内燃机曲轴分析案例
从多起曲轴折断案例分析事故原因
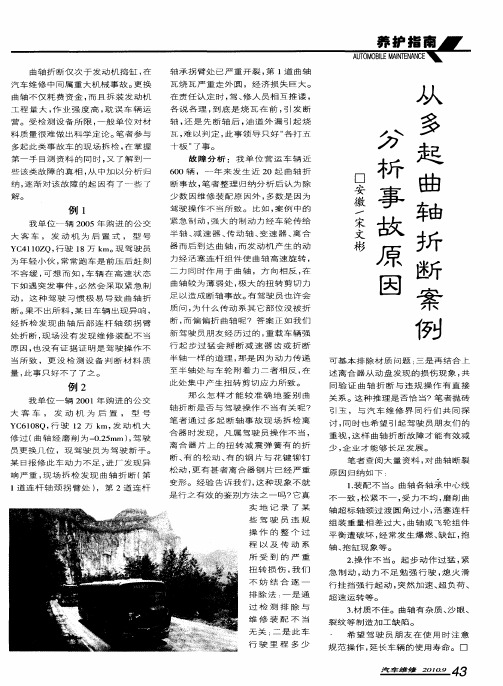
乏 证据 证 明是 驾驶 操作 不 有
更 没 检 测 设 备 判 断 材 料 质
] 不 了了之 。 \ 好
例 2
位 一 辆 2 01年 购 进 的 公 交 0
发 动 机 为 否 恰 当?笔 者 抛 砖 引 玉 ,与 汽 车 维 修 界 同 行 们 共 同探
中 同属 重 大 机 械 事 故 。 换 更
耗 费 资 金 , 且 拆 装 发 动 机 而
,
作 业 强 度 高 , 误 车 辆 运 耽
测 设 备 所 限 , 般 单 位 对 材 一
难 做 出 科 学 定 论 。 者 参 与 笔 事 故 车 的 现 场 拆 检 , 掌 握 在 测 资 料 的 同 时 , 了 解 到 一 又
折 断仅次 于 发动机 捣 缸 , 在
轴 承 拐 臂 处 已 严 重 开 裂 , 1道 曲 轴 第
瓦烧 瓦严 重走 外 圆 ,经济 损 失 巨大 。 在 责任 认 定 时 , 、 人 员相 互推 诿 , 驾 修
各 说 各 理 , 底 是 烧 瓦 在 前 , 发 断 到 引 轴 , 是 先 断 轴 后 , 道 外 漏 引 起 烧 还 油
组装 重 量相 差过 大 , 轴 或 飞轮 组件 曲 平衡遭 破 坏 , 常发 生爆 燃 、 缸 , 经 缺 抱 轴 、 缸现 象等 。 抱
操 作 的 整 个 过 程 以 及 传 动 系 所 受 到 的 严 重 扭 转 损 伤 , 们 我 不 妨 结 合 逐 一 排 除 法 : 是 通 一 过 检 测 排 除 与 维 修 装 配 不 当
发 事 件 , 然 会 采 取 紧 急 制 必
驾 驶 习 惯 极 易 导 致 曲 轴 折
足 以 造 成 断 轴 事 故 。 驾 驶 员 也 许 会 有
内燃机车柴油机锻钢曲轴氮化变形超差校直工艺方法
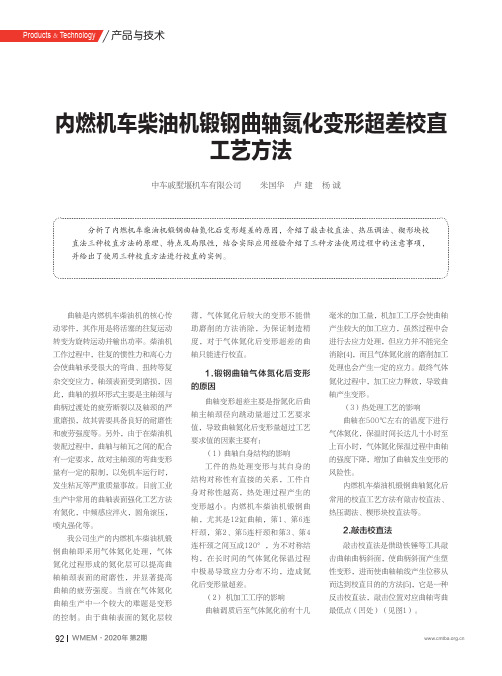
产品与技术内燃机车柴油机锻钢曲轴氮化变形超差校直工艺方法中车戚墅堰机车有限公司 朱国华 卢 建 杨 诚分析了内燃机车柴油机锻钢曲轴氮化后变形超差的原因,介绍了敲击校直法、热压调法、楔形块校直法三种校直方法的原理、特点及局限性,结合实际应用经验介绍了三种方法使用过程中的注意事项,并给出了使用三种校直方法进行校直的实例。
曲轴是内燃机车柴油机的核心传动零件,其作用是将活塞的往复运动转变为旋转运动并输出功率。
柴油机工作过程中,往复的惯性力和离心力会使曲轴承受很大的弯曲、扭转等复杂交变应力,轴颈表面受到磨损,因此,曲轴的损坏形式主要是主轴颈与曲柄过渡处的疲劳断裂以及轴颈的严重磨损,故其需要具备良好的耐磨性和疲劳强度等。
另外,由于在柴油机装配过程中,曲轴与轴瓦之间的配合有一定要求,故对主轴颈的弯曲变形量有一定的限制,以免机车运行时,发生粘瓦等严重质量事故。
目前工业生产中常用的曲轴表面强化工艺方法有氮化,中频感应淬火,圆角滚压,喷丸强化等。
我公司生产的内燃机车柴油机锻钢曲轴即采用气体氮化处理,气体氮化过程形成的氮化层可以提高曲轴轴颈表面的耐磨性,并显著提高曲轴的疲劳强度。
当前在气体氮化曲轴生产中一个较大的难题是变形的控制。
由于曲轴表面的氮化层较薄,气体氮化后较大的变形不能借助磨削的方法消除,为保证制造精度,对于气体氮化后变形超差的曲轴只能进行校直。
1.锻钢曲轴气体氮化后变形的原因曲轴变形超差主要是指氮化后曲轴主轴颈径向跳动量超过工艺要求值,导致曲轴氮化后变形量超过工艺要求值的因素主要有:(1)曲轴自身结构的影响工件的热处理变形与其自身的结构对称性有直接的关系,工件自身对称性越高,热处理过程产生的变形越小。
内燃机车柴油机锻钢曲轴,尤其是12缸曲轴,第1、第6连杆颈,第2、第5连杆颈和第3、第4连杆颈之间互成120°,为不对称结构,在长时间的气体氮化保温过程中极易导致应力分布不均,造成氮化后变形量超差。
内燃机曲轴的刚度分析

第15卷增刊计算机辅助工程 V ol. 15 Supp1.年月20069COMPUTER AIDED ENGINEERING Sep. 2006 文章编号:1006-0871(2006)S1-0151-02内燃机曲轴的刚度分析彭北京,郑松涛,陈海彬,郭东劭(浙江钱江摩托股份有限公司,浙江温岭 317500)摘要:应用MSC Patran前处理系统对摩托车用汽油机的曲轴、连杆机构进行网格划分和用非线性有限元分析软件MSC Marc进行刚度计算分析,得出汽油机实际运行中所受到最大载荷工况下的曲轴、连杆机构各零件应力和变形云图. 通过有限元模拟计算,为曲轴、连杆机构的结构设计提供指导和优化方向,以满足各项性能要求.关键词:MSC Patran;MSC Marc;摩托车;曲轴连杆机构;刚度中图分类号:TP391.4; U483.133.3文献标志码:A0 引言近年来,为提高内燃机的比功率、减小质量和尺寸,内燃机的设计转速越来越高,因而对其力学性能的研究更显重要.本文着重讨论某摩托车用发动机曲柄连杆机构的强度和刚度计算分析. 在发动机性能测试过程中,发现该款发动机的性能指标比同类机型低,经反复对比和原因查找分析后发现是该发动机的机械损失偏大所致. 为此,对该曲柄连杆机构进行建模作对比分析. 首先,对曲轴、连杆、主轴承按符合实物的要求进行三维建模和装配,合理简化后直接导入到MSC Patran中并利用其强大的前处理功能进行网格划分,再将单元、节点信息导入到非线性有限元分析软件MSC Marc进行刚度计算分析,各零件之间的接触定义均按照实际工作模型执行.1 有限元模型的建立根据曲柄连杆机构的结构几何特征和承载方式,以Pro-E软件建造的符合实物要求的三维装配件实体模型为基础,经适当的、合理简化建立详细的曲柄连杆机构有限元模型.1.1 网格划分采用4节点4面体单元进行网格划分. 结点数和单元数见表1.表 1 曲轴连杆机构的结点数和单元数零件结点数单元数曲轴连杆机构81 398 48 6311.2 材料与属性计算中所使用的材料参数如下:合金钢的材料参数:弹性模量:2.06e+005 MPa材料密度:7.85e-009 t/mm3泊松比:0.268 5长度单位:mm曲轴连杆机构有限元模型受力及约束图见图1:图 1 曲柄连杆机构有限元模型受力及约束原始设计计算结果,变形云图见图2:图 2 变形云图曲柄连杆机构各部位最大变形偏角,见表2:计算机辅助工程年152 2006表 2原始设计各部位最大变形偏角2 改进结构计算结果从提高曲柄连杆机构刚度(减小变形偏角)角度出发,根据计算结果对该款机型的曲轴连杆机构进行结构改进,并按照原始设计结构的步骤重新进行建模分析. 计算结果见表3.3 分析与结论由表3可以看出,改进结构使曲轴连杆机构各部位的变形偏角减小近30%. 采用改进结构的曲轴重新做实验,发动机的功率提高近20%,结果数据表明采用有限元计算结果与实际测试结果基本一致,并且根据有限元计 表 3改进结构各部位最大变形偏角算结果所提出的改进方向和结构非常具有实效.表 4 结果对比参考文献:me A:Theory And User Information[K]社,1994.数值方法[M]. 北京:清华大出版社. (编辑 吴彦生)[1] MSC Marc Volu [2] MSC Patran User's Manual[K].[3] 机械工程材料性能数据手册[K]. 北京:机械工业出版[4] 王勖成. 邵敏. 有限元基本原理和学。
