鄂钢新1号高炉炉体工艺设计
某钢铁厂1号高炉大修施工方案设计方案

X X X X钢铁股份有限公司铁厂1号高炉大修施工设计批准: XX审核: XXX编制: XXXXXXXX钢铁集团建设有限责任公司二00九年元月三日目录1.概述2.工程大修方针、工程管理目标及承诺3. 高炉大修主要施工方法4. 安全保证体措施5.文明施工<含治安保卫、消防、环保、防汛、成品保护)6. 质量保证措施7. 确保工期的技术措施<施工网络计划)一、概述1.1编制依据1)XXXX钢铁股份有限公司铁厂1号高炉大修工程工程施工招标技术文件2)国家、地方现行有关施工、质量的技术标准;3)XXXX钢铁股份有限公司有限公司工程施工管理的相关文件和制度;4)合钢建设公司企业内部管理标准;5)本公司以往承担类似工程的建设经验。
1.2编制原则(1)积极响应招标文件的规定,确保工期、质量、安全目标的实现;(2)在总体部署和资源配置上尽量做到科学、优化、充沛;(3)在具体施工方案上尽量做到先进、合理,编制上突出重点;(4)为工程着想,积极向业主提出合理化建议。
1.3 工程简况及特点工程名称:XXXX钢铁股份有限公司铁厂1号高炉大修工程工程地点:XXXX钢铁股份有限公司工程类型:冶金大修工程1.3.1工程简介XXXX钢铁股份有限公司铁厂1号高炉大修工程主要工作为:1. 炉顶系统(含固定受料斗、布料器、小钟部分、大钟部分、炉顶法兰、探尺系统、炉顶润滑系统、均压系统、高炉各平台>。
2. 高炉本体、炉前(看水系统、高炉本体及炉前>;3. 筑炉部分 <高炉本体、热风炉、热风管道)。
b5E2RGbCAP1.3.3 工期要求:XXXX钢铁股份有限公司铁厂1号高炉大修工程工期:26天。
二、工程大修方针、工程管理目标及承诺2.1 工程大修方针在本工程的工程大修过程中,我们本着服务于长江钢铁,一切为业主着想的指导思想,以建设公司牵头,集中全公司的资源,组织高效、务实的工程班子,以雄厚的技术力量、优良的技术装备、先进的施工工艺、苛求认真的工作态度和严格科学的管理来实施本工程的施工。
高炉炼铁工艺设计规范
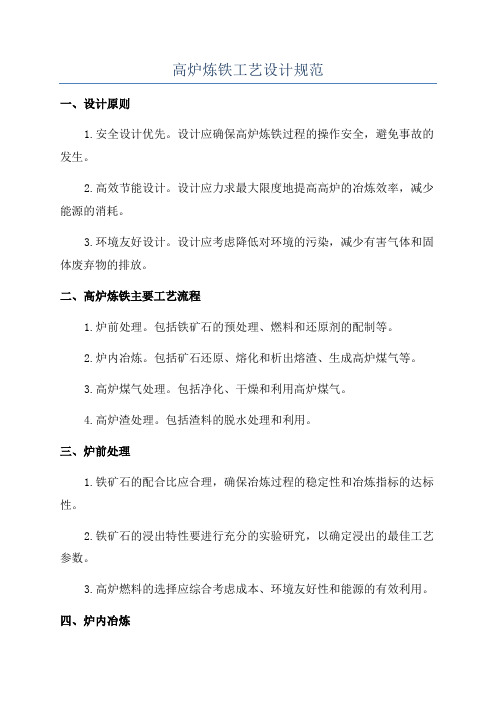
高炉炼铁工艺设计规范一、设计原则1.安全设计优先。
设计应确保高炉炼铁过程的操作安全,避免事故的发生。
2.高效节能设计。
设计应力求最大限度地提高高炉的冶炼效率,减少能源的消耗。
3.环境友好设计。
设计应考虑降低对环境的污染,减少有害气体和固体废弃物的排放。
二、高炉炼铁主要工艺流程1.炉前处理。
包括铁矿石的预处理、燃料和还原剂的配制等。
2.炉内冶炼。
包括矿石还原、熔化和析出熔渣、生成高炉煤气等。
3.高炉煤气处理。
包括净化、干燥和利用高炉煤气。
4.高炉渣处理。
包括渣料的脱水处理和利用。
三、炉前处理1.铁矿石的配合比应合理,确保冶炼过程的稳定性和冶炼指标的达标性。
2.铁矿石的浸出特性要进行充分的实验研究,以确定浸出的最佳工艺参数。
3.高炉燃料的选择应综合考虑成本、环境友好性和能源的有效利用。
四、炉内冶炼1.高炉内部的结构设计应保证炉缸的良好通风,以保证冶炼过程中的燃烧效率。
2.炉缸内的冷却系统设计应考虑耐用性和冷却效果,以确保高效的冷却。
3.高炉炼铁时,应定期对高炉进行倒渣、换衬等操作,以保持高炉的正常运行。
4.高炉内的矿石还原过程应控制在适宜的温度和还原度范围内,以保证冶炼指标的达标。
五、高炉煤气处理1.高炉煤气的净化应采用适当的设备和工艺,以去除其中的有害物质和尘埃。
2.煤气的干燥设备应保证干燥效果良好,以确保后续的煤气利用过程的正常运行。
3.高炉煤气的利用应采用先进的技术,以最大限度地提高煤气的利用效率,并减少对环境的污染。
六、高炉渣处理1.高炉渣的脱水处理应采用适当的设备和工艺,以去除渣中的水分,并达到可使用的要求。
2.渣的利用应采用最佳工艺,如制砖、制磷肥等,以最大限度地提高渣的综合利用效率。
七、安全管理1.在工艺设计中应考虑高炉作业人员的安全,在设计中提供安全防护装置和设备。
2.并应为高炉作业人员提供防护用品和紧急避险通道,并进行相应的安全培训。
3.在设计中考虑高炉熔铁和高炉煤气的安全处理和防护,确保高炉作为整个冶炼系统的安全运行。
本钢新1号高炉生产创新实践
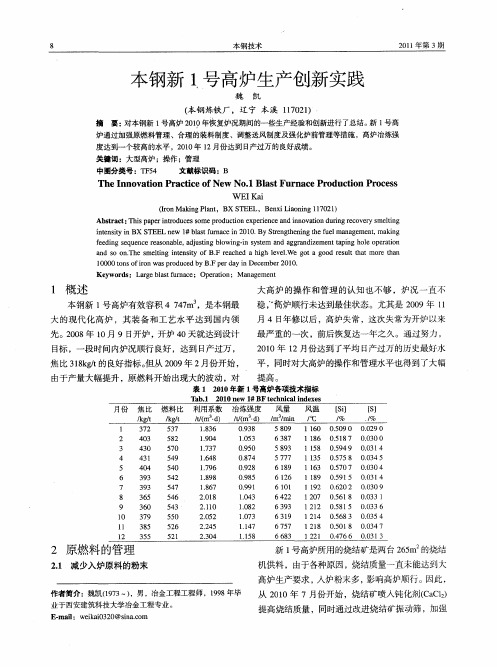
2 原燃料 的管理
21 减少入炉原料的粉末 .
