冷轧作业指导书
冷轧钢板进料检验作业指导书

6.2长度须符合表1规定(摘自GB708-2006)
表1
6.3宽度须符合表2规定(摘自GB708-2006)
表2
文件非经许可不准影印
制订部门:质量部
冷轧钢板进料检验作业指导书文件编号:
制订日期:14年3月28日第 1 版第 4/11 页
6.4厚度须符合表3规定(摘自GB708-2006)
表3
文件非经许可不准影印
6.5不平度须符合表4规定(摘自GB708-2006)
表4
文件非经许可不准影印
6.6冷轧钢板的锈蚀等级应达到C级以上,根据GB8923-88的规定,钢材表面四个锈蚀等级分别
以A、B、C和D表示,其文字叙述如下:
A:全面地覆盖着氧化皮而几乎没有铁锈的钢材表面;
B:已发生锈蚀,并且部分氧化皮已经剥落的钢材表面;
C:氧化皮已因锈蚀而剥落,或者可以剥除,并且有少量点蚀的钢材表面;
D:氧化皮已因锈蚀而全面剥落,并且已普遍发生点蚀的钢材表面。
6.7化学成份
6.7.1 碳素结构钢冷轧钢板之化学成份须符合表5规定(摘自GB700-2006)
表5
文件非经许可不准影印
6.8力学性能
6.8.1 碳素结构钢冷轧钢板之力学性能须符合表6规定(摘自GB700-2006)
表6
文件非经许可不准影印。
最新冷作生产作业指导书资料
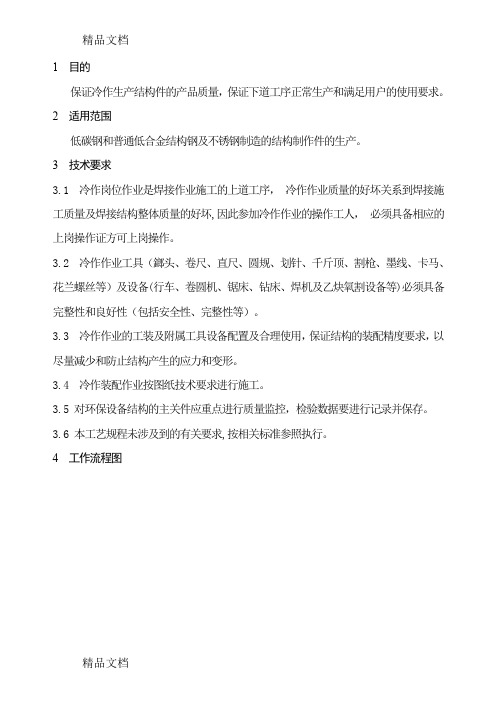
1 目的保证冷作生产结构件的产品质量,保证下道工序正常生产和满足用户的使用要求。
2 适用范围低碳钢和普通低合金结构钢及不锈钢制造的结构制作件的生产。
3 技术要求3.1 冷作岗位作业是焊接作业施工的上道工序,•冷作作业质量的好坏关系到焊接施工质量及焊接结构整体质量的好坏,因此参加冷作作业的操作工人,•必须具备相应的上岗操作证方可上岗操作。
3.2 冷作作业工具(鎯头、卷尺、直尺、圆规、划针、千斤顶、割枪、墨线、卡马、花兰螺丝等)及设备(行车、卷圆机、锯床、钻床、焊机及乙炔氧割设备等)必须具备完整性和良好性(包括安全性、完整性等)。
3.3 冷作作业的工装及附属工具设备配置及合理使用,保证结构的装配精度要求,以尽量减少和防止结构产生的应力和变形。
3.4 冷作装配作业按图纸技术要求进行施工。
3.5 对环保设备结构的主关件应重点进行质量监控,检验数据要进行记录并保存。
3.6 本工艺规程未涉及到的有关要求,按相关标准参照执行。
4 工作流程图┌───────┐│图纸、工艺│┌────┐└───┬───┘│预处理│││(矫正)││└──┬─┘↓┌──────┐↓┌───────┐│板材、型材├──────→│放样、划线│└──────┘┌──┐└───┬───┘│检├─────→↓└──┘┌───────┐┌─────┐│下料、去毛刺├──→│冷、热成形│└───┬───┘└──┬──┘│←─────────┘┌──┐││检├─────→│└──┘┌───┴───┐│部装│┌────┐└───┬───┘┌──┐│预处理││←──────┤检││(烘焙)││└──┘└─┬──┘││↓┌──────┐↓┌───────┐│焊接材料├──────→│焊接│└──────┘└───┬───┘├───────────→│┌───┐│┌──┐│←──┤其他件│││检├────→↓└───┘│└──┘┌─────┐││总装││└──┬──┘┌──┐│←───────────┘│检├────→↓└──┘┌─────┐│焊接│└─────┘┌──┐││检├────→↓└──┘┌─────┐│打磨│└─────┘┌──┐││检├────→↓└──┘┌─────┐│油漆│└─────┘┌──┐││检├────→↓└──┘┌─────┐│交付│└─────┘5 工作步骤及具体要求5.1凡是在图样或设计文件中无特殊要求时,均应符合本规范要求。
冷轧带肋钢筋作业指导书
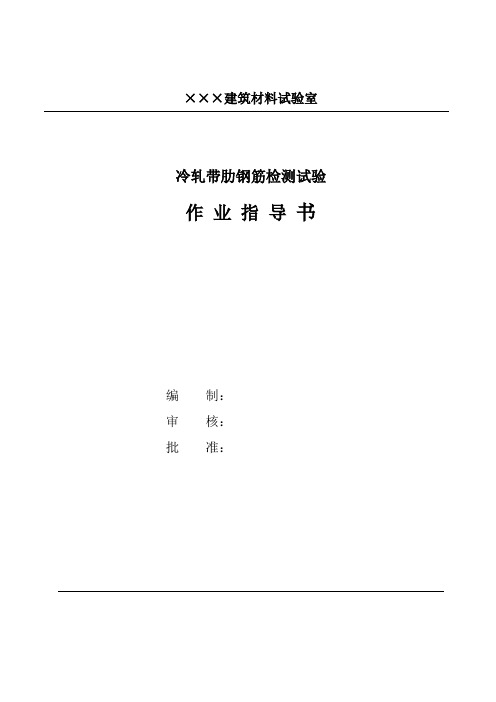
GB 13788-2008
冷轧带肋钢筋检测试验
页码
第4页,共6页
