旋压车轮
铝车轮旋压模具优化设计

的力学性能 , 如图 1 所示。可以看 出随着温度升高 , 合
金 的强 度下 降 , 塑性 提 高 , 特别 是 在 30o , 塑性 5 C时 其 随温度 的升 高急 剧增加 , 强度也 快速 降低 , 而 因此 旋压
4 O 3 5
变 细 , 具有 明显 的纤维 组织 , 并 大大 提高 了车 轮 的整 体
强度 和耐 腐蚀性 - 。 -
文献 [- ] 4 6 对铝 合金 车轮 旋 压成 形影 响 较 大 的工
3 0 2 5
\
艺参数, 如旋压道次匹配 、 旋轮形状 、 旋轮进 给速度和
旋压 力等 分别进 行 了模 拟 分 析 和试 验 研 究 , 出 了一 得 系列 重要 结论 。但 均未对 旋压 模具 优化 改进 进行 过研 究 。旋压模 具 与车 轮毛坯 的贴 合状 态对旋 压成 形起 到 至关 重要 的作用 。 本 文 通过对 车 轮改进 前后 的旋 压模具 和 毛坯进 行
( e a met f n i n e t n ier g E v omet ngmet D p r n vr m na E gnei , n i n n ae n t oE o l n r Ma C l g f hn , ih ag a 6 0 4 C o eeo C ia Qn u n d o 6 0 , HN) l 0
开始逐渐应用到汽车轮辋的制造和生产中去。车轮正
面采 用低 压铸 造 、 轮辋 采 用热 旋 压 加 工 是 目前 车轮 加 工 中最安 全 、 经 济适 用 、 受 关 注 的一 种 加 工 方 法 , 最 最
车 轮材料 均选 用 A 5 。A 5 3 6 3 6经过 热旋 压 后 金属 晶粒
轮 的旋 压变 形 , 而新型 模具 设计 能够有 效 防止车 轮 变形 。对 新 型模 具 进 行 了试 验 验证 。 模 具设 计 为
热旋压对铝车轮轮辋性能影响的试验研究
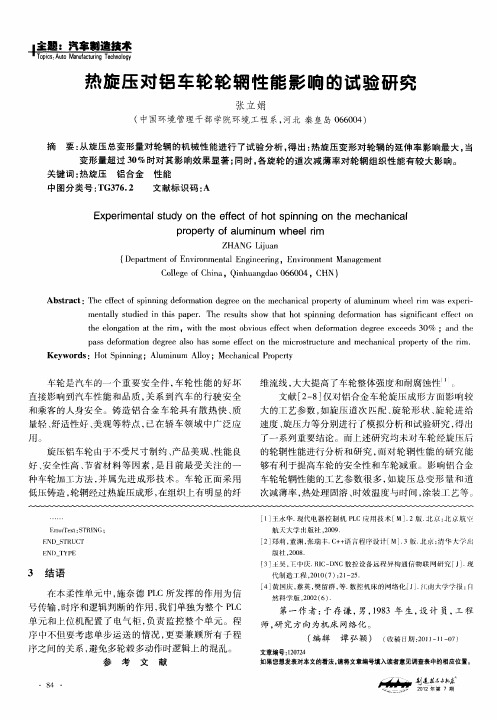
低 压铸 造 , 辋经 过热旋 压成形 , 组织 上有 明显 的纤 轮 在
次减 薄率 , 热处 理 固溶 、 时效温 度与 时 间 , 涂装 工 艺等 。
[] 1 王永华. 现代电器控制 机 P 1 C应用 技术 [ . M] 2版 北京 :七 』 京航 空
Ero T x : T NG r r e t S RI
FND TRUC S T ENI TYP ) E
航 天 大 学 出版 社 ,0 9 20 .
[] 2 郑莉 , 董渊 , 张瑞丰. + 语言程序设计 【 . c+ M] 3版. 北京 : 清华大 、 出
版 社 ,0 8 20 .
[ ]E , 3 = 吴 乇中庆. I D C数控设备远程异构通信物联 网研究 f ] 脱 RC— N J
摘 要 : 从旋压 总变 形量对 轮辋 的机 械性 能进行 了试 验分 析 , 出 : 旋压 变形对 轮辋 的延 伸率 影晌 最大 , 得 热 当 变形量 超过 3 %时对 其影 响效 果显著 ; 0 同时 , 各旋 轮 的道次 减薄 率对轮 辋组 织性 能有 较大 影响 。
关 键词 : 热旋压 铝合金 性 能
l tcul lc n l y m : u o Ma ua tr g h oo o n e g
热旋 压 对 铝 车 轮 轮 辋性 能 影 响的 试验 研 究
张立 娟 ( 中国环境 管理 干部 学 院环境工 程 系 , 河北 秦 皇 岛 060 ) 604
Absr c t a t:Th fe to p n i g d f r to e r e o h c a ia r p ry o l mi um e ef c fs i n n eo main d g e n t e me h n c lp o e t fau n whe lrm se p r- e i wa x e i me t l t d e n t i a e . T e r s ls s w h th ts nnn e o mai n h s sg i c n fe to n al su i d i h s p p r h e u t ho t a o pi ig d fr t a in f a tefc n y o i t ln ai n a he rm ,wi h s b iu fe twh n d f r t n d g e x e d 0% ;a d te he eo g t tt i o t t e mo to v o s ef c e eo ma i e r e e c e s 3 h o n h
基于simufact.forming软件的车轮旋压模拟分析

基于simufact.forming软件车轮旋压模拟仿真段小亮1,李光杰1(1.西模发特信息科技(上海)有限公司技术工程部,上海 200336)摘要:旋压轮毂具有重量轻、强度高、寿命长、表面光洁,机械加工余量少等优点。
而旋压工艺过程复杂,影响因素多,造成实际旋压加工中工艺参数和工装的选择和调试较为困难,本文采用理论结合实际对钢质重型卡车车轮及铝合金轿车车轮旋压工艺进行模拟分析,得出了旋压件的应力应变、厚度尺寸变化、旋压力变化情况,验证了工艺参数的准确性与工艺的可行性,仿真结果与实际有较好的相符性。
通过simufact.forming软件在旋压产品研制过程中的应用发现,仿真分析软件可以提前判断旋压工艺的可行性及合理性,为旋压产品的研制提供重要参考。
