基于PLC控制的自动配料系统的研究与应用
基于PLC模糊控制自动配料系统研究

20 w wbc-i. r w . i teo rk lc n
落在 落 料 区 , 皮 带 运 送 到 达 称 重 区 . 经 由电子 皮 带秤 对皮带 上 的物料 进行称 重 称 重 传感器 根 据所受 力 的
自适应调整 , 以满足不同 e e 时对控制参数的要求 和 c
该 系 统 实 现 自调 整 PD 参 数 的计 算 公 式 如 下 : I
An h e e r h r s ls a e s o d t a h uzy c n r ls se i e tr t a h r d t n l PI c n- d t e r s a c e u t r h we h tt e f z o to y t m s b te h n t e ta i o a D o i to lr nd c n q i k y c ry o r c so r p rin n ,wh c sl we o ta d g o c n mi e eis r le ,a a u c l ar utp e iin p o o to i g i h i o rc s n o d e o o c b n ft. Ke o ds:P yW r LC,f z y PI c n rl u o p o ri n n u z D o to ,a t— r po t i g o
Ab t a t s r c :An a t — r p ni n n y t m i u z o to a e n t e P C i i t d c d i h a e . u o p o o 0 i g s se w t f zy c n r l b s d o h L s n r u e n t e p p r h o
制 器成 本 要 低 很 多 . 而 产 生 了较 高的 经 济 效 益 从
基于PLC的自动配料系统设计

基于PLC的自动配料系统设计摘要本文针对自动化配料系统的设计与实现展开研究,系统采用了PLC控制技术,以此来实现物料的自动配送,提高生产效率。
文中介绍了自动化配料系统的组成结构、PLC控制器选型、系统工作原理及软件开发等关键技术,为自动化生产提供了技术支持。
关键词:自动化配料系统;PLC控制技术;配料;软件开发;工作原理AbstractThis paper focuses on the design and implementation of an automatic batching system using PLC control technology to achieve automatic material delivery and improve production efficiency. The composition structure of the automatic batching system, PLC controller selection, system working principle, and software development are key technologies discussed. This provides technical support for automated production.Keywords: automatic batching system; PLC control technology; batching; software development; working principle一、引言随着工业自动化水平的提高,自动化生产逐渐成为了行业发展的趋势。
其中,自动化配料系统是一个比较重要的环节,对于提高生产效率和降低生产成本具有重要意义。
本文主要针对自动化配料系统进行研究,采用PLC控制技术,以此实现物料自动化配送控制,达到提高生产效率的目的。
基于PLC控制的自动配料系统的研究与应用

( Beijing General Research Institute of Mining and Metallurgy,Beijing 100070 , China) ABSTRACT : Blending process plays a very important role in industries such as food,chemical,and petroleum as well. The accuracy of online blending is difficult to control in industrial production process. The accuracy of blending is determined by the performance of control system. Control system with high accuracy has been developed by this paper,which is realized based on PLC. This paper describes in detail the design scheme of hardware and software. Furthermore,this paper also introduces the communication parameter setting between the PLC and touch screen ,and system controlling process as well. After many industrial tests, this system has been proved of following advantages such as stable operation,high accuracy,strong electromagnetic interface resistance ability,and etc. KEY WORDS: PLC ; blending; automatic control; accuracy 在食品、 化工、 石油等行业中, 配料环节起着重 , 要的作用 配料工序的质量直接影响着产品的质量 。 在食品行业中, 各种成分按照一定的比例进行添加 配制, 长期以来多采用由单片机构成的仪表进行控 制, 由于单片机组成的仪表抗电磁干扰能力差 , 在具 有强电磁干扰的环境中, 系统的稳定性受到影响, 甚 至无法正常工作。 可编程控制器 PLC 是按照直接 应用于工业环境设计的, 因此可编程控制器具有可
自动配料系统论文

本毕业设计是西门子可编程序控制器和组态王组态软件在配料控制系统中的应用和研究,采用的是德国Siemens公司的S7-200系列PLC,运用与之相配的STEP7编程软件,通过LAD编程语言编制了下位机的控制程序,从而使配料系统可以按要求自动完成配料和装料全过程,并且在发生故障时可以自动停机。采用了组态王组态软件对上位机监控软件组态,实现了现场的实时监控,实时模拟等具有Windows风格的动态操作画面。通过PLC和组态软件的有效结合使配料系统大幅度提高其方便性、可靠性。
本文基于可编程序控制器PLC和组态软件设计自动配料系统的控制系统和监控系统。首先,利用德国Siemens公司的S7-200系列PLC对自动配料系统进行控制。运用与之相配的STEP7编程,通过LAD编程语言编制了下位机的控制程序,从而使该配料系统可以按要求完成自动配料,装料全过程。其次,自动配料系统的监控系统则采用了组态王组态软件对上位机监控软件组态,实现现场数据的实时监控。
可编程控制器对用户来说,是一种无触点设备,改变程序即可改变生产工艺,因此可在初步设计阶段选用可编程控制器,在实施阶段再确定工艺过程。另一方面,从制造生产可编程控制器的厂商角度看,在制造阶段不需要根据用户的要求专门设计控制器,适合批量生产。由于这些特点,可编程控制器问世以后很快受到工业控制界的欢迎,并得到迅速的发展。
基于PLC的自动配料系统

南昌航空大学课程设计题目:基于PLC得自动配料系统专业:自动化班级:110441班学号:姓名:指导老师:摘要自动配料系统就是集输送、计量、配料、定量等功能于一体得动态计量系统,在建材、化工、冶金、矿山、电力、食品、饲料加工等行业中得到广泛应用.随着科学技术得发展,工业化程度得提高,常需要对自动配料系统中输送得流量进行调节、控制达到准确得配比。
本论文主要针对自动配料系统恒流量控制达到配比得控制要求,设计一套基于PLC得自动配料系统,并使用触摸屏开发运行管理界面。
自动配料系统由可编程控制器(PLC)、变频器、皮带驱动电动机、称重传感器等构成。
系统包含三台皮带驱动电动机,它们根据需要依次顺序启动。
采用变频器实现对三相电动机得变频调速。
称重传感器对物料进行称重并实时计量,PLC计算出实时流量及累计流量,比较设定值与实际流量得偏差经PID调节改变输出信号以控制变频器对皮带驱动电动机得速度调节,从而实现恒流量控制,并对系统进行监控.关键词:自动配料,变频调速,PID调节,PLCﻬ目录摘要ﻩ错误!未定义书签。
Abstract........................................................................................................... 错误!未定义书签。
第一章绪论ﻩ错误!未定义书签。
1、1 课题背景及意义ﻩ错误!未定义书签。
1、2 自动配料系统ﻩ错误!未定义书签。
1、2、1电子皮带秤................................................................... 错误!未定义书签。
1、2、2可编程控制器(PLC)ﻩ错误!未定义书签。
1、2、3 变频器ﻩ错误!未定义书签。
1、3 本课题主要研究内容ﻩ错误!未定义书签。
第二章自动配料系统理论分析及方案确定ﻩ错误!未定义书签。
基于PLC 控制的自动配料系统的研究

