精密铸造铸件工艺及浇冒口系统设计
《冒口系统设计》课件
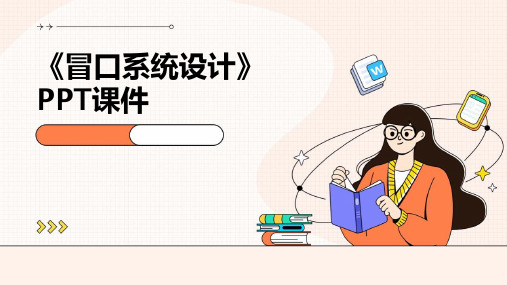
冒口系统是铸造工艺中的重要组成部分,其主要作用是容纳多余的金属液体。一个完整的冒口系统通 常包括冒口本身、溢流槽和保温材料等部分。冒口的设计应考虑金属液的容量、模具的冷却速度等因 素。溢流槽的作用是将多余的金属液引入冒口,保温材料则用于保持金属液的温度。
冒口系统的分类
要点一
总结词
根据用途和结构,冒口系统可分为热冒口和冷冒口两类。
压接焊
通过施加压力使两个金属表面紧密接触,然后加热熔化表面层, 形成连接。
钎焊
使用熔点低于母材的钎料作为填充金属,将母材加热至钎料熔化 ,然后冷却凝固形成连接。
热处理工艺
退火
将金属加热至高温并保持一段时 间,然后缓慢冷却至室温,以消 除内应力、提高塑性和韧性。
正火
将金属加热至高温并保持一段时 间,然后快速冷却至室温,以细 化晶粒、提高强度和韧性。
环保性原则要求在选择冒口材料时,要优先选择可再生、 可回收、低污染的材料,同时还要考虑到冒口系统的冷却 方式、废弃物的处理方式等因素,以实现绿色铸造的目标 。
03 冒口系统设计流程
需求分析
需求调研
深入了解用户需求,明确设计目标, 收集相关数据和信息。
需求整理
对收集到的需Байду номын сангаас进行分类、筛选和整 理,形成详细的需求文档。
方案制定
方案构思
根据需求分析结果,初步拟定设计方 案,包括功能模块、界面布局等。
方案评审
邀请专家或团队成员对方案进行评审 ,提出改进意见,完善设计方案。
详细设计
界面设计
根据方案制定界面风格、色彩搭配、图标和按钮 等视觉元素。
交互设计
确定各个功能模块的交互流程、操作方式和反馈 机制。
精密铸造铸件工艺与浇冒口系统设计
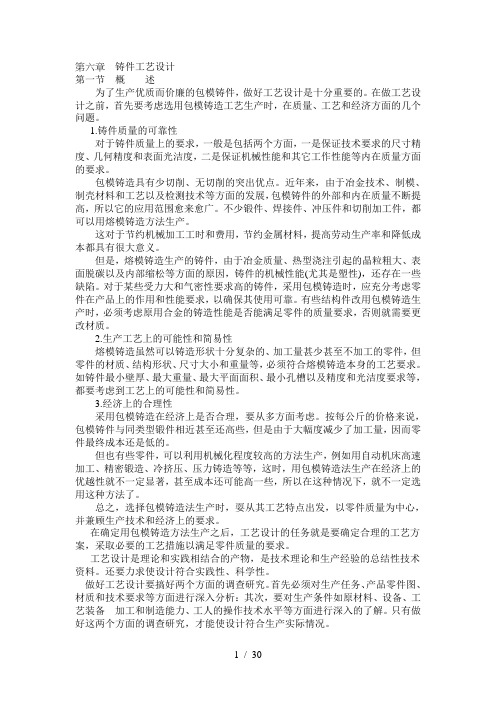
第六章铸件工艺设计第一节概述为了生产优质而价廉的包模铸件,做好工艺设计是十分重要的。
在做工艺设计之前,首先要考虑选用包模铸造工艺生产时,在质量、工艺和经济方面的几个问题。
1.铸件质量的可靠性对于铸件质量上的要求,一般是包括两个方面,一是保证技术要求的尺寸精度、几何精度和表面光洁度,二是保证机械性能和其它工作性能等内在质量方面的要求。
包模铸造具有少切削、无切削的突出优点。
近年来,由于冶金技术、制模、制壳材料和工艺以及检测技术等方面的发展,包模铸件的外部和内在质量不断提高,所以它的应用范围愈来愈广。
不少锻件、焊接件、冲压件和切削加工件,都可以用熔模铸造方法生产。
这对于节约机械加工工时和费用,节约金属材料,提高劳动生产率和降低成本都具有很大意义。
但是,熔模铸造生产的铸件,由于冶金质量、热型浇注引起的晶粒粗大、表面脱碳以及内部缩松等方面的原因,铸件的机械性能(尤其是塑性),还存在一些缺陷。
对于某些受力大和气密性要求高的铸件,采用包模铸造时,应充分考虑零件在产品上的作用和性能要求,以确保其使用可靠。
有些结构件改用包模铸造生产时,必须考虑原用合金的铸造性能是否能满足零件的质量要求,否则就需要更改材质。
2.生产工艺上的可能性和简易性熔模铸造虽然可以铸造形状十分复杂的、加工量甚少甚至不加工的零件,但零件的材质、结构形状、尺寸大小和重量等,必须符合熔模铸造本身的工艺要求。
如铸件最小壁厚、最大重量、最大平面面积、最小孔槽以及精度和光洁度要求等,都要考虑到工艺上的可能性和简易性。
3.经济上的合理性采用包模铸造在经济上是否合理,要从多方面考虑。
按每公斤的价格来说,包模铸件与同类型锻件相近甚至还高些,但是由于大幅度减少了加工量,因而零件最终成本还是低的。
但也有些零件,可以利用机械化程度较高的方法生产,例如用自动机床高速加工、精密锻造、冷挤压、压力铸造等等,这时,用包模铸造法生产在经济上的优越性就不一定显著,甚至成本还可能高一些,所以在这种情况下,就不一定选用这种方法了。
最新冒口系统设计

Mr=1.2Mc=2.3cm
查标准圆柱形暗冒口表:当Mr=2.38cm, 收缩 率为5%、每个暗冒口能补缩的最大铸件体积 为 4.1L ( 重 量 32kg ) 时 , 冒 口 的 尺 寸 为 ¢ 120mm×188mm(h) (h=1.5d) 。 可 见 设 计一个冒口已经足够。
冒口系统设计
一、冒口的作用
为了使铸件在凝固的最后阶段得到补缩,防 止缩孔、缩松、裂纹、变形等产生,则在铸件上 设置冒口。
冒口-储备足量的液态金属,又可排气、集 渣。铸造合金凝固时,均产生体积收缩,凝固后 均会形成孔洞-缩孔、缩松。
三、冒口的设计原则 (一)设置冒口的必要性
