汽车弹簧液压弯管机设计
弯管机设计范文范文

弯管机设计范文范文一、引言弯管机是一种用于对金属管材进行弯曲加工的专用机械设备。
它在工业生产中具有广泛的应用,可以用于制造汽车零部件、家具、建筑结构等各种产品。
本文将介绍一种弯管机的设计方案,以满足一般工业生产需求。
二、设计要求1. 预期加工管材的直径范围为20mm-100mm;2.加工管材的最大弯曲角度为180度,且允许一定的误差范围;3.设备结构紧凑,便于操作和维护;4.设备具有稳定的性能和高效的加工能力。
三、设计方案1.设备整体结构设计弯管机的整体结构采用框架式设计,由主机、液压系统、电气控制系统等部分组成。
主机采用铸铁材料制作,确保设备的稳定性和强度。
液压系统采用双泵双回路设计,保证加工过程中的压力和流量的稳定控制。
电气控制系统采用PLC程序控制,实现精确的弯曲控制和操作界面的友好性。
2.弯管机构设计弯管机构设计采用液压弯曲方式,通过液压缸施加力对管材进行弯曲。
弯管机构由弯曲头、弯曲模具和夹紧装置组成。
弯曲头采用合金刚性材料制作,确保强度和耐磨性能。
弯曲模具采用可拆卸设计,方便更换不同直径的管材。
夹紧装置采用液压夹紧方式,确保管材在弯曲过程中的稳定性和安全性。
3.控制系统设计控制系统设计采用PLC程序控制,通过传感器实时检测管材的位置和角度。
根据设定的弯曲参数,控制液压系统的工作,实现精确的弯曲加工。
同时,为了提高操作的便捷性和安全性,增加了触摸屏显示和报警系统,确保操作人员可以清晰地了解设备的工作状态和异常情况。
四、设计优势1.设备具有较宽的加工管材直径范围,可以满足一般工业生产的需求;2.设备的弯曲角度控制精度高,可以满足产品的精度要求;3.设备结构紧凑,占地面积小,方便移动和维护;4.设备采用液压控制,加工效率高且稳定性好。
五、结论通过对弯管机的设计方案进行介绍,可以看出该设备具有较好的工业应用性能。
设计方案采用可靠的机械结构和先进的控制系统,可以满足工业生产的要求,提高生产效率和产品质量。
弯管机设计手册

弯管机设计手册摘要弯管机是一种常用于金属加工行业的机械设备,主要用于将金属管子或管材弯曲成所需的形状。
本手册旨在介绍弯管机的设计原理、结构特点、工作原理、安全操作规范以及维护保养方法,帮助用户更好地了解和使用弯管机。
一、引言弯管机是用于对金属管子进行弯曲加工的机械设备,广泛应用于汽车、航空航天、建筑等行业。
随着工业自动化水平的不断提高,弯管机在生产线上起着越来越重要的作用。
了解弯管机的设计原理和使用方法对于相关行业的从业人员至关重要。
二、弯管机的设计原理和结构特点1. 设计原理弯管机主要通过应用力对金属管子进行弯曲变形,其基本原理是利用沿管子周长产生等效弯矩的方法。
在弯管机的设计中,需要考虑材料的拉伸、挤压和弯曲变形,以实现预期的弯曲效果。
2. 结构特点弯管机通常由机床、液压系统、控制系统和弯头装置等部件组成。
弯头装置是实现管子弯曲的关键部件,通常包括弯曲机构、支撑辊、托辊装置等。
三、弯管机的工作原理1. 工作流程弯管机的工作流程主要包括工件夹持、弯曲、回程、松开和取件等步骤。
将待加工的金属管子夹紧在弯头装置上,然后通过控制系统对液压系统施加力,使弯头运动,最终实现管子的弯曲。
2. 控制系统弯管机的控制系统通常由数控系统和液压系统组成,通过对液压系统施加不同的压力和控制弯头的运动轨迹,实现对管子的精确控制。
四、安全操作规范1. 操作人员必须经过专业培训,了解弯管机的结构和工作原理,并熟悉相关安全操作规程。
2. 在操作过程中,必须严格按照操作规程操作,确保夹持和弯曲过程中工件的安全。
3. 弯管机在运行时,操作人员不得离开操作位置,以确保随时可以停止机器运行。
4. 弯管机具有一定的运行噪音和振动,操作人员需佩戴相应的防护设备,注意保护听力和身体健康。
五、维护保养方法1. 定期对弯管机的液压系统进行检查和维护,确保液压系统工作正常。
2. 对弯头装置的传动部件进行润滑保养,保证弯曲机构的稳定运行。
3. 定期检查和调整弯管机的机床和夹持装置,确保其工作精度和安全性。
专用弯管机液压系统设计

目录1弯管机原理 (2)1.1弯管机的工作原理 (2)1.2弯管机的工艺过程 (2)1.3弯管控制流程 (3)2液压系统 (4)2.1液压流程 (4) (4)2.2液压系统工况分析 (5)2.3.1液压缸工作负载的计算 (6)2.3.2 确定缸的内径和活塞杆的直径 (6)2.3.3计算液压缸在工作循环中各个阶段的压力、流量和功率的实际值 (7)3.4选择液压泵和电机 (8)3.4.1确定液压泵的工作压力、流量 (8)3.4.2液压泵的确定 (8)3.5辅助元件的选择 (9)3.6确定管道尺寸 (9)3.7确定油箱容积 (9)3.8液压电磁阀 (10)3.8.1 电磁阀选择 (10)3总结 (11)1弯管机原理1.1弯管机的工作原理弯管机主要由机械装置、液压系统、等组成。
机械装置主要有卡紧装置、小车推进装置、导向轮装置和摇臂回转装置等组成。
其工作原理是将钢管匀速推进,使钢管沿预设的轨道行走从而形成具有一定曲率半径和角度的弯管。
先将钢管安装就位,通过摇臂回转装置上的丝杠丝母传动装置调整好弯曲半径,从而获得所需的弯管管件。
特点:弯出的管具有形变小,壁厚差小,无应力。
弯曲半径0-1800可调节。
1.2弯管机的工艺过程本课题的研究工作主要是根据弯管机的工艺流程对弯管机的控制系统进行分析和数学建模,确定适用于该系统的控制算法,完成理论与实践的结合。
如图2-1所示。
图2-1弯管机流程由于管材的材质各异,管径、壁厚、弯曲角度等差异较大,使得中频电源加热温度和弯管推进速度之间的关系都不一样,并且各工艺参数的设定也比较复杂,而参数设定的合适与否会极大影响弯管的各种机械性能,所以要根据工况的不同进行参数选择,并由此控制弯管的质量。
其次在对弯管机的系统以及弯管工艺有一个很好的了解的基础上,根据实际情况,完成硬件设备的选型。
1.3弯管控制流程根据弯管机简单的工艺流程我们可以写出弯管机软件编程的流程框图,根据流程图可以很好的编写软件程序,以便更好、更准、更精的控制弯管机,生产出合格的弯管来。
