金属切削刀具课程设计
金属切削刀具课程设计

1 绪论1.1 刀具的发展切削加工是现代制造业应用最广泛的加工技术之一。
据统计,国外切削加工在整个制造加工中所占比例约为80%~85%,而在国内这一比例则高达90%。
刀具是切削加工中不可缺少的重要工具,无论是普通机床,还是先进的数控机床(NC)、加工中心(MC)和柔性制造系统(FMC),都必须依靠刀具才能完成切削加工。
刀具的发展对提高生产率和加工质量具有直接影响。
材料、结构和几何形状是决定刀具切削性能的三要素,其中刀具材料的性能起着关键性作用。
国际生产工程学会(CIRP)在一项研究报告中指出:“由于刀具材料的改进,允许的切削速度每隔l0年几乎提高一倍”。
刀具材料已从20世纪初的高速钢、硬质合金发展到现在的高性能陶瓷、超硬材料等,耐热温度已由500~600℃提高到1200℃以上,允许切削速度已超过1000m/min,使切削加工生产率在不到100年时间内提高了100多倍。
因此可以说,刀具材料的发展历程实际上反映了切削加工技术的发展史。
1.2 设计目的金属切削刀具课程设计是学生在学完“金属切削原理及刀具”等有关课程的基础上进行的重要的实践性教学环节,其目的是使学生巩固和深化课堂理论教学内容,锻炼和培养学生综合运用所学知识和理论的能力,是对学生进行独立分析、解决问题能力的强化训练。
通过金属切削刀具课程设计,具体应使学生做到:(1) 掌握金属切削刀具的设计和计算的基本方法;(2) 学会运用各种设计资料、手册和国家标难;(3) 学会绘制符合标准要求的刀具工作图,能标注出必要的技术条件。
2 成形车刀设计被加工零件如图1.所示,工件材料为:青铜;硬度HBS115 ;强度σb = 360Mpa 。
2.1 棱体成形车刀的结构尺寸棱体成形车刀多采用燕尾结构,夹固可靠,能承受较大切削力。
主要结构尺寸有:刀体总宽度0L 、刀体高度H 、刀体厚度B 及燕尾尺寸M 等。
图1(1) 刀体总宽度0L ,如图1所示c L L =0,式中:c L ——成形车刀切削刃总宽度,d c b a l L c ++++=l ——工作廓形宽度;d c b a 、、、——成形车刀的附加刀刃;a ——为避免切削刃转角处过尖而设的附加刀刃宽度,常取为0.5~3mm 。
金属切屑刀具课程设计

金属切屑刀具课程设计一、教学目标本课程旨在让学生了解和掌握金属切削刀具的基本知识、使用方法和维护技巧。
通过本课程的学习,学生将能够:1.描述金属切削刀具的类型、构造和性能参数。
2.解释金属切削原理,分析刀具在切削过程中的作用。
3.选择合适的刀具进行金属切削加工。
4.演示刀具的安装、调整和使用方法。
5.分析并解决金属切削过程中出现的常见问题。
6.掌握刀具的维护和保养方法,延长刀具使用寿命。
二、教学内容本课程的教学内容主要包括以下几个部分:1.金属切削刀具的基本概念:介绍刀具的类型、构造和性能参数,使学生了解刀具的基本特点和用途。
2.金属切削原理:讲解切削力、切削温度等基本概念,分析刀具在切削过程中的作用。
3.刀具的选择与使用:教授如何根据加工材料、加工工艺等条件选择合适的刀具,并演示刀具的安装、调整和使用方法。
4.金属切削常见问题分析:分析切削过程中出现的各种问题,如切削不稳定、刀具磨损等,并提供解决方法。
5.刀具的维护与保养:讲解刀具的维护保养方法,引导学生养成良好的刀具使用习惯,延长刀具使用寿命。
三、教学方法为了提高教学效果,本课程将采用多种教学方法相结合的方式进行授课,包括:1.讲授法:讲解金属切削刀具的基本概念、原理和操作方法。
2.讨论法:学生针对切削过程中遇到的问题进行讨论,培养学生的分析问题和解决问题的能力。
3.案例分析法:分析实际生产中的典型刀具应用案例,使学生更好地理解刀具的选择和使用。
4.实验法:安排实验室实践环节,让学生亲自动手操作,提高实际操作能力。
四、教学资源为了支持本课程的教学,我们将准备以下教学资源:1.教材:选用权威、实用的金属切削刀具教材,为学生提供系统、全面的知识体系。
2.参考书:提供相关的参考书籍,丰富学生的知识储备。
3.多媒体资料:制作课件、视频等多媒体资料,生动展示刀具的构造、使用方法等。
4.实验设备:准备充足的刀具、机床等实验设备,确保每个学生都能动手实践。
金属切削与刀具教案

金属切削与刀具教案
一、教学目标
1.了解金属切削的基本原理和方法;
2.熟悉金属切削时所使用的刀具类型、刀具特性及相关参数;
3.能够根据工件特性及要求,正确选择刀具与切削参数,使用合适的
刀具完成金属切削工作;
4.掌握正确的使用方法,养成良好的操作习惯,保护刀具。
二、教学内容
1.金属切削的基本原理
金属切削是一种利用刀具切削工件表面,使其加工成所要求形状的加
工方法,是机械加工常用的方法之一、在金属切削过程中,刀具对工件施
加切削力,使工件材料被断离,形成特定的形状,这种过程称为切削。
切
削力分成两种:推力和挤压力。
在金属切削过程中,工件的表面由于切削
力的作用,通常产生壳形变形,称为切痕。
2.常见刀具类型及特性
主要的刀具类型有:铣刀、锯刀、钻头、拉刀、钻头和磨刀等。
(1)铣刀:采用锯片或钻头的方式,在工件表面进行平面或螺纹铣削。
铣刀的刃形有钻头刃、V形刃、U形刃、多棱刃等,其特性主要体现在:
刃的厚度、形状、材料等;
(2)锯刀:用于锯削工件,形状一般为拉锯刀、快速锯刀、摆角锯刀等,其特性体现在锯刃的厚度、形状、材料等;
(3)钻头:主要用于钻孔。
金属切削刀具的课程设计报告
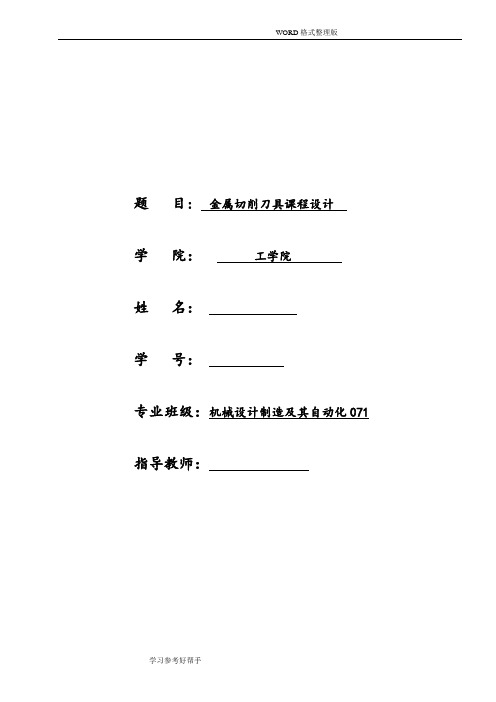
