微切片制作
微切片制作-(四)微蚀算老几

微切片XXX(四)1.4 微蚀算老几微切片之XXX经仔细抛光后,即需进行小心的微蚀,如此方可使各种金属层次得以清楚的界分开来。
通常微蚀液会因不同金属而有不同的配方,针对铜金属而言,起最理想的配方是“稀氨水+双氧水”(体积比3-10%氨水约300cc,再加上新鲜有效的双氧水2-3滴即可。
早期所用稀硫酸加铬酸的配方,其效果没有氨水法来的好)。
配方虽然有了,要注意有是正确的使用才能呈现出应有的效果。
以下即为笔者多年来的一些实务心得,特据以实报分享读者:1、此种微蚀液一定要用纯水或蒸馏水去配制,不可用含有杂质的自来水,因在00-500X高倍显微镜下,任何不良的蚀液都会造成细部效果的失佳。
不信您可实地加以比较,一试便知真假。
2、所配微蚀液之量不可太多,以30-50cc为宜,因其寿命仅约1-2小时而已。
一旦放置太久双氧水将会失效,此时虽可再加1-2滴做为补充,但效果并没有新配液来的好。
且用过的棉花棒也不可重用,以全新者为宜。
3、抛光面上经微蚀液擦抹后,其铜面将迅速产生微小气泡,此即表示反应已在进行。
来回擦蚀约1-3秒钟后,应立即用卫生纸迅速擦干试净,之后可做显微观察,若效果不足时,再用新棉花棒继续吸液擦抹。
4、若PTH孔样中已有填锡时,由于贾凡尼效应的缘故,会使得铜结晶不易被咬出来。
须改采较低浓度微蚀液及较长时间去小心擦咬,否则铜面很容易过度氧化而变红变暗。
一旦如此则只好再重行抛光及微蚀了。
5、其他金属之微蚀液并无定论,专书中虽曾列有多种配方,但均需实做以找出可行之道,此处不再祥述。
图1.此放大500倍之二图。
左图为尚未微蚀之孔环与孔壁互连画面,只看到模糊的概略影像,分不清孔壁与孔环之铜层组织。
右为同一孔样在6-8%稀氨水约三秒钟的微蚀后,即可见到清晰的画面,二者几有天壤之别。
图2.此为同一孔样同位置处放大200倍之切片,其微蚀前后有判若两人的感觉,连各铜层的厚度也出现真假不同的对比。
至于环壁之间未能除尽的胶渣,更令人有大小不同的感受,由此可知微蚀的重要性。
微切片手册

第二部分:切片的制作程序
&研磨:
1.打开研磨机电源,并调节转速钮 2.在研磨过程中需加入适当之水量帮助研磨。 3.用150目砂纸,将观察孔研磨至孔邊。 4.用600目砂纸,将观察孔研磨至约1/4处。 5.用1200目砂纸,将观察孔研磨至约1/3处。 6.用2000目砂纸,将观察孔研磨至约1/2处。 7.研磨方向应与切片成45角,并不断以90旋转,以确保切片表面完全 研磨。 8.研磨时用力应均匀,防止磨偏。禁止用力过度,导致切片与压克力 胶分裂。 9.在接近孔中心时,应注意防止过磨,检查有无喇叭孔、磨偏及研磨不 够等缺陷
第四部分:導同孔常見異常及允收標准 &.除胶渣不良
圖示一 圖示二 不允收/钻孔时钻针与板材强力摩擦所产生的温度甚高,故所累积的热量常使得 孔壁瞬间温度高达200℃以上,如此一来不免使得部份树脂被软化而成为胶糊, 随着钻针的旋转而涂满孔壁,各内孔环的內層铜面也自不能幸免,冷却后变成胶 渣導致PTH后殘膠不能除盡
自動取樣機
手動取樣機
第二部分:切片的制作程序 &封胶:
1.将沖切下來的切片试样用吹风机吹干,并卡于灌胶模内(或以双面胶将 切片研磨边固定于塑料灌胶模内),竖直固定。 2.将压克力粉与硬化剂(约1:1)调和均匀,缓慢注入灌胶模,并检视无气 泡后,自然固化约15分钟。 注意事项: 1.若切片孔内存有气泡,则用棉花棒沿切片边缘来回移动,直至赶出气 泡为止。 2.固化时间必须充足,否则研磨时,会导致切片与压克力胶分裂。
B
第七部分:切孔的判讀
項目 允收規格及說明 圖片說明
粗糙度
≦1.2mil
回蝕
0.2-3 mil
第七部分:切孔的判讀
項目 允收規格及說明 圖片說明
PCB微切片制作及缺点判读简介

3. 切片判断
3.13 回蚀(Etc back) 针对孔璧内层铜环上下对其介电层加以移除而退回之部分,铜孔壁与突 出内层孔环形成三面包夹结合, 但如过度回蚀造成孔壁粗糙也会导致应 力断裂可能
20 of 26
3. 切片判断
3.11 金属层与通孔孔壁的介电层间距
IPC:金属层自孔壁退后形成导体 间距>0.1mm或优于采购文件
21 of 26
3. 切片判断
3.12 灯芯效应(Wicking)
通常是结合力不好或者是钻孔等导致玻纤之间结合不 好,电镀时,药水渗入,形成灯芯状。
IPC:渗铜未超过0.1mm
15 of 26
3. 切片判断
3.6 孔铜完整性 有否镀瘤(Nodule), 夹杂物(Inclusion)孔口铜层结晶情形
IPC:不影响孔径
16 of 26
3. 切片判断
3.7 破洞(孔破)
一个切片只允许有三个破洞出现,破洞是焊锡时吹孔(Blow Hole) 最大原因,另外,会导致产品导致严重的失效。
IPC:1. 不可超过3个破洞 2. 大小未超过总板厚5% 3. 内层孔环与孔璧互连 接口不可出现镀层破洞 4. 破洞</=1/4圆周
NG
OK
17 of 26
3. 切片判断
3.8 钻孔品质 孔壁是否有孔壁粗糙及挖破情形
厂规:<1.4mil IPC:粗糙未降低孔铜 且孔径符合规格
18 of 26
3. 切片判断
9 of 26
2. 切片制作技巧
2.5 微蚀(micro-etch) 空板通孔直切切片一般可看到现象有 to layer registration)、孔环(Annular板材结构、孔铜厚度、孔铜 完整情形、破洞(VOID)、流锡情形、钻孔对准及层间对准(layer ring)、蚀刻情形、胶渣(Smear)情形、叠构及钻孔情形等
金相切片

