挑撞生产流程图
钣金车间生产流程图
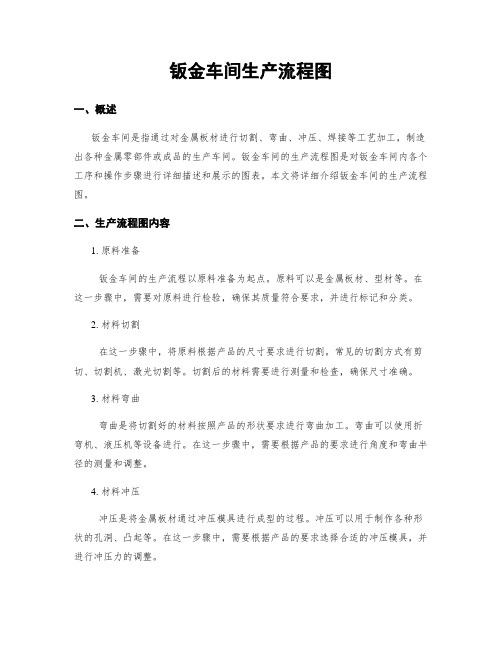
钣金车间生产流程图一、概述钣金车间是指通过对金属板材进行切割、弯曲、冲压、焊接等工艺加工,制造出各种金属零部件或成品的生产车间。
钣金车间的生产流程图是对钣金车间内各个工序和操作步骤进行详细描述和展示的图表。
本文将详细介绍钣金车间的生产流程图。
二、生产流程图内容1. 原料准备钣金车间的生产流程以原料准备为起点。
原料可以是金属板材、型材等。
在这一步骤中,需要对原料进行检验,确保其质量符合要求,并进行标记和分类。
2. 材料切割在这一步骤中,将原料根据产品的尺寸要求进行切割。
常见的切割方式有剪切、切割机、激光切割等。
切割后的材料需要进行测量和检查,确保尺寸准确。
3. 材料弯曲弯曲是将切割好的材料按照产品的形状要求进行弯曲加工。
弯曲可以使用折弯机、液压机等设备进行。
在这一步骤中,需要根据产品的要求进行角度和弯曲半径的测量和调整。
4. 材料冲压冲压是将金属板材通过冲压模具进行成型的过程。
冲压可以用于制作各种形状的孔洞、凸起等。
在这一步骤中,需要根据产品的要求选择合适的冲压模具,并进行冲压力的调整。
5. 材料焊接焊接是将不同的金属板材通过焊接工艺连接在一起的过程。
焊接可以使用电弧焊、气体焊等方式进行。
在这一步骤中,需要进行焊接工艺参数的设定,并进行焊缝的质量检查。
6. 表面处理表面处理是对产品进行防腐、美观处理的过程。
常见的表面处理方式有喷涂、电镀、激光雕刻等。
在这一步骤中,需要根据产品的要求选择合适的表面处理方式,并进行表面质量的检查。
7. 组装组装是将各个零部件按照产品的要求进行组合的过程。
在这一步骤中,需要进行零部件的配对、装配工艺的设定,并进行组装质量的检查。
8. 检验检验是对成品进行质量检查的过程。
在这一步骤中,需要对成品进行尺寸、外观、功能等方面的检查,并记录检验结果。
9. 包装和出货包装和出货是将成品进行包装和运输的过程。
在这一步骤中,需要选择合适的包装材料和包装方式,并进行出货前的最终检查。
三、生产流程图的作用1. 优化生产流程生产流程图可以帮助钣金车间的管理人员和工人清晰地了解整个生产流程,发现并优化生产中的瓶颈和不合理之处,提高生产效率。
分析引起撞件过程的流程图
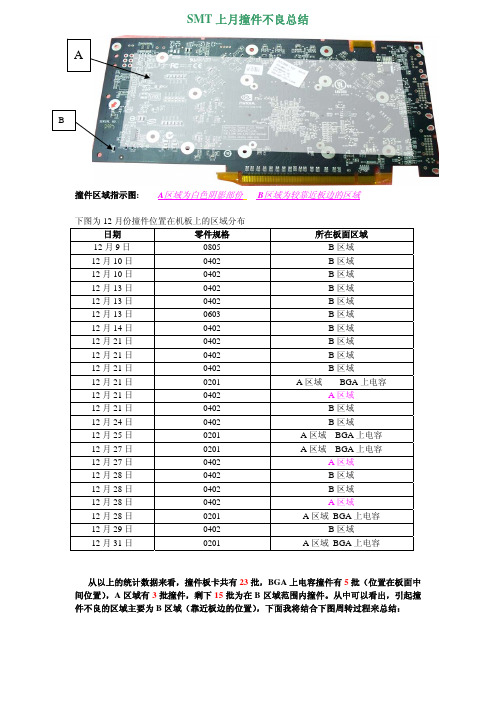
SMT上月撞件不良总结撞件区域指示图:A区域为白色阴影部份 B区域为较靠近板边的区域下图为12月份撞件位置在机板上的区域分布日期零件规格所在板面区域12月9日 0805 B区域12月10日 0402 B区域12月10日 0402 B区域12月13日 0402 B区域12月13日 0402 B区域12月13日 0603 B区域12月14日 0402 B区域12月21日 0402 B区域12月21日 0402 B区域12月21日 0402 B区域12月21日 0201 A区域BGA上电容12月21日 0402 A区域12月21日 0402 B区域12月24日 0402 B区域12月25日 0201 A区域BGA上电容12月27日 0201 A区域BGA上电容12月27日 0402 A区域12月28日 0402 B区域12月28日 0402 B区域12月28日 0402 A区域12月28日 0201 A区域 BGA上电容12月29日 0402 B区域12月31日 0201 A区域 BGA上电容从以上的统计数据来看,撞件板卡共有23批,BGA上电容撞件有5批(位置在板面中间位置),A区域有3批撞件,剩下15批为在B区域范围内撞件。
从中可以看出,引起撞件不良的区域主要为B区域(靠近板边的位置),下面我将结合下图周转过程来总结:下图为SMT过炉后板卡到FQA检验的周转过程:据统计初步认为以下各方面存在撞件的因素项目撞件隐患建议1、炉后捡板a、炉后接板人员接板不及时,造成炉后叠板导致板边撞件。
b、如为铝架过炉,从铝架取板不慎造成撞件a、炉后捡板要及时,避免叠板b、取板要轻拿轻放2、把机板插入静电框的动作从上图可以看出从机板过炉后至FQA检验,插入周转框的次数频繁,如不慎,很容易造成撞到板边零件。