基于PLC 控制的自动配料系统的研究杨龙兵王有文全强(西华大学应用技术学院,四川成都)此项目受西华大学“西华杯”大学生科技创新项目(2015090)资助。
摘要:针对配料系统提出的快速性和准确性等要求,以PLC 为主控制器,通过485 总线实现PLC 与组态软件的通信,设计了基于S7-200 系列的PLC 自动配料配料系统。
此系统介绍了PLC 和上位机触摸屏之间的通信参数设定及系统控制流程。
经过多次试验,此PLC 控制系统具有运行稳定可靠、较高的控制精度、抗电磁干扰能力强等优点。
关键词: PLC; 配料; 自动控制在现实生活中,不论在食品加工业还是在工程制造业都涉及到配料环节,其经济、技术指标对于整个工程的质量和成本有着举足轻重的关系。
实际工程中,以单片机控制的系统故障率很高,精度不高,误差大,严重的制约了产品的质量,以致制约整个公司的工程质量。
所以设计高速、高效、精确、性能稳定的和智能化的配料系统势在必行。
本文采用性能稳定的 PLC、高精度称重仪表设计自动配料控制系统,该系统可以实现从配料计量,到出料生产全过程的自动化、智能化。
一、系统自动配料控制方案图1为系统配料控制图图 1为系统配料控制图,此系统采用主从式结构。
以工控机为上位主机,以西门子PLC、变频器和称重仪表为下位从机。
主机处于主导地位,实现对各从机的通信管理和控制,将工控机的RS-232异步通信口经电平转换后与PLC相连,形成上、下位机通信的一个物理通道;将主机的另一个RS-232口和称重仪表的通信口相连,构成第二个物理通道。
上位机采用轮询方式,逐个与从站通信。
上位机把任务规划的结果传送给PLC,在PLC进行控制的过程中,上位机使用上位机连接命令监视下位机的运行状态和数据区内容,实时读取PLC的内部状态以及称重仪表的实时数据,在上位机上显示。
二、硬件设计整个全自动配料混合系统由工控机、PLC、工业称重仪表、变频器、振动电机、混料机、传感器、传送带等部分组成。
基于PLC智能化在烧结配料系统中的设计与应用

基于PLC智能化在烧结配料系统中的设计与应用董磊波(河钢唐钢信息自动化部 河北唐山 063000)摘 要 烧结矿化学成分的稳定性对高炉操作有着密切的关系,烧结矿成分波动,就会导致高炉炉温波动,使炉况失常引起生铁成分不合格。
因此配料系统中配混比例的精准,适宜的混合料含水量,是优质烧结矿的前提。
本文通过研究重量配料计算方法的逻辑控制、分析混合料自动加水系统的控制方案,来提高烧结矿的品质。
因此合理的PLC逻辑控制,能大大减少烧结矿成分的波动,在稳定混合料含水量方面起到了积极的作用,在烧结矿产量、质量等指标中起到了关键的促进作用。
关键词 配料 自动加水 水分 料流跟踪 PID中图法分类号 TG155.4 文献标识码 BDoi:10 3969/j issn 1001-1269 2022 Z2 0191 前言某360m2烧结自动化控制系统采用施耐德M580系列PLC进行集中远程控制。
系统包括燃破自动控制系统;配料自动控制系统;烧结自动控制系统;主抽自动控制系统。
工业编程软件采用施耐德UnityProXL13.1,上位机画面操作软件采用IFix5.9。
PLC与上位机(ES站)采用以太网进行数据通讯,通讯速率100mps。
采用施耐德EIO网络实现PLC与各个远程站之间的数据通讯。
2 配料自动控制系统烧结矿是高炉炼铁的前提,烧结矿的品质决定着高炉炼铁的一项重要指标。
烧结就是将各种含铁的粉状原料,按照计算配比配入一定数量的燃料和熔剂,通过混合机和制粒机混合制粒后均匀布料到烧结机台车上在燃料燃烧产生高温和一系列物理化学反应的作用下,混合料中部分易熔物质发生软化、熔化,产生一定数量的液相,液相物质润湿其他未熔化的矿石颗粒;随着温度的降低,液相物质将矿粉颗粒粘结成块,这个过程称为烧结,所得的块矿叫烧结矿。
烧结矿物理性能不好将使高炉炉料的透气性变差,焦比升高,产量下降。
2.1 配料室的构成以及配料计算方法烧结配料室一般有17个矿仓分别为:混匀矿仓6个,燃料仓3个,生石灰、高炉返矿、烧结返矿仓各2个,轻烧白云石、除尘灰仓各1个。
基于PLC控制的自动配料系统

基于PLC控制的自动配料系统
Abstract
With the development of electric power and electronic technology and control technology,AC frequency conversion velocity modulation technology is widely used in the
equipment contr01.Configuration software technology is one software platform tool that with CUStOm·made function,friendly human—machine windows,which can be developed on the PC machine,used the PLC to intelligently control the automatic eqmpment.
生亟盗 作者签名: 猛垫圣 导师签名:
邕!』年』月旦日
大连理工大学硕士学位论文
1.引 言
1.1概论
配料是精细化工厂生产工艺过程中的一道非常重要的工序,配料工序质量对整个 产品的质量举足轻重,落后的配料系统不仅效率低而且配料不准,手工操作又将人为因 素引入配料环节,使工艺配方难以在生产中实现,严重影响产品质量的稳定及进一步提 高,因此实现高精度自动配料对工业企业生产有极为重要的意义。
we confirm the realization programme of the system and choose Siemens S7—300 Plc product.
Combining features of the product and its preparation software programming to achieve automatic contr01.The system also elaborates the Mitsubishi FR—A540 transducer application. the structure of the system,its hardware configuration and the application of software
基于PLC控制的自动配料系统的研究与应用

