电镀镍故障处理
电镀镍故障处理

电镀镍故障处理1,镀镍层发暗镀镍层表面发暗也是常见的电镀故障之一,这种故障多数出现在低电流密度区电镀获得的镀镍层,偶尔也出现在中电流密度区或高电流密度区,低电流密度区镀镍层发暗可能是镀镍液的温度太高,阴极电流密度太小,硫酸镍浓度太低;I,4一丁炔二醇或其他次级光亮剂过多或镀液中有铜、锌杂质污染引起;中电流密度区镀镍层发暗可能是由于镀液中次级光亮剂太少,有机杂质过多或有一定量的铁杂质污染造成的;高电流密度区镀层发暗可能是镀液pH值太高,初级光亮剂太少或镀液中有少量的铬酸盐、磷酸盐及铅杂质污染引起。
此外,镀前处理不良,镀件表面有碱膜或有机物吸附膜,或底镀层(氰化镀铜等)不好也会导致光亮镍镀层出现发暗现象。
可以取镀镍液做霍耳槽试验来分析这类电镀故障,对于低电流密度区出现的发暗现象,目前有的镀镍出现了比较好的走位剂,专门使得在低电流密度范围内获得光亮镀镍层。
另外还可以观察霍耳槽试片的外观进行逐步分析,如果镀液成分所做的霍耳槽样板上镀镍层状况良好,没有出现发暗的现象,那么电镀时出现的故障,就有可能是镀前处理不良或底镀层不好造成的,应该认真检查电镀镍前的情况。
若霍耳槽试验所得的阴极样板上出现低电流密度区镀层发暗,则可以根据前面提到的可能原因进行试验确定,或者加入合适的走位剂成分最后排除这种电镀故障。
中、高电流密度区的镀镍层发暗,也可用类似的方法进行试验分析。
2,镀镍层脆性镀层发脆,往往影响镀层的加工和质量,而且镀层的脆性与镀层应力有关。
镀镍液中次级光亮剂过多或初级光亮剂太少,铜、锌、铁或有机杂质过多,pH值过高或温度过低等都会使镀镍层发脆。
检查镀镍层脆性的方法,一是将镀好镍的小零件放在手中搓摩,或将镀镍薄片零件弯曲至18009若有碎镍层脱落,说明该镍层脆性大;另外就是将镍层镀在不锈钢试片上,控制镀层厚度在10ym左右,然后把镍层剥离下来,弯曲1800,用力挤压弯曲处,若不断裂,表示镀镍层不脆,弯曲折断,该镀镍层脆性就大。
镀镍问题与解决方案
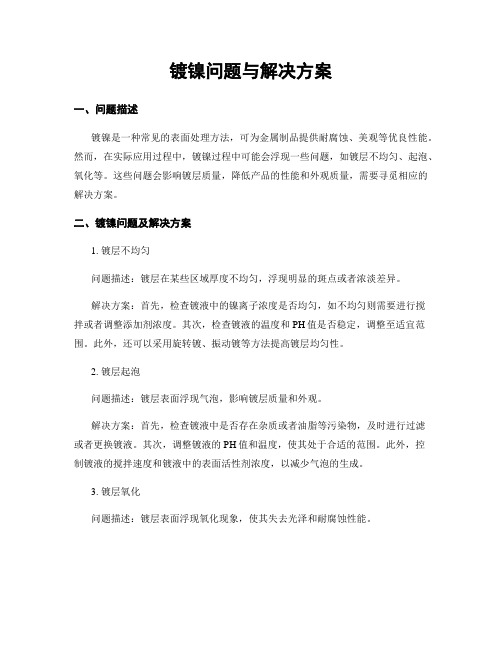
镀镍问题与解决方案一、问题描述镀镍是一种常见的表面处理方法,可为金属制品提供耐腐蚀、美观等优良性能。
然而,在实际应用过程中,镀镍过程中可能会浮现一些问题,如镀层不均匀、起泡、氧化等。
这些问题会影响镀层质量,降低产品的性能和外观质量,需要寻觅相应的解决方案。
二、镀镍问题及解决方案1. 镀层不均匀问题描述:镀层在某些区域厚度不均匀,浮现明显的斑点或者浓淡差异。
解决方案:首先,检查镀液中的镍离子浓度是否均匀,如不均匀则需要进行搅拌或者调整添加剂浓度。
其次,检查镀液的温度和PH值是否稳定,调整至适宜范围。
此外,还可以采用旋转镀、振动镀等方法提高镀层均匀性。
2. 镀层起泡问题描述:镀层表面浮现气泡,影响镀层质量和外观。
解决方案:首先,检查镀液中是否存在杂质或者油脂等污染物,及时进行过滤或者更换镀液。
其次,调整镀液的PH值和温度,使其处于合适的范围。
此外,控制镀液的搅拌速度和镀液中的表面活性剂浓度,以减少气泡的生成。
3. 镀层氧化问题描述:镀层表面浮现氧化现象,使其失去光泽和耐腐蚀性能。
解决方案:首先,检查镀液中的氧气含量,如过高则需要采取相应的措施减少氧气进入。
其次,加强镀液的过滤和除杂工作,减少镀液中的杂质对镀层的影响。
此外,可以采用添加剂或者改变镀液成份的方法,提高镀层的耐氧化性能。
4. 镀层粘附力不强问题描述:镀层与基材之间的粘附力不强,容易剥离或者脱落。
解决方案:首先,检查基材表面的清洁度和粗糙度,确保其符合镀层的要求。
其次,采用预处理方法,如酸洗、机械打磨等,增加基材与镀层之间的结合力。
此外,还可以调整镀液中的添加剂浓度和镀液的温度,以提高镀层的粘附力。
5. 镀层色差问题描述:镀层表面浮现色差,影响产品的外观质量。
解决方案:首先,检查镀液中的金属离子浓度和PH值是否稳定,调整至适宜范围。
其次,控制镀液的温度和搅拌速度,以保持镀层的一致性。
此外,可以采用添加剂或者改变镀液成份的方法,调整镀层的颜色。
电镀镍常见3大问题以及镀镍出现针孔故障解决办法
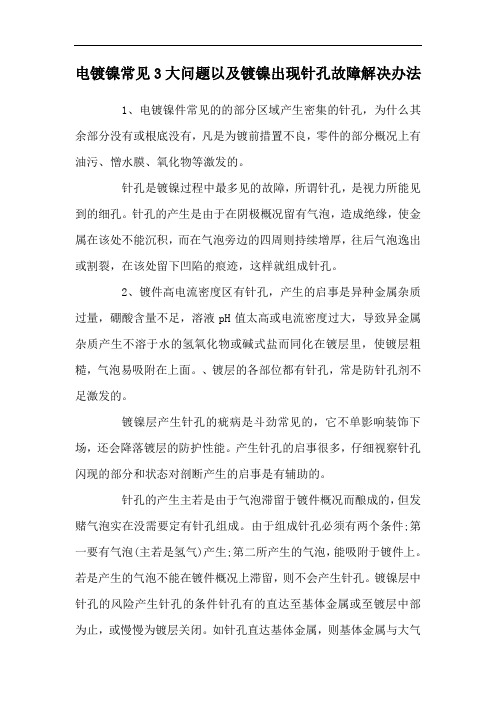
电镀镍常见3大问题以及镀镍出现针孔故障解决办法1、电镀镍件常见的的部分区域产生密集的针孔,为什么其余部分没有或根底没有,凡是为镀前措置不良,零件的部分概况上有油污、憎水膜、氧化物等激发的。
针孔是镀镍过程中最多见的故障,所谓针孔,是视力所能见到的细孔。
针孔的产生是由于在阴极概况留有气泡,造成绝缘,使金属在该处不能沉积,而在气泡旁边的四周则持续增厚,往后气泡逸出或割裂,在该处留下凹陷的痕迹,这样就组成针孔。
2、镀件高电流密度区有针孔,产生的启事是异种金属杂质过量,硼酸含量不足,溶液pH值太高或电流密度过大,导致异金属杂质产生不溶于水的氢氧化物或碱式盐而同化在镀层里,使镀层粗糙,气泡易吸附在上面。
、镀层的各部位都有针孔,常是防针孔剂不足激发的。
镀镍层产生针孔的疵病是斗劲常见的,它不单影响装饰下场,还会降落镀层的防护性能。