作者简 介 : 魏凯( 7 ~ , ,冶金工程工程师 ,1 8 1 3 )男 9 9 年毕 9
业 于西安建筑科技 大学 冶金 工程专业。
E- i :wek i 3 0 sn .o ma l ia 0 2 @ i ac m
新1 号高炉所用的烧结矿是两台 25 。 6m 的烧结 机供料 ,由于各种原因,烧结质量一直未能达到大
高炉生产要求 , 人炉粉末多 , 影响高炉顺行 。 因此 ,
从 21 00年 7月份开始 ,烧结矿喷人钝化 ̄ (a 1 I C2 J C ) 提高烧结质量 ,同时通过改进烧结矿振动筛 ,加强
魏
凯 :本钢新 1 号高炉生产创新实践
9
烧结矿的筛分。
炉 料的衔接不好 ,容易造成风压高或管道现象发
关键 词 :大型高炉 ;操作 ;管理 中图分 类号 :T 5 F4 文献标 识码 :B
The I nno a i n Pr c ie o w . a tFu n c o v to a tc fNe No 1Bl s r a ePr duc i n o e s to Pr c s
月 4日年修以后 ,高炉失常 ,这次失常为开炉以来
最严 重 的一 次 ,前后恢 复 达一 年之 久 。通 过 努力 , 21 0 0年 1 份达 到 了平 均 日产过 万 的历史 最好 水 2月
大的现代化高炉 ,其装备和工艺水平达到 国内领
先 。20 0 8年 l 0月 9日开炉 , 炉 4 就 达到设 计 开 0天 目标 ,一 段 时 间内炉况 顺行 良好 ,达到 日产 过万 ,
现在的方法是短这种制度的优点是煤气利用率高能有效的降低焦期休风或降压后恢复时5001000m3min的大幅比和燃料比但它对原燃料的要求和操作水平比较度加风快速提压控制较低的压差这样可以快高到2009年2月份以后随着原燃料的变差速吹透中心稳定煤气分布防止慢风时间过长而高炉的顺行也进一步变差甚至到了失常的地步
本钢新1号高炉强化冶炼实践
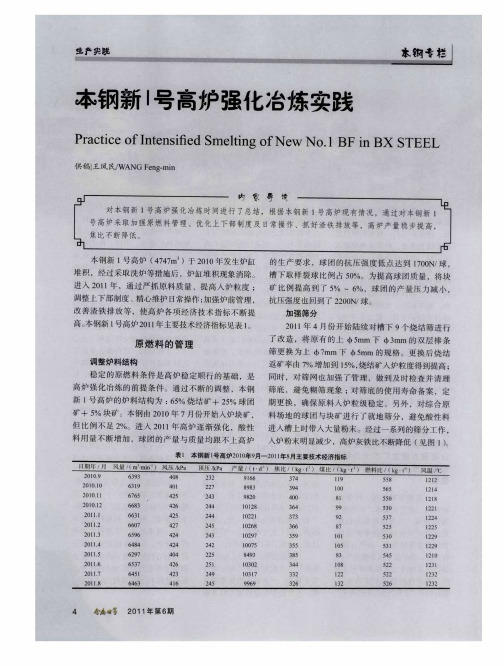
四 的小 粒级 比例 比焦 三多 出近两 成。 为 了提 高入 炉 快 的一侧 缩小 风 口面积 ,下 料慢 的一侧则 相反 。另
焦 炭粒 级 ,公 司专 门改造 了焦 四高落 差 中转 站 ,减 外 ,根 据矿石 与焦 炭 的落料 点不 同 ,将矿 石料线 改
少 焦炭 在运 输途 中 的摔打 ,而且在 人槽前 进行 了分 为 1.5m,焦 炭料线 提高至 1.3m。这些 措施 的采用 有
料 角度 不变 ,矿 角差 由l0。扩 展到 1 o以增 加矿 平 台 185
表2 本钢新 1号 高炉焦炭 的粒级 分布 %
180
日 山
175
l7O
20.24 69.25
竺
88.6
5.8
坌 堡垄坌 全堕
l1.88 1.O3
O.65
165
0
0
0
…
0
-_ 0
温波 动。
160%,因此铜冷却壁热 面要有一 而影 响炉 况顺行 ,还可 以适 当缩
固定 风 温
层 渣皮保 护层 ,能够 减少 铜冷 却 小铁 口直 径 ,增 加 出铁 时间 ,减
风 温 是 高 炉最 经 济 的 热 源 , 壁 区域 热损失 和保 持合理 操作 炉 少全 天铁 次 ,减 少耐材 与 开铁 口
风炉 ,为 提高 风温 ,将 热 风炉 的 铸 铁 冷 却 壁 温 度 在 80~ 120℃, 铁 时 间 通 常 在 15~30min,全 天
烧炉 方式 由三烧 一送 改 为二烧 二 软水进水 温度控 制在 42~45℃, 8~9次 铁 ,开 铁 口 钻 头 直 径 为
送 ,同时增加 拱顶 温度到 1400℃ 炉腹 至炉 喉 的水 温 差 (不包 括冷 55r am 。
年产万吨生铁的高炉炼铁车间工艺设计

年产万吨生铁的高炉炼铁车间工艺设计1. 引言高炉炼铁车间是钢铁企业中重要的生产部门之一,承担着将铁矿石通过高温还原产生生铁的任务。
本文旨在设计一套年产万吨生铁的高炉炼铁车间工艺,以确保高效、稳定地生产高质量的生铁。
2. 工艺流程为了实现年产万吨生铁的目标,我们采用以下工艺流程:2.1 矿石预处理矿石预处理是高炉炼铁的第一步,目的是将原始矿石进行破碎、筛分、洗选等工序,以去除杂质并获得合适的粒度分布。
矿石预处理的具体工艺流程包括: 1.矿石破碎:通过破碎设备将原始矿石破碎至适合进一步处理的大小; 2. 筛分:经过筛分设备将破碎后的矿石按照粒度分布分级,分别进入不同的处理线路; 3. 洗选:利用洗选设备去除矿石中的杂质和尾矿,获得洗选后的矿石。
2.2 炼铁炉料配料炼铁炉料配料是将预处理好的矿石与其他辅助炼铁原料按照一定的配比混合,以形成合适的炉料,满足高炉内燃烧和还原的需求。
炼铁炉料配料的工艺流程包括:1. 矿石称量:将预处理后的矿石按照设定的配比进行称量,并放入配料设备中; 2. 辅料添加:将其他辅助炼铁原料如焦炭、石灰石等按照一定比例添加到配料设备中;3. 搅拌混合:通过搅拌设备对矿石和辅料进行混合,确保配料均匀。
2.3 高炉炉缸操作高炉炉缸操作是指将配料装入高炉内,并控制高炉内的温度、气氛和流动状态,使炉料逐渐进行还原反应并生成生铁。
高炉炉缸操作的工艺流程包括: 1. 入炉:将配料从炼铁炉料配料设备中装入高炉的料斗中,并通过配料装置均匀地投放到炉缸中; 2. 点火:在炉缸底部点火,通过引入适量的空气使焦炭燃烧,形成高温的还原气体; 3. 加料:在还原气氛下,定期加入炉料和燃料以保持高炉的运行; 4.排渣:定期排出炉缸内产生的废渣和不可燃物,以保持炉缸的畅通。
2.4 生铁产出在高炉炼铁的过程中,生铁通过熔化和融合的过程逐渐生成,并且由底部口出高炉。
生铁的质量受到炉料配比、温度和操作的影响,需要进行质量监控和调整。
钢铁厂高炉设计施工方案