微切片制作(十三)1.13 孔壁怎粗糙这是业界非常流行的一种说法,笔者时常被问到国际规范对孔壁粗糙是如何检验及允收的。
甚至有很多人以话传话,认为规范中允收的上限是1mil,事实上这全是子虚乌有的传说。
著名的各国际规范中均从未提到过Hole Roughness一词,只有孔铜破洞(Voids)或孔铜厚度不足等。
当然某些供需双方所自行订定的规范则不在此限,且其优先程度也高过国际规范。
"孔壁粗糙"当然是来自钻孔的不良,其中又以钻针情况不佳为主因。
说的更仔细一点,那就是针尖上两个第一面(First Facet)的切削前缘(Cutting Lips)出现崩破(Chipping),无法顺利切削玻璃束所致。
或针尖外侧两刃角(Corner)崩损磨圆,失去原来直角修整孔壁的功能。
于是在破烂刀具的又劈又撞情形下,经常会把迎面而来的纵向玻织束撞成破裂陷落的坑洞,不过横向撞折断者则尚可维持平坦。
下附各图中读者可清楚的看到其孔壁放大的细部情形。
图1 迎面而来纵向纱束被劈散成坑的详情(注意:此切片在采样切板时,剪裁落点太靠近孔体,以致造成内层孔环铜箔被严重拉扯弯曲变形的画面,此样已完成PTH与一次铜,故起伏落差情形更为夸张明显)。
图2 此为六层板之全层通孔,各铜箔内环已明显出现钉头(Nail Heading),并有玻织束被挖破的画面,但这种孔壁钻破与钉头之间似乎并无必然的关系。
注意:切片制作时的灌胶一定要小心,不但一定要填满而且烘烤硬化时也不可太急,以防胶内产生空洞。
如此不但画面不美且还会影响到孔铜厚度的观察与细部真相。
图3 孔壁上虽已出现一个挖破之凹陷,不过铜箔内环并无明显的钉头。
图4 过度钉头几乎一定会出现较大的挖破,出自钻孔的纵向玻璃纱束之挖破,除与钻针尖部的"刃角"损耗有密切关系外,也与钻针的偏转(Run Out)或摇摆(Wobble)有关。
此图可清楚见到钉头已远超过允收规格(钉头宽度不可超过铜箔厚度的1.5倍)。
PCB微切片

明视200X之斜 切片
暗视200X之斜 切片
三、制作技巧
微切片需填胶抛光与微蚀,才能看清各种真实品质.以下为 制作过程的重点:
1、取 样(Sample culling)
剥膜及蚀刻后尚未熔锡之画面,其二铜与锡铅之横 向扩镀
网印负片法熔锡后的切片
由圖可以看出二铜镀得特别厚,不但超越 油墨而且还侧爬颇远 ,孔环外缘截面呈现缺口
2、干 膜 阻 剂
此200X画面的油墨阻剂(如同墙壁)出现 异常,致使二次铜一开始往墙外恻向伸出, 有了镀铜层在非导体表面建立基地,锡铅镀 层当然就毫不客气顺理成章的成长,其结果 不免造成板子的报废。
各种直接电镀法),即全板镀铜直到完成孔壁铜厚之要求随即以 干膜进行盖孔式(Tenting)的影像转移,再直接蚀刻 .
4.1.2孔銅完整情形 1.銅瘤
是否有銅瘤(Nodule)夾雜物(Inclusion)孔口之階梯式鍍層 (Step plating)及銅層結晶情形.
一銅鍍銅不均形 成的铜瘤
鑽孔毛刺造成,鍍一銅時, 形成的瘤狀
膠渣會影響孔环与铜壁的互连 IPC-6012对此明文规定:过份除胶渣所造成的回蚀深度的不可超
过1mil。
内层孔环与孔壁之间有未除尽的残余胶渣
镀上的铜壁又被拉开的情形
一面镀一面不断被拉开的情形
重铬酸过镀除胶渣造成孔 壁表面的树脂全部溶出, 其缩陷造成断点整齐的玻 纤束突出
除膠渣良好圖片
未做除胶渣的双面板孔铜壁 经喷锡后退即出现了罕见的 严重拉离(Pull Away)
二、分类
电路板解剖式的破坏性微切法,大体上可分为三类: 1、 微 切 片
显微镜标本切片的制作方法
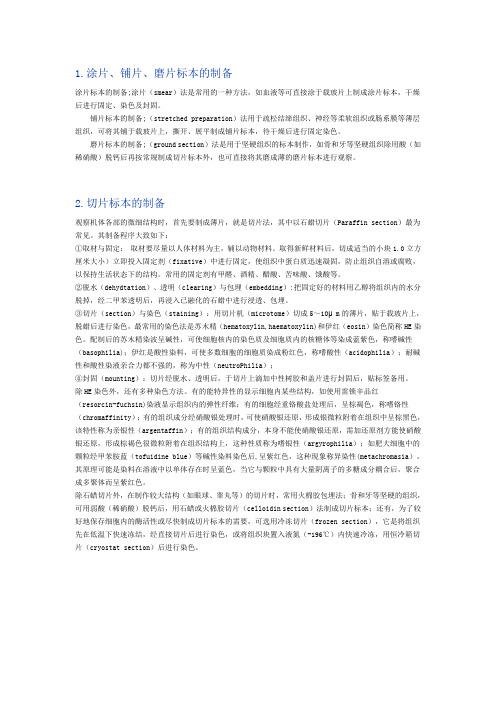
1.涂片、铺片、磨片标本的制备涂片标本的制备;涂片(smear)法是常用的一种方法,如血液等可直接涂于载玻片上制成涂片标本,干燥后进行固定、染色及封固。
铺片标本的制备;(stretched preparation)法用于疏松结缔组织、神经等柔软组织或肠系膜等薄层组织,可将其铺于载玻片上,撕开、展平制成铺片标本,待干燥后进行固定染色。
磨片标本的制备;(ground section)法是用于坚硬组织的标本制作,如骨和牙等坚硬组织除用酸(如稀硝酸)脱钙后再按常规制成切片标本外,也可直接将其磨成薄的磨片标本进行观察。
2.切片标本的制备观察机体各部的微细结构时,首先要制成薄片,就是切片法,其中以石蜡切片(Paraffin section)最为常见。
其制备程序大致如下:①取材与固定:取材要尽量以人体材料为主,辅以动物材料。
取得新鲜材料后,切成适当的小块1.0立方厘米大小)立即投入固定剂(fixative)中进行固定,使组织中蛋白质迅速凝固,防止组织自溶或腐败,以保持生活状态下的结构。
常用的固定剂有甲醛、酒精、醋酸、苦味酸、饿酸等。
②脱水(dehydtation)、透明(clearing)与包埋(embedding):把固定好的材料用乙醇将组织内的水分脱掉,经二甲苯透明后,再浸入已融化的石蜡中进行浸透、包埋。
③切片(section)与染色(staining):用切片机(microtome)切成5~10μm的薄片,贴于载玻片上,脱蜡后进行染色,最常用的染色法是苏木精(hematoxylin,haematoxylin)和伊红(eosin)染色简称HE染色。
配制后的苏木精染波呈碱性,可使细胞核内的染色质及细胞质内的核糖体等染成蓝紫色,称嗜碱性(basophilia);伊红是酸性染料,可使多数细胞的细胞质染成粉红色,称嗜酸性(acidophilia);耐碱性和酸性染液亲合力都不强的,称为中性(neutroPhilia);④封固(mounting):切片经脱水、透明后,于切片上滴加中性树胶和盖片进行封固后,贴标签备用。
PCB微切片手工制作