插入机板时要轻且避免碰到别的机板用静电框边3、静电框的搬运从上图看出,静电框的搬运也较频繁,主要分为两种情况:a、人员拿静电框时数量过多,(有时2-3框),容易造成机板倾倒导致撞件.每一次最好是拿一个静电框,用双手拿住框的两边较稳。
钣金车间生产流程图
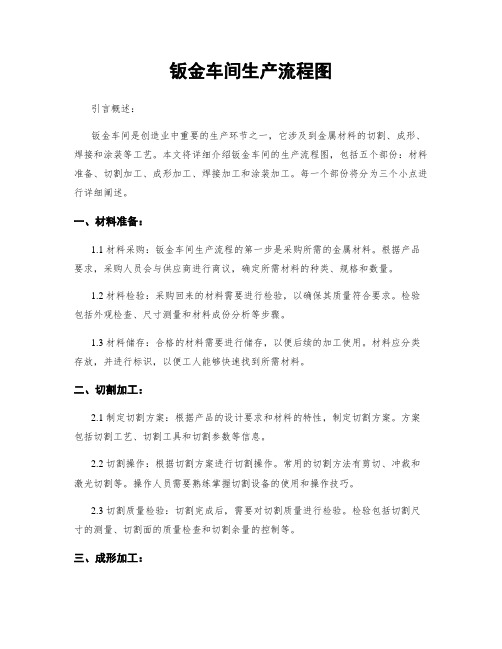
钣金车间生产流程图引言概述:钣金车间是创造业中重要的生产环节之一,它涉及到金属材料的切割、成形、焊接和涂装等工艺。
本文将详细介绍钣金车间的生产流程图,包括五个部份:材料准备、切割加工、成形加工、焊接加工和涂装加工。
每一个部份将分为三个小点进行详细阐述。
一、材料准备:1.1 材料采购:钣金车间生产流程的第一步是采购所需的金属材料。
根据产品要求,采购人员会与供应商进行商议,确定所需材料的种类、规格和数量。
1.2 材料检验:采购回来的材料需要进行检验,以确保其质量符合要求。
检验包括外观检查、尺寸测量和材料成份分析等步骤。
1.3 材料储存:合格的材料需要进行储存,以便后续的加工使用。
材料应分类存放,并进行标识,以便工人能够快速找到所需材料。
二、切割加工:2.1 制定切割方案:根据产品的设计要求和材料的特性,制定切割方案。
方案包括切割工艺、切割工具和切割参数等信息。
2.2 切割操作:根据切割方案进行切割操作。
常用的切割方法有剪切、冲裁和激光切割等。
操作人员需要熟练掌握切割设备的使用和操作技巧。
2.3 切割质量检验:切割完成后,需要对切割质量进行检验。
检验包括切割尺寸的测量、切割面的质量检查和切割余量的控制等。
三、成形加工:3.1 选择成形工艺:根据产品的形状和要求,选择合适的成形工艺。
常用的成形工艺有折弯、拉伸和冲压等。
3.2 成形操作:根据成形工艺进行成形操作。
操作人员需要掌握成形设备的使用和操作技巧,确保成形过程中材料的形状和尺寸符合要求。
3.3 成形质量检验:成形完成后,需要对成形质量进行检验。
检验包括尺寸测量、表面质量检查和形状偏差的控制等。
四、焊接加工:4.1 焊接准备:根据产品的设计要求和焊接工艺,准备焊接所需的材料和设备。
材料包括焊接电极、焊接材料和保护气体等。
4.2 焊接操作:根据焊接工艺进行焊接操作。
操作人员需要熟练掌握焊接设备的使用和操作技巧,确保焊接接头的质量和强度。
4.3 焊接质量检验:焊接完成后,需要对焊接质量进行检验。
钣金车间生产流程图
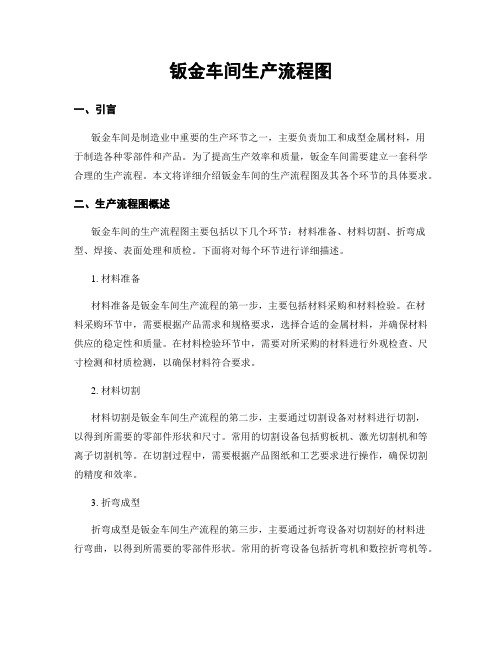
钣金车间生产流程图一、引言钣金车间是制造业中重要的生产环节之一,主要负责加工和成型金属材料,用于制造各种零部件和产品。
为了提高生产效率和质量,钣金车间需要建立一套科学合理的生产流程。
本文将详细介绍钣金车间的生产流程图及其各个环节的具体要求。
二、生产流程图概述钣金车间的生产流程图主要包括以下几个环节:材料准备、材料切割、折弯成型、焊接、表面处理和质检。
下面将对每个环节进行详细描述。
1. 材料准备材料准备是钣金车间生产流程的第一步,主要包括材料采购和材料检验。
在材料采购环节中,需要根据产品需求和规格要求,选择合适的金属材料,并确保材料供应的稳定性和质量。
在材料检验环节中,需要对所采购的材料进行外观检查、尺寸检测和材质检测,以确保材料符合要求。
2. 材料切割材料切割是钣金车间生产流程的第二步,主要通过切割设备对材料进行切割,以得到所需要的零部件形状和尺寸。
常用的切割设备包括剪板机、激光切割机和等离子切割机等。
在切割过程中,需要根据产品图纸和工艺要求进行操作,确保切割的精度和效率。
3. 折弯成型折弯成型是钣金车间生产流程的第三步,主要通过折弯设备对切割好的材料进行弯曲,以得到所需要的零部件形状。
常用的折弯设备包括折弯机和数控折弯机等。
在折弯成型过程中,需要根据产品图纸和工艺要求进行操作,确保折弯的角度和尺寸准确。
4. 焊接焊接是钣金车间生产流程的第四步,主要通过焊接设备将零部件进行连接,以得到所需要的产品形状。
常用的焊接设备包括手工电弧焊机、气体保护焊机和激光焊接机等。
在焊接过程中,需要根据产品图纸和工艺要求进行操作,确保焊接的强度和质量。
