低温甲醇洗工艺
低温甲醇洗净化工艺技术进展及应用概况
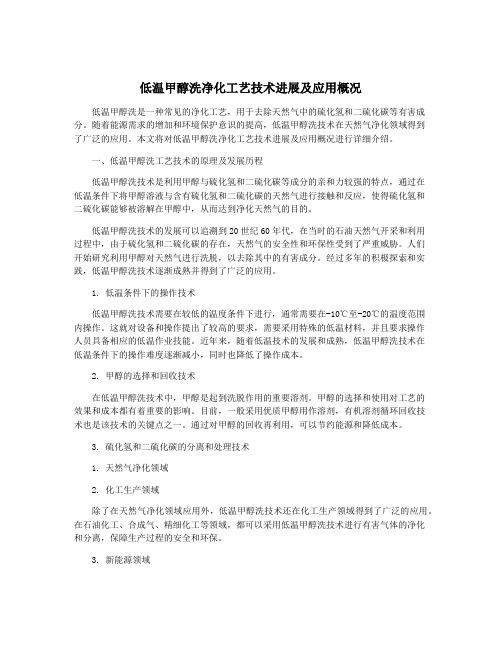
低温甲醇洗净化工艺技术进展及应用概况低温甲醇洗是一种常见的净化工艺,用于去除天然气中的硫化氢和二硫化碳等有害成分。
随着能源需求的增加和环境保护意识的提高,低温甲醇洗技术在天然气净化领域得到了广泛的应用。
本文将对低温甲醇洗净化工艺技术进展及应用概况进行详细介绍。
一、低温甲醇洗工艺技术的原理及发展历程低温甲醇洗技术是利用甲醇与硫化氢和二硫化碳等成分的亲和力较强的特点,通过在低温条件下将甲醇溶液与含有硫化氢和二硫化碳的天然气进行接触和反应,使得硫化氢和二硫化碳能够被溶解在甲醇中,从而达到净化天然气的目的。
低温甲醇洗技术的发展可以追溯到20世纪60年代,在当时的石油天然气开采和利用过程中,由于硫化氢和二硫化碳的存在,天然气的安全性和环保性受到了严重威胁。
人们开始研究利用甲醇对天然气进行洗脱,以去除其中的有害成分。
经过多年的积极探索和实践,低温甲醇洗技术逐渐成熟并得到了广泛的应用。
1. 低温条件下的操作技术低温甲醇洗技术需要在较低的温度条件下进行,通常需要在-10℃至-20℃的温度范围内操作。
这就对设备和操作提出了较高的要求,需要采用特殊的低温材料,并且要求操作人员具备相应的低温作业技能。
近年来,随着低温技术的发展和成熟,低温甲醇洗技术在低温条件下的操作难度逐渐减小,同时也降低了操作成本。
2. 甲醇的选择和回收技术在低温甲醇洗技术中,甲醇是起到洗脱作用的重要溶剂。
甲醇的选择和使用对工艺的效果和成本都有着重要的影响。
目前,一般采用优质甲醇用作溶剂,有机溶剂循环回收技术也是该技术的关键点之一。
通过对甲醇的回收再利用,可以节约能源和降低成本。
3. 硫化氢和二硫化碳的分离和处理技术1. 天然气净化领域2. 化工生产领域除了在天然气净化领域应用外,低温甲醇洗技术还在化工生产领域得到了广泛的应用。
在石油化工、合成气、精细化工等领域,都可以采用低温甲醇洗技术进行有害气体的净化和分离,保障生产过程的安全和环保。
3. 新能源领域随着清洁能源的需求日益增加,低温甲醇洗技术也在新能源领域得到了应用。
低温甲醇洗工艺原理
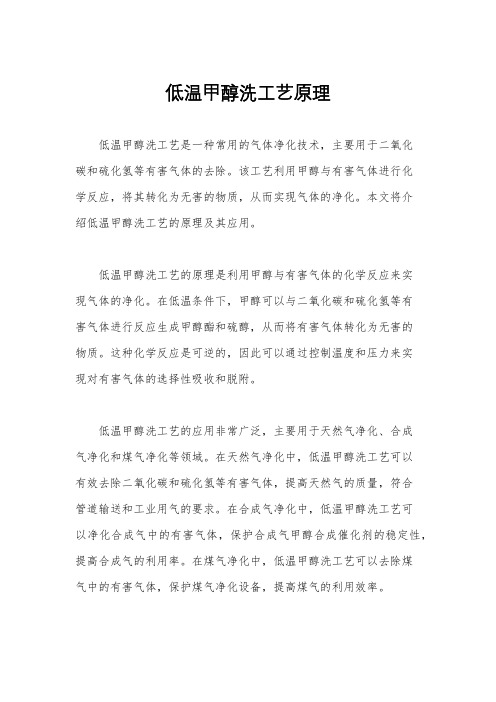
低温甲醇洗工艺原理
低温甲醇洗工艺是一种常用的气体净化技术,主要用于二氧化
碳和硫化氢等有害气体的去除。
该工艺利用甲醇与有害气体进行化
学反应,将其转化为无害的物质,从而实现气体的净化。
本文将介
绍低温甲醇洗工艺的原理及其应用。
低温甲醇洗工艺的原理是利用甲醇与有害气体的化学反应来实
现气体的净化。
在低温条件下,甲醇可以与二氧化碳和硫化氢等有
害气体进行反应生成甲醇酯和硫醇,从而将有害气体转化为无害的
物质。
这种化学反应是可逆的,因此可以通过控制温度和压力来实
现对有害气体的选择性吸收和脱附。
低温甲醇洗工艺的应用非常广泛,主要用于天然气净化、合成
气净化和煤气净化等领域。
在天然气净化中,低温甲醇洗工艺可以
有效去除二氧化碳和硫化氢等有害气体,提高天然气的质量,符合
管道输送和工业用气的要求。
在合成气净化中,低温甲醇洗工艺可