关键词:轮毂旋压;Simufact.forming;模拟仿真Simulation of wheel spinning by simufact.formingXiaoliang.Duan1,Jason.Li1(1.ManuSim Solutions Co,.Ltd Engineering department, Shanghai 200336)Abstract:The spinning wheel has the advantages of light weight, high strength, long service life, smooth surface, less machining allowance. But the spinning process is complicated, many influence factors that cause selection and debugging parameters and tooling is difficult in actual spinning process, this paper simulation of the spinning process of steel heavy truck wheels and aluminum alloy car wheel, give the result of the stress and strain, thickness, pressure changes of the parts, verify the feasibility and accuracy of process parameters, Through the simufact.forming software used in the process of spinning in the product development of discovery, analysis and simulation software can advance to judge the feasibility and rationality of the spinning process, provides the important reference for the development of spinning products.Keywords:wheel spinning;Simufact.forming;numerical Simulation1引言轮毂作为汽车中的重要部件之一,起着承载着汽车的重量,同时也体现着汽车的外观造型。
汽车轮毂多道次旋压成形工艺分析及数值模拟

2 有 限元 模 型
坯 料成 形 方 案确 定后 , 利用 Ab q sC a u AE模 块 的三 维造 型功 能建立 各道次 下旋 压的有 限元模 型 。为简化模 型 以提 高运 算 的 精度 和 速 度 , 只对
轮 毂 锻 坯 变 形 部 分 进 行 模 拟 分 析 。定 义 坯 料 为 刚 塑 性 变 形 体 , 用 材 料 为 A3 6铝 合 金 , 性 模 量 所 5 弹 为 7 P , 松 比为 0 5 屈 服 强 度 为 1 3MP , 0M a 泊 ., 3 a
基 金 项 目: 安徽 省 优 秀青 年 科 技 基 金 资 助 项 目( o 4 6 6 1 . 1 o o 0 Y2 ) 作 者 简 介 : 陈豪 ( 9 7) 男 , 肥 工 业 大 学 博 士 生 . — i qa _ h n a @ y a . e 钱 1 8一 , 合 E mal in c e h o e h n t : 通 讯 作 者 : 克 敏 ( 9 3) 男 , 肥 工 业 大 学 教 授 , 士 生 导 师 . — i x e m0 2 @ s a c r 薛 1 6一 , 合 博 E mal u k 7 1 i . o : n n
大减 薄率受 到 限制 , 至少 需 要 采 用 两 个 道 次 的剪
切 旋 压完成 总 的壁 厚 减 薄 , 以旋 压 成 形方 案 拟 所 定 为 先进行 两 道次剪 切旋 压 , 进 行普通 旋压 , 再 每
道 次后 都要 进行 退火 处 理 , 以消除 残余应 力 。
验 或理 论解 析方 法 难 以准 确 、 效 地 解 决 生 产 中 高
一
() 压 成 形 至 1 a旋 / 3时
一
() 压 成 形 至 23时 h旋 /
铝合金车轮旋压成形工艺因素分析

的喷射方式 、 新材料的运用上必须进行技术创新 。该公司尝试将喷涂 方式改为模具表面 经过验 证. 毛坯容易脱模 , 即提高了生产效率又利 于环 保 。所 以有 必 要更 改 喷涂 方 式 . 装 模 具 专 用 喷 涂 系 统 及 良好 的 安 排气装置。使其更合理 , 更环保 , 以此来稳定旋压工艺 。
【 要】 摘 本文从铸造铝合金 车轮 的热旋压成 形工艺出发 , A 5 材料 的旋压性做 了进一步分析, 对 36 对车轮 旋压模 具与毛坯贴合程度、 模具
润滑方式、 模具结构进行 了数值模拟和试验验证。结果表明 , 选择合适的旋压温度能够避免 由于旋压过冷而造成的车轮毛坯缺 陷, 模具热膨胀
21 压 温度 选 择 .旋
A36合金其室温塑性较差 . 5 需热态下成形 旋压温度的选择对其 成形性和成形质量有很大影响 采用高温拉伸实验测定合金在不 同温 度下的力学性能 , 随着温度升高 , 合金 的强度 下降 , 塑性提高 特别是 在 30 时 , 5 o 其塑性随温度的升高急剧增加 , C 而强度也快速降低 , 因此 旋压温度 一般选择在 3 0C 5 o以上 . 同时若温度过高 . 则金属强度太低 , 也容易 引起车轮轮辐处的变形且旋压时的金属流动不容易控制 . 因此 旋压成形温度一般控制在 30 4 0C 5 ℃一 0 q之间 22缺陷分析 _ 铝车轮热旋压是一个材料 塑性变形的复杂过程 , 于影响车轮安 对
