煤制尿素
煤化工装置尿素生产过程节能降耗的分析

煤化工装置尿素生产过程节能降耗的分析随着社会的发展和经济的快速增长,对能源的需求日益增加。
在这种情况下,能源的节约和高效利用成为了人们关注的焦点。
煤化工装置尿素生产过程是一个消耗能源较大的过程,因此在节能降耗方面具有一定的挑战性。
本文将从几个方面进行分析,探讨煤化工装置尿素生产过程节能降耗的技术途径及其可行性。
我们来分析目前煤化工装置尿素生产过程中存在的能源消耗情况。
煤化工装置尿素生产过程主要包括合成氨、尿素合成和尿素颗粒化三个步骤。
合成氨过程中主要能源消耗体现在天然气的蒸汽重整制氢和氮气的制氮,尿素合成过程中主要能源消耗体现在合成氨和二氧化碳的消耗,尿素颗粒化过程中主要能源消耗体现在旋流器和离心机耗能。
煤化工装置尿素生产过程中的能源消耗主要集中在原料气的消耗和设备耗能上。
针对煤化工装置尿素生产过程中存在的能源消耗情况,我们可以从以下几个方面来探讨节能降耗的技术途径。
可以通过优化合成氨工艺来降低原料气的消耗。
采用先进的蒸汽重整技术和新型的氮气制备技术,可以提高合成氨过程的能源利用效率,降低原料气的消耗。
可以通过改进尿素合成工艺来降低合成氨和二氧化碳的消耗。
采用高效的催化剂和优化的反应条件,可以提高尿素合成过程的能源利用效率,降低合成氨和二氧化碳的消耗。
可以通过更新和优化尿素颗粒化设备来降低能耗。
采用新型的旋流器和离心机,可以提高尿素颗粒化过程的能源利用效率,降低设备耗能。
在探讨节能降耗的技术途径之后,我们可以分析一下这些技术途径的可行性。
从技术上来看,这些技术途径已经在一些煤化工装置尿素生产过程中得到了应用,并取得了良好的效果。
一些尿素生产企业采用了先进的合成氨工艺和尿素合成工艺,实现了原料气的节约和能耗的降低。
从经济上来看,这些技术途径的投资成本较高,但是在长期运行中可以获得较好的经济效益。
通过技术改造和设备更新,可以降低能源消耗,提高产品质量,降低生产成本,从而增强企业的竞争力。
煤化工装置尿素生产过程节能降耗的技术途径主要包括优化合成氨工艺、改进尿素合成工艺和更新尿素颗粒化设备。
2024年煤制尿素市场分析报告

2024年煤制尿素市场分析报告1. 市场概述煤制尿素是一种从煤炭中提取的有机化合物,经过加工后可用作农业肥料。
近年来,随着环保意识的增强和化学农药的限制,煤制尿素作为一种安全可靠的肥料得到了广泛应用。
本报告将对煤制尿素市场进行详细的分析和评估。
2. 市场规模和趋势据统计数据显示,煤制尿素市场在过去五年中保持了稳定的增长态势。
根据相关机构的预测,未来几年内,煤制尿素市场有望进一步扩大。
这主要归因于以下几个因素:•环保要求的提高:煤制尿素相较于传统化学肥料,具有更低的氮素排放和环境污染风险,符合现代农业对环境友好产品的需求。
•农业生产的增加:随着人口的增长和农业现代化的推进,对有效肥料的需求也在增加,煤制尿素能够满足这种需求。
•可持续发展战略:煤制尿素作为一种对煤炭资源的有效利用方式,符合国家的可持续发展战略。
3. 市场竞争情况目前,煤制尿素市场主要由几家大型化肥企业垄断,市场竞争较为激烈。
主要竞争因素包括产品质量、价格、品牌影响力等。
此外,技术创新和产品研发也是企业竞争的关键要素。
虽然市场竞争激烈,但是由于煤制尿素市场规模较大且增长潜力巨大,新进入市场的企业依然有机会获得一定的市场份额。
此外,政府对煤制尿素行业的支持和鼓励也为企业发展提供了机遇。
4. 市场分析和前景煤制尿素作为一种新兴的肥料产品,具有较高的市场发展潜力。
与传统化学肥料相比,煤制尿素具有以下优势:•环保:煤制尿素可减少氮肥的使用量和氮素排放,对土壤生态环境的影响较小。
•高效:煤制尿素的养分含量较高,能够提高农作物产量和质量。
•经济:煤制尿素的生产成本相对较低,价格较为合理,能够降低农业生产成本。
未来几年内,煤制尿素市场有望继续保持稳定增长,市场规模和市场份额有望继续扩大。
此外,随着技术的不断进步,煤制尿素的生产工艺和质量也将不断改善和提升,进一步促进市场的发展。
5. 总结煤制尿素市场作为一种新兴的肥料市场,具有广阔的市场前景。
市场竞争激烈,但是随着环保意识的增强和农业生产的发展,煤制尿素市场有望继续保持稳定增长。
煤制尿素产业链梳理

煤制尿素产业链梳理煤制尿素1. 空气压缩制得氮气;2. 煤燃烧制的氢气+一氧化碳+二氧化碳;3. 1+2制的氮气;4. 氮气+二氧化碳制的尿素。
尿素制三聚氰胺三聚氰胺(Melamine)(化学式:C3H6N6),俗称密胺、蛋白精,IUPAC命名为“1,3,5-三嗪-2,4,6-三氨基”,是一种三嗪类含氮杂环有机化合物,被用作化工原料。
它是白色单斜晶体,几乎无味,微溶于水(3.1g/L常温),可溶于甲醇、甲醛、乙酸、热乙二醇、甘油、吡啶等,不溶于丙酮、醚类、对身体有害,不可用于食品加工或食品添加物。
三聚氰胺是氨基氰的三聚体,由它制成的树脂加热分解时会释放出大量氮气,因此可用作阻燃剂。
它也是杀虫剂环丙氨嗪在动物和植物[体内的代谢产物。
CO(NH2)2—→C3H6N6 + 6 NH3 + 3 CO2 (一定条件)三聚氰胺制甲醛氨基树脂三聚氰胺甲醛树脂由三聚氰胺和甲醛缩聚而成,随反应物摩尔比不同产生不同产物。
三聚氰胺制树脂胶黏剂三聚氰胺制泡沫尿素制碳酸丙烯酯碳酸丙烯酯制碳酸二甲酯碳酸二甲酯制碳酸甲乙酯碳酸甲乙酯(Ethyl Methyl Carbonate)别名碳酸乙基甲酯,为无色透明液体,不溶于水,可用于有机合成,是一种优良的锂离子电池电解液的溶剂。