(二)、冒口位置选择原则
(2)冒口要能根据设计的要求提供足够的 金属来补偿铸件的液态收缩,凝固收缩以及 由于型腔扩大而增加的体积。而且要力求铸 件的成品率高。
(3)冒口和铸件受补缩部位之间,要保持 一定的温度梯度和凝固梯度,以保证补缩通 道畅通。
(五)校验方向性(顺序)凝固和多冒口的 综合效果
由于冒口的有无及其位置、大小等将直接 影响铸件的温度场,从而影响凝固的进行状 态。此外,在多冒口的情况下还有可能发生 相互间的干扰。因此需要校验是否不产生缺 陷。
3-3冒口的设计及计算
以铸钢件冒口设计为主,凡实行顺序凝 固的一切合金铸件均适用。 冒口的设计: 凝固时间原则:模数法 几何关系原则:缩管法
热节圆法
(一)模数法
模数:体积和散热表面积的比值称模数
M=V/A 其中:M - 模数(m);
V - 铸件体积(m3) A - 散热表面积(m2)
模数法:根据铸件凝固理论,铸件凝固时间决定于 它的体积和表面积的比值,即铸件的模数。M小的 铸件凝固时间短;M大的铸件凝固时间长,模数方 法计算冒口尺寸就是建立在模数的基础之上。
铸造工艺学冒口设计
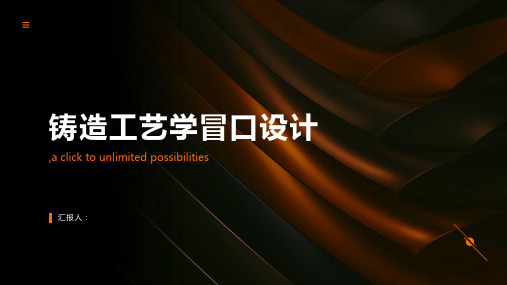
铸造工艺学是一门 研究金属材料成型 规律和工艺方法的 科学
铸造工艺学涉及到 金属材料的性能、 组织结构、成分和 加工方法等方面
铸造工艺学是机械 制造领域中重要的 分支之一
铸造工艺学在汽车 、航空航天、能源 等领域有着广泛的 应用
铸造工艺学的研究对象和内容
添加标题
研究对象:铸造工艺学是研究铸造生产过程及其相关技术的一门学科,包括铸造材料、铸造设备、铸造工 艺等方面的内容。
置,以获得最佳补缩效果
注意浇注温度对冒口的影响
浇注温度过低可能导致冒口 补缩不足,产生缩孔、缩松 等缺陷
合适的浇注温度需要根据合 金种类、铸件结构、浇注系
统等因素固,影响补缩效果
在实际生产中,可以通过调 整浇注温度来优化冒口设计,
提高铸件质量
注意浇注时间对冒口的影响
优化冒口位置: 将冒口设置在 铸件的非重要 部位或应力集 中区域,以减 少后续加工或 修复工作量。
考虑环保因素: 选择环保型冒 口材料,减少 废弃物对环境 的影响,降低
处理成本。
05 冒口设计的具体方法
确定冒口的位置
确定冒口的位置:根据铸件的结构和尺寸,选择合适的冒口位置,以保证铸件的质量和生产效 率。
球墨铸铁材质的冒口设计实例
材质特性:球墨铸 铁具有高强度、高 韧性、耐磨性等特 点
冒口设计原则:根 据铸造工艺要求, 确定冒口的位置、 大小和形状
实例分析:以某实 际生产中的球墨铸 铁零件为例,详细 介绍冒口的设计过 程和优化方案
效果评估:通过对 比分析,阐述优化 后的冒口设计对提 高铸件质量、降低 废品率等方面的作 用
添加 标题
壁厚对冒口尺寸的影响:壁厚越大,需要的 冒口体积也越大,以补偿铸件凝固过程中的 收缩。
第三、四章 浇冒口系统的设计

1
1
2 h
A阻
有效
4、上层内浇口面积 A内(上) = 1~2 A内(底)
湖北汽车工业学院材料工程系 Department of Materials Engineering
小结—浇注系统设计步骤
选择浇注系统类型;
确定内浇道在铸件上的位置、数目和金属引入方 向; 决定直浇道高度(一般取决于砂箱高度); 计算浇注时间并核算金属在型内的上升速度; 计算阻流(最小)截面积; 确定组元截面积比; 于铸造工艺上绘制浇注系统结构及组元截面图。
3)核算金属液在型腔中的液面上升速度
型内金属液面在型腔中的上升速度过低可能形成氧化膜 或结壳,易产生冷隔;铸件顶面和侧壁易出现夹砂等缺陷。内铸铁液最小上升速度
型内铸钢液最小上升速度
湖北汽车工业学院材料工程系 Department of Materials Engineering
Department of Materials Engineering
第二节 浇注系统的计算
1、 奥赞(Osann)公式
—阻流(最小)截面积 的计算 。
阻流(最小)组元指浇 注系统中最小截面积的浇道, 一般为内浇道,即 m A阻= 2 gHp
H P H0 P
2
2C
湖北汽车工业学院材料工程系 Department of Materials Engineering
4)流量系数μ的确定
铸铁件流量系数
球墨铸铁件流量系数
铸钢件流量系数
湖北汽车工业学院材料工程系 Department of Materials Engineering
2、垂直分型面浇注系统的计算
技术难点是各层铸件充型 压力不一致,底层压力比顶层 压力大好几倍。怎么办呢?