系数 的 正 确 选取 、 具 结构 的合 理 设 计对 旋 压 成 形 工 艺至 关 重要 。 模
影响A356铝合金车轮旋压成形品质的因素分析
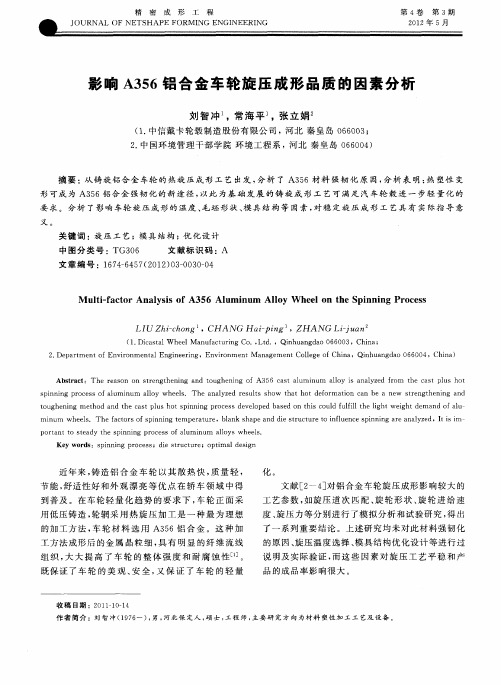
Ke y wor :s nn n o e s;d es r c ur ds pi i g pr c s i t u t e; o tm a e i p i ld sgn
近年来 , 造铝 合 金 车 轮 以其 散 热快 , 量 轻 , 铸 质 节能 , 舒适性 好 和外 观 漂亮 等 优 点在 轿 车 领 域 中得 到普及 。在车 轮轻 量化 趋 势 的要求 下 , 车轮 正 面采
化 。
文献 [ —4 对铝 合金 车轮旋 压成 形影 响较大 的 2 ]
工艺参 数 , 旋压 道 次 匹配 、 轮 形状 、 如 旋 旋轮 进 给 速 度 、 压力等 分别进 行 了模 拟 分析和试 验研 究 , 出 旋 得
了 一 系 列 重 要 结 论 。上 述 研 究 均 未 对 此 材 料 强 韧 化
Ab ta t The e s n on s r ng he i g n ou src : r a o te t n n a d t ghe i 3 c s l i um al y i a a y e fom t e a t pl nng ofA 56 a t aum n lo s n l z d r h c s us hot s nnig pr c s l i um loy whe l. The a a y e e uls s w ha pi n o e sofaum n al es n l z d r s t ho t thotdeor a i n c n b w te t nig an f m to a e a ne s r ng he n d
铝轮毂旋压成型工艺和设备的探究
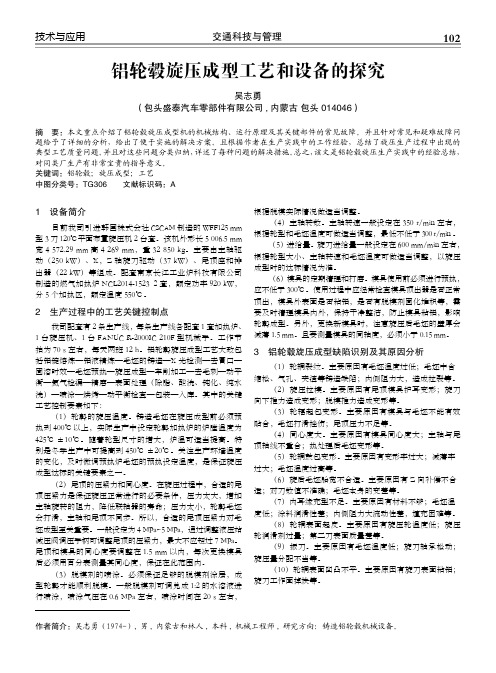
102交通科技与管理技术与应用1 设备简介 目前我司引进韩国株式会社CSCAM 制造的WFF125 mm型3刀120℃平面布置旋压机2台套。
该机外形长5 006.5 mm宽4 572.29 mm 高4 269 mm,重32 850 kg。
主要由主轴驱动(250 kW)、X,Z 轴旋刀驱动(37 kW)、尾顶座和排出器(22 kW)等组成。
配套南京长江工业炉科技有限公司制造的燃气加热炉NCL2014-15232套,额定功率920 kW,分5个加热区,额定温度550℃。
2 生产过程中的工艺关键控制点 我司配套有2条生产线,每条生产线各配套1套加热炉、1台旋压机、1台FANUC R-2000IC 210F 型机械手。
工作节拍为70 s 左右,每天两班12 h。
铝轮毂旋压成型工艺大致包括铝锭熔炼—铝液精炼—毛坯的铸造—X 光检测—去冒口—固溶时效—毛坯预热—旋压成型—车削加工—去毛刺—动平衡—氦气检漏—精磨—表面处理(除脂、酸洗、钝化、纯水洗)—喷涂—烘烤—动平衡检查—包装—入库。
其中的关键工艺控制要素如下: (1)轮毂的旋压温度。
铸造毛坯在旋压成型前必须预热到400℃以上,实际生产中设定轮毂加热炉的炉膛温度为425℃±10℃。
随着轮型尺寸的增大,炉温可适当提高。
特别是冬季生产中可提高到450℃±20℃。
关注生产环境温度的变化,及时微调预热炉毛坯的预热设定温度,是保证旋压成型达标的关键要素之一。
(2)尾顶的压紧力和同心度。
在旋压过程中,合适的尾顶压紧力是保证旋压正常进行的必要条件,压力太大,增加主轴旋转的阻力,降低联轴器的寿命;压力太小,轮毂毛坯会打滑,主轴和尾顶不同步。
所以,合适的尾顶压紧力对毛坯成型至关重要。
一般设定为4 MPa~5 MPa,通过调整液压站减压阀调压手柄可调整尾顶的压紧力,最大不应超过7 MPa。
尾顶和模具的同心度要调整在1.5 mm 以内,每次更换模具后必须用百分表测量其同心度,保证在此范围内。
轮毂旋压工艺标准
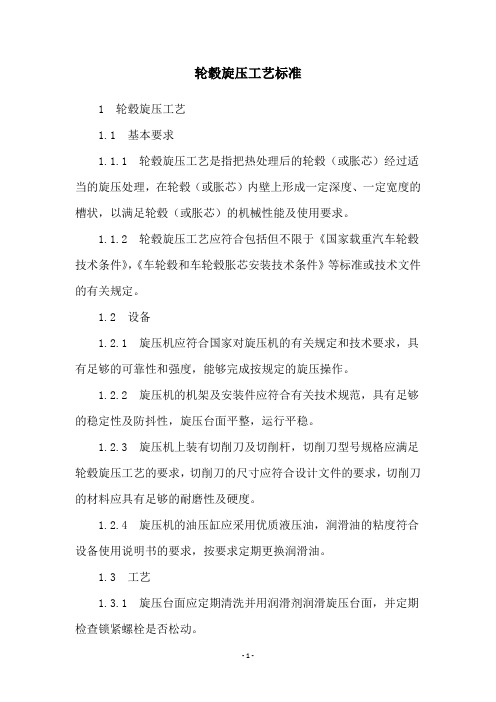
轮毂旋压工艺标准1 轮毂旋压工艺1.1 基本要求1.1.1 轮毂旋压工艺是指把热处理后的轮毂(或胀芯)经过适当的旋压处理,在轮毂(或胀芯)内壁上形成一定深度、一定宽度的槽状,以满足轮毂(或胀芯)的机械性能及使用要求。
1.1.2 轮毂旋压工艺应符合包括但不限于《国家载重汽车轮毂技术条件》,《车轮毂和车轮毂胀芯安装技术条件》等标准或技术文件的有关规定。
1.2 设备1.2.1 旋压机应符合国家对旋压机的有关规定和技术要求,具有足够的可靠性和强度,能够完成按规定的旋压操作。
1.2.2 旋压机的机架及安装件应符合有关技术规范,具有足够的稳定性及防抖性,旋压台面平整,运行平稳。
1.2.3 旋压机上装有切削刀及切削杆,切削刀型号规格应满足轮毂旋压工艺的要求,切削刀的尺寸应符合设计文件的要求,切削刀的材料应具有足够的耐磨性及硬度。
1.2.4 旋压机的油压缸应采用优质液压油,润滑油的粘度符合设备使用说明书的要求,按要求定期更换润滑油。
1.3 工艺1.3.1 旋压台面应定期清洗并用润滑剂润滑旋压台面,并定期检查锁紧螺栓是否松动。
1.3.2 旋压机上装有切削刀,切削刀应定期检查,磨刀定期调整,以保证切削刀锋利,达到规定的切削要求。
1.3.3 轮毂(或胀芯)应在清洁干燥的环境下,经过润滑处理,放入旋压台面,扳动锁紧螺栓,旋压机上切削刀应在轮毂(或胀芯)的中心点下切,并以外螺纹扳动紧固,当旋压压力达到规定值时,切削深度和宽度达到规定深度和宽度时,切削完成,拧松锁紧螺栓,取出轮毂(或胀芯),进行检查,满足要求可投入使用。
