压铸生产工艺
压铸工艺流程
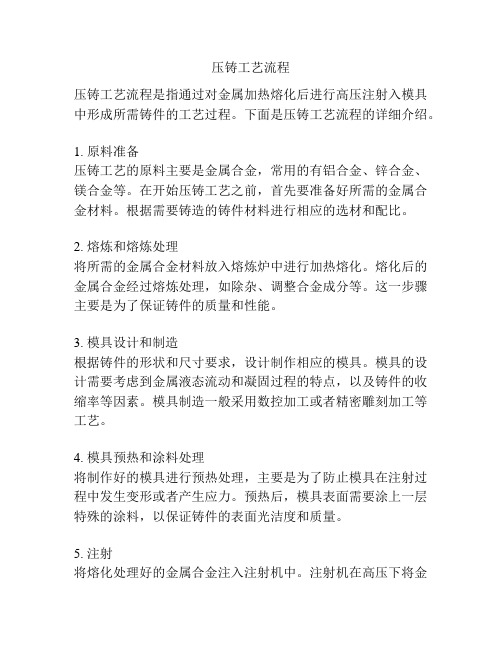
压铸工艺流程压铸工艺流程是指通过对金属加热熔化后进行高压注射入模具中形成所需铸件的工艺过程。
下面是压铸工艺流程的详细介绍。
1. 原料准备压铸工艺的原料主要是金属合金,常用的有铝合金、锌合金、镁合金等。
在开始压铸工艺之前,首先要准备好所需的金属合金材料。
根据需要铸造的铸件材料进行相应的选材和配比。
2. 熔炼和熔炼处理将所需的金属合金材料放入熔炼炉中进行加热熔化。
熔化后的金属合金经过熔炼处理,如除杂、调整合金成分等。
这一步骤主要是为了保证铸件的质量和性能。
3. 模具设计和制造根据铸件的形状和尺寸要求,设计制作相应的模具。
模具的设计需要考虑到金属液态流动和凝固过程的特点,以及铸件的收缩率等因素。
模具制造一般采用数控加工或者精密雕刻加工等工艺。
4. 模具预热和涂料处理将制作好的模具进行预热处理,主要是为了防止模具在注射过程中发生变形或者产生应力。
预热后,模具表面需要涂上一层特殊的涂料,以保证铸件的表面光洁度和质量。
5. 注射将熔化处理好的金属合金注入注射机中。
注射机在高压下将金属液态材料注射到模具腔中,填充整个空腔。
这个过程需要控制注射速度和注射压力,以确保铸件的完整和一致性。
6. 冷却和固化注射完成后,模具中的金属液态材料会迅速冷却凝固。
在这个过程中,需要对模具进行适当的冷却措施,例如喷水冷却、通风散热等,以防止铸件产生缺陷。
同时,还需要对铸件进行固化处理,使其达到所需的力学性能。
7. 模具开启和脱模当铸件完全冷却固化后,模具开始开启。
脱模时需要小心操作,避免因剥离过快导致铸件破损。
脱模后,可以对铸件进行涂装、抛光等表面处理,使其达到所需的外观要求。
8. 修磨和后处理对于一些不合格的铸件,需要进行修磨处理,消除表面缺陷或尺寸偏差。
修磨后的铸件需要进行清洁、除锈等后处理,以便进行下一步的装配和加工。
9. 检验和质量控制对于每个生产批次的铸件,需要进行严格的检验和质量控制。
检验项目包括尺寸、外观、力学性能等。
压铸生产工艺流程

压铸生产工艺流程压铸生产工艺流程压铸是一种常用的金属制造工艺,用于制造各种金属件,尤其是复杂形状的零件。
下面将介绍一下压铸的生产工艺流程。
首先,原料的准备非常关键。
通常情况下,压铸常用的原料是铝合金。
在开始生产之前,需要将铝合金锭进行熔炼,将其熔化成液态金属。
然后,将液态金属倒入坩埚中,待其冷却后形成固态金属块。
接下来,需要进行模具设计和制造。
模具是压铸过程中非常重要的工具,它决定了最终产品的形状和尺寸。
根据产品的图纸和要求,设计师会运用计算机辅助设计软件进行模具的设计,并制作出精密的模具。
然后,进行模具预热和涂层处理。
在使用模具之前,需要进行模具的预热和涂层处理,以提高模具的耐热性和耐磨性。
预热可以在炉中进行,将模具加热到适当的温度,然后进行涂层处理,将耐磨材料涂覆在模具的表面。
接下来是压铸的核心步骤,即注射和压铸。
首先,将模具安装在压铸机上,并加热至一定温度。
然后,将固态金属块放入注射室中,通过注射器将其注入模具中。
同时,压铸机会施加压力,将金属块注入模具内,填充模具的空腔。
注射的时间和注射速度需要根据产品的要求进行调整。
注射完成后,需要将模具进行冷却。
冷却时间一般较长,以确保金属能够完全凝固。
冷却结束后,打开模具并取出压铸件。
此时,压铸件已经具备了初步的形状和尺寸。
最后,需要进行后处理和加工。
压铸件在冷却过程中可能会出现一些缺陷,如气孔、缩短等。
为了保证产品的质量,需要对压铸件进行修整、抛光和清洁。
有时候还需要进行机械加工,如钻孔、车削等,以达到最终的产品要求。
以上就是压铸生产工艺流程的介绍。
压铸生产工艺非常复杂,需要经过多个步骤,并且每个步骤都需要仔细操作和严格控制,以确保产品的质量和性能。
压铸生产工艺的研发和改进,不仅可以提高产品的生产效率和质量,还有助于推动金属制造行业的发展。
压铸件的工艺流程
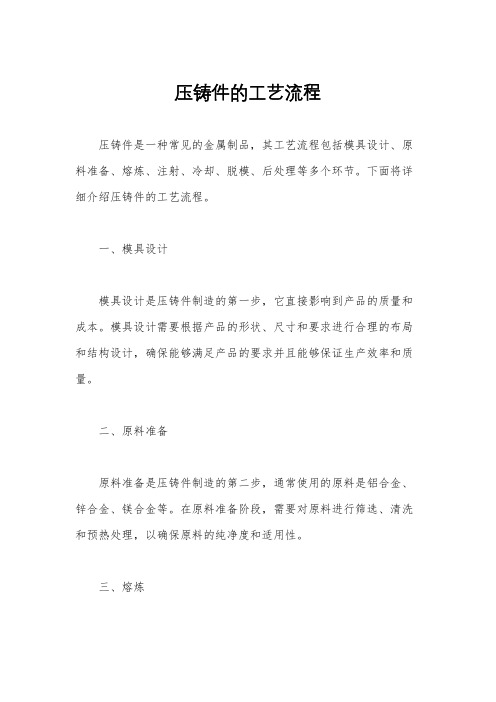
压铸件的工艺流程压铸件是一种常见的金属制品,其工艺流程包括模具设计、原料准备、熔炼、注射、冷却、脱模、后处理等多个环节。
下面将详细介绍压铸件的工艺流程。
一、模具设计模具设计是压铸件制造的第一步,它直接影响到产品的质量和成本。
模具设计需要根据产品的形状、尺寸和要求进行合理的布局和结构设计,确保能够满足产品的要求并且能够保证生产效率和质量。
二、原料准备原料准备是压铸件制造的第二步,通常使用的原料是铝合金、锌合金、镁合金等。
在原料准备阶段,需要对原料进行筛选、清洗和预热处理,以确保原料的纯净度和适用性。
三、熔炼熔炼是将原料加热至熔化状态的过程,通常使用电炉或燃气炉进行熔炼。
在熔炼过程中,需要控制炉温和炉内气氛,确保原料能够完全熔化并且保持一定的温度。
四、注射注射是将熔化的金属液注入模具腔体的过程,通常使用压铸机进行注射。
在注射过程中,需要控制注射速度和压力,确保金属液能够充分填充模具腔体并且形成完整的产品形状。
五、冷却冷却是将注射后的模具进行冷却的过程,通常使用冷却水或风冷设备进行冷却。
在冷却过程中,需要控制冷却速度和温度,确保产品能够快速冷却并且保持一定的结构和硬度。
六、脱模脱模是将冷却后的产品从模具中取出的过程,通常使用振动或冲击的方式进行脱模。
在脱模过程中,需要注意保护产品表面,避免产生划痕或变形。
七、后处理后处理是对脱模后的产品进行去除余料、修磨、喷漆等加工的过程。
在后处理过程中,需要根据产品的要求进行相应的处理,以确保产品的表面光滑、尺寸精度和表面质量。
总结压铸件的工艺流程包括模具设计、原料准备、熔炼、注射、冷却、脱模、后处理等多个环节,每个环节都需要严格控制和操作,以确保产品的质量和成本。
压铸件制造是一个复杂的工艺过程,需要生产厂家具备一定的设备和技术实力,以满足客户的需求。
压铸工艺及生产操作

压铸工艺及生产操作
压铸工艺及生产操作是一种利用金属材料在高压下通过模具形成所需形状的金属成型工艺。
下面是压铸工艺及生产操作的一般步骤:
1. 模具制作:根据产品的形状和尺寸要求,制作相应的压铸模具。
2. 材料准备:选择合适的金属材料,并进行加热熔化。
3. 注射:将熔化的金属材料倒入注射机中,并在高压的作用下通过喷嘴注入到模具腔中。
