IE知识改善知识生产线平衡.pptx
合集下载
IE生产线平衡的资料PPT资料37页

稼动率=投入工时/可供工时 *100% 计划停线工时=计划停线时间*人数 计划停线时间=无计划时间+换线时间+判停时间
上例中,若换线时间是15分钟,则计划停线工时为20人 *15min=300min=5H,则投入工时和稼动率为:
60H-5H=55H 稼动率=55H/60H=92%
2019/10/22
时间测试
分解动作时间量测,一般每个动作测量5 次为宜; 量测人员应站在作业员斜后面1米以外, 以能看清楚全部操作动作为准则; 测试中不能打扰作业员的正常操作和引 起作业员的紧张;
时间测量流程
作业内容
数据与信息记录
测试中判断作业员的速度水平,并作如 实记录,不可修改量测数据; 若有其他特殊情況,也应加以实录;
2019/10/22
6
相关的概念
概念6:平衡损失 平衡损失=(总工时-单件标准时间)*设定产能
时间
T1 T2 T3 T4 T5
等待时间
单个产品平衡损失 =等待时间之和
S1 S2 S3 S4 S5
工站
概念7:平衡率100%代表﹕ 1.工站之间无等待,前后产能一致﹔ 2.工站节拍相同,动作量相同(动作量是指工站中各种必要动
素的时间总量); 3.平衡损失时间为零; 4.设计效率最大化; 5.前后流程的设计可以更完善(如下图).
2019/10/22
7
相关的概念
(交叉流程)
(直通流程 1 ) (直通流程 2 )
概念8:高效率 1. 通常认为高效率就是:快速,简单&大规模 2. 我们认为沒有浪费的时候才是高效率的 操作效率=实际产量/设定产能*100% 整体工厂效率(OPE)=平衡率*稼动率*操作效率
上例中,若换线时间是15分钟,则计划停线工时为20人 *15min=300min=5H,则投入工时和稼动率为:
60H-5H=55H 稼动率=55H/60H=92%
2019/10/22
时间测试
分解动作时间量测,一般每个动作测量5 次为宜; 量测人员应站在作业员斜后面1米以外, 以能看清楚全部操作动作为准则; 测试中不能打扰作业员的正常操作和引 起作业员的紧张;
时间测量流程
作业内容
数据与信息记录
测试中判断作业员的速度水平,并作如 实记录,不可修改量测数据; 若有其他特殊情況,也应加以实录;
2019/10/22
6
相关的概念
概念6:平衡损失 平衡损失=(总工时-单件标准时间)*设定产能
时间
T1 T2 T3 T4 T5
等待时间
单个产品平衡损失 =等待时间之和
S1 S2 S3 S4 S5
工站
概念7:平衡率100%代表﹕ 1.工站之间无等待,前后产能一致﹔ 2.工站节拍相同,动作量相同(动作量是指工站中各种必要动
素的时间总量); 3.平衡损失时间为零; 4.设计效率最大化; 5.前后流程的设计可以更完善(如下图).
2019/10/22
7
相关的概念
(交叉流程)
(直通流程 1 ) (直通流程 2 )
概念8:高效率 1. 通常认为高效率就是:快速,简单&大规模 2. 我们认为沒有浪费的时候才是高效率的 操作效率=实际产量/设定产能*100% 整体工厂效率(OPE)=平衡率*稼动率*操作效率
现场IE改善案例分析.pptx
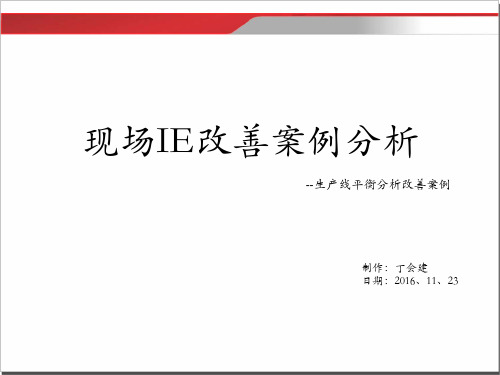
4、工时测定分析(蓝色为作业的时间红色为失去平
衡的时间)
5、生产线平衡的计算
生产平衡率(%)=各工程净时间总计/(时间最长工程*人 员数)*100%
如上图表中,生产线平衡率=1505/(90*19)*100%=88% 不平衡率%=100%-平衡率(%) 对生产线来说,不平衡率越小越好,一般控制5%-13%之间,
有多少岗位是不增值的
扑克牌游戏规则