以净化合成气中的有害气体,保护合成气甲醇合成催化剂的稳定性,提高合成气的利用率。
在煤气净化中,低温甲醇洗工艺可以去除煤
气中的有害气体,保护煤气净化设备,提高煤气的利用效率。
总之,低温甲醇洗工艺是一种重要的气体净化技术,具有高效、环保、经济的特点,广泛应用于天然气净化、合成气净化和煤气净
化等领域。
通过对其原理和应用的深入了解,可以更好地掌握和应
用这一技术,为气体净化工作提供有力的支持。
低温甲醇洗工艺技术讲解
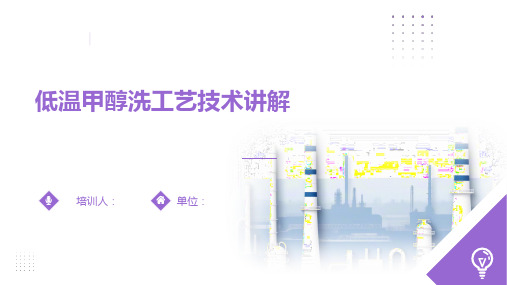
低温甲醇洗工艺技术讲解培训人:单位:低温甲醇洗工作原理1低温甲醇洗工作任务2低温甲醇洗各塔作用3低温甲醇洗工艺流程4开停车步骤操作要点5CONTENTS目录1低温甲醇洗工作原理PROJECT INTRODUCTION低温甲醇洗工艺原理国内外应用情况低温甲醇洗是20世纪50年代初德国林德公司和鲁奇公司联合开发的一种气体净化工艺。
低温甲醇洗工艺技术成熟,被广泛应用于国内外合成氨、合成甲醇及其他羰基合成、城市煤气、工业制氢和天然气脱硫等气体净化装置中。
工艺特点低温高压净化度高该工艺为典型物理吸收法,是以冷甲醇为吸收溶剂,利用甲醇在低温下对酸性气体溶解度极大的特性,脱除原料气中的酸性气体。
工艺原理低温甲醇洗工艺原理是以拉乌尔定律和亨利定律为基础,依据低温状态下的甲醇具有对H 2S和CO 2等酸性气体的溶解吸收性大、而对H 2和CO溶解吸收性小的这种选择性,来脱除变换气、未变换气中的H 2S和CO 2等酸性气体。
甲醇对H 2S、COS和CO 2 都有高的溶解度,而对H 2 、CH 4和CO等气体的溶解度小,说明甲醇有高的选择性。
低温对气体吸收是很有利的:待脱除的酸性气体,如H 2S、COS、CO 2等的溶解度在温度降低时增加很多,有用气体如H 2、CO及CH 4等的溶解度在温度降低时却增加很少。
甲醇对H 2S的吸收速度要比CO 2 快好几倍,而且溶解度也比CO 2 大,所以表现出可以先吸收H 2S。
-40℃(233K )时各种气体在甲醇中的相对溶解度气体参比H 2的溶解度参比CO 2的溶解度H 2S 2540 5.9COS 1555 3.6CO 2430 1.0CH 412 CO 5 H 2 1.0N 22.5溶剂的蒸汽压不仅与溶剂的性质有关,而且还与溶液中溶解组分浓度有关。
低温甲醇洗工艺原理气液相平衡拉乌尔定律:一定温度下,稀溶液溶剂的蒸气压等于纯溶剂的蒸气压乘以溶液中溶剂的摩尔分数。
纯溶剂稀溶液在稀溶液中溶质若服从亨利定律,则溶剂必然服从拉乌尔定律。
低温甲醇洗工艺

煤为原料的低温甲醇洗
三、关于能耗:
(1)酸气的溶解热要取出,以确保吸收温度要求.(闪蒸回 收能量约60~70%) (2)动力消耗:泵; (3)热再生耗汽. (4)冷损的补偿.(低温操作,保冷严格)
煤为原料的低温甲醇洗
四、关于设备选材考虑:
(1)羰基铁问题:原料气中有一氧化碳,它同钢铁作用,生
成羰基铁,当有硫化氢气体时,更易生成. (2)羰基铁的生成,造成腐蚀,羰基铁和硫化氢作用,生成含 硫的中间羰基产物,该产物发生热解,生成硫\硫化亚铁,造 成堵塞.
