企业现场七大浪费的认识(上,下全篇)
企业管理七大浪费

企业管理七大浪费浪费 1:管理工作“等”等待上级的指示:上级不安排工作下级就坐等,上级不指示下级就不执行,上级不询问下级就不汇报,上级不检查下级就拖着办。
多干事情多吃亏,出了问题怎么办?听从指示没有错,再大责任可分担。
很多工作是在多次检查和催办下才完成的,造成极大的浪费。
等待下级的汇报:任务虽已布置,但是没有检查、监督。
不主动深入调查情况,掌握第一手资料,只是被动地听下级汇报,不做核实就做决定或者向上级汇报,出了问题,责任还可以往下级身上推。
等待对方的回复:已与对方联系过,什么时候得到回复我无法决定,延误工作的责任应该由对方负责,我只能等。
追究责任也不怕,我某月某日把这份文件送给对方,这里记录得很清楚,对方不回复我能怎么办?你还是和对方联系一下吧,以免耽误工作。
等待生产现场的联系:职能部门不主动去为现场提供服务,而是坐等现场的联系,有时还很不耐烦,认为多等一会有什么了不起,却没有设身处地去为现场着想,严重地影响了生产现场问题的及时解决。
浪费 2:管理工作无序职责不清造成的无序:由于制度、管理等方面的原因,造成某项工作好像两个部门都管,却纠缠不休,整天扯皮,使原来的有序反而变成无序,造成极大浪费。
某个部门某个人,当看到一项工作比较紧急,如果不做就会影响到公司利益时,进行了补位。
这时就出现了一种怪现象:那么,今后这项工作就由你们来做吧,责任部门反而放任不管了,这也是一种无序。
业务能力低下造成的无序:素质低下、能力不能满足工作需要,都会造成了工作的无序。
应该承担某项工作的部门和人员,因能力不够而导致工作混乱无序;当出现部门和人员变更时,工作交接不力,协作不到位,原来形成的工作流程经常被推翻,人为增加了从“无序”恢复到“有序”的时间。
一个有效的管理者应该是一个规范化的高手,能把复杂无序的工作标准化、规范化、简单化,从而使普通员工可以完成原本无法完成的工作。
有章不循造成的无序:随心所欲,把公司的规章制度当成他人的守则,没有自律,不以身作则,不按制度进行管理考核,造成无章无序的管理,影响员工的积极性和创造性,影响部门的整体工作效率和质量。
生产管理中的七大浪费

生产管理中的七大浪费引言在现代制造业中,高效的生产管理对于企业的竞争力至关重要。
然而,在生产过程中,存在着一些浪费现象,这些浪费会导致资源的过度消耗、时间的浪费以及产品质量的下降。
本文将介绍生产管理中的七大浪费,并提出相应的解决方案,以帮助企业提高生产效率和节约成本。
一、物料浪费物料浪费是指在生产过程中由于物料的错误使用或过度消耗导致的浪费现象。
常见的物料浪费包括过剩的原材料处理、废弃物料的处理以及物料的过度采购等。
这会增加企业的成本,降低生产效率。
解决方案:- 优化物料采购策略,减少过多采购 - 引入物料追溯系统,提高物料使用效率 - 建立合理的废料回收机制,减少废弃物料的处理成本二、人力浪费人力浪费是指在生产过程中由于人力资源的错误分配、人员培训不足或不适当的工作设计等原因导致的浪费现象。
常见的人力浪费包括员工重复劳动、不必要的等待时间以及过度的人员调动等。
这会导致生产成本的上升和生产效率的降低。
解决方案:- 合理分配人力资源,确保每个员工都能发挥其最大的价值 - 加强员工培训,提高员工的技能水平和工作效率 - 优化工艺流程,减少员工的等待时间和重复劳动三、时间浪费时间浪费是指在生产过程中由于工艺缺陷、设备故障或生产计划不合理等原因导致的时间的浪费现象。
常见的时间浪费包括设备停机时间、生产线调整时间以及生产计划变更所引起的时间延误等。
这会导致生产效率的降低和交货期的延迟。
解决方案:- 加强设备维护和保养,减少设备故障和停机时间 - 优化生产计划,避免频繁的调整和变更 - 优化工艺流程,减少生产线调整时间和产品切换时间四、能源浪费能源浪费是指在生产过程中由于能源的不合理使用或过度消耗导致的浪费现象。
常见的能源浪费包括未关闭的电器、过度的加热和制冷以及能源的无效利用等。
这会增加企业的能源成本和环境负担。
解决方案:- 加强能源管理,确保设备的合理使用和节能措施的实施 - 定期检查和维护设备,减少能源的损耗 - 优化生产工艺和设备设计,提高能源利用率五、运输浪费运输浪费是指在物料运输过程中由于不合理的运输方式或过长的运输距离导致的浪费现象。
对生产现场七大浪费的认识

造成动作浪费的原因
走动
频繁
动作 幅度 大
单手
空闲
查找 工具、 材料
过度 伸展 弯腰
不连 贯、 停顿
双手
空闲
动作经济原则
动作经济原则
措施
缩短距 离 减少多 余的动 作
两手同 时使用
轻松工 作
课程回顾
等待的浪费 动作 的浪 费 加工的浪费学的聆听!
对生产现场七大浪费的认知
第六组
消除浪费 创造价值
通过学习与现场结合
等待的浪费
ECRS分析原则
取 消
合 并
重 排
简 化
搬运的浪费
思考
辨别浪费的种类 改变员工的理念
精益就是消除一切生产现场存在的浪 费,疏通优化工艺流程,简化不必要 的工序。
加工的浪费
例如:钢板100*100*200加工成曹为50*50*100活块(1万件)。
方法就是用200*350*25钢板锻打制作
1、材料每块节约2KG
2、加工成本每块节约20元
这种锻打制作方法降成本约20吨 *3000元/吨+20万=26万 精益工作日常化,日常工作精益化。
动作的浪费
定义:指生产操作上的动作不合理导致的时间的时间浪费。如: 生产作业时调整位置、翻转产品、取放工具、物料等不必要的 动作的浪费。 也可以理解为:产生的附加价值与付出的劳动不成比例,这样 的动作就是动作浪费。
工厂中常见的七大浪费

