PCB线路板半金属化孔的合理设计及加工方法
半金属化槽孔成型加工技术

Contour Routing Technology of Half PTH半金属化槽/孔的成型加工技术探讨深南电路有限公司梁飞孙俊杰518053摘要:半面金属化槽/孔在成型加工过程中的毛刺和铜皮翻起问题是PCB机械加工中的一个难点,传统的改良方法,即更改走刀方向、下刀点以及定位方式很难完全消除这些问题,继而在后续焊接过程中出现虚焊、桥接短路等问题。
本文在对比总结灌锡铣、正反钻、正反铣工艺的同时,提出了机械加工和化学加工相结合的最优解决方案——带锡铣。
关键词:半金属化槽/孔带锡铣Abstract: It is difficult to avoid copper burr in routing the PCB with HALF PTH.The technical requirements can not be meet only by improving the path direction, starting point and locate mode. While the copper burr remaining on the hole/slot wall would induce welding failure or short circuit. The following article summarizes some traditional technical methods such as filling stannum, double side drilling and double side routing to resolve this problem, meanwhile, an optimum solution is offered.Keywords: half PTH hole/slot routing with stannum一、前言背景所谓半金属化槽/孔,多指在PCB外形线上只留有半个金属化槽/孔的设计,而另一半要在成型加工时将其铣掉。
pcb半孔板工艺流程

pcb半孔板工艺流程PCB半孔板工艺流程PCB半孔板工艺流程是指在PCB(Printed Circuit Board,印刷电路板)制造过程中,使用半孔板工艺来加工半孔(Blind Via)。
半孔是一种特殊的孔洞结构,在PCB上表现为从一面穿过到另一面的孔洞,但并不贯穿整个板厚。
半孔板工艺的应用可以实现更高密度的连接和更复杂的布线,提高PCB的可靠性和性能。
PCB半孔板工艺流程主要包括以下几个步骤:1. 设计和制作半孔板:根据设计要求,在PCB设计软件中进行布线和设计,确定半孔的位置和尺寸。
然后,通过光绘、蚀刻和掩膜工艺制作出半孔板。
2. 钻孔:将半孔板放入钻孔机中,通过钻头钻出半孔的位置。
钻孔时需要控制好钻头的速度和压力,以避免破坏半孔板。
3. 镀铜:钻孔完成后,需要在孔壁上进行铜镀,以增强导电性能。
首先,在半孔板的孔壁上涂上一层导电涂料,然后将半孔板放入铜镀槽中进行电化学镀铜。
4. 清洗:镀铜完成后,半孔板需要进行清洗,去除表面的污染物和残留物。
清洗过程可以使用溶剂、超声波或喷淋等方式进行。
5. 化学除锡:在半孔板的表面通常会有锡层,为了保证半孔的通电性能,需要进行化学除锡处理。
化学除锡可以使用酸性溶液或碱性溶液来去除锡层。
6. 表面处理:半孔板完成除锡后,需要进行表面处理,以提高半孔板的耐腐蚀性和焊接性能。
常见的表面处理方法包括喷镀、喷锡、喷金等。
7. 检测和修复:半孔板制作完成后,需要进行检测,检查半孔的质量和连接性能。
如果发现问题,需要进行修复或重新制作。
8. 完成产品:经过检测和修复后,半孔板可以进一步组装和测试,最终形成完整的PCB产品。
PCB半孔板工艺流程的关键在于钻孔和镀铜的过程。
钻孔需要精确控制钻头的位置和深度,以避免钻孔偏移或损坏半孔板。
镀铜过程需要保证铜层的均匀性和附着力,以确保半孔的导电性能和可靠性。