低温甲醇洗----基本理论
四、硫化氢在甲醇中的溶解度:
1、硫化氢和甲醇都是极性物质,从而溶解能力大. 2、低压下,在甲醇中,溶解度同温度的关系是: ①PH2S<400mmHg,符合Herry定律PH2S= kx,(500#,总压26.5, YH2S=0.38% PH2S=76mmHg) ②当二氧化碳存在时,硫化氢溶解度降低,温度越低,影响越明显. ③在0~-78℃, PH2S= 15-400mmHg条件下,硫化氢的溶解度可进行计算: S=692PH2S/(1.9P0H2S-PH2S) 而 lgP0H2S=7.453-973.5/T ④温度低,溶解度大,且随着温度的降低,温度对溶解度的影响更明显. ⑤在甲醇体系中,溶解度同温度的关系能进行定量计算lgS=C/T-D.
低温甲醇洗
工艺基础知识
低温甲醇洗----概述
• 低温甲醇洗是由德国林德公司和鲁奇公司共同 开发的,采用冷甲醇作为吸收溶剂,世界上第 一套低温甲醇洗工业化装置于1954年建于南非 萨索尔,1964年林德公司又设计了低温甲醇洗 串液氮洗装置。70年代以来,国外所建的以煤 和重油为原料的大型氨厂,大部分采用该法, 低温甲醇洗工艺技术成熟,使用业绩多,我国 已有多套大型合成氨装置采用这一技术。
低温甲醇洗
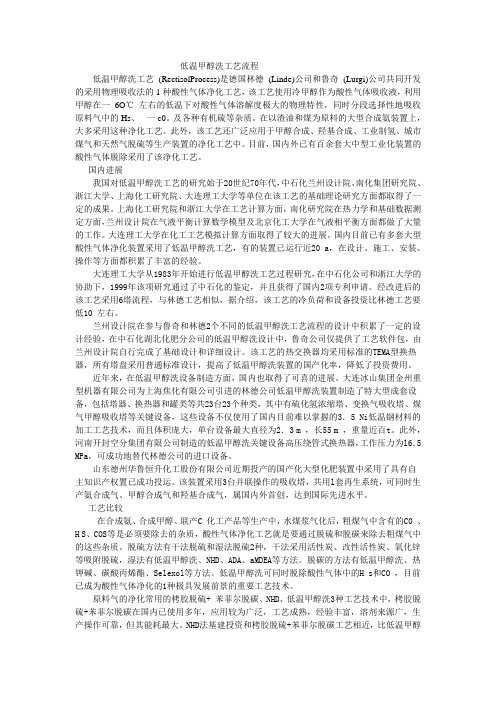
低温甲醇洗工艺流程低温甲醇洗工艺(RectisolProcess)是德国林德(Linde)公司和鲁奇(Lurgi)公司共同开发的采用物理吸收法的1种酸性气体净化工艺,该工艺使用冷甲醇作为酸性气体吸收液,利用甲醇在一6O℃左右的低温下对酸性气体溶解度极大的物理特性,同时分段选择性地吸收原料气中的Hs、一c0。
及各种有机硫等杂质。
在以渣油和煤为原料的大型合成氨装置上,大多采用这种净化工艺。
此外,该工艺还广泛应用于甲醇合成、羟基合成、工业制氢、城市煤气和天然气脱硫等生产装置的净化工艺中。
目前,国内外已有百余套大中型工业化装置的酸性气体脱除采用了该净化工艺。
国内进展我国对低温甲醇洗工艺的研究始于20世纪70年代,中石化兰州设计院、南化集团研究院、浙江大学、上海化工研究院、大连理工大学等单位在该工艺的基础理论研究方面都取得了一定的成果。
上海化工研究院和浙江大学在工艺计算方面,南化研究院在热力学和基础数据测定方面,兰州设计院在气液平衡计算数学模型及北京化工大学在气液相平衡方面都做了大量的工作。
大连理工大学在化工工艺模拟计算方面取得了较大的进展。
国内目前已有多套大型酸性气体净化装置采用了低温甲醇洗工艺,有的装置已运行近20 a,在设计、施工、安装、操作等方面都积累了丰富的经验。
大连理工大学从1983年开始进行低温甲醇洗工艺过程研究,在中石化公司和浙江大学的协助下,1999年该项研究通过了中石化的鉴定,并且获得了国内2项专利申请。
经改进后的该工艺采用6塔流程,与林德工艺相似,据介绍,该工艺的冷负荷和设备投资比林德工艺要低10 左右。
兰州设计院在参与鲁奇和林德2个不同的低温甲醇洗工艺流程的设计中积累了一定的设计经验,在中石化湖北化肥分公司的低温甲醇洗设计中,鲁奇公司仅提供了工艺软件包,由兰州设计院自行完成了基础设计和详细设计。
该工艺的热交换器均采用标准的TEMA型换热器,所有塔盘采用普通标准设计,提高了低温甲醇洗装置的国产化率,降低了投资费用。