液压弯管机的设计设计共46页文档
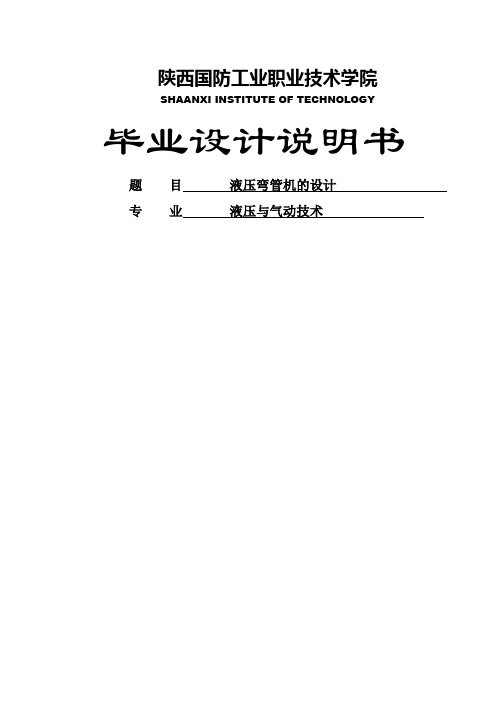
陕西国防工业职业技术学院SHAANXI INSTITUTE OF TECHNOLOGY 毕业设计说明书题目液压弯管机的设计专业液压与气动技术主题抄词液压与气动技术作为现代化机械设备实现传动与控制的重要技术手段,在国民经济的各个领域得到了广泛的应用。
与其他传动控制技术相比,液压与气动技术具有很多的优点,像功率密度大,工作平稳且快速性好,易于控制并过载保护,易于实现自动化和机电一体化的整合,因而广泛应用。
液压系统的设计制造和使用维护方面等具有多种显著的技术优势,故此使其成为现代机械工程的基本技术构成和现代控制工程的基本要素。
液压与气动技术相比之下,液压技术在机械工程领域应用非常广泛,所以本次的设计主要用的是液压技术。
电动弯管机是弯曲管材成型的主要设备之一,适用于可塑性材料的弯曲工艺加工。
它在建筑、制造、煤矿、石油、军工、工程等行业得到广泛应用。
本设计根据实际生产的需要和要求,再结合电动弯管机自身特点,设计了一款新型便携式半自动化电动弯管机。
该机可配备多式样不同半径的弯曲模具,从而实现管材不同半径和不同角度的弯曲加工。
在本设计中,利用液压传动的原理,拟定合理的液压系统图,经过必要的计算,确定液压系统的参数,据此来系统结构的设计和液压元件选型。
而对于机械结构,则是根据实际所需设计其结构,紧密、美观,符合人机工程学。
半自动化的设计,提高了生产效率和系统的安全性。
无论是液压系统,还是机械结构,都全方位的考虑使用者的安全和效率。
尤其是本次对液压接够采用车载卧式布局,更是结构简单,外形新颖美观,给使用者一种全新的感受。
毕业设计(论文)原创性声明和使用授权说明原创性声明本人郑重承诺:所呈交的毕业设计(论文),是我个人在指导教师的指导下进行的研究工作及取得的成果。
尽我所知,除文中特别加以标注和致谢的地方外,不包含其他人或组织已经发表或公布过的研究成果,也不包含我为获得及其它教育机构的学位或学历而使用过的材料。
对本研究提供过帮助和做出过贡献的个人或集体,均已在文中作了明确的说明并表示了谢意。
汽车用螺旋弹簧设计课件
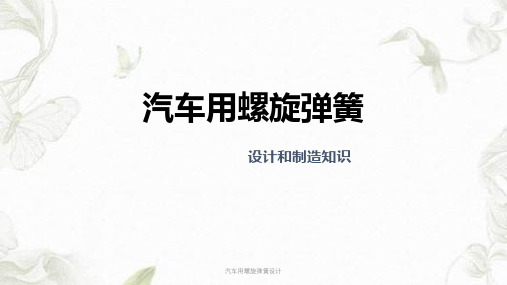
圆柱螺旋扭转弹簧
扭簧的结构型式:
汽车用螺旋弹簧设计
汽车用螺旋弹簧设计
扭簧设计参数
1. 扭簧钢丝直径 d mm
2. 扭簧圈中径D mm D1 内径 mm
D D1 D2 2
D2 外径 mm
3. 旋绕比 C=D/d 可按表1
4. 扭簧的试验扭矩T Nm
T
d 3
32
s
s 弯曲应力 N/m㎡
汽车用螺旋弹簧设计
螺旋弹簧(压缩、拉伸)的许用应力
许用应力按所受载荷类型可分三类: 1. Ⅰ类载荷:交变载荷次数在 1106 以上 的弹簧 。 2. Ⅱ类载荷:交变载荷次数在 1103~1106 次
范围内的载荷,以及冲击载荷等弹簧 。 3. Ⅲ类载荷:受静载荷以及交变载荷次数在 1103
次以下的载荷等。
740
710
570
许用剪
Ⅱ类
455
590
应力
〔τ〕
445
430
Ⅰ类
340
汽车用螺旋弹簧设计
选取许用应力的原则
1.对于行驶安全有重大影响的弹簧,许用剪切应力 应适当降低。
2.当弹簧的实际剪切应力大于许用应力而又无法通 过调整弹簧设计参数来降低时,则可考虑采用强 压处理或喷丸处理等工艺措施来实现。
汽车用螺旋弹簧设计
Ⅰ类
(0.35 ~ 0.40) (0.30~ 0.38) (0.25~ 0.30)
σb
σb
σb
汽车用螺旋弹簧设计
具体冷拔材料的许用剪切应力τ(MPa)注:不适用于直径小于
表5
1mm的钢丝
材料
65Mn
55Si2Mn; 55Si2MnB; 60Si2Mn;60Si2MnA;
专用弯管机液压系统设计

专用弯管机液压系统设计专用弯管机是一种用于加工金属管材的机械设备,其主要功能是将直管弯曲成所需要的形状。
专用弯管机的工作原理是通过液压系统控制液压缸来对管材进行弯曲。
因此,设计一个高效可靠的液压系统对专用弯管机至关重要。
下面将从液压系统的工作原理、液压元件的选择和系统的优化设计等方面进行详细介绍。
首先,液压系统的工作原理是通过液压能量来驱动液压缸进行工作。
液压系统主要包括液压泵、液压缸、液压阀、油箱和管路等组成部分。
液压泵通过吸油沟吸取液压油并将其压力增加,然后将液压油送入系统中的液压缸,从而实现对液压缸的驱动。
液压阀主要用于控制液压缸的工作速度、方向和力量等参数。
油箱则起到存储液压油和冷却液压油的作用。
其次,在选择液压元件时,需要考虑其性能、可靠性和适用性。
液压泵是液压系统中最关键的组件之一,其性能直接影响着液压系统的工作效果。
一般情况下,可选择柱塞泵或齿轮泵等类型的液压泵。
柱塞泵具有高压、高效的特点,适用于对液压缸施加大力的情况。
齿轮泵则是一种常用的液压泵,其特点是结构简单、价格便宜,适用于对液压缸施加较小力的情况。
液压缸的选型要考虑到专用弯管机的弯曲需求和工作环境。
液压缸的工作压力和行程需要与实际工作条件相匹配,以确保液压缸能够稳定可靠地完成工作任务。
液压阀是控制液压缸动作的关键元件,因此其稳定性和可靠性也需要高度重视。
根据弯管机的工作需要,可选用油液流量可调的溢流阀、双向阀和方向阀等。
最后,在系统的优化设计方面,需要确保系统的工作稳定、高效和安全。
在液压系统的布局上,需要合理安排各个液压元件的位置,以便提高系统的工作效率。
在管路布置上,应尽量减少管路的阻力,以减小对液压泵的负荷。
当液压系统工作压力较高时,可在系统中加入减压装置,以保护系统的安全使用。
在液压系统的使用上,需要定期对液压油进行检查和更换,以确保液压系统的正常运行。
同时,也需要对液压系统进行定期维护和保养,以延长其使用寿命。
综上所述,专用弯管机液压系统的设计需要考虑液压系统的工作原理、液压元件的选择和系统的优化设计等因素。
弯管机设计手册

弯管机设计手册一、弯管机概述弯管机是一种用于弯曲金属管材的机械设备,主要应用于金属加工行业,如汽车制造、航空航天、管道工程等领域。