工厂中常见的七大浪费库存是祸根,是万恶之源,精益生产方式追求生产的同步化、生产的均衡化、作业人数的弹性化、物流供应的准时化、极大限度的排除传统生产方式中诸多浪费,及缩短制程时间创造出低成本、高品质、少库存、能快速对应市场的生产系统。
什么是浪费:不增加价值的活动是浪费尽管是增加价值的活动,所用的资源超过了绝对最少的界限也是浪费精益生产是排除所有浪费。
凡是超出增加产品价值,所必须的绝对值、最少的物料、机器和人力资源的部分,都是浪费在生产过程中,只有实体上改变物料的活动才能增加价值。
增加价值的活动:炼胶、成型、冲拨、包装、不增加价值的活动:点数、库存、品质检验减少价值的活动:搬运(常引起损伤、报废)不增加价值的活动反而增加成本,因而都是浪费工序间如果有两个在制品就能维持生产,超出两个的部分都是浪费。
以为所用的资源超过了(绝对最少)的界限。
工厂中常见的七大浪费如下一、不良、修理的浪费是指生产中发生不良品时,需要进行处置的时间、人力、物力以及由此造成相关浪费。
材料的损失。
设备人员工时的损失。
额外的修复、选别、追加检查。
额外的检查预防人员。
降价处理。
出货延误,取消订单。
信誉下降等。
二、加工的浪费1.过分加工的浪费一方面指多余的加工、另一方面指过分精细的加工。
(实际加工精度比要求要高,造成资源的浪费)2.需要多余的作业时间和辅助设备3.生产电、气、油等能源的浪费4.管理工时增加等三、动作的浪费生产现场作业的不合理导致的浪费物品去放、反转、对准。
作业步行、弯腰、转身等。
四、搬运的浪费搬运是一种不产生附加价值的动作,搬运的损失分为放置、堆积、移动、整列等动作的浪费。
1.物品移动所需空间的浪费。
2.时间的耗费,人力工具的占用等。
五、库存的浪费(含在制品)库存量越大,资金积压越大。
库存包括材料库存、半成品库存、已向供应商订购在途材料库存,及已发货的在途成品库存,库存浪费的形式多种多样,主要表现在1、生产不必要的搬运、堆积、放置、防护、寻找等浪费的时间、空间和动作。
生产现场常见浪费及识别方法

生产现场常见浪费及识别方法
浪费的概念
浪费是指实际需求和应当投入的资源之间,实际投入资源过多的情况。
它并非只指金钱,也可以是人力、物力等劳动资源的过多投入,以至于导
致系统效率降低。
必须要熟悉它的概念,不但知道了解它,而且要清楚浪
费的定义,这样才能有效减少浪费,提高效率,发挥最大价值。
生产现场七大浪费
1、过程等待:当当前进行的工作因等待物料、没有及时调整机器,
设备,等待一些特殊情况或问题的解决而被迫停止时,就产生了过程等待
的浪费。
2、过多加工:当任何地方都不符合和客户预期或者所需的标准时,
就可能存在过多加工的问题,例如上面加工的超出客户的要求,超出需求
的特殊处理,或长度不足以够一次性输送时,都会产生过多加工的浪费。
3、运输:运输浪费主要是指在生产和成品库存的移动过程中所用的
时间、人力和能源上的浪费。
比如物料在做搬运时,空距行走搬运,物料
的搬运距离太长,搬运途中浪费时间,运输设备的搬运距离太长等等,都
会产生运输浪费。
4、过度库存:如果公司的库存水平超出它的实际生产需求,就会产
生过度库存,而过度库存又会造成物料、货币和空间的浪费。
现场管理7大浪费的定义
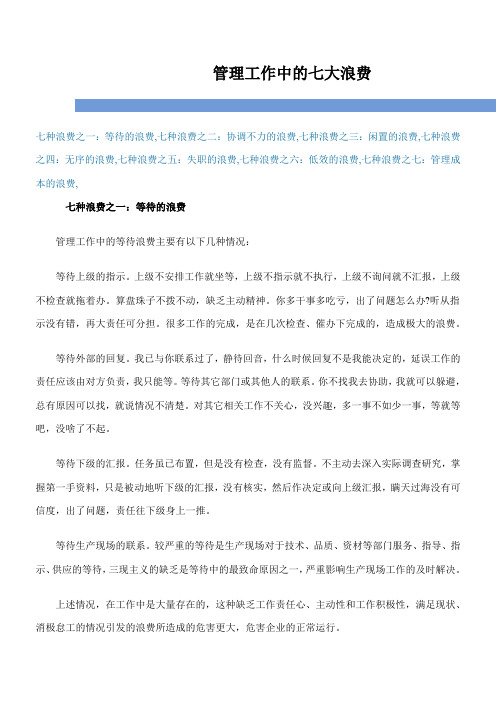
管理工作中的七大浪费七种浪费之一:等待的浪费,七种浪费之二:协调不力的浪费,七种浪费之三:闲置的浪费,七种浪费之四:无序的浪费,七种浪费之五:失职的浪费,七种浪费之六:低效的浪费,七种浪费之七:管理成本的浪费,七种浪费之一:等待的浪费管理工作中的等待浪费主要有以下几种情况:等待上级的指示。
上级不安排工作就坐等,上级不指示就不执行,上级不询问就不汇报,上级不检查就拖着办。
算盘珠子不拨不动,缺乏主动精神。
你多干事多吃亏,出了问题怎么办?听从指示没有错,再大责任可分担。
很多工作的完成,是在几次检查、催办下完成的,造成极大的浪费。
等待外部的回复。
我已与你联系过了,静待回音,什么时候回复不是我能决定的,延误工作的责任应该由对方负责,我只能等。
等待其它部门或其他人的联系。
你不找我去协助,我就可以躲避,总有原因可以找,就说情况不清楚。
对其它相关工作不关心,没兴趣,多一事不如少一事,等就等吧,没啥了不起。
等待下级的汇报。
任务虽已布置,但是没有检查,没有监督。
不主动去深入实际调查研究,掌握第一手资料,只是被动地听下级的汇报,没有核实,然后作决定或向上级汇报,瞒天过海没有可信度,出了问题,责任往下级身上一推。
等待生产现场的联系。
较严重的等待是生产现场对于技术、品质、资材等部门服务、指导、指示、供应的等待,三现主义的缺乏是等待中的最致命原因之一,严重影响生产现场工作的及时解决。
上述情况,在工作中是大量存在的,这种缺乏工作责任心、主动性和工作积极性,满足现状、消极怠工的情况引发的浪费所造成的危害更大,危害企业的正常运行。
七种浪费之二:协调不力的浪费管理中相互配合、协调不力,造成工作停滞浪费主要有下述几种情况:工作进程的协调不力。
某项工作在两个部门间协调不力、交接不清,工作进度受到影响,相互之间都不主动联系。
某些工作应哪个部门负责没有明确界定,处于部门间的断层,工作缺乏协作精神和交流意识,都在观望停滞,认为应该别的部门负责,结果工作没人管了,原来的小问题被拖成了大问题。
现场七大浪费解读

