隧道窑温度曲线
陶瓷隧道窑微机温度控制系统

陶瓷隧道窑微机温度控制系统摘要目前我国陶瓷隧道窑炉大多采用人工或简单仪表控制,要想使窑炉长期达到最佳工作状态是不可能的,造成产品合格率、一级品率一直处于较低的水平。
陶瓷隧道窑炉是由预热带、烧成带和冷却带三个部分组成,瓷件烧成温度在1320℃左右,窑内温度场主要由烧成带12对喷嘴燃冷煤气产生,窑炉系统用8组风机来调节窑内的压力场。
排烟风、助燃风将直接影响烧成带的温度场,急冷风会影响最终产品的质量。
温度控制系统将采集的各点温度值,经A/D转换后与设定值进行比较,控制器输出经由D/A变换,变成 4~20mA形式模拟量输出给电动执行器,驱动蝶形阀调节喷嘴的煤气进给量,从而控制烧成带的温度。
12只温度传感器与12个喷嘴一一对应。
关键词:MSP430F149单片机、热电偶,变送器、大林算法、I2C总线、多路开关一.总体方案设计 1.对象的工艺过程陶瓷隧道窑炉是由预热带、烧成带和冷却带三个部分组成,瓷件烧成温度在1320℃左右,窑内温度场主要由烧成带12对喷嘴燃冷煤气产生,窑炉系统用8组风机来调节窑内的压力场。
排烟风、助燃风将直接影响烧成带的温度场,急冷风会影响最终产品的质量。
温度控制系统将采集的各点温度值,经A/D转换后与设定值进行比较,控制器输出经由D/A变换,变成 4~20mA 形式模拟量输出给电动执行器,驱动蝶形阀调节喷嘴的煤气进给量,从而控制烧成带的温度。
12只温度传感器与12个喷嘴一一对应。
窑温控制示意图2.对象分析被控过程传递函数se s s G 403o )251(25.2)(-+=是一个大的延迟环节,而且温度的控制对系统的输出超调量有严格的限制,用最少拍无纹波数字控制器的设计,和PID算法效果欠佳,所以本设计采用大林算法设计数字控制器。
3.控制系统设计要求窑温控制在1320±10℃范围内。
微机自动调节:正常工况下,系统投入自动。
模拟手动操作:当系统发生异常,投入手动控制。
微机监控功能:显示当前被控量的设定值、实际值,控制量的输出值,参数报警时有灯光报警。
隧道窑用程序表升温曲线怎么烧制陶瓷产品

隧道窑用程序表升温曲线怎么烧制陶瓷产品烧成曲线是表示焙烧温度和焙烧时间关系的曲线。
它包括升温、保温和冷却三个阶段(在其概念上有区别窑炉操作中的预热、烧成、保温和冷却带的划分)。
能在最短的时间内(烧成周期)获得合格产品的烧成曲线,成为最佳烧成曲线。
每一种原料均存在一个最佳烧成曲线,但受窑炉结构、加热方法、码坯形式等许多因素的限制,在实际生产中,很难达到最佳烧成曲线状态,只能结合生产实际确定一个合理的烧成曲线。
合理的烧成曲线是窑炉设计和烧成热工制度(包括温度、压力、气氛及顶车制度等)的主要依据。
合理烧成曲线的制定关系到窑炉结构、产量与质量,有着很重要的实际意义和经济效益。
一、合理升温时间的确定升温时间是指从常温下将砖坯加热到最高允许烧成温度的时间。
在升温过程中,要注意影响加热速率的三个过程,即脱水过程、膨胀与收缩过程、可燃物的燃烧和氧化过程。
(1)脱水过程在坯体中,残留的空隙水和黏土矿物层间水的蒸发,各种矿物结构水的释放,来自氧化物生成的水分等均会在预热带出现。
在预热带,各种水分的蒸发和排出,就意味着坯体可能出现显微结构上的裂纹或是裂纹的扩展、松弛等现象,使坯体结构强度降低,从而影响最终的产品质量。
(2)膨胀与收缩过程在加热期间坯体产生收缩与膨胀,如果这种过程发生在很狭窄的温度范围内,就极有可能由于膨胀应力导致了坯体内部显微裂纹的扩展。
例如,石英晶体的转变。
剧烈膨胀出现的温度区域约在650~850℃之间,所以在该区域升温速度应该平缓。
另外,当原料中含有较高的碳酸盐时,在分解温度内(800~900℃)也会出现所谓的“中间状态”的收缩,此时,如果焙烧不当,也有可能在坯体中产生裂纹。
预热带产生的裂纹断面粗糙,而冷却带产生的裂纹断面平滑,要以此辨别裂纹产生的原因,采取相应防治措施。
(3)可燃物的燃烧和氧化过程为了保证氧化物在坯体出现液相之前充分氧化,或为限制大断面隧道窑焙烧窑产量的关键因素之一,也给窑炉设计与操作带来了困难。
隧道窑操作规程 2
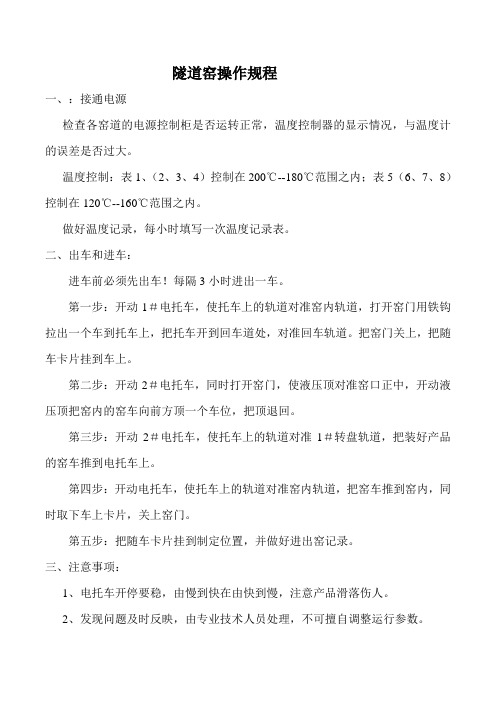
隧道窑操作规程
一、:接通电源
检查各窑道的电源控制柜是否运转正常,温度控制器的显示情况,与温度计的误差是否过大。
温度控制:表1、(2、3、4)控制在200℃--180℃范围之内;表5(6、7、8)控制在120℃--160℃范围之内。
做好温度记录,每小时填写一次温度记录表。
二、出车和进车:
进车前必须先出车!每隔3小时进出一车。
第一步:开动1#电托车,使托车上的轨道对准窑内轨道,打开窑门用铁钩拉出一个车到托车上,把托车开到回车道处,对准回车轨道。
把窑门关上,把随车卡片挂到车上。
第二步:开动2#电托车,同时打开窑门,使液压顶对准窑口正中,开动液压顶把窑内的窑车向前方顶一个车位,把顶退回。
第三步:开动2#电托车,使托车上的轨道对准1#转盘轨道,把装好产品的窑车推到电托车上。
第四步:开动电托车,使托车上的轨道对准窑内轨道,把窑车推到窑内,同时取下车上卡片,关上窑门。
第五步:把随车卡片挂到制定位置,并做好进出窑记录。
三、注意事项:
1、电托车开停要稳,由慢到快在由快到慢,注意产品滑落伤人。
2、发现问题及时反映,由专业技术人员处理,不可擅自调整运行参数。
隧道窑热工制度及热工操作详解

隧道窑内温度分布特点
预热带:前高后低、上高下低、中间高两边低 烧成带:均匀 冷却带:后高前低、下高上低、中间高两边低
但对某一砖垛:预热带:中间低两边高
冷却带:中间高两边低(传热学)
温度的检测与控制
