PCB沉锡工艺研究
pcb沉板工艺

pcb沉板工艺今天咱们来聊一个特别有趣的东西,叫PCB沉板工艺。
你知道吗?咱们身边好多电子产品都离不开一种小小的板子,就像它们的心脏一样。
这个板子就是PCB板,它可神奇啦。
那PCB沉板工艺呢,就像是给这个小“心脏”做一种特殊的打扮。
比如说,咱们想象一下,PCB板是一个小城堡。
这个城堡里住着好多小电子元件,就像城堡里住着很多小居民一样。
但是有时候呢,这个城堡的地面如果是平平的,那些小居民就会觉得有点拥挤,而且城堡看起来也不那么酷。
这时候,沉板工艺就像给城堡挖一些小坑或者小地下室一样。
有一次呀,我看到一个小小的手机充电器。
它里面的PCB板就用了沉板工艺。
那个小PCB板上有些地方是凹下去的,就像小池塘一样。
这样的话,那些小零件就可以住在这些“小池塘”里啦。
这样做有什么好处呢?就像咱们把东西都收拾到小盒子里一样,整个充电器就可以变得更小更精致。
再说说电脑的主板吧。
电脑主板就像一个超级大的城市,上面有超级多的小零件。
如果不做沉板工艺,那这个主板就会特别大,电脑机箱也就会变得很大很大。
可是呢,用了沉板工艺之后,就像在城市里挖了一些地下停车场一样,一些零件可以放在这些“地下停车场”里,主板就可以节省很多空间,电脑机箱也就不用做那么大啦。
还有呀,在一些智能手表里。
智能手表那么小,可是功能却那么多。
这其中就有PCB沉板工艺的功劳呢。
它的PCB板上有些小地方沉下去,那些小电子元件就像躲在小山洞里一样,整整齐齐的。
这样手表才能做得那么小巧玲珑,戴在手腕上就像一个小装饰品一样。
PCB沉板工艺就像一个小小的魔法,让那些小小的PCB板可以容纳更多的小零件,还能让我们的电子产品变得更小、更轻便、更漂亮。
下次当你拿着手机或者戴着智能手表的时候,你就可以想象一下,在它们小小的身体里,那些PCB板上的小“池塘”“地下室”“小山洞”,是不是很有趣呢?。
沉锡工艺原理简介
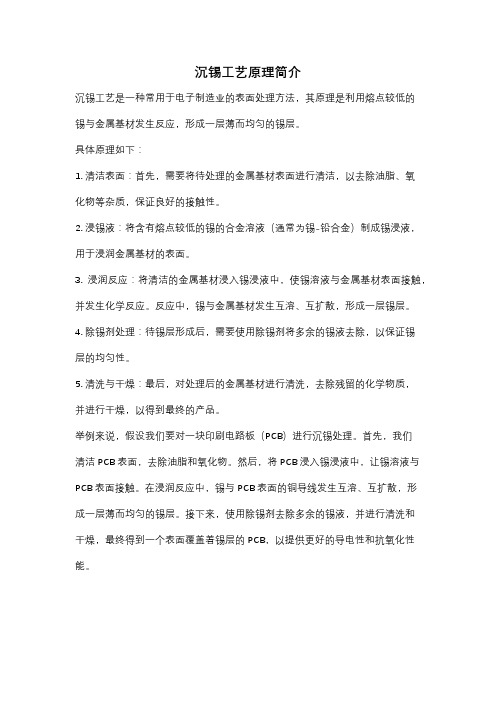
沉锡工艺原理简介
沉锡工艺是一种常用于电子制造业的表面处理方法,其原理是利用熔点较低的
锡与金属基材发生反应,形成一层薄而均匀的锡层。
具体原理如下:
1. 清洁表面:首先,需要将待处理的金属基材表面进行清洁,以去除油脂、氧
化物等杂质,保证良好的接触性。
2. 浸锡液:将含有熔点较低的锡的合金溶液(通常为锡-铅合金)制成锡浸液,用于浸润金属基材的表面。
3. 浸润反应:将清洁的金属基材浸入锡浸液中,使锡溶液与金属基材表面接触,并发生化学反应。
反应中,锡与金属基材发生互溶、互扩散,形成一层锡层。
4. 除锡剂处理:待锡层形成后,需要使用除锡剂将多余的锡液去除,以保证锡
层的均匀性。
5. 清洗与干燥:最后,对处理后的金属基材进行清洗,去除残留的化学物质,
并进行干燥,以得到最终的产品。
举例来说,假设我们要对一块印刷电路板(PCB)进行沉锡处理。
首先,我们
清洁PCB表面,去除油脂和氧化物。
然后,将PCB浸入锡浸液中,让锡溶液与PCB表面接触。
在浸润反应中,锡与PCB表面的铜导线发生互溶、互扩散,形
成一层薄而均匀的锡层。
接下来,使用除锡剂去除多余的锡液,并进行清洗和
干燥,最终得到一个表面覆盖着锡层的PCB,以提供更好的导电性和抗氧化性能。
沉锡基本工艺工作和问题处理

沉锡基本工艺工作和问题处理
沉锡是一种将锡融化后涂覆在金属表面上的工艺,常用于印刷电路板制造等领域。
具体的工艺步骤如下:
1. 准备工作:清洁金属表面,去除杂质和氧化物。
2. 准备锡料:将锡料熔化至适当温度,保持在一定范围内以保持流动性。
3. 涂覆锡料:将金属表面浸入熔化的锡料中,使其涂覆整个表面。
4. 接触时间:保持金属表面与锡料的接触时间适当,以确保锡层的均匀涂覆。
5. 去除多余锡料:将金属表面从锡料中取出,使多余的锡料自然滴落。
6. 冷却固化:待涂覆的锡料自然冷却,形成坚固的锡层。
