汽车模具工艺案例分析
汽车模具加工解决方案
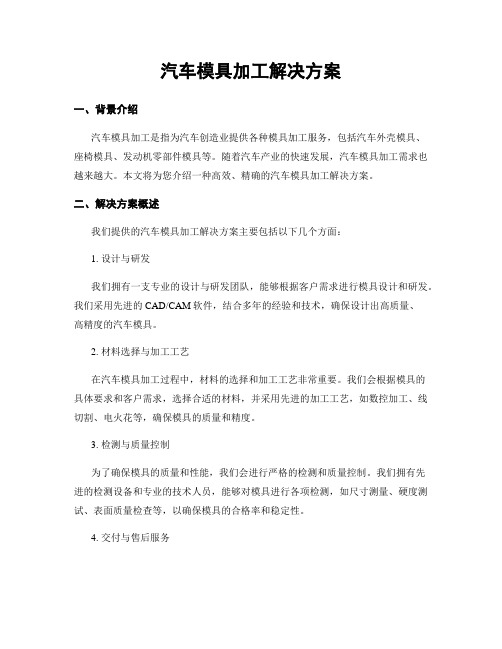
汽车模具加工解决方案一、背景介绍汽车模具加工是指为汽车创造业提供各种模具加工服务,包括汽车外壳模具、座椅模具、发动机零部件模具等。
随着汽车产业的快速发展,汽车模具加工需求也越来越大。
本文将为您介绍一种高效、精确的汽车模具加工解决方案。
二、解决方案概述我们提供的汽车模具加工解决方案主要包括以下几个方面:1. 设计与研发我们拥有一支专业的设计与研发团队,能够根据客户需求进行模具设计和研发。
我们采用先进的CAD/CAM软件,结合多年的经验和技术,确保设计出高质量、高精度的汽车模具。
2. 材料选择与加工工艺在汽车模具加工过程中,材料的选择和加工工艺非常重要。
我们会根据模具的具体要求和客户需求,选择合适的材料,并采用先进的加工工艺,如数控加工、线切割、电火花等,确保模具的质量和精度。
3. 检测与质量控制为了确保模具的质量和性能,我们会进行严格的检测和质量控制。
我们拥有先进的检测设备和专业的技术人员,能够对模具进行各项检测,如尺寸测量、硬度测试、表面质量检查等,以确保模具的合格率和稳定性。
4. 交付与售后服务我们提供及时的交付和售后服务。
我们会按照客户的要求和时间节点进行交付,并提供必要的售后支持和维护服务,以确保客户的满意度。
三、解决方案优势我们的汽车模具加工解决方案具有以下几个优势:1. 高效性:我们拥有先进的设备和技术,能够快速、高效地完成模具加工,缩短交付周期。
2. 精确性:我们注重细节和精确度,确保模具的尺寸和质量符合客户要求。
3. 可靠性:我们采用优质的材料和先进的加工工艺,确保模具的可靠性和稳定性。
4. 个性化定制:我们能够根据客户的需求进行个性化定制,满足不同客户的要求。
5. 专业团队:我们拥有一支专业的团队,具有丰富的经验和技术,能够提供全方位的服务和支持。
四、案例分析以下是我们近期完成的一个汽车模具加工案例:客户:某汽车创造公司需求:汽车外壳模具加工解决方案:我们根据客户提供的设计图纸和要求,使用CAD/CAM软件进行模具设计和研发。
关于汽车覆盖件冲压工艺与实例分析
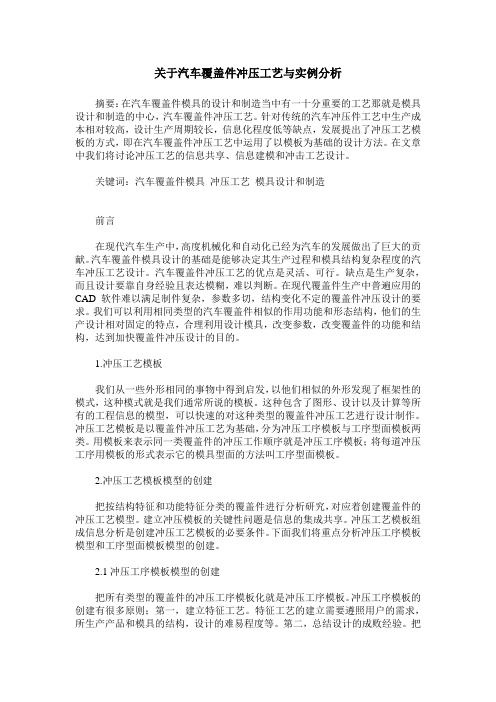
关于汽车覆盖件冲压工艺与实例分析摘要:在汽车覆盖件模具的设计和制造当中有一十分重要的工艺那就是模具设计和制造的中心,汽车覆盖件冲压工艺。
针对传统的汽车冲压件工艺中生产成本相对较高,设计生产周期较长,信息化程度低等缺点,发展提出了冲压工艺模板的方式,即在汽车覆盖件冲压工艺中运用了以模板为基础的设计方法。
在文章中我们将讨论冲压工艺的信息共享、信息建模和冲击工艺设计。
关键词:汽车覆盖件模具冲压工艺模具设计和制造前言在现代汽车生产中,高度机械化和自动化已经为汽车的发展做出了巨大的贡献。
汽车覆盖件模具设计的基础是能够决定其生产过程和模具结构复杂程度的汽车冲压工艺设计。
汽车覆盖件冲压工艺的优点是灵活、可行。
