变换催化剂积碳处理办法
转化催化剂硫中毒的原因和处理

转化催化剂硫中毒的原因和处理肖春来(辽宁葫芦岛锦西石化分公司,辽宁葫芦岛125001) 2007-11-14 制氢转化过程中,硫对转化催化剂具有明显的毒害作用,因硫中毒导致转化催化剂失活甚至报废的情况时有发生,给炼厂造成巨大的经济损失。
为保证装置安全生产,保证转化催化剂长周期运行,需要高度重视硫对催化剂的危害。
1 硫的来源硫是转化催化剂最主要的毒物之一,制氢原料中均含有不同量的硫。
随着焦化干气制氢技术的普及,原料含硫量也在进一步增加。
脱硫单元效果变差,是使硫进入转化系统的最直接来源,大多数时候是由于加氢条件异常使原料中的有机硫氢解不完全,导致脱硫剂出现硫穿透现象;也可能由于原料中的硫含量在短时间内大幅度上升致使加氢脱硫能力不足引起硫穿透。
此外,汽包给水也有可能带入一定量的硫酸根。
2 硫对转化催化剂的危害硫是转化催化剂最常见、也是难以彻底清除的毒物。
不同的制氢原料含有不同量的硫,硫存在的形态十分复杂,大致可分为有机硫和无机硫。
常用的干法脱硫流程是先用加氢催化剂将有机硫氢解成无机硫H2S,然后用脱硫剂将无机硫脱除。
现有工业装置的脱硫精度一般能达到小于0.5×10-6或小于0.2×10-6的水平,残余的微量硫进入转化系统。
转化催化剂具有一定的抗硫性能,就目前常用的转化催化剂而言,脱硫气中硫含量小于0.5×10-6时,能够保证转化催化剂正常发挥活性,可以保证转化催化剂长期使用。
但是,如果进入转化催化剂的硫含量超标,将会引起转化催化剂中毒。
转化催化剂中毒是可逆的。
一般情况下,硫主要引起转化炉上部催化剂中毒,而不易引起整个床层中毒,硫严重超标时也会导致整个系统被污染。
硫中毒后的转化催化剂可以通过蒸汽再生而恢复活性。
转化催化剂严重硫中毒将使转化催化剂严重失活甚至报废。
3 硫中毒的机理转化催化剂中毒一般认为是硫化氢与催化剂的活性组分镍发生了反应:硫化氢使活性镍变成非活性的Ni3S2,因而使转化催化剂活性下降甚至失活。
工业除去催化剂积碳的方法

工业除去催化剂积碳的方法嘿,朋友们!今天咱来聊聊工业除去催化剂积碳这个事儿。
你说这催化剂啊,就像是工厂里的小能手,一直在默默地干活儿。
可时间一长,它也会被积碳这个“小淘气”给缠上。
咱就打个比方吧,这催化剂就好比是一辆汽车,跑得久了,发动机里就会有积碳,影响它的性能。
那怎么给催化剂“洗洗澡”,去掉这些积碳呢?有一种方法叫燃烧法。
这就好像给催化剂来一场“大火烧烤”,把积碳给烧得干干净净。
但这火候可得掌握好啊,要是太猛了,把催化剂也给伤着了,那不就糟糕啦?所以得小心翼翼地操作。
还有一种方法是用化学药剂去清洗。
这就像是给催化剂做个“高级SPA”,用专门的药剂把积碳一点点地溶解掉。
但这药剂可得选对了呀,不然不但积碳没除掉,还可能带来其他麻烦呢!有时候呢,还可以用蒸汽去吹扫。
这就像给催化剂来一阵温暖的“春风”,把积碳轻轻地吹走。
不过这风也不能太大,不然会把催化剂也给吹跑啦!那在实际操作中,可得注意很多细节哦!要根据催化剂的特性和积碳的情况,选择合适的方法。
就像医生看病一样,得对症下药。
而且在操作过程中,要时刻关注催化剂的状态,稍有不对就得赶紧调整。
不然等出了问题再后悔,那可就来不及咯!你想想,如果不及时除掉积碳,催化剂的效率就会下降,那生产还能顺利进行吗?那肯定不行啊!这就好比是人的身体里有了毒素,不排出去能舒服吗?所以啊,我们一定要重视这个问题。
在工业生产中,我们可不能小瞧了这些细节。
每一个环节都关系到最终的产品质量和生产效率。
就像盖房子,一块砖没放好,可能整座房子都会不稳。
所以啊,对于催化剂积碳的问题,我们一定要认真对待,不能马虎。
总之呢,工业除去催化剂积碳可不是一件简单的事儿,需要我们有耐心、细心和专业知识。
只有这样,才能让我们的工业生产像一辆顺畅的汽车一样,快速前进!原创不易,请尊重原创,谢谢!。
连续重整装置催化剂粉尘异常分析及应对措施