在沉锡过程中常会遇到一些问题,需要及时处理:
1. 锡层太厚或不均匀:可能是由于接触时间不足或锡料温度不恰当。
解决方法是调整接触时间和锡料温度,确保涂覆均匀。
2. 锡球:在沉锡过程中,锡料容易形成小球状,无法均匀涂覆。
可以尝试调整锡料的温度和浸泡方式,避免锡球的产生。
3. 氧化:金属表面没有清洁干净或未及时涂覆锡料可能导致氧化的问题。
应确保金属表面干净,及时涂覆锡料,避免氧化的发生。
4. 粘附不良:可能是由于金属表面没有充分清洁或锡料质量不佳。
应仔细清洁金属表面,并使用质量良好的锡料。
以上是沉锡的基本工艺和问题处理的一般步骤和方法,具体处理方法可以根据实际情况进行调整。
喷锡与沉锡异同点及化学沉锡常见问题分析

喷锡与沉锡异同点及化学沉锡常见问题分析PCB沉锡工艺是为有利于SMT与芯片封装而特别设计的在铜面上以化学方式沉积锡金属镀层,是取代Pb-Sn合金镀层制程的一种绿色环保新工艺,已广泛应用于电子产品、五金件、装饰品等。
印刷线路板有两个较为常用的工艺:喷锡和沉锡。
喷锡,主要是将PCB板直接侵入到熔融状态的锡浆里面,在经过热风整平后,在PCB铜面会形成一层致密的锡层,厚度一般为1um-40um。
沉锡,主要是利用置换反应在PCB板面形成一层极薄的锡层,锡层厚度大约在在0.8um-1.2um之间,沉锡工艺更普遍应用在线路板表面处理工艺当中。
化学沉锡常见技术问题分析化学沉锡是PCB沉锡工艺的一种,应用较为普遍,其工作原理是通过改变铜离子的化学电位使镀液中的亚锡离子发生化学置换反应,其实质是电化学反应。
被还原的锡金属沉积在铜基材的表面上形成锡镀层,且其浸锡镀层上吸附的金属络合物对锡离子还原为金属锡起催化作用,以使锡离子继续还原成锡,其化学反应方程式为2Cu+4TU+Sn2→2Cu+(TU)2+Sn。
化学沉锡层的厚度大约在在1um-40um之间,表面结构较为致密,硬度较大,不容易刮花;喷锡在生产过程中只有纯锡,所以表面容易清洗,正常温度下可以保存一年,并且在焊接的过程中不易出现表面变色的问题;沉锡,锡厚大约在在0.8um-1.2um之间,表面结构较为松散,硬度小,容易造成表面刮伤;沉锡是经过复杂的化学反应,药剂较多,所以不容易清洗,表面容易残留药水,导致在焊接中易出现异色问题,保存时间较短,正常温度下可以保存三个月,如果时间久会出现变色。
化学沉锡板的主要缺陷表现为锡面发暗、锡面污染导致的可焊性不良问题,经过大量数据分析及现场调查,基本确定造成原因主要由以下几个方面,首先,生产过程药液拖带消耗:因锡槽药水具有粘度较大特性,致使生产带出量较大,从而导致锡槽药液消耗量大。
同时,由于锡槽槽液大量带入硫脲洗槽,造成硫脲洗槽铜含量上升快,影响生产板清洗效果,易。
沉锡PCB贴装后锡面发黑分析及改善
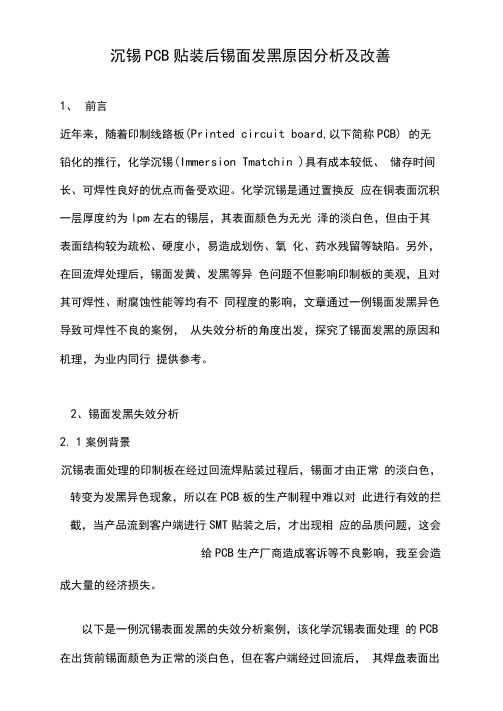
沉锡PCB贴装后锡面发黑原因分析及改善1、前言近年来,随着印制线路板(Printed circuit board,以下简称PCB) 的无铅化的推行,化学沉锡(Immersion Tmatchin )具有成本较低、储存时间长、可焊性良好的优点而备受欢迎。
化学沉锡是通过置换反应在铜表面沉积一层厚度约为lpm左右的锡层,其表面颜色为无光泽的淡白色,但由于其表面结构较为疏松、硬度小,易造成划伤、氧化、药水残留等缺陷。
另外,在回流焊处理后,锡面发黄、发黑等异色问题不但影响印制板的美观,且对其可焊性、耐腐蚀性能等均有不同程度的影响,文章通过一例锡面发黑异色导致可焊性不良的案例,从失效分析的角度出发,探究了锡面发黑的原因和机理,为业内同行提供参考。
2、锡面发黑失效分析2.1案例背景沉锡表面处理的印制板在经过回流焊贴装过程后,锡面才由正常的淡白色,转变为发黑异色现象,所以在PCB板的生产制程中难以对此进行有效的拦截,当产品流到客户端进行SMT贴装之后,才出现相应的品质问题,这会给PCB生产厂商造成客诉等不良影响,我至会造成大量的经济损失。
