浅谈铸件砂眼气孔缺陷及预防措施_杨建林
铸件常见缺陷的产生原因及防止方法
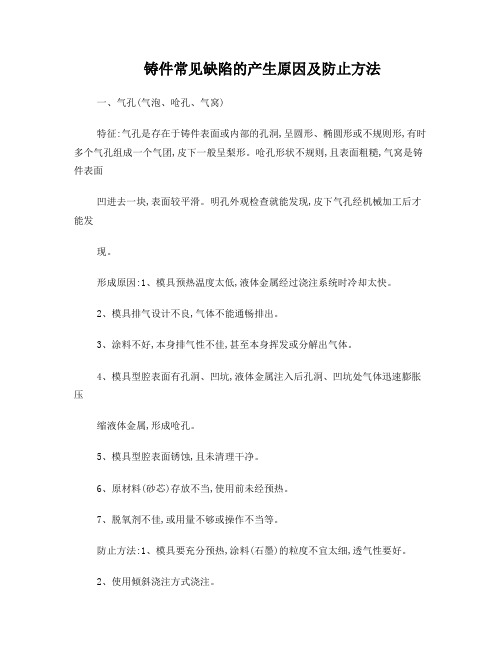
铸件常见缺陷的产生原因及防止方法一、气孔(气泡、呛孔、气窝)特征:气孔是存在于铸件表面或内部的孔洞,呈圆形、椭圆形或不规则形,有时多个气孔组成一个气团,皮下一般呈梨形。
呛孔形状不规则,且表面粗糙,气窝是铸件表面凹进去一块,表面较平滑。
明孔外观检查就能发现,皮下气孔经机械加工后才能发现。
形成原因:1、模具预热温度太低,液体金属经过浇注系统时冷却太快。
2、模具排气设计不良,气体不能通畅排出。
3、涂料不好,本身排气性不佳,甚至本身挥发或分解出气体。
4、模具型腔表面有孔洞、凹坑,液体金属注入后孔洞、凹坑处气体迅速膨胀压缩液体金属,形成呛孔。
5、模具型腔表面锈蚀,且未清理干净。
6、原材料(砂芯)存放不当,使用前未经预热。
7、脱氧剂不佳,或用量不够或操作不当等。
防止方法:1、模具要充分预热,涂料(石墨)的粒度不宜太细,透气性要好。
2、使用倾斜浇注方式浇注。
3、原材料应存放在通风干燥处,使用时要预热。
4、选择脱氧效果较好的脱氧剂(镁)。
5、浇注温度不宜过高。
二、缩孔(缩松)特征:缩孔是铸件表面或内部存在的一种表面粗糙的孔,轻微缩孔是许多分散的小缩孔,即缩松,缩孔或缩松处晶粒粗大。
常发生在铸件内浇道附近、冒口根部、厚大部位,壁的厚薄转接处及具有大平面的厚薄处。
形成原因:1、模具工作温度控制未达到定向凝固要求。
2、涂料选择不当,不同部位涂料层厚度控制不好。
3、铸件在模具中的位置设计不当。
4、浇冒口设计未能达到起充分补缩的作用。
5、浇注温度过低或过高。
防治方法:1、提高磨具温度。
2、调整涂料层厚度,涂料喷洒要均匀,涂料脱落而补涂时不可形成局部涂料堆积现象。
3、对模具进行局部加热或用绝热材料局部保温。
4、热节处镶铜块,对局部进行激冷。
5、模具上设计散热片,或通过水等加速局部地区冷却速度,或在模具外喷水,喷雾。
6、用可拆缷激冷块,轮流安放在型腔内,避免连续生产时激冷块本身冷却不充分。
7、模具冒口上设计加压装置。
8、浇注系统设计要准确,选择适宜的浇注温度。
导轨铸件气孔缺陷分析及改进措施
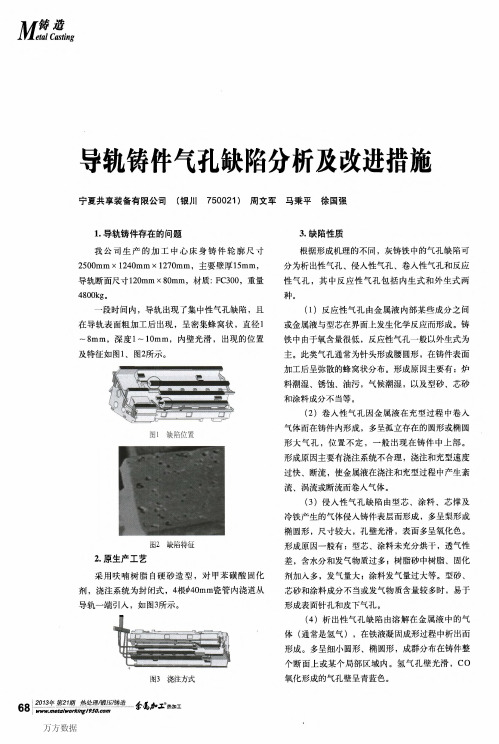
(续)
涂料 试块 烘干失去 烘干后水损失 15h吸湿 吸收水 15h吸收水分 编号 编号
4
(4)充分烘烤砂型和砂芯,尤其对于后期补 刷涂料的区域必须再次烘烤。 (5)增加砂型、砂芯内部气道、气眼设置, 保证气体流畅排出,使出气面积大于1.5倍阻流截
面积。
水重幢
OHale Waihona Puke 08 0.04 0.04 O.07 0.06 0.04
2.原生产工艺
采用呋喃树脂自硬砂造型,对甲苯磺酸固化 剂,浇注系统为封闭式,4kl虱b40mm瓷管内浇道从 导轨一端引入,如图3所示。