它通过在金属管材上施加力量,使管材弯曲成所需的角度和形状。
弯管机的设计和使用涉及材料力学、机械设计、液压控制等多个领域的知识。
二、弯管机设计原理1. 结构原理弯管机主要由机架、弯管装置、液压系统、控制系统等部件组成。
机架支撑着整个弯管机的结构,弯管装置用于夹持和弯曲管材,液压系统提供所需的压力和动力,控制系统用于控制整个弯管过程。
2. 弯管原理在弯管机的操作过程中,首先将金属管材放入弯管装置中固定好,然后通过液压系统施加力量,使管材产生弯曲变形。
在这个过程中,要控制好所施加的力量和变形角度,确保弯管的精度和质量。
三、弯管机设计要点1. 结构设计弯管机的机架和弯管装置的结构设计应考虑到工作稳定性、承载能力和操作便捷性。
机架要具有足够的刚性和稳定性,弯管装置应能够灵活调整,适用于不同直径和厚度的管材。
2. 液压系统设计弯管机的液压系统设计应满足对不同管材的弯管需求,包括对压力、流量和速度的稳定控制。
应考虑到节能、安全和维护方便等因素。
3. 控制系统设计控制系统是弯管机自动化操作的关键,应具备精确的控制能力和灵活的调整功能,确保弯管过程的精确性和可靠性。
四、弯管机的应用和发展趋势1. 应用领域弯管机广泛应用于汽车制造、石油化工、航空航天、管道工程等领域,为这些行业提供了高效、精密的金属加工解决方案。
2. 发展趋势随着工业自动化和数字化的发展,弯管机的智能化、柔性化和自动化程度将会不断提高。
新材料和新工艺的出现也将对弯管机的设计和技术提出更高的要求。
五、弯管机操作与维护1. 操作注意事项在使用弯管机时,操作人员应熟悉设备的操作规程,严格按照操作要求进行操作,保证工作安全和产品质量。
2. 维护保养定期进行弯管机的润滑、清洁和检查,发现问题及时处理,保证设备的正常运行和寿命。
结语随着工业制造技术的不断进步,弯管机作为一种重要的金属加工设备,为加工行业提供了高效、精确的加工解决方案。
弯管机设计范文
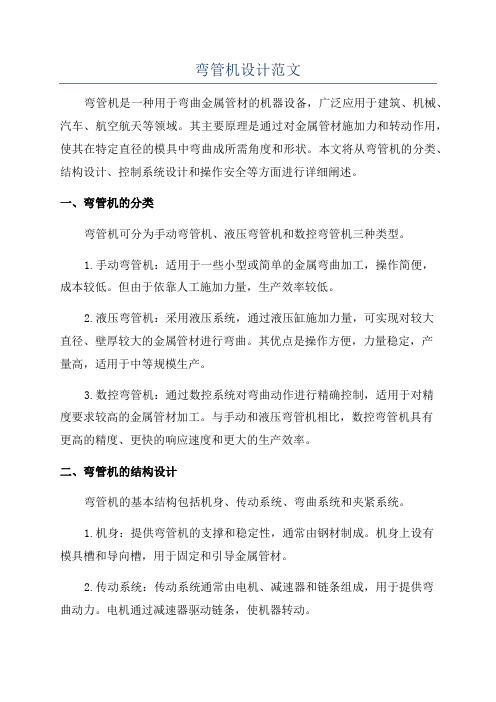
弯管机设计范文弯管机是一种用于弯曲金属管材的机器设备,广泛应用于建筑、机械、汽车、航空航天等领域。
其主要原理是通过对金属管材施加力和转动作用,使其在特定直径的模具中弯曲成所需角度和形状。
本文将从弯管机的分类、结构设计、控制系统设计和操作安全等方面进行详细阐述。
一、弯管机的分类弯管机可分为手动弯管机、液压弯管机和数控弯管机三种类型。
1.手动弯管机:适用于一些小型或简单的金属弯曲加工,操作简便,成本较低。
但由于依靠人工施加力量,生产效率较低。
2.液压弯管机:采用液压系统,通过液压缸施加力量,可实现对较大直径、壁厚较大的金属管材进行弯曲。
其优点是操作方便,力量稳定,产量高,适用于中等规模生产。
3.数控弯管机:通过数控系统对弯曲动作进行精确控制,适用于对精度要求较高的金属管材加工。
与手动和液压弯管机相比,数控弯管机具有更高的精度、更快的响应速度和更大的生产效率。
二、弯管机的结构设计弯管机的基本结构包括机身、传动系统、弯曲系统和夹紧系统。
1.机身:提供弯管机的支撑和稳定性,通常由钢材制成。
机身上设有模具槽和导向槽,用于固定和引导金属管材。
2.传动系统:传动系统通常由电机、减速器和链条组成,用于提供弯曲动力。
电机通过减速器驱动链条,使机器转动。
3.弯曲系统:弯曲系统包括模具、液压或机械弯曲装置。
具体设计根据弯曲材料和应用需求进行选择。
4.夹紧系统:夹紧系统由夹具和气缸组成,用于固定金属管材以防止其在弯曲过程中滑动。
三、弯管机的控制系统设计弯管机的控制系统包括传感器、执行器和控制器。
1.传感器:传感器用于检测金属管材的位置、角度和力度。
常见的传感器包括位置传感器、角度传感器和压力传感器。
2.执行器:执行器根据传感器信号控制弯管机的动作。
液压弯管机的执行器通常是液压缸,而数控弯管机的执行器通常是伺服电机。
3.控制器:控制器根据传感器信号和用户设置的参数,控制弯管机的动作和操作。
常见的控制器有PLC、伺服控制器和数控系统,其中数控系统具有更高的精度和灵活性。
液压可变刚度螺旋弹簧设计与分析
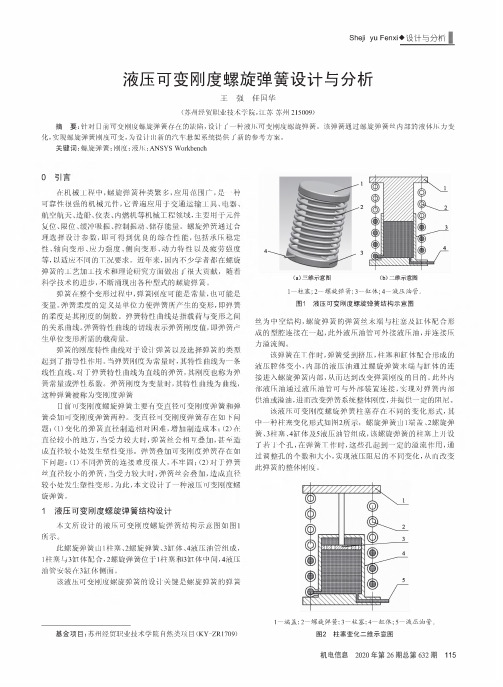
Sheji yu Fenxi♦设计与分析]液压可变刚度螺旋弹簧设计与分析王强任国华(苏州经贸职业技术学院,江苏苏州2150093摘要:针对目前可变刚度螺旋弹簧存在的缺陷,设计了一种液压可变刚度螺旋弹簧。
该弹簧通过螺旋弹簧丝内部的液体压力变化,实现螺旋弹簧刚度可变,为设计出新的汽车悬架系统提供了新的参考方案。
关键词:螺旋弹簧;刚度;液压;ANSYS Workbench0引F在机械工程中,螺旋弹簧种类繁多,应用范围广,是一种可靠性很强的机械元件,它普遍应用通工内机机械工程领域,主要用元件复位、限位冲存。
螺旋弹簧通过合设计参,可的性,压性变形、应力强度变力特性强度,应不同的工况要求。
,国内不少学者都在螺旋弹簧的工工技术方出了很,伶学技术的,现出种的螺旋弹簧。
弹簧在变过程中,弹簧刚度可是,也可是变量。
弹簧度的是位力弹簧的变,即弹簧的度是刚度的。
弹簧性是变的系。
弹簧性的弹簧刚度,弹簧产位变的。
弹簧的刚度性对设计弹簧弹簧的类了性用。
当弹簧刚度为,性为一条性。
对于弹簧性为的弹簧,刚度为弹簧弹性系。
弹簧刚度为变,性为,种弹簧为变刚度弹簧目前可变刚度螺旋弹簧主要有变径可变刚度弹簧弹簧叠加可变刚度弹簧两种。
变直径可变刚度弹簧存在如下问题:(1)变化的弹簧径相对困难,增成本;(2)在径较小的地方,当受力较,弹簧丝会相互叠,甚至成径较小处发生塑性变。
弹簧叠可变刚度弹簧存在如下问题*1)弹簧的连接难度很大,牢固;(2)对于弹簧丝径较小的弹簧,受力较,弹簧丝会叠,成径较小处发生塑性变形。
为此,本文设计了一种液压可变刚度螺旋弹簧。
!液压可变刚度螺旋弹簧结构设计本文所设计的液压可变刚度螺旋弹簧结构示意图如图1所示。
此螺旋弹簧由1柱塞、2螺旋弹簧、3缸体、4液压油管组成, 1柱塞与3缸体配,2螺旋弹簧位1柱塞3缸体中,4液压油管安装在3缸体。