题目: 金属切削刀具课程设计学院:工学院姓名:学号:专业班级:机械设计制造及其自动化071 指导教师:目录一、课程设计目的及要求 (1)金属切削原理与刀具课程设计的目的 (1)金属切削刀具课程设计的要求 (1)1、对刀具工作图的要求 (1)2、对设计说明书的要求 (2)3.已知条件: (2)二、精加工内拉刀的设计 (4)(一)拉刀条件的选择 (4)1.拉削特点 (4)2.确定拉刀类型及拉削方式 (4)3.选择刀具材料。
(4)4.选择刀具的前角γf和后角αf (4)(二)拉刀工作部分的设计 (5)1.确定拉削余量 (5)f (5)2.确定齿升量z3.确定齿距P及同时工作齿数 (5)4.确定容屑槽形状和尺寸 (5)5.确定拉刀齿数和直径 (6)(三)拉刀其它部分设计 (8)1.柄部和颈部及过渡锥 (8)2.前导部与后导部及尾部 (8)L (9)3.拉刀总长度(四)拉刀强度及拉床校验 (9)1.拉削力 (9)2.拉力强度校验 (10)3.拉床拉力校验 (10)(五)拉刀技术条件 (10)(六)拉刀工作图 (11)1.容屑槽形状 (11)2.拉刀工作总图 (11)(七)、参考文献: (12)一、课程设计目的及要求金属切削原理与刀具课程设计的目的金属切削原理与刀具课程设计是机械设计及自动化专业学生在“金属切削原理”和“金属切削刀具”及其它有关课程的基础上进行的重要的实践性教学环节,是素质教育的主要措施之一。
其目的是使学生巩固和深化课堂理论教学内容,锻炼和培养学生综合运用所学过的知识和理论的能力,是对学生进行独立分析、解决问题能力的强化训练。
通过金属切削刀具课程设计,具体应使学生做到:(1) 掌握金属切削刀具的设计和计算的基本方法;(2) 学会运用各种设计资料、手册和国家(部或厂颁)标准;(3) 学会绘制符合标准要求的刀具工作图,能标注出必要的技术条件;(4) 掌握CAD在刀具设计中的应用。
金属切削刀具课程设计的要求1、对刀具工作图的要求刀具工作图应包括制造及检验该刀具所需的全部图形、尺寸、公差、粗糙度要求及技术条件等。
金属切削刀具设计基础课 程 设 计

金属切削刀具设计基础课程设计一.设计内容:1.设计一把指定型号的可转位车刀2.综合轮切式圆孔拉刀设计二. 时间安排:设计时间1周。
时间分配:每把刀具在0.5周内完成周一上午:布置设计题目及设计要求,借资料周一下午:设计可转位车刀结构及参数周二上午:绘制可转位车刀结构图一张(A3);周二下午:绘制可转位车刀刀杆图一张(A3);周三上午:编写设计说明书一份。
周四上午:设计综合轮切式圆孔拉刀结构及参数周四下午:绘制综合轮切式圆孔拉刀工作图一张(A2)周无上午:编写设计说明书一份周五下午:答辩三.指导教师及指导班级:宋建新:08010111(01-19号),08010112(01-19号),08010113(01-18号)宋书汉:08010112(20-38号),08010113(19-50号),08010114(20-50号)焦可如:08010114(01-19号),08010115(01-16),G0*******(01-10号)石莉:08010115(17-35号),G0*******(11-20号),08010111(20-50号)四.指导时间和地点:周一上午:jx301周五下午:答辩jx305其余:辅导jx305五.设计题目及分配:(一).可转位机夹车刀刀具设计题目1.已知:工件材料45钢(正火),使用机床CA6140,加工后dm=90,Ra3.2,需粗、半精车完成,加工余量自定,设计装C刀片900直头外圆车刀2.已知:工件材料GCr15,使用机床CA6140,加工后dm=72,Ra3.2,需粗、半精车完成,加工余量自定,设计装C刀片750直头外圆车刀3.已知:工件材料18CrMnTi,使用机床CA6140,加工后dm=36,Ra3.2,需粗、半精车完成,加工余量自定,设计装S刀片750直头外圆车刀4.已知:工件材料Cr18Ni9Ti,使用机床CA6140,加工后dm=26,Ra3.2,需粗、半精车完成,加工余量自定,设计装C刀片750弯头外圆车刀5.已知:工件材料40Cr,使用机床C630,加工后dm=140,Ra6.3,需粗、半精车完成,加工余量自定,设计装S刀片450直头外圆车刀6.已知:工件材料HT200,使用机床CA6140,加工后dm=95,Ra3.2,需粗、半精车完成,加工余量自定,设计装C刀片950偏头外圆车刀7.已知:工件材料Y12,使用机床CA6140,加工后dm=22,Ra3.2,需粗、半精车完成,加工余量自定,设计装T刀片950偏头外圆车刀8.已知:工件材料45钢,使用机床CA6140,加工后dm=45,Ra3.2,需粗、半精车完成,加工余量自定,设计装F刀片950偏头外圆车刀9.已知:工件材料Y12,使用机床CA6140,加工后dm=18,Ra3.2,需粗、半精车完成,加工余量自定,设计装D刀片930偏头外圆车刀10.已知:工件材料18CrMnTi,使用机床CA6140,加工后dm=100,Ra3.2,需粗、半精车完成,加工余量自定,设计装T刀片930偏头外圆车刀11.已知:工件材料40Cr,使用机床CA6140,加工后dm=120,Ra3.2,需粗、半精车完成,加工余量自定,设计装C刀片930偏头外圆车刀12.已知:工件材料HT200,使用机床CA6140,加工后dm=240,Ra3.2,需粗、半精车完成,加工余量自定,设计装S刀片750偏头端面车刀13.已知:工件材料45钢,使用机床CA6140,加工后dm=120,Ra3.2,需粗、半精车完成,加工余量自定,设计装C刀片950偏头外圆、端面车刀14.