7.5把试样放好后,关闭回油阀,开动送油阀,缓慢而均匀地加荷。从测力盘上读取上屈服,也就是试样发生屈服而力首次下降前的最高应力。测定上屈服时的应变速率应保持恒定并在表规定的应力速率范围内:
材料弹性模量E/(N/mm2)
应力速率/【(N/㎡)/s】
10.2试验出现下列情况之一其实验结果无效,应重做同样数量试样的试验:a.试样断在标距外或断在机械刻划的标距标记上,而且断后伸长率小于规定最小值;b.试验期间设备发生故障,影响了试验结果。
10.3试验后试样出现2个或2个以上的颈缩以及显示出肉眼可见的冶金缺陷(如分层、气泡、夹渣、缩孔等),应在试验记录和报告中说明。
Rp0.2=FP0.2/So
Rp0.2——规定非比例延伸率为0.2%所对应的荷载
So——试样原始横截面积
×××建筑材料试验室
检验规范
GB 13788-2008
冷轧带肋钢筋检测试验
页码
第6页,共6页
10.结果判定
10.1冷轧带肋钢筋试验如有一项不符合要求, 从未试验的盘中双倍取样复验,不合格则该批不得交货或逐盘检验。
9.2试验方法:
一般情况下,绘出力一延伸曲线,在过延伸率轴上延伸率为0. 2%的点,划一条与曲线的弹性直线段部分平行的直线,该平行线与曲线的交点对应的应力即为Rp0.2对应的力,用该力除以试样原始横截面积得到Rp0.2。
当力一延伸曲线的弹性直线段部分不明显,不能准确划出平行线时,建议用如下方法:将试样拉伸至略超过预期的Rp0.2对应的力F始后,将力降至F始的10%,然后再将力加至F始,这样在力一延伸曲线上形成滞后环,过滞后环划一直线,然后在过延伸率轴上延伸率为0.2%的点,划一条与该直线平行的线,该平行线与曲线的交点对应的应力即为Rp0.2对应的力,用该力除以试样原始横截面积So得到Rp0.2。公式如下:
冷轧作业指导书
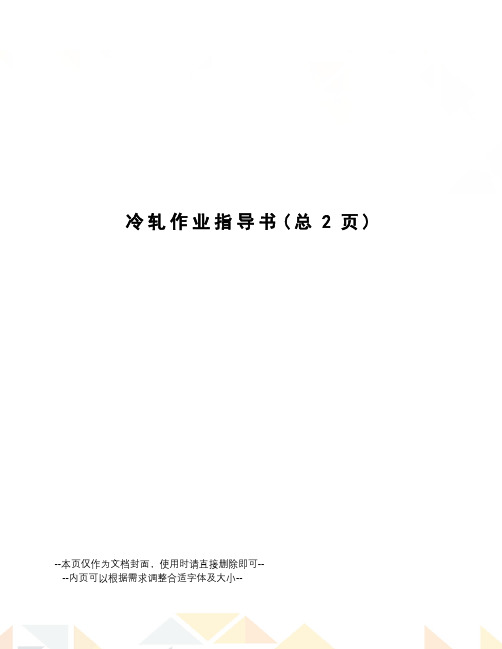
冷轧作业指导书(总2页)--本页仅作为文档封面,使用时请直接删除即可----内页可以根据需求调整合适字体及大小--冷轧作业指导书1、冷轧机分为1-6号机。
2、操作工人上岗前应穿戴好劳护用品,并由当班的管理人员开会安排工作任务及安全方面的注意事项。
3、冷轧工操作时选择与轧机的相符编号的坯管,未经得生产计划部同意不准私自更改轧制规格。
4、原料检查:①原料外表面要求无裂纹、翘皮等缺陷。
②外径、壁厚尺寸要求与生产传票相等。
③所有来料均要切除尾部飞皮,并无毛刺。
④特别检查钢号、标识是否与传票一致。
⑤如果不符合以上要求,需查明原因后才能生产。
5、轧机检查①检查所有按钮是否有效。
②检查所有油路是否正常。
6、轧管装料打开芯杆卡紧装置,将坯管装入芯杆卡紧装置和回转送进箱,进入中间床身的轧制中心线上,同事将坯管卡盘退至后极限位置或坯管长相适宜的位置。
调节三爪或液压夹紧装置将芯棒杆卡紧,并放上芯杆限位装置。
轧制启动开关,使用快捷键使坯管端面和卡盘接近(距离不超过10mm),开始轧制管子。
轧制第一支管子时,应先把送进速度调到低速轧制,并沿管子旋转方向用手带动旋转。
在轧出300mm时,应停机按技术要求进行检查,检查合格后可继续生产,不合格则调整斜楔来调试外径大大小,调整芯杆滑座位置来调试内孔的大小。
直到表面质量和尺寸精度符合生产技术要求。
当卡盘走到前端碰到限位开关时,停止前进,主电机停车,使其快速退回到后端,松开卡盘,等待重新上料再次轧制。
管子轧出轧机箱后,要及时放上刮油装置。
正常轧制后,应把调试管不合格部位切除,整支不合格的应拿出并作好标识和记录(写明钢号和实际尺寸)。
7、所轧坯管检查在调试正常后应检查:外径、壁厚、内孔、长度、直线度是否符合生产传票要求,并取样保留样品(所有精管,即下工序不需要热处理的)取样350mm,其他坯管取样100mm左右。
原则上统一规格取一个样,若中途有更换芯棒,调动轧机应及时取样看是否合格。
轨枕钢筋冷轧、桁架钢筋安装作业指导书
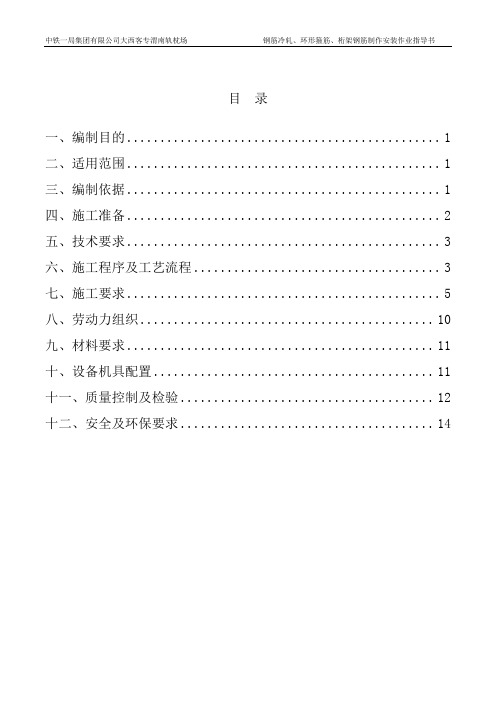
