氨酸法工艺技术简述
氨酸法造粒工艺流程
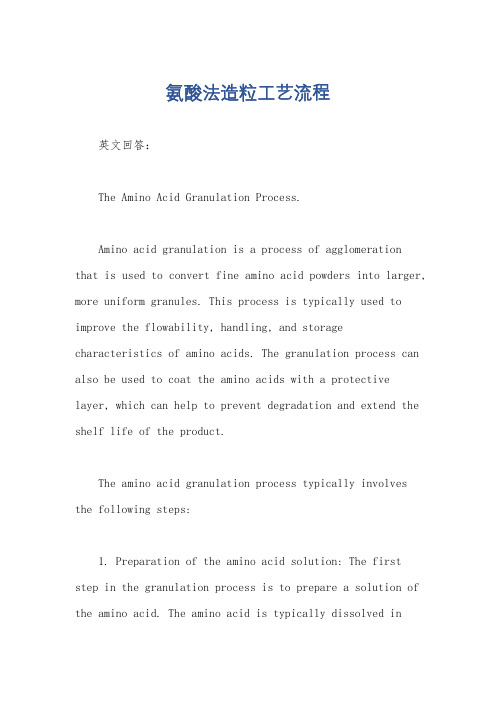
氨酸法造粒工艺流程英文回答:The Amino Acid Granulation Process.Amino acid granulation is a process of agglomerationthat is used to convert fine amino acid powders into larger, more uniform granules. This process is typically used to improve the flowability, handling, and storage characteristics of amino acids. The granulation process can also be used to coat the amino acids with a protective layer, which can help to prevent degradation and extend the shelf life of the product.The amino acid granulation process typically involves the following steps:1. Preparation of the amino acid solution: The first step in the granulation process is to prepare a solution of the amino acid. The amino acid is typically dissolved inwater, but other solvents can also be used. The concentration of the solution will vary depending on the desired properties of the final granules.2. Addition of a binder: A binder is then added to the amino acid solution. The binder helps to hold the granules together and prevent them from breaking apart. The type of binder used will depend on the desired properties of the final granules.3. Formation of droplets: The amino acid solution is then atomized to form small droplets. The size of the droplets will determine the size of the final granules.4. Drying: The droplets are then dried to remove the solvent. The drying process can be carried out in a variety of ways, including fluidized bed drying, tray drying, and spray drying.5. Granulation: The dried droplets are then granulated to form larger, more uniform granules. The granulation process can be carried out in a variety of ways, includingtumbling, agglomeration, and compaction.6. Coating: The granules can be coated with aprotective layer to help prevent degradation and extend the shelf life of the product. The coating can be applied using a variety of methods, including spraying, dipping, and tumbling.The amino acid granulation process is a versatile process that can be used to produce a variety of different types of granules. The process can be tailored to meet the specific requirements of the desired product.中文回答:氨基酸造粒工艺流程。
氨酸法用管式反应器工艺生产复合肥技术

氨酸法用管式反应器工艺生产复合肥技术氨酸法用管式反应器工艺生产NPK技术摘要:硫酸、氨管式反应器技术是结合TVA氨化造粒技术和十字管反应器技术而开发的,将TVA埋床式硫酸、氨双喷管开发设计为悬挂式单管道反应器。
硫酸与氨在此进行反应,释放大量的反应热,将造粒机内部分固体物料融化及溶解,改变了原料的物性,保证了造粒在较低的水份条件下,各种原料能够成粒,形成外观光泽、强度高的NPK颗粒。
该技术具有:技术含量高、投资小、配方灵活、生产成本低、产品质量好等显著优点。
同时,简要介绍了硫酸、合成氨用管式反应器的应用情况。
当前,管式反应器技术在复合肥生产中的主要的应用有如下几种:磷铵联产复合肥装置(十字管反应器)、低温转化硫基复合肥生产装置(混酸反应器)以及硫酸、氨管式反应器。