图3浇注方式
氧化形成的气孔壁呈青蓝色。
谭’脚矿‘”…1 O石i赢证猫赫谢锄谚鳓占而 68{戮麓勰搿嚣篆燃参磊加r黝工
万方数据
M篡囊诹
我公司生产的导轨铸件气孔出现在局部表层1 ~lOmm深位置,呈密集蜂窝状,具有反应性和侵 入性气孔的特点。 4.原因分析 铁液浇入铸型后,砂型、涂料中有机/无机粘 结剂、树脂砂及附加物等高温分解产生大量的气体 (见表1)。
③ ② ①
2 3 4 5 6 7 8 9
涂料 试块 烘干失去 烘干后水损失 15h吸湿 吸收水 15h吸收水分 编号 编号
1
水重倡
O.07 O.07 0.04
比率(%)
O.0l 0.01 0.00
后重Ig
76.65 76.05 79.47
分重倌 比率(%)
O.11 0.11 0.11 1.60 1.89 1.11
0.25%~0.6%,WM。=1.4%~1.6%,WP≤0.04%,
W
1.铸件结构及铸造难点分析 铸件几何形状和传统工艺如图1、图2所示。 该铸件外形尺寸长4060mm、宽1510mm、
铸钢件气孔缺陷的分析及预防

铸钢件气孔缺陷的分析及预防铸钢件是一种广泛应用于制造工业的产品,在各行各业都有着广泛的应用。
然而,在铸钢件的生产过程中,常常会出现气孔缺陷。
在本文中,将对铸钢件气孔缺陷的分析及预防进行详细的介绍。
气孔缺陷是铸钢件生产过程中经常出现的一种缺陷,其原因主要是由于铸造过程中,铸钢件内的气体无法顺利释放,而形成的空气泡所致。
具体分析如下:1.铸造温度过高或过低铸造温度过高或过低会导致铸造过程中熔化金属与气体相互作用不充分,或者是在凝固时,金属凝固异常迅速,导致铸造件内部气体排放不及时,进而形成气孔缺陷。
2.金属液中气体含量过高铸钢件气孔缺陷的一个重要原因是金属液中气体含量过高。
这主要是由于铸造过程中,将熔化的金属液错流于模具中时,金属液中气体无法快速排出,而形成的气泡后来就会形成气孔缺陷。
3.模具设计不合理模具是制造铸造件的核心部分之一。
如果模具设计不合理,例如模具壁厚不符合要求、孔隙率过高等造成模具过于松散、不好密封,使熔融金属鼓荡时容易进入焦模震荡区域,从而使气体被气团包裹形成气泡,而成为铸钢件气孔缺陷.了解了铸钢件气孔缺陷发生的原因,我们可以采取一些技术性措施来预防气孔缺陷的出现。
1.合适的铸造温度我们可以在铸造前对熔融金属的净化处理,或者使用真空、熔覆反应等特殊工艺。
这些技术手段可以有效地去除金属液中的气体,减少气孔的发生。
合理的模具设计可以有效地避免铸造中应力集聚,提供良好的流动通道和顺畅的气流通道,避免产生气泡,降低气孔发生的概率。
对于大型铸钢件,可以采用完整的、结构合理的模具,避免模具的壁厚不符合要求等情况。
4.严格的生产工艺控制在生产过程中,我们还需要严格执行质量控制方案,不断优化铸造工艺,并加强现场监督管理。
避免铸造过程中出现偏差,加强对炉温、铸型、冷却等关键环节的控制,并在浇注后及时进行冷却处理,以提高铸钢件的质量。