以下是一例沉锡表面发黑的失效分析案例,该化学沉锡表面处理的PCB 在出货前锡面颜色为正常的淡白色,但在客户端经过回流后,其焊盘表面出现上锡不良和锡面发黑的现象,如下图1所示:图1异色不良样品与正常样品锡面外观a-l・上锡不良焊盘(50X): a・2•上锡不良焊盘(100X):b・l•发黑PCBA外观图:b・2•正常沉锡表面颜色。
由上图1所示,不良PCBA锡面发黑与正常沉锡表面所呈现的淡白色明显不一致,且焊接面有退润湿现象,现通过失效分析手段来排查可焊性不良的原因,并探究锡面发黑的机理。
2.2失效原因排査2.2.1锡层厚发确认采用X-Ray测厚仪,对沉锡焊盘进行锡厚测量,结果如表1所示:表1锡厚数据(单位:gm )测量位置 1 2 3 4 A 平均要求测量结果 1.080 1.061 1.051 1.022 1.073 •航2 如表1所示,沉锡焊盘实测单点锡厚和平均锡厚都满足工艺控制要求。
PCB沉金工艺介绍解析
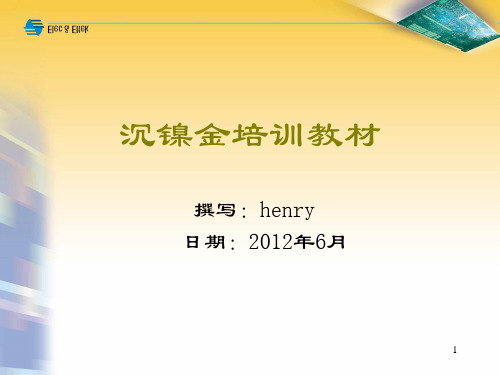
4、预浸
作用:
维持活化缸的酸度及使铜面在新鲜状 态(无氧化物)的情况下,进入活化缸。
操作条件:
温度: 时间: 搅拌: 槽材质: 室温 1±0.5min 摆动及药液循环搅拌 PVC或PP
18
作用: 在电化序中,铜位于镍的后面,所以必须 将铜面活化,才能进行化学镀镍。PCB行 业大多是采用先在铜面上生成一层置换钯 层的方式使其活化。 反应式:Pd2++Cu Pd+Cu2+ PCB沉镍金工序之活化剂一般为硫酸型和 盐酸型两种,现较多使用硫酸型钯活化液。 行业中也有使用Ru(Ruthenium)做催化 晶核,效果也较为理想。
42
操作条件
A、温度 不同系列的沉镍药水其控制范围不 同。一般情况下,镍缸的操作范围是 86±50C,有的药水则控制在81±50C。 具体操作温度应根据试板结果来定, 不同型号的制板,有可能操作温度不同。 一个制板的良品操作范围一般情况下只 有±20C,个别制板也有可能小于±10C.
41
•E、镀液应连续过滤,以除去溶液中的 固体杂质。镀液加热时,必须要有空气 搅拌或连续循环系统,使被加热的镀液 迅速扩散开。当槽内壁镀有镍层时,应 及时用硝酸(1:3)褪除,适当时可考虑加 热,但不可超过50OC, 以免污染空气。 •F、镀液寿命一般控制在4MTO(即Ni离 子添补量累积达到4倍开缸量),超过此 限主要问题是镍厚不足。
29
C、缓冲剂、络合剂 缓冲剂主要用处是维持镀液的pH值防止化学镀镍 时由于大量析氢所引起的pH值下降 络合剂作用主要是与镍离子进行络合降低游离镍 离子的浓度,提高镀液的稳定性。
一般均使用NaH2PO2,其控制浓度一般为2040g/l。在镀液中,主反应将Ni2+还原成为 金属Ni,副反应为其本身的歧化反应生成 单质P,主反应及副反应过程中均伴随H2逸 出。
PCB沉锡工艺研究
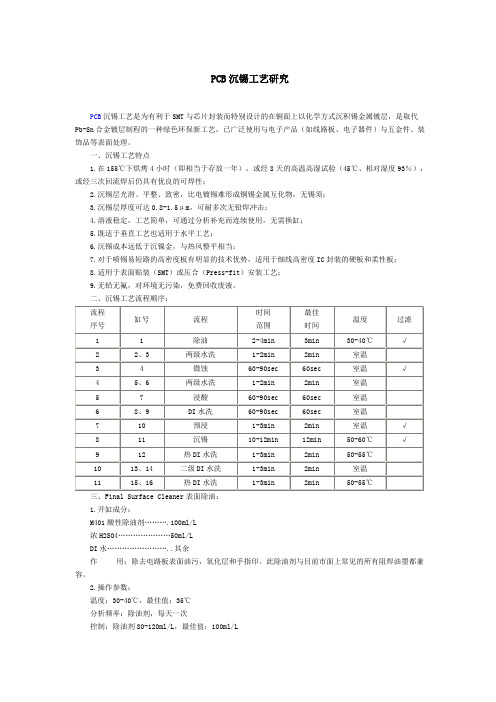
PCB沉锡工艺研究PCB沉锡工艺是为有利于SMT与芯片封装而特别设计的在铜面上以化学方式沉积锡金属镀层,是取代Pb-Sn合金镀层制程的一种绿色环保新工艺,已广泛使用与电子产品(如线路板、电子器件)与五金件、装饰品等表面处理。
一、沉锡工艺特点1.在155℃下烘烤4小时(即相当于存放一年),或经8天的高温高湿试验(45℃、相对湿度93%),或经三次回流焊后仍具有优良的可焊性;2.沉锡层光滑、平整、致密,比电镀锡难形成铜锡金属互化物,无锡须;3.沉锡层厚度可达0.8-1.5μm,可耐多次无铅焊冲击;4.溶液稳定,工艺简单,可通过分析补充而连续使用,无需换缸;5.既适于垂直工艺也适用于水平工艺;6.沉锡成本远低于沉镍金,与热风整平相当;7.对于喷锡易短路的高密度板有明显的技术优势,适用于细线高密度IC封装的硬板和柔性板;8.适用于表面贴装(SMT)或压合(Press-fit)安装工艺;9.无铅无氟,对环境无污染,免费回收废液。