发动机曲轴磨损案例

发动机曲轴磨损案例一、案例描述本案例涉及一台使用中的发动机曲轴发生磨损。
曲轴是发动机中非常重要的部件,负责将活塞的往复运动转化为旋转运动,以驱动车辆前进。
磨损发生在一个曲轴轴承上,导致曲轴在旋转时产生摩擦噪音,并可能影响发动机的性能。
二、磨损原因分析经过详细检查和分析,发现曲轴轴承磨损的主要原因是润滑不良。
润滑系统未能提供足够的润滑油,导致曲轴轴承在高速运转时受到严重摩擦。
此外,润滑油的清洁度不够,含有大量杂质,也加剧了轴承的磨损。
三、损坏的影响曲轴轴承的磨损对发动机的性能和寿命产生了严重影响。
首先,摩擦噪音的产生会影响驾驶的舒适性。
其次,曲轴轴承的磨损会导致发动机效率降低,功率输出下降。
最后,由于曲轴是发动机的核心部件,其损坏可能会引发一系列其他问题,如连杆断裂、活塞磨损等,最终可能导致发动机完全失效。
四、修复与更换决策针对曲轴轴承磨损的问题,有两种可能的解决方案:修复或更换曲轴。
修复方案包括对磨损的轴承进行研磨,以恢复其光滑度,并更换清洁的润滑油。
如果磨损程度较轻,这是一个可行的选择。
然而,在本案例中,由于磨损程度较严重,修复可能无法完全解决问题,且存在一定的风险。
因此,更换曲轴成为更安全、更可靠的解决方案。
新的曲轴经过精密加工,能够确保轴承的光滑度和正确的配合。
更换曲轴需要专业技术人员进行,以确保新曲轴正确安装和调整。
五、预防措施为了防止类似的问题再次发生,需要采取一系列预防措施。
首先,定期检查润滑系统,确保润滑油充足且清洁。
其次,定期更换润滑油,以避免油泥和杂质的积累。
此外,对于使用较长时间的车主来说,考虑对发动机进行全面检查和维护,以确保各部件的正常运行。
通过实施这些预防措施,可以显著降低曲轴轴承磨损的风险,延长发动机的使用寿命。
同时,车主应选择高品质的润滑油并定期更换,以提供良好的润滑效果。
总之,发动机曲轴轴承磨损是一个严重的问题,需要得到及时解决。
通过分析磨损原因、评估损坏影响、采取修复或更换措施以及实施预防措施,可以确保发动机的正常运行并延长其使用寿命。
内燃机曲轴动态特性分析及结构改进

( c )节面2 在Z 轴位移
曲线
:
率 依 然 高 于 基 频 避 开 了共 振 , 曲轴 的 改进 设 计 是 合 理 的 。表 5 为 改 进前 后 的 曲轴 模 态对 比 。选取 同 样 的3 个 节面 进 行 谐 响应 分析 得 到 的幅 频特 性 曲线
如 图8 ~图 l O 所示。
参考文献 :
【 1 】 白鑫 , 吕丽平 , 赵雪梅 . Mo d b u s 协 议 在 柴 油 发 电机 组 监 控
系统 中的应用研究[ J ] . 制造 业 自动化, 2 0 1 2 , 0 3 : 9 — 1 1 .
【 2 ]李 鹏 飞 , 孟泰 , 王薇婕 . 基 于M o d b u s 总线协议 的并行通信
图4 数 据 处 理 流 程 图
出
童‘ 童‘ 矗‘ 出
. 蠡‘ 出
量‘ j童‘ 矗‘ 童‘ &I 矗‘ . . ‘ .{重I 矗‘ 矗・ {盘‘ 蠡‘ . 出
变形 。
~
~
…
一
0
( a ) 节面3 在X 轴位移
( b ) 节 面3 在Y 轴位移
( c )节面3 在Z 轴位移
图1 O 节面3 的 幅 频 特 性 曲线
从 图 中 看 出 曲轴 在 共 振 频 率 4 4 0 Hz 时 振 幅 最 大 , 曲轴 的谐 响 应 节 面 在 共 振 时 发 生 的轴 向变 形
如 表6 所示。
表6 曲轴谐响应位移对比
3 曲轴 的结构 改进
3 . 1 曲轴的结构改进方案 曲轴 改 进 的材料 选 择QT 8 0 0 ,它 的吸振 特 性能
有 效 减 小 变 形 ,但 从 结 构 考 虑 还 要 提 高 曲轴 的 刚
内燃机曲轴系多体动力学分析
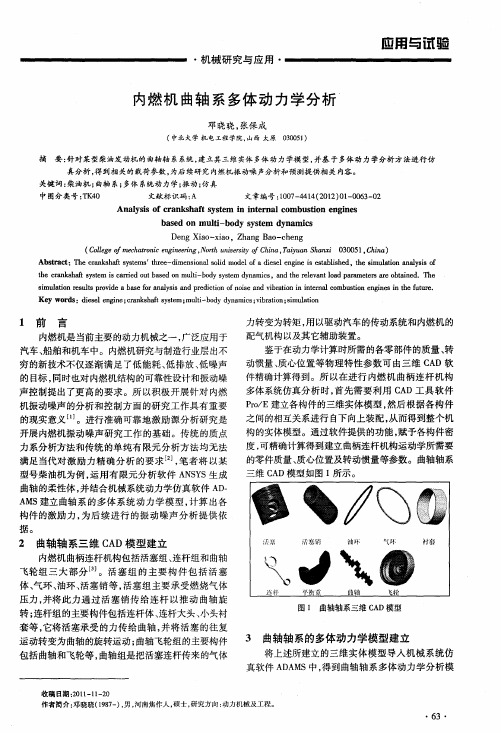
构的实体模型。通过软件提供的功能 , 赋予各构件密 度, 可精确计算得到建立曲柄连杆机构运动学所需要 的零件 质量 、 质心位 置及转 动惯量 等参 数 。曲轴 轴系
三维 C D模 型如 图 I A 所示 。
A n y i f c a ks a ts s e n i e na o bu to e i e alss o r n h f y t m i nt r lc m s n ng n s i
ba e s d on mul .b y s se y mis i t . od y tm d na c De g Xio x a n a - io,Z a g Ba -c e g h n o h n
一
20 0
0
20 0
40 0
60 0
80 0
曲轴 转 角 ( )
图 4 某型柴油机气 体压力示功 图
振动和噪声 。所以曲轴作为曲轴系的关键部件是弹 性体而非刚体 , 为更真实地计算其对 内燃机 内部激励 载荷 的影 响 , 对其 进行 柔性化 处理 。 需要 将在 P / m E软件建立 的曲轴模型导人有 限元分 析软件 A S S中, NY 通过对 曲轴进行离散化处理建立 曲轴的有限元模型 , 进行模态综合分析 , 产生一个包 括曲轴的材料 、 节点、 单元和模态信息的模态中性文 件, 将通 过 有 限元软 件柔 性 化处理 过 的 曲轴构 件 ( N 模态中性文件) M F 导人 A A S刚体模型中, DM 并 替代刚性 曲轴 , 建立 曲轴 为柔性体 的多体动力学模 型。曲轴 的柔性化模型如图 3 所示 。
0  ̄0 0 0 0
G170柴油机曲轴有限元分析

