制壳工艺守则
制壳生产安全操作规程

制壳生产安全操作规程
一、工作前首先要熟悉本工序工艺规程及设备安全操作要点。
劳保用品必须按规定穿戴齐全。
二、使用T1140涂料搅拌机时,应集中精力掌握操纵手把,使叶轮回旋摆动、上下运动,叶轮不能碰击涂料缸壁。
三、轴节、销节、螺杆等处要经常加油润滑,有轴承的一年要加一次黄油。
四、使用T1117L涂料搅拌机之前要检查减速机油位,不够时要加到规定的高度,每星期观察检查一次。
五、T1117L如遇停电,必须将叶片提起,若停电后,叶片没有被提起时,切勿启动电机,否则将造成丝杆弯曲,电机烧毁。
六、M394斗式雨淋撒沙机与除尘机组要配合使用;先开动、再去尘,然后用小车推入滑轮撒沙。
要定期清除收集的尘埃。
七、电动葫芦、吊具在吊运滑轮过程中要慢、要平稳,不能晃动,更不能碰撞到其它物件,并要注意周围人员安全。
八、使用电动葫芦作业时,应注意避免斜拉、斜吊,禁止使用湿手开启手电门,工作时声音有异常,控制失灵等应紧急停止使用。
硅溶胶制壳工艺流程

硅溶胶制壳工艺流程一、工艺流程:成型蜡模→硅溶胶面层涂料配制→沾浆→撒砂→风干→硅溶胶过渡层涂料配制→沾浆→撒砂→风干→水玻璃加固层涂料配制→沾浆→撒砂→风干→包浆→脱蜡→焙烧。
二、车间温度和湿度:1.层面工序:温度:24—25℃. 湿度:60—70%。
2.过渡层工序(2—3层):温度:23—25℃. 湿度:35—40%。
三、涂料工艺:1.层面涂料:(1).硅溶胶:803:1430=1:3(2).配比:硅溶胶:100kg锆英粉:360-400kg润湿剂:200ml消泡剂:130ml(3)流杯粘度:34-40秒2.过渡层涂料:(1).硅溶胶:803:1430=1:3(2).配比:硅溶胶:100kg莫来粉:120-150kg(3).流杯粘度:13-20秒。
四、结壳工艺:1.面层结壳:(1).锆砂:100-140目。
(2).干燥时间:4-6小时。
2.二层结壳:(1).莫来砂:30-60目。
(2).干燥时间:大于18小时。
(风机风速6-8米/秒)3.三层结壳:(1).莫来砂:16-30目。
(2).干燥时间:大于18小时。
(风机风速6-8米/秒)4.四层以上结壳:(1).按水玻璃工艺加固。
四、脱蜡工艺:1.水中加入工业盐酸1%。
2.水温:95-98℃.3.脱蜡时间:15-20分钟,最多不超过30分钟。
4.脱蜡后用80℃以上的热水冲洗型腔。
五、焙烧工艺:1.焙烧温度:1050-1100℃.2.保温时间:小件:60-90分钟.中大件:90-120分钟。
水玻璃制壳工艺

涂料配置1工艺要求1.1工艺材料主要技术参数1.1.1水玻璃1.1.2石英粉(用于表面涂料)1.1.3高铝合成粉(用于加固层涂料)1.1.4铝矾土粉(用于加固层涂料)1.1.5煤矸石粉(用于加固层涂料)1.2涂料配置1.3涂料粘度注:a.室内低于8度,涂料粘度应提高:表面层应提高2~3s,加固层应提高1~2s。
b.室内高于30度,涂层粘度应降低:表面层应降低2~3s,加固层应降低1~2s。
c.手工制壳的涂料粘度应增加:表面层应提高5~10s,加固层应提高2~3s。
2操作程序2.1检查涂料搅拌机运转是否正常,按1.2的规定分别计算水玻璃、粉料、JFC 的加入量,并准确称量。
2.2按1.1.1的规定,水玻璃加水处理合格后一次性加入涂料搅拌机中,加JFC 搅匀,粉料应分2~3次加入,边加边搅拌至全部完成,再搅拌60~90min。
可间断搅拌每次搅拌时间不得小于30min。
2.3配好的涂料应静置4~8h,使用前应充分搅拌,达到1.3的规定后方能使用。
3注意事项3.1若在表面层与加固层之间增加过渡层,其涂料粘度应在表面层的基础降低5~10s。
3.2涂料配比作为一次性配料的工艺要求,最终按室温调整到工艺规定的粘度。
4检查项目4.1水玻璃、耐火粉料按进货批次进行检验,检验结果应符合2.1和有关材料标准要求。
4.2涂料粘度采用体积100ml,流出孔φ6±0.02mm的标准流杯,每班测定1~2次,测定结果应符合1.3的规定。
4.3期采用不锈钢涂片或玻璃片测定涂料的覆盖性(涂料厚度及均匀性),要求达到涂料无堆积、涂层均匀。
4.4水玻璃模数、涂料的粘度和覆盖性的测定方法,按JB4007——85《熔模铸造涂料试验方法》的规定进行。
制壳1范围本标准规定了制造型壳(以下简称制壳)的工艺要求、操作程序、注意事项和检查项目。
本标准适用于水玻璃、石英砂、铝矾土砂、高岭石系列砂等材料的型壳制造。
2工艺要求2.1室温:15~32度,湿度40%~60%.2.2工艺材料主要技术参数2.2.1水玻璃涂料应符合标准CICBA/B02.07。
制壳生产作业指导书7

