模架尺寸确定
模板的厚度、材质、硬度与大小的设计规范

一、目的推行作业标准化,实现模具设计快速统一.二、适用范围龙光模具厂设计部三、内容一、模板厚度、材质设计规范(厚度T,单位mm)(1)连续模模板设计规范2)复合模设计规范3)冲孔模设计规范4)折弯模设计规范二、模板的规范1)在设计中,定模板尺寸大小时,模板的一边尽可能用尾数为50与00的整数,如(150*AA,200*AA,250*AA,300*AA),以方便机加工快速开料。
2)当模板需750*450线割机线割时,需线割的边到模板边不小于25mm,当模板需520*370,或500*350线割机线割时,需线割的边到模板边不小于20mm,当模板需320*220线割机线割时,需线割的边到模板边不小于14mm。
以上均为要保证一个直角边在此范围内,设计时,销钉孔、导柱孔位置应尽量考虑以上要求。
3)模板中,弹钉孔、定位避位孔,材料避位孔,且在钻铣加工时不会影响到有用工作部分,不用线割4)脱垫板(止挡板)一般不用线割,若需定位或安装入块时可线割或CNC加工。
5)优力胶孔、弹簧孔一般采用钻孔加工,而不用线割。
6)滑块和滑块主体一般情况下不需分开备料,滑块部份需磨好工作边。
(注:视情况也可用滑块分开备料)。
7)在备模板时,单块钢板的外型尺寸最大只能备长度不超650mm,宽600mm。
三、落料、冲孔模模具板料备料设计规范(上下垫板、上下夹板、脱料板、母模板)。
四、模座设计规范1、当模座长小于700时,上下模座厚度为35mm ;当模座长大700小于800时,上模座厚度35mm ,下模座厚度40mm ;当模座长度大于800小于1000时,上模座厚度40mm 下模座厚度40; 当模座长度大于10000时,上模座厚度50,下模座厚度50mm; 2、模座材质全部用A3。
3、模架标准形式有四种(如图4.1, 4.2, 4.3, 4.4,)模座模板图41图4模板模座模座模板模座模板图4图44、模座板板料备料规范有两种形式:1.第一种形式:没有外导柱情况下按下表2、第二种形式:有外导柱的情况下按下表。
知名企业注塑模具技术规范

注塑模具技术规范发布1.目的1.1 为不断提升模具质量和模具产出,确保模具制造出合格产品并正常稳定的生产;1.2 通过实现模具的一致性来达到产品的一致;1.3 进一步细化和规范注塑模具模具设计与制造,2. 范围本标准适用于家用空调国内事业部注塑模具设计与制造。
3.规范性引用文件无4.术语和定义无5.模具分类:根据模架尺寸将模具分为大、中、小三类。
5.1模架尺寸6060以上称为大型模具;5.2模架尺寸3030~6060之间为中型模具;5.3模架尺寸3030以下为小型模具。
6. 模架选用6.1 模架的指定供方6.2 优先选用标准模架,若选用非标模架,应优先选用标准板厚。
6.3 大型非标模架,导柱直径不小于Φ60mm。
6.4 三板细水口的大型/中型模架,导套材质采用青铜石墨套。
例如:分体机底盘。
6.5 大型非标模架导套孔壁厚与模架边不得小于20mm,回针孔壁厚与模架边为35~40mm,回针直径不小于Φ30。
6.6 模架非成型部分的模板零件应采用1050材质, 硬度HB170-220。
6.7 钢导柱、导套及回针等所用材料的表面硬度不低于HRC60 2°。
6.8 A板、B板镶件框壁厚一般为:(小模)30~50mm、(中模)50~80mm、(大模)80~120mm。
6.9 开镶件框后B板厚度一般为:(小模)30~50mm、(中模)50~80mm、(大模)80~120mm。
6.10 镶件成型部位厚度一般为:(小模)25~35mm、(中模)35~50mm、(大模)50~70mm。
7. 模具钢材7.1 模具钢材的选用7.2 模具钢材的指定供方7.3 模具钢材的热处理7.3.1 滑块材料(外观)用2738H、2083H钢料,硬度为 HRC34~38,(非外观)用738、2083钢料,硬度 HRC29~33。
7.3.2 斜顶材料用LKM738钢料,表面进行氮化处理,硬度HV700。
7.3.3 铍铜硬度HRC36~42。
项目1 模块8 模架选用与标准件
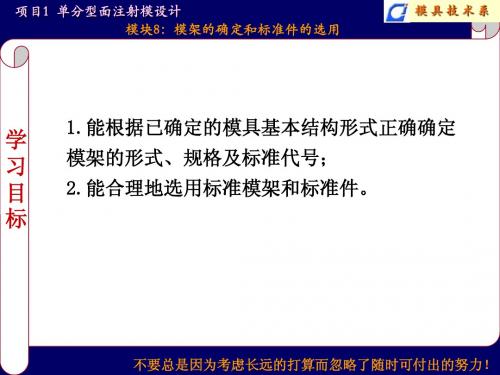
项目1 单分型面注射模设计 模块8:模架的确定和标准件的选用
模技术系
3.推杆
相 关 实 践 知 识
根据制品的结构特点,确定在制品上设置
六根普通的圆顶杆。普通的圆形顶杆按
GB4169.1-1984选用,均可满足顶杆刚度
要求。查手册选用Φ4mm×100mm型号的 圆形顶杆12根。由于件小且精度要求不高 ,推出装置不需要设导向装置。
模具技术系
4.垫块
相 关 理 论 知 识
作用:调节模具闭合高度,形成推出机构所需的推 出空间。 安装要求:两边垫块高度应一致,保证模具上下表 面平行。 材料:中碳钢45
不要总是因为考虑长远的打算而忽略了随时可付出的努力!
项目1 单分型面注射模设计 模块8:模架的确定和标准件的选用
模具技术系
根据图示的塑件零件图以及已确定的模具基本结 构,确定模架的具体形式、规格及标准代号并选 用具体的标准件。
项目1 单分型面注射模设计 模块8:模架的确定和标准件的选用
模具技术系
5.锥面定位机构 当成型精度高的大型、薄壁、深腔塑件时,型腔 内会产生较大侧压力使型芯或型腔偏移,将会导致 相 导柱卡死或损坏。故采用锥面结构。
关 理 论 知 识
不要总是因为考虑长远的打算而忽略了随时可付出的努力!
