ug冲压模具设计教程
ug冲压模具设计教程
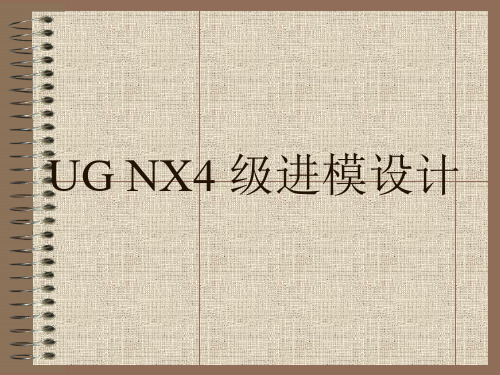
2
3
4
1
2 3
练习 弯曲组件设计 用工程初始化从bend文件夹打开a8_control_000.prt 第1步 单击 ,die节点被设为显示部件。
第2步 设置第9工位上的向上弯边所需的空间大小。
检查pdw_striptools_blank 文件,测量弯边在弯曲过程中所 需的距离值。
第6步 生成向上弯边的弯曲冲头。
8 9
5
第3步
第4步 为第1工位上最左边的3mm孔废料设计冲裁凹模 镶块
1
2
3
4
5 6
模型里包含了两个实体,一个是描述零件本身形状的实体 零件(Ture Body),一个是用来在模板上开设零件安装孔的 工具实体(False Body)
第5步 为新插入的凹模镶块设计落料孔。 1
2
3
4
两个复选框分别控制BBP 和DS板上落料孔的数量。如果 用户将For each scrap复选框选 中,所选的多块废料在BBP和 DS板上分别生成各自的落料孔。 否则,多块废料将在BBP和DS 板上共用一个落料孔。
1
2
3
4
5
7
6
4 5
第7步 设置冲头参数。 1 2
3 4
第8步 设置弯曲凹模参数。 2
1
3
4
5
6 7
局部成型组件设计 form文件夹下的装配体
第1步 为第2工位bead特征设计局部成形冲头。 34
2 5
1
6 7
8 9
10 11
12
第2步 设计局部成形凹模。
4
3
5
2
1
6
10 11
7
第10步 为凹模镶块设计落料孔。 1
冲压模具设计

冲压模具设计一、冲压模具设计的步骤1.确定需求:首先要明确冲压件的形状、尺寸和质量要求,以及加工工艺的要求,包括材料选材、工艺流程等。
2.分析冲压过程:了解冲压过程中的受力情况,确定冲压件的受力情况,考虑冲压件的结构和形状。
分析完成后,可以确定模具的结构和工作原理。
3.制定设计方案:设计方案是根据需求和分析决策,形成的模具设计的主要思路,包括模具的结构形式、材料选材、零件加工工艺等。
4.细化设计:在设计方案的基础上,进一步细化设计,包括每个零件的尺寸、形状和工艺要求,确保每个零件都符合设计要求。
5.制作样品:制作模具样品,进行试验和调试,验证设计方案的可行性,确定调整和改进方案。
6.定稿设计:根据试验结果,对设计方案进行调整和优化,形成最终的设计方案。
二、冲压模具设计的关键要点1.良好的受力结构:冲压模具在工作过程中要经受巨大的冲击力和挤压力,因此必须具备良好的受力结构,包括合理的分布受力、合理的受力传递和合理的受力集中。
2.优秀的耐磨材料:冲压模具的工作环境往往十分恶劣,耐磨材料可以大大延长模具的使用寿命,提高生产效率。
3.精密的加工工艺:冲压模具的加工精度直接影响到冲压件的质量,因此必须采用精密的加工工艺,确保模具的精密度和可靠性。
4.优化的结构设计:冲压模具的结构设计要尽可能简单,降低成本,提高生产效率。
同时也要考虑模具的易维护性,方便维修和更换零件。
5.可靠的试验与调试:为了保证冲压模具的质量和可靠性,必须进行全面的试验和调试,包括模具的运行测试、冲压件的检测评价等。
三、结语冲压模具设计是一个复杂而细致的工程,需要综合运用材料学、结构设计、机械加工、模具试验等多方面的知识。
只有具备扎实的理论基础和丰富的实践经验,才能设计出高质量的冲压模具。
希望以上内容对冲压模具设计有所帮助,能够指导相关行业的人士更好地进行冲压模具设计工作。
冲压模具设计是一个复杂的过程,需要设计人员深入且全面地了解冲压工艺、材料特性、机械结构、模具加工工艺等多方面知识,并且需要经验丰富的工程师进行设计。
UG模具设计实用技巧

UG模具设计实用技巧一、合理的模型准备在进行UG模具设计前,首先需要对模型进行准备。
这包括模型的导入、几何形状的修补和分离等。
在导入模型时,需要确保模型文件格式正确且完整,避免导入错误或缺失部分;在修补模型时,需要修复模型表面的孔洞、尖锐边或褶皱等问题;在分离模型时,需要将需要设计的部分单独提取出来,方便后续的设计操作。
二、标准件库的使用UG软件自带了丰富的标准件库,使用这些标准件可以大大简化设计过程,提高设计效率。
在进行模具设计时,可以先查找标准件库中是否存在所需要的标准件,并将其导入到设计模型中,然后对其进行必要的修改调整。
这样可以避免从头开始设计标准件,减少工作量。
三、合理的构思和设计在进行UG模具设计时,需要根据实际需求进行合理的构思和设计。
不同的模具有不同的设计要求,需要考虑到模具的结构、功能和加工工艺等方面。
在进行设计时,需要全面考虑各种因素,如模具的易于装配和拆卸、模具的强度和稳定性、模具的使用周期和维修方便性等。
同时还需要充分利用UG软件的分析功能,进行模拟和检查,确定设计的可行性和合理性。
四、灵活的参数化设计在进行UG模具设计时,可以利用UG软件的参数化设计功能进行设计。
通过定义和控制参数,可以方便地修改和调整模具的尺寸和形态。
这样可以大大增加设计的灵活性和可修改性,减少设计重复工作。
同时还可以通过参数化设计,快速生成多个类似的模型,提高设计效率。
五、充分利用UG软件的分析功能UG软件具有强大的分析功能,可以进行模拟、分析和优化等操作。
在进行UG模具设计时,可以通过分析功能对模具进行强度、刚度和可行性等方面进行验证。
通过模拟和分析,可以找出设计中的问题,并对其进行调整和优化。
这样可以使设计更加合理和可靠,提高模具的质量和效率。
六、合理的设计结构在进行UG模具设计时,需要设计合理的结构。
合理的设计结构可以提高模具的稳定性和精度,降低零件的加工难度和成本。
在设计时,需要注意模具的分段、引导、润滑和保护等方面。
UG智能冲压模具原型系统设计

文 章编 号 : 1 6 7 3 — 9 9 6 5 ( 2 0 1 3 ) 1 0 ~ 8 0 4 — 0 5
UG 智 能 冲 压 模 具 原型 系 统设 计
校 江超
( 西 安 工 业 大 学 机 电 工程 学 院 , 西安 7 1 O 0 2 1 )
摘 要 : 以 UG NX 4 . 0为 C AD 平 台 , VC+ + 6 . 0为 集 成 环 境 , 使 用第三方软件接 1 : 2函数 UG/ OP E N AP I 对 UG 二 次开发技 术进行 研 究 , 并 将 冲压件 特征 识别 、 C AP P和 UG二 次 开发
平台, 以 Mi c r o s o f t 公 司 的 Mi c r o s o f t Vi s u a l C + +
取 冲 压件 的制造 特 征 和 特 征 参 数并 传 递 给 冲压 件
C AP P模块 , 同时输 出 特 征 和 特 征 参 数 , 特 征 识 别
模 块 运行结 束 ; C AP P模 块在 特 征识 别模 块 运行 结 束 并 接收 到其 传 递 的数 据后 , 进行 工 艺决 策 , 将 工 艺数据 传递 给模具 生成模 块 , 并 输 出工 艺 数 据 ,
作者简介 : 校江超 ( 1 9 7 8 一 ) , 男, 西 安工业 大学讲师 , 主要研究方 向为机械 C A D / C A M. E — m a i l :  ̄ c 1 0 2 7 @1 6 3 . C O I T L
第 1 O期
校 江超 : UG智能 冲压模具原型 系统设计
8 0 5
件C AP P模 块 和模具 生成 模块 .
获 取 了特征 号 , 即获 取 了制 造 工艺 , 只需 要 对 此 工
ug冲压模具设计教程

1
3
UG NX4 级进模设计(PDW)
4
UG NX4 级进模设计(PDW)
5
6
7
UG NX4 级进模设计(PDW)
局部成型组件设计 form文件夹下的装配体 文件夹下的装配体 工位bead特征设计局部成形冲头。 特征设计局部成形冲头。 第1步 为第 工位 步 为第2工位 特征设计局部成形冲头
3 4
第6步 生成向上弯边的弯曲冲头。 步 生成向上弯边的弯曲冲头。
1
2 3 4 5 7
6
UG NX4 级进模设计(PDW)
4
5
UG NX4 级进模设计(PDW)
第7步 设置冲头参数。 步 设置冲头参数。
1 2
3
4
UG NX4 级进模设计(PDW)
第8步 设置弯曲凹模参数。 步 设置弯曲凹模参数。
2
,将其他的部件隐藏,只显示Strip 将其他的部件隐藏,只显示
注意:新生成的组件会被设为可见, 注意:新生成的组件会被设为可见,所以在设计新的组件 之前,将其他的组件设为不可见, 之前,将其他的组件设为不可见,新生成的组件将不会受到影 在实际应用中,如果装配模型很大, 响。在实际应用中,如果装配模型很大,为了简化图形窗口的 显示, 将以前设计的组件隐藏。 显示,常使用 将以前设计的组件隐藏。 第3步 步
2 5 1
UG NX4 级进模设计(PDW)
6 7
8
9
UG NX4 级进模设计(PDW)
10 11
12
UG NX4 级进模设计(PDW)
第2步 设计局部成形凹模。 步 设计局部成形凹模。
4 3 5 2 1
UG NX4 级进模设计(PDW)
7 6
UG NX 10.0模具设计教程第4章
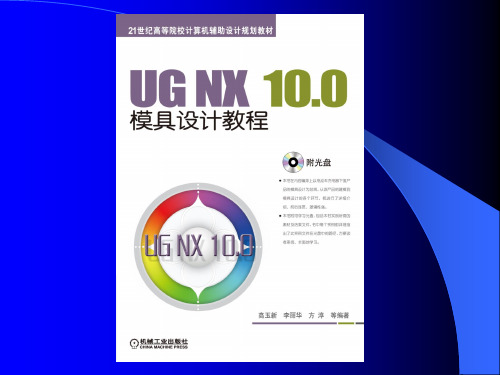
【例4-2】 定义模具坐标系 继续以例4-1的模型进行讲述,首先打开附带光盘 ch04/ch04_02_02中的顶层装配文件“shiduyi_top_050”,操作步骤 如图4-12所示。
2
1
3
图4-9
3)完成产品模型加载后,系统会自动载入一些装配文件,并自动保
存在项目路径下
4.3 模具坐标系
模具坐标系是所有模具装配部件的参考基准,它的正确设置与
否直接关系到模具的结构设计。在定义模具坐标系之前,首先要 分析产品结构,弄清产品的开模方向及分型面所处的位置;然后
通过坐标系的移动及旋转操作将模型的工作坐标系调整到产品模
默认的参数,单击“确定”按钮,生成工件,如图4-4所示。
图4-4
4.型腔布局
8
8
单击“注塑模向导”工具栏中的“型腔布局”按钮,弹出“型腔 布局”对话框,其操作过程如图4-5所示。
1
3
2
4
5
图4-5
4.2 初始化项目
UG NX 10.0 模具设计中产品模型 的加载是通过“注塑模向导”工具栏 的“初始化项目”工具按钮来完成, 并可设置项目的名称及保存路径。
1.插入腔 2.变换
3.移除
移除功能用于对工件进行移除操作。选择待移除工件后,单击“移除” 按钮即可,但至少留下一个型腔。
4.自动对准中心 自动对准中心的功能是将模具坐标系自动移动到模具布局的中心位置, 该中心位置将作为模架的调入中心。单击“编辑布局”分组中的 “自动对准中心”按钮,即可执行模具坐标系对中操作。 【例4-4】 型腔布局
ug冲压模具设计教程

ug冲压模具设计教程UG冲压模具设计教程UG软件是一款功能强大的三维建模软件,广泛应用于机械设计和制造领域。
在冲压模具设计中,UG软件的使用可以极大地提高设计效率和准确性。
本教程将介绍UG软件在冲压模具设计中的常用功能和技巧,帮助初学者快速上手和掌握相关技能。
一、UG软件基础知识在使用UG软件进行冲压模具设计前,需要掌握一些基础知识,包括软件界面布局、基本操作和常用工具。
在软件界面布局方面,可以通过调整工作区和视图窗口来使软件界面更加适合自己的使用习惯;在基本操作方面,需要熟悉鼠标操作和快捷键,例如左键选择、右键菜单和中键旋转等;在常用工具方面,需要掌握绘制几何体、编辑实体和创建装配体等操作。
二、冲压模具设计流程冲压模具设计的流程一般包括产品分析、零件设计、模具设计、装配设计和检测分析等步骤。
在产品分析阶段,需要对产品进行外形分析、尺寸分析和材料分析,确定设计方案;在零件设计阶段,需要绘制产品的零件图形,并考虑冲压工艺要求;在模具设计阶段,需要根据零件图形设计冲压模具的上模、下模和导向装置;在装配设计阶段,需要将上模、下模和导向装置进行装配,并进行运动仿真;在检测分析阶段,可以使用UG软件提供的检测工具进行冲压仿真和分析。
三、常用UG软件功能1. 建模功能:UG软件提供了丰富的建模工具,包括绘制二维图形、创建三维实体、布尔运算和曲面建模等。
通过这些功能,可以根据零件的形状和尺寸要求进行建模。
2. 编辑功能:UG软件具备强大的编辑功能,可以对零件进行参数化编辑、实体编辑和几何体编辑。
这些编辑功能可以方便地修改零件的尺寸、形状和特征,满足冲压工艺的要求。
3. 组装功能:UG软件提供了组装功能,可以将零件组装成模具,并进行运动仿真。
通过模具的组装和运动仿真,可以检验模具的合理性和运动性能,避免设计上的问题。
4. 2D图纸功能:UG软件具备绘制2D图纸的功能,可以根据零件和模具的3D模型生成2D图纸。
通过2D图纸,可以提供给制造部门进行加工和组装。
2012_ug冲压三维模具设计

摘要 ............................................................................................................................. 错误!未定义书签。
第一章绪论.......................................................................................................... 错误!未定义书签。
第一节目的...................................................................................................... 错误!未定义书签。
第二节设计任务.......................................................................................... 错误!未定义书签。
1. UG软件使用........................................................................................... 错误!未定义书签。
2. 零件冲压方案......................................................................................... 错误!未定义书签。
3. 模具结构设计......................................................................................... 错误!未定义书签。
第三节设计要求................................................................................................ 错误!未定义书签。
UG模具设计基础教程

1.4 注塑成型模具基础
• 2 注塑成型的工艺过程
• 加料:将粒状或粉状塑料原料加入到注塑机的料斗中,并使用柱塞或螺杆带入料筒。 • 塑化:加入的塑料在料筒中经过加热、压实和混料等过程后,使其由松散的原料转变为
熔融状态并具有良好的可塑性的均化熔体。 • 充模:塑化好后的熔体被柱塞或螺杆推挤至料筒的前端,经过喷嘴、模具浇注系统进入
1.4 注塑成型模具基础
• 5 分型面的选择 合理选择分型面举例 (3)型腔排气顺利
型腔气体的排除,除了利用顶出元件的配合间隙外,主要 靠分型面,排气槽也都设在分型面上。因此,分型面应该 选择在熔体流动的末端。
1.4 注塑成型模具基础
• 5 分型面的选择 合理选择分型面举例
(4)确保塑件质量 右图所示的塑件,为一双联齿 轮,要求大、小齿、内孔三者 保持严格同轴,以利于齿轮传 动平稳,减小磨损。若将分型 面按图(a)设计,大齿和小齿 分别在定模和动模,难以保证 二者良好的同轴度,若改用图 (b)中方案使分型面位于大齿 端面,型腔完全在动模,可保 证良好的同轴度。
1.4 注塑成型模具基础
• 1 注塑模具的成型理论 在模具开始工作,将加热融化的塑料注满一个挖有空腔的模块,然
后对模块强制冷却,熔料凝固成固体。为了取出凝固体,用分型面把 模块分割成型芯和型腔两部分。包裹凝固体外表面轮廓的一半模块称 为型腔工件,包裹凝固体内表面轮廓的另一半模块称为型芯工件,型 芯和型腔零件统称为成型工件。包裹着凝固体内外表面的相交线称为 分型线。分型线水平地向四周延伸形成切割模块的分型面。实现把分 型模腔方法按照适当的比例(1+收缩率)加工成需要的形状,凝固体 就成为了有用的塑料制品。
1.4 注塑成型模具基础
• 6 浇注系统设计
UG NX 10.0模具设计教程第2章
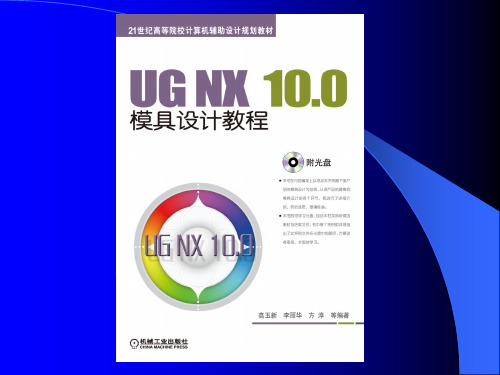
2.3 特征操作
特征操作是对已创建特征模型进行局部修改,从而对模型进行细化,
也叫细节特征。通过特征操作,可以用简单的特征创建比较复杂的特征 实体。常用的特征操作有拔模、边倒圆、倒斜角、镜像特征、阵列、螺 纹、抽壳、修剪体等。
2.3.1 拔模
1
3 选择固定面 1 2
3 选择固定边
2
4 捕捉该点
5
4 选择拔模面
生成扫掠特征(操作文件见附带光盘ch02/ch02_02/saolue.prt)。
1 选择截面 2 选择引导线
图2-47
3
2.2.6 布尔运算
1.和运算 和运算将两个或两个以上的实体组合成一个新实体。 2.差运算 差运算将目标体中与刀具体相交的部分去掉而生成一个新的实体。 3.交运算 相交运算截取目标体与工具体的公共部分构成新的实体。
创建一段圆弧,如图2-24所示,同时系统自动显示相切符号。双击图中的尺寸
R25.5,在弹出的文本框中输入R23.29并单击鼠标中键确认,绘制第一段圆弧,如 图2-25所示。
2.2 实体建模
2.2.1 实体建模概述
常用术语 UG 实体建模中,通常会使用一些专业术语,了解和掌握这些术语是用户进行实体
建模的基础,这些术语通常用来简化表述,另外便于与相似的概念相区别。UG实
图 2-37
4 选择孔的放置面 1 5
2
3 6 修改孔的定位尺寸
7
图2-38
2.2.5 扫描特征
扫描特征包括拉伸、回转、扫掠等特征。其特点是创建的特征与 截面曲线或引导线是相互关联的,当其用到的曲线或引导线发生 变化时,其扫描特征也将随之变化。 1.拉伸
生成实体
封闭曲线 生成片体
UG教程模具编程设计
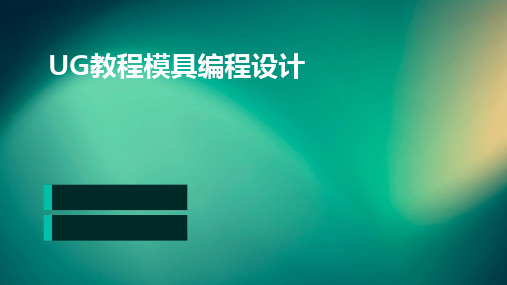
contents •模具编程设计概述•UG软件基础•模具编程设计前期准备•UG模具编程设计实战•模具编程设计后期处理•UG模具编程设计案例解析目录01模具编程设计概述提高生产效率保证产品质量降低生产成本030201模具编程设计的目的和意义模具设计需求分析编程与仿真试模与调试加工制造模具编程设计的流程模具编程设计的常用软件AutoCAD SolidWorksMastercam UG(Unigraphics)02UG软件基础UG具有强大的建模、装配、工程图、钣金设计、注塑模具设计等功能,支持参数化设计和直接建模。
UG软件支持多平台操作,可在Windows、Linux等操作系统上运行。
UG(Unigraphics NX)是一款高端CAD/CAM/CAE软件,广泛应用于航空航天、汽车、模具、机械制造等领域。
UG软件简介UG软件界面及功能介绍功能模块界面组成UG软件包含建模、装配、工程图、钣金设计、注塑模具设计等模块,各模块之间相互独立又相互联系。
定制界面分析操作包括距离测量、角度测量、面积测量等分析命令,用于评估模型尺寸或者形状。
包括移动、旋转、缩放、镜像等编辑命令,用于修改模型形状或者位置。
选择操作包括单选、框选、全选等操作,用于选择对象进行编辑或者分析。
文件操作包括新建文件、打开文件、保视图操作UG 软件基本操作03模具编程设计前期准备分析产品结构确定分型面设计浇注系统设计冷却系统模具结构分析与设计加工工艺规划确定加工设备根据模具的结构和尺寸,选择合适的加工设备,如铣床、磨床、电火花等。
制定加工流程根据模具的结构和加工要求,制定合理的加工流程,包括粗加工、半精加工、精加工等阶段。
选择切削参数根据加工设备和刀具的性能,以及模具的材料和硬度等因素,选择合适的切削参数,如切削速度、进给量、切削深度等。
刀具选择与参数设置选择合适刀具设置刀具参数优化切削条件04UG模具编程设计实战分型面设计原则分型面设计应遵循产品形状、脱模方向、加工精度等原则,确保模具顺利脱模并满足产品精度要求。
UG模具设计基础教程(NX 6版) 课件 第二章
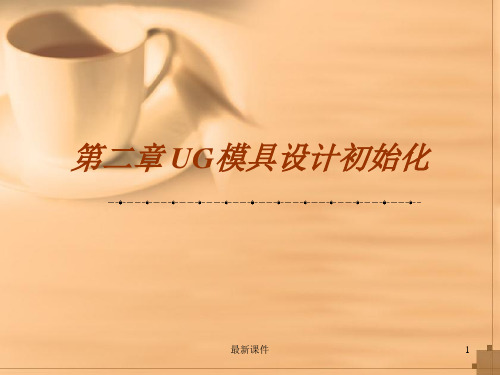
图标,弹出 “打开”对话框。
最新课件
4
2.1加载产品和项目初始化
在“打开”对话框的 指定路径中选择产品 零件文件,单击“OK” 按钮,系统将自动进 行项目初始化操作, 并弹出 “初始化项目” 对话框。
最新课件
5
2.1加载产品和项目初始化
材料和收缩率选项
通过选择“材料”下拉列表中的选项,如图2-4所示,即 可确定材料的收缩率。也可以单击“编辑材料数据库”图 标,在打开的Excel图表中编辑材料的收缩率。
2-4
最新课件
2-5
6
2.1加载产品和项目初始化
项目单位
该选项组是设置在项目中长度的单位,有“英寸” 和“毫米”这两个选项。
重命名组件
通过勾选该选项,可以在下一 步打开的“部件名管理”对话框中 对项目中所用的文件名称进一步 进行设置。
XC-YC平面的位置不最变新课。件
14
2-11
2.3设置模具收缩率
在注塑模向导工具栏中单击“收缩率”图 标,弹出 “缩放体”对话框 。
最新课件
15
2-12
2.4设置模具工件
工件是用来生成模具的型芯和型腔的实体, 并且与模架相连接。所以工件的尺寸的确 定以型芯或型腔的尺寸以及标准模架的尺 寸为依据 。
第二章 UG模具设计初始化
最新课件
1
目录
➢2.1加载产品和项目初始化 ➢2.2 定义模具坐标系 ➢2.3设置模具收缩率 ➢2.4设置模具工件 ➢2.5型腔布局 ➢2.6多件模 ➢2.7实例——模具设计初始化
最新课件
2
2.1加载产品和项目初始化
1、加载产品
2、项目装配和产品装配
冲压模具设计技术手册优秀课件

3-2 不繡鋼類下料沖切刀間隙,以料厚5%~7%
單邊間隙,而STRIPPER INSERT之間隙視 料厚而定,以0.003/SIDE---0.005/SIDE為宜.2004/1/Fra bibliotek3/21
上減少不必要之肉厚改善.(如下圖)
原沖子形狀改為:
可減少此段之PG(光學磨床)研磨加工時 間及金錢,但不影響沖子之本身功能.