连续重整装置催化剂粉尘异常分析及应对措施李江山【摘要】通过对催化重整装置粉尘异常现象的归纳总结,分别阐述了粉尘异常时还原段、反应器、催化剂输送系统、再生器、闭锁料斗以及分离料斗的现象及危害.同时,从操作和设备两个方面分析了粉尘淘析、进料工况、设备安装、催化剂烧焦等导致的粉尘异常原因,并提出了相应的处理措施.为催化重整装置异常工况的处理及日常操作提供了一定的借鉴意义.【期刊名称】《广州化工》【年(卷),期】2019(047)008【总页数】3页(P125-127)【关键词】催化重整;粉尘;堵塞;差压;约翰逊网【作者】李江山【作者单位】中海油惠州石化有限公司,广东惠州 516086【正文语种】中文【中图分类】TE624根据UOP定义,粉尘指直径小于1.2 mm的催化剂半颗粒及破碎催化剂颗粒。
按照粉尘产生的原因,可分为摩擦以及由温度和压力的剧烈变化导致的催化剂颗粒的破裂两个方面。
摩擦产生的粉尘,在多数情况下是重整装置产生粉尘的主要原因。
摩擦导致粉尘量的大小与两个方面有关,一是催化剂的强度;二是与催化剂接触的输送管道、约翰逊网(Johnson screen)、环形挡板等的表面因为粉尘附着、施工打磨不彻底导致摩擦力变大。
压力、温度的剧烈波动也是产生粉尘的原因之一。
对于有闭锁料斗的装置而言,闭锁料斗承担着将催化剂从低压往高压输送的功能。
因此催化剂在短时间内承受压力的变化,可能会导致粉尘的产生。
再生烧焦前后的温度波动非常大,催化剂在短时间内温升近400 ℃。
而再生器烧焦后,一般进行干燥和冷却,同样存在温度急剧下降的情况。
本文主要讨论的是粉尘增多导致的问题,从操作和设备两个方面对粉尘的产生进行分析。
1 粉尘增多的现象及危害粉尘在某部位异常增多之后的现象各有不同,且粉尘量的不同,表现也存在差异。
因此,该部分是一些装置已经出现过得异常现象,并且部分是粉尘严重增多的异常现象。
1.1 还原段粉尘增多现象及危害(1)还原尾氢出口过滤网反复堵塞,还原尾氢排放不畅。
甲醇制烯烃反应中的催化剂积碳机理

甲醇制烯烃反应中的催化剂积碳机理柴涵语(中国石油乌鲁木齐石化公司研究院,新疆乌鲁木齐830019)摘要:MTO反应中产生的碳沉积物会导致分子筛催化剂的孔隙和活性位点的堵塞,加速其性能下降而失去活性。
文中从催化剂积碳物质形成机理出发,阐述了MTO反应中催化剂积碳形成的影响因素,包括分子筛酸性、孔径结构及反应条件等;分析了积碳对催化剂及MTO反应产物选择性的变化。
得到结论,催化剂孔道和空腔内产生的芳香族中间物的大量沉积形成焦炭分子是致使催化剂失活的主要原因,为改进催化剂及工艺技术开发提供研究依据。
关键词:甲醇;烯烃;分子筛催化剂;积碳中图分类号:TQ426.94文献标识码:B文章编号:1671-4962(2023)01-0011-04 Mechanism of catalyst carbon deposition in methanol to olefin reactionChai Hanyu(Research Institute,PetroChina Urumchi Petrochemical Company,Urumchi830019,China)Abstract:In the MTO reaction,the carbon deposition produced will lead to the blockage of the pores and active sites of the molecular sieve catalyst,thus accelerating the decline of its performance and the loss of activity.Based on the formation mechanism of catalyst carbon deposition material,this paper describedthe influencing factors of catalyst carbon deposition in MTO reaction, including acidity of molecular sieve,pore size and reaction conditions,analyzed the change of selectivity of carbon deposition on catalyst and MTO reaction products.The results showed that coke molecules formed by large amount of aromatic intermediates deposited in catalyst channels and cavities during the reaction process were the main cause of catalyst deactivation,which provided research basis for improving catalyst and technological development.Keywords:methanol;olefin;molecular sieve catalyst;carbon deposition随着原油储量的减少,石油化工产品尤其是乙烯、丙烯的需求量明显增加,代替原料工艺引起了学者们的研究热潮,包括乙烯、丙烯和丁烯在内的轻质烯烃成为现代化工产品的重要构成之一[1,2]。
贵金属催化反应中的积碳问题

贵金属催化反应中的积碳问题2016-05-15 13:05来源:内江洛伯尔材料科技有限公司作者:研发部积碳催化剂的再生贵金属催化剂,特别是铂钯类,在石油化工行业用量很大。
催化剂在使用一段时间后活性明显下降,且催化剂表面混杂有大量的含碳物种,工业上称这种类型的失活为积碳现象。
1、什么是积碳以含碳化合物为原料的催化反应的第一步通常是在催化剂表面上进行吸附形成含碳物种,如含碳物种经过分解、聚合等反应生成碳或焦炭沉积在催化剂表面,即所谓的积碳或结焦。
积碳会堵塞催化剂的活性位或催化剂的孔道,从而导致催化剂的失活!2、积碳产生的原因积碳主要产生于热裂解和催化裂解过程。
热裂解积碳是气相有机原料在高温下热裂解形成烟炱、焦油,它们在催化剂表面上生成有序的或无序的碳;催化积碳是在催化剂的作用下,烃类化合物发生催化积碳反应,它与催化剂的性质密切相关。
3、积碳的形态积碳的形态一般分为无定形碳、层状石墨碳、管须状结晶碳以及粘稠状液态碳或焦油。
4、如何防止积碳防止积碳主要有以下几种路线:合金化,如Pt重整催化剂中添加第二组分金属形成合金,可减缓催化剂的积碳;添加助剂,Pt重整催化剂采用少量Cl改性,可以减缓酸性积碳;利用载体活性组分的相互作用,降低积碳;对于酸性催化剂或载体,添加碱性助剂(K2O、MgO),减弱酸性积碳;通入水蒸气,消碳;添加其他元素如稀土,加速消碳,防止积碳。
5、积碳的再生催化剂因为积碳而失活,其催化剂再生通常采用烧碳的方法可以部分恢复催化剂的活性。
烧碳条件如气氛、温度、气体组分等都会影响到再生后催化剂的结构、物化性质以及催化性能,因此必须严加控制。
几条注意事项(三步骤):1)除催化剂上的烃类和挥发物,必须在惰性气氛下进行;2)除去硫和轻质碳,必须在低温250-350度下先使金属氧化除去硫,同时某些聚合物和轻质碳也随之除去;3)最后除碳,根据碳的量以及类型在较高温度下进行。
催化剂的处置知识