低温甲醇洗工艺

3、溶解度随温度的变化同溶解热的大小有关。对于物理吸收法,溶解 热数值较小,从而溶解度随温度的变化就小,但是温度变化范围大 时,溶解度数据不能按常量对待。
三、气体的溶解度同压力的关系:
低温甲醇洗原理图
GH PSA
400# GR
5600#
脱油
预洗
脱硫
轻油回收
H2S 回收
700#/800#
脱碳
脱硫 精洗 主
洗
CO2 回收
600# GEC
石脑油
脱硫气
二氧化碳
低温甲醇洗气体净化流程
脱碳气
粗煤气:18.3万,其 中6万去预洗塔;脱硫 气6.8万去变压吸附.
预 洗 塔
粗煤气 冷却 冷却
脱硫气
硫 化 氢 吸 收 塔
预
洗
段
H2S
再生
精 洗
精洗 甲醇
段
二 氧 化 碳 吸 收
主洗
主 甲醇
洗
段
变
冷却 换
塔
气 冷却
冷
甲醇
却
段
冷却
预洗再生
主洗再生
低温甲醇洗主洗、冷却及再吸收回路
冷 却 回 路
FRC 5007
精 洗 段
二 氧 化 碳 吸 收 P塔
换热器
冷 却
段
氨冷器 P502
精洗 甲醇
P
主 洗 段
FRC 5008
一、不同气体在甲醇中的溶解度:
1、溶解度顺序: SH2S > SCOS > SCO2 > SCH4 > SCO > SN2 > SH2 2、除了氢气和氮气外,其它组分在甲醇中,温度低、溶解度大。 3、最低甲醇用量:指气体中的二氧化碳全部被溶液吸收而所需溶液的最小量。
化工设计低温甲醇洗
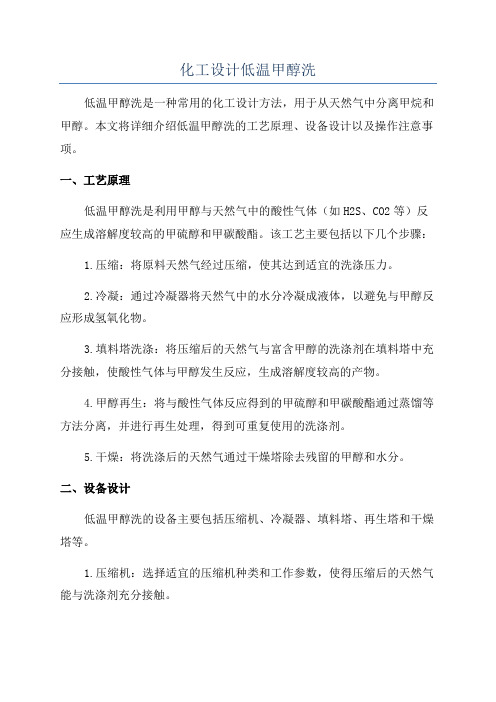
化工设计低温甲醇洗低温甲醇洗是一种常用的化工设计方法,用于从天然气中分离甲烷和甲醇。
本文将详细介绍低温甲醇洗的工艺原理、设备设计以及操作注意事项。
一、工艺原理低温甲醇洗是利用甲醇与天然气中的酸性气体(如H2S、CO2等)反应生成溶解度较高的甲硫醇和甲碳酸酯。
该工艺主要包括以下几个步骤:1.压缩:将原料天然气经过压缩,使其达到适宜的洗涤压力。
2.冷凝:通过冷凝器将天然气中的水分冷凝成液体,以避免与甲醇反应形成氢氧化物。
3.填料塔洗涤:将压缩后的天然气与富含甲醇的洗涤剂在填料塔中充分接触,使酸性气体与甲醇发生反应,生成溶解度较高的产物。
4.甲醇再生:将与酸性气体反应得到的甲硫醇和甲碳酸酯通过蒸馏等方法分离,并进行再生处理,得到可重复使用的洗涤剂。
5.干燥:将洗涤后的天然气通过干燥塔除去残留的甲醇和水分。
二、设备设计低温甲醇洗的设备主要包括压缩机、冷凝器、填料塔、再生塔和干燥塔等。
1.压缩机:选择适宜的压缩机种类和工作参数,使得压缩后的天然气能与洗涤剂充分接触。
2.冷凝器:采用适当的冷却介质(如冷水或液氨)冷凝天然气中的水分,以避免与甲醇反应。
3.填料塔:选择合适的填料材料和填充方式,使得洗涤剂和天然气在塔内充分接触,增加反应效率。
4.再生塔:通过适当的加热和分离操作,将洗涤剂中的甲硫醇和甲碳酸酯分离出来,再经过一系列处理后进行再生。
5.干燥塔:使用适当的干燥剂(如活性炭或分子筛)除去洗涤剂中的甲醇和水分,保证出口天然气的干燥度。
三、操作注意事项在低温甲醇洗的操作中,需要特别注意以下几点:1.洗涤剂的选择:应选择溶解度适宜的洗涤剂,以提高酸性气体的去除效率。