5-2 原沖子形狀改為.(如下圖所示)
減少肉厚以減少研磨時間及成本,但還不影響沖 子強度沖子根部尺寸太大,則光學研磨會磨掉很
多材料,而造成沖子壓槽被磨掉.
2004/1/
5/21
2004/1/
21/21
22-2. 下模背板中之線割下料尺寸為DIE INSERT中之下料尺 寸單邊加0.5MM.
22-3. 下模座中之線割下料尺寸為DIE INSERT中之下料尺寸 單邊加0.1MM.
22-4. 導料板逃STRIPPER INSERT或沖子之深度(如圖之D)最 好不可太深,不然導料板铣切後熱處理時會變形,D至 少小於1/2W(如圖所示)
冲压模具设计技术 手册
1 LAYOUT資料: PITCH料寬.工站及
衝切間隙
MM
使用材料
厚x寬xCON
使用機械
T
成品毛重
GM/PCS
閉合高度
MM
送料PITCH
MM
2 沖子所需之剪斷力=周長x厚度x材 料標準之剪應力.
2004/1/
2/21
3.刀口零件間隙:
3-1 端子銅材類下料沖切間隙,以料厚4%~5%
冲压模具设计手册
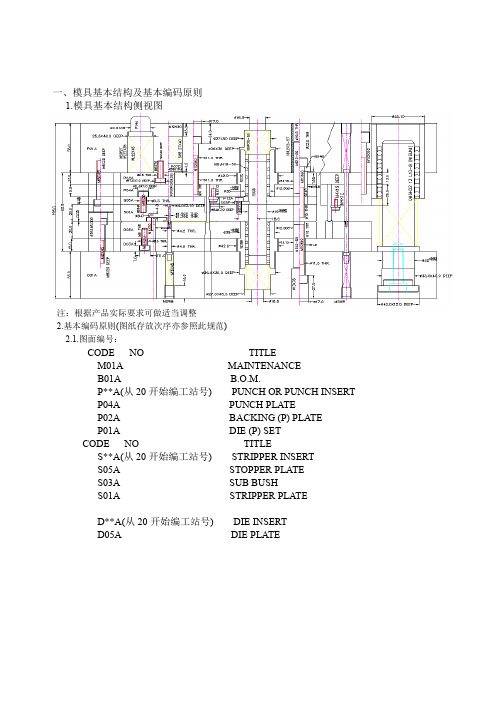
一、模具基本结构及基本编码原则1.模具基本结构侧视图注:根据产品实际要求可做适当调整2.基本编码原则(图纸存放次序亦参照此规范)2.1.图面编号:CODE NO TITLEM01A MAINTENANCEB01A B.O.M.P**A(从20开始编工站号) PUNCH OR PUNCH INSERTP04A PUNCH PLATEP02A BACKING (P) PLATEP01A DIE (P) SETCODE NO TITLES**A(从20开始编工站号) STRIPPER INSERTS05A STOPPER PLATES03A SUB BUSHS01A STRIPPER PLATED**A(从20开始编工站号) DIE INSERTD05A DIE PLATED03A BACKING (D) PLATED01A DIE (D) SETA03A PROGRESSIVE (P) DIEA02A PROGRESSIVE (D) DIEA01A PROGRESSIVE (P&D) DIEL03A STRIPPER LAYOUTL02A ARRANGEL01A FINAL FORMING2.2.基本孔位编号:编码注解A 下模座主导柱孔,上模座主导套孔.(M10-35)B 下模板副导套孔,下垫板,下模座让位.剥料板副导柱孔.冲子固定板副导柱孔,上垫板,上模座让位.C 下模板M10螺丝孔,下垫板直径11.0 mm,下模座M10沉头孔深27mm.(M10-60)冲子固定板M10螺丝孔,上垫板直径11.0mm,上模座M10沉头孔深24mm.(M10-60)D 下模板直径12.006mm合销孔,下垫板直径12.10mm,下模座12.006mm合销孔.(MS12-50)冲子固定板直径12.006mm合销孔,上垫板直径12.10mm,上模座直径16.5mm.(MS12-50,KNLB12-57)E 下模板M6螺丝孔,下垫板M6沉头孔.(M6-20)剥料板M6螺丝孔,剥料垫板直径6.5mm,冲子固定板让位直径11mm深7mm.(M6-20)上模座M6螺丝孔,上垫板M6沉头孔.(M6-20)F 下模板M4螺丝孔,导料板直径4.5mm,剥料板让位直径8mm深(导料板厚度+5).(M4-12)冲子固定板M4螺丝孔,剥料垫板让位直径8mm深7mm .(M4-12)G 下模板直径4.020mm合销孔,导料板4.006合销孔.(MS4-10)剥料板直径4.020mm合销孔,剥料垫板直径4.006mm合销孔.(MS4-10)H 下垫板直径4.5mm孔,下模座直径6mm.I剥料板导料销孔.下模板浮升销孔直径4.2mm,下垫板直径4.5mm,下模座弹簧孔,M8止付螺丝.J 下模板固定SENSOR M3螺丝孔.(M3-12)K 下模座固定SENSOR M4 螺丝孔.(M4-12)L 下模座STOPPER M8螺丝孔.(M8-45)上模座STOPPER M8螺丝孔.(M8-45)M 下模板直径2mm,让位导料销.N下模板案内孔(五金零件).O剥料板M10螺丝孔(等高套筒),冲子固定板直径16.5mm,上垫板直径16.5mm, 上模座直径22mm.(M10-60)P 剥料板M5螺丝孔(压副导柱).(M5-15)R 冲子固定板传力销孔直径13.5mm,上垫板直径13.5mm,上模座M30止付螺丝.S 上模座快速定位孔.3.模板厚度及材质一般标准(一般状况下,PUNCH定长):T≤1.0 T>1.0P01A 58.0 MM 58.0 MM S45CP02A 15.000 MM 15.000 MM D2P04A 18.000 MM 18.000 MM SKD11 (超深冷处理)S05A 9.000 MM 9.000 MM SKD11S01A 20.XXX MM 25.XXX MM SKD11 (超深冷处理)D05A 20.000 MM 25.000 MM SKD11 (超深冷处理)D03A 15.000 MM 15.000 MM D2D01A 55.0 MM 55.0 MM S45C三、新模设计标准步骤1.蓝图核对1.1.按蓝图重新绘制AutoCAD档1.2.确认尺寸正确性1.3.确认公差链的正确性1.4.产品尺寸公差缩放缩放原理:由于产品冲出来之后,总是存在微小的毛边(一般情况下).其内孔一般偏小,外形一般偏大(毛边的大小与冲裁间隙及冲子与刀口的锐利度有关).2.产品图的尺寸展开展开原理:利用体积不变的原则:用某一截面的总面积去除以材料厚度可得到该方向的展开长度,其实展开就是同一尺寸也因各人经验而异,没有绝对的一个数值,只要在公差范围即可展开要点:步骤如下2.1.看懂产品图(展开前的基本要求)2.2.弄清楚产品的材厚和材质2.3.具体展开计算2.3.1.用体积法(一般适合有变薄的弯曲)2.3.2.用展开计算公式由于产品在弯曲过程中有的地方被拉长或压缩但总可以找到某一层的弯曲线长度是不变的,这一不变的层叫中心层(不是中间层),我们就是利用中心层来进行展开的:因此,我们想进行展开,就必须找出中心层,如图1设中心层系想为K,变曲内半径为r,材料厚度为t,变曲角为a,L1,L2为直线部分长度,展开长度值为L,那么则有L=L1+L2+2 (r+kt)a/360中心层系数K的大小根据实践经验可按下列公式选取1):当r/t<=0.50时k=0.252):当0.5<r/t<=1.0时k=0.25~0.303):当1.0<r/t<=2时k=0.30~0.334):当2.0<r/t<=4时k=0.33~0.385):当r/t>4.0时k=0.38~0.45此公式适合一切材料厚度的弯曲展开计算,具体在实践应用中,当R/T取上限时,K也应取上限值,如当R/T=0.5时,K=0.30*当r/t=0~0.5时,即所谓的清角,此时k=0.25t~0.3t,若是90︒清角率曲时L=0.4~0.45t”的值是一样的,只不过后者是前者的一个特例,在此推算一下.L=2 K/4=2 *0.25t/4= t/8=0.3925t=0.40tL=2 K/4=2 *0.30t/4= t/8=0.4710t=0.45t也就是说当清角90︒弯曲时用L=0.4t~0.45t或K=0.25~0.30t两个公式来展开计算都行2.4.