管道全位置自动焊施工工法
管道全位置自动焊施工工法
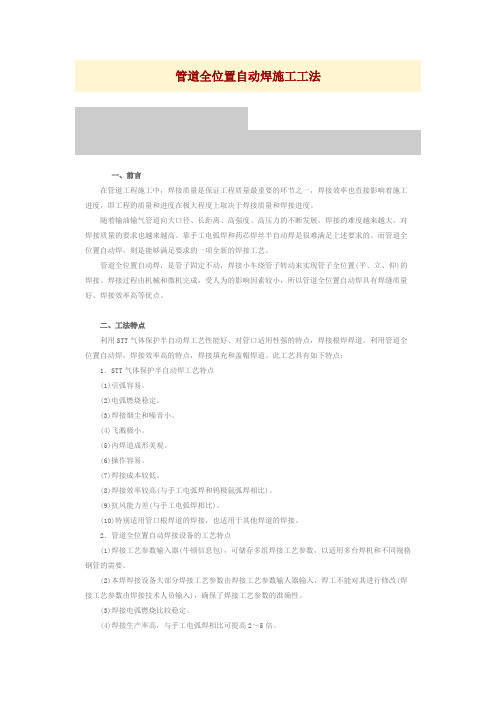
管道全位置自动焊施工工法一、前言在管道工程施工中,焊接质量是保证工程质量最重要的环节之一,焊接效率也直接影响着施工进度,即工程的质量和进度在极大程度上取决于焊接质量和焊接进度。
随着输油输气管道向大口径、长距离、高强度、高压力的不断发展,焊接的难度越来越大,对焊接质量的要求也越来越高。
靠手工电弧焊和药芯焊丝半自动焊是很难满足上述要求的。
而管道全位置自动焊,则是能够满足要求的一项全新的焊接工艺。
管道全位置自动焊,是管子固定不动,焊接小车绕管子转动来实现管子全位置(平、立、仰)的焊接。
焊接过程由机械和微机完成,受人为的影响因素较小,所以管道全位置自动焊具有焊缝质量好、焊接效率高等优点。
二、工法特点利用STT气体保护半自动焊工艺性能好、对管口适用性强的特点,焊接根焊焊道。
利用管道全位置自动焊,焊接效率高的特点,焊接填充和盖帽焊道。
此工艺具有如下特点:1.STT气体保护半自动焊工艺特点(1)引弧容易。
(2)电弧燃烧稳定。
(3)焊接烟尘和噪音小。
(4)飞溅极小。
(5)内焊道成形美观。
(6)操作容易。
(7)焊接成本较低。
(8)焊接效率较高(与手工电弧焊和钨极氩弧焊相比)。
(9)抗风能力差(与手工电弧焊相比)。
(10)特别适用管口根焊道的焊接,也适用于其他焊道的焊接。
2.管道全位置自动焊接设备的工艺特点(1)焊接工艺参数输入器(牛顿信息包),可储存多组焊接工艺参数,以适用多台焊机和不同规格钢管的需要。
(2)本焊焊接设备大部分焊接工艺参数由焊接工艺参数输人器输入,焊工不能对其进行修改(焊接工艺参数由焊接技术人员输入),确保了焊接工艺参数的准确性。
(3)焊接电弧燃烧比较稳定。
(4)焊接生产率高,与手工电弧焊相比可提高2~5倍。
(5)焊缝成形美观,内部质量好。
(6)可采用CO2气体或混合气体(Ar+CO2)作为保护介质。
(7)适用管径φ≥325mm,适用管壁厚度δ≥5mm。
管径越大、壁厚越厚,其经济效益越好。
三、适用范围本工法适用于低碳钢、低合金钢输油、输气和输水等管道的焊接。
核电厂管道卡钳式全位置自动焊工艺
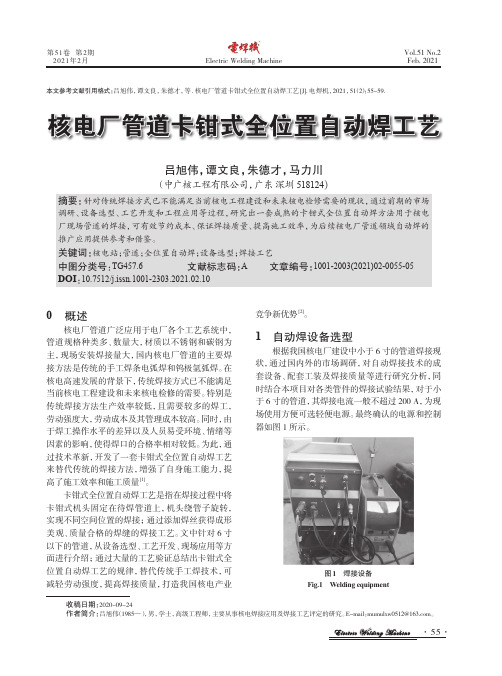
Electric Welding Machine·55·第51卷 第2期2021年2月Electric Welding MachineVol.51 No.2Feb. 2021本文参考文献引用格式:吕旭伟,谭文良,朱德才,等. 核电厂管道卡钳式全位置自动焊工艺[J]. 电焊机,2021,51(2):55-59.核电厂管道卡钳式全位置自动焊工艺0 概述 核电厂管道广泛应用于电厂各个工艺系统中,管道规格种类多、数量大,材质以不锈钢和碳钢为主,现场安装焊接量大,国内核电厂管道的主要焊接方法是传统的手工焊条电弧焊和钨极氩弧焊。
在核电高速发展的背景下,传统焊接方式已不能满足当前核电工程建设和未来核电检修的需要。
特别是传统焊接方法生产效率较低,且需要较多的焊工,劳动强度大,劳动成本及其管理成本较高。
同时,由于焊工操作水平的差异以及人员易受环境、情绪等因素的影响,使得焊口的合格率相对较低。
为此,通过技术革新,开发了一套卡钳式全位置自动焊工艺来替代传统的焊接方法,增强了自身施工能力,提高了施工效率和施工质量[1]。
卡钳式全位置自动焊工艺是指在焊接过程中将卡钳式机头固定在待焊管道上,机头绕管子旋转,实现不同空间位置的焊接;通过添加焊丝获得成形美观、质量合格的焊缝的焊接工艺。
