LEAN相关指标的定义与计算方法
精益生产衡量指标计算方法

库存周转期和周转率
原材料的库存周转期(天)=30天/原材料的库存周 转率; 原材料的库存周转率=2×当月原材料的出库金额 总和/(月期初原材料库存金额总和+月期末原材料 库存金额总和);
成品的库存周转期(天)=30天/成品的库存周转率; 成品的库存周转率=2×当月成品的出库金额总和/ (月期初成品库存金额总和+月期末成品库存金额 总和);
BTS计算方法
Volume%产量性能用于监控生产计划完成情况 Volume%=实际生产数量/计划生产数量; 混线性能Mix%用于测量在厂内制造的产品系/ 型号/类型等在适当的生产日的完成比率。 Mix%=实际生产品种数/计划生产品种数;
顺序性能Sequence%用于测量在适当的生产日 按照正确的生产顺序完成生产任务的比率 Sequence%=按计划顺序生产品种数/计划生产品 种数;
A B
90
100-10 (補修+報廢) /100 = .90 一次合格產出
6
100
100-16 (補修+報廢) /17 5
90-12 (補修+報廢) /90 = .86 一次合格產出
R
K
報廢 2
D
87-7 (補修+報廢) /87 = .91 一次合格產出
報廢品
生产周期
计算一批(1000件)产品需要的生产时间;
设备总效率OEE
OEE = 设备利用率 x 作业效率 x 良品率 對象: 瓶颈工程/產能較不足之工程
设备利用率
稼动率=设备实际作业时间/设备可用时间 可用时间:指设备可以利用的时间, 设备可用时间=(设备计划运行时间-固定 的休息/停机时间)设备实际作业时间=每天 设备实际工作时间之和 举例:甲班全天出勤时间为8小时,中途休息时 间为20分钟,设备故障停机修理时间为40分钟 设备稼动率=(8x60-20-40)/(8x60-20)
精益生产(LEAN线)介绍
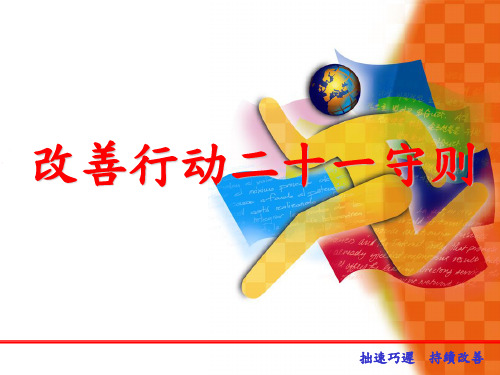
拙速巧迟 持续改善
第三招:实施一人多序 ——标准作业
★ 确定制造节拍 ★ 确定作业顺序 ★ 确定标准手持 ★ 搬运工作标准化 ★ 少人化 ★ 多能工培养 ★ 动作的三不政策:不摇头、不转身、 不“插秧”
第十招: 追求完美的持续改善
1、改善的需求为基础 2、并不只做会做的事,向应该做的事挑战 3、应成为改善者,不能成为被改善者 4、彻底的追究真相 5、改善设备之前先进行作业改善 6、 改善方案确定之后,首先确认安全和质 量
拙速巧迟 持续改善
企业的钱都去了哪里?
几乎没有一个企业认为自己有充足的 资金,那么整个供应链上的资金去了哪里? 全部变成了库存被“储存”起来。破产企业 的共同点:库存巨大 。
拙速巧迟 持续改善
工厂中七大浪費
1.制造过多(早)的浪費. 2.库存的浪費. 3.等待的浪費. 4.加工的浪費. 5.不良重修的浪費. 6.动作的浪費. 7.搬运的浪費.
