烷基化装置开工方案(终版)
离子液体烷基化装置工业试验开工试运转岗位操作法

离子液体烷基化装置工业试验开工试运转岗位操作法1反应温度高的影响因素及调节方法影响因素:①原料中烯煌含量高;②原料含水过多;③冷剂温度过高;④提量太快。
调节方法:①原料换罐或降原料量;②加强原料脱水;③调整冷剂冷却温度,减少防喘振流量;④缓慢提量、保持操作平衡。
2.反应器压力的影响因素及调节方法影响因素:①原料、异丁烷、冷剂量波动较大;②原料、冷剂、异丁烷中的丙烷含量较高。
③闪蒸罐的压力较高。
调节方法:①稳定原料、异丁烷、冷剂量。
②从冷剂罐顶部排部分丙烷。
③将闪蒸罐压力控制在指标以内。
3.闪蒸罐带离子液体的原因及处理方法带离子液体的原因:①酸沉降罐内离子液体液面高。
②酸沉降罐的压力过低或压力波动较大。
③进料量波动大。
④反应器管束漏。
处理方法:①降低酸沉降罐内的离子液体的液面。
②提反应系统压力并稳定D-2压力。
③稳定进料,搞好平稳操作。
④停工堵漏。
4.分液罐带液的原因及调节方法带液原因:①闪蒸罐两侧的液面过高。
②分液罐压力较低。
③闪蒸罐液面控制失灵。
调节方法:①降低闪蒸罐两侧液面。
②提高分液罐压力。
③联系仪表工处理仪表。
5.压缩机出口压力高的原因及调节方法原因分析:①冷剂中丙烷含量高。
②E-2的冷却水喷头堵。
③E-2冷却水量不够。
调节方法:①从D-4顶排丙烷。
②处理冷却水喷头。
③及时给E-2补水。
6.闪蒸罐压力高的原因及调节方法原因分析:①反喘振流量控制阀开的太大。
②压缩机入口阀关小。
③反应温度∣≡Jo④丙烷含量高。
调节方法:①关小反喘振流量控制阀。
②开大压缩机入口阀。
③降低原料量。
④从D-4顶排丙烷。
7.反应器倒酸(离子液体)的原因及处理方法原因:当反应器进料中断(包括烯烧、循环异丁烷、循环冷剂)后,未及时关闭进料总阀,原料罐压力降低后,离子液体倒入原料罐。
处理方法:当反应器所有进料中断后,应立即关闭反应器进料总阀。
8.D-2沉降效果不好的原因及处理方法原因分析:①反应温度过高。
②原料流量不稳。
烷基化装置

重化物
尾气
3248
11092
6.58
22.46
3984
15248
5.99
23.23
3163
12970
5.18
21.24
损失
开工时间
388
5676
0.78
64.79
520
6802
0.79
77.65
487
6844
0.8
77.91
九、装置改造方案
原料油脱水 烷基化反应器进料要严格控制水含量,国内尚无满足 该工艺要求的设备,装置内已有一台引自美国Peteollte 电脱水器内件,经实际生产运行证明使用效果不好,因 此,为了净化方应器进料,降低酸耗和减小设备损失, 利用上游同步配套改造的轻碳四选择性加氢装置区,增 设了脱二甲醚塔措施,可将烷基化原料中的水含量脱至 100PPm以下,并且在改造时,在D-1顶加压力控制阀门, 来满足D-1脱水的压力条件。
吸入闪蒸罐中反应侧的流出物在E-1/A、B、C中 与 原料换热后,再经酸洗混合器(M-1)与98%的新硫酸 混合后进入反应产物碱洗罐(D-7)脱除硫酸酯,酸相 至R-1/A、B,油相与10%NaOH,经碱洗混合器(M-2)混 合后进入反应产物碱洗罐(D-8/A)脱除酸性物,碱相循 环使用、定期排出系统。油相经反应产物二级沉降罐 (D-8/B)脱除碱性物后,经T-1进料与产品换热器(E4)、T-1进料加热器(E-5)加热至70℃后进入脱异丁 烷塔(T-1)分离。 T-1顶分出的异丁烷经T-1顶冷凝器(E-6/A,B)冷至 40℃后进入T-1顶回流罐(D-9),异丁烷由T-1回流泵 ((P-6/A、B)自D-9抽出,一部分打回T-1顶作回流, 大部分循环异丁烷返回反应系统与原料混合,少部分过 剩异丁烷送出装置或送至D-14。
烷基化装置工艺流程说明

烷基化装置工艺流程说明本装置由原料加氢精制、反应、致冷压缩、流出物精制和产品分馏及化学处理等几部分组成,现分别简述如下:1.原料加氢精制自MTBE 装置来的未反应碳四馏分经凝聚脱水器(104-D-105)脱除游离水后进入碳四原料缓冲罐(104-D-101),碳四馏分由加氢反应器进料泵(104-P-101)抽出经碳四-反应器进料换热器(104-E-104)换热后,再经反应器进料加热器(104-E-101)加热到反应温度后与来自系统的氢气在静态混合器(104-M-101)中混合,混合后的碳四馏分从加氢反应器(104-R-101)底部进入反应器床层。
加氢反应是放热反应。
随混合碳四带入的硫化物是使催化剂失活的有害杂质。
催化剂失活后可用热氢气吹扫使其活化。
反应后的碳四馏分从加氢反应器顶部出来与加氢裂化液化气混合。
自液化气双脱装置过来的加氢裂化液化气进入加氢液化气缓冲罐(104-D-102),加氢裂化液化气由脱轻烃塔进料泵(104-P-102)抽出与反应器(104-R-101)顶部出来的碳四馏分混合后进入脱轻烃塔(104-C-101)。
脱轻烃塔(104-C-101)的任务是脱去碳四馏分中的碳三以下的轻组分,同时将二甲醚脱除。
脱轻烃塔是精密分馏的板式塔,塔顶压力控制在1.7MPa(g)。
塔顶排出的轻组分经脱轻烃塔顶冷凝器(104-E-103A/B)冷凝冷却后,进入脱轻烃塔回流罐(104-D-103)。
不凝气经罐顶压控阀(PIC-10401)后进入全厂燃料气管网。
冷凝液由脱轻烃塔回流泵(104-P-103)抽出,一部分做为(104-C-101)顶回流,另一部分作为液化气送出装置。