文中针对6寸以下的管道,从设备选型、工艺开发、现场应用等方面进行介绍;通过大量的工艺验证总结出卡钳式全位置自动焊工艺的规律,替代传统手工焊技术,可减轻劳动强度,提高焊接质量,打造我国核电产业收稿日期:2020-09-24作者简介:吕旭伟(1985—),男,学士,高级工程师,主要从事核电焊接应用及焊接工艺评定的研究。
E-mail:*******************。
竞争新优势[2]。
1 自动焊设备选型 根据我国核电厂建设中小于6寸的管道焊接现状,通过国内外的市场调研,对自动焊接技术的成套设备、配套工装及焊接质量等进行研究分析,同时结合本项目对各类管件的焊接试验结果,对于小于6寸的管道,其焊接电流一般不超过200 A,为现场使用方便可选轻便电源。
管道全自动外焊机焊接工艺
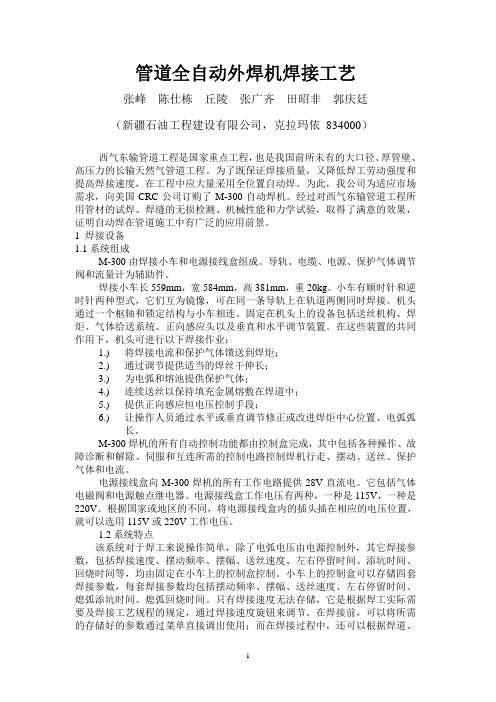
管道全自动外焊机焊接工艺张峰陈仕栋丘陵张广齐田昭非郭庆廷(新疆石油工程建设有限公司,克拉玛依 834000)西气东输管道工程是国家重点工程,也是我国前所未有的大口径、厚管壁、高压力的长输天然气管道工程。
为了既保证焊接质量,又降低焊工劳动强度和提高焊接速度,在工程中应大量采用全位置自动焊。
为此,我公司为适应市场需求,向美国CRC公司订购了M-300自动焊机。
经过对西气东输管道工程所用管材的试焊、焊缝的无损检测、机械性能和力学试验,取得了满意的效果,证明自动焊在管道施工中有广泛的应用前景。
1 焊接设备1.1系统组成M-300由焊接小车和电源接线盒组成。
导轨、电缆、电源、保护气体调节阀和流量计为辅助件。
焊接小车长559mm,宽584mm,高381mm,重20kg。
小车有顺时针和逆时针两种型式,它们互为镜像,可在同一条导轨上在轨道两侧同时焊接。
机头通过一个枢轴和锁定结构与小车相连。
固定在机头上的设备包括送丝机构、焊炬、气体给送系统、正向感应头以及垂直和水平调节装置。
在这些装置的共同作用下,机头可进行以下焊接作业:1.)将焊接电流和保护气体馈送到焊炬;2.)通过调节提供适当的焊丝干伸长;3.)为电弧和熔池提供保护气体;4.)连续送丝以保持填充金属熔敷在焊道中;5.)提供正向感应恒电压控制手段;6.)让操作人员通过水平或垂直调节修正或改进焊炬中心位置、电弧弧长。
M-300焊机的所有自动控制功能都由控制盒完成,其中包括各种操作、故障诊断和解除、伺服和互连所需的控制电路控制焊机行走、摆动、送丝、保护气体和电流。
电源接线盒向M-300焊机的所有工作电路提供28V直流电。
它包括气体电磁阀和电源触点继电器。
电源接线盒工作电压有两种,一种是115V,一种是220V。
根据国家或地区的不同,将电源接线盒内的插头插在相应的电压位置,就可以选用115V或220V工作电压。
1.2系统特点该系统对于焊工来说操作简单,除了电弧电压由电源控制外,其它焊接参数,包括焊接速度、摆动频率、摆幅、送丝速度、左右停留时间、添坑时间、回烧时间等,均由固定在小车上的控制盒控制。
全自动管道焊接操作方法

全自动管道焊接操作方法
全自动管道焊接是一种高效、精准的焊接方法,可以提高焊接质量和生产效率。
以下是全自动管道焊接的一般操作方法:
1. 准备工作:根据焊接要求选择合适的设备、工具和焊接材料。
检查设备和工具的状态,确保其正常运行。
2. 准备管道:清洁管道表面,去除任何污垢、油脂和氧化物。
确保管道端部平整、无毛刺。
检查管道的尺寸和焊缝线,确保其符合要求。