拙速巧迟 持续改善
两大支柱 精益生产方式 自 动 化
拙速巧迟 持续改善
准 时 化
自动化的定义
自动化是当生产有问题时,设备或生 产线具有自动停止或作业员使之停止的能 力。
理念的挑战拙速巧迟持续改善拙速巧迟持续改善用力做并没有效率在现场员工的动作有创造价值和不创造价值之分通过增加劳动强度和延长劳动时间的做法并不能提高劳动效率努力改善消除不创造价值的工作是人性化管理的表现只有这样效率才能提高拙速巧迟持续改善改善是这样完成的改善目标的达成以克服问题为主要手段不要被问题挡住改善的脚步拙速巧迟持续改善拙速巧迟持续改进凡事都有更好的方法
Lean 之定义
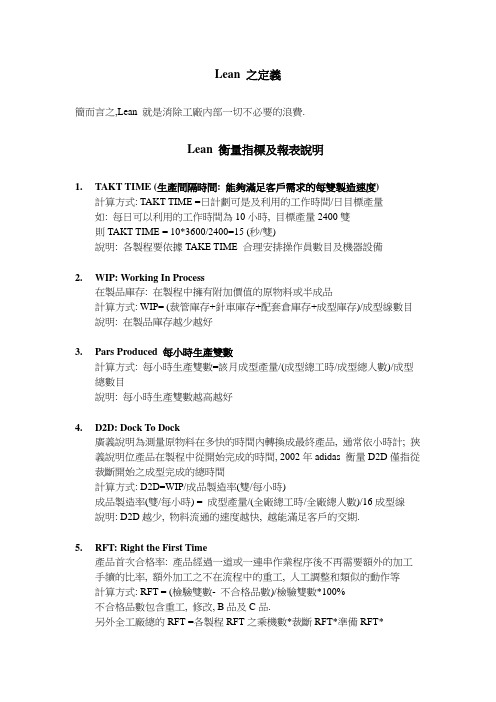
Lean 之定義簡而言之,Lean 就是消除工廠內部一切不必要的浪費.Lean 衡量指標及報表說明1.TAKT TIME (生產間隔時間: 能夠滿足客戶需求的每雙製造速度)計算方式: TAKT TIME =日計劃可是及利用的工作時間/日目標產量如: 每日可以利用的工作時間為10小時, 目標產量2400雙則TAKT TIME = 10*3600/2400=15 (秒/雙)說明: 各製程要依據TAKE TIME 合理安排操作員數目及機器設備2.WIP: Working In Process在製品庫存: 在製程中擁有附加價值的原物料或半成品計算方式: WIP= (裁管庫存+針車庫存+配套倉庫存+成型庫存)/成型線數目說明: 在製品庫存越少越好3.Pars Produced 每小時生產雙數計算方式: 每小時生產雙數=該月成型產量/(成型總工時/成型總人數)/成型總數目說明: 每小時生產雙數越高越好4.D2D: Dock To Dock廣義說明為測量原物料在多快的時間內轉換成最終產品, 通常依小時計; 狹義說明位產品在製程中從開始完成的時間, 2002年adidas 衡量D2D僅指從裁斷開始之成型完成的總時間計算方式: D2D=WIP/成品製造率(雙/每小時)成品製造率(雙/每小時) = 成型產量/(全廠總工時/全廠總人數)/16成型線說明: D2D越少, 物料流通的速度越快, 越能滿足客戶的交期.5.RFT: Right the First Time產品首次合格率: 產品經過一道或一連串作業程序後不再需要額外的加工手續的比率, 額外加工之不在流程中的重工, 人工調整和類似的動作等計算方式: RFT = (檢驗雙數- 不合格品數)/檢驗雙數*100%不合格品數包含重工, 修改, B品及C品.另外全工廠總的RFT =各製程RFT之乘機數*裁斷RFT*準備RFT*針車RFT*底加工RFT* 成型RFT註; RFT 越高品質越好, 越穩定6.BCS: Build to Customer Schedule依客戶計劃生產實際達成率計算方式: A全廠BCS =週訂單生產達成率之乘積週訂單生產達成率指訂單生產的雙數而非訂單張數B 每條線BCS= 每日實際產能/每日目標產能*100%說明; BCS 越高, 越能準時按客戶交期出貨.7.V A: Value – Adding附加價值, 任何活動或作業能轉換原料成為顧客願意花錢支付的產品, 這樣的活動或作業稱為有附加價值, 如高周波, 電繡等.計算方式: 附加價值比率=作業時間之和(包括裁管, 針車, 底加工, 成型)/總的生產前置時間(D2D)作業時間之和= 各型體本月份生產作業時間之平均值.說明: 附加價值率越高, 工廠浪費就越少.8.Productivity (生產力; 每人每小時生產雙數Prs/Head Hour)計算方式: 生產力=成型產量/直接勞工的總工時(直工人數指從裁斷至大包裝所有直接人力, 但幹部, 領料, 發料, 技工, 電工, 生管, 品管, 資材, 成品倉人員均不包括在內)說明: 生產力越高, 效率越好.9.Inventory Turn (資材庫存週轉量)計算方式: 庫存週轉量=前12個月的材料成本總合/本月材料庫存金額(含面底部材料)說明: 庫存週轉量越高越好一、Lean 的意義說明:減少浪費, 使生產順暢;Lean 試著去讓生產順利後, 再對員工, 機器作最佳化的處理, 平衡;Lean 要求第一次就做對, 減少重工所衍生的浪費;Lean 提倡*小組化*, 強調*改善*信念:Lean 是百分之二十的技術搭配百分之八十的實行二、附加價值的定義任何改變原物料, 是他成為顧客願意出錢支付的產品的作業及活動三、非附加價值的定義浪費時間或資源卻無法增加顧客任何價值的活動作業四、工廠七大致命的浪費五、OPF(單件流程)的好處:1.縮短前置時間(從前到後)2.維持原有產出3.