产生针孔的启事很多,仔细视察针孔闪现的部分和状态对剖断产生的启事是有辅助的。
针孔的产生主若是由于气泡滞留于镀件概况而酿成的,但发赌气泡实在没需要定有针孔组成。
由于组成针孔必须有两个条件;第一要有气泡(主若是氢气)产生;第二所产生的气泡,能吸附于镀件上。
若是产生的气泡不能在镀件概况上滞留,则不会产生针孔。
镀镍层中针孔的风险产生针孔的条件针孔有的直达至基体金属或至镀层中部为止,或慢慢为镀层关闭。
如针孔直达基体金属,则基体金属与大气接触,易被侵蚀。
如针孔止于镀层中部,则虽不致于马上被侵蚀,但总是镀层的弱点,耐侵蚀性能降落,也影响了镀层的雅观,在抛光后有拉延的痕迹,使故障加倍较着。
3、针孔的故障是一个相当复杂的问题问题,因独霸条件或溶液成分分歧标准而产生针孔,则解救尚易,只需改改独霸条件或调剂溶液成分使之合适请求便可能解决。
如因溶液有杂质(金属杂质或有机杂质)的传染而产生针孔,则必须找出其根源,隔靴搔痒,才干获得解决。
在没有杂质的景象下,一个简略而有用的编制为插手防针孔剂,在光泽性镀镍中可插手润湿剂如十二烷基硫酸钠,用量为~克/升。
电镀镍故障处理
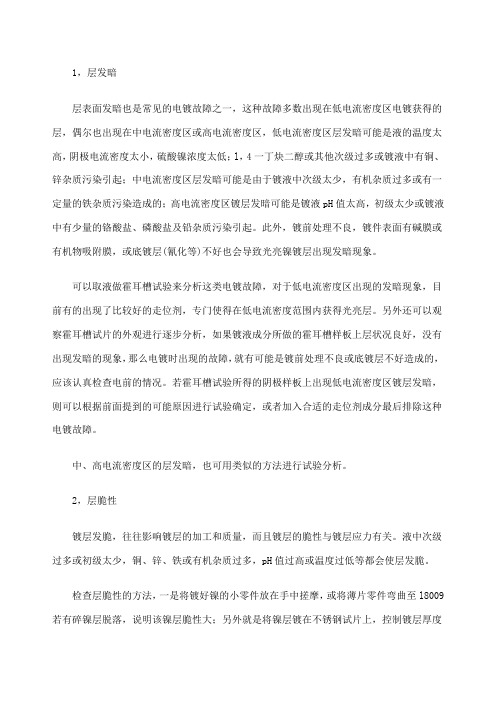
1,层发暗层表面发暗也是常见的电镀故障之一,这种故障多数出现在低电流密度区电镀获得的层,偶尔也出现在中电流密度区或高电流密度区,低电流密度区层发暗可能是液的温度太高,阴极电流密度太小,硫酸镍浓度太低;l,4一丁炔二醇或其他次级过多或镀液中有铜、锌杂质污染引起;中电流密度区层发暗可能是由于镀液中次级太少,有机杂质过多或有一定量的铁杂质污染造成的;高电流密度区镀层发暗可能是镀液pH值太高,初级太少或镀液中有少量的铬酸盐、磷酸盐及铅杂质污染引起。
此外,镀前处理不良,镀件表面有碱膜或有机物吸附膜,或底镀层(氰化等)不好也会导致光亮镍镀层出现发暗现象。
可以取液做霍耳槽试验来分析这类电镀故障,对于低电流密度区出现的发暗现象,目前有的出现了比较好的走位剂,专门使得在低电流密度范围内获得光亮层。
另外还可以观察霍耳槽试片的外观进行逐步分析,如果镀液成分所做的霍耳槽样板上层状况良好,没有出现发暗的现象,那么电镀时出现的故障,就有可能是镀前处理不良或底镀层不好造成的,应该认真检查电前的情况。
若霍耳槽试验所得的阴极样板上出现低电流密度区镀层发暗,则可以根据前面提到的可能原因进行试验确定,或者加入合适的走位剂成分最后排除这种电镀故障。
中、高电流密度区的层发暗,也可用类似的方法进行试验分析。
2,层脆性镀层发脆,往往影响镀层的加工和质量,而且镀层的脆性与镀层应力有关。
液中次级过多或初级太少,铜、锌、铁或有机杂质过多,pH值过高或温度过低等都会使层发脆。
检查层脆性的方法,一是将镀好镍的小零件放在手中搓摩,或将薄片零件弯曲至l8009若有碎镍层脱落,说明该镍层脆性大;另外就是将镍层镀在不锈钢试片上,控制镀层厚度在10μm左右,然后把镍层剥离下来,弯曲1800,用力挤压弯曲处,若不断裂,表示层不脆,弯曲折断,该层脆性就大。
产生镍层脆性的原因,若镀液pH值和温度没有问题,那么可能是镀液中光亮添加剂比例失调或镀液中杂质的造成的,由于光亮添加剂比例失调造成的脆性可以通过提高糖精添加剂(或其他应力消除成分)的含量来改善,通过补充糖槔等成分,观察层脆性是否改善来判断。
实战:光亮镀镍故障处理解决方案

实战:光亮镀镍故障处理解决方案1前言镀镍是常见的镀种之一,它已从普通镀镍(暗镍)发展到全光亮镀镍,镀镍用的光亮剂也从无机光亮剂发展到第四代有机光亮剂。
电镀行业现用的全光亮镀镍槽液基本上是瓦特型,其配方及工艺规范除浓缩型光亮剂外,基本上大同小异。
镀镍出现故障时,应检查工艺执行情况,分析故障出现的原因,将其解决。
2故障产生原因及排除方法2.1工艺失衡2.1.1镀层光亮度不足2.1.1.1产生原因(1)光亮剂太少,主盐含量太低,阳极板太短太少,镍离子的沉积速度与迁移速度达不到平衡,致使镀层光亮度不足。
(2)pH和温度太高。
此时主盐易水解成Ni(OH)2沉淀,部分Ni(OH)2夹杂在镀层中,造成镀层光亮度不足。
(3)酸性镀铜后,零件未洗净。
此时零件表面(铜层)上有一层碱性膜,镍沉积在膜层上,致使镀层达不到镜面光亮。
2.1.1.2排除方法(1)补充主光亮剂,相应地也需补充助光剂。
按工艺要求调整主盐及其它组成,增加阳极镍板。
(2)用稀硫酸调节pH,降低温度至工艺规范。
(3)酸性镀铜后应彻底洗净零件,必要时可用稀硫酸除膜。
2.1.2镀镍层呈橘皮状2.1.2.1产生原因镀液pH太高,润湿剂过量时,润湿剂易与Ni2+作用,生成不溶性的化合物,杂乱地吸附(或沉淀)在零件表面上,造成镀层厚薄不均。
2.1.2.2排除方法加入少量活性炭吸附掉部分润湿剂,过滤后再用稀硫酸调节pH至工艺规范。
2.1.3镍层易烧焦2.1.3.1产生原因镀液中主盐太少,温度太低,pH过高,电流密度太大。
镍沉积的过程中,失去Ni2+的量与迁移到阴极附近的Ni2+量需达到动态平衡。
但是,由于主盐太少,温度太低,很低浓度的Ni2+在低温条件下只能缓慢地迁移到阴极附近放电沉积。