研 磨 、 抛 光 。 I C标 准 上 要 求 用 P
美 制 1 20或 1 ≠ 2 80≠、 40≠、 32 、 ≠ 0
4 0≠ 6 0 0 ≠ 和 0 N目 数 砂 纸 逐 步 进 行 研
磨 ( 图 2), 然 后 用 6 m、 1 如 到 0. 05 图 l 垂 直 切 片 , 要 求 磨 到 孔 中 心 位 a 置 ( 般 允 许 1% 差 ) 以观 察铜 — O偏 , 厚 ,介 电层 厚 和 其他 参 数 或缺 陷 图1 b水 平 切 片 , 一 般 用 来 观 察 孔 的 钻 孔 对 位 , 孔 径 和 内 层 铜 的 连 接 状 况 等 m
I PC— TM 一 650 T estMet od Man h ua1 ti cl .I n udes t at i s.not he m eral es and eval i orM i osec i so uaton f cr ton al K ey or w ds: PCB; Tes i abor or Mi os tng l at y; cr ect i on
对 多 板 品 质 控 与 工 程 改 善 , 倒 是 一 种 花 费 不 多 却 收 获 颇 大 的
21 镀 通 孔 、研 磨 .
P C B做 得 最 多 的 为 镀 通 孑 L
P TH ( at P1 ed ThIough Ho1es)的 F
选 用 . 烯 酸 树 脂 ( c 1j ) 环 内 A y , r C 氧 树 脂 ( P y E ox )或 不 饱 和 聚 酯 树
2 制 作 过程 .
微 切 片 制 作 一 般 步 骤 为 : 取 样 ( SamPl cutting)、 封 胶 e
( ncaPsu1 Resjn E atio n) 、 研 磨
pcb微切片制作及不良分析

p c b微切片制作及不良分析(总12页)-CAL-FENGHAI.-(YICAI)-Company One1-CAL-本页仅作为文档封面,使用请直接删除微切片制作(一)一、概述电路板品质的好坏、问题的发生与解决、制程改进的评估,在都需要微切片做为客观检查、研究与判断的根据(Microsectioning此字才是名词,一般人常说的Microsection是动词,当成名词并不正确)。
微切片做的好不好真不真,与研判的正确与否大有关系焉。
一般生产线为监视(Monitoring)制程的变异,或出货时之品质保证,常需制作多量的切片。
次等常规作品多半是在匆忙几经验不足情况下所赶出来的,故顶多只能看到真相的七、八成而已。
甚至更多缺乏正确指导与客观比较不足下,连一半的实情都看不到。
其等含糊不清的影像中,到底能看出什么来这样的切片又有什么意义若只是为了应付公事当然不在话下。
然而若确想改善品质彻底找出症结解决问题者,则必须仔细做好切取、研磨、抛光及微蚀,甚至摄影等功夫,才会有清晰可看的微切片画面,也才不致误导误判。
二、分类电路板解剖式的破坏性微切法,大体上可分为三类:1、微切片系指通孔区或其他板材区,经截取切样灌满封胶后,封垂直于板面方向所做的纵断面切片(Vertical Section),或对通孔做横断面之水平切片(Horizontal section),都是一般常见的微切片。
图1.左为200X之通孔直立纵断面切片,右为100X通孔横断面水平切片。
若以孔与环之对准度而言,纵断面上只能看到一点,但横断面却只可看到全貌的破环。
2、微切孔是小心用钻石锯片将一排待件通孔自正中央直立剖成两半,或用砂纸将一排通孔垂直纵向磨去一般,将此等不封胶直接切到的半壁的通孔,置于20X~40X的立体显微镜下(或称实体显微镜),在全视野下观察剩余半壁的整体情况。
此时若另将通孔的背后板材也磨到很薄时,则其半透明底材的半孔,还可进行背光法(Back Light)检查其最初孔铜层的敷盖情形。
PCB板微切片制作钉头问题分析