硅溶胶制壳生产作业指导书:Fy/JS7.5.1-05-1操作周期:每次新品
客户名称:产品名称:产品型号:材质:No:
涂料配制
层数
锆粉320目
(kg)
煤干粉
270~320目(kg)
硅溶胶
(kg)
消泡剂
(ml)
湿润剂
(ml)
石墨粉
(kg)
面层
过渡层
背层
封浆层
浆料粘度干燥工艺
类别
层次
浆液粘度(S)
2、面层、二层时,不允许直接吹风,风扇斜吹,保证室内空气流动就可。
3、二层粘浆前吹浮砂再预湿。小内孔、内槽、外圆凹槽用60-80目砂防止表面膨胀跑火。
4、注意每层粘浆前吹浮砂,防止表面膨胀,内空进砂。
5、粘浆要特别注意,防止断件。
产品样图
编制:/日期:技术部审核/日期:次送交技术部整理(总经理)批准:年月日
砂型(目)
干燥时间(h)
温度℃
湿度%
风扇
时间(h)
干燥室
备注
面层
锆浆
锆(莫来,刚玉)砂
面干室
过渡层预湿
莫来浆
莫来砂
面干背干
背层
石墨浆
莫来砂
背干室
封浆层
莫来浆
莫来砂
背干蜡脱
共几层
操作规范及注2小时后→清洗蜡树→水洗蜡树→吹干→前处理液(湿润济→蒸流水→硅溶胶→吹干→面层。
制壳作业指导书
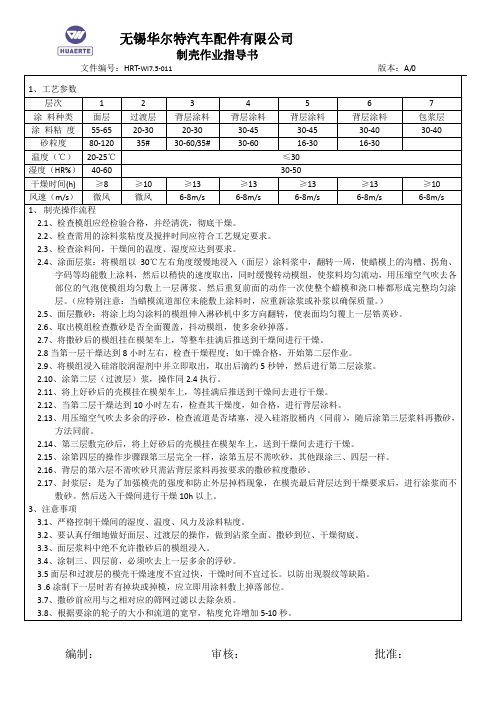
2.6、取出模组检查撒砂是否全面覆盖,抖动模组,使多余砂掉落。
2.7、将撒砂后的模组挂在模架车上,等整车挂满后推送到干燥间进行干燥。
2.8当第一层干燥达到8小时左右,检查干燥程度;如干燥合格,开始第二层作业。
2.9、将模组浸入硅溶胶润湿剂中并立即取出,取出后滴约5秒钟,然后进行第二层涂浆。
≥13
≥13
≥13
≥10
风速(m/s)
微风
微风
6-8m/s
6-8m/s
6-8m/s
6-8m/s
6-8m/s
1、制壳操作流程
2.1、检查模组应经检验合格,并经清洗,彻底干燥。
2.2、检查需用的涂料浆粘度及搅拌时间应符合工艺规定要求。
2.3、检查涂料间,干燥间的温度、湿度应达到要求。
2.4、涂面层浆:将模组以30℃左右角度缓慢地浸入(面层)涂料浆中,翻转一周,使蜡模上的沟槽、拐角、字码等均能敷上涂料,然后以稍快的速度取出,同时缓慢转动模组,使浆料均匀流动,用压缩空气吹去各部位的气泡使模组均匀敷上一层薄浆。然后重复前面的动作一次使整个蜡模和浇口棒都形成完整均匀涂层。(应特别注意:当蜡模流道部位未能敷上涂料时,应重新涂浆或补浆以确保质量。)
3 .6凃制下一层时若有掉块或掉模,应立即用涂料敷上掉落部位。
3.7、撒砂前应用与之相对应的筛网过滤以去除杂质。
3.8、根据要涂的轮子的大小和流道的宽窄,粘度允许增加5-10秒。
编制:审核:批准:
2.10、涂第二层(过渡层)浆,操作同2.4执行。
2.11、将上好砂后的壳模挂在模架车上,等挂满后推送到干燥间去进行干燥。
2.12、当第二层干燥达到10小时左右,检查其干燥度,如合格,进行背层涂料。
制壳作业标准规范(0806)