项目1 单分型面注射模设计 模块8:模架的确定和标准件的选用
模具技术系
(二)支撑零件的设计
相 关 理 论 知 识
动、定模座板
固定板 支承板
垫块
不要总是因为考虑长远的打算而忽略了随时可付出的努力!
项目1 单分型面注射模设计 模块8:模架的确定和标准件的选用
模具技术系
模架支撑相关要求
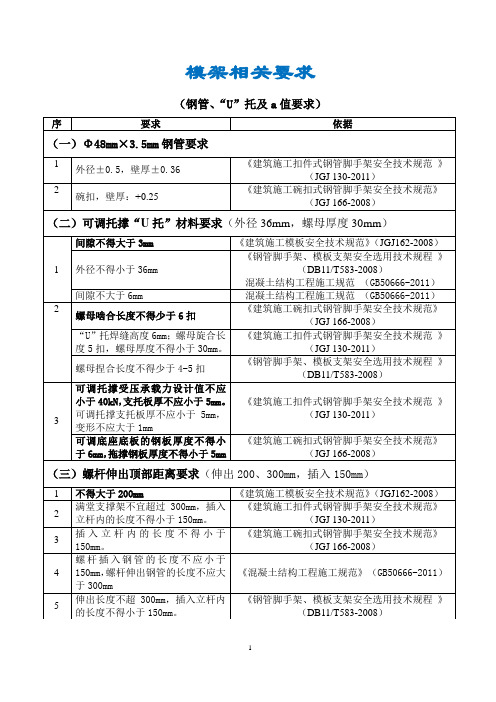
模架相关要求(钢管、“U”托及a值要求)扣件拧紧值40 N²m ~65N²m(混凝土施工规范及选用规程)检查与验收《钢管脚手架、模板支架安全选用技术规程》(DB11/T583-2008)脚手架、模板支架搭设完成钢管扣件式脚手架、模板支架搭设完后对螺栓拧紧扭力矩进行检查模板支架构造要求✧剪刀撑设置、连墙件设置(一)《建筑施工模板安全技术规范》(JGJ162-2008)1.当层高在8~20m时,在最顶步距两水平拉杆中间应加设一道水平拉杆,当层高大于20m时,在最顶两步距水平拉杆中间应分别增加一道水平拉杆。
所有水平拉杆的端部均应与四周建筑物顶紧顶牢。
无处可顶时,应于水平拉杆端部和中部沿竖向设置连续式剪刀撑。
2.(钢管)满堂模板和共享空间模板支架立柱,在外侧周圈应设由下至上的竖向连续式剪刀撑;中间在纵横向应每隔10m左右设由下至上的竖向连续式的剪刀撑,其宽度宜为4~6m,并在剪刀撑部位的顶部、扫地杆处设置水平剪刀撑。
剪刀撑杆件的底端应与地面顶紧,夹角宜为45°~60°。
当建筑层高在8~20m时,除应满足上述规定外,还应在纵横向相邻的两竖向连续式剪刀撑之间增加之字斜撑,在有水平剪刀撑的部位,应在每个剪刀撑中间处增加一道水平剪刀撑。
当建筑层高超过20m时,在满足以上规定的基础上,应将所有之字斜撑全部改为连续式剪刀撑。
3. (钢管)当支架立柱高度超过5m时,应在立柱周圈外侧和中间有结构柱的部位,按水平间距6~9m、竖向间距2~3m与建筑结构设置一个固结点。
●当支架立柱高度超过5m时,应在立柱周圈外侧和中间有结构柱的部位,按水平间距6~9m、竖向间距2~3m与建筑结构设置一个固结点。
(二)《建筑施工扣件式钢管脚手架安全技术规范》(JGJ130-2011)1.(普通型)在架体外侧周边及内部纵、横每5~8m,连续设置剪刀撑,剪刀撑宽度5~8m。
2.竖向剪刀撑顶部交点应连续设置水平剪刀撑,当支撑高度大于8m,或施工总荷载大于15kN/m2,或集中线荷载大于20kN/m的支撑架,,扫地杆的设置层应设置水平剪刀撑,间距不大于8m。
注塑模具设计规范
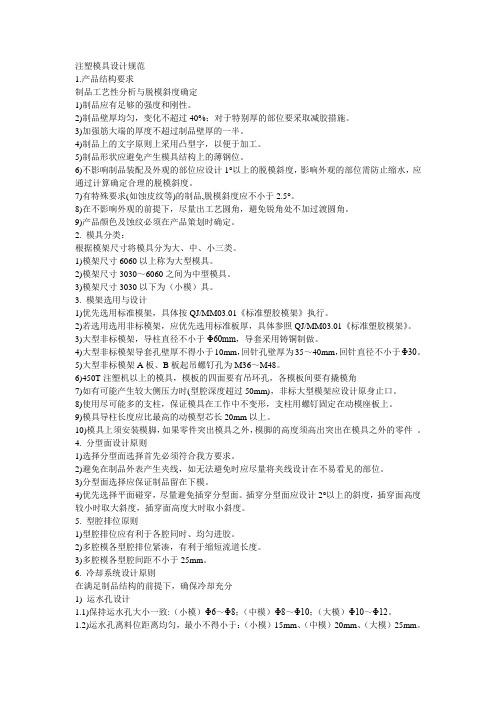
注塑模具设计规范1.产品结构要求制品工艺性分析与脱模斜度确定1)制品应有足够的强度和刚性。
2)制品壁厚均匀,变化不超过40%;对于特别厚的部位要采取减胶措施。
3)加强筋大端的厚度不超过制品壁厚的一半。
4)制品上的文字原则上采用凸型字,以便于加工。
5)制品形状应避免产生模具结构上的薄钢位。
6)不影响制品装配及外观的部位应设计1°以上的脱模斜度,影响外观的部位需防止缩水,应通过计算确定合理的脱模斜度。
7)有特殊要求(如蚀皮纹等)的制品,脱模斜度应不小于2.5°。
8)在不影响外观的前提下,尽量出工艺圆角,避免锐角处不加过渡圆角。
9)产品颜色及蚀纹必须在产品策划时确定。
2. 模具分类:根据模架尺寸将模具分为大、中、小三类。
1)模架尺寸6060以上称为大型模具。
2)模架尺寸3030~6060之间为中型模具。
3)模架尺寸3030以下为(小模)具。
3. 模架选用与设计1)优先选用标准模架,具体按QJ/MM03.01《标准塑胶模架》执行。
2)若选用选用非标模架,应优先选用标准板厚,具体参照QJ/MM03.01《标准塑胶模架》。
3)大型非标模架,导柱直径不小于Φ60mm,导套采用铸铜制做。
4)大型非标模架导套孔壁厚不得小于10mm,回针孔壁厚为35~40mm,回针直径不小于Φ30。
5)大型非标模架A板、B板起吊螺钉孔为M36~M48。
6)450T注塑机以上的模具,模板的四面要有吊环孔,各模板间要有撬模角7)如有可能产生较大侧压力时(型腔深度超过50mm),非标大型模架应设计原身止口。
8)使用尽可能多的支柱,保证模具在工作中不变形,支柱用螺钉固定在动模座板上。
9)模具导柱长度应比最高的动模型芯长20mm以上。
10)模具上须安装模脚,如果零件突出模具之外,模脚的高度须高出突出在模具之外的零件。