同时,pH太高使本来就很稀少的Ni2+还有部分生成微溶于水的浅绿色Ni(OH)2沉淀,造成镀液中Ni2+更少。
在大电流密度作用下,阴极附近的正负离子达不到平衡,致使镀层烧焦。
2.1.3.2排除方法按分析报告补充主盐,提高镀液温度,用稀硫酸调节pH至工艺规范,过滤镀液,适当调整电流密度。
镀镍问题与解决方案
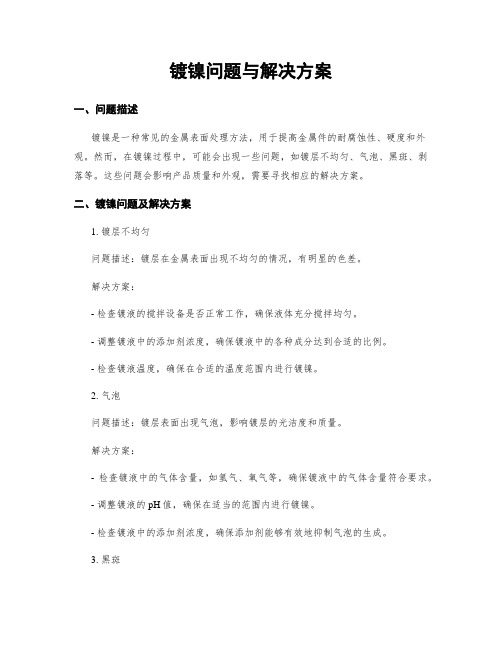
镀镍问题与解决方案一、问题描述镀镍是一种常见的金属表面处理方法,用于提高金属件的耐腐蚀性、硬度和外观。
然而,在镀镍过程中,可能会出现一些问题,如镀层不均匀、气泡、黑斑、剥落等。
这些问题会影响产品质量和外观,需要寻找相应的解决方案。
二、镀镍问题及解决方案1. 镀层不均匀问题描述:镀层在金属表面出现不均匀的情况,有明显的色差。
解决方案:- 检查镀液的搅拌设备是否正常工作,确保液体充分搅拌均匀。
- 调整镀液中的添加剂浓度,确保镀液中的各种成分达到合适的比例。
- 检查镀液温度,确保在合适的温度范围内进行镀镍。
2. 气泡问题描述:镀层表面出现气泡,影响镀层的光洁度和质量。
解决方案:- 检查镀液中的气体含量,如氢气、氧气等,确保镀液中的气体含量符合要求。
- 调整镀液的pH值,确保在适当的范围内进行镀镍。
- 检查镀液中的添加剂浓度,确保添加剂能够有效地抑制气泡的生成。
3. 黑斑问题描述:镀层表面出现黑斑,影响产品的外观质量。
解决方案:- 检查镀液中的杂质含量,如铁离子等,确保镀液中的杂质含量达到要求。
- 检查镀液的过滤设备,确保能够有效地去除镀液中的杂质。
- 调整镀液的pH值,确保在适当的范围内进行镀镍。
4. 剥落问题描述:镀层容易剥落,降低产品的耐腐蚀性和使用寿命。
解决方案:- 检查镀液中的添加剂浓度,确保添加剂能够提供足够的附着力。
- 检查镀液中的金属离子浓度,如镍离子等,确保金属离子的浓度符合要求。
- 检查金属基材的表面处理情况,确保金属基材的清洁度和粗糙度符合要求。
三、结论镀镍问题的解决方案需要综合考虑镀液的成分、工艺参数和设备状况等多个因素。
通过调整镀液的配方、控制工艺参数和改进设备,可以解决镀层不均匀、气泡、黑斑和剥落等问题,提高镀层的质量和外观。
在实际应用中,还需根据具体情况进行调整和优化,以达到最佳的镀镍效果。
电镀镍故障处理

精心整理1,镀镍层发暗镀镍层表面发暗也是常见的电镀故障之一,这种故障多数出现在低电流密度区电镀获得的镀镍层,偶尔也出现在中电流密度区或高电流密度区,低电流密度区镀镍层发暗可能是镀镍液的温度太高,阴极电流密度太小,硫酸镍浓度太低;l,4一丁炔二醇或其他次级光亮剂过多或镀液中有铜、锌杂质污染引起;中电流密度区镀镍层发暗可能是由于镀液中次级光亮剂太少,有机杂质过多或有一定量的铁杂质污染造成的;高电流密度区镀层发暗可能是镀液pH值太高,初级光亮剂太少或镀液中有少量的铬酸盐、磷酸盐及铅杂质污染引起。
此外,镀前处理不良,镀件表面有碱膜或有机物吸附膜,或底镀层(氰化镀铜等)不好也会导致光亮镍镀层出现发暗现象。
可以取镀镍液做霍耳槽试验来分析这类电镀故障,对于低电流密度区出现的发暗现象,目前有的镀镍出现了比较好的走位剂,镀镍前的情况。
2液中次级光亮剂过多或初级脆。
l800910μm或其并当镀镍或其他次级光亮剂)含量低,镀层的光亮度差,不能获得镜面光亮镀层。
可以通过霍耳槽试验分析排故,镀镍层光亮度差,可向镀液中加入适量的1,4一丁炔二醇(或其他次级光亮剂),使阴极样板上镀层的光亮度提高,而且保证高电流密度处镀镍层不脆裂,低电流密度处镀层不出现灰暗。
1,4一丁炔二醇(或其他次级光亮剂)含量高,镀镍层光亮,但镀层的张应力也会提高,并导致镍镀层发脆,次级光亮剂含量过高,镍镀层亮而发乌,零件低电流密度区镀层灰暗,高电流密度区镀层脆裂。
这种情况可适当提高镀液中糖精含量(保持初级与次级光亮剂比例适当)和电解处理,使镀镍液恢复正常;次级光亮剂含量过多时,需要电解时间增长或用活性炭处理排除此种光亮镀镍故障。
3,橘皮状镀镍层精心整理有时光照下镀镍层呈现出隐隐的波纹状现象(橘皮状镀层)。
这表明与镀前处理不良,镀液中有油或有胶类杂质,十二烷基硫酸钠过多、异金属杂质过多或镀液中有未过滤掉的活性炭粉末等的影响导致橘皮状镀镍层的产生。
十二烷基硫酸钠可以降低镀件和溶液之间的界面张力,使溶液润湿镀件,防镀镍层产生针孔,所以它既是润湿剂,又有防针孔的功效。
镀镍问题与解决方案
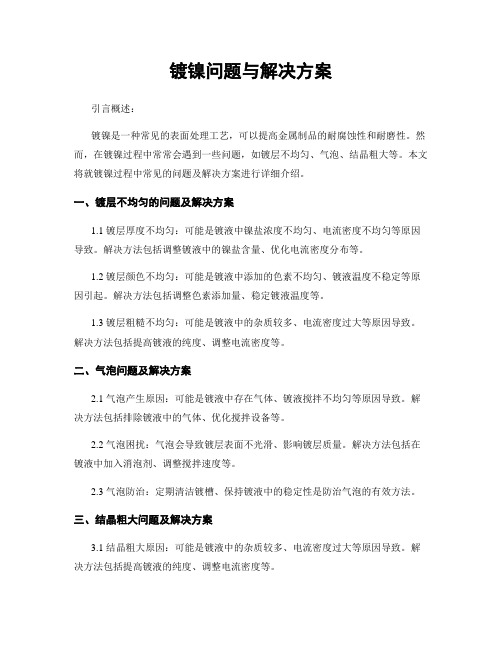
镀镍问题与解决方案引言概述:镀镍是一种常见的表面处理工艺,可以提高金属制品的耐腐蚀性和耐磨性。
然而,在镀镍过程中常常会遇到一些问题,如镀层不均匀、气泡、结晶粗大等。
本文将就镀镍过程中常见的问题及解决方案进行详细介绍。
一、镀层不均匀的问题及解决方案1.1 镀层厚度不均匀:可能是镀液中镍盐浓度不均匀、电流密度不均匀等原因导致。
解决方法包括调整镀液中的镍盐含量、优化电流密度分布等。
1.2 镀层颜色不均匀:可能是镀液中添加的色素不均匀、镀液温度不稳定等原因引起。