目录一、编制目的 (1)二、适用范围 (1)三、编制依据 (1)四、施工准备 (2)五、技术要求 (3)六、施工程序及工艺流程 (3)七、施工要求 (5)八、劳动力组织 (10)九、材料要求 (11)十、设备机具配置 (11)十一、质量控制及检验 (12)十二、安全及环保要求 (14)CRTSⅠ型双块式无砟轨道双块式轨枕钢筋冷轧、环形箍筋、桁架钢筋制作安装作业指导书一、编制目的明确CRTSⅠ型双块式无砟轨道双块式混凝土轨枕钢筋施工工艺、工艺流程、质量控制要点和质量标准,指导钢筋施工作业,使作业人员能够规范施工,确保轨枕生产用钢筋施工质量。
二、适用范围本作业指导书适用于中铁一局集团有限公司大西客专渭南轨枕场SK-2型双块式轨枕生产用钢筋冷轧、环形箍筋、桁架钢筋制作安装过程的控制。
三、编制依据1。
《新建时速300-350公里客运专线铁路设计暂行规定》(铁建设[2007]47号)2。
《客运专线无砟轨道铁路设计指南》(铁建设函[2005]754号)3。
《客运专线铁路双块式无砟轨道双块式混凝土轨枕暂行技术条件》科技基[2008]74号4。
《CRTSⅠ型双块式无砟轨道双块式轨枕结构设计》通线[2011]2351—Ⅰ5. 相关规范和标准四、施工准备4.1作业人员必须经过岗前培训,熟知工作内容及工作要领,经过考核合格后方可上岗。
4。
2钢筋加工设备试运转正常。
4.3原材料进场存放、标识、检验符合要求,且材料储备量满足生产需求.4.3作业人员必须认真阅读技术交底,看懂施工作业所需的结构、构件,熟悉结构、构件中所需钢筋的型号、种类、材质、数量。
4。
4检查进场钢筋具有出厂合格证、进场检验合格证,在得到物资部门确认后方可投入使用。
4。
5钢筋原材进场检验流程:钢筋进场分规格存放标识(待检)物设部委托试验室进行检验检验合格后发放工班使用.钢筋的堆放存放要求:场地硬化处理、平整、干燥,做到上遮下垫,避免锈蚀或油污;各类钢筋摆放做到分类堆放,标识清楚,易于识别,不产生混淆.4。
冷轧厂卷取岗位作业指导书教材
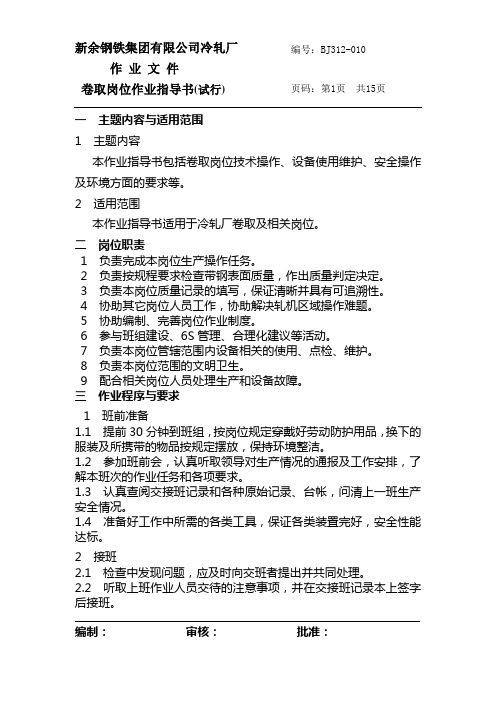
新余钢铁集团有限公司冷轧厂作 业 文 件 卷取岗位作业指导书(试行)编制: 审核: 批准:编号:BJ312-010页码:第1页 共15页一 主题内容与适用范围 1 主题内容本作业指导书包括卷取岗位技术操作、设备使用维护、安全操作及环境方面的要求等。
2 适用范围本作业指导书适用于冷轧厂卷取及相关岗位。
二 岗位职责1 负责完成本岗位生产操作任务。
2 负责按规程要求检查带钢表面质量,作出质量判定决定。
3 负责本岗位质量记录的填写,保证清晰并具有可追溯性。
4 协助其它岗位人员工作,协助解决轧机区域操作难题。
5 协助编制、完善岗位作业制度。
6 参与班组建设、6S 管理、合理化建议等活动。
7 负责本岗位管辖范围内设备相关的使用、点检、维护。
8 负责本岗位范围的文明卫生。
9 配合相关岗位人员处理生产和设备故障。
三 作业程序与要求1 班前准备1.1 提前30分钟到班组,按岗位规定穿戴好劳动防护用品,换下的服装及所携带的物品按规定摆放,保持环境整洁。
1.2 参加班前会,认真听取领导对生产情况的通报及工作安排,了解本班次的作业任务和各项要求。
1.3 认真查阅交接班记录和各种原始记录、台帐,问清上一班生产安全情况。
1.4 准备好工作中所需的各类工具,保证各类装置完好,安全性能达标。
2 接班2.1 检查中发现问题,应及时向交班者提出并共同处理。
2.2 听取上班作业人员交待的注意事项,并在交接班记录本上签字后接班。
编号:BJ312-010页码:第2页共15页3 