二、沉锡工艺流程顺序:三、Final Surface Cleaner表面除油:1.开缸成分:M401酸性除油剂……….100ml/L浓H2SO4…………………50ml/LDI水……………………..其余作用:除去电路板表面油污,氧化层和手指印。
此除油剂与目前市面上常见的所有阻焊油墨都兼容。
2.操作参数:温度:30-40℃,最佳值:35℃分析频率:除油剂,每天一次控制:除油剂80-120ml/L,最佳值:100ml/L铜含量:小于1.5g/L补充:M401,增加1%含量需补充10ml/L过滤:20μ滤芯连续过滤,换缸时换滤芯。
寿命:铜含量超过1.5g/L或每升处理量达到500呎。
四、Microetch微蚀:1.开缸成分:Na2S2O4……………….120g/LH2SO4…………………40ml/LDI水………………….其余程序:①向缸中注入85%的DI水;②加入计算好的化学纯H2SO4,待冷却至室温;③加入计算好的Na2S2O4,搅拌至全溶解;④补DI水至标准位置。
消除PCB沉银层的技术和方法
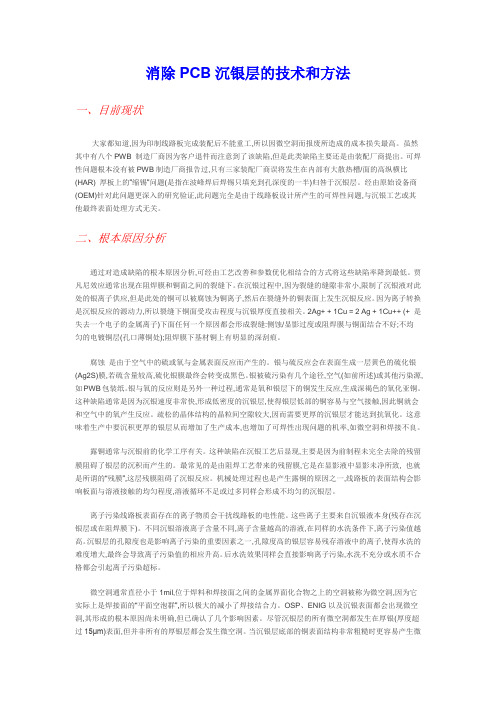
消除PCB沉银层的技术和方法一、目前现状大家都知道,因为印制线路板完成装配后不能重工,所以因微空洞而报废所造成的成本损失最高。
虽然其中有八个PWB 制造厂商因为客户退件而注意到了该缺陷,但是此类缺陷主要还是由装配厂商提出。
可焊性问题根本没有被PWB制造厂商报告过,只有三家装配厂商误将发生在内部有大散热槽/面的高纵横比(HAR) 厚板上的”缩锡”问题(是指在波峰焊后焊锡只填充到孔深度的一半)归咎于沉银层。
经由原始设备商(OEM)针对此问题更深入的研究验证,此问题完全是由于线路板设计所产生的可焊性问题,与沉银工艺或其他最终表面处理方式无关。
二、根本原因分析通过对造成缺陷的根本原因分析,可经由工艺改善和参数优化相结合的方式将这些缺陷率降到最低。
贾凡尼效应通常出现在阻焊膜和铜面之间的裂缝下。
在沉银过程中,因为裂缝的缝隙非常小,限制了沉银液对此处的银离子供应,但是此处的铜可以被腐蚀为铜离子,然后在裂缝外的铜表面上发生沉银反应。
因为离子转换是沉银反应的源动力,所以裂缝下铜面受攻击程度与沉银厚度直接相关。
2Ag+ + 1Cu = 2 Ag + 1Cu++ (+ 是失去一个电子的金属离子)下面任何一个原因都会形成裂缝:侧蚀/显影过度或阻焊膜与铜面结合不好;不均匀的电镀铜层(孔口薄铜处);阻焊膜下基材铜上有明显的深刮痕。
腐蚀是由于空气中的硫或氧与金属表面反应而产生的。
银与硫反应会在表面生成一层黄色的硫化银(Ag2S)膜,若硫含量较高,硫化银膜最终会转变成黑色。
银被硫污染有几个途径,空气(如前所述)或其他污染源,如PWB包装纸。
银与氧的反应则是另外一种过程,通常是氧和银层下的铜发生反应,生成深褐色的氧化亚铜。
这种缺陷通常是因为沉银速度非常快,形成低密度的沉银层,使得银层低部的铜容易与空气接触,因此铜就会和空气中的氧产生反应。
疏松的晶体结构的晶粒间空隙较大,因而需要更厚的沉银层才能达到抗氧化。
这意味着生产中要沉积更厚的银层从而增加了生产成本,也增加了可焊性出现问题的机率,如微空洞和焊接不良。
关于PCB化学沉锡常见技术问题的分析研究与改善

关于PCB化学沉锡常见技术问题的分析研究与改善作者:赵金亮来源:《中国新通信》2016年第24期【摘要】 PCB沉锡工艺是为有利于SMT与芯片封装而特别设计的在铜面上以化学方式沉积锡金属镀层,是取代Pb-Sn合金镀层制程的一种绿色环保新工艺,已广泛应用于电子产品、五金件、装饰品等。
印刷线路板有两个较为常用的工艺:喷锡和沉锡。
喷锡,主要是将PCB 板直接侵入到熔融状态的锡浆里面,在经过热风整平后,在PCB铜面会形成一层致密的锡层,厚度一般为1um-40um。