题。 产生钉头的劣质钻针,其额外的发热与粗鲁的拉扯动作,会减弱黑化层与树脂的接著力,
进而出现细缝引入空气,又在毛细作用下促使含稀硫酸的酸性镀铜槽液不断微渗其中,于是 逐渐扩散深入吃掉黑化层而发生粉红圈(Pink Ring),并几乎造成 Wedge Void.此种情节由 上左50X 全域图与上右200X 局部放大图中,可清楚了解与实地认知。
PCB 板微切片制作钉头问题分析 "Nail Heading 钉头"在早期规范与品质观念中,被认为是一项必须检查的重点。例如 MIL-P-55110E 中即规定,多层板内环之钉头宽度不可超过该铜箔厚度的1.5倍。钉头的起因 是出于钻针的过度损耗,或钻孔作业管理不良,使得钻针在穿孔过程中,并未对铜箔做正常 的切削,而是用不利的钻针在强迫切削穿过之际,同时也对铜箔产生侧向推挤的动作,致使 所形成孔环的侧壁,于瞬间高温及强压下被挤扁变宽而成为钉头。 看到钉头时几可立刻判断是钻孔制程管理不善所致,并成为容易被客户所发现与挑剔的 缺失,表示钻孔的其他品质也颇有问题。但自从 SMT 与起后,大部份零件已改为板面贴装, 只有少数仍采用通孔插焊。因而排除引脚焊脚而只用于导通互连的通孔,其品质已不如早期 那么关键与受到重视。 虽然大环境已发生上述的变化,但许多客户对"钉头"仍然进行检验,尤其是过度的钉头, 仍然是钻孔不良的一种表徵,也一定是出自钻针切削前缘的不利,崩刃、刃角变圆等问题, 而这些问题也一定会引发出孔壁其他品质的不良。此等纰漏一旦被发现时自不免又要大伤脑 筋,要面对应如何搪塞客户如何改善缺失的窘境了。 当钻针情况最好时,其所切削过的孔环侧缘并未受到不当的挤压,因而铜箔截面宽度应 如上左画面一般,不应有任何增宽才对。上右图即为受到高温推挤变形而造成的钉头。 钻孔动作中高速旋转的钻针最后与孔壁接触者为"刃角"(Corner),当其呈现900时切削 效果最好,一旦变圆后即容易出现钉头。 出现钉头的孔壁其他品质也好不到那里去 画面轻微的钉头也带来 Wedge Void 的明显趋势(幸亏被化 学铜良好电度所罩住,若 PTH 是其他直接电镀施工时,八成逃不了成为楔形孔破的可能。注 意:凡有玻织渗铜者多半是出自化学铜制程)。 钉头的形成多半是受到瞬间大量热能对铜箔的软化,再被推挤压延而成钉头模样,故谓 之。当孔环宽度很窄时,其高热量较易传到环体的另一末端,进而造成该介面处的树脂缩陷。 如上左图所示。而此毛病再经漂锡后其缩陷还会再次加剧,如上右图所示。 内环有钉头,附近孔壁几乎一定会受到负面影响。上二图可见到玻织束的不齐与黑化层 压合处被拉开拉松的证据。 上左六层板经钻孔及化铜后立即切片,可看清各内层孔环出现严重钉头。若按早期钉头 规范上限不可超过铜箔厚度1.5倍时,则此样已列柜收之林。由下图及上右之200X 画面可知, 当钻针情况很差时,孔口常会发生十分难看的单向钉头,连带也会出现过度的胶渣与其他问
化铜厚化铜

微切片制作(七)1.7 化铜厚化铜化学铜(Chemical Copper)又称为无电铜(Electroless Copper),是利用槽液之“自我催化”(Self-Autocatalytic)方式,大量沉积在有氢气包围的“钯金属”活化的非导体表面,对不能导电的孔壁基材表面进行“金属化”制程,使后来的电镀铜层能顺利的增厚孔壁,完成导通互连的任务。
化学铜在业界使用已达50年以上,也是目前可靠度最好最容易操作的“金属化”制程。
可惜由于配方中含有甲醛,会在操作中不断被吹散到空气中,有致癌的可能性,对人身安全造成威胁。
再加上还有大量的钳合剂(Chelator,系为防止强碱溶液中铜离子沉积而添加)存在,对废水处理也造成很大的干扰。
在工安与环保的压力下各种“直接电镀”制程纷纷出笼,大有取代化学铜的态势。
化学铜室温作业配方中的主剂有硫酸铜、氢氧化钠、甲醛以及钳合与错合盐类等五项。
此外尚有多种少量的其他添加剂,使化铜镀层变得更为实用。
1975-1985年代业界计曾盛行一种高温(45℃)操作的“厚化铜”,厚度从60μin到120μin视作业时间而定,比传统化铜层的20μin要厚得很多(因而有时也称为薄化铜Thin Build),因此可节省一次铜流程,使在厂房、设备、管理、流程缩短等方面都十分有利,但因总体成本比一次铜之做法要贵,且槽液管理不易,品质也不稳定,故而今年来已渐从台湾业界绝迹了。
IPC-6012在3.2.6.1节中对化学铜层的厚度并无具体要求,只要能完成导电即可。
业界曾盛行一种“背光法”检查化学铜层的覆盖性(Coverage),似乎并不具太大的使用性。
因即使使孔壁未全盖满,但仍可被后来增厚的电镀栋所填充连平。
与所谓“小时了了大未必佳”说法的未必正确,其道理如出一辙。
不过背光法对各种直接电路后,再刻意镀上少许电镀铜才检查其覆盖性时,则甚具参考价值。
图1. 左3000X之电子显微镜(SEM)图面,即为一般化学铜的立体结晶形态。
微切片手册新