解决方法包括调整色素添加量、稳定镀液温度等。
1.3 镀层粗糙不均匀:可能是镀液中的杂质较多、电流密度过大等原因导致。
解决方法包括提高镀液的纯度、调整电流密度等。
二、气泡问题及解决方案2.1 气泡产生原因:可能是镀液中存在气体、镀液搅拌不均匀等原因导致。
解决方法包括排除镀液中的气体、优化搅拌设备等。
2.2 气泡困扰:气泡会导致镀层表面不光滑、影响镀层质量。
解决方法包括在镀液中加入消泡剂、调整搅拌速度等。
2.3 气泡防治:定期清洁镀槽、保持镀液中的稳定性是防治气泡的有效方法。
三、结晶粗大问题及解决方案3.1 结晶粗大原因:可能是镀液中的杂质较多、电流密度过大等原因导致。
解决方法包括提高镀液的纯度、调整电流密度等。
3.2 结晶粗大影响:结晶粗大会导致镀层表面不光滑、影响镀层的耐腐蚀性能。
解决方法包括优化镀液成分、控制电流密度等。
3.3 结晶粗大防治:定期清洁镀槽、保持镀液中的稳定性是防治结晶粗大的有效方法。
四、镀液稳定性问题及解决方案4.1 镀液变质原因:可能是镀液中的添加剂浓度不稳定、镀槽温度波动等原因导致。
解决方法包括定期检测镀液成分、保持镀槽温度稳定等。
4.2 镀液变质影响:镀液变质会导致镀层质量下降、影响镀层的性能。
解决方法包括及时更换镀液、加强镀液管理等。
4.3 镀液变质防治:定期监测镀液质量、避免镀液受到外界污染是防治镀液变质的有效方法。
五、镀层质量检测问题及解决方案5.1 镀层质量检测方法:常用的镀层质量检测方法包括厚度测量、硬度测试、显微镜观察等。
镀镍常见故障及解决办法

镀镍常见故障及解决办法(1)沉速低镀液pH值过低:测pH值调整,并控制pH在下限值。
虽然pH值较高能提高沉速,但会影响镀液稳定性。
镀液温度过低:要求温度达到规范时下槽进行施镀。
新开缸第一批工件下槽时,温度应达到上限,反应开始后,正常施镀时,温度在下限为好。
溶液主成分浓度低:分析调整,如还原剂不足时,添加还原补充液;镍离子浓度偏低时,添加镍盐补充液。
对于上规模的化学镀镍,设自动分析、补给装置是必要的,可以延长连续工作时间(由30h延至56h)和镍循环周期(由6周延至11周)。
亚磷酸根过多:弃掉部分镀液。
装载量太低:增加受镀面积至1dm2/L。
稳定剂浓度偏重:倾倒部分,少量多次加浓缩液。
(2)镀液分解(镀液呈翻腾状,出现镍粉)温度过高或局部过热:搅拌下加入温去离子水。
次亚磷酸钠大多:冲稀补加其它成分。
镀液的pH值过高:调整pH值至规范值。
机械杂质:过滤除去。
装载量过高:降至1dm2/L槽壁或设备上有沉淀物:滤出镀液,退镀清洗(用3%HNO3溶液)。
操作温度下补加液料大多:搅拌下少量多次添加。
稳定剂带出损失:添加少量稳定剂。
催化物质带入镀液:加强镀前清洗。
镀层剥离碎片:过滤镀液。
(3)镀层结合力差或起泡镀前处理不良:提高工作表面的质量,加工完成后应清除工件上所有的焊接飞溅物和焊渣。
工件表面的粗糙度应达到与精饰要求相当的粗糙义,如碳钢工件表面粗糙度Ra<1.75μm时,很难获得有良好附着力的镀层;对于严重锈蚀的非加工表面,可用角向磨光机打磨,最好采用喷砂或喷丸处理;工件镀前适当的活化处理可以提高镀层的附着力。
如合金钢、钛合金可用含氟化物的盐酸活化后,与碳钢件混装施镀;高级合金钢和铅基合金预镀化学镍;碳钢活化时注意脱碳。
温度波动太大:控制温度在较小的范围波动。
下槽温度太低:适当提高下槽温度。
清洗不良:改进清洗工序。
金属离子污染:用大面积废件镀而除去。
有机杂质污染:活化炭1-2g/L 处理。
热处理不当:调整热处理时间和温度。
电镀镍常见九大故障解决办法

电镀镍常见九大故障解决办法电镀镍的不良主要在:前处理不良、有金属杂质、硼酸含量太少、镀液温度太低都会导致电镀镍层出现针孔,而镀液维护及严格控制流程是关键所在。
解决好以下这“九”大故障,基本问题就控制住了。
1)麻坑(针孔)麻坑(针孔)是有机物污染的结果。
大的麻坑通常说明有油污染要分解油污碳处理了。
搅拌不良,就不能驱逐掉气泡,就会形成麻坑(针孔)可以使用润湿剂来减小其影响。
2)粗糙(毛刺)粗糙就说明溶液脏经充分过滤就可纠正值太高易形成氢氧化物沉淀,应加以控制;电流密度太高、阳极泥及补加水不纯带人杂质,严重时都将产生粗糙(毛刺)。
3)结合力低如果铜镀层未经活化去除氧化层铜和镍之间的附着力就差,就会产生镀层剥落现象。
如果电流中断有可能会造成镍镀层的自身剥落;温度太低,也会产生剥落现象。
4)镀层脆、可焊性差当镀层受弯曲或受到一定程度的磨损时,通常会显露出镀层的脆性,这就表明存在有机物或重金属物质污染。
添加剂过多,使镀层中夹带的有机物和分解产物增多,是有机物污染的主要来源,可用活性炭加以处理;重金属杂质可用电解等方法除去。
5)镀层发暗和色泽不均匀镀层发暗和色泽不均匀说明有金属污染。
因为一般都是先镀铜后镀镍,所以带人的铜溶液是主要的污染源。
重要的是,要把挂具所沾的铜溶液减少到最低程度,为了消除镀镍槽中的金属污染,采用波纹钢板作阴极,在02-0.5A/dm2的电流密度下电解处理。
前处理不良、底镀层不良、电流密度太小、主盐浓度太低、导电接触不良都会影响镀层色泽。