5. 表面处理表面处理是钣金车间生产流程的第五步,主要通过表面处理设备对产品进行除锈、喷涂和镀膜等处理,以提高产品的表面质量和耐腐蚀性能。
常用的表面处理设备包括除锈机、喷涂设备和电镀设备等。
在表面处理过程中,需要根据产品要求和工艺要求进行操作,确保表面处理的效果和质量。
钣金车间生产流程图
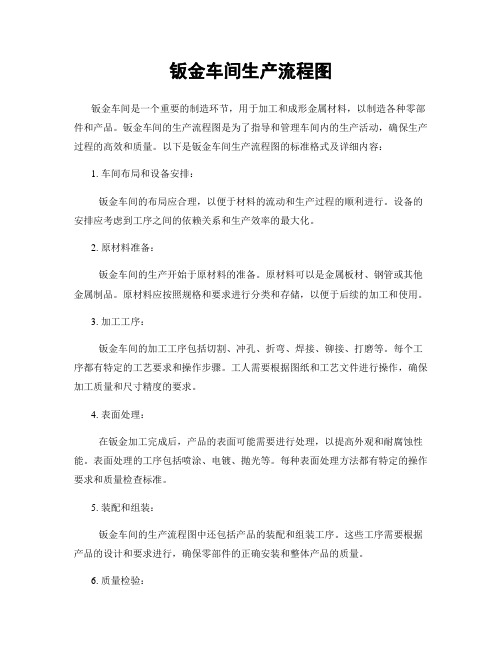
钣金车间生产流程图钣金车间是一个重要的制造环节,用于加工和成形金属材料,以制造各种零部件和产品。
钣金车间的生产流程图是为了指导和管理车间内的生产活动,确保生产过程的高效和质量。
以下是钣金车间生产流程图的标准格式及详细内容:1. 车间布局和设备安排:钣金车间的布局应合理,以便于材料的流动和生产过程的顺利进行。
设备的安排应考虑到工序之间的依赖关系和生产效率的最大化。
2. 原材料准备:钣金车间的生产开始于原材料的准备。
原材料可以是金属板材、钢管或其他金属制品。
原材料应按照规格和要求进行分类和存储,以便于后续的加工和使用。
3. 加工工序:钣金车间的加工工序包括切割、冲孔、折弯、焊接、铆接、打磨等。
每个工序都有特定的工艺要求和操作步骤。
工人需要根据图纸和工艺文件进行操作,确保加工质量和尺寸精度的要求。
4. 表面处理:在钣金加工完成后,产品的表面可能需要进行处理,以提高外观和耐腐蚀性能。
表面处理的工序包括喷涂、电镀、抛光等。
每种表面处理方法都有特定的操作要求和质量检查标准。
5. 装配和组装:钣金车间的生产流程图中还包括产品的装配和组装工序。
这些工序需要根据产品的设计和要求进行,确保零部件的正确安装和整体产品的质量。
6. 质量检验:在钣金车间生产流程的各个环节中,质量检验是一个非常重要的环节。
质量检验可以包括尺寸检查、外观检查、功能测试等。
质量检验的结果将决定产品是否合格,是否可以进入下一个生产环节或出货。
7. 包装和出货:钣金车间生产流程的最后一个环节是产品的包装和出货。
产品应按照客户的要求进行包装,并进行标识和记录。
包装的目的是保护产品不受损坏,并确保产品在运输过程中的安全。
钣金车间生产流程图是车间管理和生产指导的重要工具。
它可以帮助车间管理者和工人了解整个生产过程的顺序和要求,提高生产效率和产品质量。
同时,生产流程图也可以用于培训新员工,使他们快速掌握工序和操作要点。
通过不断优化和改进生产流程图,钣金车间可以实现更高效、更精确的生产,满足客户的需求和要求。
起重机生产流程图
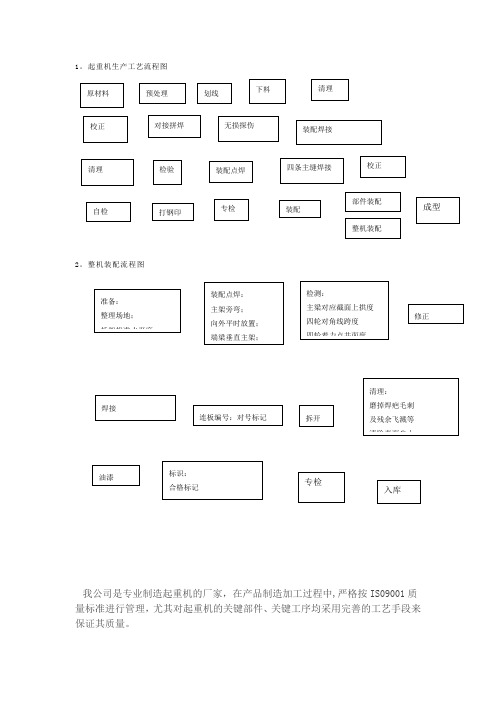
1。
起重机生产工艺流程图2。
整机装配流程图我公司是专业制造起重机的厂家,在产品制造加工过程中,严格按IS09001质量标准进行管理,尤其对起重机的关键部件、关键工序均采用完善的工艺手段来保证其质量。
一、板材及型材的预处理为保证金属结构的防腐和增强油漆的附着力,所有板材和型材在下料前均在我厂自备的预处理设备上进行抛丸预处理,除锈等级达到GB8923标准规定的Sa2。
5级,除锈后立即双面喷涂底漆予以保护,然后才转入下料工序.二、起重机金属结构(桥架的加工)1、主梁、端梁等主要受力结构件采用GB/T1591—94S标准中Q235—B碳素结构钢板制造,次要受力件和非受力构件如走台、罩子等零部件采用Q235-A钢材制造,桥架中所采用的材料均需具有炉号、批号、材料化学成份、机械性能的试验报告及出厂合格证书,材料到厂后由质检部门取样进行理化复检,合格的材料方可投入车间进行产品制造.2、腹板及上盖板的下料采用微机控制的大型火焰数控切割机双枪一次切割,可根据不同跨度工况条件割出二次曲线,四次曲线及二、四线的迭加曲线,有效地保证了起重机的预制拱度,使预制拱度与起重机上拱曲线相吻合,此预拱度值根据主梁制造工艺过程中每一道工序进行严格控制。
3、主梁的焊接有焊接和拼装工艺,通过焊接顺序的合理安排减少起重机的焊接变形。
4、主梁腹板和上、下盖板的对接焊接缝均采用埋弧自动焊,主梁和端梁的纵向焊缝采用微机控制的二氧化碳气体自动保护焊,焊后进行100%探伤。
5、焊接完成后,进行时效处理清除焊接应力。
注:我厂起重机主梁焊接工艺获得河南省技术进步一等奖。