1、每个分厂安排4个人(厂长、工艺、作业长、班长) 2、小组内部自己安排4个人的工作 3、要求是将52张扑克牌按同一花色、从大到小的排成一排 4、时间最少的小组获胜 5、开始和结束计时以固定的人员手敲桌子为准 6、游戏开始由工作人员将牌洗好
评分标准
1.2.3.4名分别100.80.60.40分错 一张牌,扣10分
(2)IE动作改善的4原则:
• ECRS原则 1.Eliminate —取消 2、Combine —合并 3、Rearrange —重排 4、Simplify —简化
(3)ECRS法运用图示ห้องสมุดไป่ตู้介
生产线平衡—例1:缩短生产节拍
提升生产速度,维持人手不变
缩短生产节拍 将工序2里一部 分可抽离的时间 转至3工序里, 以缩短整体的生 产节拍
降低线体速度,减少生产产量
减少人手(2) 因生产需求量降低而可 降低线体速度
将工序3.4的工作时间 分配至工序1.2.5里,从 而工序3.4工作岗位的 人手可调配至其它生产 线去。
(4)4种增值的工作
站在客户的立场上,有四种增值的工作
1、使物料变形 2、组装 3、改变性能 4、部分包装
现在请大家思考一下…… 我们的生产线上
电装7人线标准工时
请 计 算 平 衡 率
IE生产线平衡资料课件
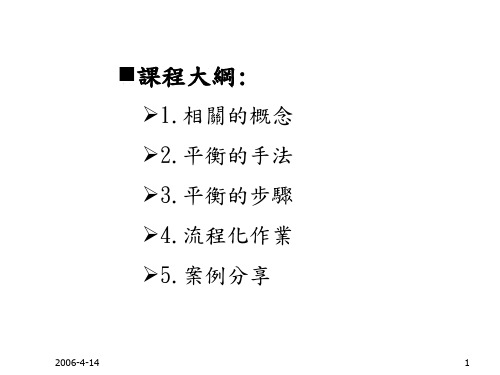
平衡的步驟
Steps 7: 改善總結報告: 平衡率 設定產能﹑實際產能﹑人均產能(單機產能) 損失分析 品質分析 成本改善率 Steps 8: 標準化
流程化作業
1. 平衡率目標:與大設備相連≧85% 其他≧ 95%
2. 平衡改善小組的職責:
生產單位:改善前/后之工時測量,山積表制作﹑分析及改善方案之實施.制工單位:協助生產單位擬定及推動改善方案,跟蹤方案效果評估及各種相關文件修訂及系統表單發行﹔品管單位:負責改善前/后產品品質評估﹔工務單位:主導及其它改善事項協助﹐設備改善﹔ IE﹑經管﹑企划:改善前后產線效益評估及跟進.
平衡的步驟
S1標准時間為﹕t2+t3; S1工站時間為﹕t4
S1-2
S1-1
當S1-1不需等S1-2就能開始, S1工站時間為﹕ T3+S1-1提前開始的時間(t4-t3)
S1工站時間=?
?
Steps 5: 建立新的模擬流程 新的FLOW CHART/ SOP (SWR發行)Steps 6: 實施新的模擬流程 改善后時間測量 改善后山積表制作
程序分析使用的圖表: 工藝程序圖 / 流程程序圖/ 路線圖程序分析符號--表示操作--表示搬運/運輸--表示檢驗--表示暫存或等待--表示受控的貯存 --派生符號,由上面的符號合成.
程序改善
例: 流程程序圖
程序分析技巧通過5W1H系統地分析程序的組成是否合理和必要“ECRS”四大原則: 取消(Eliminate); “完成了什么?是否必要?為什么?” 合並(Combine); “誰完成?何時完成?哪里?如何?” 重排(Rearrange); 取消合並重排 簡化(Simplify); 確認必要簡單方法/設備生產.五大內容: 工藝流程分析—取消/合並/重排工序,減少浪費 搬運分析—考量重量、距離、方法、工具、路線 檢驗分析—按產品要求設計合理站點和方法 貯存分析—使物料及時供應 等待分析—減少和消除引起等待的因素
Steps 7: 改善總結報告: 平衡率 設定產能﹑實際產能﹑人均產能(單機產能) 損失分析 品質分析 成本改善率 Steps 8: 標準化
流程化作業
1. 平衡率目標:與大設備相連≧85% 其他≧ 95%
2. 平衡改善小組的職責:
生產單位:改善前/后之工時測量,山積表制作﹑分析及改善方案之實施.制工單位:協助生產單位擬定及推動改善方案,跟蹤方案效果評估及各種相關文件修訂及系統表單發行﹔品管單位:負責改善前/后產品品質評估﹔工務單位:主導及其它改善事項協助﹐設備改善﹔ IE﹑經管﹑企划:改善前后產線效益評估及跟進.