塔底抽出的碳四馏分经(104-E-104)与原料换热后再经碳四馏分冷却器(104-E-105)冷至40℃进入烷基化部分。
塔底重沸器(104-E-102)采用0.45MPa 蒸汽加热,反应器(104-R-101)进料加热器使用1.0MPa 蒸汽加热,凝结水都送至凝结水回收罐(104-D-304)回收。
离子液体烷基化装置工业试验开工试运转开工方案
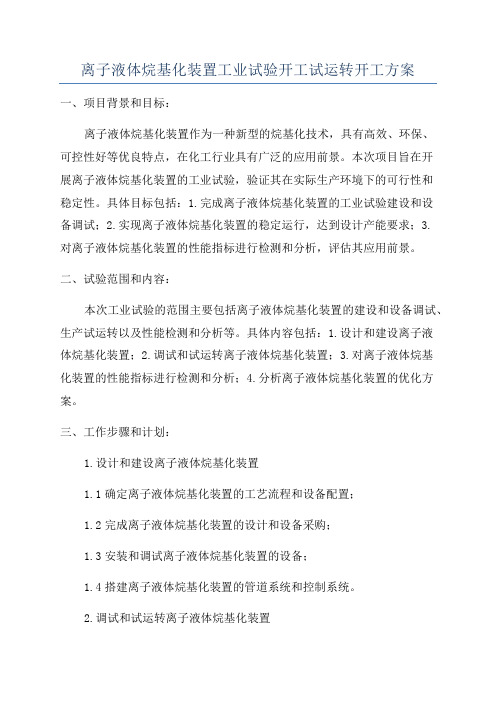
离子液体烷基化装置工业试验开工试运转开工方案一、项目背景和目标:离子液体烷基化装置作为一种新型的烷基化技术,具有高效、环保、可控性好等优良特点,在化工行业具有广泛的应用前景。
本次项目旨在开展离子液体烷基化装置的工业试验,验证其在实际生产环境下的可行性和稳定性。
具体目标包括:1.完成离子液体烷基化装置的工业试验建设和设备调试;2.实现离子液体烷基化装置的稳定运行,达到设计产能要求;3.对离子液体烷基化装置的性能指标进行检测和分析,评估其应用前景。
二、试验范围和内容:本次工业试验的范围主要包括离子液体烷基化装置的建设和设备调试、生产试运转以及性能检测和分析等。
具体内容包括:1.设计和建设离子液体烷基化装置;2.调试和试运转离子液体烷基化装置;3.对离子液体烷基化装置的性能指标进行检测和分析;4.分析离子液体烷基化装置的优化方案。
三、工作步骤和计划:1.设计和建设离子液体烷基化装置1.1确定离子液体烷基化装置的工艺流程和设备配置;1.2完成离子液体烷基化装置的设计和设备采购;1.3安装和调试离子液体烷基化装置的设备;1.4搭建离子液体烷基化装置的管道系统和控制系统。
2.调试和试运转离子液体烷基化装置2.1对离子液体烷基化装置的设备进行一次全面的检查和调试;2.2开展装置稳定性试验,验证其在不同操作条件下的稳定性;2.3逐步提高离子液体烷基化装置的生产能力,达到设计产能要求。
3.对离子液体烷基化装置的性能指标进行检测和分析3.1对离子液体烷基化装置的产量、能耗、产品质量等性能指标进行实时监测;3.2分析离子液体烷基化装置的产能和能耗之间的关系;3.3对离子液体烷基化装置的产物进行质量分析和评价。
4.分析离子液体烷基化装置的优化方案4.1根据实际试验结果,分析离子液体烷基化装置存在的问题和不足;4.2提出离子液体烷基化装置的优化方案,以提高其生产能力和经济效益。
四、工作条件和要求:1.工作地点:离子液体烷基化装置试验基地;2.工作时间:按照工作计划进行;3.工作条件:保持工作现场的清洁和安全,按照相关规定使用和管理试验设备;4.工作要求:全体工作人员必须按照操作规程进行工作,保障试验的顺利进行。
石油化工烷基化装置仪表施工方案

工程编号:发放编号:此施工方案包含了许多仪表施工共性的专业知识、现场实际经验,有些条款在任何书本规范中是查不到的,但在实战中非常有用,细心的读者一定会发现北京燕山分公司炼油厂烷基化装置恢复生产仪表工程施工技术方案编制:周乐平审核:审定:安全:会签:2004年12月8日目录一、工程概况二、施工方案编制依据三、施工过程及技术质量要求1、仪表材料、配件、设备验收检验及保护2、仪表校验、标定3、槽板安装4、仪表设备安装5、保护管及电缆的敷设6、仪表线路的配线7、导压管路及伴热管路敷设8、气动管线敷设9、仪表施工中应注意的其它事项四、施工顺序五、施工管理及质量保证体系、质量验收1、施工管理及质量保证体系2、质量控制点3、交工资料六、HSE管理1、HSE安全管理网络2、安全教育3、安全防火措施4、安全用电措施5、高空作业注意事项6、仪表施工风险评估一、工程概况炼油厂烷基化装置系引进美国菲利普斯石油公司技术专利,本装置年产烷基化油6万吨,烷基化是在氢氟酸存在下异丁烷与丁烯化合生成异辛烷(即烷基化油)的工艺过程。
装置内加工的原料和生产的产品均属于低沸点、易燃易爆的烃类,反应催化剂为具有剧毒和强腐蚀性的氢氟酸,危险性很高。
为了保障长周期的安全生产,美国菲利普斯石油公司设置一整套完整的设计、施工、操作规范。
本次改造控制室内监控仪表采用FOXBORO公司的DCS系统,使用DCS的顺序逻辑控制功能块来实现酸快速转移系统。
为了便于统一操作、管理,本装置DCS控制站设在邻近的气体分馏装置DCS机柜间内,同时设置AMS系统,DCS操作站设在同一生产作业部的重整-加氢联合装置操作室内,控制站、操作站之间采用光纤连接。
在烷基化装置区设置副操作区,副操作区内仅设置氢氟酸有毒气体报警器、可燃气体报警器及酸快速转移系统操作台。
室外就地仪表分为氟区和非氟区(普通)两类,仪表工程量较大,仪表类型很多,除常规仪表差压变送器、压力变送器、浮筒、调节阀、热电偶、温变等外,还有雷达液位计、超声波液位计等特殊仪表。
2007石油二厂烷基化装置改造工程施工方案
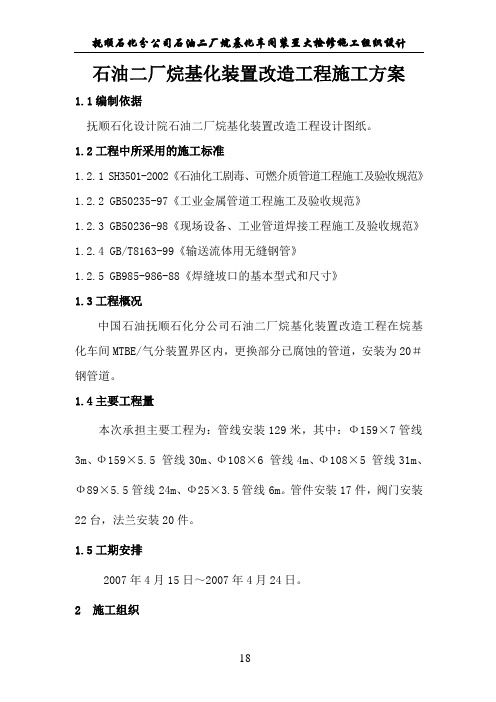
石油二厂烷基化装置改造工程施工方案1.1编制依据抚顺石化设计院石油二厂烷基化装置改造工程设计图纸。
1.2工程中所采用的施工标准1.2.1 SH3501-2002《石油化工剧毒、可燃介质管道工程施工及验收规范》1.2.2 GB50235-97《工业金属管道工程施工及验收规范》1.2.3 GB50236-98《现场设备、工业管道焊接工程施工及验收规范》1.2.4 GB/T8163-99《输送流体用无缝钢管》1.2.5 GB985-986-88《焊缝坡口的基本型式和尺寸》1.3工程概况中国石油抚顺石化分公司石油二厂烷基化装置改造工程在烷基化车间MTBE/气分装置界区内,更换部分已腐蚀的管道,安装为20#钢管道。