铸造工艺学冒口设计方案

保温作用:冒口可 以减缓铸件凝固速 度,提高铸件质量
冒口的设计原则
保证补缩量:根据铸件的结 构、尺寸、壁厚等确定冒口 的补缩量
便于操作:冒口的位置应便 于操作,以便于浇注和清理
减少金属消耗:在保证补缩 量的前提下,尽量减少冒口 的金属消耗
避免形成热节:冒口的设计 应避免形成热节,以防止铸 件产生缩孔和缩松等缺陷
计算法
冒口体积计算 冒口直径计算 冒口高度计算 冒口材料选择
实验法
实验目的:确定最 佳冒口尺寸和位置
实验步骤:设计多 种方案,进行实际 铸造实验
实验结果:观察铸 件质量,分析实验 数据
结论:根据实验结 果,确定最佳冒口 设计方案
05 冒口的设计优化
减小冒口体积
优化冒口结构: 采用合理的冒 口结构,如分 片式、组合式 等,以减
冒口的设计原则: 根据铸件的结构、 尺寸、材质等因 素进行设计
冒口的设计方法: 根据铸造工艺学 原理,采用合适 的冒口尺寸、形 状和位置
冒口设计的实际 应用:在铸铁件 生产中,根据实 际情况选择合适 的冒口设计方案, 提高铸件质量和 生产效率
铝合金铸件的冒口设计
口体积
降低冒口高度: 通过减小冒口 高度,减少冒 口体积,同时 保证补缩效果
减小冒口直径: 采用较小的冒 口直径,以减 小冒口体积, 同时保证补缩
效果
改进冒口材料: 采用轻质、高 强度、低热膨 胀系数的材料 制作冒口,以 减小冒口体积
提高冒口补缩效率
确定冒口的位置和数量 选择合适的冒口类型 优化冒口尺寸和形状 控制冒口补缩时间
铸造工艺学冒口设计 方案
,a click to unlimited possibilities
汇报人:
铸造工艺学-冒口设计

顶冒口, M r (1.2 1)MC
2 检验冒口提供足够的金属液够不够
(V V ) V V
c
r
e
r
式中 ε 金属从浇注完到凝固完毕的体收缩率,η 冒口的 补缩效率。η=(补缩体积/冒口体积)。
通常用上式来校核冒口的尺寸够不够。
ε、η对冒口体积的影响
模数的计算
模数:又称为铸 件折算厚度.
M=V/A =体积/散热面积
1 简单几何体 模数的计算
29
2 相交节点的模数计算
a)测量法
测量出热节中心处的凝 固时间和平壁中心处的凝 固时间 ,用下式计算
T M
பைடு நூலகம்
j
2
式中,T--平板壁厚;
j--热节中心处凝固时间;
--平壁中心处凝固时间。
b)一倍厚度法
以相交的地方为基 准,分别向外移动一倍 的板宽的长度,得图中 阴影部分;然后用阴影 部分的模数,作为热节
38
(2)轮毂冒口计算 把轮毂看作长方形断面的杆,用类似的方法计算.该
补缩节点的热节圆直径为50mm.于是50mmˣ1.1=55mm,计算得, Mc=5.5ˣ12.7/2ˣ(5.5+12.7)=1.92cm
Mr=1.2Mc=2.30cm 查标准圆柱形冒口表,当Mr=2.38cm收缩率5%每个冒口能补缩最大 铸件体积为4.2L(质量32kg)时,冒口尺寸Φ120mmˣ180mm (h=1.5d)。可见设置一个冒口已足够。
的材料(如铸铁、石墨或铸钢等)作为冷铁。 12
2 冒口位置的选择原则
① 在热节的上方或侧旁;
② 尽量在铸件最高、最厚部位, 低处热结设补贴或冷铁;
第2章石膏型精密铸造1

硬脂酸 60~40 60~40
松香 30~20 30~20
石蜡 5~20 5~20
褐煤蜡 5~20 5~20
EVA 1~5 1~5
聚苯乙烯 —
10~30
表2-2 48#及48T#的某些性能
性能 滴点 软化点 线收 缩率
模料 (℃) (℃) (%)
抗弯 强度 (MPa)
热稳定 性40℃ /2h (mm)
4、石膏型透气性极差,要合理设置浇注系统及 排气系统,防止浇不足、气孔等缺陷。
5、石膏型的耐火度低,故适于生产铝、锌、铜、 金和银等合金的精密复杂铸件。
2.1.3应用范围 石膏型精密铸造适于生产精密铸件,特别适宜 生产大型复杂薄壁铝合金铸件。 该法已被广泛用于航空、宇航、兵器、电子、 船舶、仪器、计算机等行业的零件制造中,也常 用于艺术品铸造中。
典型铸件
波音767飞机 燃油增压泵壳体 材质:365铝合金
(美国牌号) 重量:63kg
雷达用波导管 材质:铝合金 铸件要求: 内通道精度要求高, 表面粗糙度:
Ra =1.6 μm。
叶轮 材质:铝合金 尺寸:外径尺寸
25~900mm, 最小壁厚0.5mm 铸件要求: 表面粗糙度: Ra=1.6~3.2μm。
镁合金
1.2
1.6
锰黄铜 1.8~2.0 2.0~2.3
石膏型精密铸件的综合收缩率A可按下式计算:
A% (a c d)%
三、铸造斜度 石膏型精密铸件的铸造斜度可参考熔模铸造斜 度。
2.2.3浇注系统及冒口设计 石膏型精密铸件浇注系统及冒口设计可参考熔
模铸造或砂型铸造。应注意以下几点: 1、石膏导热性差,金属液保持流动时间长, 故浇注系统截面积尺寸可比砂型铸造减少 20%左右。
铸造工艺图及设计实例

在保证产品质量的前提下,尽量减少不必要的生 产环节,降低成本。
提高材料利用率
合理规划铸件结构和浇注系统,减少材料浪费, 提高材料利用率。
引入智能化技术
利用先进的铸造模拟软件和智能化设备,提高铸 造工艺图的准确性和可靠性。
铸造工艺图的未来发展趋势
绿色铸造
随着环保意识的提高,未来铸造工艺图将更加注重环保和节能, 减少对环境的负面影响。
熟练掌握所选软件的基本操作和功能是进 行铸造工艺图设计的前提条件。
参考实例和教程
不断实践和总结经验
通过参考实例和教程可以快速掌握软件的 使用技巧和方法,提高设计效率。
