丙烯羰基合成生产丁辛醇
有机化工-丁辛醇-工艺流程

体循环使用,液体经稳定塔处理将其中的气体驰放后,再经异构物分离塔除 去异丁醛;正丁醛塔除去重组分而从塔顶获得正丁醛产品。 2.正丁醛的加氢和缩合生产丁辛醇: 正丁醇的生产可直接加氢后经精馏而获得。辛醇则需要先经缩合再加氢而得 到。(现以辛醇的生产为例介绍) 正丁醛送入缩合反应器中,反应在氢氧化钠下发生缩合和脱水,反应生成辛 烯醛水溶液经冷却后进入分离器利用密度差分为油层和水层。水层送碱性污 水池处理。
一、丁辛醇的生产方法:
1、发酵法: 以粮食为原料,由丙酮-丁醇菌为发酵剂而得。该法设备简单,投资
少,但消耗粮食太多。 2、醇醛缩合法:
以乙醛为原料经缩合、酸化、蒸馏、脱水成为丁烯醛,再经催化加氢 得正丁醇。此法操作压力低,无异构体产生,但流程长、步骤多、设 备腐蚀严重,总收率低,目前只有少数工厂采用此法生产。 3、雷普法:
主要原因。同时用膦化物取代络合物中的羰基配位体,可提高
催化剂的热稳定性,并使正构醛含量增加,还可降低反应中所
需的压力。
(二)工艺条件:
1.反应温度: 钴413~453K, 铑373~383K 温度升高,反应速率加
快,生产能力提高但正、 异构体比例却随之降低, 副反应加剧,选择性下 降,催化剂失活速率加 快。
以丙烯、一氧化碳和水为原料,在催化剂五羰基化铁的作用下,一 步合成丁醇。此法产品单一,灵活性差而没有得到广泛应用。 4、共聚法:
用两种低级烯烃共聚生成高碳的烯烃,然后以此进行羰基合成而获 得辛醇。特点:组成复杂,产品不纯,异构物较多。 5.丙烯羰基合成法:
以丙烯和合成气为原料在催化剂作用下进行羰基化反应生成脂肪醛, 再经加氢、蒸馏而得产品。特点:灵活性好,反应速度快,产品收每 高,环境污染少而得到广泛应用。
低压羰基合成丁辛醇工艺技术

低压羰基合成丁辛醇工艺技术摘要:低压羰基合成法是目前生产丁辛醇的主要方法。
世界上羰基合成丁醛装置中,低压羰基合成工艺技术占55%。
丁辛醇装置以丙烯、合成气为原料,采用Davy/DOW低压羰基合成工艺技术生产2-乙基己醇和正丁醇,同时副产异丁醇,设计年运行时间为8000小时,操作弹性为60%~110%。
关键词:低压羰基;丁辛醇;工艺技术;分析引言:丁辛醇装置采用世界较为先进的LP OxoSM SELECTORSM 10液体循环技术,生产2-乙基己醇(俗称辛醇)和正丁醇,它以丙烯和合成气为原料,在铑、三苯基膦催化剂的作用下,发生羰基合成反应生成混合丁醛,丁醛经过丁醛异构物分离得到高纯度正丁醛,在0.2×10-2mol的NaOH溶液作用下,发生缩合反应生成辛烯醛,辛烯醛在铜催化剂作用下与H2发生加氢反应生成粗辛醇,再经过精制后得到产品辛醇;混合丁醛加氢后得到粗混合丁醇,经过预精馏和精馏系统进入丁醇异构物塔。
丁醇异构物塔顶分离出的混合丁醛也可直接进行异构物分离得到正丁醛和异丁醛,异丁醛直接外送至界外,正丁醛经加氢、精制后,得到产品正丁醇。
1.低压羰基合成丁辛醇技术七十年代中期,美国UCC公司、英国DAVY公司和J.M公司合作开发了铑膦催化体系─低压羰基合成工艺。
压力1.6-1.8MPa,正异比高达10:1~12:1,基建投资和生产成本均低于高、中压羰基合成技术。
1.1气相法将催化剂加入并联的两台反应器中,丙烯、合成气按一定比例分别从反应器和分馏塔底部进入。
产品由循环气带出,经冷凝、分离后,由分馏塔底部采出,过量气体循环进入反应系统,催化剂留在反应器内直至失效取出再生。
因该羰基合成反应为气相反应,故称气相法。
1.2液相法液相法是以丙烯、合成气为原料,以铑为催化剂生产丁辛醇的低压羰基合成法,是低压羰基合成的进一步改进。
其优点是:一是反应器容积小,产率高;二是原料单耗降低;三是成本及能耗降低;四是催化剂使用形式为活性循环型;五是反应温度低,可用于生产高碳醇。
丁辛醇生产技术及投资分析

丁辛醇生产技术及投资分析摘要:丁辛醇生产技术主要有乙醛缩合法、发酵法、齐格勒法和羰基合成法,羰基合成法中的液相循环低压铑法是当今世界最先进、最广泛使用的丁辛醇合成技术。
丁辛醇主要用于增塑剂,广泛用于各种塑料和橡胶制品的生产,目前全球丁辛醇的生产消费情况供需基本趋于平衡,我国的进口量较大,但近年陆续有多套装置投产,丁辛醇项目的投资属于稳健的大宗产品投资。
关键词:正丁醇,异丁醇,辛醇,羰基合成法,铑催化剂丙烯含有十分活泼的双键,因而化学活性高,反应性强。
丙烯在进行聚合、烃化(烷基化)、水合、氧化、氯化、氨氧化、羰基化以及齐聚等反应后,可以得到一系列重要而实用的丙烯衍生物。
丙烯已成为最主要的石油化工基础原料,其使用的广泛性和市场价格已超过乙烯,石化企业都想方设法围绕丙烯做扩大产业链的文章。
巴陵石化在化工项目的规划中拟建35万吨/年丁辛醇装置,将从外部获取21万吨/年丙烯资源。
本文通过介绍丁辛醇的生产技术及市场,达到知己知彼的作用。
1、丁辛醇的基本性质丁辛醇是重要的基本有机化工原料,它有三个重要的品种:正丁醇、异丁醇、辛醇(或称2-乙基己醇)。
正丁醇主要用于制造邻苯二甲酸二丁酯(DBP)和脂肪族二元酸酯类(邻苯二甲酸丁苄酯,BBP)增塑剂,广泛用于各种塑料和橡胶制品的生产,也是制造丁醛、丁酸、丁胺和乳酸丁酯等有机化合物的原料,是树脂、油漆、粘接剂的溶剂及选矿用的消泡剂,也可做油脂、药物(如抗菌素、激素和维生素)和香料的萃取剂及醇酸树脂涂料的添加剂等。
异丁醇主要用于生产乙酸异丁酯、丁酸异丁酯、乳酸异丁酯、苯二甲酸异丁酯、柠檬酸三异丁酯;人造革、织物、涂料等的复合溶剂;硝化纤维棉、醋酸纤维素;石油添加剂;少量异丁醇用于医药,如麻醉剂(氨基甲酸异丁酯)和人造麝香的合成。