PCB半孔板工艺流程的应用广泛,特别适用于高密度和高性能的电子产品制造。
浅析印制电路板孔金属化及其工艺改进途径

浅析印制电路板孔金属化及其工艺改进途径摘要:PBC孔金属化技术被认为是印制电路板生产过程中的关键环节,本文将深入探讨这一技术的概念,并结合实际应用,提出有效的改善方案。
此外,本文还将探讨如何通过整平、氧化、催化和电镀等技术来提高PBC的性能,以及如何通过这些技术来实现PBC的长期可持续发展。
关键词:印制电路板。
孔金属化;工艺现状;优化方法引言:随着电子IT的飞速发展,印刷电路板(PBC)行业迎来了前所未有的机遇,而孔金属化则成为PBC生产过程中不可或缺的一部分。
随着PBC孔金属化技术的不断发展,其工艺已经变得越来越成熟,制造质量也越来越稳定,但仍然存在着复杂的工艺流程、昂贵的成本以及严重的环境污染问题。
因而,提升PBC孔金属化技术的效率与质量显得尤为重要,本文将从多方面探讨这一问题,以期达到更好的效果。
1 PBC孔金属化概念覆铜板(CCP)为PCB制造。
CCP是一种具有重要应用价值的基础材料,它可以通过精心设计的加工工艺,如电镀铜、刻蚀等,制作出具有良好导电性能的电路,从而实现高性能的PCB电路。
在PCB盘面上的每个孔都被完全封装之前,才能够将其与PCB电路连接起来,并安装相应的电子元器件。
从宏观视角来看,孔金属化技术指的是采用电化学镀、电镀或其他技术,将一层导电金属覆盖在PCB板孔壁上,以增强电路与电子元件之间的联系,以达到改善电路效率和电子元件耐久性的目的。
金属化是PCB制造过程中至关重要的一步,它需要确保金属化孔的机械强度和导电性能达到最佳水平。
此外,铜镀层的结构必须完善,分布均匀,厚度也应该适中(一般为25~30μm)。
同时,孔洞内部也应避免出现分层和气泡等缺陷,并且孔的电阻值应小于<1000MΩ。
近年来,随着高密度封装技术的普及,PCB结构的创新和发展得到了显著推动,成为工业界的一大亮点。
通过安装金属孔,可以有效地将不同电路连接起来,从而提高电子元件的性能和可靠性。
通过表面安装技术的应用,可以有效地缩小金属化孔空洞的尺寸,从而推动PCB制造技术的发展,实现微纳通孔和薄型化的生产。
印刷线路板孔的金属化工艺及配方
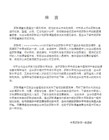
配方2 焦磷酸铜(以铜计)21-31克/升,焦磷酸钾(以P2O7计)150-1210克/升,氢氧化铵(25%)8毫升/升,硝酸钾5-10克/升,柠檬酸铵20克/升,PH值8-9,温度18-58度,阴极电流密度1-3安/分实2,阴极移动需要,
加厚镀铜:在电镀其他金属之前,必须进行加厚镀铜,其溶液的配方和工艺规范与孔内镀铜溶液相同,电镀时间约为1—1.5小时,厚度约为25-30微米。
孔内硫酸型镀铜水液配方:
配方1 硫酸铜80-100克/升,硫酸200克/升,2—四氢基噻唑硫铜0.001克/升,聚二硫二丙烷磺酸钠0.01克/升,聚醚化物0.15克/升,亚甲基磺酸钠(D—1)0.2克/升,氯离子20毫升/升,阳极含磷0.01—0.03%的铜板,电流密度1—3安/分米2,溶液温度10-25度,沉积速度1.5微米/时。
有关工艺及配方如下:
脱膜剂配方:海鸥洗涤剂1份,水10份。
涂保护漆:用过氯乙烯防腐清漆浸2-3次,再晾干或烘干。
新水处理:在5-10%的氢氧化钠水溶液中,于室温下浸10分钟左右,去除Байду номын сангаас内残留的油污。
孔壁粗化:在浓硫酸溶液中,于室温下浸1-2分钟,使孔壁非常清洁,但表面粗糙(微观),粗化时间不能太长,粗化后孔内环氧玻璃钢的表面应呈现均匀的暗红色。
配方3(浓度)硫酸铜10克/升,酒石酸钾钠40克/升,氢氧化钠20克/升,十二烷基硫酸钠0.2-0.3克/升,2—巯基苯并噻唑0.01—0.02克/升,甲醛(37%)20-25毫升,温度20-25度,时间15-25分钟。