总结:铸钢件气孔缺陷的原因主要是铸造温度过高或过低导致气体无法充分释放,金属液中气体含量过高,模具设计不合理等情况所致。
铸件气孔的产生

型芯怎么防止铸件气孔的产生用什么办法才能防止型芯的干燥..树脂砂芯因浇注时会产生气体从而导致铸件产生气孔最终导致铸件打废品..1、防止侵入气孔的措施(1)提高砂型和砂芯的透气性,控制砂型的紧实度砂型和砂芯的透气性越差,紧实度越高,侵入气孔产生的倾向性越大。
应严格控制砂型的紧实度和透气性。
在保证砂型强度的条件下,尽量降低砂型的紧实度。
采用面砂加粗背砂的方法是提高砂型透气性的有效措施。
(2)控制气体产生的速度严格控制型砂和芯砂中发气物质的加入量,控制湿型的分。
干型应保证烘干质量,并及时浇注,停放时间不要过长。
冷铁或芯铁应保证表面清洁、干燥。
浇口圈和冒口圈应烘干后使用。
(3)提高砂型和砂芯的排气能力铸型上扎排气孔帮助排气,保持砂芯排气孔的畅通,铸件顶部设置出气冒口。
采用合理的浇注系统。
(4)适当地提高浇注温度提高浇注温度可使侵入气体有充足的时间排出。
浇注时应控制浇注高度和浇注速度,保证金属液平稳地流动和充型。
(5)提高金属液的熔炼质量尽量降低铁水中的含硫量,保证铁水的流动性。
防止金属液过分氧化,减小气体排出的阻力。
2、防止卷入气孔的措施尽量降低浇包与浇口的距离,控制浇注液流的大小,使金属液平稳流动和充型。
正确设计浇口杯的形状和尺寸,用扁圆形浇口杯替代圆锥形浇口杯,避免金属液直接进入直浇道。
横浇道可设计挡渣挡气装置,可采用开放式浇注系统。
对小型铸件或薄壁铸件不应浇注太快。
同时,提高金属液的熔炼质量对防止卷入气孔的产生具有很重要的作用。
3、防止析出气孔的措施炉料进炉前,对炉料应进行清理,保证炉料的清洁,可采用烘干和喷丸处理,去除炉料表面的氧化皮、油污和水分。
合理地选择熔炼设备和熔炼工艺,对要求比较高的铸件,可采用真空熔炼工艺。
严格控制炉料的配比,尽量降低废钢的用量。
采用各种脱气方法(如浮游气泡脱气、冷凝脱气)对金属液进行精炼,如铝合金熔炼应在铝液上面加覆盖剂并进行精炼;阻止气体析出,如铝合金铸件采用冷铁加速铸件的冷却。
浅谈铸件气孔的产生及其防止措施

浅谈铸件气孔的产生及其防止措施气孔是铸造生产中常见的铸件缺陷之一。
在铸件的废品中,据统计,由于气孔导致的铸件废品占废品总数的三分之一左右。
气孔是气体聚集在铸件表面、皮下和内部而形成的空洞。
气孔的孔壁光滑,无一定的形状、尺寸和位置。
气孔有各种类型,其产生的原因各不相同,按气体来源,一般将气孔分为三类:侵入性气孔、析出性气孔和反应性气孔。
一、侵入性气孔由于浇注过程中液态金属对铸型激烈的热作用,使型砂和芯砂中的发气物(水分、粘接剂等)气化、分解和燃烧,生成大量气体,加上型腔中原有的气体,这些气体部分侵入液态金属内部而不能逸出所产生的孔洞,称为侵入性气孔。