4. 固化:在模具中,金属材料会迅速冷却凝固,形成所需形状的产品。
5. 脱模:待金属材料完全凝固后,打开模具,取出成品。
6. 产品处理:对成品进行去除余料、修磨、喷涂等后续处理工序。
压铸工艺及生产操作的优点包括生产效率高、产品形状复杂度高、尺寸精确等。
但也存在一些注意事项,如需要考虑材料的热胀冷缩性、模具的耐磨性等。
此外,操作人员需要具备相关的操作技能和安全意识,以确保生产过程的顺利进行。
压铸件工艺流程
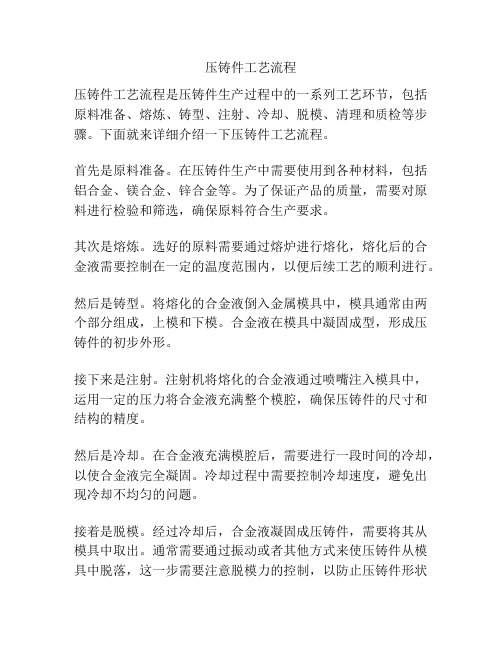
压铸件工艺流程压铸件工艺流程是压铸件生产过程中的一系列工艺环节,包括原料准备、熔炼、铸型、注射、冷却、脱模、清理和质检等步骤。
下面就来详细介绍一下压铸件工艺流程。
首先是原料准备。
在压铸件生产中需要使用到各种材料,包括铝合金、镁合金、锌合金等。
为了保证产品的质量,需要对原料进行检验和筛选,确保原料符合生产要求。
其次是熔炼。
选好的原料需要通过熔炉进行熔化,熔化后的合金液需要控制在一定的温度范围内,以便后续工艺的顺利进行。
然后是铸型。
将熔化的合金液倒入金属模具中,模具通常由两个部分组成,上模和下模。
合金液在模具中凝固成型,形成压铸件的初步外形。
接下来是注射。
注射机将熔化的合金液通过喷嘴注入模具中,运用一定的压力将合金液充满整个模腔,确保压铸件的尺寸和结构的精度。
然后是冷却。
在合金液充满模腔后,需要进行一段时间的冷却,以使合金液完全凝固。
冷却过程中需要控制冷却速度,避免出现冷却不均匀的问题。
接着是脱模。
经过冷却后,合金液凝固成压铸件,需要将其从模具中取出。
通常需要通过振动或者其他方式来使压铸件从模具中脱落,这一步需要注意脱模力的控制,以防止压铸件形状变形。
然后是清理。
脱模后的压铸件表面通常会有一些余渣和污垢,需要进行清理工作。
可以通过切削、喷砂等方式对压铸件表面进行处理,以获得光洁的表面。
最后是质检。
生产完成的压铸件需要进行质量检验,以确保产品符合设计要求。
对压铸件的尺寸、外观和物理性能等方面进行检测,如果发现不合格的情况需要重新制作。
以上就是压铸件工艺流程的主要步骤。
整个工艺流程中需要密切配合各个环节,保证每一步都严格按照要求进行,以获得高质量的压铸件产品。
同时,工艺流程中需要注意安全和环保等要求,确保生产过程的安全和环境的可持续发展。
压铸工艺
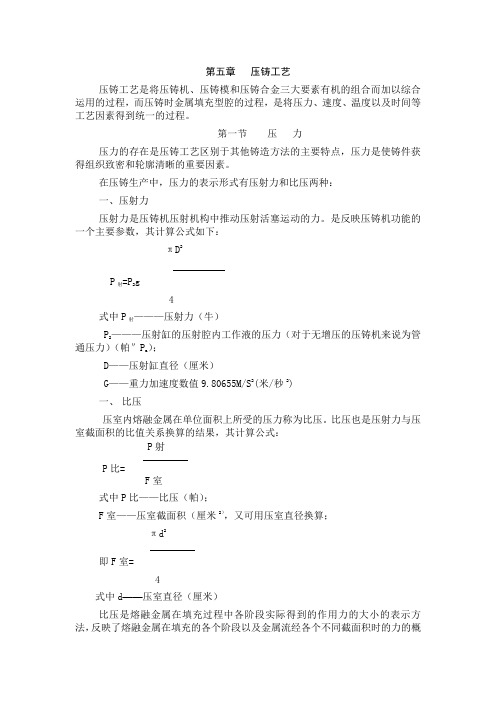
第五章压铸工艺压铸工艺是将压铸机、压铸模和压铸合金三大要素有机的组合而加以综合运用的过程,而压铸时金属填充型腔的过程,是将压力、速度、温度以及时间等工艺因素得到统一的过程。
第一节压力压力的存在是压铸工艺区别于其他铸造方法的主要特点,压力是使铸件获得组织致密和轮廓清晰的重要因素。
在压铸生产中,压力的表示形式有压射力和比压两种:一、压射力压射力是压铸机压射机构中推动压射活塞运动的力。
是反映压铸机功能的一个主要参数,其计算公式如下:πD2P射=P2g4式中P射———压射力(牛)P2———压射缸的压射腔内工作液的压力(对于无增压的压铸机来说为管通压力)(帕″Pa);D——压射缸直径(厘米)G——重力加速度数值9.80655M/S2(米/秒2)一、比压压室内熔融金属在单位面积上所受的压力称为比压。
比压也是压射力与压室截面积的比值关系换算的结果,其计算公式:P射P比=F室式中P比——比压(帕);F室——压室截面积(厘米2),又可用压室直径换算;πd2即F室=4式中d——压室直径(厘米)比压是熔融金属在填充过程中各阶段实际得到的作用力的大小的表示方法,反映了熔融金属在填充的各个阶段以及金属流经各个不同截面积时的力的概念。
将填充阶段的比压称为填充比压(又称压射比压,以P比压表示;增压阶段的比压,称为增压比压,以P比增表示。
填充比压用来克服浇注系统和型腔中的流动阻力,而增压比压则是决定了正在凝固的金属所受到的压力以及这时所形成的胀型力的大小。
三、压力的作用和影响⑴比压对铸件机械性能的影响比压增大,结晶细,结晶层增厚,由于填充特性改善,表面质量提高,会孔影响减轻,从而抗拉强度提高,但延伸率有所降低。
⑵对填充条件的影响。
合金熔液在高比压作用下填充型腔,合金温度升高,流动性改善。
有利于铸件质量的提高。
四、影响压力的因素⑴压铸合金的特性,如熔点、流动性等,熔点高,有效比压越大。
⑵合金浇注温度和模具温度,温度过低,压力损耗增大。
压铸生产工艺
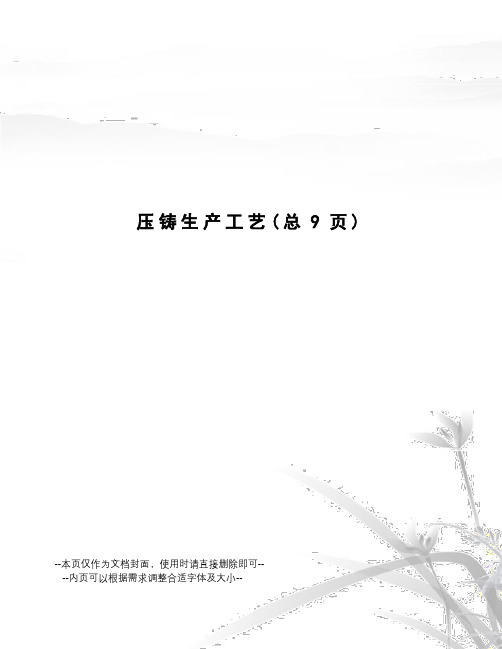
压铸生产工艺(总9页)--本页仅作为文档封面,使用时请直接删除即可----内页可以根据需求调整合适字体及大小--压铸生产工艺知识一.压铸生产的概念** 压铸(DIE CASTING)就是将熔融合金在高压﹑高速条件下充满金属模并使其在高压下凝固冷却成型的精密铸造生产.压铸制造出来的工件称为压铸件(DIE CASTINGS),压铸件主要特点尺寸公差很小(精密公差±,一般公差±,精密度高,表面不需经车削加工而只是经过整缘处理(如去批锋.抛光等)即可用于后工序如静电喷涂或装配生产.二.压铸机(CASTING MACHINE)压铸机为热料室压铸机,基本结构如图所示:所用压铸机有两种型号:台)﹑台),机器制造商:力劲机械厂有限公司 .***机器的主要工作参数列表如下供参考:压铸机基本结构各部分作用;固定机板----用以固定压铸模的静模(前模)部分;移动机构----用以固定压铸模的动模(后模)部分;顶出机构----用以顶出压铸件;锁紧机构----实现在压射过程中可靠地锁紧模具;配电及数显—电源供应﹑显示溶料温度﹑压铸程序及时间控制等;操纵台------控制压铸操作的系列动作;射料机构----将合金液推入模具型腔,进行充填成型;熔料室------将铸绽熔化为合金液并维持恒温.***压铸机工序流程步骤:正常所采用的半自动生产操作,每个生产周期是靠开和关安全门来触发下一个局期,其流程可如图表达:关门--→(顶针退回)锁模--→扣咀前--→一速身料--→二速射料回锤喷(刷)说模剂←--顶针顶出/钻取啤件←--开模←--离咀三.压铸用的锌(Zinc)合金材料本公司所用皆为锌3#合金(EZDA 3PRESSURE KIECASTING ALLOY),其化学成份含量及作用如下表(见下页):1.锌合金主要性能特点如下:a)熔点较低;b)压铸成型效果好;c)铸件表面可镀金属,可以进行(静电)喷涂装饰;d)缺点:铸件易老化,抗腐蚀能力差.2.