基于PLC控制的自动配料系统的研究与应用1. 绪论a. 研究背景和意义b. 国内外研究现状和发展动态c. 研究目的和意义2. PLC控制系统的原理和结构a. PLC定义和功能b. PLC控制系统的结构和作用c. PLC控制系统的应用领域3. 自动配料系统的设计和实现a. 自动配料系统的概念和优势b. 自动配料系统的设计要点和目标c. 自动配料系统的实现流程和方法4. PLC控制自动配料系统的实验分析a. 实验设置和参数调整b. 实验结果分析和数据统计c. 实验总结和结论5. 自动配料系统的应用和展望a. 自动配料系统的市场前景和发展趋势b. 自动配料系统的应用领域和发展方向c. 自动配料系统的未来发展趋势和展望1. 绪论近年来,随着工业自动化程度的不断提高,自动化设备在各个行业的生产过程中的应用越来越广泛。
其中,PLC控制技术已成为工业自动化的核心技术之一,具有很高的可靠性、高效率、灵活性和易维护等优点。
在自动化生产中,自动配料系统是广泛应用的一种PLC控制系统,它主要是用于对不同物料进行配比和调整,并通过PLC程序控制实现自动化运作,从而提高生产效率、保障产品质量、降低生产成本,具有很高的技术和经济价值。
本文旨在研究PLC控制的自动配料系统的原理、性能和应用,分析探讨其在工业自动化中的优势和应用。
首先,本章将介绍研究背景和意义,包括自动化技术应用的趋势和需要,以及PLC控制技术在自动化生产中的应用优势。
其次,本章将综述国内外研究现状和发展动态,展示PLC控制的自动配料系统的研究和应用现状和未来发展方向。
最后,本章将概述本文的研究内容和意义,阐明本研究的目的和意义,为后续章节的内容铺垫。
1.1 研究背景和意义随着科技的发展和工业生产的逐步改善,自动化设备在工业生产过程中得到了广泛应用。
自动化生产的核心技术是PLC控制技术,它是一种基于数字计算机技术的控制系统,具有很高的可靠性、灵活性和稳定性,能够实现自动化生产环节的监控和控制。
基于PLC的自动配料控制系统设计
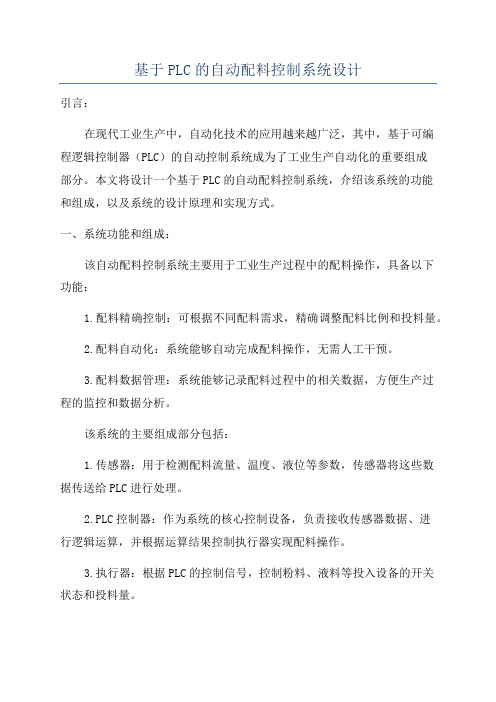
基于PLC的自动配料控制系统设计引言:在现代工业生产中,自动化技术的应用越来越广泛,其中,基于可编程逻辑控制器(PLC)的自动控制系统成为了工业生产自动化的重要组成部分。
本文将设计一个基于PLC的自动配料控制系统,介绍该系统的功能和组成,以及系统的设计原理和实现方式。
一、系统功能和组成:该自动配料控制系统主要用于工业生产过程中的配料操作,具备以下功能:1.配料精确控制:可根据不同配料需求,精确调整配料比例和投料量。
2.配料自动化:系统能够自动完成配料操作,无需人工干预。
3.配料数据管理:系统能够记录配料过程中的相关数据,方便生产过程的监控和数据分析。
该系统的主要组成部分包括:1.传感器:用于检测配料流量、温度、液位等参数,传感器将这些数据传送给PLC进行处理。
2.PLC控制器:作为系统的核心控制设备,负责接收传感器数据、进行逻辑运算,并根据运算结果控制执行器实现配料操作。
3.执行器:根据PLC的控制信号,控制粉料、液料等投入设备的开关状态和投料量。
4.人机界面:提供一个友好的操作界面,供操作员输入配料参数、查看配料数据等。
二、系统设计原理和实现方式:1.传感器的应用:通过给配料过程中的关键参数(如流量、温度、液位)配置相应的传感器,将实时的数据通过模拟量或数字量输入模块传送给PLC进行处理。
2. PLC的控制:PLC使用逻辑运算单元(Ladder Diagram)进行逻辑控制。
根据传感器数据和预设的配料参数,PLC能够判断哪些配料需要进行投料,调整投料设备的开关状态和投料量。
3.执行器的控制:PLC将控制信号发送给执行器,执行器根据信号的状态进行相应的操作,控制粉料、液料等的投入设备。
4.人机界面的设计:采用触摸屏、按钮等电子元件实现人机交互,提供一个用户友好的操作界面,操作员可以输入配料参数、查看配料数据等。
三、系统优势和应用前景:1.提高生产效率:系统能够自动完成配料操作,减少人工操作的时间和精力投入。
基于PLC控制的自动配料系统的应用

基于PLC控制的自动配料系统的应用
0.引言
自动配料系统是精细化工厂生产工艺过程中一道非常重要的工序,配料工序质量对整个产品的质量举足轻重。
自动配料控制过程是一个多输入、多输出系统,各条配料输送生产线严格地协调控制,对料位、流量及时准确地进行监测和调节。
系统由可编程控制器与电子皮带秤组成一个两级计算机控制网络,通过现场总线连接现场仪器仪表、控制计算机、PLC、变频器等智能程度较高、处理速度快的设备。
在自动配料生产工艺过程中,将主料与辅料按一定比例配合,由电子皮带秤完成对皮带输送机输送的物料进行计量。
PLC 主要承担对输送设备、秤量过程进行实时控制,并完成对系统故障检测、显示及报警,同时向变频器输出信号调节皮带机转速的作用。
1.自动配料系统的构成
该自动配料系统由5 台电子皮带秤配料线组成,编号分别为1#、2#、3# 、4#、5#、,其中1#~4#为一组,1#为主料秤,其余三台为辅料秤。
当不需要添加辅料时,5#电子秤单独工作输送主料。
系统具有恒流量和配比控制两种功能。
对于恒流量控制时,电子皮带秤根据皮带上物料的多少自动调节皮带速度,以达到所设定流量要求。
以主秤(1#)系统工艺流程来分析,工艺流程如图1 所示。
自动配料系统加电后,皮带驱动电机开始旋转,微处理机根据当前操作控制电机转速。
料斗中的物料落在落料区,经皮带运送到达称重区,由电子皮带秤对皮带上的物料进行称重。
称重传感器根据所受力的大小输出一个电压信号,经变送器放大,输出一个正比于物料重量的计量电平信号。
该信号送至上位机的接口,经采样后并转换成一个流量信号,在上位机上显示当前流量值。
基于PLC的自动配料控制系统设计
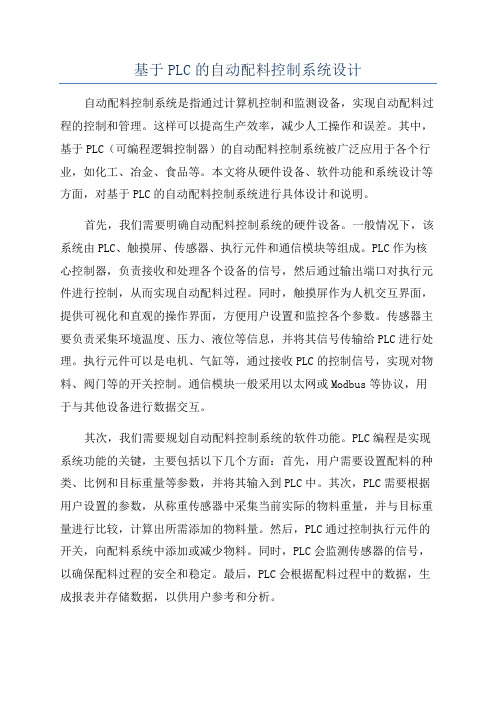
基于PLC的自动配料控制系统设计自动配料控制系统是指通过计算机控制和监测设备,实现自动配料过程的控制和管理。
这样可以提高生产效率,减少人工操作和误差。
其中,基于PLC(可编程逻辑控制器)的自动配料控制系统被广泛应用于各个行业,如化工、冶金、食品等。
本文将从硬件设备、软件功能和系统设计等方面,对基于PLC的自动配料控制系统进行具体设计和说明。
首先,我们需要明确自动配料控制系统的硬件设备。
一般情况下,该系统由PLC、触摸屏、传感器、执行元件和通信模块等组成。
PLC作为核心控制器,负责接收和处理各个设备的信号,然后通过输出端口对执行元件进行控制,从而实现自动配料过程。
同时,触摸屏作为人机交互界面,提供可视化和直观的操作界面,方便用户设置和监控各个参数。
传感器主要负责采集环境温度、压力、液位等信息,并将其信号传输给PLC进行处理。
执行元件可以是电机、气缸等,通过接收PLC的控制信号,实现对物料、阀门等的开关控制。
通信模块一般采用以太网或Modbus等协议,用于与其他设备进行数据交互。
其次,我们需要规划自动配料控制系统的软件功能。
PLC编程是实现系统功能的关键,主要包括以下几个方面:首先,用户需要设置配料的种类、比例和目标重量等参数,并将其输入到PLC中。
其次,PLC需要根据用户设置的参数,从称重传感器中采集当前实际的物料重量,并与目标重量进行比较,计算出所需添加的物料量。
然后,PLC通过控制执行元件的开关,向配料系统中添加或减少物料。
同时,PLC会监测传感器的信号,以确保配料过程的安全和稳定。
最后,PLC会根据配料过程中的数据,生成报表并存储数据,以供用户参考和分析。
最后,我们需要进行系统的整体设计。
首先,根据具体需求,选择合适的PLC型号和配置。
其次,根据工艺流程和设备布局,设计配料系统的结构和连接方式。
确定传感器的类型和位置,以满足读取环境信息的需求。
然后,编写PLC程序和触摸屏界面,实现用户设置和参数输入的功能。
自动配料控制实验报告