2.填料塔的操作:应控制好填料塔的进料流量和填料高度,使洗涤剂得以充分接触酸性气体。
3.洗涤液的分离与再生:应选择适宜的再生方法,避免成本过高或对环境造成污染。
4.安全操作:在操作过程中应注意安全防护,避免甲醇或酸性气体对人身安全和设备造成伤害。
综上所述,低温甲醇洗是一种常用的化工设计方法,通过使用甲醇洗涤剂与酸性气体反应,实现对天然气中甲醇和甲烷的分离。
低温甲醇洗工艺流程

低温甲醇洗工艺流程低温甲醇洗工艺流程低温甲醇洗工艺是一种常用的物理吸附法,用于去除气体或液体中的硫化物、二硫化碳等有害物质,在化工、石化等行业得到广泛应用。
以下是低温甲醇洗工艺的典型流程。
1. 原料气体净化和预冷首先,将原料气体通过净化装置去除其中的颗粒物、油雾和其他杂质,保证后续工艺的正常运行。
然后,将原料气体送入预冷器中,通过对流换热的方式,将气体冷却到合适的温度。
2. 低温甲醇洗吸收塔将预冷后的气体引入低温甲醇洗吸收塔,与冷却后的甲醇液体相接触。
在吸收塔内部,置入填料,用于增加气液接触面积,提高传质效果。
3. 脱硫反应在低温甲醇洗吸收塔中,气体中的硫化物和二硫化碳会被甲醇吸收,形成含有硫元素的甲醇溶液。
最常用的脱硫反应是甲醇和硫化氢(H2S)反应生成甲硫醇(CH3SH)。
4. 脱硫液循环从低温甲醇洗吸收塔底部,将含有硫元素的甲醇溶液抽出,通过分离器进行气液分离,使甲醇溶液中的气体逸出。
然后,将甲醇溶液经过冷凝器进行冷却,再经过再生器,将溶液中的硫化物还原为硫化氢,再循环回低温甲醇洗吸收塔。
5. 甲醇回收从冷凝器中冷却后的甲醇气体进一步冷却,通过压缩机增压,然后经过冷凝器,将甲醇气体冷凝成液体,回收利用。
6. 尾气处理最后,将位于低温甲醇洗吸收塔顶部的尾气送至尾气处理系统,经过吸收剂的吸附和吸附剂的再生,去除其中的甲醇和其他有害物质,然后排放或进行二次利用。
综上所述,低温甲醇洗工艺流程简单明了,通过原料气体净化和预冷、低温甲醇洗吸收塔、脱硫反应、甲醇溶液循环、甲醇回收和尾气处理等步骤,可以高效地去除气液中的硫化物、二硫化碳等有害物质,保证生产过程的安全和环保性。
这一工艺在化工、石化等行业的应用前景广阔,有着重要的经济和环境效益。
- 1、下载文档前请自行甄别文档内容的完整性,平台不提供额外的编辑、内容补充、找答案等附加服务。
- 2、"仅部分预览"的文档,不可在线预览部分如存在完整性等问题,可反馈申请退款(可完整预览的文档不适用该条件!)。
- 3、如文档侵犯您的权益,请联系客服反馈,我们会尽快为您处理(人工客服工作时间:9:00-18:30)。
中。
不过,即使能够输送,煤所含杂质的类型和数量会迅速使蒸汽转化用的催化剂及下游其他对毒物敏感的催化剂失活。
采用比轻石脑油重的液态烃,情况也是如此。
解决办法是利用气化法,或部分氧化,煤与适量氧气或富含氧的空气以及蒸汽燃烧,以便与CO或在不完全燃烧中所生成的气态烃反应生成CO2和多余H2。
燃烧过程为不采用催化剂、有蒸汽参与的反应提供充分热量,因而不会出现合成气反应塔内催化剂损坏的问题。
由煤和重质烃原料气化而来的合成气原料含氢、CO、CO2和剩余蒸汽,还包括气化剂不是纯氧的极少数情况下,来自空气中的氮、惰性气体,加上硫化氢,羰基硫(COS)、煤烟和灰。
气化后,首先采用传统气体净化方法脱除固体。