已知:工件材料50钢,使用机床CA6140,加工后dm=50,Ra3.2,需粗、半精车完成,加工余量自定,设计装S刀片750偏头外圆车刀15.已知:工件材料GCr15,使用机床CA6140,加工后dm=30,Ra3.2,需粗、半精车完成,加工余量自定,设计装S刀片450偏头外圆车刀16.已知:工件材料HT200,使用机床CA6140,加工后dm=200,Ra3.2,需粗、半精车完成,加工余量自定,设计装S刀片450偏头外圆车刀17.已知:工件材料45钢,使用机床CA6140,加工后dm=100,Ra3.2,需粗、半精车完成,加工余量自定,设计装T刀片900偏头外圆车刀18.已知:工件材料HT200,使用机床CA6140,加工后dm=80,Ra3.2,需粗、半精车完成,加工余量自定,设计装F刀片900偏头外圆车刀19.已知:工件材料HT200,使用机床CA6140,加工后dm=80,Ra3.2,需粗、半精车完成,加工余量自定,设计装W刀片500直头外圆车刀20.已知:工件材料HT200,使用机床CA6140,加工后dm=50,Ra3.2,需粗、半精车完成,加工余量自定,设计装T刀片900偏头外圆车刀注:班内每人一题,前20号粗加工,后20号精加工(二).拉刀设计已知:被加工孔直径D,拉前孔直径D0,拉削长度L,工件材料,机床型号(L6110),拉削粗糙度Ra(1.6)注:班内每人一题,前20号加工精度IT7,后20号加工精度IT8。
金属切削原理与刀具第5版课程设计

金属切削原理与刀具第5版课程设计简介金属切削是制造业中最广泛应用的技术之一,主要用于加工各种金属材料制造精密零部件。
刀具作为实现切削的基本设备,对于切削加工的精度、效率和成本等方面起着至关重要的作用。
因此,在现代制造业中,深入理解金属切削原理和刀具的应用技术显得尤为重要。
本次课程设计旨在深入介绍金属切削原理和刀具的技术,帮助学生理解切削加工的基本流程,并掌握刀具选择、切削力计算和数控切削程序编制等方面的知识,为学生提高金属切削技术水平奠定基础。
课程设计内容一、金属切削原理1. 切削力与切削热切削过程中,刀具与工件之间的接触产生了切削力和切削热,两者对加工效果和工具寿命有着非常重要的影响。
本节将介绍切削力和切削热的产生机理及其对工具和加工效果的影响。
2. 切削削角与切削力切削削角是影响切削力的重要因素之一,切削削角的设计和选择对切削加工的质量和效率有着关键的作用。
本节将详细讲解切削削角的设计原理和计算方法,并介绍切削力的计算方法。
3. 切削介质的选择切削介质对于切削加工的效果和寿命有着很大的影响。
本节将介绍切削介质的种类和应用,帮助学生理解和掌握切削介质的选择和使用。
二、刀具技术1. 刀具材料刀具材料是影响切削加工效果和寿命的重要因素之一。
本节将介绍刀具材料的种类和特性,解析不同类型的刀具适用的加工材料和工况,以及影响刀具寿命的因素和措施。
2. 刀具几何参数刀具几何参数的设计和调整对于切削加工的效率和品质有着很大的影响。
本节将详细讲解刀具几何参数的意义和设计方法,并针对不同类型的切削应用进行选择和调整。
3. 刀具磨损与寿命切削加工中,刀具的磨损和寿命是关键问题之一。
本节将介绍刀具磨损的种类和原因,以及刀具寿命的计算和措施。
三、刀具选择与切削力计算1. 刀具选择切削加工中,选择合适的刀具对于加工效率和成本至关重要。
本节将介绍刀具选择的基本原则和方法,以及不同类型的刀具在特定切削情况下的优劣势。
2. 切削力计算切削力的大小和方向对于切削加工的精度和工具寿命都有着非常重要的影响。
金属切削原理与刀具教案

金属切削原理与刀具教案一、教学目标1.了解金属切削的基本概念,掌握金属切削的原理。
2.掌握刀具的种类、结构及切削性能,学会选择合适的刀具进行金属切削。
3.了解金属切削过程中的切削力、切削温度、表面质量等影响因素,掌握切削参数的合理选择。
4.培养学生的动手能力,提高金属切削操作技能。
二、教学内容1.金属切削的基本概念(1)金属切削的定义(2)金属切削的分类2.金属切削原理(1)切削层(2)切削力(3)切削温度(4)表面质量3.刀具的种类、结构及切削性能(1)车刀(2)铣刀(3)钻头(4)铰刀4.切削参数的选择(1)切削速度(2)进给量(3)切削深度5.金属切削操作技能训练三、教学重点与难点1.教学重点:金属切削原理、刀具的种类及切削性能、切削参数的选择。
2.教学难点:切削力、切削温度的计算及影响因素,切削参数的合理选择。
四、教学方法1.理论教学:讲解金属切削的基本概念、原理及刀具的种类、结构等。
2.实践教学:通过金属切削实验,让学生动手操作,提高操作技能。
3.案例分析:分析金属切削过程中出现的问题,引导学生学会解决实际问题的方法。
五、教学安排1.理论教学:共6学时,分2次进行。
2.实践教学:共6学时,分2次进行。
3.案例分析:共2学时,分1次进行。
六、教学评价1.理论考试:占总评成绩的40%。
2.实践操作:占总评成绩的40%。
3.平时表现:占总评成绩的20%。
七、教学资源1.教材:《金属切削原理与刀具》。
2.辅助资料:金属切削相关学术论文、实验指导书。
3.设备:车床、铣床、钻床、铰床等。
4.软件:金属切削仿真软件。
八、教学进度安排1.第1周:金属切削的基本概念、分类。
2.第2周:金属切削原理。
3.第3周:刀具的种类、结构及切削性能。
4.第4周:切削参数的选择。
5.第5周:金属切削操作技能训练(1)。
6.第6周:金属切削操作技能训练(2)。
7.第7周:案例分析。
8.第8周:复习、考试。
九、教学总结本课程通过理论教学、实践教学和案例分析相结合的方式,使学生掌握金属切削原理、刀具的种类及切削性能、切削参数的选择等知识,培养学生的动手能力,提高金属切削操作技能。