α文章编号:100127445(2000)022*******G 170柴油机曲轴有限元分析蒲明辉,黄世伟(广西大学机械工程学院,广西南宁 530004)摘要:阐述了有限元法的基本理论,并介绍将有限元法应用于G 170柴油机曲轴的强度和刚度分析方法,应用I D EA S 软件对连杆计算模型进行计算,得出曲轴应力和变形分布图,并对结果进行了分析.关 键 词:有限元法;曲轴;曲轴计算模型中图分类号:TB 115 文献标识码:A曲轴是柴油机的主要零件,应具有足够的强度和刚度,其设计是否可靠,对柴油机的使用寿命有很大影响,因此在研制过程中需给予高度重视.由于曲轴的形状及其载荷比较复杂,对其采用经典力学的方法进行结构分析往往有局限性[1].有限元法是根据变分原理求解数学物理问题的一种数值计算方法,它最初是在50年代作为处理固体力学问题的方法出现的[2].有限元法是分析各种结构问题的强有力的工具,不论结构的几何形状和边界条件多么复杂,不论材料性质和外加载荷如何多变,无论是大型飞机、大型舰船,还是高层建筑、水利大坝,使用有限元法均可方便地进行分析和获得满意的答案.在国外,许多制造企业,把有限元分析作为设计过程的一个必需步骤,规定不经过有限元分析和优化的设计,不能用于生产.G 170柴油机是南宁机械厂正在开发的新产品,为检验其曲轴的强度和刚度,确保产品开发进度,作者用有限元法对该曲轴进行了分析.1 有限元的基本理论有限元分析是一种预测结构的偏移与其他应力影响的过程,有限元建模将这个结构分割成单元网格以形成实际结构的模型,每个单元具有简单形态(如正方形或三角形)并通过节点相连,每个单元上的未知量就是节点的位移.将这些单个单元的刚度矩阵相互组合起来以形成整个模型的总体刚度矩阵,并给予已知力和边界条件来求解该刚度矩阵从而得出未知位移,从节点上位移的变化就可计算出每个单元中的应力.有限元分析可使有限元计算模型在离散化后归结为一个线性方程组求解,其形式如下[3,4]{F }=[K ]{∆},(1)式中{F }为所受的外力向量,[K ]是计算模型的整体刚度矩阵,{∆}是计算模型上各节点的位移向量.根据有限元理论,[K ]是由每个单元的刚度矩阵迭加而成,即[K ]=6[E ]e ,(2)式中[K ]e 表示单元的刚度矩阵,其计算公式为[E ]e =µ[B ]T [D ][B ]d x d y d z ,(3)式中[B ]表示单元的几何矩阵,该矩阵与单元类型有关,[D ]是材料的弹性矩阵,该矩阵是6×6阶的对称矩阵,具体形式取决于材料的特性.第25卷第2期2000年6月广西大学学报(自然科学版)Journal of Guangxi U niversity (N at Sci Ed )V o l .25,N o.2 June, 2000 α收稿日期:20000103;修订日期:20000201作者简介:蒲明辉(1964),男,广西合浦人,广西大学讲师.式(1)中所受的外力向量可由下式表达{F }=6({R }e +{Q }e +{P }e ),(4)式(4)中{R }e 是单元的集中力,{Q }e 是单元的表面力,{P }e 是单元的体积力.在得出方程(1)的各系数后,给出边界条件,可得出所求有限元模型上各节点的位移{∆}.为了求出模型上的应力[Ρ],先求出单元上各节点的应变[Ε],{Ε}=[B ]{∆}e ,然后根据弹性方程{Ρ}=[D ]{Ε}计算出应力.2 曲轴计算模型的建立212 几何模型的建立(1)材料特性 曲轴的材料是40C r 合金结构钢,其材料特性为:弹性模量E =206M Pa ,泊松比Λ=0.28,屈服极限Ρs =784M Pa ,强度极限Ρb =980M Pa .(2)几何模型的建立 先根据曲轴的设计图纸在计算机上用I D EA S 6.0软件对曲轴进行三维实体建模.为避免有限元网格尺寸大小相差悬殊而影响有限元单元质量和计算精度,对一些影响曲轴强度极微的小倒角、小圆角及键槽等结构作了简化处理(如图1).由于曲轴的几何形状和所受载荷对称于其中剖面,因此可取二分之一曲轴作为计算模型,并选用四节点四面体单元进行有限元网格划分,共计27731个节点,17668个单元(见图2).图1 曲轴零件简图 图2 曲轴有限元网格图212 计算工况和边界条件 (a ) 最大惯性力分布 (b ) 最大爆发力分布图3 曲轴载荷分布情况(1)曲轴受力情况 根据计算数据分析,曲轴在作功行程上止点处(即曲轴转角360°)受到最大爆发压力作用,其值为P 1=22942.17N ,此压力通过连杆大头轴瓦作用在曲轴连杆轴颈上部的圆柱面上.在进气行程上止点时受到最大惯性力作用,其值P 2=3894.6N .此力通过连杆盖轴瓦作用在曲轴连杆轴颈下部的圆柱面上.这两个力在接触处沿周向呈余弦规律分布(见图3),其分布规律为q Η=q A co s n Η,(5)式中n 为待定系数;q A 为径向最大压力集度,N mm 2;q Η为任意点上的径向压力集度,N mm 2.在图中Υ为曲轴连杆轴颈与连杆大头轴瓦的接触角,其大小与轴颈和轴瓦的刚度,它们之间的间隙以及润滑状况有关.接触角的选取对轴颈附近应力的计算结果影响较大,且Υ取值越小应力计算结果越大,一般情况下接触角可在120°~180°范围内选取[1].由于要检验曲轴的强度和刚度情况,因此我们考虑装配和润滑最差的状况,在此取Υ=120°.当Η=Υ 2,q Η=0,于是得n =3 2.该力沿曲轴连杆轴颈的轴向均匀分布.设r 为连杆轴颈的半径,l 为连杆轴颈受压部分的轴向长度,则轴颈上所受的总压力为201广西大学学报(自然科学版)第25卷 p j =l ∫Υ2Υ2q Ηco s Η r d Η=l ∫Π3Π3q A r co s Η co s n Η d Η=65l r q A ,所以q A =5p j 6l r.因此,由(5)式得q Q =5p j 6l ・r ・co s 32Η,(6)式中p j 分别对应P 1(最大爆发压力)和P 2(最大惯性力).(2)模型和边界条件的简化 由于曲轴沿轴线的中剖面几何形状近似对称,载荷对称,因此在确定曲轴边界条件的前提下取曲轴的一半进行分析,并对实际情况的边界条件进行简化,具体简化如下:①在上述两种工况下将曲轴主轴颈与主轴承接触处的上下120°圆柱面及轴长2 3范围分别施加径向约束.②在曲轴轴线中剖面上施加对称约束.③为了限制曲轴沿轴向的刚体位移,必须在曲轴上施加轴向约束.而轴向约束必须加在曲轴在受力变形过程中没有轴向位移或位移很小的节点上.经过反复多次计算分析,在曲轴连杆轴颈轴向中点处附近的节点轴向位移最小,因此,将限制曲轴沿轴向位移的约束加在连杆轴颈轴向中点节点处.通过以上约束后,整个曲轴就不存在任何形式的刚体位移.3 曲轴的计算分析分别计算在作功行程上止点最大爆发压力和在进气行程上止点最大惯性力两个工况的应力和变形情况.求解及结果后处理工作均在集成化工程设计分析软件I D EA S 6.0版本上完成.311 变形分析在最大爆发力作用时,曲轴各部分在轴向方向的位移量在0.0172~0.0399mm 范围,在右边平衡块下端有最大的轴向位移,其值为0.0587mm (见图4),在最大惯性力作用时,曲轴变形更小(见图5).图4 最大爆发力工况变形分布图 图5 最大惯性力工况变形分布图312 应力分析在作功行程上止点时,最大爆发力作用在连杆轴颈上部,曲轴拉应力发生在连杆轴颈下部、主轴颈下部与曲柄连接处的过渡圆角等局部区域(见图6),而最大拉应力Ρ+m ax =125M Pa ,发生在连杆轴颈与曲柄相连的过渡圆角处.曲轴大部分区域受压力作用,压应力较大的部位是连杆轴颈与连杆轴瓦接触处(见图7),其值在111~123M Pa 之间,最大压应力Ρ-m ax =195M Pa ,发生在主轴颈与曲柄连接处下部过渡圆角处.按第四强度理论计算的等效应力较大值发生在主轴颈与曲柄相连的过渡圆角处及连杆轴颈与曲柄相连的过渡圆角的下部,其值在100~119M Pa 之间,最大值发生在右主轴颈与曲柄相连处过渡圆角的下部,其值为Ρm ax =125M Pa (见图8).