碳酸甲乙酯应储存于阴凉、通风、干燥处,按易燃化学品规定储运。
碳酸甲乙酯制碳酸二乙酯碳酸二乙酯(CAS: 105-58-8 ,英语名:Diethyl carbonate)是乙醇的二碳酸酯,常温下为无色清澈液体。
主要用作硝酸纤维素、树脂和一些药物(如红霉素)的溶剂,及有机合成(如苯巴比妥、除虫菊酯)的中间体。
它还可用在锂电池的电解液中。
碳酸二甲酯制碳酸二苯酯碳酸二苯酯(DPC)是一种不溶于水,溶于热乙醇、苯、乙醚、四氯化碳、冰醋酸等有机溶剂的白色结晶固体,能被热碱分解。
主要用于工程塑料聚碳酸酯和聚对羟基苯甲酸酯等的合成原料,也可以用作硝酸纤维素的增塑剂和溶剂。
煤制尿素工艺技术方案

煤制尿素工艺技术目前,世界上最具有竞争性的尿素合成工艺是荷兰Stamicarbon公司的CO2汽提工艺、意大利Snamprogetti公司的NH3汽提工艺和日本东洋公司的ACES工艺。
它们在世界上建厂数量为:CO2汽提工艺115套,氨汽提工艺80套,ACES工艺9套。
1980以后建厂的工艺以氨汽提工艺居多。
近年来,CO2汽提工艺有很大的发展,Stamicarbon与Sandvik公司合作,推出了一种耐腐蚀性能更优异的专门双相钢材料——Safurex (Stamicarbon A4-18005型BE.06),该材料可以在无氧情况下,能耐高温甲铵液的腐蚀,在中国宁夏用新的CO2汽提工艺成功的改造了NH3汽提工艺,使装置增产50%。
(一)国外尿素技术工艺概况1、CO2汽提工艺该工艺由荷兰Stamicarbon公司于1964年开始中间试验,1967年建成第一套工业装置。
该工艺在70年代初期发展迅速,目前己在世界范围内承建200多套尿素装置,总能力大约为50 Mt/a,占世界尿素总能力的45%,设计能力范围在70~3250t/d。
我国也己有18套大型装置在运行,最大的单系列是中海油富岛化学有限公司的2700t/d。
该工艺包括原料压缩、尿素合成及未反应物的高压分解和回收、未反应物的低压分解和回收、尿液浓缩与造粒、工艺冷凝液处理等工序。
该工艺用CO2作汽提剂,在与合成等压条件下将合成塔出料在汽提塔内加热汽提,使未转化的大部分甲铵分解成CO2和NH3蒸出,分解及汽化所需的热量由2.45MPa蒸汽供给。
汽提塔出汽在高压冷凝器内生成甲铵冷凝液,冷凝反应所放出的热量副产低压蒸汽,供低压分解、尿液蒸发使用,汽提塔出液减压后进入精馏塔,将残余甲铵和氨进一步加热分解并蒸出,然后经真空闪蒸,两段真空蒸发浓缩至99.7%的尿液送造粒塔造粒,或者直接用一段蒸发的96%尿液去生产大颗粒尿素。
2、NH3汽提工艺NH3汽提工艺由意大利Snamprogetti公司于1967年试验成功并获得专利。
煤制尿素工艺流程
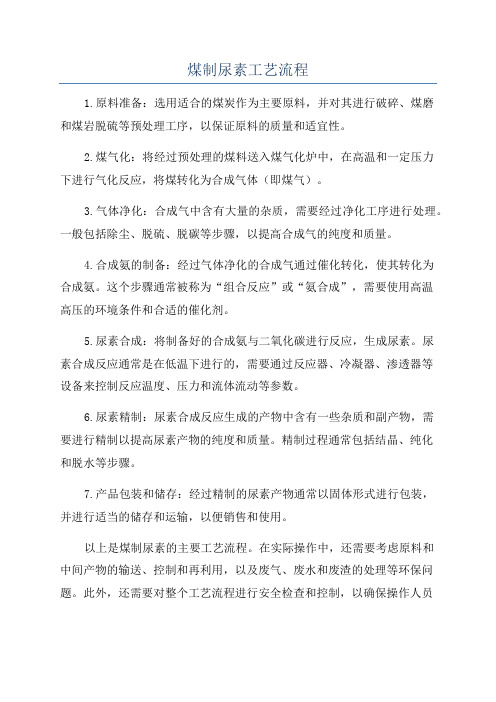
煤制尿素工艺流程
1.原料准备:选用适合的煤炭作为主要原料,并对其进行破碎、煤磨
和煤岩脱硫等预处理工序,以保证原料的质量和适宜性。
2.煤气化:将经过预处理的煤料送入煤气化炉中,在高温和一定压力
下进行气化反应,将煤转化为合成气体(即煤气)。
3.气体净化:合成气中含有大量的杂质,需要经过净化工序进行处理。
一般包括除尘、脱硫、脱碳等步骤,以提高合成气的纯度和质量。
4.合成氨的制备:经过气体净化的合成气通过催化转化,使其转化为
合成氨。
这个步骤通常被称为“组合反应”或“氨合成”,需要使用高温
高压的环境条件和合适的催化剂。
5.尿素合成:将制备好的合成氨与二氧化碳进行反应,生成尿素。
尿
素合成反应通常是在低温下进行的,需要通过反应器、冷凝器、渗透器等
设备来控制反应温度、压力和流体流动等参数。
6.尿素精制:尿素合成反应生成的产物中含有一些杂质和副产物,需
要进行精制以提高尿素产物的纯度和质量。
精制过程通常包括结晶、纯化
和脱水等步骤。
7.产品包装和储存:经过精制的尿素产物通常以固体形式进行包装,
并进行适当的储存和运输,以便销售和使用。
以上是煤制尿素的主要工艺流程。
在实际操作中,还需要考虑原料和
中间产物的输送、控制和再利用,以及废气、废水和废渣的处理等环保问题。
此外,还需要对整个工艺流程进行安全检查和控制,以确保操作人员
及设备的安全。
煤制尿素工艺的技术和经济指标也是关键的研究和改进对象,涉及到原料利用率、能耗、产品质量和成本等方面的考虑。
尿素生产工艺流程简介

经蒸发、造粒后包装销售。
粗甲醇经精馏得到精甲醇销售。
二氧化碳经净化和压缩后,与氨一起送入尿素合成塔,在适当的温度和压力下,合成尿素,的氮氢混合气压缩到高压,并在高温、有催化剂存在的情况下合成为氨。
脱碳解吸出来的换、二次脱硫、脱碳、精脱硫、甲醇、烃化等工艺将气体净化,除去各种杂质后,将纯净 原料煤利用蒸汽和空气为气化剂,在煤气发生炉内产生半水煤气,经一次脱硫、变生产流程说明一分厂生产流程一分厂生产流程及说明1、造气工段工艺流程说明:采用间歇式固定常压气化法,即在煤气发生炉内,以无烟块煤或焦炭为原料,并保持一定的炭层,在高温下,交替地吹入空气和蒸汽,使煤气化,以制取合格的半水煤气。
经除尘、热量回用降温后送入气柜。
自上一次开始送风至下一次开始送风为止,称为一个工作循环,每个循环分吹风、上吹、下吹、二次上吹和吹净五个部分。
各工段流程2、一脱工段除去焦油等杂质后送往压缩一入。
目前使用的脱硫方法为栲胶脱硫法。