三、桥架组装焊接1、主梁、端梁组装焊接:将验收合格的两根主梁摆放在垫架上,以主梁的上盖板中心线为基准点,按技术要求调整各部分尺寸。
为使桥架安装车轮后能正常运行、组装时将四组弯板采用水平仪测量调在同一平面内。
并以水平面为组装调整门架各部的基准,达到要求后才能焊接.2、桥架组装对接的立焊缝在大型的翻转工装上焊接,将立焊缝全部改为平焊,确保了焊接质量.3、主梁、端梁、小车架等结构件均在厂房内制造、组装、检验,确保不受环境温度、日照变形的影响,尺寸精度受到严格的控制.主梁、端梁、小车架都是在专用铸造平台上制造,从而保证有效地控制尺寸和变形。
钣金车间生产流程图
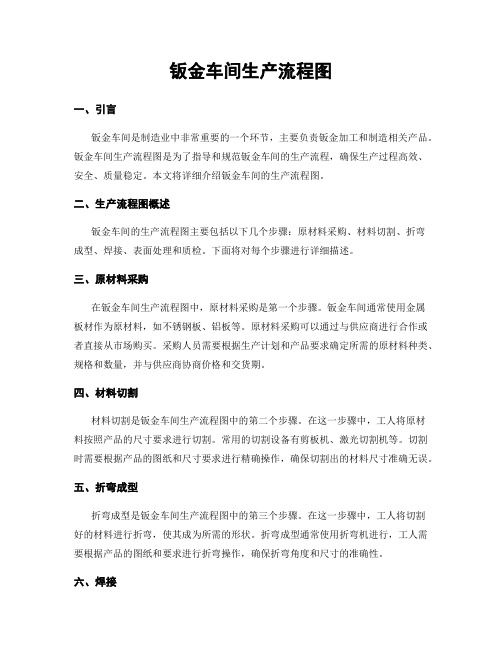
钣金车间生产流程图一、引言钣金车间是制造业中非常重要的一个环节,主要负责钣金加工和制造相关产品。
钣金车间生产流程图是为了指导和规范钣金车间的生产流程,确保生产过程高效、安全、质量稳定。
本文将详细介绍钣金车间的生产流程图。
二、生产流程图概述钣金车间的生产流程图主要包括以下几个步骤:原材料采购、材料切割、折弯成型、焊接、表面处理和质检。
下面将对每个步骤进行详细描述。
三、原材料采购在钣金车间生产流程图中,原材料采购是第一个步骤。
钣金车间通常使用金属板材作为原材料,如不锈钢板、铝板等。
原材料采购可以通过与供应商进行合作或者直接从市场购买。
采购人员需要根据生产计划和产品要求确定所需的原材料种类、规格和数量,并与供应商协商价格和交货期。
四、材料切割材料切割是钣金车间生产流程图中的第二个步骤。
在这一步骤中,工人将原材料按照产品的尺寸要求进行切割。
常用的切割设备有剪板机、激光切割机等。
切割时需要根据产品的图纸和尺寸要求进行精确操作,确保切割出的材料尺寸准确无误。
五、折弯成型折弯成型是钣金车间生产流程图中的第三个步骤。
在这一步骤中,工人将切割好的材料进行折弯,使其成为所需的形状。
折弯成型通常使用折弯机进行,工人需要根据产品的图纸和要求进行折弯操作,确保折弯角度和尺寸的准确性。
六、焊接焊接是钣金车间生产流程图中的第四个步骤。
在这一步骤中,工人将折弯好的材料进行焊接,使其固定在一起。
焊接可以使用手工焊接或者自动焊接设备进行。
焊接时需要根据产品的要求进行精确的焊接操作,确保焊接强度和质量。
七、表面处理表面处理是钣金车间生产流程图中的第五个步骤。
在这一步骤中,工人将焊接好的产品进行表面处理,如打磨、喷涂等。
表面处理可以提高产品的美观度和耐腐蚀性。
表面处理的方式可以根据产品的要求进行选择,确保产品的质量和外观。
八、质检质检是钣金车间生产流程图中的最后一个步骤。
在这一步骤中,质检人员对生产好的产品进行检查,确保产品符合质量标准和要求。
钣金车间生产流程图
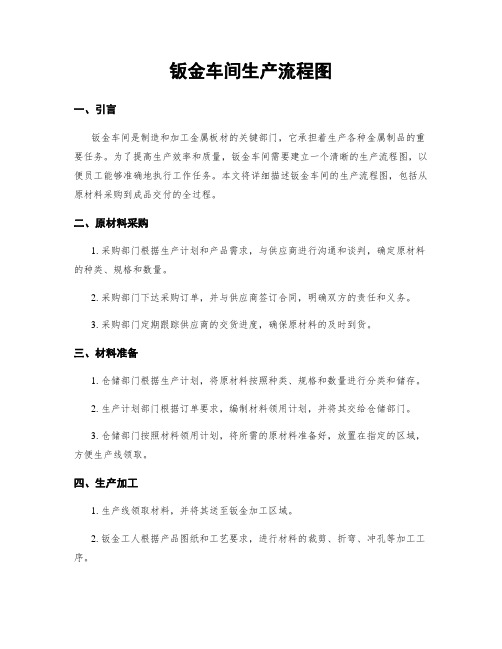
钣金车间生产流程图一、引言钣金车间是制造和加工金属板材的关键部门,它承担着生产各种金属制品的重要任务。
为了提高生产效率和质量,钣金车间需要建立一个清晰的生产流程图,以便员工能够准确地执行工作任务。
本文将详细描述钣金车间的生产流程图,包括从原材料采购到成品交付的全过程。
二、原材料采购1. 采购部门根据生产计划和产品需求,与供应商进行沟通和谈判,确定原材料的种类、规格和数量。
2. 采购部门下达采购订单,并与供应商签订合同,明确双方的责任和义务。
3. 采购部门定期跟踪供应商的交货进度,确保原材料的及时到货。
三、材料准备1. 仓储部门根据生产计划,将原材料按照种类、规格和数量进行分类和储存。
2. 生产计划部门根据订单要求,编制材料领用计划,并将其交给仓储部门。
3. 仓储部门按照材料领用计划,将所需的原材料准备好,放置在指定的区域,方便生产线领取。
四、生产加工1. 生产线领取材料,并将其送至钣金加工区域。
2. 钣金工人根据产品图纸和工艺要求,进行材料的裁剪、折弯、冲孔等加工工序。
3. 完成加工的零件经过质检部门的检验,合格的零件送至下一道工序,不合格的零件退回进行返工。
4. 经过一系列的加工工序,最终形成成品零件。
五、组装与焊接1. 成品零件按照产品图纸和工艺要求,进行组装和焊接。