该液压可变刚度螺旋弹簧的设计关键是螺旋弹簧的弹簧基金项目:苏州经贸职业技术学院自然类项目(KY-ZR1709)(a)三维示意图(b)二维示意图1—柱塞;2—螺旋弹簧;3—缸体;4—液压油管。
液压自动弯管机设计

本科毕业设计(论文)通过答辩摘要随着现代科技的高速发展,弯管技术已广泛应用于各个生产行业,特别是在锅炉、压力容器、石油石化工程等领域。
本次课题研究的双向弯管机是锅炉行业广泛使用的专业设备,属于液压弯管机,主要完成锅炉部件所需蛇形管的弯制。
这次研究中主要设计出了双向弯管机的模子提升装置和液压系统。
模子提升装置主要作用是使弯管模具提升或下降,因此,我们设计出其结构主要由定位油缸、杠杆、和机架组成,由液压泵提供动力,由杠杆传递,满足使弯管模的提升。
设计出了装置的所有零件后,计算分析了主要零件的的受力、强度情况,并用Pro/E软件进行三维实体建模与装配。
另外,我们设计了采用液压为整个双向弯管机提供动力,通过液压泵输出高压油来满足各个执行元件的正常工作。
主要设计出了液压泵站、油箱和一些辅助元件。
在管子的加工过程中,有加紧装置、转模装置、提升装置及模子横移装置都是采用液压来提供动力的,因此液压系统的设计尤其重要。
关键词:双向弯管机;模子提升;液压系统本科毕业设计(论文)通过答辩ABSTRACTAlong with the modern science and technology development, the elbow technology has widely applied in many realms of production, specially in the boiler, the pressure vessel as well as petroleum petrification project. Bidirectional pipe bending machine that we research is the specialized equipment used widespread in boiler profession, belongs to the hydraulic pressure pipe bending machine.It mainly curves the serpentuator pipes,which is a part of the boiler.In this research we had mainly designed the mold lifting gear and the hydraulic system,which belong to the bidirectional pipe bending machine.The function of the mold lifting gear is that makes the elbow piece mold promotion or drop, therefore, we designed that was made by the locating cylinder, the release lever, and the base, provided the power by the hydraulic pump, transmited by the release lever, then makes the elbow piece mold promotion and drop. After designing all components of the installment, analyzing the stress, the intensity situation of the major parts, wo carried them on the three dimensional entity modelling and the assembly with the Pro/E software.Moreover, we designs the hydraulic pressure provides the power for the bidirectional pipe bending machine, that can satisfy each functional element through the high-pressure oil outputed by hydraulic pump.We designe the station of hydraulic pressure pumping, the tank and some auxiliary parts. There are many installments provided power by hydraulic in the work of curving pipes, such as the step-up installment, the extension mold installment, the lifting gear , therefore the hydraulic system is especially important.Key words: Bidirectional pipe bending machine; Mold promotion; Hydraulic system本科毕业设计(论文)通过答辩目录第1章绪论 (1)1.1 本课题研究的目的及意义 (1)1.2 弯管机的概述 (1)1.3 课题背景 (3)1.4 国内外相关领域研究现状及成果 (3)1.4.1 弯管机的发展概况 (3)1.4.2 弯管机模子提升装置的发展概述 (5)1.4.3 弯管机动力系统的发展概述 (6)1.5 本章小结 (7)第2章机械结构总体方案设计 (8)2.1 模子提升装置总体设计要求及内容 (8)2.1.1 提升装置的设计要求 (8)2.1.2 提升装置的设计内容 (8)2.2 模子提升装置的设计方案 (8)2.2.1 模子提升装置整体机构的设计 (8)2.2.2 模子提升装置主要部分的设计方案 (9)2.3 模子提升装置的设计 (9)2.3.1 