七大浪费解读七大浪费之一:过度库存的浪费降低企业的制造成本,就是要提高企业的增值能力,减少或消除企业的非增值部分。
那么企业经营活动过程中什么业务是增值,什么业务又是非增值呢?仔细想一下:我们把物品从一个地方移到另外一个地方,物品增加价值了吗?当然没有,顾客不会因此多付给企业一分钱;非增值的部分就是企业经营活动中顾客不愿意支付费用的活动,而增值部分就是为实现产品特定工艺特性的经营管理活动。
通过这样的一个定义和区分,我们就能够感觉到企业的经营活动中存在太多的不增值活动,需要我们通过管理技术和方法来不断改善,消除这些非增值的部分,实现企业经营的目标。
精益生产的创始人大野耐一在企业精益化的过程中总结出企业的非增值部分的工作中存在大量浪费环节,这些浪费分为七大浪费,他们分别是:不良品生产浪费、制造过多(早)浪费、过度加工浪费、不合理运输浪费、过度库存浪费、、、多余动作浪费和等待浪费在下面的内容里面我们一一阐述七大浪费的内容和核心思想,以帮助我们训练一双火眼睛睛,识别企业存在的浪费部分,为企业流畅制造模式的实现提供条件。
七大浪费之一:不良品生产的浪费不良品生产的浪费定义:对产品或服务的检验或返工、返修活动。
产品制造过程中,任何的不良品产生,都会造成材料、机器、人工等的浪费。
任何修补都是额外的成本支出。
我们要思考一个企业非常普遍的现象:企业的生产不良品所产生的原因经过统计之后发现,很多产生不良品的原因都是非常类似或相同的,企业为了应对反复发生的不良问题而不断组织资源进行扑救,以尽快解决企业的不良问题,日复一日,年复一年,似乎这些管理者非常勤劳和努力,不断为企业解决无数的不良问题,他们的行为真的能够给企业创造价值吗?我们的答案是否定的,他们的管理行为不一定能够为企业创造价值。
企业价值实现的过程中由各个工序组成共同实现企业价值创造,每个工序或作业单元都是由人、机、料、方法和环境等要素构成,我们从问题产生的源头来解析制造过程产生问题的根本方法。
七大浪费识别与原因分析、改善对策总结

七大浪费识别与原因分析、改善对策总结浪费的定义:一切不创造价值的活动,换言之:不能够提高附加价值的部分。
1、最大的浪费:生产过剩的浪费生产过剩的表现形式“过量生产MUDA”会产生新的MUDA(二次的MUDA)①材料、部品被提前吞吃;②电、空气等能源的浪費;③货架与箱子的增加;④搬运者、运输的增加;⑤会把等待的浪费隐藏起来,掩盖稼动率不足的问题;⑥使先进先出的工作产生困难;⑦会造成库存空间的浪费;⑧ LEAD-TIME变长(在库增加)。
到销售为止的时间变长(转换为钱的速度减慢即现金流减缓)生产过剩的发生原因过量生产的MUDA是所有MUDA产生的原因:①对于机械故障、不良等的安心保证;②错误的稼动率向上、外观的能率向上;③生产线停线是罪恶的想法;④作业员太多(没有按照TACT-TIME进行生产);⑤业务订单预测有误;⑥生产计划与统计错误。
解决对策①顾客为中心的弹性生产系统;②单件流生产线;③看板管理的贯彻;④快速换线换模;⑤少人化的作业方式;⑥均衡化生产。
注意点①设备余力并非一定是埋没成本;②生产能力过剩时,应尽量先考虑减少作业人员,但并非辞退人员,而是更合理、更有效率地应用人员。
2、最恶的浪费:库存的浪费库存浪费的表现形式①不良品存在库房内待修;②设备能力不足所造成的安全库存;③换线时间太长造成每次大批量生产的浪费;④采购过多的物料变成库存。
造成二次浪费:①产生不必要的搬运、堆积、放置、找寻、防护处理等浪费的动作;②使先进先出的作业困难;③损失利息及管理费用;④物品之使用价值会减低,变成呆滞品;⑤占用厂房、造成多余的工作场所、仓库建设投资的浪费;⑥造成无形的浪费。
隐藏的问题点①没有管理的紧张感;②设备能力及人员需求误判;③对场地需求的误判;④产品品质变差的可能性;⑤容易出现呆滞物料。
库存浪费的发生原因①视库存为当然;②设备配置不当或设备能力差;③大批量生产,重视稼动时间;④物流混乱,呆滞物品未及时处理;⑤提早生产;⑥无计划生产;⑦客户需求信息未了解清楚。
企业常见的七大浪费

