飞机制造中的尺寸管理和容差仿真分析技术
飞机薄壁零件装配偏差建模与仿真分析

艺, 如图 2 所示。
图 3 飞机薄壁零件装配过程
(1) 薄壁零件的确定性定位
将进入装配的飞机薄壁零件基于 3 - 2 - 1 原理通
过工装进行确定性定位, 此时将薄壁零件视为刚体,
不发生弹性变形。
确定性定位法是指依据 3 - 2 - 1 定位原则完全约
LIU Yinjie, TIAN Xitian, GENG Junhao, ZHANG Min, MA Liping
( School of Mechanical Engineering, Northwestern Polytechnical University, Xian Shaanxi 710072, China)
第 48 卷 第 2 期
Jan 2020
Vol 48 No 2
DOI: 10.3969 / j issn 1001-3881 2020 02 031
本文引用格式: 刘殷杰,田锡天,耿俊浩,等.飞机薄壁零件装配偏差建模与仿真分析[ J] .机床与液压,2020,48(2) :138-143.
这些零件具有刚度小、 尺寸大、 壁厚薄等特点,
在装配过程中, 随着装配工艺过程的进行, 零件自身
制造偏差与夹紧力、 铆接力等造成的装配变形耦合,
造成装配精度变化, 进而影响飞机装配质量。
为保证飞机装配质量, 需要找出影响飞机装配精
度的影响因素, 即装配偏差源, 对偏差源进行分析和
优化, 使装配偏差满足要求。 飞机薄壁零件装配偏差
并在此基础上基于偏差源敏感度实现装配精度的优化。
1 飞机薄壁零件装配偏差源分析
薄壁零件是指由各种薄板及加强筋构成的轻量化
飞行器制造中的仿真验证技术

飞行器制造中的仿真验证技术在现代航空航天领域,飞行器制造是一项极其复杂且高要求的工程。
为了确保飞行器的安全性、可靠性和性能,仿真验证技术发挥着至关重要的作用。
仿真验证技术是什么呢?简单来说,它是一种在飞行器实际制造之前,通过计算机模型和模拟软件来预测和评估飞行器性能、结构强度、飞行特性等方面的技术手段。
这就好比在真正踏上旅途之前,先通过地图和规划来预想可能遇到的情况和结果。
首先,在飞行器的结构设计阶段,仿真验证技术就开始大展身手。
通过建立精细的三维模型,工程师们可以模拟飞行器在各种受力情况下的结构响应,比如飞行中的空气动力、起降时的冲击、高空的低温和低压环境等。
这样一来,就能提前发现潜在的结构弱点,优化设计方案,避免在实际制造后才发现问题,从而节省大量的时间和成本。
在材料选择方面,仿真验证技术同样功不可没。
不同的材料具有不同的性能特点,如强度、刚度、疲劳寿命等。
通过模拟材料在各种工况下的表现,工程师可以准确地选择最适合的材料,确保飞行器在复杂的使用环境中能够长期稳定运行。
再来说说飞行性能的仿真验证。
这包括对飞行器的升力、阻力、稳定性、操纵性等方面的模拟。
通过模拟不同的飞行条件,如不同的速度、高度、姿态,工程师可以评估飞行器的性能是否满足设计要求,并对飞行控制系统进行优化和调试。
而且,仿真验证技术在飞行器的热管理方面也有着重要的应用。
飞行器在高速飞行时,会因空气摩擦产生大量的热量,发动机等部件也会散发出高温。
通过热仿真,可以分析热量的分布和传递情况,设计合理的散热方案,保证飞行器各部件在正常的温度范围内工作。
另外,在飞行器的制造工艺方面,仿真验证技术也能提供有力的支持。
例如,在焊接、铸造、复合材料成型等工艺过程中,通过模拟可以预测可能出现的缺陷和变形,优化工艺参数,提高制造质量和效率。
那么,仿真验证技术是如何实现的呢?这离不开强大的计算机软件和硬件支持。
常见的仿真软件包括有限元分析软件、计算流体力学软件、多体动力学软件等。