定位油缸的设计 (9)2.3.2杠杆的设计 (19)2.3.3机架的设计 (21)2.4 本章小结 (21)第3章模子提升装置三维实体建模 (22)3.1 Pro/E软件简介 (22)3.2 模子提升装置三维实体建模 (22)3.2.1 定位油缸的建模 (22)3.2.2 杠杆、机架的建模 (24)3.3 模子提升装置的装配 (25)3.3.1模子提升装置的装配 (25)3.4 本章小结 (26)第4章双向弯管机液压系统设计 (28)本科毕业设计(论文)通过答辩4.1 双向弯管机液压系统概述 (28)4.1.1 双向弯管机的液压系统的组成 (28)4.1.2 双向弯管机的液压执行元件 (28)4.2双向弯管机液压系统设计 (29)4.2.1 液压站的设计 (29)4.2.2 油箱的设计 (33)4.2.3 辅助元件的确定 (34)4.3液压系统漏油、噪声控制 (38)4.3.1 液压系统漏油控制 (38)4.3.2 液压系统噪声控制 (39)4.4本章小结 (39)结论 (40)参考文献 (41)致谢 (43)本科毕业设计(论文)通过答辩第1章绪论1.1 本课题研究的目的及意义1、研究的目的本次研究的双向弯管机主要由机床、加紧装置、弯曲装置、转换装置、模子横移装置、传动装置、角度发讯和松紧发讯装置及滑动副等等。
弹簧制作简易弯管器的原理
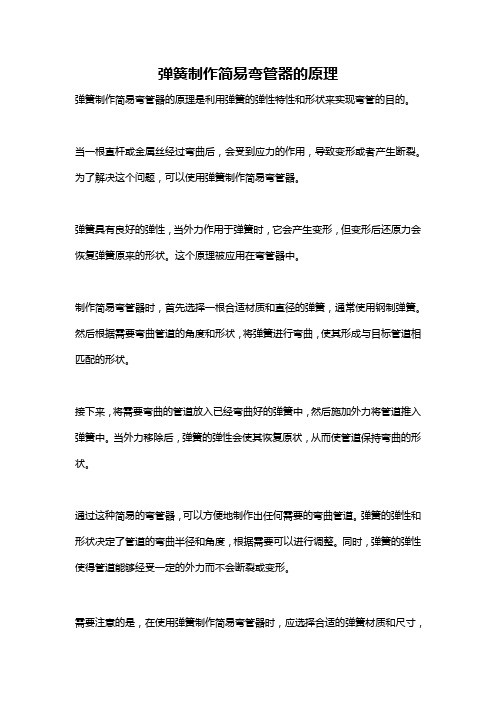
弹簧制作简易弯管器的原理
弹簧制作简易弯管器的原理是利用弹簧的弹性特性和形状来实现弯管的目的。
当一根直杆或金属丝经过弯曲后,会受到应力的作用,导致变形或者产生断裂。
为了解决这个问题,可以使用弹簧制作简易弯管器。
弹簧具有良好的弹性,当外力作用于弹簧时,它会产生变形,但变形后还原力会恢复弹簧原来的形状。
这个原理被应用在弯管器中。
制作简易弯管器时,首先选择一根合适材质和直径的弹簧,通常使用钢制弹簧。
然后根据需要弯曲管道的角度和形状,将弹簧进行弯曲,使其形成与目标管道相匹配的形状。
接下来,将需要弯曲的管道放入已经弯曲好的弹簧中,然后施加外力将管道推入弹簧中。
当外力移除后,弹簧的弹性会使其恢复原状,从而使管道保持弯曲的形状。
通过这种简易的弯管器,可以方便地制作出任何需要的弯曲管道。
弹簧的弹性和形状决定了管道的弯曲半径和角度,根据需要可以进行调整。
同时,弹簧的弹性使得管道能够经受一定的外力而不会断裂或变形。
需要注意的是,在使用弹簧制作简易弯管器时,应选择合适的弹簧材质和尺寸,
以及合适的管道直径,以确保弹簧能够承受所需的外力并保持稳定的弯曲形状。
液压弯管机支承部件设计

液压弯管机支承部件设计作者:陈翔来源:《环球人文地理·评论版》2014年第01期摘要:液压弯管机一种新型的具有弯管功能及起顶功能的弯管工具。
具有结构合理、使用安全、操作方便、价格合理、装卸快速、便于携带、一机多用等众多优点,在国内液压弯管机市扬占据很大份额,主要用于工厂、仓库、码头、建筑、铁路、汽车等安装管道和修理。
文章对液压弯管机支承部件进行设计。
关键词:液压弯管机;结构;创新高端装备制造业是高端制造业的主要部分,《国务院关于加快培育和发展战略性新兴产业的决定》,将高端装备制造产业囊括其间,凸显了其在产业链的核心地位。
“十二五”期间的发展重点主要集中在智能制造、绿色制造和服务性制造等方面。
装备制造业由大到强的转变,使高端装备制造业成为国民经济新的增长点并发展成为支柱产业。
保守估计到2020年,高端装备制造业销售产值将占装备制造业销售产值的30%以上,国内市场覆盖率也将超过25%。
中国生产方式换代升级的步伐可以从从国家十大振兴规划到未来重点发展七大新兴产业的发展趋势中窥见端倪,基于目前产业发展的现状。
主要进行重点产业的结构调整,转变升级“中国制造”为“中国创造”。
因此,高端装备制造业必然成为新兴产业的重中之重。
从这方面看,中国弯管机接下来的发展方向,必须在技术上下功夫,让液压弯管机的生产和制造过程走绿色、低碳之路。
1程控液压弯管机的主要技术参数弯管直径: ø80mm最小曲率半径: 180mm最大回转角度: 195°电动机:功率4KW转速: 960r/min模具回转速度: 1.4-2r/min外形尺寸: 1910*1840*1075mm流量: 70L/min重量:约2000kg2液压弯管机支承部件设计支承部分所采用的机构及零部件有:(1)床身:由钢板焊接而成,支承液压弯管机(2)机架盖板:有钢板焊接而成,机身内装有六个组成部件(3)工作台:工作台是一个箱体结构,这样便于拆装维修。
液压弯管机的设计设计
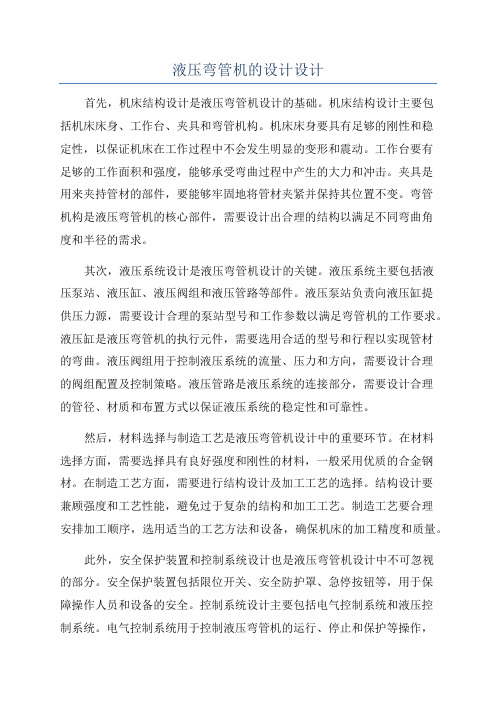
液压弯管机的设计设计首先,机床结构设计是液压弯管机设计的基础。
机床结构设计主要包括机床床身、工作台、夹具和弯管机构。
机床床身要具有足够的刚性和稳定性,以保证机床在工作过程中不会发生明显的变形和震动。
工作台要有足够的工作面积和强度,能够承受弯曲过程中产生的大力和冲击。
夹具是用来夹持管材的部件,要能够牢固地将管材夹紧并保持其位置不变。
弯管机构是液压弯管机的核心部件,需要设计出合理的结构以满足不同弯曲角度和半径的需求。
其次,液压系统设计是液压弯管机设计的关键。
液压系统主要包括液压泵站、液压缸、液压阀组和液压管路等部件。
液压泵站负责向液压缸提供压力源,需要设计合理的泵站型号和工作参数以满足弯管机的工作要求。
液压缸是液压弯管机的执行元件,需要选用合适的型号和行程以实现管材的弯曲。
液压阀组用于控制液压系统的流量、压力和方向,需要设计合理的阀组配置及控制策略。
液压管路是液压系统的连接部分,需要设计合理的管径、材质和布置方式以保证液压系统的稳定性和可靠性。
然后,材料选择与制造工艺是液压弯管机设计中的重要环节。
在材料选择方面,需要选择具有良好强度和刚性的材料,一般采用优质的合金钢材。
在制造工艺方面,需要进行结构设计及加工工艺的选择。
结构设计要兼顾强度和工艺性能,避免过于复杂的结构和加工工艺。
制造工艺要合理安排加工顺序,选用适当的工艺方法和设备,确保机床的加工精度和质量。