过度钉头几乎一定会出现较大的挖破,出自钻 孔的纵向玻璃纱束之挖破,除与钻针尖部的"刃 角"损耗有密切关系外,也与钻针的偏转(Run Out)或摇摆(Wobble)有关
网印负片法熔锡后的切片
由圖可以看出二铜镀得特别厚,不但超越油墨 而且还侧爬颇远 ,孔环外缘截面呈现缺口
2 、干 膜 阻 剂
此200X画面的油墨阻剂(如同墙壁)出现异常,致 使二次铜一开始往墙外恻向伸出,有了镀铜层在 非导体表面建立基地,锡铅镀层当然就毫不客气 顺理成章的成长,其结果不免造成板子的报废。
6.蚀 刻 因 子 Etching factor 6.蚀
X V 所谓蚀刻因子(F)系指向下的蚀深V,除 以侧蚀X所得商值F之谓也(F=V/X)。而X 定义是指“从阻剂边缘横量到最细铜腰 之宽距而言”
同一孔壁处被咬薄的放大特写镜头,其两端虽已塞有绿漆, 同一孔壁处被咬薄的放大特写镜头,其两端虽已塞有绿漆,但可能仍留有 细缝,造成蚀刻液的毛细渗入而局部咬薄的现象。 细缝,造成蚀刻液的毛细渗入而局部咬薄的现象。
黑孔孔壁全景(由于孔中央之黑膜太薄,致使皮膜 导电不良,造成孔中央全部镀不上电镀铜层而断孔)
孔壁粗糙
孔壁粗糙是因為钻孔而造成不良, 其中又以钻针情况不佳为主因。说的更仔 细一点,那就是针尖上两个第一面(First Facet)的切削前缘(Cutting Lips)出现崩破(Chipping),无法顺利切削玻璃束所致。或针尖外侧两刃角 (Corner)崩损磨圆,失去原来直角修整孔壁的功能,在破烂刀具的又劈又撞 情形下,经常会把迎面而来的纵向玻织束撞成破裂陷落的坑洞,不过横向撞 折断者则尚可维持平坦。下附各图中读者可清楚的看到其孔壁放大的细部情 形 纵向纱束被劈散成坑
孔壁背后的基材在漂 锡前多半完整无缺,漂锡 后因树脂局部继续硬化聚 合,或挥发份的逸走,造 成局部缩陷而自孔铜背后 退缩之现象即为本词。此 缺点虽然IPC-6012已可允 收,但日本客户仍坚持拒 收.
超薄切片技术的步骤
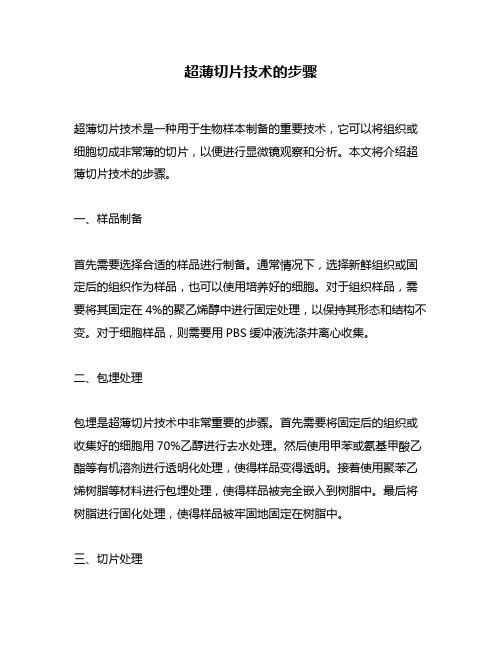
超薄切片技术的步骤超薄切片技术是一种用于生物样本制备的重要技术,它可以将组织或细胞切成非常薄的切片,以便进行显微镜观察和分析。
本文将介绍超薄切片技术的步骤。
一、样品制备首先需要选择合适的样品进行制备。
通常情况下,选择新鲜组织或固定后的组织作为样品,也可以使用培养好的细胞。
对于组织样品,需要将其固定在4%的聚乙烯醇中进行固定处理,以保持其形态和结构不变。
对于细胞样品,则需要用PBS缓冲液洗涤并离心收集。
二、包埋处理包埋是超薄切片技术中非常重要的步骤。
首先需要将固定后的组织或收集好的细胞用70%乙醇进行去水处理。
然后使用甲苯或氨基甲酸乙酯等有机溶剂进行透明化处理,使得样品变得透明。
接着使用聚苯乙烯树脂等材料进行包埋处理,使得样品被完全嵌入到树脂中。
最后将树脂进行固化处理,使得样品被牢固地固定在树脂中。
三、切片处理切片是超薄切片技术中最核心的步骤。
首先需要使用超微型切片机进行样品的切割处理。
在切割过程中,需要使用钻石或玻璃刀片等材料进行切割,以保证样品被完全切成非常薄的切片。
接着将切好的样品放入冷却盘中,并用冷却盘冷却10-20分钟,使得样品变得更加坚硬和易于操作。
最后使用显微镜或电镜等设备对样品进行观察和分析。
四、染色处理染色是超薄切片技术中常用的一种方法,它可以使得样品更加清晰明了地显示出来。
通常情况下,可以采用吉姆萨染色、银染色、荧光染色等多种方法进行染色处理。
在染色过程中,需要注意不要过度染色以避免影响观察结果。
五、结果分析最后需要对观察到的结果进行分析和解读。
通过对超薄切片图像的观察和分析,可以了解样品的结构、形态、组成等信息,从而为后续的研究提供重要的参考。
总结:超薄切片技术是一种非常重要的生物样品制备技术。
它可以将组织或细胞切成非常薄的切片,以便进行显微镜观察和分析。
超薄切片技术包括样品制备、包埋处理、切片处理、染色处理和结果分析等多个步骤。
在实际操作中需要注意各个步骤的细节,以保证制备出高质量的样品。
微切片制作及缺陷分析

分层/起泡(Delamination/Blister)
IPC-A-600G对分层/起泡的要求:
允收-2、3级: 无分层或起泡。
拒收-2、3级: 有分层或起泡。
共127页
31
互连后分离
多层板各内层孔环与后来之铜孔壁完成互连后,大功即 告成一半,但这些介面的“互连”(Interconnecting)还要 耐得住后续各种高温考验而不分离才算合格。通常模拟 方法即“288℃十秒钟之漂锡”,称为热应力试验或漂锡 试验(Thermo-Stress Test or Solder Floating Test)。经过此 严苛试验而不出现分离的板件才能允收。IPC-6012只要求 一次漂锡,但部分日本客户却要求连做五次才行 。 按IPC-6012B 3.6.2.1节“镀层完整性”规定,镀覆层的镀 层完整性应符合表3-6所列述的要求。对于2级和3级产品, 不应有镀层分离(除表3-6中注明外)或镀层裂缝,且内层 互连处不应有镀覆孔孔壁与内层间的分离或污染。
共127页
16
IPC-A-600F对孔壁粗糙的要求
允收-1、2、3级
拒收-1、2、3级 粗糙或节瘤已使镀层厚度或 孔径减少到低于最小的规定 要求。
粗糙或节瘤没有使镀层厚度 或孔径减少到低于最小的规 定要求。
共127页
17
孔壁粗糙
过度去钻污造成的孔壁 粗糙。
轻微的撞破。
钻孔的机械挖破(Gouging)与过度除钻污(De-smear)所造成 的孔壁粗糙,两者从不清楚的切片上有时是很难分辨的 。
共127页 11
图电前后判读标准
共127页
12
孔无铜
特点:孔口边缘断
铜,断铜面较整齐;
原因:基本可断定
QA工程师试题(答案)