1.侵入性气孔的形成条件由于浇注时铸型在液态金属的高温作用下产生大量气体,从而使液态金属和铸型界面上的气体压力骤然增加,气体可能侵入液态金属,也有可能从型砂或冒口、出气孔中排出型外,只有在满足下列条件的情况下型(芯)砂中的气体才会侵入液态金属即P气>p液+p阻+p腔式中p气:液态金属和砂型界面的气体压力;P液:液态金属的静压力(p液=ρgh)P阻:气体侵入液态金属时,由于液态金属表面张力而引起的阻力P腔:型腔中液态金属液面上的气体压力2.防止侵入性气孔的主要方法和工艺措施(1)降低砂型(芯)界面的气体压力是最有效的手段。
如选用透气性好,发气量低的造型材料;控制型砂的水分及其它发气附加物;应用发气量低、发气速度慢、发气温度高的粘结剂;砂型(芯)排气要畅通,增加出气孔,提高铸型的排气能力;浇注后及时引火。
引火后可听到气体的爆燃声和砂箱周围燃烧的火焰,砂箱移开后,可看到下部潮湿的痕迹。
说明有大量的气体产生如H2、O2、CO、H2S等气体。
(2)适当提高浇注温度,延迟凝固时间,使侵入的气体有充分的时间从液态金属中上浮和逸出。
(3)加快浇注速度,增加上砂型高度,使有效压力头增加,提高液态金属的静压力。
(4)浇注系统在设置时,应注意液态金属流的平稳,浇注千万不能中断,防止气体卷入金属液中。
铸件气孔类缺陷的特征及预防措施
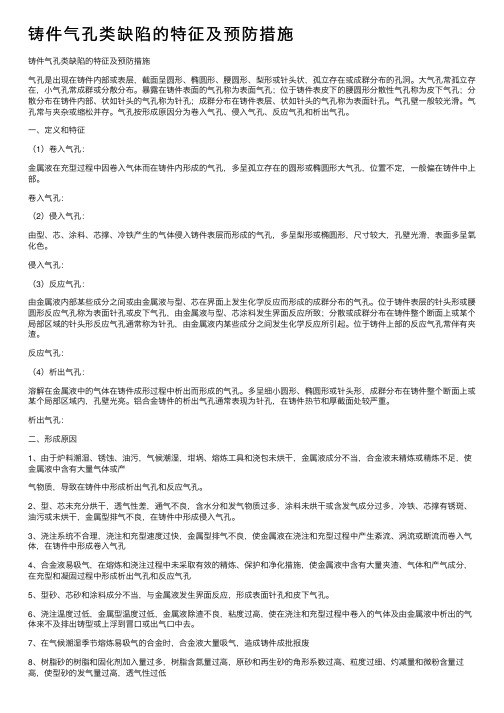
铸件⽓孔类缺陷的特征及预防措施铸件⽓孔类缺陷的特征及预防措施⽓孔是出现在铸件内部或表层,截⾯呈圆形、椭圆形、腰圆形、梨形或针头状,孤⽴存在或成群分布的孔洞。
⼤⽓孔常孤⽴存在,⼩⽓孔常成群或分散分布。
暴露在铸件表⾯的⽓孔称为表⾯⽓孔;位于铸件表⽪下的腰圆形分散性⽓孔称为⽪下⽓孔;分散分布在铸件内部、状如针头的⽓孔称为针孔;成群分布在铸件表层、状如针头的⽓孔称为表⾯针孔。
⽓孔壁⼀般较光滑。
⽓孔常与夹杂或缩松并存。
⽓孔按形成原因分为卷⼊⽓孔、侵⼊⽓孔、反应⽓孔和析出⽓孔。
⼀、定义和特征(1)卷⼊⽓孔:⾦属液在充型过程中因卷⼊⽓体⽽在铸件内形成的⽓孔,多呈孤⽴存在的圆形或椭圆形⼤⽓孔,位置不定,⼀般偏在铸件中上部。
卷⼊⽓孔:(2)侵⼊⽓孔:由型、芯、涂料、芯撑、冷铁产⽣的⽓体侵⼊铸件表层⽽形成的⽓孔,多呈梨形或椭圆形,尺⼨较⼤,孔壁光滑,表⾯多呈氧化⾊。
侵⼊⽓孔:(3)反应⽓孔:由⾦属液内部某些成分之间或由⾦属液与型、芯在界⾯上发⽣化学反应⽽形成的成群分布的⽓孔。
位于铸件表层的针头形或腰圆形反应⽓孔称为表⾯针孔或⽪下⽓孔,由⾦属液与型、芯涂料发⽣界⾯反应所致;分散或成群分布在铸件整个断⾯上或某个局部区域的针头形反应⽓孔通常称为针孔,由⾦属液内某些成分之间发⽣化学反应所引起。
位于铸件上部的反应⽓孔常伴有夹渣。
反应⽓孔:(4)析出⽓孔:溶解在⾦属液中的⽓体在铸件成形过程中析出⽽形成的⽓孔。
多呈细⼩圆形、椭圆形或针头形,成群分布在铸件整个断⾯上或某个局部区域内,孔壁光亮。