此外,安全保护装置和控制系统设计也是液压弯管机设计中不可忽视的部分。
安全保护装置包括限位开关、安全防护罩、急停按钮等,用于保障操作人员和设备的安全。
控制系统设计主要包括电气控制系统和液压控制系统。
电气控制系统用于控制液压弯管机的运行、停止和保护等操作,需要设计合理的电气控制回路和程序。
液压控制系统用于对液压系统进行控制,需要设计相关的控制策略和参数。
综上所述,液压弯管机的设计需要考虑到机床结构设计、液压系统设计、材料选择与制造工艺、安全保护装置及控制系统等方面,以确保机床的性能和可靠性。
液压自动弯管机设计
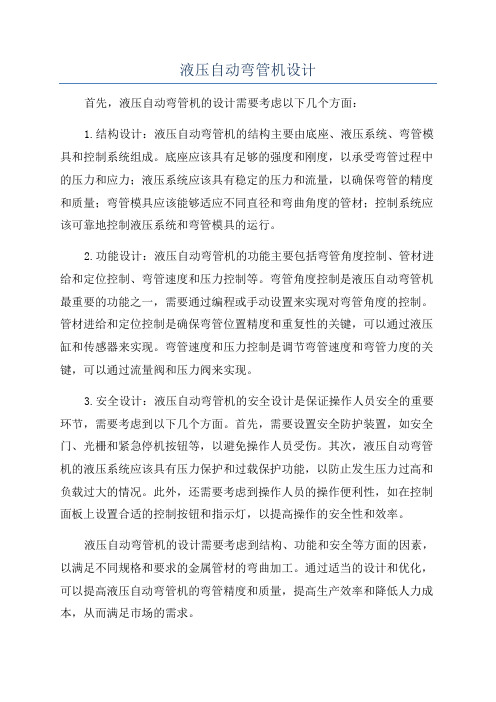
液压自动弯管机设计
首先,液压自动弯管机的设计需要考虑以下几个方面:
1.结构设计:液压自动弯管机的结构主要由底座、液压系统、弯管模具和控制系统组成。
底座应该具有足够的强度和刚度,以承受弯管过程中的压力和应力;液压系统应该具有稳定的压力和流量,以确保弯管的精度和质量;弯管模具应该能够适应不同直径和弯曲角度的管材;控制系统应该可靠地控制液压系统和弯管模具的运行。
2.功能设计:液压自动弯管机的功能主要包括弯管角度控制、管材进给和定位控制、弯管速度和压力控制等。
弯管角度控制是液压自动弯管机最重要的功能之一,需要通过编程或手动设置来实现对弯管角度的控制。
管材进给和定位控制是确保弯管位置精度和重复性的关键,可以通过液压缸和传感器来实现。
弯管速度和压力控制是调节弯管速度和弯管力度的关键,可以通过流量阀和压力阀来实现。
3.安全设计:液压自动弯管机的安全设计是保证操作人员安全的重要环节,需要考虑到以下几个方面。
首先,需要设置安全防护装置,如安全门、光栅和紧急停机按钮等,以避免操作人员受伤。
其次,液压自动弯管机的液压系统应该具有压力保护和过载保护功能,以防止发生压力过高和负载过大的情况。
此外,还需要考虑到操作人员的操作便利性,如在控制面板上设置合适的控制按钮和指示灯,以提高操作的安全性和效率。
液压自动弯管机的设计需要考虑到结构、功能和安全等方面的因素,以满足不同规格和要求的金属管材的弯曲加工。
通过适当的设计和优化,可以提高液压自动弯管机的弯管精度和质量,提高生产效率和降低人力成本,从而满足市场的需求。
280t弹簧式底座钢管压力矫直机设计
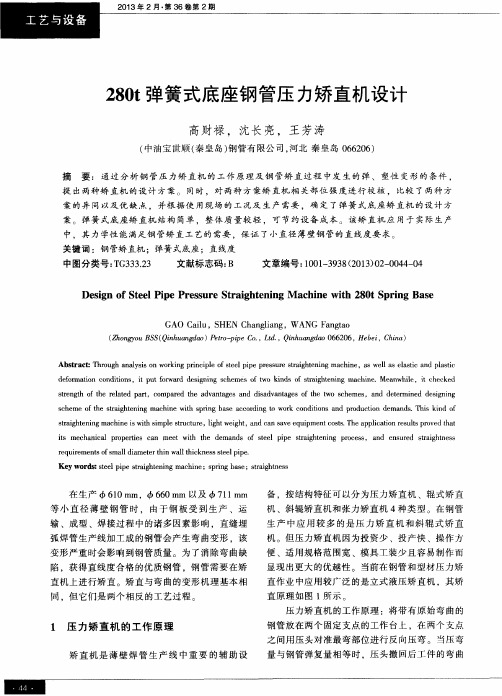
高 财 禄 ,沈长 亮 ,王 芳 涛
( 中油宝世 顺 ( 秦皇岛) 钢管 有 限公 司 , 河 北 秦皇 岛 0 6 6 2 0 6 ) 摘 要 :通过 分 析 铜 管压 力矫 直 机 的工 作 原理 及 铜 管矫 直过 程 中发 生 的 弹 、塑性 变形 的条 件 ,
( Z h o n g y o u B S S ( Q i n h u a n g d a o ) P e t r o - p i p e C o . , L t d . , Q i n h u a n g d a o 0 6 6 2 0 6 , He b e i , C h i n a )
中.其 力 学性 能 满足钢 管矫 直工 艺的需要 。保证 了小直径 薄壁钢 管 的直线度要 求 。
关键词 :钢 管矫 直机 :弹簧 式底座 ;直线度
中图分 类号 : T G 3 3 3 . 2 3
文献标 志码 : B
文 章编 号 : 1 0 0 1 — 3 9 3 8 ( 2 0 1 3 ) 0 2 — 0 0 4 4 — 0 4
s c h e me o f t h e s t r a i g h t e n i n g ma c h i n e w i t h s p i r n g b a s e a c c o r d i n g t o w o r k c o n d i t i o n s a n d p r o d u c t i o n d e ma n d s . T h i s k i n d o f s t r a i g h t e n i n g ma c h i n e i s wi t h s i mp l e s t r u c t u r e , l i g h t we i g h t , a n d c a n s a v e e q u i p me n t c o s t s . T h e a p p l i c a t i o n r e s u l t s p r o v e d t h a t i t s me c h a n i c a l p r o p e r t i e s c a n me e t wi t h t h e d e ma n d s o f s t e e l p i p e s t r a i g h t e n i n g p r o c e s s ,a n d e n s u r e d s t r a i g h t n e s s r e q u i r e me n t s o f s ma l l d i a me t e r t h i n wa l l t h i c k n e s s s t e e l p i p e . Ke y wo r d s : s t e e l p i p e s t r a i g h t e n i n g ma c h i n e ;s p r i n g b a s e ;s t r a i g h t n e s s
液压弯管机的设计

液压弯管机的设计引言液压弯管机是一种用于弯曲金属管道或管材的机械设备。
其采用液压系统提供动力,并通过一系列的弯曲模具和控制装置实现对金属管道的弯曲。
液压弯管机具有弯曲精度高、生产效率高的优点,广泛应用于航空、航天、汽车、机械制造和建筑等领域。
本文将详细介绍液压弯管机的设计原理和关键部件。
设计原理液压弯管机的设计原理基于液压传动和弯管原理。
液压传动是利用液体在封闭管道中的流动和压力传递力的原理,通过液压泵提供高压油液,经过阀门和管道传输到液压缸中,推动弯管机的工作部件实现弯管操作。
弯管原理是根据管材的强度和可塑性,通过施加力矩来改变管道的形状,实现管材的弯曲。