飞机薄壁零件装配偏差建模与仿真分析

飞机薄壁零件装配偏差建模与仿真分析摘要飞机装配是整个飞机制造过程的关键和核心,为保证飞机装配质量和性能,飞机装配对装配精度要求极高。
飞机结构中包含大量形状复杂的柔性薄壁零件,如机翼、机身的蒙皮结构,在装配过程中,由于零件制造偏差、夹具定位偏差、装配变形及装配过程中随机误差的耦合作用,不可避免地产生装配偏差,造成装配精度超差,直接影响到后续部件及总装的装配质量,最终影响飞机的整体性能。
关键词:飞机薄壁零件;确定性定位;影响系数法;蒙特卡洛法中图分类号:U235文献标识码:A1、飞机薄壁零件装配偏差源分析薄壁零件是指由各种薄板及加强筋构成的轻量化结构,其外形直径与厚度比通常为50~200,壁厚较小,质量较轻。
飞机结构中包含大量的薄壁零件,如机翼和机身壁板中的蒙皮、长桁等。
这些零件具有刚度小、尺寸大、壁厚薄等特点,在装配过程中,随着装配工艺过程的进行,零件自身制造偏差与夹紧力、铆接力等造成的装配变形耦合,造成装配精度变化,进而影响飞机装配质量。
为保证飞机装配质量,需要找出影响飞机装配精度的影响因素,即装配偏差源,对偏差源进行分析和优化,使装配偏差满足要求。
飞机薄壁零件装配偏差源主要有3类:零组件偏差、工装夹具偏差、装配工艺。
(1)零件偏差在零件制造过程中,受加工方法、制造设备精度和材料内应力等因素的影响,使零件产生初始制造偏差。
同时,由于零件中存在大量刚度较小的薄壁零件,在装配过程中受自身重力、连接力等作用产生变形,与初始制造偏差耦合,沿着偏差传递路径传递形成最终装配偏差。
(2)工装夹具偏差在飞机装配中,零组件通过工装夹具保证外形、位置等的准确性,工装夹具起着至关重要的作用。
工装夹具除在制造过程中产生的偏差外,在安装调试时会受到测量设备的精度、自身重力等因素的影响,产生定位偏差,影响最终装配精度。
1.装配工艺装配工艺包括零组件定位方案、装配顺序、连接工艺等,装配工艺的好坏决定着装配精度的高低。
定位方案和装配顺序决定了偏差累积传递方向,铆接等连接工艺使零件产生变形,造成装配精度变化。
飞机机身装配工艺及仿真技术研究
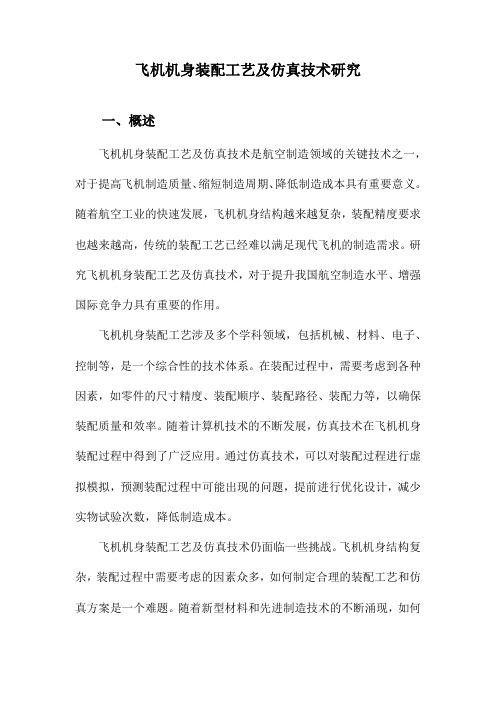
飞机机身装配工艺及仿真技术研究一、概述飞机机身装配工艺及仿真技术是航空制造领域的关键技术之一,对于提高飞机制造质量、缩短制造周期、降低制造成本具有重要意义。
随着航空工业的快速发展,飞机机身结构越来越复杂,装配精度要求也越来越高,传统的装配工艺已经难以满足现代飞机的制造需求。
研究飞机机身装配工艺及仿真技术,对于提升我国航空制造水平、增强国际竞争力具有重要的作用。
飞机机身装配工艺涉及多个学科领域,包括机械、材料、电子、控制等,是一个综合性的技术体系。
在装配过程中,需要考虑到各种因素,如零件的尺寸精度、装配顺序、装配路径、装配力等,以确保装配质量和效率。
随着计算机技术的不断发展,仿真技术在飞机机身装配过程中得到了广泛应用。
通过仿真技术,可以对装配过程进行虚拟模拟,预测装配过程中可能出现的问题,提前进行优化设计,减少实物试验次数,降低制造成本。
飞机机身装配工艺及仿真技术仍面临一些挑战。
飞机机身结构复杂,装配过程中需要考虑的因素众多,如何制定合理的装配工艺和仿真方案是一个难题。
随着新型材料和先进制造技术的不断涌现,如何将这些新技术应用于飞机机身装配过程中,提高装配质量和效率,也是当前研究的热点和难点。
本文旨在深入研究飞机机身装配工艺及仿真技术,探讨其发展现状和趋势,分析存在的问题和挑战,并提出相应的解决方案和优化措施。
通过本文的研究,可以为航空制造领域的发展提供有益的参考和借鉴。