烧成曲线是保证烧成产品质量的主要工艺参数, 只要保证预热带、烧成带和冷却带的温度曲线符 合工艺要求即可。 温度的检测多采用接触式的测温热电偶,配 以非接触式红外辐射高温计。 温度的控制: 烧成带——控制两侧喷枪的燃料量进行温度控制; 冷却带——改变冷却风机的鼓风量及抽热风机的抽风
近似认为:
hg0 =hg1(hg = Hg(ρh-ρa)),
hk0 =hk1 (hk = ρhu2/2) ,
则 hs0=hs1+hw0-1
hs1—排烟机或烟囱所造成的抽力,通常情况,
可视为常数
hs0hw0-1,hw0-1 烟道闸板。
hs0hw0-1,hw0-1 烟道闸板。
hs0=hs1+hw0-1 ①提起烟道闸板, hw0-1减小, hs0则减小,若原
出,通过窑顶、窑墙通道送入窑内; ②喷射器将窑内砖垛下部的气体引射到窑内 上部,形成窑内上下气流循环。
7
5
⑸增热循环: 排烟孔抽出的烟气与增热炉出来的烟气混合后, 从窑顶重新送入窑内各砖垛间,使烟气上下循环, 可以加快对流换热,降低上下温差。
⑹辅助烧嘴
(预热带安装高速烧嘴,耐火
材料窑炉很少用) ⑺采用低蓄热窑车
B.零压位的调节:零压位的位置,通过调节烟 道闸板来控制 提起闸板,零压位向冷却带方向移动; 降低闸板,零压位向预热带方向移动。
0
Ⅱ
Ⅰ
0 Ⅱ
Ⅰ
在0压位0—0面与Ⅰ—Ⅰ(预热带总烟道处)
隧道窑
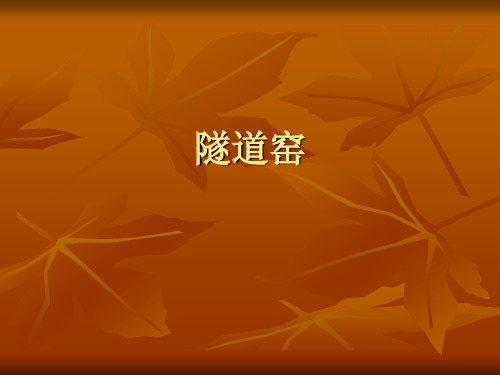
隧道窑
1.概述 2.隧道窑的结构 3.隧道窑的温度制度
概述
在耐火材料、陶瓷等制品的生产过程中, 烧成是一道重要工序,对产品的产量和质 量影响较大。 烧成设备主要有两大类,一类是连续式窑, 如隧道窑;另一种为间歇式窑,如倒焰窑 等。
高铝砖(3.5 万吨/年): 预热带/烧成带/冷却带 = 72/24/60.6(米)
镁质制品(4~4.5 万吨/年): 预热带/烧成带/冷却带 = 72/24/60(米)
日用瓷(7 x 106 吨/年): 预热带/烧成带/冷却带 = 29.86/26.47/35.67(米)
电瓷(还原焰)(562 万吨/年): 预热带/烧成带/冷却带 = 38.52/28.0/50.07(米)
概念: 一次空气:通过烧嘴直接进入燃烧室(或直接 进入窑内空间)与燃料混合燃烧的空气。它可 以是冷却带抽出的多余热风,可以是冷空气。 二次空气:在冷却带吹入的冷风的一部分,流 到烧成带,与燃料混合燃烧。
一次空气送风装置:风机、喷射器
★一次空气为冷空气时: 冷空气→通风机→空气管道→烧嘴。
★一次空气为热风时: 冷却带的多余热风→耐热风机→管道→烧嘴;
★窑的各带长度确定的一般原则:
1.预热带长度应根据排出废气温度来确 定,废气离开排烟机温 度应低于250℃;
2. 烧成带长度根据保温时间来确定 3.冷却带长度根据出窑制品的温度来确
定,一般应低于100℃
隧道窑长度及各带长度计算式:
V— 隧道窑的有效容积, m3;
1.4-1.8(隧道窑热工制度节能等)

材料窑炉很少用) ⑺采用低蓄热窑车
图1-23
窑 车 蓄 热 占 总 热 耗 的 30% 以上。采用轻质材料砌筑窑车 衬砖,并改进窑炉的结构。
⑻改进窑的结构
(低、宽、短方向发展)
图1-18
图1-18
沿隧道窑长度方向压力(静压)分布的规律。压 力制度是为了保证温度制度和气氛制度的实现。理想 的状况为窑内零压左右。 隧道窑内压力分布特点: 预热带负压; 烧成带微正压; 冷却带正压 预热带靠近烧成带“零压”
为0压,经调节变为负压,0压位向冷却带方向移
动,如移至01点,全窑负压增大;
Ⅱ
Ⅰ
Ⅱ Ⅰ
hs0hw0-1,hw0-1 烟道闸板。 hs0=hs1+hw0-1 ②降低烟道闸板, hw0-1增大, hs0则增大,若原
为0压,经调节变为正压,0压位向预热带方向移
动,如移至02点,全窑正压增大。
Ⅱ
Ⅰ
Ⅱ Ⅰ
为了综合考虑各种因素, 码砖操作必须注意下列参数的正确选取:
①装砖密度:单位体积内的装砖量。
它反映砖垛的阻力状况和传热情况。装砖密度 与烧成制度相配合。装砖密度影响产量。
G成 g 60 24 J
g—装砖密度,t/车; △ τ—推车间隔时间, min; J —年工作日,日; η—成品率;
图1-21
①耐热风机把预热带的热气体由窑顶小孔抽 出,通过窑顶、窑墙通道送入窑内;
②喷射器将窑内砖垛下部的气体引射到窑内
上部,形成窑内上下气流循环。
7
5
⑸增热循环:
排烟孔抽出的烟气与增热炉出来的烟气混合后, 从窑顶重新送入窑内各砖垛间,使烟气上下循环, 可以加快对流换热,降低上下温差。
隧道窑工作原理及系统操作

隧道窑工作原理及系统操作隧道窑的系统设置是否合理、窑体结构能否满足要求、操作是否得当,对产品质量、产量、燃料消耗以及窑炉使用寿命都有影响。
(一)隧道窑工作原理隧道窑属于泥流操作的热工设备,沿窑长度方向分为预热带、烧成带、冷却带。
制品与气流以相反方向运动,在三带中依次完成制品的预热、烧成、冷却的过程。
隧道窑两端设有窑门,每隔一定的时间,将装好砖坯的窑车推入一辆,同时,已经烧成砖瓦成品的窑车被推出一辆。
坯体进入预热带后,首先与来自烧成带的燃烧产物(烟气)接触而且被加热,而后进入烧成带,燃料燃烧放出的热量及生成的燃烧产物加热坯体,使之达到一定的温度而烧成,并经过一定时间的保温,生成稳定的制品。
燃烧产物自预热带的排烟口、烟道,经风机或烟囱排出窑外。
烧成的制品进入冷却带,将热量传递给入窑的冷空气制品本身冷却后出窑。
被加热的空气一部分抽进去进行余热利用。
简单来说,隧道窑的烧成过程就是燃料在窑内燃烧、坯体与气体进行热交换、湿交换的过程。
通过燃料燃烧产生的热量,将窑内温度升高到坯体烧成所需温度,在烧成温度时,坯体内各组分发生一系列物理、化学变化,经过这一系列变化,坯体由生坯焙烧为具有一定强度和耐久性,符合建筑要求的砖成品。