配方4(浓度)硫酸铜28克/升,乙二胺四乙酸二钠50克/升,氢氧化钠20克/升,甲醇250毫升/升,甲醛(37%)12毫升/升,温度32—34度,PH值13,时间15-25分;沉铜配方中的甲醛用量,由温度高低而定,当温度高时取下限,反之取上限,只有当溶液有较强的碱性时,甲醛对铜才有足够的还原能力,所以PH值太低,反应便慢,甚至不反应,太高,则反应太快,难于控制。
Pcb电路板厂家浅谈半孔pcb加工工艺

Pcb电路板厂家浅谈半孔pcb加工工艺随着PCB的进一步发展,不仅有盲孔PCB,还有埋孔,甚至半孔。
半孔是对于已经金属化的孔切割一半的加工,看上去非常简单只要对常规的加工板进行最后的铣外形就行了,实则不然。
特别是有些半孔有纯锡焊接的要求,要在使用过程中不得爆孔和镀层不得剥离的要求,没有合适的工艺安排,是不容易做到的。
半孔pcb又分两种情况:一种是没有焊盘连接的半孔;另一种是有焊盘连接的半孔。
根据半孔的连接状况和最终表面加工工艺的不同,生产所需要的工艺也略有不同。
为了能够达到顾客的要求,我们对此特殊工艺要求的板进行了可行性的探索。
半孔pcb制作工艺和要求是什么?1)图形转移(根据板的具体情况采用干膜或者湿膜)所用的菲林在设计阶段要为在半孔与半孔连接处的铜箔做成一套负片。
2)图像电镀:镀铜按1.0A/dm2施镀15·20分钟,电镀按1.0~1.2A/dm28~12分钟,力求镀层均匀。
退膜:退掉图形转移的膜即可,不可经过蚀刻。
钻孔:需采用精度较高的数控钻孔设备。
在此过CAD数据文件时,辅助钻孔的设计遵循以下原则:A。
正确选择辅助钻孔点,辅助钻孔必须与被加工孔在两边的切割点正相交;不可采用太大的钻刀,若采用不适合的大钻刀,会造成部分半孔的抗蚀镀层被破坏,最终导致经过蚀刻出现孔内无铜,易产生百孔。
B钻刀的大小选择,要保证半孔两边的铜与被辅助钻孔间距最小保持在0.1mm不可以太近3)铣槽孔:必须要求精度较高的铣床进行槽孔。
4)蚀刻:蚀刻后需要检查面铜和半边孔上的铜是否蚀刻干净,若蚀刻不干净会导致后续图镍金工序将其上镍金,从而出现连路。
5)图电镍金:在电镀过程中主要是预防一种特殊情况,表面上的铜箔受镀面积较大,而实际的半孔间距又特别小的情况下,需要特别的控制好电镀的电流,适当的降低电流,延长电镀时间,否则易出现电流过大将油墨击穿而导致连路问题。
6)注意事项:若最后的成品板相对较小,而我们的拼板相对比较大的时候,在外形工序就得先辅助增加定位,否则可能会影响最终半孔的尺寸,因为有的半孔在铣槽孔的时候,可能会出现四边都有铣槽孔的情形,尤其是板厚在1.2mm的产品,就更加容易出现半孔不平整的现象。
什么是金属化半孔PCB?

什么是⾦属化半孔PCB?什么叫⾦属化半孔PCB?所谓⾦属化半孔是指⼀钻孔(钻、锣槽)经孔化后,再⼆钻、外形⼯艺,最终保留⾦属化孔(槽)⼀半。
为控制⽣产⾦属半孔板时,因⼯艺问题⾦属化半孔与⾮⾦属化孔交叉位孔壁铜⽪,通常会采取⼀些措施。
在⽬前电路板打样板⼚很饱和的状态下,愿意和能够⽣产半孔板的板⼚也不多。
宏联电路就是为数不多的⼚家之⼀。
⾦属化半孔PCB相对PCB在各⾏业的应⽤少。
⾦属化半孔容易在铣边时容易将孔内沉铜拉出,因此报废率⾮常⾼。
对于披锋内翻,预防产品因质量⽽须在后⼯序作出修正处理,对此类型板的制作⼯艺流程按以下流程进⾏处理:⼀钻孔(钻、锣槽----板⾯电镀----外光成像----图形电镀----烘⼲-----半孔处理--退膜、蚀刻、退锡----其他流程----外形⾦属化半孔PCB具体⾦属化半孔按以下⽅式处理:所有⾦属化半孔PCB孔位必须以钻孔的⽅式在图镀后,蚀刻前将半孔两端交叉点各钻⼀个孔,1)⼯程部按⼯艺流程制定MI流程,2)⾦属半孔为⼀钻时钻出(或锣出)、图镀后、蚀刻前的⼆钻半孔,必须考虑外形锣槽时会不会露铜,将钻半孔向单元内移动,3)右边孔(钻半孔)a.先钻完,再把板翻转(或镜向);钻左边孔b.其⽬的是为了减少钻⼑对半孔内孔铜的拉扯,造成孔铜缺失。
4)依据外形线的间距取决钻半孔的钻咀⼤⼩。
5)绘制阻焊菲林,锣空位作挡点开窗加⼤4mil处理。