6)镀层烧焦硼酸不足、金属盐的浓度低、工作温度太低、电流密度太高、PH 值太高或搅拌不充分都是引起镀层烧焦的可能原因7)沉积速率低值低或电流密度低都会造成沉积速率低。
8)镀层起泡或起皮镀前处理不良、中间断电时间过长、有机杂质污染、电流密度过大、温度太低、PH值太高或太低、杂质的影响严重时会产生起泡或起皮现象。
9)阳极钝化阳极活化剂(氯化镍)不足、阳极面积太小、电流密度太高都会导致阳极钝化。
电镀镍常见3大问题以及镀镍出现针孔故障解决办法

电镀镍常见3大问题以及镀镍出现针孔故障解决办法1、电镀镍件常见的的部分区域产生密集的针孔,为什么其余部分没有或根底没有,凡是为镀前措置不良,零件的部分概况上有油污、憎水膜、氧化物等激发的。
针孔是镀镍过程中最多见的故障,所谓针孔,是视力所能见到的细孔。
针孔的产生是由于在阴极概况留有气泡,造成绝缘,使金属在该处不能沉积,而在气泡旁边的四周则持续增厚,往后气泡逸出或割裂,在该处留下凹陷的痕迹,这样就组成针孔。
2、镀件高电流密度区有针孔,产生的启事是异种金属杂质过量,硼酸含量不足,溶液pH值太高或电流密度过大,导致异金属杂质产生不溶于水的氢氧化物或碱式盐而同化在镀层里,使镀层粗糙,气泡易吸附在上面。
、镀层的各部位都有针孔,常是防针孔剂不足激发的。
镀镍层产生针孔的疵病是斗劲常见的,它不单影响装饰下场,还会降落镀层的防护性能。
产生针孔的启事很多,仔细视察针孔闪现的部分和状态对剖断产生的启事是有辅助的。
针孔的产生主若是由于气泡滞留于镀件概况而酿成的,但发赌气泡实在没需要定有针孔组成。
由于组成针孔必须有两个条件;第一要有气泡(主若是氢气)产生;第二所产生的气泡,能吸附于镀件上。
若是产生的气泡不能在镀件概况上滞留,则不会产生针孔。
镀镍层中针孔的风险产生针孔的条件针孔有的直达至基体金属或至镀层中部为止,或慢慢为镀层关闭。
如针孔直达基体金属,则基体金属与大气接触,易被侵蚀。
如针孔止于镀层中部,则虽不致于马上被侵蚀,但总是镀层的弱点,耐侵蚀性能降落,也影响了镀层的雅观,在抛光后有拉延的痕迹,使故障加倍较着。
3、针孔的故障是一个相当复杂的问题问题,因独霸条件或溶液成分分歧标准而产生针孔,则解救尚易,只需改改独霸条件或调剂溶液成分使之合适请求便可能解决。
如因溶液有杂质(金属杂质或有机杂质)的传染而产生针孔,则必须找出其根源,隔靴搔痒,才干获得解决。
在没有杂质的景象下,一个简略而有用的编制为插手防针孔剂,在光泽性镀镍中可插手润湿剂如十二烷基硫酸钠,用量为0.01~0.05克/升。
电镀镍工艺的故障处理与分析
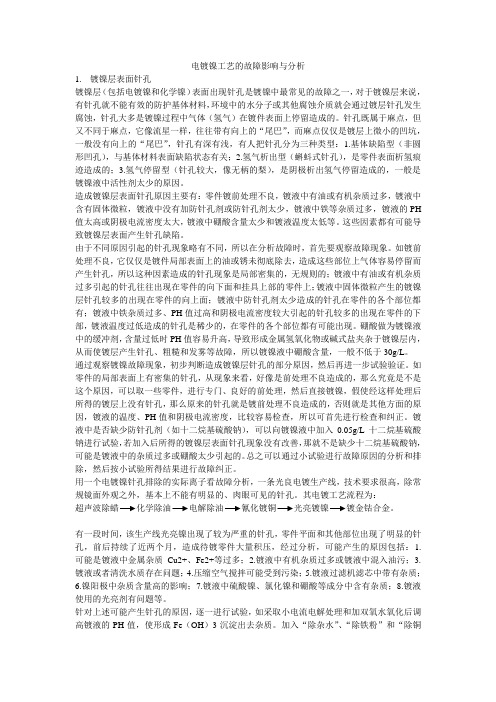
电镀镍工艺的故障影响与分析1.镀镍层表面针孔镀镍层(包括电镀镍和化学镍)表面出现针孔是镀镍中最常见的故障之一,对于镀镍层来说,有针孔就不能有效的防护基体材料,环境中的水分子或其他腐蚀介质就会通过镀层针孔发生腐蚀,针孔大多是镀镍过程中气体(氢气)在镀件表面上停留造成的。
针孔既属于麻点,但又不同于麻点,它像流星一样,往往带有向上的“尾巴”,而麻点仅仅是镀层上微小的凹坑,一般没有向上的“尾巴”,针孔有深有浅,有人把针孔分为三种类型:1.基体缺陷型(非圆形凹孔),与基体材料表面缺陷状态有关;2.氢气析出型(蝌蚪式针孔),是零件表面析氢痕迹造成的;3.氢气停留型(针孔较大,像无柄的梨),是阴极析出氢气停留造成的,一般是镀镍液中活性剂太少的原因。
造成镀镍层表面针孔原因主要有:零件镀前处理不良,镀液中有油或有机杂质过多,镀液中含有固体微粒,镀液中没有加防针孔剂或防针孔剂太少,镀液中铁等杂质过多,镀液的PH 值太高或阴极电流密度太大,镀液中硼酸含量太少和镀液温度太低等。
这些因素都有可能导致镀镍层表面产生针孔缺陷。
由于不同原因引起的针孔现象略有不同,所以在分析故障时,首先要观察故障现象。
如镀前处理不良,它仅仅是镀件局部表面上的油或锈未彻底除去,造成这些部位上气体容易停留而产生针孔,所以这种因素造成的针孔现象是局部密集的,无规则的;镀液中有油或有机杂质过多引起的针孔往往出现在零件的向下面和挂具上部的零件上;镀液中固体微粒产生的镀镍层针孔较多的出现在零件的向上面;镀液中防针孔剂太少造成的针孔在零件的各个部位都有;镀液中铁杂质过多、PH值过高和阴极电流密度较大引起的针孔较多的出现在零件的下部,镀液温度过低造成的针孔是稀少的,在零件的各个部位都有可能出现。
硼酸做为镀镍液中的缓冲剂,含量过低时PH值容易升高,导致形成金属氢氧化物或碱式盐夹杂于镀镍层内,从而使镀层产生针孔、粗糙和发雾等故障,所以镀镍液中硼酸含量,一般不低于30g/L。
镀镍问题与解决方案
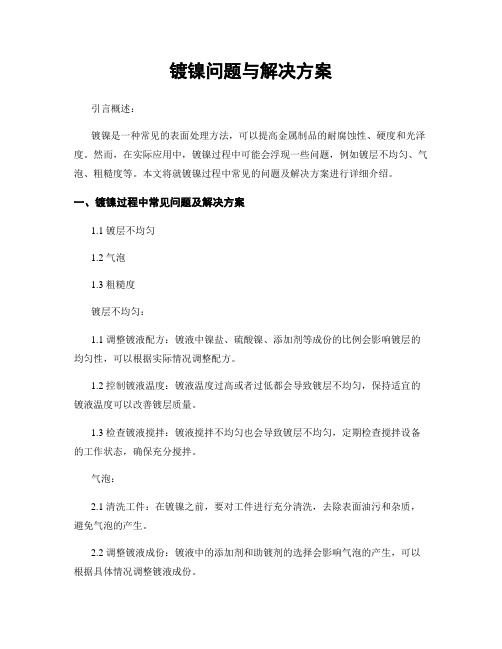
镀镍问题与解决方案引言概述:镀镍是一种常见的表面处理方法,可以提高金属制品的耐腐蚀性、硬度和光泽度。
然而,在实际应用中,镀镍过程中可能会浮现一些问题,例如镀层不均匀、气泡、粗糙度等。
本文将就镀镍过程中常见的问题及解决方案进行详细介绍。