自动配料控制实验报告自动配料控制实验报告一、引言自动配料控制是一种应用于工业生产中的重要技术,它能够准确地控制原料的配比,提高生产效率和产品质量。
本实验旨在通过设计一个自动配料控制系统,并进行实际操作,来验证其在工业应用中的可行性和效果。
二、实验设计与装置本实验采用了PLC(可编程逻辑控制器)作为控制核心,配合传感器、执行器等设备,构建了一个简单的自动配料控制系统。
该系统包括了原料仓、输送带、称重装置、PLC控制器和人机界面。
三、实验步骤1. 设定配料比例:根据实际需求,设定不同原料的配料比例,并将其输入到PLC控制器中。
2. 启动系统:通过人机界面操作,启动自动配料控制系统。
3. 检测原料仓状态:传感器检测原料仓的状态,如是否有足够的原料,是否需要补充。
4. 原料输送:根据配料比例和实际需求,PLC控制器指导输送带将相应的原料输送到称重装置上。
5. 称重与控制:称重装置对输送过来的原料进行称重,并将数据传送给PLC控制器。
PLC根据设定的配料比例和实际称重数据,控制执行器的开关,调整原料的配比。
6. 反馈与调整:PLC控制器根据执行器的反馈信号,对配料过程进行实时调整,以保证配料的准确性和稳定性。
7. 停止系统:完成配料后,通过人机界面操作,停止自动配料控制系统。
四、实验结果与分析通过多次实验,我们得到了一系列的实验数据,并进行了统计和分析。
结果表明,自动配料控制系统能够准确地控制原料的配比,实现了预期的效果。
在不同的配料比例下,系统的响应速度和稳定性都得到了有效的保证。
五、实验总结与展望本实验成功地验证了自动配料控制系统在工业生产中的可行性和效果。
然而,我们也发现了一些问题和改进的空间。
例如,系统在处理大批量配料时的效率还有待提高,同时,对于一些特殊原料的配料控制,还需要更加精细的调整和优化。
未来,我们可以进一步研究和改进自动配料控制系统,以适应更多工业生产场景的需求。
例如,可以引入更先进的传感器技术,提高系统对原料状态的检测精度;可以优化控制算法,提高系统的响应速度和稳定性;可以加强系统的可视化界面,方便操作和监控等。
基于PLC的自动配料系统设计