根据多年⽣产经验,可建议设计师设计线路时进⾏修改,改变边缘线到孔中⼼的距离,⼀般设计都是将孔中⼼放在边缘线上,可将控中⼼向下移动,例如孔的直径为1.4mm,两孔之间的距离为2.54mm,板边缘线距离通孔中⼼0.33mm,板厚0.6mm。
壁被切断点的切线和铣⼑的轨迹之间的夹⾓,以前是90度,这次约为60度。
由于板边缘线距离通孔中⼼有⼀定的距离,改变了铣⼑的切⼊⾓,加上板厚特别⼩,孔内的铜就不易被拉出。
⼩批量pcb设计和⽣产同时改进,则可⼤⼤改进PCB半孔板的⽣产良率。
金属化半孔半槽加工的原理与工艺

因为采用顺时针铣刀与顺时针的主轴搭配, 总有因为切削关系,固定有一边产生披锋。于是 根据机械原理,可以使用逆时针铣刀与逆时针 主轴搭配,由顺时针铣刀顺时针旋转制作一边, 再由逆时针铣刀逆时针旋转制作另外一边(如图 4),在这样的制作过程中就不会因为切削关系而 导致披锋。该方法的流程简介便利,采用成型时 一并制作。
图4 顺逆时针各铣半边
图2 顺时针铣刀从左至右效果
图3 顺时针铣刀从右至左效果
1.1 采用电镀锡保护的方法制作的流程与原理
采用电镀锡保护的方法,利用碱性电镀锡 的抗碱性蚀刻的能力,利用碱性蚀刻,将披锋咬 蚀,从而达到去除披锋的目的。同时为了保证在 制作过程中图形的线宽/线隙,会优先采用先蚀刻 出线路不退锡,制作完半孔后使用一个较快的蚀 刻速度去除披锋,再退锡的方法制作。其流程如 下:图形电镀→退膜→碱性蚀刻→铣半孔半槽→ 碱性蚀刻→退锡→后续制作。
机械加工 Mechanical Processing
印制电路信息 2019 No.5
金属化半孔半槽加工的原理与工艺
焦 阳 陈 龙 曾向伟 谢伦魁 (深圳景旺电子股份有限公司,广东 深圳 518102)
摘 要 金属化半孔半槽作为一种方便快捷的侧面导通设计,被应用于各种PCB中。本文通过 铣刀反旋、主轴反转、线路优化、路径优化等技术,对PTH半孔半槽的工艺流程进行 优化,解决板面擦花、披峰等问题,保证了产品品质,同时也大大提升了生产效率。
关键词 金属化半孔半槽;铣刀反旋;主轴反转 中图分类号:TN41 文献标识码:A 文章编号:1009-0096(2019)05-0042-03
The principle and craft of a meliorate process for edge planting
- 1、下载文档前请自行甄别文档内容的完整性,平台不提供额外的编辑、内容补充、找答案等附加服务。
- 2、"仅部分预览"的文档,不可在线预览部分如存在完整性等问题,可反馈申请退款(可完整预览的文档不适用该条件!)。
- 3、如文档侵犯您的权益,请联系客服反馈,我们会尽快为您处理(人工客服工作时间:9:00-18:30)。
PCB线路板半金属化孔的合理设计及加工方法
摘要:半金属化孔成型后的孔壁铜皮翘起、披锋残留问题一直是PCB板件机械加工中的一个难题。
残留在半金属化孔内的铜丝和披锋在下游的SMT厂家的焊接过程中,容易出现焊点不牢、虚焊、桥接短路等问题。
因此半金属化孔的铜皮翘起和披锋一般不为大多SMT厂家的IQC所接受。
本文介绍了从CAM/CAD设计上以及加工技巧上有效的控制、减小半金属化孔的铜皮翘起和披锋的几种方法,同时评估各种加工方法对成本控制和制作周期的影响。
如何控制半金属化孔成型后的孔壁铜皮翘起、披锋残留的产生一直是PCB板件机械加工中的一个难题。
这是因为一般的PCB成型的机械加工方式无外乎数控锣床锣板、机械冲床冲切等方式,这些方式在切断PTH孔铜的时候,无可避免的会导致余下部分PTH孔的断面上残留下铜丝披锋,严重的甚至有孔壁铜皮翘起现象。
这样单元边整排有半金属化孔的PCB,个体都比较小,多用于载板上,作为一个母板的子板,通过这些半金属化孔与母板以及元器件的引脚焊接到一起。
所以如果这些半金属化孔内残留有铜丝披锋,在SMT 厂家进行焊接的时候,将导致焊脚不牢、虚焊;严重的造成两引脚之间的桥接短路。