通过不断实践和总结经验可以逐步提高铸 造工艺图设计的水平,提升设计质量和效 率。
THANKS
谢谢您的观看
Autodesk Inventor
一款专业的机械设计软件,提供全面的铸造工艺 图设计功能,支持参数化设计和协同工作。
3
ProCAST
一款专业的铸造工艺模拟软件,可进行铸造工艺 图设计和模拟分析,提高铸造工艺设计的准确性 和可靠性。
通用的CAD软件在铸造工艺图绘制中的应用
AutoCAD
一款通用的CAD软件,广泛应用于铸造工艺图绘制,支持二维和三维建模,提供丰富的绘图工具和编辑功能。
作用
铸造工艺图是铸造生产的基础,它为 生产人员提供了明确的工艺指导和要 求,确保铸造产品的质量和生产的顺 利进行。
铸造工艺图的绘制流程
确定产品需求
明确产品的尺寸、重 量、材料等要求。
产品分解
将产品分解成多个铸 造部分,确定每个部 分的功能和要求。
设计浇注系统
根据产品特点和生产 要求,设计合适的浇 注系统,确保金属液 能够顺利填充型腔。
铝合金砂型铸造案例分析- 浇冒口系统设计

接下来,使用冒口设计向导(Riser Design Wizard)确定每个补缩区的冒口 大小。冒口尺寸是根据模数(冒口模数必 要大于铸件模数)和补缩量(冒口必须提 供足够的补缩量,以补充合金的液态收缩
和凝固收缩)确定的。
假设,我们需要一个冒口补两件,则调整 冒口尺寸以提供两个铸件的补缩量。
及最大出品率的冒口尺寸。
联系方式 天津富宇创想科技有限公司
公司网站:
行分析,得到铸件模数*。根据模数就可以
知道铸件每部分的凝固顺序,并用来确定冒 口或浇口放置的最佳位置及给冒口尺寸。
*注: 传统的模数定义为——体积:表面积,SOLIDCast使用的是热 模数,这比传统的方法要准确的多。
铸件上的模数分布
冒口设计向导(Riser Design Wizard)通 过分析铸件上的模数分布,给出推荐的冒
口数量,放置位置及冒口大小。
冒口设计向导(Riser Design Wizard)开始界面
推荐冒口数量
接下来,使用X射线透视方式观察铸件,分 析铸件上的高模数位置,理论上每个位置
都需要放置一个冒口进行补缩。
主补缩区
次补缩区
接下来一系列的图片显示的是SOLIDCast 推荐的主补缩区最佳冒口放置点,也就是
接下来,确定次补缩区-小冒口的大小。
冒口 2 推荐直径1.5英寸X 高3英寸
冒口3 尺寸相同,直径1.5英寸X 高3英寸
接下来,使用浇注系统设计向导(Gating Design Wizard™)确定最优浇注时间,
直浇道、横浇道及内浇口尺寸
最优浇注时间
直浇道形状 浇口位置
浇注系统截面比
直浇道直径
铸件上的缩松(弥散的缩松)分布
精密铸造介绍
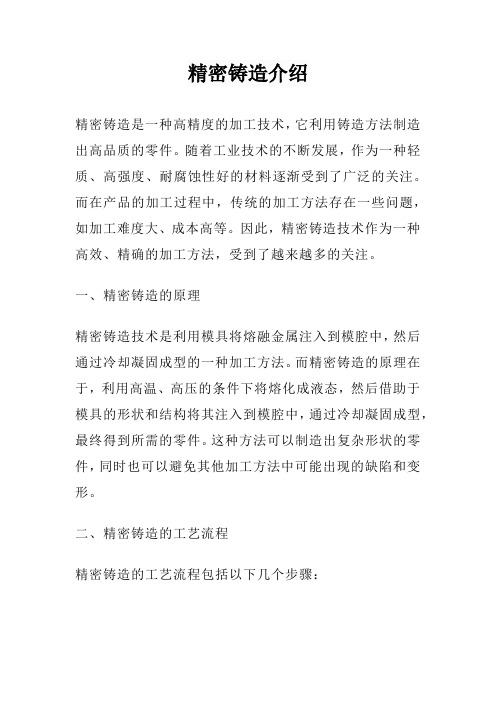
精密铸造介绍精密铸造是一种高精度的加工技术,它利用铸造方法制造出高品质的零件。
随着工业技术的不断发展,作为一种轻质、高强度、耐腐蚀性好的材料逐渐受到了广泛的关注。
而在产品的加工过程中,传统的加工方法存在一些问题,如加工难度大、成本高等。
因此,精密铸造技术作为一种高效、精确的加工方法,受到了越来越多的关注。
一、精密铸造的原理精密铸造技术是利用模具将熔融金属注入到模腔中,然后通过冷却凝固成型的一种加工方法。
而精密铸造的原理在于,利用高温、高压的条件下将熔化成液态,然后借助于模具的形状和结构将其注入到模腔中,通过冷却凝固成型,最终得到所需的零件。
这种方法可以制造出复杂形状的零件,同时也可以避免其他加工方法中可能出现的缺陷和变形。
二、精密铸造的工艺流程精密铸造的工艺流程包括以下几个步骤:A:模具制备:根据所需的零件的形状和尺寸,制作相应的模具。
B:材料准备:将材料按照一定比例混合并加热熔化。
C:浇注:将熔化的液体借助于浇口注入到模具中。
D:冷却凝固:待液体冷却凝固后,将模具打开,取出所需零件。
E:后处理:对所得到的零件进行后处理,如去毛刺、抛光等。
三、精密铸造的应用领域精密铸造技术应用广泛,可用于航空航天、汽车、医疗器械、电子产品等领域。
例如,精密铸造技术可用于制作航空发动机叶轮、汽车发动机零件、医疗器械等高精度零件,具有较大的市场前景。
四、精密铸造的优势和限制A:精密铸造技术具有以下优势:1、精密铸造提供了特殊的设计灵活性,复杂、精密的部件可以被浇铸成接近成品的形状。
它在熔模铸造材料方面提供了几乎无限的自由度。
广泛的适应性,不受铸件尺寸、厚度和形状复杂性的限制。
还可以将商标、名称或数字等符号特征直接铸造在产品上。
2、各种材料都可以用于精密铸造。
这些材料包括不锈钢、碳钢、低碳合金钢、铜、铝、铁、钴等。
因此,由精密铸造工艺生产的铸件可用于各种行业。
3、精密铸造可以应用于各个行业。
主要用于航空航天、发电、枪械、汽车、军事、商业、食品服务、天然气和石油以及能源行业。
铸造CAD-CAE智能冒口工艺优化设计

铸造CAD/CAE智能冒口工艺优化设计2010-10-29 23:15:39 作者:廖敦明,陈立亮,周建新,魏鹏程,龚雪丹来源:互联网基于华铸CAE和UG平台,开发了铸造CAD/CAE铸钢件智能冒口优化设计CAD系统,实现铸造工艺设计(CAD)与模拟仿真(CAE)的紧密结合。
首先,使用CAE模拟得到不带冒口工艺的铸钢件的孤立液相区信息;接着应用二次开发技术,在UG显示孤立液相区,然后结合周界商法,自动建立冒口的三维模型;最后以简单铸件为例,进行了实际浇注实验.设计结果基本合理。
系统实现了冒口工艺的自动设计。
为模拟验证乃至实际生产提供较佳的推荐方案。