4. 分型面设计原则1)选择分型面选择首先必须符合我方要求。
2)避免在制品外表产生夹线,如无法避免时应尽量将夹线设计在不易看见的部位。
注塑模之标准模架

注塑模之标准模架模架之标准模架模具是制造模型的⼯具,按特定形状去成型具有⼀定形状和尺⼨的制品的⼯具。
模具技术在制造业中占⽤很⾼的地位。
对于我们产品设计⼈员来说,模具在⼯作中频繁出现,与我们的⼯作内容关系紧密,因为我们设计出来的产品零件很多需要通过模具来实现,对于模具知识的掌握是必不可少的。
模具(注射模)组成:成型部分、浇注系统、导向机构、脱模装置、侧向分型抽芯机构、温度调节和排⽓系统和标准模架。
⼀,标准模架结构简述不同产品零件所需要的模具不⼀样,⽽模具结构⼜有很多相同的结构,所以为了更加效率地做出模具,⼈们开始使⽤⼀些标准模架,标准模架构成了模具的⾻架,只要换成不同的匹配模仁,就能成型不同的零件,对于整个模具来说,就有三个部分组成:前模板、后模板和模仁,当然,⼀套模具是相当复杂的,这⾥只是介绍模具的⾻架--标准模架。
1标准模架的分类对于塑胶模具,按照基本结构分类,⼀般分为⼆板模式模具(⼤⽔⼝)和三板式模具(细⽔⼝),其中三板式模具⼜可以细分为细⽔⼝模具和简化型细⽔⼝模具,对应的就有⼤⽔⼝模架、细⽔⼝模架和简化型细⽔⼝模架。
2,模架的基本结构(以⼆板模CI型为例)由上图可以看出标准模架的组成(1),板⼦部分:前模底板、后模底板、前模板、后模板、上顶出板、下顶出板、两个模脚。
前后模底板:分别要和注塑机上⾯的定模扳和动模板固定在⼀起。
前后模板:两个模仁就是要镶嵌在两个模板⾥⾯。
上下顶出板:注塑机上⾯的合模系统中的顶出机构会顶住这两块板,进⽽将塑件顶出。
模脚:为零件的顶出⽀撑出⼀定的空间。
(2),固定螺钉部分:前模固定螺钉,、后模板固定螺钉、顶出板锁紧螺钉、模脚固定螺钉。
(3),辅助零部件:导柱与导套、回针。
导柱与导套:导柱在后模板,导套在前模板,当前后模合并时起导向作⽤。
回针:也较复位杆,上⾯套有弹簧,当注塑机上⾯的顶出杆顶出顶出板并将塑件顶出,此时回针上⾯的弹簧使顶出板复位。
(4),辅助零件部分:吊环孔,为了在模具加⼯时⽅便搬运⽽设计的。
模架国标要求

第9章模具的管理模具做为一种高寿命的专用工艺装备有以下生产特点:1.属于单件、多品种生产模具是高寿命专用工艺装备,每副模具只能生产某一特定形状、尺寸和精度的制件。
这就决定了模具生产属于单件、多品种生产规程的性质。
2.客观要求模具生产周期短当前由于产品更新换代的加快和市场的竞争,客观上要求模具生产周期越来越短。
模具的生产管理、设计和工艺工作都应该适应客观要求。
3.模具生产的成套性当某个制件需要多付模具来加工时,各副模具之间往往互相牵连和影响,只有最终制件合格,这一系列模具才算合格。
因此在生产和计划安排上必须充分考虑这一特点。
4.试模和试修由于模具生产的上述特点和模具设计的经验性,模具在装配后必须通过试冲或试压,最后确定是否合格,同时有些部位需要试修才能最后确定。
因此在生产进度安排上必须留有一定的试模周期。
5.模具加工向机械化、精密化和自动化发展目前产品零件对模具精度的要求越来越高,高精度、高寿命、高效率的模具越来越多。
而加上精度主要取决于加工机床的精度、加工工艺条件、测量手段和方法。
目前精密成型磨床、CNC 高精度平面磨床、精密数控电火花线切割机床、高精度连续轨迹坐标磨床以及三坐标测量机的使用越来越普遍,使模具加工向高技术密集型发展。
9.1 模具标准化9.1.1 模具标准化的意义模具是机械工业的基础装备,随着机械工业的发展,模具工业也得到相应的发展。
模具标准化是模具生产技术发展到一定水平的产物,足一项综合性技术工作和管理工作,它涉及到模具设计、制造、材料、检验和使用的各个环节。
同时模具标准化工作又对模具行业的发展起到促进作用,是模具专业化生产、专门化生产和采用现代技术装备的基础。
模具标准化的意义主要体现以下几个方面:1.模具标准化是模具现代化生产的基础模具标准化工作贯穿于模具标准的制定,修定和贯彻执行的全过程。
模具标淮的产生为组织模具专业化和专门化生产奠定了基础,模具标准化的贯彻又推动模具生产和技术的发展。
塑胶模架的选取方法
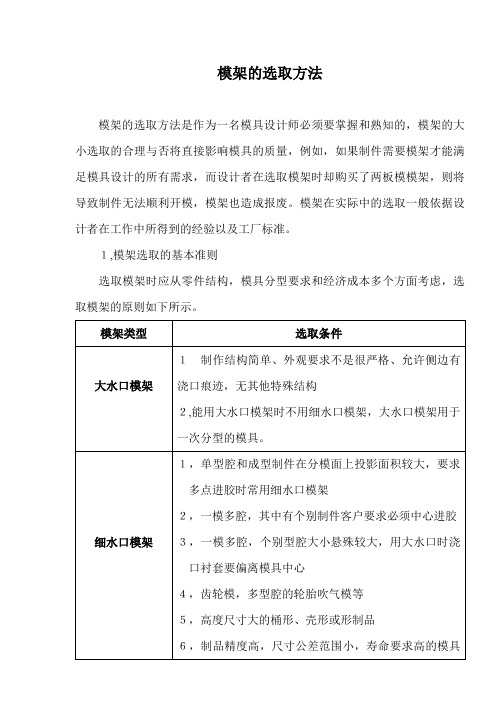