制壳工艺参数及操作规范一、浆料配制1.浆料配比及工艺参数制壳工艺参数及操作规范2.涂料搅拌时间A.面层锆浆配料由专人负责,新料配成后搅拌24小时以上方可使用,中途添加配料必须12小时后方可使用.B.二层锆浆配料完成后搅拌12小时以上方可使用, 中途添加配料必须8小时后方可使用.C.莫来石粉新配浆料完成后搅拌至少4小时以上方可使用, 中途添加配料必须0.5小时后方可使用.3.测量和调整:A.量杯测量时间以上涂料配完后0.5小时后粗测,到达规定时间时再次测量,若不符合要求,超出上限或下限2秒,需加硅溶胶或粉料调整,并作记录.B.使用过程中一般每2小时测量一次,如涂料粘度增加时,可用蒸馏水或同种硅溶胶加以调整.4.面层涂料使用期限:≤15天.5.涂料作业区温度:20~25℃,允许超出上限或下3℃.二、操作要点:1.开始作业前必须测浆浓度,合格后方可浸涂(沾浆)2.每班涂挂结束后,应在涂料层表面撒上50-100毫升蒸馏水(夏季100毫升,冬季50毫升)以补充水分挥发.制壳工艺参数及操作规范3.表面层使用到期后,应倒入第二层锆浆桶内使用.4.涂料桶涂料后加盖,减少空气硬化反应及水分挥发.5.字体及细小痕迹处应喷硅溶胶液,然后用压缩空气气枪吹扫,再次浸浆一次,以防出现铁豆缺陷.6.涂挂涂料力求均匀,涂时上下左右均匀转动,滴流干净,但浸涂取出后至撒砂时间最佳为10-20秒,不得超过30秒,以免涂层干涸,出现砂浆分层.三安全及注意事项1.在向搅拌桶中加料及用手揉搓过程中注意勿将衣服等挂到桶体上以免发生伤人事故.2.倾入粉料时应尽量轻松、慢放,以免粉尘飞扬,操作者要戴口罩.3.搅拌桶有浆料时必须连续转动,停用72小时以上时要将桶内浆料倾出并清洗干净.4.面层涂料配制时要严格按加料顺序,依次加入硅溶胶、湿润剂、锆粉、消泡剂,加料顺序应正确.5.涂料浆务必保持干净,不得有蜡屑、砂粒等,不得有过多的气泡。
每天上下班用筛子清理浆内杂质.6.涂料浆粘度每班上、下班时均需测定、调整并做记录.制壳工艺参数及操作规范一.敷砂工艺参数(GS硅溶胶)制壳工艺参数及操作规范二、层数选择原则预湿剂之滴法:对复杂件可采用滴杯滴沾浆死角,且要转动产品,注意只要润湿即可.预湿剂之浸法:将模壳浸入硅溶胶预湿剂中,不要超过2秒,取出后约滴5秒钟,保证不再滴预湿剂.三、操作要点和注意事项1.严格控制制壳区温度和干燥区湿度、温度和风速.2.要特别注意制好面层型壳,确保深孔和尖角处涂料与蜡模间无气泡,无涂料堆积、糊住孔等现象.制壳工艺参数及操作规范3.第一层最好自然干燥,不允许用电扇直接吹型壳,以免产生裂纹及脱壳;注意面层和二层型壳干燥速度不应太快,干燥时间不应太长,以免出现龟裂等缺陷。
制壳车间作业标准

《模壳分配表》《制壳车间生产日报表》
脱蜡工
车间统计
车间主任
①模壳脱蜡工模壳搬运至模壳脱蜡作业区
②确认当天脱蜡的蜡模串数并完成当天生产任务
③对模壳脱蜡的容器/及蜡板容器进行日常检查及维护
①模壳脱蜡工必须严格执行《制壳作业指导书》中热水脱蜡工艺规定,以确保脱蜡过程的模壳质量。
①制壳用材料须经检验合格方可进厂
②及时采购所缺制壳用材料
③制壳车间主任在《焊接原始记录单》签字确认后才可领取蜡模串
《焊接原始记录单》
车间主任配浆工
①制壳的涂料配制,硬化剂的配制
②配浆工专人负责配制
③每日填《制壳工艺操作原始记录》
①配制工艺必须严格按《制壳作业指导书》执行
②车间主任必须不定期的对涂料、硬化剂的工艺性能进行检测,监督车间工艺执行
xx有限公司
页次
1/1
标准书
批准
xx
版序
A
制壳车间作业标准
审核
xx
文件编号
ZDS-C-002
制订
xx
发行日期
2009.10.18
制订单位
生产部
作业流程
责任人
工作内容
管理要点
相关表单
搪壳工
车间主任
①搪壳工领取水玻璃、石英粉、石英砂,硬化剂用料氯化铵、氯化镁等原料
②从注蜡车间接领取蜡模串数
③按确认后的蜡模串数填写《模壳分配表》,并把产品分配给搪壳工
②模壳陪烧前须按规定堆放区域并控制模壳堆放高度
③控制模壳搬运中堆放高度,防止搬运中模壳倒塌损坏
《模壳发放日报表》
《模壳陪烧单》
车间统计
枳壳工艺规程

目录2、生产工艺流程4、质量监控:见“SCGL539601 枳壳生产关键工序质量监控要点”。
5、原辅料、半成品、成品质量标准5.1 枳壳原料质量标准:见“ZLJS100101 原药材质量标准”。
5.2 枳壳中间产品质量标准:见“ZLJS400101 饮片中间产品质量标准”。
5.3 枳壳成品质量标准:见“ZLJS500101 饮片成品质量标准”。
6、包材质量标准和文字说明6.1 包材质量标准:见“ZLJS300101~ZLJS300601包装材料质量标准”6.2 包装说明文字:品名:枳壳规格:产地:重量:产品批号:生产日期:贮藏:置干燥处生产企业:7、生产区的工艺卫生要求7.1 生产区卫生要求:执行“CSGL001401一般生产区环境卫生管理规程”,7.2 生产区清洁工作要求:执行“CSSOP000301一般生产区厂房清洁规程”,7.3 生产区人员卫生要求:执行“SCGL000101一般生产区个人卫生规程”,7.4 生产区工作服管理要求:执行“SCGL005701一般生产区工作服管理规程”9、技术经济指标核算9.2包装材料物料平衡使用量+残损量+剩余量塑料袋物料平衡= ×100%(99.0-101.0%) 本批领用量使用数+残损数+剩余数标签物料平衡= ×100%(99.0-101.0%) 本批领用数10、技术安全及劳动保护10.1 员工转岗或新工上岗前均要进行安全操作培训,熟悉本岗位的操作要点、质控要点及注意事项。
10.2 严格按工艺规程和岗位标准操作程序操作,切忌擅改工艺和岗位操作方法,工作应严肃认真。
10.3 电机设备严禁用水直接冲洗,清洁时亦不可用湿布擦拭。
在确保一切准备工作就绪后方可开机,以防轧手等事故发生。
10.4 设备定期保养,严格按设备维护保养管理制度操作使用。
10.5 拣选、切药、干燥、筛分等产尘、产湿岗位应有除尘排湿装置。
11、劳动组织和岗位定员11.1 劳动组织11.1.1 由生产制造部下达生产指令,车间依此组织生产。
制壳工艺操作规程及注意事项