班中作业3.1技术方面的要求3.1.1操作准备1)按下灯测试按钮,检查信号灯是否正常2)检查卷取机是否打到远程控制3)检查急停是否复位,没有要复位,复位后通知主操人员确认4)确认转盘挡块是否锁紧,没有锁紧要锁紧5)确认转盘锁定销是否锁定,如锁定要解锁6)卷筒涨开7)皮带助卷器上升且抱臂合拢8)接通助卷器皮带张力9)通知主操接通卷取张力10)穿带位外支撑臂抬起11)卷取位上入口和下出口缓冲压辊在缩回状态12)根据计划确认套筒摆放情况,若摆放出错及时与主操联系,并由主操处理13)检查台钢卷小车在中间位置14)检查台缓冲压辊、压辊、引导板在缩回位置15)检查台侧导板在打开位置16)检查台夹送辊在打开位置17)废料剪处于打开位置18)开卷机卷筒处于收缩状态3.1.2卷取操作(穿带)3.1.2.1正常情况下,自动穿带或卸卷操作,只要在画面中选择各自对应自动模式程序执行命令3.1.2.2手动穿带操作1)带头咬入穿带位置卷筒且包上3-5圈,皮带助卷器抱臂松开并下降2)穿带位置外支撑臂缩回3)转盘挡块缩回4)转盘逆时针方向旋转1800卷筒由穿带位置切换至钢卷位置5)转盘挡块锁紧6)卸卷位置钢卷小车驶入卷筒下7)关闭保护门3.1.3手动卸卷操作1)打开钢卷小车侧保护门编号:BJ312-010页码:第3页共15页2)钢卷小车上升(钢卷接触位置)3)钢卷小车上升(至HIGH PRESS位置)4)上、下入口缓冲压辊打开5)外支承臂缩回6)卷筒收缩7)用钢卷小车将钢卷运送至步进梁接管位置3.1.4套筒安装准备1)套筒收集框在占用位置且装满套筒2)套筒1#挡块关闭3.1.5套筒运输及装载操作1)套筒1#挡块打开2)打开套筒2#、3#挡块使套筒滚下至4#套筒挡块上并且完成对中3)将套筒伸出臂前进至套筒装载小车上放下套筒4)套筒装载小车前进将套筒装上卷筒,卷筒涨开5)套筒装载小车返回3.1.6检查台操作3.1.6.1自动上卷操作在正常状态下,钢卷上检查台检查质量为自动程序执行,只要将程序设定为自动方式3.1.6.2手动操作1、操作检查小车将钢卷装上卷筒2、卷筒涨开3、检查小车下降,压辊和缓冲辊应用压住带头,引导板升起。
冷扎钢板冲压成型作业指导书

产品型号产品图号产品名称交流接触器零部件名称 底 板工序名称成 型材料名称冷扎钢板材料牌号Q235-A.F 使用设备63T压力机辅助材料润滑油序号123456注意事项检 验 手 段检测频次责任人目测(自 检/专 检)首检:换模/修模操作者/专检4. 26.3±0.2游标卡尺(自检/专检)自检:5件/小时操作者5. 97.85游标卡尺(自检/专检)巡检:5件/小时专 检6. 20.3游标卡尺(自检/专检)(专检每次记录1个数据)Re=0专 检会签(日期)文件变更代号文件编号作 业 指 导 书合 格 产 品 图 样生产中出现质量问题时,必须立即停机并标识隔离,立即上报,经查明原因并合理解决,经杜绝质量事故发生与出现方可继续生产。
按1200只/小时冲压,将做好的产品和废料放入固定区域内,并做好标识。
操作描述备 料开机检查调试模具毛刷/擦布/拖把辅助工具合格生产材料规格#VALUE!2×140过程检验要求首件检验检验项目检 验 图 样生 产 步 骤游标卡尺具体操作步骤说明核对物料与生产计划一致性。
按点检记录要求进行检查,并记录。
将预备好的产品放入模具凹模内进行成型。
脚踩脚踏板,完成一次成型,成型后的产品与模具末件一致,并用专用检具,游标卡尺检测,合格后在生产。
首件产品放置在首件摆放区域。
清洁设备审核(日期)不良品原因陈述(1)模具破损或有异物在模具里导致变形标识不清修模或调整设备行程高度#VALUE!(2)模具断芯子或行程不到位导致不平变形外观尺寸过 程 检 验不 良 品 图解 决 方 法清理模具或修模分类不良品并上报表面平整、光滑、无毛刺和缺料等编制(日期)不 良 品 的 处 理1. 127活动扳手35MM-75MM标准卡轨/平板百分表/游标卡尺完工后,关闭电源,清洁设备及周边工作场所。
2. 943. 10批量生产气。
冷轧企业换辊作业指导书

1、换银操作1.1工作辘中间馄换馄1.1.1轧机停车关闭乳液1.1.2打到停止状态换辘状态(主控)1.1.3压上汕缸降到最低位(主控)1.1.4提升压下螺杆及上支撑馄平衡装巻到最髙位(主控)1.1.5提升工作辘及中间馄轨道到最高位1.1.6豐上下中间辘横移缸到中间位置(100mm)1.1.7上下接轴扁孔处于垂直位宜(主控)1.1.8接轴抱紧装置夹紧(更换工作馄)1.1.9换工作辘或中间辘都要把四辘的汕雾快速接头卸掉(避免撞断)1.1.10打开所要换下辘的锁板或夹钳1.1.11降下活动盖板1.1.12换馄车大车锁紧缸退回1.1.13空换辘箱对准轧机并开进,在接轨位置锁左大车1.1.14牵引车向前开到抽馄位軋各夹钳夹紧相应的辘头1.1.15开动牵引车抽出旧馄1.1.16牵引车夹钳脱开,后退到极限1.1.17横移车横移,新辘对准轧机窗口1.1.18牵引车前行新辘推入机内1.1.19锁上新辘的锁板或左位夹钳1.1.20打开接轴夹紧装置1.1.21牵引车后退到极限1.1.22大车锁紧缸退回,换馄大车退到后极限位苣锁立1.1.23根据轧制规格进行中间馄横移1.1.24降下上工作馄中间偲轨道1.1.25升起活动盖板1.1.26插上油雾快速接头1.1.27轧制线标高调整a.