TPM 六大损失讲义
TPM讲义
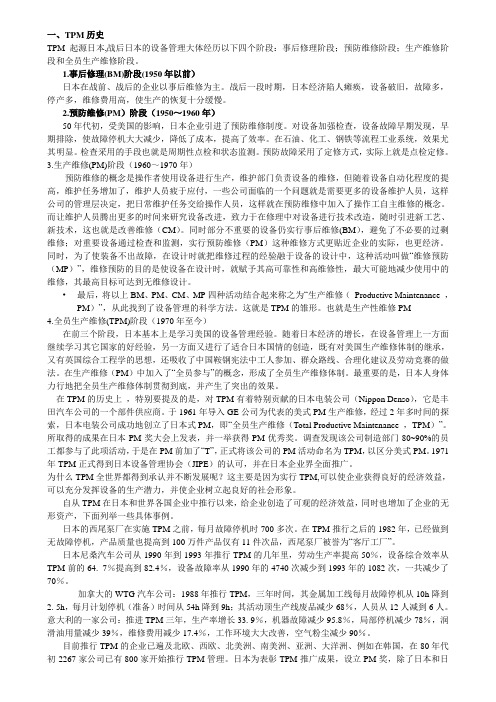
一、TPM历史TPM起源日本,战后日本的设备管理大体经历以下四个阶段:事后修理阶段;预防维修阶段;生产维修阶段和全员生产维修阶段。
1.事后修理(BM)阶段(1950年以前)日本在战前、战后的企业以事后维修为主。
战后一段时期,日本经济陷人瘫痪,设备破旧,故障多,停产多,维修费用高,使生产的恢复十分缓慢。
2.预防维修(PM)阶段(1950~1960年)50年代初,受美国的影响,日本企业引进了预防维修制度。
对设备加强检查,设备故障早期发现,早期排除,使故障停机大大减少,降低了成本,提高了效率。
在石油、化工、钢铁等流程工业系统,效果尤其明显。
检查采用的手段也就是周期性点检和状态监测。
预防故障采用了定修方式,实际上就是点检定修。
3.生产维修(PM)阶段(1960~1970年)预防维修的概念是操作者使用设备进行生产,维护部门负责设备的维修,但随着设备自动化程度的提高,维护任务增加了,维护人员疲于应付,一些公司面临的一个问题就是需要更多的设备维护人员,这样公司的管理层决定,把日常维护任务交给操作人员,这样就在预防维修中加入了操作工自主维修的概念。
而让维护人员腾出更多的时间来研究设备改进,致力于在修理中对设备进行技术改造,随时引进新工艺、新技术,这也就是改善维修(CM)。
同时部分不重要的设备仍实行事后维修(BM),避免了不必要的过剩维修;对重要设备通过检查和监测,实行预防维修(PM)这种维修方式更贴近企业的实际,也更经济。
同时,为了使装备不出故障,在设计时就把维修过程的经验融于设备的设计中,这种活动叫做“维修预防(MP)”,维修预防的目的是使设备在设计时,就赋予其高可靠性和高维修性,最大可能地减少使用中的维修,其最高目标可达到无维修设计。
•最后,将以上BM、PM、CM、MP四种活动结合起来称之为“生产维修(Productive Maintenance ,PM)”,从此找到了设备管理的科学方法。
这就是TPM的雏形。
六大损失认识
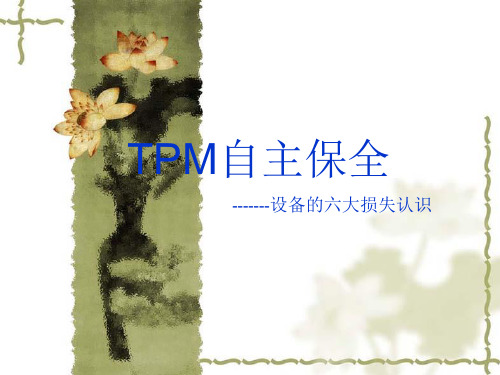
提高对设备的 信赖度 确保设备的清 洁状态 提高设备的可 保养性
学习机械的动 作和工作原理 发掘对设备改 善的兴趣 享受改善带来 的喜悦
OP(onepoint lesson,要点教 讲授分析什 材或经验教 么、如何分析、 材)不合理 解析现况的思 发现清单K 考方式和方法 NOW-WHY 讲授改善的具 分析(简称 体方法 K-W分析)
TPM自主保全
-------设备的六大损失认识
六大损失的来源
根据TPM专家的统计,造成现场设备 及生产率低下的主要原因有:故障、换模 换线、调整、空转及加工速度短暂降低、 不良及再加工、启动耗时等六大项,从 而对设备与生产效率的高低分析得到设 备只有改变这 “设备六大损失”就可以 大幅度提升设备使用效率。
第二步:发生源及困难源的对策
目标是解决造成设备脏污的来源,并对 清扫、润滑、点检等困难点加以改善,使 作业人员易于进行设备的清扫、润滑、点 检等工作。由于是作业人员自己在做维持 管理,因此,在此步中TPM小组成员们累 积的自行改善的经验很重要。
第三步:编制清扫、润滑、点检标准
此项目标是整理作业人员应该遵守的事 项,其重点是:自己编制的清扫、润滑、点检 事项,自己是否能够确实遵守。