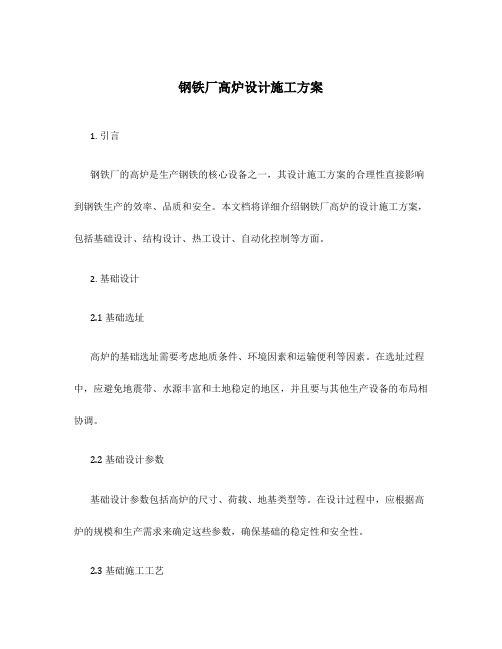
钢铁厂高炉设计施工方案1. 引言钢铁厂的高炉是生产钢铁的核心设备之一,其设计施工方案的合理性直接影响到钢铁生产的效率、品质和安全。
本文档将详细介绍钢铁厂高炉的设计施工方案,包括基础设计、结构设计、热工设计、自动化控制等方面。
2. 基础设计2.1 基础选址高炉的基础选址需要考虑地质条件、环境因素和运输便利等因素。
在选址过程中,应避免地震带、水源丰富和土地稳定的地区,并且要与其他生产设备的布局相协调。
2.2 基础设计参数基础设计参数包括高炉的尺寸、荷载、地基类型等。
在设计过程中,应根据高炉的规模和生产需求来确定这些参数,确保基础的稳定性和安全性。
2.3 基础施工工艺基础施工工艺包括地表开挖、基坑处理、灌注桩施工等。
在施工过程中,应根据地质条件和基础设计要求,采用适当的工艺和设备,确保基础的牢固和可靠。
3. 结构设计3.1 结构材料高炉的主要结构材料为钢结构和混凝土。
钢结构用于高炉的外壳和内部设备支撑,混凝土用于高炉的炉壁和炉底。
3.2 结构设计参数结构设计参数包括高炉的尺寸、结构荷载、抗震性能等。
在设计过程中,应根据高炉的规模和使用条件来确定这些参数,确保结构的强度和稳定性。
3.3 结构施工工艺结构施工工艺包括钢结构的焊接、混凝土的浇筑和养护等。
在施工过程中,应根据设计要求,采用适当的工艺和设备,确保结构的质量和可靠性。
4. 热工设计4.1 热工参数高炉的热工参数包括燃料消耗、风温、炉温、炉压等。
在设计过程中,应根据炼铁工艺和产品品质要求,确定这些参数,确保高炉的热工效果和生产效率。
4.2 热工设备热工设备包括燃烧系统、风机系统、排烟系统等。
在设计过程中,应根据热工参数和炼铁工艺要求,选择适当的设备类型和规格,确保设备的稳定运行和高效能耗。
4.3 热工控制热工控制包括燃烧控制、风量控制、温度控制等。
在设计过程中,应根据热工参数和自动化程度要求,选择适当的控制策略和仪表设备,确保高炉的热工过程稳定可控。
武钢1号高炉炉底与炉缸长寿新技术 (1)
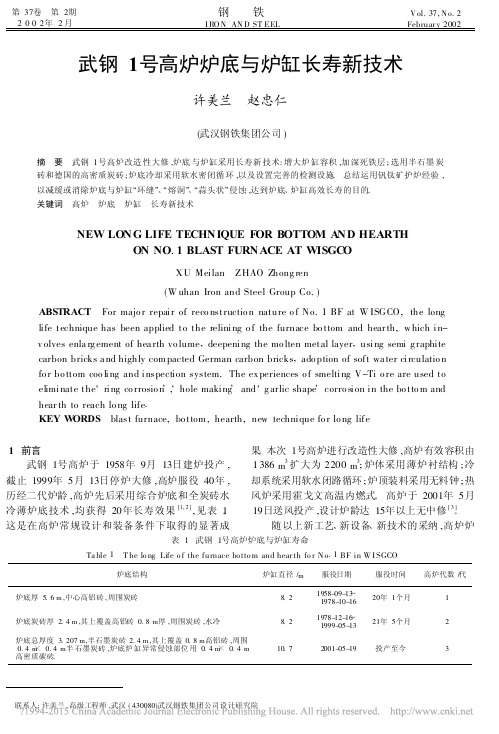
第37卷 第2期2002年2月钢 铁I RO N AN D ST EELV ol.37,N o.2Februar y2002武钢1号高炉炉底与炉缸长寿新技术许美兰 赵忠仁(武汉钢铁集团公司)摘 要 武钢1号高炉改造性大修,炉底与炉缸采用长寿新技术:增大炉缸容积,加深死铁层;选用半石墨炭砖和德国的高密质炭砖;炉底冷却采用软水密闭循环,以及设置完善的检测设施。
总结运用钒钛矿护炉经验,以减缓或消除炉底与炉缸“环缝”、“熔洞”、“蒜头状”侵蚀,达到炉底、炉缸高效长寿的目的。
关键词 高炉 炉底 炉缸 长寿新技术NEW LONG LIFE TECHNIQUE FOR BOTTOM A ND HEARTHON NO.1BLAST FURNACE AT WISGC OXU Meilan ZHAO Zhong ren(W uhan Iron and Steel Group Co.)ABSTRACT For majo r repair of reco nstructio n nature o f No.1BF at W ISGCO,the long life technique has been applied to the relining o f the furnace bo ttom and hear th,w hich in-v olves enla rg ement of hea rth vo lume,deepening the mo lten metal layer,using semi g raphite carbon bricks a nd highly com pacted German carbon bricks,ado ption of soft wa ter circulatio n fo r bo ttom coo ling and inspection system.The ex periences o f smelting V-Ti o re are used to eliminate the`ring co rrosio n’,`hole making’and`g arlic shape’corro sion in the bo tto m and hear th to reach lo ng life.KEY W ORDS blast furnace,bo ttom,hearth,new technique fo r lo ng life1 前言武钢1号高炉于1958年9月13日建炉投产,截止1999年5月13日停炉大修,高炉服役40年,历经二代炉龄,高炉先后采用综合炉底和全炭砖水冷薄炉底技术,均获得20年长寿效果[1,2],见表1。
高炉本体设计

高炉炼铁综合计算及高炉本体设计目录前言 (3)摘要 ........................................................................................... 错误!未定义书签。