1.4主要工程量本次承担主要工程为:管线安装129米,其中:Ф159×7管线3m、Ф159×5.5 管线30m、Ф108×6 管线4m、Ф108×5 管线31m、Ф89×5.5管线24m、Ф25×3.5管线6m。
管件安装17件,阀门安装22台,法兰安装20件。
1.5工期安排2007年4月15日~2007年4月24日。
2 施工组织2.1 项目经理部组织机构见检修方案3主要施工方案3.1施工前准备3.1.1由于春季施工气侯多变,风较大,为保证焊接质量,用6分管80m制作6个焊接棚,在5个面上遮上苫布。
尺寸如下:3.1.2对施工人员进行技术交底、宣贯已批准生效的施工方案。
将施工用具、设备、材料运到现场。
3.2管线安装3.2.1工艺管线安装(1)为保证工期,工艺管线预制量应达到80%以上。
预制完的管段根据标记运至安装现场对应位置。
(2)安装管线后对于有弯头的管线尤其要做好临时固定防护,确保施工人员的连续作业的安全。
(3)管线就位时,其焊缝、法兰及其它连接件的设置应便于检查、检修,不得紧贴管架、墙壁等处。
利用3-5吨起重机将管线拉到位进行组对焊接。
烷基化装置开工规程
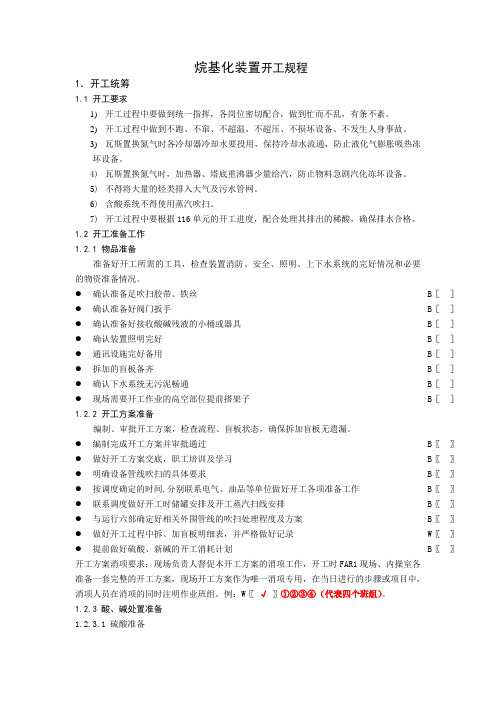
烷基化装置开工规程1.开工统筹1.1 开工要求1)开工过程中要做到统一指挥,各岗位密切配合,做到忙而不乱,有条不紊。
2)开工过程中做到不跑、不窜、不超温、不超压、不损坏设备、不发生人身事故。
3)瓦斯置换氮气时各冷却器冷却水要投用,保持冷却水流通,防止液化气膨胀吸热冻坏设备。
4)瓦斯置换氮气时,加热器、塔底重沸器少量给汽,防止物料急剧汽化冻坏设备。
5)不得将大量的烃类排入大气及污水管网。
6)含酸系统不得使用蒸汽吹扫。
7)开工过程中要根据116单元的开工进度,配合处理其排出的稀酸,确保排水合格。
1.2 开工准备工作1.2.1 物品准备准备好开工所需的工具,检查装置消防、安全、照明、上下水系统的完好情况和必要的物资准备情况。
●确认准备足吹扫胶带、铁丝B[]●确认准备好阀门扳手B[]●确认准备好接收酸碱残液的小桶或器具B[]●确认装置照明完好B[]●通讯设施完好备用B[]●拆加的盲板备齐B[]●确认下水系统无污泥畅通B[]●现场需要开工作业的高空部位提前搭架子B[]1.2.2 开工方案准备编制、审批开工方案,检查流程、盲板状态,确保拆加盲板无遗漏。
●编制完成开工方案并审批通过B〖〗●做好开工方案交底,职工培训及学习B〖〗●明确设备管线吹扫的具体要求B〖〗●按调度确定的时间,分别联系电气、油品等单位做好开工各项准备工作B〖〗●联系调度做好开工时储罐安排及开工蒸汽扫线安排B〖〗●与运行六部确定好相关外围管线的吹扫处理程度及方案B〖〗●做好开工过程中拆、加盲板明细表,并严格做好记录W〖〗●提前做好硫酸、新碱的开工消耗计划B〖〗开工方案消项要求:现场负责人督促本开工方案的消项工作,开工时FAR1现场、内操室各准备一套完整的开工方案,现场开工方案作为唯一消项专用,在当日进行的步骤或项目中,消项人员在消项的同时注明作业班组。
例:W〖√〗①②③④(代表四个班组)。
1.2.3 酸、碱处置准备1.2.3.1 硫酸准备1)装置道路通畅,施工器具全部撤离现场,脚手架、钢丝绳全部拆除,地面平整无杂物。
离子液体烷基化装置工业试验开工试运转开工方案
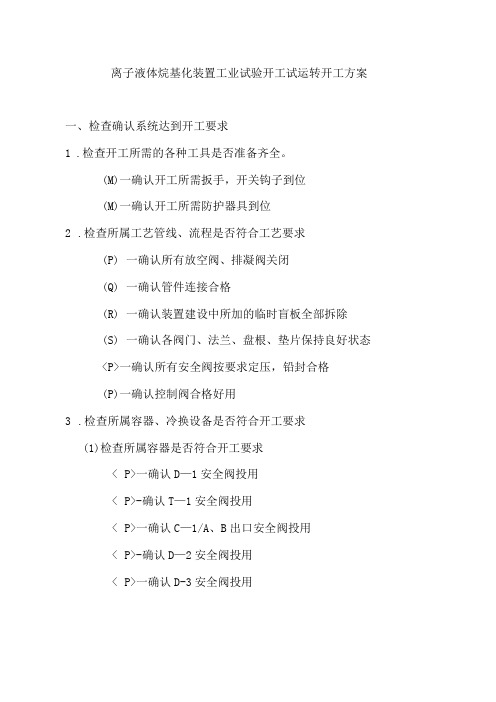
离子液体烷基化装置工业试验开工试运转开工方案一、检查确认系统达到开工要求1.检查开工所需的各种工具是否准备齐全。
(M)一确认开工所需扳手,开关钩子到位(M)一确认开工所需防护器具到位2.检查所属工艺管线、流程是否符合工艺要求(P)一确认所有放空阀、排凝阀关闭(Q)一确认管件连接合格(R)一确认装置建设中所加的临时盲板全部拆除(S)一确认各阀门、法兰、盘根、垫片保持良好状态<P>一确认所有安全阀按要求定压,铅封合格(P)一确认控制阀合格好用3.检查所属容器、冷换设备是否符合开工要求(1)检查所属容器是否符合开工要求<P>一确认D—1安全阀投用<P>-确认T—1安全阀投用<P>一确认C—1/A、B出口安全阀投用<P>-确认D—2安全阀投用<P>一确认D-3安全阀投用<P>-确认D—4安全阀投用<P>一确认D-6安全阀投用<P>一确认D-7安全阀投用<P>-确认D-8安全阀投用<P>-确认D-9安全阀投用<P>-确认D-IO安全阀投用<P>一确认D-I1安全阀投用<P>-确认D—24安全阀投用<P>一确认D—32安全阀投用<P>-确认T-2安全阀投用<P>一确认T-3安全阀投用(2)检查所属冷换设备是否符合开工要求<P)一确认ET具备投用条件<P)—确认E-2具备投用条件<P)一确认E-3具备投用条件<P)—确认E-4具备投用条件<P)一确认E-5具备投用条件<P)—确认E-6具备投用条件<P)一确认E-7具备投用条件<P)—确认E-8具备投用条件<P)一确认E-9具备投用条件<P)一确认ETO具备投用条件(P)-确认E-12具备投用条件<P)一确认ET3具备投用条件4.