启动/初 始损失
注塑机升温到 设定温度不及 时安排人员上 班
发电机启动时, 叉车电池不 油路漏气,延 足,启动延 长启动时间 期5分钟
为何找出不正常部位如此重要
当损失发生后才注意到设备的不正常,已经为时已晚了。因为一个 不正常现象发生之后没有得到及时解决,就会引起设备以下的所有元 件的不正常,最终造成设备故障或不良品的产生,甚至整个设备的损 坏。 这是因为当代企业的效率越来越高,对设备和管理越来越依赖。例 如一次性打火机生产线的速度是一秒钟一个(3600个/h),小汽车 生产线的装配速度为45~60s一台(68~80台/h)。如果一台机器 出了故障,一个小小的螺钉不能及时到位,一小时就有3600个打火机、 60~80台小汽车在生产线上进退不得。
TPM全面生产维护经典讲义

综合上述维护方法,系统的维护方
案
1960年前后
4
维修预防
(MP: Maintenance Prevention) 设
计不发生故障的设备,设备FMEA
1960年前后
22
TPM(全面生产性维护)
设备管理的沿革- TPM与TQM的关系
智联培训
TQM 是 W.Edwards Deming 博 士 在 影 响 日 本 工 业 的 直 接 效 果 下 发 展 得 来 .
25
TPM(全面生产性维护
)
TPM设备的流程图
日常点检
发现缺陷
定期检查
发现缺陷
可 简单处理?
否
实施简单 处理
简单处理?
否 立刻修理?
可 实施简单 处理
要
计划修理
计划修理 卡
备件等的 准备
改善修理 故障修理 故障修理
突发故障
实施简单
处理
可
确认缺陷
简单处理?
维修联席 会议
事后修理
否
立刻修理?
要
否
故障修理
人员管理--设备操作人员的素质 会使用
会维护 四会
会检查
会修理
智联培训 31
TPM(全面生产性维护 )
三好四会五纪律
人员管理--设备操作人员的素质 遵守操作规程
保持设备整洁 五
项
纪 律
发现异常就处 理
遵守交接班制
度
管好工具和附 件
智联培训 32
TPM(全面生产性维护 )
TPM的人员管理
智联培训
设备操作人员的素质
当工厂维护的问题作为TQM程序部分被检查出来,一些通用概念看起来在维护环 境中就不太适合或不能发挥作用。原始的TQM概念做了一些修正。这些调整将维 护提升至全面质里管理程序的一个重要部分。
TPM-六大损失讲义

吃饭、休息时间
生产调整、开会 计划保全、检修
1
故障
每1台设备的故障频度 10分钟以上1次/月
2
准备 准备交替调整时间/次 交替 10分钟以下
3
瞬间 空转瞬间停止频度 停止 10分钟以上1次/月以下
4
速度 实现理论Cycle Time 降低 提高15%以上
5
不良 工程不良率 修整 0.1%以下
6
收率
投入材料的 99%以上
扫 就 是
照片 扫 就 是
润
改
滑
善
姓姓名名:: 手手机机:: 格清格需言扫言要:就:精清是设心备照扫润就料就滑像,是、孩才点清子能检扫一健就样康,成是长改。善
《爱人一样爱护,子女一样关照》
MY-JOB(我的职责)
MY-AREA(我的区域)
1 充分理解PRO-3M活动的概要。
地面 保持干净、无油污的状态
TPM自主保全 特点:减少浪费,提高效率 遵命老婆,我用TPM技巧抓羊, 一抓一个准,哈哈,亲爱的小 肥羊,我灰太狼大王来了!