S,然后进入冷却清洗塔上段降温后,经静电除焦2后进入脱硫塔,脱除部分H 油等杂质并降低一定温度后由萝茨风机加压送到冷却清洗塔下段降温、除尘 来自造气的半水煤气,经半水煤气气柜出口冷洗塔除去部分粉尘,煤焦3、变换工段流程说明:半水煤气经除油器除去气体挟带的油等杂质后,一氧化碳与水蒸汽借助于催化剂的作用,在一定的温度下变换成二氧化碳和氢气。
通过变换既除去了一氧化碳,又得到了制合成氨的原料气氢和制尿素所需的原料气二氧化碳,使热量得到有效回收。
本工段采用全低变工艺进行变换。
4.二次脱硫流程说明:变换气经过气液分离器后进入脱硫塔脱除变换气中的H2S后送往压缩三入。
并经溶液再生,提取单质硫。
采用栲胶脱硫法脱硫。
利用二氧化碳气体在碳丙液中溶解度大的特点,除去变换气中的二氧化碳,净化气经精脱硫脱除微量硫后送往压缩四段。
二氧化碳气体经净化、压缩,送至尿素合成塔。
碳丙液对CO2的吸收在低压下符合亨利定律,因此采用加压吸收,减压再生。
煤制尿素市场分析报告

煤制尿素市场分析报告1.引言1.1 概述概述部分的内容:煤制尿素是一种重要的化肥原料,是通过以煤为原料制造尿素的过程。
随着环保和资源利用的重视,煤制尿素市场逐渐受到关注。
本报告将对煤制尿素市场进行深入分析,包括市场现状、趋势分析、竞争格局、发展前景和投资建议等方面。
通过本报告,读者可以全面了解煤制尿素市场的现状和未来发展趋势,为相关投资决策提供参考。
文章结构部分应该包括对整篇文章的各个部分进行简要介绍,帮助读者更好地理解整篇文章的组成和内容安排。
可以按照以下内容进行编写:"1.2 文章结构本文主要分为引言、正文和结论三个部分。
在引言部分,将介绍煤制尿素市场的概述、文章结构和目的,为读者提供一个总体的了解。
在正文部分,将分析煤制尿素市场现状、市场趋势和竞争格局,帮助读者更深入地了解市场的情况。
在结论部分,将对煤制尿素市场发展前景进行展望,提出投资建议,并对全文进行总结。
通过这种结构,读者可以全面而系统地了解煤制尿素市场的情况和发展前景。
"1.3 目的目的部分内容:本报告旨在对当前煤制尿素市场进行深入分析,以揭示其市场现状、趋势和竞争格局。
同时,通过对煤制尿素市场的发展前景和投资建议进行分析,旨在为投资者和相关行业从业者提供可靠的市场参考,帮助他们更好地把握市场机遇,做出明智的投资决策。
1.4 总结总结:通过对煤制尿素市场现状、趋势分析以及竞争格局的深入探讨,可以得出以下结论:煤制尿素市场具有巨大的发展潜力,受益于煤炭资源丰富以及尿素在农业、化工等领域的广泛应用,市场需求持续增长。
随着技术进步和创新的推动,煤制尿素的生产成本逐渐降低,并且在环境友好性和能源利用方面具有优势,这将为市场带来更多发展机遇。
在煤制尿素市场竞争格局方面,国内外企业都在加大投入,市场竞争将更加激烈,进一步推动行业健康发展。
综上所述,煤制尿素市场具有广阔的发展前景,投资者可关注市场趋势,抓住机遇,积极参与市场投资。
2024年煤制尿素市场前景分析

2024年煤制尿素市场前景分析1. 引言煤制尿素是一种重要的化肥原料,广泛应用于农业领域。
随着人口增长和农业需求的增加,煤制尿素市场呈现出不断增长的趋势。
本文将对煤制尿素市场的前景进行分析,以帮助投资者了解其潜在的商机。
2. 煤制尿素市场概述煤制尿素是通过煤炭气化和合成氨工艺制备的一种合成氨肥料。
其化学性质与传统尿素相似,但制备工艺更加环保且原料资源丰富。
市场上的煤制尿素主要分为工业级和农业级,其中农业级是主要应用在农业生产中,具有较高的市场需求。
3. 煤制尿素市场驱动因素3.1 农业需求增加随着全球人口增长以及改善生活水平,农业产量的需求不断增加。
煤制尿素作为有效的氮肥,能够提供植物生长所需的养分,满足农作物的高产要求。
因此,农业需求的增加是推动煤制尿素市场增长的重要因素。
3.2 煤制尿素技术进步煤制尿素的生产工艺在近年来得到了不断的改进和优化。
新技术的应用使得生产过程更加高效和环保,并降低了生产成本。
这些技术进步促进了煤制尿素市场的发展,并增强了其竞争力。
3.3 环保政策的支持随着全球环保意识的提高,各国政府纷纷出台了促进环保发展的政策。
煤制尿素作为一种环保的肥料替代品,在政策的支持下受到越来越多的关注。
这些环保政策的出台为煤制尿素市场的发展提供了良好的环境和机遇。
4. 煤制尿素市场挑战4.1 市场竞争加剧随着煤制尿素市场的发展,市场竞争也日益激烈。
传统尿素等其他氮肥产品仍然占据着较大的市场份额,使得煤制尿素面临较大的竞争压力。
投资者需要关注市场竞争的因素,以找到自身的优势和定位。
4.2 原料价格波动煤制尿素的原料主要是煤炭,而煤炭价格受市场供需关系和政策等因素的影响较大。
原料价格的波动会直接影响到煤制尿素的生产成本和市场价格,增加了投资的风险。
4.3 环保要求加大虽然煤制尿素相对于传统尿素更环保,但仍然存在着一定的环保问题。
政府对煤制尿素生产的环保要求也逐渐加大,投资者需要注重环境保护并遵循相关法规,以确保正常生产和市场准入。
煤化工如何生产尿素的原理

煤化工如何生产尿素的原理
尿素是一种重要的化学品,广泛用于肥料、化肥、塑料、药品和化妆品等领域。
煤化工生产尿素的过程主要分为以下几个步骤:
1. 合成氨:首先,通过煤炭或天然气等原料制备氢气和氮气。
然后,将氢气和氮气在高温和高压条件下反应,生成氨气。
这个过程通常采用哈柏-博什过程或斯特劳斯-博什过程。