锌合金原料中掺入水口料对铸件的影响:在锌合金压铸生产中,适当地在材料中掺入水口料可降低铸件成本,但水口料掺入也会引致某些质量问题:a)水口料中往往含有杂质,使材料机械性能变差,使铸件不能满足使用要求:b)水口料中的化学成份巳发生变化,铝镁成份的减少会使材料理化性能变坏,从而会使铸件花纹和气泡等问题增多.如果通过化学鉴定及处理,在掺有水口料的锌合金(水口料一般不超过50%)中适当地加入铝和镁元素,并协同改善压铸模的排溢条件,选择适当的压铸参数,能够在一定程度上提高铸件质量,减少废品产生.3.合金溶液温度控制:锌合金在熔化时,温度在435-440℃时段为理想,温度不可超过450℃免引起其他成份下降;但如温度降低则溶化浮渣不易浮出,影响流动及使材料强度下降.4.合金料加入熔炉注意事项:a)冷进料明,铸绽显放在盘上或其他地方充分预热才可投入;b)不可投入潮湿的铸绽或水口料,以免发生危险;c)不可投入沾有油污,杂物的铸绽或水口料,以免影响溶液质量.5.合金料的存放:应把锌绽置放在于有遮盖的地方,避免受潮,风吹雨林而便锌绽表面出现「白绣」及在投入熔炉时发生危险.四.压铸生产工艺流程***压铸生产工艺流程图:***压铸生产过程及其有关说明:压铸生产实施的基础为:a) 压铸机的功能实现及其可靠性;b) 压铸模的质量及其结构合理性;c) (锌)合金材料含量接近值及其**温度的**性﹔d) 压铸模作的技术质素等等.1.压铸表型:过程描述:a) 开动压铸机,使压铸模合理,顶杆复位并**模具,打料杆迅速下降通过中头将合金溶液通过鹅颈--→发热套--→进料道--→推入型腔,在充型时废物冷科技排在排溢位(垃圾位)内.实际上,射料的运动分三个阶级:减速--→高速--→增压,也就冲头是以越来越快的速度将熔液推型再施以持续加压.持续加压能改善溶液的结晶效果及对压铸件的冷纹和缺料方面有直接影响.当熔液冲过唧胡时的冲挚力非常大,进入模腔后为张开模力,这时机器的钻模机构必须提供大的钻模力保证模的充分垒合,否会产生批锋(飞边)等缺陷.另外要提到的一点就是射咀和唧咀的大小关系一定要相配,避免压力不或损耗压力.b) 冷却固化后,压铸机开模,在顶出机构作用下脱出铸件.刚出模的铸件温度是很高的,一般需经过浸水(个别细小件可免),水加快其冷却并能有效防上成型后的变形.C) 影响成型工艺的有关因素:包括压力﹑温度﹑速度﹑时间参数及脱模剂的影响.i) 压力:压力分为压射力和压比压,压射力是压铸机的料力(单位:顿),而压射比压是合金熔液实际得到的作用压强(单位:kg/㎝2),生产时压射比压的调节视乎铸件结构及模具情况依经验一般定在50-70kg/㎝2左右.ii) 温度:温度包括合金熔液温度和模具的工作温度(单位:℃).熔液温度一般控制在420-440℃,根据铸件情况具体做调整,如对结构复杂,薄壁的件宜选用较高的熔液温度以免造成冷痕﹑花纹﹑走料不到;而对于结构简单的厚壁件应选用较低的温度避免粘模﹑晶料粗大(可致机被强下降)且因凝固改缩大造开裂等题.经验证明:在使用较高的压射比压情况下,适当降低的温度可以减少因体积改缩导致的组机蔬松等.模具温度是通过运水冷却来控制,模具上合理的冷却运水道设计是控制好模温从而保证铸件均匀冷却的根本所在.模温一般控制在120-150℃.若模温运动部件卡死问题,同时过高的模温还使铸件冷却缓慢造成晶粒粗大而使其冲挚强度下降;若模温太低又会造成严重花纹﹑冷痕﹑甚至走料不到等问题.iii> 速度:包括合金熔液的压射速度和合金熔液对压铸的充填速度(单位:m/s).压射速度是指压射冲头运动的线速度,由机器本身决定,一般在~7m/s内变动.充填速度是指熔融触合金在压射冲头压力作用下(一般应在35-~45m/s之范围.)通过内进口(入水口)的线速度,根据流量连续原理,可知充填速度成正比,而与内浇口截面积成反比.射速利用流量阀控制,速度切换由慢快--→高速,最后施以增压iv> 时间:包括充模时间,持续庇压时间和冷却留模时间(单位:s).充模时间:金属液自进入模具型腔至充满所需时间,适当的填模时间为~.注:压铸以下铸件时,填模时间问题小于或等于:薄铸件(厚度小于1mm);轻铸件(重量小于500g);需要进行电镀加工的铸件.充填时间长,充模速度慢有利于排气,但铸件表面光洁度较差.充填时间短,充速度高可以获得光洁度的铸件,但件的致密度差,组织内部气孔,蔬松较多,所以要调节选取最佳的充填时间.持压时间:即液态金属充满型腔到内浇口完全凝固,在冲头压力作用下的持续的时间.其作用是使压射冲头有足够时间将压力传给未凝固的金属,使之在压力状态下结晶并获得致密组织的铸件,一般持压时间1-4s.持压时间的长短主要取决于铸件材质和壁厚,壁厚件持压时间要长些.持压不足会造成铸件内部组织蔬松,甚至形成空洞;而对于细薄铸件,持压时间过长并无有效作用.冷却时间实际上冷却从射料一刻巳开始,这里的冷却时间仅指从压射终了到型腔打开这一段时间(一般取5~12s范围).冷却时间过短,铸件出模时间强度尚低可能会引起变形.粘模或开裂,或因为内部气孔膨胀而使表面起泡;冷却时间过长则首先影响生产效率并且因为铸件温度过低,收缩大而使脱模阻力增大,使显,出困难等.v> 脱模剂:现用锌合金脱模剂为油脂性水乳化液,原装脱模剂与水兑(比例约1:200)所得.上脱模剂方式是用喷枪或毛刷上,而喷枪喷较能保证均匀适当的用量.脱模剂有以下作用:?预防沽模,并能降低铸件表面粗适度;?避免金属液直接冲击模****表面,改善模具工作条件;?降低模具寻热率,保持金属液面的流动性能,改善合金充模性能,预防铸件过度剧冷?对活动件部位润滑作用;?减少铸件与压铸机高温条件下的磨损,延长模具寿命;2.铸件的整理工作:a) 去水口垃圾位:现时生产中常用的方法为手直接写新及用木棒敲打令其脱离铸件,这种方法的优缺点如下:优点:快捷﹑方便缺点:i.>对进水口厚的件或形状复杂的件不适用ii.>去除不整齐,有机会拉伤料位及易使工作变形.另外一种方法是用冲模冲击,操作时应注意上下模调位对正确可靠的行程限制位.其优点:i.>整齐﹑对位准确; ii.>可以击除复杂水口.缺点为:慢,操作要借助夹具,不方便.b) 清边除批锋及钻孔:采用钢挫除铸件的多余批锋,当批锋较厚时采用布轮抛光机,未碰穿或不够深的孔用钻咀来加工,非圆形则需采用冲模的方法.c) 抛光:对表面有起皮或花纹及夹模线位置用流研磨光是无法消除的,这时必须针对性将夹模线﹑起皮或花纹位置进行抛光.