2、转产停止损失 特点:用时长 我爱美,所以每天都要换衣服 化妆,打扮不好我是不工作的。
4、速度降低损失 特点:慢 唉,年纪大了,做什么都慢。 想当年,我跑的比羚羊还快。
6、收率减少损失 特点:浪费大 哎,长这么多肉干吗?又不漂 亮,该减肥了。
10 进行持续性的事后管理及实施。
表格文件 表格填写正规及时,文件管理正规有效
TPM自主保全活动具体内容
推行 日常6S
整理 整顿 清扫 清洁 清心 安全
运用 5感 视觉 触觉 听觉 味觉 嗅觉
探究 6大系统 紧固件 驱动传导
润滑 空压 液压 电装控制
全面生产维护(TPM)讲义

❖ 2)相关的工艺装备不配套。在刀具、夹具、量具、 软件、维修和环境等方面的投资不足,造成机床使用 的寿命和效率的低下。
❖ 3)工艺编排不合理。没有根据精益生产的“一个流” 去编排产品加工的工艺过程,只是根据设备的种类编 组,在某一工步或工序节省了部分时间,而没有从根 本上提高效率。
投资或员工的加班加点也就是资源的投入实现的。但是这种资源投入型
的生产方式由于固定成本的增加并不能有效提高企业生产经营的效益,
同时这种粗放型的生产方式也不利于资源的节约和环境保护。
❖ 现代设备管理的理念是通过加强设备管理,提高设备的综合效率以 实现生产能力的提高。因为生产设备综合效率的提高可以减少各种形式 的设备非计划停机时间,从而实现提高设备生产能力的目标。
❖ 为了解决这些问题,美国等制造业提出了“事后维 修(Breakdown Maintenance ,BM)”,即当装 备出现故障后马上采取应急措施进行事后处置。
❖ 这一时期,设备最显著的特点是半自动、手动操作 设备多,结构也简单,因此工人可以自己动手修理, 现象是不坏不修、坏了再修。
❖ BM从上世纪初一直持续到40 年代。
❖ (2)预防维修
❖ 上世纪50年以后,开始出现复杂设备,复杂设备由大 量零件组成,修理所占用的时间已成为影响生产的一 个重要因素。
❖ 另外,人们发现设备故障总在某个部位出现,因此在 维护时主要去查找薄弱部位并对其进行改良。
❖ 为了尽量减少设备修理对生产的影响,苏联提出计划 维修制度;美国提出预防维修制度,即PM (Preventive Maintenance / 1951 ) ,即通过对设 备的“物理性检查”预防其故障的发生,从而达到延 长设备使用寿命的目的。
TPM——讲义PPT课件

•2020/3/28
•29
2 自主保养step2导入推动 哲理小故事
•小蜗牛:为什么我们从生下来,就要背负这个又重又硬的壳呢? •妈妈:因为我们的身体没有骨骼的支撑,只能爬,又爬不快,所以
要这个壳的保护!
•小蜗牛:毛虫姐姐没有骨头,也爬不快,为什么她不用背这壳呢? •妈妈:因为毛虫姐姐能变成蝴蝶,天空会保护她啊。
2 -原因
表
文件中所有带有“为什么”的语句都3 -为会什么定? 义真正的3根-原源因 (通常需要至少5个“为什么”)
4 -为什么?
4 -原因
5 -为什么?
5 –根源
•2020/3/28
•35
2 自主保养step2导入推动
5Why质量工具简介
注意!!!
五个为什么
问五次为什么
5
•2020/3/28
•36
•2020/3/28
•8
1 TPM基础概念回顾
“一套三表”的概念
何谓“一套三表”?
《自主保养暂定基准书》----岗位操作员每月例行常规保养项目标准
《自主保养查检表》--------依照《自主保养暂定基准书》的执行记 录
《不良点标签汇总表》------执行保养的过程中发现异常(不良点) 记录,
并追踪复原、改善
奇怪为什麽?每周都要 换 O型密封圈。
换上一个 O型密封圈, 再换上一个活塞杆。
•2020/3/28
•20
2 自主保养step2导入推动
一个月之后,汽缸又
开 始漏油。
为什么 活塞杆
又
损坏,认真观察发现是
工
•2020/3/28
•21
2 自主保养step2导入推动
换上一个 O型密封圈, 再换上一个活塞杆, 加上一个盖子。
设备管理六大损失与TPM安灯系统

设备管理六大损失与TPM安灯系统企业生产制造过程中能对设备造成影响的因素有很多,故把直接影响到设备停机、故障、损耗等不良情形的各类因素叫做项目损失,为了提高设备的综合使用效率,保证产品的质量,提高生产效率需要实施TPM管理降低设备的损失,但在降低设备损失之前需要我们认识这些项目损失具体包括了:1、故障损失;2、换模具与调整损失;3、空运转与暂停损失;4、减速损失;5、质量缺陷和返工;6、开工损失等,分为六大损失。