金属切削原理与刀具课程设计说明书

《金属切削原理与刀具》课程设计说明书设计题目:成形车刀与圆孔拉刀设计专业:机械设计制造及其自动化班级:机本100*班学号: ***********设计人:指导老师:2012年06月目录一、圆体成形车刀设计1.1设计课题1.2选择刀具材料1.3选择前角γf及后角αf1.4刀具廓形及附加刃计算1.5计算切削刃总宽度Lc,并校验Lc/d min之值1.6确定结构尺寸1.7用计算法求圆体成形车刀廓形上各点所在圆的半径R x1.8廓形深度R 的公差1.9校验最小后角1.10计算车刀廓形宽度l x1.11 绘制刀具的加工工作图和样板工作图二、圆孔拉刀设计2.1刀具材料选取2.2拉削方式的选择2.3几何参数的选择2.4校准齿直径2.5确定拉削余量A2.6齿升量的选取2.7确定容屑槽形状和尺寸2.8分屑的确定2.9齿数及每齿直径2.10前柄部形状和尺寸2.11拉刀其他部分2.12拉刀总长度计算和校验2.13技术条件三、总结四、参考文献圆体成形车刀设计1.1设计课题(1)工件材料:50Cr(2)热处理状态:调质(3)材料直径:33mm(4)工件尺寸及图如下:(5)备注:加工全部表面及预切槽1.2选择刀具材料根据工件材料为50Cr,材料直径为33mm,查高速钢牌号及用途表,选用普通高速钢W18Cr4V制造。
1.3选择前角γf及后角αf根据材料的力学性能,查成形车刀的前角和后角表得:γf=5°,αf=10°。
1.4刀具廓形及附加刃计算根据设计要求,倒角部分附加切削刃的主偏角与倒角角度同为=20°,a=3mm,45°,预切槽部分附加切削刃的主偏角rb=1.5mm,c=5mm,d=0.5mma、b、c、d ------ 成形车刀的附加刀刃;a ------ 为避免切削刃转角处过尖而设的附加刀刃宽度,常取为0.5—3mm;b ------ 为考虑工件端面的精加工和倒角而设的附加刀刃宽度,其数值应大于端面精加工余量和倒角宽度。
金属切削原理与刀具教案

课程安排与考核方式
01
课程安排
02
考核方式
本课程共分为理论教学和实验教学两部分,其中理论教学包括课堂讲 授、课堂讨论等环节,实验教学包括切削实验、刀具磨损实验等。
采用平时成绩和期末考试成绩相结合的方式,其中平时成绩占总评成 绩的40%,期末考试成绩占总评成绩的60%。平时成绩包括课堂表现 、作业完成情况、实验报告等。
金刚石刀具
具有极高的硬度、导热性 和耐磨性,用于超精密切 削和加工非金属材料。
立方氮化硼刀具
具有极高的硬度、耐磨性 和耐热性,用于高速切削 难加工材料和高硬度材料 。
05
金属切削过程优化与控制
合理选择切削用量三要素
切削速度
根据工件材料、刀具材料和加工 要求,合理选择切削速度,以保
证加工效率和刀具寿命。
3
案例分析
以加工轴类零件为例,介绍车削加工的工艺过程 、切削用量选择、刀具选用及切削液使用等。
铣削加工方法及案例
铣削加工原理
利用铣刀的旋转和工件的移动进行切削,主要用于加工平面、沟 槽、齿轮等复杂形状。
铣削刀具类型
根据加工需求和工件材料选择不同直径、齿数和材质的铣刀,如 立铣刀、面铣刀、槽铣刀等。
良好的工艺性和经济性
刀具材料应具备良好的可加工性、 热处理性能以及较低的成本,以便 于制造和降低成本。
常用刀具材料及其选用
01
碳素工具钢
用于制造形状简单、切削速度 较低的刀具,如车刀、铣刀等
。
02
合金工具钢
在碳素工具钢的基础上加入合 金元素,提高了硬度和耐磨性 ,用于制造形状较复杂、切削
速度较高的刀具。
02
金属切削基本原理
切削运动与切削要素
《金属切削原理与刀具》教案

《金属切削原理与刀具》教案一、教学内容本节课的教学内容来自于小学《金属切削原理与刀具》教材的第三章,主要介绍金属切削的基本原理和刀具的分类及使用方法。
具体内容包括:金属切削的过程、切削力与切削功率、刀具的类型与结构、刀具的磨损与更换等。
二、教学目标1. 让学生了解金属切削的基本原理,知道切削力与切削功率的概念。
2. 使学生熟悉刀具的类型与结构,掌握刀具的磨损与更换方法。
3. 培养学生动手操作和实践能力,提高他们的技术素养。
三、教学难点与重点重点:金属切削的基本原理、刀具的类型与结构、刀具的磨损与更换。
难点:切削力与切削功率的计算、刀具的磨损规律及更换时机。
四、教具与学具准备教具:多媒体课件、刀具实物、切削实验装置。
学具:笔记本、课本、尺子、剪刀。
五、教学过程1. 导入:通过展示金属切削加工的视频,让学生初步了解金属切削的过程,引出本节课的主题。
2. 讲解:讲解金属切削的基本原理,介绍切削力与切削功率的概念,分析刀具的类型与结构,讲解刀具的磨损与更换方法。
3. 实践:让学生分组进行切削实验,观察刀具的磨损情况,学会正确更换刀具。
4. 讨论:分组讨论切削力与切削功率的计算方法,分享刀具磨损与更换的实践经验。
六、板书设计金属切削原理与刀具1. 金属切削过程2. 切削力与切削功率3. 刀具类型与结构4. 刀具磨损与更换七、作业设计1. 题目:计算切削力与切削功率已知条件:切削速度v = 50m/min,切削深度d = 2mm,切削宽度b = 10mm,刀具前角γ = 20°,刀具后角α = 15°,材料硬度HB = 200。
求:切削力F和切削功率P。
答案:切削力F = 150N切削功率P = 15W2. 题目:分析刀具磨损规律及更换时机要求:结合实践经验,分析刀具磨损的原因,判断何时需要更换刀具。
八、课后反思及拓展延伸1. 反思:本节课的教学效果如何?学生是否掌握了金属切削原理和刀具的使用方法?2. 拓展延伸:研究金属切削液的作用,探讨如何提高切削加工效率。