企业常见的七大浪费 Last revision date: 13 December 2020.中国式现场管理之五十:企业常见的七大浪费企业常见的七大浪费现场混乱,插不进脚;员工仪容不整,两眼无光;物料混放,标志不清;设备故障不断,苟延残喘;人海战术,加班加点但还是要待工待料…这是国内不少企业的现状。
一切不增加对客户和企业价值的活动都是浪费。
在此前提下,企业每产一件产品就在制造一份浪费。
伴随企业运营中各业务环节不被察觉或不被重视的浪费,日本企业管理界将之形象地比喻为“地下工厂”。
日本专家通过长期的实践和研究发现,企业内有七种常见的浪费:1.等待浪费等待并非加工过程,不能改变物料的形状、尺寸、性质和状态从而改变韧料的功能,所以等待不创造价值。
待工和待料是两种最常见的等待情形。
常见的等待现象有:物料供应或前工序能力不足造成待料,监视设备作业造成员工作业停顿,设备故障造成生产停滞,质量问题造成停工,型号切换造成生产停顿。
造成等待的常见原因有:流水线能力不平衡,计划不合理,设备维护不到位,物料供应不及时等。
2.搬运浪费搬运也非加工过程,不能改变物料的形状、尺寸、性质和状态从而改变物料的功能,而且搬运过程中的放置、堆积、移动、整理等造成空间、时间、人力和工具等浪费,可谓费时费力费资源。
3.不良浪费美国零缺陷大师克劳斯比说:“任何事情没有一步做到位都会造成额外或本。
”质量不良也不例外。
常见的不良浪费有:材料损失,设备折旧,人工损失,能源损失,价格损失,订单损失,信誉损失等。
4.动作浪费多余的动作、不合适的动作增加员工作业强度、降低生产效率,因此也是一种浪费。
常见的浪费动作有:两手空闲,单手空闲,作业动作停止,动作幅度过大,左右手交换,步行多,转身角度大,移动中变换动作,未掌握作业技巧,伸背动作,弯腰动作,重复动作及不必要动作。
5.加工浪费每提高一级加工精度将增加数倍甚至数十倍的费用。
过高的加工精度造成浪费,它付出了额外的成本,或造成了不必要的高质量。
企业现场管理的七大浪费

实实在在服务客户浪费在企业中的表现两类浪费、现场管理中的浪费、企业管理中的浪费现场管理中的七种浪费在工业生产中,/I 是不能直接创造出价值的一切活动,均机为浪费。
七种浪费之一:等待的浪费等待就是闲着没事,等着下一个动作的来临,这种浪费是无庸置疑的。
造成等待的原因通常有:作业不平衡、安排作业不当、停工待料、品质不良等。
以生产部装配车间等待包装箱为例,由于包装箱不能按要求及时入厂,有可能无法按期交货,而当包装箱入厂后,又需要抢进度,可能会出现加班、质量问题等。
另有一种就是“监视机器” 的浪费,有些工厂买了一些速度快、价格高的自动化机器,为了使其能正常运转或其他原因,例如:排除小故障、补充材料等等,通常还会另外安排人员站在旁边监视。
所以,虽然是自动设备,但仍需人员在旁照顾,特称之为“闲视”的浪费。
例如在产品检测过程中,调试人员和生产人员站在产品旁边等待,这种情况是否还有?除了在直接生产过程中有等待外,其他管理工作中就没有等待这种浪费发生吗?当生产部在生产产品发生一些问题时,技术、品质部是否能立即解决而不需要现场人员长时间等待?如何减少这种等待?大部分人皆会认同搬运是一种无效的动作,也有人会认为搬运是必须的动作,因为没有搬运,如何做下一个动作?很多人都有这种想法。
正因为如此,大多数人默认它的存3!!在,而不设法消除它。
有些人想到用输送带的方式来克服,这种方式仅能称之为花大钱减少体力的消耗,但搬运本身的浪费并没有消除,反而被隐藏了起来。
搬运的浪费若分解开来,又包含放置、堆积、移动、整理等动作的浪费。
在不可能完全消除搬运的情况下,应重新调整生产布局,尽量减少搬运的距离。
大家可以考虑一下本公司的生产布局应该怎样变更?如何最大限度地减少搬运?产品制造过程中,任何的不良品产生,皆造成材料、机器、人工等的浪费。
任何修补都是额外的成本支出。
精益的生产方式,能及早发掘不良品,容易确定不良的来源, 从而减少不良品的产生。
企业现场七大浪费的认识上下全篇