检查C-1/A.B、反应产物泵及其它各机泵单机试运是否达到正常运转条件(1)检查CT/A、B是否达到正常运转条件(P)一确认电机润滑油油位达到要求(P)一确认润滑油冷却水投用(P)一确认润滑油箱油质、油量、油位达到要求,冷却水系统畅通,(2)润滑油系统建立(P)一确认盘车结束(I)一确认现场与操作室参数指示相同(3)检查反应产物泵是否达到正常运转条件(参考基础设备操作规程)(M)一确认反应进料泵具备开车条件(4)检查各泵是否达到正常运转条件(参考基础设备操作规程)(P)一确认PT/A、B具备正常运转条件(P)一确认P-3具备正常运转条件(P)一确认P-5具备正常运转条件(P)一确认P-6具备正常运转条件(P)一确认P-8具备正常运转条件(P)一确认P-9具备正常运转条件(P)一确认PTO具备正常运转条件(P)一确认p-11/A、B具备正常运转条件(P)一确认P-12具备正常运转条件(P)一确认P-14具备正常运转条件(P)-确认P-15具备正常运转条件5.做好开工前的联系准备工作[M]一联系化验做好开工分析化验的准备工作[M]-联系维修部门做好开工维护的准备工作[M]一联系罐区和调度准备合格的异丁烷及碳四原料,并做好化验分析记录[M]一准备好生产运行大记录、报表打印纸及交接班日记6.检查仪表电气系统(P)一确认压力表现场指示与操作室指示相同(P)一确认温度测量组件等安装完毕,且现场与DCS指示相同(P)一确认控制阀安装完毕且动作准确灵敏(I)一确认DCS系统具备开工条件(I)一确认主控制室及装置内的通讯设施信号良好、语音清晰7.检查安全环保设施是否齐全好用(M)一确认岗位员工按要求穿戴好劳动保护用品(P)一确认现场干净整洁,无污油、无垃圾,排水沟、下水井畅通无阻(M)—确认消防设施、消防器材、防护用具齐全到位((M)一确认可燃气体报警仪测试合格投用(M)一确认便携式可燃气体报警仪测试合格投用(M)—确认正压呼吸器备用(M)一确认过滤式防毒面具备用备用8.开工前盲板确认(1)确认以下抽出线盲板处于盲位(P)-P-1/C进口(Q)一D-I底部(R)-P-16进口((S)-E-7底部(T)-E-9底部(U)一ET2底部(V)-D-20底部(W)-D-3反应侧、冷剂侧(X)-D-4(Y)-D-6碱混合器,E-3碱进口(Z)-D-6底部(AA)-P-4/A处(BB)-D-19底部(CC)一塔T顶部(DD)一塔-2顶部(EE)一塔-3顶部(FF)-D-9顶部(2)确认装置与外围系统进出物料线盲板已拆除(P)一原料进装置总阀(GG)一丁烯-2进装置总阀(HH)一进装置新酸线总阀(II)一进装置碱线总阀(JJ)一异丁烷出装置总阀(KK)一正丁烷出装置总阀(LL)一航空异辛烷出装置总阀(MM)一车汽到66泵房出装置阀(NN)一车汽到62泵房出装置阀(OO)一燃料气线出装置总阀(PP)一冷凝水出装置总阀(QQ)一乏汽出装置总阀(RR)一循环水上、下水总阀(SS)一重化物出装置总阀(TT)一重化物到三叶精细厂(UU)一硫酸至190出装置阀(VV)一碱至190出装置阀9.检查公用工程系统是否具备条件(1)引新鲜水(P)一确认与系统连接阀门关闭[M]一联系调度准备引新鲜水[P]一打开新鲜进装置总阀(P)-确认新鲜水引入装置(2)引除盐水(P)一确认系统内所有阀门关闭[M]一联系调度准备引除盐水[P]一打开界区阀门(P)一确认除盐水引至D-26阀前(3)引1oMPa蒸汽[P]一改好1OMPa蒸汽流程(P)一确认各支线阀门全部关闭[M]-联系调度准备引1.0MPa蒸汽(P)一确认1OMPa蒸汽界区外排凝处脱尽存水,微量见汽[P]-缓慢打开1oMPa蒸汽界区阀门(P)一确认管网排凝阀见汽(P)一确认蒸汽压力控制阀下排凝阀见汽(4)引3.0MPa蒸汽[P]一改好3.OMPa蒸汽流程(P)一确认各支线阀门全部关闭[M]-联系调度准备引3.OMPa蒸汽(P)一确认3.0MPa蒸汽界区外排凝处脱尽存水,微量见汽[P]一缓慢打开3.0MPa蒸汽界区阀门(P)一确认管网排凝阀见汽(P)一确认蒸汽压力控制阀下排凝阀见汽(5)引氮气(P)一确认系统内支线阀门全部关闭[P]一拆除氮气界区盲板[M]-联系调度准备引氮气[P]一打开界区阀门(P)一确认氮气线内有压力(6)引循环水(P)一确认装置内各用户阀门关闭[P]一打开各冷换及主网循环水阀[M]-联系调度引循环水(P)一确认循环水主网循环正常[P]一打开各换热器出、入口阀[P]一关闭各循环阀(P)一确认各换热器循环正常二、开车步骤:装置进料[P]一各岗位详细检查流程,打开有关的阀门,[P]一校对各控制阀,处备用状态;[P]一将D-17∕A.B罐内的新酸开泵T1打入沉降器D-2内90吨98%酸;[P]一开P-5泵向碱洗罐D-8装入10%Na0H到1/4液面;[I]一塔-1、塔-2、塔-3引蒸汽缓慢升温;[M]一联系71泵房开P-1/C泵抽停工前备好的异丁烷[P]一从开工线向塔T进料,[I]一同时该塔升温并建立循环;[I]一当塔T回流罐D-9液面达到1/2时,启用液面控制[P]一循环异丁烷线按流程将E-1/A.B.C、D-UD-2、反应器等设备逐一填充物料;[I]一当反应器压力达到0.35MPa时,启用压力控制阀P1C-201;[P]一当闪蒸罐D-3产物端液面达到1/2时,启动P-2泵给E-1/A.B.C管程向D-8/A进料[P]—D-8/A进料的同时开P-5泵建立碱循环,同时向D-8/B进料;[I]—D-8/B压力达到0.8MPa的时候,启用压力控制PICTO1 [P]一同时向D-7进料;[P]一待D-7满,塔T进料后,此时停PT∕C,停抽异丁烷[P]一检查启动压缩机,使D-3压力降至0.015MPa,反应温度为4℃;[P]一打开P-2泵至反应器封油线阀,并调节封油压力高于反应器壳体压力0.05-0.IMpa[P]一启动RT搅拌电机;[P]一将D-2至反应器重腿手阀打开,逐渐再将碟阀开大,建立酸循环;[M]一联系71泵房开PT/A泵抽G原料向反应进料;[I]一调节控制反应温度不超过12℃;[I]一当塔T底液面达到1/2时,启用液面控制1IC-302向塔-2进料;[P]—塔-2进料后,DTO液面达到1/2时,开泵P-8建立循环;[I]一当塔-2底液面至1/2时,启用液面控制11C-303,向塔-3进料;[I]一塔-3进料,塔顶出产品后,建立循环,当DT1罐液面达到1/2时,启用液面控制1IC-406,向半成品罐DT3/A.B输送产品,待满罐分析合格后送至贮运厂;[I]一当塔-3底部液面达到1/2时,启用T-3底液面控制阀1IC-405,重化物经E-13冷却送入D-12罐内;[I]一流程全部打通后,逐步调整操作条件,使各项参数达到工艺指标范围;[P]一待循环酸浓度降到90%时,由D-2排除废酸,同时开PT1泵向D-2补充新酸。
离子液体烷基化装置工业试验开工试运转原则流程及说明

离子液体烷基化装置工业试验开工试运转原则流程及说明1.工艺流程简述1.1原料脱水及反应、分储流程:经加氢预处理后的MTBE尾气与循环异丁烷混合后经电脱水器脱水至900PPm(必需保证值)以下后,进入活性氧化铝脱水系统的干燥器(V-1O1/A-D)中,将原料中水含量脱至IOPPm后,进入离子液反应器(RT/A),在离子液体催化剂的作用下反应,生成烷基化油后,与离子液体一道自反应器流出至沉降罐(D-2/A)沉降分离,离子液体返回至反应器,反应产物至反应器管程取走反应热后,再吸入闪蒸罐(D-3)中反应侧分出气液两相。
液相送至精制系统,气相经压缩机压缩后至冷剂缓冲罐(D-4),一部分返回吸入闪蒸罐(D-3)闪蒸侧,另一部分进入外甩冷剂碱洗罐(D-6),经碱洗后送出装置。
吸入闪蒸罐中闪蒸侧的液相作为循环冷剂返回至反应器入口。
吸入闪蒸罐中的流出物经碱洗后进入脱异丁烷塔(T-1),塔顶异丁烷一部分送出装置,一部分作循环异丁烷,塔底烷基化油进入脱正丁烷塔(T-2)。
塔顶正丁烷出装置,塔底烷基化油出装置。
流程参见反应部分改造工艺管线及自控流程图,艺-31/1-1266/04及相关图纸艺-31/1-1227/07~13,1.2离子液催化剂装卸及补充、离子液渣过滤流程装置内不单独设置离子液体催化剂储罐,首次开工的催化剂由汽车储罐运至装置内,由催化剂卸料泵(PTO2)抽出装填入沉降罐(D-2/A)及新剂罐(VTo3),停工后利用该泵将系统内的催化剂退至汽车槽车罐内运出装置。
离子液催化剂的循环由装置现有的新酸泵(P-11/A.B)为反应间断补充新剂;反应过程中离子液形成的失活离子液固渣的过滤,采用反应旁路过滤,由离子液体沉降罐(原酸沉降罐D-2/A)排出,由泵循环至过滤器过滤后,返回至离子液体沉降罐(原酸沉降罐D-2∕A)0新剂罐设置氮封和外盘罐伴热,过滤装置设置氮封和保温。
流程参见艺-31/1T266/04。
1.3原料脱水干燥及再生流程原料脱水工艺采用活性氧化铝将原料中的水含量由900PPnI脱至IOPPm,共设四台干燥器,正常情况下两台并联干燥(也可串联),两台再生。
烷基化操作规程
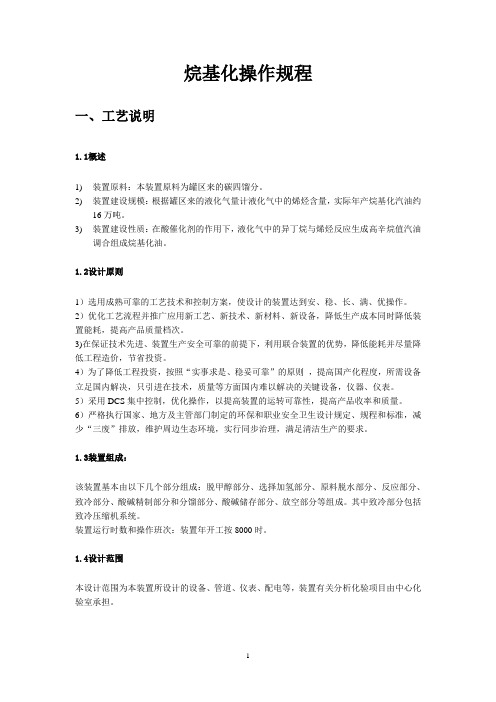
烷基化操作规程一、工艺说明1.1概述1)装置原料:本装置原料为罐区来的碳四馏分。
2)装置建设规模:根据罐区来的液化气量计液化气中的烯烃含量,实际年产烷基化汽油约16万吨。
3)装置建设性质:在酸催化剂的作用下,液化气中的异丁烷与烯烃反应生成高辛烷值汽油调合组成烷基化油。
1.2设计原则1)选用成熟可靠的工艺技术和控制方案,使设计的装置达到安、稳、长、满、优操作。
2)优化工艺流程并推广应用新工艺、新技术、新材料、新设备,降低生产成本同时降低装置能耗,提高产品质量档次。
3)在保证技术先进、装置生产安全可靠的前提下,利用联合装置的优势,降低能耗并尽量降低工程造价,节省投资。
4)为了降低工程投资,按照“实事求是、稳妥可靠”的原则,提高国产化程度,所需设备立足国内解决,只引进在技术,质量等方面国内难以解决的关键设备,仪器、仪表。
5)采用DCS集中控制,优化操作,以提高装置的运转可靠性,提高产品收率和质量。
6)严格执行国家、地方及主管部门制定的环保和职业安全卫生设计规定、规程和标准,减少“三废”排放,维护周边生态环境,实行同步治理,满足清洁生产的要求。
1.3装置组成:该装置基本由以下几个部分组成:脱甲醇部分、选择加氢部分、原料脱水部分、反应部分、致冷部分、酸碱精制部分和分馏部分、酸碱储存部分、放空部分等组成。
其中致冷部分包括致冷压缩机系统。
装置运行时数和操作班次:装置年开工按8000时。
1.4设计范围本设计范围为本装置所设计的设备、管道、仪表、配电等,装置有关分析化验项目由中心化验室承担。
1.5工艺设计技术方案烷基化装置是以液化气中的烯烃及异丁烷为原料,在催化剂的作用下烯烃与异丁烷反应,生成烷基化油的气体加工装置。
本装置包括原料加氢精制和烷基化两部分。
原料加氢精制的目的是通过加氢脱除原料中的丁二烯。
因为丁二烯是烷基化反应中主要的有害杂质,在烷基化反应过程中,丁二烯会生成多支链的聚合物,使烷基化油干点升高,酸耗加大。
化工生产装置开工方案
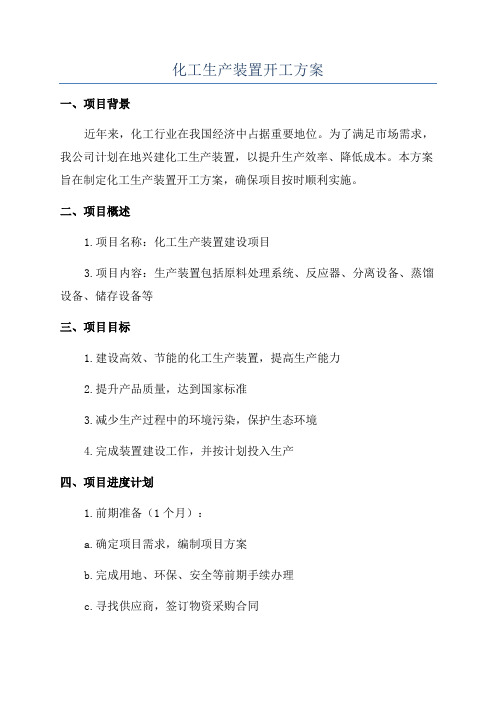
化工生产装置开工方案一、项目背景近年来,化工行业在我国经济中占据重要地位。
为了满足市场需求,我公司计划在地兴建化工生产装置,以提升生产效率、降低成本。