基于PLC的自动配料系统设计近年来,随着制造业的快速发展和自动化技术的不断成熟,基于PLC的自动配料系统在工业生产中扮演着越来越重要的角色。
自动配料系统的设计能够提高生产效率、降低人工成本,同时还能提升产品质量和生产过程的稳定性。
本文将对进行深入探讨,分析其原理、优势和应用,旨在为相关领域的研究和实践提供参考。
首先,我们需要了解什么是PLC(Programmable Logic Controller,可编程逻辑控制器)。
PLC是一种专门用于工业控制领域的数字计算机,它可以根据预先设定的程序来控制生产设备的运行。
PLC系统通常由输入模块、输出模块、处理器和通信模块组成,能够实现对自动化生产过程的精准控制。
因此,基于PLC的自动配料系统设计是在这样一种控制器的基础上实现的,其核心在于通过编写程序来实现对配料设备的控制和管理。
在实际的自动配料系统设计中,首先需要考虑的是配料的准确性和稳定性。
由于配料的准确性直接影响最终产品的质量,因此在设计系统时需要选择合适的传感器来实时监测物料的流量、温度和压力等参数,以确保配料的准确性。
同时,为了提高系统的稳定性,还需要考虑到设备的安全性和故障恢复能力,避免因设备故障导致生产中断和产品质量问题。
基于PLC的自动配料系统设计可以通过编写逻辑控制程序来实现对配料设备的自动化控制和监测,提高配料的准确性和稳定性。
另外,基于PLC的自动配料系统设计还可以实现生产过程的自动化管理和优化。
通过在PLC系统中编写智能化的控制程序,可以实现对生产过程中各个环节的实时监测和调整,提高生产效率和节约人力成本。
此外,基于PLC的自动配料系统设计还可以实现生产过程的数据采集和分析,为生产决策提供支持。
通过对生产数据的分析,可以及时发现生产过程中的问题和瓶颈,为生产优化提供参考。
基于PLC的自动配料系统设计的优势还包括系统的可扩展性和灵活性。
由于PLC系统采用模块化设计,可以根据生产需要灵活地修改和扩展系统的功能和容量,适应不同生产规模和工艺要求。
基于PLC控制的自动配料系统的研究与应用
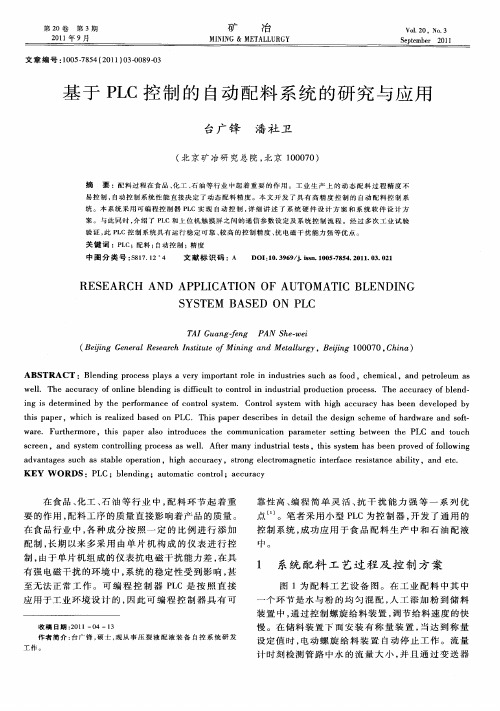
( 京矿 冶研 究总 院 , 京 10 7 ) 北 北 0 0 0
摘 要 :配料过程 在食 品 、 化工 、 石油等行业 中起着重 要的作用 。工业生 产上 的动态配料 过程精 度不
易控 制 , 自动 控 制 系 统 性 能 直 接 决 定 了动 态 配 料 精 度 。 本 文 开 发 了 具 有 高精 度 控 制 的 自动 配 料 控 制 系 统 。本 系 统 采 用 可 编 程 控 制 器 P C实 现 自动 控 制 , 细 讲 述 了 系 统 硬 件 设 计 方 案 和 系 统 软 件 设 计 方 L 详 案 。 与 此 同 时 , 绍 了 P C和 上 位机 触 摸 屏 之 间 的 通 信 参 数 设 定 及 系 统 控 制 流 程 。经 过 多 次 工 业 试 验 介 L 验 证 , P C控 制 系统 具 有 运 行 稳定 可 靠 、 高 的 控 制 精 度 、 电磁 干 扰 能 力 强 等优 点 。 此 L 较 抗
S TEM YS BAS ED 0N C PL
T IG a gf n P h — i A un - g e AN S ewe
( eig Gnrl eer ntue fMii n tl ry B in 0 0 0, hn ) B in eea s c Is tt o nn a dMe l g , eig1 0 7 C ia j R a h i g au j
关键 词 :P C;配料 ; L 自动控制 ; 度 精
中 图 分 类 号 :8 7 1 4 ¥1.2
文献标 识码 : A
D I1 .9 9 ji n 10 - 5 . 0 1 0 .2 O :03 6 /. s. 0 57 4 2 1 .3 0 1 s 8
基于PLC的自动配料控制系统的研究

基于PLC的自动配料控制系统的研究随着工业自动化的快速发展,PLC(可编程逻辑控制器)在自动化控制领域的应用越来越广泛。
其中,基于PLC的自动配料控制系统成为了不可忽视的研究方向。
本文将从系统的基本原理、系统的优势以及未来发展方向等方面对基于PLC的自动配料控制系统进行研究。
基于PLC的自动配料控制系统的基本原理是通过PLC对物料的输送、称量、混合等过程进行控制。
系统一般包括物料输送装置、称量装置、混合装置以及PLC控制系统等组成部分。
物料输送装置负责将需要配料的物料输送到称量装置,称量装置通过传感器对物料进行精确称量,然后将称量的物料送到混合装置进行混合。
PLC控制系统根据预设的配方,通过对各个装置的控制,实现对配料过程的自动控制。
基于PLC的自动配料控制系统相较于传统的手动控制方式具有多方面的优势。
首先,系统大大提高了生产效率。
自动化控制系统可以实现物料的连续输送、精确称量和高效混合,大大减少了人力投入和生产时间。
其次,系统提高了产品质量的稳定性。
自动化控制可以减少人为因素对配料过程的影响,保证了每次配料的准确性和一致性。
此外,系统具有可编程的特点,可以实现不同配料要求下的灵活调整,提高了生产的适应性。
最后,系统的可靠性和安全性也得到了增强。
PLC控制系统具有自我诊断和故障保护功能,当发生异常情况时能及时进行报警和停机保护,保证了设备和人员的安全。
基于PLC的自动配料控制系统还有许多待发展的方向。
首先,可以进一步提高系统的可扩展性和智能化水平。
通过加入更多的传感器和设备,实现对配料过程更全面的监测和控制,使系统变得更智能化。
其次,可以进一步优化系统的人机界面。
提供更直观、友好的操作界面,使系统的使用更加方便和易于操作。
同时,可以将系统与远程监控和管理系统进行整合,实现对生产过程的远程监控和智能管理。
另外,基于PLC的自动配料控制系统还可以与其他工业自动化技术相结合,如无人机技术、物联网等,实现生产线的智能化和自动化。
基于PLC、称重模块、触摸屏的工业配料自动控制.

