咬合力,增强其附着力; (3)由于磷化过程除去了工件表面的各种无机污染物,如金 属屑,轻微氧化物以及其他污物等,减少了影响附着力的 内在不利因素; (4) 磷化膜作为一种屏障,终止了有机层与基体金属之间 的化学反应,如皂化等; (5)磷化膜给金属表面各处提供一个同等的电化学电位,抑 制了任何局部的阴极和阳极的“点腐蚀”,从而消除了电 化学腐蚀区,减少了电化学腐蚀;同时也抑制了漆膜或其 他有机膜下面的腐蚀扩张,这应归于磷化膜的绝缘性。
四、磷化工艺
• 磷化工艺的早期应用是防锈,钢铁件经磷
化处理形成一层磷化膜,起到防锈作用。 经过磷化防锈处理的工件防锈期可达几个 月甚至几年(对涂油工件而言),广泛用 于工序间、运输、包装贮存及使用过程中 的防锈,磷化主要有铁系磷化、锌系磷化、 锰系磷化三大品种。 下面以我司常规JH-31 锌系磷化作槽浸和喷淋工艺的讲解:
5、按用途分类
• A:用于密封层打底保护,耐磨,耐微动磨损和抗 •
•
•
擦伤,还可用于冷作成形中的润滑剂载体的磷化 膜,这类磷化膜多数为厚膜,以锰系膜居多。 B:用于不发生形变的油漆底层,用于成形不太严 格的润滑剂载体的磷化膜,这类膜多数为中等厚 度的磷化膜,以普通锌系,锌钙系膜居多。 C:一般用于有机涂层打底,即涂装前的磷化,多 以改性锌系磷化膜。 D:同C类似,也用于涂装前的磷化,但防护的标 准较C低,或用于涂覆有机层后有较大成形场合的 磷化膜,这类膜通常为铁系磷化膜。
• 1 除油脂
除油脂的目的在于清除掉工件表面的油 脂、油污。包括机械法、化学法两类。机 械法主要是:手工擦刷、喷砂抛丸、火焰 灼烧等。化学法主要:溶剂清洗、酸性清 洗剂清洗、强碱液清洗,低碱性清洗剂清 洗。以下介绍化学法除油脂工艺。
• 1.1 溶剂清洗
溶剂法除油脂,一般是用非易燃的卤代烃蒸 气法或乳化法。最常见的是采用三氯乙烷、三氯 乙烯、全氯乙烯蒸汽除油脂。蒸汽脱脂速度快, 效率高,脱脂干净彻底,对各类油及脂的去除效 果都非常好。在氯代烃中加入一定的乳化液,不 管是浸泡还是喷淋效果都很好。由于氯代卤都有 一定的毒性,汽化温度也较高,再者由于新型水 基低碱性清洗剂的出现,溶剂蒸汽和乳液除油脂 方法现在已经很少使用了。
•
浸泡型清洗剂主要应注意的是表面活性剂的 浊点问题,当处理温度高于浊点时,表面活性剂 析出上浮,使之失去脱脂能力,一般加入阴离子 型活性剂即可解决。喷淋型清洗剂应加入足够的 消泡剂,在喷淋时不产生泡沫尤为重要。 铝件、锌件清洗时,必须考虑到它们在碱性 条件下的腐蚀问题,一般宜用接近中性的清洗剂。
• 1.5中性脱脂
• 1.4低碱性清洗液清洗
低碱性清洗液是当前应用最为广泛的一类除 油脂剂。它的碱性低,一般pH值为9~12。对设 备腐蚀较小,对工件表面状态破坏小,可在低温 和中温下使用,除油脂效率较高。特别在喷淋方 式使用时,除油脂效果特别好。低碱性清洗剂主 要由无机低碱性助剂、表面活性剂、消泡剂等组 成。无机型助剂主要是硅酸钠、三聚磷酸钠、磷 酸钠、碳酸钠等。其作用是提供一定的碱度,有 分散悬浮作用。可防止脱下来的油脂重新吸附在 工件表面。表面活性剂主要采用非离子型与阴离 子型,一般是聚氯乙烯OP类和磺酸盐型,它在除 油脂过程中起主要的作用。在有特殊要求时还需 要加入一些其它添加物,如喷淋时需要加入消泡 剂,有时还加入表面调整剂,起到脱脂、表调双 重功能。