辛醇主要用于生产邻苯二甲酸二辛酯(DOP)、己二酸二辛酯(DOA)、对苯二甲酸二辛酯(DOTP)等增塑剂,DOP产品素有王牌增塑剂之称,广泛用于聚氯乙烯、合成橡胶、纤维素脂的加工等。
丁辛醇生产工艺
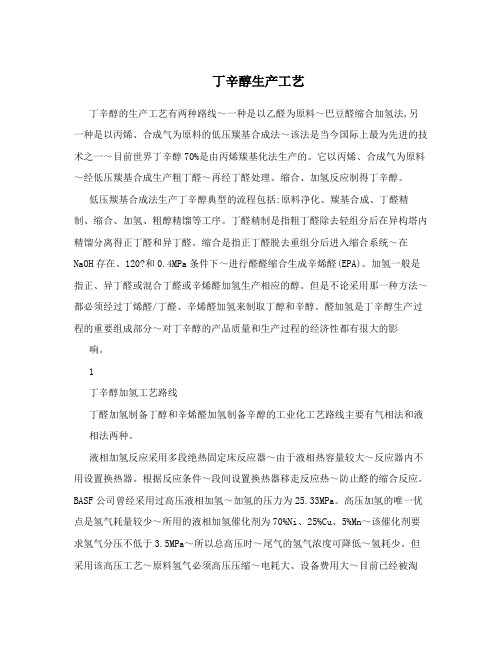
丁辛醇生产工艺丁辛醇的生产工艺有两种路线~一种是以乙醛为原料~巴豆醛缩合加氢法,另一种是以丙烯、合成气为原料的低压羰基合成法~该法是当今国际上最为先进的技术之一~目前世界丁辛醇70%是由丙烯羰基化法生产的。
它以丙烯、合成气为原料~经低压羰基合成生产粗丁醛~再经丁醛处理、缩合、加氢反应制得丁辛醇。
低压羰基合成法生产丁辛醇典型的流程包括:原料净化、羰基合成、丁醛精制、缩合、加氢、粗醇精馏等工序。
丁醛精制是指粗丁醛除去轻组分后在异构塔内精馏分离得正丁醛和异丁醛。
缩合是指正丁醛脱去重组分后进入缩合系统~在NaOH存在、120?和0.4MPa条件下~进行醛醛缩合生成辛烯醛(EPA)。
加氢一般是指正、异丁醛或混合丁醛或辛烯醛加氢生产相应的醇。
但是不论采用那一种方法~都必须经过丁烯醛/丁醛、辛烯醛加氢来制取丁醇和辛醇。
醛加氢是丁辛醇生产过程的重要组成部分~对丁辛醇的产品质量和生产过程的经济性都有很大的影响。
1丁辛醇加氢工艺路线丁醛加氢制备丁醇和辛烯醛加氢制备辛醇的工业化工艺路线主要有气相法和液相法两种。
液相加氢反应采用多段绝热固定床反应器~由于液相热容量较大~反应器内不用设置换热器。
根据反应条件~段间设置换热器移走反应热~防止醛的缩合反应。
BASF公司曾经采用过高压液相加氢~加氢的压力为25.33MPa。
高压加氢的唯一优点是氢气耗量较少~所用的液相加氢催化剂为70%Ni、25%Cu、5%Mn~该催化剂要求氢气分压不低于3.5MPa~所以总高压时~尾气的氢气浓度可降低~氢耗少。
但采用该高压工艺~原料氢气必须高压压缩~电耗大、设备费用大~目前已经被淘汰。
BASF公司和三菱化成工艺中醛的加氢采用中压液相加氢工艺~加氢压力为4.0-5.0MPa~加氢反应器形式采用填充床~反应温度为60-190?。
气相加氢法由于操作压力相对较低~工艺设备简单而被广泛应用。
目前~工业上丁辛醇装置上大多采用铜系催化剂气相加氢工艺。
如U.D.J联合工艺中采用低压气相加氢~压力为0.59-0.69MPa。
丁辛醇生产技术及发展

"!
2003 年第 26 卷第 1 期 化工科技市场
由于发酵法及乙醛法工艺流程长,设备腐蚀严 重,极不经济,现有装置已基本淘汰。当今丁辛醇生 产的主要方法是以丙烯为原料的羰基合成法。以丙 烯为原料的羰基合成法又分为高压钴法、改性铑法、 高压铑法和改性铑法。其中改性铑法是当代丁辛醇 合成技术的主流。改性铑法又分为气相循环和液相 循环两种方法。液相循环改性铑法是当今世界最先 进、最广泛使用的丁辛醇合成技术。
HRhCOL3 三苯基磷 丁醛、高沸物
~ 2.0 ~ l00 (9 ~ 8)= l
鼓泡塔式
高 较高
低 较高 较长 较多 不需要
小
三菱化成
鲁尔
丙烯,CO,H2 R(h OAC)(TPP)3
三苯基磷
丙烯,CO,H2 醋酸铑
三苯基磷三磺酸钠盐
甲苯
水
连续补充,废催化剂
连续排放每年废催化 每年就地回收再利用
剂送催化剂制造厂回收
2.2 国内发展概况 我国的丁辛醇生产技术在 1980 年以前主要采 用粮食发酵法制丁醇;采用乙醛缩合制巴豆醛(丁烯 醛),巴豆醛缩合、加氢制辛醇。由于工艺技术落后, 这一类的丁辛醇生产装置均已停产。 1976 年,吉化公司从德国 BASF 公司引进 50 kt / a 年的高压钴法丁辛醇装置,1982 年建成投产。随 后,大庆石化总厂、齐鲁石化公司从英国 DAVY 公司 成套引进丁辛醇生产技术,并在 1986 年、1987 年相 继投产。 1992 年北京化工四厂从日本三菱化学公司引进 丁辛醇生产的专利技术及关键设备,于 1996 年投 产。 1996 年齐鲁石化公司在原有装置基础上,将原 来低压羰基合成气相循环法改为液相循环法,在反 应器不变的情况下,将产量扩大为原产量的 1 . 9 倍。 1998 年吉化公司对原有的 BASF 高压羰基合成装置 进行改造,引进了 UCC / DAVY 第四代低压液相循环 羰基合成技术,在保留了原装置的异构物分离、丁醛 缩合、辛烯醛液相加氢、醇的精馏分离等几部分基础 上,另外扩建了一套气相加氢、丁醛缩合、液相加氢、 醇精馏分离系统,改造后装置于 2000 年 8 月投产, 目前吉化公司丁醇、辛醇合计最大生产能力可达 120 kt / a。 3 丁辛醇生产技术概况 丁辛醇的生产工艺有两种路线,一种是以乙醛 为原料,巴豆醛缩合加氢法;另一种是以丙烯为原料 的羰基合成法,
低压羰基合成丁辛醇工艺技术王琪

低压羰基合成丁辛醇工艺技术王琪发布时间:2021-09-23T08:13:01.767Z 来源:《中国科技人才》2021年第16期作者:王琪[导读] 作为化工生产中的基础性化工材料之一,丁辛醇可用于橡胶制品生产环节,可作为增塑剂使用,也属于良好的脱水剂与消泡剂,还具备溶剂的功能。
在丁辛醇生产过程中,主要应用的是低压羰基合成技术。
文章将以低压羰基合成技术的分析入手,分别对其三种合成方法进行阐述,而后概述了当前我国丁辛醇工艺技术的发展状况,并展望了未来丁辛醇生产工艺的发展方向。