然后使CO与蒸汽进一步反应生成CO2和H2,以调整气体组分使之更适于甲醇或其他产品合成,或者在氢或氨装置中尽量增加氢气量,无论最终采取何种办法脱除CO,都要尽量减少残留的CO。
水气变换反应需要催化剂,即使在高温变换(HTS)工艺,原料气中的硫含量对所采用的更耐用的催化剂而言都显得较高,在采用转化法的氢和氨装置中,为进一步降低气体中CO含量需进行低温变换(LTS)反应,那么原料气中的硫对更敏感的催化剂而言浓度就显得更高了。
因此在气体到达HTS催化剂之前,要将气体中的硫脱除到一定程度,但若将硫浓度脱除到不破坏LTS催化剂的低浓度就不切实际了,所以,即使气化法合成气装置含LTS工序,仍存在少量硫。
在必需脱除所有碳氧化物的情况下,象氨装置和制取高纯度氢气的装置,高温变换后用某些湿法净化工艺脱除大量CO2,随后再采用物理吸收法如变压吸附(PSA)、深冷分离或催化甲烷化脱除残留CO2和CO。
最后一种方法的缺点是碳氧化物会转化回甲烷,在氨装置中,甲烷在合成回路中积累,增加了净化要求。
在采用清洁原料的蒸汽转化合成气装置中,脱除CO2的大型装置一般采用再生式化学洗涤溶液如活化热钾碱(Benfield,Vetrocoke,Catacarb,Carsol工艺)或活化MDEA。
但重质原料生成合成气时,其中的杂质易与这些化学洗涤液发生不可逆反应,影响效率,并可能加重腐蚀。
因此,气化法制合成气装置往往普遍采用可逆的物理吸收工艺脱除大量CO2。
这在高压气化装置尤为适用。
2 低温甲醇洗净化工艺几十年来,酸气脱除工艺在气化合成装置中一直占主导地位,因为该工艺极适合这种特殊条件。
这就是低温甲醇洗净化工艺,由林德和鲁奇两家股份公司共同开发。
工业化低温甲醇洗净化工艺为氨、甲醇、纯CO或含氧气体净化氢气和合成气,以达到脱除酸性气体之目的。
低温甲醇洗净化工艺是操作温度低于水冰点时利用甲醇(21业类“A”级)作为净化吸收剂的一种物理酸气净化系统。
净化合成气总硫(H2S与COS)低于0.1×10—6(体积分数),根据应用要求,可将CO2物质的量浓度调整到百分之几,或百万分之几(体积分数)。
气体去最终合成工艺(氨、甲醇、羰基合成醇、费—托法合成烃类等)之前,无需采取上游COS水解工艺或使气体通过另外的硫防护层。
(如氨合成),要么是含低浓度CO2的未变换或部分变换的气体(如CO、含氧气体或甲醇合成气),也可能是上述气体的混合。
在后一种条件下,将低温甲醇洗净化装置设计成同时处理变换和未变换的2种原料气(如同时生产CO和甲醇),如图3所示。
可以采取两种不同的净化流程,但要采用1个共同的溶剂再生系统。
利用一种优化的贫液/半贫液溶剂能显著提高这种配置的工艺经济性,减少需要热再生的溶剂量,并能将该工艺与林德公司深冷CO冷箱匹配。
2.1 一步法与二步法低温甲醇洗净化工艺传统的二步法低温甲醇洗净化工艺设计中(见图4),H2S与羰基硫在变换上游的第1步被脱除,CO2在变换下游的第2步被脱除。
每一步都有各自独立的洗涤塔。
因气体己脱除到较高程度,所以铁铬催化剂能在变换过程中安全使用。
操作压力一般低于5.5 MPa。
最近,林德公司开发了1种先进的一步法低温甲醇洗净化工艺,见图5。
硫化合物和CO2分别在1个独立设备中的不同部位被选择性脱除。
由于低温甲醇洗净化工艺位于变换反应之后,需采用耐硫(酸性)变换催化剂。