输入上下工作馄,上中间偲,上支撑伦直径1.1.28升起压上汕缸,馄系压靠零位,准备轧制。
2、换馄注意事项:2.1在标轧制线道上支承辘之前,必须和滑下轨道松开接轴2.2换中间辘,在标轧制线之前必须中间馄是锁紧。
2.3换支承馄,在抽馄之前必须松开靠紧缸。
2.4换辘完毕后,必须装好油雾管。
2.5换馄之前,必须检査新辘是否有缺陷。
2.6横移公式:S=L-B-K2L——工作辘而长度B—一带宽度K——取1003、主控岗位操作规程3.1轧制时的操作步骤前提条件:天传机主画面各泵站、电机、通讯须正常3. 1.1开卷轧制:a、首先将所要轧的卷宗的工艺输入AGC操作机。
冷轧钢板理化试验作业指导书

审核:
编制:
冷轧钢板理化试验作业指导书
序号
检验项目
技术要求
检验方法
1
机械性能
1抗拉强度≥275N/mm²
2伸长率:
板材厚度(mm)长(%)
<0.60≥34
≥0.60 <1.00≥36
≥1.00 <1.60≥37
≥1.60 <2.50≥38
≥2.50≥39
将钢板剪成长220mm,宽20mm的样条,用拉力试验机以20mm/min的速度测试
2
含碳量
≤0.1%
气体容量法:在坩锅底部铺一层硅钼粉和锡粒,然后称取1g钢样放入坩锅中,将坩锅放入燃烧炉中,启动碳硫分析仪,开始试验。试验结果从碳硫分析仪直接读数
3
硬度
按采购标准要求
将一块平整的钢板放在维氏硬度计上,以5kg的压力测试
深圳培训网www55topcom冷轧钢板理化试验作业指导书修订日期修订单号修订内容摘要页次版次修订审核批准20110330更多免费资料下载请进
冷轧钢板理化试验作业指导书
修订
日期
修订
单号
修订内容摘要
页次
版次
修订
审核
批准
2011/03/30
/
系统文件新制定
4
A/0
/
/
/
更多免费资料下载请进:好好学习社区
冷轧加工安全操作手册
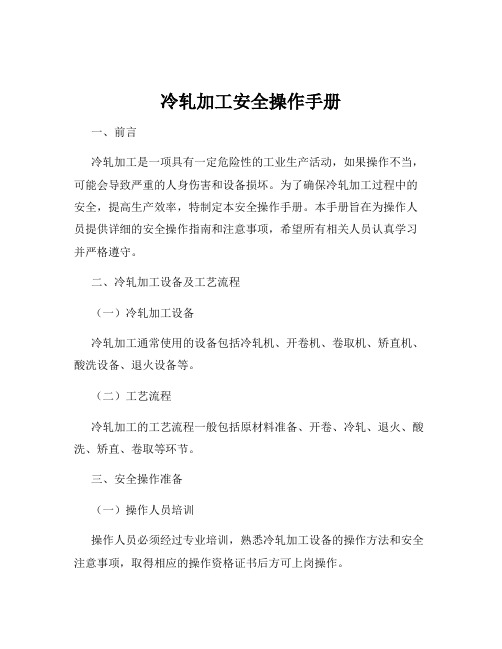
冷轧加工安全操作手册一、前言冷轧加工是一项具有一定危险性的工业生产活动,如果操作不当,可能会导致严重的人身伤害和设备损坏。
为了确保冷轧加工过程中的安全,提高生产效率,特制定本安全操作手册。
本手册旨在为操作人员提供详细的安全操作指南和注意事项,希望所有相关人员认真学习并严格遵守。
二、冷轧加工设备及工艺流程(一)冷轧加工设备冷轧加工通常使用的设备包括冷轧机、开卷机、卷取机、矫直机、酸洗设备、退火设备等。
(二)工艺流程冷轧加工的工艺流程一般包括原材料准备、开卷、冷轧、退火、酸洗、矫直、卷取等环节。
三、安全操作准备(一)操作人员培训操作人员必须经过专业培训,熟悉冷轧加工设备的操作方法和安全注意事项,取得相应的操作资格证书后方可上岗操作。
(二)个人防护装备操作人员在工作时必须穿戴符合标准的个人防护装备,如安全帽、工作服、防护手套、防护鞋、护目镜等。
(三)设备检查在开机前,操作人员必须对设备进行全面检查,包括设备的机械部件、电气系统、润滑系统、冷却系统等,确保设备处于正常状态。
如发现设备存在故障或安全隐患,应及时报告并进行维修。
四、冷轧机安全操作要点(一)开机操作1、开机前,应确保操作人员处于安全位置,设备周围无障碍物。
2、按照操作规程依次启动设备,先启动辅助设备,如润滑系统、冷却系统等,然后再启动主电机。
3、开机过程中,密切观察设备的运行状态,如有异常声音、振动或异味,应立即停机检查。
(二)运行操作1、操作人员应时刻关注设备的运行参数,如轧制力、轧制速度、张力等,确保其在规定范围内。