在管式反应器工艺中,氨和磷酸;混酸;以及硫酸,在管式反应器内进行反应,生成高温低湿料浆,该热熔体料浆在造粒机内均匀的喷涂于造粒物料的表面(喷雾造粒干燥技术除外),同时,大量的反应热使造粒床层温度升高,使部分原料融化及溶解,来满足造粒所需的液相,而不是传统团粒使用蒸汽或水帮助造粒,并提供NPK中的有效养分。
硫酸、氨管式反应器技术是通过十几年来对田纳西流域管理局(TVA)开发的氨化转鼓造粒装置的生产实践,并结合十字管反应器技术而开发的,取得了一系列生产经验和研究成果。
管式反应器工艺较预中和工艺及TVA氨化转鼓(床层氨化)工艺来说,更能有效利用氨化的反应热和降低氨耗,同时可有效控制氨化反应,避免酸过度所带来的不良副反应的进行。
保证了造粒过程的平稳性。
1、硫酸、氨管式反应器在磷复肥行业中,通常所说的管式反应器是指十字管反应器。
磷酸和硫酸分别进入十字管反应器相对两支管中,在这里二者充分混合后,再与中心管来的气氨(或液氨有时加水)、进行反应。
进入的氨量应使磷酸硫酸全部中和,反应生产的料浆通过一肘型管喷到造粒机中。
它主要用于磷酸一铵、磷酸二铵的生产,在其返料系统中添加钾盐,则生产NPK产品。
氨酸法复合肥工艺流程531
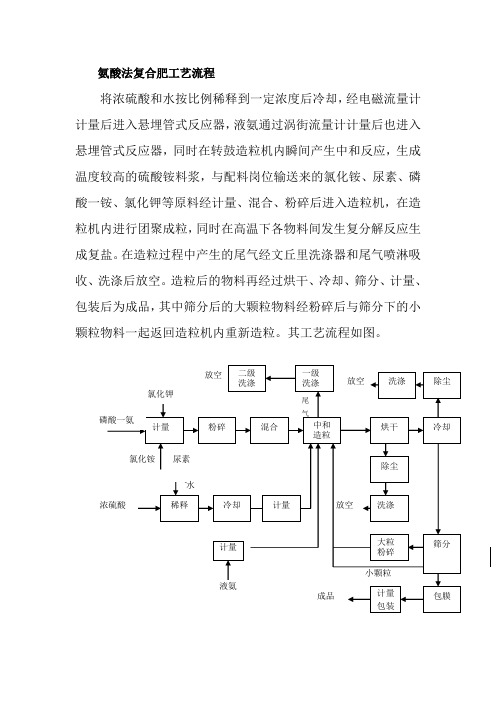
氨酸法复合肥工艺流程
将浓硫酸和水按比例稀释到一定浓度后冷却,经电磁流量计计量后进入悬埋管式反应器,液氨通过涡街流量计计量后也进入悬埋管式反应器,同时在转鼓造粒机内瞬间产生中和反应,生成温度较高的硫酸铵料浆,与配料岗位输送来的氯化铵、尿素、磷酸一铵、氯化钾等原料经计量、混合、粉碎后进入造粒机,在造粒机内进行团聚成粒,同时在高温下各物料间发生复分解反应生成复盐。
在造粒过程中产生的尾气经文丘里洗涤器和尾气喷淋吸收、洗涤后放空。
造粒后的物料再经过烘干、冷却、筛分、计量、包装后为成品,其中筛分后的大颗粒物料经粉碎后与筛分下的小颗粒物料一起返回造粒机内重新造粒。
其工艺流程如图。
对以上新增设备名称、型号、材质数量及要求均见新增设备一览表。
10万吨/年氨酸造粒复合肥技改项目新增设备一览表。
蒸汽造粒改氨酸法技术简析

蒸汽造粒改氨酸法技术简析蒸汽造粒复混肥生产装置,经自主创新改造后,有效降低了生产成本,并提高了产品质量。
在此基础上,采用硫酸、液氨中和反应直接生产氯基复合肥工艺技术,对原蒸气转鼓造粒复混肥生产装置进行技术改造,开发出氨酸法氯基复合肥新产品,其产品质量达到国家标准,取得了较好经济效果。
1 复合肥生产原理利用氨酸造粒法生产复合肥,其基本原理分为三个主要步骤(原理)。
1)液氨与硫酸的中和反应。
将浓硫酸稀释后,再与定量的液氨在管式反应器中进行中和反应,最后生成硫酸铵料浆,并放出大量的热量。
2)复分解反应与复盐的生成。
利用氯化钾、磷酸一铵、硫酸铵间的复分解反应,实现复盐的生成。
从配料岗位输送到造粒机内的氯化钾和磷酸一铵,在低温下可进行复分解反应,并生成磷酸二氢钾和氯化铵(该反应在温度低时反应缓慢,生成的磷酸二氢钾量相对较低)。
当硫酸与液氨进行中和反应放出大量的热量时,物料温度升高,从而加速了其反应的速度,同时生成的硫酸铵又与物料中的氯化钾进一步发生复分解反应,生成硫酸钾和氯化铵。
3)复盐固溶体的形成。
上述物料中氯化钾和磷酸一铵发生复分解反应,生成的氯化氨与原料中的氯化钾将形成氯化铵钾复盐固溶体[(NH4,K)C1]。
而硫酸与液氨进行中和反应,生成的硫酸铵又与氯化钾复分解反应产生的硫酸钾形成硫酸铵钾固溶体[(NH4,K)2SO4]。
氯化钾和磷酸一铵反应生成的磷酸二氢钾与原料中的磷酸一铵又形成磷酸铵钾固溶体[(NH4,K)H2PO4]。
以上三方面生成的固溶体,就是该肥料所需要的主要成分,它们在造粒的过程中也形成了成球状态。
2 复合肥生产工艺流程在复合肥的生产过程中,先将浓硫酸和水按比例稀释到一定质量分数后冷却,再经转子流量计计量进入管式反应器。
液氨经汽化后,通过涡街式流量计计量,同时也进入管式反应器,瞬间产生中和反应,生成温度较高的硫酸铵料浆,并产生压力将硫酸铵料浆喷入转鼓造粒机内。
经配料岗位的计量、混合、粉碎后的氯化钾和磷酸一铵被输送到转鼓造粒机内,粉状物料与硫酸铵料浆混合,形成一定液相的固溶体,并在转鼓造粒机内滚动造粒。
氨酸法复合肥项目技术简介
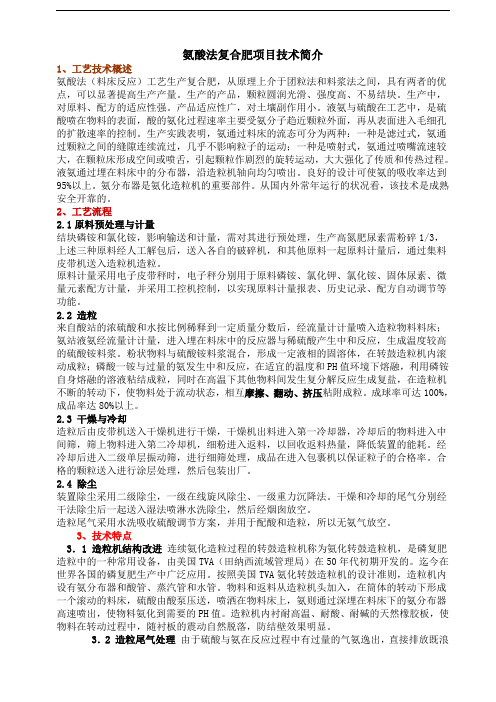
氨酸法复合肥项目技术简介1、工艺技术概述氨酸法(料床反应)工艺生产复合肥,从原理上介于团粒法和料浆法之间,具有两者的优点,可以显著提高生产产量。
生产的产品,颗粒圆润光滑、强度高、不易结块。
生产中,对原料、配方的适应性强。
产品适应性广,对土壤副作用小。
液氨与硫酸在工艺中,是硫酸喷在物料的表面,酸的氨化过程速率主要受氨分子趋近颗粒外面,再从表面进入毛细孔的扩散速率的控制。
生产实践表明,氨通过料床的流态可分为两种:一种是滤过式,氨通过颗粒之间的缝隙连续流过,几乎不影响粒子的运动;一种是喷射式,氨通过喷嘴流速较大,在颗粒床形成空间或喷舌,引起颗粒作剧烈的旋转运动,大大强化了传质和传热过程。
液氨通过埋在料床中的分布器,沿造粒机轴向均匀喷出。
良好的设计可使氨的吸收率达到95%以上。
氨分布器是氨化造粒机的重要部件。
从国内外常年运行的状况看,该技术是成熟安全开靠的。
2、工艺流程2.1原料预处理与计量结块磷铵和氯化铵,影响输送和计量,需对其进行预处理,生产高氮肥尿素需粉碎1/3,上述三种原料经人工解包后,送入各自的破碎机,和其他原料一起原料计量后,通过集料皮带机送入造粒机造粒。
原料计量采用电子皮带秤时,电子秤分别用于原料磷铵、氯化钾、氯化铵、固体尿素、微量元素配方计量,并采用工控机控制,以实现原料计量报表、历史记录、配方自动调节等功能。