该技术能提高冒口工艺设计效率与精度,缩短设计周期,保证产品质量.提高工艺出品率。
铸造凝固模拟(CAE)技术可以在铸件实际浇注前对多个铸造工艺方案进行验证,预测缩孔、缩松、卷气、夹杂、裂纹、应力集中等常见铸造缺陷,为优化铸造工艺提供参考。
因为CAE的前提是必须要有一个初始工艺方案,所以目前CAE的作用还基本体现在对已有工艺方案的验证,不能智能地设计铸造工艺。
一个合理的铸造工艺依赖工艺人员丰富的专业知识和宝贵的经验,而对经验不足者,很难在短时间内得到合理的工艺方案。
即便借助CAE软件,由于对模拟显示结果的理解程度不同,基于模拟结果进行工艺优化的能力也因人而异。
专业技能知识,现场经验积累、软件的正确使用和熟练程度等,都决定了凝固模拟(CAE)与工艺优化设计(CAD)的有效衔接。
本研究以铸钢件的冒口智能优化为突破口,结合CAE模拟得到的铸件孤立液相区信息与周界商法,进行了铸钢件冒口的自动优化设计研究,实现了CAD与CAE 的耦合,开发出了一套基于UG(UniGraphics)和孤立液相区的铸钢件智能冒口优化设计系统。
1 智能化冒口工艺设计路线冒口的选择是铸造工艺设计中非常重要的一部分,同时是铸造工艺设计的难点所在。
常用的冒口设计方法包括模数法、补缩液量法、比例法、Q参数法、三次方程法、周界商法。
铝合金低压铸造浇暗冒口设计-概述说明以及解释
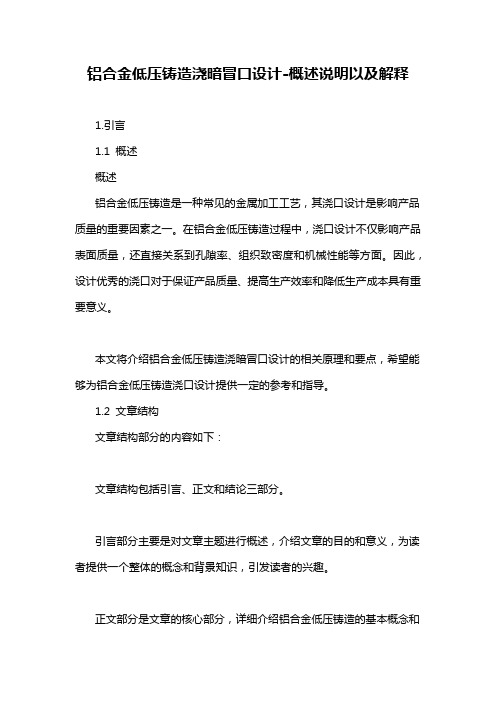
铝合金低压铸造浇暗冒口设计-概述说明以及解释1.引言1.1 概述概述铝合金低压铸造是一种常见的金属加工工艺,其浇口设计是影响产品质量的重要因素之一。
在铝合金低压铸造过程中,浇口设计不仅影响产品表面质量,还直接关系到孔隙率、组织致密度和机械性能等方面。
因此,设计优秀的浇口对于保证产品质量、提高生产效率和降低生产成本具有重要意义。
本文将介绍铝合金低压铸造浇暗冒口设计的相关原理和要点,希望能够为铝合金低压铸造浇口设计提供一定的参考和指导。
1.2 文章结构文章结构部分的内容如下:文章结构包括引言、正文和结论三部分。
引言部分主要是对文章主题进行概述,介绍文章的目的和意义,为读者提供一个整体的概念和背景知识,引发读者的兴趣。
正文部分是文章的核心部分,详细介绍铝合金低压铸造的基本概念和浇口设计原理,重点阐述低压铸造浇暗冒口设计的要点,包括设计原则、方法和注意事项等内容。
结论部分是对文章内容的总结和归纳,提出设计建议和展望未来的发展方向,为读者提供一个全面的结论和展望。
1.3 目的:本文旨在探讨铝合金低压铸造中浇暗冒口设计的重要性及设计要点,旨在帮助读者更好地了解低压铸造中浇口设计的原理及实践操作。
通过深入分析和总结,为相关从业人员提供参考,以便他们在实际生产过程中能够更有效地设计和应用适合的浇口方案,提高铝合金低压铸造产品的质量和生产效率。
同时,也旨在促进铝合金低压铸造技术的进一步发展和提升。
2.正文2.1 铝合金低压铸造简介铝合金低压铸造是一种常用的金属铸造工艺,其特点是在铸造过程中施加一定程度的压力。
通过施加压力,可以有效减少铸件表面气孔和缩松,提高铸件的密度和机械性能。
铝合金是一种轻质、耐腐蚀性强的金属材料,被广泛应用于汽车、航空航天等领域。
在低压铸造过程中,铝合金材料先被加热至熔化状态,然后通过特定的浇注系统注入到金属模具中。
在注入过程中,施加一定的压力使铝合金充分填充模具腔体,并通过凝固后的收缩力来实现压力浇铸。
先进低成本的铸件浇冒系统设计方法

先进低本钱的铸件浇冒系统设计方法徐志安1,凌勇1,Ilse Evenepoel1,臧桂铭2,左绪娟2〔1.SIRRIS比利时国家工业技术研究所,比利时,根特9052;2.济南玫德铸造,山东济南250400〕摘要:用实例介绍了一项用于铸造生产的三维模拟技术,通过对铸件充型和凝固过程的数值模拟帮助铸造技术人员进行铸造工艺设计,从而在计算机上实现可视铸造过程,能保证既快又省地设计一个优化的铸造工艺。
与传统的模数法,经验和试错的工艺设计不同,本模型是用铸件的凝固时间计算补缩系统。
从一个铸件凝固模拟开始,根据凝固时间和被补缩的体积,计算冒口和冒口颈的尺寸和数量,再进行铸件加冒口的模拟计算,做必要的修正,直到获得满意的结果,最后根据铸件的临界壁厚,体积,充型速度和浇注温度等参数计算浇注系统。
当整个系统设计完成后,模拟计算整个充型和凝固过程以验证设计,做必要的修正,直到获得一个能生产无铸造缺陷铸件的铸造工艺,即保证一次成功生产出合格铸件,节约了时间和本钱。
关键词:模拟;浇冒系统;凝固时间;中图分类号:文献标识码:文章编号:An Advanced and Cost-Saving Method for Designing A Gating and feeding System ofCastingsXU Zhi-an1, LING Yong1, Ilse Evenepoel1, ZANG Gui-ming2, ZUO Xu-juan2(1.Sirris,Belgian Research Centre of the Technological Industry Technolgiepark919, Zwijnaarde9052, Belgium; 2.Jinan Meide Casting Co.,LTD, 250400 Jinan, Shandong, China)Abstract: This paper describes a 3-D simulation technology that assists