平滑流程4.最低的在製品數量5.容易找出問題點六、什麼是小組設計(Cell Design)?1.為了減少浪費並達到單件流程所連接附加價值活動的順序型製造小組.2.達成Lean 生產管理工具, 手段小組設計的目標;1.較高的附加價值比2.較短的前置時間3.較少的空間使用4.較簡單的生產模式5.人員使用的最佳化七、疏失和不良品的定義疏失: 錯誤或不當的行為, 情況, 造成不完美的流程不良品: 由於不成功的流程所造成無法銷售的產品八、5SSort (整理): 去掉不需要的東西Set in Order (整頓): 需要品定點訂位放置使工作現場有條理有順序, 當需要是能以最快的速度取出.Shine (清掃): 把工作區域打掃乾淨, 創造一個安全, 舒適的工作環境Standardize (清潔): 創造標準的作業程序Sustain (素養):養成良好的行為習慣,提高員工士氣,滲透以廠為榮的自豪思想,確定工作環境之污染的根本原因並實施解決方案。
Lean基础知识简介
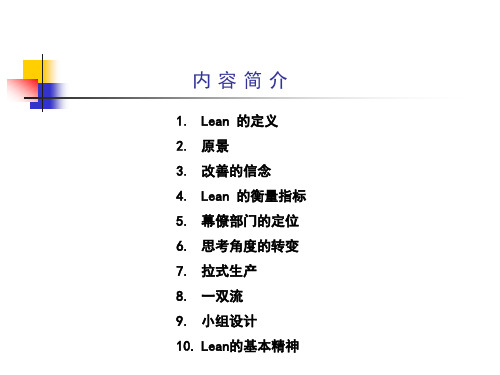
Lean 定義 定义:消除工厂内一切不必要的浪费,亦称精实生 产; Lean試著去讓生產順利後,再對員工、機器作最 佳化的處理、平衡; Lean要求第一次就做對,減少重工所衍生的浪費;
பைடு நூலகம்
VISION願景
Vision─願景,心中對未來的一種景象; 有願景,沒行動,只不過是一場夢罷了; 沒願景,有行動,只不過浪費力氣; 結合願景與行動卻可改變世界;
好的願景如何造成?
由領導人發起; 是可以共享並給予支持的; 是整體的但亦是細緻的; 是正面的且令人鼓舞的;
信念
“Lean
是百分之二十的技術搭配百分 之八十的實行。”
没有计划的工作是空洞 没有措施的管理是空谈
成功的人找方法,失敗的人找理由 今日工作不努力,明日努力找工作
Lean构成要素
即使我拥有原料除非我收到訊號否所花費的更多所花費的更多所花費的更多所花費的更多opf一双流容易找出問題點基本的小組概念leanean生產管理的工具手段生產管理的工具手段原料仓成品仓中转仓中转仓成品仓原料仓人員使用的最佳化lean推行后你将会发现
内容简介
1. Lean 的定义 2. 原景 3. 改善的信念 4. Lean 的衡量指标 5. 幕僚部门的定位 6. 思考角度的转变 7. 拉式生产 8. 一双流 9. 小组设计 10. Lean的基本精神
计算公式:WIP/小时产能;
LEAN衡量指标—D2D
D2D(总前置时间):从材料进厂至成品出货 的时间,包含MLT,原材料及成品存放时间;
计算公式:D2D=MLT+原材料库存时间+成品 库存时间;
LEAN 相关名词解释

1.LEAN 相關名詞解釋(1)WIP: WORKING IN PROCESS在製品庫存:在製程中擁有附加價值的原物料或半成品WIP=(裁管庫存+針車庫存+配套倉庫存+成型庫存)/16如:全廠WIP=[16503(裁管)+47796(針車)+67294(配套倉)+43341(成型)]/16=10933雙(平均每條線)(2)D2D: DOCK-TO-DOCK製程完成期:由原物料轉換成最終產品所需的時間,這裡僅指從裁斷開始至成型完成的總時間D2D=WIP/每小時成品率;如:每小時成品率=成型產量/(全廠總工時/全廠總人數)/n條成型線=759948/(2308576/11286)/成型線數=233雙/小時(平均每條線)全廠D2D=10933(WIP)/233=46.93小時(平均每條線)(3)RFT: RIGHT THE FIRST TIME產品第一次合格率=(檢驗雙數-不合格品數)/檢驗雙數*100% ;不合格品數包含重工、修理、B品和C品全廠總的RFT=各製程RFT之乘積=裁斷RFT*準備RFT*台板印刷RFT*電繡RFT*電腦針車RFT*針車RFT*底加工RFT*成型RFT (注:各製程中凡設有全檢站的地方都應包含在內)如:全廠RFT=98.99%*99.48%*99.75%*98.51%*94.49%*96.02%*98.4%*94.01%=81.22%(4)BCS: BUILD TO CUSTOMER SCHEDULE依客戶(計畫)生產實際達成率BCS=周訂單生產達成率之成積(周訂單生產達成率指訂單生產的雙數而非訂單張數)如:全廠BCS=93.3%(第一周) X 100% X 97.63% X 99.3%=90.45% (5)TAKT TIME生產間隔時間:能夠滿足客戶需求的每雙製造速度TAKT TIME=日計畫可實際利用的工作時間/日目標產量如:每日可利用的工作時間為10小時,目標產量2400雙,則TAKT