模架的选取方法模架的选取方法是作为一名模具设计师必须要掌握和熟知的,模架的大小选取的合理与否将直接影响模具的质量,例如,如果制件需要模架才能满足模具设计的所有需求,而设计者在选取模架时却购买了两板模模架,则将导致制件无法顺利开模,模架也造成报废。
模架在实际中的选取一般依据设计者在工作中所得到的经验以及工厂标准。
1,模架选取的基本准则选取模架时应从零件结构,模具分型要求和经济成本多个方面考虑,选取模架的原则如下所示。
**当模胚整体尺寸在250mm(包括250mm)以下时,用工字型模模架。
模架在250~350mm时,用直身有面板模架(T型)。
模架在400mm以上并且有滑块时用直身有面板模架(T型),没有滑块时用直身无面板模架(H 型)。
**当A板开框深度较深(一般大于60mm)时,可考虑开通框或选用无面板的模架;有滑块或母模滑块的模架,A板不应开通框,当A板开框深度较深(一般大于60mm)时,可考虑不用面板。
**有推板的模架一定不可以母模导柱后模导套。
**当模仁是圆形时,选用有托板的模架。
**当有滑块或母模滑块时导柱一定要先入10~15mm到斜导柱才可以顶入滑块内,即当导柱特别长时,应母模导柱,公模导套,以方便加长导柱。
2,选取模架的计算方法模架的形式确定后接着开始确定模架的尺寸大小,模架尺寸大小主要取决于模仁尺寸。
模仁尺寸越大,模架尺寸相对也比较大,两者之间成正比关系。
1)确定模架宽度方向尺寸模架顶针板宽度尺寸应与模仁宽度尺寸相当。
两者的相差单边应在5~10mm之间。
2)确定模架长度方向尺寸模仁长度边沿至回针外圆边之间的距离应大于10~15mm,40以上的模架最好取15mm.3)确定模架高度尺寸模架高度尺寸主要指A板、B板和方铁高度,其他模板之间的厚度都是标准件,选取或计算模架无须进行调整。
(1)A板高度:有面板的模架一般等于A板开框深度20~30mm;无面板系列模架一般等于开框深度加30~40mm。
塑胶模具设计规范-1
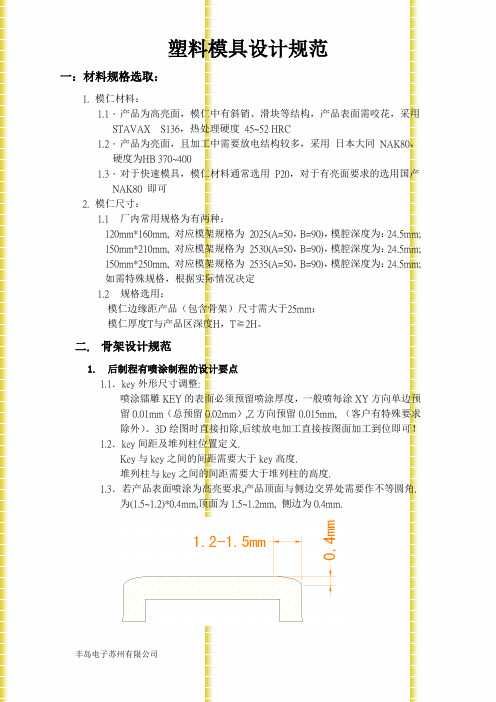
一:材料规格选取:1.模仁材料:1.1.产品为高亮面,模仁中有斜销、滑块等结构,产品表面需咬花,采用STAVAX S136,热处理硬度45~52 HRC1.2.产品为亮面,且加工中需要放电结构较多,采用日本大同NAK80,硬度为HB 370~4001.3.对于快速模具,模仁材料通常选用P20,对于有亮面要求的选用国产NAK80 即可2.模仁尺寸:1.1厂内常用规格为有两种:120mm*160mm, 对应模架规格为2025(A=50,B=90),模腔深度为:24.5mm;150mm*210mm, 对应模架规格为2530(A=50,B=90),模腔深度为:24.5mm;150mm*250mm, 对应模架规格为2535(A=50,B=90),模腔深度为:24.5mm;如需特殊规格,根据实际情况决定1.2规格选用:模仁边缘距产品(包含骨架)尺寸需大于25mm;模仁厚度T与产品区深度H,T≧2H。
二. 骨架设计规范1. 后制程有喷涂制程的设计要点1.1.key外形尺寸调整:喷涂镭雕KEY的表面必须预留喷涂厚度,一般喷每涂XY方向单边预留0.01mm(总预留0.02mm),Z方向预留0.015mm, (客户有特殊要求除外)。
3D绘图时直接扣除,后续放电加工直接按图面加工到位即可!1.2.key间距及堆列柱位置定义.Key与key之间的间距需要大于key高度.堆列柱与key之间的间距需要大于堆列柱的高度.1.3.若产品表面喷涂为高亮要求,产品顶面与侧边交界处需要作不等圆角.为(1.5~1.2)*0.4mm,顶面为1.5~1.2mm, 侧边为0.4mm.2. 后制程有印刷制程的设计要点2.1.不可有任何凸出物高于印刷面,防止凸出物刮伤网板,3.确定进(出)胶方式:按键类产品须有进胶口和出胶口,其方式主要有直接进(出)胶和搭接进(出)胶两种,进胶方式决定于产品结构:①, 产品侧边允许有毛边,或者产品周边有裙边,通常采用直接进胶.②, 产品侧边不允许有毛边,且无裙边的产品通常采用搭接进胶.C.进(出)胶位置及数量:①按键类产品如果进(出)胶选择在长边,长边尺寸小于14mm,尽量做1个进胶1个出胶的方式;(进出胶需错位) 长边尺寸大于14mm,可采用1个进胶2个出胶的方式;②按键类产品如果进(出)胶选择在短边, 采用1个进胶1个出胶的方式即可.(进出胶无需错位)③对于圆环型产品需要做1进3出,分别均匀分布在产品四周.D. 进(出)胶口尺寸:㈠对于直接进出胶:进(出)胶口宽度尺寸设计,视KEY的形状而定,通常进胶比出胶口大0.5~1.0mm。
模具设计常用参数
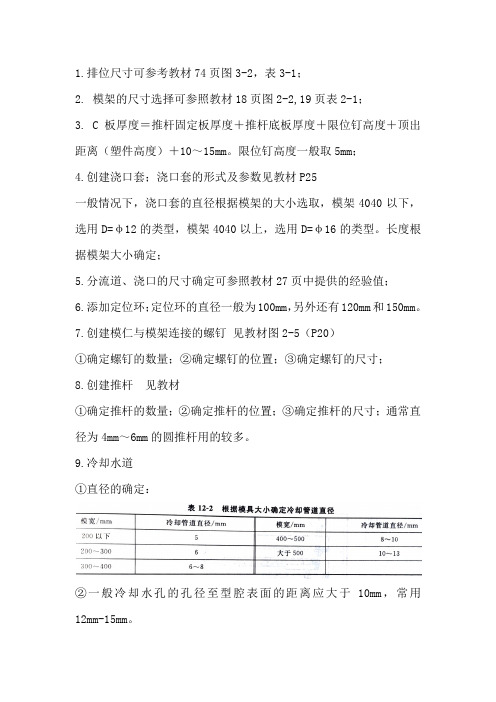
1.排位尺寸可参考教材74页图3-2,表3-1;
2. 模架的尺寸选择可参照教材18页图2-2,19页表2-1;
3. C板厚度=推杆固定板厚度+推杆底板厚度+限位钉高度+顶出距离(塑件高度)+10~15mm。
限位钉高度一般取5mm;
4.创建浇口套;浇口套的形式及参数见教材P25
一般情况下,浇口套的直径根据模架的大小选取,模架4040以下,选用D=φ12的类型,模架4040以上,选用D=φ16的类型。
长度根据模架大小确定;
5.分流道、浇口的尺寸确定可参照教材27页中提供的经验值;
6.添加定位环;定位环的直径一般为100mm,另外还有120mm和150mm。
7.创建模仁与模架连接的螺钉见教材图2-5(P20)
①确定螺钉的数量;②确定螺钉的位置;③确定螺钉的尺寸;
8.创建推杆见教材
①确定推杆的数量;②确定推杆的位置;③确定推杆的尺寸;通常直径为4mm~6mm的圆推杆用的较多。
9.冷却水道
①直径的确定:
②一般冷却水孔的孔径至型腔表面的距离应大于10mm,常用12mm-15mm。
③水喉间距:。
模架加工要求

用料标准:
1、未注明的所有模板和模架小零件都用S50C或类似性能的材料。
2、模架导向零件(包括复位杆)统一用SUJ-2材料硬度HRC58以上或类似性能的材料。
3、垃圾钉使用S45C材料硬度HRC48~52或类似性能的材料。
4、开模限距拉杆使用较高韧性的材料,比如SCM435,硬度在HRC33~38等类似性能的材料。
加工标准:
1、加工以3D模型为准,3D模型中有的零件必须全部加工完毕。
2、精框的长度、宽度、深度公差为0~+0.02mm,主要模板(包括A板、B板、定模垫板、动模垫板、模脚、顶针垫板等)厚度公差为±0.02mm。
3、如未特别注明,所有水嘴接头螺纹统一用PT1/4,所有水孔赌头螺纹为直径8mm用PT1/8’,直径10mm用PT1/4’。
4、模架出厂前必须装配成套,不允许有散零件。
5. 模架所有倒角为C1.5,倒角要光滑匀称。
所有表面无划伤要光亮平整。
另外(如果图纸是公制模架):
1、模架装配图中用指引线指出的所有零件都要加工(包括热流道板)
2、所有模架用的标准配件允许全部用最接近尺寸的公制零件,相应的孔加工都可以改为公制,水路孔直径也同样可以改为最接近的整数公制尺寸。
3、所有的精口袋、精圆槽、通槽尺寸保留两位小数,顶出孔位置也保留英制的尺寸。
4、最终贵司的加工图纸须待我方确认方可开始加工。
5、附件中模锁图是我公司加工的零件,需要贵司按照此零件配加工精框。
6,模架厂一般配好的零件如:平衡块,支撑柱,精定位,垃圾钉等。
其余小配件我司加工,此标准即日执行!。
模架的尺寸确定

d(mm) 6
25~32(30)
8
32~38(35)
10
38~50(45)
12
44~64(50)
16
塑料注射模具设计——池寅生
6
50~76(60)
20
②模仁至定模板上表面的厚度h3 = 25~35 mm ③定模仁厚度h2 = 制品厚度h+型腔背后模芯厚度h1 ④定模板厚度h4 =定模仁厚度h2+模仁至定模板上表面的厚度h3
六、模架的选择
1、确定模架组合形式:根据塑件成型所需的模具总体结构和技术要求 2、确定模架的类型:根据浇口和推出结构的特点 3、模架的尺寸确定 模架核心尺寸 定模板和动模板的周界尺寸(宽和长) 定模板和动模板的厚度尺寸 垫块的厚度
模架其他组成零件的尺寸
塑料注射模具设计——池寅生
1
塑料注射模具设计——池寅生
产品(或型腔)之间的距离b
模仁尺寸B0×L0
无流道:b一般取15~25mm。
B0=2a+2w+ b′ L0=2a+2l+ b
型腔之间布置有流道:b′可取
>200×200时,必须做成拼块结塑构料注。射模具设计——2池5寅~4生0mm,一般取30mm。 4
B
BK
B0
150
35
80
200
45
110
250
9
七、注射模具的排位设计
塑件产品在模具中的摆放位置的设计 ——决定了模具型腔的位置关系; ——确定了模具的总体结构和尺寸; ——直接影响后期的注射工艺; 设计原则 1、力求平衡、对称。 ①各型腔在相同温度下同时充模。
采用平衡布局
塑料注射模具设计——池寅生
(仅供参考)模架的尺寸确定

11
②浇口平衡 防止模具胀开力不平衡
③大小制品对称布置
④模具力平衡,即注射压力中心与主流道中心重合,防止飞边。
塑料注射模具设计——池寅生
12
2、流道尽可能短,以降低废料率、成型周期和热损失。H型排位优于 环形和对称型。 3、对高精度制品,型腔数目尽可能少。因为每增加一个型腔,制品 精度下降4%。精密模具型腔数目一般不超过4个。 4、相同颜色、相同原料。 5、结构紧凑,节约钢材。
d(mm) 6
25~32(30)
8
32~38(35)
10
38~50(45)
12
44~64(50)
16
塑料注射模具设计——池寅生
6
50~76(60)
20
②模仁至定模板上表面的厚度h3 = 25~35 mm ③定模仁厚度h2 = 制品厚度h+型腔背后模芯厚度h1 ④定模板厚度h4 =定模仁厚度h2+模仁至定模板上表面的厚度h3
9
七、注射模具的排位设计
塑件产品在模具中的摆放位置的设计 ——决定了模具型腔的位置关系; ——确定了模具的总体结构和尺寸; ——直接影响后期的注射工艺; 设计原则 1、力求平衡、对称。 ①各型腔在相同温度下同时充模。
采用平衡布局
塑料注射模具设计——池寅生
10
非平衡布局可通过调节浇口尺寸达到平衡
塑料注射模具设计——池寅生
2
以一模四腔为例,说明模架 核心尺寸的确定方法
制品——w l h
模仁(模芯)——B0 L0 h2 h6
模架规格(核心)尺寸——B L h4 h8
塑料注射模具设计——池寅生
3
型腔到模仁边的距离a
a = 0.2×l + 17 通常25~30 一模一腔(产品长和宽) 250以下:15,20,25,30mm 400~800:40,50,60mm 注:对模芯边走冷却水的 深腔模具或带侧抽芯的模 具,a可适当增加。
产品排位设计,模仁尺寸及模架大小的确定
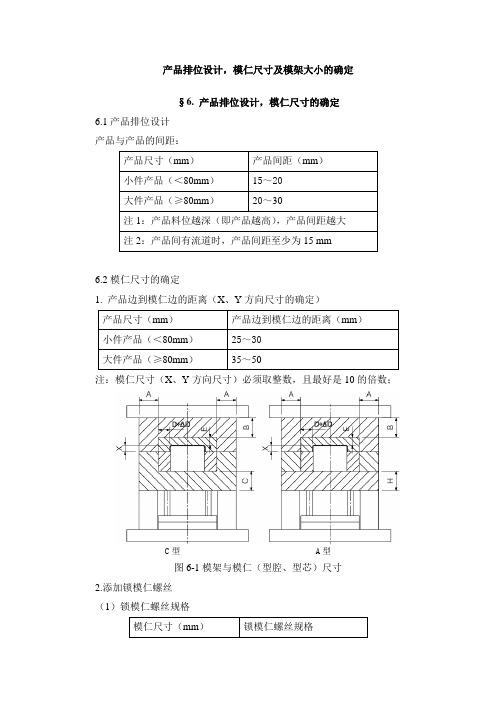
产品排位设计,模仁尺寸及模架大小的确定§6. 产品排位设计,模仁尺寸的确定6.1产品排位设计产品与产品的间距:产品尺寸(mm)产品间距(mm)小件产品(<80mm)15~20大件产品(≥80mm)20~30注1:产品料位越深(即产品越高),产品间距越大注2:产品间有流道时,产品间距至少为15 mm6.2模仁尺寸的确定1. 产品边到模仁边的距离(X、Y方向尺寸的确定)产品尺寸(mm)产品边到模仁边的距离(mm)小件产品(<80mm)25~30大件产品(≥80mm)35~50注:模仁尺寸(X、Y方向尺寸)必须取整数,且最好是10的倍数;C型 A型图6-1模架与模仁(型腔、型芯)尺寸2.添加锁模仁螺丝(1)锁模仁螺丝规格模仁尺寸(mm)锁模仁螺丝规格(2)锁模仁螺丝布置3.初步绘制冷却水道,以确定模仁尺寸(1)冷却水道的直径一般为Φ6、Φ8、Φ10,优先采用大直径冷却水道,其冷却效果较好;(2)冷却水道边到螺丝孔边、顶针孔边的距离最少为4mm;(3)冷却水道中心到模仁边的距离不少于12mm;(4)冷却水道边到产品边的距离不能太近,一般在15mm左右。
4. 模仁高度(厚度)尺寸的确定(Z方向尺寸的确定)度为整数。
§7. 产品排位设计,模架大小的确定7.1模架大小的确定(1)模架的宽×长模架的宽与长由模仁的宽与长和模仁边到A板边或B板边的距离确定模仁边到A板边或B板边的距离一般取50~70mm,于是:模架宽=模仁宽+2×(50~70)mm模架长=模仁长+2×(50~70)mm模仁大小与模架的关系见图7-1。
图中有关尺寸可参考表7-1的经验数据确定。
()图7-1模仁大小与模架注:表中数据为一般情况下的模具设计经验尺寸。
(2)A板和B板的厚度大水口模(二板模):细水口模(三板模):确定本实例的模架为CI2023-A60-B80-C70大水口模架。
“CI”代表工字模,“A”表示A板,“B”表示B板,“C”表示C板(方铁、垫块)7.2调出标准模架(1)调出CI2023-A60-B80-C70标准模架(2)检验调出的模架是否合适a.将后模视图调入模架的后模视图中,调出合适的复位弹簧,检验模仁边到弹簧孔边的距离一般应有5~10mm;(回针中心到距离=ΦD+5~10mm,ΦD为回针直径;或模仁边到回针边的距离≥10~15mm,(40 以上的模胚最好取15mm))。
标准模架尺寸

标准模架尺寸标准模架尺寸是指在工业生产中常用的模架尺寸标准,它对于模具设计和生产具有重要的指导意义。
标准模架尺寸的确定,可以帮助企业规范生产流程,提高生产效率,降低生产成本,提高产品质量。
下面我们将介绍一些常见的标准模架尺寸及其应用。
首先,我们来介绍一下常见的标准模架尺寸。
在模具设计中,常用的标准模架尺寸包括A类、B类、C类、D类四种尺寸。
A类模架尺寸主要用于小型模具,其尺寸范围为200mm×200mm至400mm×400mm。
B类模架尺寸适用于中等尺寸的模具,尺寸范围为400mm×400mm至800mm×800mm。
C类模架尺寸适用于大型模具,尺寸范围为800mm×800mm至1600mm×1600mm。
D类模架尺寸适用于超大型模具,尺寸范围为1600mm×1600mm以上。
这些标准模架尺寸可以根据具体的模具设计要求进行选择和应用。
其次,我们来谈谈标准模架尺寸的应用。
在模具设计和生产中,选择合适的标准模架尺寸可以提高模具的稳定性和精度,减少加工工序,降低成本,提高生产效率。
同时,标准模架尺寸的应用也有利于模具的标准化和通用化,方便模具的更换和维护,提高生产的灵活性和适应性。
因此,合理应用标准模架尺寸对于模具设计和生产具有重要的意义。
最后,我们需要注意一些关于标准模架尺寸的问题。
在选择标准模架尺寸时,需要根据具体的模具设计要求和生产工艺进行合理的选择,避免盲目跟风或者一刀切的情况。
同时,需要注意标准模架尺寸的更新和改进,及时掌握最新的标准和技术,不断提高模具设计和生产水平。
另外,标准模架尺寸的应用也需要与模具材料、加工设备、生产工艺等方面进行综合考虑,确保模具的质量和性能。
总之,标准模架尺寸对于模具设计和生产具有重要的指导意义,合理选择和应用标准模架尺寸可以提高生产效率,降低生产成本,提高产品质量。
因此,我们需要认真学习和理解标准模架尺寸的相关知识,不断提高自身的设计和生产水平,为企业的发展做出更大的贡献。
模具相关尺寸的计算:
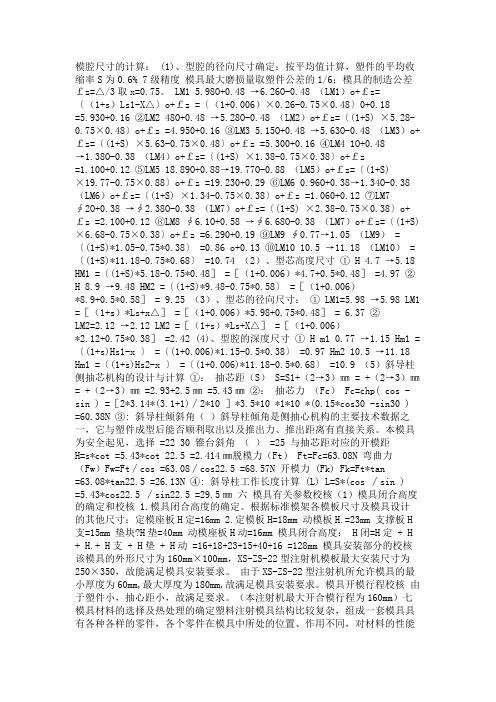
模腔尺寸的计算: (1)、型腔的径向尺寸确定:按平均值计算,塑件的平均收缩率S为0.6% 7级精度模具最大磨损量取塑件公差的1/6;模具的制造公差£z=△/3取x=0.75。
LM1 5.98O+0.48 →6.26O-0.48 (LM1)o+£z=〔(1+s)Ls1-X△〕o+£z =〔(1+0.006)×0.26-0.75×0.48〕0+0.18=5.930+0.16 ②LM2 48O+0.48 →5.28O-0.48 (LM2)o+£z=〔(1+S) ×5.28-0.75×0.48〕o+£z =4.950+0.16 ③LM3 5.15O+0.48 →5.63O-0.48 (LM3)o+£z=〔(1+S) ×5.63-0.75×0.48〕o+£z =5.300+0.16 ④LM4 1O+0.48→1.38O-0.38 (LM4)o+£z=〔(1+S) ×1.38-0.75×0.38〕o+£z=1.100+0.12 ⑤LM5 18.89O+0.88→19.77O-0.88 (LM5)o+£z=〔(1+S)×19.77-0.75×0.88〕o+£z =19.230+0.29 ⑥LM6 0.96O+0.38→1.34O-0.38 (LM6)o+£z=〔(1+S) ×1.34-0.75×0.38〕o+£z =1.060+0.12 ⑦LM7∮2O+0.38 →∮2.38O-0.38 (LM7)o+£z=〔(1+S) ×2.38-0.75×0.38〕o+£z =2.100+0.12 ⑧LM8 ∮6.1O+0.58 →∮6.68O-0.38 (LM7)o+£z=〔(1+S) ×6.68-0.75×0.38〕o+£z =6.290+0.19 ⑨LM9 ∮0.77→1.05 (LM9) =〔(1+S)*1.05-0.75*0.38〕=0.86 o+0.13 ⑩LM10 10.5 →11.18 (LM10) =〔(1+S)*11.18-0.75*0.68〕 =10.74 (2)、型芯高度尺寸① H 4.7 →5.18 HM1 =〔(1+S)*5.18-0.75*0.48] =[(1+0.006)*4.7+0.5*0.48]=4.97 ② H 8.9 →9.48 HM2 =〔(1+S)*9.48-0.75*0.58〕 =[(1+0.006)*8.9+0.5*0.58] = 9.25 (3)、型芯的径向尺寸:① LM1=5.98 →5.98 LM1 =[(1+s)*Ls+x△] =[(1+0.006)*5.98+0.75*0.48]= 6.37 ②LM2=2.12 →2.12 LM2 =[(1+s)*Ls+X△] =[(1+0.006)*2.12+0.75*0.38] =2.42 (4)、型腔的深度尺寸① H m1 0.77 →1.15 Hm1 =〔(1+s)Hs1-x 〕 =〔(1+0.006)*1.15-0.5*0.38〕=0.97 Hm2 10.5 →11.18 Hm1 =〔(1+s)Hs2-x 〕 =〔(1+0.006)*11.18-0.5*0.68〕 =10.9 (5)斜导柱侧抽芯机构的设计与计算①:抽芯距(S) S=S1+(2→3)㎜ = +(2→3)㎜= +(2→3)㎜ =2.93+2.5㎜ =5.43㎜②:抽芯力(Fc) Fc=chp( cos -sin ) =[2*3.14*(3.1+1)∕2*10 ]*3.5*10 *1*10 *(0.15*cos30 -sin30 ) =60.38N ③: 斜导柱倾斜角()斜导柱倾角是侧抽心机构的主要技术数据之一,它与塑件成型后能否顺利取出以及推出力、推出距离有直接关系。
产品排位设计,模仁尺寸及模架大小的确定
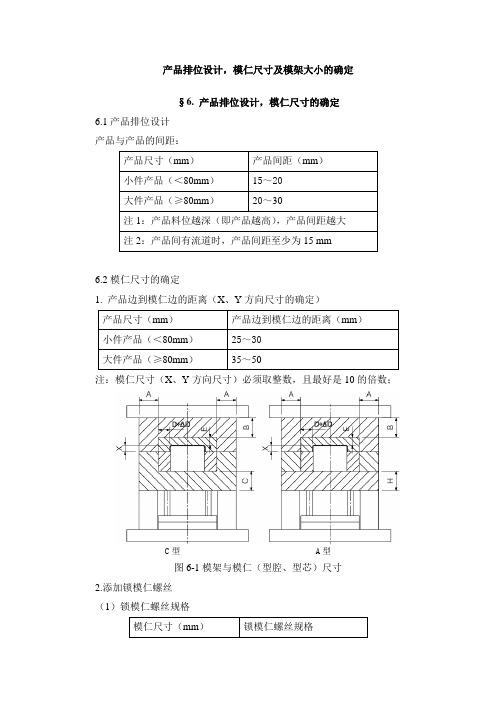
产品排位设计,模仁尺寸及模架大小的确定§6. 产品排位设计,模仁尺寸的确定6.1产品排位设计产品与产品的间距:产品尺寸(mm)产品间距(mm)小件产品(<80mm)15~20大件产品(≥80mm)20~30注1:产品料位越深(即产品越高),产品间距越大注2:产品间有流道时,产品间距至少为15 mm6.2模仁尺寸的确定1. 产品边到模仁边的距离(X、Y方向尺寸的确定)产品尺寸(mm)产品边到模仁边的距离(mm)小件产品(<80mm)25~30大件产品(≥80mm)35~50注:模仁尺寸(X、Y方向尺寸)必须取整数,且最好是10的倍数;C型 A型图6-1模架与模仁(型腔、型芯)尺寸2.添加锁模仁螺丝(1)锁模仁螺丝规格模仁尺寸(mm)锁模仁螺丝规格(2)锁模仁螺丝布置3.初步绘制冷却水道,以确定模仁尺寸(1)冷却水道的直径一般为Φ6、Φ8、Φ10,优先采用大直径冷却水道,其冷却效果较好;(2)冷却水道边到螺丝孔边、顶针孔边的距离最少为4mm;(3)冷却水道中心到模仁边的距离不少于12mm;(4)冷却水道边到产品边的距离不能太近,一般在15mm左右。
4. 模仁高度(厚度)尺寸的确定(Z方向尺寸的确定)度为整数。
§7. 产品排位设计,模架大小的确定7.1模架大小的确定(1)模架的宽×长模架的宽与长由模仁的宽与长和模仁边到A板边或B板边的距离确定模仁边到A板边或B板边的距离一般取50~70mm,于是:模架宽=模仁宽+2×(50~70)mm模架长=模仁长+2×(50~70)mm模仁大小与模架的关系见图7-1。
图中有关尺寸可参考表7-1的经验数据确定。
()图7-1模仁大小与模架注:表中数据为一般情况下的模具设计经验尺寸。
(2)A板和B板的厚度大水口模(二板模):细水口模(三板模):确定本实例的模架为CI2023-A60-B80-C70大水口模架。
“CI”代表工字模,“A”表示A板,“B”表示B板,“C”表示C板(方铁、垫块)7.2调出标准模架(1)调出CI2023-A60-B80-C70标准模架(2)检验调出的模架是否合适a.将后模视图调入模架的后模视图中,调出合适的复位弹簧,检验模仁边到弹簧孔边的距离一般应有5~10mm;(回针中心到距离=ΦD+5~10mm,ΦD为回针直径;或模仁边到回针边的距离≥10~15mm,(40 以上的模胚最好取15mm))。
模架和模仁尺寸的确定

模架和模仁尺寸的确定
模架与镶件尺寸的确定
模具的大小主要取决于塑料制品的大小和结构。
对于模具而言吗,在保证足够强度的前提下,结构越紧凑越好。
根据产品的外形尺寸(平面投影面积与高度),以及产品的本身结构(测向分型滑块等结构)可以确定模仁的外形尺寸,确定好摸仁的大小后,可参考下面的数据:
以上数据,仅作为一般性结构的塑料制品的摸架参考,对于特殊的塑料制品,应注意以下几点:
1、当产品高度过高时(产品高度D≦X),应适合加
大“D”,加大值△D=(X-D)/2;
2、有时为了冷却水道的需要,也要对模仁的尺寸加
以调整,已达到较好冷却效果;
3、结构复杂需特殊分型或顶出机构,或有侧向分型
结构需要作滑块时,应根据不同情况适当调整模
仁和模架的大小以及各模板的厚度,与保证模架
的强度。