本方案旨在制定化工生产装置开工方案,确保项目按时顺利实施。
二、项目概述1.项目名称:化工生产装置建设项目3.项目内容:生产装置包括原料处理系统、反应器、分离设备、蒸馏设备、储存设备等三、项目目标1.建设高效、节能的化工生产装置,提高生产能力2.提升产品质量,达到国家标准3.减少生产过程中的环境污染,保护生态环境4.完成装置建设工作,并按计划投入生产四、项目进度计划1.前期准备(1个月):a.确定项目需求,编制项目方案b.完成用地、环保、安全等前期手续办理c.寻找供应商,签订物资采购合同2.设计阶段(2个月):a.编制工艺设计、设备设计和结构设计方案b.完成土建设计和设备布置设计c.编制施工图纸3.采购阶段(3个月):a.根据设计方案,进行设备、原材料、配件等采购b.签订采购合同并安排物资进场4.施工阶段(6个月):a.按照施工图纸进行土建施工b.设备安装调试c.管道、电气等系统安装及调试d.设备整体联调5.试生产阶段(1个月):a.进行小规模试生产,验证装置性能和产品质量b.整理试生产数据,反馈调整设备工艺参数6.正式投产阶段(1个月):a.完成装置调试和生产能力测试b.正式投入商业运营五、质量与安全控制措施2.施工质量控制:加强对施工过程的质量检查和监督,确保施工质量符合要求3.设备安全保障:严格按照国家相关安全标准进行设备安装、调试和运行,确保设备的安全性和稳定性4.安全教育培训:加强对施工人员和操作人员的安全教育培训,提升其安全意识和操作技能5.环境保护措施:优化工艺流程,减少废水、废气和固体废物的排放量,通过合理处理和回收,降低环境污染风险六、预算与资金筹措1.建设投资预算:a.设备采购及安装费用:3000万元b.工程建设费用:1000万元c.人工费用、材料费用:500万元d.其他费用(包括设计、检测、环保等):500万元2.资金筹措方式:a.自筹资金:3000万元b.银行贷款:2000万元七、风险分析与应对措施1.投资风险:由于市场变化、政策变化等原因,有可能影响项目回报率。
烷基化装置开停工指南

IV STARTUP/SHUTDOWN GUIDELINES第四章开/停工指南The purpose of this section is to provide a basic understanding of the general steps taken in startup and shutdown of an alkylation unit.本章主要介绍烷基化装置开停工的一般步骤。
The following are general recommended startup and shutdown guidelines for a STRATCO®Effluent Refrigerated Sulfuric Acid Alkylation. The final startup and shutdown guidelines will vary depending on different refineries’ alkylation unit layouts and operating practices. No attempt is made here to describe the opening or closing sequence of each valve or the exact flow rate of medium through each line. Sufficient description is given to demonstrate the general startup and shutdown of the major equipment only.下面为STRATCO®流出物致冷硫酸法烷基化装置的推荐开停工方案,不同装置的最终开停工方案须根据不同炼厂烷基化装置的实际设计和操作状况制定。
此处并不具体描述每条管线的阀门开关顺序以及介质流率,仅对主要设备的一般开停工步骤进行充分说明。
- 1、下载文档前请自行甄别文档内容的完整性,平台不提供额外的编辑、内容补充、找答案等附加服务。
- 2、"仅部分预览"的文档,不可在线预览部分如存在完整性等问题,可反馈申请退款(可完整预览的文档不适用该条件!)。
- 3、如文档侵犯您的权益,请联系客服反馈,我们会尽快为您处理(人工客服工作时间:9:00-18:30)。
海右石化集团烷基化装置开工方案二零一七年十二月目录一、开工组织指挥系统二、开工装置概况三、总体开工要求四、开工注意事项五、开工应具备的条件六、公用工程系统投用安排和要求七、安全环保开工方案八、安全、消防、环保要求九、开工所需物料及产品储存方案十、附:1、开工流程2、工作危害分析(JHA)评价表十一、事故预案一、开工组织指挥系统为确保试本次烷基化装置顺利开工,特成立开工领导小组,全面负责和指挥本次开工工作。
组长:王晓东副组长:杜光宗袁从春成员:王贵仁王玉玺洪希明厚安政相文袁建伟于晓龙金祥单庆庆唐振富彦帅西键宋学平主要职能:1. 负责本次装置总体开工的指挥、协调。
2.负责装置开工方案的制定、具体组织实施和开工进度的协调控制,以及开工过程中的异常状况处置。
3.做好开工期间的设备维修工作,配合生产开工进度,及时解决开工过程中装置设备、仪表、电力等异常情况的处置。
4. 负责开工前安全环保措施的制定,开工过程中安全环保检查落实工作。
二、开工装置概况1.开工装置为烷基化装置及相关配套的污水、循环水系统。