不可逆中毒:不可以再生的、永久性的中毒。
例如:合成氨反应中,H2S会使Fe催化剂不可逆中毒
H 2S Fe FeS
1、金属催化剂的中毒
金属催化剂的三类毒物:
1)第VA族和VIA族元素具有孤对电子的非金属化合物,如N、P、As、Sb和O、S、 Se、Te的化合物
• 例如:在把炔烃还原为烯烃的过程中,如果直接用钯做催化剂会把炔烃直接还原为烷烃,此 时就需要对催化剂毒化(即钝化)通常是用吡啶或者醋酸铅做毒化剂,在碳酸钙的载体上 进行催化!
• 例如:“干法硫化”,催化剂应该是以分子筛为载体,必须进行钝化。因为分子筛催化剂, 如果直接接触原料,反应器顶部催化剂会发生剧烈反应,迅速积碳,导致催化剂积碳失活, 反应器床层压降增大,影响长周期运转。钝化的目的就是抑制催化剂硫化后的初始活性, 使其活性稳定在一个合适的状态。常用的钝化方法就是向系统中注氨,用氨与酸性中心结 合,抑制部分催化剂的酸性中心,让催化剂的性能慢慢释放出来。
颗粒破碎 结污
结果
表面积减少,堵塞 表面积减少和催化活性降低 活性位减少
表面积减少 活性组分丧失和表面积减少 催化剂组成改变,表面积减少 活性位减少 活性组分减少 催化剂床层沟流,堵塞 表面积减少
失活原因总结
1、结焦 2、金属污染 3、毒物吸附 4、烧结 5、生成化合物 6、相转变和相分离 7、活性组分被包围 8、组分挥发 9、颗粒破裂 10、结污
学习重点、难点
课程重点:催化剂的钝化、失活与再生 课程难点:再生实例
目录
CONTENTS
PART 01 催化剂的钝化 PART 02 催化剂的失活与再生 PART 03 再生实例 PART 04 课后习题
重整反应器器壁积碳原因分析及预防措施

重整反应器器壁积碳原因分析及预防措施摘要连续重整装置在石油加工产业链中占据着举足轻重的地位,对于炼化企业的整体物料平衡和效益提升起着至关重要的作用。
作为大型炼化企业最重要的二次加工装置之一,连续重整装置可以把上游装置来的廉价石脑油通过重整反应转化成高效的汽油产品和化工产品,同时富产氢气和液化气,供其它用氢装置使用。
但是,随着连续重整工艺的不断发展和重整反应苛刻度的不断提高,重整装置在运行中出现的问题也层出不穷,其中重整反应器器壁积碳问题就是其中之一,重整反应器器壁积碳严重影响重整装置的安稳运行,必须采取有效的措施加以预防和控制。
本文通过对重整反应器器壁积碳的原因进行详细的分析,提出有效的预防和控制措施,从而保证重整装置的长周期安稳运行。
关键词连续重整;反应器;器壁;积碳;丝状碳;硫含量1 概述某连续重整装置于2018年9月建成投产,装置由70万吨/年预加氢、140万吨/年连续重整、1360kg/小时催化剂连续再生以及配套的公用工程部分组成。
本装置以直馏石脑油、渣油加氢石脑油和加氢裂化重石脑油为原料,生产拔头油、戊烷油、C6~C7馏分(抽提装置原料)、混合二甲苯(去PX装置)、C9C10高辛烷值汽油调和组分、重芳烃,同时副产H2和液化气等产品。
装置设计操作弹性为60~110%,年开工时间为8400小时。
重整反应部分采用UOP超低压连续重整工艺技术及R-334 催化剂,平均反应压力0.35MPa,反应温度536℃,体积空速1.6h-1,氢烃分子比2.5:1(体积分数),C5+馏份辛烷值为RON105.2。
重整4台反应器采用并列2台+2台叠置式,物流为上进上出,降低了反应-再生构架高度。
作为连续重整工艺核心部分的催化剂再生系统采用美国UOP公司最新的CycleMaxⅢ工艺技术,并采用Chlorsorb工艺技术回收再生放空气体中的氯,在Chlorsorb氯吸附后又增加了再生气脱氯设施。
2 装置存在的主要问题装置自2018年9月投产运行至今,总体运行比较平稳,但是催化剂再生系统因为仪表原因、阀门故障、保温伴热不到位、催化剂提升管线不畅等原因发生多起热停车事件。
最正确的清洗三元催化器方法

最正确的清洗三元催化器方法清洗三元催化器是保持汽车排放系统正常工作的重要步骤。
在使用过程中,由于燃油质量不佳、行驶环境差、长期低速行驶或高速行驶等原因,三元催化器内部会积累大量毒害物质,降低其效能。
本文将从三个方面,分别是物理方法、化学方法和综合方法,详细介绍最正确的清洗三元催化器方法。
一、物理方法清洗三元催化器物理方法清洗三元催化器是利用物理力学原理和化学反应原理来清洗催化器内部积累的杂质和毒害物质。
常用的物理方法有冲洗、振动和烘烤等。
1. 冲洗:使用特殊清洗剂,将其注入催化器并通过加压装置进行物理冲洗。
冲洗可以有效去除催化器内的碳颗粒和沉积物,但有些情况下无法完全清除催化剂表面的污垢。
2. 振动:利用机械振动装置将催化器进行振动,使其中的杂质和毒害物质脱落。
振动清洗可以有效去除杂质和污垢,但严重剧烈振动可能导致催化剂层烧结,进而影响催化器效能。
3. 烘烤:将催化器置于高温环境下进行烘烤,通过高温将积聚在催化剂表面的杂质和毒害物质烧掉。
烘烤是一种较为简单的清洗方法,但高温烘烤可能影响催化剂活性和寿命。
以上物理方法具备不同的优缺点,在选择时需根据实际情况进行合理选择。
二、化学方法清洗三元催化器化学方法清洗三元催化器是利用酸碱性强的清洗剂和化学反应来清除催化剂内的积碳和杂质。
常见的化学方法有酸洗和还原剂处理等。
1. 酸洗:使用酸性清洗剂将催化器表面的碳堆积进行酸性酸洗,将碳及污垢溶解破坏。
酸洗具备快速、高效的优点,但一些有机物质可能会对酸洗剂产生抗性,使清洗效果降低。
2. 还原剂处理:使用具有还原性能的溶液进行催化器的还原反应,将其中的积碳还原成水和二氧化碳等易于排除的物质。
还原剂处理方法较为温和,但需要选择合适的还原剂,以免对催化剂表面产生不良影响。
三、综合方法清洗三元催化器综合方法清洗三元催化器是结合物理和化学方法进行清洗,以充分发挥各种方法的优点。
常见的综合方法有超声波清洗和脉冲气流清洗。
1. 超声波清洗:通过将催化器置于装有清洗液的超声波槽中,利用超声波的机械振动作用和溶解反应来清洗催化剂。
化学工程中的催化剂失活方法