2. 组装完成的产品进行外观检查和功能测试,确保产品质量符合要求。
3. 合格的产品送至下一道工序,不合格的产品进行返工修复或报废处理。
六、喷涂和表面处理1. 对需要进行喷涂和表面处理的产品,进行清洗和除油处理。
2. 进行底漆喷涂、中涂和面漆喷涂等工艺操作。
3. 喷涂完成后,产品进行烘干和固化处理。
七、质量检验1. 质检部门对成品进行全面检查,包括外观、尺寸、焊接质量等方面。
2. 对不合格的产品进行返工或报废处理。
3. 合格的产品进行质量记录和标识,准备出厂。
八、包装与出货1. 包装部门根据产品的性质和要求,选择合适的包装材料和方式。
起重机工艺流程图

起重机工艺流程图1、箱形主梁工艺流程图检划划半剪清割坡验出出自除渣口入拱外动切焊等打库度形气区物磨线线割达度埋反超确垂内工清焊到要弧面声保直部电除渣平求自清波隔度行焊内杂直动根检板用接脏物焊焊测手内焊装成清磨修修腔缝配箱埋HJ431 除光正正检质下形弧直焊焊拱旁验量盖主自流渣疤度弯板梁动反焊接操代专质表作码检量者填控写制2、轮组装配工艺流程图煤清轮确尺轴部油洗孔认寸承位或轴等各及等加洗承部种公工润涤,位规差作滑济轴格剂3、场按领煤清轴确尺轴加最注地技取油洗及认寸承油后油清术各或轴孔各及内脂减理文件洗承等件公、速件涤齿部规差齿箱济轮位格面内螺手起行噪钉工升走音松盘机机震紧动构构动度灵活性4、端梁工艺流程图接板划板确垂内工口点出上保直部焊处焊连孔弯水先接连于接位板平手接工艺度清磨内每垂装成埋或除光腔组直配箱弧 CO2焊焊焊 2. 度下形自气渣疤缝件平盖端动保质弯行板梁焊焊量板度清磨校垂装两两两除光正直车轮轮轮焊焊弯度轮轴端端渣疤板组平面面行垂共度直面度度操作者代号5、桥架工艺流程图整托水主向端平主上四跨四面道理架平梁外梁行梁拱轮度轮度轨场找度旁平垂放对度对着轨地准弯行直置应角力距放主截线点置梁面共磨毛号掉刺飞除标焊及溅表记疤残等面合安格装标标记记电动单梁起重机工艺流程图1、U型主梁工艺流程图检表涂剪冷验面无切压入除害弯库锈漆U 对装先后划外气形型接配焊外出形割成槽 U 点内侧 U 尺两上外型焊侧清型寸边拱形槽隔对根槽裕度钢板接焊量缝清超 U焊焰拱字热除等腔焊声型缝修度钢求内杂及缝波槽正火拱腔物工探对焰度焊字伤接装磨清填控斜掉除写制腹焊焊质表板疤渣量2、端梁工艺流程图检喷油剪冷验丸锈切压入除弯库U 对装先后清装装型接配焊外除封垫槽 U 点内侧内底板外型焊侧清腔板形槽隔对根杂钢板缝焊物校操正保作旁机者弯加代工码量轮轴平孔面3、车轮组装配工艺流程图确格轴油洗孔认尺承或轴等各寸内洗承部件及加涤轴位规公油济差脂4、主梁连接板装配工艺流程图打焊机调磨疤组整度梁端轮毛等装与梁着刺用端平力胎梁行点垂共直面整涂漆(学习的目的是增长知识,提高能力,相信一分耕耘一分收获,努力就一定可以获得应有的回报)。
Technical Textile Training (Sweater)--毛衣的工艺
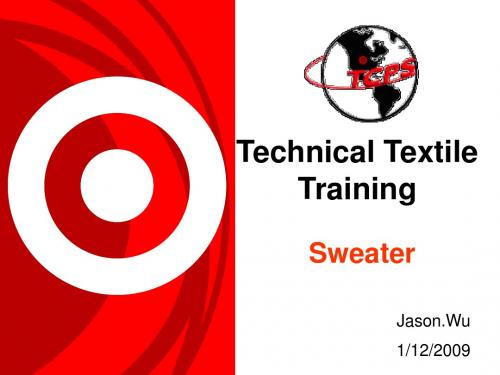
挑撞 撞的目的是必须根据编织的基本结构而去做缝合的工 作。 撞的时候即是用原身毛去联合位置,以便成为衫片编 织的部分。因此挑即是用手针联合生死口,而撞即是 用手针去编织及联合生口等。
21
撞
挑撞
挑的举例: 1.挑圆领口:只需要两边以线对位联起,以不露挑线及联口的骨位不易察觉为 主。 2.挑杏领咀:将杏领贴成V形联起,对支数,不露挑线,联口完整及咀长度合适 为标准。 3.挑开胸衫直贴脚:以缝毛将直脚贴线圈全部穿起成合适的阔度,以不会散脱 为标准。 4.挑袋口横贴:以缝线将线圈逐个挑于衫身上,高度以贴阔为标准。
23
毛衫疵点分类
原料疵点
织片疵点
毛衫疵点
套口疵点
整理疵点
24
织片疵点
1.Yarn/thread end 毛线头 2. Fly yarn 杂毛,杂丝
3. Uneven yarn 粗细纱
5.拉线
4. Loosing stitch漏针
6. 紧松档
7.扎钩疤;挂砣;挂针,一般12针以上易见。 8.单丝 10.针路 9. Needle line 反丝 11.片子花
12.横路
14.Wrong course 错转数 16.包头针
13.Color shading 色差