液压弯管机的主要部件包括:液压泵、液压缸、工作台、弯管模具和控制装置。
液压泵负责提供高压油液,液压缸负责将高压油液转化为线性运动力,工作台用于固定和支撑金属管道,弯管模具用于施加力矩进行弯管操作,控制装置用于控制液压系统的工作。
设计要点液压弯管机的设计中有几个重要要点需要注意:1. 弯管材料的选择液压弯管机可以用于弯曲各种材质的管道,例如碳钢、不锈钢和铜管等。
在设计中需要根据具体应用场景选择合适的管材,考虑管材的强度、可塑性和耐腐蚀性等因素。
2. 弯管角度和半径的控制液压弯管机可以实现不同角度和半径的弯曲操作,设计时需要考虑工作台和弯管模具之间的距离和角度调节装置。
合理设计这些部分可以实现精确控制弯曲角度和半径,以满足不同工件的要求。
3. 液压系统的设计液压弯管机的液压系统是实现机械运动的核心部件,设计时需要考虑油液的供给和压力调节,以及流速的控制。
合理设计液压系统可以提高工作效率和精度,并确保机械设备的可靠性和稳定性。
4. 安全措施的设计液压弯管机在操作过程中可能会受到较高的压力和力矩,设计时需要考虑安全措施,以保证操作人员的安全。
例如增加机器的防护罩和安全传感器,设置急停开关和紧急停止装置等。
结论液压弯管机是一种应用广泛的机械设备,其设计原理基于液压传动和弯管原理。
- 1、下载文档前请自行甄别文档内容的完整性,平台不提供额外的编辑、内容补充、找答案等附加服务。
- 2、"仅部分预览"的文档,不可在线预览部分如存在完整性等问题,可反馈申请退款(可完整预览的文档不适用该条件!)。
- 3、如文档侵犯您的权益,请联系客服反馈,我们会尽快为您处理(人工客服工作时间:9:00-18:30)。
汽车弹簧液压弯管机设计摘要在汽车弹簧生产工艺中,卷耳包耳工序是关键。
单工位弯耳机是对汽车钢板弹簧主板进行切头弯耳一次成型的液压设备。
首先,文中提出了几种钢板切头弯耳的可行性方案以及工艺措施,并进行了分析、比较、论证,选出最佳方案。
其次,确定出单工位液压弯耳设备主要需要的机构及运动,并选定出各自具体的运动结构方案。
再通过以上分析、考虑,综合确定出设备的总体运动结构方案。
利用所给有关数据,对设备的各个机构进行动力、运动设计计算,确定各机构的尺寸。
绘制总体装配图及部件图,确定本设备的布局尺寸,设计出达到要求的汽车钢板弹簧的单工位液压弯耳。
而且在最后对整个设计工作进行总结、归纳,对部分设计问题进行分析说明。
关键词:液压设备弯耳机单工位弯耳机AbstractBending is the key in the plate spring production.This description is a general design and elucidation relevant to automobile steel plate bending machine what is used as cutting-out the head of the plate spring and bending the plate spring. Designed in the description is a single working hydraulic plate bending equipments.First, in this description, it raised several executable programmers and posed several technological specifications to product the automobile plate spring. And then we proceeded to compare and argued the programmers. Be virtue of the argument, we selected the best project. Then make sure the main requirements of the machines and sport construction of the single working hydraulic plate bending equipments, and definitude the specific structures. Then we were virtue of these researches, and combined various opinions, we made selection out concretely the project again. Sum up the above analysis and consider again, synthesize to make sure the total sport construction of the equipments and the project. Then we can be virtue of the parameter and refer to the reference book, make use of an each organization for count, we proceed to design and calculate of the motive power and sport movement of the equipment, and make sure the size of each organization.Then we drafted the general assembly diagram and parts assembly diagram of this equipment, certain this equipments attain the requests that we needed to product the spring. At finally proceeds to whole design work, and we can get the equipment of the simplex