2.2 造粒来自酸站的浓硫酸和水按比例稀释到一定质量分数后,经流量计计量喷入造粒物料料床;氨站液氨经流量计计量,进入埋在料床中的反应器与稀硫酸产生中和反应,生成温度较高的硫酸铵料浆。
粉状物料与硫酸铵料浆混合,形成一定液相的固溶体,在转鼓造粒机内滚动成粒;磷酸一铵与过量的氨发生中和反应,在适宜的温度和PH值环境下熔融,利用磷铵自身熔融的溶液粘结成粒,同时在高温下其他物料间发生复分解反应生成复盐,在造粒机不断的转动下,使物料处于流动状态,相互摩擦、翻动、挤压粘附成粒。
成球率可达100%,成品率达80%以上。
氨酸法工艺在复合肥料生产中的应用分析
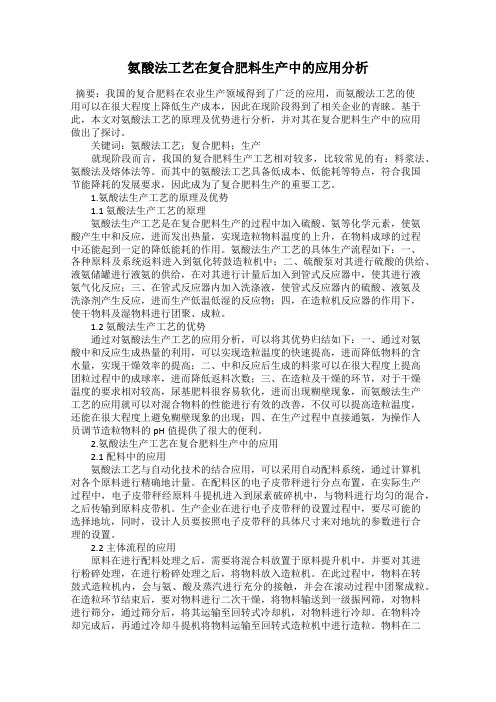
氨酸法工艺在复合肥料生产中的应用分析摘要:我国的复合肥料在农业生产领域得到了广泛的应用,而氨酸法工艺的使用可以在很大程度上降低生产成本,因此在现阶段得到了相关企业的青睐。
基于此,本文对氨酸法工艺的原理及优势进行分析,并对其在复合肥料生产中的应用做出了探讨。
关键词:氨酸法工艺;复合肥料;生产就现阶段而言,我国的复合肥料生产工艺相对较多,比较常见的有:料浆法、氨酸法及熔体法等。
而其中的氨酸法工艺具备低成本、低能耗等特点,符合我国节能降耗的发展要求,因此成为了复合肥料生产的重要工艺。
1.氨酸法生产工艺的原理及优势1.1氨酸法生产工艺的原理氨酸法生产工艺是在复合肥料生产的过程中加入硫酸、氨等化学元素,使氨酸产生中和反应,进而发出热量,实现造粒物料温度的上升,在物料成球的过程中还能起到一定的降低能耗的作用。
氨酸法生产工艺的具体生产流程如下:一、各种原料及系统返料进入到氨化转鼓造粒机中;二、硫酸泵对其进行硫酸的供给、液氨储罐进行液氨的供给,在对其进行计量后加入到管式反应器中,使其进行液氨气化反应;三、在管式反应器内加入洗涤液,使管式反应器内的硫酸、液氨及洗涤剂产生反应,进而生产低温低湿的反应物;四,在造粒机反应器的作用下,使干物料及湿物料进行团聚、成粒。
1.2氨酸法生产工艺的优势通过对氨酸法生产工艺的应用分析,可以将其优势归结如下:一、通过对氨酸中和反应生成热量的利用,可以实现造粒温度的快速提高,进而降低物料的含水量,实现干燥效率的提高;二、中和反应后生成的料浆可以在很大程度上提高团粒过程中的成球率,进而降低返料次数;三、在造粒及干燥的环节,对于干燥温度的要求相对较高,尿基肥料很容易软化,进而出现糊壁现象,而氨酸法生产工艺的应用就可以对混合物料的性能进行有效的改善,不仅可以提高造粒温度,还能在很大程度上避免糊壁现象的出现;四、在生产过程中直接通氨,为操作人员调节造粒物料的pH值提供了很大的便利。
2.氨酸法生产工艺在复合肥料生产中的应用2.1配料中的应用氨酸法工艺与自动化技术的结合应用,可以采用自动配料系统,通过计算机对各个原料进行精确地计量。
氨酸法——精选推荐

(一)酸氨管式反应器造粒技术的工艺过程工艺流程简述来自配料工序的各固体原料(氯化钾、磷酸一磷、固体尿素、氯化铵、普钙、填充剂等)和系统的返料进入转鼓造粒机,由硫酸贮罐来的浓硫酸和尾气洗涤系统的洗涤液,经计量后加入到特制的管式反应器的混和段进行混和稀释;来自氨站的液氨经计量后分为两路,一路通过液氨蒸发器和混和器A与少量蒸汽混和气化,经管式反应器混和段进入反应段,通过特制的分布器快速与混和后的稀硫酸反应,生成的高温硫酸铵溶液经雾化喷头均匀喷涂到造粒机料床上。
另一路液氨通过液氨蒸发器和混和器B与蒸汽混和气化后,由混和分布器进入料层与料层中的磷酸一铵、普钙等继续在造粒机内进入化学反应,同时释放出化学反应热,干湿物料在造粒机的转动作用下团聚成粒,如有尿液等液体原料喷入,则氨、酸及洗涤水量适当降低,以保证造粒的液相与热量平衡。
管式反应器排出的水蒸汽以及料层中排出的水蒸汽随造粒尾气排出,造料尾气经复喷管和洗涤塔进行洗涤吸收,经洗涤后的净化尾气经尾气风机烟囱排空,洗涤液用泵送至洗涤塔和管式反应器,洗涤水通过管式反应器后形成过热蒸汽及高温料浆予以回收。
出造粒机的物料经干燥、筛分、冷却、筛分、包膜处理后进入成品库进行包装,大粒返料经破碎后与细粉返料一起返回造粒系统,干燥、冷却尾气以及吸尘尾气分别经旋风除尘器、重力沉降和水浴洗涤三级处理后达标排放。
(二)氨酸管式反应器喷浆造粒新技术的主要特征1、造粒工况明显改善和稳定造粒部分利用气氨与硫酸、磷酸一铵的化学反应热来提高造粒物料温度和改善物料特性,提温幅度可达15-30℃,而并非主要靠蒸汽和尿液来提高造粒温度,造粒温度可高达75-85℃,物料水份小于2.5%,成球率高达60%以上。
2、实现一段干燥工艺、简化工艺过程由于造粒物料温度较高,水份较低,一段干燥便于使产品水份降至1.5%以下,实现了一段干燥工艺生产高氮尿基复合肥工艺过程,简化了工艺过程。
3、实现热筛分、热破碎工艺、提高能源利用率由于干燥后产品水份较低(小于1.5%)可满足热筛分和热大粒破碎工艺,同时也提高了热返料的热量利用效率,以及降低了冷却负荷,缓解了产品的热结块倾向。
氨酸法复合肥生产工艺

氨酸法复合肥生产工艺氨酸法复合肥是将氨基酸、氮磷钾等营养元素有机结合,制成颗粒状或粉末状的肥料。
下面介绍氨酸法复合肥的生产工艺。
首先,氨酸法复合肥的生产工艺主要分为原料处理、发酵、压球造粒、干燥和包装等几个步骤。
原料处理是指将各种原料进行加工,以提高其可发酵性。
一般来说,氨酸法复合肥的原料包括有机氮源、无机氮源、磷酸盐和钾肥等。
这些原料需要经过破碎、筛分和配比等工艺处理,以保证各种原料的比例合理、均匀。
发酵是指将处理好的原料进行发酵,使之转化为有机氮源。
一般来说,发酵工艺采用固态发酵或液态发酵。
固态发酵一般是将原料放入发酵罐中,通过控制温度、湿度和通风量等参数,使之发生微生物的发酵作用,转化为有机氮源。
液态发酵一般是将原料放入发酵罐中,加入适量的水和发酵菌种,通过控制温度、搅拌和通气等参数,使之发生液态发酵作用,转化为有机氮源。
压球造粒是指将发酵好的原料进行造粒,制成颗粒状的肥料。