故障停机/损失是指故障停机造成时间损失和由于生产缺陷产品导致数量损失。
因偶发故障造成的突然的、显着的设备故障通常是明显的并易于纠正;而频繁的、或慢性的微小故障则经常被忽略或遗漏。
由于偶发性故障在整个损失中占较大比例,所以许多企业都投入了大量时间努力寻找避免这种故障,然而,要消除这些偶发性故障是很困难的。
所以,必须进行提高设备可靠度的研究,要使设备效率最大化,必须使故障减小到零,因此,首先需要改变传统故障维修中认为故障是不可避免的观点。
推行生产和设备管理体系时,找到自己的问题结合安灯系统TPM分析.可开展全员设备维护。
换装和调试损失是因换装和调试而导致停机和产生废品所造成的损失,一般发生在当一个产品的生产完成后,因生产另一种产品进行换装和调试的时候。
为了达到单一时间内的换装(少于10分钟),可以通过明确区分内换装时间(在机器停机后才能完成操作)和外换装时间(在机器运转时可以完成操作),以及减少内换装时间来减少整个换装时间损失。
安灯系统其中的及时响应可以非常有效的解决的该问题,一线工人只需按下对应事件的按钮,设备管理部门能立刻知道并作出反应。
减速损失是指设计速度与实际速度的差别。
速度损失对设备效率的发挥产生了较大障碍,应当仔细研究,以消除设计速度和实际速度二者之间的差别。
设备实际速度低于设计速度或理想速度的原因是多种多样的,如机械问题和质量缺陷,历史问题或者设备超负荷等。
通常,通过揭示潜在的设备缺陷,谨慎地提高操作者的速度有助于问题的解决。
TPM学习培训教材

第一章 TPM概述第一节 TPM的产生和发展一、TPM的产生TPM是“Total Productive Maintenance”的缩写,中文译为“全员生产维修”,起源于生产现场的设备管理,是一种对生产现场的改善活动。
TPM是在美国生产维修(PM)的基础上发展起来的。
20世纪60年代,日本从美国引进了PM活动,并在推进这项活动的过程中不断充实其活动内容。
为了引导企业有效开展这项活动,以中岛清一等人为首的日本设备管理协会在总结日本企业推进PM活动实践的基础上,吸取了美国的后勤工程学、英国的综合工程学和中国鞍钢宪法中提出的“台台(设备)有人管,人人有专责”群众管理设备的思想,于1971年将PM活动开发扩展为整个企业全员参与的模式,即TPM,并首次制定了统一的TPM定义,之后的10年间,日本许多企业依据TPM定义开展这项活动,并取得了成效。
1982年,第一本标准化(字典式)的PTM 专著问世,即《TPM活动程序》。
1989年,TPM又一次被重新定义,活动本身被注入了更多的内容。
从这个时期起,TPM在日本得到更大范围的普及,并从日本逐步走向世界,受到各国企业界的欢迎,而且给许多企业带来了效益。
注:鞍钢宪法的核心是“两参一改三结合”:“两参”是指干部参加集体生产活动,工人参加企业管理;“一改”是指改革不合理的规章制度;“三结合”是指领导干部、管理技术人员和工人群众相结合,共同解决生产中出现的技术、经济问题。
二、TPM的发展进程TPM的发展进程如表1—1表示。
表1-1 TPM的发展进程以下对几个基本概念做简要阐述,希望读者从中领会TMP的发展进程,这同时也是国际设备维修的技术进步过程。
•事后维修(BM):即设备发生故障后再修理。
缺点是设备故障频繁。
•预防维修(PM):即设备发生故障前就进行维修。
缺点是日常检查和定期检查过于频繁,更换的零件过多,导致了维修费用的增加。
•生产维修(PM):即只对重点设备实行预防维修,对一般设备实行事后维修。
TPM培训教程 PPT课件72页PPT

• 最后,PM、MI和MP被统一为一个全新的PM的定义,即创造性维 护(prod uctive maintenance)
护和检查
●
预测性维护
●延长设备寿命
●备件控制
●故障分析
●润滑控制
●设定设计目标
●维护基础(设备 ●可维护性
子系统)
● ●可操作性
预测技术 维修技术
● ●查
●可靠性 ●较低的寿命 ●周期成本
找故障及诊断
●在设计、审核阶段预
见和防止问题
TOTAL PRODUCTIVE MA0 INTENANCE
16
TPM培训教程
15
TPM培训教程
我们的目标
消除六种主要损失
●零损坏 ●零故障
●生产人员维修人 员工程队
●找出六大主要损
失
●计
算OEE并制定目标
●分析、查找原因