金属切削原理与刀具课程设计——圆孔拉刀设计设计

目录1已知条件 (5)2刀具材料的选择 (6)3几何参数的确定 (6)4齿升量的确定 (7)5齿距的确定 (7)6拉刀刚度允许最大槽深 (7)7检验容屑系数 (8)8容屑槽尺寸 (8)9柄部的计算 (9)10拉刀强度的校核 (9)11机床拉刀校核 (10)12拉刀校准齿直径 (10)13拉刀余量 (11)14切削齿齿数 (11)15校准齿齿数 (11)16确定各刀齿直径 (11)17切削部分长度 (11)18校准切削部分长度 (12)19分屑槽长度 (12)20前导部的直径和长度 (12)21后导部的直径和长度 (12)22柄部前端到第一齿长度 (13)23拉刀总长度 (13)24中心孔 (13)参考书目 (14)小结 (15)金属切削原理与刀具课程设计圆孔拉刀设计 1. 已知条件:a.被拉孔直径 0.022026mD表面粗糙度为0.8a R m b.预加工孔直径: 0D =w D =0.10.125c.拉削长度:000.134l mmd.工件材料: 45钢,0.735bGPa ,185——220HBS ,孔为钻孔坯。
e.拉床型号: L6110型卧式拉床 2.刀具材料的选择刀具材料选定为W18Cr4V 柄部选取为40Cr 3.几何参数的确定 a. 前角0r前角0r 的大小是根据被加工材料性质选择的,材料的强度或硬度高,前角宜小;反之,前角宜大,前角的偏差值一般取为2°。
由《复杂刀具设计手册》表1-1-7可以查得:0r =15°2°b. 后角后角是拉刀的类型及被加工工件所需的精度来决定的,内拉刀的后角应比外拉刀选的小些,校准齿的后角比切削齿的后角选的小些,切削齿后角的偏差取'30,校准齿后角的偏差取'15。
由《复杂刀具设计手册》表1-1-8可以查得: 切削齿后角0''23030校准齿后角0''13015zc.刃带1a b 的选择刃带应根据拉刀的类型及被加工材料的性质选择,在拉刀的切削齿上,允许有=0°,宽度1a b =0.05mm 的刃带。
金属切削刀具课程设计

(金属切屑刀具设计)题目:可转位外圆粗车刀学院:机械工程学院专业:机械设计制造及其自动化班级:姓名:指导教师:完成日期:一、概述 (1)二、加工表面 (1)三、选择刀片加固结构 (1)四、设计刀片材料 (2)五、选择车刀合理角度 (2)六、选择切削用量 (5)七、选择刀片型号和尺寸 (5)八、选择硬质合金刀垫型号和尺寸 (6)九、计算刀槽角度 (6)十、计算铣制刀槽时需要的角度 (8)十一、选择刀杆材料和尺寸 (9)十二、选择偏心销及其相关尺寸 (9)结论 (11)致谢 (12)一、概述硬质合金刀片是标准化、系列化生产的,其几何形状均事先磨出。
而车刀的前后角是靠刀片在刀杆槽中安装后得到的,刀片可以转动,当一条切削刃用钝后可以迅速转位将相邻的新刀刃换成主切削刃继续工作,直到全部刀刃用钝后才取下刀片报废回收,再换上新的刀片继续工作。
因此可转位式车刀完全避免了焊接式和机械夹固式车刀因焊接和重磨带来的缺陷,无须磨刀换刀,切削性能稳定,生产效率和质量均大大提高,是当前我国重点推广应用的刀具之一。
二、加工表面工件30CrMn 2Mo13 HB269-302尺寸:自由锻毛坯:φ125×1000,Ra =6.3 单边余量5~7图1 工件三、选择刀片加固结构考虑到加工在C630普通机床上进行,且属于连续切削,根据《金属切屑刀具设计简明手册》表1-1典型刀片加固结构简图和特点,采用偏心式刀片夹固结构。
四、设计刀片材料有原始材料给定:被加工工件材料为30CrMn 2Mo13,连续切削完成粗车工序,《金属切屑刀具设计简明手册》附录表-4选取刀片材料(硬质合金牌号)为YT5。
五、选择车刀合理角度根据刀具几何参数的选用原则,并考虑到可转位车刀的几何角度形成特点,选取如下四个主要角度:1、前角的设计查课本表得,根据刀具材料和工件材料的刀具的前角γο=13°—18°。
精加工的前角较大;粗加工和断续切削的前角较小;加工成形面前角应小,这是为了减小刀具的刃形误差对零件加工精度的影响。
金属切削教案课程

金属切削教案课程第一章:金属切削基础1.1 金属切削概念介绍金属切削的定义和作用解释切削加工的基本原理1.2 切削工具介绍不同类型的切削工具(刀片、钻头等)解释切削工具的选用原则1.3 切削参数介绍切削速度、进给量和切削深度的概念解释切削参数对加工质量的影响第二章:金属切削机床2.1 机床概述介绍金属切削机床的分类和特点解释机床的主要组成部分(床身、主轴等)2.2 数控机床介绍数控机床的定义和工作原理解释数控编程的基本概念和步骤2.3 机床选用与维护介绍机床选用的考虑因素(加工需求、预算等)解释机床的日常维护和保养方法第三章:金属切削加工方法3.1 车削加工介绍车削加工的定义和应用范围解释车削加工的基本步骤和操作要点3.2 铣削加工介绍铣削加工的定义和应用范围解释铣削加工的基本步骤和操作要点3.3 钻削加工介绍钻削加工的定义和应用范围解释钻削加工的基本步骤和操作要点第四章:金属切削工艺与参数调整4.1 切削工艺概述介绍切削工艺的概念和作用解释切削工艺的分类和选用原则4.2 切削参数调整介绍切削速度、进给量和切削深度的调整方法解释切削参数调整对加工质量的影响4.3 切削液的使用介绍切削液的作用和种类解释切削液的使用方法和注意事项第五章:金属切削加工质量控制5.1 加工质量概述介绍加工质量的概念和重要性解释加工质量的评估方法和指标5.2 加工误差分析介绍加工误差的种类和产生原因解释加工误差控制的方法和措施5.3 加工质量改进介绍加工质量改进的方法和步骤解释加工质量持续改进的重要性和实施策略第六章:金属切削刀具选择与应用6.1 