第一章高炉炼铁综合计算 .. (5)1.1 原始条件 (5)1.2 工艺计算 (8)1.2.1 配料计算 (8)1.2.2 物料平衡 (13)1.2.3 热平衡计算 (19)1.2.3.2 热平衡表 (24)m的高炉本体设计 (26)第二章有效容积127532.1 技术经济指标确定 (26)2.2 高炉内型尺寸计算 (26)2.2 炉衬材质及厚度 (29)2.2.1炉底衬砖的设计 (29)2.2.2炉腹、炉腰及炉身下部的砌筑 (30)2.2.3炉身上部和炉喉砌筑 (30)2.3高炉冷却 (30)2.3.1冷却的目的和意义 (32)2.3.2高炉冷却介质 (32)2.3.3冷却设备 (32)2.4炉体钢结构 (33)2.4.1炉体钢结构 (33)2.4.2炉壳 (34)2.5 高炉基础 (34)结论 ........................................................................................... 错误!未定义书签。
谢辞 . (37)参考文献 (38)前言高炉炼铁是以铁矿石(天然富矿、烧结矿、球团矿)为原料,以焦炭、煤粉、重油、天然气等为燃料和还原剂,以石灰石等为熔剂,在高炉内通过燃料燃烧、氧化物中铁元素的还原以及非铁氧化物造渣等一系列复杂的物理化学过程获得生铁。
其主要副产品有高炉炉渣和高炉煤气。
为实现优质、低耗、高产和延长炉龄,高炉本体结构和辅助系统必须满足耐高温,耐高压,耐腐蚀,密封性好,工作可靠,寿命长,产品优质,产量高,消耗低等要求。
现代化高炉已成为高度机械化、自动化和大型化的一种综合生产装置。
新1#高炉开炉方案
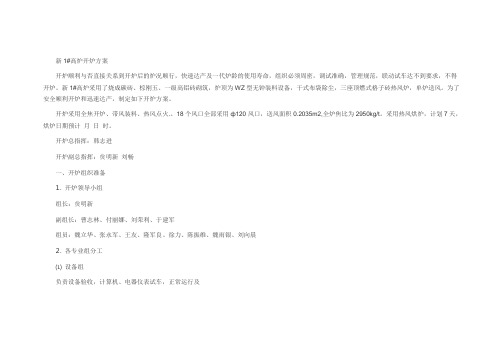
新1#高炉开炉方案开炉顺利与否直接关系到开炉后的炉况顺行,快速达产及一代炉龄的使用寿命,组织必须周密,调试准确,管理规范,联动试车达不到要求,不得开炉。
新1#高炉采用了烧成碳砖、棕刚玉、一级高铝砖砌筑,炉顶为WZ型无钟装料设备,干式布袋除尘,三座顶燃式格子砖热风炉,单炉送风。
为了安全顺利开炉和迅速达产,制定如下开炉方案。
开炉采用全焦开炉、带风装料、热风点火.。
18个风口全部采用ф120风口,送风面积0.2035m2,全炉焦比为2950kg/t。
采用热风烘炉,计划7天,烘炉日期预计月日时。
开炉总指挥:韩志进开炉副总指挥:贠明新刘畅一、开炉组织准备⒈开炉领导小组组长:贠明新副组长:曹志林、付丽娜、刘荣利、于建军组员:魏立华、张永军、王友、隆军良、徐力、陈振维、魏雨银、刘向晨⒉各专业组分工⑴设备组负责设备验收,计算机、电器仪表试车,正常运行及烘、开炉达产的安全用电。
组长:魏立华组员:徐利、贾云贺、何振生、吕凤余、贾国明、赵继明⑵炉内工艺组负责制定烘、开炉方案,配料计算和达产计划。
组长:于建军组员:曹志林刘相晨魏雨银⑶炉前组负责炉前设备试车,出铁厂、风口平台、渣铁沟提砌筑、高炉烘、开炉炉前操作工作。
组长:齐凤刚组员:三班炉前班长。
⑷热风炉和煤气除尘组负责开炉前热风炉和煤气系统试车,开炉前的热风烘炉及开炉后的风温等工作。
组长:陈振维组员:王洪成、蔡国永⑸卷称组负责上料系统的试车及开炉后上料系统的操作。
组长:吴建飞组员:张建波⑹冷却水系统组负责水系统试车与烘、开炉冷却系统的操作。
组长:隆君良、王献柱组员:全体水工⑺原燃料供应和渣铁平衡生产组负责开炉及达产的原燃料供应及渣铁处理组长:付丽娜组员:王友何会林陆云龙刘久明⑻材料和备件组负责开炉达产期间各种材料和备件的催办和落实。
组长:魏立华组员:机动科职员⑼劳动调配组组长:张永军组员:调度员。
⑽安全保卫组负责烘、开炉达产安全检查、安全措施的落实、安全保卫防火等工作。
国内部分高炉炉缸炉底设计特点
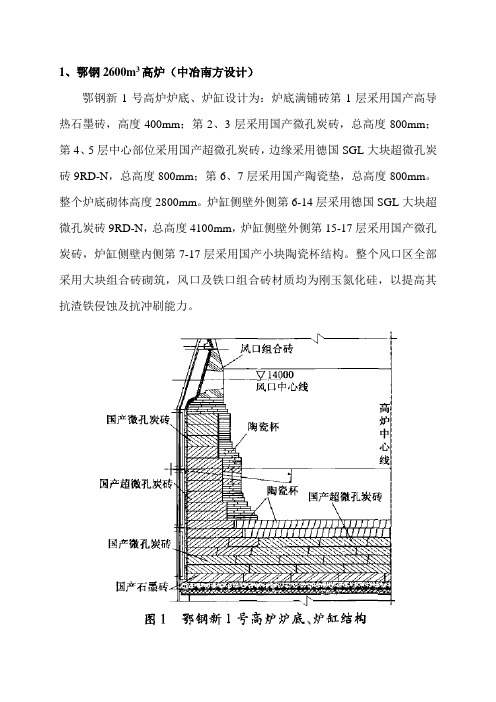
1、鄂钢2600m3高炉(中冶南方设计)鄂钢新1号高炉炉底、炉缸设计为:炉底满铺砖第1层采用国产高导热石墨砖,高度400mm;第2、3层采用国产微孔炭砖,总高度800mm;第4、5层中心部位采用国产超微孔炭砖,边缘采用德国SGL大块超微孔炭砖9RD-N,总高度800mm;第6、7层采用国产陶瓷垫,总高度800mm。
整个炉底砌体高度2800mm。
炉缸侧壁外侧第6-14层采用德国SGL大块超微孔炭砖9RD-N,总高度4100mm,炉缸侧壁外侧第15-17层采用国产微孔炭砖,炉缸侧壁内侧第7-17层采用国产小块陶瓷杯结构。
整个风口区全部采用大块组合砖砌筑,风口及铁口组合砖材质均为刚玉氮化硅,以提高其抗渣铁侵蚀及抗冲刷能力。
2、鞍钢2580m3高炉鞍钢11号高炉在本次大修中, 采用了法国SA VOIE的陶瓷杯和日本ND K的微孔碳砖, 见图2。
陶瓷杯底为两层抗铁水侵蚀性能优良的刚玉莫来石砖MS-4R,中心大块为棕刚玉质预制件, 陶瓷杯杯壁为抗渣铁侵蚀性能优良的棕刚玉质大型预制件组合砖, 其背部采用碗形锁砖结构。
日本大块碳砖砌筑砖缝要求小于0.5mm以减小热阻, 保证碳砖热面温度低于80℃(碳砖两端温差大于800℃易发生断裂)。
大块碳砖与MS-4R采用顶砌, 不留膨胀缝, 陶瓷杯底MS-4R采用无水胶泥CRU4由边缘到中心压迫式环形砌筑,以防漂浮,MS-4R与中心大块之间80mm膨胀缝采用刚玉质浇注料现场浇注联接。
3、重钢2500m3高炉(中冶赛迪设计)重钢3号高炉炉缸炉底采用炭砖+陶瓷杯结构,如下图所示。
炉底第1层为满铺400mm厚的石墨砖,第2-4层为满铺400mm厚的半石墨砖,第5层为满铺400mm厚的微孔炭砖。
炉缸靠近冷却壁侧环砌微孔炭砖炉缸。
陶瓷杯底砌2层400mm厚的刚玉莫来石砖,陶瓷杯壁环砌刚玉莫来石砖。
陶瓷杯与炭砖之间用炭素胶泥(TJ-2)填充;砌筑陶瓷杯砖用刚玉质磷酸盐耐火泥浆(GP-85);陶瓷杯砖与炭砖之间膨胀缝缓冲耐火泥浆(HCN-177L);炉底满铺保护砖与陶瓷杯砖之间的环缝及陶瓷杯与保护砖之间的环缝用刚玉捣打料。
鄂钢新转炉工程热负荷试车方案