制壳工艺操作规程及注意事项一.工艺要求:面层:室温:24±2℃湿度:50-70% 风速:6-8m/s硬化时间:8-10分钟,干燥时间:≥3h且干透手工撒砂:40-70目石英砂过度层:室温:24±2℃湿度:40-60% 风速:6-8m/s硬化时间:11-15分钟,干燥时间:≥4h且干透手工撒砂:20-40目石英砂加固层:室温24±2℃湿度:40-60% 风速:6-8m/s硬化时间:20-35分钟,干燥时间:≥0.5h第一层撒砂:12-20目石英砂,第二、三、四层撒砂8-12目石英砂封浆(半层)干燥时间: ≥12h二.操作程序:1.面层涂挂前,检查清洗后的模组是否有掉件的情况,并检查是否彻底干燥。
2.检查涂料粘度和设备转速是否符合要求,如不正常应加以调整(涂料粘度用4#詹氏杯测检,32±2秒)3.从运送小车上取下模组,以30度左右角度将模组较慢的浸入面层涂料浆中稍做旋转,注意使蜡模沟槽和尖角处泡在涂料中的空气减到最少,有铸字或凹槽的要用毛刷涂刷或压缩空气吹除气泡。
预先喷涂涂料。
4.以稍快的速度取出模组,使多余涂料滴除,用压缩空气吹破包在蜡模孔洞和尖角内的气泡,以不同角度不停的转动模组,模组上形成完整均匀涂层,若不能获得均匀完整涂层需重新沾浆。
5.将敷有均匀涂层的模组伸入淋砂机翻转,让全部表面均匀敷上一层砂。
6.取出模组吊挂在运送小车上,等整车挂满后,推到适当位置,让面层型壳干燥到技术规定时间。
7.将面层型壳已干燥的模组运送到过渡层制壳车间。
8.取下模组检查型壳内角,孔内是否彻底干燥,若有涂层堆积皱纹或开裂等的情况,应立即另做处理。
9.取下模组轻轻震落多余浮砂。
10.把模组浸入硅溶胶中,不超过2秒钟取出后滴约5秒钟。
11.把不再滴预湿剂的模组以30度左右角度缓慢浸入过渡层涂料中稍做旋转3-4秒,以稍快速度取出模组不停转动,滴除多余涂料形成均匀涂层,如孔洞等处有涂料闭塞和堆积可使用压缩空气或毛刷弄开。
精铸制壳工安全操作规程

精铸制壳工安全操作规程一、前言精铸制壳工是一项高风险的操作工作,为了确保工作人员的人身安全和生产环境的稳定,制定本安全操作规程。
本规程适用于精铸制壳工的全部工作环节,包括操作前的准备、操作过程中的注意事项以及操作后的清理和保养等。
二、操作前的准备1. 检查设备:操作前需仔细检查所需设备,确保设备完好无损,各项安全装置齐全有效,如发现异常情况应立即上报主管。
2. 穿戴防护装备:操作人员应穿戴好符合要求的防护服、手套、眼镜等防护装备,保护好自己的身体。
3. 熟悉操作流程:在进行任何操作之前,操作人员应熟悉操作流程,了解每个步骤的要求和技巧,确保能够熟练操作。
三、操作过程中的注意事项1. 严守操作规程:在操作过程中,操作人员应严格按照相关操作规程进行操作,杜绝违章操作和危险行为。
2. 注意人身安全:操作人员应保持良好的工作姿态,避免疲劳操作,防止因操作不当造成人身伤害。
3. 控制操作区域:操作人员应保持操作区域的整洁和干净,确保没有杂物和障碍物,防止摔倒和滑倒。
4. 遵守操作要求:在精铸制壳工过程中,必须按照工艺要求进行操作,严禁随意更改和调整工艺参数。
四、操作后的清理和保养1. 清理工作区域:操作完成后,操作人员应及时清理工作区域,将杂物和废料清理干净,确保工作环境整洁。
2. 设备保养:操作人员应定期对所使用的设备进行检查和保养,确保设备的正常运转和安全使用。
3. 责任交接:在交接班的过程中,操作人员应将使用情况和设备状态进行详细交接,确保接班人员了解操作要点和注意事项。
4. 安全培训:定期进行安全培训,提醒操作人员注意安全操作和事故预防,增强安全意识。
五、应急措施1. 紧急开关:在发现紧急情况时,操作人员应立即将设备紧急开关打开,切断电源,防止进一步事故的发生。
2. 报警求助:在无法自行解决的紧急情况下,操作人员应及时向主管报警求助,寻求专业的帮助和指导。
3. 自救逃生:若发生火灾等危险情况,操作人员应迅速采取自救和逃生措施,确保自身安全。
涂料制壳安全操作规程