平衡的步驟
S1標准時間為﹕t2+t3; S1工站時間為﹕t4
S1-2
S1-1
當S1-1不需等S1-2就能開始, S1工站時間為﹕ T3+S1-1提前開始的時間(t4-t3)
S1工站時間=?
?
Steps 5: 建立新的模擬流程 新的FLOW CHART/ SOP (SWR發行)Steps 6: 實施新的模擬流程 改善后時間測量 改善后山積表制作
程序分析使用的圖表: 工藝程序圖 / 流程程序圖/ 路線圖程序分析符號--表示操作--表示搬運/運輸--表示檢驗--表示暫存或等待--表示受控的貯存 --派生符號,由上面的符號合成.
程序改善
例: 流程程序圖
程序分析技巧通過5W1H系統地分析程序的組成是否合理和必要“ECRS”四大原則: 取消(Eliminate); “完成了什么?是否必要?為什么?” 合並(Combine); “誰完成?何時完成?哪里?如何?” 重排(Rearrange); 取消合並重排 簡化(Simplify); 確認必要簡單方法/設備生產.五大內容: 工藝流程分析—取消/合並/重排工序,減少浪費 搬運分析—考量重量、距離、方法、工具、路線 檢驗分析—按產品要求設計合理站點和方法 貯存分析—使物料及時供應 等待分析—減少和消除引起等待的因素
IE生产线平衡资料PPT课件
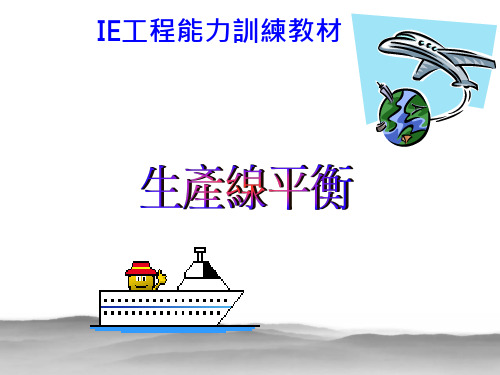
23.11.2020
16
例: 流程程序圖
材料仓库
2 AI、 SMT加 工 1 前加工
3 手插件 4 锡炉 5 剪脚 6 修 整 (正 背 面 )
7 折分基板 8 ICT测 试
8 穿 焊 OPC(PSC) 9 锡 面 /正 面 检 查 10 中 间 检 查 11 组 装 CASE 12 溶 着 /锁 螺 丝 13 电 测 检 查 14 包 装 15 OQC检 查
2
2
0
12 0.5
1.8 1
1.5
10
10
2 2.5 5 2
5
3
1 0.5
4
2 1.5
0.5 1 1
0
0 2
0.5 1
2
10 2
12
2 1.5 6.5 4
2 2.5
1
M5 M4 M3 M2 M1
S1 S2 S3 S4 S5 S6 S7 S8 S9 S10 S11 S12 S13 S14 S15 S16 工站
数据整理和计算
测试完毕,对数据进行整理和计算,补充 测量有怀疑或错漏的数据; ❖ 计算可信度95%所需的样本数量,补测差 异样本数量.
资料分析与处理
对量测记录之所有资料进行分析,对比 ST的差异程度,解决发现的问题; ❖ 若分析发现标准时间制定不当,应及时 修改,必要时调整制程.