为维持催化剂活性,要求气体中H2S保持在最低浓度。
压力一般为8MPa。
因一步法低温甲醇洗净化工艺仅需1个净化器和1个气体冷却设备,所以明显地节省投资。
2.2 工业应用目前全球已建或处于设计/在建阶段的采用林德公司低温甲醇洗净化的装置约40套。
除了鲁奇公司一直提供低温甲醇洗净化装置外,低温甲醇洗净化工艺净化世界上75%由石油残渣、煤和废料制成的合成气,净化90%用气化法供非IGCC应用的合成气。
林德公司的低温甲醇洗净化工艺主要用于GE/德士古和壳牌公司气化器的煤和石油原料,也用于沥青和尤里卡沥青以及高温温克勒和科珀煤气化工艺的工业装置。
需特别指出的是20世纪80年代投运的GE/德士古煤气化装置中,有5套林德公司低温甲醇洗净化装置正可靠运行,其中2套运行压力为6 MPa左右。
2004年,林德公司签订合同,在壳牌煤气化装置下游建造3套低温甲醇洗净化装置。
其中2套用于中国云南省年产量超过550 kt 氨的合成气。
另1套是双系列装置,用于净化内蒙古1套煤液化装置中的氢气。
2005年林德公司又签订3份合同,为净化GE/德士古煤气化装置制成的合成气建造低温,甲醇洗工艺。
其中2套包括共同生产低温CO和甲醇合成气,第3套用于3种不同合成气——氢气、含氧合成气和甲醇合成气的混合气体。
2.3 比较甲醇与PEGE吸收剂由于H2S与CO2在甲醇的溶解性均较高,低温甲醇洗净化工艺在溶剂循环速率相当低的条件下运行,该速率比PEGE为溶剂(如UOP—SelexoR,BASF—SepasolvR,Clariant GenosorbR等)的另一种物理吸收工艺的循环速率低25%。
图6对CO2与H2S在PEGE和甲醇的溶解度加以比较,PEGE溶剂对H2S的选择性高于CO2。
因此采用PEGE脱硫的吸收工艺仅能脱除工艺气中极有限的一部分CO2,一般在20%左右。
但在甲醇装置中这可能是个优势,因为在甲醇装置中CO2是合成气中一个受欢迎的组分,但在氨装置中CO2必须全部脱除,所以需要其他工艺步骤。
这就是变压吸附(PSA)。
但是,若采用PSA脱除大量CO2,许多H2会与CO2一起排到废气中。
PSA中H2回收率最多为90%,尽管采用液氮洗,回收率可能会增加几个百分点,但也存在局限性,尤其是在高压条件。
总之,通过加大所有上游设备(原料准备、合成气生产/调节、空气分离装置等)以及增加相应的原料需求,分别增加10%就可以补偿H2的高损失率。
这种增加设备尺寸的作法比起在下游脱除酸气和合成气净化工艺中减少资金和操作成本的作法要有效得多。
由图6得出以下结论:a)由于溶剂循环率低得多,动力消耗指数(如电能、蒸汽和冷却水)明显下降。
低温甲醇洗净化工艺一般不需要膨胀涡轮机再发电。
b)对大型合成装置而言,可以将低温甲醇洗工艺的酸气脱除装置设计成单个装置。
c)大部分设备(换热器、泵和特定容器)尺寸由液体循环速率决定,所以它们比PEGE工艺的尺寸要小。
与PEGE系统相比,低温甲醇洗净化工艺的其他优点如下:a)无需上游加氢过程,譬如COS,通常在煤或油气化所制成的气体当中,它能完全被脱除。
PEGE溶剂只能脱除部分COS。
b)甲醇的化学性质非常稳定。
PEGE溶剂随运行时间增加而逐渐降解。
c)来自低温甲醇洗净化装置的工艺气非常干燥,仅含少量甲醇。