抛光的设备是用布轮抛光机,使用时需先在布轮四周涂上一层工业牛胶,再在牛胶粘上一层合金砂,打磨时就是利用金砂来对铸件打磨抛光.***注意:事项:抛光质量的好坏与操作工人的熟练程度有很大关系如果力度及手势不当就极易将铸件表面特别是线条凸起位磨伤.d ) 磨光及清洗:经过以上工序后,铸件表面仍残留的毛刷毛边表面气化层,残留物(合金灰)及油污需进行磨光处理(实际上几乎仍所有件需经过此工序),磨光机设备全称为「螺旋流动研磨机」,工作时通过机器的震荡,使研磨池中的小石子与铸件产生摩擦从而达到打光滑的效果,一般磨光时间需20-30分钟左右.***影响磨光效果的因素:i> 石块越细小,磨光效果越好,但生产效率太低;ii> 厉磨池需要通入不间断水流以便磨掉的污物圈水排出不会沉积于铸件之上iii> 磨光时一次加入的铸件不可太多,以免件之间碰伤,撞伤及致变形.磨光后的件即行用清水浮洗,浮洗后的件再进行烘炉的温度150℃,时间1小时左右,注意温度不能太亮,防止起泡,造成不应有的次品.五.压铸模及其对铸件质量的影响压铸模是压锛成型的母体,是压铸生产及关连的要素,压铸模设计,制造的优劣直接影响着铸件的质量.1.压铸模基本结构:压铸模由静模和动模两部分和组成,两部分合在一起组成型腔.静模上设有型腔的进料道,进料道田入料口﹑从浇口﹑横浇口及水口组成.型腔的末端是排溢槽(垃圾位).动模上设有压铸件的顶出机构以及合模时的复位机构.2.压铸模对铸件的质量影响:a)进水口设计的好坏影响到铸件表面成型沙孔﹑花纹﹑起泡等;b)分模面选取直接影响到生产加工的**.c)冷却通水系统的布置影响到模温的控制而影响到铸件的质量;d)压铸模型遣材料的硬度﹑刷度影响到铸件表面光洁度及批锋情况;e)排溢槽﹑排气位设计的位置大小也直接影响铸件的外观质量.六.压铸件的质量要求及常见缺陷的解决方法1.压铸件的质素要求:一般检查重点为外观(如造型效果﹑表面光洁度)及记位尺寸,有时根据客户要求而增加理化及机械性能(强度)或其他特殊要求.2.造成铸件缺陷的各方面原因录述:a)铸件设计不良:如出模斜度不当就不易脱模.易导致铸件顶出时变形;另外,铸件之壁厚应尽可能保持一致,转角位圆滑过度,否则会使铸件充填不良,且在厚壁产生缩孔及组蔬松.b)压铸作业工艺参数不适当:如锁模力﹑射出力不足及射出速度不适当等.或压铸温度不佳﹑时间设定不合理等等.c)模具不良:如模具精度(尺寸及零件配合)不当.冷却水道布置及大小不当.分型面设置﹑流道﹑水口之大小位置,排气道﹑垃圾位之大小及位置开设不当等等.d)(锌)合金冶炼及原料设置不适当:如溶化﹑保温未按正常程序,合金锌锭存放未能及潮防雨,对水口料未妥善处理等等.e)作业人员的技术能力不够造的原因等等.3.次品与废品:压铸件的某此缺陷是可以通进其他工艺手段如加工整形可以补救或清除的,所以有缺陷的次品并不一定就是废品,压铸的件报废标准要视铸件的具体使用技术要求而定.七.附件数据1.附件<1>----《常见铸件缺陷及其改善对策》(共2页)2.附件<2>----《压铸机开机二作指令》(共2页)附件<1>常见铸件缺陷及其改善对策一览表合金机操作说明合金压铸机是在高温度压下工作的.所以需要工模有足够温度.压铸时有足够的压力,对于压铸成形温度压力(射料)尢为重要.以下几点请各位留意:1.射料速度:射速一般分为两段.即一速和二速.一速的作用在于将料筒中的空气排出;二速的作用是填充塑腔,所以一速较慢,二速则较快大约为秒.2.模温:模具的温度是保证产品质量的一个重要条件,模温低会造成产品表面的多种缺陷.如:有冷纹﹑欠料等,所以模具正常情况时应150℃.3.料温:合金的同样溶料温度也是保证产品及正常压铸的条件.温度控制在420~450℃.4.压力压铸机中一般有两块压力表.一块是在机的尾端,它反映射料压力﹑锁模压力﹑顶针压力等.这些都是可以通过按键自赋调节的.按键上的数字是表示比例数,而不是直接读的数值.按键的调方法如下:按键是由1~99个数码进行自由调节,先将射料压力键调:任意一个数.如:AB这时我们可以在压力表中读出一射料压力.我们在将顶针压力键调至任意一个数如:CD.那提出顶针压力为CD/AB*YY,其它压力同样算法.。
压铸生产工艺
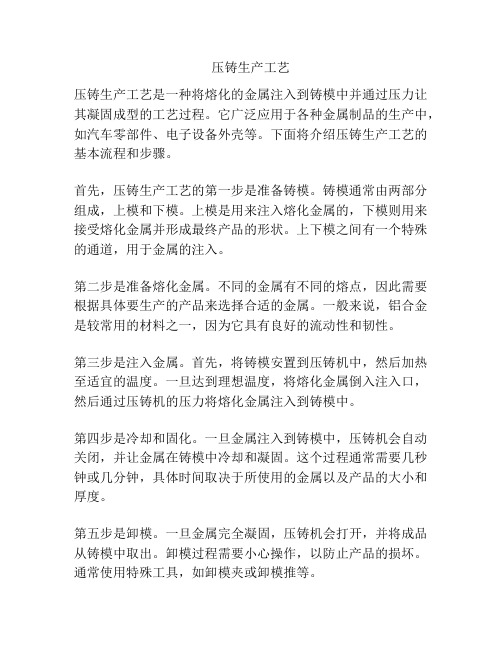
压铸生产工艺压铸生产工艺是一种将熔化的金属注入到铸模中并通过压力让其凝固成型的工艺过程。
它广泛应用于各种金属制品的生产中,如汽车零部件、电子设备外壳等。
下面将介绍压铸生产工艺的基本流程和步骤。
首先,压铸生产工艺的第一步是准备铸模。
铸模通常由两部分组成,上模和下模。
上模是用来注入熔化金属的,下模则用来接受熔化金属并形成最终产品的形状。
上下模之间有一个特殊的通道,用于金属的注入。
第二步是准备熔化金属。
不同的金属有不同的熔点,因此需要根据具体要生产的产品来选择合适的金属。
一般来说,铝合金是较常用的材料之一,因为它具有良好的流动性和韧性。
第三步是注入金属。
首先,将铸模安置到压铸机中,然后加热至适宜的温度。
一旦达到理想温度,将熔化金属倒入注入口,然后通过压铸机的压力将熔化金属注入到铸模中。
第四步是冷却和固化。
一旦金属注入到铸模中,压铸机会自动关闭,并让金属在铸模中冷却和凝固。
这个过程通常需要几秒钟或几分钟,具体时间取决于所使用的金属以及产品的大小和厚度。
第五步是卸模。
一旦金属完全凝固,压铸机会打开,并将成品从铸模中取出。
卸模过程需要小心操作,以防止产品的损坏。
通常使用特殊工具,如卸模夹或卸模推等。
第六步是后处理。
一旦成品取出,可能需要进行一些后处理操作。
例如,修剪零部件的多余材料,打磨表面,清洗,甚至涂上保护性的涂层。
这些操作可以根据具体产品的需求来决定。
最后一步是质检。
在将成品交付给客户之前,需要进行质量检查。
这包括检查产品的尺寸、外观、表面质量等。
如果存在任何问题,需要进行修复或重新生产。
总的来说,压铸生产工艺是一种高效、精确的生产方法。
它可以大量生产各种金属制品,并且具有较高的成形精度和一致性。
然而,压铸生产工艺也有一些局限性,例如制品边角处可能出现缩孔或翘曲等问题。
因此,在进行压铸生产之前,需要进行详细的工艺设计和模具制作,以确保最终产品质量的稳定性和可靠性。
压铸工艺