一、镀镍过程中常见问题及解决方案1.1 镀层不均匀1.2 气泡1.3 粗糙度镀层不均匀:1.1 调整镀液配方:镀液中镍盐、硫酸镍、添加剂等成份的比例会影响镀层的均匀性,可以根据实际情况调整配方。
1.2 控制镀液温度:镀液温度过高或者过低都会导致镀层不均匀,保持适宜的镀液温度可以改善镀层质量。
1.3 检查镀液搅拌:镀液搅拌不均匀也会导致镀层不均匀,定期检查搅拌设备的工作状态,确保充分搅拌。
气泡:2.1 清洗工件:在镀镍之前,要对工件进行充分清洗,去除表面油污和杂质,避免气泡的产生。
2.2 调整镀液成份:镀液中的添加剂和助镀剂的选择会影响气泡的产生,可以根据具体情况调整镀液成份。
2.3 控制镀液搅拌速度:搅拌速度过快或者过慢都会导致气泡的产生,控制好搅拌速度可以减少气泡问题。
粗糙度:3.1 调整镀液温度:镀液温度过高或者过低都会导致镀层粗糙,保持适宜的镀液温度可以改善镀层质量。
3.2 检查镀液PH值:镀液PH值的变化也会影响镀层的粗糙度,定期检查PH 值并进行调整。
3.3 检查工件表面处理:工件表面处理不当也会导致镀层粗糙,确保工件表面平整光滑可以减少粗糙度问题。
四、结语镀镍是一种常见的表面处理方法,但在实际应用中可能会浮现一些问题。
通过调整镀液配方、控制镀液温度、检查镀液搅拌等方法,可以有效解决镀镍过程中的常见问题,提高镀层质量。
希翼本文的介绍对大家在镀镍过程中遇到问题时有所匡助。
镀镍故障及处理方法

镀镍故障及处理方法镀镍常见故障及处理方法2 Watts型镀光亮镍(见表1)项目规范作用及要求硫酸镍(NiSO4?6H20) 170—450g;L 导电盐,提供廉价镍离子氯化镍(NiCl2?6H20) 37.5-150g;L 1:导电盐,提供镍离子2:氯离子,促进阳极溶解。
含量太高,阳极溶解太快,并使镀层缺乏柔韧性镍总量 43~137g;L 太低,因扩散慢而影响阴极电流密度上限?太高,带出损失严重。
镍总量与工件复杂程度相关硼酸 37.5~56:3g;L pH缓冲剂,减少针孔,提高阴极电流密度上限pH值3~5(一般4.0~4.8) 低pH倾向~增加柔韧性,减少硬度和阴极电流效率高pH倾向~减少柔韧性,增加硬度,略微增加阴极电流效率温度 50~70?120~160? 低温倾向于~高硬度低柔韧性镀层,生产效率低高温有利于降低电压,强化生产,增加镀层柔韧性阴极电流密度1.08—10.8A/dm2 太低,生产效率低,锌、铜杂质易析出太高,镀层易烧焦,铝、硅、磷杂质易析出阳极及其电流密度?3.25A/dm2空气搅拌?1.95A/dm2其它搅拌避免阳极钝化,使电解体系稳定阳极面积要及时调整,使施镀更加趋于一致搅拌需要提高电流密度上限,便于镀液浓度、温度均匀一致,减少针孔麻点。
空气搅拌要均匀,否则,二次电流分布不同,浓度高低不同,难于施镀均一添加剂适量没有添加剂,镀层显灰暗色添加剂(Carrior,即柔软剂、开缸剂等)的浓度范围较宽,对镀层影响较小?)主亮剂浓度范围较窄,要少加勤加,否则,柔韧性、套铬性能和分散能力将受到影响。
低浓度)主亮剂产生灰暗、填平性差的镀层,高浓度光亮剂光亮、填平极好,但脆性大,套铬性能差,高内应力,漏镀,对各种杂质容忍度下降3 镀镍故障电镀的许多故障是经过“量”的积累才“质”的发现。
我们今天所关注的焦点在镍槽中。
许多复杂的问题往11/7页往让我们判断不清铜、锌杂质都在低电流密度区,铝和硅都在高电流密度区均形成无光泽镀层,如何区分?成片的微细针孔被误认为是粗糙面铬杂质的影响,误认为主光剂加入过量,锌杂质的影响被误认为套铬低电流不佳?硼酸不足,被认为缺乏湿润剂等等。
镀镍常见故障及解决办法
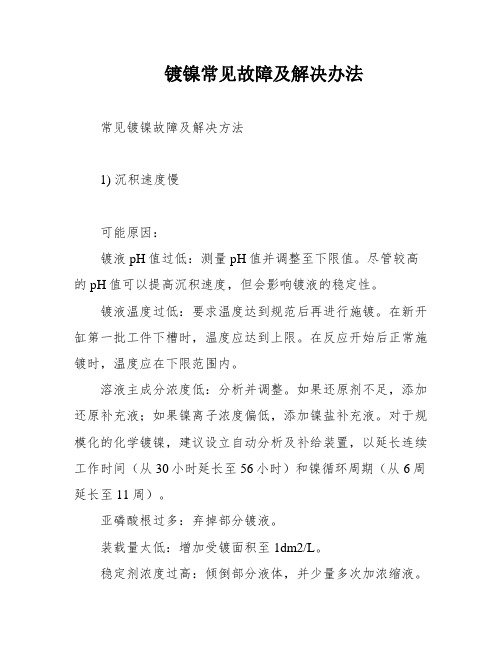
镀镍常见故障及解决办法常见镀镍故障及解决方法1) 沉积速度慢可能原因:镀液pH值过低:测量pH值并调整至下限值。
尽管较高的pH值可以提高沉积速度,但会影响镀液的稳定性。
镀液温度过低:要求温度达到规范后再进行施镀。
在新开缸第一批工件下槽时,温度应达到上限。
在反应开始后正常施镀时,温度应在下限范围内。
溶液主成分浓度低:分析并调整。
如果还原剂不足,添加还原补充液;如果镍离子浓度偏低,添加镍盐补充液。
对于规模化的化学镀镍,建议设立自动分析及补给装置,以延长连续工作时间(从30小时延长至56小时)和镍循环周期(从6周延长至11周)。
亚磷酸根过多:弃掉部分镀液。
装载量太低:增加受镀面积至1dm2/L。
稳定剂浓度过高:倾倒部分液体,并少量多次加浓缩液。
2) 镀液分解(镀液呈翻腾状,出现镍粉)可能原因:温度过高或局部过热:在搅拌的同时加入温去离子水。
次亚磷酸钠过多:冲稀补加其他成分。
镀液的pH值过高:调整pH值至规范值。
机械杂质:过滤除去。
装载量过高:降至1dm2/L。
槽壁或设备上有沉淀物:滤出镀液,退镀清洗(使用3% HNO3溶液)。
在操作温度下,少量多次添加补给液。
稳定剂带出损失:添加少量稳定剂。
催化物质带入镀液:加强镀前清洗。
镀层剥离碎片:过滤镀液。
3) 镀层结合力差或起泡可能原因:镀前处理不良:提高工作表面的质量。
加工完成后应清除工件上所有的焊接飞溅物和焊渣。
工件表面的粗糙度应达到与精饰要求相当的粗糙度。