foundry engineers in designing the feeding and gating systems, and simulates mould filling as well as solidification. While the traditional design was based upon pen and paper calculations (modulus), experience and guesses, this technology enables to conduct a fast and inexpensive virtual design and verify the effect of any change, resulting in an optimal casting configuration. T he underlying model is based upon the solidification time of the casting to calculate the feeding system. First of all, the solidification of the cast product only is simulated. Based on the solidification time and the volume to be fed, the feeding system is proposed by the calculation. Then, the proposed feeding system is taken into account in the simulation and if necessary, the feeding system can be modified until a satisfied designing is obtained. Finally the gating system is calculated depending on the volume of the casting, including the risers, the critical wall thickness of the cast product and the pouring temperature.When the complete casting system has been designed, mould filling and solidification simulation are started to validate the design, and execute necessary modifications until a defect free casting is achieved. The technology enables leading foundries to produce first time right castings on a daily base. An industrial case clearly illustrates how time, money and energy can be saved using this casting simulation technology.Key words: simulation; gating and feeding System; solidification time铸造过程包括了流体流动,传热传质和相变的复杂过程。
铸造CAD-CAE智能冒口工艺优化设计

铸造CAD/CAE智能冒口工艺优化设计2010-10-29 23:15:39 作者:廖敦明,陈立亮,周建新,魏鹏程,龚雪丹来源:互联网基于华铸CAE和UG平台,开发了铸造CAD/CAE铸钢件智能冒口优化设计CAD系统,实现铸造工艺设计(CAD)与模拟仿真(CAE)的紧密结合。
首先,使用CAE模拟得到不带冒口工艺的铸钢件的孤立液相区信息;接着应用二次开发技术,在UG显示孤立液相区,然后结合周界商法,自动建立冒口的三维模型;最后以简单铸件为例,进行了实际浇注实验.设计结果基本合理。
系统实现了冒口工艺的自动设计。
为模拟验证乃至实际生产提供较佳的推荐方案。
该技术能提高冒口工艺设计效率与精度,缩短设计周期,保证产品质量.提高工艺出品率。
铸造凝固模拟(CAE)技术可以在铸件实际浇注前对多个铸造工艺方案进行验证,预测缩孔、缩松、卷气、夹杂、裂纹、应力集中等常见铸造缺陷,为优化铸造工艺提供参考。
因为CAE的前提是必须要有一个初始工艺方案,所以目前CAE的作用还基本体现在对已有工艺方案的验证,不能智能地设计铸造工艺。
一个合理的铸造工艺依赖工艺人员丰富的专业知识和宝贵的经验,而对经验不足者,很难在短时间内得到合理的工艺方案。
即便借助CAE软件,由于对模拟显示结果的理解程度不同,基于模拟结果进行工艺优化的能力也因人而异。
专业技能知识,现场经验积累、软件的正确使用和熟练程度等,都决定了凝固模拟(CAE)与工艺优化设计(CAD)的有效衔接。
本研究以铸钢件的冒口智能优化为突破口,结合CAE模拟得到的铸件孤立液相区信息与周界商法,进行了铸钢件冒口的自动优化设计研究,实现了CAD与CAE 的耦合,开发出了一套基于UG(UniGraphics)和孤立液相区的铸钢件智能冒口优化设计系统。
1 智能化冒口工艺设计路线冒口的选择是铸造工艺设计中非常重要的一部分,同时是铸造工艺设计的难点所在。