第三部分压铸工艺一、工艺参数1、压力参数:①压射力用压射压力和压射比压来表示,是获得组织致密、轮廓清晰的压铸件的主要因素,在压铸机上其大小可以调节。
②压射压力压射时压射油缸内的油压,可以从压力表上直接读出,是一个变量,当压铸机进入压射动作时产生压射压力,按照压射动作分段对应的称为一级压射压力(慢压射压力)、二级压射压力(快压射压力)等;增压阶段后转变为增压压力,此时的压射压力达到极大值。
③压射比压压射时压室内金属液在单位面积上所受的压力,简称比压。
可通过改变压射力或更换不同直径的压室及冲头来进行调整。
计算公式为:比压=压射力÷(冲头直径)²×4/π2、速度参数:①压射速度压射时冲头移动的速度。
按照压射过程的不同阶段,压射速度分为慢压射速度(低速压射速度)和快压射速度(高速压射速度)。
一般慢压射速度的选择根据“压室充满度”(即压室内金属液的多少,用百分比快压射速度,是在一定填充时间条件下确定的。
根据铸件的结构特征确定其填充时间后,可用以下公式进行计算:快压射速度=坯件重量/合金比重/压室内截面积/填充时间×[1+(N-1)+0.1]式中“坯件重量”含浇冒系统;“N”为型腔穴数;“填充时间”可查表得到。
按此公式计算出来的快压射速度,是获得优质铸件的理论速度,实际生产中选其1.2倍;对有较大镶嵌件的铸件时可选1.5~2倍。
②内浇口速度金属液在压力作用下通过内浇道导入型腔时的线速度,称为内浇口速度。
内浇口速度对铸件质量有着重要影响,主要是表面光洁度、强度和塑性等方面。
内浇口速度的大小可通过查表得到,调节的方法有:调整压射速度、改变压室直径、调整比压、改变内浇口截面积。
铸件平均壁厚、填充时间、内浇口速度对照表3、时间参数:①填充时间金属液自开始进入型腔到充满铸型的过程所需要的时间。
影响填充时间的因素有:金属液的过热度、浇注温度、模具温度、涂料性能与用量、排气效果等。
压铸生产工艺知识
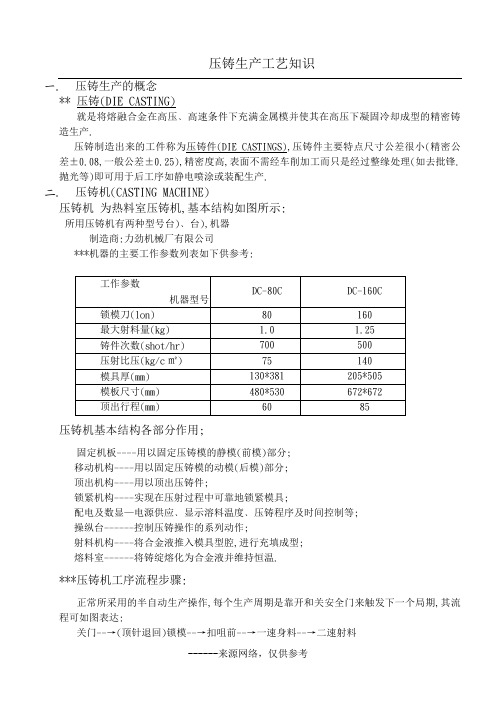
压铸生产工艺知识一.压铸生产的概念** 压铸(DIE CASTING)就是将熔融合金在高压﹑高速条件下充满金属模并使其在高压下凝固冷却成型的精密铸造生产.压铸制造出来的工件称为压铸件(DIE CASTINGS),压铸件主要特点尺寸公差很小(精密公差±0.08,一般公差±0.25),精密度高,表面不需经车削加工而只是经过整缘处理(如去批锋.抛光等)即可用于后工序如静电喷涂或装配生产.二.配电及数显—电源供应﹑显示溶料温度﹑压铸程序及时间控制等;操纵台------控制压铸操作的系列动作;射料机构----将合金液推入模具型腔,进行充填成型;熔料室------将铸绽熔化为合金液并维持恒温.***压铸机工序流程步骤:正常所采用的半自动生产操作,每个生产周期是靠开和关安全门来触发下一个局期,其流程可如图表达:关门--→(顶针退回)锁模--→扣咀前--→一速身料--→二速射料喷(刷)说模剂←--顶针顶出/钻取啤件←--开模←--离咀三. 压铸用的锌(Zinc)合金材料本公司所用皆为锌3#合金(EZDA 3PRESSURE KIECASTING ALLOY),其化学成份含量及作用如下表(见下页):a)b)c)d)a)高铸件质量,减少废品产生.3.合金溶液温度控制:锌合金在熔化时,温度在435-440℃时段为理想,温度不可超过450℃免引起其他成份下降;但如温度降低则溶化浮渣不易浮出,影响流动及使材 料强度下降.4.合金料加入熔炉注意事项:a)冷进料明,铸绽显放在盘上或其他地方充分预热才可投入; 回锤b)不可投入潮湿的铸绽或水口料,以免发生危险;c)不可投入沾有油污,杂物的铸绽或水口料,以免影响溶液质量.5.合金料的存放:应把锌绽置放在于有遮盖的地方,避免受潮,风吹雨林而便锌绽表面出现「白绣」及在投入熔炉时发生危险.四.压铸生产工艺流程内.实际上,射料的运动分三个阶级:减速--→高速--→增压,也就冲头是以越来越快的速度将熔液推型再施以持续加压.持续加压能改善溶液的结晶效果及对压铸件的冷纹和缺料方面有直接影响.当熔液冲过唧胡时的冲挚力非常大,进入模腔后为张开模力,这时机器的钻模机构必须提供大的钻模力保证模的充分垒合,否会产生批锋(飞边)等缺陷.另外要提到的一点就是射咀和唧咀的大小关系一定要相配,避免压力不或损耗压力.b) 冷却固化后,压铸机开模,在顶出机构作用下脱出铸件.刚出模的铸件温度是很高的,一般需经过浸水(个别细小件可免),水加快其冷却并能有效防上成型后的变形.C) 影响成型工艺的有关因素:包括压力﹑温度﹑速度﹑时间参数及脱模剂的影响.i) 压力:压力分为压射力和压比压,压射力是压铸机的料力(单位:顿),而压射比压是合金熔液实际得到的作用压强(单位:kg/㎝2),生产时压射比压的调节视乎铸件结构及模具情况依经验一般定在50-70kg/㎝2左右.ii) 温度:温度包括合金熔液温度和模具的工作温度(单位:℃).熔液温度一般控制在420-440℃,根据铸件情况具体做调整,如对结构复杂,薄壁的件宜选用较高的熔液温度以免造成冷痕﹑花纹﹑走料不到;而对于结构简单的厚壁件应选用较低的温度避免粘模﹑晶料粗大(可致机被强下降)且因凝固改缩大造开裂等题. 经验证明:在使用较高的压射比压情况下,适当降低的温度可以减少因体积改缩导致的组机蔬松等..充填(入水口)(重间.其冷却时间实际上冷却从射料一刻巳开始一段时间(一般取5~12s范围).冷却时间过短,铸件出模时间强度尚低可能会引起变形.粘模或开裂,或因为内部气孔膨胀而使表面起泡;冷却时间过长则首先影响生产效率并且因为铸件温度过低,收缩大而使脱模阻力增大,使显,出困难等.v> 脱模剂:现用锌合金脱模剂为油脂性水乳化液,原装脱模剂与水兑(比例约1:200)所得.上脱模剂方式是用喷枪或毛刷上,而喷枪喷较能保证均匀适当的用量.脱模剂有以下作用:?预防沽模,并能降低铸件表面粗适度;?避免金属液直接冲击模****表面,改善模具工作条件;?降低模具寻热率,保持金属液面的流动性能,改善合金充模性能,预防铸件过度剧冷?对活动件部位润滑作用;?减少铸件与压铸机高温条件下的磨损,延长模具寿命;2.铸件的整理工作:a) 去水口垃圾位:现时生产中常用的方法为手直接写新及用木棒敲打令其脱离铸件,这种方法的优缺点如下:优点:快捷﹑方便缺点:i.>对进水口厚的件或形状复杂的件不适用ii.>去除不整齐,有机会拉伤料位及易使工作变形.,未碰穿***(合金灰),,防止起泡,五.