涂料制壳安全操作规程涂料制壳是一项非常重要的工艺,它可以为物体表面提供保护、美化以及防腐蚀的功能。
然而,由于涂料常含有有害的化学物质,所以在进行涂料制壳操作时,必须严格遵守安全操作规程,以确保自身安全和工作环境的安全。
下面是涂料制壳的安全操作规程。
1. 个人防护措施在进行涂料制壳操作时,必须穿戴适当的个人防护装备,包括防护服、防护手套、防护眼镜和防护面具等。
这些装备可以有效地防止涂料直接接触皮肤、眼睛和呼吸道,减少对身体的损害。
2. 通风设施在涂料制壳过程中,需要使用各种有害的化学物质,这些化学物质会释放出有毒气体。
为了保护工作人员的健康,必须在操作区域设置良好的通风设施,确保室内空气的流通和清新。
3. 安全存储涂料是易燃易爆的化学物质,必须妥善存放,避免与火源接触。
涂料应存放在防火防爆的储存柜中,并按照相关规定进行分类和标识。
同时,应定期检查涂料容器的密封性以及标识的完整性,确保涂料的质量和安全。
4. 废弃物处置在涂料制壳过程中产生的废弃物必须妥善处理,不能随意丢弃。
废弃涂料容器和溶剂等应按照相关规定进行分类,然后交由专门的废物处理机构进行处理。
必须确保废弃物处置过程中不会对环境和人体健康造成任何危害。
5. 灭火设备由于涂料易燃易爆,必须在操作区域内配备足够的灭火器材,以应对突发火灾。
工作人员必须熟悉使用灭火器,并定期进行演练,提高自己的灭火技能。
6. 禁止吸烟在涂料制壳过程中严禁吸烟,因为涂料中的挥发性有机物可以与空气中的烟雾产生化学反应,形成易燃易爆的混合物,导致火灾和爆炸的发生。
7. 操作培训在进行涂料制壳操作之前,必须接受相关的操作培训。
工作人员应该熟悉涂料的性质和使用方法,了解各种化学物质的危害性,并掌握正确的操作技术和事故处理方法,确保操作的安全。
8. 急救准备在涂料制壳操作过程中,由于误操作或不可预测的意外,可能会导致人员受伤或中毒。
因此,在操作区域内必须配备完善的急救设施和急救药品,以便及时处理突发情况,保护伤员的生命和健康。
制壳作业标准规范(0806)

制壳工艺参数及操作规范一、浆料配制1.浆料配比及工艺参数制壳工艺参数及操作规范2.涂料搅拌时间A.面层锆浆配料由专人负责,新料配成后搅拌24小时以上方可使用,中途添加配料必须12小时后方可使用.B.二层锆浆配料完成后搅拌12小时以上方可使用, 中途添加配料必须8小时后方可使用.C.莫来石粉新配浆料完成后搅拌至少4小时以上方可使用, 中途添加配料必须0.5小时后方可使用.3.测量和调整:A.量杯测量时间以上涂料配完后0.5小时后粗测,到达规定时间时再次测量,若不符合要求,超出上限或下限2秒,需加硅溶胶或粉料调整,并作记录.B.使用过程中一般每2小时测量一次,如涂料粘度增加时,可用蒸馏水或同种硅溶胶加以调整.4.面层涂料使用期限:≤15天.5.涂料作业区温度:20~25℃,允许超出上限或下3℃.二、操作要点:1.开始作业前必须测浆浓度,合格后方可浸涂(沾浆)2.每班涂挂结束后,应在涂料层表面撒上50-100毫升蒸馏水(夏季100毫升,冬季50毫升)以补充水分挥发.制壳工艺参数及操作规范3.表面层使用到期后,应倒入第二层锆浆桶内使用.4.涂料桶涂料后加盖,减少空气硬化反应及水分挥发.5.字体及细小痕迹处应喷硅溶胶液,然后用压缩空气气枪吹扫,再次浸浆一次,以防出现铁豆缺陷.6.涂挂涂料力求均匀,涂时上下左右均匀转动,滴流干净,但浸涂取出后至撒砂时间最佳为10-20秒,不得超过30秒,以免涂层干涸,出现砂浆分层.三安全及注意事项1.在向搅拌桶中加料及用手揉搓过程中注意勿将衣服等挂到桶体上以免发生伤人事故.2.倾入粉料时应尽量轻松、慢放,以免粉尘飞扬,操作者要戴口罩.3.搅拌桶有浆料时必须连续转动,停用72小时以上时要将桶内浆料倾出并清洗干净.4.面层涂料配制时要严格按加料顺序,依次加入硅溶胶、湿润剂、锆粉、消泡剂,加料顺序应正确.5.涂料浆务必保持干净,不得有蜡屑、砂粒等,不得有过多的气泡。
每天上下班用筛子清理浆内杂质.6.涂料浆粘度每班上、下班时均需测定、调整并做记录.制壳工艺参数及操作规范一.敷砂工艺参数(GS硅溶胶)制壳工艺参数及操作规范二、层数选择原则预湿剂之滴法:对复杂件可采用滴杯滴沾浆死角,且要转动产品,注意只要润湿即可.预湿剂之浸法:将模壳浸入硅溶胶预湿剂中,不要超过2秒,取出后约滴5秒钟,保证不再滴预湿剂.三、操作要点和注意事项1.严格控制制壳区温度和干燥区湿度、温度和风速.2.要特别注意制好面层型壳,确保深孔和尖角处涂料与蜡模间无气泡,无涂料堆积、糊住孔等现象.制壳工艺参数及操作规范3.第一层最好自然干燥,不允许用电扇直接吹型壳,以免产生裂纹及脱壳;注意面层和二层型壳干燥速度不应太快,干燥时间不应太长,以免出现龟裂等缺陷。
涂制壳型工艺规程