3. 安装焊接设备:根据焊接要求,安装好自动焊接设备,包括自动焊机、电源和控制系统。
调整设备参数,使其适应具体焊接工艺。
4. 设置焊接参数:根据管道材料、厚度和焊接要求,设置合适的焊接参数,包括焊接电流、电压、速度和电弧稳定性等。
确保参数的合理性和稳定性。
5. 开始焊接:根据焊接程序和机器人的编程,启动焊接过程。
焊接机器人自动识别焊缝位置,自动对焊接速度进行控制,实现全自动焊接。
6. 检查焊接质量:焊接完成后,对焊缝进行质量检查。
检查焊缝的外观、尺寸和无损检测结果,确保其符合要求。
7. 收尾工作:清理焊接现场,将焊接设备和工具进行维护和保养。
整理焊接记录和报告,做好焊接质量的记录和归档工作。
总结起来,全自动管道焊接的操作方法主要包括准备工作、设备安装、参数设置、起焊、质检和收尾工作等环节。
通过合理操作和严格管理,可以实现高质量、高效率的全自动管道焊接。
中小口径厚壁管全位置自动焊施工工法
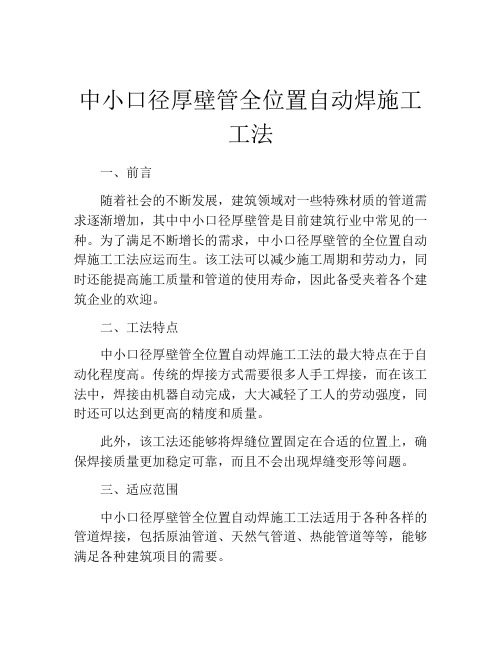
中小口径厚壁管全位置自动焊施工工法一、前言随着社会的不断发展,建筑领域对一些特殊材质的管道需求逐渐增加,其中中小口径厚壁管是目前建筑行业中常见的一种。
为了满足不断增长的需求,中小口径厚壁管的全位置自动焊施工工法应运而生。
该工法可以减少施工周期和劳动力,同时还能提高施工质量和管道的使用寿命,因此备受夹着各个建筑企业的欢迎。
二、工法特点中小口径厚壁管全位置自动焊施工工法的最大特点在于自动化程度高。
传统的焊接方式需要很多人手工焊接,而在该工法中,焊接由机器自动完成,大大减轻了工人的劳动强度,同时还可以达到更高的精度和质量。
此外,该工法还能够将焊缝位置固定在合适的位置上,确保焊接质量更加稳定可靠,而且不会出现焊缝变形等问题。
三、适应范围中小口径厚壁管全位置自动焊施工工法适用于各种各样的管道焊接,包括原油管道、天然气管道、热能管道等等,能够满足各种建筑项目的需要。
四、工艺原理中小口径厚壁管全位置自动焊施工工法的实际工程应用基于以下几个方面的技术和实践经验:1、焊机自动贯通控制:对焊接的控制贯通特别重要,如果焊接位置不稳定,可能会导致焊缝形变和焊接质量下降。
此外,对于厚壁管道的焊接,还需要控制合适的热量、焊缝宽度、焊道深度等多个参数。
2、高效自动化设备:对于中小口径厚壁管道的自动化焊接,需要采用高效的设备,例如自动化焊接机、翻转机、定位器等等,才能够实现精准的焊接。
3、具有高密度和高强度的焊接低氢电极:在中小口径厚壁管道的焊接工艺中,选用的低氢电极应该具有较高的密度和强度,以保证焊缝的质量和强度。
五、施工工艺1、焊前准备:在焊接前需要对管子进行磨边、获取焊接参数和检查焊接区域的清洁程度等步骤,以确保启动焊接的质量和效率。
2、起炉降温:焊接之前,需要使用起炉降温降低管子的温度,以便更好地控制焊接的温度。
3、定位:使用机器自动定位设备,将需要焊接的管子位置精确定位,以确保焊接的准确性。
4、自动化焊接:珂以在上游获得焊接质量稳定的中小口径厚壁,而不必费力手工焊接,达到施工效率的提高和质量的保障。
管道全位置自动焊接技术
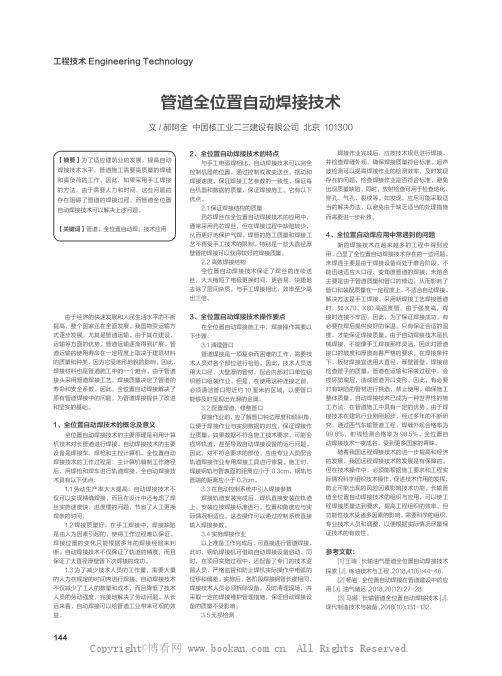
探索 [J]. 炼油技术与工程 ,2018,41(6):44-46. [2] 杨岩 . 全位置自动焊接在管道建设中的应
用 [J]. 油气储运 ,2018,20(12):27-28. [3] 马娜 . 长输管道全位置自动焊接技术 [J].
现代制造技术与装备 ,2018(10):131-132.