沉锡,主要是利用置换反应在PCB板面形成一层极薄的锡层,锡层厚度大约在在0.8um-1.2um之间,沉锡工艺更普遍应用在线路板表面处理工艺当中。
本文就PCB化学沉锡导致的可焊性不良的问题进行详尽的分析与研究,希望能给业界同仁一点启发。
【关键词】化学沉锡喷锡可焊性不良一、前言作为电子产业高速发展的基础工程,印制电路板(PCB)已是现代电子设备不可缺少的配件,无论上天下海之高端电子设备,还是家用电器和电子玩具都少不了负载电子元器件和电信号的PCB,PCB是随着整个电子信息产业的发展而发展的。
沉锡工艺是较为常见的一种线路板表面处理技术,主要目的是为了保证电子元器件和线路板之间连接的牢固、可靠,使电信号的传输更加稳定,由此可见,沉锡技术在线路板制造工艺中的应用还是十分重要的。
在实际生产过程中,化学沉锡也是有很多技术难题,沉锡不良、表面变色、厚度不均、厚度超差等等,这些问题了一直困扰着技术人员,本人根据这么多年的工作经验,结合自己扎实的理论基础,就化沉锡不良问题进行简要的剖析,具体如下。
二、化学沉锡常见技术问题分析化学沉锡是PCB沉锡工艺的一种,应用较为普遍,其工作原理是通过改变铜离子的化学电位使镀液中的亚锡离子发生化学置换反应,其实质是电化学反应。
被还原的锡金属沉积在铜基材的表面上形成锡镀层,且其浸锡镀层上吸附的金属络合物对锡离子还原为金属锡起催化作用,以使锡离子继续还原成锡,其化学反应方程式为2Cu+4TU+Sn2→2Cu+(TU)2+Sn。
PCB板上沉锡焊盘上锡不良失效分析

PCB 板上沉锡焊盘上锡不良失效分析
PCB 应用广泛,但由于成本以及技术的原因,PCB 在生产和应用过程中出现了大量的失效问题,并因此引发了许多质量纠纷。
为了弄清楚失效的原因以便找到解决问题的办法和分清责任,必须对所发生的失效案例进行失效分析。
沉锡焊盘上锡不良失效分析
1.背景:
送检样品为某PCBA 板,该PCB 板经过SMT 后,发现少量焊盘出现上锡不良现象,样品的失效率大概在千分之三左右。
该PCB 板焊盘表面处理工艺为化学沉锡,该PCB 板为双面贴片,出现上锡不良的焊盘均位于第二贴片面。
2.分析说明:
首先进行外观检查,通过对失效焊盘进行显微放大观察,焊盘存在不上锡。
沉锡工艺工作和问题处理

汕头超声印制板公司工作指示CHINA CIRCUIT TECHNOlOGY (SHANTOU) CORPORATIONWORK INSTRUCTION标题:沉锡工艺工作与问题处理TITlE:WORK INSTRUCTION FOR TECHNICS WORK TASK AND PROMBLEM TREATMENT文件编号:WI-Y1-ME-A 版本:0D O C U ME N T N O.:VERSIONNO.:生效日期:页数:E F F E C T I V ED A T E:PAGES:编写:日期:DRAFTED BY:DATE:审核:日期:AUDITED BY:DATE:批准:日期:APPROVED BY:DATE:工作指示修改表1.目的使新工艺人员了解沉锡的工艺工作要点及问题的处理2.适用范围沉锡工艺人员3. 注意内容3.1. 工艺控制注意事项:1.锡缸加药顺序及方法:首先添加基本剂LP,然后添加基本剂2000,循环20min后添加锡溶液C,循环10min后才能添加添加剂。
2.锡缸要特别提防含铁的物质进入,以免造成药水的报废;3.当药水中铜离子浓度较高时,用铜离子处理器进行冷却过滤,除掉铜离子,以免造成品质问题及药水报废;4.更换锡缸棉芯时由于气体未排尽使药水变得浑浊时,须及时将过滤桶中的气体排走,以免造成药水报废;3.3沉锡添加药水配制发红的调查和完善甲磺酸与Sn2+可以络合,有稳定Sn2+的作用;硫脲与Ag+有强的络合能力;当SF-C加入没有混合均匀即加入添加剂,即Sn2+和Ag+都没有被充分的络合情况下( Sn2+为还原剂和Ag+为氧化剂),导致局部发生如下反应:2Ag++Sn2+=2Ag↓+Sn4+生成单质银沉淀。