武钢集团鄂钢企业新1#转炉技改工程热负荷试车方案鄂钢新1#转炉技改工程指挥部2009-8-30目录1 总纲 (3)2 热负荷试车旳前提条件 (15)3 热负荷试车计划与安排 (16)4 转炉系统热负荷试车方案 (17)5 连铸系统热负荷试车方案 (37)6 安全、消防与救护方案 (48)7 附件………………………………………………………………………1 总纲1.1 目旳为确保新1#转炉技改工程一次热负荷试车成功, 充分做好热负荷试车前旳各项准备工作, 做到科学安排、周密布置, 安全、顺利、圆满地完毕热负荷试车任务, 特制定本方案。
1.2合用范围本热负荷试车方案合用于转炉炼钢厂新1#转炉技改工程全部人员及与热负荷试车有关旳各外围单位。
1.3热负荷试车组织机构1.3.1企业热负荷试车领导小组及职责1.3.1.1企业热负荷试车领导小组组长:组员: 转炉炼钢厂、工程管理部、生产部、供给部、动力厂、机动部、安环部、计控处、制氧厂、质检中心、技术部、研究院、铁运中心、保卫部、鄂钢医院。
1.3.1.2职责由组长统一指挥协调各厂、处室配合新1#转炉热负荷试车, 各组员分别负责生产、备品备件、原材料、工艺技术、保卫、消防、救护、后勤保障等工作, 详细制作如下:1)转炉炼钢厂负责热负荷试车旳前期准备及热负荷试车全过程, 涉及热负荷试车纲领旳制定、审核、报批, 人员旳培训、取证上岗、岗位练兵, 原材物料旳联络进厂、就位, 安全、消防、救护措施到位, 多种应急方案齐全、可行, 人员各就各位, 职责明确, 分工详细。
2)工程管理部负责帮助转炉炼钢厂做好热负荷试车准备工作, 尤其是组织、协调各施工单位及时处理热负荷试车前发觉旳工程遗留问题, 并作好热负荷试车护航工作, 发觉问题及时配合处理。
3)中国一冶、十三冶、武钢建工、西安鹏远等对工程旳施工质量负责, 对转炉炼钢厂等提出旳整改意见应及时进行处理。
4)中冶南方、中冶京城对工程设计旳合理性、可操作性负责, 对热负荷试车中发觉旳设计不合理内容应及时进行设计变更。
新冶钢1号520m_3高炉炉役后期生产实践_
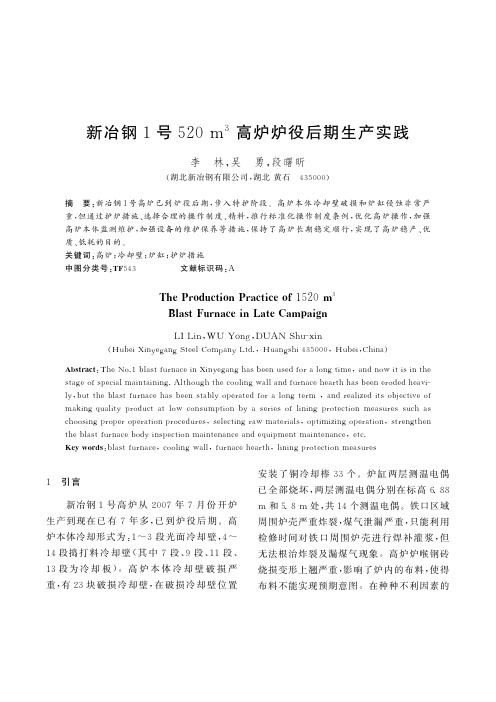
新冶钢1号520m3高炉炉役后期生产实践李 林,吴 勇,段曙昕(湖北新冶钢有限公司,湖北黄石 435000)摘 要:新冶钢l号高炉已到炉役后期,步入特护阶段。
高炉本体冷却壁破损和炉缸侵蚀非常严重,但通过护炉措施、选择合理的操作制度、精料,推行标准化操作制度条例,优化高炉操作,加强高炉本体监测维护,加强设备的维护保养等措施,保持了高炉长期稳定顺行,实现了高炉稳产、优质、低耗的目的。
关键词:高炉;冷却壁;炉缸;护炉措施中图分类号:TF543 文献标识码:AThe Production Practice of 1520 m3Blast Furnace in Late CampaignLI Lin,WU Yong,DUAN Shu-xin(Hubei Xinyegang Steel Company Ltd.,Huangshi 435000,Hubei,China)Abstract:The No.1blast furnace in Xinyegang has been used for a long time,and now it is in thestage of special maintaining.Although the cooling wall and furnace hearth has been eroded heavi-ly,but the blast furnace has been stably operated for a long term,and realized its objective ofmaking quality product at low consumption by a series of lining protection measures such aschoosing proper operation procedures,selecting raw materials,optimizing operation,strengthenthe blast furnace body inspection maintenance and equipment maintenance,etc.Key words:blast furnace,cooling wall,furnace hearth,lining protection measures1 引言新冶钢1号高炉从2007年7月份开炉生产到现在已有7年多,已到炉役后期。
杭钢新1号1250m3高炉开炉达产实践

杭钢新1号1250m3高炉开炉达产实践摘要:杭钢新1号高炉采用了一系列先进实用的技术和设备,通过制定合理的烘炉和开炉方案,确定合理的开炉工艺参数,加强高炉操作调剂等措施,确保了高炉顺利开炉。
关键词:高炉开炉达产0 前言杭钢1#高炉在2000年6月开炉至今,到2007年10月停炉时单位炉容出铁量达到9700 t/ m3以上,炉体冷却壁、水箱大面积烧损,铁口区域热流强度高等各种迹象表明该炉子已到炉役后期,大修后设计炉容为1250m3。
经过紧张的前期准备,杭钢新1号高炉2006年8月30日开始破土动工移地大修,于2008年10月15日点火。