铝合⾦铸件的析出⽓孔通常表现为针孔,在铸件热节和厚截⾯处较严重。
析出⽓孔:⼆、形成原因1、由于炉料潮湿、锈蚀、油污,⽓候潮湿,坩埚、熔炼⼯具和浇包未烘⼲,⾦属液成分不当,合⾦液未精炼或精炼不⾜,使⾦属液中含有⼤量⽓体或产⽓物质,导致在铸件中形成析出⽓孔和反应⽓孔。
2、型、芯未充分烘⼲,透⽓性差,通⽓不良,含⽔分和发⽓物质过多,涂料未烘⼲或含发⽓成分过多,冷铁、芯撑有锈斑、油污或未烘⼲,⾦属型排⽓不良,在铸件中形成侵⼊⽓孔。
铸钢件气孔缺陷的分析及预防

铸钢件气孔缺陷的分析及预防铸钢件在工业生产中起着至关重要的作用,然而在铸钢件的制造过程中,气孔缺陷是一种常见的质量问题。
气孔缺陷会降低铸钢件的强度和硬度,影响其使用性能,严重时甚至会导致零部件的失效。
对铸钢件气孔缺陷进行分析并采取有效的预防措施,对于提高铸钢件的质量、延长零部件的使用寿命具有重要意义。
一、铸钢件气孔缺陷的成因分析1. 原料质量不良:铸造过程中使用的铸造原料如熔剂、砂型、砂芯等质量不良或含有杂质,会促使气体聚集并形成气孔。
2. 浇注过程不当:浇注过程中铸钢件内部的气体未能得到有效的排除,导致气孔的产生。
这与铸钢件的设计、浇注方式、浇注温度、浇注速度等因素密切相关。
3. 砂型和砂芯的设计不合理:砂型和砂芯的设计不合理、结构松散、容易剥落等都会导致气孔的产生。
4. 浇注温度过高:浇注温度过高会导致铸造原料的气体释放不完全,造成气孔缺陷。
5. 铸造工艺控制不当:在铸造工艺中,未能有效控制气体的排除和熔化金属的充填速度,是导致气孔缺陷产生的重要原因之一。
6. 熔化金属中含气过多:熔化金属中含气过多,未能得到有效的排除,会在铸钢件中形成气孔。
1. 优化原料选择:选择质量良好的铸造原料,尽可能减少熔剂、砂型、砂芯中的杂质含量。
2. 浇注过程的优化:合理设计浇注系统,采用适当的浇注方式和浇注温度,加强浇注过程中的气体排除。
3. 砂型和砂芯的优化:优化砂型和砂芯的设计,保证其结构紧密,避免砂型和砂芯剥落。
4. 控制熔化金属中的气体含量:采用适当的炉料和合理的炉前处理工艺,减少熔化金属中的气体含量。
5. 增强铸造工艺控制:加强铸造工艺中气体排除和熔化金属的充填控制,确保铸造工艺的稳定性和可靠性。
6. 合理设计铸造结构:在铸钢件的设计中,合理设计零部件的结构和形状,避免零部件内部的气体积聚,减少气孔的产生。
7. 强化检验和管控:强化对原料、砂型、砂芯、熔化金属和铸造工艺的检验和管控,确保所有加工环节都符合要求。
铸钢件气孔缺陷的分析及预防
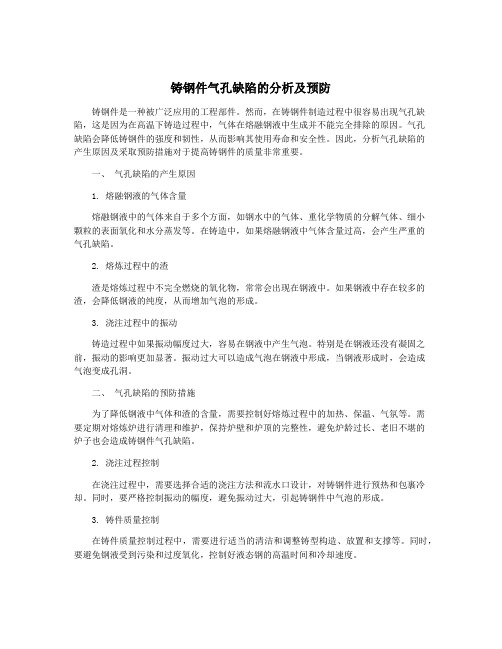
铸钢件气孔缺陷的分析及预防铸钢件是一种被广泛应用的工程部件。
然而,在铸钢件制造过程中很容易出现气孔缺陷,这是因为在高温下铸造过程中,气体在熔融钢液中生成并不能完全排除的原因。
气孔缺陷会降低铸钢件的强度和韧性,从而影响其使用寿命和安全性。