最新资料,word文档,可以自由编辑!!精品文档下载【本页是封面,下载后可以删除!】QA工程师技能评估考试试卷姓名:工号:得分:一、填空题(每空1分,共62分)1、微切片的制作过程2、图电线镀锡的主要目的是(抗蚀刻)。
3、蚀刻能力主要通过蚀刻因子来测量,蚀刻因子是指(线路铜)厚度同(线两边侧蚀)平均值的比值,蚀刻因子越(高)说明蚀刻能力越好。
4、热冲击条件是在( 288 )度锡炉中保持( 10 )秒并循环( 3 )次。
5、内层线路使用的菲林为(负)片菲林,外层线路使用菲林为(正)片菲林。
6、百倍镜读数:一小格为(0.4 )MIL,测量某一线宽为12小格,线宽为( 4.8 )MIL7、实验室锡炉中的锡铅比率为(63/37 )。
8、正常生产板长方向为(纬)向,短方向为(径)向。
9、影响孔粗的主要因素有(钻嘴寿命)(翻磨次数)(落速)(转速)。
10、NPTH孔上金是沉金板的缺陷之一,造成问题的原因是NPTH孔壁上残留有(沉铜)工序的(钯)此种残留物在沉金镍缸被催化还原而造成孔壁上金,我们可以使用过(整孔)流程去除此种残留而改善此问题。
11、(背光)是检测沉铜工序品质的重要方法,本厂的检测频率为(2小时)/次。
12、层间对位情况可以通过过X-RAY检测做在内层的(同心圆)来判定。
13、内层线路的缺口、开路主要是(垃圾)造成,短路残铜主要是(菲林擦花)(膜碎)造成。
14、沉铜前过磨板机主要是为了去除(孔边毛刺),内外线、阻焊工序前过磨板机主要是为了去除(铜面污染物)并对铜面进行(粗化)以保证干膜或阻焊同铜面的(结合力)。
15、TG是指(玻璃转化温度),TG越(高)相对材料越脆,在二钻或外形生产时容易出现(爆板)。
16、需要温湿度控制的主要工序有(钻孔)(内外线)(阻焊)(电测),有洁净度控制的工序有(预排)(内外线)(阻焊)。
17、阻焊预烤主要目的是让阻焊初步固化而方便(对位),预烤参数为(75 )度*(45 )分钟。
微切片讲解

2、 封 胶(Resin Encapsulation) 封胶之目的是为夹紧检体减少变形,系采用适宜的树脂类将通孔灌满 及将板样封牢。把要观察的孔壁与板材予以夹紧固定,使在削磨过程中 其铜层不致被拖拉延伸而失真 (封膠形式有很多種,本廠是购买现成的 压克力成型模塊,将待檢切片固定在模塊槽中灌入冷凝胶封膠。)
5、机 械 外 力 效 果
上三图均为电性测试时,发现断路(Continuity Failure 或Open)时,再去 做切片发现是因镀锡铅不良而于蚀刻时被咬断的孔。这种不通的孔常会多测 一两次,以致孔口出现被探针所顶挤变形的样,电测机所施加压力的影响可 见一般
上三图均为V-Cut之圖片。左邊上下切口对齐度较好,中間稍歪,右图未對齊 且上下切口深度不同(欧洲客户尤其是德国客戶十分在意V-Cut對準度)
过度钉头几乎一定会出现较大的挖破,出自钻 孔的纵向玻璃纱束之挖破,除与钻针尖部的"刃 角"损耗有密切关系外,也与钻针的偏转(Run Out)或摇摆(Wobble)有关
过度除胶引起的孔壁 粗糙度
轻微的撞破引起的孔 壁粗糙度及釘頭
由于玻织纱束中的破洞造成 的孔壁粗糙度
画面右边的黑洞及中央的断层,由于落差太大连化学铜与一次铜都镀不上, 可见粗糙之严重性。这种由于玻织布中断纱太多而不良的基材板,进而又造 成孔壁的粗糙,並不是鑽孔造成的粗糙度
本廠的孔壁粗糙度的允收標準為:
鑽孔粗糙度<1200U” 電鍍孔壁粗糙度<1500U”
互连后分离
多层板各内层孔环与后来之铜孔壁完成互连后(Interconnecting)还要耐得住 后续各种高温考验而不分离才算合格,通常模拟方法即“288°C十秒钟之漂锡” 即热应力试验或漂锡试验(Thermo-Stress Test or Solder Floating Test), 美式规范(如IPC-6012或MIL-P-5511OE)都只要求一次漂锡,但部分日商客户 却要连做五次才行 IPC-6012 中規定通孔热应力漂锡后各内环与孔壁之互连 处不可分离 产生后分离的原因主要是内层孔环之侧面,在化学铜或直接电镀之前, 就可能存在氧化物或钝化物皮膜,使得二者附著力不够牢靠所致
制作微小组织切片的技术探讨

生 影响 , 片质量 的好 坏直 接影 响着 诊断 的准 确性 。 切 因此 , 制作 一张 优 良的切 片 , 要 必须要 考虑 多方 面 的
包埋 冷 台上 , 快速 用 加 热 的包埋 镊 将 一 块 或 多 块 微 小组 织按 顺 序转 移 人 包埋 模 中 , 中或 平 放 且 不 能 集 重叠 ; 将组 织包 埋 盒 放 在 包埋 模 上移 至 操 作 台热 ③
12 1 固定 方法 ..
绝 大 多 数 医师 习惯 于将 所 取 的
小标本 按活 检组 织 顺 序 附 在作 为标 底 的滤 纸 上 , 经
1 % 甲醛 固定送 病 理科进 一 步诊 断 。而我 们 与 胃镜 0 室 医师 紧 密配合 , 改用 光 面 白纸 作 为组 织 标 本 固定
3 讨 论
微 小 组 织 标 本 固定 得 好 坏 , 接影 响病 理诊 断 直
的准 确性 [ 大多数 内窥 镜 为多 点取 材 , 织 常延搁 , 组 在滤纸 上 不能及 时 固定 , 易造 成 微 小 组 织 因 标底 常 滤纸 吸水 , 织 紧紧 吸附在 滤纸 上无 法分 离 , 组 即使 强 制取 下 , 也常 粘带 上 肉眼难 以发 现 的滤纸 纤维 , 利 不 微小 组织 固定 , 成切 片 易碎裂 , 响诊 断质量 。改 造 影
台加满 蜡 。
124 冷 冻方 法 ..
电路板微切片制作的三类方法