刀具材料介绍常用刀具材料的特性与应用范围解释不同材料刀具的选用原则6.2 刀具几何参数介绍刀具几何参数(前角、后角等)的概念和作用解释刀具几何参数对加工质量的影响6.3 刀具选择与应用介绍刀具选择的方法和步骤解释刀具在实际加工中的应用技巧第七章:金属切削加工安全与环保7.1 安全操作规程介绍金属切削加工中的安全操作规程解释遵守安全操作规程的重要性7.2 常见事故预防与处理分析金属切削加工中常见事故的原因和预防措施介绍事故发生时的应急处理方法7.3 环保意识与实践强调金属切削加工中对环境保护的重要性介绍实施绿色加工的方法和途径第八章:金属切削加工实例分析8.1 轴类零件加工分析轴类零件的加工工艺和操作要点解释不同材料轴类零件的加工方法选择8.2 平面零件加工分析平面零件的加工工艺和操作要点解释不同材料平面零件的加工方法选择8.3 腔体零件加工分析腔体零件的加工工艺和操作要点解释不同类型腔体零件的加工方法选择第九章:金属切削加工自动化与智能制造9.1 数控技术应用介绍数控技术在金属切削加工中的应用解释数控加工的优势和局限性9.2 辅助加工介绍在金属切削加工中的应用解释辅助加工的优势和局限性9.3 智能制造发展趋势探讨金属切削加工行业向智能制造转型的趋势分析智能制造对金属切削加工的影响和挑战第十章:金属切削加工技能提升与职业发展10.1 技能提升途径介绍金属切削加工技能提升的途径(培训、实践等)解释持续学习与技能提升的重要性10.2 职业资格认证介绍金属切削加工行业的职业资格认证体系解释获得职业资格认证的意义和价值10.3 职业发展规划探讨金属切削加工职业技能人员的职业发展路径分析职业发展规划的制定方法和注意事项重点解析本文教案主要围绕金属切削加工展开,涵盖了基础概念、机床种类、加工方法、工艺参数、刀具选择、安全环保、实例分析、自动化智能制造以及职业发展等多个方面。
金属切削原理与刀具教案

金属切削原理与刀具教案一、教学目标1. 了解金属切削的基本概念和原理。
2. 掌握刀具的分类、构造及选用原则。
3. 熟悉金属切削过程中各种参数的作用和调整方法。
4. 掌握金属切削过程中常见问题的解决方法。
二、教学内容1. 金属切削基本概念:切削、切削力、切削热等。
2. 刀具的分类及构造:车刀、铣刀、钻头、磨头等。
3. 刀具的选用原则:根据加工材料、加工工艺等选择合适的刀具。
4. 金属切削过程参数:切削速度、进给量、切削深度等。
5. 金属切削过程中常见问题的解决方法。
三、教学方法1. 讲授法:讲解金属切削基本概念、原理和刀具知识。
2. 演示法:展示刀具实物,讲解刀具的选用原则和切削过程。
3. 案例分析法:分析实际加工过程中遇到的问题,探讨解决方法。
4. 小组讨论法:分组讨论金属切削过程中参数调整的方法。
四、教学准备1. 准备刀具实物、图片等教学资源。
2. 准备相关加工设备的视频资料。
3. 准备金属切削过程的模拟软件。
五、教学过程1. 引入:介绍金属切削在机械加工中的应用,引发学生兴趣。
2. 讲解金属切削基本概念和原理,展示相关图片和视频资料。
3. 讲解刀具的分类、构造及选用原则,展示刀具实物。
4. 讲解金属切削过程参数的作用和调整方法,进行案例分析。
5. 讨论金属切削过程中常见问题的解决方法,分享经验。
6. 总结本节课的重点内容,布置课后作业。
7. 使用模拟软件让学生实际操作,巩固所学知识。
六、教学评价1. 课堂讲授:评价学生对金属切削基本概念和原理的理解程度。
2. 刀具选用:评价学生对刀具分类、构造及选用原则的掌握情况。
3. 参数调整:评价学生对金属切削过程参数作用和调整方法的熟悉程度。
4. 问题解决:评价学生分析解决金属切削过程中常见问题的能力。
5. 软件操作:评价学生在模拟软件中实际操作的能力。
七、教学拓展1. 刀具的材料:介绍刀具材料的种类、性能及选择。
2. 先进加工技术:介绍数控加工、激光切割等先进加工技术。
《金属切削原理与刀具》课程设计指导书
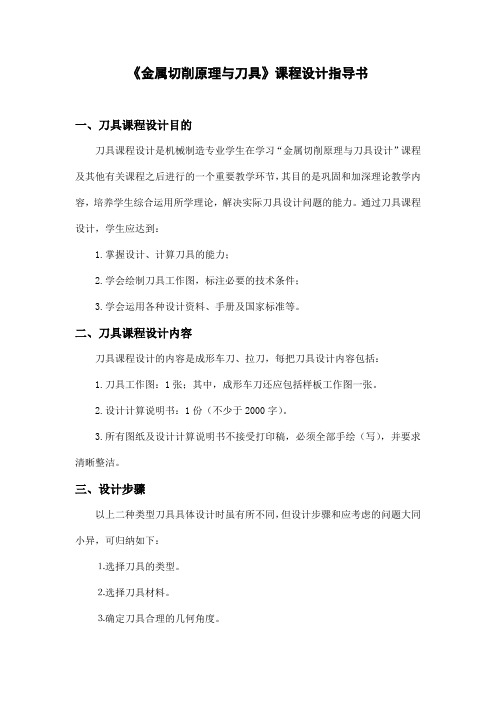
《金属切削原理与刀具》课程设计指导书一、刀具课程设计目的刀具课程设计是机械制造专业学生在学习“金属切削原理与刀具设计”课程及其他有关课程之后进行的一个重要教学环节,其目的是巩固和加深理论教学内容,培养学生综合运用所学理论,解决实际刀具设计问题的能力。
通过刀具课程设计,学生应达到:1.掌握设计、计算刀具的能力;2.学会绘制刀具工作图,标注必要的技术条件;3.学会运用各种设计资料、手册及国家标准等。
二、刀具课程设计内容刀具课程设计的内容是成形车刀、拉刀,每把刀具设计内容包括:1.刀具工作图:1张;其中,成形车刀还应包括样板工作图一张。
2.设计计算说明书:1份(不少于2000字)。
3.所有图纸及设计计算说明书不接受打印稿,必须全部手绘(写),并要求清晰整洁。
三、设计步骤以上二种类型刀具具体设计时虽有所不同,但设计步骤和应考虑的问题大同小异,可归纳如下:⒈选择刀具的类型。
⒉选择刀具材料。
⒊确定刀具合理的几何角度。
⒋确定刀具的结构参数,包括刀体尺寸、刀齿齿数、刀齿及容屑槽的形状和尺寸、刀具装夹部分的尺寸等。
⒌设计计算刀具的廓形(对成形刀具)。
⒍制定合理的技术条件,包括重要尺寸公差、形位公差、各重要表面的粗糙度、对刀具材料及热处理的要求等。
⒎考虑刀具的制造工艺和检验方法。
⒏绘制刀具的工作图。
四、设计要求⒈对刀具工作图的要求⑴刀具工作图应包括制造及检验该刀具所需的全部图形、尺寸、公差、粗糙度要求及技术条件等。
⑵工作图应反应出该刀具各部分的形状,同时又应使各视图的配置与安排整洁、匀称。