摘要自动配料系统是一个针对各种不同类型的物料(固体或液体)进行输送、配比、加热、混合以及成品包装等全生产过程的自动化生产线。
广泛应用于化工、冶金、建材、食品、饲料加工等行业。
本文介绍了一种基于西门子PLC和新型称重配料控制器ID551的技术特性。
根据西门子s7-200 PLC和称重仪表作为控制器,以完成控制过程。
液体灌装配料系统主要由s7-200 PLC,称重仪表,HMI和四通道灌装设备构成。
通过对称重仪表清零和标定等参数的设置,来完成相应的设置质量的精确称重。
设置校准标定值为1Kg, 允许误差范围在10 g以内。
系统采用慢喂阀和快喂阀两种方式添加原料,是为了达到高速、准确的目的。
在设计本系统过程中考虑了可能影响系统误差诸多因素,如液体在空中停留的时间即空中飞料时间、影响水流速快慢的压力大小即蓄水池液位等。
为了进一步减小误差,我们可以通过设置空中飞料时间来调整,设置空中飞料时间为1s。
当称重结束时,完成称重,开始放料。
当称重仪表称的桶中液体质量为零时,此时放料结束,完成一次原料称重。
整个过程可以通过触摸屏设置并观测。
把水、水泥、砂、碎石,分别在四个通道称重,当且仅当四个通道放料阀都处于复位状态时,搅拌电机开始工作,原料进行搅拌,完成一个工业配料的实际应用——混凝土搅拌自动控制系统。
基于PLC、称重仪表、触摸屏的工业配料自动控制,可在材料精确、快速称重的生产行业进行应用。
关键词:PLC;称重仪表;人机界面;工业配料。
Title:Based on PLC and weighing instrument, touch screen, industrial automatic controlAbstractAutomatic batching system is one for all the different types of materials (Solid or liquid)In transmission、Matching、heating、mingle and so on. Then form the whole production process automation production line. Be widely used in chemical industry, metallurgy industry, building materials industry, food industry, feed processing industry etc. To introduce this system, the article takes a method to solve it. Liquid filling batching system is mainly composed of S7-200 PLC, weighing instrument, HMI and liquid filling equipment of four channels. Through to the weighing instrument reset Settings, Setting the calibration value set etc. To complete the corresponding setting quality and accurately of weighing, then setting calibrating the calibration value to 1 kg, allowed error range of 10 g. Set the air time to 1s. When the dosing and at the beginning of the start switch, then give S7-200 PLC a rising edge. In the design of this system in the process of considering many factors may affect the system error, calculating the air time. And the pressure of the reservoir water level size affect water pipe water injection flow rate, etc. In order to further decrease the error, we can set up through the air to fly time value to adjust it. When four of discharging valve are reset, mixer began to stir, then complete an industrial weighing ingredients. And industrial ingredients, weighing module, touch screen based on PLC automatic control system design, available in high precision material accurate formula of raw material and production industry.Keywords: Programmable Logic Controller; Weighing instrument; Human Machine Interface ;Industrial ingredients.目录第一章绪论 (1)1.1课题的提出 (1)1.1.1 工业配料自动控制系统设计的提出 (1)1.1.2 课题设计的目的和意义 (1)1.2工业配料技术的前景 (2)1.3课题设计的主要内容 (2)1.3.1 系统实现原理 (2)1.3.2 硬件电路的实现 (2)1.3.3 软件程序的编制 (3)1.3.4 误差分析 (3)1.4课题设计的基本要和技术参数 (3)1.4.1 课题设计的基本要求 (3)1.4.2 系统的主要技术参数 (3)第二章系统设计实现方案与原理 (4)2.1引言 (4)2.2系统的设计方案及PLC选型 (4)2.2.1 设计方案论证 (4)2.2.2 PLC选型方案论证 (6)2.2.3 S7-200 PLC的特征 (9)2.2.4 S7-200的主要组成部件 (9)2.2.5原理分析 (10)2.3本章小结 (11)第三章自动配料系统硬件设计 (12)3.1引言 (12)3.2自动配料系统简介 (12)3.2.1 自动配料系统的特点 (12)3.2.2 自动配料系统组成 (12)3.3自动配料系统的设计 (13)3.3.1 配料系统 (13)3.3.2 配料系统的组成 (14)3.4称重仪表的选择及参数的设定 (15)3.4.1 称重仪表的介绍 (15)3.4.2 键盘菜单 (16)3.4.3 预置点应用 (20)3.5系统硬件连接 (20)3.5.1 系统硬件连接总体框图 (20)3.5.2 称重仪表端口设置 (21)3.5.3 输入/输出接线 (22)3.5.4 S7-200接线图 (22)3.6称重传感器 (23)3.6.1 称重传感器特点 (23)3.6.2 称重传感器原理 (23)3.6.3 称重传感器接线 (23)第四章软件设计 (26)4.1引言 (26)4.2顺序控制法 (26)4.2.1 顺序控制 (26)4.2.2 顺控系统的结构 (26)4.2.3 顺控功能图的结构 (28)4.3监控组态软件WINCC简介和应用 (31)4.3.1 WINCC简介 (31)4.3.2 WINCC的特点 (31)4.3.3 WINCC的组态 (33)4.3.4 操作界面设置 (33)4.3.5 操作站的选配 (35)4.4软件流程图 (35)4.4.1 主程序流程图 (35)4.4.2 整体软件流程图 (36)4.5PLC控制梯形图 (37)4.5.1 单桶配料梯形图 (37)4.6误差分析 (39)第五章全文总结 (40)致谢 (41)参考文献 (42)第一章绪论1.1课题的提出1.1.1 工业配料自动控制系统设计的提出在带有自动化配料系统的工业生产中,配料工序是工业生产过程中非常重的环节,在混凝土制作过程中的纤维水泥浆由水、水泥、砂、碎石,等四种物料接一定比倒进行配制的,其配料精度直接影响着混凝土。
PLC实验报告:实验八自动配料控制实验