新1号高炉采用了一系列先进实用的技术和设备,风机采用陕鼓AV63-15 型全静叶可调电动轴流鼓风机,平均流量Q=3000m3/min ,出口压力P=0.45MPa(A),风机配一台过滤风量为7000 m3/min 空气过滤器;煤气处理系统采用干法布袋除尘工艺;煤气余压发电(TRT )采用全干式透平主机,配10000kW 无刷励磁同步发电机;渣处理系统综合分析了INBA、轮法、搅笼等工艺,最后采用沉淀池加底滤池工艺;冷却系统采用全覆盖冷却壁,热负荷较高的炉身中下部、炉腰、炉腹和炉缸二层采用铸钢冷却壁;炉缸2.8m的深死铁层和陶瓷垫加大炭块综合炉底,大炭块加模压小炭块炉缸;炉前采用单矩形平坦化出铁场、贮铁式主沟和摆动流嘴,主要设备为全液压式开口机和300T矮身液压泥炮,同侧布置;槽下焦、矿槽采用双排并列布置,焦炭、烧结矿和球团分散筛分和分散称量,碎焦运至车间外回收焦丁入炉,上料采用主胶带上料;炉顶采用串罐式无钟,多环布料方式;热风炉采用性价比较高顶燃式热风炉和煤气空气预热器等等。
新1号高炉于2008年10月15日点火送风,17日1:50第一次开铁口出渣,6:50~7:10出第一炉铁,铁量约30t,到10月21日日产达2563.8t,利用系数达到2.0,11月4日日产3039.5t,系数超过2.4,达到了高炉设计指标。
鄂钢高炉技改工程新1#高炉管道安装方案剖析

目录一、工程概况二、编制依据三、项目施工组织四、管道及水泵安装施工方法及技术措施五、工程质量保证措施六、安全文明施工保证措施七、施工及管理人员安排八、主要施工机具第一章工程概况1、工程简介1.1鄂钢高炉技改工程新1#高炉软/净循环水泵房位于1#高炉南边。
地下管廊从北至南成“Z”型将高炉和循环水泵房连成整体,管廊内有8根管道通向高炉。
1.2根据所需用水压力及水质的不同,主循环水泵站系统分为:软水补充系统及软水密闭循环系统,净循环系统,直流增压供水系统。
1.3软水补充系统及软水密闭循环系统组成包括:①软水补充水泵组:电动水泵2台(1用1备),另设事故用柴油机泵1台。
电泵型号:KQW125/235-45/2,Q=100m3/h,H=72m。
电机功率45KW,电压380V。
柴油机泵型号为NPS200-230,Q=200m3/h,H=72m②主供水泵组:电动水泵3台(2用1备),另设事故用柴油机泵1 台。
电泵型号:KQSN450-N13/465,Q=2350m3/h,H=55m,电机型号:Y500-4,功率500KW,电压10KV。
柴油机泵型号为CB2820/55,Q=2820m3/h,H=55m③风口中套增压泵组:电动水泵2台(1用1备)。
电泵型号:KQSN350-M9/473,Q=1300m3/h,H=65m,电机型号:Y450-4,功率315KW,电压10KV。
④风口小套增压供水泵组:电动水泵3台(2用1备)。
电泵型号:KQSN350-N6/575(T),Q=980m3/h,H=95m,电机型号:Y450-4,功率400KW,电压10KV。
⑤蒸发式冷却器14套,P=1.0MPa。
型号:ZSK-ZP9*3,冷却水量Q=400 m3/h*台,进水温度520C,出水温度38.50C,风机型号Y-SF24-L4(3台/套)。
⑥加药装置1套包括:φ1200*1200溶解罐1个,带搅拌机1台,配计量泵2台。
流量100L/h,扬程70m.⑦全自动软水器1套,制备能力50 m3/h。
新建高炉初步设计方案

新建高炉初步设计方案高炉是一种炼铁设备,用于将铁矿石还原成生铁的过程。
高炉的初步设计方案需要考虑多个因素,包括炉容、冶炼工艺、燃料选用等。
第一步,确定高炉的炉容。
炉容是指高炉的容积,通常以立方米为单位。
炉容的大小决定着高炉的产能,以及铁矿石的装载量。
为了提高生产效益,可以选择较大的炉容。
第二步,选择合适的冶炼工艺。
冶炼工艺是指高炉内铁矿石的还原过程。
常用的冶炼工艺包括焦炭还原法和直接还原法。
焦炭还原法是将焦炭作为还原剂,通过高温将铁矿石还原为生铁。
直接还原法是指使用氢气或天然气等直接还原铁矿石。
根据实际情况选择合适的冶炼工艺。
第三步,选择燃料。
燃料主要用于提供高炉的热能,驱动冶炼过程。
常用的燃料包括焦炭、煤炭、煤气等。
根据燃料价格、能源利用效率等因素选择合适的燃料。
第四步,确定高炉内部结构。
高炉内部结构包括上、中、下三层,每层都有自己的功能。
上层主要用于装载铁矿石和燃料,中层主要进行还原反应,下层主要蓄热。
确定内部结构要考虑到冶炼工艺和燃料的特点。
第五步,设计高炉周边设施。
高炉周边设施包括炉渣处理装置、炉气处理装置等。
炉渣处理装置用于处理高炉冶炼产生的炉渣,以回收炉渣中的有用物质。
炉气处理装置用于处理高炉冶炼产生的炉气,以回收炉气中的有用物质,减少环境污染。
以上是高炉初步设计方案的基本步骤和要点。
在设计过程中,需要考虑实际情况和生产需求,对每个环节进行充分的分析和比较,以保证设计方案的合理性和可行性。
同时还需要考虑到设备的安全性和可维护性,确保设备的长期稳定运行。
高炉冶炼工艺设计炉前出铁
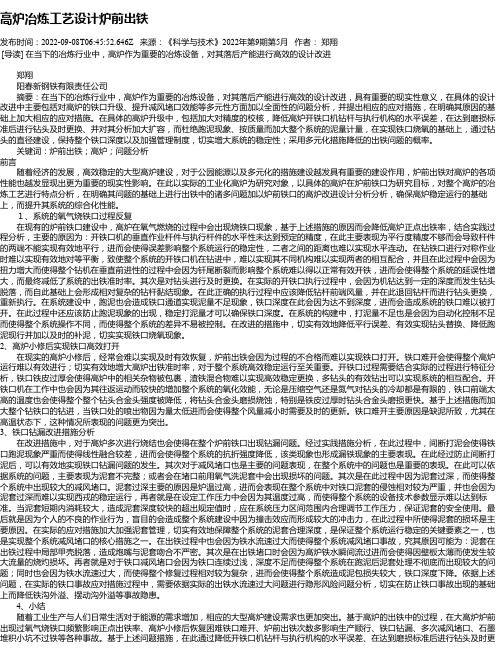
高炉冶炼工艺设计炉前出铁发布时间:2022-09-08T06:45:52.646Z 来源:《科学与技术》2022年第9期第5月作者:郑翔[导读] 在当下的冶炼行业中,高炉作为重要的冶炼设备,对其落后产能进行高效的设计改进郑翔阳春新钢铁有限责任公司摘要:在当下的冶炼行业中,高炉作为重要的冶炼设备,对其落后产能进行高效的设计改进,具有重要的现实性意义,在具体的设计改进中主要包括对高炉的铁口升级、提升减风堵口效能等多元性方面加以全面性的问题分析,并提出相应的应对措施,在明确其原因的基础上加大相应的应对措施。
在具体的高炉升级中,包括加大对精度的校核,降低高炉开铁口机钻杆与执行机构的水平误差,在达到磨损标准后进行钻头及时更换、并对其分析加大扩容,而杜绝跑泥现象、按质量而加大整个系统的泥量计量,在实现铁口烧氧的基础上,通过钻头的直径建设,保持整个铁口深度以及加强管理制度,切实增大系统的稳定性;采用多元化措施降低的出铁问题的概率。
