储罐氮封方案
氮封设计方案

氮封设计方案
氮封设计方案是指在封闭环境下使用氮气来封存产品或材料的一种工艺。
氮气具有无色无味、不可燃、不支持生物生长等特点,适用于各种领域的封存需求。
以下是一个常见的氮封设计方案:
1. 设备准备:首先需要准备一台氮气产生器或氮气罐,并确保其性能和氮气纯度符合要求。
同时,还需要配备相应的氮气输送管道和控制系统。
2. 封存容器选择:根据封存产品的特点和需求,选择合适的封存容器。
常用的封存容器有气密包装袋、密封罐等。
容器要具备良好的气密性,可以防止氧气和湿气进入容器内部。
3. 氮气处理:将氮气导入封存容器,确保容器内无氧气存在。
可采用两种方式处理氮气,即置换法和补充法。
1
- 置换法:将容器内的空气排出,然后将干净的氮气注入容器,直到容器内没有空气存在。
这种方法通常用于开封过的容器。
- 补充法:在容器内注入足够量的氮气,以保持容器内压力较高,阻止空气进入容器。
这种方法通常适用于封存后不再开封的情况。
4. 封存操作:将产品或材料放入封存容器中,并通过密封装置将容器密封。
确保容器的气密性,以防止外界的空气和湿气进入容器内部。
5. 控制和监测:使用相关的控制系统对氮气供应进行监测和控制,确保氮气供应的稳定和持续。
同时,也需要定期检查封存容器的密封性能和气密性。
以上是一个常见的氮封设计方案,具体方案可以根据实际情况进行
调整和改进。
2。
氮封设计方案办法

欢迎阅读附件2氮封设计方案方案一:压力控制设计方案(LPEC )一、基本原理确确性,两开口之间的距离不宜小于1m 。
4)量油孔应加导向管,确保量油作业时不影响氮封压力。
5)储罐罐顶增加紧急泄压人孔接口。
2.工艺流程1)在每台储罐上设置先导式氮封阀组和限流孔板旁路,正常情况下使用氮封阀组维持罐内气相空间压力在1.2KPa左右,当气相空间压力高于1.4KPa时,氮封阀关闭,停止氮气供应;当气相空间压力低于0.8KPa时,氮封阀开启,开始补充氮气;当氮封阀需要检修或故障时,使用限流孔板旁路给储罐内补充氮气,压力高于1.5KPa 时,通过带阻火器的呼吸阀外排(短时间连续补充氮气)。
方案二:氧含量控制设计方案(SEI)1)在储罐内安装氧气检测器,实时监测储罐内气相空间氧气浓度,同时将高浓度报警与氮气管道控制阀门联锁。
当氧气浓度达到高浓度值时报警,联锁打开氮气阀门,向储罐内补充氮气,直至检测指标达到设定要求时联锁关闭氮气阀门。
补充氮气的流量控制使用限流孔板,流量宜控制在Q=Q1-Q2(Q1-油品出罐流量,Q2-气相连通罐中与油品出罐同时进行的油品进罐流量),且Q不应小于100m3/h,氮气管道的管径为DN50,氮气的操作压力为0.5Mpa。
氧气浓度监测信号引入控制室,控制室设氧气浓度超标报警仪。
2)同一种油品的多个储罐在生产运行过程中,储罐区域收油作业和付油作业经常同时进行。
为节省氮气用量,建议在同种油品储罐之间设置气相联通管道,可以实现多个运行过程中的储罐进气量宜接近浮盘。
可在氮气橡胶软管出口连接一个环形不锈钢管,管壁水平方向上开若干个通气孔,用于向四周喷射氮气。
环形不锈钢管应固定安装在浮盘上。
3)储罐之间设置DN150气相联通管道,每个储罐的气相联通管道均应设置管道阻火器,阻火器应选用安全性能满足要求的产品。
阻火器应尽量靠近储罐接口安装,每个储罐的气相联通管道均应设置截断阀。
气相联通管道宜在罐顶之间跨接。
甲醇储罐氮封系统工艺设计

甲醇储罐氮封系统工艺设计甲醇储罐氮封系统工艺设计一、引言甲醇是一种重要的工业原料,广泛应用于化工、医药等领域。
在甲醇的生产和储存过程中,由于其易挥发性和易燃性,需要采取一系列的安全措施来确保生产过程的安全性。
其中,甲醇储罐氮封系统是一种常用的安全措施,本文将详细介绍其工艺设计。
二、设计目标1. 实现甲醇储罐内部气体压力的控制,防止罐内压力过高或过低;2. 阻止外界空气进入储罐内部,避免甲醇挥发和与氧气发生反应;3. 在必要时能够通过调节氮气流量来实现储罐内部压力的调节;4. 设计合理的排放系统,确保储罐内部压力过高时能够及时排放。
三、系统组成1. 氮气供应系统:包括氮气源、压缩机、干燥器等设备。
氮气源可以选择液态氮或者其他形式的高纯度氮气,通过压缩机将氮气压缩至所需压力,并通过干燥器去除其中的水分和杂质。
2. 氮气输送系统:包括输送管道、阀门等组件。
输送管道应选择耐腐蚀材料,如不锈钢或聚四氟乙烯等,以保证氮气的纯净度。
3. 氮气封闭系统:包括储罐内部的封闭装置。
一般来说,储罐顶部设有一个密封盖,并通过密封圈与储罐连接。
在密封盖上设置有进气阀门和排放阀门,用于调节储罐内部的压力。
4. 压力控制系统:包括压力传感器、控制仪表等设备。