1.3.4 轮毂(或胀芯)在旋压过程中如出现异物或杂质,应及时清除,以免造成轮毂损坏。
1.4 检查1.4.1 检查旋压机是否符合设备使用说明书的要求,旋压台面平整、旋压铣刀锋利,油压缸液压油粘度符合设备使用说明书的要求,切削刀的尺寸及材料是否符合设计要求。
1.4.2 检查轮毂(或胀芯)是否符合有关技术标准和技术文件的要求,轮毂(或胀芯)内壁的槽状是否满足规定的深度及宽度,轮毂(或胀芯)外形尺寸是否符合规定。
铸旋铝合金轮毂旋压模具设计及压料方式研究
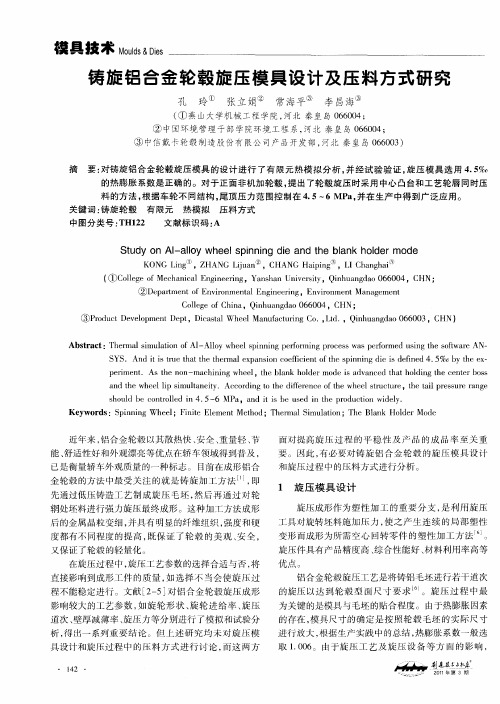
S u y o — l y wh e pn ig de a d t e ba k h le d t d n AIa l e l inn i n h ln od rmo e o s
K N ig Z N i a ②,C A G Ha ig O G Ln , HA G Lj n u H N i n ⑧,L h n hi p I ag a。 C ( ol eo ca i l n ier g Y nh nU iesy i u n do0 6 0 C N; ①C l g f e Meh nc gn e n , asa nvri ,Qn ag a 6 0 4, H aE i t h
De at n fEn io me tlEn i e rn p rme to vr n n a g n e i g, En io m e tM a a e n vr n n n g me t
C l g f hn ,Qn u nd o0 6 0 C o eeo ia ih a g a 6 0 4, HN; l C
和 旋压过 程 中的压 料方式 进行 分析 。
金轮毂 的方 法 中最受 关 注 的就 是 铸旋 加 工 方 法 J 即 , 先通 过低压 铸造 工艺 制 成 旋 压 毛坯 , 后 再 通过 对 轮 然
1 旋 压 模 具 设 计
旋压 成形作 为 塑性 加 工 的 重要 分 支 , 利 用旋 压 是 工 具对旋 转坯 料施 加 压力 , 之 产 生 连续 的局 部 塑性 使
模 具 技 术 Ml D os i u &e d s
铸 旋 铝合 金 轮 毂 旋压 模 具 设 计 及压 料 方 式 研究
孔
( 燕 山大学机 械工 程 学院 , 北 秦 皇 岛 0 6 0 ① 河 6 0 4; ( 中国环 境 管理干部 学院环境 工程 系 , 河北 秦 皇 岛 0 6 0 6 0 4;
旋轮转速对变截面钢车轮旋压成形影响分析

据 。 典 型 的 无 内胎 载 重 汽 车 钢 车 轮 ( 1 的 轮 辋 截 图 ) 面 形 状 及 其 尺 寸 如 图 2所 示 。 工 艺 结 构 特 点 : 面 其 截
良好 。
图 1 无 内 胎 钢 车轮
特 点 , 而旋 压 因
时 旋 轮 单 向 进
给 无 法 满 足 其
成 形 要 求 , 须 必
采 用 旋 轮 双 向
1 . 轮辐 2轮辋 . 3焊缝 .
大, 仅强 力旋 压机 和滚 型机 , 辱 单
格 就 超 过 10万 欧 5
5o 0
钢 制汽车 车轮
成 形 一 滚 压 凸 缘一 冲 制 气 门 孔一 与 轮 辐 组 焊 。 中旋 压 成 形 为 主 要 成 形 工 序 , 制 件 的 形 状 尺 寸 和 使 用 性 能 其 对
起 决 定 性 作 用 。 旋 压 技 术 为 变 截 面 钢 车 轮 的 生 产 和 使 用 提 供 了可 靠 的工 艺 保 障 。 关 键 词 f 械 制造 ; 压 成 形 ; 速 ; 截 面 钢 车 轮 机 旋 转 变 中 图 分 类 号 : 3 51 TG 3 .9 文 献 标 识 码 : B
异 性 、 口径 大 、 轴 向高 度 长 、 环
壁 薄 。由 于 变 截
面 无 焊 车 轮 具 有 中 间 直径 小 , 两 端 直 径 大 的
GI ANE I 荷 兰 RONT — NE等 车 轮 公 司 在 生 产 。 T I和 IJ 车轮 通常 是通 过卷 圆 、 接 、 整 等 工序 加 工而 成 , 焊 扩 工艺效率 高 , 精度低 , 达 不到等 强度要 求 。随后 但 且 德 国 L I O、 班 牙 DE EC 西 NN 等 公 司 田 出 了 ~ 种 适 推 应 大 批 量 生 产 的 旋 压一 滚 形 工 艺 ,其 方 法 是 用 无 缝 钢管下料 , 用 强力旋 压机 旋压成 不等截 面 中间坯 , 再 然后用 滚型机 滚成 轮辋 , 后与轮 辐焊成 轮毂 。 种 最 这 方 法 制 造 的 车 轮 , 由 于 轮 辋 没 有 焊 缝 ,在 使 用 过 程 中 不 会 漏 气 ,安 全 可 靠 。但 设 备 投 资 巨
先进的铝合金轮毂旋压成形技术
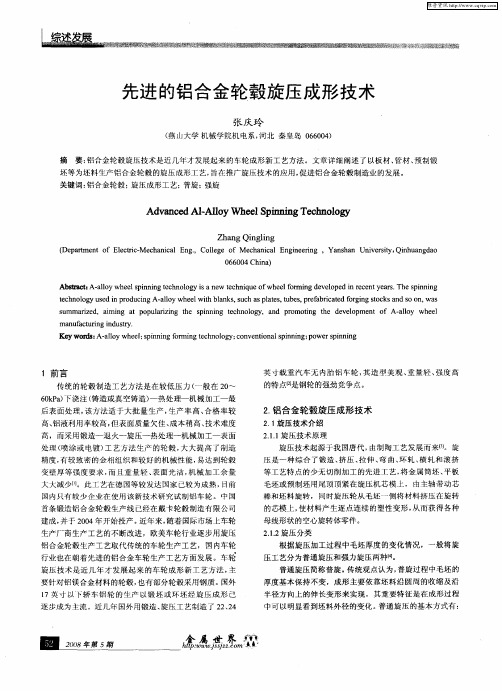
1前言
传统的轮毂制造工艺方法是在较低压力 ( 一般在 2 ~ 0 6k a 下浇注 ( 0P) 铸造或真空铸造) 一热 处理一机械加工一最 后表面处理 , 该方法适于大批 量生产 , 生产率高 、 合格率较
高 、 液 利 用 率 较 高 , 表 面 质 量 欠 佳 、 本 稍 高 、 术 难 度 铝 但 成 技 高 ,而 采 用 锻造 一 退 火 一 旋 压一 热 处 理一 机 械 加 工 一 表 面
首 条 锻造 铝合 金 轮 毂 生 产 线 已经 在 戴 卡轮 毂 制 造 有 限公 司 建 成 , 于 20 并 0 4年 开始 投 产 。 年 来 , 近 随着 国际 市场 上 车 轮
的芯模上 , 使材料产 生逐 点连续 的塑性变形 , 从而获得各种
母 线 形 状 的 空心 旋 转 体 零 件 。 21 .2旋 压 分 类 .