大庆石化公司化工二厂丁辛醇造气车间摘要:作为化工生产中的基础性化工材料之一,丁辛醇可用于橡胶制品生产环节,可作为增塑剂使用,也属于良好的脱水剂与消泡剂,还具备溶剂的功能。
在丁辛醇生产过程中,主要应用的是低压羰基合成技术。
文章将以低压羰基合成技术的分析入手,分别对其三种合成方法进行阐述,而后概述了当前我国丁辛醇工艺技术的发展状况,并展望了未来丁辛醇生产工艺的发展方向。
关键词:丁辛醇;低压羰基;工艺技术;发展方向丁辛醇因可利用同一装置采用羰基合成方法同步制备丁醇与辛醇而得名,合成后可得到油状透明液体,其属于无色、可燃性液体,可在化工生产中可作为精细原料而使用,除了化工领域之外,在医药、食品等其他行为具有较高的应用价值。
基于此,了解丁辛醇的生产工艺,探究利用低压羰基合成此材料的具体方法具有重要意义。
1.基于低压羰基合成的丁辛醇技术分析根据合成中所用压力的高低不同,可将低压羰基合成丁辛醇技术分为三种工艺类别,具体如下: 1.1戴维合成技术这是一种源于英美两国,诞生于上世纪七十年代的丁辛醇合成技术,该时期美国研制出了首台铑法低压羰基合成装置,可以丙烯原料以及合成气为基础,在羰基铑的催化作用下进行丁辛醇的合成,所属压力仅为1.76MPa即可。
属于一种低压合成方法。
此合成方式无需应用大量设备,对反应条件没有较高要求,并且操过程便捷简单,所应用的催化剂具有较高活性,此技术一经推出便得到了广泛应用。
丁辛醇生产技术现状及其发展趋势
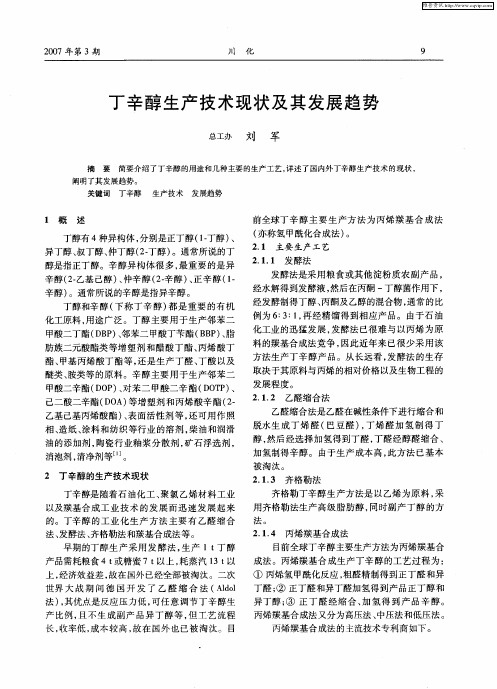
20 0 7年 第 3期
川 化
9
丁辛 醇 生产 技 术 现状 及 其发 展 趋 势
总 办 刘 军 工
摘 要 简要介绍 了丁辛醇 的用途和几种主要 的生产工艺 , 详述 了国内外 丁辛醇生产技术 的现状 ,
阐明了其发展趋势 。 关键词 丁辛醇 生产技术 发展趋势
1 概
述
前 全球丁 辛 醇 主要 生 产方 法 为 丙烯 羰 基 合 成 法
( 称氢 甲酰 化合成 法 ) 亦 。
2 1 主要 生产 工 艺 .
丁 醇有 4种异 构体 , 分别是 正丁 醇 ( . ) 1丁醇 、 异 丁醇 、 叔丁醇 、 仲丁醇 ( . 2丁醇 ) 。通常所 说 的丁
醇是指正丁醇。辛醇异构体很多 , 最重要 的是异
发酵 法是 采用 粮 食 或其 他 淀粉 质 农 副产 品 , 经 水解得 到发 酵液 , 然后在 丙酮 一丁醇菌 作用下 , 经 发酵制 得 丁醇 、 酮及 乙醇 的混 合物 , 丙 通常 的 比
例为 6 3 1再经精馏得到相应产 品。由于石油 ::,
化 工业 的迅猛 发 展 , 酵法 已很 难 与 以丙 烯 为 原 发
长, 收率低 , 本 较 高 , 在 国外 也 已被 淘 汰 。 目 成 故
维普资讯
1 0
川 化
20 0 7年第 3期
高压法 : 鲁尔 ( ur技术、 R h) 巴斯夫( A F 技 B S)
术、 三菱 ( C ) M C 技术、 壳牌( hl 技术。 Se ) 1
法。
的。丁辛 醇 的工 业 化 生 产 方 法 主 要 有 乙醛 缩 合 法 、 酵法 、 发 齐格勒法 和羰 基合成 法 等 。 早期 的丁醇 生 产 采 用 发 酵 法 , 产 1t 醇 生 丁
丁醇合成路线发展历史

[luxury]技术进步的重点在于催化剂技术的改进提高,目前主要是低压铑法1、概述我国丙烯消费中有约12%丙烯用来生产丁、辛醇。
丙烯经羰基合成制得正丁醛,正丁醛经加氢可得正丁醇;或正丁醛经碱催化缩合成辛醛,再加氢为辛醇(2-乙基己醇)。
这是当前丁辛醇最主要生产方法。
丁、辛醇的生产路线经历较多的变迁和发展。
20世纪初,大多采用发酵法生产丁醇(粮食发酵制酒精的联产物)。
,70年代后来由于化学法的发展,发酵法生产技术逐渐淘汰。
近年来由于石油价格的飞速上涨,加之石油资源的日益紧缺,粮食发酵法生产丙酮、丁醇的技术重新显示出其优势,特别是发酵法生产丙酮丁醇是以再生资源替代不可再生的石油基原料制造,符合国家能源安全的长远战略考虑。
二次大战期间,德国开发了以乙醛为原料的醇醛缩合法制取丁、辛醇的工艺,迅速得到普遍的采用。
直到60年代末,乙醛路线是丁、辛醇的主要生产方法。
在50年代还研制成功乙炔雷珀法和高压下的羰基钴为催化剂的丙烯羰基合成法。
丙烯羰基合成丁醛进而合成丁、辛醇工艺由于比发酵法、乙醛法和雷珀法在原料和工艺上更为优越。
故从60年代以来,成为生产丁、辛醇的主要方法。
传统的高压钴法存在的主要缺点是其正、异构醇比为2-4:1,而人们对异构醇需求有限,异构醇的利用存在困难,致使提高正异结构比成为羰基合成技术开发的目标。
1976年美国Celanese和UCC公司分别实现了使用铑羰基化催化剂的低压工艺的工业应用。
以后国外许多高压钴工艺厂家转而采用低压铑法。
1978年以后,新建的装置则几乎全部采用低压铑法,统计到1997年全球丁、辛醇生产中采用佬法的工艺占总生产能力的80%以上。
2.国内外生产和消费据统计,国外1997年丁辛醇生产能力各约为240万吨/年和230 万吨/年。
美国1995年丁、辛醇产量约为68万吨和34万吨。
1996年丁醇的消费量5***万吨。
用于丙烯酸酯类生产占36%,乙二醇醚占31%、醋酸酯和溶剂占25%,其它8%。
化学工艺学第八章-4丙烯羰基化合成丁醇、辛醇

化学工艺学第八章-4丙烯羰基化合成丁醇、辛醇第八章羰基化过程8(4 丙烯羰基化合成丁醇、辛醇 8(4(1 烯烃氢甲酰化反应的基本原理8(4(1(1 反应过程烯烃氢甲酰化主反应是生成正构醛,由于原料烯烃和产物醛都具有较高的反应活性,故有连串副反应和平行副反应发生。