一般来说,压球造粒工艺采用双辊压球机,通过辊式压制的方式,将发酵好的原料进行挤压和成形,制成颗粒状的肥料。
干燥是指将压球造粒好的肥料进行干燥,使其含水率达到标准要求。
一般来说,干燥工艺采用旋转干燥机,通过加热和风力作用,将肥料的含水率降低到标准范围内。
包装是指将干燥好的肥料进行包装和贮存,以便运输和销售。
一般来说,包装工艺采用自动包装机,将肥料装入袋子中,并进行称重、封口和码垛等操作,最终成品肥料可以直接投放市场。
总之,氨酸法复合肥的生产工艺包括原料处理、发酵、压球造粒、干燥和包装等几个步骤。
通过科学的生产工艺和技术手段,可以生产出高质量的氨酸法复合肥,满足农业生产的需求。
氨酸法与水汽法工比较
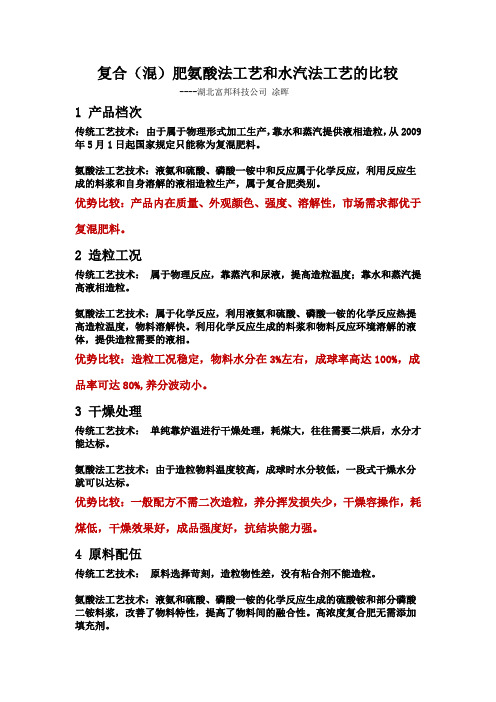
复合(混)肥氨酸法工艺和水汽法工艺的比较----湖北富邦科技公司凃晖1 产品档次传统工艺技术:由于属于物理形式加工生产,靠水和蒸汽提供液相造粒,从2009年5月1日起国家规定只能称为复混肥料。
氨酸法工艺技术:液氨和硫酸、磷酸一铵中和反应属于化学反应,利用反应生成的料浆和自身溶解的液相造粒生产,属于复合肥类别。
优势比较:产品内在质量、外观颜色、强度、溶解性,市场需求都优于复混肥料。
2 造粒工况传统工艺技术:属于物理反应,靠蒸汽和尿液,提高造粒温度;靠水和蒸汽提高液相造粒。
氨酸法工艺技术:属于化学反应,利用液氨和硫酸、磷酸一铵的化学反应热提高造粒温度,物料溶解快。
利用化学反应生成的料浆和物料反应环境溶解的液体,提供造粒需要的液相。
优势比较:造粒工况稳定,物料水分在3%左右,成球率高达100%,成品率可达80%,养分波动小。
3 干燥处理传统工艺技术:单纯靠炉温进行干燥处理,耗煤大,往往需要二烘后,水分才能达标。
氨酸法工艺技术:由于造粒物料温度较高,成球时水分较低,一段式干燥水分就可以达标。
优势比较:一般配方不需二次造粒,养分挥发损失少,干燥容操作,耗煤低,干燥效果好,成品强度好,抗结块能力强。
4 原料配伍传统工艺技术:原料选择苛刻,造粒物性差,没有粘合剂不能造粒。
氨酸法工艺技术:液氨和硫酸、磷酸一铵的化学反应生成的硫酸铵和部分磷酸二铵料浆,改善了物料特性,提高了物料间的融合性。
高浓度复合肥无需添加填充剂。
优势比较:原料选择范围广成本低,产品洁白、光滑圆润,无不溶性残渣,避免了填料颜色不稳定影响产品外观,溶解性能好,作为易吸收。
5 生产条件传统工艺技术:造粒受天气湿度和原料特性影响大,操作弹性小,设备不能长周期稳定运行,限制了多品种开发生产。
氨酸法工艺技术:由于有化学反应,改善物料配伍特性,保证不同原料、配方、季节的造粒效果,能有效提高装置操作弹性。
优势比较:不受原料和季节限制,可生产多品种、多系列产品,实现装置长周期稳定运行。
氨酸法造粒工艺及岗位操作规程

氨酸法造粒工艺及岗位操作规程一、前言氨酸法造粒工艺是一种常见的药品制剂工艺。
该工艺主要采用氨酸为溶剂,将固体药品制剂喷雾成小颗粒,以适应不同的用药需求。
本文将详细介绍氨酸法造粒工艺及岗位操作规程。
二、氨酸法造粒工艺概述氨酸法造粒工艺是一种湿法造粒工艺,其主要原理是通过喷雾器将氨酸和制剂混合,形成小颗粒,然后通过干燥装置将其干燥固化。
氨酸法造粒工艺常用于制备药品的微、小颗粒。
这些颗粒可以轻松地组合成胶囊、丸剂或直接制成口服溶液。
总体而言,氨酸法造粒工艺包括以下几个步骤:1. 药品混合。
将需要制备成颗粒的药品加入氨酸中混合均匀。
2. 喷雾成颗粒。
将药品混合液通过喷雾器喷出,形成小颗粒。
3. 干燥固化。
将喷出的小颗粒通过干燥装置干燥,使其成为坚硬的颗粒。
4. 筛分。
将干燥后的颗粒进行筛分,以去除不必要的细颗粒和杂质。
5. 包装。
最后将筛分后的颗粒包装成所需的制剂。
三、岗位操作规程作为一个行业工作者,在执行任何任务之前,必须遵守制定的操作规程。
下面是氨酸法造粒工艺的操作规程。
1. 工具和设备准备在进行氨酸法造粒工艺之前,必须检查和准备所需的工具和设备。
2. 工作区准备操作人员应确保工作区域干净整洁,并有足够的净化和通风系统,以确保在操作中尽量减少空气中的污染物。
3. 安全保障在进行任何实验室操作之前,必须遵循安全标准,包括穿戴个人防护装备如口罩、手套等,并在使用化学品时要注意保护眼睛和皮肤。
在必要的情况下,应对药品进行排气、灭菌等处理。
4. 药品加入将所需的药品主要成分逐一加入氨酸中,并使用搅拌器确定其充分混合。
5. 摇匀将所需的辅料逐一加入氨酸混合物中,利用搅拌器按预定比例摇匀。
在摇匀时,搅拌头必须保持在混合液中,以确保混合均匀。
6. 造粒调节喷雾器的操作参数,根据药品需求逐步调整氨酸流量和喷雾器压力,逐渐喷雾出小颗粒。
在造粒时,操作者必须注意氨酸的量,确保其满足制作颗粒的要求。
7. 干燥和筛分将喷出的小颗粒通过干燥装置进行干燥固化。
氨酸法氨站设计技术方案
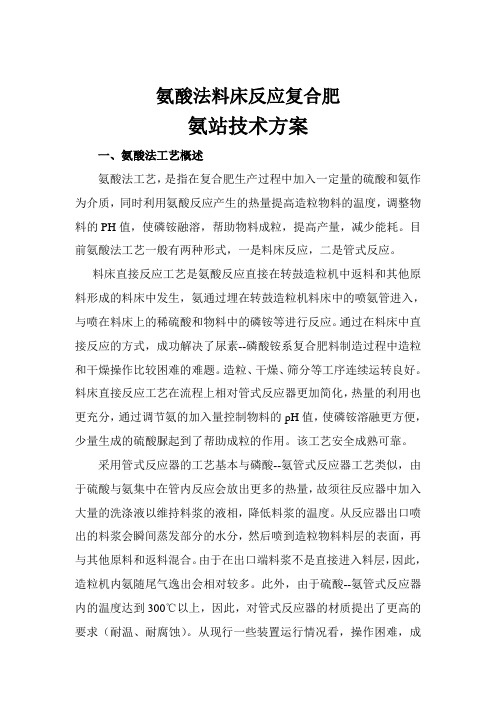
氨酸法料床反应复合肥氨站技术方案一、氨酸法工艺概述氨酸法工艺,是指在复合肥生产过程中加入一定量的硫酸和氨作为介质,同时利用氨酸反应产生的热量提高造粒物料的温度,调整物料的PH值,使磷铵融溶,帮助物料成粒,提高产量,减少能耗。
目前氨酸法工艺一般有两种形式,一是料床反应,二是管式反应。
料床直接反应工艺是氨酸反应直接在转鼓造粒机中返料和其他原料形成的料床中发生,氨通过埋在转鼓造粒机料床中的喷氨管进入,与喷在料床上的稀硫酸和物料中的磷铵等进行反应。
通过在料床中直接反应的方式,成功解决了尿素--磷酸铵系复合肥料制造过程中造粒和干燥操作比较困难的难题。
造粒、干燥、筛分等工序连续运转良好。
料床直接反应工艺在流程上相对管式反应器更加简化,热量的利用也更充分,通过调节氨的加入量控制物料的pH值,使磷铵溶融更方便,少量生成的硫酸脲起到了帮助成粒的作用。
该工艺安全成熟可靠。