实验名称自动配料控制实验指导老师______________ 成绩__________专业机自班级1203 _________ 姓名 ____ 学号_____________一、实验目的:1、掌握综合系统的应用2、了解整个控制系统的设计过程。
二、功能要求:系统启动后,配料装置能自动识别货车到位情况及对货车进行自动配料,当车装满时,配料系统能自动关闭。
(1)初始状态系统启动后,红灯L2灭,绿灯L1亮,表明允许汽车开进装料。
料斗出料口D2关闭,若料位传感器S1置为OFF(料斗中的物料不满),进料阀开启进料(D4亮)。
当S1置为ON(料斗中的物料已满),则停止进料(D4灭)。
电动机Ml M2 M3和M4均为OFF。
(2)装车控制装车过程中,当汽车开进装车位置时,限位开关SQ1置为ON红灯信号灯L2亮,绿灯L1灭; 同时启动电机M4经过1S后,再启动启动M3再经2S后启动M2再经过1S最后启动M1,再经过1S后才打开出料阀(D2亮),物料经料斗出料。
当车装满时,限位开关SQ2为ON料斗关闭,1S后M1停止,M2在M1停止1S后停止,M3在M2停止1S 后停止,M4在M3停止1S后最后停止。
同时红灯L2灭,绿灯L1亮,表明汽车可以开走。
(3)停机控制按下停止按钮SB2,自动配料装车的整个系统终止运行。
三、实验连线图:CPU224模块四、输入/输出地址分配及功能说明1主程序得吕I I也址1io n?偉止祜妞ini10. □SQ1闻上10 5G带4lu.tT10.7&Sc11 0311 11D口口111□电机on 2血机QO 313Dcajn,Q0 +1 4L)1QO 口DZ QD5it.D3Q0.&1 7ID 4QO.71 & 1 1口 1 n19L2Q1 120他机洁已M0.121M0i2J2L屯机信骂waa23L)田.机信寻M0.1曲小信号MD.5MD J S?h口详号MQ727W信号Ml □L1信号Ml 129L堆号M1.230白封]洁吕M1 .GJI关1丹f£号Ml .3偌1KIH行肓罚M1L433M1匸Ti '初躺化MO.O35笛4R皓母1MZQ3E匕电机信号1M21137M2.2拥L电机信号1MZ3%D萌申MZ42传送带启动子程序1 符吕]釧.闿当型1 CM I IN BOOLLW0殳里1】IN WORDININ^OLITOUTL2JJ黄里1UU 1BUDLIL2 1□UT BOOLL2.2变蛋3OUT DODLL?3靈卑4OUT BOOLL24□UT BOOLL2<5賁更E TEMP BOOLL2.6复里F TEMP HUOLLA75<SQ TCM"COOLL3f芟軍9TEMP FOOLL3.1HSW TEMP BOOL3传送带关闭子程序五、实验程序询飞冊讯叩、塢初拘关闭住号Ml 31-i51^o-.詞:信号“恬WltMaj51 IC.3 D能W M0.7 —I I——()DO骨^ Mn 7 D希w ■104 D艮机CD4 Lift & M1 T SQ7KX5 信号;MMT I ----- ( O1SQ>IQ'5 □llS^:M0 6-H - I——(H)I曲X 诂Mi? ■:Ml 5 零虫11 卑.更I Sts?召■护 专圭£ _____ 空理P 匚荐号W2 4 •:电7-l.|s^T1HZ3 -期R 倚号1*12? -旳机的1血1•确.机信吕皿航SMU.OLZU15—I ”卜MJ.n DU■Efc^t.:QOEJ 电机贡(1*H * I —I —I ‘ I —feints ■:Ml. = ?T0fr^:MO.OJ •—r^:〉 醴豹MT 肌s —'Oco-^□V_WEMENO□u 「-vwoE 审机:DJZ< $〕 时:com < $ )D2OQ5传住需信’畦机[s^- M2 - 強朴GI11T I —I ——逮机佶雪M2J:)电 tJLlq®:v23 P^fcla?4―II ------- f H 、n? innD4Q(7{)2传送带启动子程序^^11L^U咗鱼 2L21-1 :1—i~C :]DO2)丁诒号NR5DI QC.O〔)D3言 E :MClTL'Sqt.GL1皆号WilL UI..:)1_2直号.阿2L2Q11<S _________________ u iruM[ -----EI IQO JMT37 t^.S 1 -2 2——1 1——<* R \T>)建机甘£742.1 E 电HQ12—r i —心!.^0 J SMD J迪收里机10-IN ION. rr 1 oo huT:- ____ i L l£ft«L23r i. >k H JtRB l:L20〕傾卑ULWJ T十153■.IONT-FT100 rrj4K£':L20=憧毘4:L21*^S3>LZ^3传送带关闭子程序IM TON FT100 mi■ IT* I L丸口这次实验中,包括了这学期以来学习的信号互锁、传送、定时器、计数器、有记忆输出、子程序的相关知识,让我深深了解到了自己的不足,pic不是一门简单的课,需要勤思考多动手。
- 1、下载文档前请自行甄别文档内容的完整性,平台不提供额外的编辑、内容补充、找答案等附加服务。
- 2、"仅部分预览"的文档,不可在线预览部分如存在完整性等问题,可反馈申请退款(可完整预览的文档不适用该条件!)。
- 3、如文档侵犯您的权益,请联系客服反馈,我们会尽快为您处理(人工客服工作时间:9:00-18:30)。
基于PLC控制的自动配料系统的研究与应用一、绪论1.1 研究背景和意义1.2 相关研究现状及发展趋势1.3 研究目的和内容二、PLC控制的自动配料系统原理2.1 PLC控制系统基础知识2.2 自动配料系统分析2.3 PLC控制系统工作原理及流程三、PLC控制的自动配料系统设计3.1 系统设计概述3.2 配置工具与设备选择3.3 数据采集和监控设计3.4 硬件设计3.5 软件程序设计四、系统验证与性能测试4.1 系统测试环境和方法4.2 测试结果分析4.3 系统性能评估与优化五、PLC控制的自动配料系统应用和前景5.1 系统应用案例介绍5.2 系统应用效果评估5.3 系统未来发展趋势六、结论6.1 研究成果总结6.2 存在问题和改进措施6.3 研究展望和意义 elucidate.一、绪论1.1 研究背景和意义随着人工智能和自动化技术的快速发展,PLC(可编程逻辑控制器)在工业自动化控制领域中的应用越来越广泛。
在生产加工过程中,配料是不可或缺的一个环节,传统的人工配料方式已经不能满足现代工业化生产的需求,最佳方式是实施自动配料系统。
PLC控制的自动配料系统可以使生产过程更加高效、准确、节约能源。
PLC是一种可编程控制器,具有高度的可编程性和灵活性。
PLC控制的自动配料系统采用传感器实时采集物料配比情况,通过PLC实时控制阀门的开关,实现自动的配料过程。
相比人工配料,PLC控制的自动配料系统具有较高的精度和效率。
1.2 相关研究现状及发展趋势自动化生产已成为智能制造的重要组成部分,PLC控制的自动配料系统也因其高效、准确、可靠等特点,广泛应用于化工、医药、食品、工业制造等领域。
自动配料系统的研究在过去几十年内得到了很大的发展,但还存在一些问题需要进一步研究。
目前,国内外很多学者和工程师致力于研究和开发PLC控制的自动配料系统。
国外现有的自动配料控制系统包括基于PLC的控制系统和SCADA(监控、控制与数据采集)系统。
国内的研究基本上还是停留在基于单片机控制的小型自动配料系统,对于大型工厂的生产线还没有完善的解决方案。
1.3 研究目的和内容本文旨在研究和设计一种基于PLC控制的自动配料系统,以提高生产效率、降低人力成本和能源浪费。
本文将重点研究以下几个内容:(1)PLC控制技术及其在自动配料系统中的应用;(2)自动配料系统的硬件设计,包括选型、配接等;(3)自动配料系统的软件程序设计及应用;(4)自动配料系统的性能测试和验证;(5)自动配料系统的应用和前景。
通过本文的研究,可为工业生产配料自动化的控制提供一些有益的参考,以及为制造行业提供有力的支撑。
二、PLC控制技术在自动配料系统中的应用2.1 PLC控制系统的组成PLC是一种数字电子设备,它可以通过编程来控制不同的运动或模拟过程。