平行副反应主要是异构醛的生成和原料烯烃的加氢,这两个反应是衡量催化剂选择性的重要指标。
主要连串副反应是醛加氢生成醇和缩醛的生成。
以丙烯氢甲酰化为例说明。
主反应CH= CHCH+CO+H?CHCHCHCHO (8—39) 232322副反应CH=CHCH+CO+H (CH3)CHCHO (8—40) 2222异丁醛CH2=CHCH+HCHCHCH (8—41) 22323CHCHCHCHO+H?CHCHCHCHOH (8—42) 322232222CHCHCHCHO?CHCHCHCH(OH)CH(CH())CHCH (8—43) 32232223缩二丁醛CHCHCHCHO+(CH)CHCHO ? 32232CHCH(CH)33CH(OH)CH(CHO)CHCH 23缩醛 (8—44)在过量丁醛存在下,在反应条件下,缩丁醛又能进一步与丁醛化合,生成环状缩醛、链状三聚物,缩醛很容易脱水生成另一种副产物烯醛CHCHCH(OH)CH(CHO)CHCH?CHCHCHCH—C(CH)CHO +HO CH32223322252(8—45) 8(4(1(2 催化剂各种过渡金属羰基配位化合物催化剂对氢甲酰反应均有催化作用,工业上经常采用的有羰基钴和羰基铑催化剂,现分别讨论如下。
1.催化剂及特性催化剂名称活性组分缺点HCO(CO) 羰基钴催化剂热稳定性差,容易分解析出钴而失去4活性HCO(CO).[P(n-R)] 膦羰基钴催化33剂可看作是[P(n-R)]取催化剂的热稳定性好,直链正构醛的3代了HCO(CO)中的选择性佳,加氢活性高、醛缩合及醇4CO.(R为烷基、芳基、醛缩合等连串副反应少等优点。
丁辛醇生产工艺

丁辛醇的生产工艺有两种路线,一种是以乙醛为原料,巴豆醛缩合加氢法;另一种是以丙烯、合成气为原料的低压羰基合成法,该法是当今国际上最为先进的技术之一,目前世界丁辛醇70%是由丙烯羰基化法生产的。
它以丙烯、合成气为原料,经低压羰基合成生产粗丁醛,再经丁醛处理、缩合、加氢反应制得丁辛醇。
低压羰基合成法生产丁辛醇典型的流程包括:原料净化、羰基合成、丁醛精制、缩合、加氢、粗醇精馏等工序。
丁醛精制是指粗丁醛除去轻组分后在异构塔内精馏分离得正丁醛和异丁醛。
缩合是指正丁醛脱去重组分后进入缩合系统,在NaOH 存在、120℃和0.4MPa条件下,进行醛醛缩合生成辛烯醛(EPA)。
加氢一般是指正、异丁醛或混合丁醛或辛烯醛加氢生产相应的醇。
但是不论采用那一种方法,都必须经过丁烯醛/丁醛、辛烯醛加氢来制取丁醇和辛醇。
醛加氢是丁辛醇生产过程的重要组成部分,对丁辛醇的产品质量和生产过程的经济性都有很大的影响。
1丁辛醇加氢工艺路线丁醛加氢制备丁醇和辛烯醛加氢制备辛醇的工业化工艺路线主要有气相法和液相法两种。
液相加氢反应采用多段绝热固定床反应器,由于液相热容量较大,反应器内不用设置换热器。
根据反应条件,段间设置换热器移走反应热,防止醛的缩合反应。
BASF公司曾经采用过高压液相加氢,加氢的压力为25.33MPa。
高压加氢的唯一优点是氢气耗量较少,所用的液相加氢催化剂为70%Ni、25%Cu、5%Mn,该催化剂要求氢气分压不低于3.5MPa,所以总高压时,尾气的氢气浓度可降低,氢耗少。
但采用该高压工艺,原料氢气必须高压压缩,电耗大、设备费用大,目前已经被淘汰。
BASF公司和三菱化成工艺中醛的加氢采用中压液相加氢工艺,加氢压力为4.0-5.0MPa,加氢反应器形式采用填充床,反应温度为60-190℃。
气相加氢法由于操作压力相对较低,工艺设备简单而被广泛应用。
目前,工业上丁辛醇装置上大多采用铜系催化剂气相加氢工艺。
如U.D.J联合工艺中采用低压气相加氢,压力为0.59-0.69MPa。
低压铑羰基合成法制丁辛醇工艺简介

低压铑羰基合成法制丁辛醇工艺简介2中国五环工程有限公司湖北省武汉市 430000摘要:本文介绍了低压羰基合成法的反应机理及催化剂毒物,同时对低压铑羰基合成工艺技术进行了简介。
关键词:丁辛醇装置;低压铑法;羰基合成1、概述丁醇和辛醇是丙烯下游第三大衍生产品,作用重要的基本化工原料主要用作溶剂和生产增塑剂。
丁醇和辛醇可在同一装置中生产,生产方法主要有乙醛缩合法、发酵法、齐格勒法和羰基合成法等(1)。
随着生产技术的不断革新,羰基合成法成为目前丁辛醇的主要生成方法。
羰基合成方法是以丙烯、合成气为原料在催化剂作用下生成丁醛,丁醛再经加氢得到丁醇,也可利用丁醛缩合得到辛烯醛,辛烯醛加氢得到辛醇。
各羰基合成法区别主要在丙烯氢甲酰化工艺不同,按照压力区分可分为高压法、中压法和低压法,按照催化体系可分为钴法和铑法。
低压铑法因其较低的设备制造难度、简单的工艺流程、较高丙烯的转化率和正丁醛选择性成为目前最广泛应用的丁辛醇生产方法。
2、羰基合成反应机理工业上采用乙酰丙酮二羰基铑、三苯基膦乙酰丙酮羰基铑等为反应母体,在过量三苯基膦和CO存在情况下生成起催化作用的活性铑-膦络合物。
活性物铑-膦络合物处于一系列平衡中,当三苯基膦PPh浓度高时平衡向右移动,3当CO浓度高时平衡向左移动。
正丁醛生成机理如下:(1)在反应条件下,活性铑-膦络合物与丙烯生成烯烃铑络合物。
(2)烯烃铑络合物发生插入反应(3)烯烃铑络合物中的CO插入烃基与铑之间,得到酰基铑络合物(4)酰基铑络合物与H发生氧化加成,进而发生还原消去反应得到醛,并2释放催化剂络合物。
(5)释放的催化剂络合物再结合一分子CO得到,完成催化剂循环。
在发生烯烃铑络合物反应时,如果Rh与丙烯链端的的碳原子结合时即可得到正丁醛,如果Rh与中间的碳原子结合时即得到异丁醛。