如碳钢工件表面粗糙度Ra<1.75μm 时,很难获得有良好附着力的镀层。
对于严重锈蚀的非加工表面,可用角向磨光机打磨,最好采用喷砂或喷丸处理。
工件镀前适当的活化处理可以提高镀层的附着力。
如合金钢、钛合金可用含氟化物的盐酸活化后,与碳钢件混装施镀;高级合金钢和铅基合金预镀化学镍;碳钢活化时注意脱碳。
温度波动太大:控制温度在较小的范围内波动。
下槽温度太低:适当提高下槽温度。
清洗不良:改进清洗工序。
金属离子污染:用大面积废件镀而除去。
电镀镍常见3大问题以及镀镍出现针孔故障解决办法

电镀镍常见3大问题以及镀镍出现针孔故障解决办法1、电镀镍件常见的的部分区域产生密集的针孔,为什么其余部分没有或根底没有,凡是为镀前措置不良,零件的部分概况上有油污、憎水膜、氧化物等激发的。
针孔是镀镍过程中最多见的故障,所谓针孔,是视力所能见到的细孔。
针孔的产生是由于在阴极概况留有气泡,造成绝缘,使金属在该处不能沉积,而在气泡旁边的四周则持续增厚,往后气泡逸出或割裂,在该处留下凹陷的痕迹,这样就组成针孔。
2、镀件高电流密度区有针孔,产生的启事是异种金属杂质过量,硼酸含量不足,溶液pH值太高或电流密度过大,导致异金属杂质产生不溶于水的氢氧化物或碱式盐而同化在镀层里,使镀层粗糙,气泡易吸附在上面。
、镀层的各部位都有针孔,常是防针孔剂不足激发的。
镀镍层产生针孔的疵病是斗劲常见的,它不单影响装饰下场,还会降落镀层的防护性能。
产生针孔的启事很多,仔细视察针孔闪现的部分和状态对剖断产生的启事是有辅助的。
针孔的产生主若是由于气泡滞留于镀件概况而酿成的,但发赌气泡实在没需要定有针孔组成。
由于组成针孔必须有两个条件;第一要有气泡(主若是氢气)产生;第二所产生的气泡,能吸附于镀件上。
若是产生的气泡不能在镀件概况上滞留,则不会产生针孔。
镀镍层中针孔的风险产生针孔的条件针孔有的直达至基体金属或至镀层中部为止,或慢慢为镀层关闭。
如针孔直达基体金属,则基体金属与大气接触,易被侵蚀。
如针孔止于镀层中部,则虽不致于马上被侵蚀,但总是镀层的弱点,耐侵蚀性能降落,也影响了镀层的雅观,在抛光后有拉延的痕迹,使故障加倍较着。
3、针孔的故障是一个相当复杂的问题问题,因独霸条件或溶液成分分歧标准而产生针孔,则解救尚易,只需改改独霸条件或调剂溶液成分使之合适请求便可能解决。
如因溶液有杂质(金属杂质或有机杂质)的传染而产生针孔,则必须找出其根源,隔靴搔痒,才干获得解决。
在没有杂质的景象下,一个简略而有用的编制为插手防针孔剂,在光泽性镀镍中可插手润湿剂如十二烷基硫酸钠,用量为0.01~0.05克/升。
镀镍故障
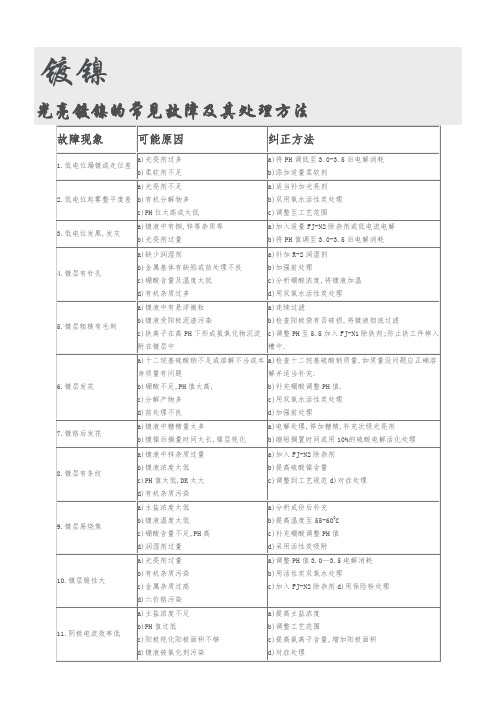
(1)镍镀层表面钝化;
(2)镍层上光亮剂吸附或有凝结物;
(3)镀镍液中金属杂质过多。
处理方法
(1)对镀镍后放置较长时间的镀件,可用质量分数为10%的硫酸溶液或用铬酸浸渍后镀铬。
(2)适当减少光亮剂,必要时用活性炭处理。在冬季时,为了防止工件带出液在表面形成凝结物,难以在冷水中洗净。因此,镀镍后应先在温水中清洗,然后经活化处理后镀铬,就可以消除发花现象。
a)镀液中锌杂质过量
b)镀液浓度太低
c)PH值太低,DK太大
d)有机杂质污染
a)加入FJ-N2除杂剂
b)提高硫酸镍含量
c)调整到工艺规范d)对症处理
9.镀层易烧焦
a)主盐浓度太低
b)镀液温度太低
c)硼酸含量不足,PH高
d)润湿剂过量
a)分析成份后补充
b)提高温度至55-60OC
c)补充硼酸调整PH值
镀镍
光亮镀镍的常见故障及其处理方法
故障现象
可能原因
纠正方法
1.低电位漏镀或走位差
a)光亮剂过多
b)柔软剂不足
a)将PH调低至3.0-3.5后电解消耗
b)添加适量柔软剂
2.低电位起雾整平度差
a)光亮剂不足
b)有机分解物多
c)PH位太高或太低
a)适当补加光亮剂
b)双用氧水活性炭处理
c)调整至工艺范围
3.低电位发黑,发灰
Fe¨成为Fe(on)沉淀,过滤除去。如果不能停产,
可用电解法,增大阴极面积,用0.1 A/dm2阴极电流
密度电解处理一段时间,问题得到缓解。
2.针孔、麻点在镀件棱边和面向阳极的一面
产生原因
(1)阴极电流密度过大;
- 1、下载文档前请自行甄别文档内容的完整性,平台不提供额外的编辑、内容补充、找答案等附加服务。
- 2、"仅部分预览"的文档,不可在线预览部分如存在完整性等问题,可反馈申请退款(可完整预览的文档不适用该条件!)。
- 3、如文档侵犯您的权益,请联系客服反馈,我们会尽快为您处理(人工客服工作时间:9:00-18:30)。
1,镀镍层发暗
镀镍层表面发暗也是常见的电镀故障之一,这种故障多数出现在低电流密度区电镀获
得的镀镍层,偶尔也出现在中电流密度区或高电流密度区,低电流密度区镀镍层发暗可能
是镀镍液的温度太高,阴极电流密度太小,硫酸镍浓度太低;I,4一丁炔二醇或其他次级
光亮剂过多或镀液中有铜、锌杂质污染引起;中电流密度区镀镍层发暗可能是由于镀液中次级光亮剂太少,有机杂质过多或有一定量的铁杂质污染造成的;高电流密度区镀层发暗可能是镀液pH值太高,初级光亮剂太少或镀液中有少量的铬酸盐、磷酸盐及铅杂质污染引起。