电路板微切片制作的三类方法1.概述品质的好坏,问题的发生与解决,制程改进的情况,在在都需要微切片(croseconing)做为观察研究与判断的根据,微切片做的好不好,真不真与讨论研判的正确与否大有关系在焉。
一般生产线为品质监视(monitoring)或出货时品管为求品质的保证等所做的多量切片,因系在匆忙及经验不足情况下所赶出的,故至多只能看到真相的六、七成而已,有的在缺乏指导及比较情况下,甚至连一半的实情都看不到,在一片模糊及含混的影像下,能看出什么来?这样的切片有什么意义?若只是为了应付公事当然不在话下,若的确想要做好品质及彻底找出问题解决问题,则必须仔细做切、磨、抛及咬等功夫才会有清晰可看的微切片,不致造成误判。
2.分类板的解剖式破坏性切片法大体上可分为三类:(1)一般切片(正式名称为微切片)可对区及板面其它区域灌满封胶后做了垂直切片(Vercal Secon),也可对通孔做水平切片(Horizontal Secon)是一般常见的做法。
(2)切孔是小心用钻石锯片将一排通孔自正中央切成两半,或用砂纸将一排通孔磨去一半,将切半不封胶的通孔置于20x-40x的立体显微镜(或称实体显微镜)下观察半个的全部情况。
此时若也将通孔的后背再磨的很薄时,则底材将呈透明状,可进行背光法(Back light)检查孔铜层敷盖的情形。
(3)斜切片(45°或30°)可对面区或通孔区做层次间45°的斜切,然后以实体显微镜观察45°切面上导体间的情形。
3.制作技巧除第二类切孔法是用以观察半个孔壁的原状表面情况外,其余第一及第三类都需最后的仔细抛光,才能看到各种真实的情况,此点为切片的成败关键,此点至为重要不可掉以轻心。
以下为制作过程的重点。
3.1取样:以特殊的切模自板上任何处取样或用剪床剪样,注意不可太逼近孔边,以防造成通孔受拉力而变形,也应注意取样的方法,最好先切剪下来,再用钻石锯片切下所要的切样,减少应力的后患。
微切片之分类图解