Ad a c dA1 o e l pn i gTe h oo y vne - AU yWh e inn c n lg S
Z ag n l g h n gi Qi n
( eat n fEetc c ai lE g,C lg fMeh nclE g er g ,Y nhn U i ri , n un do D pr meto l r — hnc n . ol e o c ai n i e n c i Me a e a n i a sa nv sy Qi a ga e t h 0 6 0 hn) 60 4C ia
Ke ywo d : aly wh e : pn i g f r n c n lg c n e t n l p n i g p we in n r s A- l e ls i n n mig t h o o y: o v n i a i nn : o r p n i g o o e o s s
铝车轮旋压水冷工艺研究
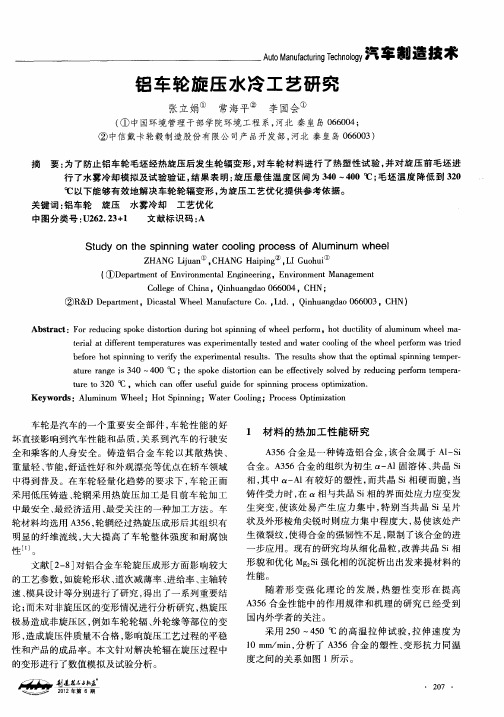
一
采用 低压 铸造 、 辋 采用 热 旋 压 加 工 是 目前 车 轮 加 工 轮
车 轮是 汽 车的一 个 重 要 安 全 部 件 , 车轮 性 能 的好
坏直 接影 响 到汽 车性 能 和 品质 , 系到 汽 车 的行 驶 安 关
1 材 料 的 热 加 工 性 能 研 究
A5 3 6合 金是 一 种 铸造 铝 合 金 , 合金 属 于 A — i 该 ls
全和 乘 客 的人 身 安 全 。铸 造 铝 合 金 车 轮 以其 散 热快 、 重量 轻 、 节能 , 舒适 性 好 和外 观漂亮 等优 点 在轿 车领 域
a u e r n e i 3 0 ~ 0 ℃ ;t e s o e d s r o a e ef ci ey s le y r d c n e fr t mp r — t r a g s 4 4 0 h p k itt n c n b f t l ov d b e u i g p rom o i e v e e a
beo e h ts n ng t e f he e p rme tlr s ls f r o pini o v r y t x e i i n a e u t .Ther s lss o t tt e o tma p n i g tmp r e u t h w ha h p i ls i n n e e —
t r o 3 0 ℃ ,wh c a fe s f lg d o p n i g p o e so tmiai n. u e t 2 i h c n ofr u eu ui e f rs i n n r c s p i z to Ke wor s:Almi u W he l y d u n m e ;Ho pi i g;W ae oi g;P o e sOp i z to tS nn n t rCo ln r c s tmiai n
铸旋铝合金车轮旋压模具的优化设计

铸旋铝合金车轮旋压模具的优化设计徐世文;张立娟;常海平;李华友【摘要】目的保证铸旋车轮短流程制造工艺的实现,提高旋压模具与同一轮型不同铸造毛坯的配合能力,防止因旋压后毛坯尺寸变化过大,造成车轮机加成品率下降的现象.方法以某款车轮旋压模具为研究对象,对其旋压模具结构进行重新设计,增加定位滑块、垫板等设计,提高毛坯与模具的定位与配合,增强模具对毛坯的自适应性.结果对改进后的旋压模具进行试验验证,新结构的旋压模具能够满足不同铸造毛坯的旋压,且控制上模压力在4.5 MPa内,毛坯尺寸合格,性能无影响.结论该旋压模具设计的方法已经应用到了其他铸旋车轮的设计中.【期刊名称】《精密成形工程》【年(卷),期】2018(010)002【总页数】4页(P122-125)【关键词】铸旋车轮;旋压模具;设计【作者】徐世文;张立娟;常海平;李华友【作者单位】中信戴卡股份有限公司工程技术研究院,河北秦皇岛 066011;河北环境工程学院环境工程系,河北秦皇岛 066000;中信戴卡股份有限公司工程技术研究院,河北秦皇岛 066011;中信戴卡股份有限公司工程技术研究院,河北秦皇岛066011【正文语种】中文【中图分类】TG315.2铸造+旋压铝合金车轮(简称“铸旋车轮”)的内部组织均匀、流线成纤维状,其性能大大高于低压铸造车轮,能够满足车轮市场大直径、高强度、轻量化的发展趋势,已在轿车中得到应用[1]。
为了节省制造成本、缩短制造流程,目前铸旋工艺的应用已经取消了预机加工,毛坯与旋压模具的配合主要采用了铸造封层定位[2]。
为了生产节拍的匹配,一般是多套铸造模具毛坯匹配一台旋压模具。
由于铸造模具的制造精度及车轮生产过程中产生的磨损,会造成铸造毛坯的定位内径出现偏差,尺寸变化不完全一致,同时,旋压模具在生产过程中也会出现磨损,造成同款轮型不同铸造模具的毛坯与旋压模具的配合、定位不精确,使得旋压后的毛坯出现变形和尺寸变化不一致,造成了机加工序的废品,直接影响了铸旋产品的成品率。
皮带轮旋压工艺

皮带轮旋压工艺引言:皮带轮是一种常见的机械传动装置,广泛应用于各类机械设备中。
而皮带轮的制作则需要经过一系列的工艺过程,其中皮带轮旋压工艺是一种常用的制造方法。
本文将介绍皮带轮旋压工艺的原理、步骤和应用。
一、皮带轮旋压工艺的原理皮带轮旋压工艺是通过旋转式机械设备,将金属板材进行冷加工的一种方法。
其原理是将金属板材置于旋转的模具中,通过模具的挤压和冲击作用,使金属板材逐渐变形成皮带轮的形状。
旋压工艺具有高效、精确、经济的特点,能够满足皮带轮的各种要求。
二、皮带轮旋压工艺的步骤1. 材料准备:选择适合的金属板材,根据皮带轮的要求进行尺寸裁剪和表面处理,以确保后续工艺的顺利进行。
2. 模具设计:根据皮带轮的设计要求,设计制作适合的旋压模具。
模具应具备良好的刚性和耐磨性,以保证旋压过程中的精度和质量。
3. 机器调试:将模具安装在旋压机上,根据材料的性质和要求调整旋压机的参数,包括旋压速度、旋压力度等。
4. 旋压操作:将金属板材放置在模具中,并启动旋压机。
旋压机开始旋转,同时施加压力,使金属板材逐渐变形成皮带轮的形状。