关键词:炉前出铁;高炉;问题分析前言随着经济的发展,高效稳定的大型高炉建设,对于公园能源以及多元化的措施建设越发具有重要的建设作用,炉前出铁对高炉的各项性能也越发显现出更为重要的现实性影响。
在此以实际的工业化高炉为研究对象,以具体的高炉在炉前铁口为研究目标,对整个高炉的冶炼工艺进行特点分析,在明确其问题的基础上进行出铁中的诸多问题加以炉前铁口的高炉改进设计分析分析,确保高炉稳定运行的基础上,而提升其系统的综合化性能。
1、系统的氧气烧铁口过程反复在现有的炉前铁口建设中,高炉在氧气燃烧的过程中会出现烧铁口现象,基于上述措施的原因而会降低高炉正点出铁率,结合实践过程分析,主要的原因为:开铁口机的垂直作业杆件与执行杆件的水平性未达到预定的精度,在此主要表现为平行度精度不够而会导致杆件的两端不能实现有效地平行,进而会使得误差影响整个系统运行的稳定性,二者之间的距离也难以实现水平连动。
在钻铁口进行对称作业时难以实现有效地对等平衡,致使整个系统的开铁口机在钻进中,难以实现其不同机构难以实现两者的相互配合,并且在此过程中会因为扭力增大而使得整个钻机在垂直前进性的过程中会因为钎尾断裂而影响整个系统难以得以正常有效开铁,进而会使得整个系统的延误性增大,而最终减低了系统的出铁准时率。
- 1、下载文档前请自行甄别文档内容的完整性,平台不提供额外的编辑、内容补充、找答案等附加服务。
- 2、"仅部分预览"的文档,不可在线预览部分如存在完整性等问题,可反馈申请退款(可完整预览的文档不适用该条件!)。
- 3、如文档侵犯您的权益,请联系客服反馈,我们会尽快为您处理(人工客服工作时间:9:00-18:30)。
因此,此区域冷却壁镶砖采用浸磷酸粘土砖,即满足 工艺要求,又适当降低投资。
现在冷却壁的制造质量有了大幅度提高,冷却 系统也日益完善,在采用软水密闭循环冷却系统的 条件下,冷却强度能够得到充分保证,这为炉体采用 砖壁合一、薄壁内衬技术创造了条件。
砖壁合一、薄壁内衬结构具有许多优点: (1)高炉内衬薄,内型稳定,设计炉型基本上就 是生产炉型,高炉在一代炉役里炉型始终处于最佳 状态。 (2)高炉内衬薄,耐材耗量大量减少,节省大量 投资。 (3)内衬直接镶嵌在冷却壁中,支撑效果好;内 衬不会产生膨胀霍加,应力小。 (4)内衬可预先炉外砌筑,可缩短施工周期。 炉顶煤气密封罩上的喷涂层,其锚固件采用固 定杆、支撑板、六角锚固件相结合的方式,增强喷涂 料与炉壳的黏结性。选用的喷涂料抗折强度高、耐 CO侵蚀性能优良。 4冷却元件 鄂钢新1号高炉采用全冷却壁结构,其中炉腹 以上采用砖壁合一冷却壁,炉腹、炉腰、炉身下部区 域采用铜冷却壁。整个高炉设置冷却壁共14段 (见表3)。
鄂钢新1号高炉炉底、炉缸设计为:炉底满铺砖 第1层采用国产高导石墨砖,高度400mm;第2、3 层采用国产微孔炭砖,总高度800ram;第4、5层中 心部位采用国产超微孔炭砖,边缘采用德国SGL大 块超微孔炭砖9RD—N,总高度800mm;第6、7层采 用国产陶瓷垫,总高度800mm。整个炉底砌体高度 2800mm。炉缸侧壁外侧第6~14层采用德国SGL 大块超微孔炭砖9RD—N,总高度4100mm,炉缸侧 壁外侧第15~17层采用国产微孔炭砖,炉缸侧壁内 侧第7一17层采用国产小块陶瓷杯结构。
联系人:杜春松高级工程师023-63548626 (400013)重庆市渝中区中冶赛迪工程技术股份有限公司炼铁事业 部 收稿I:l期:2010—5—10
加深死铁层等方面,其目的是为了改善料柱透气性、 改善煤气分布、提高喷煤比、适当抑制边缘、吹透中 心,以实现高产、长寿、低耗、顺行的目的。
操作炉型是在高炉投产几年后的实际炉型。由 于内衬大部分已被侵蚀,炉腰扩大,炉身及炉腹角变 小,此时的炉型与设计炉型相差较大,对高炉的顺 行、稳定、高产和煤气利用率都有不利的影响。砖壁 合一、薄壁内衬结构的高炉炉型,在设计上就考虑了 实际生产中出现的问题,设计炉型基本上就是操作 炉型,一代炉役其操作炉型基本维持不变。在确定 鄂钢新1号高炉炉型时,以此为前提,同时总结同类 容积高炉的内型尺寸,并结合鄂钢具体的原燃料条 件,确定了本高炉内型尺寸(见表2)。
枷㈣珊∞啪似|善∞姗枷∞湖加砷∞咖姒鳓∞硼|詈啪靴啦矾搅
铁口数,个
风口数,个
。
3 内衬 鄂钢新1号高炉在内衬设计上充分考虑高炉各
部位的不同工作条件和侵蚀机理,结合原燃料条件, 外部冷却元件的差异,有针对性的选用耐火材料,并 在结构上加强砖衬的稳定性。
炉底、炉缸是高炉长寿的关键部位,特别是铁口 及铁口以下的异常侵蚀区,越来越成为制约高炉长 寿的最重要因素。因此选择合理的炉底、炉缸结构 形式对整个高炉长寿具有非常重要的意义。本设计 采用“国产小块陶瓷杯+水冷炭砖”炉缸、炉底结 构。陶瓷材料的保温性能较好,炉缸热损失少,可得 到较高的炉缸温度。同时由于陶瓷材料抗铁水冲刷 能力强,完全侵蚀需要一定的时间,有利于节能、降 耗和稳定操作。随着陶瓷材料的侵蚀,炭砖将直接 与铁水接触,为保证炉缸寿命,炉缸炭砖的性能尤其
表2鄂钢新1号高炉炉型主要尺寸
项目
数值
高炉容积Vu,m3 炉缸直径d,mill
炉腰直径D,mm 炉喉直径dj,nlnl
死铁层深度ho,i11/11
炉缸高度hl,rain
炉腹高度h2,mm
炉腰高度h3,mill 炉身高度h4,mill
炉喉高度hs,1111'11
有效高度Hu,mm
炉腹角n
炉身角B
Hu/’D
节省运行费用260—350万元,节水效果也十分明
炉喉钢砖设置l段,无水冷。通过其下部吊挂 显)。
通过关键部位超微孔炭砖的采用,利用炭砖良 好的热导能力和外部较高的冷却强度,鄂钢新l号 高炉炉底、炉缸的设计,在保证炉底、炉缸长寿的基 础七,实现了工程投资的优化。鄂钢新1号高炉炉 底、炉缸结构如图l所示。