印制电路板显微剖切技术研究1前言印制电路板制造质量的好坏、使用可靠性的高低、制造过程中问题的发生与解决、制程能力及改进的评估,往往都需要采用显微剖切来作为客观检察、研究和判断的依据。
显微剖切(Microsectioning),又称微切片、金相切片,它的制作有着一套相对专业的制造技术和检测手段。
微切片制作质量的好坏,将直接关系到研究和判断的正确性。
俗话说得好,外行看热闹、内行看门道,各家有各家的高招。
真应了那句名言——条条大路通罗马。
作者长期从事各类印制电路板的制造工艺及品质控制技术的研究,曾专长于金相切片的制作,并有大量第一手金相切片照片在握。
本不该在各位专家面前献丑,但每每翻看这些照片,总有一种与人共研之冲动。
今特将之分类后,陆续登出,望各位不吝赐教,共同为业界之发展贡献些许绵力。
2微切片制作工艺流程2.1取样待检印制电路板试样的采取有以下几种方法:(1)采用机械装置剪切或辊切、锯切;(2)平面冲头之冲切;(3)凹陷冲头之冲切;(4)铣切;(5)带锯切割;上述诸种方法,各有利弊。
从对待检印制电路板部位的损伤来讲,第一种和第二种较为严重;第三种和铣切则适中。
266至于带锯切割法,虽然同冲切和铣切一样的快速、便捷,但对操作者来说,存在潜在的伤害危险。
2.2试样续处理2.3试样入模方式用双面胶粘住样品的正截面(较薄的板用订书子夹住样品待检测的侧截边),使样品垂直立于凝胶模中央。
如是试验切片,建议一个模放两个样品,待检测的侧截边分放于切片的两面,以便从两面磨孔均能磨到孔中央,但样品间要保持最少2mm间距,以免固化后影响样品的牢固性。
2.4调胶处理本处理的重点在于各组分混合充分均匀,且尽可能减少搅拌所造成的气泡产生量。
正误搅拌方式对比请参见下左图9。
搅拌方式对比2.5灌胶入模将上述搅拌均匀的胶料,缓慢倒入模内,直至淹没横担试样的铅芯或鱼线(对于待检部位在模具底部之情况除外)。
对于可能粘附于试样上的气泡,可通过轻敲模壁或用牙签将其引出。
- 1、下载文档前请自行甄别文档内容的完整性,平台不提供额外的编辑、内容补充、找答案等附加服务。
- 2、"仅部分预览"的文档,不可在线预览部分如存在完整性等问题,可反馈申请退款(可完整预览的文档不适用该条件!)。
- 3、如文档侵犯您的权益,请联系客服反馈,我们会尽快为您处理(人工客服工作时间:9:00-18:30)。
具体 1
2
3
4
5
6
7
流程 简介 取样 灌胶 研磨 拋光 微蚀 判读
7.3 胶渣 Smear IPC-A-600H-3.3.12.~ 3.3.13
允收
拒收
拒收
垂 直 切 片
允收
水 平 切 片
拒收
拒收
微切片制作与检验
具体 1
2
3
4
5
6
7
流程 简介 取样 灌胶 研磨 拋光 微蚀 判读
7.4 孔壁粗糙度 Roughness
2
3
4
5
6
7
流程 简介 取样 灌胶 研磨 拋光 微蚀 判读
6. 微蚀
微蚀液的配方是: “氨水+水+双氧水” 配比为:1:1:0.1
观察面上滴微蚀液用棉花棒擦抹后,铜面产生微小 气泡,即表示反应已在进行,来回擦蚀约1~~3秒钟,立刻用 口罩擦干,勿使铜面继续氧化变色. 良好的微蚀将呈现鲜 红铜色,且结晶分界清楚。
7.1 龟裂 Crack IPC-A-600F-3.3.5~3.3.6
允收-孔壁及转角均无裂痕
拒收-镀铜层均有裂痕
微切片制作与检验
具体 1
2
3
4
5
6
7
流程 简介 取样 灌胶 研磨 拋光 微蚀 判读
7.2 芯吸 Wicking IPC-A-600F-3.3.11
允收
拒收: 芯吸≧4mil
微切片制作与检验
具体 1
2
3
4
5
6
7
流程 简介 取样 灌胶 研磨 拋光 微蚀 判读
5. 拋光
拋光粉
拋光
微切片制作与检验
具体 1
2
3
4
5
6
7
流程 简介 取样 灌胶 研磨 拋光 微蚀 判读
6. 微蚀
微蚀的作用是:分出金属之各层面与其结晶状况 ,效果 不好时抛掉不良铜面重做微蚀 。
微蚀前
微蚀后
微切片制作与检验
具体 1
允收
拒收:粗糙度 > 1mil :
微切片制作与检验
具体 1
2
3
流程 简介 取样 灌胶
7.5 结瘤 Nodules
4
5
6
7
研磨 拋光 微蚀 判读
IPC-A-600H-3.3.7
允收
拒收:影响到孔径:
微切片制作与检验
具体 1
2
3
4
5
6
7
流程 简介 取样 灌胶 研磨 拋光 微蚀 判读
7.6 树脂內缩 Resin Recession IPC-A-600F-3.1.8
微切片制作与检验
具体 1
2
3
4
5
流程 简介 取样 灌胶 研磨 拋光
1.1 微切片作用
6
7
微蚀 判读
微切片: 是观察PCB內部结构狀 况及內部数据据测量的一种工具, 能有力帮助现场发现问题,解决问题.
微切片制作与检验
具体 1
2
3
4
5
流程 简介 取样 灌胶 研磨 拋光
1.2 微切片分类
6
7
微蚀 判读
微切片可分为垂直切片、水平切片、斜切片及微切片。
微切片制作与检验
具体 1
2
3
4
5
6
7
流程 简介 取样 灌胶 研磨 拋光 微蚀 判读
6. 微蚀
微蚀液
微蚀
微切片制作与检验
具体 1
2
3
4
5
6
7
流程 简介 取样 灌胶 研磨 拋光 微蚀 判读
7. 判读
观察及测量用的金相显微镜量
微切片制作与检验
具体 1
2
3
4
5
6
7
流程 简介 取样 灌胶 研磨 拋光 微蚀 判读
孔內铜厚:(A~F) 基板铜厚:G 电镀铜厚:H 表面铜厚: I
微切片制作与检验
具体 1
2
3
4
5
6
7
流程 简介 取样 灌胶 研磨 拋光 微蚀 判读
7.11 钉头 Nail Heading IPC-A-600H-3.4.2
钉头≦1.5倍铜箔厚度可接受 钉头> 1.5倍铜箔厚度拒受
微切片制作与检验
具体 1
热应力后的树脂内缩均为允收
微切片制作与检验
具体 1
2
3
4
5
6
7
流程 简介 取样 灌胶 研磨 拋光 微蚀 判读
7.7 电镀空洞 Plating Void IPC-A-600F-3.3.9
允收
拒收: 镀层空洞超过一个
微切片制作与检验
具体 1
2
3
4
5
6
7
流程 简介 取样 灌胶 研磨 拋光 微蚀 判读
7.8 镀层分离 Pullaway
6
7
微蚀 判读
金相胶粉与固化剂的配比为3:1调匀后灌入模具内,3~ 5分钟后即可固化研磨。
微切片制作与检验
具体 1
2
3
4
5
流程 简介 取样 灌胶 研磨 拋光
4. 研磨
6
7
微蚀 判读
研磨用双盘研磨机加上不同目数的砂纸将样品 研磨至孔的
2
3
4
5
流程 简介 取样 灌胶 研磨 拋光
微切片制作与检验
具体 1
2
3
4
5
流程 简介 取样 灌胶 研磨 拋光
3. 灌胶
6
7
微蚀 判读
灌胶的做法有很多种,现列举行业内在用的三种:
3.1 AB胶 + 树脂 3.2 压克力粉 + 固化剂 3.3 水晶胶 + 固化剂
微切片制作与检验
具体 1
2
3
4
5
流程 简介 取样 灌胶 研磨 拋光
3. 灌胶
金相胶粉 + 固化剂
允收
拒收
微切片制作与检验
具体 1
2
3
4
5
6
7
流程 简介 取样 灌胶 研磨 拋光 微蚀 判读
7.9 玻璃纤维突出Class Fiber Protrusion
允收
拒收:影响到孔径
微切片制作与检验
具体 1
2
3
4
5
6
7
流程 简介 取样 灌胶 研磨 拋光 微蚀 判读
7.10 銅厚 Copper thickness
注意事项: 在冲取切片时,将待观察的孔放置于冲床凹 槽的正中间位置, 以保证待观察孔的完整性.
微切片制作与检验
具体 1
2
3
4
5
流程 简介 取样 灌胶 研磨 拋光
2. 取樣
6
7
微蚀 判读
切片冲床
冲取好的样片
微切片制作与检验
具体 1
2
3
4
5
流程 简介 取样 灌胶 研磨 拋光
3. 灌胶
6
7
微蚀 判读
灌胶目的: 用样板夹夹紧切片试样减少变形,将通孔灌满 胶,使其在研磨过程中其铜层不致被拖拉延伸而失真。
微切片制作与检验
具休 1
2
3
4
5
流程 简介 取樣 灌胶 研磨 拋光
1.3 微切片制作流程
6
7
微蚀 判读
取样
灌胶
研磨
判读
微蚀
拋光
微切片制作与检验
具体 1
2
3
4
5
流程 简介 取样 灌胶 研磨 拋光
2. 取样
6
7
微蚀 判读
成品取样: 直接冲取最小的过电孔孔数需达到三个或三个以 上,优先选则BGA和密集孔位置.
2
3
4
5
6
7
流程 简介 取样 灌胶 研磨 拋光 微蚀 判读
7.12 层压板空洞 Laminate Void IPC-A-600F-3.1.1
允收: 空洞小于或等于 3mil且不违反介质间距 的规定
4. 研磨
6
7
微蚀 判读
双盘研磨机
各种型号的砂纸
研磨时冲水
微切片制作与检验
具体 1
2
3
4
5
6
7
流程 简介 取样 灌胶 研磨 拋光 微蚀 判读
5. 拋光
在抛光布上加入抛光粉并用水稀释,将转速调至 150~200 转/分,将切片轻微接触拋光布,不断转换方向,直 到砂痕消失切面光亮为止 。
微切片制作与检验