用语言教学,可以教会一只鹦鹉;用生命教学,可以成就一粒种子
20 动作改善旳
个原则
工
工具物料应放置在固定场合
作
工具物料装置应依工作顺序就近排列
场
利用重力“喂”料,越近越好
“怕出问题” 旳心态
用语言教学,可以教会一只鹦鹉;用生命教学,可以成就一粒种子
库存隐藏旳问题
庫存
廢料
機器當機 廠商散漫
過度的工程設 計
在製品過多 (非必要的)
工單變動
待檢驗品 大排長龍
書面作業 工單 大排長龍 大排長龍
待決策事項 大排長龍
生產力 問題
用语言教学,可以教会一只鹦鹉;用生命教学,可以成就一粒种子
企业现场七大挥霍旳认识
用语言教学,可以教会一只鹦鹉;用生命教学,可以成就一粒种子
竞争力提升
改善 消除挥霍 标准化 现场5S
动作改善、作业流程改善、物流改善、 设备模夹治具改善、品质改善、管理改善等
七大挥霍、三无工程等
动作原则化、作业流程原则化、操作 流程原则化、包装运送原则化等
整顿、整顿、打扫、清洁、素养等
用语言教学,可以教会一只鹦鹉;用生命教学,可以成就一粒种子
做出不良旳挥霍
原因:
•材料錯誤或不良 •原则作业欠缺 •过分要求品质 •人员技能欠缺 •品质控制点设定错误 •以为可整修而做出不良 •检验措施、基准等不完备 •设备、模夹治具造成旳不良
对策:
•自动化、原则作业 •防误装置 •在工程内做出品质确保--“三不政策” •一种流旳生产方式 •品保制度确实立及运营 •定时旳设备、模治具保养 •连续开展“5S活动”
七大浪费终稿

危害: 大批量提前生 产,产生库存 的浪费。
危害: 大批量提前生 产,产生库存 的浪费。
危害:
危害:难以判断员工作业是否饱满、 物料转运是否及时等问题。
危害:掩盖问题,不能及时发现不合格品。 更改图纸 等 被动
危害:
如何改善和消除生产过剩的浪费
生产过剩浪费改善着眼点:
危害:掩盖问题,不能及时发现不合格品。 更改图纸 等 被动
危害: 如何改善和消除生产过剩的浪费 1)工序与工序之间的生产过剩; 2)车间与车间之间的生产过剩; 3)库存过剩。
七大浪费的识别与改善
一、什么是生产过剩的浪费 二、生产过剩产生的原因 三、生产过剩浪费的案例 四、如何改善和消除生产过剩的浪 费
1、什么是生产过剩的浪费
生产出多余需求的产品,
叫生产过剩。 多下的工件
1.1、什么是生产过剩的浪费
生产出多余需求的产品, 叫生产过剩。 多下的工件
危害:
危害:掩盖问题,不Байду номын сангаас及时发现不合格品。 更改图纸 等 被动
七大浪费认识

成本管理
讲师:张合神
现场浪费七要素 现场 浪费 七要素 1.等待的浪费 2.搬运的浪费 3.不良品的浪费 4.動作的浪费 5.加工的浪费 6.在庫的浪费 7.制造过多(早)的浪费
现场 浪费 七要素之 一 等待的浪費: (闲视的浪费) 闲着没事,等着下一个动作的来临.作业 平衡,安排作业不当.缺料,等料,待料,品质 不良所造成.
现场 浪费 七要素之二
搬运的浪费: (堆积,移动,整列) 布置采用批量生产,依工站别集中的水 平式佈置所致. 缺流水线化生产观念.
现场 浪费 七要素之 三 不良修理的浪费: 所谓不良,修理的浪费,指的是由于工厂 内产出的不良品,需要进行处置的时间,人 力,物力上的浪费,以及由此造成的相关捐 失.这类浪费具体包括:材料的损失,不良 品变成废品;设备人员和工时的损失,额外 的修复,鉴别,追加檢查的损失;有时需要 降级处理产品,或者由于耽误出货而导致 工厂信誉的下降.
现场 浪费 七要素之 六 库存的浪费: 有些企业由于生产能力比较强大,为了不 浪费生产能力而不中断生产,增加了制品, 使得制品周期变短,空间变大,还增加了搬 运,堆积的浪费,此外,制造过多或过早,會 带来庞大的库存量,利息负担增加,不可避 免地增加了贬值的风险.
现场浪费七要素之 七 管理的浪费 管理浪费指的是问题发生以后,管理人员 才采取相应的对策来进行补救,而产生 的额外浪费,管理浪费是由于事先管理不 到位而造成的问题,科学的管理应该是具 有相当的预见性,有合理的规划,并在事情 的推进过程中加强管理,控制和反馈,这样 就可以在很大程度上减少管理浪费现象 的发生.
現場 浪費 七要素之 四 动作的浪费: 两手空闲,单手空闲,作业动作突然停止, 作业动作过大,左右手交换,步行过多,转 身的角度太大,移动中变换”状态”,不明 技巧,伸背动作,变腰动作以及重复动作和 不必要的动作等,這些动作的浪費造成了 時间和体力上的不浪费: 加工的浪费也叫过分加工的浪费,主要包 含两层含义:第一是多余的加工和过分精 确的加工,例如实际加工精度过高造成资 源浪费,第二是需要多余的作业时间和辅 助设备,还要增加生产用电,气压,油等能 源的浪费,另外还增加了管理的工时.
生产现场的七大浪费