化学工程中的催化剂失活方法催化剂是化学工程中常用的一种材料,能够加速化学反应速率而不被反应消耗。
然而,随着时间的推移,催化剂会逐渐失去其活性,这被称为催化剂的失活。
催化剂失活对化学工程的效率和经济性有重要影响。
本文将探讨化学工程中常见的催化剂失活方法,并提供相应的解决方案。
1. 催化剂中的积碳催化剂在某些反应中可能发生积碳现象,导致催化剂活性降低或完全失活。
积碳会堵塞催化剂表面上的活性位点,降低催化剂的反应活性。
为解决这一问题,可以采取以下措施:- 改变反应条件:调整反应温度、压力等条件,以减少积碳的发生。
- 催化剂再生:将受积碳影响的催化剂进行再生,通常会采用高温氧化或酸洗等方法,将积碳物质从催化剂表面清除。
2. 中毒催化剂可能会受到来自原料或反应产物的中毒物质的影响,导致活性降低或失活。
这些中毒物质可能会与催化剂表面发生不可逆的反应,降低催化剂的反应活性。
解决方法如下:- 原料预处理:对原料进行预处理,去除或减少中毒物质的含量。
- 催化剂改良:通过改变催化剂的成分或结构,使其对中毒物质的敏感性降低。
3. 硫化催化剂常常受到硫化物的影响,从而降低其活性。
硫化物可以与催化剂表面产生硫化物覆盖层,阻碍催化剂与反应物之间的接触。
解决方法如下:- 氧化:使用氧化剂将硫化物氧化为易于去除的形式。
- 催化剂再生:通过高温氧化或酸洗等方法,将硫化物从催化剂表面清除。
4. 机械磨损催化剂在使用过程中会受到机械磨损的影响,导致催化剂活性降低。
机械磨损可能来自于颗粒间的碰撞或流体中的剪切力。
为解决这一问题,可以采用以下方法:- 增加催化剂的强度:制备更坚硬或更耐磨损的催化剂材料,以延长其使用寿命。
- 优化反应系统设计:通过改变反应系统的结构、流动路径等,减少机械磨损的发生。
总结催化剂在化学工程中扮演着重要的角色,但失活是催化剂使用过程中常见的问题。
本文介绍了常见的催化剂失活方法,并提供了相应的解决方案。
通过了解催化剂失活问题的成因和解决方法,可以改善化学工程的效率和经济性,推动相关行业的发展。
炼油过程中的废催化剂,应该这样处理!

炼油过程中的废催化剂,应该这样处理!90%以上的石油化学反应是通过催化剂来实现的。
催化剂再生后原有的活性受损,多次再生后,活性低于可接受的程度时,就成为废催化剂。
随着石油化工业的迅速发展,石油化工废催化剂的产量也迅猛增长。
昨日,流程君看到后台有粉丝留言:这个内容确实关注地比较少,感谢@博雅久富同学给了小编一个很好的选题哦,下面,流程君搜集了一些资料,整理成文,供各位同仁参考。
石油化工废催化剂中往往含有一些有毒成分,主要是重金属和挥发性有机物,具有很大的环境风险,对其进行无害化处理处置显得尤为重要。
此外,石油化工废催化剂中有较高含量的贵金属或其他有价金属,有些甚至远高于某些贫矿中的相应组分的含量,金属品位高,可将其作为二次资源回收利用。
对石油化工废催化剂进行综合利用既可以提高资源利用率,更可以避免废催化剂带来的环境问题,实现可持续发展。
1、废催化剂有多少?据报道,全球每年产生废催化剂50万~70万吨,其中,废炼油催化剂占很大的比例。
随着我国炼油催化剂销量的逐年递增,废炼油催化剂的产生量也逐年增加。
如果不对废炼油催化剂加以科学管理,其中的有毒有害成分会污染环境并危害人体健康,并且其中的一些贵重金属资源也会流失。
因此,对废炼油催化剂进行有效的处理和利用已成为一个十分重要的课题。
目前,FCC催化剂的使用量占据了较大的市场份额,约为炼油催化剂总使用量的68.9%;加氢精制、加氢裂化和催化重整催化剂所占比例分别为9.4%,6.2%,3.3%;其他种类的炼油催化剂所占比例约为12.2%。
2015年我国石油消费量达到5.85亿吨(估算值),废炼油催化剂的产生量也达到20.7万吨(估算值)。
2、主要成分及含量几种催化裂化、加氢精制、加氢裂化和催化重整新鲜催化剂的主要成分及含量见表2。
由于催化剂反应活性的需要,有些新鲜催化剂本身就含有有毒有害成分。
如加氢精制与加氢裂化催化剂中含有NiO,属于致癌性物质。
炼油过程中,原油中的一些有毒有害成分会进入到催化剂中,废炼油催化剂的主要成分及含量见表3~4。
二氧化碳加氢催化剂 积碳