旋压过程中需要注意控制旋压力度和速度,以避免过度变形或损坏。
5. 检验和修整:旋压完成后,对制作的皮带轮进行检验。
检查皮带轮的尺寸、形状和表面质量是否符合要求。
如有不合格的地方,需要进行修整或重新制作。
三、皮带轮旋压工艺的应用皮带轮旋压工艺广泛应用于各种机械设备中,如汽车、工程机械、农机等。
它能够制作出各种不同尺寸和形状的皮带轮,满足不同机械设备的传动需求。
旋压工艺制作的皮带轮具有高精度、高强度和稳定性好的特点,能够确保机械设备的正常运行。
结论:皮带轮旋压工艺是一种常用的制造方法,能够高效、精确地制作出各种尺寸和形状的皮带轮。
通过合理的工艺步骤和严格的质量控制,可以获得符合要求的皮带轮产品。
随着科技的进步和制造技术的不断发展,皮带轮旋压工艺将进一步完善和应用于更多领域,为机械设备的传动效果提供更好的支持。
铝合金轮毂强力旋压的研究
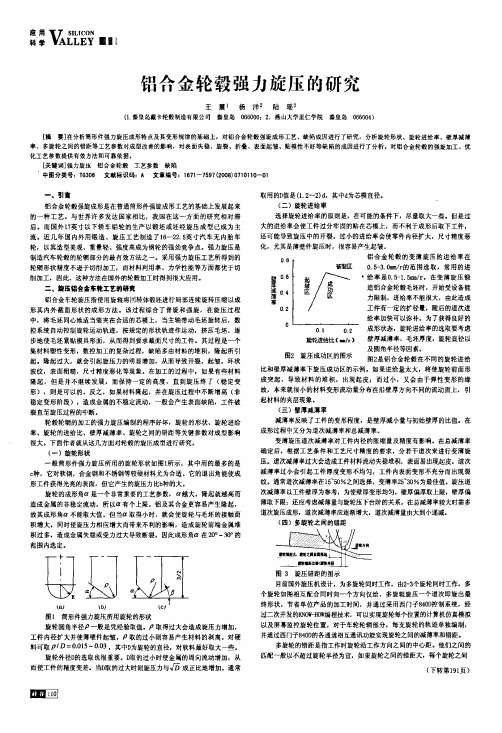
应用科学SI LI C o NL L E Y露鬟2铝合金轮毂强力旋压的研究王震1杨洋2陆瑶2(1.秦皇岛戴卡轮毂制造有限公司秦皇岛066000;2.燕山大学里仁学院秦皇岛066004)【摘要]在分析筒形件强力旋压成形特点及其变形规律的基础上,对铝合金轮毂强旋成形工艺、缺陷成因进行了研究。
分析旋轮形状、旋轮进给率、壁厚减薄率、多旋轮之间的错距等工艺参数对成型改善的影响,对表面失稳、旋裂、折叠、表面起皱、贴模性不好等缺陷的成因进行了分析。
对铝合金轮毂的强旋加工、优化工艺参数提供有效方法和可靠依据。
[关键词]强力旋压铝合金轮毅工艺参数缺陷’中图分类号:T G306文献标识码:^文章编号:167卜一7597(2008)0710110一01一、引曹铝合金轮毂强旋成形是在普通筒形件强旋成形工艺的基础上发展起来的一种工艺。
与世界许多发达国家相比,我国在这一方面的研究相对滞后。
而国外17英寸以下轿车铝轮的生产以锻坯或坯经旋压成型已成为主流。
近几年国内外用锻造、旋压工艺制造了16—22.5英寸汽车无内胎车轮,以其造型美观、重量轻、强度高成为钢轮的强劲竞争点。
强力旋压是制造汽车轮毂的轮辋部分的最有效方法之一。
采用强力旋压工艺所得到的轮辋形状精度不逊于切削加工,而材料利用率、力学性能等方面都优于切削加工。
因此,这种方法在国外的轮毂加工时得到很大应用。
=、旋压铝合盒车轮工艺的研究铝合金车轮旋压指使用旋辊将回转体锻坯进行局部连续旋转压缩以成形其内外截面形状的成形方法。
该过程综合了普旋和强旋,在旋压过程中,将毛坯同心地适当装夹在合适的芯模上。
当主轴带动毛坯旋转后,数控系统自动控制旋轮运动轨迹,按规定的形状轨迹作运动,挤压毛坯,逐步地使毛坯紧贴模具形面,从而得到要求截面尺寸的工件。
其过程是一个集材料塑性变形,数控加工的复杂过程,缺陷多由材料的堆积,隆起所引起。
隆起过大,就会引起旋压力的明显增加,从而导致开裂,起皱。
环状波纹,表面粗糙,尺寸精度恶化等现象。
旋压技术在轮毂加工中的应用

1旋压成形技术应用在轮毂生产 中工艺特点 ( 4 ) 金属材料 的热处理也是旋压工艺 中主要的因素 , 在旋压过程 传统的轮毂生产工艺 由于表 面质量不高 以及成本费用 、技术难 中由于受到强大 的压 、 拉应力 , 致使材料硬化严重 , 必须采取热处理 度都 高等因素 , 造成在 实际生产工作 中存在相 当严重 的问题 , 整体影 手段加 以软化 ,为了改变终极工件 的机械性能也需要进行必要的热 响汽车制造企业 的可持续发展 。 为 了解决这一问题 , 并且满足现代化 处 理 。 社会发展需求 , 各 大汽车制造企业纷纷采用旋压技术 , 整体提升轮毂 2 . 2旋压技术原理 旋压技术起源于我国唐代 , 由制 陶工艺发展而来 。旋压是一种综 制造工作效率 , 在一定 的工艺技术下生产符合标准的产物 。 如下对旋 压成形技术在轮毂生产工艺中应用特点进行详细介绍 : 合了锻造 、 挤压 、 拉伸 、 弯曲、 环轧 、 横轧 和滚挤等工艺特点 的少无切 将金属筒坯 、 平板毛坯或预制坯用尾顶顶紧在旋 ( 1 ) 对于旋压技术而言 , 在进行轮毂生产环 节时 , 旋压设备 中旋 削加工 的先进工艺 , 轮对坯料采用 的是逐点旋压 , 不 同于传统 的制造生产手法 , 这样能够 压机芯模上 , 由主轴带动芯棒和坯料旋转 , 同时旋压轮从毛坯一侧将 减小接触面积 , 单位压力能够达到常规技术的几倍之多。同时对于部 材料挤压在旋转 的芯模上 , 使材料产生逐点连续 的塑性变形 , 从而获 分难 于加工 的材料 ,这种生产技术 同样能够保障总变形力 的最小化 得各种母线形状的空心旋转体零件。 2 . 3 旋压分类 模式 , 整体降低功率的消耗 。 ( 2 ) 在进行轮毂生产过程中 , 一般坯料的金属 晶粒会在三向变形 根据旋压加工过程 中毛坯厚度 的变化情况 , 一般将旋压工艺分为 普旋 力 的作用下 , 整体材料沿着变形 区滑移面进行错位移动 , 这样能够保 普通旋压和强力旋压两种。普通旋压简称普旋 。传统观点认为 , 障滑移面各滑移层的方向与变形方 向一致 ,从而实现金属纤维连续 过程中毛坯的厚度基本保持不变 ,成形主要依靠坯料沿 圆周的收缩 性和完整性。同时通过运用旋压技术生产轮毂 , 由于金属晶格结构应 及沿半径方 向上 的伸长变形来实现 ,其重要特征是在成形过程中可 以明显看到坯料外径 的变化。 普通旋压的基本方式有 : 强力旋压简称 变快速化 , 提升了旋压制品的强度 、 硬度 、 抗拉强度以及屈服极限。 为强旋。强旋工艺主要依靠坯料厚度的减薄来实现成形 , 坯料外径基 ( 3 ) 传统 的轮毂制造方法最 大的问题就是成品表面质量不高 , 严 重影响整体外观。对于旋压技术而言 , 在强大 的旋压压力下 , 使 制品 本保持不变 。 在进行强力旋压 时, 旋轮加于坯料上的压力要 比普通旋 坯料的变形情况和普通旋压时也不大相同。 在普旋过程 达到 了较高的尺寸精度 和表面光泽度。