压力传感器安装在储罐内部,用于实时监测储罐内部的压力变化;控制仪表则根据传感器反馈的数据来控制进气阀门和排放阀门的开闭程度,以实现对储罐内部压力的控制。
四、工艺流程1. 氮气供应:将液态氮或高纯度氮气从氮气源输送至压缩机,经过压缩机的压缩和干燥器的处理后,得到所需的氮气。
2. 氮气输送:将氮气通过输送管道输送至储罐顶部的封闭装置。
在输送过程中,应注意保持管道的密封性,避免外界空气进入。
3. 储罐封闭:将储罐顶部的密封盖与储罐连接,并确保密封圈的完好。
在密封盖上设置进气阀门和排放阀门,并确保其与储罐内部相连通。
4. 压力控制:安装压力传感器于储罐内部,通过控制仪表对传感器反馈的数据进行处理,并根据设定值控制进气阀门和排放阀门的开闭程度,以实现对储罐内部压力的控制。
甲醇储罐氮封系统工艺设计

甲醇储罐氮封系统工艺设计一、引言甲醇储罐是工业生产中常见的一种容器,用于储存甲醇等化学品。
由于甲醇具有易燃、挥发性等特性,为了确保储存安全,需要对甲醇储罐进行氮封,防止空气进入罐内引发事故。
本文将对甲醇储罐氮封系统的工艺设计进行探讨。
二、储罐氮封系统的作用和原理1.作用:–防止罐内产生过高的压力和温度,保证储存安全;–防止罐内氧气进入,防止发生爆炸事故;–防止空气中的湿气进入,降低甲醇损失。
2.原理:–利用氮气替代空气,降低罐内氧气浓度;–利用氮气的惰性,防止甲醇与氧气发生反应;–控制罐内温度和压力,确保储存的稳定和安全。
三、储罐氮封系统的工艺设计1.氮气供应系统:–选择稳定可靠的氮气供应商;–根据储罐容量和氮气消耗率确定氮气供应量;–设置氮气供应参数,包括压力、流量和纯度等。
2.氮气管网:–根据储罐布置和氮气需求确定管网布置;–确定管道材质和规格,保证氮气输送的安全和可靠;–设置管网阀门和仪表,实现氮气的控制和监测。
3.氮气发生器:–根据储罐容量和氮气需求选择合适的氮气发生器;–确定氮气发生器的工艺参数,包括温度、压力和流量等;–设计和布置氮气发生器的设备和管道,确保氮气的产生和输送。
4.氮气封闭装置:–在储罐上设置氮气封闭装置,包括氮气进口和出口管道、阀门和仪表等;–设置氮气封闭装置的参数,如进出口压力、流量和纯度等;–根据储罐的特点和氮气需求,设计和选择合适的封闭装置。
四、储罐氮封系统的操作流程1.氮气供应准备:–检查氮气供应系统的氮气质量和供应压力,确保正常运行;–打开氮气供应系统的阀门,准备供应氮气。
2.开启氮气封闭装置:–打开储罐上的氮气进口阀门,将氮气导入罐内;–监测氮气的进口压力和流量,调整控制阀门,保持稳定。
3.控制储罐温度和压力:–根据储罐的工艺要求,调整氮气供应参数,控制罐内温度和压力;–监测罐内温度和压力,及时调整氮气供应量,保持稳定。
4.停止氮气供应:–当储罐内压力和温度稳定时,可以停止氮气供应;–关闭氮气封闭装置的进口阀门,停止氮气的供应。
储罐氮封系统装置
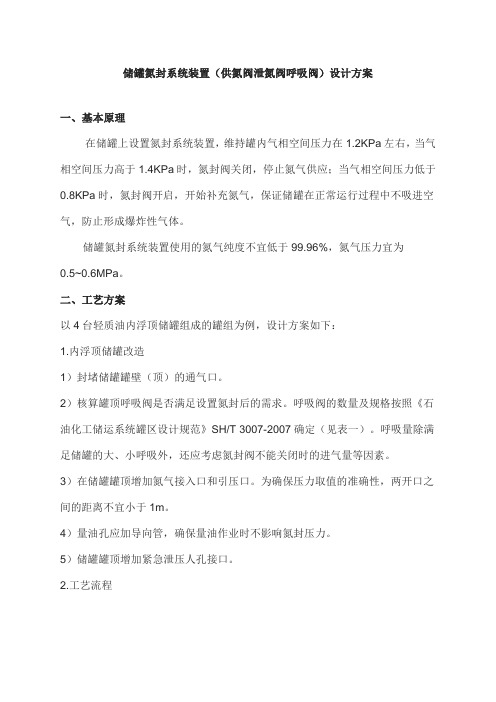
储罐氮封系统装置(供氮阀泄氮阀呼吸阀)设计方案一、基本原理在储罐上设置氮封系统装置,维持罐内气相空间压力在1.2KPa左右,当气相空间压力高于1.4KPa时,氮封阀关闭,停止氮气供应;当气相空间压力低于0.8KPa时,氮封阀开启,开始补充氮气,保证储罐在正常运行过程中不吸进空气,防止形成爆炸性气体。
储罐氮封系统装置使用的氮气纯度不宜低于99.96%,氮气压力宜为0.5~0.6MPa。
二、工艺方案以4台轻质油内浮顶储罐组成的罐组为例,设计方案如下:1.内浮顶储罐改造1)封堵储罐罐壁(顶)的通气口。
2)核算罐顶呼吸阀是否满足设置氮封后的需求。
呼吸阀的数量及规格按照《石油化工储运系统罐区设计规范》SH/T 3007-2007确定(见表一)。
呼吸量除满足储罐的大、小呼吸外,还应考虑氮封阀不能关闭时的进气量等因素。
3)在储罐罐顶增加氮气接入口和引压口。
为确保压力取值的准确性,两开口之间的距离不宜小于1m。
4)量油孔应加导向管,确保量油作业时不影响氮封压力。
5)储罐罐顶增加紧急泄压人孔接口。
2.工艺流程1)在每台储罐上设置先导式氮封阀组和限流孔板旁路,正常情况下使用氮封阀组维持罐内气相空间压力在1.2KPa左右,当气相空间压力高于1.4KPa时,氮封阀关闭,停止氮气供应;当气相空间压力低于0.8KPa时,氮封阀开启,开始补充氮气;当氮封阀需要检修或故障时,使用限流孔板旁路给储罐内补充氮气,压力高于1.5KPa时,通过带阻火器的呼吸阀外排(短时间连续补充氮气)。
2)当氮封阀事故失灵不能及时关闭,造成罐内压力超过1.5Kpa时,通过带阻火器的呼吸阀外排;当氮封阀事故失灵不能及时开启时,造成罐内压力降低至-0.3Kpa时,通过带阻火器呼吸阀向罐内补充空气,确保罐内压力不低于储罐的设计压力低限(-0.5Kpa)。