图中有些细小部分可以放大画出,如切削刃上的分屑槽、刀具上的刃带、小圆角等。
⑶刀具工作图中允许采用简化画法,如拉刀正投影图中可采用简化画法:粗切齿、精切齿、校准齿等各类刀齿允许只画出少数刀齿,其余刀齿用简化画法,齿顶用粗实线表示,容屑槽底用细实线表示,同时各个刀齿的尺寸及公差不标注在投影图中,而用尺寸表的方式写在拉刀工作图上。
⑷刀具图的图形、尺寸标注、公差标注等都应符合国家标准。
- 1、下载文档前请自行甄别文档内容的完整性,平台不提供额外的编辑、内容补充、找答案等附加服务。
- 2、"仅部分预览"的文档,不可在线预览部分如存在完整性等问题,可反馈申请退款(可完整预览的文档不适用该条件!)。
- 3、如文档侵犯您的权益,请联系客服反馈,我们会尽快为您处理(人工客服工作时间:9:00-18:30)。
1绪论1.1刀具的发展切削加工是现代制造业应用最广泛的加工技术之一。
据统计,国外切削加工在整个制造加工中所占比例约为80%〜85%,而在国内这一比例则高达90%。
刀具是切削加工中不可缺少的重要工具,无论是普通机床,还是先进的数控机床(NC)、加工中心(MC)和柔性制造系统(FMC),都必须依靠刀具才能完成切削加工。
刀具的发展对提高生产率和加工质量具有直接影响。
材料、结构和几何形状是决定刀具切削性能的三要素,其中刀具材料的性能起着关键性作用。
国际生产工程学会(CIRP)在一项研究报告中指出:“由于刀具材料的改进,允许的切削速度每隔10年几乎提高一倍”。
刀具材料已从20世纪初的高速钢、硬质合金发展到现在的高性能陶瓷、超硬材料等,耐热温度已由500〜600r提高到1200r以上, 允许切削速度已超过1000n Z mi n,使切削加工生产率在不到100年时间内提高了100多倍。
因此可以说,刀具材料的发展历程实际上反映了切削加工技术的发展史。
1.2设计目的金属切削刀具课程设计是学生在学完“金属切削原理及刀具”等有关课程的基础上进行的重要的实践性教学环节,其目的是使学生巩固和深化课堂理论教学内容,锻炼和培养学生综合运用所学知识和理论的能力,是对学生进行独立分析、解决问题能力的强化训练。
通过金属切削刀具课程设计,具体应使学生做到:(1)掌握金属切削刀具的设计和计算的基本方法;(2)学会运用各种设计资料、手册和国家标难;(3)学会绘制符合标准要求的刀具工作图,能标注出必要的技术条件。
2成形车刀设计被加工零件如图1.所示,工件材料为:青铜;硬度HBS115 ;强度c b = 360Mpa 。
(1)刀体总宽度L 0,如图1所示L 0 L c ,2.1棱体成形车刀的结构尺寸0. 8 W 6^0 01『':?-/ 列— 10■ l-fc20■ -----4812.5其余:一3.2\/ 0 0 -5-3.23.2f1.66d106键均布 0.012 A1x45°图1.图2.棱体成形车刀多采用燕尾结构,夹固可靠,能承受较大切削力 主要结构尺 寸有:刀体总宽度L o 、刀体高度H 、刀体厚度B 及燕尾尺寸M等。
图1式中:L c ――成形车刀切削刃总宽度, L c l a b c dl ――工作廓形宽度;a、b、c、d ――成形车刀的附加刀刃;a -- 为避免切削刃转角处过尖而设的附加刀刃宽度,常取为0.5~3mm。
b――为考虑工件端面的精加工和倒角而设的附加刀刃宽度,其数值应大于端面精加工余粮和倒角宽度。
为使该段刀刃在主剖面内有一定后角,常作成偏角k 15 ~45,b值取为1~3mm;如工件有倒角,k值应等于倒角角度值,b值比倒角宽度大1~1.5mmc --- 为保证后续切断工序顺利进行而设的预切槽刀刃宽度,c值常取为3~8mm d ――为保证成形车刀刀刃延长到工件毛坯表面之外而设的附加刀刃宽度,常取d =0.5~2mm。
(2)刀体高度H刀体高度H与机床横刀架距中心高度有关。
应在机床刀夹空间允许的条件下,尽量取大些,以增加刀具的重磨次数。
一般推荐H=55~100mm。
(3)刀体厚度B刀体厚度B应保证刀体有足够强度,要易于装入刀夹,排屑方便,切削顺利。
最小厚度应满足 B E A max (0.25~0.5)L。
,A max为工件最大廓形深度。
(4)燕尾测量尺寸M燕尾测量尺寸M值应与切削俄未能总宽度L c相适应。
此外,为调整棱体成形车刀的高度,增加成形车刀工作时的刚度,刀体地不做有螺孔以旋入螺钉,螺孔常取M6。
2.2棱体成形车刀材料及几何尺寸1)选择刀具材料参考附录表5,选择普通高速钢W18Cr4V制造2)选择前角f与后角f3)由表2-4,f选择0 , f 在12 ~ 17。
因此取 f 0 , f 15 4)画出刀具廓形计算图取u 20 , a 3mm , b 2mm , c 6mm , d 1mm 。
标出工件廓形各组成点1-14以0-0线(通过9-10段切削刃)为基准(以便于对刀),计算出1-14 各点处的计算半径r jx (为避免尺寸偏差值对计算准确性的影响,故常采用计算 尺寸一一计算半径、计算长度和计算角度来计算)18—mm 9mm 20.1r j6 30 01mm 14.975mm j2 4 r j8 r j1 1mm 8mmr j9 r j10 r j8 2mm 7mmr jx 基本半径半径公差2rj1rj2rj3rj4252mm 12.475mmrj5rj71232 J —102mm12.490mmrj11 r j12rj70.5mmtan 2011.116mmI j7 48mmI j6 10mm图25)在以1点为基点,计算出计算长度l jxI jx 基本公差公差 2l j5 20mml j2 40mm6)确定刀具结构尺寸L c l j7 a