因此,分析气孔缺陷的产生原因及采取预防措施对于提高铸钢件的质量非常重要。
一、气孔缺陷的产生原因1. 熔融钢液的气体含量熔融钢液中的气体来自于多个方面,如钢水中的气体、重化学物质的分解气体、细小颗粒的表面氧化和水分蒸发等。
在铸造中,如果熔融钢液中气体含量过高,会产生严重的气孔缺陷。
2. 熔炼过程中的渣渣是熔炼过程中不完全燃烧的氧化物,常常会出现在钢液中。
如果钢液中存在较多的渣,会降低钢液的纯度,从而增加气泡的形成。
3. 浇注过程中的振动铸造过程中如果振动幅度过大,容易在钢液中产生气泡。
特别是在钢液还没有凝固之前,振动的影响更加显著。
振动过大可以造成气泡在钢液中形成,当钢液形成时,会造成气泡变成孔洞。
二、气孔缺陷的预防措施为了降低钢液中气体和渣的含量,需要控制好熔炼过程中的加热、保温、气氛等。
需要定期对熔炼炉进行清理和维护,保持炉壁和炉顶的完整性,避免炉龄过长、老旧不堪的炉子也会造成铸钢件气孔缺陷。
2. 浇注过程控制在浇注过程中,需要选择合适的浇注方法和流水口设计,对铸钢件进行预热和包裹冷却。
同时,要严格控制振动的幅度,避免振动过大,引起铸钢件中气泡的形成。
3. 铸件质量控制在铸件质量控制过程中,需要进行适当的清洁和调整铸型构造、放置和支撑等。
同时,要避免钢液受到污染和过度氧化,控制好液态钢的高温时间和冷却速度。
综上所述,铸钢件气孔缺陷是由于多种因素所引起的。
防止气孔缺陷的产生需要通过控制钢液中气体和渣的含量、严格控制振动幅度以及在铸件质量控制过程中进行适当的准备来实施。
只有采取有效的预防措施,才能提高铸钢件的质量和使用寿命。
- 1、下载文档前请自行甄别文档内容的完整性,平台不提供额外的编辑、内容补充、找答案等附加服务。
- 2、"仅部分预览"的文档,不可在线预览部分如存在完整性等问题,可反馈申请退款(可完整预览的文档不适用该条件!)。
- 3、如文档侵犯您的权益,请联系客服反馈,我们会尽快为您处理(人工客服工作时间:9:00-18:30)。
浅谈铸件砂眼气孔缺陷及预防措施
杨建林
上汽依维柯红岩商用有限公司铸造厂
摘要:本文介绍了用湿型砂生产铸钢件对预防砂眼、气孔的措施提供了宝贵的经验供同行参考。
关键词:铸钢件砂眼气孔
铸件在生产过程中经常会发生各种不同的铸造缺陷,如何预防这些缺陷,一直是铸件生产厂家关注的问题。
本文主要介绍了笔者在这方面的一些认识和实践经验。
我车间主要采用传统湿型砂铸造工艺生产铸钢件,在长期的生产中,发现铸钢件主要出现以下铸造缺陷,砂眼,粘砂,气孔,缩孔,夹砂结疤,胀砂等等。
现主要谈谈砂眼和气孔。
1 砂眼
2.1 特征
铸件上表面附近出现的形状不规则的,而且往往呈现紧实状态的型砂夹杂物。
往往在铸件的毛坯面上就能看出砂眼来,但有的可能要在切削加工后才露出来。
一般来说,铸件的其他部位上有大块的金属凸起物。
此外,如上述的缺陷,还带有2~6毫米深的凹孔,这类凹孔又或多或少地露出铸件表面。