●找到并设定最佳
设备状态
全面工厂改善,建立最优人机系统
主动性维护
有计划的维护
维护、操作技能培 训
目标
●操作人员了解其 设备 ●操作人 员将负责维护设备
●更多有效的低耗 的维护工作
totalproductivemaintenancetpm培训教程15我们的目标totalproductivemaintenancetpm培训教程消除六种主要损失主动性维护有计划的维护维护操作技能培mp设计及早期设备管理零损坏零故障操作人员了解其设备操作人员将负责维护设备更多有效的低耗的维护工作操作人员和维护人员具有更高的技能水平更为可靠的设备易于维护和操作安装后尽快稳定运行生产人员维修人员工程队操作班组维修组操作人员和维修工人生产设计工程人员维修人员找出六大主要损算oee并制定目标分析查找原因找到并设定最佳设备状态初始化清洁使清洁检查易于完成发展检查技能实施一般性检查日常和周期性维护和检查预测性维护延长设备寿命备件控制故障分析润滑控制维护基础设备子系统找故障及诊断设定设计目标可维护性可操作性可靠性较低的寿命周期成本在设计审核阶段预见和防止问题全面工厂改善建立最优人机系统目标参与特殊活动16tpm的一个主要特点是它有明确的追求目标例如零故障及无缺陷等什么事情为零意味着它一次也不会发生因而tpm尤为重视预防性工作如果要等到问题发生才去解决那就已经太迟了
TPM

计划 损失
故 障 部署 调整 模具交换 起动损失
实质运转时间
(净稼动时间) 不良 (价值稼动时间) 损失
性能稼动率 =
模具交换 起动损失 不良修整 良品率 =
稼动时间 加工数量 不良品数
有效运转时间
加工数量
设备总效率=时间稼动率*性能稼动率*良品率
(2)整车透视图overall vier of AEOLUS (interior)
减少功能也是一种浪费
• 两种类型的浪费 * 功能丧失 * 功能减少
• 在功能减少时,机器虽然在进 行,但是会产生生产延误和出 现次品
机器为什么会出现故障
大多数的故障可以追溯到我们可以控 制的事件上,例如:
误操作 miss-operation 缺乏保养 lack of maintenance 疏忽退化 neglected deterioration
2
11 12 1 10
13
14 15 16 17 19 5
18
9 23 22 21
20
发动机(engine) 发动机横剖视图(cross-sectional view of engine)
1、防溅板(splashboard) 2、气缸盖罩(cylinder head cover) 3、气缸盖(cylinder head) 4、机油盘(oil pan) 5、防溅板(splashboard) 6、放油塞(drain plug) 7、气缸体(cylinder block) 8、排气支管(exhaust manifold) 9、进气支管(intake manifold) 10. 空气滤清器(air cleaner) 11. 发火顺序(ignition order) 1-3-4-2 12. 压缩比(compression ratio)
TPM讲义

- 从设备的设计就开始对设备进行控制 - 最终目的是实现无故障和方便日常维护
• Planed Maintenance
计划维护 (PM)
• Predictive Maintenance 预测维护 (PM)
3
PM的发展历史
• Preventative Maintenance • Corrective Maintenance • Maintenance Prevention • Planed Maintenance • Predictive Maintenance 预防性维护 纠正性维护 维护的预防 计划维护 预测维护 美国
0
设计 制作 测试 安装 试运行 接收
时间 问题
问题
很多问题导致难以维持和改进
29
自主安全管理-SHE金字塔
设备灾害 疲劳累积 慢性损失 微缺陷搁置
TPM — 安全,健康,环境(SHE) TPM — 消灭3K (肮脏,劳累,危险 ) TPM — 创造零灾害,零公害的工厂环境(设备灾害和人员灾害)
30
Page 7
Bestway Consultants
TPM目标—零损失
• Zero Accident • Zero Defect • Zero Breakdown • Zero Waste
TPM
TPM
15