2. 合成尿素:将合成氨与二氧化碳反应,生成尿素。
这个过程叫做哈柏-博什法。
在这个过程中,氨气和二氧化碳通过催化剂反应,生成尿素。
这个反应通常在高温和高压条件下进行。
3. 结晶和分离:合成的尿素溶液经过结晶和分离过程,将尿素从溶液中分离出来。
通常采用蒸发和结晶的方法,将尿素溶液中的水蒸发掉,得到固体尿素。
4. 精制和包装:最后,将得到的固体尿素进行精制和包装,以便供应和使用。
需要注意的是,煤化工生产尿素的过程可能会因生产工艺、设备和原料等因素而有所不同。
以上只是一般的工艺流程,具体的生产过程可能会有所差异。
煤制尿素工艺技术方案

煤制尿素工艺技术目前,世界上最具有竞争性的尿素合成工艺是荷兰Stamicarbon公司的CO2汽提工艺、意大利Snamprogetti公司的NH3汽提工艺和日本东洋公司的ACES工艺。
它们在世界上建厂数量为:CO2汽提工艺115套,氨汽提工艺80套,ACES工艺9套。
1980以后建厂的工艺以氨汽提工艺居多。
近年来,CO2汽提工艺有很大的发展,Stamicarbon与Sandvik公司合作,推出了一种耐腐蚀性能更优异的专门双相钢材料——Safurex (Stamicarbon A4-18005型BE.06),该材料可以在无氧情况下,能耐高温甲铵液的腐蚀,在中国宁夏用新的CO2汽提工艺成功的改造了NH3汽提工艺,使装置增产50%。
(一)国外尿素技术工艺概况1、CO2汽提工艺该工艺由荷兰Stamicarbon公司于1964年开始中间试验,1967年建成第一套工业装置。
该工艺在70年代初期发展迅速,目前己在世界范围内承建200多套尿素装置,总能力大约为50 Mt/a,占世界尿素总能力的45%,设计能力范围在70~3250t/d。
我国也己有18套大型装置在运行,最大的单系列是中海油富岛化学有限公司的2700t/d。
该工艺包括原料压缩、尿素合成及未反应物的高压分解和回收、未反应物的低压分解和回收、尿液浓缩与造粒、工艺冷凝液处理等工序。
该工艺用CO2作汽提剂,在与合成等压条件下将合成塔出料在汽提塔内加热汽提,使未转化的大部分甲铵分解成CO2和NH3蒸出,分解及汽化所需的热量由2.45MPa蒸汽供给。
汽提塔出汽在高压冷凝器内生成甲铵冷凝液,冷凝反应所放出的热量副产低压蒸汽,供低压分解、尿液蒸发使用,汽提塔出液减压后进入精馏塔,将残余甲铵和氨进一步加热分解并蒸出,然后经真空闪蒸,两段真空蒸发浓缩至99.7%的尿液送造粒塔造粒,或者直接用一段蒸发的96%尿液去生产大颗粒尿素。
2、NH3汽提工艺NH3汽提工艺由意大利Snamprogetti公司于1967年试验成功并获得专利。
煤产尿素工艺流程感悟总结

煤产尿素工艺流程感悟总结Working on the coal to urea process has provided me with a unique insight into the intricate mechanisms involved in converting coal into urea. It is truly fascinating to see the transformation of a raw material like coal into a valuable product like urea, which is widely used in the agricultural industry. The process involves several stages, each of which requires precision and expertise to ensure the final product meets the required standards. From coal gasification to ammonia synthesis and urea production, every step in the process contributes to the overall efficiency and quality of the end product.参与煤制尿素工艺流程为我提供了独特的见解,让我了解将煤转化为尿素所涉及的复杂机制。
看到一种原材料如煤如何被转化成农业界广泛使用的有价值产品尿素,实在是令人着迷。
这个过程涉及到多个阶段,每个阶段都需要精确和专业的技术来确保最终产品符合相关标准。
从煤气化到氨合成再到尿素生产,流程中的每一步都对最终产品的效率和质量产生影响。
One of the most crucial aspects of the coal to urea process is the coal gasification stage, where coal is converted into syngas through a series of chemical reactions. This syngas serves as the primaryfeedstock for the production of ammonia, which is a key intermediate in the urea manufacturing process. The efficiency of the coal gasification stage directly impacts the overall performance of the urea plant, making it vital to optimize this step for maximum productivity.煤制尿素流程中最关键的一环是煤气化阶段,通过一系列化学反应将煤转化为合成气。