working bending machine of the automobile spring.Key word: Hydraulic equipment Bending equipment A single working bending equipment目录第一章总体方案论证 (6)1.1 液压式双工位弯椭圆耳型设备介绍 (6)1.1.1 生产布置 (6)1.1.2 工艺措施 (6)1.2机械式多工位卷耳设备介绍 (7)1.2.1 生产布置 (7)1.2.2 工艺措施 (7)1.3 液压式单工位弯耳设备介绍 (8)1.3.1 生产布置 (8)1.3.2 工艺措施 (8)1.4方案分析比较 (9)第二章具体运动结构方案设计 (11)2.1 抽芯机构运动结构方案的选定 (11)2.2切头机构运动结构方案选定 (12)2.3 定位机构运动结构方案选定 (15)2.4 抓紧机构运动结构方案选定 (15)2.5压紧机构运动结构方案选定 (16)2.6 转位弯耳机构运动结构方案选定 (17)2.7工作台升降机构运动结构方案选定 (18)第三章总体方案的选定 (19)3.1 设备工作程序如下: (20)第四章设计参数 (21)第五章计算 (22)5.1 动力设计计算 (22)5.1.1 压紧缸载荷分析并选定压紧缸缸径 (22)5.1.2计算切头缸载荷并选定切头缸缸径。
(22)5.1.3计算抓紧缸载荷并选定抓紧缸缸径 (23)5.1.4分析摆动缸载荷并选定摆动缸缸径 (26)5.1.5计算转动缸载荷并选定转动缸缸径 (26)5.1.6 分析移位缸载荷并选定移动缸缸径 (28)5.2 运动设计计算 (29)5.2.1 确定切头刀具工作角度: (29)5.2.2 确定齿轮齿条模数及齿轮齿数 (29)5.2.3计算抓紧机构转位角度 (29)5.2.4计算转位缸行程并选定标准行程 (30)5.2.5计算切头缸工作行程并选定标准行程 (31)5.2.6分析压紧缸工作行程并选定压紧缸标准行程 (31)5.2.7选定抓紧缸标准行程 (32)5.2.8选定切头机构移动缸标准行程 (32)5.2.9计算切头机构摆动缸并选定标准行程 (32)5.2.10选定抽芯缸标准行程 (33)5.2.11选定定位缸标准行程 (33)5.3 选定各工作油缸标准型号 (34)第六章部分设计问题说明 (35)6.1机架、切头架及抓紧架结构及材料 (35)6.2设备的润滑措施 (35)6.3芯轴的冷却措施 (36)结论 (38)致谢 (39)参考文献 (40)引言汽车钢板弹簧是极易损坏的零件,其主要是用于汽车、拖拉机和铁道车辆中作为一种弹性悬挂装置,起缓冲和减振作用,也可以在各种机械中作为防振装置。
具有机构简单,修理方便的特点。
它不仅用量大,消耗多,而且对汽车工业发展有不可替代作用。
汽车弹簧单工位弯耳机是对汽车钢板弹簧进行切头弯耳的设备。
去年我到湖北东风汽车公司进行了实习,在实习中我发现其对钢板弹簧弯耳工序都采用陈旧的单工位机械式弯耳设备或双工位液压式弯耳设备。
而国外则大多采用单工位液压式自动控制设备及工艺。
我们对汽车弹簧单工位弯耳机设备的产品开发和研究可以提高我国的钢板弹簧弯耳技术,使我国的弹簧弯耳技术跟上国际技术水平,加速我国汽车产业的发展。
本文所设计的设备,实现了一机多能即切头弯耳一机加工,提高生产效率,减低生产成本,使加工工艺变得简单易行,并且缩短了工作节拍,提高了加工的质量。
采用液压和PC自动控制,使设备的维护变简单。
第一章总体方案论证目前汽车生产厂家对钢板弹簧弯耳这一工序主要有以下三种。
1.1 液压式双工位弯椭圆耳型设备介绍该设备主要用于加工椭圆耳型的钢板弹簧卷耳,该卷耳结构如图1-1。
图1-11.1.1 生产布置在生产中设备的布置如图1-2。
工件→加热设备—950℃→冲床—切头→弯耳设备—成型→合格品图1-21.1.2 工艺措施将钢板弹簧加热至950 C高温,在冲床上切头,然后在弯耳机上进行卷耳加工,完成一个合格的卷耳,其工艺流程见图1-3。
1工位:切头 2工位1工步:弯耳成型 2工步:抽芯取工件图1-31.2机械式多工位卷耳设备介绍该设备用于加工钢板弹簧卷耳耳型,耳型结构见图1-4。
卷耳图1-41.2.1 生产布置在生产中,设备的布置如图1-5。
工件→加热设备—950℃→冲床—切头→弯耳设备—弯耳→整形设备—整型→合格品图1-51.2.2 工艺措施钢板弹簧加热至950 C高温后,在冲床上进行切头,在弯耳设备上分三个工步进行弯耳,最后在整形设备上进行整形,完成一个合格的卷耳耳型,其工艺流程见图1-6。
工位1:切头 2工位1工步:初弯 2工步:二次弯曲 3工步:成型 3工位:整形图1-61.3 液压式单工位弯耳设备介绍该设备用于加工平卷耳。
这种耳型较上、下卷耳及椭圆卷耳减小了耳型的内应力,因其纵向力作用方向和弹簧主片断面中线重合,使用性能较上、下卷耳好,因此是以后汽车应用的趋势,以前应用受阻碍的原因在于其制造较复杂。
平卷耳结构见图1-7。
图1-71.3.1 生产布置生产中设备的布置见图1-8。
工件→加热设备—950℃→弯耳设备—成型→合格品图1-81.3.2 工艺措施将钢板弹簧加热至950 C高温,在弯耳机上分3个工步完成一个弯耳弯曲。
其工艺流程见图1-9。
工步1:切头工步2:抓紧转位弯耳成型工步3:抽芯取工件图1-91.4方案分析比较从上面的方案分析可以知道:机械式多工位弯耳机设备属于比较老的设备,其加工方法是靠模板的推移和工件沿模型强制卷曲成型。
其模具复杂,更换调整困难,生产效率不高,并且最后产品精度还须靠整型磨具来保证,提高了成本。
双工位液压弯耳机虽然相对于机械式多工位弯耳机多了液压自动制,多了芯轴结构,加工质量较容易保证,但同样存在即多了冲床设备,扩大了生产面积,增加了工人配额,劳动生产率还是很不高,工人劳动强度同样过大等机械式多工位弯耳机的缺点。
而单工位液压弯耳设备较前两种设备有了许多改进和优点:首先,它将切头功能揉合到了设备中实现了一机多能并且无须整型,减少了生产设备,缩小了生产面积,同时提高了生产效率,降低了工人劳动强度,减少了工人配额,降低了板簧生产成本。