压铸模是压锛成型的母体,是压铸生产及关连的要素,压铸模设计,制造的优劣直接影响着铸件的质量.1.压铸模基本结构:压铸模由静模和动模两部分和组成,两部分合在一起组成型腔.静模上设有型腔的进料道,进料道田入料口﹑从浇口﹑横浇口及水口组成.型腔的末端是排溢槽(垃圾位).动模上设有压铸件的顶出机构以及合模时的复位机构.2.压铸模对铸件的质量影响:a)进水口设计的好坏影响到铸件表面成型沙孔﹑花纹﹑起泡等;b)分模面选取直接影响到生产加工的**.c)冷却通水系统的布置影响到模温的控制而影响到铸件的质量;d)压铸模型遣材料的硬度﹑刷度影响到铸件表面光洁度及批锋情况;e)排溢槽﹑排气位设计的位置大小也直接影响铸件的外观质量.六.压铸件的质量要求及常见缺陷的解决方法1.压铸件的质素要求:一般检查重点为外观(如造型效果﹑表面光洁度)及记位尺寸,有时根据客户要求而增加理化及机械性能(强度)或其他特殊要求.,合金机操作说明合金压铸机是在高温度压下工作的.所以需要工模有足够温度.压铸时有足够的压力,对于压铸成形温度压力(射料)尢为重要.以下几点请各位留意:1.2.:有冷纹3.4...按键那提。
压铸件工艺
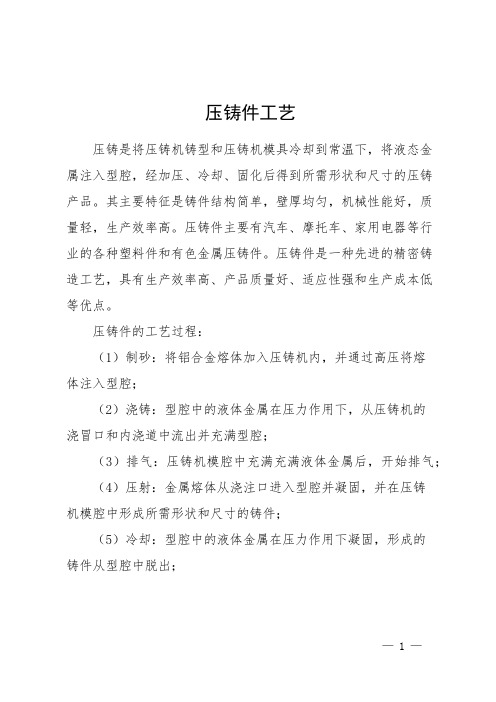
压铸件工艺
压铸是将压铸机铸型和压铸机模具冷却到常温下,将液态金属注入型腔,经加压、冷却、固化后得到所需形状和尺寸的压铸产品。
其主要特征是铸件结构简单,壁厚均匀,机械性能好,质量轻,生产效率高。
压铸件主要有汽车、摩托车、家用电器等行业的各种塑料件和有色金属压铸件。
压铸件是一种先进的精密铸造工艺,具有生产效率高、产品质量好、适应性强和生产成本低等优点。
压铸件的工艺过程:
(1)制砂:将铝合金熔体加入压铸机内,并通过高压将熔
体注入型腔;
(2)浇铸:型腔中的液体金属在压力作用下,从压铸机的
浇冒口和内浇道中流出并充满型腔;
(3)排气:压铸机模腔中充满充满液体金属后,开始排气;
(4)压射:金属熔体从浇注口进入型腔并凝固,并在压铸
机模腔中形成所需形状和尺寸的铸件;
(5)冷却:型腔中的液体金属在压力作用下凝固,形成的
铸件从型腔中脱出;
— 1 —
(6)固化:压铸件经过冷却和固化后,得到所需形状和尺寸的压铸产品。
— 2 —。
压铸的工艺流程
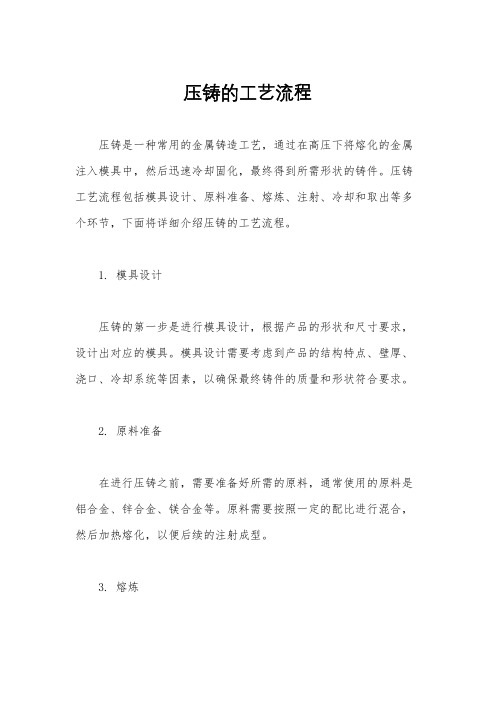
压铸的工艺流程
压铸是一种常用的金属铸造工艺,通过在高压下将熔化的金属注入模具中,然后迅速冷却固化,最终得到所需形状的铸件。
压铸工艺流程包括模具设计、原料准备、熔炼、注射、冷却和取出等多个环节,下面将详细介绍压铸的工艺流程。
1. 模具设计
压铸的第一步是进行模具设计,根据产品的形状和尺寸要求,设计出对应的模具。
模具设计需要考虑到产品的结构特点、壁厚、浇口、冷却系统等因素,以确保最终铸件的质量和形状符合要求。
2. 原料准备
在进行压铸之前,需要准备好所需的原料,通常使用的原料是铝合金、锌合金、镁合金等。
原料需要按照一定的配比进行混合,然后加热熔化,以便后续的注射成型。
3. 熔炼
熔炼是将原料加热至一定温度,使其熔化成液态金属的过程。
熔炼需要控制好温度和时间,以确保熔化后的金属质量符合要求。
4. 注射
熔化后的金属液通过注射机注入模具中,注射过程需要控制好
注射压力和速度,以确保铸件的充填和密实度。
5. 冷却
一旦金属液注入模具中,就需要迅速进行冷却,使其固化成型。
冷却过程需要通过模具内部的冷却系统来控制,以确保铸件的内部
和外部温度均匀。
6. 取出
冷却固化后,铸件可以从模具中取出,然后进行后续的去毛刺、修磨、清洗等工艺处理,最终得到符合要求的铸件成品。
以上就是压铸的工艺流程,通过模具设计、原料准备、熔炼、
注射、冷却和取出等多个环节,最终实现了对金属铸件的精确成型。
压铸工艺具有生产效率高、成本低、产品质量稳定等优点,因此在汽车、航空航天、电子等领域得到了广泛的应用。
压铸企业生产工艺

压铸企业生产工艺压铸是一种常用的金属加工方法,也是制造工业中重要的一环。
压铸企业生产工艺是指通过压铸机将金属熔化后注入模具中,经过压力和冷却后形成所需产品的过程。
下面将从模具制作、材料熔化、注入模具、冷却、脱模等方面介绍压铸企业的生产工艺。
首先,模具制作是压铸企业生产工艺中至关重要的一环。
模具的制作要根据所需产品的形状和尺寸来确定,通常采用数控加工设备来完成。
首先,需要根据产品的图纸设计出模具的结构和尺寸,然后将设计好的模具零件加工成所需形状,并进行组装。
最后,进行模具的调试和优化,以确保模具的质量和性能满足生产的要求。
其次,材料熔化是压铸企业生产工艺中的关键步骤之一。
常用的压铸材料有铝合金、镁合金、锌合金等。
首先,将适量的原料按照所需比例投放到熔炉中进行加热熔化。
材料熔化后,要通过化学分析检测保证材料的成分符合要求,然后将熔融金属倒入铸造机的溶腔中。
再次,注入模具是压铸企业生产工艺中的核心环节。
在注入模具之前,需要根据产品的形状和尺寸,确定注入过程中的注入速度和压力。
同时,要确保气体顺利排出,以免在注入过程中产生气泡。
注入模具后,需要进行适当的震动和振动处理,以确保熔融金属充分填充模具,并保证产品的密度和表面质量。
然后,冷却是压铸企业生产工艺中的重要环节。
冷却的时间和方法要根据金属的类型和产品的要求来确定。
通常,可以通过喷水冷却或者将模具放入水中冷却。
冷却过程中,要防止产生过度冷却或者过快冷却的情况,以免影响产品的质量和性能。
最后,脱模是压铸企业生产工艺中的最后一步。
脱模要根据产品的形状和结构选择适当的脱模方式。
通常,可以通过机械脱模、液压脱模或者气动脱模来完成。
脱模后,要仔细检查产品的质量和表面,确保产品的完整性和外观质量。
综上所述,压铸企业生产工艺是一个复杂的过程,涉及到模具制作、材料熔化、注入模具、冷却和脱模等多个环节。
只有在每个环节都严格控制和操作才能保证产品的质量和性能。
压铸企业需要不断优化生产工艺,在提高产品质量的同时,提高生产效率和降低生产成本。
压铸产品工艺流程及优势特点【详述】

压铸产品基本工艺流程
内容来源网络,由“深圳机械展(11万㎡,1100多家展商,超10万观众)”收集整理!更多cnc加工中心、车铣磨钻床、线切割、数控刀具工具、工业机器人、非标自动化、数字化无人工厂、精密测量、3D打印、激光切割、钣金冲压折弯、精密零件加工等展示,就在深圳机械展.