当包圆时,此时展开计算公式已和上面不一样,因为包圆时,材料厚度变薄很小,或都几乎不变,中性层接近中间层2.4.1.当包小圆时(∅D<5.0),其中心层系数K=0.452.4.2.当包圆时5.0<∅D<10.0)其中心层系数K=0.45~0.502.4.3.当包大圆时(∅K>10.0),其中心层系数K=0.5~0.552.5.通过查表,找出中心层系数的大小,再进行展开计算也行,在此不作详细叙述2.6.产品的圆角处理:产品上的圆角一般保持不变它,但若是尖角,一般用最小圆角R0.13去拟化它,对于产品上R0.1的圆角,尽量用R0.13去代替;对于R<0.1的圆角或清角,如果是重要尺寸(改变会影响功能)则不变它,采用过切来达到要求图12.7.举例如下:2.7.1.如圆3所示:设材料厚度为0.15元素实体内半径系数比中心层半径元素角度元素展开长度总和Entity IN-Radius r/t CNE-Radius Angle LINE-Length (+)total 线段1 ------ ------ ------ 170.000︒0.5953 0.5953 圆弧2 0.400 0.4/0.15 0.46 60.000︒0.4817 1.077 线段3 ------ ------ ------ 110.000︒0.5521 1.6291 圆弧4 0.250 0.25/0.15 0.3025 70.000︒0.3696 1.9987 线段5 ------ ------ ------ 0.000︒ 3.0210 5.0197 圆弧6 0.000 0.000 0.000 90.000︒0.0589 5.0786 线段7 ------ ------ ------ 90.000︒ 1.0000 6.0786 圆弧8 0.300 0.3/0.15 0.36 120.000︒0.7540 6.8326 线段9 ------ ------ ------ 210.000︒0.8000 7.6346 该图形的展开总长7.6346,取7.63,在展开时,直线部位可取材料厚度的任一边,(因为两两产行相等)在圆弧部分,必须是内r偏离一个Kt距离,再用LIST命令量出这个半径为r+Kt的圆弧的长度,就是圆弧部分展开长度技巧:找出中心层后可把中心层各段直线圆弧首尾连接起来,再用PE命令把直线和圆弧编辑成一条多义线,再用len命令量出这条多义线的长度(即展开总长):这样快一点可以省略一个个去相加如本例中:1.2.3;4.5;7.8.9可把这9条线段编辑成1条多义线,再量出长度即可得展开全长如图42.7.2.如图5所示:设材料厚度为0.25从图中可以看出:向上弯曲的两个耳朵材料已经被挤薄了(0.12)那么在展开时,就只能按体积计算了其展开长度L=L1+L2*t1/T3.按照成形步骤排出成形分解图排样原理:一根料带经过冲孔落料压毛边接伸抽蕊弯曲成形各个工序,最后形成产品的过程,现在你做的如何组织这些工步:哪个在前,哪个在后,总共要多少工步,各工序之间互相调协,使其承前继后,合情合理排样设计:步骤如下4.1确认产品展开尺寸后,根据产品的毛边方向,确定冲裁和成形方向,无毛边要求时一般不受限制;若产品上有毛边方要求时,这时一定要注意它的冲裁和成形方向:向下还是向下成形)冲孔毛边留在刀口面,落料毛边留在冲子面:一般机箱外壳类零件出于使用美观和安全性能要求,其毛边要留在产品的里边(成形的内边)如图6图7属于外壳类电子五金零件,如果图低上有毛边要求时,则要按要求去做,没写毛边要求也应尽量让志边留在里边,若成形更方例,也可留在外边;如图8已规定毛边方向,只能向下成形4.2.依据产品展开尺寸,精略估算步距(PITCH=产品该方向最大长度+1.0~2.0-中间有连接带除外)用ARRAY命令作出横排,纵排,对称排,交错排,斜排(很少用)几种方案,进行分析,比较,综合,在保证产品顺利生产出来的前提下,选择最佳方案,肯体注意以下几点:4.2.1.第一要考虑这样排成形是否容易和稳定,后一工步是否对前量工步已成形好的产生破坏作用,或者后一工步无法成形,冲子和入子强度是否足够4.2.2.第二要考虑料带在模具中能否顺利送料,前一工步成形之后能否继续平稳送过下模板厚度的1/2:因为太高易引起摆动,料带定位不准和变形;连接带(又叫载体-CARRY)有以下几种形式A.无连接带,属于无废料排样,零件外形往往具有对称性和互补性,通常采用单PIN切断落料或双PIN一个落料一个切断,如下图9.B.边料连接带,是利用条料搭边废料作为载体的一种形式,这种载体传送料带强度较好,简单,主要用于落料型排样中,如下图10.A.无连接带该产品无连接带排样采用单侧裁边定位四种方案都行,前两种采用切断形式,产品从旁边滑下去,后两种采用落料形式,一个落下去另一个从旁边滑下去,此种排样形式特点:材料利用率高,毛刺方向不一致,产品精度氏,应用很少.B.边料连接带特点条料导向性好,易收集,为了提高材料利用率,连接带可取小些,一般双需2.0~4.0即可.该产品采用先冲孔后落料方式生产,采用搭边产料作连接带,并先冲一导正孔作定位孔,如果产品上有现成圆孔且圆孔精度要求不高时(即公差较大)可采用该圆孔作导正孔由于产品一般有毛边要求:毛边不能过大,因此下模板刀口常做镶拼式入子结构形式(有的产品批量很少,也不做入子)由于刀口入子四周壁厚即L值)一般取4.0~3.0mm在排样时要注意两个入子之间的距离(即L1值)一般要>=2.0,少于时要么移到下一工步,要么割通两入子相连,如上图第五工步向前移一工步与第三工步相边,这样将会缩小模板的尺寸.C.单连接带,是在产品条料的一侧留出一定宽度的材料,并在适当位置与产品相连接,实现对产品条料的运送,一般适合切边型排样,如下图11,图12,图13,图14,图15,图16.图11:图12:图13:图14:图15:图16:说明:由于产品一般有电镀和装配要求,对于小电子五金零件,为电镀和装配方便,大多数采用料带的形式先打预断,电镀后装配时再用手或机械手折断,当然也有少数采用落散PIN的形式,具体形式依图低要求或与产品工程师磋商.单连接带特点:比双连接带宽度要大,在冲压过程中条料易产生模赂弯曲,无载体一侧导向较困难,单连接带每边连料宽度一般为3.0~5.0,材料越宽越薄,取较大值.图11:材料较厚,加上料宽较小,连接带宽度取得较小.图12:与图11差不多,它是单个落料形式,由于材料较薄且条料较宽,为了增加条料传送的强度,连接带应适当加宽注意点:1).单连接带适合大多数五金电子小零件,但必须保证条料运送哟度,料带不能太宽(W<70~60),不过在实践应用中,有时考虑产品生产批量较大,或为了提高材料利用率,常常采用双向排(如图14)或双向交叉排(如图15),实际上就是一模出两根料带并且尽可能想办法在两个产品相邻的地方找出合适的部位以一定的宽度W>0.5(没有成形的部位)把两边料带相连起来(类似双连接带动-不防叫”手牵手”),这样大大增加整个料带的强度,可以先打凸点,压毛边,成形等一切做好之后,再把”手牵手”部位冲掉即可,这样料带在模具中传送顺利,定位性好,成形稳定;要不然就会经常出现卡料或”打架”,当然这种情况适合”分手”之前有较多的成形工步(>1),如果仅仅一工步,倒不必多费心思了.2).