2.装置原料及产品流向三、总体开工要求1.严格按照开工方案要求开工,严格执行各项票证制度,严格执行生产调度指令。
2.开工期间严格执行安全环保相关制度规定,确保万无一失。
3.装置开工后达到设计负荷,各产品收率达到预期目标,实现低耗、优质、高效的目的。
4.开工期间,其他车间严禁出现物料互串,尤其公用系统与生产系统的互串。
四、开工注意事项1. 开工前,各装置改造、检修施工已全部完成,具备开工条件,开工前各装置制定开工前检查确认表并确认落实。
2.各装置开工前制定详细的开工方案,储运车间做好装置的引、退料方案,要根据方案提前做好相关准备工作。
3.车间所有人员必须认真学习开工方案,工艺和设备的整改,车间组织交底和解释。
4.装置严格执行操作规程以及相关工艺规定,做到令行禁止,禁止“三违”行为。
5.装置开工时做好安全环保工作,严格执行相关规定,禁止随便排放污水以及废气等废弃污染物。
6.开工期间调度室要做好装置开工的协调工作,各相关单位做好配合。
7.装置各项应急预案编制完成,并已组织学习传达。
8.开工过程中,凡与安全生产有矛盾的,均服从“安全第一”原则。
五、开工应具备的条件1.装置检修、改造全面竣工,并验收合格。
2.水(新鲜水、循环水、除盐水)、电、汽、风(净化风、非净化风)、氮气均供应正常,运行指标满足开工要求。
3.原料、燃料、中间产品、成品储罐均已安排就绪。
4.各类事故应急预案均已制定并组织学习。
5.开工方案编制完成,并组织学习讨论,熟练掌握。
6.开工人员经培训考试合格并持证上岗。
7.开工所需备品、备件、辅助物料、工器具等齐全并满足要求。
8.安全消防设施配备齐全,现场急救措施已经落实。
9.化工原材料、润滑油脂准备齐全。
10.通讯联络系统运行正常,各岗位、对讲机完好备用。
11.岗位责任制为中心的各项生产管理制度全部落实。
12.各装置机泵全部试运合格,并具备开工条件。
六、公用工程系统投用安排和要求1.蒸汽、空压站、除盐水、循环水、污水处理系统已做好准备,具备装置开工运行条件。
2. 装置所有设备具备送电条件。
七、安全环保开工方案(一)安全方针:安全第一,预防为主1.按照要求编制开车方案并进行备案;2.成立开车领导小组,完善安全规章制度、操作规程、工艺卡片;3.参与开车人员经培训和考核合格、人员责任措施落实到位;4.安全设施完好投用;5.特种设备依法检测检验合格;(二)环保措施:1.严格执行环保要求,确保应急设备完好,应急人员到位,应急措施有力。
2.加强开工期间的环保巡检工作,防止物料发生跑、冒、串料等问题。
3.严格遵守各项环保规定,严禁乱排乱放,并组织相关人员进行检查。
4.坚决杜绝水体环境污染事故。
5.防止发生大气环境污染事故。
6.防止发生噪声扰民事件。
7.确保外排水质达标八、安全、消防、环保要求1.开工过程中严格遵守有关安全、消防、环保法律法规及公司各项规章制度。
2.硫化氢、氮气、可燃气体区域主操作要有专人监护,并佩戴各种防护用具。
3.消防器材到位,消防设施完好。
4.开工过程中严格执行操作规程,杜绝违章指挥、违章操作。
5.开工过程中,严格执行各项生产调度指令。
6.参与开工人员能熟练使用各种消防、防护器具,并掌握有关急救方法。
7.开工过程中,要制定全面的各项应急措施,并认真组织学习。
8.全厂消防水系统投用,具备使用条件。
9.消防泡沫系统检查合格,流程顺通,具备使用条件。
10.装置开工期间,消防车现场24小时值班。
11.装置盲板抽堵全部检查完毕,并具备开工条件。
九、开工所需物料及产品储存方案1.物料准备:十、附:1.开工流程2.工作危害分析评价表1.开工流程烷基化车间开工方案(17小时)7烷基化车间各岗位开工时间统筹表(17小时)2017年12月 7 日89开工总则1.装置检修结束,组织车间人员检查工程质量,装置达到“工完、料净、场地清”,所有遗留问题处理完毕。
2.车间将开工方案送调度室审批、会签完毕。
3.车间所有人员必须认真学习开工方案,设备的检修情况,车间组织交底和解释。
4.开工过程应一切听从车间的安排,在调度室的统一指挥下,分工负责,协调一致,严格按开工方案进行,特殊情况须及时汇报调度室。
5.开工过程中,凡与安全生产有矛盾的,均服从“安全第一”原则。
开工准备1、装置各通道畅通,各明沟、暗沟畅通,无积油。
2、通讯系统良好畅通,对讲机充足电,照明正常良好。
3、配备好装置消防器材,装好各消防水带、蒸汽带、铜F扳手,备好防毒面具,并处于备用状态。
4、联系调度员做好循环水、新鲜水、除盐水、1.0MPa蒸汽、净化风、非净化风、氮气等的供应。
5、联系技术科、维修、电仪对制冷压缩机、反应器等大型转动设备进行最终调试和确认,并送电。
各设备处于备用状态,并做好相应的维护工作。
6、联系储运车间做好开工原料的供应和产品的接收工作。
7、联系化验做好正常生产和特需加样的分析工作。
尤其是硫酸、碳四原料、烷基化油组分含量分析。
8、联系技术科做好装置开工及正常生产的工艺技术指导和咨询工作。
9、联系技术科、维修车间、电仪车间按装置要求逐步启用所有仪表和DCS的最终调试确认工作。
做好可燃气体及H2S报警仪的调试工作。
联系电仪车间按装置要求逐步对电气设备送电。
12、车间准备好操作记录、交接班记录及其它用具。
开工步骤一、引公用介质1.引蒸汽(1)联系调度引低压蒸汽(2)确认1.0MPa蒸汽线进装置界区阀门的沿途排凝稍开脱水(3)蒸汽引至装置蒸汽分水器后关闭沿途排凝。