15.片子不配 17.未清机头纱
25
套口疵点
1.漏眼 2.锁错横行
3.吃边
5.缝线不规则 7.跳线 9.缝线口没锁住 11.锄眼针路不对
4.烂边
6.缝线太松 8.缝线错色 10.缝线太紧 12.布片上盘不匀
撞的举例: 1.胸衫直贴脚:以编织方法逐个线圈织起而成锁口的方法。 2.撞拨花领:以编织方法逐个线圈织起,将拨花领片联于前幅衫身上。
最新产品生产流程图资料讲解
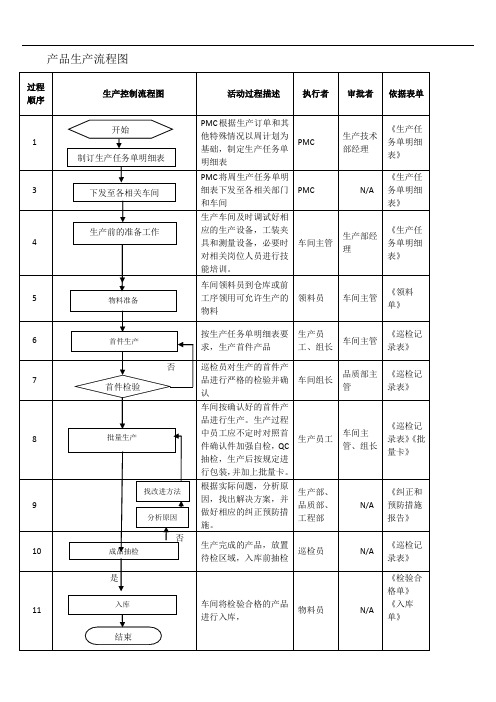
产品生产流程图Text: A white heron 白鹭1 The forest was full of shadows as a little girl hurried through it one summer evening in June. It was already eight o’clock and Sylvia wondered if her grandmother would be angry with her for being so late.2 Every evening Sylvia left her grandmother’s house at five thirty to bring their cow home. It was Sylvia’s job to bring the animal home to be milked. When the cow heard Sylvia’s voice calling her, she would hide among the bushes.1 六月的一个黄昏,森林里树影婆娑,一个小女孩正在其中匆匆穿行。
已经是晚上八点了,西尔维娅想,这么晚回家,外婆会不会生气呢?2 每天傍晚五点半,西尔维娅就离开外婆家去把母牛牵回家。
她的活就是把这头牲口赶回家挤奶。
母牛听到西尔维娅叫她的声音时,老是躲到灌木丛中去。
3 This evening it had taken Sylvia longer than usual to find her cow. The child hurried the cow through the dark forest, toward her grandmother’s home. As the cow stopped at a small stream to drink, Sylvia put her bare feet in the cold, fresh water of the stream.4 She had never before been alone in the forest as late as this. Sylvia felt as if she were a part of the gray shadows and the silver leaves that moved in the evening breeze.3 这天晚上,西尔维娅花了比平时更长的时间才找到母牛。
起重机生产流程图

1.起重机生产工艺流程图2.整机 装 配 流 程 图轨道轨距我公司是专业制造起重机的厂家,在产品制造加工过程中,严格按 IS09001 质 量标准进行管理,尤其对起重机的关键部件、关键工序均采用完善的工艺手段 来保证其质量。
一、板材及型材的预处理为保证金属结构的防腐和增强油漆的附着力,所有板材和型材在下料前均在我厂自备的预处理设备上进行抛丸预处理,除锈等级达到GB8923标准规定的Sa2.5级,除锈后立即双面喷涂底漆予以保护,然后才转入下料工序。
二、起重机金属结构(桥架的加工)1、主梁、端梁等主要受力结构件采用GB/T1591-94S标准中Q235-B碳素结构钢板制造,次要受力件和非受力构件如走台、罩子等零部件采用Q235-A钢材制造,桥架中所采用的材料均需具有炉号、批号、材料化学成份、机械性能的试验报告及出厂合格证书,材料到厂后由质检部门取样进行理化复检,合格的材料方可投入车间进行产品制造。