涂制壳型工艺规程一.原材料要求:1. 石英砂(粉):含SiO2>98%,颗粒均匀,干燥洁白,无金属或非金属杂质。
2. 水玻璃:模数3.3~3.5,比重:1.32~1.403. 耐火粘土:耐火度>1710℃4.氯化铵:含NH3>98%二.制壳涂料的配制:1. 检测水玻璃比重是否符合使用要求,否则应加于调整后使用。
2. 称量水玻璃,石英粉的重量3. 涂料配制方法:A:面层涂料:(1)将称量好的水玻璃倒入涂料缸内,以称量1/3石英粉加入于水玻璃中进行缓慢搅拌,然后在搅拌过程中分批加入剩余的石英粉。
(2)涂料经过充分搅拌(约10~20分钟)均匀后静置40分钟,然后进行检测粘度,符合规范方可使用。
(注:面层涂料最好提前一个班配好,第二班搅拌检测粘度,调正后使用。
)B:过渡层涂料(第二层),加强层(第三层)以后各层涂料:(1)配制方法:应先加石英粉,后加耐火粘土,在搅拌过程中将耐火粘土加完,然后继续搅拌10~20分钟,静置30分钟左右,再测量其粘度,如果不合格再加调整。
三.涂料配制比例:层次重量比例粘度(秒)备注水玻璃石英粉耐火粘土面层100 110~115 42~45石英粉:250~270耐火粘土:170~220 过渡层100 80~85 20 26~28加强层100 30~40 60~70 35~40注:1.对于涂料粘度夏天可取上限,冬天可取下限,进行适当调整粘度使用2.根据蜡模零件复杂程度可以适当调整涂料的粘度,对于结构较复杂的(有细小孔眼,沟槽夹小而深)的零件可取上限,而形状简单较大的零件时可取下限四.涂制模壳:1. 涂制各层工艺参数:模壳层料涂料类别撒砂粒度(目)硬化剂浓度(%)硬化时间(分)硬化剂温度(℃)晾干时间(分)1 面层涂料50~70 25~35 8~10 20~30 30~402 过渡层涂料30~40 25~35 10~15 20~30 30~40 3~5 加强层涂料10~20 25~35 15~25 35~40 50~60 2.涂制壳型操作程序:(1)检查蜡模组的浇口棒的顶平面是否平整,不允许有裂纹,深的孔眼,沟槽等缺陷,否则须修补平整或更换模组。
制壳工序脱蜡管理制度

制壳工序脱蜡管理制度
为确保型壳质量,使蜡能脱干净,能够保障型壳满足浇注需要,根据实际脱蜡条件,制定本管理办法。
1、采用水脱蜡工艺;要点是高温快速脱蜡。
2、a.水温设定:93—98℃,严禁沸腾,以免将箱底的砂粒及脏物翻起而进入型腔。
b.水箱中加入3%—8%的氯化铵,使型壳脱蜡时得到补充硬化并可防止模料在脱蜡时皂化,并定期检查,随时补充氯化铵,作好记录,
c.型壳制成后需要停放12—24小时以上才可进行脱蜡,停放期间也是型壳中残留硬化剂对涂料层继续硬化的过程。
把涂完料的合格型壳脱蜡将浇口杯顶部浮沙及涂料清理干净,并把浇口杯侧放置于铁框内(禁止浇口杯向下脱蜡)。
d.每框待脱蜡的型壳只允许放同一种型壳,并合理放置数量和方向,使蜡液能及时顺畅排出,每框放置高度不能超过铁框上沿5—8cm。
e.当型壳放置在热水中脱蜡10分钟左右时,必须让型壳透气,吊出水面(蜡面)2分钟左右,再继续放入热水中脱蜡,脱蜡时间一般应控制掌握在15—20分钟。
厚大零件适当延长时间,视具体情况而定,以不超过30分钟为宜。
f.在东边水箱中脱完蜡后,吊起铁框使蜡液很快流完并放置在西边水箱中,必须进行二次脱蜡,时间控制在5分钟左右,并上、下反复用热水清洗数次,使蜡保证能够完全脱干净,及时倒净型壳里面的蜡水及杂质。
并摆放到指定地方,分类放置,进行自干。
g.禁止浇口杯向下脱蜡,防止型壳胀裂。
h.每半个月定期更换脱蜡水,清理水箱底部砂粒及脏物。
j.谁脱蜡谁负责,因脱蜡而导致型壳报废,按产品半价在工资中扣除。
3、下班前必须关闭脱蜡箱电源。
制壳工艺操作规程及注意事项

4.应经常清除涂料表面的蜡屑等杂物。
5要确保背层干燥期间,模组之间的空气流动,除湿机能处于最佳状态。
16.取出模组让多余涂料滴落,连续操作时可挂在沾浆机上方架上。让涂料滴回浆桶,然后取下模组,不停转动使各处涂层均匀,要注意浇口杯缘处涂层不要太薄。
17.将模组伸入浮砂桶内敷砂,当浇口杯缘已达砂中时,缓慢抽出模组震落多余砂粒,把模组吊挂回小车上,推到干燥区进行规定时间的充分干燥。
18.重复以上步骤进行背层第二、三层涂挂敷砂,充分干燥后再封浆。注意封浆干燥时间通常情况下时间相对延长。
12.将模组伸入浮砂桶内敷砂,当浇口杯缘已有砂时,即可缓慢抽出模组,震落多余的砂粒,目视应无任何区域尚未被砂敷住,如有无覆盖处,可用手辅助敷砂,直到均匀。
13.把模组吊挂到运送小车上,整车挂满后,推到干燥区干燥8小时以上。
14.将小车推到背层涂料处,取下模组轻摇,去除型壳上松散的浮砂。
15.小心将模组浸入背层涂料桶中,轻轻转动最少10秒钟。
7.将面层型壳已干燥的模组运送到过渡层制壳车间。
8.取下模组检查型壳内角,孔内是否彻底干燥,若有涂层堆积皱纹或开裂等的情况,应立即另做处理。
9.取下模组轻轻震落多余浮砂。
10.把模组浸入硅溶胶中,不超过2秒钟取出后滴约5秒钟。
11.把不再滴预湿剂的模组以30度左右角度缓慢浸入过渡层涂,如孔洞等处有涂料闭塞和堆积可使用压缩空气或毛刷弄开。
19.各层涂挂完毕,及时清理现场,清扫设备等保养。
三.注意事项:
1.严格控制制壳车间湿度、温度、风速及涂料粘度。
2.要特别认真制好面层,确保深孔和尖角处涂料与蜡模间无气泡,无涂料堆积,糊住孔等现象,面层型壳刚制完不得置于风扇前后,注意面层和过滤层干燥速度不宜过快,干燥时间不应过长,以防出现龟裂缺陷。
制壳生产安全操作规程