随着我国远程焊接技术的进一步提高和经济 的发展,我国远程焊接技术的发展是有保障的。 但在技术操作中,必须能根据施工要求和工程实 际情况科学组织技术操作,促进技术作用的发挥, 防止可能出现的风险因素影响技术功能。长输管 道全位置自动焊接技术的组织与应用,可以使工 程焊接质量达到要求,提高工程组织的效率。但 功能性技术受诸多因素的影响,需要科学的组织、 专业技术人员和调整,以便根据实际情况尽量保 证技术的有效性。
2、全位置自动焊接技术的特点 与手工电弧焊相比,自动焊接技术可以完全
控制机器的位置。通过控制或改变送丝、摆动和 焊接速度,保证焊接工艺参数的一致性,保证每 台机器和数据的质量,保证焊接施工。它有以下 优点。
2.1 保证焊接结构的质量 药芯焊丝在全位置自动焊接技术的应用中, 通常采用药芯焊丝,但在焊接过程中缺陷较少, 从而更好地保护气焊。焊管的施工质量和焊接工 艺不再受手工技术的限制。特别是一些大直径厚 壁管的焊接可以获得较好的焊接质量。 2.2 高效焊接结构 全位置自动焊接技术保证了焊丝的连续送 丝,大大缩短了电极更换时间,更容易、快捷地 去除了层间杂质。与手工焊接相比,效率至少高 出三倍。
工程技术
管道全位置自动焊接技术
文 / 郝阿全 中国核工业二三建设有限公司 北京 101300
【摘要】为了适应建筑业的发展,提高自动 焊接技术水平,管道施工需要高质量的焊缝 和高负荷的工作。因此,如果采用手工焊接 的方法,由于需要人力和时间,这些问题的 存在阻碍了管道的焊接过程,而管道全位置 自动焊接技术可以解决上述问题。
中小口径厚壁管全位置自动焊施工工法
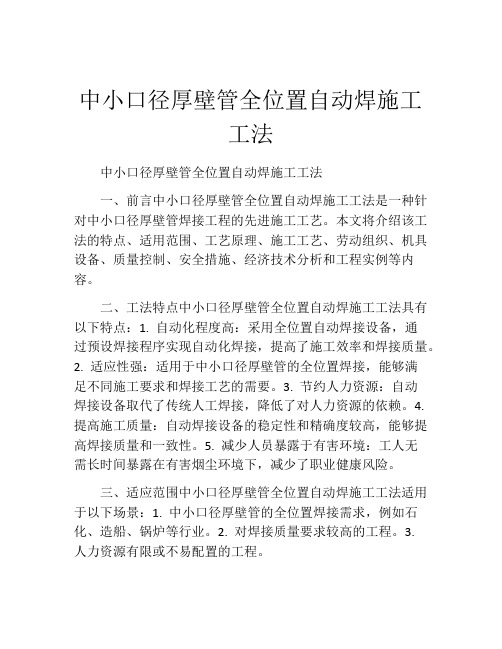
中小口径厚壁管全位置自动焊施工工法中小口径厚壁管全位置自动焊施工工法一、前言中小口径厚壁管全位置自动焊施工工法是一种针对中小口径厚壁管焊接工程的先进施工工艺。
本文将介绍该工法的特点、适用范围、工艺原理、施工工艺、劳动组织、机具设备、质量控制、安全措施、经济技术分析和工程实例等内容。
二、工法特点中小口径厚壁管全位置自动焊施工工法具有以下特点:1. 自动化程度高:采用全位置自动焊接设备,通过预设焊接程序实现自动化焊接,提高了施工效率和焊接质量。
2. 适应性强:适用于中小口径厚壁管的全位置焊接,能够满足不同施工要求和焊接工艺的需要。
3. 节约人力资源:自动焊接设备取代了传统人工焊接,降低了对人力资源的依赖。
4. 提高施工质量:自动焊接设备的稳定性和精确度较高,能够提高焊接质量和一致性。
5. 减少人员暴露于有害环境:工人无需长时间暴露在有害烟尘环境下,减少了职业健康风险。
三、适应范围中小口径厚壁管全位置自动焊施工工法适用于以下场景:1. 中小口径厚壁管的全位置焊接需求,例如石化、造船、锅炉等行业。
2. 对焊接质量要求较高的工程。
3.人力资源有限或不易配置的工程。
四、工艺原理中小口径厚壁管全位置自动焊施工工法的工艺原理是通过预设焊接程序,控制焊接补偿和动作轨迹,使焊接设备在全位置焊接过程中稳定运行,并通过电弧压力调节和保护气体控制,保证焊缝质量和稳定性。
五、施工工艺中小口径厚壁管全位置自动焊施工工法的施工工艺包括以下几个阶段:1. 准备阶段:包括焊接设备的安装调试、焊接工艺参数的设置,以及现场的准备工作。
2. 安装定位:将待焊管件进行定位和夹紧,确保焊接过程中的稳定性和准确性。
3. 焊接过程:通过预设的焊接程序,控制焊接设备自动进行焊接,包括填充和盖面焊接。
4. 检测与修复:对焊缝进行辅助检测,如射线检测、超声波检测等,如有缺陷,进行修复。
5. 清理整理:清理焊接残渣和打磨焊接表面,使之达到施工要求。
六、劳动组织中小口径厚壁管全位置自动焊施工工法的劳动组织包括焊接工、焊工助手、质检人员和协调人员等。
管道全位置焊工艺
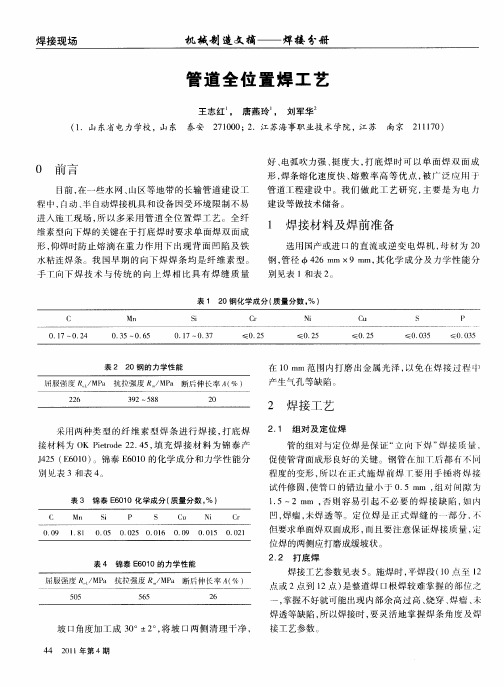
速 将 电弧 移 到 坡 口的 另 一 侧 , 到 恢 复 正 常 为 止 。在 直
l 至 1点半 处适 当拉 长 电弧 , 做 往返 运 条 , 2点 并 以控 制 坡 口两侧各 熔 化 0 5~1m 为 宜 ; 1点半 至 4点 处 . m 在