一、压铸工艺的流程为
压铸机调试——压铸模安装——模具预热、涂料——合模——浇注压射——保压——开模、抽芯取件——表面质量检查——清理——时效处理——铸件处理——终检验。
流程如图所示:
二、压铸工艺的特点
1、优点
(1)可以制造形状复杂、轮廓清晰、薄壁深腔的金属零件。
压铸件的尺寸精度较高,表面粗糙度达Ra0.8—3.2um,互换性好。
(2)材料利用率高。
由于压铸件的精度较高,只需经过少量机械加工即可装配使用,有的压铸件可直接装配使用。
生产效率高。
由于高速充型,充型时间短,金属业凝
固迅速,压铸作业循环速度快。
方便使用镶嵌件。
2、缺点
(1)由于高速填充,快速冷却,型腔中气体来不及排出,致使压铸件常有气孔及氧化夹杂物存在,从而降低了压铸件质量。
不能进行热处理。
(2)压铸机和压铸模费用昂贵,不适合小批量生产。
(3)压铸件尺寸受到限制。
压铸合金种类受到限制。
主要用来压铸锌合金、铝合金、镁合金及铜合金。
内容来源网络,由“深圳机械展(11万㎡,1100多家展商,超10万观众)”收集整理!更多cnc加工中心、车铣磨钻床、线切割、数控刀具工具、工业机器人、非标自动化、数字化无人工厂、精密测量、3D打印、激光切割、钣金冲压折弯、精密零件加工等展示,就在深圳机械展.。
- 1、下载文档前请自行甄别文档内容的完整性,平台不提供额外的编辑、内容补充、找答案等附加服务。
- 2、"仅部分预览"的文档,不可在线预览部分如存在完整性等问题,可反馈申请退款(可完整预览的文档不适用该条件!)。
- 3、如文档侵犯您的权益,请联系客服反馈,我们会尽快为您处理(人工客服工作时间:9:00-18:30)。
压铸生产工艺知识一.压铸生产的概念** 压铸(DIE CASTING)就是将熔融合金在高压﹑高速条件下充满金属模并使其在高压下凝固冷却成型的精密铸造生产.压铸制造出来的工件称为压铸件(DIE CASTINGS),压铸件主要特点尺寸公差很小(精密公差±,一般公差±,精密度高,表面不需经车削加工而只是经过整缘处理(如去批锋.抛光等)即可用于后工序如静电喷涂或装配生产.二.压铸机(CASTING MACHINE)压铸机为热料室压铸机,基本结构如图所示:所用压铸机有两种型号:台)﹑台),机器制造商:力劲机械厂有限公司.***机器的主要工作参数列表如下供参考:压铸机基本结构各部分作用;固定机板----用以固定压铸模的静模(前模)部分;移动机构----用以固定压铸模的动模(后模)部分;顶出机构----用以顶出压铸件;锁紧机构----实现在压射过程中可靠地锁紧模具;配电及数显—电源供应﹑显示溶料温度﹑压铸程序及时间控制等;操纵台------控制压铸操作的系列动作;射料机构----将合金液推入模具型腔,进行充填成型;熔料室------将铸绽熔化为合金液并维持恒温.***压铸机工序流程步骤:正常所采用的半自动生产操作,每个生产周期是靠开和关安全门来触发下一个局期,其流程可如图表达:关门--→(顶针退回)锁模--→扣咀前--→一速身料--→二速射料喷(刷)说模剂←--顶针顶出/钻取啤件←--开模←--离咀三. 压铸用的锌(Zinc)合金材料本公司所用皆为锌3#合金(EZDA 3PRESSURE KIECASTING ALLOY),其化学成份含量及作用如下表(见下页):1.锌合金主要性能特点如下:a) 熔点较低;b) 压铸成型效果好;c) 铸件表面可镀金属,可以进行(静电)喷涂装饰; d)缺点:铸件易老化,抗腐蚀能力差.2.锌合金原料中掺入水口料对铸件的影响:在锌合金压铸生产中,适当地在材料中掺入水口料可降低铸件成本,但水口料掺入也会引致某些质量问题: a)水口料中往往含有杂质,使材料机械性能变差,使铸件不能满足使用要求: b) 水口料中的化学成份巳发生变化,铝镁成份的减少会使材料理化性能变坏,从而会使铸件花纹和气泡等问题增多.如果通过化学鉴定及处理,在掺有水口料的锌合金(水口料一般不超过50%)中适当地加入铝和镁元素,并协同改善压铸模的排溢条件,选择适当的压铸参数,能够在一定程度上提高铸件质量,减少废品产生.3.合金溶液温度控制:回锤锌合金在熔化时,温度在435-440℃时段为理想,温度不可超过450℃免引起其他成份下降;但如温度降低则溶化浮渣不易浮出,影响流动及使材料强度下降.4.合金料加入熔炉注意事项:a)冷进料明,铸绽显放在盘上或其他地方充分预热才可投入;b)不可投入潮湿的铸绽或水口料,以免发生危险;c)不可投入沾有油污,杂物的铸绽或水口料,以免影响溶液质量.5.合金料的存放:应把锌绽置放在于有遮盖的地方,避免受潮,风吹雨林而便锌绽表面出现「白绣」及在投入熔炉时发生危险.四.压铸生产工艺流程***压铸生产工艺流程图:***压铸生产过程及其有关说明:压铸生产实施的基础为:a) 压铸机的功能实现及其可靠性;b) 压铸模的质量及其结构合理性;c) (锌)合金材料含量接近值及其**温度的**性﹔d) 压铸模作的技术质素等等.1.压铸表型:过程描述:a) 开动压铸机,使压铸模合理,顶杆复位并**模具,打料杆迅速下降通过中头将合金溶液通过鹅颈--→发热套--→进料道--→推入型腔,在充型时废物冷科技排在排溢位(垃圾位)内.实际上,射料的运动分三个阶级:减速--→高速--→增压,也就冲头是以越来越快的速度将熔液推型再施以持续加压.持续加压能改善溶液的结晶效果及对压铸件的冷纹和缺料方面有直接影响.当熔液冲过唧胡时的冲挚力非常大,进入模腔后为张开模力,这时机器的钻模机构必须提供大的钻模力保证模的充分垒合,否会产生批锋(飞边)等缺陷.另外要提到的一点就是射咀和唧咀的大小关系一定要相配,避免压力不或损耗压力.b) 冷却固化后,压铸机开模,在顶出机构作用下脱出铸件.刚出模的铸件温度是很高的,一般需经过浸水(个别细小件可免),水加快其冷却并能有效防上成型后的变形.C) 影响成型工艺的有关因素:包括压力﹑温度﹑速度﹑时间参数及脱模剂的影响.i) 压力:压力分为压射力和压比压,压射力是压铸机的料力(单位:顿),而压射比压是合金熔液实际得到的作用压强(单位:kg/㎝2),生产时压射比压的调节视乎铸件结构及模具情况依经验一般定在50-70kg/㎝2左右.ii) 温度:温度包括合金熔液温度和模具的工作温度(单位:℃).熔液温度一般控制在420-440℃,根据铸件情况具体做调整,如对结构复杂,薄壁的件宜选用较高的熔液温度以免造成冷痕﹑花纹﹑走料不到;而对于结构简单的厚壁件应选用较低的温度避免粘模﹑晶料粗大(可致机被强下降)且因凝固改缩大造开裂等题.经验证明:在使用较高的压射比压情况下,适当降低的温度可以减少因体积改缩导致的组机蔬松等.模具温度是通过运水冷却来控制,模具上合理的冷却运水道设计是控制好模温从而保证铸件均匀冷却的根本所在.模温一般控制在120-150℃.若模温运动部件卡死问题,同时过高的模温还使铸件冷却缓慢造成晶粒粗大而使其冲挚强度下降;若模温太低又会造成严重花纹﹑冷痕﹑甚至走料不到等问题.iii> 速度:包括合金熔液的压射速度和合金熔液对压铸的充填速度(单位:m/s).