零事故 零缺陷 零故障 零浪费
扮演的角色
零故障的五个对策
建立设备 基本条件
保持设备 建立设备 基本状况 操作状况
清洁 SEIKETSU Setting standards 修养 SHITSUKE Sticking to rules
9
TPM的基础—VCS
看得见的管理 一目了然的管理
设备六大损失课件

E:1天的运转时间=C-D=5h
时间运转率(稼动率)=E/C=5/7.5*100=66.7%
5
■作业率
作业率=实作业时间/实动时间 实动时间(总勤务时间)=实作业时间+间接作业+
2R10S.2R13S 0
2
2
ZP10UN
0
1
5
无
1
30
5
TS-910
3
5
无
0
0
1
0
0
5
0
2
5
无
0
3
10
无
0
0
1
无
0
0
1
无
0
4
1
无
0
0
1
无
0
1
2
7#
0
7
20
0
10
5
无
0
1
1套
无
0
2
1
无
0
0
1
2R10S.2R13S 0
2
2
差异 -1 -2 1 0 0 -4 25 -2 -1 -5 -3 -7 -1 -1 3 -1 -1 -13 5 0 1 -1 0
这里所说的负荷时间,从工作1天(或者1个月)的作业时间 中扣除了生产计划的停歇时间、计划保全的停歇时间、日常管 理方面的朝会等停歇时间。
停止时间,是指因故障、准备、调整、换刀等而停止的时间
2
■损失时间
TPM六大损失分析

TPM六大损失分析tpm零目标指需要通过TPM系统的管理方法预防和消除这些损失。
从设备应用时间的基础上,不同时间段都有可能造成损失和浪费。
零目标重点需要解决tpm六大损失。
TPM六大损失包括哪些,下面就来看看。
TPM六大损tpm 六大损失1--设备停机损失设备由于故障不能正常运转而造成的损失叫作设备停机损。
设备停机损失是明显的,是被重点关注的,也是在大多数企业里人们花费大量时间去解决的损失,TPM的工作则是杜绝和降低这类损失。
通过TPM,最重要的是改变大家“设备故障不可避免”这种根深蒂固的传统思想,并不断向“预防为主”的思想转变,从而防止和不断降低设备故障的发生频率。
tpm 六大损失2--换型损失由于产品品种之间的切换而造成的损失。
这个损失看上去与设备本身的状态没有关系,但实际上生产不同产品需要切换不同的工装、模具,造成设备事实上的损失。
所以,丰田公司提出单分钟快速换型,指产品之间切换的目标时间控制在10分钟以内,当然越快越好。
实现SMED要尽可能减少机内的换型时间,机内时间是指需要停机进行换型操作的时间。
SMED是对管理者智慧和勇气的挑战,是不断精益求精的过程。
随着个性化、小批量定制时代的来临,实现SMED减少换型损失显得尤为重要。
tpm 六大损失3--较小停机的损失由于误操作、报警停机等原因造成设备短时间停顿的损失。
这种损失常常不被人们所关注,例如,由于设备卡料、加工时崩刀、出现不合格报警、过载保护等原因所造成设备的较小停机。
将较小停机列入损失之列,提醒我们要留意各种损失,尽管这种损失单个看来似乎微不足道。
所以管理者要培养“现地现物”的工作习惯,并且要有敏锐的眼光发现和关注这些损失。
同时,调动全体人员的积极性,对这些损失及时发现和报告。
比如,公司有一台自动化程度属于四级的设备,经常发生某个时间段不能完成产量的问题。
因为该设备效率比较高,整个班次的产量还暂时可以满足客户订单要求,所以,没有人过多关注设备的问题。
设备管理六大损失与TPM安灯系统
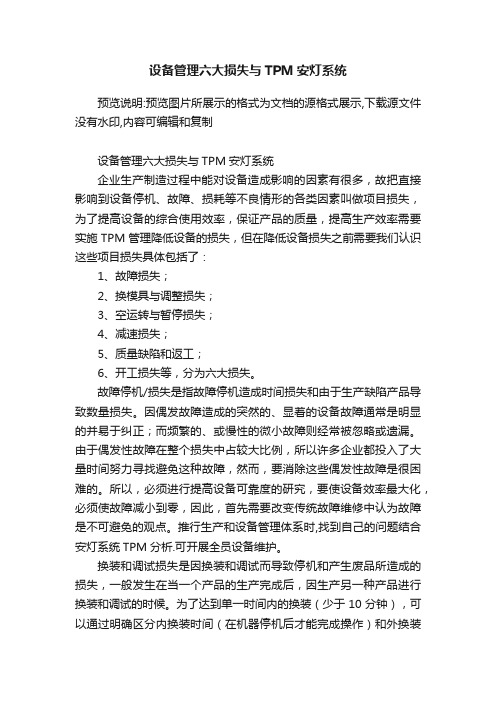
设备管理六大损失与TPM安灯系统预览说明:预览图片所展示的格式为文档的源格式展示,下载源文件没有水印,内容可编辑和复制设备管理六大损失与TPM安灯系统企业生产制造过程中能对设备造成影响的因素有很多,故把直接影响到设备停机、故障、损耗等不良情形的各类因素叫做项目损失,为了提高设备的综合使用效率,保证产品的质量,提高生产效率需要实施TPM管理降低设备的损失,但在降低设备损失之前需要我们认识这些项目损失具体包括了:1、故障损失;2、换模具与调整损失;3、空运转与暂停损失;4、减速损失;5、质量缺陷和返工;6、开工损失等,分为六大损失。
故障停机/损失是指故障停机造成时间损失和由于生产缺陷产品导致数量损失。
因偶发故障造成的突然的、显着的设备故障通常是明显的并易于纠正;而频繁的、或慢性的微小故障则经常被忽略或遗漏。