3)为确保设置氮封储罐事故工况下的安全排放,应在储罐上设置紧急泄放阀,紧急泄放阀定压不应高于储罐的设计压力上限(2.0Kpa)。
储罐氮封系统装置演示教学

储罐氮封系统装置(供氮阀泄氮阀呼吸阀)设计方案一、基本原理在储罐上设置氮封系统装置,维持罐内气相空间压力在1.2KPa左右,当气相空间压力高于1.4KPa时,氮封阀关闭,停止氮气供应;当气相空间压力低于0.8KPa时,氮封阀开启,开始补充氮气,保证储罐在正常运行过程中不吸进空气,防止形成爆炸性气体。
储罐氮封系统装置使用的氮气纯度不宜低于99.96%,氮气压力宜为0.5~0.6MPa。
二、工艺方案以4台轻质油内浮顶储罐组成的罐组为例,设计方案如下:1.内浮顶储罐改造1)封堵储罐罐壁(顶)的通气口。
2)核算罐顶呼吸阀是否满足设置氮封后的需求。
呼吸阀的数量及规格按照《石油化工储运系统罐区设计规范》SH/T 3007-2007确定(见表一)。
呼吸量除满足储罐的大、小呼吸外,还应考虑氮封阀不能关闭时的进气量等因素。
3)在储罐罐顶增加氮气接入口和引压口。
为确保压力取值的准确性,两开口之间的距离不宜小于1m。
4)量油孔应加导向管,确保量油作业时不影响氮封压力。
5)储罐罐顶增加紧急泄压人孔接口。
2.工艺流程1)在每台储罐上设置先导式氮封阀组和限流孔板旁路,正常情况下使用氮封阀组维持罐内气相空间压力在1.2KPa左右,当气相空间压力高于1.4KPa时,氮封阀关闭,停止氮气供应;当气相空间压力低于0.8KPa时,氮封阀开启,开始补充氮气;当氮封阀需要检修或故障时,使用限流孔板旁路给储罐内补充氮气,压力高于1.5KPa时,通过带阻火器的呼吸阀外排(短时间连续补充氮气)。
2)当氮封阀事故失灵不能及时关闭,造成罐内压力超过1.5Kpa时,通过带阻火器的呼吸阀外排;当氮封阀事故失灵不能及时开启时,造成罐内压力降低至-0.3Kpa时,通过带阻火器呼吸阀向罐内补充空气,确保罐内压力不低于储罐的设计压力低限(-0.5Kpa)。
3)为确保设置氮封储罐事故工况下的安全排放,应在储罐上设置紧急泄放阀,紧急泄放阀定压不应高于储罐的设计压力上限(2.0Kpa)。
氮封方案

氮封设计方案一、基本原理在储罐上设置氮封系统,维持罐内气相空间压力在 1.2KPa 左右,当气相空间压力高于1.4KPa时,氮封阀关闭,停止氮气供应;当气相空间压力低于0.8KPa时,氮封阀开启,开始补充氮气,保证储罐在正常运行过程中不吸进空气,防止形成爆炸性气体。
储罐氮封系统使用的氮气纯度不宜低于99.96%,氮气压力宜为0.5~0.6MPa。
二、工艺方案以4台轻质油内浮顶储罐组成的罐组为例,设计方案如下:1.内浮顶储罐改造1)封堵储罐罐壁(顶)的通气口。
2)核算罐顶呼吸阀是否满足设置氮封后的需求。
呼吸阀的数量及规格按照《石油化工储运系统罐区设计规范》SH/T 3007-2007确定(见表一)。
呼吸量除满足储罐的大、小呼吸外,还应考虑氮封阀不能关闭时的进气量等因素。
3)在储罐罐顶增加氮气接入口和引压口。
为确保压力取值的准确性,两开口之间的距离不宜小于1m。
4)量油孔应加导向管,确保量油作业时不影响氮封压力。
5)储罐罐顶增加紧急泄压人孔接口。
2.工艺流程1)在每台储罐上设置先导式氮封阀组和限流孔板旁路,正常情况下使用氮封阀组维持罐内气相空间压力在1.2KPa左右,当气相空间压力高于1.4KPa时,氮封阀关闭,停止氮气供应;当气相空间压力低于0.8KPa时,氮封阀开启,开始补充氮气;当氮封阀需要检修或故障时,使用限流孔板旁路给储罐内补充氮气,压力高于1.5KPa时,通过带阻火器的呼吸阀外排(短时间连续补充氮气)。
2)当氮封阀事故失灵不能及时关闭,造成罐内压力超过1.5Kpa时,通过带阻火器的呼吸阀外排;当氮封阀事故失灵不能及时开启时,造成罐内压力降低至-0.3Kpa时,通过带阻火器呼吸阀向罐内补充空气,确保罐内压力不低于储罐的设计压力低限(-0.5Kpa)。
3)为确保设置氮封储罐事故工况下的安全排放,应在储罐上设置紧急泄放阀,紧急泄放阀定压不应高于储罐的设计压力上限(2.0Kpa)。
4)当需要使用限流孔板旁路补充氮气时,流量宜等于油品出罐流量,氮气管道的管径为DN50,氮气的操作压力为0.5MPa。
氮封设计方案

附件2氮封设计方案方案一:压力控制设计方案(LPEC)一、基本原理在储罐上设置氮封系统,维持罐内气相空间压力在1.2KPa左右,当气相空间压力高于1.4KPa时,氮封阀关闭,停止氮气供应;当气相空间压力低于0.8KPa时,氮封阀开启,开始补充氮气,保证储罐在正常运行过程中不吸进空气,防止形成爆炸性气体。