2、腹板及上盖板的下料采用微机控制的大型火焰数控切割机双枪一次切割,可根据不同跨度工况条件割出二次曲线,四次曲线及二、四线的迭加曲线,有效地保证了起重机的预制拱度,使预制拱度与起重机上拱曲线相吻合,此预拱度值根据主梁制造工艺过程中每一道工序进行严格控制。
3、主梁的焊接有焊接和拼装工艺,通过焊接顺序的合理安排减少起重机的焊接变形。
4、主梁腹板和上、下盖板的对接焊接缝均采用埋弧自动焊,主梁和端梁的纵向焊缝采用微机控制的二氧化碳气体自动保护焊,焊后进行100%探伤。
5、焊接完成后,进行时效处理清除焊接应力。
注:我厂起重机主梁焊接工艺获得河南省技术进步一等奖。
三、桥架组装焊接1、主梁、端梁组装焊接:将验收合格的两根主梁摆放在垫架上,以主梁的上盖板中心线为基准点,按技术要求调整各部分尺寸。
为使桥架安装车轮后能正常运行、组装时将四组弯板采用水平仪测量调在同一平面内。
并以水平面为组装调整门架各部的基准,达到要求后才能焊接。
钣金车间生产流程图
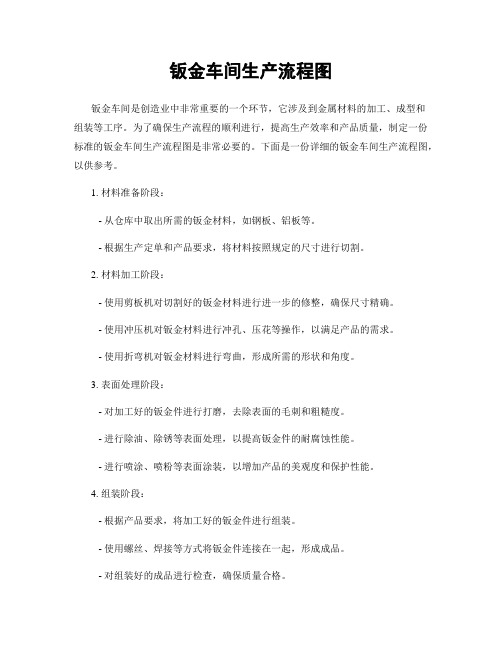
钣金车间生产流程图钣金车间是创造业中非常重要的一个环节,它涉及到金属材料的加工、成型和组装等工序。
为了确保生产流程的顺利进行,提高生产效率和产品质量,制定一份标准的钣金车间生产流程图是非常必要的。
下面是一份详细的钣金车间生产流程图,以供参考。
1. 材料准备阶段:- 从仓库中取出所需的钣金材料,如钢板、铝板等。
- 根据生产定单和产品要求,将材料按照规定的尺寸进行切割。
2. 材料加工阶段:- 使用剪板机对切割好的钣金材料进行进一步的修整,确保尺寸精确。
- 使用冲压机对钣金材料进行冲孔、压花等操作,以满足产品的需求。
- 使用折弯机对钣金材料进行弯曲,形成所需的形状和角度。
3. 表面处理阶段:- 对加工好的钣金件进行打磨,去除表面的毛刺和粗糙度。
- 进行除油、除锈等表面处理,以提高钣金件的耐腐蚀性能。
- 进行喷涂、喷粉等表面涂装,以增加产品的美观度和保护性能。
4. 组装阶段:- 根据产品要求,将加工好的钣金件进行组装。
- 使用螺丝、焊接等方式将钣金件连接在一起,形成成品。
- 对组装好的成品进行检查,确保质量合格。
5. 质检阶段:- 对成品进行全面的质量检测,包括尺寸、外观、功能等方面。
- 对不合格的产品进行修复或者重新制作,确保产品达到标准要求。
6. 包装和出库阶段:- 对合格的成品进行包装,以保护产品在运输和储存过程中的安全。
- 将包装好的成品进行入库,并进行相应的记录和标识。
- 根据定单要求,将成品出库,准备发货。
以上是一份标准的钣金车间生产流程图,其中涵盖了材料准备、材料加工、表面处理、组装、质检以及包装和出库等关键环节。
通过严格按照这个流程进行生产,可以确保产品的质量和交货期的准时性。
固然,具体的生产流程还需要根据实际情况进行调整和优化,以适应不同产品和生产规模的需求。
Technical Textile Training (Sweater)--毛衣的工艺
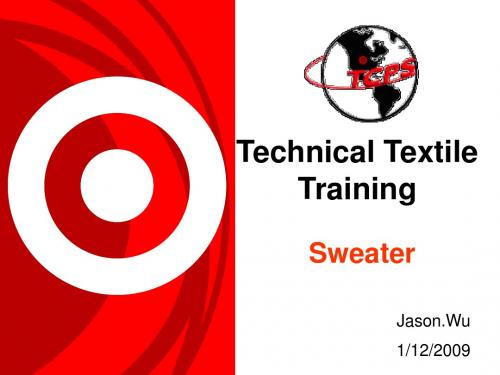
成衣检验
15
缝纫拼片
缝盘主要用于各类羊毛线,毛线,晴纶 膨体纱线及各混纺纱线编织的衣口,袖 口,领口及膊位等的精细埋缝成衣,通 常将衫片置上针盘中的沟形短针后就用 锁链线部将其缝合。 衣片采用“包缝缝合”和“套口缝合” 组装成衣,通常,服装的前后片、袖子 和腋下部位采用包缝缝合,而肩部和领 子是套口缝合。二者的区别在于,套口 缝合是线圈对线圈的连接起来,而包缝 缝合是将织物的边缘缝合起来。一般需 要3横列握持部分,称为缝耗。 一般套口机的针号大于其所套织片横机 机号2—4针/英寸
准备 工程
编结 工程
12
准备工序
1.送到羊毛衫厂的各种毛纱,大都是绞纱形式,不能 直接在针织机上进行编结加工; 2.同时在这些纱线上还存在着各种疵点和杂质将影响 编结的质量和产量。
原因
目的
1.将绞纱绕成筒装形式,以适应编织生产中纱线退绕的 需要; 2.清除毛纱表面的疵点和杂质,对毛纱进行腊处理使之 柔软光滑; 3.根据工艺要求对毛纱作加捻、并股处理以提高毛纱牢 度和增加毛织物厚度。 络纱时应尽量保持毛纱的弹性 和延伸性,要求张力均匀,退绕顺利。
4
Sweater Knits 毛衫
手工编织
毛衫织片机
电脑横机 手摇织机