(二)隧道窑烧成制度隧道窑工作系统的设置就是在热工基础知识的指导下,针对特定的原料和制品,制定出适宜的烧成制度并保证烧成制度的实现。
窑炉的烧成制度包括温度制度和压力制度,温度制度需要根据原料性能和产品要求而定,而压力制度是保证窑炉按照既定的温度制度进行烧成。
因此影响产品性能的关键是烧成的温度制度。
(1)温度制度温度制度依据物料在烧成过程中的化学、物理变化制定的温度及其与时间的关系,包括升温速度、烧成温度、保温时间、降温速度等参数,并最终形成适宜的烧成曲线。
隧道窑的烧成曲线隧道窑的烧成曲线也是沿窑长装在窑顶或窑侧的热电偶测得的窑内温度曲线(见图5-3),在低温阶段接近气体温度,在高温阶段接近制品温度。
陶瓷隧道窑
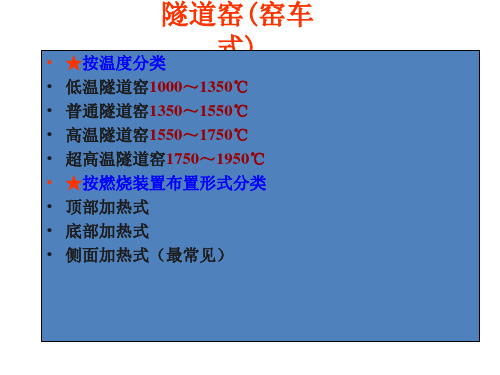
相对即两侧燃烧室相对称布置
相错即两侧燃烧室略有错开(以半个到一个车位为宜)
#一排还是二排: 一排布置时接近车台面处;烧气且用棚板装车时,分两层布置。 2)烧煤、烧重油、烧煤气的燃烧室: 3)烧嘴: 现代隧道窑采用液体和气体燃料,多用高速烧嘴,其焰气喷出速度为70-100m/s。 * 特点: a焰气以高速直接喷向物料表面,可减薄物料表面的气体层流底层,增大传热速率, “冲击加热”。 b其焰气可带动周围的烟气在窑内循环,形成强烈的搅拌,使窑内温度和气氛均匀,强 化传热,提高产量和质量。
• 注意: *热气体温度应尽量与该断面处温度接近;
*喷出速度应在10m/s以上(国外>100m/s) *作为搅动气幕的热气来源可以是烟道内的烟气,烧成带窑顶
二层拱内的热空气或冷却带抽来的热空气。 *气流喷出角度可以90℃垂直向下,也可以120-180℃喷入。 • 现代隧道窑在预热带靠近烧成带附近设置高速调温烧嘴来代 替搅动气幕。烧嘴喷出的气体可以调节到该处所需的温度, 达到快速烧成。
二、隧道窑的结构:
窑体 窑内输送设备
燃烧设备
通风设备
1、窑体:由窑墙和窑顶所组成 窑墙:作用 窑顶:作用
现代隧道窑:多采用平吊顶,用异形砖砌筑窑顶,其 下沿为平顶或近似平顶。
检查坑道: 窑门:旧式隧道窑窑头及窑尾都设有窑门,防止窑头漏入冷 空气和窑尾漏出冷风。 2、窑车及窑具: 1)、窑车:用来运载制品,窑车在窑内构成封闭的活动窑 底,窑车由金属车架及其上耐火材料组成。
21
操作控制
温度、气氛、压力三个部分的控制
一、各带的温度控制: 1、预热带: * 满足预热升温曲线以保证均匀的加热制品,从制品入窑起到第一对燃烧室止,其中 控制约500℃以及末端约900℃的温度稳定。 * 测量:用热电偶测量窑顶温度近车台面温度 * 控制手段:调节烟气总闸、排烟支闸以及各种气幕。 总闸:开度大小影响预热带负压、漏入空气多少、气体分层、上下温差
陶瓷工艺学--8 烧成-09.10

这些碳素和有机物加热即发生氧化反应:
C(有机物)+O2
350º C
CO2
C(碳素)+O2
2H2 + O2
600º C
CO2
2H2O
250~ 920º C
S + O2
2CO+O2
SO2
2CO2
这些反应要在釉面熔融和坯体显气孔封闭前
结束。否则,就会产生烟熏、起泡等缺陷。
2. 硫化铁的氧化 FeS2+O2
1. 升温速度的确定
A.低温阶段:升温速度主要取决于坯体入窑时的 水分。
如果坯体进窑水分高、坯件较厚或装窑量大,则升
温过快将引起坯件内部水蒸气压力增高,可能产生开 裂现象; 对于入窑水分不大于1%~2%的坯体,一般强度也 大,在120℃前快速升温是合理的;对于致密坯或厚胎
坯体,水分排除困难,加热过程中,内外温差也较大,
3MgO4SiO2H2O
600~ 970º 3(MgOSiO )(原顽火辉石)+ SiO +H O C 2 2 2
蒙脱石脱水:
Al2O34SiO2nH2O
Al2O34SiO2+nH2O
5. 晶型转变
石英在573℃时, -石英迅速地转变为 -石英, 体积膨胀0.82%;在870℃-石英缓慢地转变为 -鳞石 英,体积膨胀16%。石英晶型转变造成的体积膨胀, 一部分会被本阶段的氧化和分解所引起的体积收缩所 抵消。如果操作得当,特别是保持窑内温度均匀,这 种晶型转变对制品不会带来多大的影响。 由粘土脱水分解生成的无定形Al2O3,在950℃时 转化为-Al2O3。随着温度的升高,-Al2O3与SiO2反应 生成莫来石晶体。
(三)高温玻化成瓷阶段 (从950℃到最高烧成温度)
1800℃燃气高温隧道窑设计与工程实践

压力曲线的斜率较小,压力曲线比较平缓,使窑炉接近于零压状态下操作,这样,漏出和吸入窑内的气体量都较少,有利于生产【11。
可以说,TK7真正实现了微正压操作。
窑内实际压力曲线见图1。
TK7隧道窑设计了车下压力平衡系统,该系统采用了自动控制,变频调节,作用是保证车下压力的绝对值始终比车上压力的绝对值高。
所以隧道窑的车下温度低,烧成带车下温度不超过150℃。
窑车上设计了两层窀心结构的砖,使TK7的窑车的绝热性能非常好。
车下温度低为窑车的正常运行创造了良好的条件。
3自动控制系统
3.1控制系统基本情况
图1TK7隧道窑实时温度曲线与压力曲线
TK7以德国SIEMENSSTEP7和WlNCC为隧道窑自动控制软件开发平台。
该软件针对性较强,具有界面友好、操作方便、性能良好、安全叮靠的特点。
控制软件易于学习和使用,拥有非常丰富人机对话与错误报警窗口,能够满足高温隧道窑的自动化控制要求。
TK7共有控制回路13个,主要控制回路有:烧成带温度控制回路,窑内压力控制回路,助燃风与窑内氧含量控制回路等。
在主控界面上可随时查看到所有测温点温度值、测压点压力值、天然气流量、助燃风流量、引射风流量、冷却风流量以及所有风机的运行情况等。
能够动画显示推车过程,包括2道窑门的起落、推车机的推进动作、窑尾出车情况。