二氧化碳加氢催化剂积碳二氧化碳加氢催化剂在化学领域中扮演着重要的角色。
它可以将二氧化碳转化为有用的化学物质,从而实现碳资源的高效利用。
然而,使用二氧化碳加氢催化剂进行反应时,会出现积碳的问题。
积碳是指在催化剂表面上形成碳层,降低催化剂的活性,从而影响反应的效率和选择性。
因此,解决积碳问题成为了二氧化碳加氢催化剂研究中的一个重要课题。
为了解决积碳问题,科学家们进行了大量的研究和探索。
他们发现,积碳的原因主要有两个方面:一是催化剂表面与二氧化碳反应生成碳层;二是反应过程中产生的中间体在催化剂表面上发生聚合反应,形成碳层。
因此,科学家们提出了一系列解决方案。
改变催化剂的物理和化学性质,以提高其抗积碳能力。
例如,添加助剂可以改变催化剂的表面活性和稳定性,减少碳层的生成。
此外,改变催化剂的晶体结构和表面形貌,也可以增加催化剂与反应物之间的接触面积,提高反应效率。
优化反应条件,控制反应的温度、压力和反应物浓度等参数。
在适当的反应条件下,可以减少二氧化碳与催化剂表面的接触时间,从而降低碳层的生成。
此外,合理选择溶剂和添加剂,也可以起到抑制积碳的作用。
还可以采用周期性的活化和再生策略,即在反应过程中定期对催化剂进行再生,去除表面的碳层,以恢复催化剂的活性。
这种策略可以延长催化剂的使用寿命,提高反应的持续性和稳定性。
解决二氧化碳加氢催化剂积碳问题是一个复杂而又关键的问题。
通过改变催化剂的性质,优化反应条件,以及采用周期性的活化和再生策略,可以有效地降低积碳的程度,提高催化剂的稳定性和效率。
这将为二氧化碳的加氢转化提供更加可行和可持续的途径,为实现碳资源的高效利用做出重要贡献。
我们相信,在不久的将来,积碳问题将会得到更加全面和彻底的解决,为可持续发展做出更大的贡献。
催化剂积碳行为
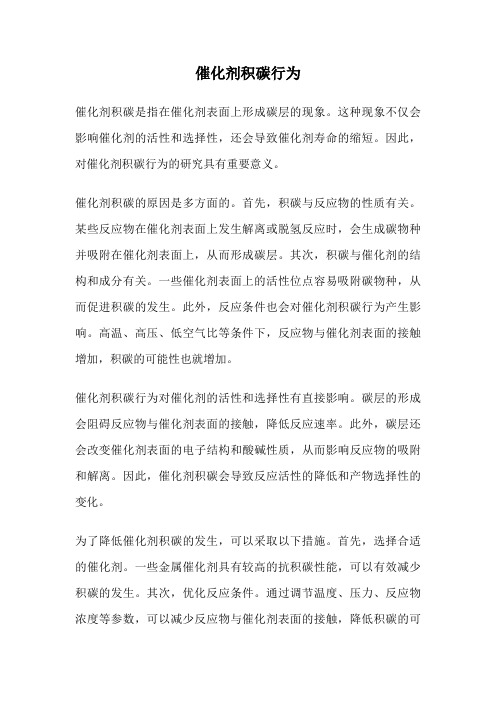
催化剂积碳行为催化剂积碳是指在催化剂表面上形成碳层的现象。
这种现象不仅会影响催化剂的活性和选择性,还会导致催化剂寿命的缩短。
因此,对催化剂积碳行为的研究具有重要意义。
催化剂积碳的原因是多方面的。
首先,积碳与反应物的性质有关。
某些反应物在催化剂表面上发生解离或脱氢反应时,会生成碳物种并吸附在催化剂表面上,从而形成碳层。
其次,积碳与催化剂的结构和成分有关。
一些催化剂表面上的活性位点容易吸附碳物种,从而促进积碳的发生。
此外,反应条件也会对催化剂积碳行为产生影响。
高温、高压、低空气比等条件下,反应物与催化剂表面的接触增加,积碳的可能性也就增加。
催化剂积碳行为对催化剂的活性和选择性有直接影响。
碳层的形成会阻碍反应物与催化剂表面的接触,降低反应速率。
此外,碳层还会改变催化剂表面的电子结构和酸碱性质,从而影响反应物的吸附和解离。
因此,催化剂积碳会导致反应活性的降低和产物选择性的变化。
为了降低催化剂积碳的发生,可以采取以下措施。
首先,选择合适的催化剂。
一些金属催化剂具有较高的抗积碳性能,可以有效减少积碳的发生。
其次,优化反应条件。
通过调节温度、压力、反应物浓度等参数,可以减少反应物与催化剂表面的接触,降低积碳的可能性。
此外,还可以采取预处理和再生等方法,清除催化剂表面的碳层,延长催化剂的使用寿命。
催化剂积碳是一个重要的研究课题。
深入了解催化剂积碳的机理和影响因素,对于提高催化剂的活性和选择性,延长催化剂的使用寿命具有重要意义。
通过合理设计催化剂和优化反应条件,可以有效降低催化剂积碳的发生,提高催化反应的效率和经济性。
炼油过程中的废催化剂处理【建筑工程类独家文档首发】