3、低压铑法工艺简介目前普遍采用的低压铑法的生产技术有UCC/Davy/Johnson Mattey技术、三菱化成技术、巴斯夫技术,另外鲁尔改性铑法(中压法)因其优异的催化活性和易分离的水性催化剂也具有较强的竞争优势。
丁辛醇生产工艺
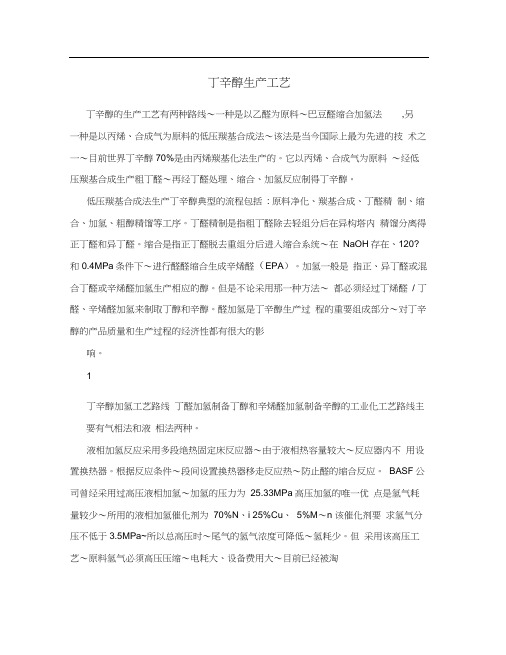
丁辛醇生产工艺丁辛醇的生产工艺有两种路线〜一种是以乙醛为原料〜巴豆醛缩合加氢法,另一种是以丙烯、合成气为原料的低压羰基合成法〜该法是当今国际上最为先进的技术之一〜目前世界丁辛醇70%是由丙烯羰基化法生产的。
它以丙烯、合成气为原料〜经低压羰基合成生产粗丁醛〜再经丁醛处理、缩合、加氢反应制得丁辛醇。
低压羰基合成法生产丁辛醇典型的流程包括: 原料净化、羰基合成、丁醛精制、缩合、加氢、粗醇精馏等工序。
丁醛精制是指粗丁醛除去轻组分后在异构塔内精馏分离得正丁醛和异丁醛。
缩合是指正丁醛脱去重组分后进入缩合系统〜在NaOH存在、120?和0.4MPa条件下〜进行醛醛缩合生成辛烯醛(EPA)。
加氢一般是指正、异丁醛或混合丁醛或辛烯醛加氢生产相应的醇。
但是不论采用那一种方法〜都必须经过丁烯醛/ 丁醛、辛烯醛加氢来制取丁醇和辛醇。
醛加氢是丁辛醇生产过程的重要组成部分〜对丁辛醇的产品质量和生产过程的经济性都有很大的影响。
1丁辛醇加氢工艺路线丁醛加氢制备丁醇和辛烯醛加氢制备辛醇的工业化工艺路线主要有气相法和液相法两种。
液相加氢反应采用多段绝热固定床反应器〜由于液相热容量较大〜反应器内不用设置换热器。
根据反应条件〜段间设置换热器移走反应热〜防止醛的缩合反应。
BASF公司曾经采用过高压液相加氢〜加氢的压力为25.33MPa高压加氢的唯一优点是氢气耗量较少〜所用的液相加氢催化剂为70%N、i 25%Cu、5%M〜n 该催化剂要求氢气分压不低于3.5MPa~所以总高压时〜尾气的氢气浓度可降低〜氢耗少。
但采用该高压工艺〜原料氢气必须高压压缩〜电耗大、设备费用大〜目前已经被淘汰。
BASF公司和三菱化成工艺中醛的加氢采用中压液相加氢工艺〜加氢压力为 4.0-5.0MPa〜加氢反应器形式采用填充床〜反应温度为60-190?。
气相加氢法由于操作压力相对较低〜工艺设备简单而被广泛应用。
目前〜工业上丁辛醇装置上大多采用铜系催化剂气相加氢工艺。
8.羰基合成(新)详解

以Rh配合物和HI为催化剂系统的甲醇低压羰基
化反应具体反应方程式如下:
速率控制步骤 反 应 机 理
动力学方程—孟山都法
甲醇低压法羰基化合成乙酸法 研究表明:动力学方程式如下:
d [CH 3COOH ] k[CH 3 I ][ Rh 配合物 ] dr
2. 甲醇低压羰基化生产醋酸工艺流程
(4) 反应系统和精制系统合为一体; (5)副产物很少,三废排放物也少,生产环境清 洁
3 工艺的优缺点 主要缺点: 催化剂铑的资源有限,设备用的耐腐蚀 材料昂贵。
4、 甲醇低压羰基化合成醋酸研究新进展 主要方面:
1、开发出高活性、低水含量、 低消耗的高效催 化剂体系, 以大幅提高现有装置的产能, 有效 降低生产成本;
③膦羰基铑催化剂
选择性好,催化剂性能比较稳定,
活性比羰基氢钴高102~104倍,正/异构 醛比例也高 。 (方法:改变配位基和中心原子)
8.2 甲醇低压羰基化合成醋酸
主要内容:
1、醋酸生产方法简介 2、甲醇低压羰基化合成醋酸 (原理、工艺流程及其优缺点)
醋酸的用途
醋酸是一种重要的基本有机化工原料,主要
其他用途:溶剂、脱水剂、消泡剂、
分散剂、浮选剂、石油添加剂 。
8.3.1 丁辛醇生产方法简介
乙醛缩合法 发酵法 工业化生产主要方法 齐格勒法 羰基合成法
8.3.1 丁辛醇生产方法简介 1、乙醛缩合法:
P(OR)3
3、各类催化剂的特点
①羰基钴催化剂
羰基钴催化剂的活性组分、热稳定性
差、容易分解;异构化活性高
P(OR)3
3、各类催化剂的特点
②膦羰基钴催化剂
热稳定性增加,对直链产物的选择性
丙烯羰基合成生产丁辛醇
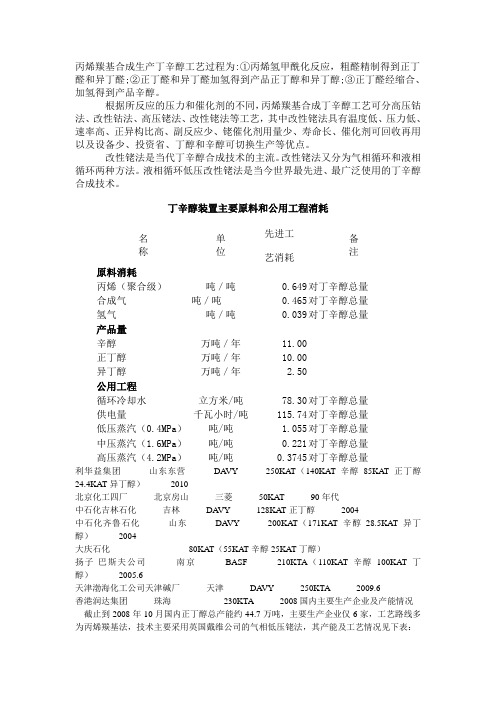
丙烯羰基合成生产丁辛醇工艺过程为:①丙烯氢甲酰化反应,粗醛精制得到正丁醛和异丁醛;②正丁醛和异丁醛加氢得到产品正丁醇和异丁醇;③正丁醛经缩合、加氢得到产品辛醇。
根据所反应的压力和催化剂的不同,丙烯羰基合成丁辛醇工艺可分高压钴法、改性钴法、高压铑法、改性铑法等工艺,其中改性铑法具有温度低、压力低、速率高、正异构比高、副反应少、铑催化剂用量少、寿命长、催化剂可回收再用以及设备少、投资省、丁醇和辛醇可切换生产等优点。
改性铑法是当代丁辛醇合成技术的主流。
改性铑法又分为气相循环和液相循环两种方法。
液相循环低压改性铑法是当今世界最先进、最广泛使用的丁辛醇合成技术。