缺点是生产复杂,而且设计要靠自身经验且表达模糊,难以判断。
在现代覆盖件生产中普遍应用的CAD软件难以满足制件复杂,参数多切,结构变化不定的覆盖件冲压设计的要求。
我们可以利用相同类型的汽车覆盖件相似的作用功能和形态结构,他们的生产设计相对固定的特点,合理利用设计模具,改变参数,改变覆盖件的功能和结构,达到加快覆盖件冲压设计的目的。
1.冲压工艺模板我们从一些外形相同的事物中得到启发,以他们相似的外形发现了框架性的模式,这种模式就是我们通常所说的模板。
这种包含了图形、设计以及计算等所有的工程信息的模型,可以快速的对这种类型的覆盖件冲压工艺进行设计制作。
冲压工艺模板是以覆盖件冲压工艺为基础,分为冲压工序模板与工序型面模板两类。
用模板来表示同一类覆盖件的冲压工作顺序就是冲压工序模板;将每道冲压工序用模板的形式表示它的模具型面的方法叫工序型面模板。
2.冲压工艺模板模型的创建把按结构特征和功能特征分类的覆盖件进行分析研究,对应着创建覆盖件的冲压工艺模型。
建立冲压模板的关键性问题是信息的集成共享。
冲压工艺模板组成信息分析是创建冲压工艺模板的必要条件。
下面我们将重点分析冲压工序模板模型和工序型面模板模型的创建。
2.1冲压工序模板模型的创建把所有类型的覆盖件的冲压工序模板化就是冲压工序模板。
冲压磨具结构设计案例展示成功案例的启发与学习

冲压磨具结构设计案例展示成功案例的启发与学习冲压磨具在工业生产中起到了非常关键的作用,它能够通过对材料的加工和成型,实现产品的各种形状和尺寸要求。
冲压磨具的结构设计对于产品的质量和效率具有重要影响。
本文通过展示一些成功的冲压磨具结构设计案例,总结了其中的启发和学习。
1. 案例一:汽车车身冲压件的磨具设计在汽车制造过程中,冲压工艺是非常常见和重要的一种工艺。
汽车车身的冲压件形状复杂,尺寸严格,因此对冲压磨具的结构设计要求很高。
一家汽车制造公司成功设计了一套高效、稳定的冲压磨具,使得汽车车身冲压件的生产效率大幅提升。
该案例的启发是,冲压磨具的结构设计需要考虑到产品的形状、尺寸和工艺要求,同时要考虑到工艺的稳定性和效率。
合理的冲压磨具结构设计可以减少材料的浪费和加工的时间,提高产品的质量和生产效率。
2. 案例二:数控机床冲孔磨具的设计数控机床在制造业中扮演着重要的角色,而冲孔磨具则是数控机床的常用附件。
一家机械设备制造公司设计了一套先进的数控机床冲孔磨具,实现了高效、精准的孔加工。
该案例的启发是,冲孔磨具的结构设计需要考虑到孔的形状、尺寸和加工要求。
合理的冲孔磨具结构设计可以提高孔的加工精度和加工速度,降低产品的成本和工时。
3. 案例三:金属件的弯曲冲孔磨具设计金属件的弯曲冲孔磨具在家具和建筑行业中得到广泛应用。
一家金属制品公司设计了一套创新的弯曲冲孔磨具,实现了金属件的高效弯曲和冲孔加工。
该案例的启发是,弯曲冲孔磨具的结构设计需要考虑到金属件的形状、尺寸和加工要求。
合理的弯曲冲孔磨具结构设计可以提高金属件的加工精度和加工速度,同时兼顾产品的质量和外观要求。