在进气行程上止点,最大惯性力作用在连杆轴颈的下部,相对前面工况而言,应力很小,对曲轴的静强度影响不大,但对曲轴的疲劳强度则有一定影响,其等效应力分布情况可参见图9.301第2期蒲明辉等:G 170柴油机曲轴有限元分析图6 最大爆发力工况最大主应力分布图 图7 最大爆发力工况最小主应力分布图图8 最大爆发力工况等效应力分布图 图9 最大惯性力工况等效应力分布图由上述分析结果可知,曲轴有很大的静强度储备,静强度安全系数n =Ρs Ρm ax =6.27.并且有很好的刚度以抵抗变形,完全能满足该柴油机对强度和刚度的要求.参考文献:[1] 郭成壁,陈全福.有限元法及在动力机械中的应用[M ].北京:国防工业出版社,1984.49255,1612173.[2] 张国端.有限元法[M ].北京:机械工业出版社,1991.1217.[3] 监凯维奇O C .有限元法:上册[M ].北京:科学出版社,1985.962151.[4] 劳尔S S .工程中的有限元法[M ].北京:科学出版社,1991.2622273.A f i n ite elem en t ana lysis for crankshaf t of G 170d iesel eng i nePU M ing 2hu i ,HU AN G Sh i 2w ei(Co llege of M echanical Engineering ,Guangxi U niversity ,N anning ,530004)Abstract :T he basic theo ry of the FEA and the m ethod of u sing th is theo ry to analyze the crank shaft of G 170diesel engine are p resen ted .T he softw are of I D EA S is u sed in calcu lating and analyzing the stress and the disp lacem en t of that crank shaft .Key words :FEA (fin ite elem en t analysis );crank shaft ;FEA m odel of crank shaft(责任编辑 刘海涛)401广西大学学报(自然科学版)第25卷 。
东风7内燃机车柴油机曲轴箱超压问题的分析及解决措施

收稿 日 : 1- 0 1 期 2 1 1L 1 0 -
东风 7内燃机车柴油机 曲轴箱超压 问题 的分析及解 决措施
周 万忠 , 陈永 忠 , 万学一
( 太原铁路局 湖东 电力机务段 , 山西大同 ,305 070 )
摘
要: 对柴油机 曲轴箱 常见故 障的超 压 问题 引起 的危害作 了统计分析 , 讨 了其原 探
轴箱超压故 障共发生 1 , O次 造成更换活塞 l , O个 活塞 环 2 , 4组 气缸套 1 , 2个 给我段造成经济损失 2 o多万元 。而 2 0 年 上半 08 年曲轴箱超压故障引起停机 4起 , 6件低转速 维持运行 ( 回段检 修) 。这些故障 的发生不但影 响我段 的经济效益 , 同时增加 了工 人的劳动强度。 由此产生的机车扣修 , 延长 了机 车的检修 停时 , 降低了机车的运行率 。因此 , 如何减少 曲轴箱超压 的故 障 , 摆 是
社 ,0 9 20
十分恶劣 , 空间容纳 大量 的润滑 曲轴 、 内部 活塞 、 连杆等运 动部 件所产生的油气及气缸燃烧 室下窜的燃气 ,导致 曲轴箱 内部的 压力高于外界压力 。曲轴箱 内部正常情况下 , 在标准大气压 的条
件下 , 压力 为 O1 P 。当压力达到 06k a 差示压力计动作 , .k a . P, 超 压严重时还会 造成 曲轴箱检 查孔 盖打 出,有 可能危 及人身安全 或损坏柴 油机零部件 , 至会 产生 曲轴 箱爆炸 , 甚 造成严 重后果 。 因此 ,曲轴箱压力 的高低直 接影响柴油机 的正 常工作和机车的
版社 ,0 0 2 1.
学 电气与动力 工程学院 20 级在职工程硕士研究生 , 09 助理工程 师, 山西大唐 国际临汾热 电有限责任公 司 , 山西省临汾市尧都 区
内燃机用曲轴和连杆研发生产方案(二)
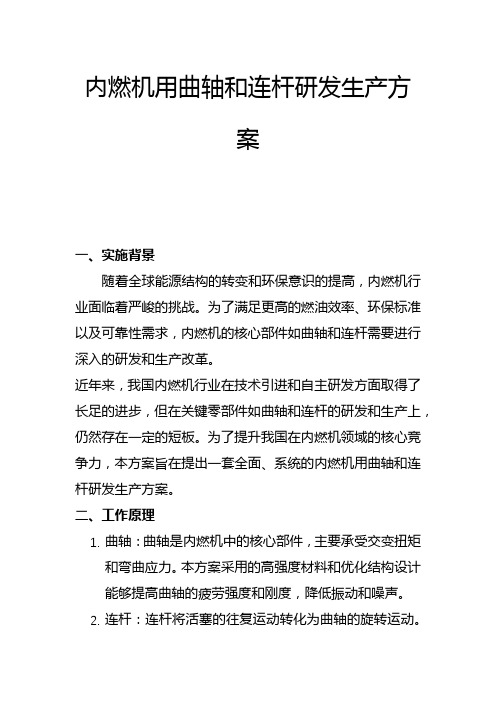
内燃机用曲轴和连杆研发生产方案一、实施背景随着全球能源结构的转变和环保意识的提高,内燃机行业面临着严峻的挑战。
为了满足更高的燃油效率、环保标准以及可靠性需求,内燃机的核心部件如曲轴和连杆需要进行深入的研发和生产改革。
近年来,我国内燃机行业在技术引进和自主研发方面取得了长足的进步,但在关键零部件如曲轴和连杆的研发和生产上,仍然存在一定的短板。
为了提升我国在内燃机领域的核心竞争力,本方案旨在提出一套全面、系统的内燃机用曲轴和连杆研发生产方案。
二、工作原理1.曲轴:曲轴是内燃机中的核心部件,主要承受交变扭矩和弯曲应力。
本方案采用的高强度材料和优化结构设计能够提高曲轴的疲劳强度和刚度,降低振动和噪声。
2.连杆:连杆将活塞的往复运动转化为曲轴的旋转运动。
本方案通过精确控制连杆的长度、直径以及材料选择,优化其力学性能,降低惯性力和冲击载荷,提高运行平稳性。
三、实施计划步骤1.技术调研:深入了解国内外内燃机用曲轴和连杆的研发生产现状,分析行业发展趋势和技术瓶颈。
2.研发团队建设:组建由材料科学家、机械工程师、分析师等组成的跨学科研发团队。
3.材料选择与优化:结合性能需求,筛选合适的材料,进行材料性能测试和优化。
4.结构设计:根据功能需求和性能要求,进行曲轴和连杆的结构设计。
5.样品试制:制作原型样品,进行严格的测试和验证。
6.生产工艺制定:确定生产工艺流程,制定质量控制标准。
7.批量生产:通过与合作伙伴共同投资,建立生产线,实现批量生产。
8.市场推广:与内燃机制造商合作,推广新型曲轴和连杆产品,同时拓展海外市场。
9.持续改进:收集用户反馈,不断优化产品设计和生产工艺。
四、适用范围本方案适用于大功率内燃机如船用、机车用、发电机组用内燃机的曲轴和连杆研发生产。
同时,也可应用于汽车、工程机械等领域的内燃机核心部件研发生产。
五、创新要点1.独特的材料选择和优化方法:通过多学科交叉研究,提出了一种新型的高强度材料及其制备方法,显著提高了曲轴和连杆的性能。
内燃机用曲轴和连杆研发生产方案(一)
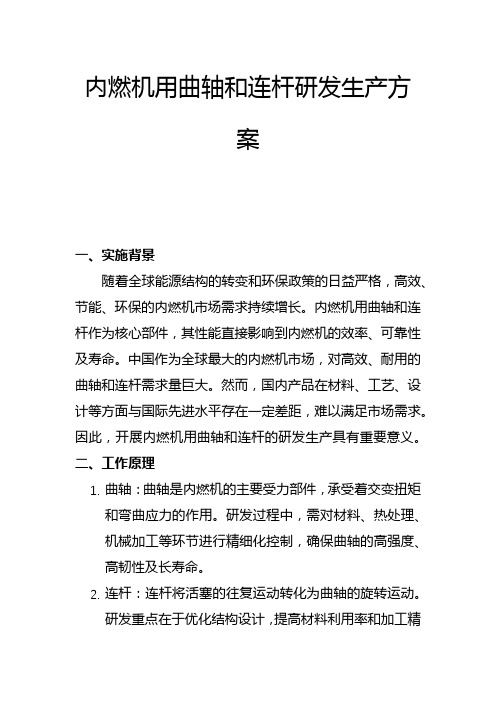
内燃机用曲轴和连杆研发生产方案一、实施背景随着全球能源结构的转变和环保政策的日益严格,高效、节能、环保的内燃机市场需求持续增长。
内燃机用曲轴和连杆作为核心部件,其性能直接影响到内燃机的效率、可靠性及寿命。
中国作为全球最大的内燃机市场,对高效、耐用的曲轴和连杆需求量巨大。
然而,国内产品在材料、工艺、设计等方面与国际先进水平存在一定差距,难以满足市场需求。