采用管式反应器的工艺基本与磷酸--氨管式反应器工艺类似,由于硫酸与氨集中在管内反应会放出更多的热量,故须往反应器中加入大量的洗涤液以维持料浆的液相,降低料浆的温度。
从反应器出口喷出的料浆会瞬间蒸发部分的水分,然后喷到造粒物料料层的表面,再与其他原料和返料混合。
由于在出口端料浆不是直接进入料层,因此,造粒机内氨随尾气逸出会相对较多。
此外,由于硫酸--氨管式反应器内的温度达到300℃以上,因此,对管式反应器的材质提出了更高的要求(耐温、耐腐蚀)。
从现行一些装置运行情况看,操作困难,成球率低。
故本项目采用料床直接反应工艺。
二、氨站技术指标氨酸法工艺的基本介质是硫酸和液氨。
目前氨的使用有两种,一是直接使用液氨,二是将液氨蒸发成气氨使用(国家生产许可证现场审核要求,实际生产中使用液氨多)。
本项目拟采用直接使用液氨,省去液氨蒸发设备投资、蒸发液氨耗用大量蒸汽能源,同时避免了液氨蒸发的高危操作。
根据项目装置设计要求,氨站采用设计压力2.2MPa,工作压力1.8MPa,工作温度45℃,设计温度53℃,设计储存量25400kg,装量系数0.85,容器类别三的50立方米的氨液储槽2个。
复合肥氨酸法造粒工艺
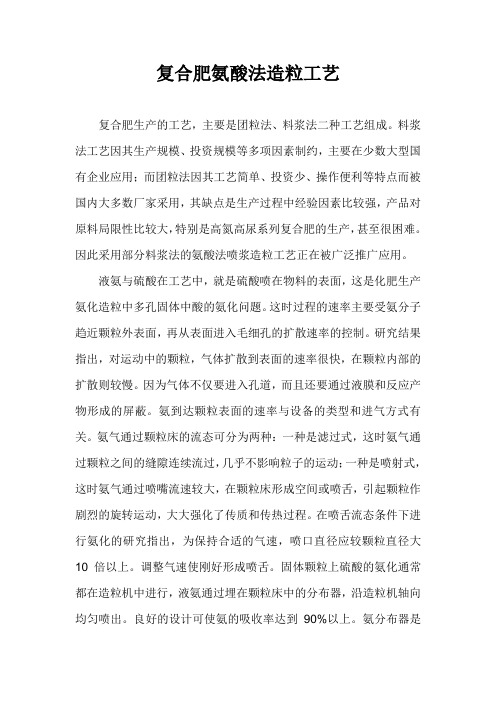
复合肥氨酸法造粒工艺复合肥生产的工艺,主要是团粒法、料浆法二种工艺组成。
料浆法工艺因其生产规模、投资规模等多项因素制约,主要在少数大型国有企业应用;而团粒法因其工艺简单、投资少、操作便利等特点而被国内大多数厂家采用,其缺点是生产过程中经验因素比较强,产品对原料局限性比较大,特别是高氮高尿系列复合肥的生产,甚至很困难。
因此采用部分料浆法的氨酸法喷浆造粒工艺正在被广泛推广应用。
液氨与硫酸在工艺中,就是硫酸喷在物料的表面,这是化肥生产氨化造粒中多孔固体中酸的氨化问题。
这时过程的速率主要受氨分子趋近颗粒外表面,再从表面进入毛细孔的扩散速率的控制。
研究结果指出,对运动中的颗粒,气体扩散到表面的速率很快,在颗粒内部的扩散则较慢。
因为气体不仅要进入孔道,而且还要通过液膜和反应产物形成的屏蔽。
氨到达颗粒表面的速率与设备的类型和进气方式有关。
氨气通过颗粒床的流态可分为两种:一种是滤过式,这时氨气通过颗粒之间的缝隙连续流过,几乎不影响粒子的运动;一种是喷射式,这时氨气通过喷嘴流速较大,在颗粒床形成空间或喷舌,引起颗粒作剧烈的旋转运动,大大强化了传质和传热过程。
在喷舌流态条件下进行氨化的研究指出,为保持合适的气速,喷口直径应较颗粒直径大10倍以上。
调整气速使刚好形成喷舌。
固体颗粒上硫酸的氨化通常都在造粒机中进行,液氨通过埋在颗粒床中的分布器,沿造粒机轴向均匀喷出。
良好的设计可使氨的吸收率达到90%以上。
氨分布器是氨化造粒机的重要部件。
用在需连续氨化造粒过程的转鼓造粒机称为氨化转鼓造粒机,是磷复肥造粒中的一种常用设备,是美国TVA(田纳西流域管理局)在50年代初期开发的。
迄今在世界各国的磷复肥生产中广泛应用。
按照美国TVA氨化转鼓造粒机的设计准则,在造粒机靠筒体轴线的上方设有一管梁,以便安装氨分布器和酸管、蒸汽管,返料从造粒机头加入,在筒体的转动下形成一滚动的物料床,硫酸由酸泵压送,从硫酸喷洒管的喷嘴喷洒在物料床上进行造粒。
氨酸法项目说明
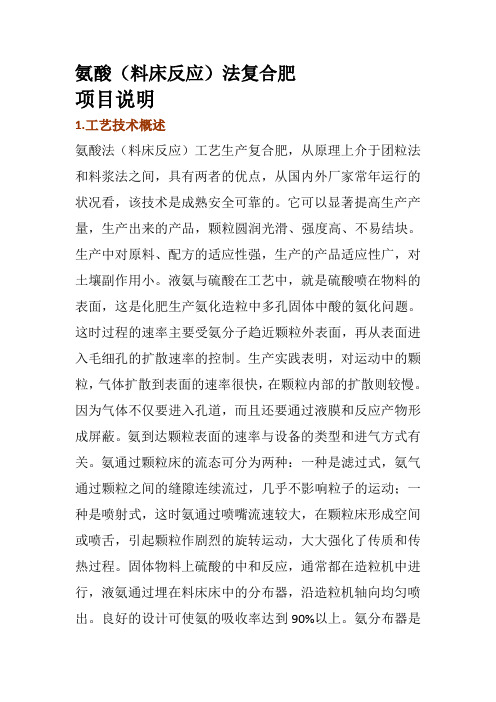
氨酸(料床反应)法复合肥项目说明1.工艺技术概述氨酸法(料床反应)工艺生产复合肥,从原理上介于团粒法和料浆法之间,具有两者的优点,从国内外厂家常年运行的状况看,该技术是成熟安全可靠的。
它可以显著提高生产产量,生产出来的产品,颗粒圆润光滑、强度高、不易结块。
生产中对原料、配方的适应性强,生产的产品适应性广,对土壤副作用小。
液氨与硫酸在工艺中,就是硫酸喷在物料的表面,这是化肥生产氨化造粒中多孔固体中酸的氨化问题。
这时过程的速率主要受氨分子趋近颗粒外表面,再从表面进入毛细孔的扩散速率的控制。
生产实践表明,对运动中的颗粒,气体扩散到表面的速率很快,在颗粒内部的扩散则较慢。
因为气体不仅要进入孔道,而且还要通过液膜和反应产物形成屏蔽。
氨到达颗粒表面的速率与设备的类型和进气方式有关。
氨通过颗粒床的流态可分为两种:一种是滤过式,氨气通过颗粒之间的缝隙连续流过,几乎不影响粒子的运动;一种是喷射式,这时氨通过喷嘴流速较大,在颗粒床形成空间或喷舌,引起颗粒作剧烈的旋转运动,大大强化了传质和传热过程。
固体物料上硫酸的中和反应,通常都在造粒机中进行,液氨通过埋在料床床中的分布器,沿造粒机轴向均匀喷出。
良好的设计可使氨的吸收率达到90%以上。
氨分布器是氨化造粒机的重要部件。
2. 氨酸法工艺流程经配料岗位计量、混合、粉碎后的固相物料被输送到转鼓造粒机内。
浓硫酸和水按比例稀释到一定质量分数后,经流量计计量喷入造粒物料料床,液氨经流量计计量,进入埋在料床中的反应器与稀硫酸产生中和反应,生成温度较高的硫酸铵料浆。
粉状物料与硫酸铵料浆混合,形成一定液相的固溶体,在转鼓造粒机内滚动成粒;磷酸一铵与过量的氨发生中和反应,在适宜的温度和PH值环境下熔融,利用磷铵自身熔融的溶液粘结成粒,同时在高温下各物料间发生复分解反应生成复盐,在造粒机不断的转动下,使物料处于流动状态,相互摩擦、翻动、挤压粘附成粒。
造粒过程中产生的尾气,经文丘里洗涤器洗涤后放空。
氨酸法工艺简介

氨酸法工艺简介氨酸法工艺是近两年来国内出现的一种最新的复肥生产技术,传统复混肥生产工艺相比,氨酸法工艺以其低成本,低能耗,高产量等特点得到了迅速发展,代表了复工艺发展的一个方向。
传统复肥生产为团粒法转鼓造粒,利用蒸气提供热量和水分,而氨酸法造粒则是利用氨酸反应时产生的大量反应热来加热物料,2NH3+H2SO4=(NH4)2SO4+热量与传统复复肥蒸汽受热方式相比,由于受热面以及受热方式的不同,氨酸造粒可以加热物料至80-100度,而传统工艺只有60度左右,这就进一步提高了化学盐类的溶解度,在同相的液相比例下造粒物料水分可以降低2-3%,同时成球率明显提高。