同时由于旋压技术的工艺生 压 时大得多 , 产压力过大 , 也会起到平整和压延的效果 , 整体提升轮毂的外在观赏 中 , 坯料厚度变化不大但直径变化很大 , 由大变小 或由小变大 , 而在 强旋过程中, 坯料直径基本保持不变 , 但厚度变化很大 , 由厚变薄 。因 度。 ( 4 ) 在进行旋压技术应用过程 中 , 其中铸造旋压铝合金车轮一般 此强力旋压又称为变薄旋压 。 由于技术 自身特点 , 能够有效地降低 轮毂本身结构上的重量 , 这样不 2 . 4旋压工艺在预制锻坯铝合金轮毂生产中的应用 仅能够减少一定的原材料投入 , 同时还能整体提升汽车的驾驶性能 , 预制锻坯铝合金轮毂生产 的第一步工序是制坯 , 制坯工序并不仅 仅是简单的镦粗 , 而较多 的方式是用旋锻机把 圆柱棒料碾压成饼状 , 保障最优化模式的形成。 ( 5 ) 铸造旋压铝合金车轮具有显著的价格优势。目前而言旋压技 预制坯的形状对后续的旋压成形会有很大 的影响。预制锻坯铝合金 术 已经逐渐被汽车制造 厂商所广泛应用 ,这种技术一定程度上节省 轮毂生产可 以采用普旋和强旋两种工艺。 f 】 ) 预制锻坯强力旋压整体车轮。锻造毛坯通过强旋工艺 , 轮毂重 了制造成本费用 , 降低 了原材料以及相关零件资金量的投入 , 从 而能 够 以较低的价格进行市场竞争 ,这样推动了轮毂 的市场竞争综合实 量可减轻大约 2 5 %, 这是 因为该工艺不仅允许变截面厚度 , 而且 实现 力。 了更高的材料致密性, 这样就可 以增强机械性能 。 所有这些优点可将 . 0 a r m一 6 . 0 m m减薄至 2 . 7 — 3 . 0 m m( J  ̄ . 旋轮毂) 。并且 , 该工 ( 6 ) 部分汽车制造技术对于坯料来源这个 问题 , 就各 自有各 自的 工件厚度从 4 生产工艺要求 , 这样就无形 中增加了生产难度。旋压技术坯料来 源一 艺可保持轮毂辐部 的形状和设计如 同标准的铸造轮毂。 般较为广泛 ,无论是纯质材料还是合金 材料都能够进行相应的生产 f 2 1 预制锻坯劈开旋压整体车轮。 与前面讲到的以厚板为坯料 的劈 加工 , 通过旋压技术保障汽车轮毂制造的高效性。 开式车轮生产工艺相同 , 只是这里的坯料不是板料而是预制锻坯。 结 束 语 2旋压技术在轮毂生产 中应用 伴随我国社会不断 陕速发展 , 促使人们生活质量的提升 , 为 了能 2 . 1 旋压技术工艺要素 ( 1 )普通旋压 主要是改变毛坯的外形 ,而壁厚改变很小或不改 够方便 出行车辆购买量将会大大增加。为了满足现代社会发展需求 , 变, 其毛坯外形及尺寸的设计计算是关键技术。其工艺要素为旋压轮 实现汽车制造企业的可持续快速高效发展 , 加强新型生产技术 的投
旋压技术在轮毂加工中的应用探讨

1 旋压技术在轮毂加工中的应用原理及其重要性 1.1 旋压技术的应用原理
随着工业水平的不断提高,旋压技术在轮毂加工中得到 了广泛的应用。从旋压技术的本质来说,它就是一种变形技 术,通过这项技术中的特殊手段,使得金属得到想要的形状。 从旋压技术的基本原理来看,旋压技术和我国古代时候的制 陶技术相类似,但是相对于制陶技术,旋压技术有其先进性。 旋压技术的所施力的对象为旋压毛坯,主要是厚壁桶形或是 圆形,通过旋压机的相互作用,完成旋压技术的整个工艺。 对于旋压机来说,在旋压机的结构中最为重要的一部分是存 在轴向运动的旋轮架,而固定在旋轮架中的旋轮可以根据旋 压机进行径向运动 [1]。在这个结构中,旋压毛坯主要在旋轮 架中,通过和旋轮架的方向运动所产生的力进行运动,从而 达到旋压的目的。除此之外,旋轮架主要是通过轴向运动以 及径向运动所产生的力的共同作用,从而使得旋压毛坯在力 的作用下进行连续性地变形。这就是旋压技术的基本原理。
随 着 我 国 制 造 业 水 平 的 不 断 提 高,在 轮 毂 加 工 的 过 程 中,对其工艺也有着更高的要求,相对于普通的轮毂加工来 说,不仅需要外形美观,更需要的是达到高硬度、高强度的 要求 [3]。在轮毂加工的过程中,旋压技术一方面可以根据加 工时的实际要求去进行自动的转换,另一方面旋压技术可以 对一些较为复杂的工件进行加工。
关键词 :旋压技术 ;轮毂加工 ;应用
中图分类号 :TG306
文献标识码 :A
文章编号 :1002-5065(2019)04-0229-2
Application of Spinning Technology in Hub Processping
(Zhejiang Wanfeng Aowei Steam Turbine Co., Ltd.,Shaoxing 312500,China)
旋压轮毂和锻造轮毂有什么区别

旋压轮毂和锻造轮毂有什么区别
旋压轮毂和锻造轮毂之间的区别主要在于成本、外观、性能三方面。
成本方面来说,旋压轮毂技术相对简略,适宜批量生产且成本较低,锻造轮毂技术复杂,成本较高但性能非常好。
两者的外观很难区别,但在金属特性上有较大的不同,锻造轮毂的耐疲劳性、抗冲击力和强度相对旋压轮毂更好,质量上旋压轮毂普遍要比锻造轮毂重20%左右。
一、轮毂旋压好还是锻造好
这要看是哪种旋压轮毂,在性能方面上旋压轮毂肯定是比不上锻造的,但如果是用冷轧板或锻造毛胚制造的旋压轮毂,那性能就跟锻造轮毂接近了。
并且这种轮毂使用的原材料比锻造轮毂少,所以从成本和价格方面来说更加实惠一些。
二、挑选轮毂的方法
1、不要盲目加大轮毂。
有人为了改善汽车性能而加大轮毂,在轮胎外径不改变的情况下,大轮毂需要配合宽而扁的轮胎,车的横向摆动小了,稳定性因此得到提升。
但扁小的轮胎,其厚度也越薄,在减震性能和舒适方面就会变得很差。
2、不要只挑选自己喜欢外形的轮毂,要听从专业人员的建议来选择合适三距的轮毂。
3、尽量选择铝合金材质的轮毂,与过去的铁铸轮毂相比,铝合金轮毂的抗变形能力有了很大提高,重量大幅度减轻,车动力损失小,跑起来快,省油而且散热性好。
另外,选择轮毂也要尽量挑选结构简约的,因为结构复杂的轮毂可能在洗车的时候会被多收费或者拒洗。
(声明:图文均转载自网络,若有来源标注错误或侵犯了您的合法权益,请作者持权属证明与小万联系,我们将及时更正、删除,谢谢。
)。