煤产尿素工艺流程感悟总结

煤产尿素工艺流程感悟总结Title: Reflection and Summary of Coal-to-Urea Process FlowAbstract:The coal-to-urea process is a significant industrial operation that transforms coal, a carbonaceous resource, into urea, a vital nitrogen fertilizer. This paper reflects on the process flow of coal-to-urea conversion, highlighting its complexities, challenges, and opportunities for optimization. Through this reflection, insights are gained into the intricate interplay of chemical reactions, engineering design, and environmental considerations in the production of urea from coal.Keywords: coal, urea, process flow, reflection, optimizationReflection and Summary:The coal-to-urea process involves several intricate steps, each contributing to the overall conversion of coal into urea. Initially, coal undergoes gasification to produce syngas, primarily composed of carbon monoxide (CO) and hydrogen (H2). This syngas is then subjected to the Fischer-Tropsch synthesis, where CO and H2 react over catalysts to produce a mixture of hydrocarbons, including methanol.Following the synthesis of methanol, the process proceeds with the conversion of methanol to formaldehyde, and subsequently to urea through a series of chemical reactions. These reactions involve the condensation of ammonia and carbon dioxide, leading to the formation of urea as the final product.Throughout the process flow, various challenges emerge, ranging from the optimization of reaction conditions to the efficient utilization of resources. The selection and design of catalysts play a crucial role in enhancing reaction kinetics and product yields. Additionally, the management of by-products and waste streams necessitates effective environmental stewardship to mitigate potential environmental impacts.Furthermore, technological advancements offer opportunities for optimizing the coal-to-urea process. Integration of novel catalysts, process intensification techniques, and advanced process control systems can enhance the efficiency and sustainability of urea production. Moreover, the integration of carbon capture and utilization technologies presents a promising avenue for reducing greenhouse gas