丁辛醇装置主要原料和公用工程消耗名称单位先进工艺消耗备注原料消耗丙烯(聚合级)吨/吨0.649 对丁辛醇总量合成气吨/吨0.465 对丁辛醇总量氢气吨/吨0.039 对丁辛醇总量产品量辛醇万吨/年11.00正丁醇万吨/年10.00异丁醇万吨/年 2.50公用工程循环冷却水立方米/吨78.30 对丁辛醇总量供电量千瓦小时/吨115.74 对丁辛醇总量低压蒸汽(0.4MPa)吨/吨 1.055 对丁辛醇总量中压蒸汽(1.6MPa)吨/吨0.221 对丁辛醇总量高压蒸汽(4.2MPa)吨/吨0.3745 对丁辛醇总量利华益集团山东东营DA VY 250KAT(140KAT辛醇85KAT正丁醇24.4KAT异丁醇)2010北京化工四厂北京房山三菱50KAT 90年代中石化吉林石化吉林DA VY 128KAT正丁醇2004中石化齐鲁石化山东DAVY 200KAT(171KAT辛醇28.5KAT异丁醇)2004大庆石化80KAT(55KAT辛醇25KAT丁醇)扬子-巴斯夫公司南京BASF 210KTA(110KAT辛醇100KAT丁醇)2005.6天津渤海化工公司天津碱厂天津DA VY 250KTA 2009.6香港润达集团珠海230KTA 2008国内主要生产企业及产能情况截止到2008年10月国内正丁醇总产能约44.7万吨,主要生产企业仅6家,工艺路线多为丙烯羰基法,技术主要采用英国戴维公司的气相低压铑法,其产能及工艺情况见下表:表2 国内主要生产企业及产能情况单位:万吨企业名称产能工艺中石化齐鲁石化 5.0 英国戴维气相低压铑法北京东方石油化工 4.0 日本三菱液相低压循环工艺中石油吉林石化17 英国戴维气相低压铑法大庆石化 2.5 英国戴维气相低压铑法中石化与BASF合资扬子一巴斯夫公司10 巴斯夫技术吉安生化 6.0 粮食发酵法其它0.2合计44.7正丁醇生产供需状况近年来国内正丁醇生产供需情况见下表:表3 近年来国内正丁醇生产供需情况单位:万吨年份2001 2002 2003 2004 2005 2006 2007 2 008(1-10)产能21.2 21.2 21.2 28.0 38.0 38.0 44.5 44.5 产量16.0 17.5 20.4 20.5 29.4 38.0 40.0进口量22.28 24.3 29.6 29.35 23.99 23.58 29.4 19.05出口量0.07 0.06 0.1 0.19 0.20 0.09 0.026 0.11 表观消费量39.91 41.8 50.0 49.66 53.19 61.49 69.37自给率,% 40.1 41.9 40.8 41.3 55.3 61.8 57.7从以上分析可知:国内正丁醇自给率不足60%,长期依赖进口。
第七章 丙烯系产品的生产(1)
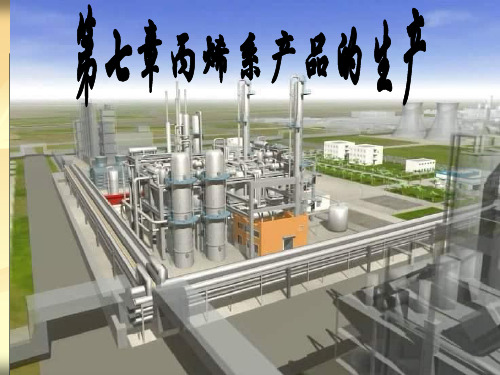
丙烯的用途
聚丙烯是我国丙烯最大的消费衍生物。2003年,我国聚丙烯的产量为
445.5万吨,消耗丙烯约444.0万吨,约占全国丙烯总消费量的72.1%,;2004 年我国聚丙烯产量为474.9万吨,消耗丙烯约480.0万吨,比2003年增长约 8.1%; 丙烯腈是我国丙烯的第二大衍生物,2003年,我国丙烯腈的产量约为 56.0万吨,消费丙烯约62.7万吨,约占全国丙烯总消费量的10.2%;2004年产 量约为58.0万吨,消费丙烯约为65.0万吨,比2003年增长约3.7%; 环氧丙烷是我国丙烯的第三大消费衍生物,2003年,全国环氧丙烷 的产量约为39.8万吨,消耗丙烯约35.8万吨,约占全国丙烯总消费量的5.8%; 2004年产量约为42.0万吨,消耗丙烯约37.8万吨,比2003年增长约13.1%; 丁醇和辛醇也是丙烯的主要衍生物之一,2003年我国丁辛醇的产量合 计约为45.35万吨,共消耗丙烯约40.7万吨,约占全国丙烯总消费量的6.6%; 2004年产量合计为44.91万吨,共消耗丙烯约40.3万吨,比2003年减少约1.0%;
三、操作条件
原料纯度 原料配比 接触时间 原料丙烯是从烃类裂解气或催化裂化气分离得到,其中可能含有的杂 质是碳二、丙烷和碳四,也可能有硫化物存在。 反应压力 (1)丙烯与氨的配比(氨比) 丙烷和其它烷烃对反应没有影响,它们的存在只是稀释了浓度, 反应温度
丙烯氨氧化反应是气 —固相催化反应,反应是在 (2) 丙烯与空气的配比(氧比) 实际上含丙烯 50%的丙烯—丙烷馏分也可作原料使用。 (催化剂表面进行的。因此,原料气和催化剂必须 3 )丙烯与水蒸气的配比(水比) 丙烯氨氧化生产丙烯腈是体积缩小的 乙烯在氨氧化反应中不如丙烯活泼,因其没有活泼的α-H,一 当温度低于 350℃时,几乎不生成丙烯腈。 反应,提高压力可增大反应的平衡转 有一定的接触时间,使原料气能尽量转化成目的 般情况下,少量乙烯存在对反应无不利影响。 当反应温度升高时,丙烯转化率、丙烯腈收率都明显地增加, 化率。 产物。 但丁烯或更高级烯烃存在会给反应带来不利,因为丁烯或更高 而副产物乙腈和氢氰酸收率则有所增加。 同时,提高压力也可增加气体的浓度, 一般说来,适当增加接触时间,可以提高丙烯转 级烯烃比丙烯易氧化,会消耗原料中的氧,甚至造成缺氧,而使催 随着温度的升高,丙烯腈收率和乙腈收率都会出现一个最大值, 提高反应速度,相应地可增加设备的 化率和丙烯腈收率,而副产物乙腈、氢氰酸和丙 化剂活性下降; 丙烯腈收率的最大值所对应的温度大约在460℃左右,乙腈收率 生产能力。 烯醛的收率变化不大,这对生产是有利的。 最在值所对应的温度大约在 417℃左右。 正丁烯氧化生成甲基乙烯酮(沸点 80℃),异丁烯氨氧化生成 但实验表明,由于加压对副反应更有利, 但是,增加接触时间是有限度的,过长的接触时 在457℃以上反应时,丙烯易于与氧作用生成大量 CO2, 甲基丙烯腈(沸点 90℃),它们的沸点与丙烯腈沸点接近,会给丙 反而降低了丙烯腈的收率。 间会使丙烯腈深度氧化的机会增大,反而使丙烯 放热较多,反应温度不易控制。 烯腈的精制带来困难。 因此,一般采用常压操作,适当加压只 腈收率下降。 过高的温度也会使催化剂的稳定性降低。 是为了克服后部设备及管线的阻力。 因此,丙烯中丁烯或更高级烯烃含量必须控制。 同时,过长的接触时间,还会降低设备的生产能 生产中通常采用在460℃左右进行操作。 硫化物的存在,会使催化剂活性下降,应预先脱除。 力,而且由于尾气中氧含量降低而造成催化剂活 性下降,故接触时间一般为5~l0s。