烧成带温度自动控制回路控制精度高,温度偏差可控制在±5℃以内。
・l5
0・。
陶瓷窑炉及设计 第一章隧道窑 第二节隧道窑的工作系统和结构(1)

墙体上孔洞砌筑方法 (a)宽度小于250的孔洞砌筑方法;(b)宽度小于450的孔洞砌筑方法
SUST
陶瓷窑炉与设计----第一章 隧道窑 圆形墙错缝与直形墙错缝方法相同,圆形墙应按中心线砌筑
圆形墙的错缝砌法
SUST
陶瓷窑炉与设计----第一章 隧道窑
砌体检查方法 (a)水平度检查方法,(b)倾斜度检查方法,(c)垂直度检查方法
SUST
陶瓷窑炉与设计----第一章 隧道窑
在砌筑工作中有停歇时,不允许留垂直的缺口,应按图留 成阶梯或退台状。
墙体阶梯形退台砌筑方法
SUST
陶瓷窑炉与设计----第一章 隧道窑
炉墙为两种或两种以上砖砌筑:
每一种砌体必须单独砌筑,犹如一堵单墙。 内外墙互相咬砌的砌筑层
窑
名
焙烧卫生陶瓷明焰隧道窑 焙烧卫生陶瓷隔焰隧道窑 焙烧釉面砖素烧明焰隧道窑 焙烧釉面砖釉烧明焰隧道窑
焙烧锦砖明焰隧道窑
各带长度比例% 预热带 烧成带 冷却带 32~34 18~20 46~48 34~38 20~22 44~46 36~44 16~22 32~40 30~32 15~20 46~50 40~50 17~20 32~40
SUST
陶瓷窑炉与设计----第一章 隧道窑
窑顶用材料: 内衬耐火砖 中间隔热砖, 粉状或粒状 隔热材料之上,用一些粉状或粒状的材料填平上部, 硅藻土、粒状高炉矿渣,废碎耐火砖等 红砖 外表的整齐和便于人行走,上面平铺一层红砖。
SUST
陶瓷窑炉与设计----第一章 隧道窑 窑内温度在1300℃以下:
陶瓷窑炉与设计----第一章 隧道窑-结构
隧道焙烧窑烧成曲线

隧道焙烧窑烧成曲线隧道焙烧窑是一种应用广泛的烧成设备,主要用于陶瓷和建材行业的产品烧成。
隧道窑的烧成曲线对产品的质量、成色和耐用度有着重要的影响,因此烧成曲线的优化是提高窑炉生产效率和产品质量的关键之一。
隧道窑的烧成曲线一般包括升温段、保温段和冷却段三个阶段。
升温段是将窑内的温度逐渐升高到烧成温度,保温段是将产品保持在烧成温度一段时间,冷却段则是将产品从高温状态逐渐降温到室温。
在升温段,窑炉会逐渐升温到设定温度。
升温速度的选择很关键,如果升温过快,可能会导致产品内外温差过大,产生烧裂和变形,而升温过慢则会降低生产效率。
因此,升温速度需要根据具体产品的特性和窑炉的热处理能力进行调整。
保温段是使产品达到烧成温度,并保持一段时间以确保产品的烧结均匀。
保温时间的长度和保温温度的选择也对产品质量有着重要的影响。
保温时间过短,可能导致产品没有充分烧结,而过长则会浪费能源和降低生产效率。
保温温度的选择则取决于产品的成色要求和窑炉的热处理能力。
冷却段是将产品从高温状态逐渐冷却到室温。
冷却速度的选择很关键,过快的冷却速度可能会导致产品烧结不充分,而过慢的冷却速度则会延长生产周期。
因此,冷却速度需要根据产品的特性和窑炉的冷却能力进行调整。
除了升温段、保温段和冷却段外,隧道窑的烧成曲线还包括进料段和排料段。
进料段是将产品进入窑炉,而排料段是将烧成好的产品从窑炉中取出。
进料段和排料段的速度和时间也对产品质量有一定的影响。
优化隧道窑的烧成曲线可以通过多种方式实现。
首先,可以通过调整燃料与风量的配比和窑炉结构的改进来提高窑炉的热处理能力。
其次,可以通过优化控制系统和自动化设备来实现烧成过程的精准控制。
此外,还可以通过监测和调整烧成曲线中各个阶段的温度、时间和速度等参数来进一步改进烧成效果。
总之,隧道窑的烧成曲线是影响产品质量和生产效率的重要因素。
通过优化烧成曲线,可以提高产品的质量、成色和耐用度,实现陶瓷和建材行业的可持续发展。
隧道窑

电热推板窑
WDSJ-0.5/1000型电热升降窑
第四章
隧道窑
• 1、定义:采用轨道窑车输送制品的连续式窑炉 • 2、分类
• 3、隧道窑的特点:
按热源分
分类根据
窑 名
特
点
• 约200℃; 1. 明焰隧道窑 火焰直接进入隧道 • 2)产品冷却之热加热空气,可助燃或作干燥 介质, 按火焰是否 2. 隔焰隧道窑 火焰在马弗道内通过固体辐射传热 进入隧道分 • 产品出窑温度低; 3. 半隔焰隧道窑 隔焰马弗板开有小孔,部分火焰入窑 1. 窑车隧道窑 • 3)连续窑,窑体温度不变,不蓄热,热耗低。
按窑内运 输设备分 2. 3. 4. 5. 6. 推板隧道窑 辊道窑 输送带隧道窑 步进隧道窑 气垫隧道窑
1. 火焰隧道窑 以煤、油或煤气为燃料 1)利用烟气余热预热坯体,废气排出温度低, 2. 电热隧道窑 利用电热元件加热
按通道多少分
1. 单孔隧道窑 2. 多孔隧道窑
推板隧道窑
第一节
形状:普通砖 异型砖
三、不定型耐火材料
• • • • 耐火混凝土, 耐火泥, 耐火喷涂料, 耐火浇注料与捣打料
四、砌窑用隔热材料:λ < 0.14 W/m · ℃。
• • • • 1、轻质粘土砖 2、轻质高铝砖 3、高铝聚轻球砖 4、陶瓷纤维材料
隔热材料
• YK系列轻质隔热砖采用ASTM标准。 • AB系列氧化铝空心球砖是由氧化铝空心 球,氧化铝微粉添加复合结合剂,经振 动成型,高温烧成得制品。 用于1650℃以下工业窑炉炉衬材料。
棚板装烧
2)车架
• 铸铁车架:刚度大,变形小,抗氧化,节约钢材,造价低, • 型钢车架:轻便,易制造,成本高,易变形,铆接成型。
隧道窑温度控制系统设计(毕业设计)