多数SMT厂家不易接受此类PCB缺陷,而据笔者所知,现在多数PCB厂家是以人工修理作为应对方案。
机械加工原理:下面我们从机械加工的原理来分析披锋的成因。
由于机械冲床冲切方式几乎不大可能应用到半金属化孔的外形加工上,在此只针对数控锣床锣外形的原理进行分析介绍。
我们知道,一般的数控锣床的SPINDLE的旋转方向都是顺时针的,习惯上称为右旋刀。
如下图(一),假定一个金属化孔在PCB单元外形上,A、B两点是它们的交点,锣板方向如图所示。
那么当右旋的锣刀在锣到B点的时候,B点受到一个向右的剪切力F。
理想状况下剪切力F将B处切断。
但是附着在孔壁上的铜是具有延展性和韧性的,锣刀在切到孔壁以铜为主的金属化层的时候,会由于以下原因产生披锋残留:
1、锣刀由于转速不够和磨损的原因,造成锣刀的切割力不足;
2、孔铜与孔壁结合力不足,在F的作用下,断口附近孔铜脱离;
3、孔铜的延展性,特别是热风整平或沉金等表面处理后,又增加了金属层的厚度和延展性及韧性,造成切割不断;
大多数情况下,披锋只在B点而不会在A点产生。
这是因为锣刀在切割到A点的断面的时候,先切割到A点的孔壁金属化层。
A点金属化层同B点的孔壁金属化层一样,会由于金属的延展性发生形变,但A 点断面背靠着基材层,有效地防止了金属层的延伸以及金属层与孔壁的脱离。
只要锣刀没有严重磨损,切割力足够,A点锣后的断面会很平滑,没有披锋产生。
从原理分析中,我们很容易想到只要我们先将板件反转过来,还是用原来的锣板方向,先把B点处的铜丝锣断,再按正常情况锣板,就能防止披锋的
产生。
不过此种方法只适用于单个金属化孔在外形线上,而且孔径比较大的情况。
现时常规最小直径的锣刀是中0.80mm,如果我们面对的是一整排的类似邮票孔的半金属化孔,并且孔间距比较小、孔径也比较小的时候,我们应该怎么做呢?如下图(二)所示。
设计和加工方法
一、二次钻法
设计方法:
按锣板方向在半金属化孔的B点处在PTH后加钻一个适当的NPTH孔,预先切断B点断面。
这里要注意几个细节。
1、 NPTH孔的孔径的选择:
2、一般数控钻机的S P I NDL
E的旋转方向也是顺时针的,将PCB板件翻转过来钻孔;并且应选用槽形钻嘴钻孔。
所以要切断B点的孔铜,必须考虑到PCB板件的涨缩变化和二次钻以及锣机的对位精度,NP TH孔应该在钻带中设计为削入板件内2-4mil ;
3、如果按下面的碱性蚀刻流程,需要把半金属化孔的焊盘单元外的部分削入外形线2-4mil如果采用下面的酸性蚀刻流程,则单元外的焊盘要保留单边比孔大5mil以上。
生产流程:
l. 碱性蚀刻流程:板件→一次钻孔→PTH→外层图形转移→图形电镀→退膜→碱性蚀刻→二次钻孔→退锡→感光阻焊→表面处理→字符印刷→锣外形
2. 酸性蚀刻流程:板件→一次钻孔→PTH直接加厚孔铜→外层图形转移→酸性蚀刻→二次钻孔→感光阻焊→表面处理
加工效果:下面是我们采用上述两种流程批量生产某板件后采集的数据。
每个流程的量产数量是350个PANAL,4200个出货拼板单元,16800个PCS。
二次钻孔时采用两块/叠生产,按出货单元计量比例。
(如果按PCS计量,比例更低。
)改善效果十分明显。
优劣分析:从制作成本的角度来看,增加的二次钻孔流程延长了生产的制作周期,钻孔成本也成倍增加。
这是因为要保证加钻孔有效的切断孔铜,需要使用特殊槽形钻嘴并且钻孔参数需要调整,钻孔叠数也不可能多。
同时二次钻法对后面工序的影响也不可忽视。
首先二次钻后在半PTH孔内将残留部分板粉,必须采用高压水洗的方法予以清除,以免对绿油和表面处理带来不利的影响。
同时对绿油工序而言,在加钻孔位置必须要加单边比孔大2mil左右的绿油开窗,防止绿油残留在半金属化孔里。
采用碱蚀二次钻法注意尽量避免对板件锡面的擦花。
使用之前钻机机台要清洁干净。
碱蚀二次钻法的外层线路菲林削焊盘之后也存在着在图形电镀时孔内上锡不良的潜在缺点。
不过相对于人工修理给交期带来的巨大影响和工时成本增加,二次钻法在大批量生产时不失为一个可行方法。