弧 , 电弧 引燃 后迅 速将 电弧 压 低 , 当 送入 坡 口根 部 的 间 隙 内 。当熔 孔 形成 后 , 焊条 沿 焊 接方 向均 匀行 走 , 电弧 高度 0 5—1m . m左 右 , 若焊 接过 程 中发现 熔 孔 变形 , 可
通 过运 条及 时 进行 调整 , 熔 孔 偏 向坡 口的 一侧 , 迅 如 应
打磨 , 方法 同上 。再接 头 时 , 焊条 角度 应在 8 。 向 内压 0,
送 的时间稍 长 一 些 。最 后 一 根 焊 条 收 弧 , 超 过 6点 应
位置 1 3 0~ 0mm为 佳 , 便 于再接 头 。收弧 很关 键 , 这样
收弧产 生 的熔 孔 过大 , 对再 接 头不 利 , 以变 化 焊条 角 所 度 应 大一些 。1 处 的冷 接头 , 2点 必须 要 用 磨 光 机进 行
维 素 型向下 焊 的关 键在 于打 底 焊 时要求 单 面 焊双 面 成 形 , 焊时 防止 熔 滴 在 重 力作 用 下 出现 背 面 凹陷 及 铁 仰
1 焊 接材 料 及 焊 前 准 备
选用 国产 或进 口的直 流 或 逆 变 电焊 机 , 母材 为 2 0 钢, 管径 4 6f 9 f 其 化学 成 分 及 力 学 性 能 分 2 l x l i m i m,
2 2 打底 焊 .
焊接 工艺参 数 见表 5 。施焊 时 , 焊段 ( 0点 至 1 平 1 2
服 强 度 R / P 抗拉强度 R / a 断后伸 长率 A % ) Ma MP (
长输管道全自动焊接单元施工方案

长输管道全自动焊接单元施工方案■刘智,毛静丽,王强,巩向楠摘要:为了真正有效提高长输管道全位置自动焊接施工工效和焊接质量,根据“人、机、料、法、环”五因素对管道全位置自动焊施工质量管理的影响,科学制定管道全自动焊接施工方案。
关键词:人员;设备;焊接施工流程;焊接方法;辅助工器具1.概述长输管道纤维素下向焊和自保护药芯焊丝半自动焊接操作技术,目前已是管道建设成熟的焊接工艺,但随着长输管道钢级的不断提高和国内外对环保问题日趋严格的要求,推广和采用全自动焊接技术进行管道施工,提高全自动焊接技术,制定科学合理的长输管道全自动焊接单元施工方案尤为重要。
传统的焊接机组(纤维素根焊+自保护药芯焊丝填盖)从人员和机械设备的配置,到施工现场的工序流程安排已经不适合全自动焊接机组的正常运转,导致全自动焊接质量和工效低于半自动焊接。
因此,如何用好全自动焊接技术,真正提高焊接质量和施工工效成为亟待解决的问题。
2.长输管道全自动焊接单元施工方案结合长输管道纤维素下向焊和自保护药芯焊丝半自动焊接施工机组的施工经验,对比分析影响施工质量和工效的制约点,针对全自动焊接技术制定科学合理的焊接单元施工方案。
例:某国外项目外输管线工程管线钢级为X52,φ508mm×8.7mm。
采用手工纤维素根焊+气保护药芯焊丝向上全自动填盖的焊接工艺施工。
(1)全自动焊接机组的人员配置分析关键岗位打破传统机组配置,执行能者上、弱者下的用人原则,具体见表1。
(2)全自动焊接机组的设备配置分析设备选型、数量按照施工要求配备,机动性、经济性、稳定性尤其重要,见表2。
(3)全自动焊接机组的材料、工具的配置分析管材、焊接材料必须有加盖红章的材质单和质量证明合格证书,工具类必须为正规类厂家生产,并具有安全生产合格证,见表3。
(4)全自动焊接机组施工方案的制定和工效分析图1为采用纤维焊条根焊,全自动气体保护药芯向上全位置全自动填充、盖面的全自动焊接机组施工的工艺流程和工作站作业内容。
中小口径厚壁管全位置自动焊施工工法(2)
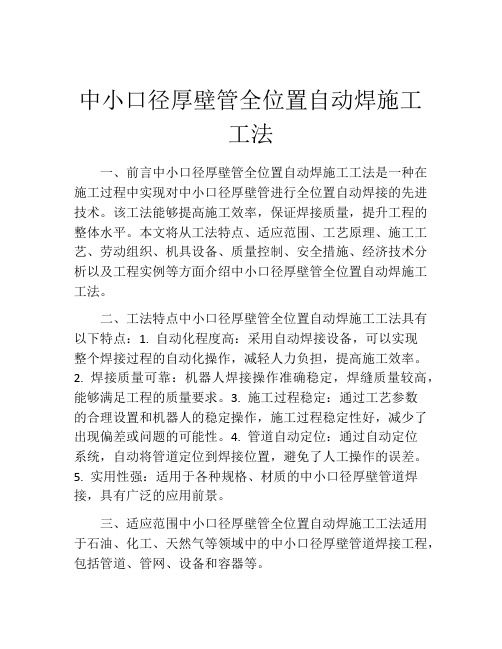
中小口径厚壁管全位置自动焊施工工法一、前言中小口径厚壁管全位置自动焊施工工法是一种在施工过程中实现对中小口径厚壁管进行全位置自动焊接的先进技术。
该工法能够提高施工效率,保证焊接质量,提升工程的整体水平。
本文将从工法特点、适应范围、工艺原理、施工工艺、劳动组织、机具设备、质量控制、安全措施、经济技术分析以及工程实例等方面介绍中小口径厚壁管全位置自动焊施工工法。