制壳生产安全操作规程
一、工作前首先要熟悉本工序工艺规程及设备安全操作要点。
劳保用品必须按规定穿戴齐全。
二、使用 T1140 涂料搅拌机时,应集中精力掌握操纵手把,使叶轮回旋摆动、上下运动,叶轮不能碰击涂料缸壁。
三、轴节、销节、螺杆等处要经常加油润滑,有轴承的一年要加一次黄油。
四、使用 T1117L 涂料搅拌机之前要检查减速机油位,不够时要加到
规定的高度,每星期观察检查一次。
五、 T1117L 如遇停电,必须将叶片提起,若停电后,叶片没有被
提起时,切勿启动电机,否则将造成丝杆弯曲,电机烧毁。
六、M394斗式雨淋撒沙机与除尘机组要配合使用;先开动、再去尘,然后用小车推入滑轮撒沙。
要定期清除收集的尘埃。
七、电动葫芦、吊具在吊运滑轮过程中要慢、要平稳,不能晃动,更
不能碰撞到其它物件,并要注意周围人员安全。
八、使用电动葫芦作业时,应注意避免斜拉、斜吊,禁止使用湿手开启手电门,工作时声音有异常,控制失灵等应紧急停止使用。
精密铸造 制壳工艺

精密铸造制壳工艺一、概述精密铸造制壳工艺是指利用铸造技术,将金属或合金熔化后注入模具中,通过冷却凝固形成各种形状的零件。
该工艺具有生产周期短、成本低、制造精度高等优点,广泛应用于航空航天、汽车制造、电子通讯等领域。
二、材料选择1. 铸造材料:通常选择高强度、高耐腐蚀性能的金属或合金,如不锈钢、铝合金等。
2. 模具材料:通常选择高温耐磨性能好的材料,如钢铁等。
三、模具设计1. 根据零件形状和尺寸要求设计模具结构,并确定模具开口方向。
2. 考虑到零件表面质量和模具使用寿命,对模具表面进行光洁度处理或涂覆耐磨涂层。
四、制备模具1. 根据设计图纸将所选材料切割成相应尺寸。
2. 将各部分零件组装成完整的模具,并进行调试和检查。
五、铸造准备1. 清洗和涂覆模具表面,确保表面干净平整。
2. 准备铸造材料,进行熔炼和净化处理。
3. 将模具加热至一定温度,以保证铸造材料能够充分流动并填充模具。
六、铸造过程1. 将预热好的模具放置在注塑机上,并通过控制系统进行开合操作。
2. 将已经熔化和净化处理好的铸造材料注入到模具中。
3. 控制注塑机的压力、温度等参数,确保铸造材料能够均匀地填充到模具中,并冷却凝固。
七、零件取出1. 等待铸造材料完全冷却后,将模具打开并取出零件。
2. 对零件进行清洗和抛光等表面处理。
八、质量检查1. 对零件尺寸、形状、表面质量等进行检查,并与设计要求进行比对。
2. 对铸造过程中产生的废品和次品进行分类和处理。
九、结论精密铸造制壳工艺是一种高效、精度高的制造工艺,在现代工业生产中得到广泛应用。
通过合理的材料选择、模具设计和铸造过程控制,可以生产出高质量的零件。
制壳工艺守则