emissions associated with coal-based urea production.In conclusion, the coal-to-urea process represents a complex interplay of chemical, engineering, and environmental factors. Through reflection on its process flow, valuable insights are gained into the challenges and opportunities for optimization. By addressing these challenges and leveraging technological innovations, the coal-to-urea industry can strive towards more sustainable and efficient production practices.流程感悟总结:煤制尿素工艺涉及多个复杂步骤,每个步骤都对将煤转化为尿素做出了贡献。
煤制合成氨尿素简介

六、氨的合成
第三十二页,共44页。
氨的合成
n 来自液氮洗装置的合格新鲜气( H2:N2=3:1),经合成气压缩机加压 后,送入氨合成塔,在高温(380~ 430℃)、高压(14.2MPa)下通过 氨合成催化剂的催化作用使部分气体 合成为氨。以液氨的形式送至尿素装 置用。
第三十三页,共44页。
▪ 这是氨合成装置的生产任务。
五五五液氮洗涤精制氢气和配氮液氮洗涤精制氢气和配氮液氮洗涤精制氢气和配氮??五液氮洗涤精制氢气和配氮液氮洗涤精制和配氮?低温甲醇洗产出的高纯度氢气中还有少?低温甲醇洗产出的高纯度氢气中还有少量的一氧化碳co惰性气体ch4ar会影响氨合成催化剂的寿命及造成合成回路中的惰性气积累而影响合成反应使惰性气体弛放气量增加造成有效气体损失需进步对制得的氢气进行精制损失需进一步对制得的氢气进行精制
第二十二页,共44页。
• 5、低温甲醇一步法酸性气体 脱除工艺
第二十三页,共44页。
5.1以-64℃甲醇作为吸收剂,在同一个吸收塔内分步吸收
脱除变换气中的H2S、COS和CO2,制得的净化气的组
成为:
成 分 H2
N2
CO
Ar
CH4
CO2
H2S CH3OH
mol%/ 干
96.42
0.46
2.80
0.19
第十页,共44页。
• 四、氢、二氧化碳的制取
第十一页,共44页。
煤的元素组成(wt%, 干基)
红山2#
C
68.37
H
4.12
N
0.85
O
12.05
S
0.32
Cl
184ppm
Ash Ash analysis (wt%) 灰成分分析(wt%) CaO
2024年煤制尿素市场发展现状

2024年煤制尿素市场发展现状引言煤制尿素是一种重要的化工产品,广泛应用于农业、医药和化工等领域。
本文将对煤制尿素市场的发展现状进行综述和分析。
煤制尿素的生产过程煤制尿素的生产过程包括胺解、氨化和尿素合成等步骤。
煤作为原料,通过高温煤气化和氨合成工艺转化为尿素。
该过程具有高效、低能耗和环保等优点。
煤制尿素市场规模目前,全球煤制尿素市场呈现稳定增长的态势。
据统计数据显示,煤制尿素的年产量已经突破1000万吨,并且呈现逐年增长的趋势。
中国是全球煤制尿素产能最大的国家,其市场占据了全球市场的很大比例。
煤制尿素市场需求煤制尿素作为一种多功能化肥,广泛应用于农业领域。
随着全球人口的增长和农作物种植面积的扩大,对煤制尿素的需求也在不断增加。
此外,煤制尿素还广泛应用于医药和化工等领域,对市场需求也起到了推动作用。
煤制尿素市场竞争态势煤制尿素市场存在着激烈的竞争。
主要竞争对手包括国内外的化工企业和煤炭企业。
这些企业通过不断提高生产工艺和产品质量,降低生产成本,积极开拓市场,争夺市场份额。
煤制尿素市场发展趋势煤制尿素市场在未来将持续保持稳定增长的态势。
随着环保意识的提高和政府对环保产业的支持,煤制尿素的生产工艺将进一步优化,减少环境污染。
此外,煤制尿素还具有资源丰富、生产成本较低等优势,将更好地满足市场需求。
结论煤制尿素市场作为一种重要的化工产品,市场规模不断扩大。
在全球范围内,煤制尿素市场呈现出良好的发展趋势。
未来,煤制尿素行业将继续努力提高生产工艺,提高产品质量,满足市场需求,推动产业进一步发展。
煤头尿素生产工艺

煤头尿素生产工艺
煤头尿素生产工艺是利用天然煤炭作为原料制造尿素的一种工艺。
下面将分为前处理、氨解、浸脱、脱水、干燥和制粒等几个步骤进行介绍。
首先,前处理阶段。
原始煤炭经破碎、筛分等工序,得到一定粒度的煤炭颗粒。
然后进行脱硫除灰,通过化学方法去除煤中的硫和灰分,提高煤质纯度。
第二,氨解阶段。
将预处理后的煤炭与过量的氨水进行反应,得到气相中的氨、甲醛和甲酸铵。
氨和甲醛在高温下反应生成甲酰胺,甲酸铵则通过水溶液的形式得到。
第三,浸脱阶段。
将氮素溶液与尿素溶液进行浸脱,即将尿素溶解在氮素溶液中,得到一定浓度的尿素溶液。
此工艺能有效提高尿素产率和氮转化率。
第四,脱水阶段。
通过脱水系统将尿素溶液中的水分除去,使尿素达到一定的浓度。
脱水过程一般采用蒸汽加热和旋风分离等方法,将溶液中的水分从尿素中分离出来。
第五,干燥阶段。
将脱水后的尿素溶液进行干燥,除去余留的水分。