因此,开展内燃机用曲轴和连杆的研发生产具有重要意义。
二、工作原理1.曲轴:曲轴是内燃机的主要受力部件,承受着交变扭矩和弯曲应力的作用。
研发过程中,需对材料、热处理、机械加工等环节进行精细化控制,确保曲轴的高强度、高韧性及长寿命。
2.连杆:连杆将活塞的往复运动转化为曲轴的旋转运动。
研发重点在于优化结构设计,提高材料利用率和加工精度,以实现连杆的高效、稳定运行。
三、实施计划步骤1.市场调研:了解国内外内燃机用曲轴和连杆的市场需求、技术动态及发展趋势。
2.技术研究:开展材料、工艺、设计等方面的技术研究,为产品研发提供技术支持。
3.产品设计:根据市场需求和技术研究结果,进行内燃机用曲轴和连杆的设计。
4.样品试制:根据设计图纸和技术要求,制作样品进行试验和验证。
5.试验与改进:对样品进行性能试验、寿命测试等,根据试验结果对产品设计进行改进。
6.批量生产:经过多次试验验证后,开始批量生产内燃机用曲轴和连杆。
7.质量管理体系建设:建立完善的质量管理体系,确保产品的稳定性和可靠性。
8.市场营销与推广:开展市场营销和推广活动,提高产品知名度和市场占有率。
四、适用范围本研发生产方案适用于内燃机行业,包括汽车、船舶、工程机械等领域。
同时,也可为新能源动力系统、发电机组等提供技术支持。
五、创新要点1.材料选择:采用高强度合金钢、钛合金等新型材料,提高曲轴和连杆的强度和寿命。
2.结构设计:优化曲轴和连杆的结构设计,提高其承载能力和稳定性。
3.制造工艺:引入先进的机械加工技术和热处理工艺,提高产品的加工精度和整体质量。
内燃机曲轴粗加工定心工序演变及选用分析
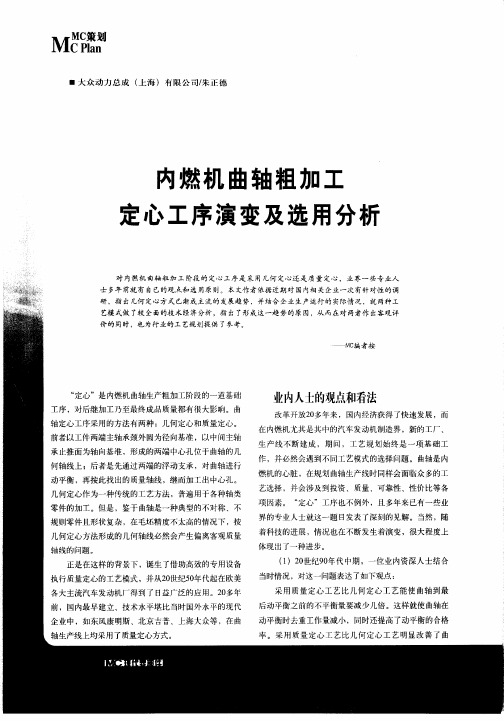
_ 大 众 动 力 总 成 ( 海 )有 限 公 司/ 上 朱正 德
内燃机 曲轴粗加工
定心工序演变及选用分析
对 内燃 机 曲轴粗 加 工 阶段 的 定心 工序 是 采 用几何 定心还 是 质 量 定 心 ,业 界 一些 专 业人
士 多年前就有 自已的观点和选 用原 则。本文作者依据近期对国内相关企业一次有针对性的调
进行动平衡时 ,初始不平衡量可能超 出平衡机要求而 无 法平衡。在这种 情况下应 优先选 用质量 定心机 。 ( )近 期 ,在 一些 主流汽车 发动机 厂工艺 规划 人 3 员的交流中 ,则进一 步形成 了如 下共识 :
传统 的几何定心方法又重新取得主流地位呢?
两种工艺模式的技术经济性分析
各大主流汽车 发动机厂得到 了 日益广 泛的应用。2 多年 0
前 ,国内最早 建立 、技术水平堪 比当时国外水平的现代
( )2 世纪9 年代 中期 ,一位业 内资深人 士结合 1 0 0
当时情 况 ,对这一 问题表达 了如下观点 : 采 用质 量定 心工 艺 比几何 定心 工艺 能使 曲轴 到最 后动平衡之前的 不平衡量 要减 少几倍 。这样就使 曲轴在
轴线的问题。
艺选择 ,并会涉及到投资 、质量、可靠性 、性价比等各
项 因素 。 “ 定心 ”工序也 不例 外 ,且多年来 已有一些业 界的专业人士就这一题 目发表 了深 刻的见解。当然 ,随 着科技的进展 ,情况也在 不断发生着演变 ,很大程度上 体现出了一种进步 。
正是 在这样的背景下 ,诞生 了借助高效的专用设备 执行 质量定心 的工艺模式 ,并从2 世纪5 年代起在欧美 0 0
10 0 %
项目一 单缸内燃机部分机构设计

任务一 绘制单缸内燃机机构运动简图
相关知识
运动副
一、机构的组成 使两构件直接接触并能产生一定相对运动的连接
图1-1-1 运动副
高副 两构件由点、线接触形成的运动副 低副 两构件由面接触形成的运动副 平面机构 所有构件都在同一平面上的机构
项目一 单缸内燃机部分机构设计
任务一 绘制单缸内燃机机构运动简图
项目一 单缸内燃机部分机构设计
任务一 绘制单缸内燃机机构运动简图
平面高副 图1-1-4所示,在曲线构成的运动副中,构件2既可沿接触点处切 线方向移动,又可绕接触点A转动,运动副保留了2个自由度,引进了一个约束。
图1-1-4 平面高副
项目一 单缸内燃机部分机构设计
任务一 绘制单缸内燃机机构运动简图
图1-0-1 单缸内燃机
当内燃机工作时,燃气推动活塞作往复 运动,经连杆使曲轴作旋转运动。凸轮和顶杆 用来控制进气和排气。曲轴经齿数比为1:2的 一对齿轮带动凸轮轴转动,曲轴每转两周,进、 排气阀各启闭一次,就把燃气的热能转换为曲 轴转动的机械能。
项目一 单缸内燃机部分机构设计
任务安排
任务一 绘制单缸内燃机机构运动简图 任务二 曲柄滑块机构设计 任务三 配气凸轮机构设计 任务四 气门弹簧设计分析
图1-1-5 平面运动构件的自由度
项目一 单缸内燃机部分机构设计
任务一 绘制单缸内燃机机构运动简图
相关知识 二、机构的运动简图
机构的相对运动与运动副的数目、类型、相对位置及某些尺寸有关,而与 构件的截面尺寸大小、组成构件的零件数目、运动副的具体结构等无关,因此 在研究机器或机构运动时,的类型,按一定比例确定运动副的相对位置及与运 动有关的尺用线条表示构件,用简单符号表示运动副寸,这种简明表示机构各 构件间运动关系的图形称为机构运动简图。
内燃机车柴油机曲轴故障分析与维修方法

内燃机车柴油机曲轴故障分析与维修方法摘要:本文旨在介绍内燃机车柴油机曲轴故障的常见原因和相应的维修方法。
通过对曲轴故障的分析,可以帮助车辆维修工程师快速定位问题并进行有效维修,以确保柴油机的正常运行。
关键词:内燃机车;柴油机;曲轴;故障维修内燃机车柴油机是目前广泛使用的一种动力装置,但在长时间的运行过程中,由于多种因素的影响,柴油机曲轴可能会出现故障。
本文针对柴油机曲轴故障进行分析,并提供了相应的维修方法。
一、故障原因分析1. 曲轴过度磨损曲轴的过度磨损是常见的故障原因之一。
曲轴过度磨损是指曲轴表面与其他部件摩擦过程中遭到异常磨损,超过了正常范围。
曲轴在长时间使用后会产生磨损,特别是由于缺乏定期更换机油导致润滑不良时,磨损会变得更加严重。
曲轴润滑不良是导致过度磨损的一个重要原因。
曲轴与连杆、活塞等部件之间需要润滑油起到减少摩擦的作用,防止磨损。
然而,如果润滑系统出现故障,润滑油供应不足或质量不佳,就会导致曲轴在工作时与其他部件的直接接触,从而加剧磨损。
其次,柴油机所使用的燃油也可能导致曲轴过度磨损。
如果长期使用低品质的燃油,其中所含有的杂质和颗粒物会进入曲轴及其轴承内部,同时燃烧不完全的油渣也会沉积在曲轴表面,加速磨损过程。
1.曲轴严重偏摆柴油机的曲轴通常由铸造或锻造而成,然后进行精密加工。
如果在这个过程中出现了质量问题,就会影响到曲轴的运转。
另外,安装时如果没有严格按照生产厂家的要求进行操作,也可能引起曲轴的偏摆。
其次,柴油机的曲轴还会受到机油的润滑情况和冷却系统的影响。
机油的润滑状况不良会增加曲轴的摩擦阻力,导致曲轴偏摆。
而冷却系统的故障,例如冷却液不充足或散热器堵塞等问题,会使曲轴过热,从而导致偏摆。
最后,柴油机的长期使用也会造成曲轴严重偏摆。