储罐氮封系统使用的氮气纯度不宜低于99.96%,氮气压力宜为0.5~0.6MPa。
二、工艺方案以4台轻质油内浮顶储罐组成的罐组为例,设计方案如下:1.内浮顶储罐改造1)封堵储罐罐壁(顶)的通气口。
2)核算罐顶呼吸阀是否满足设置氮封后的需求。
呼吸阀的数量及规格按照《石油化工储运系统罐区设计规范》SH/T 3007-2007确定(见表一)。
呼吸量除满足储罐的大、小呼吸外,还应考虑氮封阀不能关闭时的进气量等因素。
3)在储罐罐顶增加氮气接入口和引压口。
为确保压力取值的准确性,两开口之间的距离不宜小于1m。
4)量油孔应加导向管,确保量油作业时不影响氮封压力。
5)储罐罐顶增加紧急泄压人孔接口。
2.工艺流程1)在每台储罐上设置先导式氮封阀组和限流孔板旁路,正常情况下使用氮封阀组维持罐内气相空间压力在1.2KPa左右,当气相空间压力高于1.4KPa时,氮封阀关闭,停止氮气供应;当气相空间压力低于0.8KPa时,氮封阀开启,开始补充氮气;当氮封阀需要检修或故障时,使用限流孔板旁路给储罐内补充氮气,压力高于1.5KPa时,通过带阻火器的呼吸阀外排(短时间连续补充氮气)。
2)当氮封阀事故失灵不能及时关闭,造成罐内压力超过1.5Kpa 时,通过带阻火器的呼吸阀外排;当氮封阀事故失灵不能及时开启时,造成罐内压力降低至-0.3Kpa时,通过带阻火器呼吸阀向罐内补充空气,确保罐内压力不低于储罐的设计压力低限(-0.5Kpa)。
3)为确保设置氮封储罐事故工况下的安全排放,应在储罐上设置紧急泄放阀,紧急泄放阀定压不应高于储罐的设计压力上限(2.0Kpa)。
甲醇储罐氮封系统工艺设计方案

甲醇储罐氮封系统工艺设计方案甲醇储罐是工业生产中常见的储存液体甲醇的设备。
为了确保储罐内甲醇的安全存放和运输,氮封系统的设计至关重要。
本文将对甲醇储罐氮封系统的工艺设计方案进行深入探讨,并分享我对该系统的观点和理解。
1. 储罐氮封系统的基本原理储罐氮封系统是通过向储罐内注入氮气,使储存的液体甲醇与外界的空气隔绝,从而达到防止甲醇蒸发、避免氧化和减少爆炸风险的目的。
通过控制氮气的流量和压力,可以实现储罐内气氛的稳定,确保储存甲醇的质量和安全。
2. 氮封系统的组成和工艺设计(1)氮气供应系统:氮气供应系统是氮封系统的核心部分,主要由氮气压缩机、氮气贮存罐和氮气输送管道组成。
氮气供应系统需要根据实际情况确定氮气的供应量和压力,并通过管道将氮气输送到储罐内。
(2)氮气流量和压力控制系统:氮气流量和压力控制系统用于控制氮气的供应量和压力,确保储罐内气氛的稳定。
通过采用流量控制阀和压力传感器等设备,可以实现对氮气流量和压力的精确控制。
(3)安全监测和报警系统:安全监测和报警系统是氮封系统中必不可少的部分,用于监测储罐内气氛的浓度和压力,并在出现异常情况时及时发出警报。
这样可以确保操作人员能够及时采取措施,防止事故的发生。
3. 深度探讨甲醇储罐氮封系统的关键问题和挑战(1)氮气流量和压力的确定:氮气流量和压力的确定是氮封系统设计中的一个重要问题。
过高的流量和压力会导致能源浪费,过低则无法满足储存甲醇的要求。
在设计过程中需要考虑储罐的容量、环境温度、甲醇的性质等因素,并结合经验数据确定合适的流量和压力范围。
(2)系统的稳定性和可靠性:储罐氮封系统的稳定性和可靠性是确保储存甲醇安全的关键。
系统设计中应充分考虑部件的选型和安装质量,并采取必要的措施确保系统的正常运行。
定期进行系统维护和检修也是保证系统稳定性和可靠性的重要手段。
4. 我对甲醇储罐氮封系统的观点和理解甲醇储罐氮封系统的设计方案需要综合考虑流程工艺、安全性和经济性等因素。
轻质油品储罐氮封优化方法分析

轻质油品储罐氮封优化方法分析轻质油品储罐是石油行业中常见的设备之一,其内部储存着轻质油品,需要保证储罐内气体的密闭性,防止氧气进入储罐内与轻质油品发生反应,造成安全事故。
氮封是一种常用的方法,通过注入氮气形成惰性气氛,达到保护和封闭储罐内轻质油品的目的。
本文将对轻质油品储罐氮封的优化方法进行分析。
首先,氮封系统的设计要合理。
氮封系统主要由氮气源、氮气管道、氮气调压阀、氮气注入口等组成。
在设计氮封系统时,需要考虑储罐的尺寸、形状、储存的油品类型和储存量等因素,确定合适的氮气注入量和注入位置,以及合理的氮气注入速度。
另外,还需考虑氮气管道的布置方式和管道材料的选择,以确保氮气能够均匀分布到储罐内的各个角落。
其次,氮气质量要可靠。
氮气作为氮封系统的关键组成部分,其质量和纯度直接影响氮封效果。
因此,在选择氮气供应商时,应考虑其信誉和资质,并与供应商签订合同,保证氮气的质量和纯度符合要求。