由于偶发性故障在整个损失中占较大比例,所以许多企业都投入了大量时间努力寻找避免这种故障,然而,要消除这些偶发性故障是很困难的。
所以,必须进行提高设备可靠度的研究,要使设备效率最大化,必须使故障减小到零,因此,首先需要改变传统故障维修中认为故障是不可避免的观点。
推行生产和设备管理体系时,找到自己的问题结合安灯系统TPM分析.可开展全员设备维护。
换装和调试损失是因换装和调试而导致停机和产生废品所造成的损失,一般发生在当一个产品的生产完成后,因生产另一种产品进行换装和调试的时候。
为了达到单一时间内的换装(少于10分钟),可以通过明确区分内换装时间(在机器停机后才能完成操作)和外换装时间(在机器运转时可以完成操作),以及减少内换装时间来减少整个换装时间损失。
安灯系统其中的及时响应可以非常有效的解决的该问题,一线工人只需按下对应事件的按钮,设备管理部门能立刻知道并作出反应。
减速损失是指设计速度与实际速度的差别。
速度损失对设备效率的发挥产生了较大障碍,应当仔细研究,以消除设计速度和实际速度二者之间的差别。
设备实际速度低于设计速度或理想速度的原因是多种多样的,如机械问题和质量缺陷,历史问题或者设备超负荷等。
影响OEE的6大损失PPT幻灯片

0.5分/个× 400个 400分
×
100 = 50%
良 品 率 = 加工数量–不良数量 × 100 加工数量
(例)
400个– 8个 400个 × 100 = 98%
设备综合效率 = 时间稼动率 × 性能稼动率 × 良品率 (例) 0.87 × 0.50 × 0.98 × 100 = 42.6%
10
失,或运行时对设置的改动。其原因有:
–移交工具 –寻找工具 –安装新工具 –调节新设置
5. 生产次品的损失 由于报废、返工或管理次品所导致的时
间损失。其原因有:
–人工错误 –劣质材料 –工具破损 –软件程序缺陷
3. 空转和瞬间停机的损失
由于小问题引起的短暂中断。其原因有:
–零件卡在滑道里 –清除碎屑 –感应器不工作 –软件程序出错
(O.E.E.) 85%
2020/2/7
14
综合设备效率
工作时间 Total operating time A 负荷时间 Loading time
计划
B 稼动时间 Running time
停止
C 性能稼动时间
性能
D 价值稼动时间 不良
负荷率
时间稼动率 性能稼动率 良品率
OEE=时间稼动率x性能稼动率x良品率=B/A x C/B x D/C
2020/2/7
8
影响OEE的六大损失
1. 停工和故障的损失 设备失效需要执行维护操作。其原因有:
–机器过载 –螺钉和螺帽松开 –过渡磨损 –缺少润滑油 –污染物
4. 降低速度的损失 设备在低于其标准设计速度运行导致的
损失。其原因有:
–机器磨损 –人为干扰 –工具磨损 –机器过载
2. 换装和调试的损失 从一种产品到另一种产品换产的时间损
TPM

记录分析
• 维修记录分析:维修记录分析是全面生产维修的一
项重要内容,尤其是“平均故障间隔时间”分析(MTBF), 很受日本设备维修界的重视。
• 分析平均故障间隔期的作用是分析设备停机
维修作业是怎样发生的,把发生的时间、现象、原因、所 需工时、停机时间等所有总是都记录下来,制成分析表。 通过分析可获得下列信息: ----选择改进维修作业的对象 ----估计零件的寿命 ----选择点检点,确定和修改点检标准 ----备件标准的确定
TPM
TPM的具体内容: • 日常点检 • 定期检查 • 计划修理 • 改善修理 • 故障修理 • 维修记录分析
TPM
• 日常点检:即操作者每天班前用听、看、摸等方 法方法,按点检标准对设备进行检查。日常点检 的目的是保证设备正常运转,不发生故障。 点检的主要内容:异声、漏油、振动、温度、 润滑和调整等。 • 定期检查:即维修工人按计划定期对重点设备进 行的检查。定期检查的目的是保证设备达到规定 的性能。检查工作包括:测定设备的劣化程度, 确定设备性能,调整设备等。
实施简单 处理 突发故障 确认缺陷 维修联席 会议
事后修理 可 简单处理? 否 否 立刻修理? 要 故障修理
掌握实际 情况
零故障实施的三大方向
运 转 技 术 提 升 操作失误的防止 设备清扫的实施 人的技术提升 日常点检的实施 人的技术提升
人的技术提升
零 故 障
保 养 技 术 提 升
巡回点检的实施 故障解析的实施 保养计划的确立 修复整备技术提升 预防保养的实施
减少六大损失扩展到减少十六大损失
7、 速度损失; 8、 废品与返工; 9、 管理损失:等待指示货等待材料; 10、操作损失:设备停机、运行、方法、工 艺、技能和劳动情绪影响; 11、生产线组织损失:生产线安排组织,自 动化及失效损失;
- 1、下载文档前请自行甄别文档内容的完整性,平台不提供额外的编辑、内容补充、找答案等附加服务。
- 2、"仅部分预览"的文档,不可在线预览部分如存在完整性等问题,可反馈申请退款(可完整预览的文档不适用该条件!)。
- 3、如文档侵犯您的权益,请联系客服反馈,我们会尽快为您处理(人工客服工作时间:9:00-18:30)。
扫 就 是
照片 扫 就 是
润 手手机机:: 格清格需言扫言要:就:精清是设心备照扫润就料就滑像,是、孩才点清子能检扫一健就样康,成是长改。善
《爱人一样爱护,子女一样关照》
MY-JOB(我的职责)
MY-AREA(我的区域)
1 充分理解PRO-3M活动的概要。
地面 保持干净、无油污的状态
设备综合效率(OEE)计算方法
设备综合效率=时间开动率*性能开动率*良品率 OEE要达到85%以上
台历时间(台历时间=12小时)
工作时间 (应生产的时间)
休息
负荷时间 (设备应开动的时间)
计划 停止
运行时间 (设备实际开动时间)
停止 损失
净开动时间 (生产产品的时间)
速度 损失
价值开动时间
不良
(生产良品的时间) 损失
10 进行持续性的事后管理及实施。
表格文件 表格填写正规及时,文件管理正规有效
TPM自主保全活动具体内容
推行 日常6S
整理 整顿 清扫 清洁 清心 安全
运用 5感 视觉 触觉 听觉 味觉 嗅觉
探究 6大系统 紧固件 驱动传导
润滑 空压 液压 电装控制
查找 5大不合理
劣化 发生源 困难点 疑点 整理整顿
吃饭、休息时间
生产调整、开会 计划保全、检修
1
故障
每1台设备的故障频度 10分钟以上1次/月
2
准备 准备交替调整时间/次 交替 10分钟以下
3
瞬间 空转瞬间停止频度 停止 10分钟以上1次/月以下
4
速度 实现理论Cycle Time 降低 提高15%以上
5
不良 工程不良率 修整 0.1%以下
6
收率
投入材料的 99%以上
消除 6大浪费 MTBF/MTTR LOSS1+LOSS2
CT↔ 瞬间停止减少
PPM↓ 报废减少
2 积极参与团队的活动。
货架 货架无灰尘,物品进行可视化管理
3 研究标杆团队的活动事例提升团队的水平等级。
工作橱 无不必要品,必要品进行定置管理
4 PRO-3M活动切实实践并形成习惯化。
清扫工具 清扫工具齐全、实用,不得浪费
5 团队领导赋予的任务保质保量执行。
润滑油 润滑油可视化,添加时避免浪费及污染
6 挖掘现场的不合理及浪费,开展复原消除工作。
物料容器 物流容器无垃圾、无污染,三定管理
7 通过现场体验,确保设备固有功能的充分利用。
工具 工具无缺少及损坏,能快速取放使用
8 通过团队活动来提升与保全人员的团队协作能力。
工装 工装状态良好,无污染,拿取方便
9 进行活动指标及提升度统计管理。
备件 备件适量,更换登记并分析原因
时间开动率 负荷时间-停止时间
负荷时间 95%以上
性能开动率 理论CT*生产数量
开动时间 90%以上
良品率 生产数量-不良数量
生产数量 99.9%以上
明确 职业-3M
我的设备
我的职责
我的区域
MY MACHINE 我的设备
设备名称
弯管机
清扫就是点检
设备编号 清扫周期
擦拭
533-6 天/次
锁紧
给油
清
清
狼来了 羊没了
TPM-自主保全与六大损失
经营的需要
六大损失
我不要浩瀚的宇宙, 我要新鲜的羊肉。 灰太狼,抓羊去。
1.故障停止损失 特点:突发、紧急 我是最聪明的,只要我在,你 就什么也做不了。
3、瞬间停止损失 特点:难以统计、偷吃产能 我好吃懒做。你稍不注意,我 就偷偷睡个懒觉。
5、不良发生损失 特点:破坏性强 我脾气暴躁,喜怒无常,没事 就揍你个鼻青脸肿。
TPM自主保全 特点:减少浪费,提高效率 遵命老婆,我用TPM技巧抓羊, 一抓一个准,哈哈,亲爱的小 肥羊,我灰太狼大王来了!
2、转产停止损失 特点:用时长 我爱美,所以每天都要换衣服 化妆,打扮不好我是不工作的。
4、速度降低损失 特点:慢 唉,年纪大了,做什么都慢。 想当年,我跑的比羚羊还快。
6、收率减少损失 特点:浪费大 哎,长这么多肉干吗?又不漂 亮,该减肥了。