8.羰基合成(新)解析

不对称合成目前在药物合成和天然 产物全合成中都有十分重要的地位。
8.1.1.2 甲醇的羰化反应
(1) 甲醇羰化合成醋酸---孟山都法
CH 3OH CO CH 3COOH
(2) 醋酸甲酯羰化合成醋酐CH3COOCH3 CO (CH3CO)2 O
醋酸甲酯可由甲醇羰化再酯化制得
3OH CH3OH CO CH3COOH CH CH3COOCH3
(>C=O)的反应均归入羰化反应的范围。
羰基合成的重要性
①羰基合成的初级产品是醛。在有机合成中醛是最活 泼的基团之一,可进行加氢成醇、氧化成酸、氨化成
胺以及歧化、缩合、缩醛化等一系列反应;
②原料烯烃的多种多样和醇、酸、胺等产物的后续加 工,由此构成以羰基合成为核心的内容十分丰富的产 品网络,应用领域涉及化工领域的多个方面。
③膦羰基铑催化剂
选择性好,催化剂性能比较稳定,
活性比羰基氢钴高102~104倍,正/异构 醛比例也高 。 (方法:改变配位基和中心原子)
8.2 甲醇低压羰基化合成醋酸
主要内容:
1、醋酸生产方法简介 2、甲醇低压羰基化合成醋酸 (原理、工艺流程及其优缺点)
醋酸的用途
醋酸是一种重要的基本有机化工原料,主要
8.1.1 羰基化反应类型
羰基化反应主要类型:
不饱和化合物的羰基化反应和甲醇的羰基化反应。 8.1.1.1 不饱和化合物的羰基化反应 (1)烯烃的氢甲酰化 制备比原料烯烃多一个碳原子的饱和醛或醇
例如
CH2=CH2+CO+H2→CH3CH2CHO → CH3CH2CH2OH
HO CH 2 CH CHO H 2 HOCH2 CH 2 CH 2 CH 2OH
煤制丙稀,丙稀合成丁辛醇调查报告

煤制丙稀,丙稀合成丁辛醇技术与市场调查一、丁辛醇概况1:丁辛醇概况丁辛醇包括正丁醇和辛醇,丁醇有4中异构体,分别是正丁醇,异丁醇,叔丁醇,仲丁醇,通常所说的丁醇是指正丁醇。
正丁醇化学名称为1-丁醇。
辛醇的异构体很多,最重要的是异辛醇(2-乙基已醇),仲辛醇(2-辛醇),正辛醇(1-辛醇)。
通常所说的辛醇是指异辛醇,化学名称为2-乙基-1-己醇。
2:性能简介丁辛醇是重要的基本有机化工原料。
丁醇(指正丁醇,n-butanol)主要用于制造邻苯二甲酸二丁酯(DBP),邻苯二甲酸丁苄酯(BBP)和脂肪族二元酸酯类增塑剂和醋酸丁酯,丙烯酸丁酯,甲基丙烯酸丁酯等,还是生产丁醛,丁酸以及谜类,胺类等的有机化合物原料。
广泛用于各种塑料和橡胶制品的生产。
可用作树脂、油漆、粘接剂的溶剂及选矿用消泡剂,也可用做油脂、药物(如抗菌素、激素和维生素)和香料的萃取剂及醇酸树脂涂料的添加剂。
用丁醇生产的各种醚类、胺类可分别用作乳胶漆、织物加工粘合剂、农药和橡胶加工及皮革处理剂等。
辛醇(指2-乙基己醇,2-ethylhexanol)主要用于制造邻苯二甲酸二辛酯(DOP)。
DOP产品素有王牌增塑剂之称,是一种物美价廉的理想增塑剂,用于对苯二甲酸二辛脂(DOP),己二酸二辛酯(DOA)等增塑剂,表面活性剂。
广泛用于聚氯乙烯(PVC)、合成橡胶、纤维素脂的加工等。
辛醇可用作柴油和润滑油的添加剂,还用作照相、造纸、涂料、油漆和纺织等行业的溶剂、陶瓷工业釉浆分散剂、矿石浮选剂、消泡剂、清净剂等。
二、丁辛醇生产工艺及技术进展1:丁辛醇的生产技术现状随着石化工业和羰基合成技术的发展,早期淀粉质农副产品发酵路线和乙醛缩合路线相继淘汰,羰基合成法(即丙烯氢甲酰化法)生产丁辛醇迅速发展起来,其生产过程为丙烯和合成气(一氧化碳和氢气)羰基合成粗醛,精制得到正丁醛和异丁醛;分别加氢得到产品正丁醇和异丁醇;两分子正丁醛缩合脱水生成辛烯醛,加氢得到产品辛醇。
丁辛醇安全生产要点
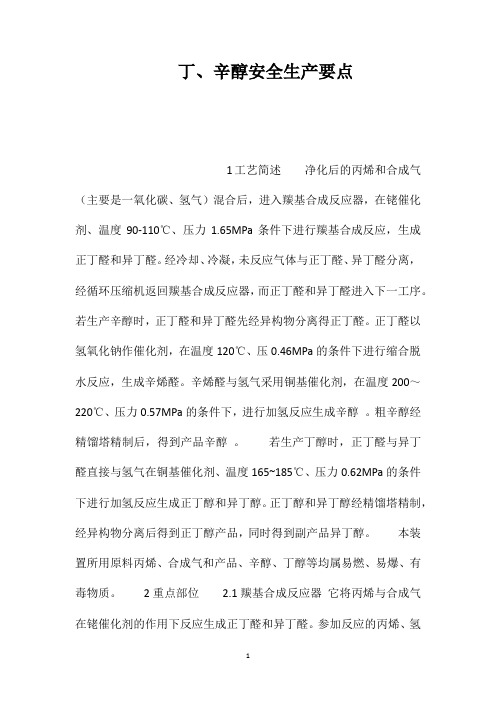
丁、辛醇安全生产要点1工艺简述净化后的丙烯和合成气(主要是一氧化碳、氢气)混合后,进入羰基合成反应器,在铑催化剂、温度90-110℃、压力1.65MPa条件下进行羰基合成反应,生成正丁醛和异丁醛。
经冷却、冷凝,未反应气体与正丁醛、异丁醛分离,经循环压缩机返回羰基合成反应器,而正丁醛和异丁醛进入下一工序。
若生产辛醇时,正丁醛和异丁醛先经异构物分离得正丁醛。
正丁醛以氢氧化钠作催化剂,在温度120℃、压0.46MPa的条件下进行缩合脱水反应,生成辛烯醛。
辛烯醛与氢气采用铜基催化剂,在温度200~220℃、压力0.57MPa的条件下,进行加氢反应生成辛醇。
粗辛醇经精馏塔精制后,得到产品辛醇。
若生产丁醇时,正丁醛与异丁醛直接与氢气在铜基催化剂、温度165~185℃、压力0.62MPa的条件下进行加氢反应生成正丁醇和异丁醇。
正丁醇和异丁醇经精馏塔精制,经异构物分离后得到正丁醇产品,同时得到副产品异丁醇。
本装置所用原料丙烯、合成气和产品、辛醇、丁醇等均属易燃、易爆、有毒物质。
2重点部位 2.1羰基合成反应器它将丙烯与合成气在铑催化剂的作用下反应生成正丁醛和异丁醛。
参加反应的丙烯、氢气、一氧化碳,以及生成物正丁醛、异丁醛等都是易燃、易爆、易中毒的物质。
铑催化剂非常昂贵、易中毒,其反应条件非常苛刻。
曾多次发生因进料配比不当造成部分催化剂中毒,并使反应压力急剧下降,几乎导致循环压缩机喘振而损坏的事故。
也曾多次发生因丁醛泄漏,遇氧气及碱性物质而自燃着火的事故。
还曾发生因合成气泄漏,产生静电着火的事故。