同时,还需定期对氮气进行检测和分析,确保其质量稳定。
另外,氮封系统的操作要规范。
操作人员应熟悉氮封系统的工作原理和操作流程,掌握氮气调压阀和注入口的使用方法,并能根据实际情况及时调整氮气注入的量和速度。
操作人员还应定期检查氮气系统的工作状态,包括氮气管道是否有泄漏、调压阀是否正常工作等,并及时进行维护和修理。
此外,氮封系统的监控和报警要及时。
监控设备可以实时检测储罐内的氮气浓度和压力,并与报警系统联动,当发现异常情况时及时发出警报。
监控设备还可以记录储罐内氮气的浓度和压力变化情况,以便后续的分析和改进。
最后,还可以进行氮封系统的模拟和优化。
通过建立氮封系统的模型,可以对氮气注入量、注入速度等参数进行模拟和优化,以达到最佳的氮封效果。
模拟和优化的结果可以作为改进氮封系统的依据,指导实际操作。
综上所述,轻质油品储罐氮封的优化方法包括合理设计氮封系统、确保氮气质量可靠、规范操作、及时监控和报警,以及进行模拟和优化。
通过采取这些方法,可以提高轻质油品储罐氮封的效果,减少安全事故的发生,保障工作人员和设备的安全。
轻质油储罐增设氮封提高本质安全方案

轻质油储罐增设氮封提高本质安全方案摘要:由于多种因素的作用,造成轻质油储罐发生火灾爆炸的概率变高,氮封系统能够较好的解决这一问题。
本文介绍了公司轻质油储罐运行情况、氮封系统原理和作用,以及现有轻质油储罐氮封改造方案,分析了改造过程中出现的问题并提出解决方案。
关键字:轻质油储罐,氮封,改造方案前言2013年-2018年期间,国内炼油企业多次发生轻质油储罐火灾事故,使企业对轻质油储罐的安全性提出了质疑。
根据火灾事故情况分析,储存介质硫含量及挥发性组分含量高等因素是导致轻质油储罐发生火灾事故的主要原因。
结合公司加工高硫原油的实际,依据《关于开展炼油企业轻质油储罐安全运行情况调查的通知》要求,公司提出了对现有11台轻质油储罐进行增设氮封改造的建议,目的是降低蒸发损耗,有利于油品储运的安全生产,提高储罐使用的安全可靠性,保护环境。
1 公司轻质油储罐运行情况1.1轻质油罐范围轻质油罐是指储存终馏点不大于220℃轻质油品的立式圆筒形钢制焊接常压储罐。
主要包括石脑油储罐、焦化汽油储罐(含焦化汽柴油混装储罐,下同)、催化汽油(未加氢、精制,下同)储罐等中间原料轻质油储罐,以及含有轻质油组分的轻污油储罐、含硫污水储罐等,大多为内浮顶及拱顶结构。
1.2轻质油罐运行问题1.2.1油品的蒸发损耗大查阅有关资料得知[1]油品储运损耗约占加工量的3‰~5‰,其中储罐蒸发损耗约占50 %~60 %。
蒸发损耗主要是自然通风损耗、大呼吸损耗、小呼吸损耗三种。
为解决降低油品的蒸发损耗问题,目前虽已采用多种措施,诸如:喷淋水冷却,采用浅色涂料、呼吸阀安装挡板,提高储罐的承压能力等取得了一定的降耗效果,但并不理想,成本也较高,不仅蒸发损耗问题亟待解决,同时存在安全隐患问题。
1.2.2储罐壁腐蚀公司生产的石脑油中硫含量一般检测为0.026%(v/v);焦化柴油、催化柴油(柴油加氢原料),硫含量高达0.8%(v/v);这些生产的柴油、石脑油等都含有以H2S和R-SH形成存在的大量酸性硫化物,对铁具有很强的腐蚀性,因为硫化物首先分解成H 2S,H2S与铁反映生成FeS, FeS附在金属表面可防止H2S与铁进一步接触,但由于环烷酸能与FeS反应生成油溶性的环烷酸铁,能使FeS保护膜遭到破坏暴露出新的金属表面,使金属腐蚀继续进行。
储罐氮封系统装置

储罐氮封系统装置(供氮阀泄氮阀呼吸阀)设计方案一、基本原理在储罐上设置氮封系统装置,维持罐内气相空间压力在1、2KPa左右,当气相空间压力高于1、4KPa时,氮封阀关闭,停止氮气供应;当气相空间压力低于0、8KPa时,氮封阀开启,开始补充氮气,保证储罐在正常运行过程中不吸进空气,防止形成爆炸性气体。
储罐氮封系统装置使用的氮气纯度不宜低于99、96%,氮气压力宜为0、5~0、6MPa。
二、工艺方案以4台轻质油内浮顶储罐组成的罐组为例,设计方案如下:1、内浮顶储罐改造1)封堵储罐罐壁(顶)的通气口。
2)核算罐顶呼吸阀就是否满足设置氮封后的需求。
呼吸阀的数量及规格按照《石油化工储运系统罐区设计规范》SH/T 3007-2007确定(见表一)。
呼吸量除满足储罐的大、小呼吸外,还应考虑氮封阀不能关闭时的进气量等因素。
3)在储罐罐顶增加氮气接入口与引压口。
为确保压力取值的准确性,两开口之间的距离不宜小于1m。
4)量油孔应加导向管,确保量油作业时不影响氮封压力。
5)储罐罐顶增加紧急泄压人孔接口。