也就是说,在同等规模烘干系统设备规格下,可以大大提高烘高能力。
在氨酸反应过程控制中,氨是略过量的,这一方面是为了保证硫酸的充分反应,确保成品PH值在合理范围,另一方面略微过量的氨还可以进一步中和原料中磷酸一铵的酸性,改善物料的成球物性,大大提高了物造粒成球率。
据测算,氨酸工艺的造粒成球率可以达到60-90%,而按常规工艺只有40-60%。
返料比的改变直接提高了装置的生产能力,一般而言,常规设计的复肥生产线能力如果改为氨酸工艺生产,一般产量可以提高30%-50%,每吨成品能耗可以降低40%左右,这也体现了集约型社会的发展理念。
由于造粒过程成球物性的改善,对于常规15-15-15,16-16-16等配方,生产时无需再加入任何粘结剂便可以达到良好的成球状况,就当前市场行情,氮源中氯化铵与尿素单位养分价格存在较大差距的前提下,可以大量使用低价氮源,从而最大程度的降低了产品的原料成本。
就目前原料市场价格而言,氨酸法工艺生产成本平均可比传统工艺降低50-100元/吨。
在市场竞争如此激烈的今天,这无疑是一个重大利好,由此可见,氨酸法工艺确实代表了复肥发展的一个方向。
5-30万吨/年氨酸法(尿基)复合肥生产技术一.氨酸法工艺特点:①将化工原料硫酸、液氨引入到复合肥生产中,将简单的复混肥生产提升到了复合化的程度,提升了产品的质量。
氨酸法工艺技术简述
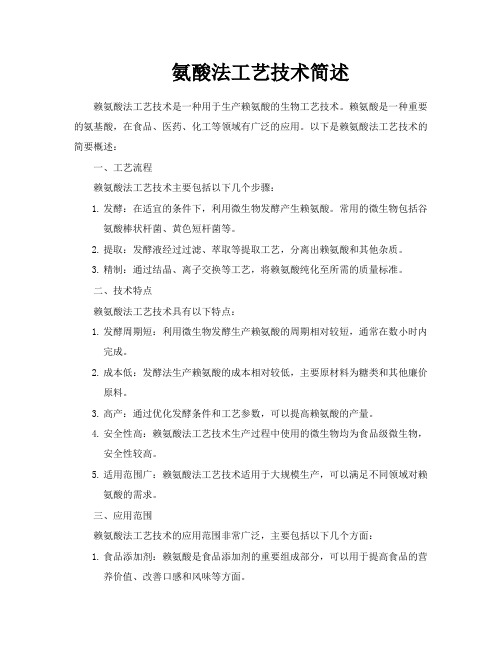
氨酸法工艺技术简述赖氨酸法工艺技术是一种用于生产赖氨酸的生物工艺技术。
赖氨酸是一种重要的氨基酸,在食品、医药、化工等领域有广泛的应用。
以下是赖氨酸法工艺技术的简要概述:一、工艺流程赖氨酸法工艺技术主要包括以下几个步骤:1.发酵:在适宜的条件下,利用微生物发酵产生赖氨酸。
常用的微生物包括谷氨酸棒状杆菌、黄色短杆菌等。
2.提取:发酵液经过过滤、萃取等提取工艺,分离出赖氨酸和其他杂质。
3.精制:通过结晶、离子交换等工艺,将赖氨酸纯化至所需的质量标准。
二、技术特点赖氨酸法工艺技术具有以下特点:1.发酵周期短:利用微生物发酵生产赖氨酸的周期相对较短,通常在数小时内完成。
2.成本低:发酵法生产赖氨酸的成本相对较低,主要原材料为糖类和其他廉价原料。
3.高产:通过优化发酵条件和工艺参数,可以提高赖氨酸的产量。
4.安全性高:赖氨酸法工艺技术生产过程中使用的微生物均为食品级微生物,安全性较高。
5.适用范围广:赖氨酸法工艺技术适用于大规模生产,可以满足不同领域对赖氨酸的需求。
三、应用范围赖氨酸法工艺技术的应用范围非常广泛,主要包括以下几个方面:1.食品添加剂:赖氨酸是食品添加剂的重要组成部分,可以用于提高食品的营养价值、改善口感和风味等方面。
2.医药领域:赖氨酸在医药领域也有广泛的应用,如合成抗生素、抗癌药物等。
3.化工领域:赖氨酸在化工领域的应用主要包括合成香料、助剂等。
4.其他领域:赖氨酸还可以应用于畜牧业、农业等领域,如作为饲料添加剂等。
四、未来发展方向随着科技的不断进步和应用领域的不断拓展,赖氨酸法工艺技术也在不断发展和改进。
未来,赖氨酸法工艺技术的研究和发展方向主要包括以下几个方面:1.发掘新菌种:寻找新的高效产赖氨酸的菌种,提高赖氨酸的产量和效率。
2.优化发酵条件:进一步优化发酵条件和工艺参数,提高赖氨酸的生产效率和产品质量。
3.联合其他技术:将赖氨酸法工艺技术与其他技术相结合,如基因工程技术、膜分离技术等,以实现更高效的生产和分离纯化。
氨酸法复合肥工艺流程
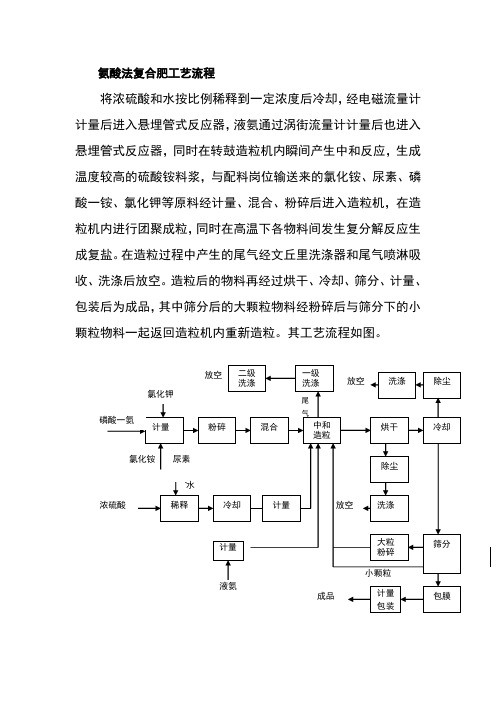
氨酸法复合肥工艺流程
将浓硫酸和水按比例稀释到一定浓度后冷却,经电磁流量计计量后进入悬埋管式反应器,液氨通过涡街流量计计量后也进入悬埋管式反应器,同时在转鼓造粒机内瞬间产生中和反应,生成温度较高的硫酸铵料浆,与配料岗位输送来的氯化铵、尿素、磷酸一铵、氯化钾等原料经计量、混合、粉碎后进入造粒机,在造粒机内进行团聚成粒,同时在高温下各物料间发生复分解反应生成复盐。
在造粒过程中产生的尾气经文丘里洗涤器和尾气喷淋吸收、洗涤后放空。
造粒后的物料再经过烘干、冷却、筛分、计量、包装后为成品,其中筛分后的大颗粒物料经粉碎后与筛分下的小颗粒物料一起返回造粒机内重新造粒。
其工艺流程如图。
对以上新增设备名称、型号、材质数量及要求均见新增设备一览表。
10万吨/年氨酸造粒复合肥技改项目新增设备一览表。
氨酸法无填充料造粒技术
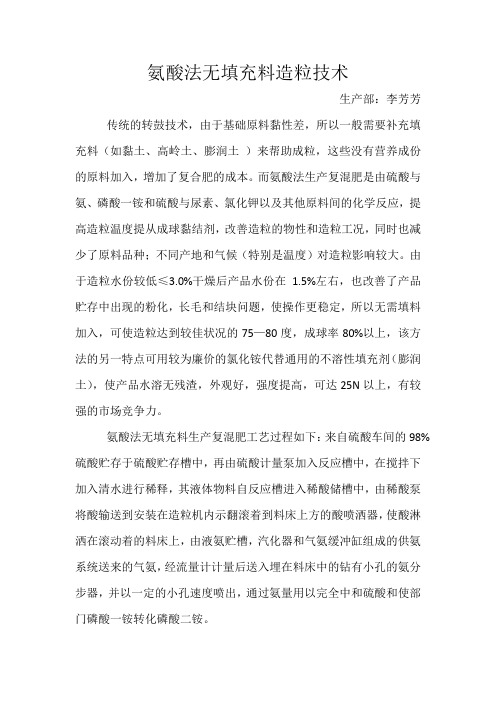
氨酸法无填充料造粒技术生产部:李芳芳传统的转鼓技术,由于基础原料黏性差,所以一般需要补充填充料(如黏土、高岭土、膨润土)来帮助成粒,这些没有营养成份的原料加入,增加了复合肥的成本。
而氨酸法生产复混肥是由硫酸与氨、磷酸一铵和硫酸与尿素、氯化钾以及其他原料间的化学反应,提高造粒温度提从成球黏结剂,改善造粒的物性和造粒工况,同时也减少了原料品种;不同产地和气候(特别是温度)对造粒影响较大。
由于造粒水份较低≤3.0%干燥后产品水份在 1.5%左右,也改善了产品贮存中出现的粉化,长毛和结块问题,使操作更稳定,所以无需填料加入,可使造粒达到较佳状况的75—80度,成球率80%以上,该方法的另一特点可用较为廉价的氯化铵代替通用的不溶性填充剂(膨润土),使产品水溶无残渣,外观好,强度提高,可达25N以上,有较强的市场竞争力。
氨酸法无填充料生产复混肥工艺过程如下:来自硫酸车间的98%硫酸贮存于硫酸贮存槽中,再由硫酸计量泵加入反应槽中,在搅拌下加入清水进行稀释,其液体物料自反应槽进入稀酸储槽中,由稀酸泵将酸输送到安装在造粒机内示翻滚着到料床上方的酸喷洒器,使酸淋洒在滚动着的料床上,由液氨贮槽,汽化器和气氨缓冲缸组成的供氨系统送来的气氨,经流量计计量后送入埋在料床中的钻有小孔的氨分步器,并以一定的小孔速度喷出,通过氨量用以完全中和硫酸和使部门磷酸一铵转化磷酸二铵。