采取的完善措施延长加药间隔时间。
安排专人配药,全部白天配制培训员工树立正确操作意识,增强节约观念。
pcb电路板沉金工艺

pcb电路板沉金工艺
PCB电路板沉金工艺是常用的表面处理工艺之一,也称为ENIG (Electroless Nickel Immersion Gold)工艺。
其主要特点是先在铜板
表面镀一层镍,然后再在镍上沉积一层金,从而形成一个耐腐蚀、良好的
导电性表面保护层。
下面是pcb电路板沉金工艺的具体步骤:
1.清洗:将铜板表面的油污和氧化物清洗干净。
2.刻蚀:通过光刻技术,在铜板上形成电路图案。
3.钝化:通过化学钝化处理,对铜表面生成一层铜氧化物保护膜。
4.镀镍:在铜表面镀一层镍,获得更好的耐腐蚀性和可靠性。
5.清洗:将表面的杂质和化学残留物清洗干净。
6.沉金:在镀有镍的表面沉积一层金,形成一层良好的导电保护层。
7.清洗:清洗干净,去除任何残留物。
8.检验:对沉金之后的电路板进行检验和测试,确保其质量符合要求。
pcb电路板沉金工艺具有可控性强、导电性好、耐腐蚀性好等优点,
广泛应用于电子设备、通讯设备等领域。
PCB沉金工艺介绍解析
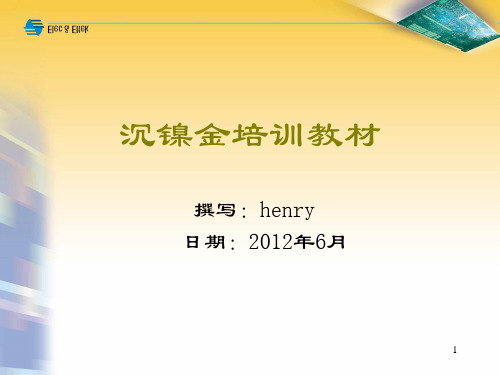
20 15 10 5 0 0 1 2 3 4 5 6
Ü Ò È º À Ï » ¯ ¶ È £ ¨MTO£ ©
35
ö ³ Î ö Ë Ù ¶ È Ó ë Ä ø Å ¨È ¶ ¹ Ø Ï µ 25
© Ì m/hr£ ¨¦ È £ Ù ¶ ö Ë ö ³ Î
24 23 22 21 20 19 4.8 5.2 5.9
24
3.小部分次磷酸根在催化氢的刺激下,产生 磷原子并沉积在镍层中。 H2PO2-+H OH-+P+H2O 4.部分次磷酸根在催化环境下,自己也会氧 化并生成氢气从镍面上向外冒出。 H2PO2- + H2O HPO32-+H++H2
25
化学镍药水的分类:
按操作温度分可将镀液分成高温镀液(85950C)、中温镀液(65-750C)、低温镀 液(500C)以下 按其使用的还原剂又可大致分为次磷酸盐 型、硼氢化物型、肼型、胺基硼烷型4种。
13
3、微蚀缸
作用: 酸性过硫酸钠微蚀液用于使铜面微 粗化,增加铜与化学镍层的密着性。沉 镍金生产也有使用硫酸双氧水或酸性过 硫酸钾微蚀液来进行的。
14
操作条件(NPS系列):
Na2S2O8: 100±20g/l H2SO4: 20 ±10g/l Cu2+ : 5~25g/l 温度: 30 ±2OC 时间: 1.5 ±0.5min 搅拌:摆动及药液循环搅拌或空气打气 槽材质:PVC或PP 加热器:石英或铁弗龙加热器
6
五、沉镍金工艺的用途
化学镍金镀层集可焊接、可接触导通,可打线、 可散热等功能于一身,是 PCB 板面单一处理却具 有多用途的湿制程。 化学镍的厚度一般控制在 4-5μm,其不但对铜面进行有效保护,防止铜的 迁移,而且具备一定硬度和耐磨性能,同时拥有 良好的平整度 。浸金的厚度一般控制在 0.050.1μm,其对镍面具有良好的保护作用,而且具 备很好的接触导通性能。
沉锡工艺介绍
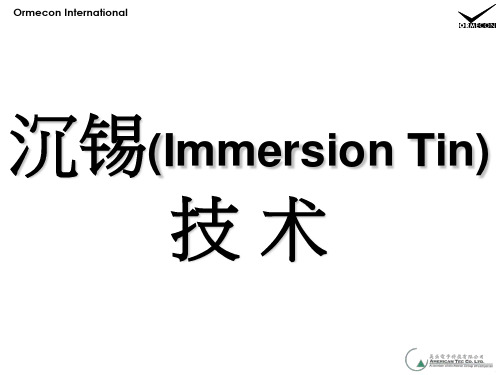
Cu3Sn
tin
copper
Cu6Sn5
Cu3Sn
时间 / 温度
Ormecon International
沉锡的应用
应用 工艺参数
锡层厚度 优越性
最后的表面处理
approx. 60 - 70 °C, 沉积时间:8 - 20 min 大约. 1 µm
▪ 良好的可焊性 i.e. 多次上锡
▪ 高的储存稳定性 ▪ 锡须的长度 <20 µm
欧洲议会通过了 RoHS 指令 (限制使用某些有害物质的指令EEE2002/95/EC, 27th January 2003).