b c d 48 3 2 6 1mm 60mm , H=75mm , F=40mm ,B=45mm, E 12.200.43mm , d 8 0.005mm,7)用计算法求出N-N剖面内刀具廓形上各点至9、10点(零点)所在后刀面的垂直距离P x之后选择1-2段廓形为基准线,计算出刀具廓形上各点到该基准线的垂直距离P x,即为所求的刀具扩线深度1、2点至0点所在后刀面的垂直距离Rr j1 9mmh 0r f1 arcsin arcsi n —0 , Af cos f19 cos0 9r j1 9C1 A1 A0 9 7 2P1 C1 cos(f f) 2 cos(15 0 ) 1.932 r j3 12.475mm5 arcsin 丄arcsin 亠0,r j3 12.475f cos f312.475 cos0 12.475j3 (15 °15兰)mm215.075mm8mm , M 52.6200.14 mm3、4点至0点所在后刀面的垂直距离P3和刀具廓形到该基准线的垂直距离P3 A3C3 A3A 12.475 7 5.475P3 C3cos( f f) 5.475 cos(15 0 ) 5.288P3 5.288 1.932 3.3565点和7点至0点所在后刀面的垂直距离P5和刀具廓形到该基准线的垂直距离r j5 12.490mm.h 0 °r f5 arcs in arcs in 0 ,r j512.490A5 f cos f512.490 cos0 12.490C5 A5 A012.490 7 5.490p5 C5 cos( f f) 5.490 cos(15 0 ) 5.303P5 5.303 1.932 3.3717点与5点情况相同6点至0点所在后刀面的垂直距离P6和刀具廓形到该基准线的垂直距离P6 r j6 14.975mm.h 0 °r f6 arcs in arcs in 0 ,r j614.975A6 f cos f614.975 cos0 14.975mmC6 A6A) 14.975 7 7.975mmp6 C6 cos( f f) 7.975 cos(15 0 ) 7.704mmP 6 7.704 1.9324 5.772mm8点至0点所在后刀面的垂直距离P s 和刀具廓形到该基准线的垂直距离P 8r j8 8mmC 8 A 8 A 08 7 1P 8 0.966 1.9320.93211、12点至0点所在后刀面的垂直距离Pn 和刀具廓形到该基准线的垂直距离P11r j11 11.116mmhr f11 arcs inrj11fcos f11 11.116 cos0 11.116C 11A 11 A 011.116 7 4.116p 11 C 11 cos( f f ) 4.116 cos(15 0 ) 3.976P 8 3.976 1.932 2.0448)根据表2-5可确定各点 P x 公差,下表1为各点至9、10点(零点)所在后刀面的垂直距离P x 和各点到该基准线的垂直距离P xP 8 C 8COS( ff) 1 cos(15 0 )0.966hr f8 arcs inrj8arcs in 0 ,8fcos f 8 8 cos0 8arcs inAn表1棱体成形车刀廓形计算表9)校验最小后角7-11段切削刃与进给方向(即工件端面方向)的夹角最小,因而这段切削刃上后角最小,其值为0arctan tan( 11 11 )sin 20 arctan tan12 sin20 4.6 一般要求最小后角不小于2 ~3,因此校验合格。
10)确定棱体成形车刀廓形宽度l x即为相应工件廓形的计算长度l jx,其数值及公差如下,(公差值是按表2-5确定的,表中未列出者可取为0.2mm) 12l j2(40 0.2)mm13l j3 (15.075 0.06)mm15l j5(20 0.2)mm16l j6(10 0.2) mm17l j7(48 0.2)mm2.3确定刀具的夹固方式采用燕尾斜块式。
3拉刀的设计被加工零件如图2•所示,工件材料为:硬铝LY12;硬度HBS115 ;强度c b =490Mpa ;工件长度 L=20mm 。
3.1选疋刀具类型、材料的依据(1) 选择刀具类型对每种工件进行工艺设计和工艺装备设计时,必须考虑选用合适的刀具类型。
事实上,对同一个工件,常可用多种不同的刀具加工出来。
采用的刀具类型不同将对加工生产率和精度有重要影响。
总结更多的高生产 率刀具可以看出,增加刀具同时参加切削的刀刃长度能有效的提高其生产效率。
例如,用花键拉刀加工花键孔时,同时参加切削的刀刃长度l=B x n x Zi ,其中B为键宽,n 为键数,Zi 为在拉削长度内同时参加切削的齿数。
若用插刀同时参加 切削的刀刃长度比插刀大得多,因而生产率也高得多。
(2) 正确选择刀具材料刀具材料选择得是否恰当对刀具的生产率有重要的影响。
因为硬质合金比高 速钢及其他工具钢生产率高得多,因此,在能采用硬质合金的情况下应尽力采用。
但由于目前硬质合金的性能还有许多缺陷,如脆性大,极难加工等,使他在许多 刀具上应用还很困难,因而,目前许多复杂刀具还主要应用高速钢制造。
根据《刀具课程设计指导书》表 29,选择高速工具钢,其应用范围用于各种烤冃7tHHcom③刀具,特别是形状较复杂的刀具。
根据表~~30,选择 W18Cr4V HRC62-65 3.2刀具结构参数、几何参数的选择和设计 (1)拉刀的结构mam表代号名称功用1柄部夹持拉刀,传递动力2 颈部连接柄部和后面各部,其直径与柄部相同或略小,拉刀材料及规 格等标记 般打在颈部。
3 过度锥 颈部到前导部的过渡部分,使拉刀容易进入工件孔中。