TIME= 10*3600/2400=15(秒/雙)(6)LEAD TIME生產前置時間(意義同D2D一樣)如成型LEAD TIME為從放一雙鞋面開始經過所有的生產工序至成品上吊籃時間為止(7)VA: VALUE-ADDING附加價值:任何活動或作業能轉換原料成為顧客願意花錢支付的產品,這樣的活動或作業稱為有附加價值,如高周波、電繡等﹔附加價值比率=附加價值時間(作業時間)/總的生產前置時間(D2D) VA=本月份生產各型體附加價值時間之平均值/D2D如:全廠VA=5638.8(附加價值時間平均值)/46.92/3600*100%=3.34%(8)NVA: NON-VALUE-ADDING非附加價值:任何花費時間和資源但卻不增加產品的價值的作業或活動。
LEAN的卡片知识

1.我们公司有CI部门,CI的含意是什么:CI是:Continuous Improvement的缩写,其中文含义是:持续改善。
2 什么是aLF?aLF是adidas Lean Fulfillment的缩写,其中文含义是:精益实施条例,每年adidas将按此标准条例对各工厂进行审核,审核范围包含:1管理/信任、2人员、3资讯、4产品、5供应商/组织/客户、6制程。
3.LEAN含意及目的是什么?LEAN的中文含义是:精益生产目的:经由消除浪费来缩短由客户下单到交运时间的生产理念精:精益求精,益:效益,意思是说精实,从实际出发,消除一切不必要的浪费。
4.什么是浪费?答:从客户角度看,任何资源的使用而未增加价值。
例如:在生产过程中,操作动作及流程工序没有任何价值的工作。
(如领料、发料、缴库、洗鞋、剪线、搬运、送修)。
5.工厂的八大致命浪费是什么?1.生产过剩 2库存 3过度加工 4人员移动或动作 5 运输 6.等待7.次品和返工 8认知断层6.什么是后拉式生产模式?答:一种基于消费而不是预测的生产模式.每当某个元件消耗时, 上游的生产环节或供应商将生产或提供刚好够的这些部件然后停止,直到他们再次得到需要补给的信号例如:加工生产依出货要求,针车、贴底生产依加工的要求;裁断、手工依针车要求7.公司有哪些方面的奖励制度?答:公司有以下方面的奖励制度:多能工考核技能奖、提案改善奖励制度、周生产奖金、6S评估奖金、材料超耗奖金、减编奖等等。
8.在改善活动中,被精减出的人员公司如何安排?答:公司对因改善活动而被精减的人员会按劳动合同确保其收入和工作条件。
公司会采用调动工种的方法培训新技能,重新分配工作,同时根据其技能发放技术津贴9.每年公司会有哪些LEAN相关的培训答:每年公司会针对全厂个各阶层拟定外部(由adidas CI 或顾问公司)、内部(CI部)带薪的培训课程。
10.何谓多能工,培训多能功好处是什么?答:多能工是指一个人在线上能够操作多项工序,具有多方面技能的人员,培训多能工的好处:是可以相互协助或顶位,使生产平衡化。
精益生产衡量指标计算方法

生产周期
计算一批(1000件)产品需要的生产时间;
设备总效率OEE
OEE = 设备利用率 x 作业效率 x 良品率 對象: 瓶颈工程/產能較不足之工程
设备利用率
稼动率=设备实际作业时间/设备可用时间 可用时间:指设备可以利用的时间,
FORD精益生产体系 的衡量指标
(Lean Manufacturing)
精益生产(Lean)的衡量指标
•首次合格率
(FTT)
•仓库进货到仓库出货時間 (DTD)
•按计划制造
(BTS)
•设备总效率
(OEE)
首次合格率FTT
隱藏 因素
報廢 10
報廢 3
報廢 2
開始 : 100 units
R 10 A
結束: 85件 “好” 的產出
FTT
首次合格率FTT是根每一工序合格率的乘积: .90 ×.84 ×.86 ×.91 = 59%
将每个月每个产品每批的FTT进行平均, 就得到每个产品的FTT;
(Lean)衡量指標
仓库进料到仓库出货时间 (DTD)
• 以平均的交货批量,如1000件为一 批计算;
设备可用时间=(24小时-固定的休息/停 机时间)×30天 设备实际作业时间=设备实际工作时间 举例:甲班全天出勤时间为8小时,中途休息时 间为20分钟,设备故障停机修理时间为40分 钟 设备稼动率=(8x60-20-40)/(8x60-20)
作业效率
作业效率=实际产量/标准理论产量; 或作业效率=总标准工时/总实际工时; 举例:设备M-01某天生产N-1产品,设备实
LEAN衡量指标

人均生产力(POH)
每人每小时的产量. 包含所有的直接员工,包含车间主管,线长, 物料传递员,机修和QC 外部的供应商不包含在内.