1)要使货物便于移动(锅盖把手,货物底部加垫子方便叉车转运) 2)要尽量把货物集中在一起(装鸡蛋的盒子、零部件盒子、筐)
危害:
产品成本的增加
设备折旧费和间接劳务费等的增加
第四层的浪费;1、多余的仓库;2、多余的搬 运工;3、多余的搬运设备;4、多余的库存管
理、质量维护人员;5、使用多余的计算机
第三层次的浪费(过剩库存 的浪费)
利息支出(机会 成本)增加
第二层次的浪费(最大的浪费) 制造过浪费(工作进展过度)
第一层次的浪费(过剩的生产能力的存在): 1、过多的人员 2、过剩的库存 3、过剩的设备
3、生产过剩的浪费案例
案例4:
危害:产品长期 堆积,锈蚀严重。
3、生产过剩的浪费案例
案例5:
危害:生产计 划的不准确性 导致产品过多 生产,占用过 大存放场地, 增加额外管理 费用,占用大 量资金。
4、如何改善和消除生产过剩的浪费 生产过剩浪费改善着眼点:
1)工序与工序之间的生产过剩; 2)车间与车间之间的生产过剩; 3)库存过剩。
4、改善搬运浪费的着眼点
4)安全轻松的搬运
不仅搬运方式很重要,对通道的保养也很重要。
通道保养的注意事项: 1、消除道路的凹凸不平 2、斜坡尽量修成缓和的坡度 3、在通道上不要设置台阶 4、在通道上不要放置障碍物 5、随时清扫通道,保持通道卫生
4、改善搬运浪费的着眼点
5)重视搬运的连接点
消除多次搬运现象,减少转运物资的距离,争取一次搬运到位。
4、如何改善和消除生产过剩的浪费
整机过剩
4、如何改善和消除生产过剩的浪费
零部件生产过多,超 过下工序需求量,造 成零部件锈蚀。
制造型企业现场管理容易产生的七大浪费

制造型企业现场管理容易产生的七大浪费1.过盈生产的浪费:过盈生产将导进一步的更多的问题,而问题的真正原因却被隐藏起来。
如果发生多余的人或机械,就会在不必要的时候不必要地制作不必要的东西.还会造成其他诸多浪费,会在现场中发生问题,所以可以称为浪费的根源。
2.等待的浪费:人们常常认为只有人或设备的等待才是浪费。
材料等待投入作业,或产品在工艺流程中停滞下来,或材料或产品堆放在仓库内,也是浪费。
3.搬运浪费:由于不合理的Lay-Out(流动分配和工艺)和过盈生产(后工序间的不平衡)及库存而产生的不必要的搬运、取下、放置、重堆放、材料再处理、物件移动、物质流动、搬运距离及搬运活力不良等问题不仅会降低生产效率,还会使产品的刮痕及损伤等不良增加。
4.加工作业本身的浪费:所谓工作,只要稳定下来后其本来的功能便会被忘记,只留下“在作业”的行为,但是我们需要考虑一下在作业方法,环境,条件等方面是否有超出必要的作业。
5.库存浪费:库存并不单单是指一般的库存,它还包含正在加工中的产品的库存。
库存不仅是材料、部件、组装品等物品处于停滞状态,及在仓库中的库存,它还包括处于工艺过程及工序之间的产品的库存,我们应该丢弃“掌握库存可以回避许多问题”的观念。
6.动作浪费:我们每天进行的作业并不都是具有附加价值的作业,这些作业大部分是活动,而具有附加价值的“工作”只占其中一部分,不能直接带来附加价值的活动只是动作浪费而已。
动作浪费在机械设备的布置,部件或工具的排列不合适时也会发生。
7.不良生产浪费:所谓工作,只要稳定下来后其本来的功能便会被忘记,只留下“在作业”的行为,但是我们需要考虑一下在作业方法,环境,条件等方面是否有超出必要的作业。
最新整理企业常见的七大浪费.doc