氨分布管是用不锈钢管制成,安装在造粒机筒体的前部分,与供氨总管接通后的导管自料层的最低处顺着滚筒转动的方向再分成几根有一定弧度的支管伸入料床。
硫酸分管处于氨分布管同一断面上,用无缝钢管制成,安装在物料翻动最剧烈的正上方。
硫酸与氨反应生成的水蒸汽及小部分未反应的氨气由尾气风抽至喷淋洗涤箱经过四次洗涤后从烟囱排空,造粒尾气洗涤水当达到一定尝试后返回造粒机造粒。
氨酸法无填充料造粒技术,由于充分利用原料间的化学反应热和生产系统的返料热量,从而降低生产能耗。
其产品特征如下:1、产品外观洁白圆整,不受填充颜色影响;2、产品速溶,无不溶性残渣;3、产品水份≤1.5%,颗料强度≥25N;4、产品养份均匀稳定;5、产品含氮调整范围大,可生产低氮产品≤15%,中氮和高氮≥25—%的品种。
- 1、下载文档前请自行甄别文档内容的完整性,平台不提供额外的编辑、内容补充、找答案等附加服务。
- 2、"仅部分预览"的文档,不可在线预览部分如存在完整性等问题,可反馈申请退款(可完整预览的文档不适用该条件!)。
- 3、如文档侵犯您的权益,请联系客服反馈,我们会尽快为您处理(人工客服工作时间:9:00-18:30)。
氨酸法(稀酸法)复合肥工艺技术简介1、工艺技术概述氨酸法(料床反应)工艺生产复合肥,从原理上介于团粒法和料浆法之间,具有两者的优点,可显著提高生产产量。
生产的产品,颗粒圆润光滑、强度高、不易结块。
生产中,对原料、配方的适应性强,产品适应性广,对土壤副作用小。
液氨与硫酸在工艺中,是硫酸喷在物料的表面,这是化肥生产氨化造粒中多孔固体中酸的氨化问题。
液氨通过埋在料床中的分布器,沿造粒机轴向均匀喷出。
生产实践表明,氨通过料床的流态可分为两种:一种是滤过式,氨通过颗粒之间的缝隙连续流过,几乎不影响粒子的运动;一种是喷射式,氨通过喷嘴流速较大,在颗粒床形成空间或喷舌,引起颗粒作剧烈的旋转运动,大大强化了传质和传热过程。
良好的设计可使氨的吸收率达到95%以上。
氨分布器是氨化造粒机的重要部件。
从国内外常年运行的状况看,该技术是成熟安全可靠的。
2、工艺流程2.1原料预处理与计量结块磷铵和氯化铵,影响输送和计量,需对其进行预处理,生产高氮肥尿素需粉碎1/3,上述三种原料经人工解包后,送入各自的破碎机,破碎后直接落入各自的原料计量贮料斗。
原料计量采用电子皮带秤,电子秤分别用于原料磷铵、氯化钾、氯化铵、固体尿素、微量元素配方计量,并采用工控机控制,以实现原料计量报表、历史记录、配方自动调节等功能。
2.2 造粒来自酸站的浓硫酸和水按比例稀释到一定质量分数后,经流量计计量喷入造粒物料料床;氨站液氨进入埋在料床中的反应器与稀硫酸产生中和反应,生成温度较高的硫酸铵料浆。
粉状物料与硫酸铵料浆混合,形成一定液相的固溶体,在转鼓造粒机内滚动成粒;磷酸一铵与过量的氨发生中和反应,在适宜的温度和PH值环境下溶融,利用磷铵自身溶融的溶液粘结其他物料成粒,同时在高温下各物料间发生复分解反应生成复盐,在造粒机不断的转动下,使物料处于流动状态,相互摩擦、翻动、挤压粘附成粒。
成球率可达95%,成品率达80%以上。
2.3 干燥与冷却造粒物料由皮带机送入干燥机进行干燥,干燥机出料进入第一冷却器,冷却后的物料进入中间筛,筛上物料进入第二冷却机,细粉进入返料,以回收返料热量,降低装置的能耗。
经二冷却后进入二级单层振动筛,进行精筛处理,合格的颗粒送入包膜机进行涂层处理,然后包装出厂。
2.4 除尘装置除尘采用二级除尘,一级在线旋风除尘、一级重力沉降法。
干燥和冷却的尾气分别经干法除尘后一起送入湿法喷淋水洗除尘,然后经烟囱放空。
造粒尾气采用水洗吸收硫酸调节方案,洗涤液用于配酸和造粒,无氨气和废水排放。
3、技术特点3.1 造粒机结构改进连续氨化造粒过程的转鼓造粒机称为氨化转鼓造粒机,是磷复肥造粒中的一种常用设备,由美国TVA(田纳西流域管理局)在50年代初期开发的。
迄今在世界各国的磷复肥生产中广泛应用。
按照美国TVA氨化转鼓造粒机的设计准则,造粒机内设有氨分布器和酸管、蒸汽管和水管。
物料和返料从造粒机头加入,在筒体的转动下形成一个滚动的料床,硫酸由酸泵压送,喷洒在物料床上,氨则通过深埋在料床下的氨分布器高速喷出,使物料氨化到需要的PH值。
造粒机内衬耐高温、耐酸、耐碱的天然橡胶板,使物料在转动过程中,随衬板的震动自然脱落,防结壁效果明显。
3.2 造粒尾气处理由于硫酸与氨在反应过程中有过量的气氨逸出,若直接排放既浪费资源又污染环境,采取在造粒机一端增加密封装置,增加一台引风机和一套文丘里洗涤装置。
采用水作洗涤液吸收气氨时,当氨的溶解度受温度影响饱时,可采用一定量稀硫酸作为气氨的吸收洗涤液,对尾气进行处理,可提高氨的回收率,减少环境污染。
该洗涤液使用一定时间后,可以泵送到配酸和造粒工序,做工艺水使用,使资源得到充分利用。
3.3干燥筛分与除尘干燥机采用特殊内件结构,提高了干燥能力,同时具有结垢自清功能。
干燥后的物料经中间筛处理后,热的细返料直接返回造粒,提高了造粒温度,提高了造粒的成粒率及装置的热效率。
产品筛分为三级筛,一级粗筛,二级分筛,三级精筛,保证产品的粒度合格。
除尘采用三级除尘(二级干法、一级湿法),粉尘通过旋风除尘直接连续返回系统,即有效的提供了造粒所需的粉状物料,改进了产品的外型,同时可增长装置的有效运转时间和劳动强度。
1)、提高产品质量,显著降低能耗硫酸与氨的反应产生了大量的反应热(6648kJ/kgNH3),造粒床层温度在3分钟内升高20-35度,床层温度的升至60-75度,使造粒出口水份含量降低到2.5%-3.5%,不仅降低了干燥系统负荷,提高了装置的生产能力,而且造粒的成粒率上升,颗粒外型光滑度、强度提高。