二、工法特点中小口径厚壁管全位置自动焊施工工法具有以下特点:1. 自动化程度高:采用自动焊接设备,可以实现整个焊接过程的自动化操作,减轻人力负担,提高施工效率。
2. 焊接质量可靠:机器人焊接操作准确稳定,焊缝质量较高,能够满足工程的质量要求。
3. 施工过程稳定:通过工艺参数的合理设置和机器人的稳定操作,施工过程稳定性好,减少了出现偏差或问题的可能性。
4. 管道自动定位:通过自动定位系统,自动将管道定位到焊接位置,避免了人工操作的误差。
5. 实用性强:适用于各种规格、材质的中小口径厚壁管道焊接,具有广泛的应用前景。
三、适应范围中小口径厚壁管全位置自动焊施工工法适用于石油、化工、天然气等领域中的中小口径厚壁管道焊接工程,包括管道、管网、设备和容器等。
四、工艺原理中小口径厚壁管全位置自动焊施工工法采用机器人焊接设备进行操作,在施工工法与实际工程之间有以下联系和技术措施:1. 工艺参数调整:根据实际工程的要求,对机器人焊接设备的工艺参数进行调整,以实现焊接质量的要求。
2. 焊接材料选择:根据工程的环境和要求,选择合适的焊接材料,确保焊接接头的稳定性和耐腐蚀性。
3. 焊接速度控制:通过调整焊接速度,控制焊接过程中的热输入,使焊缝形成合适的熔池形态,达到预期的焊接质量。
五、施工工艺中小口径厚壁管全位置自动焊施工工法的施工工艺包括以下几个阶段:1. 管道准备:对管道进行表面处理、切割、开槽等工艺,确保管道的质量和准备工作的完成。
2. 自动定位:通过自动定位系统,将管道准确地定位到焊接位置,保证焊接的精度和准确性。
无轨道全位置自动焊接管道施工技术
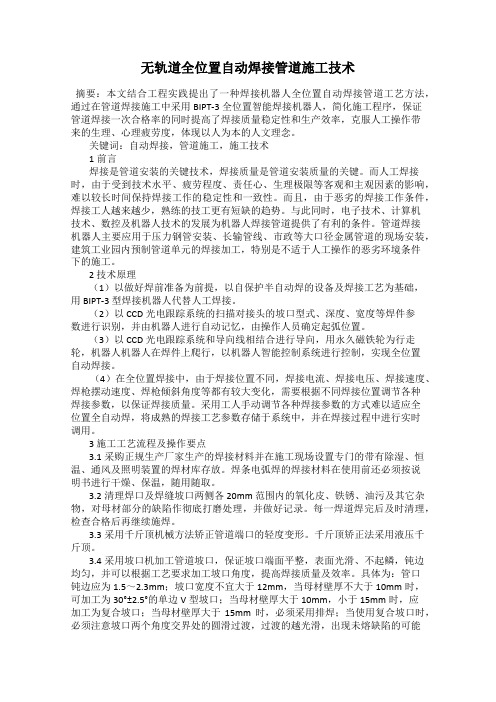
无轨道全位置自动焊接管道施工技术摘要:本文结合工程实践提出了一种焊接机器人全位置自动焊接管道工艺方法,通过在管道焊接施工中采用BIPT-3全位置智能焊接机器人,简化施工程序,保证管道焊接一次合格率的同时提高了焊接质量稳定性和生产效率,克服人工操作带来的生理、心理疲劳度,体现以人为本的人文理念。
关键词:自动焊接,管道施工,施工技术1前言焊接是管道安装的关键技术,焊接质量是管道安装质量的关键。
而人工焊接时,由于受到技术水平、疲劳程度、责任心、生理极限等客观和主观因素的影响,难以较长时间保持焊接工作的稳定性和一致性。
而且,由于恶劣的焊接工作条件,焊接工人越来越少,熟练的技工更有短缺的趋势。
与此同时,电子技术、计算机技术、数控及机器人技术的发展为机器人焊接管道提供了有利的条件。
管道焊接机器人主要应用于压力钢管安装、长输管线、市政等大口径金属管道的现场安装,建筑工业园内预制管道单元的焊接加工,特别是不适于人工操作的恶劣环境条件下的施工。
2 技术原理(1)以做好焊前准备为前提,以自保护半自动焊的设备及焊接工艺为基础,用 BIPT-3 型焊接机器人代替人工焊接。
(2)以 CCD 光电跟踪系统的扫描对接头的坡口型式、深度、宽度等焊件参数进行识别,并由机器人进行自动记忆,由操作人员确定起弧位置。
(3)以 CCD 光电跟踪系统和导向线相结合进行导向,用永久磁铁轮为行走轮,机器人机器人在焊件上爬行,以机器人智能控制系统进行控制,实现全位置自动焊接。
(4)在全位置焊接中,由于焊接位置不同,焊接电流、焊接电压、焊接速度、焊枪摆动速度、焊枪倾斜角度等都有较大变化,需要根据不同焊接位置调节各种焊接参数,以保证焊接质量。
采用工人手动调节各种焊接参数的方式难以适应全位置全自动焊,将成熟的焊接工艺参数存储于系统中,并在焊接过程中进行实时调用。
3 施工工艺流程及操作要点3.1采购正规生产厂家生产的焊接材料并在施工现场设置专门的带有除湿、恒温、通风及照明装置的焊材库存放。
管道自动焊施工工法
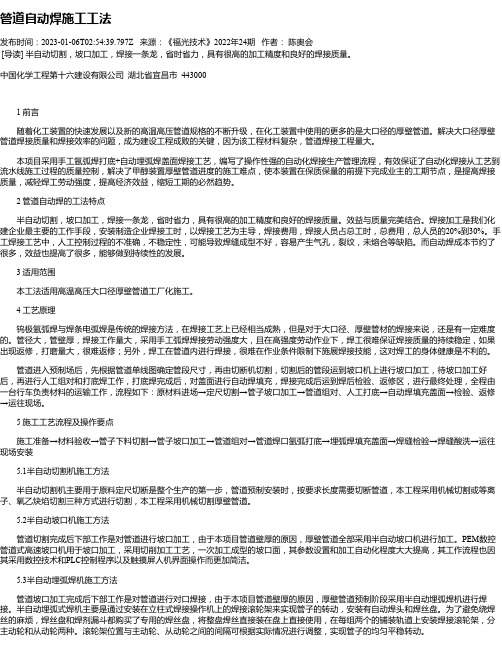
管道自动焊施工工法发布时间:2023-01-06T02:54:39.797Z 来源:《福光技术》2022年24期作者:陈奥会[导读] 半自动切割,坡口加工,焊接一条龙,省时省力,具有很高的加工精度和良好的焊接质量。