由于常年累月的工作,曲轴会受到较大的负荷和震动,从而造成疲劳断裂或变形。
另外,如果在日常维护保养中疏于检查和保养,也会逐渐加剧曲轴偏摆的问题。
1.曲轴弯曲曲轴弯曲可能由多种因素引起。
内燃机课程设计柴油机曲轴设计动力计算样本

《内燃机学》课程设计设计计算说明书题目6200柴油机曲轴设计学院专业班级姓名学号指导教师年月日目录1 动力计算 (1)1.1初始条件 (1)1.2曲柄连杆机构运动质量的确定 (2)1.3 P-φ示功图的求取 (2)1.4往复惯性力P j( α) 计算 (3)1.5总作用力P( α) 计算 (4)1.6活塞侧推力P H( α) 计算 (4)1.7连杆力P C( α) 计算 (5)1.8法向力P N( α) 计算 (5)1.9切向力P T( α) 计算 (6)1.10总切向力)(α∑T p计算 (7)1.11曲柄销负荷R B( α) 计算 (8)1.12准确性校核 (9)2 曲轴设计计算 (10)2.1曲轴各部尺寸比例 (10)2.2曲轴船规验算 (11)1 动力计算1.1初始条件母型机参数:四冲程六缸、废气涡轮增压、不可逆式、直接喷射、压缩空气启动。
D=200mm S=270mmn=600r/min Ne=440kW增压压力P k=0.241Ma,压缩比ε=12.5, 机械效率ηm=0.85,压缩复热指数n1=1.37,膨胀复热指数n2=1.26, Z点利用系数ξz=0.88, 燃烧过量空气系数α=2.0, 中冷器出水温度t=250 ,原机配气定时:进气门开——上死点前60度进气门关——下死点后40度排气门开——下死点前40度排气门关——上死点后60度行程失效系数可取约0.083。
连杆长L=540mm, 质量为34.76kg, 活塞组质量m=35.76kg, 连杆组质量分配比0.347/0.653, 单位曲柄不平衡质量m=48.67kg。
1.2曲柄连杆机构运动质量的确定将摆动的连杆用双质量系代替, 一部分质量等价到做往复运动的活塞组中, 另一部质量等价到做回转运动的曲柄组中, 从而能够求出往复质量j m 和连杆组算到大端的质量B m 。
由于连杆尺寸并未确定, 先按照母型机的连杆质量分配比。
0.347*35.760.347*34.7647.8217()j L m M m kg =+=+=0.653*0.653*34.7622.6983()B L m m kg ===上式中, M 表示活塞组质量, 0.347/0.653为连杆组质量分配比, L m 为连杆质量, 质量单位都用kg 。
新型内摆线内燃机曲轴模态分析

l
【 要】' 有限元 和试验模态 析方法 摘 f l 模态 分 对新型内 摆线内 燃机曲 轴进行了 态 研究。在 ; 动j特性 -
{Sl w rs o d o 中建立了内 i k 摆线内 燃机曲轴部件的三维模型,采用 A S S中的 Bok aco 法对其进行模 { NY l nzs cL
e gn rn s at n ie c a k h f C NY , UQ ngi HE u D u — u
( co l f c a i l A tm t eE gn eig SuhS iaU i r t o T c n lg , u n zo 6 0 C ia S h o o hnc & uo oi n ier ,ot hn nv s y f eh ooyG a ghu5 4 , hn ) Me a v n e i 1 0
摆 线 机构 , 图 1 示 。节 圆半径 为 r 小齿 轮 0 与节 圆半 径 为 如 所 的 .
尺的大齿轮构成内啮合齿轮副 , 由于 R r2 当小齿轮 0 做行星 / , = 。
节圆上的点 做直线运动。如果将活塞上的一点与小齿 内气体压力及 自身旋转惯性力引起 的周期性变化 载荷而产生弯 转动时 , 轮 O 节 圆上的点 日做成转动副 , 活塞必然也做纯粹的直线运动。 曲和扭转应力 , 这可能引起曲轴 的疲劳失效 ; 其动态特性不仅是
机 械 设 计 与 制 造
21 8
Ma h n r De in c iey sg
&
Ma fc u e nu a t r
第 5期 21 0 0年 5月
文章编号 :0 1 3 9 ( 00 0 — 2 8 0 10 — 9 7 2 1 )5 0 1 — 3
新 型 内摆 线 内燃机 曲轴模 态分析 木
发电柴油机曲轴断裂案例的分析与教训
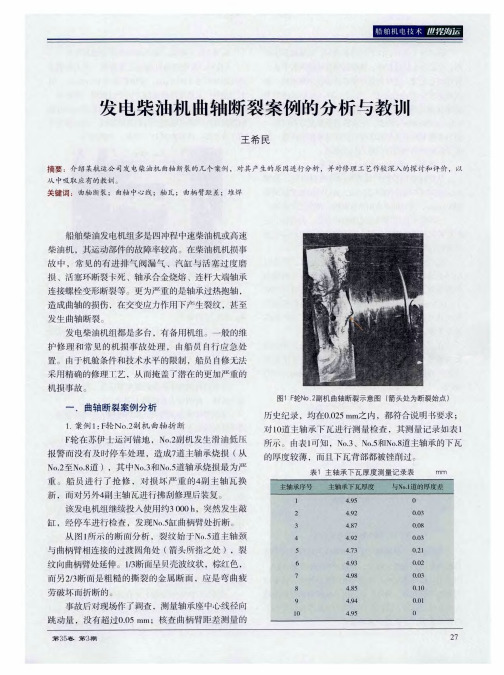
柄 销颈 和N . 主轴 颈上 有相似 的裂纹 ,裂纹 都是 从 o道 5 油 孔处 开始 ,沿轴 向成4。 伸展 。如 图3 5 所示 。
N. o 道曲轴主轴颈弯曲0 0 m,N . 2 . 2m o 道曲轴主轴颈弯 3
曲0 6 m,而且轴 颈表面非 常粗糙 ,轴 瓦发生转 动。 . 3m 任 职轮机 长没填 写过机损 事故 报告 ,但 根据 上述 测量 数据 和损坏情 况分析 ,该 柴油机 轴承 曾经发生 过 严重 的过 热事 故 。
力完 全 消除 。
图 2N .道 主 轴 颈 裂 纹 不 意 图 o3
结论 :曲轴轴颈上的裂纹 ,是 由于堆焊后残余应 力消除不充分 ,使材料产生很高 的表面硬度而引起 的。这样在曲轴颈上容易产生特征相似的裂纹 ,并具 有极大的抗拉残余应力 。
现将该 厂 的堆 焊修理 工艺介 绍如下 :先对 曲轴 全 部 预 热 至2 0℃ ,然后 局 部加 热 至 30℃ ,从 N .缸 2 5 o1
船厂对 曲轴主轴颈变形进行加热校直 ,而且对 N .主轴颈镀铬恢复原始 直径 。装复试车后测量 曲 o3 轴臂距差 ,N . o3 缸达No 4 m,超过说 明书要求 . 8 0 m
( .2 00 5mm)。经 再 次 检 查 ,发现 是 柴 油 机 机 座变
图3 N .缸 曲柄 销 颈 裂纹 照 片 o3
L o 发电柴油机曲轴过度磨损 ,其主轴颈直 轮N . 3
径 比原 始尺 寸小04 . mm,曲柄 销直径 小08 5 . mm。 日 5 本 三菱船 厂采取 堆焊磨 削 的方法予 以修理 。修 复后 ,
N . 机运行 约4 0 ,发 现该7 柴油 机 的N . 曲 o副 3 0h 0 缸 o缸 3
2 所示 。
活塞连杆组、曲轴飞轮组案例

案例六 1.故障现象 新修复的发动机运行不长时间,发动 机下部有异响。 2.故障原因 轴颈与轴瓦磨损。 3.故障诊断与排除 诊断:机体下部的响声一般都是瓦响 排除:要校正曲轴,使弯曲度不得超过 0.02mm,修磨已磨损的轴颈,更换第四道曲 轴瓦,重新组装。
案例七 • 1.故障现象 一辆刚购进来的新东风汽车在返回 途中,就发现瓦响 • 2.故障原因 轴瓦制造质量不好。 • 3.故障诊断与排除 诊断:机体下部的响声一般都是瓦响 排除:
案例十一 • 1.故障现象 一台东风发动机在修理厂修理后,着 车时发现发动机抖动的厉害。 • 2.故障原因 曲轴、飞轮的不平衡量过大。 • 3.故障诊断与排除 诊断: 排除:
案例十一 • 1.故障现象 一台东风ZQl090发动机大修后二个半 月进行了一次保养,将主轴瓦螺栓及连杆 瓦螺又紧了一遍。开始运行至第三天,发 动机摇缸,经查看发现一缸连杆螺栓折断 了。 2.故障原因 连杆螺栓扭矩过大。 • 3.故障诊断与排除 诊断: 排除:更换全部损坏的件,按规定的标 准扭矩拧紧
案例三 1.故障现象 发动机运行很正常,功率也不见下降, 却出现机油耗量急剧增加的现象。 2.故障原因 活塞环侧隙变大。 3.故障诊断与排除 诊断:活塞环与活塞环槽之间的间隙只 须保证活塞环在活塞上运动时能在活塞环槽 中径向移动,而过紧会出现卡死,过松易折 断,同时还能产生泵油作用 排除:
• 从活塞上取下活塞环,检查活塞环是否被 压缩变形。若发现塞环已压缩变形,应 更换活塞环。若活塞环未变形,则应检查 活塞环与活塞环槽的侧隙,当该间隙大于 0.30mm时,说明活塞环槽的边缘已被压缩, 应更换活塞。 • 经常发现这种情况,发动机三保换活塞 环后仍然烧机油,原因就在这里,没有注 意活塞环槽变宽。
案例八 • 1.故障现象 一辆东风EQl090汽车运行半年左右, 发现动力下降,在机体下部有异响。 • 2.故障原因 主轴颈磨损。 • 3.故障诊断与排除 诊断:润滑油太脏 排除:清洗润滑系各配件及油道,修复 磨损严重的轴颈,更换新机油。
12V240内燃机曲轴的有限元分析

WagH n z i, u H i, n H n S a gY e j i R i i g n og— h X e a Wag og , hn u — i ,Lu u —qa n n
( . eate tft n o ai a l on G nu r ne G o nG nu 7 00 , hn 1 Dp r n o rs r t no oa cut o a s p ̄i , al a s 32 0 C i m a p t o fG n yf c a a; 2 T e eh t nc nier gi tu nh uJ o n n e i , azo as 70 7 C i . h car iegnei stto L zo i t gu i rt Lnh uG nu 30 0, hn m o n n i ef a ao v sy a; 3 Ol t aeadt n o fc r a ̄o eohmcl o p n e oC i , a zo as 7 0 6 ,hn ) . is rg n a p r at yo nh u t ce i m ayo t hn L nhuG nu 30 0 C i o rs t o fL pr ac fp r a a
1V 4 t a cm ut ne ̄ ecakhf uigtesf a f N Y ,t w a r f h r khf i acr i d 2 2 0i e l o b so n n r sat s h ot r o S S i eka ao eca sa setn . nr n i n n w e A s e t n ts ae
曲轴内燃机

曲轴内燃机第一个坐标图中橘黄色部分是活塞传递到曲轴上的有效功率,阴影部分是活塞做的无用功。
检验曲轴在0——145°的运动中活塞传递到曲轴上的有用功可以通过滑块推动曲柄进行测试,也可以用一根棍使你的作用力由0——90°开始逐渐增大角度去推放在玻璃板上的物体,看水平直线推与增大角度去推物体上得到的力是否相等,而失去的力就是活塞的直线变圆周做的无用功。
下坐标图中的粉红色是排气门被打开后145°——720°曲轴上消耗掉的功,在这曲轴拉动连杆或推动连杆都会造成活塞对缸壁产生测向作用力,曲轴的圆周变直线消耗掉的有用功可以利用曲轴上的惯性转动720°后测曲轴所剩的扭力功。
内燃机汽缸里活塞上产生力的大小由两方面来决定:一是产生气体的量来决定,二是要看活塞在运动中缸体空间的大小。
在上止点上它的空间体积最小但随着活塞向下止点的运动缸体的空间也在逐渐的增大,那么后来产生的膨胀气体就必须先填满增大的空间才能够得到膨胀气体的体积与汽缸空间体积相对较大的比值也就是较大的力,这就造成了因缸体体积的逐渐增大而使活塞产生与前一点相同的作用力就必须消耗稍多的膨胀气体也就是要比前一点上要多消耗燃油。
曲轴由0°—145°从图中我们可以看出橘黄色的有效做功只有60%,而其它40%的做功都转变成了连杆对轴瓦的摩擦力而做无用功,在还没有计算膨胀气体的做功在逐渐衰减。
曲轴传动也只有在90°一个点上它的有效做功能完全传递到曲轴上,在其它的任何点都存在做或多或少的无用功,但在90°这个点上缸体的空间体积比活塞在上止点上的最小空间体积增大了5倍,由此得出曲轴0——145°的转动活塞的运动都将造成缸体空间基数逐渐增大而需要多耗能。
曲轴在145°—720°的圆周运动因与活塞直线运动方向不在一条直线上也就造成了在传递力时会做大量的无用功,那些认为内燃机的做功有25%浪费在被排放的高温气体上是完全错误的。
- 1、下载文档前请自行甄别文档内容的完整性,平台不提供额外的编辑、内容补充、找答案等附加服务。
- 2、"仅部分预览"的文档,不可在线预览部分如存在完整性等问题,可反馈申请退款(可完整预览的文档不适用该条件!)。
- 3、如文档侵犯您的权益,请联系客服反馈,我们会尽快为您处理(人工客服工作时间:9:00-18:30)。
运通内燃机曲轴结构可靠性分析案例
北京运通恒达科技有限公司
2006年7月
1.背景描述
车用内燃机的曲轴断裂故障发生的几率并不是很高。
但当柴油机的内燃机曲轴,在车辆行驶了比较长的里程(约4~5万km左右)以后常常出现断裂。
而曲轴断裂故障多属疲劳破坏。
因为曲轴是一个弹性轴,在回转中受到各缸交变的气体压力、往复惯性力和离心力,以及由此引起的弯矩、扭矩的作用,发生强迫扭转振动,形成复杂的交变应力和扭转或弯曲振动附加应力,加之曲轴形状复杂,刚性差,应力集中严重,一旦所承受的应力超过曲轴的疲劳强度(过载)就容易发生疲劳破坏。
疲劳破坏一般可分为三种类型:扭转疲劳破坏、弯曲疲劳破坏和弯曲-扭转疲劳破坏。
如图1所示;因此本文提出了对内燃机曲轴的疲劳可靠性分析。
图1 疲劳破坏实物图1
2.疲劳分析
⏹疲劳应力分析
将疲劳设计和有限元法相结合,通过有限元求解出最危险点的最大应力和最小应力,从而获得疲劳计算需要的名义平均应力及幅值。
⏹疲劳强度分析
因为内燃机内的零件一般都是无限寿命设计,即失效循环数在107以上,本问通过参数修正来将材料疲劳极限转化为零部件的疲劳极限。
材料的疲劳极限,只能代表标准光滑试样的疲劳性能,而实际零件的尺寸、形状和表面情况是各式
各样的,与标准试样有很大的差别。
影响机械零件疲劳强度的影响因素很多,其中主要的有:尺寸、形状、表面情况、平均应力、复合应力、腐蚀介质、温度等。
因此通过引入应力集中系数、尺寸系数和表面加工系数等,对试样的疲劳强度进行修正,来确定零件的疲劳强度。
其中修正系数的均值合标准差由试验或经验得到。
疲劳寿命分析
疲劳安全寿命分析可以根据S-N曲线来进行。