2)、有效解决尿基复肥物性差的问题以尿素为氮源生产复合肥的主要问题是尿素的溶解度大,尿素与磷铵生成的尿素磷酸盐等复合物的溶解度更大,后者在40度时的溶解度是尿素的4倍,因此,通常尿基复合肥生产时,造粒返料比大,且干燥机、溜槽、破碎机、筛分机等设备结垢、堵塞严重。
由于硫酸铵不能与磷铵生产低温共熔物,因此,尽管每个颗粒内的尿素与磷铵的反应仍然存在,但由于有硫铵的保护,颗粒之间的尿素与磷铵生成尿素磷酸盐的反应机会会明显降低。
可有效地解决生产过程中尿素磷酸铵等低温共熔物给生产带来的诸多问题,保证了装置的稳定运行。
3)、实现装置污水零排放装置湿法除尘的洗涤液用以造粒和配酸,得以回收利用,既解决湿法除尘污水无法处理的问题,又降低了原料消耗。
4)、可有效提高装的操作弹性水汽团粒生产复混肥,物料特性决定了造粒、干燥过程,指标不易控制,操作弹性小。
应用氨酸法通过调节酸、氨量,改善造粒物料的PH 值,保证了在品种、原料、季节等不同情况下的造粒热量、水分等指标,从而使装置在不同季节,采用不同原料,均可正常生产,有效地提高了装置的生产操作弹性。
5)有效降低了生产成本,提高了装置的盈利能力通过采用低品位氮源(如氯化铵、硫铵)替代填料,从而减少了尿素和粘土的投入量,有效的降低了原料成本。
造粒成粒率稳定,装置运行平稳,从而减少了装置故障的发生,生产能力得到了有效的提高,降低了维修费用,使产品的制造费用得到了有效的降低。
6)抗结块能力增强。
颗粒表面光滑,粒度均匀,抗压强度好。
7)生产配方灵活,可生产高氮、高磷及氮磷等多品种复合肥产品。
8)造粒成球率高,装置粉尘产生量小,生产环境好。
4、设计基础4.1 装置设计生产能力8--30万吨/年(年运转天数300天7200小时)。
4.2 产品方案质量标准:GB15063-2009,缩二脲含量在0.5%以下。
本工艺以无机复合肥产品为基础设计,适应氮、磷、钾养分25%-52%范围内高低浓度复合肥产品的生产,生产线可开发生产出不同配比的肥料品种,还适合有机无机复混肥料生产。
典型配方如下:26-10-12 25-10-10 25-12-8 20-12-13 21-11-10 20-8-12 25-10-16 22-10-16 22-8-12 25-15-513-17-15 12-18-15 12-23-10 10-22-1815-15-15 16-16-16 17-17-174.3 原料N 源:尿素N:46.3% H2O: 0.5%氯化铵N:23.5% H20: 5%-7%硫铵N:20% H2O:2%气氨或液氨P2O5源:粉状磷酸一铵11-44、10-50、9-49等H2O:2-4%普钙P2O5: 12-16% H2O:16%重钙P2O5:42%-46% H2O:8%K2O源:氯化钾白钾或红钾K2O:55-60% H2O:1--6%硫酸钾K2O:50% H2O:1.0%化学品:硫酸84%-98%(北方地区为84%-92.5%)4.4 自备公用工程电:500kw/h 380V±5%,频率50±3%水:生产水0.5t/h蒸汽:0.6-12MPa煤:10-15kg/t4.5 吨产品消耗(15-15-15为例)原辅材料损耗率0.3%(养分含量)电25度蒸汽30-80公斤原煤12-15kg/t4.6 污染物排放与噪声控制标准液态废物:废水执行《污水综合排放标准》(GB8978-1996)表4二级标准,排放量为零。
气态废物:废气执行《大气污染物综合排放标准》(GB16297-1996)表2二级标准。
(标准规定最高排放浓度:120mg/m3,本装置允许排放浓度50mg/m3 ,排放量:60000m3 /n)排气筒标高:15m-20m固态废物:无固态废物噪声:执行《工业企业厂界噪声标准》(GB12348-90)III类标准昼:65dB(A) 夜:55dB(A)5.工艺优势5.1 投资省,可实现一机两用该项目可在原转鼓蒸汽造粒复混肥装置上仅需增加料床氨酸分布器、造粒尾气洗涤装置,即可开发出氨酸造粒复合肥新产品。
投资省,操作范围大,当不采用氨酸造粒生产复合肥时,该装置还能生产水汽造粒复混肥产品,实现一机双用。
5.2 节能效果显著利用氨和硫酸中和反应生成的硫酸铵料浆和融溶的磷酸一铵溶液代替水汽进行造粒,减轻了烘干负荷,提高了产量,节约了能源。
液氨和稀酸直接进入造粒机造粒,稀硫酸既是一种粘性原料又充当液相参与造粒过程,反应热即提高了造粒物料的温度,又减少了物料的含水量,利于成球和烘干,大大减少了干燥的负荷,煤耗从每吨35Kg 下降至15Kg。
由于造粒物料温度较高,水份较低,一段干燥便使产品水份达标,可实现一段干燥工艺生产高氮尿基复合肥工艺,简化了工艺过程。
尾气处理的洗涤液用于造粒和配酸,得以回收,即解决了传统工艺湿法除尘系统洗涤液的回收问题,又降低了原料损耗,可实现污水零排放。
5.3 生产成本相对较低氨酸中和反应生成的硫酸铵料浆可代替粘性造粒填加剂,高浓度品种不需在生产工艺中加入膨润土或凹凸棒土等粘结剂,比添加粘结剂的造粒成球率还要高,物料返料比低,大大提高了装置生产能力,降低了单位生产成本。
1)生产能力提高30%-50%,使吨肥产品的各种固定成本明显下降。
2)产品质量的提高和产品的多样化,有利于产品品牌的创建,提高了产品的市场竞争力,进而吨肥销售成本有所降低。
3)充分利用原料间的化学反应热和系统的返料热量,吨肥产品的煤耗可降低30%--50%以上。
4)产品抗结块能力的增加,消耗防结块剂的成本也有所下降。
5)利用廉价的氯化铵原料代替填充剂和部分尿素,同时也可使用低品位、低价格的氯化钾、普钙等原料,使产品原料成本有所降低。
6)可采用一段干燥,直接利用颗粒尿素进行生产,简化了生产过程,固定投资和运行费用有所降低。
7)装置的连续稳定运行,降低了设备的事故率和维修费用。
5.4 产品质量好产品不溶性残渣少,外观洁白、光滑、圆润,有较强的市场竞争力;强度大于20N,水份低,颗粒粒度均匀,有较强的抗结块能力;造粒工况稳定,产品内在养分波动小。
产品不易结块,便于机械化施肥,产品质量优于国GB15063--2009标准要求。