常用的冒口设计方法包括模数法、补缩液量法、比例法、Q参数法、三次方程法、周界商法。
- 1、下载文档前请自行甄别文档内容的完整性,平台不提供额外的编辑、内容补充、找答案等附加服务。
- 2、"仅部分预览"的文档,不可在线预览部分如存在完整性等问题,可反馈申请退款(可完整预览的文档不适用该条件!)。
- 3、如文档侵犯您的权益,请联系客服反馈,我们会尽快为您处理(人工客服工作时间:9:00-18:30)。
第六章铸件工艺设计第一节概述为了生产优质而价廉的包模铸件,做好工艺设计是十分重要的。
在做工艺设计之前,首先要考虑选用包模铸造工艺生产时,在质量、工艺和经济方面的几个问题。
1.铸件质量的可靠性对于铸件质量上的要求,一般是包括两个方面,一是保证技术要求的尺寸精度、几何精度和表面光洁度,二是保证机械性能和其它工作性能等内在质量方面的要求。
包模铸造具有少切削、无切削的突出优点。
近年来,由于冶金技术、制模、制壳材料和工艺以及检测技术等方面的发展,包模铸件的外部和内在质量不断提高,所以它的应用范围愈来愈广。
不少锻件、焊接件、冲压件和切削加工件,都可以用熔模铸造方法生产。
这对于节约机械加工工时和费用,节约金属材料,提高劳动生产率和降低成本都具有很大意义。
但是,熔模铸造生产的铸件,由于冶金质量、热型浇注引起的晶粒粗大、表面脱碳以及内部缩松等方面的原因,铸件的机械性能(尤其是塑性),还存在一些缺陷。
对于某些受力大和气密性要求高的铸件,采用包模铸造时,应充分考虑零件在产品上的作用和性能要求,以确保其使用可靠。
有些结构件改用包模铸造生产时,必须考虑原用合金的铸造性能是否能满足零件的质量要求,否则就需要更改材质。
2.生产工艺上的可能性和简易性熔模铸造虽然可以铸造形状十分复杂的、加工量甚少甚至不加工的零件,但零件的材质、结构形状、尺寸大小和重量等,必须符合熔模铸造本身的工艺要求。
如铸件最小壁厚、最大重量、最大平面面积、最小孔槽以及精度和光洁度要求等,都要考虑到工艺上的可能性和简易性。
3.经济上的合理性采用包模铸造在经济上是否合理,要从多方面考虑。
按每公斤的价格来说,包模铸件与同类型锻件相近甚至还高些,但是由于大幅度减少了加工量,因而零件最终成本还是低的。
但也有些零件,可以利用机械化程度较高的方法生产,例如用自动机床高速加工、精密锻造、冷挤压、压力铸造等等,这时,用包模铸造法生产在经济上的优越性就不一定显著,甚至成本还可能高一些,所以在这种情况下,就不一定选用这种方法了。
总之,选择包模铸造法生产时,耍从其工艺特点出发,以零件质量为中心,并兼顾生产技术和经济上的要求。
在确定用包模铸造方法生产之后,工艺设计的任务就是要确定合理的工艺方案,采取必要的工艺措施以满足零件质量的要求。
工艺设计是理论和实践相结合的产物,是技术理论和生产经验的总结性技术资料。
还要力求使设计符合实践性、科学性。
做好工艺设计要搞好两个方面的调查研究。
首先必须对生产任务、产品零件图、材质和技术要求等方面进行深入分析:其次,要对生产条件如原材料、设备、工艺装备加工和制造能力、工人的操作技术水平等方面进行深入的了解。
只有做好这两个方面的调查研究,才能使设计符合生产实际情况。
工艺设计的好坏也要从质量、工艺和经济这三方面去衡量。
一项良好的工艺设计应当能在正常的生产条件下,稳定铸件质量,简化生产工艺,效率高而成本低。
熔模铸造工艺设计通常包括下列几项内容,(1).分析铸件结构工艺性, (2)确定工艺方案和工艺参数,(3)设计浇冒口系统, (4)绘制工艺图或铸件图。
第二节铸件结构工艺性分析铸件结构工艺性对于零件质量,生产工艺的可能性和简易性以及生产成本等影响很大。
结构工艺性不好的铸件,往往孕育着产生缺陷和废品的可能性,也会增加制造成本。
所以,做工艺设计时,首先要审查零件图,审查的目的有二:一是审查零件结构设计是否符合包模铸造的生产特点,对于那些设计不合理的部分进行修改。
第二个目的是根据已定的零件结构和技术要求,采取相应措施以保证质量。
根据熔模铸造生产特点,零件结构工艺性要考虑以下要求。
1)经济性在精密铸造的生产中,其蜡型是。
在包模铸造上,金属模的目的是在在射蜡机中,利用压力将液态、糊态或半固态的蜡‧挤射入金属模内,生产蜡型或塑料型,这些型是用来生产陶瓷模的,不论是实体模或型壳模。
所有的模型都是可逝性的。
在制模的关键性问题上,是如何将蜡型或塑料型从模具中取出,以及如何将芯子从模型中取出等。
至于其它的制模问题,用于砂模铸造的原理同样适用于包模铸造图2 铸件内角的重设计(2)在图1中,一个包模铸件因为内图1 铸件内角的重设计(1) 部有一圆角,而且需要用两个抽芯,A及B两个芯子进出的方向如图1(a) 所示,要想将有倒钩的芯子抽出而又不伤损工件是根本不可能。
于是,重新设计工件,如图1(b),将内圆角取消,以避开这种芯子有倒钩无法抽出的困绕。
倘若要生产原设计有内圆角的工件,惟有舍弃金属抽芯,而用成本较高的水溶性芯子,随同蜡型一起自模中取出,再用酸蚀及水溶法将芯子自蜡型中除去,如此可保持工件的内圆角而又不会损伤蜡型。
图2系一个有弧形通道的工件,同样如图2(a) 的设计也无法用金属抽芯来制模,若改为图2(b) 的设计,将内圆角改为尖角,则可以用两支抽芯做出弧形通道的内孔。
图3刀具余隙的再设计为了后继的加工,往往在工件设计时,一般为避免撞机的困绕,预先留有一个让出刀具到位时的间隙,如图3(a) 所示,但无法抽出金属芯子,若改为图3(b)的设计,就可以用金属抽芯直接做出刀具余隙。