当然并不是所有的都采用双排(它双适合批量较大或节约材料而且两料带双互不干涉时采用),实践证明,一根条料分出的料带数越我,PIN数越高,生产过程俞不稳定,且冲出来的产品精度也就是越低,故在设计排样时,在能冲出合格产品的前提下,工步数越少越好,这样模板尺寸也小一些.因此,产品成形工步较多时,采用双排样而又无相连的地方,肯定是行不能的,双能采用单排(如衅16)3).单连接带送料时,如果两成形之间成开时互不影响的话,那么最好先落这部分料,接着成形;再落另一部分料,再成形,这样分部做,它的目的是使料带有足够的强度,增加压料面积,提高成形部位的定位精度,增强成开拓的稳定性,如图16,冲破第3工站料,再成形尾端部分.D.双连接带,是在产品条料的两侧分别留出一定宽度的材料,并在适当位置与产品两边相连接,实现对产品条料的运送,它比单连带运送便顺利,料带定位精度更高,它适合产品两端都有接口可连,特别适合材料(T<=0.4)较薄时,料带运送强度较弱的情况,如下图17和图18.图17:图18:双向排(如图14):把产品展开后,确定与连接带相连的地方及宽度,再把该当产品展开图和连接带整体旋转180度,再放在原产品相对应的适当位置,既可以放在对称的位置,也可以与之交叉,关键是看能否节省材料以及两者之间是否有连料的地方;在排放时,两者之间的最小间隙@(T<0.5时,@>0.5~1.2,T>0.5时,@>1.0~2.0)应达到冲子的强度,太小冲子易断,太大又浪费材料,同理,在确定步距时也是如此,因此要根据材料厚度来选取一个合理的数值,通常取1.0左右即可.双连接带特点:送料顺利,定位精度较高,耗料较多,当条料宽度W<30时,双需一边采用导位针定位即可,条料宽度W>30时一般两边都采用导位针双连接带每边连料宽度一般为2.0~5.0,材料越宽越薄,取较大值.双连接带适合一般外壳类五金小零件.图17:材料较薄且料较宽,连接带取了5.0,当然取4.0也行.图18:由于材料较薄且料带较宽,采用桥梁式双连接带,其送料,导向强度均较好,实践证明其中间连接带宽度3.0取2.0也行,这样步距离可减少1mm,将节约材料.其最后一工步裁废料可要可不要,一般根据各厂冲压生产设备而定,若有自动收料装置时,可不要裁废料这一步,不过最好还是设计进去,到时采用自动收料时,双需切断冲子不装就行了.图18料带的料宽,步距和浮升高度设计计算过程如下:已知产品的展开尺寸长为19.74,宽29.22,采用模向排样,料宽W=宽19.22+2*连接带(2X4.0)+2*冲子最小厚度(2X1.0)=39.22=40.0(最好以0.5以单位取整)步距P=长19.74+1*连接带(1X3.0)+2*冲子最小厚度(2X1.0)=24.74=25.0浮升高度P(min值_=产品厚度3.05(因为后面有切断刀口挡佳它>=3.05)+底下凸起0.94(在送往后一工步中为了不再在模板上铁槽让位)+让位间隙量 1.0(一般取1.0~3.0)=4.99=5.0E.中心连接带,与单载体相似,是在产品条料的中间留出一定宽度的材料,并与产品前后两边相连它比前者节省材料,在弯曲工件排样中应用较多;因为导正梢孔在中间常引起拉料,故常需在引导针中间交错加一些弹性顶料定位针,图19和图20.图19:图20:中心点连接带特点:料带宽度方向导向困难,常出现卡料,中心载体易出现模向变曲其中心连接带宽度取值跟单连接带宽度差不多,其实是单连接带的综合,两者能够转换”设计”,双不过比单连接带省料一点,你不防从连接带中心两半剖开,就会发现变成两条单连接带,如图18中心连一般适合:1).产品前后首尾相连(这种排样才叫真正的中心连接带-图222).一个PIN距冲两个产品.产品旋转180度后再放在原产品相对应的连接带的另一侧,如图19 目的:可能为节省材料;或条料宽度太窄(T<5.0)3).两个对称的产品4).两个不同的产品,如图20注意:中心连接料带常出现拉料,应在适当位置设计定位顶料针.连接带的选区取总结如下:产品展开之后,仔细分析产品的各部位,哪些地方需要成形,哪些地方是仅仅落料,然后在落料的地方选择恰当一天和尚撞一天的位置引出连接带,使之既能保证料带的平稳运送,又不影响产品的成形;至于选择什么类型的连接带,要根据产品的特点而定,确定产品展开尺寸后,根据产品的毛边方向,确定冲裁和成形方向,无毛边要求.4.3.确定排样方案后,这时应该对整个产品冲压和成形过程有一个基本的认识,怎样去安排这些工序的先后关系,应做到心中有数:即先冲哪里,后冲哪里,先成形哪步,后成形哪步,以及某一成形工序能否一次成形出来还是分两步(如图23-90度弯曲),注意点:1).一般先裁边,冲导正,打预断,压线,打凸点,撕口,(切口,拉伸),后冲孔落料,压毛边,成形,分两步折弯的,先成形一半,后成形另一半2).在冲孔落料时,一般先冲小孔,后冲大孔;先冲落成形周边的废料,再落其它部位的余料:因为冲小孔若放在后面,那么它在冲裁时,冲子四周对应料带上的部位可能有缺口(前面已冲过的孔),这样,冲子在冲压过程中,将会引起受力不均(会产生侧向力),本来小孔冲子强度很弱,加之受力不均,极度容易折断(如图24);当然这仅是大多数情况,有时根据实际情况需要,小孔冲双能排在后面,不过办法还是有的,如果冲子厚度实在太小,可进行补强:A:采用脱板精密导向;B:冲子采用PG加工.冲了太弱时的参数如下:设材料厚度为T,冲子厚度为S3).第三当碰到L形弯曲或产品单排时材料利用率太低,可考虑对称排交错排,这样对称成形受力均匀,成形稳定;或者材料利用率可大大提高(如图23).图23:图24:4).第四要考虑冲裁PIN数和步距(主要针对接插件类小端子产品,一般五金外壳类或较大工件为单PIN).5).第五要考虑材料利用率,尽可能提高材料利用率,降低生产成本.4.4.确定是否采用裁边:裁边一般用在连续模和落料模上,它的作用起粗定位,在试模时便于送料;有的裁边还兼有冲外形的作用,如果模具先冲定位针孔,接着马上用引导针导正一般不用裁边了;没有引导针的,要先裁边,用来定距,一般用在落毛胚的落料膜中.裁边的冲子形状有以下几种,参数如下图25.4.5.预断,将要断,但未断的意思(一般放在工站前面)由于小五金电子产品往往有电镀要求,为电镀方便,冲出来的小产品并不直接落料,而是打个预断留在料带上,电镀后,再用手或机械折两下即可取下来.预断:两面都要切,每边切进的深一般为材料厚度的4/1,这样双需折两下(往上-往下)就可以产品摘下来;预断冲子和入子头部的宽度为0.02~0.05,角度为50度~70度,其长度比预断线的长度每边大0.2~0.5即可.