目录摘要........................................................................................................................................... ABSTRACT . (I)绪论 01 玻璃隧道窑的发展状况 (1)1.1 玻璃窑的分类及构成 (1)1.2 玻璃窑温度控制的发展状况 (2)2 结构设计方案选择 (3)2.1 玻璃窑炉的工艺流程 (3)2.2 玻璃窑炉的动态特性 (4)2.3 隧窑系统的数学模型 (6)熔化部温度的理论数学模型 (6)冷却部温度的理论数学模型 (7)2.4 隧道窑温度控制系统的控制方案选择 (7)3 硬件设计 (8)3.1 温度检测电路 (10)3.2 信号处理电路 (11)3.3 A/D转换电路 (13)3.4 温度重置电路 (13)3.5 显示接口电路 (14)3.6 功率放大及执行电路 (14)4 软件设计 (15)4.1主程序模块 (15)4.2功能实现模块 (16)转换子程序 (16)中断服务子程序 (17)步进电机驱动程序 (19)4.3运算控制模块 (20)标度转换 (20)算法 (22)4.4抗干扰措施 (24)结束语 (25)参考文献 (26)附录1 总电路图 (27)附录2 主程序代码 (28)致谢 (32)摘要隧道窑是耐火材料生产中一种重要的高温烧成设备,是耐火材料生产过程中的重要环节,隧道窑的控制水平直接影响耐火材料的质量。
近年来,我国的耐火材料工业发展迅速,窑炉设计水平有显著的提高,但隧道窑的控制技术发展相对缓慢,大部分窑炉的控制还停留在常规仪表控制的水平上,自动化程度较低。
因此,进行隧道窑烧成制度尤其是温度制度控制方面的研究,对提高产品质量和稳定产品产量都非常重要。
本文首先介绍了隧道窑及其控制技术的发展和现状,然后以某玻璃厂的隧道窑的温度为控制对象,设计一个温度控制系统,介绍了玻璃窑炉的结构、工艺流程以及生产对温度控制系统的要求,分析了窑炉温度系统的动态特性。
【doc】隧道窑快速烧成卫生洁具

隧道窑快速烧成卫生洁具佛山陶瓷,FOSHANCERAMICS1996箜兰塑箜隧道窑快速烧成卫生洁具周正付姚晓华—一一…,_一一了r,I6(石湾建华陶瓷厂佛山市陶瓷研究所测试中心528o3¨7『7一bt111~-本文在实验的基础上,对隧道窑烧成曲线各温度阶段作了详尽的分析,给出了一快速'jh,菱,关键词烧成曲线,差热分析,热膨胀,烧成周期r÷f=f-——一一一一一I,',一~u,}Ll【,\'逮J,1前言众所周知,隧道窑由于其窑车蓄热大,影响了升温速度,又由于窑炉横截面温差比较大,因而在烧制大件产品如卫生洁具时,烧成周期比较长(约20小时),鉴于此,国内很多厂家着手引进了国外先进的隧道窑来烧成卫生洁具,这些引进的隧道窑烧成截面积虽然较大,但由于采用了高速等温喷嘴,火焰长因而烧成截面上,下温差较小,可以控制在±10℃以内,有些隧道窑甚至采用全自动控温,计算机监控,所以烧成制度尤其是窑内温差更易控制和调整.如何利用这些先进的隧道窑快速烧成卫生洁具,在保证产品质量的前提下提高产量,成为卫生洁具厂家迫切需要解决的问题.针对这种情况,我们利用先进的卫生陶瓷生产专用实验仪器,分析了卫生陶瓷坯体和釉料在整个烧成过程中的各种性能变化,依据这些实验结果,对某一引进隧道窑的烧成曲线进行分析比较,得出了一条较佳生产烧成曲线.2实验条件和内容本实验过程中,保持着浆料,釉料配方和性能的相对稳定,不作大的变动.表一是实验用坯体之化学成份分析结果.表1卫生洁具坯体化学成分Si02A12O3Fe203CaOMgOKNaOIL65.3g21,651.260.501.034.236.62其坯式为:0.248KNaO10.115MgO}0.038CaO10.966Al2O30034Fe2O3l494SiO2l本实验所进行之隧道窑总长94.5米,窑车宽2米,长1.5米,有效烧成高度为0.75米,窑车装车密度较大,平均为20—22件,窑内从预温带到烧成带共分布35对高速等温喷嘴.产品入窑前先入干燥室干燥, 图1是该隧道窑日进车次为75车时之温度曲线,该温度曲线烧成周期为20.5小时.在该温度曲线下烧成卫生洁具,产品的裂纹缺陷率为12%左右,当然,仅由于烧成所致产品裂纹缺陷率应低于12%,这是因为喷釉前后的洗坯,拉坯,装车过程中造成坯体入窑前已经出现了暗裂.变形缺陷率为2%左右,对于大件卫生洁具来说,变形所占百分比已较小.为了验证该温度曲线与大生产之浆料釉料配方的相适应性以及是否有潜力可挖,特做了大量有关实验,这些实验主要包括,浆料釉料以及其按适当比例混合后组成的混合粉料的差热分析实验(DTA),坯体及釉料的热膨胀系数测试实验( TE),坯体的不可逆热膨胀测试实验(ITE),坯釉适应性热应力测试以及入窑前坯体含水率的测试等.3实验结果与分析图2是综合实验分析结果所提出的烧成温度曲线,该温度曲线的烧成周期仅为16.8小时,使得日地车次可由原来的75车次提高到90车次,即每天可多增加15车次之多.每天所进车次计算方法如下:一天所进车次:24/16.8×63:90(车次)44佛山陶瓷FOSHANCERAMICS1996年第3期注:该隧道窑等内可容纳63部车,对图1,图2可以看出,烧成温度曲线以改进在于:(1)加快了在低温阶段的升温速度;(2)较大幅度地提高了降温速度,使得烧成总体降温时间由原来的近10小时缩短到7.5小时.下面将依据所进行的实验结果就该温度曲线具体论述.3.1升温阶段从室温到500℃这一阶段,主要是排除坯体内的吸附水,经过对各种规格坯体入窑水份的多次测试和实验,证明将坯体的水份控制在1.5%以内,有利于减少产品早期开裂和由于水份过多导致急速蒸发而产生的爆裂.由图3坯体差热分析,图4釉料差热分析及图5入窑前坯体(包含釉层,入窑水分1.596)差热分析结果看出,在50012以下,无明显的差热峰出出,这证明, 排除的机械吸附水并不多,而且应是逐步进行排除的, 由图6生坯不可逆膨胀曲线知,在温度500℃这一较低预温带温度范围内,坯体虽然有所膨胀,但膨胀幅度很小,曲线平缓,为均匀缓慢膨胀,因而可以在原来的基础上,加快升温速度.