为减少试验通常利用材料S-N 曲线,进行一定的修正得出零件S-N曲线,零件的S-N曲线是名义应力有限寿命设计法的基础。
常规的S-N曲线一般是对称循环应力条件下(即r=-1)做试验的方法采集到的。
而大多数现场条件都包含非零的平均应力即非对称循环应力工作。
而循环的平均应力水平对材料的疲劳行为由很大的影响,平均应力值增大时,疲劳寿命降低。
在进行非对称循环的疲劳寿命时,需要用表示交变应力幅合平均应力之间的关系的经验公式,本分析采用Goodman曲线来分析。
3.受力分析
本文所分析的内燃机是并列连杆式曲柄连杆机构,在发动机实际运行过程中曲轴主要受连杆及轴承作用力产生的弯曲应力,由于扭转应力相对较小,不予以考虑。
活塞直径150mm,面积17671.46mm2。
气体爆发力为16MPa,作用于活塞顶面的燃气载荷为280000N。
利用ADAMS计算出的各缸运动规律及曲轴受力情况,推导出缸内气体通过连杆作用于曲拐上的力、活塞和连杆的惯性力在曲拐上产生的力。
连杆在处于爆发状态时,作用在曲柄销上的总载荷为210000N。
不考虑由于机构的摩擦力。
考虑作用在曲轴上的缸内气体压力和机构运动质量的惯性力。
4.建立有限元模型
由于曲轴外表面形状复杂,为了控制有限元网格的疏密程度合整个有限元模型规模,对实体各部分进行分区,对不同区域设定不同的单元密度,并采用半自动方法进行网格剖分。
单元类型是四面体单元,对实际使用中易发生断裂、应力集中严重的曲柄销与曲柄臂过渡圆角处进行细化,以提高计算精度。
如图2所示;
图2 有限元模型
5.确定性分析
确定性分析使可靠性分析的前提,只有理论上不发生失效的零部件才可以进行可靠性分析。
通过有限元的确定性分析可知,最大应力出现在曲柄销的过渡圆角处,主轴径的过渡圆角的应力也比较大。
如图3所示;
图3 应力集中点位置
通常只对危险因素进行可靠性分析,因此同时选择主应力较大的几个节点进行可靠度的求解计算,其结果如表1所示;
位置最大主应力(MPa)
曲柄销圆角1点125.985 2点92.2625
主轴径圆角3点99.2702 4点32.7185
其中非爆发连杆一方的主轴径圆角应力集中点(关键点4)的主应力较小,在后续计算中将不作为研究对象。
最大应力出现在爆发压力作用下的曲柄销圆角的关键点1处,max σ=125.985MPa 。
根据机械工程材料手册提供的材料40Cr 经调质处理的强度结果计算得到抗拉极限S b 为827.64MPa ,屈服极限S σ为649.93MPa 。
由于max σ<S σ,即理论上该曲轴不回发生屈服断裂,可以进行可靠性分析。
另有,最大位移、应变点出现在曲轴壁处,与过渡圆角无关,且对性能影响不大,不予讨论。
6. 可靠性分析
⏹ 静强度可靠性分析 ➢ 随机变量的选择
在工况稳定时,发动机转速变化不大,在确定性分析中假设拉应力也变化不大,即忽略因转速变化所引起合成应力变化。
曲轴销半径R 1,圆角半径R 2,燃气压力载荷P 0,连杆1的惯性力P 1,连杆2的惯性力P 2,材料属性-弹性模量E 等参数设定为随机变量,考虑这些参数的不确定性对曲轴可靠性的影响。
各随机变量的分布情况如表2所示;
R 1(mm ) R 2(mm ) P 0(N ) P 1(N ) P 2(N ) E (GPa ) 分布 均匀
均匀
正态 正态 正态 正态 均值
005
.0004
.07
+-
002.0002
.03
+-
2.8*105
7.0*104
4.4*104
193.75
标准差 0.0015 0.0007 2.5*104
8.0*103
4.4*103
16.52
➢
建立状态方程
根据应力强度干涉模型,设定极限状态方程,如下式所示:
g=s-stress
stress=f(R1, R2, P0, P1, P2,E)
其中s=
S σ,stress 为调用有限元模型求解得到。
➢进行概率计算
在NESSUS软件中的分析方法页中选择AMV+的分析方法,使用该方法计算曲轴的静强度可靠度,并设置置信度为95%,取样误差为0.01。
该方法14次迭代,得出失效概率为4.264446*10-8,可靠度约为100%。
可认为该曲轴在最大静应力作用下不失效。
➢灵敏度分析
通过灵敏度分析,若某因素对结构失效影响较大,则在设计制造过程中进行严格控制,以保证有较好的可靠性。
该曲轴的灵敏度分析结果如图4所示;
图4 灵敏度分析结果
由灵敏度分析结果可知:
✓最大爆发力的均值与标准差对可靠度的影响较大,因此如果要提高发动机的静强度可靠度可以对最大爆发力的分布情况加以控制;
✓曲轴圆角半径的尺寸参数对曲轴的可靠度影响很小,因此可以放宽对圆角半径处的尺寸公差的要求。
✓材料参数弹性模量对静强度的可靠性影响也很小,在后面的疲劳可靠性分析中,可以将该变量作为确定性的值看待。
⏹疲劳可靠性分析
作为往返运动的活塞,在其寿命周期内,会有很多次循环运动,因此在弯扭载荷作用下的高周疲劳是其主要失效模式。
σ=422MPa,根据参考文献2可知,材料40Cr的对称弯曲疲劳强度极限
1-
标准差为10.1MPa;
根据参考文献3可知,尺寸系数C均值为0.79,标准差为0.069;由于表面采用抛光加工,因此表面加工系数B均值为1.1322,标准差为0.04344;应力集中系数K=1+q(afa-1),其中q为应力集中敏感系数,其均值为0.65,标准差为0.0167,afa为理论应力集中系数,值为1.854;因此可值应力集中系数K的均值为1.555,标准差为0.0142。
如表3所示;
表3 疲劳系数分布类型
尺寸系数C 表面加工系统B 应力集中系数K
分布正态正态正态
均值0.79 1.1322 1.555
标准差0.069 0.04344 0.0142
根据疲劳强度和疲劳应力的干涉模型,在NESSUS软件中建立状态方程如下所示:
g=R-S
smin = f2(P21, P22)
smax = f1(P10, P11, P12)
r = smin/smax
sra = (1-r)*s1/2
srm = (1+r)*s1/2
src = sqrt(srm**2+sra**2)
R = c*b*src/k
sa = -(smax-smin)/2
sm = -(smax+smin)/2
S = sqrt(sm**2+sa**2)
如图5所示;
图5 NESSUS 状态方程界面
使用NESSUS软件中标准蒙特卡罗法(MC)、响应面法(RSM)、二阶矩法、AMV+、AMV_AIS组合法得到关键点1的疲劳可靠度结果如表4所示;
表4 分析结果
MC RSM SORM AMV+ AMV_AIS 可靠度指标 3.962 3.901 3.978 3.986 3.962
失效概率值0.36E-4 0.48E-4 0.35E-4 0.34E-04 0.37E-4 可靠度值0.999964 0.999952 0.999965 0.999966 0.999963 7.结论
根据上述分析结果可知,该曲轴的静强度可靠度基本为1,且其在在一百万次疲劳寿命条件下的,疲劳可靠度为0.99996,满足工程可靠性要求。