综上所述,冲压磨具结构设计是冲压工艺中至关重要的一环。
通过成功案例的展示,可以从中汲取宝贵的启发和学习。
合理的冲压磨具结构设计可以提高产品的加工效率和质量,降低成本和工时,从而使企业在激烈的市场竞争中脱颖而出。
我们应该不断学习和借鉴先进的设计理念和技术,不断创新冲压磨具的结构设计,为企业的发展和成长提供有力支撑。
汽车模具工艺案例分析

汽车模具工艺案例分析汽车模具工艺是汽车制造中不可或缺的一环,它直接关系到整个汽车的质量及生产效率。
在汽车行业中,好的模具工艺能够为企业提供竞争优势。
本文将以某汽车制造公司的汽车模具工艺为案例,进行分析。
一、背景介绍该汽车制造公司是一家具有一定规模的汽车制造企业,拥有完整的生产线和先进的生产设备。
其生产的汽车在国内市场中处于领先地位。
汽车模具工艺在其生产线上占据着重要的位置,为了提高汽车生产效率,降低成本,该公司不断进行模具工艺改进与升级。
二、分析主题该公司的模具工艺主要包括:钣金模具和塑料模具。
其中,钣金模具是生产整车重要构件的关键工艺之一。
通过对其模具工艺分析,我们可以研究其优秀的生产工艺。
三、分析内容(一)工艺流程该公司的模具工艺流程包括:准备工作、折弯、冲压、撞压、胶合、切割、焊接、钣金抛光、模具调整等步骤。
在具体操作过程中,该公司注重人员培训,力求使操作人员对工艺流程熟练掌握。
(二)模具设计该公司的模具设计部门拥有丰富的设计经验和先进的CAD/CAM技术,能够将客户的需求转化为高效的模具设计方案。
在设计阶段,该公司采用多级审批,确保模具设计质量。
同时,在模具设计方案中,该公司注重提高模具的使用寿命和稳定性,减少模具的磨损和故障。
(三)设备投入该公司在模具制造方面,采用了先进的设备,如自动化模具加工中心、激光切割机、数控冲床等。
这些设备的投入,使模具制造的效率得到了明显提高,同时也降低了制造成本。
该公司还注重维护设备,保证生产设备的正常运转。
(四)质量控制该公司在模具工艺生产的过程中,采取了严格的质量控制措施。
通过严格的质量检测和控制,保证了模具的质量,同时也带来了更高的生产效率。
该公司还在质量控制方面建立了完善的管理体系,纠正不良的工艺,降低废品率,达到了很高的质量可靠性。
四、总结以上就是该公司汽车模具工艺的案例分析。
通过对其模具工艺的分析,我们可以看到,该公司注重工艺流程的规范化、模具设计的质量和稳定性、设备的投入和维护,以及严格的质量控制体系。
冲压模具dfmea案例
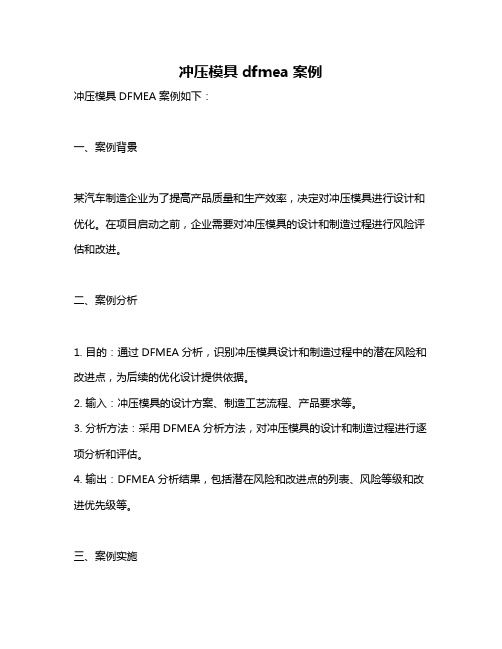
冲压模具dfmea案例
冲压模具DFMEA案例如下:
一、案例背景
某汽车制造企业为了提高产品质量和生产效率,决定对冲压模具进行设计和优化。
在项目启动之前,企业需要对冲压模具的设计和制造过程进行风险评估和改进。
二、案例分析
1. 目的:通过DFMEA分析,识别冲压模具设计和制造过程中的潜在风险和改进点,为后续的优化设计提供依据。