工时测量的作用﹕ n 获取各工站的实际操作时间,为山积表制作,时间平衡作准备; n 通过时间观测,分析作业价值,发现问题和改善空间; n 形成标准,比较实际差异,找出问题;
用语衡量流程中各工站节拍符合度的一個综
合比值;
单件标准时间
平衡率= ----------------------100%
生产线平衡分析与改善(最全面的IE分析,生产线平衡)ppt课件

0.1
0.2 0.5 1.0 2.0 5.0 ≥10
<1.0 100 50 20 10 5 2 1
1.0~2.0 50 20 20 10 5 2 1
2.0~5.0 20 20 10 5 2 2 1
5.0~10 10 10 5 2 2 1 1
13
三、流水生产线平衡的设计方法
3、 单品种流水线平衡方法 ● 案例:生产线平衡分析案例(直流式流程序为例)
10 A
工序1
工序2 11 B
工序3 12 E
C5
4 D
工序4 3
F
11 H
7
工序6
G
3 I
工序5 34
五、生产线平衡的其它案例
装配流水线平衡的方法很多,这里介绍一种简便而又能取得 满意效果的方法——阶位法。 阶位法的工作步骤如下
① 作图表示装配工艺过程中各作业元素的先后关系,并标 明每项作业元素的时间。 ② 从作业元素先后关系图找出每项作业元素的后续作业 元素,计算它们的时间总和,即每项作业元素的阶位值。 ③ 按阶位值的大小,由大到小,将作业元素排队,制成 作业元素阶位表。 ④ 从阶位值最高的作业元素开始,向工作地分配作业要 素。每分配一项作业元素,计算一次在节拍时间内的剩余 时间。若剩余时间足够安排另一项作业元素,从阶位表中 找出阶位值次高的作业元素分给该工作地。若剩余时间不 够安排其它作业元素,就向下一个工作地分配,直到全部 作业要素都被安排入工作地为止。
比较B、C两个工作站,将可发现B工作站的产能为C工作站的 2.69倍,B、C两个工作站将积压大量的半成品。若以传统追求 各工作站提升效率的方式进行管理,B工作站的效率提升,只会 恶化B、C站的半成品积压的浪费,而无助于整体产量的提高 (假设B工作站经训练生产效率达100%,则B工作站每小时产量 将达702.35个,产量为C工作站的3.36倍)。
IE线平衡改善(PPT46页)

100 108
Line Balance Concept
Station
1
2
3
4
50
11
Cycle Time 4
5
6
4
6
5
4
4
6
6
2
6 5 4 3 2 1 0
1
2
3
4
5
6
7
8
9
10
11
Cycle Time Line Balance
= 6 second = (4+5+6+4+6+5+4+4+6+6+2) / (6X11)
Line Balance Concept
Station
1
2
3
4
5
6
7
8
9
10
11
12
Cycle Time 4
5
6
4
6
5
4
4
3
3
6
2
6 5 4 3 2 1 0
1
2
3
4
5
6
7
8
9
10
11
12
Cycle Time Line Balance
= 6 second = (4+5+6+4+6+5+4+4+3+3+6+2) / (6X12)
Cycle T im e 6 6 6 5 4
Output / Hour
600 600 600 720 900
N ew S td T im e
Line Balance Concept
Station
1
2
3
4
50
11
Cycle Time 4
5
6
4
6
5
4
4
6
6
2
6 5 4 3 2 1 0
1
2
3
4
5
6
7
8
9
10
11
Cycle Time Line Balance
= 6 second = (4+5+6+4+6+5+4+4+6+6+2) / (6X11)
Line Balance Concept
Station
1
2
3
4
5
6
7
8
9
10
11
12
Cycle Time 4
5
6
4
6
5
4
4
3
3
6
2
6 5 4 3 2 1 0
1
2
3
4
5
6
7
8
9
10
11
12
Cycle Time Line Balance
= 6 second = (4+5+6+4+6+5+4+4+3+3+6+2) / (6X12)
Cycle T im e 6 6 6 5 4
Output / Hour
600 600 600 720 900
N ew S td T im e
IE基础知识现场管理改善知识培训PPT专题演示

一、什么是IE?(IE的定义) 春天的风吹过银杏树的枝头,几场春雨让刚冒出小芽的叶子,长得郁郁葱葱。当我把这个好消息告诉门口的孩子们后,他们便一个接一个的来到我们家的花园中。
春天的风吹过银杏树的枝头,几场春 雨让刚 冒出小 芽的叶 子,长 得郁郁 葱葱。 当我把 这个好 消息告 诉门口 的孩子 们后, 他们便 一个接 一个的 来到我 们家的 花园中 。
春天的风吹过银杏树的枝头,几场春 雨让刚 冒出小 芽的叶 子,长 得郁郁 葱葱。 当我把 这个好 消息告 诉门口 的孩子 们后, 他们便 一个接 一个的 来到我 们家的 花园中 。
IE 具备哪些意识
3、工作简化和标准化意识
“3S” 简化(Simplification) 专门化(Specialization) 标准化(Standardization)
春天的风吹过银杏树的枝头,几场春 雨让刚 冒出小 芽的叶 子,长 得郁郁 葱葱。 当我把 这个好 消息告 诉门口 的孩子 们后, 他们便 一个接 一个的 来到我 们家的 花园中 。
标准工时怎么测?
1.收集资料(产品数据,作业方法及设备等) 2.划分单元(每一单元应有明显易辨认的起点和终点) 3.测量时间(归零法,连续测时法等) 4.剔除异常值(三倍标准偏差法) 5.计算正常时间(客观评比法) 6.确定宽放时间(确认宽放率) 7.计算标准时间(观测时间*评比系数*(1+宽放率))
IE研究的方法
方法研究
工 作 研 究
时间研究
程序分析 作业分析 动作分析
工艺程序图 流程程序图 线图和线路图
人机作业分析 联合作业分析 双手作业分析
动素分析 影像分析 动作经济原则
直接法 合成法
秒表法 工作抽样法 预定时间标准法(PTS ) 标准资料法
班长IE专训课程-生产线平衡
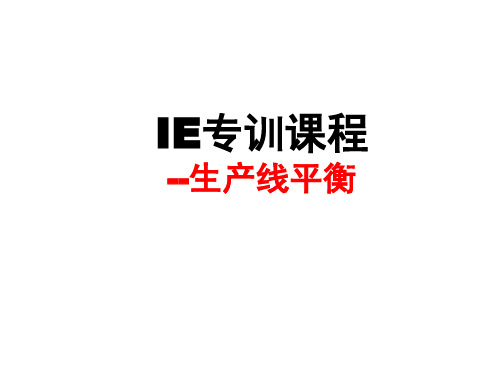
12,000个雇员中的每个和你一样每天节 约10步,可能会在公司里节省50英里的 运动浪费并且减少滥用能量……
--Henry.福特《福特理想》
二.线平衡相关概念
2.2.流水线基本特征
1) 固定生产一种或少数几种产品
2) 工作中心专业化程度高
3) 按节拍生产
表示
4) 生产能力保持平衡 常数
t1 = t2 =a = tm
三.线平衡改善
3.3.作业方法改善技术
5W2H提问技术
(包括:5why提问,通过5W2H系统地分析程序的组成是否 合理和必要)
ECRS四大原则
取消(Eliminate); “完成了什么?是否必要?为什么?” 合並(Combine);“谁完成?何时完成?哪里?如何?” 重排(Rearrange);取消合并重排 简化(Simplify);确认必要简单方法/设備生产.
平衡率﹕70% 打破平衡﹐打开了可平衡局面
瓶颈未变的情况下,平衡率短期内下降是 好事。
三.线平衡改善
3.7.总结及标准化
改善总结报告: 平衡率 设定产能﹑实际产能﹑人均产能(单机
产能) 损失分析 质量分析 成本改善率
标准化: 按照改善后的要求制作相应SOP等标准文件
下步工作:
IE专训课程
--生产线平衡
大纲
一、生产线介绍
二、线平衡相关概念
三、线平衡改善
一.生产线介绍
SMT 成型
装配
涂装 冲压
二.线平衡相关概念
2.1.流水线起源
1863:出生于美国密歇根州的农庄(父母为爱尔兰移民);12 岁自己的机械坊;15岁制造第一台内燃机 1879:底特律做机械学徒,后进入西屋电气公司 1891:爱迪生照明公司工程师,2年后任主工程师 1896:第一辆汽车“四轮车” 1896-1901:制造赛车 1903:福特汽车公司 “福特999” 1908:T型车,到1927生产1500万辆(后45年内世界记录) 员工分享、投资橡胶、研究塑料、转车型、转营销 流水线之父--亨利·福特 1945年退位 (Henry Ford,1863-1947) 1947:逝世于故乡,83岁
--Henry.福特《福特理想》
二.线平衡相关概念
2.2.流水线基本特征
1) 固定生产一种或少数几种产品
2) 工作中心专业化程度高
3) 按节拍生产
表示
4) 生产能力保持平衡 常数
t1 = t2 =a = tm
三.线平衡改善
3.3.作业方法改善技术
5W2H提问技术
(包括:5why提问,通过5W2H系统地分析程序的组成是否 合理和必要)
ECRS四大原则
取消(Eliminate); “完成了什么?是否必要?为什么?” 合並(Combine);“谁完成?何时完成?哪里?如何?” 重排(Rearrange);取消合并重排 简化(Simplify);确认必要简单方法/设備生产.
平衡率﹕70% 打破平衡﹐打开了可平衡局面
瓶颈未变的情况下,平衡率短期内下降是 好事。
三.线平衡改善
3.7.总结及标准化
改善总结报告: 平衡率 设定产能﹑实际产能﹑人均产能(单机
产能) 损失分析 质量分析 成本改善率
标准化: 按照改善后的要求制作相应SOP等标准文件
下步工作:
IE专训课程
--生产线平衡
大纲
一、生产线介绍
二、线平衡相关概念
三、线平衡改善
一.生产线介绍
SMT 成型
装配
涂装 冲压
二.线平衡相关概念
2.1.流水线起源
1863:出生于美国密歇根州的农庄(父母为爱尔兰移民);12 岁自己的机械坊;15岁制造第一台内燃机 1879:底特律做机械学徒,后进入西屋电气公司 1891:爱迪生照明公司工程师,2年后任主工程师 1896:第一辆汽车“四轮车” 1896-1901:制造赛车 1903:福特汽车公司 “福特999” 1908:T型车,到1927生产1500万辆(后45年内世界记录) 员工分享、投资橡胶、研究塑料、转车型、转营销 流水线之父--亨利·福特 1945年退位 (Henry Ford,1863-1947) 1947:逝世于故乡,83岁
IE七大手法的改善步骤.pptx
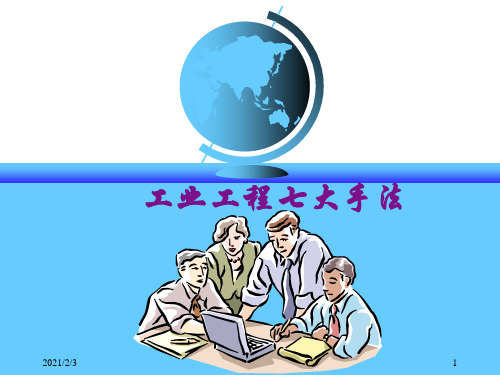
个人—聪明才智 有发展机会
IE七大手法之一 — 防错法
7
1、意义
防错法又称防愚法,其义为防止愚笨的人做错事。也就是说,连愚笨的人也不会做错事的设计 方法。
狭义: 如何设计一个东西(一套方法),使错误绝不会发生。
广义: 如何设计一个东西(一套方法),而使错误发生的机会减至最低的程度。
因此,更具体的说”防错法”是:
3、IE的目的?
应用科学及社会学的知识,以合理化、舒适化的途径来改善我们工作的品质及效率以达到提高生 产力增进公司之利润进而使公司能长期的生存发展下去,个人的前途也有寄托之所在。因此,简 单地说,IE的目的就是充分利用工厂的人力、设备、材料,以最经济有效的工作方法,使企业独 得最大的效益。
4、为甚么要有IE?
1>、具有即使有人为疏忽也不会发生错误的构造 —不需要注意力。
2>、具有外行人来做也不会做错的构造
—不需要经验与直觉。
3>、具有不管是谁或在何时工作能不出差错的构造 —不需要专门知识与高度的技能。
2、功用
1>、积极: 使任何的错误,绝不会发生。
2>、消极: 使错误发生的机会减至最低程度。
3、应用范围
IE七大手法之三 — 流程法
15
现场作业改善方法:
对象
着眼点
设备布置
生产流程化
加工的改善
制程改善
检验的改善 物料搬运浪费的分析
停滞的改善
具体手段手法 物料流程线图 加工路径图 从至图 作业相关图 设备容易移动出口与入口 接近大房间化 瓶颈工程改善 价值分析 价值工程 防呆装置 作业管制图 制程流程图 传送带 无法放入产品 同步化 同量化 降低批量 快速换模
工业工程七大手法
IE七大手法之一 — 防错法
7
1、意义
防错法又称防愚法,其义为防止愚笨的人做错事。也就是说,连愚笨的人也不会做错事的设计 方法。
狭义: 如何设计一个东西(一套方法),使错误绝不会发生。
广义: 如何设计一个东西(一套方法),而使错误发生的机会减至最低的程度。
因此,更具体的说”防错法”是:
3、IE的目的?
应用科学及社会学的知识,以合理化、舒适化的途径来改善我们工作的品质及效率以达到提高生 产力增进公司之利润进而使公司能长期的生存发展下去,个人的前途也有寄托之所在。因此,简 单地说,IE的目的就是充分利用工厂的人力、设备、材料,以最经济有效的工作方法,使企业独 得最大的效益。
4、为甚么要有IE?
1>、具有即使有人为疏忽也不会发生错误的构造 —不需要注意力。
2>、具有外行人来做也不会做错的构造
—不需要经验与直觉。
3>、具有不管是谁或在何时工作能不出差错的构造 —不需要专门知识与高度的技能。
2、功用
1>、积极: 使任何的错误,绝不会发生。
2>、消极: 使错误发生的机会减至最低程度。
3、应用范围
IE七大手法之三 — 流程法
15
现场作业改善方法:
对象
着眼点
设备布置
生产流程化
加工的改善
制程改善
检验的改善 物料搬运浪费的分析
停滞的改善
具体手段手法 物料流程线图 加工路径图 从至图 作业相关图 设备容易移动出口与入口 接近大房间化 瓶颈工程改善 价值分析 价值工程 防呆装置 作业管制图 制程流程图 传送带 无法放入产品 同步化 同量化 降低批量 快速换模
工业工程七大手法
管理资料生产管理生产管理之IE改善基础知识课件
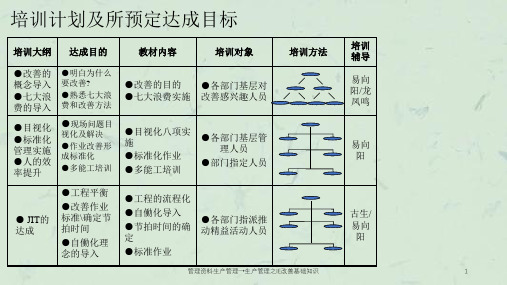
銷售價格
利潤
銷售價格
利潤
銷售價格
利潤
銷售價格
企業,顧客雙 方都有好處。
利潤
成本
成本
成本
成本
①
現在
②
③
增加利潤→必須降低成本 (在製造現場就可以做到的事)
管理资料生产管理→生产管理之IE改善基础知识
7
生產方式與成本
在成本中,生產同樣的產品各個企業有其相同費用發生的部份,以及因生產 方式之不同而產生不同的費用發生的部份。
• 4.在工厂革命中,抵制是避免不了的,所以为了 消除抵抗的势力,一定要注重【改善的基本精 神】.
管理资料生产管理→生产管理之IE改善基础知识
10
减少浪费的基本精神
• 1.舍弃作法上的固定观念.
• 2.提出不能做的理由,还不如去思考做的方法.
• 3.不可辩解,首先要否定现状.
• 4.不要太要求完美,只要有50分就可以开始了.
1
内容的分类
1.精益生产的来源(2 分钟)
2.改善的目的(5 分钟)
3.浪费的种类及说明(25分钟)
4.目视化的管理(30分钟)
5.标准作业(30分钟)
6.JIT和自働化(30分钟)
7.作业的改善方法及启示(45分钟)
管理资料生产管理→生产管理之IE改善基础知识
2
1. 生产改善的来源
齐二石 天津大学管理学院教授
浪
成
材購
本
料入 費部
品
費
費
由於生產方式所 產生的費用 (因企業而異)
各
勞 務 費
能 源 費
設 備 折 舊
公 司 相 同
費
的
. 其 他
- 1、下载文档前请自行甄别文档内容的完整性,平台不提供额外的编辑、内容补充、找答案等附加服务。
- 2、"仅部分预览"的文档,不可在线预览部分如存在完整性等问题,可反馈申请退款(可完整预览的文档不适用该条件!)。
- 3、如文档侵犯您的权益,请联系客服反馈,我们会尽快为您处理(人工客服工作时间:9:00-18:30)。
山積表:將各分解動作時間,以疊加式直方圖表現的一 種研究作業時間結構的手法.
樣式:
產品xxx工時山積表
秒
10
0
8 0 1.5
6
1.5 0.5
1.5
10 2
1.5 2
10
0.5 1.3
2
10 3
0 4
44
6
1
3
1.5 3
2
2
3.5
3.5
2
2 0
12 0.5
1.8 1
1.5
10
10
2 2.5 5 2
2006-4-14
8
相關的概念
概念9:改善
I. 同樣的投入更大的輸出; II. 不增值(無效)增值(有效)
?不增值?
等待 不良
庫存 移動
……
例1: 減少移動與庫存提高效率 例2: 減少無效動作提高效率
2006-4-14
9
概念10:多能工
2006-4-14
10
平衡的手法
工時測量 山積表 程序改善 損失分析 作業條件改善 打破平衡
稼動率=投入工時/可供工時 *100% 計劃停線工時=計劃停線時間*人數 計劃停線時間=無計劃時間+換線時間+判停時間
上例中,若換線時間是15分鍾,則計劃停線工時為20人 *15min=300min=5H,則投入工時和稼動率為
60H-5H=55H 稼動率=55H/60H=92%
2006-4-14
5
相關的概念
相關的概念
概念1: 平衡率
用於衡量流程中各工站節拍符合度的一個綜合
比值﹔
單件標準時間
平衡率= ----------------------100%
瓶頸時間工位數
時
T
瓶頸時間
間 T 2T T T
1
345
SSS S S 工 123 4 5 站
單件標准時間 = T1+T2+T3+T4+T5
(流程中各工站所有動作標准時間之和)
2006-4-14
6
相關的概念
概念6:平衡損失 平衡損失=(總工時-單件標準時間)*設定產能
時
間
等待時間
TTTT T 1234 5
SSS S S
123 4 5
單個產品平衡損失 =等待時間之和
工 站
概念7:平衡率100%代表﹕
1. 工站之間無等待,前后產能一致﹔
2.工站節拍相同﹐動作量相同(動作量是指工站中各種必要動素 的時間總量)
2006-4-14
13
工時測量的作用﹕ 獲取各工站的實際操作時間﹐為山積表制作﹐時間平
衡作准備﹔ 通過時間觀測﹐分析作業價值﹐發現問題和改善空
間﹔
形成標准﹐比較實際差異﹐找出問題﹔
……(將會在后續的培訓中詳細介紹)
測時樣本大小計算
2006-4-14
14
山積表
山積表的使用: [圖表生成方法]
工時測量(秒表)
工具: 秒表 ❖ 觀測板、鉛筆 時間記錄表、計算器 山積表
方式: 一般測時法 ❖ 連續測時法
2006-4-14
11
時間測量流程
選定測試工站
作業內容
選定工站,閱讀SOP和觀察作業員操作,了 解該工站的全部操作內容;並詢問作業員 加以確認;
拆解動作
將工站動作拆解成若幹個單一的操作內 容,並填入<<時間記錄表>>
IE工程能力訓練教材
-IE知识,改善知识
2006-4-14
编辑﹕lisy 1
課程大綱:
➢1.相關的概念 ➢2.平衡的手法 ➢3.平衡的步驟 ➢4.流程化作業 ➢5.案例分享
2006-4-14
2
相關的概念
產出的速度取決于時間 最長的工站,稱之瓶頸
瓶頸在哪里? 了解加工的過程
2006-4-14
3
3.平衡損失時間為零 4.設計效率最大化 5.前后流程的設計可以更完善(如下圖)
2006-4-14
7
相關的概念
(交叉流程)
(直通流程 1 )
(直通流程 2 )
概念8:高效率 1. 通常認為高效率就是:快速,簡單&大規模 2. 我們認為沒有浪費的時候才是高效率的
操作效率=實際產量/設定產能*100% 整體工廠效率(OPE)=平衡率*稼動率*操作效率
2006-4-14
4
相關的概念
概念2:可供工時
可供工時=可供時間 *人數-借出工時
可供時間:上班時間內,பைடு நூலகம்某產品生產而投入的所有時間
例:A線有20個直接作業人員,某天14:00開始換線生產B產品,到17:00生 產結束,那麼,投入到B產品的可供時間為:
20人*3H=60H 概念3:投入工時
投入工時=可供工時-計劃停線工時
時間測試
分解動作時間量測,一般每個動作測量5 次為宜; ❖ 量測人員應站在作業員斜后面1米以外, 以能看清楚全部操作動作為准則; 測試中不能打擾作業員的正常操作,和 引起作業員的緊張;
2006-4-14
12
時間測量流程
作業內容
測試中判斷作業員的速度水平,並作如 數據與信息記錄 實記錄,不可修改量測數據;
程序分析使用的圖表: 工藝程序圖 / 流程程序圖/ 路線圖
程序分析符號 1. --表示操作 2. --表示搬運/運輸 3. --表示檢驗 4. --表示暫存或等待 5. --表示受控的貯存 6. --派生符號,由上面的符號合成.
2006-4-14
16
例: 流程程序圖
1 電視機投入及外觀檢查 2 取出廠編號標簽並貼上 3 取塑膠袋,將電視機套入 4 取襯套, 套入電視機 5 遙控器投入及外觀檢查 6 取塑膠袋,將遙控器套入 7 附件投入及外觀檢查
概念4:設定產能 設定產能(H) =3600(S)/瓶頸時間(S) 設定產能(班)=投入時間/瓶頸時間(S)
思考:1)為什么設定產能(班) =投入工時/總工時 總工時=瓶頸時間*作業人數
2)總工時 VS 單件標準時間
概念5:實際產量 實際產量是可供時間內所產出的良品數 1)人均產能=實際產量/投入時間/人數 2)單機台產能=實際產量/投入時間/機台數
5
3
1 0.5
4
2 1.5
0.5 1 1
0
0 2
0.5 1
2
10 2
12
2 1.5 6.5 4
2 2.5
1
S1 S2 S3 S4 S5 S6 S7 S8 S9 S10 S11 S12 S13 S14 S15 S16
使用工站時間制作山積表
M5 M4 M3 M2 M1
工站
2006-4-14
15
程序改善
2006-4-14
❖ 若有其他特殊情況,也應加以實錄;
數據整理和計算
測試完畢,對數據進行整理和計算,補充 測量有懷疑或錯漏的數據; ❖ 計算可信度95%所需的樣本數量,補測 差異樣本數量
資料分析與處理
對量測記錄之所有資料進行分析,對比 ST的差異程度,解決發現的問題; ❖ 若分析發現標準時間制定不當,應及時 修改,必要時調整制程.