出货检验流程图
IQC--IPQC--FQC--OQC检验控制流程图
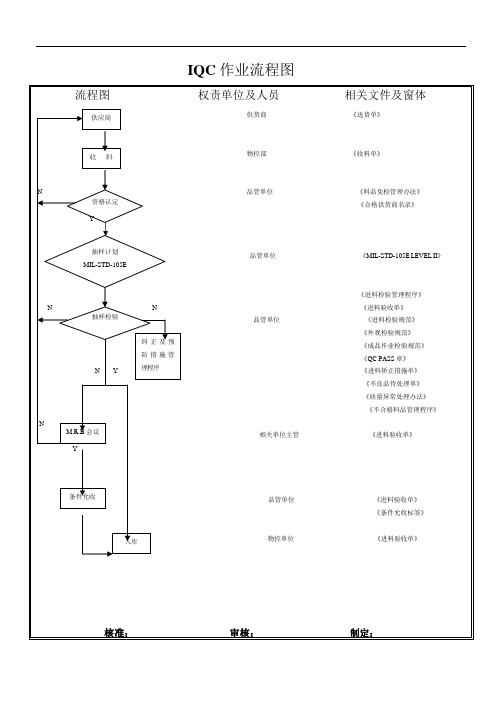
纠 正 及 预防 措 施 管
理程序
IQC 作业流程图
流程图
权责单位及人员
相关文件及窗体
供货商
《送货单》
物控部
《收料单》
N
品管单位
《料品免检管理办法》 资格认定
Y
《合格供货商名录》
抽样计划 MIL-STD-105E
品管单位 《MIL-STD-105E LEVEL II 》
《进料检验管理程序》
N
N
《进料验收单》 抽样检验
品管单位
《进料检验规范》 《外观检验规范》 《成品作业检验规范》 《QC PASS 章》 N
Y
《进料矫正措施单》 《不良品待处理单》 《质量异常处理办法》 《不合格料品管理程序》
N
相关单位主管
《进料验收单》
Y
品管单位
《进料验收单》 《条件允收标签》
物控单位 《进料验收单》
核准: 审核: 制定:
供应商
收
料
入库
M.R.B 会议 条件允收
核准:审核:制定:。
OQC出货检验程序(含表格)

OQC出货检验程序(ISO9001-2015)1.0目的:为确保生产线所生产的成品品质符合客户品质要求,对整个出货检验过程进行有效的管理,特制定本程序.2.0范围:适用于汕头市万晖实业有限公司所有产品出货品质检验作业.3.0职责:3.1OQC:出货品质检验、品质判定、状态标识、异常反馈与跟踪、检验结果记录。
3.2QE:制定或修订出货品质检验标准、异常原因分析、异常跟踪及作业指导。
3.3生产部:出货待检通知、不合格批的重工作业、不合格品处理.3.4仓库:成品入库管理、库存超保质期成品再检通知。
3.5业务部:成品特采申请、重工作业安排.4.0定义无5.0作业内容5.1入库成品待检通知生产部入库待检的成品必须是经FQC全检并判定合格(需贴合格标识)的产品,入库前需核对入库数量与检验数量是否相符,最后将待检之成品移入成品仓库指定的出货待检区域。
然后开立《出货待检通知单》通知OQC进行出货检验。
5.3出货品质检验作业5.3.1检验依据OQC检验时依据《成品检验规范》、《产品检验标准书》、工程样办等对产品进行品质检验和判定,抽样作业时按照MIL-STD-105E普通Ⅱ级抽样,合格质量允收水准(AQL):致命缺陷(CRI):0、主要缺陷(MAJ):0.65、次要缺陷(MIN):1.5,若客户有特别要求按照客户要求的允收水准进行抽样作业,具体参照《抽样检验计划》执行.5.3.2检验项目检验项目包括:外观/尺寸/结构/特性/包装/标识等项目,具体检验项目参照《成品检验规范》中规定检验项目进行检验.5.3.3OQC出货检验作业时应按照抽样计划规定的抽检数量从待检批中的不同部位、不同箱号的箱子中抽取指定数量进行检验,尽量减少不量流入客户端.检验完成后需在《出货待检通知单》上进行品质判定,然后将《出货待检通知单》归还生产部.5.3.4正常情况出货检验需在6个工作小时内完成,急出货情形需在2个工作小时内完成检验.检验结果是否合格都需真实且详细的记录于《OQC成品检查报告》上,以便追溯和统计分析.5.3.5经OQC检验合格批次,由生产部门填写《成品入仓单》办理入库.5.4检验状态标识检验合格在标签上盖PASS印章,不合格贴红色REJECT标签,特采使用贴黄色特采使用标签.挑选或加工使用则贴挑选/加工使用标签.具体参考《产品标识与追溯性控制程序》.5.5品质异常反馈及处理经抽检判不合格批次,需在产品外箱上贴上红色的不合格(REJECT)标签,并将判定结果记录于《成品待检通知单》上并归还仓库,同时OQC开立《出货检验异常报告》给OQC组长确认/主管审核/经理核准,然后由业务/PMC/生产/品质/工程等相关单位会签评审.最终由(副)总经理批准,不合格批的处理方式按(副)总经理批准意见执行,会签完后将此单给责任单位进行原因分析和制定改善对策,至于检验发现之不合格品的处理方式参照《不合格品的控制程序》执行.5.6特采放行作业5.6.1经OQC检验不合格批产品,经公司(副)总经理批准决定特采使用的,由业务开立《特采申请单》并附上《出货检验异常报告》给品质部/工程部/生产部/PMC等相关单位会签评审,由公司(副)总经理批准执行,最后由OQC将不合格标签撕下,在标签上盖PASS印章,若是经客户同意特采使用需在外箱贴特采使用标识.5.7不合格批重工再检判重工的不合格批,OQC需对重工过程进行跟踪(包括重工项目是否与反馈之项目相符,重工之数量是否与判退的数量相符等内容),重工后生产部必须重新报验此批,并在《出货待检通知单》上注明”已重工”字样.重工再检OQC必须再次填写《OQC成品检查报告》,报告上需详细注明为”重工再检”字样,并详细记录《出货检验异常报告》编号和其他相关信息,以便于追溯.5.8库存成品再检所有库存成品超过保存期限,仓库必须重新提报给OQC重检和判定.重检后原标识需更换,若重检判不合格,需开立《出货检验异常报告》给相关单位会签评审,不合格批的处理参照5.5/5.6/5.7执行,不合格品参照《不合格品控制程序》执行.5.9控制计划的传递和执行5.9.1在新产品投产之前,由品质经理针对此项产品的特殊特性内容,对检查员进行培训,要求品管员严格按特殊特性的内容执行检查。
ISO9001:2015成品出货检验控制程序
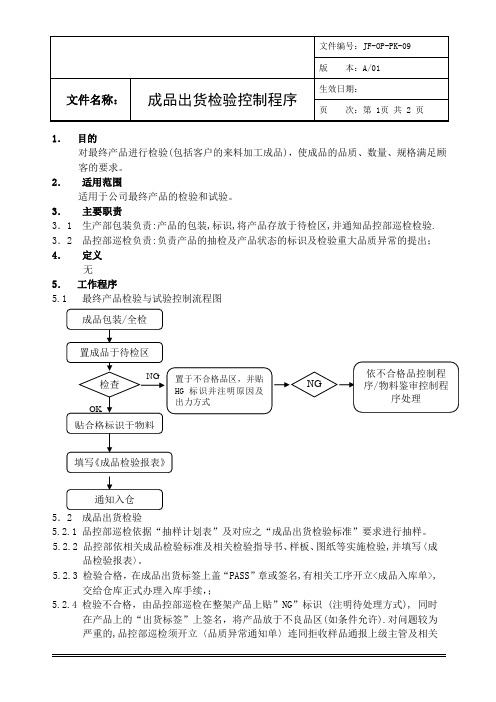
1. 目的对最终产品进行检验(包括客户的来料加工成品),使成品的品质、数量、规格满足顾客的要求。
2. 适用范围适用于公司最终产品的检验和试验。
3. 主要职责3.1 生产部包装负责:产品的包装,标识,将产品存放于待检区,并通知品控部巡检检验.3.2 品控部巡检负责:负责产品的抽检及产品状态的标识及检验重大品质异常的提出;4. 定义无5. 工作程序5.1 最终产品检验与试验控制流程图5.2 成品出货检验5.2.1 品控部巡检依据“抽样计划表”及对应之“成品出货检验标准”要求进行抽样。
5.2.2 品控部依相关成品检验标准及相关检验指导书、样板、图纸等实施检验,并填写〈成品检验报表〉。
5.2.3 检验合格,在成品出货标签上盖“PASS ”章或签名,有相关工序开立<成品入库单>,交给仓库正式办理入库手续,;5.2.4 检验不合格,由品控部巡检在整架产品上贴”NG ”标识 (注明待处理方式), 同时在产品上的“出货标签”上签名,将产品放于不良品区(如条件允许).对问题较为严重的,品控部巡检须开立〈品质异常通知单〉连同拒收样品通报上级主管及相关单位。
具体以“不合格品控制程序”处理。
5.3.5 如出货紧急或其它原因(原则对成品的品质没有致命或重大的影响),需要特采使用时,可由生产部/销售部提出〈物料鉴审单〉经过相关部门会审后,方可特采使用,具体依“物料鉴审控制程序”处理。
5.3.6 所有检验产品的标识以“产品标识/可追溯性控制程序”处理;5.3.7对于重复性发生,品质严重超出允收水准的重大品质不良的,为防止不良再次发生,品控部巡检须提出〈纠正/预防措施要求书〉,责令责任单位进行原因分析及改善对策,具体依“纠正与预防措施控制程序”处理。
5.4 记录的保存〈成品检验报表〉由品控部保存期限为一年,具体依“质量记录控制程序”为准。
6.相关文件6.1《检验标准》6.2《抽样计划表》6.3《不合格品控制程序》6.4《物料鉴审控制程序》6.5《纠正与预防措施控制程序》6.6《质量记录控制程序》7.应用表单7.1〈成品检验报表〉---------------------------7.2〈物料鉴审单〉----------------------------------7.3〈纠正/预防措施要求书〉--------------------------。
产品质量检验管理程序(含流程图)
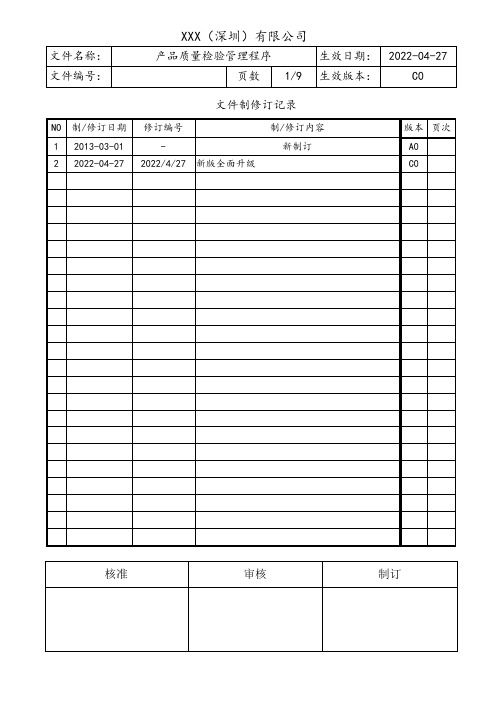
文件制修订记录1.0目的为了有效测量与监控产品从进料、制程、成品及出货各阶段检验作业能始终符合产品工程规范的各项要求。
2.0范围:适用于品管IQC、IPQC、QA过程作业。
3.0权责:3.1品管部:负责各阶段品质检验的执行、标识、追溯的管理、实际验货。
3.2工程部:产品作业标准的制定与检查。
3.3生产部:依生产计划、工程标准、验收标准执行生产作业。
3.4业务部:依订单需求验收出货数量。
3.5资材部:采购物料的外部联络。
4.0定义:无5.0作业内容:5.1进料检验5.1.1收料5.1.1.1供应商依据采购订单交货到公司仓库。
5.1.1.2仓管依据采购订单核对送货单是否一致,如若不符则退货并要求供应商重新交货,符合则点收数量并开出[进货单]。
5.1.1.3仓管将[进货单]连同要求供应商提供的相关文件(如材质报告、检验报告、测试报告等)交品管部,通知IQC进行检验。
5.1.1.4检验参照依据AQL表或依客户端需求作抽样检验。
5.1.1.5品管部IQC接到[进货单]后对供应商所提供的文件进行验证,(有法规环保类要求的产品必须依客户指定或经国家认可有检测能力机构出具的测试报告,如“SGS报告”等);品管部可以根据批量大小、价值贵重程度来对供应商所提供产品的材质进行一次确认。
5.1.1.5下列几项物料必须由品管部进料检验:a)生产性原材料。
b)外发加工产品。
c)包装材料等。
5.1.2需应用下列一种或多种方法进行验收、检验5.1.2.1接收检验及测试:a)核对材质证明(限自购原材料,样品或来料加工产品可不需要提供材质证明),核对供应商提供的相关文件。
b)依《检验标准书》逐项检验与填写[进料检验报告],无《检验标准书》时,依图面求或样板检验,检验结果可直接记录于[进料检验报告]上。
c)凡属客户提供来料进行加工,如无图面,依据客户提供的规格进行检验;如既无规格又无图面,IQC只针对其外观进行检验并记录于[进料检验报告]上。
出货检验作业流程
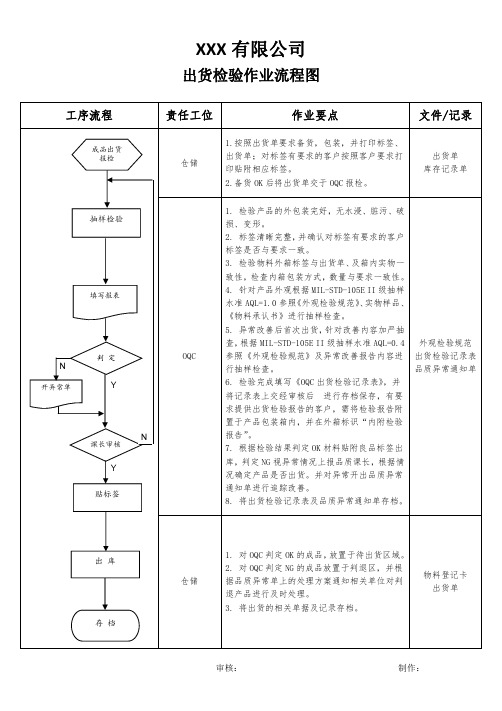
1. 检验产品的外包装完好,无水浸、脏晰完整,并确认对标签有要求的客户
标签是否与要求一致。
3. 检验物料外箱标签与出货单、及箱内实物一
致性,检查内箱包装方式,数量与要求一致性。
4. 针对产品外观根据 MIL-STD-105E II 级抽样
水准 AQL=1.0 参照《外观检验规范》、实物样品、
求提供出货检验报告的客户,需将检验报告附
置于产品包装箱内,并在外箱标识“内附检验
报告”。
7. 根据检验结果判定 OK 材料贴附良品标签出
库,判定 NG 视异常情况上报品质课长,根据情
况确定产品是否出货。并对异常开出品质异常
通知单进行追踪改善。
8. 将出货检验记录表及品质异常通知单存档。
出库 存档
仓储
XXX 有限公司
出货检验作业流程图
工序流程
责任工位
作业要点
文件/记录
成品出货 报检
仓储
1.按照出货单要求备货,包装,并打印标签、 出货单;对标签有要求的客户按照客户要求打 印贴附相应标签。 2.备货 OK 后将出货单交于 OQC 报检。
出货单 库存记录单
抽样检验
填写报表
N 开异常单
判定 Y
N 课长审核
1. 对 OQC 判定 OK 的成品,放置于待出货区域。 2. 对 OQC 判定 NG 的成品放置于判退区,并根 据品质异常单上的处理方案通知相关单位对判 退产品进行及时处理。 3. 将出货的相关单据及记录存档。
物料登记卡 出货单
审核:
制作:
《物料承认书》进行抽样检查。
5. 异常改善后首次出货,针对改善内容加严抽
查,根据 MIL-STD-105E II 级抽样水准 AQL=0.4 外观检验规范
质量检验控制流程图

10
提料
过程检验
N
技术分析
1.IPQC(制程检验员)对半成品工艺材质和作业手法进 行。2.有品质异常时技术部进行技术分析出矫正方案
1.装配组按照配置清单领料。2.对物料进行自检合格才
11
成品装配
可装配。3.现场加工部位要通知检验员确认。4.严格按
照作业指导书的工艺作业。
N产品损坏或其他异常
4.检验不合格请生产部重工后再送检。
15
装柜发货
1.样品确认后根据订单可进行外购件的批量采购普和半 成品加工; 2.自检物料合格才可生产,严格按规范操作; 3.过程不良时要按技术部的方案进行重工处理,并通知 质检员确认。 1.对供应商物料核对数量及规格查看包装完整性必须标 识有送货单,2.报检给IQC(进料检验)。3.实物不符 或检验不合格时请通知采购与供应商联络办理退货手续 。 1.核对确认样品以及技术图纸。2.按检验规范和技术参 数的要求进行检验。3.合格后在实物包装上贴上“合格 ”标签并通知仓库入库。4.有不合格品超出允收水准, 通知仓库要求退货。5.将不合格事件知会采购,通知供 应商改善。
1.根据技术参数要求外购件样品购买; 2.购买的样品要有说明书,出厂检验报告,安全器件要 有注册检验报告或者认证证书,特殊要求材料要有第三 方检验材料成份报告; 3.进行制样或者小批量生产。
1.技术员对样品进行全面的试验; 2.符合技术要求的要贴合格标签并签名; 3.样品不符合返回图纸设计到制样重新跟踪解决。
质量检验控制流程图
步 骤 采购
仓库
部门 质量
生产
技术
说明
1
图纸设计 1.根据订单要求设计产品
2
成品检验流程图和指导

生效日期
核对出库单内容、数量正确无误后,予以放行
注意事项
当检验数量小于或等于50时,采用全检方式,合格品入库,不合格品予以返工
当检验数量大于或等于51时,采用抽检的方式
成品检验合格后,方可入库或出货
检查后的合格品样品检验基准书
成品检验
编制
吴建军
审核
按成品入库单的料号、品名,调出该产品的检验标准
准备必要的设备与测试程序
以每一包装作为一检验批
检验允收后,在该批贴“检验允收”的标示
成品检验人员核对允收数量及品名后,签名确认
出货检验
按出货通知单内容,安排出货产品,通知检验人员验货
成品检验人员按出库通知单数量检验送检批,检验方式同入库检验
按检验标准检验允收后,在该批粘贴“最终检验允收标准”并在查核表上填写检验结果
三、成品检验过程指导
1、成品检验流程图
生产人员成品检验专员品质主管
2、成品检验作业指导书
名称
成品检验作业指导书
部门
班组
过程指导
包装检验
核对生产资料,签收包装样板,验证材料、配件、纸箱
过程巡检,并记录
对包装品质异常予以反馈,并跟进改善
入库检验
制造部门将待检品送到检验区,成品检验人员核对入库单与待检品的料号与品名
出货和客退检验不合格品标示和处理流程
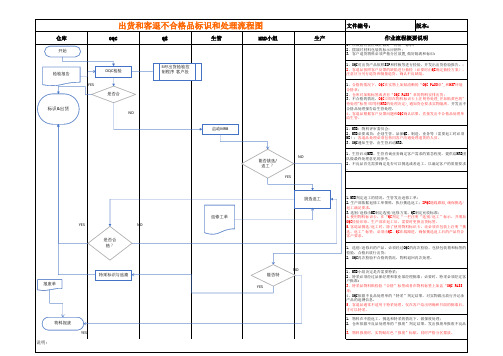
NO 特采标识与追溯
报废单
能否特 YES
1、MRB小组决定是否需要特采; 2、特采必须经过品保经理和事业部经理批准;必要时,特采必须经过客 户批准; 3、特采品物料贴检验“合格”标签或者在物料标签上加盖“OQC PASS 章; 4、OQC依据不良品处理单的“特采”判定结果,对实物做出放行并记录 产品的追溯信息。 5、客退品通常不适用于特采处理。仅在客户给出明确和书面的批准后, 才可以特采。 1. 物料在不能返工、挑选和特采的情况下,做报废处理; 2. 仓库依据不良品处理单的“报废”判定结果,发出报废单报废不良品 。 3. 物料报废时,实物贴红色“报废”标贴。同时严格分区摆放。
出货和客退不合格品标识和处理流程图
仓库
开始
文件编号: 生产
版本: 作业流程概要说明
OQC
QE
生管
MRB小组
1、应放置待检区域并做好“待检”标示; 2、摆放时材料包装的标示应朝外; 3. 客户退货物料必须严格分区放置,做好隔离和标识;
检验报告 YES
OQC检验
SIP/出货检验控 制程序 客户投
1、OQC对出货产品依照SIP和样板等进行检验,并发出出货检验报告。; 2、客退品按照客户反馈的缺陷进行抽检(必要时由QE确定抽检方案), 注意区分另行退货和批量退货,确认不良缺陷。 1、合格的情况下,OQC在实物上加贴清晰的“OQC PASS章",和HSF环境 合格章; 2、仓库对加贴标签或者有“OQC PASS”章的物料安排出货; 3、不合格的情况,OQC立即在物料标识卡上注明待处理,并加贴黄色的" 待处理"标签(即等待MRB的处理决定),通知货仓要求实物隔离,并发出不 合格品处理报告给生管处理。 4、客退品根据客户反馈问题和OQC确认结果,直接发出不合格品处理单 给生管。
出货检验标准规范
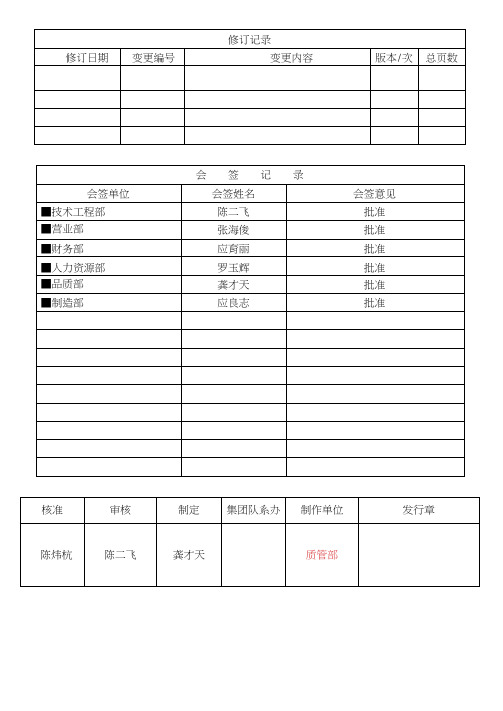
5. 4. 6钢板类检査原那么:
5. 4. 7铝板类检査原那么:
5・5出货检査流程如下:
5. 5.1业务开出?发货告知单?,需提前分发有关单位,仓库依?发货告知单?备货。
OQC 依5. 4项规定进行检査。
5. 5.2当发现异常时,OQC开出?品质异常解决单?,MRB流程作出最后鉴定成果后,OQC将有
关异常状况记录于?品质异常解决单?中发给贵任单位进行解决及改良.不合格品依MRB流程最后鉴定成果,按?不合格品控制程序?进行特采或挑选、重工解决。
由OQC每月对各类别产品进行抽样送实验室进行检测,并
5. 5. 3对环境管制物质测试工
程,对检测成果进行保存.
六.有关文献:
6.1?检査与实验控制程序? HLSG2-Q00020
6. 2?不合格品控制程序?
HLSG2-Q00017
七.有关表单:
7.1?出货检查报告? HLSGQ-QOOOU
7.2?OQC日报表? HLSGQ-Q00006
附件:出货检査流程图如下:。
产品检测流程图解
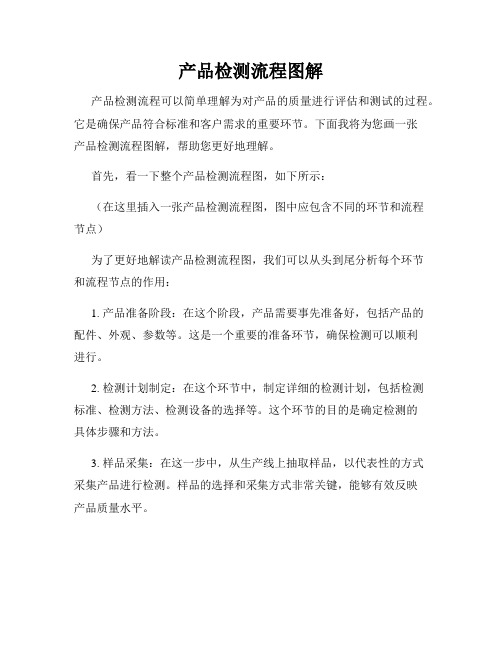
产品检测流程图解产品检测流程可以简单理解为对产品的质量进行评估和测试的过程。
它是确保产品符合标准和客户需求的重要环节。
下面我将为您画一张产品检测流程图解,帮助您更好地理解。
首先,看一下整个产品检测流程图,如下所示:(在这里插入一张产品检测流程图,图中应包含不同的环节和流程节点)为了更好地解读产品检测流程图,我们可以从头到尾分析每个环节和流程节点的作用:1. 产品准备阶段:在这个阶段,产品需要事先准备好,包括产品的配件、外观、参数等。
这是一个重要的准备环节,确保检测可以顺利进行。
2. 检测计划制定:在这个环节中,制定详细的检测计划,包括检测标准、检测方法、检测设备的选择等。
这个环节的目的是确定检测的具体步骤和方法。
3. 样品采集:在这一步中,从生产线上抽取样品,以代表性的方式采集产品进行检测。
样品的选择和采集方式非常关键,能够有效反映产品质量水平。
4. 检测操作:这个环节是实施产品检测的关键步骤,包括产品的功能性、性能、安全性等方面的测试。
根据检测计划和标准,使用相应的设备进行检测操作。
5. 数据分析与记录:在检测过程中,需要对测试结果进行数据分析和记录。
这些数据包括产品的各项指标、检测结果、不良项等。
数据分析将帮助我们评估产品的质量。
6. 检测结果评估:在这一步中,根据检测结果评估产品是否符合标准和客户需求。
评估结果将决定产品是否合格,是否需要进行改进或修正。
7. 报告生成与审核:根据检测结果生成检测报告,并进行内部审核。
检测报告将包括检测的目的、方法、结果、结论等关键信息,为后续的工作提供依据。
8. 售前检验/出货检验:这是在产品销售前的最后一道关口,确保产品质量。
对产品进行最后的检查和测试,确保产品在出厂前符合质量要求。
9. 售后服务评估:这个环节发生在用户购买产品并使用一段时间之后。
通过与用户的沟通和调查,了解产品在实际使用中的性能和质量,以改进产品设计和生产过程。
10. 不合格品纠正措施:如果产品检测不合格,需要采取相应的纠正措施。
工厂出货检验流程图及工作细则
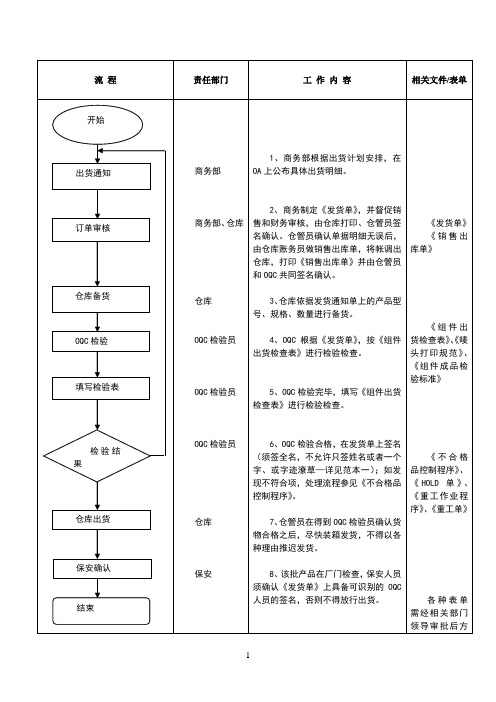
流程责任部门工Fra bibliotek内容相关文件/表单
商务部
商务部、仓库
仓库
OQC检验员
OQC检验员
OQC检验员
仓库
保安
1、商务部根据出货计划安排,在OA上公布具体出货明细。
2、商务制定《发货单》,并督促销售和财务审核,由仓库打印、仓管员签名确认。仓管员确认单据明细无误后,由仓库账务员做销售出库单,将帐调出仓库,打印《销售出库单》并由仓管员和OQC共同签名确认。
3、仓库依据发货通知单上的产品型号、规格、数量进行备货。
4、OQC根据《发货单》,按《组件出货检查表》进行检验检查。
5、OQC检验完毕,填写《组件出货检查表》进行检验检查。
6、OQC检验合格,在发货单上签名(须签全名,不允许只签姓名或者一个字、或字迹潦草—详见范本一);如发现不符合项,处理流程参见《不合格品控制程序》。
7、仓管员在得到OQC检验员确认货物合格之后,尽快装箱发货,不得以各种理由推迟发货。
8、该批产品在厂门检查,保安人员须确认《发货单》上具备可识别的OQC人员的签名,否则不得放行出货。
《发货单》
《销售出库单》
《组件出货检查表》、《唛头打印规范》、《组件成品检验标准》
《不合格品控制程序》、《HOLD单》、《重工作业程序》、《重工单》