此外,镀前处理不良,镀件表面有碱膜或有机物吸附膜,或底镀层(氰化镀铜等)不好也会导致光亮镍镀层出现发暗现象。
可以取镀镍液做霍耳槽试验来分析这类电镀故障,对于低电流密度区出现的发暗现象,
目前有的镀镍出现了比较好的走位剂,专门使得在低电流密度范围内获得光亮镀镍层。
另
外还可以观察霍耳槽试片的外观进行逐步分析,如果镀液成分所做的霍耳槽样板上镀镍层状况良好,没有出现发暗的现象,那么电镀时出现的故障,就有可能是镀前处理不良或底镀层不好造成的,应该认真检查电镀镍前的情况。
若霍耳槽试验所得的阴极样板上出现低电流密度区镀层发暗,则可以根据前面提到的可能原因进行试验确定,或者加入合适的走位剂成分最后排除这种电镀故障。
中、高电流密度区的镀镍层发暗,也可用类似的方法进行试验分析。
2,镀镍层脆性
镀层发脆,往往影响镀层的加工和质量,而且镀层的脆性与镀层应力有关。
镀镍液中次级光亮剂过多或初级光亮剂太少,铜、锌、铁或有机杂质过多,pH值过高或温度过低等都会使镀镍层发脆。
检查镀镍层脆性的方法,一是将镀好镍的小零件放在手中搓摩,或将镀镍薄片零件弯曲至
18009若有碎镍层脱落,说明该镍层脆性大;另外就是将镍层镀在不锈钢试片上,控制镀层厚度在10ym左右,然后把镍层剥离下来,弯曲1800,用力挤压弯曲处,若不断裂,表示镀镍层不脆,弯曲折断,该镀镍层脆性就大。
产生镍层脆性的原因,若镀液pH值和温度没有问题,那么可能是镀液中光亮添加剂比例失调或镀液中杂质的造成的,由于光亮添加剂比例失调造成的镀镍脆性可以通过提高糖精添加剂(或其他应力消除成分)的含量来改善,通过补充糖槔等成分,观察镀镍层脆性是否改善来判断。
如果是镀液中的杂质影响可按前述削小型试验方法进行检查和纠正。
糖精是光亮镀镍液中常用的初级光亮剂。
它能降低次级光亮剂产生的璐应力,提高镀镍层的韧性。
糖精含量过低,镀层的张应力增大,镀镍层容易发脆,而且零件的高电流密
度区镀镍层发雾,光亮度变差,这种现象在霍耳槽罚验的阴极样板上,可以明显看出来,若在霍耳槽试验时发现这类现象,再补负糖精又使这类现象消失,那就证明是镀液中糖精太少了,应及时补充糖糖等成分。
糖精含量过高也不是太好,有时会使镀镍层出现云雾状白雾,在上套铭时,铬层容易发花。
并使零件的深凹处不易镀上铬层,对于这种情况,应及日寸进行电解处理,使糖精含量降低。
当镀镍液中糖精含量足够时,镍层的光亮度主要取决于1, 4 一丁炔二醇(或其他次级光亮剂)的含量。
其含量低,镀层的光亮度差,不能获得镜面光亮镀层。
可以通过霍耳槽试验分析排故,镀镍层光亮度差,可向镀液中加入适量的1, 4 一丁炔二醇(或其他次级光亮剂),使阴极样板上镀层的光亮度提高,而且保证高电流密度处镀镍层不脆裂,低电流密度处镀层不出现灰暗。
1,4 一丁炔二醇(或其他次级光亮剂)含量高,镀镍层光亮,但镀层的张应力也会提高, 并导致镍镀层发脆,次级光亮剂含量过高,镍镀层亮而发乌,零件低电流密度区镀层灰暗, 高电流密度区镀层脆裂。
这种情况可适当提高镀液中糖精含量(保持初级与次级光亮剂比例适当)和电解处理,使镀镍液恢复正常;次级光亮剂含量过多时,需要电解时间增长或用活性炭处理排除此种光亮镀镍故障。
3,橘皮状镀镍层
有时光照下镀镍层呈现出隐隐的波纹状现象(橘皮状镀层)。
这表明与镀前处理不良,镀液中有油或有胶类杂质,十二烷基硫酸钠过多、异金属杂质过多或镀液中有未过滤掉的活性炭粉末等的影响导致橘皮状镀镍层的产生。
十二烷基硫酸钠可以降低镀件和溶液之间的界面张力,使溶液润湿镀件,防镀镍层产生针孔,所以它既是润湿剂,又有防针孔的功效。
其含量过低,不但镀镍层容易出现针孔,且镀层发花。
含量过高,就会产生橘皮状镀
若刚加过十二烷基硫酸钠后出现橘皮状镀层,那就可能是十二烷基硫酸钠过多,这时可采用电解一段时间看看故障能否消失进行判断。
如果是刚用活性炭处理的镀镍液出现的这类故障,则可能是镀液中有未过滤掉的活性炭粉末,需要再过滤镀液后观察。
倘若既没有补充过十二烷基硫酸钠,又没有用活性炭处理过镀液,那么就应通过霍耳槽试验,检查镀前处理和镀液中的杂质情况,并根据试验结果进行纠正。
4,沉积速度慢,零件的深凹处镀不上镍层
这类故障除了偶尔真实电流密度太小而引起外,多数是镀液中有氧化剂存在。
因为镀镍液中容易带人的氧化剂是六价铬和硝酸根等。
氧化剂能在阴极上还原,降低镀镍过程的阴极电流效率,甚至能排斥镍的沉积,使零件镀不上镀层。
某厂工人误把少量硝酸当成硫酸加入列镀镍槽中,导致镀镍槽不能沉积镀层的现象。
遇到这种沉积速度慢。
甚至镀不上镀层的情况,可以用霍耳槽试验进行检查。
假使取故障液做霍耳槽试验所得的阴极试片的低电流密度区无镀层,高电流密度区镀层是黑色或灰色条纹,就表明镀镍液中有硝酸根,
可以采取电解的方法处理。
假使低电流密度区无镀层而高电流密度区镀层脆裂,就有可能是镀液中六价铬离子的影响,这时可加入0. 29保险粉,搅拌5min后再做霍耳槽试验,如用保险粉处理后,阴极样板明显好转,表明故障镀液中有六价铬离子,应通过加入保险粉来清除镀液中的六价铬离子杂质。