当深冷工艺(液氮洗或H2/CO分离工艺)紧接在低温甲醇洗净化工艺的下游时,工艺气温度极低,因低温甲醇洗净化工艺能提高深冷装置效率,同时简化设计从而降低设备成本。
来自PEGE的气体充满水蒸汽,温度相当高,这就对深冷工艺进料产生不利。
d)甲醇无腐蚀性,与PEGE溶剂相比,价格便宜而且应用范围广。
e)微量组分不会在溶剂中积累,因为低温甲醇洗净化工艺有长期净化水的装置。
f)从未发生过起泡现象。
g)合成气净化参数佳。
图7对低温甲醇洗净化工艺与PEGE净化工艺的动力消耗加以比较。
为脱除大量CO2并采用溶剂蒸发发电,对PEGE设计优化,但仅有30%的PEGE是热再生。
在中国采用GE/德士古煤气化工艺的1套1 200 t/d氨装置运行压力为3.3MPa。
表2中所采用的动力比成本可以看出,PEGE工艺的动力成本比低温甲醇洗净化工艺高50%左右。
2.4 低温甲醇洗净化工艺与化学(胺)吸收工艺的比较图8表示物理和化学溶剂的CO2负荷能力及原料气中CO2分压之间的关系。
当后者超过0.8MPa,低温甲醇洗净化工艺采用冷甲醇时,CO2负荷可达最高。
这就表明在低温甲醇洗净化工艺和MDEA用于煤或油气化制成的变换气时,当CO2分压较高,前者循环的净化溶剂比后者少得多。
与物理低温甲醇洗净化装置相比,用于脱硫和脱大量CO2的活化MDEA净化装置有下列特点:a)因CO2负荷能力较低(在更复杂的二步法活化MDEA工艺中),活化MDEA溶剂循环速率明显比高压气化下游的溶剂循环速率高,因而与低温甲醇洗相比,活化MDEA装置要大,这就与低温甲醇洗净化工艺的复杂性相抵消。
b)设备与管道尺寸限制了单个设备的能力。
c)因溶剂循环多,设备动力消耗(电力、蒸汽、冷水)较高。
d)深冷工艺如液氮洗装置位于脱除CO2装置之后时,在活化MDEA 工艺中,需要冷却装置对原料气预冷,只不过该装置比低温甲醇洗净化工艺所用的冷却装置小。
此外,将增加液氮洗净化工艺冷箱尺寸。
e)活化MDEA产生低浓度H2S,不适于克劳斯装置。
因此,鉴于CO2负荷高,要将硫回收装置设计成处理大气量,需用特殊技术如运行成本高的液体氧化还原硫回收装置(需补充化学制剂),若价格昂贵,要避免另外的浓缩过程。
f)采用低温甲醇洗净化工艺时,无需按高标准对合成气脱硫。
g)CO2产品纯度较低。
h)溶剂补充成本较高。
i)需检测以防止起泡和腐蚀。
2.5 材质低温甲醇洗净化工艺实际为非腐蚀工艺。
所有管道和几乎所有的设备均由碳钢制成。
只有下列设备由不锈钢制成:a)操作温度高于周边环境温度的所有塔板。
b)再沸器管道。
c)用于甲醇/水分离器的原料加热器管道。
许多装置的广泛应用证明材质选择的正确性。
选择碳钢、低温碳钢或合金低温碳钢应依据设备的设计温度以及采用条件。
2.6 痕量组分除了脱除酸气H2S+COS与CO2,原料气通常不含其他痕量组分,如氨、氰化氢、氧化氮、苯、萘、有机硫化合物(主要是二硫化碳和硫醇)、羰基镍和羰基铁。
有利的是冷甲醇能完全将痕量组分从原料合成气中脱除;不利的是它们会在循环甲醇溶剂中积累到有害程度。
这可能不利于工艺气纯度和尾气排放物。
此外,会出现设备和管道的腐蚀与堵塞问题。
原料气中痕量组分的性质及数量与气化装置的进料、气化装置类型及设计、工艺设计以及气化和低温甲醇洗的工艺设计与先后次序相关。