宁夏朗盛精密制造技术有限公司文件编号 QB/JZ-007 版本号/修订状态:A/3制壳工艺守则(试用)2013年10月发布2013年11月实施吴忠仪表宁夏朗盛精密制造技术有限公司前言本守则在原《熔模铸造工艺操作规程》(WYZZ-JS/WJ-12-2006)的基础上,参照相关标准制定。
本守则对原规程进行了细化,使其更具有指导性。
本标准由吴忠仪表宁夏朗盛精密制造技术有限公司技术部出并归口。
本标准由吴忠仪表宁夏朗盛精密制造技术有限公司技术部负责制定。
原标准《熔模铸造工艺操作规程》(WYZZ-JS/WJ-12-2006)起草人:党李燕。
本守则修订人:闫文学。
本守则发布以后,原标准自行作废。
制壳工艺守则1 范围1.1本守则为精铸制壳技术操作的一般性规定。
1.2本守则是精铸制壳操作和技术检查的依据。
1.3操作人员须遵守安全操作规程以及佩戴相关劳保用品。
2 一般蜡模的制壳流程一般蜡模的制壳程序如下:清洗蜡模→面层→风干→过渡层→风干→加固层→硬化→挂架3. 制壳用原材料及技术条件 3.1 耐火材料:见表1表 1 耐火材料理化指标3.2加固层水玻璃(Na2O.nSiO2)要求干净无杂质。
模数:M=3.0~3.4(冬季取上限、夏季用下限)。
比重:d=1.30~1.36外购水玻璃如果d太高必须进行稀释处理,加水量计算如下(do-d)mX= do(d-1)式中:do——原水玻璃比重d——要求的水玻璃比重m——处理水玻璃总量冬天为使涂料温度不至过低,可用热水稀释水玻璃。
3.3面层硅溶胶:技术要求见表2一般使用830胶核对参数表 23.4加固层硬化剂a.结晶氯化铝:AlCl3.6H2O≥95%b.氯化铵:NH4Cl≥99%3.5表面活性剂:渗透剂T(化学名:琥珀酸酯磺酸钠)。
4.制壳工艺及操作要点4.1硬化液的配制:见表3(硬化液一般配比是饱和状态)表 34.2 涂料的配制:4.2.1 复合模壳涂料的配制见表4(涂料配比按不同层有所不同,需要调整)表 44.2.2 全硅溶胶工艺的涂料配制。
- 1、下载文档前请自行甄别文档内容的完整性,平台不提供额外的编辑、内容补充、找答案等附加服务。
- 2、"仅部分预览"的文档,不可在线预览部分如存在完整性等问题,可反馈申请退款(可完整预览的文档不适用该条件!)。
- 3、如文档侵犯您的权益,请联系客服反馈,我们会尽快为您处理(人工客服工作时间:9:00-18:30)。
宁夏朗盛精密制造技术有限公司
文件编号 QB/JZ-007 版本号/修订状态:A/3
制壳工艺守则
(试用)
2013年10月发布2013年11月实施吴忠仪表宁夏朗盛精密制造技术有限公司
前言
本守则在原《熔模铸造工艺操作规程》(WYZZ-JS/WJ-12-2006)的基础上,参照相关标准制定。
本守则对原规程进行了细化,使其更具有指导性。
本标准由吴忠仪表宁夏朗盛精密制造技术有限公司技术部出并归口。
本标准由吴忠仪表宁夏朗盛精密制造技术有限公司技术部负责制定。
原标准《熔模铸造工艺操作规程》(WYZZ-JS/WJ-12-2006)起草人:党李燕。
本守则修订人:闫文学。
本守则发布以后,原标准自行作废。
制壳工艺守则
1 范围
1.1本守则为精铸制壳技术操作的一般性规定。
1.2本守则是精铸制壳操作和技术检查的依据。
1.3操作人员须遵守安全操作规程以及佩戴相关劳保用品。
2 一般蜡模的制壳流程
一般蜡模的制壳程序如下:
清洗蜡模→面层→风干→过渡层→风干→加固层→硬化→挂架
3. 制壳用原材料及技术条件
3.1 耐火材料:见表1
风干
沾面层涂料撒面层砂沾过渡层涂料撒过渡层砂
风干
沾加固层涂料
撒加固层砂
硬化
清理冒口砂
制好的壳挂架
将蜡模放入
水中清洗
表 1 耐火材料理化指标
3.2加固层水玻璃(Na2O.nSiO2)要求干净无杂质。
模数:M=3.0~3.4(冬季取上限、夏季用下限)。
比重:d=1.30~1.36外购水玻璃如果d太高必须进行稀释处理,加水量计算如下
(do-d)m
X= do(d-1)
式中:do——原水玻璃比重d——要求的水玻璃比重
m——处理水玻璃总量
冬天为使涂料温度不至过低,可用热水稀释水玻璃。
3.3面层硅溶胶:技术要求见表2一般使用830胶核对参数
表 2
3.4加固层硬化剂
a.结晶氯化铝:AlCl3.6H2O≥95%
b.氯化铵:NH4Cl≥99%
3.5表面活性剂:渗透剂T(化学名:琥珀酸酯磺酸钠)。
4.制壳工艺及操作要点
4.1硬化液的配制:见表3(硬化液一般配比是饱和状态)
表 3
4.2 涂料的配制:
4.2.1 复合模壳涂料的配制见表4(涂料配比按不同层有所不同,需要调整)
表 4
4.2.2 全硅溶胶工艺的涂料配制。
见表5(与中温蜡硅溶胶涂料应该接近,请核对)
表 5
4.2.3 全硅溶胶制壳的工艺要求。
见表6(与中温蜡硅溶胶涂料应该接近,请核对)
表6
4.3 配制面层涂料
首先称量好硅溶胶,然后按比例称量好锆英粉,并逐步加入硅溶胶中进行搅拌。
大约搅拌2小时后,加入渗透剂T,再搅30分钟加盖密封。
(注意事项; 定时清理涂料桶,每月至少一次。
随时过滤涂料中的杂质)
4.4 配制加固层涂料
称好水玻璃(如比重高必须加水稀释进行调整,要求搅拌1~3分钟)按比例加入煤矸石粉,搅拌2小时。
4.5 表面层涂料使用前搅拌并测其粘度,检查涂挂性,如粘度过高,可加
硅溶胶。
涂挂性差可加渗透剂。
4.6加固层涂料静置2小时后方可使用,并将涂料上层的硬皮去掉,搅拌
3~5分钟后调整粘度达工艺要求,然后进行涂挂,加固层涂料使用期限为≤4天。
5. 模组制壳
5.1 将装配好的模组在含0.2~0.3%洗净剂水溶液中洗涤后,在清水中冲洗
干净。
5.2将晾干的模组浸入到表面涂料中,使模组均匀地涂挂一层0.2~0.5mm
厚的涂料。
要注意消除气泡和防止涂料堆积,轻轻转动模组,使凹部、小孔、拐角都能挂上涂料。
难涂挂部位用毛涂刷。
5.3 将涂挂好的模组放入淋砂机或砂盘中,转动模组,均匀地撒砂。
要防
止涂料被吹掉和砂子堆积及漏挂砂现象。
5.4 表面层涂挂好后模组不允许有暴露蜡模的部分。
5.5 除去表面层的浮砂,将模组挂在模组架上,通风进行强制干燥。
环境
温度20~28℃,风速≥2米/秒,干燥时间≥150分钟,以模壳内腔干透为准。
5.6 第三层开始涂挂加固层涂料,并撒煤矸石砂,经硬化液硬化,自然干
燥。
模组一般挂5~8层,零件具体结壳层数见工艺卡。
其风干硬化工艺见表7
表7 风干硬化工艺要求
层次撒砂风干(分钟) 硬化(分钟) 自干(分钟) 备注
表面层锆砂>150 风力干燥
过渡层铝钒土砂>150
加固层煤矸石砂8~12 ≥30
5.7 硬化液在每次使用前要进行检验和调整。
加入硬化剂的量参照5.1 条
的表3,使比重保持在1.17~1.19,PH1.5~2.5之间。
5.8 制好的模壳必须经过12小时的自然干燥方可进行脱蜡。