对比图1,图2两条温度曲线可以看出,改进后的温度曲线较大地提高了从室温至500℃这一温度段内的升温速度,以缩短整个烧成周期.在500℃一600*(2这个温度范围内,应减慢升温速度,缓慢升温,这一点,两条曲线一致,一是缓慢升温可以缓和一下前期快速升温所造成的大件产品的温差, 并缩小窑炉横断面上下温差,二是在该温度范围内,坯体,釉料等都发生了激烈反应,这可由图3,图4,图5的差热分析结果可知,在差热曲线上,560℃左右都出现了一强吸热峰,这主要是由于坯体中所含大量高岭石排除结构水生成编高岭石所致.另外,由图6所示的坯体不可逆膨胀曲线知,在此温度范围内,坯体的膨胀曲线陡然向上,表明此时坯体发生了较大体积膨胀,这可能是由于坯体中石英所发生的晶型转变引起的,因为坯体中SiO含量高达65% 以上,坯体配方中单独所加石英原料在10%以上.在573℃时8一石英转变为a一石英有0.82%的体积膨胀,虽然这时体膨胀不是很大,但因其转化迅速,又是在干燥条件下进行,破坏性强,因此在此温度范围内应缓慢升温..600℃以上至高温烧成,图1,图2相差不多都是以120℃/小时左右的升温度进行升温.在这一温度范围内,坯体,釉料都曾发生了较大变化,由差热分析图可知(如图4),釉料在830℃附出现一强吸热峰,这是因为釉料为长石一石灰釉,釉料中一些碳酸盐等化合物发生剧烈分解吸热所致.在这一温度范围内应控制稍缓升温,以便有时间让这些化合物充分分解,放出气体,从而减少产品针孔,提高产品釉面质量,另外,坯体,釉料中的碳素,有机物(如坯体黑泥中所含大量的碳素,有机物,釉料添加剂羧甲基纤维素钠,腐植酸钠等) 应于釉层熔融坯体气孔封闭前排除干净,以防形成烟熏,气泡,冲孔等缺陷,碳酸盐,硫酸盐等所分解的产物(CO或SO气体)都应在氧化阶段充分逸出,否则,在坯体气孔封闭以后坯内仍有气体排出来,将引起坯体的起泡.另外由图3,图5的差热分析曲线知,坯体及坯体包含釉层都在920℃一1000℃温度范围内出现较大放热峰,最高峰在97012左右,这是由于坯体中已生成的偏高岭石转化为尖晶石型的新结构所引起的,是形成一次莫来石的先兆.由图6知,在920℃左右,坯体的热膨胀曲线发生突变,由原来的热膨胀转变为收缩,且在105012附近至烧成最高温度,坯体发生急剧收缩这是由于坯体中所含长石等原料发生熔融,坯体中的玻璃相逐渐增多,结晶颗料由于表面张力而互相靠拢,因而收缩逐渐加剧, 但由于在这一温度范围内,坯体的热塑性显着增加,其抵抗破坏能力增强,所以升温速度可以适量提高.3.2保温阶段保温温度为1220℃,保温时间1小时左右,此保温时间的确定是参考图1所示之烧成曲线的保温时间来定的.因为大生产及本实验中,在该保温温度及保温时间下,坯体及釉层中各组分充分反应,其烧成后产品的吸水率很低(0.5%以下)因而该烧成最高温度1220℃, 保温时间1小时左右对于现时的浆料,釉料配方来说是比较合适的.3.3降温阶段对比图1,图2,会发现,改进后之烧成曲线加快了降温速度,首先在急冷阶段,降低了急冷温度点,图1原烧成曲线中从最高温度急速冷却至850℃左右,改进后的烧成曲线(见图2)急冷温度定为750℃左右,降低了近100℃由图七坯釉之间热应力的测试结果表明在800℃以上,坯釉之间相互内热应力很少.从最高温急冷,坯体中存在较多液相,高温下的热应力大部分可为液相的弹性和流变性所吸收.另外,通过对釉的玻化温度测试(测试结果见表2)表明,釉的玻化温度点在750 ℃左右.因此可以断定坯釉之间在750℃温度以上几乎不存在相互的内应力作用,因而从最高温急速冷却至750℃左右不会在坯体内产生有危害的内应力,坯釉之间也不会产生导致产品破坏的热应力.在750℃一600佛山陶瓷FOSHANCERAMICS鱼生箜兰塑兰℃温度范围内,缓冷,冷却速度为每小时60℃左右,这是因为此温度范围内,釉已玻化变脆而且瓷眙内液相业已固化.坯,釉之间热膨胀相差较大,釉)坯,如图8坯体釉料膨胀曲线所示,因而随着温度的降低釉层昕受的拉应力急剧增大,如图7坯釉之间热应力测试曲线所示,并且至620℃左右釉层所受拉应力达最大状态,如果在此温度范围内降温速度过快则会造成坯釉之间强大的热应力作用导至釉层被拉裂,因而需严格控制降温速度,缓慢冷却.600℃一550℃温度范围内,应更进一步缓冷.随着温度的降低,如图8坯体釉料热膨胀曲线所示,釉的热膨胀在此温度酸内减小的幅度度大过坯体,因而釉层所受的拉应力逐渐减小,即坯釉之间热应力作用减缓,图7的坯釉热应力曲线反应出了这一点,但由于石英在573℃发生晶型转变而使坯体体积急剧收缩,见图8中坯体的热膨胀曲线,在573 ℃附近,坯体的热膨胀曲线出现转折,急剧回落,另外, 经测试坯体在550℃一600℃温度范围内,其平均膨胀系数,如表2中所示,竟高达(11.0—13.50)×10/℃,因而在这一温度范围内应严格控制缓冷,以防产品出现"惊裂".在500℃以下,改进的温度曲线加快了降温速度,由图7,图8知,在此温度下,坯体与釉的热膨胀曲线趋于一致,几乎为平行线,坯体与釉的膨胀系数相差很小,如表2,坯与釉相差小于1.0×10/℃,坯釉之间的热应力小而平缓,釉层几乎受一较小而恒定的应力作用,从拉应力向压应力过渡,在420℃左右,发生转变.釉层由受一较小拉应力作用转变为受一较小压应墨t(Ⅵ图113进75车次时烧成温度曲线力作用一直到完全冷却,因而在此低温阶段fJⅡ快冷却不令造成产品开裂.200℃以下,产品出窑,在空气中自然冷却,但在冬天要防止过冷风直接吹向产品,造成" 风惊".4结论综上昕述,改进后的烧成曲线,由于其建立在一定的实验基础及实践经验之上,因而具有较好的合理性与可靠性,采用该烧成曲线烧成大件卫生洁具产品,不但能加快进车速度,增加产量,而且会在某种程度上提高产品的釉面质量,从而能大大增加企业的经济效益,当然,由于窑炉本身结构的影响以及窑炉温度梯度的连续性,不可能完全按该烧成制度进行烧成,但各窑炉的具体调试及细节问题可以此烧成曲线为基础参照执行.参考文献1陶瓷工艺学,轻工业出版社:55—612刘康时等编着.陶瓷工艺原理,华南理工大学出版社:123—125表二,坯体,釉料的膨胀系数以及釉料的玻化温度~原料坯体1坯体2杏釉玛瑙红釉100—5506.497.50'5.786.90550—60011.2013.509008.40玻化温度【℃】~720——750图2日进90车次时烧温度曲线46佛山陶瓷旦堕1996年第3期图3坯体粉料差热分析疗肋图5生坯(包括釉层.入窑前水份为1.7%)差热分析图7坯釉之间热应力测试图4釉料粉差热分析图6生坯不可逆膨胀曲线图8坯体,釉料膨胀曲线。