且近邻处伴有夹砂。
那么,这一缺陷总是与夹砂结疤同时发生。
砂眼是一种常见的铸造缺陷,往往导致铸件报废。
2.2 缺陷原因
1) 砂型或砂芯上有砂块脱落;
2) 造型时不谨慎,散落砂落入型腔;
3) 冲砂或合型压坏;
4) 由于型砂膨胀,造成型壁表层脱落。
2.3 砂眼的预防措施:
(1) 严格控制型砂性能,提高砂型芯的表面强度和紧实度,减少毛刺和锐角,减少冲砂。
(2) 合箱前把型腔和砂芯表面的浮砂处理干净,平稳合箱,如果是明冒口或贯通出气眼,应避免散砂从中掉人型腔,合箱后要尽快浇注。
(3) 设置正确合理的浇冒系统,避免金属液对型壁和砂芯的冲刷力过大。
(4) 浇口杯表面要光滑,不能有浮砂。
2 气孔
2.1 特征
在铸件内部,表面或近于表面处,有大小不等的光滑孔眼,形状有圆的,长的及不规则的,有单个的,也有聚集成片的。
颜色有白色的或带一层暗色,有时覆有一层氧化皮。
2.2 缺陷原因:
气孔和针孔是由于在凝固过程中滞留在金属中的气体形成的。
然而,除气孔之外,这些气体还可能引起其他缺陷。
1) 熔炼方面的原因
(1) 熔池中的液态金属含有大量气体,溶解的气体在凝固时析出;
(2) 钢和铸铁件:碳和氧发生反应生成一氧化碳,并以气态或氧化物形式存在,一氧化碳形成的气孔可能因氢或氮的扩散而体积增加;
2) 造型或制芯材料产生气体
(1) 铸型或砂芯中水分过高
(2) 砂芯粘结剂的发气量大
(3) 含碳氢化物的附加量过多
(4) 涂料的发气量过大
3) 卷入的气体
(1) 型腔内的气体和空气未能及时排除
(2) 砂型和砂芯的透气性差
(3) 液态金属在浇注系统中产生紊流,卷入气体
2.3 气孔的预防措施:
(1) 采用洁净干燥的炉料,限制含气量较多的炉料的使用,降低熔炼时金属的吸气量;浇包要烘干烫包;可以适当提高浇注温度以利于气体扩散。
(2) 浇注时控制好压头和速度,保证钢水平稳充填砂型型腔,避免产生紊流,防止卷入气体。
(3) 减少发气量,控制型(芯)砂水分及发气原料的含量,减少砂型在浇注过程中的发气量,不
使用受潮,生锈或有油污的冷铁和芯撑等。
(4)改善砂型的透气性,选择合适的砂型紧实度,提高砂型和型芯的透气性;合理安排出气眼,使型(芯)内气体能顺利排出。
(5)提高气体进入金属液的阻力.合理设计浇注系统,避免浇注时卷入气体,在型(芯)表面涂刷涂料以减少少金属一铸型的界面作用。
对废品分析的几点参考
1) 很大的孔洞(大气孔)通常是外源气体引起的
2) 外源性气孔往往大小不一,可能是单个的,也可能是不规则地成群分布
3) 内源性气孔一般都比较小,大小一样且均匀分布于整个铸件或铸件的某一部分
4) 钢铁铸件中,氢气孔的内壁发亮,一氧化碳气孔呈浅兰色,卷入空气形成的气孔。
其内壁并没有轻度氧化呈灰色。
对缺陷进行简单的检查,往往不能作出正确的判断,通常还需要进行调查研究,然后再对熔炼和造型等因素进行调整。