2、严禁在设备运行过程中进行维修、调试或清理工作。
3、如需要调整设备参数或处理故障,必须停机并采取可靠的安全措施后方可进行。
(三)停机操作1、停机时,应按照操作规程逐步降低设备的运行速度,然后关闭主电机。
2、停机后,应及时清理设备表面的杂物和油污,保持设备的清洁。
五、开卷机和卷取机安全操作要点(一)开卷操作1、开卷前,应检查卷材的质量和规格,确保符合生产要求。
冷轧企业成品发货作业指导书
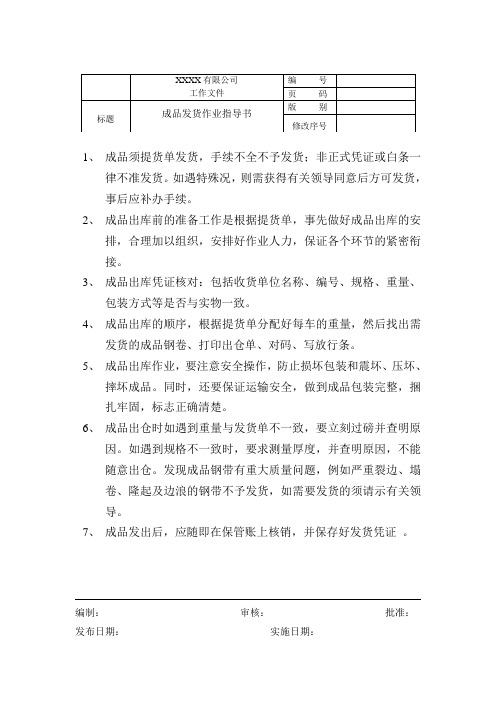
1、成品须提货单发货,手续不全不予发货;非正式凭证或白条一
律不准发货。
如遇特殊况,则需获得有关领导同意后方可发货,事后应补办手续。
2、成品出库前的准备工作是根据提货单,事先做好成品出库的安
排,合理加以组织,安排好作业人力,保证各个环节的紧密衔
接。
3、成品出库凭证核对:包括收货单位名称、编号、规格、重量、
包装方式等是否与实物一致。
4、成品出库的顺序,根据提货单分配好每车的重量,然后找出需
发货的成品钢卷、打印出仓单、对码、写放行条。
5、成品出库作业,要注意安全操作,防止损坏包装和震坏、压坏、
摔坏成品。
同时,还要保证运输安全,做到成品包装完整,捆
扎牢固,标志正确清楚。
6、成品出仓时如遇到重量与发货单不一致,要立刻过磅并查明原
因。
如遇到规格不一致时,要求测量厚度,并查明原因,不能
随意出仓。
发现成品钢带有重大质量问题,例如严重裂边、塌
卷、隆起及边浪的钢带不予发货,如需要发货的须请示有关领
导。
7、成品发出后,应随即在保管账上核销,并保存好发货凭证。
编制:审核:批准:
发布日期:实施日期:。
冷轧企业硬度测量作业指导书

1、机械操作过程
参阅硬度计说明书
2、软件操作说明
2.1、点击“进行分析/新采样”按钮进入分析程序。
2.2、试验完毕再次点击“进行分析/新采样”按钮进入分析
程序。
2.3、分析完毕,显示第一次试验结果,点击“继续采样”按
钮,重复2.2步骤。
2.4、试验4-5次后点击“数据显示”按钮,弹出数据显示
数据窗口显示文件名,操作日期/时间、试样号、仪
器号、试验力、力保持时间、试验次数以及每次试验
数据和平均数、最大/最小值、分散度、极差、操作
员工员等数据。
2.5、点击“打印”输出试验报告。
编制:审核:批准:
发布日期:实施日期:。
冷轧扭钢筋生产作业指导书
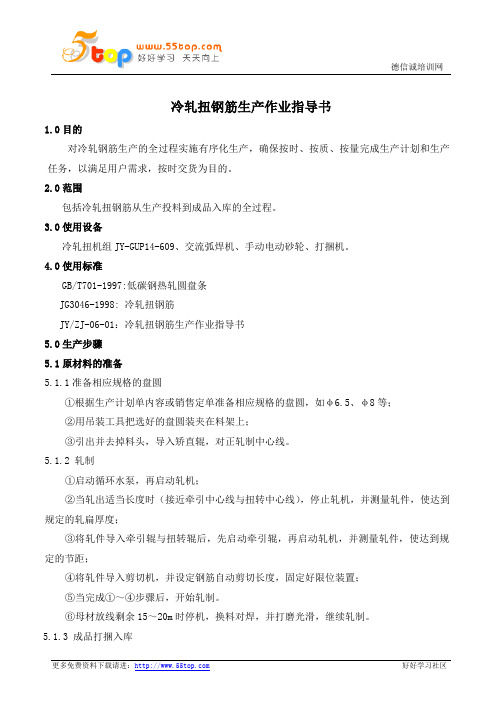
冷轧扭钢筋生产作业指导书1.0目的对冷轧钢筋生产的全过程实施有序化生产,确保按时、按质、按量完成生产计划和生产任务,以满足用户需求,按时交货为目的。
2.0范围包括冷轧扭钢筋从生产投料到成品入库的全过程。
3.0使用设备冷轧扭机组JY-GUP14-609、交流弧焊机、手动电动砂轮、打捆机。
4.0使用标准GB/T701-1997:低碳钢热轧圆盘条JG3046-1998: 冷轧扭钢筋JY/ZJ-06-01:冷轧扭钢筋生产作业指导书5.0生产步骤5.1原材料的准备5.1.1准备相应规格的盘圆①根据生产计划单内容或销售定单准备相应规格的盘圆,如φ6.5、φ8等;②用吊装工具把选好的盘圆装夹在料架上;③引出并去掉料头,导入矫直辊,对正轧制中心线。
5.1.2 轧制①启动循环水泵,再启动轧机;②当轧出适当长度时(接近牵引中心线与扭转中心线),停止轧机,并测量轧件,使达到规定的轧扁厚度;③将轧件导入牵引辊与扭转辊后,先启动牵引辊,再启动轧机,并测量轧件,使达到规定的节距;④将轧件导入剪切机,并设定钢筋自动剪切长度,固定好限位装置;⑤当完成①~④步骤后,开始轧制。
⑥母材放线剩余15~20m时停机,换料对焊,并打磨光滑,继续轧制。
5.1.3 成品打捆入库①每捆冷轧扭钢筋应是同牌号、同规格和同长度尺寸的钢筋。
每捆应有两个以上标签。
标签上应标志厂名、产品名称、规格和长度、数量及生产日期;②冷轧扭钢筋应成捆交货,每捆两头用铁丝捆扎。
当长度大于6m时,每捆应有三处捆扎点。
6.0使用表格6.1《工序流程卡》6.2《领料单》6.3《(生产过程)入库单》。
冷轧机作业指导书.doc