常采用旋风干燥器进行脱水,并通过热空气传热的方式将尿素溶液中的水分蒸发。
最后,制粒阶段。
将干燥后的尿素溶液进行颗粒化处理,得到一定粒度的尿素颗粒。
制粒一般采用多瓶制粒机,通过破碎、
筛分等工艺将尿素溶液进行颗粒化处理。
总的来说,煤头尿素生产工艺是将原始的煤炭经过前处理、氨解、浸脱、脱水、干燥和制粒等多个步骤,将煤炭转化为尿素颗粒。
这种工艺能够有效利用煤炭资源,提高尿素产率和氮转化率,对于满足农业和化工领域的需求具有重要意义。
- 1、下载文档前请自行甄别文档内容的完整性,平台不提供额外的编辑、内容补充、找答案等附加服务。
- 2、"仅部分预览"的文档,不可在线预览部分如存在完整性等问题,可反馈申请退款(可完整预览的文档不适用该条件!)。
- 3、如文档侵犯您的权益,请联系客服反馈,我们会尽快为您处理(人工客服工作时间:9:00-18:30)。
汽提法
﹛
2.二氧化碳汽提法 3.氨汽提法
生产工艺: • 氨和二氧化碳在合成塔内,一次反应只有 55%~72%转化为尿素(以CO2计),从合成 塔出来的物料是含有氨和甲铵的尿素溶液。 在进行尿素溶液后加工之前,必须将氨和 甲铵分离出去。甲铵分解成氨和二氧化碳 是尿素合成反应中式(1)的逆反应,是强吸热 反应,用加热、减压和气提等手段能促进 这个反应的进行。围绕着如何回收处理从 合成塔里出来的反应混合物料,发展了尿 素的多种生产工艺。
氨的合成
• 合成反应的压力高、低各有利弊:压力高, 压缩功高,但有利于反应平衡,设备相对 小;压力低,压缩功相对低,设备相对大。 本工程按31.4MPa氨合成设计,并设后置 式废热锅炉热回收系统。具有塔阻力小, 氨净值高,使用寿命长,操作简单稳定、 投资少的特点。 • return
甲醇精馏(略)
改良ADA法
• 优点:溶液性能稳 定, • 优点:技术经济指 标较好, • 优点:溶液无毒, • 优点:对碳钢无腐 蚀作用 • 缺点:易堵塔,即 脱硫塔内单质硫易 沉降在填料或设备 上
栲胶法
• 原料易得,脱硫液无毒,活性好,脱硫性 能稳定, • 脱硫效率及气体净化度较高,不堵塔, • 并可用自吸入空气喷射氧化使溶液再生, 具有投资省、效果好、操作方便。 • 在气柜后、压缩机一段入口前采用栲胶脱 硫。
一、合成氨
主线:造气→脱硫 →变换 →脱硫 →脱碳→精脱硫→合成氨→ 合成 尿素 支线:甲醇 →精甲醇 氢氨回收
ቤተ መጻሕፍቲ ባይዱ 造气
• 本工程以无烟煤为原料,,选用空气常压固定床间歇气化 法,并采用成熟的自动加焦及炉况寻优技术来生产合成氨。 自动加焦技术利用机电控制使原料煤通过自动加焦机均匀 地进人造气炉中,由此达到稳定炉温、提高制气时间、减 少煤耗的目的;炉况寻优即随时监视炉内操作情况,并优 化调节的技术。这两项新技术的运用,可使造气炉的产气 量在原料消耗及设备不变的情况下,提高15%。同时,再 使用“过热蒸汽制气”、“入炉蒸汽流量自动调节”、 “人炉蒸汽压力微机控制”、“余热集中回收”等有效的 节能降耗措施,提高单炉产气量,降低生产成本,使生产 运行平稳,安全可靠。
一般使用空气为载气时称为吹脱;使用蒸汽为载气时称为汽 提。
二氧化碳汽提法
• 该法由荷兰Stamicarbon公司研发 • 该法以二氧化碳气体为汽提气,在合成圈等压(14.0MPa) 的压力下,对甲铵进行分解、汽提,避免过多的甲铵进入 低压段,再分解后吸收,重新输送返回合成圈,增加能耗。 由于等压汽提的存在,减少进入低压段的甲铵量,因此无 中压系统,低压段的设备也较少。同时,由于框架的存在, 使得工艺介质以位差流动,减少了动力消耗。 • 合成塔操作条件;压力约13.8MPa、温度180~185℃、氨 与二氧化碳的摩尔比约 2.8。设备采用含钼的低碳不锈钢 (气提塔用高镍铬不锈钢)。
双甲精制
• 即甲醇化、甲烷化脱除原料气中微量的CO和CO2, 使合成氨原料气中CO+CO2≤10ppm。 • 此工艺特点:高压净化精制,电耗少;副产甲醇、 甲烷,丰富了产品类型; • 可调氨醇比,生产操作灵活; • 对变换工段的要求宽松,容易操作,节省蒸汽 • 进入甲烷化系统的CO和CO2含量少,反应氢耗少, 生成的CH4少,气体质量高。 • return
• • • • • • • • • • • •
DDS脱硫技术
• “生化铁—碱溶液催化法气体脱碳脱硫脱氰技术” • 脱硫效率高、溶液循环量小 • 用含亲硫性好氧菌、酚类物质和铁离子以及碱性物质的水 溶液,吸收气体中的有机硫、无机硫,同时,在吸收过程 中还产生少量不溶性铁盐。溶液中的好氧菌在一些络合配 体的协助下,可以将生成的不溶性铁盐瓦解,使之返回铁 碱溶液中,保证溶液中各种形态铁离子稳定地存在。铁碱 溶液在酚类物质与铁离子的共同催化下,用空气氧化再生 时,副产硫磺,再生铁碱溶液循环使用。 • 要提高脱硫液中总铁离子的浓度,同时又要设法降低溶液 中的配体的浓度,这样就可以显著提高脱硫液的脱硫能力, 在脱硫液中加入耗氧菌就可以起到这种作用。同时实验也 证实,不同种类的酚类物质的作用效果也相近. • return
二、合成尿素
主反应: 2NH3(l)+CO2 (l) → NH2CO2NH4(l) (1)
NH2CO2NH4 → NH2CONH2+H2O
(2)
反应(1)快速,强放热,平衡转化率较高,需要在 较高压力下完成(13..2~22.0MPa),温度 165~195℃,反应物料NH3与CO2摩尔比2.5~4.2 反应(2)慢速,温和吸热