中国化学工程第十六建设有限公司湖北省宜昌市 4430001 前言随着化工装置的快速发展以及新的高温高压管道规格的不断升级,在化工装置中使用的更多的是大口径的厚壁管道。
解决大口径厚壁管道焊接质量和焊接效率的问题,成为建设工程成败的关键,因为该工程材料复杂,管道焊接工程量大。
本项目采用手工氩弧焊打底+自动埋弧焊盖面焊接工艺,编写了操作性强的自动化焊接生产管理流程,有效保证了自动化焊接从工艺到流水线施工过程的质量控制,解决了甲醇装置厚壁管道进度的施工难点,使本装置在保质保量的前提下完成业主的工期节点,是提高焊接质量,减轻焊工劳动强度,提高经济效益,缩短工期的必然趋势。
2 管道自动焊的工法特点半自动切割,坡口加工,焊接一条龙,省时省力,具有很高的加工精度和良好的焊接质量。
效益与质量完美结合。
焊接加工是我们化建企业最主要的工作手段,安装制造企业焊接工时,以焊接工艺为主导,焊接费用,焊接人员占总工时,总费用,总人员的20%到30%。
手工焊接工艺中,人工控制过程的不准确,不稳定性,可能导致焊缝成型不好,容易产生气孔,裂纹,未熔合等缺陷。
而自动焊成本节约了很多,效益也提高了很多,能够做到持续性的发展。
3 适用范围本工法适用高温高压大口径厚壁管道工厂化施工。
4 工艺原理钨极氩弧焊与焊条电弧焊是传统的焊接方法,在焊接工艺上已经相当成熟,但是对于大口径、厚壁管材的焊接来说,还是有一定难度的。
管径大,管壁厚,焊接工作量大,采用手工弧焊焊接劳动强度大,且在高强度劳动作业下,焊工很难保证焊接质量的持续稳定,如果出现返修,打磨量大,很难返修;另外,焊工在管道内进行焊接,很难在作业条件限制下施展焊接技能,这对焊工的身体健康是不利的。
管道全位置熔化极氩弧自动焊施工技术分析

管道全位置熔化极氩弧自动焊施工技术分析摘要:近些年来,我国经济得到了快速发展,对能源的需求日增加,为了满足我国能源的需求,管道运输的重要性逐渐凸显出来。
而在管道运输中,管道焊接质量直接影响着管道运输的安全。
又由于我国人力成本不断的增加,传统的焊接方式已经不能满足管道的焊接需求,急需一种工作效率更高、焊接质量更好的焊接技术。
而管道全位置自动焊技术则能满足现阶段我国对管道焊接的需求。
鉴于此,本文在对管道全位置融化及氩弧自动焊技术特点进行分析的基础上,对其具体施工技术进行了分析,以期为我国管道全位置自动焊技术未来的发展提供参考关键字:管道;全位置焊接;自动焊0前言随着我国社会经济的不断发展,对能源的需求不断增加,管道运输得到了更加广泛的应用,而管道的焊接技术直接影响着管道运输的安全。
目前我国常用的全位置焊接方式主要有自动焊、半自动焊以及电弧焊。
在这三种焊接方式中,自动焊具有工作效率高,焊机质量好,稳定性高的技术优点,使得我国开始大力发展这项焊接技术。
此外,随着我国大厚度管材广泛的使用,以及人力成本的增加,对全位置自动焊技术的需求更加迫切。
1管道全位置熔化极氩弧自动焊的特点管道全位置焊接旋转一周的过程可分为平焊、立向下焊、仰焊、立向上焊,由于管道全位置焊接过程是熔池的位置是一个渐变过程,其所处不同位置的受力情况也是时刻在变化的,其中4个典型位置熔池受力情如图1所示(以TIG无填丝情况为例)。
由图1可知,焊接过程中熔池受到电弧的轴向电弧力F、液态金属的表面张力f在弯曲液面上形成的合力和重力G三种力的共同作用;在电弧轴线与管道中心重合时,只有重力不随焊枪位置的改变而变化。
在平焊位置,重力易造成熔池向下流动,与电弧力联合作用会导致内部余高过高;在仰焊位置,重力使熔池向下脱离焊缝,造成焊缝内凹、成形不均匀,但可以通过电弧力削弱重力的不利影响;立向下焊或立向上焊时熔池有越过电弧沿着坡口而向下流淌的趋势,使焊缝易形成未熔合、焊瘤、成形不均匀等焊接缺陷。
- 1、下载文档前请自行甄别文档内容的完整性,平台不提供额外的编辑、内容补充、找答案等附加服务。
- 2、"仅部分预览"的文档,不可在线预览部分如存在完整性等问题,可反馈申请退款(可完整预览的文档不适用该条件!)。
- 3、如文档侵犯您的权益,请联系客服反馈,我们会尽快为您处理(人工客服工作时间:9:00-18:30)。
管道全位置自动焊施工工法
一、前言