PLC控制系统由输入模块、中央处理器、输出模块和供电单元组成。
控制系统通过输入模块从外部读取信号,并将其送到中央处理器进行处理。
处理器将计算结果发送到输出模块,从而控制输出设备的运行状态。
控制系统的供电单元则负责为控制系统提供电源。
2.2 PLC控制技术在配料系统中的实现PLC控制技术在自动配料系统中的主要作用是控制阀门的开闭以及配料系统的实时监测。
通过PLC控制系统中的输入模块,配料系统可以实时监测物料的配比情况,根据配比情况来控制阀门的开闭。
同时,PLC控制系统能够将采集得到的数据以数字化的方式进行处理,并将结果传递给中央处理器,以便系统能够自动进行调整和控制。
在配料系统的实现中,PLC控制技术通常是采用有限状态机的方式来实现调用处理程序以控制设备的工作状态,从而提高运行效率。
PLC控制系统中的中央处理器可以根据不同的输入条件,选择合适的状态进行切换,以实现不同的功能。
2.3 需要考虑的因素在应用PLC控制技术进行自动配料系统时需要考虑的因素包括硬件设计、程序设计、人工干预、数据记录等。
主要包括以下几个方面:(1)硬件设计:硬件设计需要根据生产线的规模、生产过程的特点以及工艺要求来确定PLC的型号和IO数量。
同时还需要根据需要加装配重设备、传感器等,以确保系统可以及时准确地监测配料系统的工作状况。
(2)程序设计:PLC程序需要根据实际生产需求进行设计和调试,程序运行时需要考虑精度控制、防止误操作等问题。
此外,还需要考虑PLC系统的稳定性和可靠性,以确保系统运行正常、数据记录及时、准确。
(3)人工干预:自动配料系统应该具备一定的人工干预功能,以提高生产过程的灵活性和适应性。
PLC控制系统的操作界面需要易于操作,并以警报方式提示操作员异常情况,为操作员提供便利的信息管理工具。
(4)数据记录:自动配料系统产生的数据需要记录,以便于追溯和调试系统的问题。
记录数据的方式包括交互式显示、数据存储和数据传输。
同时还需要将记录的数据转换为易于理解的格式,以便于制定生产计划、检测过程中出现的问题和改进系统的性能。
2.4 综合应用综合应用PLC控制技术与传感器技术,可以实现更加高效、准确、可靠的自动配料系统。
自动化控制技术在化工、食品、医药等领域的应用还有很大的发展空间,未来的自动控制系统将会更加智能化、自适应,具有更广泛应用的前景。
三、PLC控制技术在自动包装系统中的应用3.1 自动包装系统的组成自动包装系统由输送带、包装机、PLC控制系统和人机界面组成。
输送带是将产品转移到包装机上的媒介,包装机是进行包装的装置,PLC控制系统是将输送带和包装机协调起来的中心控制系统。
人机界面则是提供人机交互的界面,让操作人员可以控制、调整和监控自动包装系统的运行。
3.2 PLC控制技术在自动包装系统中的应用自动包装系统中的PLC控制系统主要作用是控制输送带和包装机的运行状态、包装材料的供给和监测包装过程的实时状态信息。
PLC控制系统利用输入模块、中央处理器、输出模块和供电单元构成。
输入模块从传感器获取数据,中央处理器处理数据并根据编程策略控制输出模块完成对包装系统的控制。
在自动包装系统的实现中,PLC控制技术可以帮助系统实现快速、准确、稳定的生产过程。
PLC控制系统中的中央处理器可以根据不同的输入条件,选择合适的状态进行切换,以实现不同的功能。
例如,在输送带上放置了传感器后,PLC控制系统可以实时获取传感器的信息,并根据信息来控制输送带的运行状态,从而控制产品的流动速度和方向。
3.3 需要考虑的因素在应用PLC技术进行自动包装系统时需要考虑的因素包括硬件设计、程序设计、人工干预、数据记录等。
主要包括以下几个方面:(1)硬件设计:硬件设计需要根据生产线的规模、生产过程的特点以及包装要求来确定PLC型号和IO数量,并进行配重设备、传感器等等的安装,以便PLC控制系统能够实时准确地监测系统的运转状态。
(2)程序设计:PLC程序需要根据实际生产需求进行设计和调试,程序在运行时需要考虑到精度控制和防止误操作等问题。
此外,还需要考虑PLC系统的稳定性和可靠性,以确保系统运行正常、数据记录及时、准确。
(3)人工干预:自动包装系统应该具备一定的人工干预功能,以提高生产过程的灵活性和适应性。
PLC控制系统的操作界面需要易于操作,并以警报方式提示操作员异常情况,为操作员提供便利的信息管理工具。
(4)数据记录:自动包装系统产生的数据需要记录,以便于追溯和调试系统的问题。
记录数据的方式包括交互式显示、数据存储和数据传输。
同时还需要将记录的数据转换为易于理解的格式,以便于制定生产计划、检测过程中出现的问题和改进系统的性能。
3.4 综合应用综合应用PLC控制技术与机械视觉技术、人工智能技术,可以实现更加高效、准确、可靠的自动包装系统。
自动包装技术在食品、药品等领域的应用还有很大的发展空间,未来的自动包装系统将会更加智能化、自适应,并具有更广泛应用的前景。
四、PLC控制技术在机床控制系统中的应用4.1 机床控制系统的组成机床控制系统由数控装置、执行器、传感器、输入输出设备和用户界面组成。
数控装置是机床控制的中心,通常采用PLC 控制技术进行控制,执行器是根据PLC输出信号来执行动作的装置,传感器是用来检测执行器动作是否正确以及测量工件尺寸的装置,输入输出设备是与PLC控制器进行命令和数据交互的接口,用户界面是提供人机交互的界面,让操作人员可以对机床进行控制和监测。
4.2 PLC控制技术在机床控制系统中的应用PLC在机床控制系统中的应用主要是控制执行器的动作,使得机床可以按照预定的工艺要求进行自动加工。
PLC控制技术通过输入传感器、执行器信息来进行计算,从而控制机床的运行状态和加工过程。
机床控制系统中的PLC控制器可以根据不同的输入条件,选择合适的状态进行切换,以实现不同的加工要求。
通过PLC控制技术,机床控制系统可以实现工件自动定位、加工路径控制、刀具切削长度控制和切削速度控制等功能。
PLC控制系统具有实时性、高精度和可靠性等优点,可以大幅度提高机床的自动化程度和生产效率。
例如在机床的切削过程中,PLC可以精确控制切削深度和切削速度的大小,以确保机床加工的精度和质量。
4.3 需要考虑的因素在应用PLC技术进行机床控制系统时需要考虑的因素包括技术水平、机床的运行速度、加工精度、工艺要求等。
主要包括以下几个方面:(1)技术水平:机床操作员需要具备一定的PLC控制技术知识和相关的专业培训,以确保其能够熟练地应用PLC控制技术进行机床控制和监测。
(2)机床的运行速度:机床的运行速度对PLC控制技术的响应速度和准确度有着至关重要的影响,需要根据机床的运行速度进行PLC控制系统的硬件和软件设计。
(3)加工精度:机床控制系统需要保证加工精度的一致性和稳定性,因此需要根据加工精度要求进行PLC程序的设计和调试。
(4)工艺要求:机床控制系统需要根据工艺要求选择合适的加工程序,并在加工过程中进行实时调整,以保证加工质量。
4.4 综合应用综合应用PLC控制技术与机器视觉技术、传感器技术、人工智能技术等,可以实现更加高效、准确、可靠的机床控制和加工过程监测。
例如,在某些复杂加工任务中,可以通过机器视觉技术对加工过程进行实时监测,并根据数据对加工速度、精度等一系列参数进行调整,从而大幅度提高机床的加工效率和质量。
未来随着技术的不断发展和应用需求的不断增加,PLC控制技术在机床控制系统中的应用将不断扩大,自动化智能化方向也将越发明显,为机床加工工业带来革命性的变化,提升行业效益。
五、PLC控制技术在工业自动化中的应用5.1 工业自动化的概念工业自动化是指在产品生产、加工和制造等各个环节中,通过自动化技术和设备,实现物理流、信息流和业务流的自动化控制和协调。
工业自动化技术可以减少人工操作,提高生产效率和质量,减少生产成本,增强生产安全性等。
5.2 PLC在工业自动化中的应用PLC控制技术是工业自动化中最常用的控制技术之一,因其稳定性、可靠性、易于维护和升级而被广泛应用于工业自动化生产线的各个环节中。