• 脱硫原理 在脱硫塔内,煤气在与脱硫液逆流接触的过程中发生如下反 Na2CO3 +H2S→ NaHCO3+NaHS NaHCO3+H2S → NaHS+CO2 +H2O 4NaVO3+2NaHS+H2O →Na2V4O9+4NaOH+2S 焦钒酸钠在碱性脱硫液中被醌态(氧化态)栲胶将部分焦钒酸钠氧化 再生为偏钒酸钠 2TQ(醌态)+V4++2H2O → 2THQ(酚态)+V5+ +2OHTQ(醌态)+HS-→ THQ(酚态)+S↓ 在再生塔内,酚态栲胶与空气中的氧气发生如下反应 2THQ(酚态)+O2 → 2TQ(醌态)+H2O2 生成的H2O2可将V4+氧化成V5+,并可与HS-反应析出元素硫 H2O2+2V4+→ 2V5++2OHH2O2+HS- → H2O+S +OH焦炉煤气中的CO2、HCN、O2 引起的副反应与改良ADA法相同。
精脱硫
• 精脱:合成前应将脱碳气中的硫(H2S<10mg/m3) 脱除到总硫<0.1ppm。 • 精脱工艺以往多用ZnO、JTL常温精脱工艺,但 此工艺需设置提温、降温装置。 • 为实现常温精脱硫,选用JTL _4新工艺,即T102 串T104,其中T102为特种活性炭并添加助剂、稳 定剂制备;T104即EZX,为转化吸收型多功能精 脱硫剂,对有机硫能很好地吸收,具有较高的工 作硫容。JTL_4脱硫剂脱硫精度最高可达 <0.03ppm。 • return
水溶液全循环工艺
五六十年代被广泛采用的一类全循环工艺。 二氧化碳和氨被水吸收生成甲铵的水溶液,返回尿素合成系统。 水的返回降低了转化率,并增加了水的蒸发量,因此,用水量 必须降到最低限度。合成系统的条件是温度190~200℃、 压力 19.7~24.6MPa,氨与二氧化碳的摩尔比3.5~4.5, 合成塔内二氧化碳的一次转化率为62%~72%。氨总回收 率大于99%。甲铵分解采用逐级降压多级分解器法,每级 中分解出来的气体用下一级生成稀甲铵水溶液吸收,最后 返回合成系统。 此法工艺流程较多,但其设计都要求: ①最大限度地回收热量;②甲铵水溶液的循 环量和水量降低到最低水平;③最大限度地 降低动力消耗;④氨回收达到最佳值。
副反应 缩合反应:2CO(NH2)2↔NH2CONHCONH2+NH3 氨分压增加可抑制缩二脲生成
水解反应:CO(NH2)2+H2O↔NH2COONH4 ↔2NH3+CO2+H2O 即生成尿素的逆反应 当温度低于60℃时,水解反应缓慢; 高于100℃时,明显加快; 超过145℃时,水解速度剧增
主要方法(均采用二氧化碳与氨合成)
气提全循环工艺
这类工艺出现在60年代中期,与其他全循环工艺的 不同点在于用氨、二氧化碳或其他气体作为气提剂, 在高压下(或与合成等压)促使甲铵分解。
关于汽提法
原理:将空气或水蒸气等载气通入水中,使载气与废水充分 接触,导致废水中的溶解性气体和某些挥发性物质向气相转 移,从而达到脱除水中污染物的目的。 作用:通常用于脱除废水中的溶解性气体和某些挥发性物质。
氢回收
• 氢回收是合成氨厂节能降耗的主要措施之一,回收驰放气 中的氢,一般可使合成氨产量提高5-8%。目前,氢回收 的技术主要有低温冷冻法、变压吸附法和中空纤维膜法。 • 低温冷冻法要求对驰放气进行严格的预处理(NH3的体积分 数必须<lppm),投资和费用较高,氢回收率约为90%; • 变压吸附法的能耗较低,氢回收率较低,约为75%,切换 阀频率过高,容易损坏,运行费用高。 • 中空纤维膜法利用了合成放空气本身具有很高压力的特点, 不需动力设备,氢纯度和氢回收率均可达85%-98%,流 程简单,装置布置紧凑,占地面积少,故采用膜分离回收 氢的技术。
干法脱硫
• 变压吸附技术 • 活性炭对H2S的脱除效率大于99%. • 由于H2S比CO2易被活性炭吸附,因此可保证活 性炭的吸附能力充分消耗在对H2S的吸附上。 • 吸附能力顺序:H2O>硫化物> CO2>CO>CH4>N2>H2 • 在吸附床降压时,被吸附的CO2解吸出来,同时 吸附剂获得再生 • return
脱碳工艺NHD法
• 纯物理吸收法。NHD为多聚乙二醇二甲醚的混合 物,对H2S和CO2的吸收能力高,热化学稳定性 好,不起泡,不降解,无副反应,对碳钢设备无 腐蚀,对人及生物环境无毒。 • 在低温低压下,脱碳效果好,操作费用低,溶液 吸收能力大,循环量小,减压或气提即可再生, 不需再生热量,可降低能耗。 • return
半水煤气
•
Return
脱硫工艺
• • • • • • 湿式脱硫 1.改良ADA法 2.栲胶法 3.DDS法 干法脱硫 活性炭常温脱硫工艺 • 微量H2S是使甲醇化、 甲烷化和NH3合成等 催化剂失活的主要原 因。 • 在这里使铁触媒中毒。
改良ADA(蒽醌二磺酸钠)法
• 基本原理:该脱硫法的反应机理可分为四个阶段。 • 第一阶段,在pH—8.5~9.2范围内,在脱硫塔内稀碱 液吸收硫化氢生成硫氢化物。 • NaCO3 + H2S → NaHS + NaHCO3 (6-1) • 第二阶段,在液相中,硫氢化物被偏钒酸钠迅速氧化成硫。 而偏钒酸钠被还原成焦钒酸钠。 • 4NaVO3+2NaHS+H2O →Na2V4O9+4NaOH+2S(6-2) • 第三阶段,还原性的焦钒酸钠与氧化态的ADA反应,生 成还原态的ADA,而焦钒酸钠则被ADA氧化,再生成偏 钒酸钠盐 • 第四阶段,还原态ADA被空气中的氧氧化成氧化态的 ADA,恢复了ADA的氧化性能。