如下图26:假如材料厚度为0.2,夹板厚度为18.00,脱板规定厚度为22.00(实际厚度=规定厚度+材料厚度-0.05),背板厚度为9.00其预断冲子入子形状及高度如下:预断冲子入子高度分别为H1,H2,则计算如下:H1=夹板厚度+背板厚度+脱板厚度+t/4=18.00+9.00+22.00+0.2/4=49.55H2=下模板厚度+T/4=25.00+0.2/4=25.05注:本来H1应为49.0,H2应为25.0,但由于头部就那么一点点高双有0.05,顶部的宽度也双有0.02,强度根本不够,双要一生产早就崩掉了,或磨损掉了,因此在实际设计时,沿着预断形状斜线要往下延长0.5,这样既保证了它的强度,又可以调节打预断的深度:太深,双需把尾端磨掉一些,太浅,在冲子或入子尾端加标准垫片:上图H1=48.5,H2=24.5,L1=L2=0.55,就是这样来的.说明:为了便于加工和备料以及校模,一般每个厂的各块模板的厚度实行了标准化,厚度大小都规定了(特殊情况除外),在连续模中由于是料带的形式,为了方便控制料带的预压量和模板的平衡性,常在脱料板中间磨出一个料带槽:其槽的深度=材料厚度-0.03~0.05(也就是说预压量为3~5条),槽的宽度比料带的宽度大2~4MM即可.因此脱料板的厚度常随材料厚度变化而变化,其大小=脱料板规定厚度+材料厚度-0.03~0.05不过在工程模中,一般不需磨产品槽:因为工程模产品一般较大而不像连续模式料带那样窄而细长,也就是说工程模脱料板厚度一般不变.4.6.确导正孔的大小及位置一般的连续模都要冲导正,以便后工序的精确定位,在工程模中常用产品需件的内孔或外形来实现下一工序的定位,若既无内孔,外形又不能用来定位,那么双得借助工艺孔了:如第一工程打凸胞,第二工程落名形这程情况,那么只好在第一工程中在外形的对角同时冲两个工艺孔(孔大小与材料厚度有关:常用 3.0~6.0)以便下一工序的定位导正孔的大小选择在前面表一已经说明了,其位置一般放在连续带上,有时放在废料上到最后时随废料一起冲掉;一般一个步距一个导正孔或几PIN同介导正孔.4.7.冲子刀口设计制作冲子刀口:对于连续模,就是把料带上废料部分冲掉,留下来的产品的展开外形和连接带;对于工程模,一般来讲,就是冲孔落料.下面主要针对连续模来讲.用产品展开图排出料带成形方案后,接下来就是如何安排这些工步,一般先打凸点,打预断,冲导正,撕口,落料,再压毛边,成形.由于产品的形状常常奇怪状,其展开图形状态也必然不规则:可能有的地方有凹进去很深的狭槽,如果整个外形落料冲子做成一个整体,那么在该冲子部位可能常常发生崩柝;可能有的地方有凸出来很长的悬壁,那么在该部位的刀口强度肯定不够;有的地方要求是尖角,事实上刀口冲子割出来不可能是百分之百的尖角,总存在一个最小R值(通常是R0.15);还有的是为了保持后一工步成形的稳定性(增大压料面积),而先切去一部分,成形后,再切另一部分因此,为了解决上述问题,就必须进行刀口分解,把那些薄弱的地方单独分离出来做成不同的刀口,用2个或2个以上的工步先后互切来完成整体外形落料,分解时注意以下几点(如图27):图27:1).对于产品上要求必须是尖角的部分,此时必须采刀口互切2).对于产品上某条轮廓直线边有较严的公差要求(<=±0.05)时,一般不得在该直线上有刀口接头3).分解出来的冲子形状简单,尽量采用普通确磨或线割加工4).分解出来的冲子要有一定的强度,尽量减少PG加工,如有空地方,尽量做碱点.如图27-3中的15号16号冲子改大变成15a,16a,这样冲子强度会好一点.5).对于互切刀口采用相交(一般是直线与直线或直线与圆弧)或圆弧60~75度处作切线相交的互切方式(直线与圆弧),有时也采用圆弧相切(圆弧与圆弧)或重合相切,其互切直线长度(一般0.3~0.5不泡括两者圆弧)不宜过长,过长会产生粉屑:其目的是不要产生过大的毛头,影响产品尺寸和美观.6).注意刀口冲子上的圆角处理:通常线割MIN圆角为R0.15,也可以割R0.1的圆角但需要换铜丝(成本增加),故不重要的圆角尽量把它到R0.15,或更大R0.2~0.3,但是不能把它的功能尺寸改变,其刀口冲子上的圆角必须表示出来或者加说明未注圆角R为多少,至于脱板夹板转角处圆角既可以画清角,也可以和刀口一样,它仅仅起定位作用,线割时,它会自动清角.对于小R0.1的圆角采用PG加工.4).冲子太小时,一般要补哟;如果有空位,尽量做大一点采用线割加工,否则要PG加工,增加成本.如图27中15,16号冲子太小,要进行PG加工,由于有空位,若改为15a,16a的形式,那么冲子强度已足够,采用线割加工,节约成本.PG加工的冲了形状如下:冲子太小需要补强的尺寸规格如下:材料厚度T 冲子最小厚度K 冲子最大长度LT<=0.3 K<=0.6 L<2.0T<=0.6 K<=1.2 L<2.0T<=1.0 K<=1.8 L<2.5T<=1.5 K<=2.0 L<2.5T<=2.0 K<=2.5 L<3.04.8.刀口镶块的(通常叫入子)大小设计制作:4.8.1.做入子的目的:其主要目是方便维修:由于许多精密五金件大都有毛边要求,不得超过其规定值,而模具在冲压一段时间后,冲子和刀口因经常互相磨擦刃口发生钝化,变得不锋利,导致毛边加大.如果做入子,发现哪里毛边偏大只需把该处冲子刀口折下在刃口磨0.2~0.5,再在其背面垫片即可.可果不做入子,那么整个模板要折下来,再把刀口面磨一定的高度,这样维修起来比较麻烦且降低模具的寿命;另外在连续模和工程模式中,那些易崩裂的刀口和产品上某处尺寸要求很严时,可在该处做入子,这样方便维修,不过,并不是所有的模具做入子,因为一做入子,模具的成本,将会增加 1.5~3倍,因此具体情况还要看产品的要求精度以及生产批量和模具类型式.下面简要说明要不要做入子的情况:4.8.1.1.高速精密冲床模具(冲速>150次/每分钟,如端子模)脱板下模一般要做入子,夹板可做可不做发,建义(从节约成本出发):不做4.8.1.2.普通连续模:如果生产批量较大时,下模一般要入子,其它两板不做入子;生产批量较小时,下模可以不做入子;如果产品上某处尺寸要求经常变动或特严或展开很难把握和易崩裂的刀口部位,可在该处设计入子4.8.1.3.工程模:一般不做入子,只有在那些易崩裂的刀口部位才设计入子4.8.2.刀口镶块(入子)大小制作,主要由冲压材料的厚度和硬度以及刀口材料强度决定,入子做行太大,步距排得较松,这样会加长模板,同时对模板强度有影响,做得太小,刀口叱咤度又不够,因此要到恰当的数值,既不浪费模板又保证入子的强度:实践证明一般入子制作。
UG汽车制造自动化——冲模设计

27
© UGS Corp. 2005. All rights reserved.
模具设计简介 (Die Design)
28
© UGS Corp. 2005. All rights reserved.
汽车覆盖件冲模
f 汽车覆盖件具有结构复杂、体积大、重量大、制造成 本高且制造周期长的特点。
f 按完成的工序内容分类主要有落料模、拉深模、修边 模、翻边模、冲孔模等。
f Binder wrap(压料面)
f 可展开的 f 可延伸缺省片体 f 可选择输出三角面表
示法
UG/die engineering
19
© UGS Corp. 2005. All rights reserved.