风口区域是一个承上启下的区域,此区域内衬
图1 鄂钢新1号高炉炉底、炉缸结构
·43·
万方数据
结构和材质选择的合理与否,对高炉寿命有相当大 的影响。本设计在整个风口区全部采用大块组合砖 砌筑,以加强结构的稳定性;同时采取措施,增加风 口冷却壁与炉腹铜冷却壁交接处组合砖的厚度。风 口及铁口组合砖材质均为刚玉氮化硅,以提高其抗 渣铁侵蚀及抗冲刷能力。
在炉身中部第8一10段双层水冷铸铁冷却壁区 域,冷却壁镶砖采用si。N。一SiC砖。Si,N。一SiC砖 具有很好的抗渣、抗碱侵蚀能力,同时也具有一定的 抗冲刷能力和抗热震能力,而且其导热性能好,易结 渣皮。
在炉身上部第ll~14段单层水冷铸铁冷却壁 区域,内衬破损的原因主要是机械冲刷和碱金属侵 蚀。粘土砖通过真空浸磷酸后,具有较强的抗碱金 属侵蚀能力,同时抗冲刷能力也得到一定的提高。
(6)软水系统具有完善的检测设施和检漏设 施。
鄂钢新1号高炉的主要技术经济指标见表l。 表1 鄂钢新1号高炉的主要技术经济指标
2 炉型 合理的高炉内型是实现高产、稳产、低耗、长寿
的基本条件之一。现代高炉的内型设计特点主要表 现在大炉缸、多风口、适当矮胖、减小炉身及炉腹角、
用前置炉,需消耗更多的空煤气,不可避免的排出更 多的废气。这些高炉煤气都是焦炭及煤粉这些不可 再生能源的一种转换态,虽然节约了焦炭,但实际上 是浪费了能源,在讲究循环经济的形式下,其实整体 效果是不经济的。在多少送风温度下进行高炉冶炼 最为经济有待研究。
炉腹及其以上的部位,主要有传统内衬结构和 砖壁合一、薄壁内衬结构两种形式。鄂钢新l号高 炉设计采用砖壁合一、薄壁内衬结构。
第5—7段铜冷却壁区域,由于铜冷却壁具有十 分突出的导热性能和抗热流冲击的性能,能够在铜 冷却壁的热面形成稳定的渣皮。为了充分发挥铜冷 却壁的优越性能、增强渣皮与铜冷却壁热面燕尾槽 的直接黏结效果、降低热损失,在铜冷却壁热面采用 特种喷涂料喷涂,厚度为150mm。
浮动点相结合的固定方式,冷却壁水冷管与炉壳间 总投资较3个独立的软水密闭循环系统减少18%
加膨胀器,少量水管根据需要设置变形补偿套管,从
~20%;另外采用联合软水系统比其他冷却系统运
而根本解决因炉壳与冷却壁间的温差不同导致水管
行费用减少30%一50%旧’(对于2600m3高炉,每年
剪断而出现破漏的问题。
高炉冷却系统的好坏直接关系到各种冷却元件 的寿命,从而关系整个高炉的寿命。实践证明,普通 工业水易结垢,冷却强度低,不能满足现代大中型高
质为球墨铸铁。倒扣式镶砖冷却壁,设置内大外小 炉长寿的要求,而且能耗很高。
镶砖槽(贯通式),防止掉砖,镶砖厚度75mm。倒扣
软水密闭循环冷却系统具有不结垢、无污染、冷
(4)炉身中上部:计2段,为单层水冷镶砖冷却
万方数据
壁,水管为(t)76 mm X6mm,竖直排列。材质均为球 使用该种方式炉喉钢砖,无变形、无上翘、完好无损。
墨铸铁。
5水冷系统
(5)炉身最上部及炉喉部位:设置2段倒扣式 镶砖冷却壁。冷却壁壁体面为高炉内型尺寸。冷却 壁为单层水冷,水管(I)76mm X6mm,竖直排列。材
根据武钢集团统一规划,鄂钢公司易地新建1 号高炉,高炉有效容积2600m3,高炉已于2010年1 月投产。新l号高炉以“先进、实用、可靠、经济、节 能、环保”为设计原则,采用国内外大型高炉的成 熟、先进技术,在保证持续稳定地向炼钢供应优质铁 水、提高钢铁产品市场竞争力的同时、延长高炉寿 命、控制环境污染、提高生产效率。 1 设计特点
m,竖直排列.夕f、层
·44·
水管为枷5mm×6mm,蛇形排列。材质均为球墨铸 铁。
此区域是无渣液或渣液不足的软熔带形成部 位,长期经受炉料磨损、高热震、高温煤气流的冲刷 及碱金属的侵蚀。采用双层水冷镶砖冷却壁,增大 该区域冷却强度,实现了高热负荷冷却壁的无过热 化,抗高热负荷冲击能力强,冷却壁热面温度低,便 于结渣挂渣,渣皮脱落后也能快速恢复,因此高炉寿 命长。
关键。 要保证炉底、炉缸的寿命必须满足以下条件:①
提高炉缸、炉底耐材的性能,实现微孔或超微孔,减 少孔径大于1斗m的气孔,实现气孑L封闭,可消除或 减少铁水向炭砖内部的渗透,使铁水对炭砖的侵蚀 只能在炭砖的表面进行,从而减缓了炭砖的侵蚀速 度,延长高炉寿命。②使耐材和高温铁水隔离,降低 耐材自身的温度,减缓或者抑制化学反应的发生。 有效的方法是在耐材热面形成一层渣铁凝固层,隔 断各种化学反应的反应源,用渣铁层的低导热性降 低耐火材料内部的温度。据研究,1 150℃等温线为 铁水的凝固温度,如果1 150℃等温线位于耐材热面 的铁水内,则说明炉缸炉底有渣铁层的保护,使耐材 和高温铁水隔离。
(3)采用热风炉自身热废气进行双预热空煤气 是十分经济环保的生产方式,减少单位风量加热面 积有利于提高热风炉自身热废气温度,有利于热风 炉系统内的自身热量循环,有利于节能减排。
·42·
万方数据
(4)国内现阶段众多高炉的年平均风温处于 1 150℃,也有少数达到12500C以上。从经济生铁生 产角度考虑,减少热风炉的单位风量蓄热面积,减小 热风炉尺寸,设计余热回收,合理利用高炉煤气这种 附加产品,加强操作管理具有更现实的经济意义,符 合科学发展观理论。
表3 鄂钢新1号高炉冷却壁主要特征
(1)炉底、炉缸区(含风口带):共4段,为光面 冷却壁,每块冷却壁的水冷管4进4出,竖直排列, 铁口侧和风口带的冷却壁水管为6进6出或7进7 出,竖直管排列,所有水管直径均为+76mm×6nlnl。 冷却壁材质:1—3段为低铬铸铁,第4段为球墨铸 铁…。
(2)炉腹、炉腰及炉身下部:计3段,为单层水 冷4通道铜冷却壁。
土质高强浇注料。通过冷镶厚度为75 mill的砖,在 水密闭循环冷却系统。