2、工艺流程1)在每台储罐上设置先导式氮封阀组与限流孔板旁路,正常情况下使用氮封阀组维持罐内气相空间压力在1、2KPa左右,当气相空间压力高于1、4KPa时,氮封阀关闭,停止氮气供应;当气相空间压力低于0、8KPa时,氮封阀开启,开始补充氮气;当氮封阀需要检修或故障时,使用限流孔板旁路给储罐内补充氮气,压力高于1、5KPa时,通过带阻火器的呼吸阀外排(短时间连续补充氮气)。
2)当氮封阀事故失灵不能及时关闭,造成罐内压力超过1、5Kpa时,通过带阻火器的呼吸阀外排;当氮封阀事故失灵不能及时开启时,造成罐内压力降低至-0、3Kpa 时,通过带阻火器呼吸阀向罐内补充空气,确保罐内压力不低于储罐的设计压力低限(-0、5Kpa)。
3)为确保设置氮封储罐事故工况下的安全排放,应在储罐上设置紧急泄放阀,紧急泄放阀定压不应高于储罐的设计压力上限(2、0Kpa)。
氮封设计方案

附件 2氮封设计方案方案一:压力控制设计方案(LPEC)一、基本原理在储罐上设置氮封系统,维持罐内气相空间压力在 1.2KPa左右,当气相空间压力高于1.4KPa时,氮封阀关闭,停止氮气供应;当气相空间压力低于0.8KPa时,氮封阀开启,开始补充氮气,保证储罐在正常运行过程中不吸进空气,防止形成爆炸性气体。
储罐氮封系统使用的氮气纯度不宜低于99.96%,氮气压力宜为0.5~0.6MPa。
二、工艺方案以4台轻质油内浮顶储罐组成的罐组为例,设计方案如下:1.内浮顶储罐改造1)封堵储罐罐壁(顶)的通气口。
2)核算罐顶呼吸阀是否满足设置氮封后的需求。
呼吸阀的数量及规格按照《石油化工储运系统罐区设计规范》SH/T 3007-2007确定(见表一)。
呼吸量除满足储罐的大、小呼吸外,还应考虑氮封阀不能关闭时的进气量等因素。
3)在储罐罐顶增加氮气接入口和引压口。
为确保压力取值的准确性,两开口之间的距离不宜小于1m。
4)量油孔应加导向管,确保量油作业时不影响氮封压力。
5)储罐罐顶增加紧急泄压人孔接口。
2.工艺流程1)在每台储罐上设置先导式氮封阀组和限流孔板旁路,正常情况下使用氮封阀组维持罐内气相空间压力在1.2KPa左右,当气相空间压力高于1.4KPa时,氮封阀关闭,停止氮气供应;当气相空间压力低于0.8KPa时,氮封阀开启,开始补充氮气;当氮封阀需要检修或故障时,使用限流孔板旁路给储罐内补充氮气,压力高于1.5KPa 时,通过带阻火器的呼吸阀外排(短时间连续补充氮气)。
2)当氮封阀事故失灵不能及时关闭,造成罐内压力超过1.5Kpa 时,通过带阻火器的呼吸阀外排;当氮封阀事故失灵不能及时开启时,造成罐内压力降低至-0.3Kpa时,通过带阻火器呼吸阀向罐内补充空气,确保罐内压力不低于储罐的设计压力低限(-0.5Kpa)。
3)为确保设置氮封储罐事故工况下的安全排放,应在储罐上设置紧急泄放阀,紧急泄放阀定压不应高于储罐的设计压力上限(2.0Kpa)。
储罐氮封系统设计

风向
SW
氮封系统问题——原因
氮封系统包括: 氮封阀、呼吸阀(含阻火器)、紧急泄压阀 如果有气相回收系统,则还需要配备:单呼阀 + 管道防爆轰型阻火器
氮封系统失效原因: 各安全附件的定压不准确,压力区间有交集。
氮封系统设计原则
氮封系统设计原则
常压拱顶储罐的设计压力为:-490Pa ~ + 1960Pa - 50mmH2O ~ + 200mmH2O 在如此小的压力范围内,如何保证各安全附件的压力区间没有交集? 氮封阀:开关型,安装位置尽量靠近罐顶 呼吸阀:全开启式
4、阻火器的阻力影响呼吸阀 的流量。
储罐呼吸阀和阻火器——常见配置
储罐呼吸阀和阻火器——一体式(非低温环境)
1、呼吸阀的超压值低于 API2000标准。 2、一体式结构,流量曲线真 实。 3、便于检修维护。 4、有效散发热量,耐稳定燃 烧。
注:2005年 8月泰国某炼油厂,此阀成功 阻止了因雷电引起火灾,仅将呼吸阀壳体 的油漆烧坏,但保证了储罐安安全。
储罐安全防护与整改方案
储罐呼吸阀和阻火器——案例 1
2012年某炼油厂, 呼吸阀和阻火器冻 堵,储罐被抽瘪。
储罐呼吸阀和阻火器——案例 2
2013年某化工厂,阻火器因介质 结晶而堵塞,储罐被抽瘪。
储罐呼吸阀和阻火器——案例 3
2012年某炼油厂, 大雾天气,阻火器 堵塞,储罐被抽瘪。
储罐呼吸阀和阻火器——常见配置
0.825
2.464
SW
0.130
操作时室外 2012.6.21 9:00 成品88单元石脑油罐区 Z-178下风向 操作室
0.065 SE (东南风)
1.428
储罐氮封系统装置
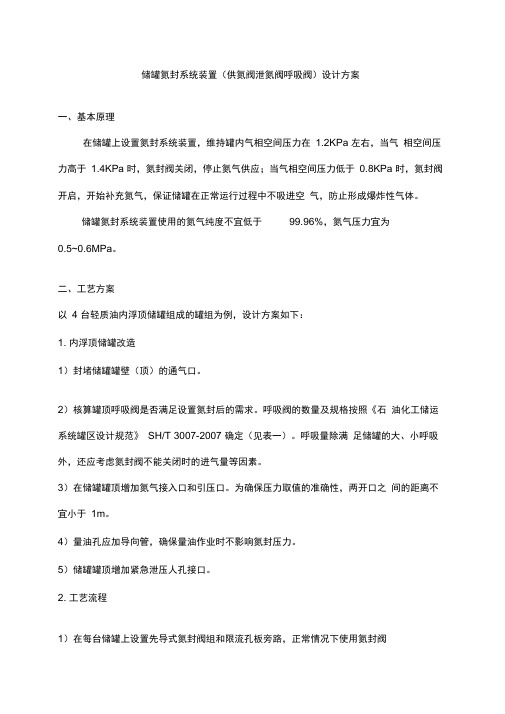
储罐氮封系统装置(供氮阀泄氮阀呼吸阀)设计方案一、基本原理在储罐上设置氮封系统装置,维持罐内气相空间压力在1.2KPa 左右,当气相空间压力高于1.4KPa 时,氮封阀关闭,停止氮气供应;当气相空间压力低于0.8KPa 时,氮封阀开启,开始补充氮气,保证储罐在正常运行过程中不吸进空气,防止形成爆炸性气体。