在管道工程施工中,焊接质量是保证工程质量最重要的环节之一,焊接效率也直接影响着施工进度,即工程的质量和进度在极大程度上取决于焊接质量和焊接进度。
随着输油输气管道向大口径、长距离、高强度、高压力的不断发展,焊接的难度越来越大,对焊接质量的要求也越来越高。
靠手工电弧焊和药芯焊丝半自动焊是很难满足上述要求的。
而管道全位置自动焊,则是能够满足要求的一项全新的焊接工艺。
管道全位置自动焊,是管子固定不动,焊接小车绕管子转动来实现管子全位置(平、立、仰)的焊接。
焊接过程由机械和微机完成,受人为的影响因素较小,所以管道全位置自动焊具有焊缝质量好、焊接效率高等优点。
二、工法特点
利用STT气体保护半自动焊工艺性能好、对管口适用性强的特点,焊接根焊焊道。
利用管道全位置自动焊,焊接效率高的特点,焊接填充和盖帽焊道。
此工艺具有如下特点:1.STT气体保护半自动焊工艺特点
(1)引弧容易。
(2)电弧燃烧稳定。
(3)焊接烟尘和噪音小。
(4)飞溅极小。
(5)内焊道成形美观。
(6)操作容易。
(7)焊接成本较低。
(8)焊接效率较高(与手工电弧焊和钨极氩弧焊相比)。
(9)抗风能力差(与手工电弧焊相比)。
(10)特别适用管口根焊道的焊接,也适用于其他焊道的焊接。
2.管道全位置自动焊接设备的工艺特点
(1)焊接工艺参数输入器(牛顿信息包),可储存多组焊接工艺参数,以适用多台焊机和不同规格钢管的需要。
(2)本焊焊接设备大部分焊接工艺参数由焊接工艺参数输人器输入,焊工不能对其进行修改(焊接工艺参数由焊接技术人员输入),确保了焊接工艺参数的准确性。
(3)焊接电弧燃烧比较稳定。
(4)焊接生产率高,与手工电弧焊相比可提高2~5倍。
(5)焊缝成形美观,内部质量好。
(6)可采用CO2气体或混合气体(Ar+CO2)作为保护介质。
(7)适用管径φ≥325mm,适用管壁厚度δ≥5mm。
管径越大、壁厚越厚,其经济效益越好。
三、适用范围
本工法适用于低碳钢、低合金钢输油、输气和输水等管道的焊接。
四、工艺原理
1.STT焊接工艺原理
STT焊接电源是一种以表面张力为熔滴主要过渡力的CO2气体保护半自动焊。
STT焊接电源具有波形控制功能,根据熔滴的不同过渡过程。
控制焊接电流和电弧电压的波形。
即焊接电源能自动调节焊接电流和电弧电压达到电弧所需的瞬时热量。
确保焊接电弧的稳定燃烧和有效地控制焊缝成形。
STT熔滴过渡电流、电压波形图如图1所示:
图1 SIT熔滴过渡电流、电压波形图
2.管道全位置自动焊工作原理
NOREAST管道全位置自动焊机,是专门用于管道焊接的自动焊设备。
它使用实芯焊丝(φ0.8~φ1.0),采用的保护气体为c02或混合气体(CO2+Ar)。
焊接方向为下向焊。
送丝速度、焊接速度和摆动频率等焊接工艺参数由焊接工艺参数输入器输入,焊工不能对其进行修改(或只能对某种参数进行一定范围的修改),确保每台焊机和每道焊口焊接工艺参数的一致性。
从而保证了各道焊口的焊接质量的均匀性,达到保证焊接质量的目的。
此焊接设备适用窄间隙坡口形式的焊接。
窄间隙坡口具有如下优点:(1)焊接接头受热范围小,焊接热影响区小。
(2)焊接变形和应力小。
(3)焊缝的组织和性能好。
(4)节省焊接材料。
(5)焊接效率高。
此焊接设备适用于各种坡口形式的焊接。
用于V形坡口的焊接时,除焊接效率较窄间隙坡口低外(仍可达到手工电焊的2~5倍),其他焊接优点仍较突出。
五、工艺流程(施工程序)
工艺流程见图2。
六、操作要点
1.焊接性试验及焊接工艺评定
管道全位置自动焊在工程施焊前,应进行焊接性试验。
当钢管的材质、规格、坡口型式、焊丝的牌号、焊丝的规格和保护气体种类等发生变化时,均应进行焊接性试验,试验步骤如下:
(1)根据标准要求、理论计算和以前的经验,初步确定焊接工艺参数范围。
(2)在确定的焊接工艺参数范围内,设定几组不同的焊接工艺数进行焊接工艺性试验。
对焊接后
在涩宁兰输气管道工程,全长860km。
在X70(φ660×10.3)的试验段中,采用管道全位置自动焊焊接了353道焊中,长度为4.12km。
外观检查焊缝一次合格率为99.7%,经100%射线探伤焊缝一次合格率为97%。