压射速度是指压射冲头运动的线速度,由机器本身决定,一般在~7m/s内变动.充填速度是指熔融触合金在压射冲头压力作用下(一般应在35-~45m/s之范围.)通过内进口(入水口)的线速度,根据流量连续原理,可知充填速度成正比,而与内浇口截面积成反比.射速利用流量阀控制,速度切换由慢快--→高速,最后施以增压iv> 时间:包括充模时间,持续庇压时间和冷却留模时间(单位:s).充模时间:金属液自进入模具型腔至充满所需时间,适当的填模时间为~.注:压铸以下铸件时,填模时间问题小于或等于:薄铸件(厚度小于1mm);轻铸件(重量小于500g);需要进行电镀加工的铸件.充填时间长,充模速度慢有利于排气,但铸件表面光洁度较差.充填时间短,充速度高可以获得光洁度的铸件,但件的致密度差,组织内部气孔,蔬松较多,所以要调节选取最佳的充填时间.持压时间:即液态金属充满型腔到内浇口完全凝固,在冲头压力作用下的持续的时间.其作用是使压射冲头有足够时间将压力传给未凝固的金属,使之在压力状态下结晶并获得致密组织的铸件,一般持压时间1-4s.持压时间的长短主要取决于铸件材质和壁厚,壁厚件持压时间要长些.持压不足会造成铸件内部组织蔬松,甚至形成空洞;而对于细薄铸件,持压时间过长并无有效作用.冷却时间实际上冷却从射料一刻巳开始,这里的冷却时间仅指从压射终了到型腔打开这一段时间(一般取5~12s范围).冷却时间过短,铸件出模时间强度尚低可能会引起变形.粘模或开裂,或因为内部气孔膨胀而使表面起泡;冷却时间过长则首先影响生产效率并且因为铸件温度过低,收缩大而使脱模阻力增大,使显,出困难等.v> 脱模剂:现用锌合金脱模剂为油脂性水乳化液,原装脱模剂与水兑(比例约1:200)所得.上脱模剂方式是用喷枪或毛刷上,而喷枪喷较能保证均匀适当的用量.脱模剂有以下作用:预防沽模,并能降低铸件表面粗适度;避免金属液直接冲击模****表面,改善模具工作条件;降低模具寻热率,保持金属液面的流动性能,改善合金充模性能,预防铸件过度剧冷对活动件部位润滑作用;减少铸件与压铸机高温条件下的磨损,延长模具寿命;2.铸件的整理工作:a) 去水口垃圾位:现时生产中常用的方法为手直接写新及用木棒敲打令其脱离铸件,这种方法的优缺点如下:优点:快捷﹑方便缺点:i.>对进水口厚的件或形状复杂的件不适用ii.>去除不整齐,有机会拉伤料位及易使工作变形.另外一种方法是用冲模冲击,操作时应注意上下模调位对正确可靠的行程限制位.其优点:i.>整齐﹑对位准确; ii.>可以击除复杂水口.缺点为:慢,操作要借助夹具,不方便.b) 清边除批锋及钻孔:采用钢挫除铸件的多余批锋,当批锋较厚时采用布轮抛光机,未碰穿或不够深的孔用钻咀来加工,非圆形则需采用冲模的方法.c) 抛光:对表面有起皮或花纹及夹模线位置用流研磨光是无法消除的,这时必须针对性将夹模线﹑起皮或花纹位置进行抛光.抛光的设备是用布轮抛光机,使用时需先在布轮四周涂上一层工业牛胶,再在牛胶粘上一层合金砂,打磨时就是利用金砂来对铸件打磨抛光.***注意:事项:抛光质量的好坏与操作工人的熟练程度有很大关系如果力度及手势不当就极易将铸件表面特别是线条凸起位磨伤.d ) 磨光及清洗:经过以上工序后,铸件表面仍残留的毛刷毛边表面气化层,残留物(合金灰)及油污需进行磨光处理(实际上几乎仍所有件需经过此工序),磨光机设备全称为「螺旋流动研磨机」,工作时通过机器的震荡,使研磨池中的小石子与铸件产生摩擦从而达到打光滑的效果,一般磨光时间需20-30分钟左右.***影响磨光效果的因素:i> 石块越细小,磨光效果越好,但生产效率太低;ii> 厉磨池需要通入不间断水流以便磨掉的污物圈水排出不会沉积于铸件之上iii> 磨光时一次加入的铸件不可太多,以免件之间碰伤,撞伤及致变形.磨光后的件即行用清水浮洗,浮洗后的件再进行烘炉的温度150℃,时间1小时左右,注意温度不能太亮,防止起泡,造成不应有的次品.五.压铸模及其对铸件质量的影响压铸模是压锛成型的母体,是压铸生产及关连的要素,压铸模设计,制造的优劣直接影响着铸件的质量.1.压铸模基本结构:压铸模由静模和动模两部分和组成,两部分合在一起组成型腔.静模上设有型腔的进料道,进料道田入料口﹑从浇口﹑横浇口及水口组成.型腔的末端是排溢槽(垃圾位).动模上设有压铸件的顶出机构以及合模时的复位机构.2.压铸模对铸件的质量影响:a)进水口设计的好坏影响到铸件表面成型沙孔﹑花纹﹑起泡等;b)分模面选取直接影响到生产加工的**.c)冷却通水系统的布置影响到模温的控制而影响到铸件的质量;d)压铸模型遣材料的硬度﹑刷度影响到铸件表面光洁度及批锋情况;e)排溢槽﹑排气位设计的位置大小也直接影响铸件的外观质量.六.压铸件的质量要求及常见缺陷的解决方法1.压铸件的质素要求:一般检查重点为外观(如造型效果﹑表面光洁度)及记位尺寸,有时根据客户要求而增加理化及机械性能(强度)或其他特殊要求.2.造成铸件缺陷的各方面原因录述:a)铸件设计不良:如出模斜度不当就不易脱模.易导致铸件顶出时变形;另外,铸件之壁厚应尽可能保持一致,转角位圆滑过度,否则会使铸件充填不良,且在厚壁产生缩孔及组蔬松.b)压铸作业工艺参数不适当:如锁模力﹑射出力不足及射出速度不适当等.或压铸温度不佳﹑时间设定不合理等等.c)模具不良:如模具精度(尺寸及零件配合)不当.冷却水道布置及大小不当.分型面设置﹑流道﹑水口之大小位置,排气道﹑垃圾位之大小及位置开设不当等等.d)(锌)合金冶炼及原料设置不适当:如溶化﹑保温未按正常程序,合金锌锭存放未能及潮防雨,对水口料未妥善处理等等.e)作业人员的技术能力不够造的原因等等.3.次品与废品:压铸件的某此缺陷是可以通进其他工艺手段如加工整形可以补救或清除的,所以有缺陷的次品并不一定就是废品,压铸的件报废标准要视铸件的具体使用技术要求而定.七.附件数据1.附件<1>----《常见铸件缺陷及其改善对策》(共2页)2.附件<2>----《压铸机开机二作指令》(共2页)附件<1>常见铸件缺陷及其改善对策一览表合金机操作说明合金压铸机是在高温度压下工作的.所以需要工模有足够温度.压铸时有足够的压力,对于压铸成形温度压力(射料)尢为重要.以下几点请各位留意:1.射料速度:射速一般分为两段.即一速和二速.一速的作用在于将料筒中的空气排出;二速的作用是填充塑腔,所以一速较慢,二速则较快大约为秒.2.模温:模具的温度是保证产品质量的一个重要条件,模温低会造成产品表面的多种缺陷.如:有冷纹﹑欠料等,所以模具正常情况时应150℃.3.料温:合金的同样溶料温度也是保证产品及正常压铸的条件.温度控制在420~450℃.4.压力压铸机中一般有两块压力表.一块是在机的尾端,它反映射料压力﹑锁模压力﹑顶针压力等.这些都是可以通过按键自赋调节的.按键上的数字是表示比例数,而不是直接读的数值.按键的调方法如下:按键是由1~99个数码进行自由调节,先将射料压力键调:任意一个数.如:AB 这时我们可以在压力表中读出一射料压力.我们在将顶针压力键调至任意一个数如:CD.那提出顶针压力为CD/AB*YY,其它压力同样算法.。