5
Hand knit sweaters 手工编织
手工编织毛衫就如它的名称一样,就像是奶奶们一般所编织的毛衫。它是通过手工 来编织成整件毛衫。
手工编织中,编织通过“放针”工序开始编出底边和袖口。同样的工序制得前后片 和袖身。编织最后再采用“收针”工序完成边缘的编织。
挑撞 撞的目的是必须根据编织的基本结构而去做缝合的工 作。 撞的时候即是用原身毛去联合位置,以便成为衫片编 织的部分。因此挑即是用手针联合生死口,而撞即是 用手针去编织及联合生口等。
挑臂工艺流程

挑臂制造工艺流程
挑臂结构图
① 单元件制造 1.顶板单元
用数控切割,纵肋分段下料。
按设计图纸组拼顶板单元。
数控二次下料,加工边缘及坡口,长度方向预留焊接收缩量。
平台上以板端为基准,精确划线分段组装纵肋,保证纵肋的相对位置及直线度。
CO 2气体保护焊,从中间向两侧对称施焊。
2.腹板单元
② 挑臂组拼工艺流程
板单元经检验合格后转组拼工序。
综合分析总拼顺序等因素,采用倒拼方案。
数控精密切割。
1.在组拼平台上铺设顶板单元,吊垂线对位检测坐标控制点及板单元各点标高。
2.安装腹板单元,检测顶板与腹板垂直度。
PMC生产进度跟催流程图

生产进度跟催流程图(使用生产增强型U3ERP 责任
人员
作业流程操作叙述
PMC 生管
车间调度
制造部
PMC 生管
制造部
仓库生管每天按照生产计划,将已
经齐套的产品进行排产,并下
发最近一天或两天的加工任
务
车间调度根据加工任务,按设
备生成工单,并指定执行人
生产部根据生产指令单,工单
领料上线生产,并将生产进度
状况反映给生管,以便在生产
出现异常时及时作相应安排
生管要及时了解各部门生产
状况,发现生产异常,要及时
召开生产会议,商讨解决方案,
并给出事务联络单通知各部
门
生产部门应及时录入工序完
工数据,此数据亦是员工工时
数据
生产完成,产品入库后通知
业务出货
相关表单
生产排程表
生产制令单
工单
事务联络单
生产日报表
生产入库单。
OP
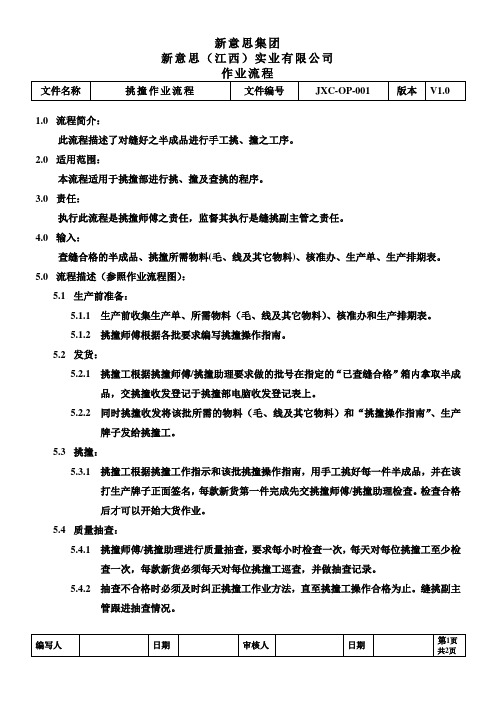
1.0流程简介:此流程描述了对缝好之半成品进行手工挑、撞之工序。
2.0适用范围:本流程适用于挑撞部进行挑、撞及查挑的程序。
3.0责任:执行此流程是挑撞师傅之责任,监督其执行是缝挑副主管之责任。
4.0输入:查缝合格的半成品、挑撞所需物料(毛、线及其它物料)、核准办、生产单、生产排期表。
5.0流程描述(参照作业流程图):5.1生产前准备:5.1.1生产前收集生产单、所需物料(毛、线及其它物料)、核准办和生产排期表。
5.1.2挑撞师傅根据各批要求编写挑撞操作指南。
5.2发货:5.2.1挑撞工根据挑撞师傅/挑撞助理要求做的批号在指定的“已查缝合格”箱内拿取半成品,交挑撞收发登记于挑撞部电脑收发登记表上。
5.2.2同时挑撞收发将该批所需的物料(毛、线及其它物料)和“挑撞操作指南”、生产牌子发给挑撞工。
5.3挑撞:5.3.1挑撞工根据挑撞工作指示和该批挑撞操作指南,用手工挑好每一件半成品,并在该打生产牌子正面签名,每款新货第一件完成先交挑撞师傅/挑撞助理检查。
检查合格后才可以开始大货作业。
5.4质量抽查:5.4.1挑撞师傅/挑撞助理进行质量抽查,要求每小时检查一次,每天对每位挑撞工至少检查一次,每款新货必须每天对每位挑撞工巡查,并做抽查记录。
5.4.2抽查不合格时必须及时纠正挑撞工作业方法,直至挑撞工操作合格为止。
缝挑副主管跟进抽查情况。
5.5交货:5.5.1每打完成之半成品交挑撞收发作电脑登记,并放于指定的“待查挑”箱内。
5.5.2每批完成之剩余物料(毛、线及其它物料)、该批挑撞操作指南交挑撞收发处理。
5.6100%检查:5.6.1查挑工椐据查挑工作指示及该批挑撞操作指南把挑撞工所完成的半成品进行100%检查,合格之半成品放在“已查挑合格”箱内,不合格半成品退回挑撞工返工,并要求挑撞工2小时内交回半成品进行再次检查,直到合格为止。
5.6.2查挑工记录疵点于“挑撞疵点记录表”中。
5.7做挑撞生产日报表及每日收货明细表:5.7.1由挑撞收发做每天挑撞生产日报表及打印出每日收货明细表,由工人签名确认后交缝挑办公室。