1. 飞机机身装配的重要性飞机机身装配是飞机制造过程中的关键环节,其重要性不言而喻。
机身作为飞机的主体结构,承载着飞机的各种功能和性能要求,其装配质量直接关系到飞机的安全性、舒适性和经济性。
飞机机身装配工艺的研究与改进,对于提升飞机制造水平、保障飞行安全具有重要意义。
飞机机身装配的精度直接影响到飞机的整体性能。
机身各部件之间的连接必须精确无误,以确保飞机在空中能够稳定飞行。
任何微小的装配误差都可能导致飞机在飞行过程中出现不稳定现象,甚至引发安全事故。
航空器制造中虚拟仿真技术的应用

航空器制造中虚拟仿真技术的应用在当今科技飞速发展的时代,航空器制造领域正经历着一场深刻的变革。
虚拟仿真技术作为一项前沿的科技手段,正逐渐成为航空器制造过程中不可或缺的重要工具。
它不仅提高了制造效率和质量,还降低了成本和风险,为航空器制造业带来了前所未有的发展机遇。
虚拟仿真技术在航空器设计阶段发挥着关键作用。
传统的设计方法往往依赖于经验和反复的物理样机试验,不仅耗时费力,而且成本高昂。
而通过虚拟仿真技术,设计人员可以在计算机中创建出高度逼真的三维模型,对航空器的外形、结构、气动性能等进行模拟和优化。
例如,利用计算流体动力学(CFD)软件,可以对航空器在不同飞行条件下的气流流动进行精确模拟,从而优化机翼和机身的形状,减少阻力,提高飞行效率。
此外,虚拟仿真技术还可以对航空器的结构强度和疲劳寿命进行预测,提前发现潜在的设计缺陷,避免在实际制造中出现问题。
在航空器制造的工艺规划方面,虚拟仿真技术同样具有重要意义。
制造工艺的合理规划直接影响到产品的质量、成本和生产周期。
通过虚拟仿真技术,可以对零部件的加工过程、装配顺序和工装夹具的设计进行模拟和验证。
例如,在数控加工中,可以模拟刀具的路径和切削参数,优化加工工艺,提高加工精度和表面质量。
在装配过程中,可以提前发现零部件之间的干涉和装配难度,优化装配顺序和工装夹具的设计,提高装配效率和质量。
虚拟仿真技术还在航空器的人机工程学研究中发挥着重要作用。
航空器的驾驶舱和客舱设计需要充分考虑人机交互的舒适性和安全性。
通过虚拟仿真技术,可以创建出虚拟的驾驶舱和客舱环境,让飞行员和乘客在虚拟环境中进行体验和评估。
设计人员可以根据反馈意见,对座椅的布局、操纵杆的位置、仪表盘的设计等进行优化,提高人机交互的效率和舒适性。
在航空器的试飞和测试阶段,虚拟仿真技术也能够提供有力的支持。
传统的试飞需要耗费大量的时间和资源,而且存在一定的风险。
而通过虚拟仿真技术,可以在实验室中对航空器的飞行性能、控制系统和故障模式进行模拟和测试。
飞机结构仿真分析及其优化设计

飞机结构仿真分析及其优化设计近年来,随着飞机制造技术的发展和飞机性能要求的提高,飞机结构仿真分析成为飞机结构设计和制造中的必要环节。
通过仿真分析,可以评估飞机结构的强度、疲劳寿命和耐损性等重要性能指标,从而指导优化设计。
本文将介绍飞机结构仿真分析的方法和优化设计的思路。
一. 飞机结构分析的方法飞机结构分析是通过计算机数值模拟方法,分析对结构的应力、位移、变形、振动、疲劳寿命等现象进行分析,并在此基础上对结构进行设计和优化。
具体来说,飞机结构分析可以分为以下几个步骤:1. 建立数值模型建立数值模型是飞机结构分析的第一步,其目的是将实际飞机结构抽象成数学模型,以便进行计算机仿真。
建立数值模型时,需要考虑飞机结构的各种几何和材料特性,如外形、结构布局、材料类型、初始条件等。
2. 网格划分飞机结构分析需要将结构抽象成一系列的单元,这些单元之间通过节点相互连接。
这种单元与节点的网格化可以大大简化计算负荷,减少计算时间。
在进行网格化时,需要根据飞机结构的几何和物理特性,选择适宜的单元尺寸和节点数量。
3. 边界条件设定在进行结构分析时,需要设定结构的边界条件,包括支撑、加载等信息。
这些边界条件需要准确地反映实际情况,以便保证分析的准确性。
4. 应力计算应力计算是飞机结构分析的重要环节,其目的是计算每个单元上的应力值。
应力计算需要考虑各种载荷因素,如自重、飞行荷载、风载等,以及外部因素,如温度、湿度、压力等。
为了提高计算精度,应该选用合适的应力计算方法,如有限元分析算法、热损伤感应算法等。
5. 变形和振动分析变形和振动分析是飞机结构仿真中的重要环节。
变形和振动分析旨在评估飞机结构在各种载荷情况下产生的位移和振动情况,以便检查结构是否满足性能要求。
变形和振动分析需要考虑不同载荷下结构的动态响应特性,对于不同类型的飞机,需要采用不同的分析方法。
6. 疲劳寿命评估疲劳寿命评估是飞机结构分析中的关键环节。
在飞机服役期间,受到载荷作用的飞机结构会出现疲劳损伤,从而导致安全隐患。
飞机装配容差分析技术探讨

飞机装配容差分析技术探讨摘要:飞机装配技术是指采用科学、合理的加工工艺,以提高装配的合理性,减少装配误差,确保飞机组装的可靠性和精度。
飞机装配容差分析的技术过程主要是对各种工作的基准进行设计、确定几何容差等,过程比较繁琐。
而飞机装配容差分析的核心技术是准确地确定设计标准,自主地选取合理的容差累积计算模式和计算方法,并在此基础上提出了完善的技术体系,引入了优秀的技术人员以及先进的技术,使飞机的装配容差分析技术得到进一步的提升。
关键词:飞机装配;容差分析;设计基准飞机装配是指采用一套专业的加工工艺,对飞机的各部件、工装等进行科学、合理的协调,使其达到精确、可靠的目的,从而达到改善飞机生产质量、保障飞行安全的目的。
近几年,随着经济的快速发展和社会的发展,对飞机制造技术提出的要求也越来越高。
飞机装配容差分析是飞机安全飞行的关键,装配过程中如果出现偏差,不但会对飞机的组装造成一定的影响,还会造成大量的人力、物力损失,从而影响到飞机项目的后续发展。
为了改进装配技术,促进飞机项目的发展,本文将对飞机装配容差分析技术展开详细的探讨。
1.飞机装配容差分析的工作流程飞机装配容差分析通常是一个循环迭代的过程:第一步,确定初始容差分析的基本输入;第二步,进行容差分析;第三步,依据容差分析的计算结果判断是否满足设计要求,是否需要对输入进行优化;如果需要优化输入,则必须从第一个步骤重新开始;在不进行输入优化的情况下,允许误差分析的运算处理完成。
飞机装配容差分析的基本工作流程详见图1。
在虚线框架中进行容差分析的计算,在粗线框架中进行特定的误差分析计算,菱形决策框用于判断容差分析是否能够结束。
图1飞机装配容差分析工作流程飞机设计基准、飞机几何容差要求、工作包设计基准、工作包内部几何容差、工作包截面控制容差、零组件设计基准和零组件几何容差要求。
在设计基准和飞机的几何容差要求、工作包括设计基准、工作包截面控制容差要求等方面,都是由主要设计单位来确定和管理的;设计包的几何容差要求、零组件设计基准和零组件容差要求通常是设计合同提供商来确定和管理的。
飞机制造中的尺寸管理和容差仿真分析技术
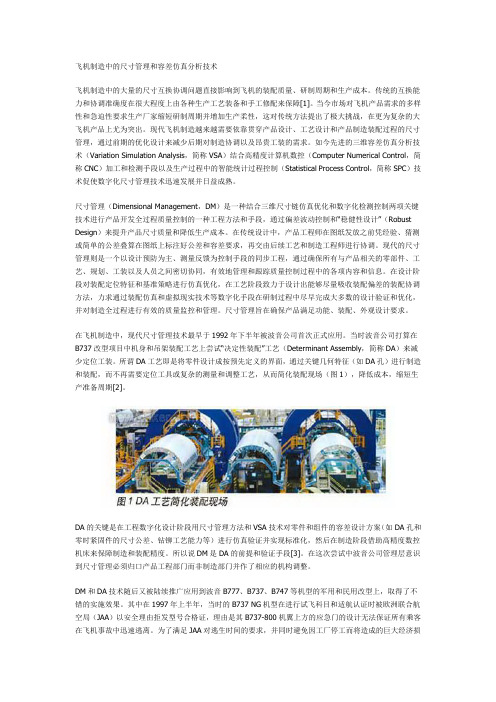
飞机制造中的尺寸管理和容差仿真分析技术飞机制造中的大量的尺寸互换协调问题直接影响到飞机的装配质量、研制周期和生产成本。
传统的互换能力和协调准确度在很大程度上由各种生产工艺装备和手工修配来保障[1]。
当今市场对飞机产品需求的多样性和急迫性要求生产厂家缩短研制周期并增加生产柔性,这对传统方法提出了极大挑战,在更为复杂的大飞机产品上尤为突出。
现代飞机制造越来越需要依靠贯穿产品设计、工艺设计和产品制造装配过程的尺寸管理,通过前期的优化设计来减少后期对制造协调以及昂贵工装的需求。
如今先进的三维容差仿真分析技术(Variation Simulation Analysis,简称VSA)结合高精度计算机数控(Computer Numerical Control,简称CNC)加工和检测手段以及生产过程中的智能统计过程控制(Statistical Process Control,简称SPC)技术促使数字化尺寸管理技术迅速发展并日益成熟。
尺寸管理(Dimensional Management,DM)是一种结合三维尺寸链仿真优化和数字化检测控制两项关键技术进行产品开发全过程质量控制的一种工程方法和手段,通过偏差波动控制和“稳健性设计”(Robust Design)来提升产品尺寸质量和降低生产成本。
在传统设计中,产品工程师在图纸发放之前凭经验、猜测或简单的公差叠算在图纸上标注好公差和容差要求,再交由后续工艺和制造工程师进行协调。
现代的尺寸管理则是一个以设计预防为主、测量反馈为控制手段的同步工程,通过确保所有与产品相关的零部件、工艺、规划、工装以及人员之间密切协同,有效地管理和跟踪质量控制过程中的各项内容和信息。
在设计阶段对装配定位特征和基准策略进行仿真优化,在工艺阶段致力于设计出能够尽量吸收装配偏差的装配协调方法,力求通过装配仿真和虚拟现实技术等数字化手段在研制过程中尽早完成大多数的设计验证和优化,并对制造全过程进行有效的质量监控和管理。
- 1、下载文档前请自行甄别文档内容的完整性,平台不提供额外的编辑、内容补充、找答案等附加服务。
- 2、"仅部分预览"的文档,不可在线预览部分如存在完整性等问题,可反馈申请退款(可完整预览的文档不适用该条件!)。
- 3、如文档侵犯您的权益,请联系客服反馈,我们会尽快为您处理(人工客服工作时间:9:00-18:30)。
飞机制造中的尺寸管理和容差仿真分析技术
飞机制造中的大量的尺寸互换协调问题直接影响到飞机的装配质量、研制周期和生产成本。
传统的互换能力和协调准确度在很大程度上由各种生产工艺装备和手工修配来保障[1]。
当今市场对飞机产品需求的多样性和急迫性要求生产厂家缩短研制周期并增加生产柔性,这对传统方法提出了极大挑战,在更为复杂的大飞机产品上尤为突出。
现代飞机制造越来越需要依靠贯穿产品设计、工艺设计和产品制造装配过程的尺寸管理,通过前期的优化设计来减少后期对制造协调以及昂贵工装的需求。
如今先进的三维容差仿真分析技术(Variation Simulation Analysis,简称VSA)结合高精度计算机数控(Computer Numerical Control,简称CNC)加工和检测手段以及生产过程中的智能统计过程控制(Statistical Process Control,简称SPC)技术促使数字化尺寸管理技术迅速发展并日益成熟。
尺寸管理(Dimensional Management,DM)是一种结合三维尺寸链仿真优化和数字化检测控制两项关键技术进行产品开发全过程质量控制的一种工程方法和手段,通过偏差波动控制和“稳健性设计”(Robust Design)来提升产品尺寸质量和降低生产成本。
在传统设计中,产品工程师在图纸发放之前凭经验、猜测或简单的公差叠算在图纸上标注好公差和容差要求,再交由后续工艺和制造工程师进行协调。
现代的尺寸管理则是一个以设计预防为主、测量反馈为控制手段的同步工程,通过确保所有与产品相关的零部件、工艺、规划、工装以及人员之间密切协同,有效地管理和跟踪质量控制过程中的各项内容和信息。
在设计阶段对装配定位特征和基准策略进行仿真优化,在工艺阶段致力于设计出能够尽量吸收装配偏差的装配协调方法,力求通过装配仿真和虚拟现实技术等数字化手段在研制过程中尽早完成大多数的设计验证和优化,并对制造全过程进行有效的质量监控和管理。
尺寸管理旨在确保产品满足功能、装配、外观设计要求。
在飞机制造中,现代尺寸管理技术最早于1992年下半年被波音公司首次正式应用。
当时波音公司打算在B737改型项目中机身和吊架装配工艺上尝试“决定性装配”工艺(Determinant Assembly,简称DA)来减少定位工装。
所谓DA工艺即是将零件设计成按预先定义的界面,通过关键几何特征(如DA孔)进行制造和装配,而不再需要定位工具或复杂的测量和调整工艺,从而简化装配现场(图1),降低成本,缩短生产准备周期[2]。
DA的关键是在工程数字化设计阶段用尺寸管理方法和VSA技术对零件和组件的容差设计方案(如DA孔和零时紧固件的尺寸公差、钻铆工艺能力等)进行仿真验证并实现标准化,然后在制造阶段借助高精度数控机床来保障制造和装配精度。
所以说DM是DA的前提和验证手段[3]。
在这次尝试中波音公司管理层意识到尺寸管理必须归口产品工程部门而非制造部门并作了相应的机构调整。
DM和DA技术随后又被陆续推广应用到波音B777、B737、B747等机型的军用和民用改型上,取得了不错的实施效果。
其中在1997年上半年,当时的B737 NG机型在进行试飞科目和适航认证时被欧洲联合航空局(JAA)以安全理由拒发型号合格证,理由是其B737-800机翼上方的应急门的设计无法保证所
有乘客在飞机事故中迅速逃离。
为了满足JAA对逃生时间的要求,并同时避免因工厂停工而将造成的巨大经济损失,波音公司必须迅速调整机身和该应急门的设计以实现新舱门在紧急情况下可以完全自动打开并保持和机身的连接,避免乘客需要费力打开再抛丢该插入式舱门[4]。
此舱门后来被称为“自展式翼上应急门”(Automatic Overwing Exit Door,简称AOED),如图2所示,属3类(Type III)舱门(成飞公司现参与制造供货)。
由于时间紧迫不允许后续的设变、报废和修配,新设计必须一次成功,用DM和DA技术来解决舱门装配工艺和门锁机构的容差问题变得至关重要。
整个工作持续了大半年,取得极大成功,该AOED门是第一个获得99.98%机身舱门互换性测试通过率的批产商用飞机增压舱门。
波音事后对该项DM工作进行了正式的财务分析,预测5年的成本节省将超过1.65亿美金,而事实上由于后来市场对该机型的需求大大超过预测,AOED的DM项目如今已带来了包括成本节省和产值增加在内超过10亿美金的经济效益,波音公司也因此决定今后所有新项目都要广泛使用DM和DA技术,包括后来的Y2(B787)项目,以及现在的B787-9和B737 MAX机型。
此外,欧洲空客的A340-600和A380机型以及现在的A350-1000机型在研制过程中也都陆续尝试应用了这些DM和DA技术[5]。
容差分析也被称为公差分析、偏差分析、尺寸链分析等,是设计阶段尺寸管理的一个重要工具和手段。
容差分析通过数理统计的计算方法来分析和评估装配尺寸链中零部件的制造偏差和工艺偏差如何影响产品的“关键产品特性”(Key Product Characteristics,简称KPC,如舱门和机身之间的阶差和缝隙),从而建立起KPC和影响KPC的各种产品特征(Product Feature,简称PF)的转换函数:KPC = f (PF1, PF2, …PFn, APV),也称作尺寸链装配函数。
容差分析可帮助产品和工艺设计人员分析和评估零部件、工艺和工装是否满足设计目标,从而通过优化设计来确保最终的产品制造质量。
传统的容差分析方法有若干种公差叠加计算,其缺点是手工计算繁杂、无法考虑三维因素、计算结果不准确。
先进的三维容差仿真分析(VSA)技术通过仿真产品的制造装配过程来预测产品的尺寸质量和偏差源贡献因子,判断某阶段的设计是否能够满足尺寸设计要求,并给出可能的整改方案,很好地弥补了传统方法的不足,有效地支持了设计面向制造和装(Design for Manufacturing and Assembly,简称DFMA)理念在实际产品研制中的应用。
Tecnomatix VATM [6] (简称VA)是一款由西门子工业软件公司开发的应用较为广泛的三维VSA软件,在上述AOED等项目中表现出色,并在用户的要求和协助下开发出了一系列针对飞机制造工艺特点的装配
和计算功能(如复合材料厚度公差),形成飞机制造工具包。
具体讲,VA软件通过建立产品和安装工艺的三维虚拟装配接触链模型来自动确立产品的尺寸链装配函数,通过统计仿真计算来分析和优化产品的容差方案和定位装配工艺,确认对产品KPC质量有重要影响的零部件几何特征,即偏差源贡献因子,作为在制造阶段必须重点监控保障的关键控制特性(Key Control Characteristics,简称KCC,如DA孔的尺寸公差)。
VA的输入包括:(1)产品数据,如3D数模、定位基准方案、公差标注和材料特性等;(2)工艺数据,如BOM(产品结构树/顺序)、BOP(工艺方法/操作)、BOR(制造资源和工装等)、KPC 质量要求和工艺能力知识等。
VA的输出则包括KPC的仿真结果和KCC贡献因子报告(图3)。
VA模型可以在零部件和工装制造之前就预测出在后续的制造和装配阶段是否会出现尺寸容差问题。
工程设计人员可以通过VA模型的仿真结果和贡献因子排列在数字化产品和工艺并行设计阶段就对产品的设计、公差、工艺和测量计划进行优化,帮助减少制造和装配偏差对产品质量的影响。
作为目前市场上唯一能够真正用三维几何特征来建模并严格根据几何尺寸和形位工差标准(Geometric Dimensioning & Tolerancing,简称GD&T)来仿真计算三维公差带的VSA软件,VA由于其先进的算法和功能性以及良好的使用性,在飞机产品研制中已得到了广泛深入的应用,目前已存在的模型和应用包括飞机主要装配件对接仿真分析(机身断面对接,机翼与机身对接,驾驶舱,引擎安装对准,总装)、空气动力学需求分析(门组件与周边外蒙皮间的缝隙与阶差)、操控中的运动学系统分析(可移动的飞行控制面,门板锁系统运转间隙,起落架与轮胎功能及运转间隙)、子总成制造与应力需求分析(装配顺序优化,局部互换性单元安装,座椅运动轨道调节,机翼装配)、设计与制造两个环节的成本平衡研究(零部件之间的DA安装和使用工装夹具装配的权衡、门控系统与调节,机械系统调节)等。
此外,VA软件还有两个非常显著的特点:(1)其模型是基于ISO国际标准的轻量化三维数模JT格式[7],一方面兼容多CAD平台,另一方面可以快速仿真诸如整机类大型装配而无需高端硬件;(2)具备公差库插入功能,一方面可以快速自动更新尺寸模型,另一方面便于企业积累形成核心的DM和DA知识知识库(图4)。
结语
由先进的VSA、CNC和SPC技术所构成的现代数字化尺寸管理(DM)有可能革命性地提升产品工程和制造之间的紧密协同,并形成单一数据源的数字化尺寸协调闭环体系。
这种闭环体系将大大减少飞机研制过程中的工程设变、报废、和修配工作,从而提升制造厂商的产品质量和经济效益,同时也会显著减少飞机制造中常见的研制周期的波动和不可预见性。
决定性装配(DA)工艺已被实践证明能够极大地减少飞机制造过程中的工艺装备,进而降低成本并缩短生产准备周期。
VSA是设计阶段尺寸管理的一个重要工具和手段,能够在工程数字化设计阶段对零件和组件的容差设计方案进行仿真验证并实现标准化,是实施DA 工艺的技术前提和验证手段。