自然条件下长大公路隧道内温度变化分析
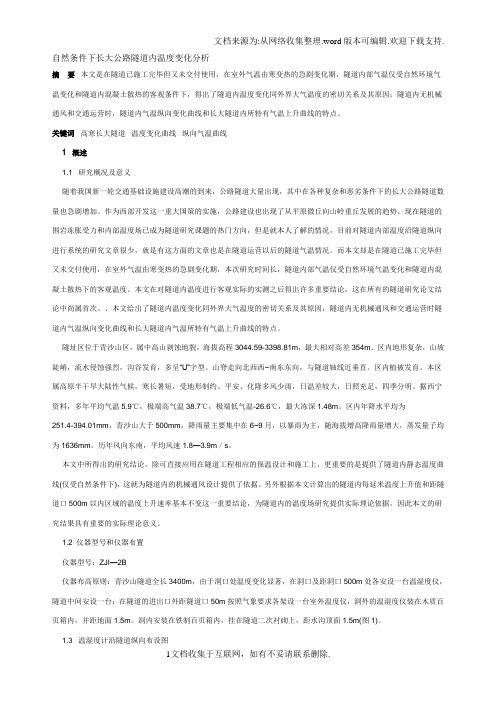
自然条件下长大公路隧道内温度变化分析摘要本文是在隧道已施工完毕但又未交付使用,在室外气温由寒变热的急剧变化期,隧道内部气温仅受自然环境气温变化和隧道内混凝土散热的客观条件下,得出了隧道内温度变化同外界大气温度的密切关系及其原因;隧道内无机械通风和交通运营时,隧道内气温纵向变化曲线和长大隧道内所特有气温上升曲线的特点。
关键词高寒长大隧道温度变化曲线纵向气温曲线1 概述1.1 研究概况及意义随着我国新一轮交通基础设施建设高潮的到来,公路隧道大量出现,其中在各种复杂和恶劣条件下的长大公路隧道数量也急剧增加。
作为西部开发这一重大国策的实施,公路建设也出现了从平原微丘向山岭重丘发展的趋势。
现在隧道的围岩冻胀受力和内部温度场已成为隧道研究课题的热门方向,但是就本人了解的情况,目前对隧道内部温度沿隧道纵向进行系统的研究文章很少,就是有这方面的文章也是在隧道运营以后的隧道气温情况。
而本文却是在隧道已施工完毕但又未交付使用,在室外气温由寒变热的急剧变化期,本次研究时间长,隧道内部气温仅受自然环境气温变化和隧道内混凝土散热下的客观温度。
本文在对隧道内温度进行客观实际的实测之后得出许多重要结论,这在所有的隧道研究论文结论中尚属首次。
、本文给出了隧道内温度变化同外界大气温度的密切关系及其原因,隧道内无机械通风和交通运营时隧道内气温纵向变化曲线和长大隧道内气温所特有气温上升曲线的特点。
隧址区位于青沙山区,属中高山剥蚀地貌,海拔高程3044.59-3398.81m,最大相对高差354m。
区内地形复杂,山坡陡峭,流水侵蚀强烈,沟谷发育,多呈“U”字型。
山脊走向北西西~南东东向,与隧道轴线近垂直。
区内植被发育。
本区属高原半干旱大陆性气候,寒长暑短,受地形制约。
平安、化隆多风少雨,日温差较大,日照充足,四季分明。
据西宁资料,多年平均气温5.9℃,极端高气温38.7℃,极端低气温-26.6℃,最大冻深1.48m。
区内年降水平均为251.4-394.01mm,青沙山大于500mm,降雨量主要集中在6~9月,以暴雨为主,随海拔增高降雨量增大,蒸发量子均为1636mm。
隧道窑的烘调方法
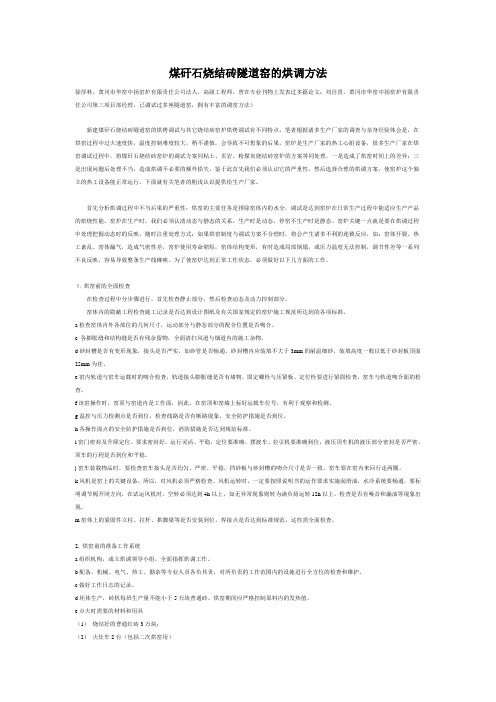
煤矸石烧结砖隧道窑的烘调方法徐厚林,黄冈市华窑中扬窑炉有限责任公司法人,高级工程师,曾在专业刊物上发表过多篇论文;刘自贵,黄冈市华窑中扬窑炉有限责任公司第三项目部经理,已调试过多座隧道窑,拥有丰富的调窑方法)新建煤矸石烧结砖隧道窑的烘烤调试与其它烧结砖窑炉烘烤调试有不同特点。
笔者根据诸多生产厂家的调查与亲身经验体会是,在烘窑过程中过火速度快,温度控制难度较大,稍不谨慎,会导致不可想象的后果。
窑炉是生产厂家的热工心脏设备,很多生产厂家在烘窑调试过程中,将煤矸石烧结砖窑炉的调试方案同粘土、页岩、粉煤灰烧结砖窑炉的方案等同处理,一是造成了烘窑时间上的差异;三是出现问题后处理不当,造成烘调不必要的额外损失。
鉴于此首先我们必须认识它的严重性,然后选择合理的烘调方案,使窑炉这个独立的热工设备能正常运行。
下面就有关笔者的粗浅认识提供给生产厂家。
首先分析烘调过程中不当后果的严重性:烘窑的主要任务是排除窑体内的水分,调试是达到窑炉在日常生产过程中能适应生产产品的焙烧性能。
窑炉在生产时,我们必须认清动态与静态的关系,生产时是动态,停窑不生产时是静态。
窑炉关键一点就是要在烘调过程中处理把握动态时的反映,随时注重处理方式;如果烘窑制度与调试方案不合理时,将会产生诸多不利的连锁反应,如:窑体开裂、热工紊乱、窑体漏气,造成气密性差,窑炉使用寿命缩短,窑体结构变形,有时造成局部倒塌,或压力温度无法控制,调节性差等一系列不良反映,容易导致整条生产线瘫痪。
为了使窑炉达到正常工作状态,必须做好以下几方面的工作。
⒈烘窑前的全面检查在检查过程中分步骤进行,首先检查静止部分,然后检查动态及动力控制部分。
窑体内的隐蔽工程检查施工记录是否达到设计图纸及有关国家规定的窑炉施工规范所达到的各项标准。
a检查窑体内外各部位的几何尺寸,运动部分与静态部分的配合位置是否吻合。
c 各膨胀缝和结构缝是否有残余留物,全面清扫风道与烟道内的施工杂物。
d砂封槽是否有变形现象,接头是否严实,加砂管是否畅通,砂封槽内应装填不大于3mm的耐温细砂,装填高度一般以低于砂封板顶面25mm为佳。
隧道窑与辊道窑

排
气引向支烟道
烟 支烟道:引导来自排烟口的排出废气进入主烟道
通
风
主烟道:汇总各支烟道的烟气,并将其引入烟囱
系
统
烟囱:将来自主烟道的废气送入高层大气空,减少废气
对工作环境的污染
注:排烟口、支烟道、主烟道的布置应避免急剧转弯,保证尽量减小废
气的流动阻力损失,使废气在烟道内顺利排出。
10
4、隧道窑燃烧系统:(分布在烧成带) 燃料的使用:
目的:窑头形成1~2Pa的微正压, 避免了冷空气漏入窑内。
设为两道: 第一道:用冷空气 第二道:用热空气
将气体以一定的速度自窑顶及 两侧墙喷入,成为一道气帘,
该热空气一般是抽车下 热风或冷却带热风。
气幕气体送入方式:1)与窑车运动方向相垂直 2)与出车方向成45℃
15
扰动气幕:
位于预热带,一般设置2-3道扰动气幕 工作过程:以一定量的热气体以较大的流速和一定的角
如果窑内的负压过大,则漏入的冷空气必然多,会使窑内 的温度降低,且气体分层严重,窑内断面上的上、下温度差加 大;同时会使烧还原气氛时,窑内的烧成带难以维持还原气氛 。所以负压大的窑就是操作不好的窑。
如果窑内的正压过大,则大量热气体会向外界冒出,这 样既损失了热量,也恶化操作人员的劳动环境。窑内的热气体 冒入车下的坑道还会烧毁窑车的金属构件,造成操作事故。 最理想的压强控制操作是将窑内维持为零压,但是办不到。只 能将窑内的关键部位——烧成带与预热带的交界面附近维持在 零压左右。
1
一、隧道窑分类:
分类根据
按隧道窑所用的热源 按火焰是否进入隧道窑 按隧道窑内运输设备来分 按隧道窑的使用 用途 按隧道窑内的通道数目
按隧道窑内的烧 成温度
- 1、下载文档前请自行甄别文档内容的完整性,平台不提供额外的编辑、内容补充、找答案等附加服务。
- 2、"仅部分预览"的文档,不可在线预览部分如存在完整性等问题,可反馈申请退款(可完整预览的文档不适用该条件!)。
- 3、如文档侵犯您的权益,请联系客服反馈,我们会尽快为您处理(人工客服工作时间:9:00-18:30)。
南
10:20
北 南
备注
2013年4月13日进车65分钟,保温8小时40分,一类点5个,二类点4个。
3#窑烧结硅质抽查温度曲线
时间 车位 烧咀 东
8:30
55# 1
56# 2
57# 3
58# 4
59# 5
60# 6
61# 7
62# 8
63# 9
64# 10
65# 11
66# 12
1405 1435 1445 1445 1450 1445 1435 1435 1450 1445 1450 1425 1415 1440 1455 1445 1445 1450 1445 1455 1455 1455 1445 1425 1400 1420 1430 1420 1420 1430 1425 1430 1420 1430 1425 1385 1390 1410 1420 1430 1425 1430 1435 1425 1435 1425 1420 1400
1#窑烧结硅质抽查温度曲线
时间 车位 50# 烧咀 北
10:00
51# 8
52# 9
53# 10
54# 11
55# 12
56# 13
57# 14
58# 15
59# 16
60# 17
61# 18
62# 19
63# 20
64# 21
65# 22
66# 23
67# 24
68# 25
7
1406 1438 1444 1448 1446 1444 1443 1439 1433 1437 1454 1456 1453 1447 1450 1438 1423 1418 1383 1415 1443 1442 1442 1445 1442 1439 1444 1440 1430 1438 1449 1461 1443 1427 1415 1438 1445 1355 1413 1426 1452 1457 1447 1438 1440 1444 1435 1437 1454 1438 1452 1452 1449 1436 1419 1430 1379 1434 1458 1444 1442 1441 1447 1441 1447 1445 1430 1437 1450 1455 1442 1430 1415 1435 1436 1335
抽测 抽测
西 东
9:00
西
2013年4月26日进车120分钟,保温22小时,一类点6个,出窑后产品尺寸+1占15%,+0占40%,-1以下占25%%。 2013年4月26日
抽测 抽测
西 东
9:30
西
2013年4月26日进车120分钟,保温22小时,一类点6个,二类点5个,出窑后产品尺寸+1占15%,+0占40%,-1以下占25%% 。
4#窑烧结硅质抽查温度曲线
时间 车位 烧咀 东
8:00
55# 1
57# 2
59# 3
61# 4
63# 5
66# 6
67# 7
1420 1440 1445 1450 1445 1440 1350 1425 1445 1450 1440 1440 1435 1360 1448 1433 1453 1454 1437 1414 1435 1453 1457 1450 1438 1446
抽测 抽测
南 北
10:20
南
备注
2013年4月13日进车90分钟,保温27小时,一类点6个,二类点8个,出窑后产品尺寸+1占15%-20%,+0占40%,-1以 下占15%-20%。
2#窑烧结粘土抽查温度曲线
时间 车位 烧咀 北
10:00
Hale Waihona Puke 24# 225# 3
26# 4
27# 5
28# 6
29# 7
30# 8
31# 9
32# 10
33# 11
34# 12
35# 13
1373 1388 1396 1407 1411 1409 1414 1414 1410 1404 1385 1305 1382 1398 1405 1409 1416 1420 1418 1417 1412 1410 1392 1310 1383 1389 1407 1396 1402 1406 1404 1407 1394 1394 1391 1292 1368 1397 1385 1405 1407 1419 1421 1428 1435 1419 1407 1303