中国式现场管理之五十:企业常见的七大浪费企业常见的七大浪费现场混乱,插不进脚;员工仪容不整,两眼无光;物料混放,标志不清;设备故障不断,苟延残喘;人海战术,加班加点但还是要待工待料…这是国内不少企业的现状。
一切不增加对客户和企业价值的活动都是浪费。
在此前提下,企业每产一件产品就在制造一份浪费。
伴随企业运营中各业务环节不被察觉或不被重视的浪费,日本企业管理界将之形象地比喻为“地下工厂”。
日本专家通过长期的实践和研究发现,企业内有七种常见的浪费:1.等待浪费等待并非加工过程,不能改变物料的形状、尺寸、性质和状态从而改变韧料的功能,所以等待不创造价值。
待工和待料是两种最常见的等待情形。
常见的等待现象有:物料供应或前工序能力不足造成待料,监视设备作业造成员工作业停顿,设备故障造成生产停滞,质量问题造成停工,型号切换造成生产停顿。
造成等待的常见原因有:流水线能力不平衡,计划不合理,设备维护不到位,物料供应不及时等。
2.搬运浪费搬运也非加工过程,不能改变物料的形状、尺寸、性质和状态从而改变物料的功能,而且搬运过程中的放置、堆积、移动、整理等造成空间、时间、人力和工具等浪费,可谓费时费力费资源。
3.不良浪费美国零缺陷大师克劳斯比说:“任何事情没有一步做到位都会造成额外或本。
”质量不良也不例外。
常见的不良浪费有:材料损失,设备折旧,人工损失,能源损失,价格损失,订单损失,信誉损失等。
4.动作浪费多余的动作、不合适的动作增加员工作业强度、降低生产效率,因此也是一种浪费。
常见的浪费动作有:两手空闲,单手空闲,作业动作停止,动作幅度过大,左右手交换,步行多,转身角度大,移动中变换动作,未掌握作业技巧,伸背动作,弯腰动作,重复动作及不必要动作。
5.加工浪费每提高一级加工精度将增加数倍甚至数十倍的费用。
过高的加工精度造成浪费,它付出了额外的成本,或造成了不必要的高质量。
常见的加工浪费情形有:加工余量过大、过高的精度、不必要的加工等,其造成的浪费有:设备折旧、人工损失、辅助材料损失、能源消耗等。
- 1、下载文档前请自行甄别文档内容的完整性,平台不提供额外的编辑、内容补充、找答案等附加服务。
- 2、"仅部分预览"的文档,不可在线预览部分如存在完整性等问题,可反馈申请退款(可完整预览的文档不适用该条件!)。
- 3、如文档侵犯您的权益,请联系客服反馈,我们会尽快为您处理(人工客服工作时间:9:00-18:30)。
用语言教学,可以教会一只鹦鹉;用生命教学,可以成就一粒种子
韵律节奏
韵律节奏就象跳舞的动作一 样有快慢节拍,而且有规律地重 复发生。恰当组合动作,使工作 产生韵律节奏,可使工作人员减 少疲劳及心理压力。
用语言教学,可以教会一只鹦鹉;用生命教学,可以成就一粒种子
动作改善的
20个原则
工具物料应放置在固定场所 工具物料装置应依工作顺序就近排列 利用重力“喂”料,越近越好 利用重力坠送
表现形式: • 材料的损失;
• • • • • • • 设备、人员、工时的损失; 额外的修复、选别、追加检查; 额外的检查预防人员; 降价处理; 出货延误取消定单; 信誉下降; ……
用语言教学,可以教会一只鹦鹉;用生命教学,可以成就一粒种子
对策:
做出不良的浪费
原因:
•材料錯誤或不良 •标准作业欠缺 •过分要求品质 •人员技能欠缺 •品质控制点设定错误
•视库存为当然 •设备配置不当或设备能力差 •大批量生产,重视稼动 •物流混乱,呆滞物品未及时处理 •提早生产 •无计划生产 •客户需求信息未了解清楚
用语言教学,可以教会一只鹦鹉;用生命教学,可以成就一粒种子
库存的浪费
过多的库存会隐藏的问题点:
•没有管理的紧张感,阻碍改善的活性化
“怕出问题” 的心态
待決策事項 大排長龍
用语言教学,可以教会一只鹦鹉;用生命教学,可以成就一粒种子
库存的浪费
过多的库存会造成的浪费:
•产生不必要的搬运、堆积、放置、找寻、防护处理等浪 费的动作
•使先进先出的作业困难
•损失利息及管理费用 •物品之价值会减低,变成呆滞品 •占用厂房、造成多余的工作场所、仓库建设投资的浪费 •造成无形的浪费 用语言教学,可以教会一只鹦鹉;用生命教学,可以成就一粒种子
连续式曲线运用比方向突变的直线运动好
方向突变的直线运动
连续式曲线运动
用语言教学,可以教会一只鹦鹉;用生命教学,可以成就一粒种子
弹道式运动更轻快
人体动作原理: 向内收缩肌肉 VS 向外抛出肌肉 ◎ 平衡时:静止 ◎ 不平衡时:动作
弹道式运动
只利用一种动作方向,只在 初期动作开始时加以控制,一旦连 动出去就无法改变方向。 弹道式运动效率较高、速度较快,比较有力量也很精确, 不易引起肌肉疼痛,比固定的运动方式舒畅。 运用弹道式运动的例子有:木匠捶钉子,打字,弹琴, 拉小提琴等。
改 善 消除浪费 标 准 化
现场5S
用语言教学,可以教会一只鹦鹉;用生命教学,可以成就一粒种子
精益生产全貌
易 缺 足
难
用语言教学,可以教会一只鹦鹉;用生命教学,可以成就一粒种子
学习目的
充分认识企业现场的七大浪费,在实 际工作中能做到有效防止与改善!
用语言教学,可以教会一只鹦鹉;用生命教学,可以成就一粒种子
用语言教学,可以教会一只鹦鹉;用生命教学,可以成就一粒种子
S=m×v
动能 质量 速度
尽可能利用物体动能
工件本身的质量 搬运或加工工具的质量 工作身体部位的质量
当无须利用动能时,应设法减小其质量或速度。 当需要利用动能时,则应适当增加其动能即质量或速度。 移动距离的缩短亦是降低疲劳的重要方法。
用语言教学,可以教会一只鹦鹉;用生命教学,可以成就一粒种子
•自动化、标准作业 •防误装置 •在工程内做出品质保证--“三不政策” •一个流的生产方式 •品保制度的确立及运行
•定期的设备、模治具保养
•持续开展“5S活动”
注意:
•能回收重做的不良 •能修理的不良 •误判的不良
•认为可整修而做出不良
•检查方法、基准等不完备 •设备、模夹治具造成的不良
用语言教学,可以教会一只鹦鹉;用生命教学,可以成就一粒种子
•工程设计适正化 •作业内容的修正
•治具改善及自动化
•标准作业的贯彻
原因:
•工程顺序检讨不足 •作业内容与工艺检讨不足 •模夹治具不良 •标准化不彻底 •材料未检讨
•VA/VE的推进
•设计FMEA的确实推进
注意:
•了解同行的技术发展 •公司各部门对于改善的共 同
参与及持续不断的改善 用语言教学,可以教会一只鹦鹉;用生命教学,可以成就一粒种子
库存的浪费
对策:
•库存意识的改革 •U型设备配置
注意:
•库存是万恶之源
•均衡化生产
•生产流程调整顺畅 •看板管理的贯彻
•快存
用语言教学,可以教会一只鹦鹉;用生命教学,可以成就一粒种子
6.制造过多的浪费
浪费的源头
表现形式:
•物流阻塞 •库存、在制品增加 •产品积压造成不良发生 •资金回转率低 •材料、零件过早取得 •影响计划弹性及生产系统的适应能力 用语言教学,可以教会一只鹦鹉;用生命教学,可以成就一粒种子
2.加工上的浪费
因技术(设计、加工)不足造成加工上的浪费--原本不必要的工程或作业被当成必要
表现形式:
•在加工时超过必要以上的距离所造成的浪费 •冲床作业上重复的试模,不必要的动作 •成型后去毛头,加工的浪费 •最终工序的修正动作
用语言教学,可以教会一只鹦鹉;用生命教学,可以成就一粒种子
对策:
加工上的浪费
材料、零件、组合件等物品的停滞状 态,包括库存及在制品
表现形式:
•不良品存在库房内待修
•设备能力不足所造成的安全库存
•换线时间太长造成大批量生产的浪费 •采购过多的物料变库存
用语言教学,可以教会一只鹦鹉;用生命教学,可以成就一粒种子
库存的浪费
是因传统以来的许 多错误生产观念所 造成的。分三种:
1)材料库存:大量采购成 本低。 2)在制品库存:不良重修 机器故障。 3)成品库存:预测生产与 实际需求量不同。
企业现场七大浪费的认识
用语言教学,可以教会一只鹦鹉;用生命教学,可以成就一粒种子
竞争力提升 品质提升 合理化成本降低 形象提升 动作改善、作业流程改善、物流改善、 设备模夹治具改善、品质改善、管理改善等 七大浪费、三无工程等 动作标准化、作业流程标准化、操作 流程标准化、包装运输标准化等 整理、整顿、清扫、清洁、素养等
用语言教学,可以教会一只鹦鹉;用生命教学,可以成就一粒种子
平衡——双手同时、反向、对称动作
☆ 两手同时开始及完成动作 ☆ 除休息时间外两手不同时空闲 ☆ 两臂动作反向且对称
单手操作使人体容易产生心理及生理上不平衡的感觉, 为克服这种不平衡,必须运用身体的应力去反制,因而使身 心容易疲劳。
用语言教学,可以教会一只鹦鹉;用生命教学,可以成就一粒种子
• 得过且过,患得 患失的惜力主义
• 明哲保身,但求 无过的好人主义
用语言教学,可以教会一只鹦鹉;用生命教学,可以成就一粒种子
• 天下太平,没有危 机意识的公司安全 主义 • 坐井观天,自我独 立的漠不关心主义
用语言教学,可以教会一只鹦鹉;用生命教学,可以成就一粒种子
• 少贪事,绕道走,免 惹麻烦主义
制造过多的浪费
制造过多是一种浪费的原因:
•只是提前用掉了费用(材料费、人工费)而已,并无其它好处
•会把等待的浪费隐藏起来,掩盖稼动不够的问题 •会使制程间积压在制品,制程时间变长,现场工作空间变大 •会产生搬运、堆积的浪费
工 作 场 所 6 原 则
适当的照明
工作台椅高度要舒适适当
用语言教学,可以教会一只鹦鹉;用生命教学,可以成就一粒种子
动作改善的
20
个原则
工 具 设 备 6 原 则
尽量以足踏、夹具代替手的工作 工具尽可能合并使用
工具、物料、预放在工作位置
按手指负荷能力分配工作
手柄接触面积尽量大
操作杆设计尽可能减少身体姿势变更
•坐姿作业 •设立了固定的半成品放置区
注意:
•工作预置的废除 •生产线直接化
•生产计划安排不当
•观念上不能有半成品放置区
•并非坐姿才可以
搬运三不原则:不要乱流、不要粗流、不要停留
用语言教学,可以教会一只鹦鹉;用生命教学,可以成就一粒种子
5.库存的浪费
不良所造成的库存,半成品所造成的库存,制造过 多所造成的库存
•设备能力及人员需求的误判
•对场地需求的判断错误 •产品品质变差的可能性
•容易出现呆滞物料
用语言教学,可以教会一只鹦鹉;用生命教学,可以成就一粒种子
库存隐藏的问题
機器當機 廢料
庫存
過度的工程設 計 在製品過多 (非必要的) 待檢驗品 大排長龍
廠商散漫
工單變動
生產力 問題
書面作業 大排長龍
工單 大排長龍
作业动作“三不”政策
不
不
不
摇 头
转 身
插 秧
用语言教学,可以教会一只鹦鹉;用生命教学,可以成就一粒种子
动作改善的
20个原则
两手同时开始及完成动作
人 体 运 用 8 原 则
除休息时间外两手不同时空闲 两臂动作反向且对称
尽可能以最低级动作工作
尽可能利用物体动能
连续式曲线运用比方向突变的直线运动好
弹导式运动更轻快 动作宜轻松有节奏
内容介绍:
1.改善意识
成本管理看板
2.何谓浪费 3.浪费的种类 5.“七大浪费”之详介 用语言教学,可以教会一只鹦鹉;用生命教学,可以成就一粒种子
改善的十条基本精神
• • • • • • • • • • 一、抛弃僵化固定的观念; 二、过多地强调理由,是不求进取的表现; 三、立即改正错误,是提高自身素质的必经之路; 四、真正的原因,在“为什么”的反复追问中产生; 五、从不可能之中,寻找解决问题的方法; 六、只要你开动脑筋,就能打开创意的大门; 七、改善的成功,来源于集体的智慧和努力; 八、更应该重视不花大钱的改善; 九、完美的追求,从点滴的改善开始; 十、改善是无止境的。