2.2加氢反应器加氢反应器用来将辛烯醛加氢生成辛醇,或将正丁醛和异丁醛加氢生成正丁醇和异丁醇。
氢气是易燃、易爆物质,一旦失控,加氢反应不易控制、易超温,会造成重大恶性事故。
曾多次发生因氢气泄漏而着火或局部爆炸的事故。
还曾发生因进料大幅度波动,使加氢反应温度急剧上升,险些造成重大事故。
2.3火炬系统火炬系统是用来将装置排出的废气、废液分离后,将废气烧掉,废液返回装置以回收有用组分的系统。
- 1、下载文档前请自行甄别文档内容的完整性,平台不提供额外的编辑、内容补充、找答案等附加服务。
- 2、"仅部分预览"的文档,不可在线预览部分如存在完整性等问题,可反馈申请退款(可完整预览的文档不适用该条件!)。
- 3、如文档侵犯您的权益,请联系客服反馈,我们会尽快为您处理(人工客服工作时间:9:00-18:30)。
丙烯羰基合成生产丁辛醇工艺过程为:①丙烯氢甲酰化反应,粗醛精制得到正丁醛和异丁醛; ②正丁醛和异丁醛加氢得到产品正丁醇和异丁醇; ③正丁醛经缩合、加氢得到产品辛醇。
根据所反应的压力和催化剂的不同,丙烯羰基合成丁辛醇工艺可分高压钴法、改性钴法、高压铑法、改性铑法等工艺,其中改性铑法具有温度低、压力低、速率高、正异构比高、副反应少、铑催化剂用量少、寿命长、催化剂可回收再用以及设备少、投资省、丁醇和辛醇可切换生产等优点。
改性铑法是当代丁辛醇合成技术的主流。
改性铑法又分为气相循环和液相循环两种方法。
液相循环低压改性铑法是当今世界最先进、最广泛使用的丁辛醇合成技术。
丁辛醇装置主要原料和公用工程消耗
名单先进工
备
称位
艺消耗注
原料消耗
丙烯(聚合级)吨/吨0.649 对丁辛醇总量
合成气吨/吨0.465 对丁辛醇总量
氢气吨/吨0.039 对丁辛醇总量
产品量
辛醇万吨/年11.00
正丁醇万吨/年10.00
异丁醇万吨/年 2.50
公用工程
循环冷却水立方米/ 吨78.30 对丁辛醇总量
供电量千瓦小时/ 吨115.74 对丁辛醇总量
低压蒸汽(0.4MPa)吨/ 吨 1.055 对丁辛醇总量
中压蒸汽(1.6MPa)吨/ 吨0.221 对丁辛醇总量
高压蒸汽(4.2MPa)吨/ 吨0.3745 对丁辛醇总量
利华益集团山东东营DAVY 250KAT ( 140KAT 辛醇85KAT 正丁醇
24.4KAT 异丁醇) 2010
北京化工四厂北京房山三菱50KAT 90 年代
中石化吉林石化吉林DAVY 128KAT 正丁醇2004
中石化齐鲁石化山东DAVY 200KAT ( 171KAT 辛醇28.5KAT 异丁
醇)2004
大庆石化80KAT (55KAT 辛醇25KAT 丁醇)
扬子-巴斯夫公司南京BASF 210KTA (110KAT 辛醇100KAT 丁
醇)2005.6
天津渤海化工公司天津碱厂天津DAVY 250KTA 2009.6
香港润达集团珠海230KTA 2008 国内主要生产企业及产能情况截止到2008 年10 月国内正丁醇总产能约44.7 万吨,主要生产企业仅 6 家,工艺路线多
为丙烯羰基法,技术主要采用英国戴维公司的气相低压铑法,其产能及工艺情况见下表:
表 2 国内主要生产企业及产能情况
单位:万吨企业名称产能工艺
中石化
齐鲁石化 5.0 英国戴维气相低压铑法
北京东方石油化工 4.0 日本三菱液相低压循环工艺
中石油
吉林石化17 英国戴维气相低压铑法大庆石化 2.5 英国戴维气相低压铑法
中石化与BASF 合资扬子一巴斯夫公司10 巴斯夫技术
吉安生化 6.0 粮食发酵法
其它0.2
合计44.7
正丁醇生产供需状况近年来国内正丁醇生产供需情况见下表:表 3 近年来国内正丁醇生产供需情况单位:万吨
年
份2001 2002 2003 2004 2005 2006 2007 2
008( 1-10)
产
能21.2 21.2 21.2 28.0 38.0 38.0 44.5 44.5
产量16.0 17.5 20.4 20.5 29.4 38.0 40.0
进口量22.28 24.3 29.6 29.35 23.99 23.58 29.4
19.05
出口量0.07 0.06 0.1 0.19 0.20 0.09 0.026 0.11 表观消费量39.91 41.8 50.0 49.66 53.19 61.49 69.37
自给率,% 40.1 41.9 40.8 41.3 55.3 61.8 57.7
从以上分析可知:国内正丁醇自给率不足由于市场缺口较大,为满足市场需求,国内丁辛醇新建、拟建项目投资概况项目名称产能投产日期天津碱厂22.5
60%,长期依赖进口。
目前国内仍有不少拟在建项目。
具体如下:单位:万吨/年
投资额地址备注
(8.5) 1.69 亿美元天津塘沽临港工业区中国化工山东华星石
油化工集团有限公司24(12) 中国石油四川乙烯项目29(21) 2009 正丁醇合计41.5
注:括号项为丁醇的产能。
随着国内拟在建项目的陆续投产,国内正丁醇长期对外依存度较高的局面将有望得以缓解。
产品质量
工业正丁醇项目指标试验方法
正丁醇含量,wt.% > 99.8 DIN 55685:1992 低压羰基铑法合成技
术
异丁醇,wt.% w 0.1 DIN 55685:1992
二丁醚,wt.% w 0.02 DIN 55685:1992
丁醛,wt.% w 0.05 DIN 55685:1992
色度,(Pt-Co 号)w5 ISO 6271:1997
酸度(以醋酸计),wt.% w 0.003 ISO 2114:2000 水分,wt.% w 0.05 DIN 51777-1:1983。