指令禁止在2006年7月1日以后在电气及电子产品中使用某些有害的物质. 成 员国必须确保在市场上销售的新电气及电子产品中不含有铅和其他的有害物 质.
为了执行2006年的指令,主要的设备制造商已经准备在2004年一月开始转换 使用无铅技术. 现在他们向他们的供应商提出越来越多的要求. 让我们现在 就准备好!
垂直: 水平:
1 min. @ 室温 - 40°C 45 - 60 sec. @ 室温 - 40°C
必需分析:
Ormecon International 提供的建议: -有机金属型(OM)的预浸是改良锡须的有效的方法
Ormecon International
沉锡工艺
水洗 水洗 热水洗 水洗 DI 水洗 烘干
测试
测试方法
1. 锡层厚度 2. 可焊性
用 AAS 机分析方法能达到要求之上
3 次回流焊 或 在老化 (4h, 155°C) 后 1 次回流焊
3. 按照 IEC 68-2-14 (热冲 100 循环 - 40°C / 125°C; 停留时间 = 30 min 击)作可焊性
PCB表面处理水平沉锡PFMEA分析范例

潜在失
严 级别
锡铜效结后合果力差 重 class
pToitmentainadl 度 ifica
failcuorpepefrfect S tion
binding force
difference
潜在失效 起因/机理 potential failure cause/mechanism
频 度 O
现行过程 控制预防current process control
too high
control in the 48
±2℃ every shift
自动控制温度 automative
control
3 30
无none 无none 无none
1/6
除油:要求除去铜面上
的绿油、手指印、胶渍
degreasing:provide a
clean copper surface
过程 功能process function
uniformity of the surface of the tin, reducing the migration speed of the copper ions, and the storage period of the plate
纳米银沉积过 慢,沉积层偏
薄OM-Ag thickness too thin
措施结果 action result
采取的措施action adopted
R S OD P
N
微蚀:粗化表面增强沉 铜层结合力micro-
etching :roughen the surface to enhance the combination with copper deposition
铜含量偏高 High copper
- 1、下载文档前请自行甄别文档内容的完整性,平台不提供额外的编辑、内容补充、找答案等附加服务。
- 2、"仅部分预览"的文档,不可在线预览部分如存在完整性等问题,可反馈申请退款(可完整预览的文档不适用该条件!)。
- 3、如文档侵犯您的权益,请联系客服反馈,我们会尽快为您处理(人工客服工作时间:9:00-18:30)。
PCB沉锡工艺研究
PCB沉锡工艺是为有利于SMT与芯片封装而特别设计的在铜面上以化学方式沉积锡金属镀层,是取代Pb-Sn合金镀层制程的一种绿色环保新工艺,已广泛使用与电子产品(如线路板、电子器件)与五金件、装饰品等表面处理。
一、沉锡工艺特点
1.在155℃下烘烤4小时(即相当于存放一年),或经8天的高温高湿试验(45℃、相对湿度93%),或经三次回流焊后仍具有优良的可焊性;
2.沉锡层光滑、平整、致密,比电镀锡难形成铜锡金属互化物,无锡须;
3.沉锡层厚度可达0.8-1.5μm,可耐多次无铅焊冲击;
4.溶液稳定,工艺简单,可通过分析补充而连续使用,无需换缸;
5.既适于垂直工艺也适用于水平工艺;
6.沉锡成本远低于沉镍金,与热风整平相当;
7.对于喷锡易短路的高密度板有明显的技术优势,适用于细线高密度IC封装的硬板和柔性板;
8.适用于表面贴装(SMT)或压合(Press-fit)安装工艺;
9.无铅无氟,对环境无污染,免费回收废液。
二、沉锡工艺流程顺序:
三、Final Surface Cleaner表面除油:
1.开缸成分:
M401酸性除油剂……….100ml/L
浓H2SO4…………………50ml/L
DI水……………………..其余
作用:除去电路板表面油污,氧化层和手指印。
此除油剂与目前市面上常见的所有阻焊油墨都兼容。
2.操作参数:
温度:30-40℃,最佳值:35℃
分析频率:除油剂,每天一次
控制:除油剂80-120ml/L,最佳值:100ml/L
铜含量:小于1.5g/L
补充:M401,增加1%含量需补充10ml/L
过滤:20μ滤芯连续过滤,换缸时换滤芯。