制造工艺设计(Die Engineering)
由于存在着倒勾形状而无法在
拉伸模中形成翻边。
制的片体,在该片体中,将考虑材料的回弹。回弹信息定义 在Die Flange Task和DIE_OUTPUT特征中
f 制造工艺顾问(DFM Advisor)
23
© UGS Corp. 2005. All rights reserved.
制造工艺设计(Die Engineering)
f 零件替换(Die Product Replace)
f 汽车行业由于CAD/CAM/CAE一体化的应用,可使模 具设计与制造周期缩短2/5,模具生产成本降低1/3。
f 针对那些正在寻找途径来提高整个产品开发效率的企 业,UGS PLM solutions提供了一整套集成的 CAD/CAM/CAE/PDM 软件,这些软件集成了产品设 计和制造流程所需的专业知识和专家经验。
需要在模具面上补充一些形状,
- 1、下载文档前请自行甄别文档内容的完整性,平台不提供额外的编辑、内容补充、找答案等附加服务。
- 2、"仅部分预览"的文档,不可在线预览部分如存在完整性等问题,可反馈申请退款(可完整预览的文档不适用该条件!)。
- 3、如文档侵犯您的权益,请联系客服反馈,我们会尽快为您处理(人工客服工作时间:9:00-18:30)。
18
第10步 为凹模镶块设计落料孔。
1
UG NX4 级进模设计(PDW)
2 3
可整理ppt
19
UG NX4 级进模设计(PDW)
第11步 为废料设计冲头,此废料的尺寸信息必须手工交互 查询。
2 1
3
可整理ppt
20
1
3 2
UG NX4 级进模设计(PDW)
可整理ppt
21
UG NX4 级进模设计(PDW)
5
6 7
可整理ppt
13
UG NX4 级进模设计(PDW)
8
9
10
可整理ppt
14
UG NX4 级进模设计(PDW)
11
12
13
14 可整理ppt
15
UG NX4 级进模设计(PDW)
第8步 将5mm直径的废料所对应的凹模镶块旋转90°。
1
2
4
3
可整理ppt
16
UG NX4 级进模设计(PDW)
可整的弯曲冲头。
1
2
3
4
5 6
UG NX4 级进模设计(PDW)
7
可整理ppt
34
UG NX4 级进模设计(PDW)
4
5
可整理ppt
35
第7步 设置冲头参数。
1 2
UG NX4 级进模设计(PDW)
3
4
可整理ppt
36
第8步 设置弯曲凹模参数。
UG NX4 级进模设计(PDW)
第9步 设计一个稍大一点的冲裁凹模镶块。
1
2
3
注意:在确定其他参数之前, 最好在【目录】页面中的下拉列 表框中选择一个较大的L值,这是 因为,如果在最后选择下拉列表 框中的值,则下拉列表框设置将 会重新设定【尺寸】页面中未被 锁定的参数。
可整理ppt
17
UG NX4 级进模设计(PDW)
可整理ppt
注意:新生成的组件会被设为可见,所以在设计新的组件之 前,将其他的组件设为不可见,新生成的组件将不会受到影响。 在实际应用中,如果装配模型很大,为了简化图形窗口的显示, 常使用 将以前设计的组件隐藏。
第3步
可整理ppt
4
UG NX4 级进模设计(PDW)
第4步 为第1工位上最左边的3mm孔废料设计冲裁凹模 镶块
可整理ppt
24
UG NX4 级进模设计(PDW)
可整理ppt
25
第15步 设计一个较大的凹模镶块。
1 2
UG NX4 级进模设计(PDW)
注意:由于冲头、落料孔和凹模镶块的设计要考虑到搭接 废料,因此这里要选中搭接废料。
3
可整理ppt
26
UG NX4 级进模设计(PDW)
可整理ppt
27
第16步 设计凹模孔和落料孔
6 7
8
9
可整理ppt
41
10 11
12
UG NX4 级进模设计(PDW)
可整理ppt
42
第2步 设计局部成形凹模。
4 3
2
UG NX4 级进模设计(PDW)
5 1
可整理ppt
43
6
10 11
UG NX4 级进模设计(PDW)
可整理ppt
2
UG NX4 级进模设计(PDW)
练习 冲裁组件设计 pierce 文件夹中的a8_control_000装配体。
第1步 单击 配体。
,激活冲裁设计模块,a8_die_02装
可整理ppt
3
第2步 单击 Layout部件。
UG NX4 级进模设计(PDW)
,将其他的部件隐藏,只显示Strip
1
2 3
可整理ppt
31
练习 弯曲组件设计
UG NX4 级进模设计(PDW)
用工程初始化从bend文件夹打开a8_control_000.prt
第1步 单击
,die节点被设为显示部件。
可整理ppt
32
UG NX4 级进模设计(PDW)
第2步 设置第9工位上的向上弯边所需的空间大小。
检查pdw_striptools_blank 文件,测量弯边在弯曲过程 中所需的距离值。
2
1
3
可整理ppt
37
UG NX4 级进模设计(PDW)
4
可整理ppt
38
UG NX4 级进模设计(PDW)
5
6
7
可整理ppt
39
局部成型组件设计
UG NX4 级进模设计(PDW)
form文件夹下的装配体 第1步 为第2工位bead特征设计局部成形冲头。
34
2
5 1
可整理ppt
40
UG NX4 级进模设计(PDW)
可整理ppt
5
1
2
UG NX4 级进模设计(PDW)
3
可整理ppt
6
UG NX4 级进模设计(PDW)
4
5
6
可整理ppt
7
UG NX4 级进模设计(PDW)
模型里包含了两个实体,一个是描述零件本身形状的实体 零件(Ture Body),一个是用来在模板上开设零件安装孔的 工具实体(False Body)
UG NX4 级进模设计(PDW)
UG NX4 级进模设 计
可整理ppt
1
第8章 冲裁组件设计
UG NX4 级进模设计(PDW)
普通冲裁设计 精密冲裁设计
【设计】:包括普通冲裁设计和精密冲裁设计;
【阵列】:可以创建、编辑和删除一个矩形或圆形的组件阵列;
【关联】:在废料和冲裁组件之间建立一种关联性,包括位置 关联和形状关联;
4 5
注意:当特征更新失败 时,尽量将组件生成,抑 制失败的特征。组件生成 后,要检查更新失败的原 因并修正其中的问题。
可整理ppt
22
第12步 重定位P8R冲头。
UG NX4 级进模设计(PDW)
5
1
2
4 3
6 7
可整理ppt
23
UG NX4 级进模设计(PDW)
第13步 编辑P8R冲头,修改更新失败的blend特征。
UG NX4 级进模设计(PDW)
可整理ppt
28
UG NX4 级进模设计(PDW)
第17步 为不规则形状的废料设计用户自定义冲头。
1
2
3
可整理ppt
29
UG NX4 级进模设计(PDW)
第19步 为第2个3mm直径的废料设计冲头。 (设计不含凹模镶块的冲裁组件)
1
2
3
可整理ppt 4
30
UG NX4 级进模设计(PDW)
可整理ppt
8
UG NX4 级进模设计(PDW)
第5步 为新插入的凹模镶块设计落料孔。
1
2
3
4
可整理ppt
9
UG NX4 级进模设计(PDW)
两个复选框分别控制BBP
和DS板上落料孔的数量。如果
用户将For each scrap复选框
选中,所选的多块废料在BBP
和DS板上分别生成各自的落料
孔。否则,多块废料将在BBP
和DS板上共用一个落料孔。
可整理ppt
10
第6步 设计圆形标准冲头。
1
UG NX4 级进模设计(PDW)
3
4
2
可整理ppt
5
11
UG NX4 级进模设计(PDW)
第7步 重复以上步骤,为第1工位上的5mm的导正孔废料设 计冲裁组件。
1 2
3 4
可整理ppt
12
UG NX4 级进模设计(PDW)