1450毫米四辗不可逆冷轧机作业指导书中色万基技术质量部一、目的二、使用范围三、质量职责四、工作步骤1目的规范1450轧机操作动作,预防误操作2使用范围1450四车昆不可逆冷轧机3质量职责1450冷轧机质量控制项目及责任人4工作步骤4.1启动准备4.1.1检查二氧化碳灭火系统正常,满足开车条件。
4. 1.2水、风压力符合开车要求。
4. 1. 3各有关部位检查正常后,机组安全送电。
4. 1.4各液压系统启动,并投入工作,操作台上显示正常。
4.1.5各工艺润滑系统启动,并投入工作,操作台上显示正常。
4.1.6稀油润滑系统启动,并投入工作,操作台上显示正常,检查各有关润滑部位的油流情况。
4.1.7油气润滑系统启动,并投入工作,操作台上显示正常,检查各有关润滑部位的润滑情况。
4. 1. 8各干油润滑点注满干油。
4. 1.9排烟罩抽风系统、主电机、开卷、卷取电机冷却水,冷却风机及油地下室的通风系统启动并投入工作,操作台上显示正常。
4. 1. 10压缩空气系统处于准备工作状态,操作台上显示正常。
4.2操作准备4.2.1上卷车停在取料位置,托座处于下极限位置。
422\开卷机谊动加莎拯L,了函状态,饬魏翊处于嗣立置。
4.2.3申缩缸处于万爾立置,極擬动缸处于辭位置,|捌騎擬于萄k立置,麽处于殛位置,屢匍处于[3立置。
4.2.4置处于函溯立置并用销子锁住;|么.唸磁瞬俅出口侧防蘆隸出口尿; 处于莎位置;轧轮轴向I倔危磁齢止场徹辰礙約处于态。
4.2.51渤翱装置处于阈位置。
4.2.6导向装置,不用助卷器时矩窮憾殊|芥專翊也用助卷器时豆険銀@ \ 档離血4.2.7 料板处于國位置;加翊a入莎f立置;卷筒处于宓状态(灯不亮)。
4.2.8不用助卷器时,|戲隱鑼处于莎极限位置;用匾麴时,处于阪位置。
4.29 殛敎于待料位置,愛处于下极限位置。
4.2.10企稣廖处于翩位置,土套筒拨》处于囲位置;御蚩筒义已处于期位置,御迤/箴超烛处于凝位置。
1450冷轧指导书
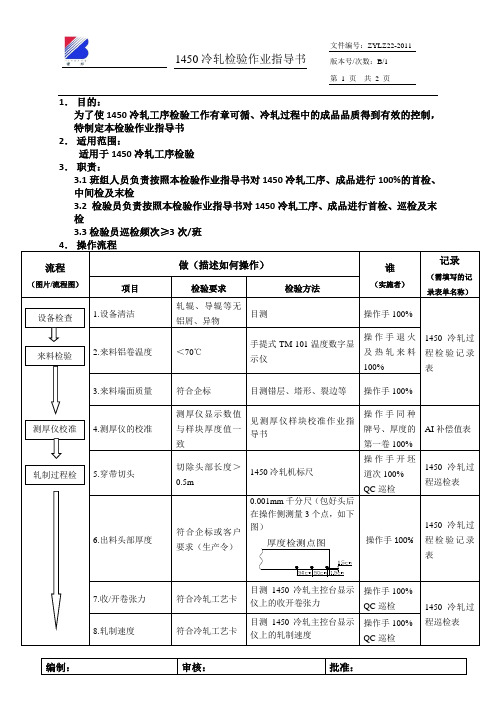
1450 冷轧检验作业指导书
版本号/次数:B/1 第 1 页 共 2 页
1. 目的: . 目的: 为了使 工序检验工作有章可循 检验工作有章可循、 过程中的成品品质得到有效的控制, 成品品质得到有效的控制 为了使 1450 冷轧工序检验工作有章可循、冷轧过程中的成品品质得到有效的控制, 特制定本检验作业指导书 特制定本检验作业指导书 2. 适用范围: . 适用范围: 冷轧工序检验 适用于 1450 冷轧工序检验 3. 职责: . 职责: 3.1 班组人员负责按照本检验作业指导书对 1450 冷轧工序、成品进行 100%的首检、 班组人员负责按照本检验作业指导书对 工序、成品进行 的首检、 的首检 中间检及末检 3.2 检验员负责按照本检验作业指导书对 1450 冷轧工序、成品进行首检、巡检及末 检验员负责按照本检验作业指导书 检验作业指导书对 工序、成品进行首检、 进行首检 检 3.3 检验员巡检频次≥3 次/班 检验员巡检频次≥ 班 4. 操作流程 . 流程
来料检验
2.来料铝卷温度
3.来料端面质量
符合企标 测厚仪显示数值
目测错层、塔形、裂边等 见测厚仪样块校准作业指 导书
操作手 100% 操作手同种 牌号、厚度的 第一卷 100% 操作手开坯 AI 补偿值表
测厚仪校准
4.测厚仪的校准
与样块厚度值一 致
轧制过程检
切除头部长度> 5.穿带切头 0.5m
1450 冷轧机标尺 0.001mm 千分尺(包好头后 在操作侧测量 3 个点,如下 图)
8.轧制速度
符合冷轧工艺卡
编制: 编制:
审核: 审核:
批准: 批准:
文件编号:ZYLZ22-2011
1450 冷轧检验作业指导书
- 1、下载文档前请自行甄别文档内容的完整性,平台不提供额外的编辑、内容补充、找答案等附加服务。
- 2、"仅部分预览"的文档,不可在线预览部分如存在完整性等问题,可反馈申请退款(可完整预览的文档不适用该条件!)。
- 3、如文档侵犯您的权益,请联系客服反馈,我们会尽快为您处理(人工客服工作时间:9:00-18:30)。