- 1、下载文档前请自行甄别文档内容的完整性,平台不提供额外的编辑、内容补充、找答案等附加服务。
- 2、"仅部分预览"的文档,不可在线预览部分如存在完整性等问题,可反馈申请退款(可完整预览的文档不适用该条件!)。
- 3、如文档侵犯您的权益,请联系客服反馈,我们会尽快为您处理(人工客服工作时间:9:00-18:30)。
铝合金轮毂旋压成型工艺研究
摘要:本文通过对6061铝合金旋压变形性能的分析,主要论述对称式碟形轮毂旋压工艺方案的实施过程及效果。
关键词:铝合金;轮毂旋压;工艺研究
1 前言
铝合金轮毂有重量轻、成本低、强度高的优点,而且铝有较强的导热性能,可大大延长汽车、摩托车轮胎使用寿命,特别是高负载卡车轮胎的寿命。
(根据欧洲车轮生产商“ALCOA”公司测试数据,铝合金轮毂使轮胎最长可延长20%的使用寿命)。
2课题的提出
近年来,随着国际市场上车轮生产厂商生产工艺的不断改进,欧美车轮行业逐步用强旋铝合金轮毂取代传统的车轮生产工艺,国内车轮行业也在朝着先进的铝合金车轮生产工艺方面发展。
下面是某厂商需要订做的典型车轮轮毂(图1)。
轮毂材料为6061合金铝,(相当于国内牌号LD30)。
3 轮毂旋压加工设备
PT30501CNC双轮卧式强力旋压机,旋压加工工件的直径范围φ100~φ1000mm,旋轮纵向行程1900mm,最大旋压力30吨。
这些机床参数说明该台旋压机满足轮毂强力旋压工艺要求。
4 铝合金轮毂旋压工艺方案
4.1 轮毂材料6061合金铝的旋压性能分析
6061铝合金属于Cu-Mg-Si-Mn系铝基合金,其化学成份如下:
Cu-0.15%~0.4%,Mg-0.45%~0.9%,Si-0.4%~0.8%,Mn-0.15%;该种材料在固溶时效状态下的机械性能指标为:
σb≥320Mpa,δ5≥12%,ψb≥25%,HB≥120。
因此,6061合金铝在固溶时效状态下的可旋性指标值——单道次极限减薄率为:
φmax=ψb/(0.17+ψb)×100%=0.25/(0.17+0.25)×100%=60%。
这个指标值说明它的可旋性比高强度钢的可旋性要差一些,旋压工艺中,必要时应适当加热,工件加热温度310℃~350℃。
另外,为提高铝合金的可旋性,可适当加入一些矿物元素——锑和锶(0.02%)。
4.2轮毂旋压工艺方案的选择
像这种对称式碟形轮毂,旋压工艺方式一般可采用取板材劈开式旋压或用铸(锻)件毛坯进行强力旋压成型两种工艺方式。
劈开式旋压工艺是将圆盘状板坯用劈开轮通过分层工艺,使毛坯在中部被劈成两个等分,之后,再用成型轮渐进普旋成型即可;强旋工艺是将铸铝毛坯或锻造毛坯进行若干道次的强旋成型工艺,旋压达到轮毂型面尺寸要求,强旋工艺生产出来的轮毂重量比锻造轮毂重量可减轻大约25%,这是因为强旋工艺可旋制出变截面厚度,在满足车轮强度指标要求的前提下,可适当减薄轮毂厚度。
由于我厂的PT30501CNC机床纵横向滚珠丝杠成75°夹角,当旋轮编程轨迹只沿工件径向移动时,机床实际运动过程中旋轮在轴向有分位移,使得旋压加工过程中劈开轮外缘端面受到一定的轴向压力,它的反作用力直接作用于机床滚珠丝杠传动部分,影响机床使用寿命及精度,因此,这种结构形式不利于轮毂劈开式旋压。
根据以上分析,我们选择强力旋压工艺来成型这种对称式碟形铝轮毂。
4.3 轮毂强旋工艺路线
精密锻造毛坯第一道次强旋第二道次强
旋成型转数控车间机加成轮毂成品。
5.工艺方案实施过程
5.1工装设计
旋压芯模材料选用,型面光洁度Ra0.4~Ra0.8um;成型旋轮预成型角°,圆角半径mm,材料选用,热处理硬度。
5.2旋压毛坯设计
用实体造型软件(Solidworks,MastCAM等)绘制轮毂旋压件实体造型,并求其金属体积。
依据体积不变性设计计算模锻件旋压毛坯。
5.3 强旋工艺实施效果
第一道次旋压工艺参数:S=0r/min,进给比F=0mm/r,第二道次强旋工艺参数:S=0r/min,F=0mm/r。
工艺试验初期,用R15成型轮进行两道次强旋成型,试验过程中产生堆积起皮,拉裂缺陷。
随后,将Rmm轮改为R成型轮,并且增大了旋压芯模上过渡圆角半径,起皮、拉裂缺陷得到了消除。
我们认为这种堆积、起皮缺陷主要是由于旋压轮成型圆角半径偏小且无预成型角,旋压成形时,金属受力面积较小,部分金属无法参与变形,加之工件型面复杂,材料变形时流动不畅;坯料底部Rmm圆弧破裂主要是由于旋压毛坯和模胎在该处的圆角半径Rmm太小,导致变形过程中应力集中较为严重,并且该处材料变形率最大,达到65%左右,
已经超过了6061铝合金(LD30)的旋压极限减薄率60%,致使加工硬化现象严重。
上述试验分析表明最初的旋压毛坯,旋压模胎存在一定的设计问题。
旋压毛坯应在满足工件金属体积要求的前提条件下,适当减小旋压成型部位的金属厚度(也就是在保证金属体积不变的前提下增大坯料高度,减小坯料外径),以此降低旋压减薄率,减小旋压加工硬化问题;旋压模胎型面上过渡圆角半径普遍偏小,且加工的型面光洁度未达到设计要求的Ra0.8mm。
根据前面旋压工艺试验的结果和质量分析,我们对后面试验件的旋压工艺方案做出了适当调整,变三道次为二道次旋压,成型旋轮均用Rmm。
堆积、起皮缺陷基本上得到了解决,但工件大端内外型面均出现了撕裂现象。
我们认为,该现象出现是由于该部位材料在两道次旋压过程中均是处于不完全贴模的普旋成型,金属之所以能够向前延伸,是
由于旋轮带着坯料表层金属向前移动,材料内部就产生了拉应力,而不是承受压应力状态。
针对工件撕裂问题,我们将旋轮预成型角由°改为°,旋压毛坯外径由φ427mm改为φ421mm,依此来减小旋压变形区域材料厚度,降低道次减薄率。
还对旋压轮的运动轨迹作了修正,使材料流动更为通畅,工件破裂问题得到了解决。
将轮毂旋压件进行固溶时效热处理,保证得到形状和尺寸较为稳定铝合金轮毂产品,同时提高轮毂的机械性能。
6.结论
利用强旋工艺方案在PT30501CNC双轮卧式强力旋压机上旋制6061铝合金轮毂是切实可行的,但是,必须设计制造出合理的旋压芯模和旋轮,并选取合理的旋压工艺参数,才能解决轮毂旋压过程中出现的堆积、起皮和破裂等缺陷。