储罐氮封系统装置使用的氮气纯度不宜低于99.96%,氮气压力宜为0.5~0.6MPa。
二、工艺方案以4 台轻质油内浮顶储罐组成的罐组为例,设计方案如下:1. 内浮顶储罐改造1)封堵储罐罐壁(顶)的通气口。
2)核算罐顶呼吸阀是否满足设置氮封后的需求。
呼吸阀的数量及规格按照《石油化工储运系统罐区设计规范》SH/T 3007-2007 确定(见表一)。
呼吸量除满足储罐的大、小呼吸外,还应考虑氮封阀不能关闭时的进气量等因素。
3)在储罐罐顶增加氮气接入口和引压口。
为确保压力取值的准确性,两开口之间的距离不宜小于1m。
4)量油孔应加导向管,确保量油作业时不影响氮封压力。
5)储罐罐顶增加紧急泄压人孔接口。
2. 工艺流程1)在每台储罐上设置先导式氮封阀组和限流孔板旁路,正常情况下使用氮封阀组维持罐内气相空间压力在1.2KPa 左右,当气相空间压力高于1.4KPa 时,氮封阀关闭,停止氮气供应;当气相空间压力低于0.8KPa 时,氮封阀开启,开始补充氮气;当氮封阀需要检修或故障时,使用限流孔板旁路给储罐内补充氮气,压力高于1.5KPa 时,通过带阻火器的呼吸阀外排(短时间连续补充氮气)。
2)当氮封阀事故失灵不能及时关闭,造成罐内压力超过 1.5Kpa 时,通过带阻火器的呼吸阀外排;当氮封阀事故失灵不能及时开启时,造成罐内压力降低至-0.3Kpa 时,通过带阻火器呼吸阀向罐内补充空气,确保罐内压力不低于储罐的设计压力低限(-0.5Kpa )。
3)为确保设置氮封储罐事故工况下的安全排放,应在储罐上设置紧急泄放阀,紧急泄放阀定压不应高于储罐的设计压力上限(2.0Kpa )。
氮封设计方案
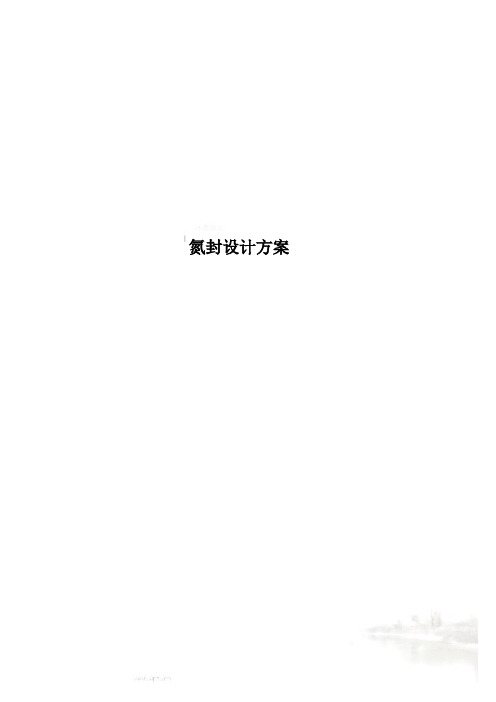
氮封设计方案附件2氮封设计方案方案一:压力控制设计方案(LPEC)一、基本原理在储罐上设置氮封系统,维持罐内气相空间压力在1.2KPa左右,当气相空间压力高于1.4KPa时,氮封阀关闭,停止氮气供应;当气相空间压力低于0.8KPa时,氮封阀开启,开始补充氮气,保证储罐在正常运行过程中不吸进空气,防止形成爆炸性气体。
储罐氮封系统使用的氮气纯度不宜低于99.96%,氮气压力宜为0.5~0.6MPa。
二、工艺方案以4台轻质油内浮顶储罐组成的罐组为例,设计方案如下:1.内浮顶储罐改造1)封堵储罐罐壁(顶)的通气口。
2)核算罐顶呼吸阀是否满足设置氮封后的需求。
呼吸阀的数量及规格按照《石油化工储运系统罐区设计规范》SH/T 3007-2007确定(见表一)。
呼吸量除满足储罐的大、小呼吸外,还应考虑氮封阀不能关闭时的进气量等因素。
3)在储罐罐顶增加氮气接入口和引压口。
为确保压力取值的准确性,两开口之间的距离不宜小于1m。
4)量油孔应加导向管,确保量油作业时不影响氮封压力。
5)储罐罐顶增加紧急泄压人孔接口。
呼吸阀选用表储罐公称容量(m3)呼吸阀数量×公称直径(mm)10001×200 20002×150 30002×200 40002×200 50002×250 100002×300 200003×300 300004×300 500004×300方案二:氧含量控制设计方案(SEI)一、基本原理在储罐上设置氮封系统,维持罐内气相空间氧气浓度不大于5%,消除爆炸条件。
二、工艺方案以4台轻质油内浮顶储罐组成的罐组为例,设计方案如下:1.内浮顶储罐改造1)在储罐罐顶透光孔法兰盖处增加开口,用于安装氧气浓度检测器。
2)封堵储罐罐壁的通气口,同时在罐顶增加呼吸阀接口。
呼吸阀的数量及规格按照(SH/T 3007-2007)《石油化工储运系统罐区设计规范》确定。
储罐氮封管理

——储以下几种情况需考虑设置氮封设施: (1)储存易氧化、易聚合不稳定的物料; (2) 储罐内易形成爆炸性可燃气体的空间; (3)储存含硫量较高的油品,易产生 FeS 自燃。
7.4.2 对于采用氮气密封的甲B 、乙类液体储 罐还应设置事故泄压设备,如:泄压人孔、呼 吸人孔等以确保储罐的安全。 7.4.3 氮封储罐通气孔等附件的封堵宜采用可 拆卸方式,以便于氮封停止使用后能及时恢复 一般储罐方式运行。
3 罐顶呼吸阀每季度检查一次,自立式压控阀 或控制阀每月检查一次,冬季每周检查一次, 特殊气候如雨雪天气增加检查次数,并保留检 查记录。 4 氮封罐首次进油前,应对罐内氧含量进行检 测合格。 5 氮气中断时,停止油罐付油作业。
7.4.4 氮气密封储罐之间宜设置气相连通线。 气相连通线上应设置切断阀和压力检测仪表。 7.4.5 氮封系统的控制阀、压力表、压力远传 等设施宜设置在罐顶近平台处。
7.4.6 氮封的使用 (1)氮封的储罐正常情况下不宜上罐顶采样、 检尺等。必须上罐操作时,需 (1)佩戴带有氧气、可燃气体和硫化氢检测报 警功能的便携式检测仪,涉及到打开作业的, 应佩戴隔离式防毒面具。 (3)应定期对氮封罐运行情况进行检查。
- 1、下载文档前请自行甄别文档内容的完整性,平台不提供额外的编辑、内容补充、找答案等附加服务。
- 2、"仅部分预览"的文档,不可在线预览部分如存在完整性等问题,可反馈申请退款(可完整预览的文档不适用该条件!)。
- 3、如文档侵犯您的权益,请联系客服反馈,我们会尽快为您处理(人工客服工作时间:9:00-18:30)。
氮封设计方案
在储罐上设置氮封系统,维持罐内气相空间氧气浓度不大于5%,消除爆炸条件。
以4台轻质油内浮顶储罐组成的罐组为例,设计方案如下:
a)内浮顶储罐改造
1)在储罐罐顶透光孔法兰盖处增加开口,用于安装氧气浓度检测器;
2)封堵储罐罐壁的通气口,同时在罐顶增加呼吸阀接口。
呼吸阀的数量及规格按照《石油化工储运系统罐区设计规范》SH/T 3007-2007确定。
3)在储罐罐顶增加氮气接入口;
4)在储罐罐顶增加气相联通管接口。
(同一种油品的多个储罐在生产运行过程中,经常是有的储罐在进行收油作业,有的储罐同时在进行发油作业。
为节省氮气用量,我们建议在同种油品储罐之间设置气相联通管道,通过这种方法,可以实现多个运行过程中的储罐进气量和排气量的部分平衡,不仅可以减少氮气用量,同时还可以减少储罐在收油作业时的油气排放。
)
b.工艺叙述
1)在储罐内安装氧气检测器,实时监测储罐内气相空间氧气的浓度,同时将高浓度报警与氮气管道控制阀门连锁,当氧气浓度达到高浓度值时报警,连锁打开氮气阀门,向储罐内补充氮气,直至检测指标达到设定要求时连锁关闭氮气阀门。
补充氮气的流量控制使用限流孔板,流量宜控制在Q=Q1-Q2(Q1—油品出罐流量,Q2—气相连通罐中与油品出罐同时进行的油品进罐流量),且Q不应小于100m3/h,氮气管道的管径为DN50,氮气的操作压力为
0.5MPa。
氧气浓度监测信号引入控制室,以便实时监测。
控制室设氧气浓度超标报警仪。
2)同一种油品的多个储罐在生产运行过程中,经常是有的储罐在进行收油作业,有的储罐同时在进行发油作业。
为节省氮气用量,我们建议在同种油品储罐之间设置气相联通管道,通过这种方法,可以实现多个运行过程中的储罐进气量和排气量的部分平衡,不仅可以减少氮气用量,同时还可以减少储罐在收油作业时的油气排放。
联通管道的管径为DN150,气体的流通能力为
500m3/h。
管道及仪表流程图见附图-1;
氧气检测器、切断阀仪表规格书见附表。
c.仪表选型说明
1)氧气气体检测器采用电化学探头,其具有可靠性高,长期稳定性好,检测精度高及反映时间短等特点。
2)切断阀采用气动切断球阀,其具有泄露等级高,切断动作快等特点。
3)氮气补气总管上配置涡街流量计进行氮气流量监测,涡街流量计具有较好的性能价格比。
d.安装布置方案
1)氧气浓度检测器通过透光孔安装在储罐拱顶与内浮盘之间,为保证既不影响储罐内浮盘的正常升降,氧气检测器的安装高度宜为储罐内浮盘可能上升到的最高位置之上300mm。
2)罐顶氮气接口的开口方位宜位于罐顶中心部位,氮气管道在罐内部分采用橡胶软管。
为保证换气效果良好,氮气橡胶软管出口宜接近浮盘。
可在氮气橡胶软管出口连接一个环形不锈钢管,管壁水平方向上开若干个通气孔,用于向四周喷射氮气。
环形不锈钢管应固定安装在浮盘上。
3)储罐之间设置DN150气相联通管道,每个储罐的气相联通管道均应设置管道阻火器,阻火器应尽量靠近储罐接口安装,每个储罐的气相联通管道均应设置截断阀。
气相联通管道宜在罐顶之间跨接。
若罐间距较大,气相联通管道需要设在地面时,应在管道的地点设置排凝管及阀门。
4)在储罐罐顶中心位置安装带阻火器的呼吸阀,呼吸阀的数量及规格推荐如下:呼吸阀选用表
储罐容量(m3)呼吸阀个数×公称直径(mm)
10001×200
20002×150
30002×200
40002×200
50002×250
100002×300
200003×300
300004×300
500004×300
e.主要工程概况
根据上述方案对罐组(4座5000m3内浮顶储罐)进行改造,需新增如下主材:
1)管道:~420米,~2.5吨。
2)阀门:DN50,8个;DN100,1个;DN150,6个。
3)管道阻火器:DN150,6个。
4)带阻火器的呼吸阀:DN250,8个。
5)氧气气体浓度检测器:4个。
6)气动切断阀:DN50,4个。
7)涡街流量计:DN80 1个。