(4)蒸汽分水器保持压力未0.45Mpa(5)引蒸汽至各重沸器入口待用(6)确认蒸汽压力表指示无异常2. 引氮气(1)确认氮气线进装置界区阀门后盲板拆除(2)改好氮气至压缩机流程(3)确认各用气点阀门全部关闭(4)缓慢打开氮气线在装置边界阀门(5)待装置外压力达到平衡后,将边界氮气阀门全开(6)确认氮气线压力表指示无异常3.引除盐水(1)联系调度中心使用除盐水(2)拆除界区除盐水盲板(3)将除盐水引入除盐水罐D306中待用4.引循环水并投用冷却器(1)确认系统各循环水冷却器上下水阀门关闭(2)联系循环水工段确认引循环水(3)开启循环水泵,缓慢打开进/出装置循环水总阀(4)观察循环水压力指示并确认正常N (5)先开启冷却器回水线阀门(6)自上水线阀门后部放空阀排水(7)确认排水干净后,关闭放空阀(8)开启循环水上水线阀门参考上述方法逐台投用循环水冷却器二、分馏岗位开工1.原料预处理系统开工(1)联系调度、罐区自罐区引烷基化碳四原料(2)确认罐区来烷基化碳四原料装置界区阀门畅通(3)从D105、D101底部放空脱水,检查罐区脱水是否干净(4)检查P101泵体情况,做好P101开泵前的准备工作(5)确认C101中部进料阀打开(6)联系调度、罐区引碳四液化气(7)从D105底部放空脱水,查罐区脱水是否干净(8)开启P101,建立C101碳四进料,控制进料量在13吨/小时(9)确认0.45MPa蒸汽引入E-102管程入口(入口最后一道阀关闭)待用(10)确认E-103循环水投用正常(11)确认C-101底部玻璃板液位达到70%时,投用E-102升温(12)打通温控阀TV10404至D304流程,控制升温速度≯30℃/h(13)投用C-101压控PV10401,从而逐步控制塔顶压力达到1.6MPa(14)逐步控制C-101底部温度达到102℃左右(15)逐步控制D-103液位达到70%(16)确认C-101顶回流流程畅通(17)检查P103泵体情况,做好P103开泵前的准备工作(18)启动P103,经回流气动调节阀向C101打回流(19)通过控制调节阀,保证D103液位保持在60-70%(20)依据D103压力,液位情况择机并入全厂燃料气管网(21)调整产品质量,联系化验采样分析,开工期可增加化验频率(22)塔底液位高时,将塔底碳四经混合液化气线送至罐区(23)控制塔底碳四异丁烷/烯烃比例达到1-1.5:1(24)根据烷基化反应部分开工进度确定继续进料还是停止进料、C101系统全回流循环(25)原料预处理系统开工完毕待命原料预处理系统控制指标:塔顶温度:40~55℃;塔底温度:90~115℃塔顶压力:1.5—1.8Mpa塔底压力:1.60~2.1MPa;回流比:19.62.脱异丁烷塔开工(1)确认0.45MPa蒸汽引入E-209管程入口(入口最后一道阀关闭)待用(2)确认E-207A/B/C/D、E208循环水投用正常,空冷器是否运转正常。
(3)确认C-201底部玻璃板液位达到30%时,投用E-209升温(4)打通重沸器管程出口阀门至D213至D304流程,控制升温速度≯30℃/h(5)投用C-201压控,从而逐步控制塔顶压力达到0.4MPa(6)逐步控制C-201底部温度达到110℃左右(7)逐步控制D-212液位达到70%(8)确认C-201顶回流流程畅通(9)检查P209泵体情况,做好P209开泵前的准备工作(10)启动P209,经回流气动调节阀向C201打回流(11)通过控制调节阀,保证D212液位保持在90%以上(12)调整产品质量,联系化验采样分析,开工期可增加化验频率(13)塔底液位高时,将塔底液位送至C202塔(14)C201系统全回流循环(15)脱异丁烷塔开工完毕待命2.脱正丁烷塔( C202 )开工(1)确认0.45MPa蒸汽引入E-212管程入口(入口最后一道阀关闭)待用(2)确认E-212、E214、E211循环水投用正常(3)确认C-202底部玻璃板液位达到70%时,投用E-212升温(4)打通重沸器管程出口至D304流程,控制升温速度≯30℃/h(5)逐步控制C-202底部温度达到108℃左右(6)逐步控制D-214液位达到70%(7)确认C-202顶回流流程畅通(8)检查P210泵体情况,做好P210开泵前的准备工作(9)启动P210,经回流气动调节阀向C202打回流(10)通过控制调节阀,保证D214液位保持在50%以上(11)调整产品质量,联系化验采样分析,开工期可增加化验频率(12)塔底液位高且化验结果不合格时,将塔底液位送至D209罐重新加工处理,直至烷基化油产品质量合格外送,产品合格后单塔循环(13)脱正丁烷开工完毕待命三.建立系统碱洗、水洗循环流出物碱洗D210、水洗D211循环(1)确认流出物碱洗罐D210碱水配备完成,浓度在5~10%(2)确认流出物水洗罐D211装水至规定液位40%(3)确认系统仪表投用且校验完成(4)打通P206至D210循环碱水流程,通用混合器M202(5)E206低低压蒸汽入口阀前部排汽备用(6)启流出物碱洗循环泵P206电机(7)打开泵出口阀门,调整循环碱水量达到流出物循环量的25%,约计25t/h(8)碱水循环正常后,缓慢投用E206管程蒸汽(9)调整E206蒸汽流量,控制碱水升温速度不大于30℃/h(10)控制E206升温,目标:使D210流出物出口温度达到47℃(11)检查P206运行情况,确认碱水循环正常(12)根据D211水洗泵P207来水量情况投用D210液控LIC21202(13)确认D210碱水界位平稳(14)至此,碱洗罐D210碱水循环建立完毕。