另外如图4(a)之原始设计虽然内孔通道很圆滑,但必须要用较昂贵的水溶性芯子或陶瓷芯子,而且,在铸造后,清除孔道中陶瓷材料非常困难,若改为(b)的设计,可直接由六个金属抽芯来射制蜡型,另在一图4内孔通道的再设计个多出的孔洞则可在铸件完成后再设法塞上或焊死。
可大幅度提高生产效率及降低成本。
2).现实性精密铸造与其它的制造方法一样,有其一定的极限,因此,在铸件精度的考虑上,应面对现实,设计可以达得到的标准,否则,良品率太低,就丧失了用精密铸造降低生产成本,提高生产效率的目的了。
当铸件芯子部位因受炽热的金属围绕,内外部份的散热状况不一致,内部陶瓷受高温而膨胀,但外部因有金属包覆又无法自由伸展,陶瓷材料因而有强烈的弯曲变形的应力,此时,外部热的不均匀分布,芯部自然向高温部分扭曲变形,便使铸件的壁厚产生了不均匀的结果。
其变其设计通则:内孔的长度in. 壁厚的公差in.<22~4>4±0.005±0.010±0.0123)铸造性a) 壁薄的包模铸件包模铸造工艺几乎制造任何金属的复杂铸件,也可以在小零件的设计及生产上,有助于达到轻薄短小的目的,获得最大的强度重量比值。
在设计最小壁厚时,金属熔液的流动性是一个非常重要的考虑因素,因为它直接影响到金属液对模穴充填的能力。
几乎同等重要的另一要素,是熔液在充填模穴时,金属液的浇注补充距离,以及铸件表面积之大小,金属的凝固状况,固、液相线的差异度,都归纳于铸造性中,尤其对薄壁铸件特别重要。
可铸出的最小壁厚与合金种类、浇注工艺方法、以及铸件的轮廓尺寸等因素有关。
表 2列举的是121in.长管件对各种金属包模铸件之最小壁厚。
其实这些数值并不是真正的最小壁厚,诚如前述,金属液的浇注过热温度、浇注速率、壳模预热温度、铸件的形状及薄壁部分的表面积等都会影响最小壁厚的尺寸,这个表中之建议值为工业生产上的经验值。
在这个标准下生产,良品率最好,亦即浇不足及微缩孔的现象最少。
在Fig. 7 的上图表显示一个在最小厚度与最大长度的相互关系,而下图表则显示在铸件有通孔或盲孔时,孔径与孔深的关系。
因为铸造过程尚有许多参数会影响其最大值与最小值,但此数值仍有其参考价值。
虽然熔融金属液是浇注入已预热的型壳,但是它仍然可能如同其它的铸造工艺一样,在金属充满薄壁部分之前,先行凝固。
当有高的面积与厚度比值时,会促使金属液快速冷却及凝固,不论如何,金属液在充满模穴的过程中,所需行进的距离必须要特别注意,虽然在同样的面积与厚度比值,且厚度相同时,若要完全注满1/2in. 宽、2in. 长的模穴,自然比注满2in. 宽、1/2in. 长的模穴要难得多。
浇注温度在某一特定厚度铸件及金属上,往往选择可能状况下以较低的温度,以期避免诸如气孔,夹渣、模壁反应及其它因温度过高而产生的铸疵。
不过在浇注薄件时,为求延长金属液在注满模穴的过程中开始凝固的时间,往往还是以提高模温及金属液温来达到目的。
通常, 较低的模温因为可以加速金属液的凝固,可以减少模壁反应,而有较好的表面光洁度,在薄壁铸件生产时,则为了能使金属液充分浇满型壳,祇有牺牲表面质量,而提高模温。
在生产高尔夫球之不锈钢金属木杆头(metal-wood )时因表面积很大且厚度绝大部分仅有0.030 in.,许多厂家在没有改变浇道系统的设计情况下,为了避免金属 最小壁厚 in. 碳钢 0.060 300系不锈钢 0.050 400系不锈钢 0.065 铝合金 0.050 镁合金 0.050 铝青铜(10%Al) 0.060 铍铜 0.040 钴-铬合金 0.050表2 121in.长管件对各种金属之最小壁厚浇不足,而一味的提高钢水温度(超出熔点约300℃)及型壳的预热温度(约1400℃),结果,浇不足的情况有明显的改善,但微缩孔一堆及因型壳超温软化变形而铸件厚度大于蜡件厚度的情况层出不穷,笔者在改正浇道系统,增大浇注速率,缩短浇注补充距离后,钢水温度降低了100℃,型壳预热温度保持在1150℃(低于硅氧胶的软化点),同样可铸满,而又不会有微缩孔及变形增加厚度的缺陷。
b)壁的连接当两壁相接便会产生图中所示的热截圆的变化,d大于a,b,c,换言之,就是d处热储量最大,凝固最慢,因此,在d处自然在没有冒口补充的情况下,非常容易产生缩孔。
在实际生产时,我们常常为了减弱两壁相接处的热点效应,任意加大该处内圆角(Fillet)的r,热点问题是解决了,但相对的增大热截图的直径,使缩孔移向铸件的内部,严重时甚至于会产生表面凹陷的现象。
如今将在生产上常会碰到的两壁相交的情况列举于图中,并提出改正的设计建议。
铸件壁厚设计要力求均匀,减少热节。
图6-1所示为重7.5公斤的壳体铸件,原设计如a图所示,在A、B、C、D、E、F五处壁过厚,易形成各种铸造缺陷。
后改成b图所示,即将上述五处壁厚减薄,形'成6~7mm壁厚的箱形结构。
ψ9D 及ψ17D o两孔铸出以消除该处热节。
F孔不铸,浇口设在此处。
修改后铸件壁厚均匀,重量减轻至2.3kg。
壁的交接处要做出圆角,不同壁厚间要均匀过渡,这是防止熔模和铸件产生变形和裂纹的重要条件。
图6-2所示为铸件壁的几种常用连接形式及其相关尺寸。
二、平面熔模铸件要尽可能避免大的平面,因为大平,干面上极易产生夹砂、凹陷、桔皮、蠕虫状铁刺等表面缺陷,所以铸件上的平面一般应小于200×200mm有大平面的铸件最好设计成曲面或阶梯形平面,或在平面上开设工艺槽、工艺筋、工艺孔等,以防止涂料堆积和型壳的分层、鼓胀。
图6-3所示零件在A、B、C处均有大平面,C处有盲孔。
在制壳流水在线生产时,几个平面均易产生缺陷,而且肓孔处在上涂料、撒砂和硬化时均感不便,铸件废品率较高.。