停机时间
停机时间是指任何非计划的停线。导致停机时间的原 因包括:短料,机器坏掉,品质问题。
核心价值流的停机时间是裁断停机时间,针车停机时 间的总和
注意 : 停机时间一般是用分钟来记录的。
绩效的衡量一定要与为客户创造价值直接相连。
衡量指标的目的
►
识别改善机会;量化改善机会
• 解决办法会带来绩效改善
改善
解决
理解
• 对问题的深入理解有助于找 出好的解决方法
• 衡量指标帮助提升对问 题的理解
衡量
衡量指标的原则
优秀的衡量指标是: 1.简单 –使用容易获取、计算和更新的指标。复杂的 计算或者过度的分析会使人们逃避。 2.直接关联 – 流程的变化对指标有清楚的,可衡量的 影响 3.提供信息 – 适当的衡量指标也许并不能总是显现出 问题的源头,但是他们可以警告我们问题的存在。 4.精简 – 每个区域有2-3个关键指标即可 5.目视显示 – 结果应该张贴公布,让每个人都能看到
►
如果返修在节拍时间之内完成,且在站内修复, 就不是重工。
首次通过率
核心价值流 FTT= 良率 (原材料) x 良率 (裁断) x 良率 (刺绣/印刷/胶水/削 边…) x 良率 (针车) 裁断的良率 : 按照片来计算
良率=
裁断总片数 – 不良- 返工) 裁断总片数
裁断总片数= 每天目标产量 x 材料片数
Lead time – “门到门”
原物料仓库
生产时间
成品
原物料仓库
W I P
LEAN

LEAN(瘦身)知識講座
(續上)
說明:BCS越高,越能准時按客戶交期出貨。
F、VA(附加价值)
定義: 任何活動或作業能轉換原料成為顧客愿意 花錢支付的產品,這樣的活動或作業稱為 有附加价值,如高周波、電繡等。 計算: 附加价值比率=作業時間之和(包括裁管、 針車、底加工、成型)/總的生產前置時 間(D2D) 注: 作業時間之和=各型体本月份生產作業時 間之平均值。
定義:從設計、下單、到提供一 個實際產品于客戶之間的 所有特定活動(包括附加价 值和非附加价值作業 ).
LEAN(瘦身)知識講座
13、何為价值流地圖(VSM)?
定義:在价值流中生產特定產品 所需要的所有步驟圖形。
LEAN(瘦身)知識講座
14、何為型体轉換?
定義:從上一型体最后一件物 品制造出來后到下一新物 品 產生出來的時間。
定義:能夠滿足客戶需求的每雙制造速度。 計算:TAKT TIME=日計划可實際利用的工作 時間/日目標產量。 說明:各制程要依据TAKT TIME合理安排操作 數目及机器設備。
B、WIP(在制品庫存);
定義:在制程中擁有附加价值的原物料或半成 品。
LEAN(瘦身)知識講座
(續上)
計算:WIP=(裁管庫存+針車庫存+配套倉庫存+成 型庫存)/X – 說明:在制品中庫存越少越好。
7、拉式生產三大指導原則是什么?
A、絕不接受瑕疵品; B、絕不制造出瑕疵品; D、絕不將瑕疵品流向下游;
LEAN(瘦身)知識講座
8、什么叫OPF(單件流程)?