2. 输入:冲压模具的设计方案、制造工艺流程、产品要求等。
3. 分析方法:采用DFMEA分析方法,对冲压模具的设计和制造过程进行逐项分析和评估。
4. 输出:DFMEA分析结果,包括潜在风险和改进点的列表、风险等级和改进优先级等。
三、案例实施
1. 根据DFMEA分析结果,对冲压模具的设计和制造过程进行优化改进。
2. 针对潜在风险和改进点,制定相应的解决措施和优化方案。
3. 对优化后的冲压模具进行试验和验证,确保改进效果符合预期。
4. 将改进后的冲压模具应用于生产线上,观察其效果并进一步优化。
四、案例总结
通过DFMEA分析,企业成功地识别了冲压模具设计和制造过程中的潜在风险和改进点,并采取有效的措施进行了优化改进。
改进后的冲压模具在质量和生产效率方面都有了显著提升,为企业的可持续发展奠定了坚实基础。
(数控模具设计)汽车模具工艺案例分析精编

(数控模具设计)汽车模具工艺案例分析覆盖件冲压工艺设计壹、工艺设计前的准备工作在拿到冲压件进行工艺设计前,必须查阅有关资料,以便明确产品的具体要求、现有的条件等,为设计合理而可行的冲压工艺做好必要的准备。
这些资料主要有:1,零件图或产品图,能够参考的模型。
2,冲压件的公差。
3,类似零件的成型性及作业性的有关资料、曾出现的各种质量问题及解决方法。
4,关于产品所用钢材的有关资料,如材料的各项性能参数值,表面质量等。
5,各种摸具设计的标准和模具零件的规格。
6,现有压力机的参数和附属装置、生产率等方面的资料。
7,产量和要求的时间。
通过对零件图和拉深件图的研究,应该了解该零件所应具有的功能、所要求的单个零件的强度,表面质量以及相关零件之间所要求的相关精度。
且明确下列事项:1,零件轮廓、法兰、侧壁及底部是否有形状急剧变化的部分、负角的部位等,以及其他成形困难的形状。
2,该零件和有关零件的焊接面、装配面、镶嵌面有什么要求。
3,孔的精度(直径、位置)、孔和孔的间距的要求,这些孔的位置在何处(平面部分、倾斜部分、侧壁部分)。
4,各个凸缘精度允许达到什么程度(包括长度、凸缘面的位置、回弹)。
5,焊接、装配的基准面和孔在何处。
6,零件冲压成形需要解决的重点问题有哪些。
7,材料的利用率如何。
在进行工艺设计之前,必须对冲压件进行合理全面的工艺分析。
根据冲压件本身原始信息(包含产品的材质,料厚,产品形状),冲压件的公差和车身中装配位置,客户和本工厂的压力机参数和生产方式(自动线,手工线),冲压件的生产批量大小以及客户提出的模具设计的技术要求来进行冲压件的工艺分析。
二、零件的工艺分析下面我们以东风项目中前碰撞梁为例零件名称:前碰撞梁材料:DC04料厚:2.0mm根据零件的数模和提供的基本信息,以及客户的技术要求我们来进行零件的前碰撞梁的工艺分析,且确定通过几道冲压工序来获得我们的零件。
冲压零件不论复杂或简单我们能够概括为它都是通过俩类模具来获得的:1成形类模具(包括拉延模,成形模,整形模,翻边模,侧翻和侧整模),2修边类模具(包括修边模,落料模,冲孔模,侧修和侧冲孔模具),成形类模具是通过不同的成形来完成我们的产品形状,修边类模具则是切除零件在成形后的废料以达到产品的尺寸精度。
汽车内饰件模具的工艺分析及设计
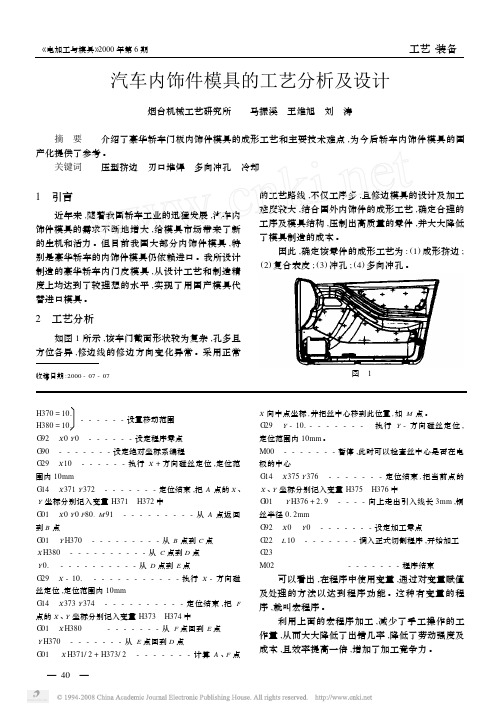
汽车内饰件模具的工艺分析及设计烟台机械工艺研究所 马振溪 王维旭 刘 涛摘 要 介绍了豪华轿车门板内饰件模具的成形工艺和主要技术难点,为今后轿车内饰件模具的国产化提供了参考。
关键词 压型挤边 刃口堆焊 多向冲孔 冷却1 引言近年来,随着我国轿车工业的迅猛发展,汽车内饰件模具的需求不断地增大,给模具市场带来了新的生机和活力。
但目前我国大部分内饰件模具,特别是豪华轿车的内饰件模具仍依赖进口。
我所设计制造的豪华轿车内门皮模具,从设计工艺和制造精度上均达到了较理想的水平,实现了用国产模具代替进口模具。
2 工艺分析如图1所示,该车门截面形状较为复杂,孔多且方位各异,修边线的修边方向变化异常。
采用正常收稿日期:2000-07-07的工艺路线,不仅工序多,且修边模具的设计及加工难度较大,结合国外内饰件的成形工艺,确定合理的工序及模具结构,压制出高质量的零件,并大大降低了模具制造的成本。
因此,确定该零件的成形工艺为:(1)成形挤边;(2)复合表皮;(3)冲孔;(4)多向冲孔。
图 1H370=10.H380=10.------设置移动范围G 92 X 0Y 0 ------设定程序零点 G 90 -------设定绝对坐标系编程G 29 X 10 ------执行X +方向碰丝定位,定位范围内10mmG 14 X 371Y 372 -------定位结束,把A 点的X 、Y 坐标分别记入变量H371 H372中G 01 X 0Y 0F 80.M 91 ---------从A 点返回到B 点G 01 Y H370 ---------从B 点到C 点X H380 ----------从C 点到D 点Y 0. ----------从D 点到E 点G 29 X -10. -----------执行X -方向碰丝定位,定位范围内10mmG 14 X 373Y 374 ----------定位结束,把F点的X 、Y 坐标分别记入变量H373 H374中G 01 X H380 -------从F 点回到E 点Y H370 -------从E 点回到D 点G 01 X H371/2+H373/2 -------计算A 、F 点X 向中点坐标,并把丝中心移到此位置,如M 点。
压铸模案例研究

压铸模案例研究
案例一:解决嵌件安装问题
某模具在生产过程中,出现了产品尺寸长短不一的问题。
经过现场排查,发现模具底孔与嵌件的配合公差较小,操作者快速将嵌件安装进去后,底孔内的空气无法排除,形成一个空气压缩后的气垫,将嵌件从安装孔中弹出。
为了解决此问题,模具的底部增加了一个排气通道,使孔内的空气能从此通道顺利排出,从而杜绝了类似问题的发生,保证了产品质量。
案例二:优化轮毂压铸模具设计
轮毂是摩托车上一个常用的零部件,过去一段时期,轮毂压铸模具常在短期内发生局部龟裂。
为了解决这一问题,企业采用了先进的模拟仿真技术,成功预测了汽车零部件在不同工况下的应力和变形情况,从而通过优化设计,减轻了零部件的重量,提高了燃油效率。
这不仅提高了铸件的外观质量,还增强了产品的市场竞争力。
案例三:引入增材制造技术
在电子行业,某企业成功引入增材制造技术,打破了传统模具制造的限制。
通过这一技术,企业创造出了更为精巧复杂的外形,使产品更具竞争力。
这种创新的压铸模具设计实现了产品的质的飞跃,为企业带来了巨大的商业价值。
总结:
压铸模的设计和制造是一项复杂的工程任务,需要深入理解材料、工艺和生产需求。
通过不断的研究和创新,企业可以解决各种挑战,提高产品质量和降低生产成本。
在未来的工业生产中,随着新技术的不断涌现,压铸模的设计和制造将更加精密、高效和环保。
- 1、下载文档前请自行甄别文档内容的完整性,平台不提供额外的编辑、内容补充、找答案等附加服务。
- 2、"仅部分预览"的文档,不可在线预览部分如存在完整性等问题,可反馈申请退款(可完整预览的文档不适用该条件!)。
- 3、如文档侵犯您的权益,请联系客服反馈,我们会尽快为您处理(人工客服工作时间:9:00-18:30)。
覆盖件冲压工艺设计
一、工艺设计前的准备工作
在拿到冲压件进行工艺设计前,必须查阅有关资料,以便明确产品的具体要求、现有的条件等,为设计合理而可行的冲压工艺做好必要的准备。
这些资料主要有:
1,零件图或产品图,可以参考的模型。
2,冲压件的公差。
3,类似零件的成型性及作业性的有关资料、曾出现的各种质量问题及解决方法。
4,关于产品所用钢材的有关资料,如材料的各项性能参数值,表面质量等。
5,各种摸具设计的标准和模具零件的规格。
6,现有压力机的参数和附属装置、生产率等方面的资料。
7,产量和要求的时间。
通过对零件图和拉深件图的研究,应该了解该零件所应具有的功能、所要求的单个零件的强度,表面质量以及相关零件之间所要求的相关精度。
并明确下列事项:
1,零件轮廓、法兰、侧壁及底部是否有形状急剧变化的部分、负角的部位等,以及其他成形困难的形状。
2,该零件和有关零件的焊接面、装配面、镶嵌面有什么要求。
3,孔的精度(直径、位置)、孔和孔的间距的要求,这些孔的位置在何处(平面部分、倾斜部分、侧壁部分)。
4,各个凸缘精度允许达到什么程度(包括长度、凸缘面的位置、回弹)。
5,焊接、装配的基准面和孔在何处。
6,零件冲压成形需要解决的重点问题有哪些。
7,材料的利用率如何。
在进行工艺设计之前,必须对冲压件进行合理全面的工艺分析。
根据冲压件本身原始信息(包含产品的材质,料厚,产品形状),冲压件的公差和车身中装配位置,客户和本工厂的压力机参数和生产方式(自动线,手工线),冲压件的生产批量大小以及客户提出的模具设计的技术要求来进行冲压件的工艺分析。
二、零件的工艺分析
下面我们以东风项目中前碰撞梁为例
零件名称:前碰撞梁
材料:DC04。