冷轧作业指导书
-标准化文件发布号:(9456-EUATWK-MWUB-WUNN-INNUL-DDQTY-KII
冷轧作业指导书
1、冷轧机分为1-6号机。
2、操作工人上岗前应穿戴好劳护用品,并由当班的管理人员开会安排工作
任务及安全方面的注意事项。
3、冷轧工操作时选择与轧机的相符编号的坯管,未经得生产计划部同意不
准私自更改轧制规格。
4、原料检查:
①原料外表面要求无裂纹、翘皮等缺陷。
②外径、壁厚尺寸要求与生产传票相等。
③所有来料均要切除尾部飞皮,并无毛刺。
④特别检查钢号、标识是否与传票一致。
⑤如果不符合以上要求,需查明原因后才能生产。
5、轧机检查
①检查所有按钮是否有效。
②检查所有油路是否正常。
6、轧管
6.1装料
打开芯杆卡紧装置,将坯管装入芯杆卡紧装置和回转送进箱,进入中间床身的轧制中心线上,同事将坯管卡盘退至后极限位置或坯管长相适宜的位置。
调节三爪或液压夹紧装置将芯棒杆卡紧,并放上芯杆限位装置。
6.2 轧制
启动开关,使用快捷键使坯管端面和卡盘接近(距离不超过10mm),开始轧制管子。
轧制第一支管子时,应先把送进速度调到低速轧制,并沿管子旋转方向用手带动旋转。
在轧出300mm时,应停机按技术要求进行检查,检查合格后可继续生产,不合格则调整斜楔来调试外径大大小,调整芯杆滑座位置来调试内孔的大小。
直到表面质量和尺寸精度符合生产技术要求。
当卡盘走到前端碰到限位开关时,停止前进,主电机停车,使其快速退回到后端,松开卡盘,等待重新上料再次轧制。
管子轧出轧机箱后,要及时放上刮油装置。
正常轧制后,应把调试管不合格部位切除,整支不合格的应拿出并作好标识和记录(写明钢号和实际尺寸)。
7、所轧坯管检查
7.1 在调试正常后应检查:外径、壁厚、内孔、长度、直线度是否符合生产
传票要求,并取样保留样品(所有精管,即下工序不需要热处理的)
取样350mm,其他坯管取样100mm左右。
原则上统一规格取一个
样,若中途有更换芯棒,调动轧机应及时取样看是否合格。
7.2 外观:内外表面光滑,不得有耳子、划伤、裂口及凹坑现象;耳子和裂
口应及时解决和切除。
7.3 若有芯棒断裂应将其选出,并把有芯棒部位的管子切除。
所有精轧管轧
制后弯曲明显,应立即停止,并通知调整员。
7.4 不合格产品应做好标识,单独堆放。
7.5 轧管完成后填写记录单及冷轧卡片(所有精管用规定的塑料标签),并
在冷轧卡片上写好下一工序(如打尖、退火、中切等)。
按我公司油
漆色标要求涂上油漆。
冷轧色标标识规定:
①所有10#一端涂黄油漆
②所有40Cr一端涂红油漆
③所有35#一端涂绿油漆
④所有20#一端涂白油漆
8、油洗
轧机工每件管子扎完后,吊入相应的堆码框,由调试人员把需浸油清洗的精管进行油洗工作,油洗滴干后放入相应的堆码框,并放好标识牌。
9、下料
①接到下料计划后在计划安排人员处领料。
安排人员和下料工都应检查原
料是否符合下料标准。
②按下料规格调整压板及左右宽度,保证下料尺寸符合要求。
添加乳化液
(桥壳管还应添加亚硝酸液)。
③齐头锯切时应分情况处理:
1.叉管齐头锯切应2-3cm,桥壳管应1cm左右。
2.齐头锯切时若发现裂口,应在裂口部位后1cm出锯切。
④下料过程中发现管子弯曲应及时通知相关人员,由其决定是否下料。
⑤第一次自动送进下料。
送进完成后应手动测量是否符合长度要求,前五
次必须每次用标准直尺和角尺测量下料长度和倾斜度。
⑥桥壳管下料时如发现锈蚀的应单独堆放,并做好记号。
⑦下料过程中该排料下完,第二排料开始时应抽查一次长度和倾斜度。
⑧按计划规定的数量完成下料工作。
⑨当天的尾料原则上当天改完。
⑩每框下料,完成后应把铁屑吹干净,毛刺整理完,然后放到指定地方。
⑪单支不好排料的管子应做好标识,写好标识牌,不准随地乱扔,应放入料框。
⑫下班前填好记录,做好周边清洁,等待交接班。
10、特别说明
冷轧管和锯床下料的桥壳管不准混堆,严禁油污附在退火后的下料管上。
11、标记标识
调整好长度止端距离及钻花高度,第一支应用同规格的废料进项调整,调试好了之后再成品管。