定義:每雙鞋子以獨自的單位流 經生產流程,也被稱作流 水線生產。
lean的衡量指标

精进改善
LEAN衡量指标的定义
衡量指标:针对检验现场管理效果成绩 的相关指标,以便及时发现问题而进行 改善。
2
精进改善
衡量指标所带来的好处
将管理目标和工厂活动相结合 建立改善的基准 找出需要改善的活动和协助消除浪费 允许我们量化、重复最佳表率
3
精进改善
如何衡量是否成功
总的前置时间D2D 首次质量正确率RFT 机器效能使用率EEOE 依客户生产率BCS
6
精进改善
D2D所带来的改善
改善顾客交期 减少成品库存 较少的不合格品 减少流程中的等待时间
7
精进改善
在制品库存Working In Process (WIP) 在制品库存 在制品库存:在制程中拥有附加价值的原 物料或半成品。 计算方式:WIP=D2D*小时产能 说明:在制品库存越少越好
例﹕某工作段D2D为0.8小时﹐小时产能70双/小 时﹐则: WIP=0.8*70=56双
例﹕某工序加工时间PT为120秒﹐加工批量PBS 为1双﹐作业人数m为8人﹐则: 该站CT周期时间=120/1/8=15秒
11
精进改善
间隔时间Takt Time (TT) 间隔时间
生产间隔时间:能够满足客户需求的每双制造 速度,通常用秒来表示。 公式: TT=工作时间/顾客需求双数 例如:某 针车组一天计划时间为9小时,顾客需求鞋子为 540双,则该线:
9
精进改善
周期时间Cycle Time (CT) 周期时间 周期时间:一人或一组人在某道工序平均完 成一件产品所花的时间。 具体定义:规定必要工作技能及熟练程度的 操作者,在正常操作条件下,以标准的作业 方法及合理的劳动强度和速度,完成符合质 量要求的工作所需的作业时间。
精益(Lean)管理工具与方法课件
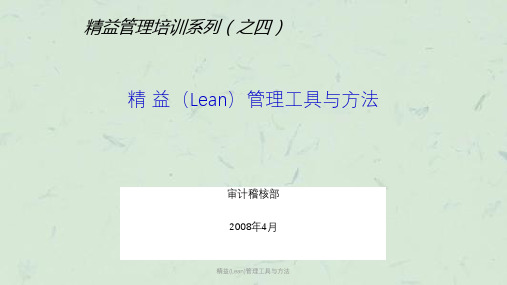
■拉动(Pull)
■ 传统的生产方式都是在前 道工序生产好零件后,将其拿 到后面的工序进行进一步加工, 即自前向后。这相对丰田,叫 作推动(Push)
什么是拉动呢?
■ 而丰田的拉动(Pull)不同 于与传统的生产方式。
大野耐一来自超市购物的启发
■由后一道工序在需要的时刻到前一道工 序去领取需要数量的、需要的东西,而前 一道工序则只生产所需领取的数量,也就 是订单分解·····(看板)
■ 价值流图的绘制
1、绘制价值流现状图 2、绘制未来价值流图
2.1 发现浪费:从顾客的角度而不是从公司、某个部门或机构的角度确定价值 2.2 设计并实施精益的未来价值流的准则 3、研究现状,找出差异并绘制未来价值流图
4、计划的制定、实施与效果评估 ,持续改进(PDCA)
精益(Lean)管理工具与方法
■ 短期看: 降低浪费、保证质量:降低不合格产品流到一个工序所
造成的相关浪费、追求零缺陷产品 ■ 长期看:
彻底消除浪费、保证顺畅流动:及时发现并找到问题根 源( 三现主义、 6WHY),彻底消除浪费。
精益(Lean)管理工具与方法
三、 TPS系统及工具的应用介绍 (价值续流程)图
■ 浪费----不增加任何价值的活动就是浪费
1、在市场稳定的情况下,可以明确 需要改进的环节,从而采取针对性的 措施进行调整 。
2、能够有效防止过量生产和供应不 连续的问题,并确定工序间的标准库 存量。
精益(Lean)管理工具与方法
三、 TPS系统及工具的应用介绍(续) 准时制是以均衡化生产为前提的,由⑴生产的流程化(FIow)、⑵节拍时间(Tact Time)、⑶拉动(Pull)这三部分组成。
二、T两P大S支架柱之构二:及自働两化大支柱(续)
Lean术语
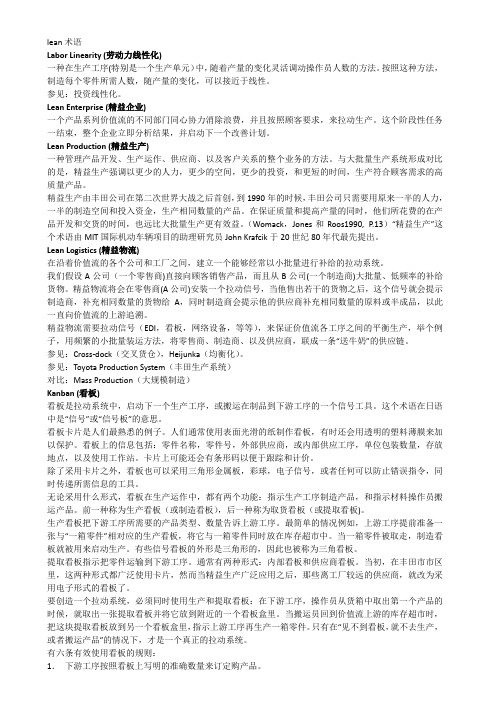
lean 术语Labor Linearity (劳动力线性化)一种在生产工序(特别是一个生产单元)中,随着产量的变化灵活调动操作员人数的方法。
按照这种方法,制造每个零件所需人数,随产量的变化,可以接近于线性。
参见:投资线性化。
Lean Enterprise (精益企业)一个产品系列价值流的不同部门同心协力消除浪费,并且按照顾客要求,来拉动生产。
这个阶段性任务一结束,整个企业立即分析结果,并启动下一个改善计划。
Lean Production (精益生产)一种管理产品开发、生产运作、供应商、以及客户关系的整个业务的方法。