寿命:铜含量超过1.5g/L或每升处理量达到500呎。
四、Microetch微蚀:
1.开缸成分:
Na2S2O4……………….120g/L
H2SO4…………………40ml/L
DI水………………….其余
程序:①向缸中注入85%的DI水;
②加入计算好的化学纯H2SO4,待冷却至室温;
③加入计算好的Na2S2O4,搅拌至全溶解;
④补DI水至标准位置。
2.操作参数:
温度:室温即可
分析频率:H2S04,每班一次
铜含量,每天一次
微蚀率,每天一次
控制:铜含量少于50g/L
微蚀率:30-50μ,最佳值:40μ
补充:Na2S2O4,每补加10g/L,增加1%的含量
H2SO4,每补加4ml/L,增加1%的含量
寿命:铜含量超过50g/L时稀释至15g/L,并补充Na2S2O4 和H2SO4
五、Predip预浸:
1.开缸:10% M901预浸液;其余:DI水
用途:在沉锡前湿润微蚀出的铜面,此预浸液对任何阻焊油墨都没有攻击性;
2.操作参数:
温度:室温
分析频率:酸当量,每天一次
铜含量:每周一次
补充:酸当量,每添加100ml/LM901,增加0.1当量
液位:以DI水补充
过滤:20μ滤芯连续过滤
寿命:与沉锡缸同时更换
3.废水处理:与后处理废液中和后过滤出固体物质。
六、Chemical Tin沉锡:
1.设备:预浸和化学锡缸均适用;
缸体: PP或PVC缸均可;
摆动:PCB架在缸内摆动,避免气体搅拌;
过滤:10μ滤芯连续过滤;
通风:建议15MPM通风量;
加热器:钛氟龙或石英加热器;
注意:不能有钢铁材料在缸内
2.开缸:100% Sn9O2 沉锡液开缸,此沉锡液对任何阻焊油墨都没有攻击性;
3.操作参数:
锡浓度:20-24g/L,最佳:22g/L
硫脲浓度:90-110g/L,最佳:100g/L
磺酸含量:90-110ml/L,最佳:100ml/L
铜离子浓度:最高8g/L时,必须冷却过滤;
温度:70-75℃
时间:10-15分钟
4.沉锡液的维护:
沉锡液维护简单,主要成分可通过分析补充,使其保持在最佳工艺范围内:
①每加入12ml/L沉锡液可提高1g/L的锡浓度,使锡浓度保持在20-24g/L之间;
②每加入10ml/L 10%硫脲溶液可提高硫脲1g/L,使硫脲浓度保持在90-110g/L之间;
③按分析值补充有机磺酸的含量,使其保持在90-110ml/L之间;
④蒸发损失可用去离子水补充液位。
5.成份分析:
1)锡的分析:
①试剂:0.1N碘溶液、30%硫酸溶液、淀粉溶液
②分析步骤:
a) 准确吸取2ml溶液到250ml烧瓶中;
b) 加入15ml 30%硫酸溶液;
c) 加入100ml去离子水;
d) 加入2ml淀粉溶液;
e) 用0.1N标准碘溶液滴定至兰紫色终点,记录毫升数V;
计算:锡含量Sn(Ⅱ)(g/L)=2.69V;
2)有机磺酸的分析:
① 试剂:
a)10%Mg EDTA溶液:加122.76g Na2EDTA 2H2O和39.6g MgSO4到800ml的去离子水中,用1N NaOH 溶液调节PH值至7,再加水至1000ml;
b)兰指示剂溶液或0.1%乙醇溶液;
c)0.1N标准NaOH溶液。
② 分析步骤:
a)准确吸取1.0ml沉锡液到250ml烧瓶中,加入100ml去离子水;
b)加入2ml Mg EDTA溶液及5滴溴酚兰指示剂溶液;
c)用0.1N标准NaOH溶液滴定至溶液由黄色变为绿色终点(PH6.7),记录毫升数V;
计算:有机磺酸(g/L)=9.61V
3)硫脲的分析:
① 分析步骤:
a)将沉锡槽内取出的样品溶液冷至室温,然后过滤,收取滤液;
b)准确吸取2ml滤液至200ml容量瓶中,加去离子水至刻度,混匀;
c)准确吸取5ml稀释液至1000ml容量瓶中,加去离子水至刻度,混匀(即总共稀释两万倍);
d)用紫外光光度计于236nm处,10mm石英比色皿,以去离子水为参比,测定稀释液的消光值;
计算:硫脲(g/L)=128×消光值
6.影响沉锡速率的因素:
1)温度的影响:在40℃至80℃的区间,沉锡速率随温度的升高而加快;
2)时间的影响:锡层厚度随时间的延长而增加,但在60℃下20分钟后厚度趋于稳定,因此生产上选择
在60℃下沉锡10-12分钟,可以得到1.5μm(60微英寸)足够厚的锡层。
3)锡浓度的影响:沉锡速度随着锡浓度的增加而上升,但沉锡层的外观幷不随着锡浓度的升高而有任何变化,因此增加锡浓度是提高沉锡速率的有效方法之一;
4)有机磺酸浓度的影响:沉锡的速率随有机磺酸的浓度上升而加快,当有机磺酸的含量超过110g/L后,速率基本不变,但当有机磺酸浓度低于50ml/L时所形成的锡层会呈雾状;
5)硫脲浓度的影响:沉锡速率随硫脲浓度的上升而加快,但硫脲浓度超过250g/L时,锡层外观变得粗糙、毛刺多。