炼油过程中的废催化剂处理【建筑工程类独家文档首发】90%以上的石油化学反应是通过催化剂来实现的。
催化剂再生后原有的活性受损,多次再生后,活性低于可接受的程度时,就成为废催化剂。
随着石油化工业的迅速发展,石油化工废催化剂的产量也迅猛增长。
石油化工废催化剂中往往含有一些有毒成分,主要是重金属和挥发性有机物,具有很大的环境风险,对其进行无害化处理处置显得尤为重要。
此外,石油化工废催化剂中有较高含量的贵金属或其他有价金属,有些甚至远高于某些贫矿中的相应组分的含量,金属品位高,可将其作为二次资源回收利用。
对石油化工废催化剂进行综合利用既可以提高资源利用率,更可以避免废催化剂带来的环境问题,实现可持续发展。
1、废催化剂有多少?据报道,全球每年产生废催化剂50万~70万吨,其中,废炼油催化剂占很大的比例。
随着我国炼油催化剂销量的逐年递增,废炼油催化剂的产生量也逐年增加。
如果不对废炼油催化剂加以科学管理,其中的有毒有害成分会污染环境并危害人体健康,并且其中的一些贵重金属资源也会流失。
因此,对废炼油催化剂进行有效的处理和利用已成为一个十分重要的课题。
目前,FCC催化剂的使用量占据了较大的市场份额,约为炼油催化剂总使用量的68.9%;加氢精制、加氢裂化和催化重整催化剂所占比例分别为9.4%,6.2%,3.3%;其他种类的炼油催化剂所占比例约为12.2%。
2015年我国石油消费量达到5.85亿吨(估算值),废炼油催化剂的产生量也达到20.7万吨(估算值)。
2、主要成分及含量几种催化裂化、加氢精制、加氢裂化和催化重整新鲜催化剂的主要成分及含量见表2。
由于催化剂反应活性的需要,有些新鲜催化剂本身就含有有毒有害成分。
如加氢精制与加氢裂化催化剂中含有NiO,属于致癌性物质。
炼油过程中,原油中的一些有毒有害成分会进入到催化剂中,废炼油催化剂的主要成分及含量见表3~4。
由表3可见,废FCC催化剂表面可能沉积有Ni,V,Fe等重金属,少量的Na,Mg,P,Ca,As,Cu等元素也会沉积在废催化剂上。
三元催化除积碳方法

三元催化除积碳方法
嘿,朋友们!你们知道三元催化器吧?它就像是汽车的健康卫士!可要是它被积碳给缠上了,那可不得了!
咱说说三元催化除积碳的方法。
就好像给汽车做个深度清洁护理一样。
首先,定期跑高速,这就好比让汽车撒开脚丫子狂欢一场,高速气流能冲刷掉一些积碳呢,你说神奇不神奇!老张就跟我说过,他跑完高速,明显感觉车子有力多了!
然后呢,试试高品质的燃油,这就如同给车子喂上营养大餐,清洁的燃油能减少积碳的产生哟!比如我上次换了好油之后,那开车的感觉都不一样了。
还有啊,定期使用专门的三元催化清洁剂,这就像是给它来个泡泡浴,能有效溶解积碳呢!我朋友小李就对这个方法特别推崇。
所以啊,咱们可得好好爱护咱的汽车,别让三元催化被积碳给欺负了!三元催化器健康了,咱们的车子才能跑得更欢快呀!咱得重视起来,赶紧行动吧!。
三元催化剂积碳处理

三元催化剂是汽车尾气处理系统中常用的组件,用于减少尾气中的有害气体排放。
然而,长时间使用后,三元催化剂可能会因为碳的积聚而失去活性,从而影响其性能。
以下是一些处理三元催化剂积碳的方法:
1. 高速行驶:在适当的时机,例如公路行驶时,进行一段时间的高速行驶,可以增加催化剂温度,帮助燃烧和清除积碳。
2. 使用高质量燃油:使用高质量的燃油,例如具有较低硫含量和较高清洁添加剂浓度的燃油,可以减少积碳的发生。
3. 定期进行汽车维护:定期更换空气滤清器、点火系统和喷油器,以确保引擎正常运行,并减少积碳的产生。
4. 定期使用燃油添加剂:定期使用清洁添加剂来清除积碳,它们可以溶解和降解积聚在催化剂表面的碳。
5. 定期检查和清洁三元催化剂:可以定期检查和清洁三元催化剂,以去除积聚的碳。
这通常需要专业的汽车维修技师进行操作。
需要注意的是,在进行任何处理之前,建议咨询专业的汽车
维修技师或经验丰富的汽车保养专家,以确保正确和安全地处理三元催化剂的积碳问题。
高温变换催化剂简介

B117-3型高温变换催化剂简介B117-3型高温变换催化剂为满足中、小型合成氨厂的需要而开发的。
该催化剂具有良好的活性、稳定性和抗毒能力,能满足中串低和中低低变换工艺的需要。
一、B117-3型高温变换催化剂的化学组成和物理性质1. 化学组成氧化铁含量(以Fe2O3计)65%~75%氧化铬含量(以Cr2O3计)4%~6%特种助剂0.5%~2.0%2.物理性质外观:具有金属光泽的棕褐色圆柱体规格:φ9mm⨯(7~9)mm堆比重: 1.4kg/L ~1.6kg/L比表面积:60m2/g ~80m2/g二、B117-3型高温变换催化剂的主要质量指标活性(按HG/T3544-1989检测,CO转化率)≥52%径向抗压碎力≥210N/cm烧失量≤10%三、B117-3型高温变换催化剂性能特点1.优异的低温活性。
变换炉入口温度280℃就能获得较高的转化率。
2.强度好。
B117-3型高温变换催化剂晶相以r-Fe2O3为主,确保了本产品具有更好的低温活性和高使用强度。
3.耐热稳定性好。
B117-3型高温变换催化剂提高了铬含量、分散均匀,且产品中基本不含六价铬,有效地提高了产品的耐热性能。
3.抗毒物能力强。
产品中添加了特殊的抗毒物助剂,提高了本产品的抗毒物能力。
4.易还原。
起始还原温度低,易还原,升温还原时间短,在200℃时就能开始还原。
B112、B112-2型高温变换催化剂简介B112-2型高温变换催化剂是一种新型铁铬系耐硫变换催化剂,该催化剂保持了B112型高温变换催化剂的优良耐硫性能,具有更高的活性和更好的稳定性。
B112、B112-2型高温变换催化剂适合于中小氮肥厂的中串低和中低低工艺,特别适用于煤制气中压变换工艺。
一、B112-2、112型高温变换催化剂的化学组成和物理性质1.化学组成氧化铁含量(以Fe2O3计)≥75%氧化铬含量(以Cr2O3计)≥6.0%总钼含量(以M O O3) 1%~2.2%特种助剂1%~2%2.物理性质外观:具有金属光泽的棕褐色圆柱体规格:φ9mm⨯(7~9)mm堆比重: 1.4kg/L ~1.6kg/L比表面积: 60m2/g ~80m2/g二、B112-2、B112型高温变换催化剂的主要质量指标活性(按HG/T3544-1989检测,CO转化率)≥52%平均径向抗压碎力≥210N/cm烧失量≤10%三、B112-2、B112型高温变换催化剂的性能特点1.由于采用了特殊的制备工艺,B112-2型高温变换催化剂以r-Fe2O3为主晶相,本催化剂具有较好的低温活性,催化剂投入运行后能保持较高的机械强度。
二段转化炉催化剂结焦原因分析及对策

('"*-())*&$ ())*##
)&$*!' )$)*%% )$$*"-
)-(*#' " #'#*#
)"&*'(
)%$*$) )!"*#!
()$*!' (--*"!
)-)*( ))"*("
装置开停车对催化剂的影响 在 " ###" $%# 二段转化催化剂具有较稳
定的结构活性和强度在 " &##" '%# 短期不熔 结收缩小不变形活性损失仍为正常运行可承 受的范围由于每次开停车添加或切断工艺空气 时二段转化炉内温度都会迅速产生温度突变从 !%# 突 升 到 " $## 或 正 常 运 转 温 度 急 剧 下 降 对二段转化炉催化剂造成热冲击$
图 ' 二段转化炉内催化剂情况 为了确保装置大修后经济运行% 对催化剂进
行了更换%卸出催化剂见图 ! 和图 $'
图 $ 卸出下部催化剂
收 稿 日 期 &!%!%,%-,!! (收 到 修 改 稿 日 期 &!%!%,'',''' 作 者 简 介 &胡 伟 艳 %女 %'&*$ 年 出 生 %本 科 学 历 %工 程 师 %!%%. 年毕业于重庆三峡学院化学工程与工艺专业% 现在重庆建峰化工 股份有限公司生产管理部从事工艺管理工作' 联系电话& '-&!$#)'$')(/,0123&'-#)$$!$-455"670'
催化剂装填方式的影响
甲醇合成工艺常出现的问题及解决办法
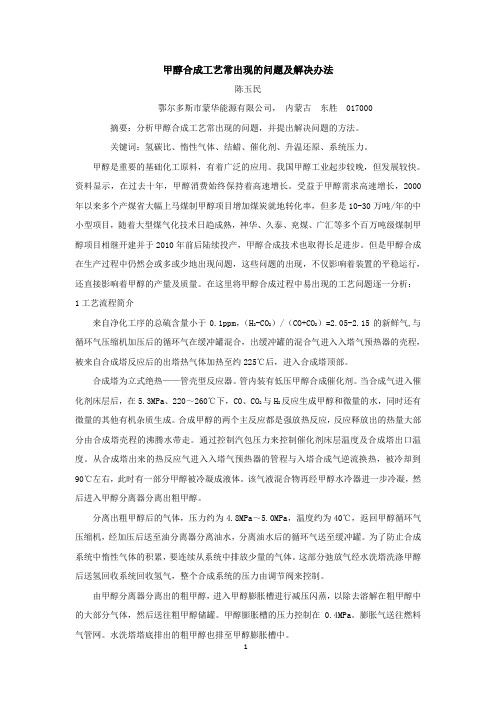
甲醇合成工艺常出现的问题及解决办法陈玉民鄂尔多斯市蒙华能源有限公司,内蒙古东胜 017000 摘要:分析甲醇合成工艺常出现的问题,并提出解决问题的方法。
关键词:氢碳比、惰性气体、结蜡、催化剂、升温还原、系统压力。
甲醇是重要的基础化工原料,有着广泛的应用。
我国甲醇工业起步较晚,但发展较快。
资料显示,在过去十年,甲醇消费始终保持着高速增长。
受益于甲醇需求高速增长,2000年以来多个产煤省大幅上马煤制甲醇项目增加煤炭就地转化率,但多是10-30万吨/年的中小型项目,随着大型煤气化技术日趋成熟,神华、久泰、兖煤、广汇等多个百万吨级煤制甲醇项目相继开建并于2010年前后陆续投产,甲醇合成技术也取得长足进步。
但是甲醇合成在生产过程中仍然会或多或少地出现问题,这些问题的出现,不仅影响着装置的平稳运行,还直接影响着甲醇的产量及质量。
在这里将甲醇合成过程中易出现的工艺问题逐一分析:1工艺流程简介来自净化工序的总硫含量小于0.1ppm,(H2-CO2)/(CO+CO2)=2.05-2.15的新鲜气,与循环气压缩机加压后的循环气在缓冲罐混合,出缓冲罐的混合气进入入塔气预热器的壳程,被来自合成塔反应后的出塔热气体加热至约225℃后,进入合成塔顶部。
合成塔为立式绝热——管壳型反应器。
管内装有低压甲醇合成催化剂。
当合成气进入催化剂床层后,在5.3MPa、220~260℃下,CO、CO2与H2反应生成甲醇和微量的水,同时还有微量的其他有机杂质生成。
合成甲醇的两个主反应都是强放热反应,反应释放出的热量大部分由合成塔壳程的沸腾水带走。
通过控制汽包压力来控制催化剂床层温度及合成塔出口温度。
从合成塔出来的热反应气进入入塔气预热器的管程与入塔合成气逆流换热,被冷却到90℃左右,此时有一部分甲醇被冷凝成液体。
该气液混合物再经甲醇水冷器进一步冷凝,然后进入甲醇分离器分离出粗甲醇。
分离出粗甲醇后的气体,压力约为4.8MPa~5.0MPa,温度约为40℃,返回甲醇循环气压缩机,经加压后送至油分离器分离油水,分离油水后的循环气送至缓冲罐。
vocs催化剂表面积碳

vocs催化剂表面积碳VOCs(挥发性有机物)是指在常温下易挥发的有机化合物,其排放对环境和人体健康都具有潜在风险。
为了减少VOCs的排放,催化剂被广泛应用于VOCs的处理过程中。
然而,长期使用后,催化剂表面积碳的积累会降低催化剂的活性和寿命。
本文将重点讨论催化剂表面积碳问题,并探讨如何解决这一问题。
一、催化剂表面积碳的形成原因1. 挥发性有机物的存在:VOCs中的有机分子在催化剂表面吸附并发生反应,形成碳沉积物。
2. 催化剂的结构和成分:催化剂的结构和成分决定了它的吸附能力和反应活性。
一些催化剂具有高表面积和丰富的活性位点,容易吸附和转化VOCs,但也更容易积累碳。
二、催化剂表面积碳对催化活性的影响1. 阻塞活性位点:催化剂表面积碳会覆盖活性位点,阻碍VOCs与催化剂之间的接触,从而降低催化剂的活性。
2. 影响物质传输:催化剂表面积碳会改变催化剂的孔隙结构和表面特性,阻碍反应物质在催化剂内部的传输,降低反应效率。
三、催化剂表面积碳的解决方法1. 物理方法:物理清洗是一种常用的去除催化剂表面积碳的方法。
通过高温燃烧或气流吹扫等方式,将表面积碳燃烧或吹离催化剂表面。
2. 化学方法:化学清洗是另一种常用的去除催化剂表面积碳的方法。
通过使用氧化剂、酸、碱等溶液对催化剂进行处理,使表面积碳发生氧化或溶解。
3. 表面改性:改变催化剂的表面特性可以防止表面积碳的积累。
例如,通过改变催化剂的结构、成分或添加助剂,可以增加催化剂的抗积碳能力。
4. 催化剂再生:当催化剂积碳严重影响其活性时,可以通过再生来恢复催化剂的活性。
再生方法包括高温热解、化学清洗等,可以去除催化剂上的表面积碳,并恢复催化剂的活性。
四、催化剂表面积碳的影响因素1. VOCs的种类和浓度:不同种类和浓度的VOCs对催化剂表面积碳的形成具有不同的影响。
一般来说,高浓度和复杂组分的VOCs更容易导致催化剂表面积碳的积累。
2. 反应条件:反应温度、压力、空气质量等因素都会影响催化剂表面积碳的形成。
- 1、下载文档前请自行甄别文档内容的完整性,平台不提供额外的编辑、内容补充、找答案等附加服务。
- 2、"仅部分预览"的文档,不可在线预览部分如存在完整性等问题,可反馈申请退款(可完整预览的文档不适用该条件!)。
- 3、如文档侵犯您的权益,请联系客服反馈,我们会尽快为您处理(人工客服工作时间:9:00-18:30)。
变换催化剂积碳如何处理?
摘自外厂家操作规程
1)联系检修导盲下列管线上的盲板。
2) 现场打开废气冷却器壳程排气阀、冷却水进口阀,待排气结束,现场关闭排气阀,打开冷却水出口阀,废气冷却器投用。
3) 联系检修导通下列管线的盲板并打开与盲板对应的截止阀:低压蒸汽管线、再生废气管线。
4) 确认中压蒸汽系统疏水器投运正常,蒸汽暖管合格后缓慢打开管线界区阀,中控微开控制阀,确认再生废气管线至放空管线打通,对变换炉进行蒸汽吹扫。
5) 中控控制变换系统压力在0.2~0.3MPa,蒸汽量逐渐增加至10000Kg/h。
现场调整蒸汽分配量约为: 124R101A:124R101B:124R102=1:1:10,床层升温速率控制在35~50℃/h之间,升压速率小于0.05MPa/分钟。
6) 中控控制蒸汽吹扫6小时,当124R101A/B和124R102床层温度均在350℃以上且恒温时,班长联系化验进行取样分析,分别在124SC-102A、124SC-102B和124SC-106取样点取样分析,连续三次分析结果均为CO+H2<0.5%、O2<0.5%为合格,每次分析间隔不小于10分钟。
7) 现场打开工艺空气124CA1001-150上的界区阀,中控缓慢打开空气控制阀124HV-1003。
确保O2含量占总体积的0.4%以下, 床层温度控制在350~450℃之间。
8) 中控控制催化剂床层温升不大于10℃时,开大控制阀124HV-1003,控制O2 含量为0.6%~0.8%。
催化剂床层温升基本消失后,恒温1小时,再逐渐加大O2含量为1%,温升消失后,将O2含量降至0.2%。
中控控制催化剂床层升温至410℃,催化剂床层最高温度不能超过450℃,变换炉升温速率为25~35℃/小时。
9) 中控再次通过控制阀124HV-1003将O2含量逐渐增至0.6%~0.8%,当床层温度稳定后,将O2含量逐渐增至3%,床层稳定在430℃恒温3小时,在124SC-102A、124SC-102B和124SC-106取样点取样分析,出口不凝气体中的CO2含量小于2%,而O2含量大于15%时认为再生过程结束。
10) 再生结束后,中控关小空气控制阀124HV-1003和蒸汽控制阀124HV-1004,确保变换炉床层以25~35℃/h的速率降温。
11) 中控控制变换炉入口温度降至250℃时,逐渐减少蒸汽量、加大空气量。
温度降至200℃时,关闭蒸汽控制阀124HV-1004,缓慢开大空气控制阀124HV-1003使床层逐渐冷却。
12) 中控控制床层温度降至50℃时,关闭控制阀124HV-1003,现场关闭前截止阀。
13) 现场关闭上述过程中打开的所有截止阀,联系检修,按要求导盲上述管线对应的盲板。
14) 如果催化剂需要再次使用,必须重新硫化,按4.3.4硫化程序进行,如果失活,则需卸出。
9.2.3再生注意事项
1) 再生过程中通入空气时,20分钟内床层温升不许超过50℃,如超过50℃须停止加入空气。
2) 严密监视蒸汽压力和流量的变化,如果蒸汽中断时,立即停止注入空气。
3) 在最后空气冷却过程中,如床层内有温升立即通入蒸汽,并降低甚至停止空气注入。
2014-12-02 海川论坛。