与大批量生产系统形成对比的是,精益生产强调以更少的人力,更少的空间,更少的投资,和更短的时间,生产符合顾客需求的高质量产品。
精益生产由丰田公司在第二次世界大战之后首创,到1990年的时候,丰田公司只需要用原来一半的人力,一半的制造空间和投入资金,生产相同数量的产品。
在保证质量和提高产量的同时,他们所花费的在产品开发和交货的时间,也远比大批量生产更有效益。
(Womack,Jones和Roos1990, P.13)“精益生产”这个术语由MIT国际机动车辆项目的助理研究员John Krafcik于20世纪80年代最先提出。
Lean Logistics (精益物流)在沿着价值流的各个公司和工厂之间,建立一个能够经常以小批量进行补给的拉动系统。
我们假设A公司(一个零售商)直接向顾客销售产品,而且从B公司(一个制造商)大批量、低频率的补给货物。
精益物流将会在零售商(A公司)安装一个拉动信号,当他售出若干的货物之后,这个信号就会提示制造商,补充相同数量的货物给A,同时制造商会提示他的供应商补充相同数量的原料或半成品,以此一直向价值流的上游追溯。
精益物流需要拉动信号(EDI,看板,网络设备,等等),来保证价值流各工序之间的平衡生产,举个例子,用频繁的小批量装运方法,将零售商、制造商、以及供应商,联成一条“送牛奶”的供应链。
lean的概念

lean的概念
“Lean”是一种管理理念和经营方法,旨在通过减少浪费、提高
效率、提供更好的价值,从而改进生产和运营过程。
它起源于丰田汽车公司的生产系统(Toyota Production System),并在
全球范围内得到广泛应用。
“Lean”强调消除所有不增加价值的活动和流程,这些被称为“浪费”。
它将价值定义为顾客愿意为之付费的活动或产品特征。
通过识别和消除浪费,企业可以提高生产效率、降低成本,并提供更高质量的产品和服务。
“Lean”注重通信、合作和员工参与,依靠团队的协作和创新来
优化工作流程。
它也强调持续改进和学习,鼓励员工提出改进建议和解决问题。
此外,“Lean”还强调为了满足客户需求而生产,避免过度生产造成的浪费。
总体而言,“Lean”的目标是实现创造价值的高效生产,提供高质量的产品和服务,满足客户需求,并最大限度地减少浪费。
精益生产管理体系方式

A车间计划
成品计划
+Hale Waihona Puke 看板看板看板
看板
JIT即日生产计划的制定与执行
各生产中心用看板指示好处?
01
02
03
主生产计划与看板实施6个基础条件
料编号码体系建立 坐标制定 房仓位坐标制定 主生产计划零点的确定 工序LT(Lead Time) 提前量计算(前置时间Lead Time )
JIT变革需要从实物流改善为起点
精益生产的座右铭: “永远不变的是‘变化’”。 “永远存在更好的方法”
JIT的信息流流将从生产指挥做起
改善的着眼点: 从现场5S为基础 由点到线,由线到面,由面到链。 1、先从制造过程瓶颈点、问题点改善。 2、在不断积累对瓶颈、停滞、搬运、库存等点 的改善,所有的物、人被激活使之流动,变 成 “流水线” 3、以选定的样板产品纵向展开,完成了线的 改善之后,就让别的车间向这个车间看齐, 就变成“面的改善”。这一般称为“横向展开”。 4、最终为链的改善:销售←生产→供应商
合同评审
致生产部: 对于上述N周、N+1周、N+2周的生产量,是否能完成。 能完成 2、附加条件能完成 3、绝对不能完成 若选2、3时,请简述原因与附加的条件等。 制定人: 审核人: 日期:
合同评审
致库房: 对于上述N周、N+1周、N+2周的生产量,物料是否具备。 有 2、不足 若选2时,请附上品名及数量明细清单 制定人: 审核人: 日期:
仓库库存成本制度案例(续一)
每月仓库管理科的经费(例办公用品、清洁费用、电费等)为 5万元 /月,请根据上述数据建立模拟公司。 分析 :建立模拟成本,也就是制定:
零部件、材料的库存 半成品的库存 成品的库存 已向供应商订购的在途零部件 已发货的在途成品
OEE的计算范文

OEE的计算范文OEE(Overall Equipment Effectiveness)是一种用于衡量设备效率的指标,它是由LEAN制造系统中推崇的一种研究方法,以便监测、管理和改进制造设备的综合生产绩效。
计算OEE需要考虑到三个主要因素:设备的可利用性(Availability)、设备的性能效率(Performance Efficiency)以及产品的质量符合率(Quality Rate)。
下面将详细介绍每个因素的计算方法及其意义,以便更好地理解和应用OEE。
1. 可利用性(Availability)的计算方法:可利用性是指设备在规定生产时间范围内,能够正常运行的时间比例。
它由设备实际运行时间减去设备计划停机时间之和再除以规定生产时间得到。
可利用性=(设备实际运行时间-设备计划停机时间)/规定生产时间*100%2. 性能效率(Performance Efficiency)的计算方法:性能效率是指设备在规定生产时间内,实际生产数量与理论生产数量之比。
它由实际生产数量除以理论生产数量得到。
性能效率=实际生产数量/理论生产数量*100%3. 质量符合率(Quality Rate)的计算方法:质量符合率是指设备在规定生产时间内,实际合格产品数量与实际产品数量之比。
它由实际合格产品数量除以实际产品数量得到。
质量符合率=实际合格产品数量/实际产品数量*100%将上述三个指标综合起来即可计算OEE,计算公式如下:OEE=可利用性×性能效率×质量符合率1.收集数据:收集设备的实际运行时间、设备计划停机时间、实际生产数量、理论生产数量、实际合格产品数量以及实际产品数量等数据。
2.计算可利用性:使用上述公式计算可利用性。
设备实际运行时间指设备从开始生产到结束生产的时间,设备计划停机时间包括计划维护、更换模具等非生产时间。
3.计算性能效率:使用上述公式计算性能效率。
理论生产数量指设备在规定时间范围内能够生产的最大数量,通常由设备的设计能力决定。
- 1、下载文档前请自行甄别文档内容的完整性,平台不提供额外的编辑、内容补充、找答案等附加服务。
- 2、"仅部分预览"的文档,不可在线预览部分如存在完整性等问题,可反馈申请退款(可完整预览的文档不适用该条件!)。
- 3、如文档侵犯您的权益,请联系客服反馈,我们会尽快为您处理(人工客服工作时间:9:00-18:30)。
LEAN 相關指標定義與計ห้องสมุดไป่ตู้方法
衡量指標:將生產流程中的各種情況(品質/效率…)量化成為一種統一標準的公式,用來客觀評估的一種績效管理方式
衡量指標及計算方法: 1.TT(節拍時間):能夠滿足客戶需求的每雙產品的製造速度。 計算公式:TT=工作時間 ÷ 生管派單量 例如:S1線計劃工作10小時,生管派單量為800則該線TT時間= (10*3600) ÷ 800=45秒 2.CT(週期時間):單指一道工序從開始到結束的循環所需要的操作時 間 例如:測量針車車前片工序CT時間 =拿料2”+車縫30”+剪線5”+檢查 2”+放下產品2”+準備拿下一個產品1”=42秒 TT與CT之間的關係: 当TT>CT时,则会制造过剩,应考虑减少作业人员; 当TT=CT时,则为最理想目标,实际产能与目标产能相同,则生产线不 平衡损失为零; 当TT<CT时,则需提高生产效率,方能满足目标产能。该工序即为整条 生产线之瓶颈工序,应发予以改善。 3.瓶頸工序:一个流程中生产节拍最慢的环节,或者是指整个流程中制约 产出的各种因素。 5.FTT(一次直通率):产品第一次经过一道或一连串作业程序后(不 再需要额外加工),通过品检的百分比。 計算公式:FTT=(生產總數-不良數-返修數)÷ 通過總數 × 100% 例如:針車某天生產總產量768雙,報廢2雙,返修88雙,FTT= (768-2-88)÷768×100%=0.8828×100%=88.28% 6.DT(停滯時間) = 停机时间+停线时间 停机时间:因为机器损坏而影响生产的时间 停线时间:计划外或工序的停顿引起停线的时间 7.POH(人均時產能):每人每小时生产的双数,它可以真实反映生产效 率之高低。 計算公式:POH=生产总双数 ÷ 生产时数 ÷ 生产总人数 生產總人數=直接人員+移交 直接人員即指直接參與生產作業的人員 例如:某針車生產實際生產1540雙,實際出勤人數25人,班長1人, 移交1人,品管1人,工作10小時,則POH=1540 ÷ 26 ÷ 10=5.92雙/人/ 小時 8.線平衡率:是对生产线的全部工序进行负荷分析,通过调整工序间 的负荷分配使各工序达到能力平衡(作业时间尽可能相近)的技术手段 制作部門:LO
編寫員:XXXXX
文件版本:
更新日期:2015/10/22
審核:
核準: