精益生产衡量指标优秀课件
精益生产各绩效指标计算公式汇总ppt课件
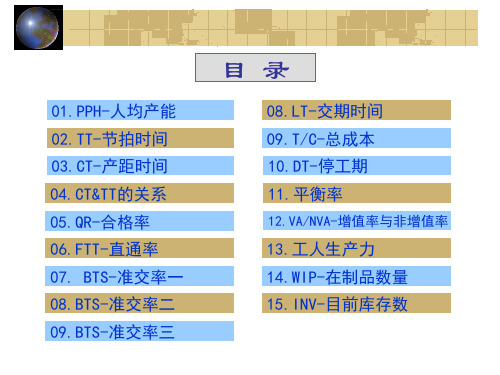
X 100%
制造周期(Manufacturing cycle time)
非增值比率计算方式:
非增值率= 1 - 增值率
在整堂课的教学中,刘教师总是让学 生带着 问题来 学习, 而问题 的设置 具有一 定的梯 度,由 浅入深 ,所提 出的问 题也很 明确
Labor Productivity -- 工人生產力
T/T
&
C/T
的聯系
如果Takt time(节拍時間)不等於Cycle Time (产距时 间),則流程存在不平衡问题。 當T/T 等于C/T 时,表示沒有生产过剩,且員工效率刚好 满足客戶需求
Process Time 流程時間= Cycle time 產距時間 x 操作員人數 Lead Time 流程週期 = Process Time 流程時間 + (在制品數 x 產距時間)
注: 材料成本:适用的所有材料 非材料成本:勞动力+企业一般管理費用+C品鞋+消費者反饋
在整堂课的教学中,刘教师总是让学 生带着 问题来 学习, 而问题 的设置 具有一 定的梯 度,由 浅入深 ,所提 出的问 题也很 明确
DT --- down time 停工期
停工期指的是任何未计划的生产线或流程停顿。原因包括:材 料短缺,生产 线饱和,机器故障,质量问题。
= 0.62 = 62%
底部(鞋材)FTT: = 合格率(大底)x合格率(PU) x合格率(PH) 例:= 0.98 x 0.89 x 0.90
= 0.78 = 78%
在整堂课的教学中,刘教师总是让学 生带着 问题来 学习, 而问题 的设置 具有一 定的梯 度,由 浅入深 ,所提 出的问 题也很 明确
INV---Inventory 目前库存数
精益生产衡量指标知识

精益生产衡量指标的相关知识精益生产之七个“零”的目标﹕零不良零库存零切换零停滞零故障零伤害零浪费用于业绩度量的三大类指标:基于合格/不合格(计数型数据)的FTY/RTY度量指标;基于缺陷数据(计点型数据)的DPU/DPMO度量指标;基于平均值/标准差(连续型数据)的Z(西格玛水平)。
它们基本覆盖了对产品、服务、商务、管理等所有类型过程的度量。
FPY:First Pass Yield定义为:一次通过率。
(FPY是第一次通过率,一般针对一个工位)(与FTY是一个意思)FTY First Time Yield 首次通过率,就是一次通过检验的合格率,就是第一次就把事情做对,由没有经返工返修就通过的过程输出单位数而计算出的合格率。
生产过程投产1000个单位,第一个子过程产生废品40个单位,返工40个单位,即第一个子过程只有920个单位一次合格。
得到FTY=92%.FTT:First Time Throghut,指首次通过率是指一次性完成一个生产过程并且满足质量要求的零件的百分率,不包括报废,返工,再测试,下线修理或返回。
FTT 用于衡量制造过程的质量。
PFY(process final yield)定义为:最终合格率。
就是过程的最后合格率(不区分是否经过返工)过程最终的合格率通常是指通过检验的合格单位数占过程投产全部单位数的比例。
但是这种质量计算方法不能计算该过程的输出在通过最终检验前发生的返工、返修的损失.(也就是说:将返工后合格的产品也算进合格品率里面去了。
):RTY:Rolled Throughput Yield 当然是全过程通过率了(直通率)。
对一个串行生产过程,假定各过程彼此独立,则其流通合格率等于每个子过程FTY的乘积,表明由这些子过程串联构成的大过程的一次合格率。
一次交验合格率就只看一个环节,而直通率应该把前面环节都考虑。
比如说:一个产品有三个工序来完成,各个环节的合格率都是90%,那么交验合格率应该是90%,而直通率应该是90%*90%*90%=72.9%一般来说交验合格率是指最后一个环节。
《精益生产》PPT课件

• 工作强度和工作时间不变,通 过消除不增值的浪费。
精选课件ppt
20
整体效率比个体效率重要
• 整体:全公司、全厂、全车间、全班组。 • 个体:个人、班组、车间。 • 整体效益的提高:组织方式、市场预测、
完善计划,顺畅的物流和信息流等。各级 领导的重视、有效沟通、有力实施。 • 个体效益提高:个体是相对的,通过洗脑、 用脑和改习惯等消除浪费。
1. 对质量的误解 2. 以防万一的逻辑 3. 控制缺陷 4. 过于形式化 5. 缺乏沟通 6. 信息流混乱
精选课件ppt
14
库存浪费
任何超过客户按时所要求的必要的产品的供应
1. 跟踪系统复杂 2. 额外仓储及搬运 3. 多余货物的管理 4. 信息流误导 5. 中间体的管理 6. 过期物料的检验 7. 退货或不合格 8. 效期的约束
销售----成品库----包装----半成品----配料----原辅料库----管理部门。
如果各企业能够关注库存,分析库存,用数据表达库存占用的资 金和资金所发生的利息以及由于库存所造成的损失,那么企业的负责 人一定会发出惊叹“浪费太大”。
李选民
精选课件ppt
18
浪费对员工的影响
• 导致身体疲劳 • 导致精神疲劳 • 增加沮丧泄气 • 增加工作压力 • 导致责备他人 • 浪费你的时间
精选课件ppt
了多长时间。
• 市场有效信息。 • 确定每个产品的安全库存。(最初值) • 偏差分析,向实际靠拢。
精选课件ppt
27
均衡生产的优点
• 市场响应更快 • 有效降低库存 • 缩短制造周期 • 供应链平稳
精选课件ppt
28
均衡生产
• 适用于价值链相对稳定的产品。 • 多品种,多批量。 • 确定经济批量。符合现有设施、设备、人员和GMP要求的最
精益生产主要衡量指标(建议收藏)

精益生产主要衡量指标(建议收藏)
运营:彭阳老师(专注薪酬绩效、股权、合伙人的实践与落地)什么是精益生产:
生产方式发展历史
精益生产定义:
精益生产(lean production )是美国麻省理工学院数位国际汽车计划组织(IMPV)的专家对日本“丰田生产方式”的赞誉之称。
精:即少而精,不投入多余的生产要素,只在适当的时间生产必要数量的市场急需品(或下道工序急需产品)
益:即所有的经营活动都需要有益有效,具有经济性
精益生产是当前工业界公认最佳的一种生产系统。
精益生产报告ppt课件
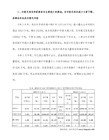
2:彩色,白色,透 明原料使AS原料开 机
3:白色大机台开机 打油使用白色次料 ,抽粒料
责任人(日期) 常鑫(1/15)
11
小工单的原因分析及改善对策
问题
原因
对策
责任人(日期)
机台及辅助设备 调度紧张(20.6%)
人力不足 (11%)
客户需求点集中
辅助设备不足或 损坏(如机械手模 温机)
孙福兰(1/15) 余倩(1/15)
12
小工单合并生产改善状况(2/15-3/15)
业务需求工单 81笔
合并工单 26笔
节省换模 损耗原料
159kg
节省原料 金额
2716RMB
节省换模损 耗工时金额 10260RMB
A:50T-160T小机台,每次换模损耗原料3kg 人工:2人/2H/30元/H B:180T-320T中型机台,每次换模损耗原料5kg 人工:2人/2H/30元/H C:420T-650T大型机台,每次换模损耗原料10kg 人工:2人/2H/30元/H
3
Leader NIU YF
王大芬 可行性评估
4
课题项目 1:库存周转天数
重要 紧泊 可行 效益 综合
性性
性
性 得分
24 18 13
15 70
是否 選用
不选
2:成型小工单与开机料
损耗管控
25Байду номын сангаас26 24
23 98
選取
3:成型前三大使用原料
的替代原料导入
24 25 22
20 91
不选
表中:每个方面的考虑区间设为1-5分,由所有圈员参与打分,最後综合后得分排序
《精益生产》课件

航空制造业
航空制造业采用精益生产方法, 通过优化生产流程和提高工厂效 率,实现生产能力的提升和交付 时间的缩短。
结论
精益生产的优势和不足
精益生产的优势包括提高效率、降低成本和改善质量,但也存在实施难度、需求变化风险等 不足之处。
3
5S
5S是一种创建清洁、整齐、有序和高效工作环境的方法,以促进工作效率和员工安全。
4
Kaizen
Kaizen是一种通过小步骤持续改进的方法,以实现生产过程的不断优化和卓越。
精益生产的应用
汽车制造业
汽车制造业采用精益生产方法, 通过优化生产流程和提高质量, 实现生产效率的提升和成本的降 低。
电子制造业《精益生产》Fra bibliotekPT课件"精益生产"是一种致力于最大限度减少浪费和提高效率的制造管理方法。本 课件将介绍精益生产的概念、核心工具和应用,并分享汽车制造、电子制造 和航空制造等领域的成功案例。
简介
什么是精益生产?
精益生产是一种致力于通过 减少浪费、提高效率和优化 流程来提高生产和运营绩效 的管理方法。
精益生产的未来发展趋势
随着技术的发展和市场的变化,精益生产将更加注重数字化、智能化和可持续发展。
如何应用精益生产提高企业生产效率?
企业可以通过培训员工、优化流程和引入先进技术来应用精益生产,以提高生产效率和竞争 力。
精益生产的主要特点
精益生产的主要特点包括价 值流导向、一次制品流动、 持续改善和员工参与。
精益生产的重要性
精益生产可以帮助企业提高 质量、降低成本、提升交付 速度,并增强市场竞争力。
精益生产的核心工具
精益生产(完美版)(PPT109页)
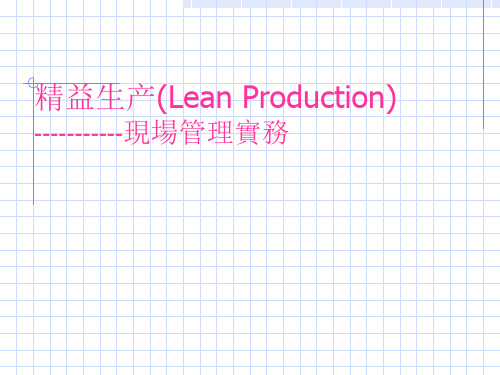
(3)消除浪费——管理的重要目的之一
Management
创造性的管理活动 提高产品和服务的附加价值
+1 增加价值
0
-1
消除浪费
最大限度地减少不增值劳动 封闭性的管理活动
精益思维(Lean Thinking)的5个基本原则
No.1 从顾客的角度而不是从某个公司、部门或机构 的角度确定价值;
No.2 确定设计、采购和生产产品的整个价值流中的 步骤,找出不增加价例 能力需求:100件/H
项目 能力 达成率 奖金 效率
工序1 100件/H
100% 标准产量奖金 个别效率合格
工序2 125件/H
125% 125%奖金 个别效率高
工序3 80件/H
80% 0
个别效率低
工序4 100件/H
80% 0
个别效率低
≠ 个别效率
整体效率
专业化作业有利于提高个别效率,不少企 业因此实行计件工资。
精益生产(Lean Production)
-----------現場管理實務
第一部分 精益生产簡介
很多精益技术源于日本企业的生产管理方法, 如看 板管理、全面质量管理(TQM)、快速换模等技术 都是 在丰田等日本公司的生产管理(NPS)中产生的。美国 的丹尼尔·琼斯教授等人通过大量细致的研究,并与 当 时欧美大量生产方式相比较后得出结论,正是这 些生 产管理方式使得日本企业(如丰田汽车公司)迅速成为 世界级的公司。这些管理思想和原则就是精益生产。
· 三不主义
77个个““零””目目标标 不良
保证
不良率高企, 批量事故多发, 忙于“救火”
· 零缺陷运动 · 工作质量 · 全员质量改善活动 · 自主研究活动 · 质量改善工具运用
《衡量指标》课件

利润率
详细描述利润率的计算方 法、影响因素和意义。
股东回报率
详细描述股东回报率的计 算方法、影响因素和意义 。
非财务指标
市场占有率
详细描述市场占有率的计 算方法、影响因素和意义 。
客户满意度
详细描述客户满意度的调 查方法、影响因素和意义 。
员工满意度
详细描述员工满意度的调 查方法、影响因素和意义 。
03
如何选择合适的衡量指标
与企业战略目标一致
01
确保衡量指标与企业长期战略目 标保持一致,能够反映企业战略 发展方向和重点。
02
避免选择过于短期或与战略目标 不相关的衡量指标,以确保指标 的有效性和指导性。
可操作性和可度量性
选择具体、可度量、可实现、相关和 有时限的衡量指标,确保指标具有可 操作性和可度量性。
THANKS
感谢观看
案例分析
案例一:某电商公司的KPI指标
01
02
03
04
销售收入
衡量公司整体销售业绩,反映 市场需求和产品竞争力。
客户满意度
通过调查问卷、在线评价等方 式了解客户对产品和服务的满
意度。
退货率
反映客户对产品和服务的认可 程度,以及公司的质量控制水
平。
员工流失率
反映公司内部管理和员工福利 情况,影响团队稳定性和工作
详细描述
通过设定合理的衡量指标,如销售额、生产效率、客户满意度等,对员工或组 织的业绩进行客观、公正的评价。这有助于识别优秀表现,激励员工继续努力 ,同时发现不足之处,为改进提供方向。
决策支持
总结词
衡量指标为决策者提供数据支持,帮助其做出更加科学、合理的决策。
详细描述
《精益生产》PPT课件
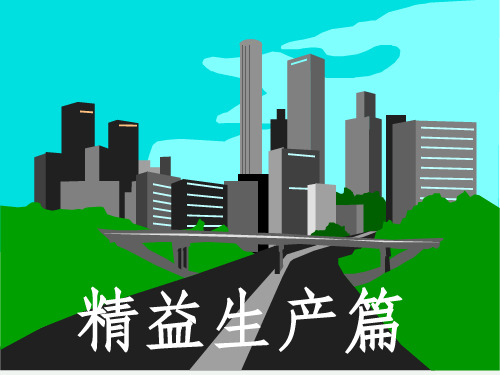
设备现场管理应用
在精益生产方式中,设备故障被视为无效劳动和浪费, 提出设备故障要向零进军,这就要求设备运行过程尽量 不发生故障,少发生故障。
实行全员维修和保养; 实行针对性预防检修; 实行改善性维修;
精益生产系统的五项原则
质量是 制造出来的
标准化
精益的 制造系统
持续改进
员工参与
短的制造周期
拉动式方法的特点:
坚持一切以后道工序需求出发,宁肯中断生产,也不搞超前超
1 量生产。拉动式生产的核心就是准时化,就是要求在需要的事
后,生产需要的产品和需要的数量,所以又把它称为准时化生 产(Just In Time)。
生产指令不仅仅是生产作业计划,而且还用看板进行为调节。
2 看板成为实施拉动式生产的重要手段。
看板来源于大野耐一从美国超级市场的启示。
拉动式方法 在生产制造过程中的具体运用
1 以市场需求拉动企业生产。
在企业内部,以后道工序拉动前道工序生产,以总装配拉动总
2 成装配,以总成装配拉动零件加工,以零件拉毛坯生产,用以
大幅度压缩在制品储备,消除无效劳动。
U型平面布置的“一个流”生产线; 多工序管理和多机床操作 成批轮番作业的生产线 快速换模技术,实现小批量多批次生产
jit以小批量生产为准则换模工作必须尽快完成消除浪费的方设计流程连接操作平衡工作站能力减小批量规减少安装换模时间2tqm全面质量管理尊重员工qcc小组合理化建议3稳定计划均衡计划不超过生产能力建立冻结区间指计划固定不弯一个时间区段4看板控制由后向前传送指令5与供应商紧密合作缩短提前期增加供货频率交货要及时保证质量可靠性6减少额外存货寻找其他区采用传送带运输机7改进产品设计产品标准化零件标准化及零件数减少改进过程设计产品质量期望jit七个前提条件61传统生产管理中的生产指令生产计划实际生产数量生产顺序表库存工序a工序b工序c库存完成生产指令计划生产数量与实际生产数量不同生产指令生产指令62jit生产计划实际生产数量生产顺序表看板工序a工序b工序c看板完成生产指令计划生产数量与实际生产数量相同63确定看板数量每个容器内数量64防止过量生产生产没有看板不能生产也不能运送目视管理看板必须附在实物上按照取下看板的顺序进行生产改善工具不能把不良品送往下一工序看板机能生产及运送的工作指令65生产系统
精益生产ppt优质版(89张)
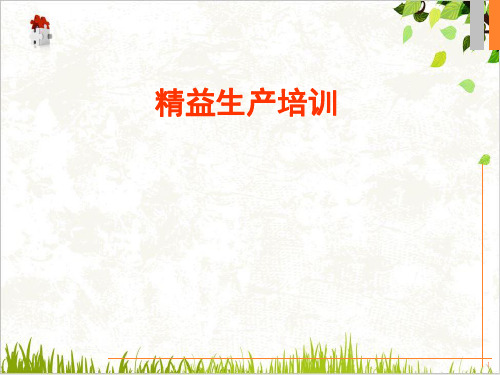
消除浪费 消除浪费 消除浪费
没有浪费
浪 费
浪
浪
费
费
目 标
精
益
成
本
企业不断地强化自己的生产过程,随时消除生产过程中的 浪费,力求使生产过程中所用的资源绝对最少,从而使整个生 产看起来很“精”,但又能达到很“益”的结果。
16
二、认识浪费
1. 浪费等于在“烧钱” 2. 制造现场的八大浪费 3. 价值流图与分析方法 4. 价值流图绘制练习
焊接
自动
设备
组装1 组装2
检测
包装
1臂间距
极少数自动设备
多数手工作业 面向生产线
2H工位轮换 (多技能)
自主质量改进
28
三、精益生产方式
3.2 单件流
何谓“一个流”?
也叫“单件流”。是指从材料投入到成品产出的整个生 产过程,零件始终处于不停滞、不堆积、不贮存,按节拍 “一个一个”地流动下去的生产方法。
概念一:
Lean Production
简称LP
精益 ·生产
上世纪80年代,美国麻省理工学院数位国际汽车计划组 (IMVP)的专家对以日本丰田公司为代表的汽车制造商进 行了为期十年的调查,发现日本汽车企业在生产管理方面 有许多独到的生产方式,正是这些生产方式的实施,使日 本汽车企业能通过低成本、高品质占领国际汽车市场,将 这些生产方式进行总结,并称之为“Lean Production , 简称LP”。
77、好朋友的定D-义交是:付你、混得反好应,他速为度你高兴;你混最得柔不好性,交他为货你着急。
“零”故障
(造7)名营医销专自家己,的通D人e过才l学i。v习在i交r患y流者、就走诊进的社问区题、上对,口很支多援人、相专信家名讲医座专等家形,式有,时把为自能己够的找专知家名学专者家给宁“推可出零舍去近”,求得停远到。滞社因会此认我可们,必营须销在好医自院己重的点人打
精益生产衡量指标价值流分析

浪费消除策略
识别浪费:通过价值流分析识别出浪费环节 消除浪费:制定针对性的消除策略,减少浪费 持续改进:不断优化生产流程,提高生产效率 培训员工:提高员工对浪费的认识和消除能力
浪费消除实施步骤
识别浪费:通过价值流分析,找出生产过程中的浪费环节 制定消除计划:针对识别出的浪费,制定具体的消除计划 实施消除:按照计划,逐步消除浪费环节 监控与改进:对消除过程进行监控,确保消除效果,并持续改进生产流程
浪费识别与消除方法介绍
浪费消除效果评估
浪费消除效果评估方法
添加标题
添加标题
浪费消除效果评估指标
添加标题
添加标题
浪费消除效果评估实践案例
质量指标定义与测量
质量指标定义:明确质量指标的概念和意义,包括产品合格率、客户满意度等
质量指标测量方法:介绍常用的质量指标测量方法,如统计过程控制、关键绩效 指标等
精益生产目标
消除浪费:通过消除生产过程中的浪费,提高生产效率和降低成本 持续改进:通过不断改进生产流程和管理方式,提高产品质量和客户满意度 快速响应:通过快速响应市场需求和变化,提高企业竞争力和市场份额 创造价值:通过创造更多的价值,提高企业盈利能力和可持续发展能力
价值流图分析
价值流图的概念 和作用
价值流图绘制
定义价值流图:一种用于描述产品从原材料到最终客户整个过程的价值流动的图表
绘制价值流图的目的:识别浪费和不增值的活动,提高生产效率和质量
绘制价值流图的步骤:确定产品族、定义增值活动和非增值活动、绘制价值流图、分析价值流图中的浪费
绘制价值流图的工具:笔、纸、时间记录表等
价值流图解读
价值流图定义: 描述产品从原 材料到成品, 包括各个工序
持续改进:根据评估结果和反馈意见,持续改进质量指标和生产过程,不断提高产品质量和生产效率
精益生产五大指标ppt课件

1-2消费线速率/节拍时间(TAKT)
Takt 节拍时间 =
可用任务时间
客户需求数量
Takt节拍时间 = (60 X 任务小时/天) - 休憩 & 午餐& 其它停顿时间
每天客户需求数量
例子:
节拍时间 = (60 x 17.0) - ((15+15+30+20)x2) = 258 件
1-1、节拍时间(TAKT)
TAKT Time determines the rate at which work must be accomplished at each operation (Operational Cycle Time) based on the line rate.
节拍时间确定了每一工位必需完成任务的速率〔 操作周期时间〕
TYPE 1 NON VALUE 10.0 10.0
TYPE 2 NON VALUE 5.0 5.0
WAIT FOR CYCLE
15.0
10.0
SECONDS / PIECE
OPERATOR TOTAL 41.0 39.0 34.0 35.0 0.0
TAKT 36.2 36.2 36.2 36.2 36.2
43+38+36+45+35 操作工数量 =
消费线节拍时间(40S)
2、FTT初次经过率
定义:指一次性完成一个消费过程并且满足质量要求的零件的百分率, 包括报废、返工、再测试、剖检和下线修缮或前往数。 初次经过率FTT%=每道工序的合格率数值相乘。
4、桑塔纳燃油箱FTT%案例 工序: 1〕挤吹成型——2〕冷却定型——3〕打孔焊接——4〕装配— —5〕水下测漏/电性能——6〕装配2
精益生产(完美版)ppt课件
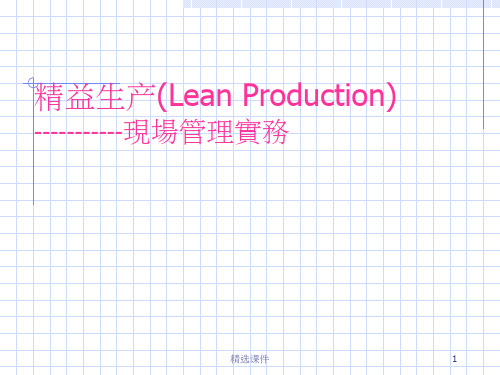
生产安定化
标准作业
非标准作业
线上操作者负责 线外“水蜘蛛”负责
对“水蜘蛛”来说 是标准作业
全体标准作业
精选课件
41
(2)产距时间 ——生产的指挥棒
考虑信息流动—— 生产指示明确
流畅
便于信息传递
☆ 后补式/前后式生产指示 ☆ 生产实绩显现化 ☆ 便于批量区分
④.少人化生产—— 人多人少都能生产
☆ 警示灯及线体控制
☆ U形布置方式
☆ 逆时针摆放 ☆ 设备间无阻隔 ☆人与设备分工:
少人 化
人—装料、卸料
设备—加工
☆启动按钮安装方式适当
精选课件
32
⑤. 质量
精选课件
8
(3)消除浪费——管理的重要目的之一
Management
创造性的管理活动 提高产品和服务的附加价值
+1 增加价值
0
-1
消除浪费
最大限度地减少不增值劳动 封闭性的管理活动
精选课件
9
精益思维(Lean Thinking)的5个基本原则
No.1 从顾客的角度而不是从某个公司、部门或机构 的角度确定价值;
37
Step3 将长屋型改为大通铺式
大 通 铺 式 布 置
Hale Waihona Puke 精选课件38Step4 整体上呈一笔画布置
一 笔 画 布 置
精选课件
39
STEP2 安定化生产
人员安定化管理
安定化 生产
设备安定化管理 质量安定化管理 切换安定化管理
现场安定化管理
精选课件
40
1、人员安定化管理
(1)标准作业与非标准作业
精选课件
27
精选精益生产的衡量指标课件
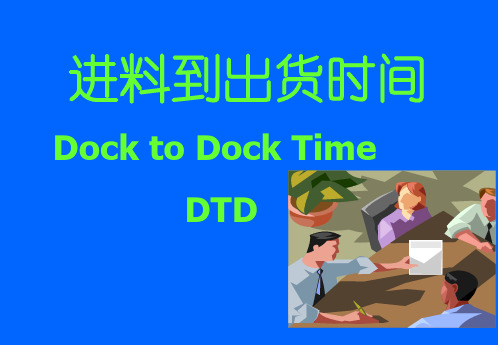
衡量指标 DTD
*何处 where :1.原物料 - 购买的零件(管制部品)接收进入工厂开始计数.运委托制件.因为已经产品構成. raw material-purchase part (control part) – begin counting when it is received in the plant .Even on consignment. Because it is already in its product from already in its product form..原物料变更成为产品构成 Raw material that is changed its product form
進料倉庫
成品倉庫
進料倉庫到出貨倉庫時間 (DTD)
製造週期時間(MCT)
生產製造過程
衡量指標(DTD)
衡量指标-DTD
DTD – 從进料仓库到出貨仓库間时间 指原料進廠製成完成品準備出貨的時間 包含製造週期時間DTD - 是衡量(时数)物料通过工厂的 速度,不是程序的速度 DTD is measure (in hours) of the speed of material through the plant, not the speed of the process.
进料到出货时间 Dock to Dock Time DTD
Dock to Dock Time (DTD)
*Definition 定义 .从原物料下货到完成成品出货之间的过去时间 the elapsed time between the unloading of raw materials and the release of finished goods for shipment .总DTD时间为产品耗费时间如原物料,制程作业,与 在厂完成品出货前在品的时间 the total dock to dock time for a product includes the time that a product spends as raw material, work-in process and as a finished product in plant, prior to being relaesed.
《精益生产完整》课件

人工智能还可以通过智能控制和优化算法等技术,对生产过程进行实时 监控和调整,提高生产过程的稳定性和效率。
绿色精益生产
绿色精益生产是指将环保理念融入生产 过程中,通过改进和优化生产过程,减 少对环境的负面影响。
精益生产的重要性
01
提高生产效率和产 品质量
通过消除浪费和优化流程,精益 生产能够显著提高生产效率和产 品质量。
降低成本
02
03
增强企业竞争力
通过减少浪费和优化库存,精益 生产能够降低生产成本和运营成 本。
精益生产能够帮助企业提高效率 和效益,从而在激烈的市场竞争 中获得竞争优势。
精益生产的历史与发展
总结词:精细管理
详细描述:某物流企业通过精益化运营实践,实现了对运输、仓储和配送等环节的精细化管理。通过 消除浪费、提高运输效率、优化仓储布局和配送路线,该企业成功降低了运营成本,提高了客户满意 度。同时,精益化运营还促进了企业内部的沟通与协作,增强了团队凝聚力。
THANK YOU
01
人才缺乏
中国在精益生产方面的专业人才相对较 少,这可能会影响精益生产的推广和应 用。
02
03
制度环境
中国的制度环境可能对精益生产的推 广和应用产生影响,例如法律法规、 政策等。
05
精益生产的未来发展
数字化精益生产
01
数字化精益生产是指利用数字化技术对生产过程进行优化和改进,以提高生产 效率和产品质量。
素养
培养员工遵守规章制度、注重 细节、积极主动的良好习惯, 提高整体素质。
快速换模
《精益生产》PPT课件

编辑ppt
持续改善
持续改善方法指逐渐、连续地增加改善。是日本持续改进之父今井正明在 《改善—日本企业成功的关键》一书中提出的,Kaizen意味着改进,涉及 每一个人、每一环节的连续不断的改进:从最高的管理部门、管理 人员到工人。持续改善的策略是日本管理部门中最重要的理念,是日本人 竞争成功的关键
自我反省和现地现物16改善原则取消合并重排简化17制造业经常面临的问题产能不够无法满足市场需求不能按时按量交货人员效率低下库存太高积压资金质量无法满足客户要求生产成本太高问题重复发生每日忙于救火研发能力不够量产时浮现大量问题供应商无法准时保质保量交货以上这些问题的解决之道精益生产
编辑ppt
1
主讲人:朱宝
15
编辑ppt
十二原则
1:消除八大浪费:过量生产、等待时间、运输、库存、过程(工序)、动 作、产品缺陷以及忽视员工创造力。 2:关注流程,提高总体效益 3:建立无间断流程以快速应变 4:降低库存 5:全过程的高质量,一次做对 6:基于顾客需求的拉动生产 7:标准化与工作创新 8:尊重员工,给员工授权 9:团队工作 10:满足顾客需要 11:精益供应链 12:"自我反省"和"现地现物”
16
改善原则
取消
编辑ppt
简化
合并
重排
17
编辑ppt
制造业经常面临的问题
➢产能不够无法满足市场需求 ➢不能按时按量交货 ➢人员效率低下 ➢库存太高,积压资金 ➢质量无法满足客户要求 ➢生产成本太高 ➢问题重复发生,每日忙于救火 ➢研发能力不够,量产时浮现大量问题 ➢供应商无法准时保质保量交货 以上这些问题的解决之道——精益生产:
4
质量、低消耗进行生产的方式在实践中摸索、创造出来了。
精益生产衡量指标计算方法

10 精选课件
良品率
良品率=合格数/总生产数
11 精选课件
Build to Schedule (BTS) 按计划制造
BTS是指在指定的生产日按照正确的生产顺序完 成生产计划的比例情况。BTS 反映了工厂能够按 照客户的要求完成生产的能力,客户需何种产品,何 时需要和客户使用产品的顺序。
顺序性能Sequence%用于测量在适当的生产日 按照正确的生产顺序完成生产任务的比率
Sequence%=按计划顺序生产品种数/计划生产品 种数;
13 精选课件
感谢亲观看此幻灯片,此课件部分内容来源于网络, 如有侵权请及时联系我们删除,谢谢配合!
100-10 (補修+報廢) /100 = .90 一次合格產出
E 100 6
B 報廢
10 W
90
C 報廢 O 9
3
R 87
5
報廢 K D 2
100-16 (補修+報廢) /100 = .84 一次合格產出 90-12 (補修+報廢) /90 = .86 一次合格產出 87-7 (補修+報廢) /87 = .91 一次合格產出
设备可用时间=(设备计划运行时间-固定 的休息/停机时间)设备实际作业时间=每天 设备实际工作时间之和 举例:甲班全天出勤时间为8小时,中途休息时 间为20分钟,设备故障停机修理时间为40分钟 设备稼动率=(8x60-20-40)/(8x60-20)
9 精选课件
作业效率
作业效率=实际产量/标准理论产量; 或作业效率=总标准工时/总实际工时; 举例:设备M-01某天生产N-1产品,设备实
- 1、下载文档前请自行甄别文档内容的完整性,平台不提供额外的编辑、内容补充、找答案等附加服务。
- 2、"仅部分预览"的文档,不可在线预览部分如存在完整性等问题,可反馈申请退款(可完整预览的文档不适用该条件!)。
- 3、如文档侵犯您的权益,请联系客服反馈,我们会尽快为您处理(人工客服工作时间:9:00-18:30)。
87/90 = .97
= 85%
85/87 = .98
產出=沒被報廢的部品
結束: 85件 “好” 的產出
7
精實(Lean)衡量指標
首次合格率
隱藏 因素
開始 : 100 units
R A 10
100-10 (補修+報廢) /100 = .90 一次合格產出
報廢品
E 100 6
2
精益生产的7个零极限目标
零切换; 零库存; 零浪费; 零不良; 零故障; 零停滞; 零灾害;
3
精益生产(Lean Manufacturing)
以消除浪費來縮短顧客之等候時間
Business as Usual
顧客訂單
Waste
貨品送達
Lean Manufacturing
顧客訂單
時間
6.7天
3.43天
C/T=3.52分 編制人數=1人 OEE=81.1% C/O=62.8分 品種=11種 FTT= %
C/T=3.75分
C/T=7.8分
編制人數=3人
編制人數=2人
OEE=75.2.3%
OEE=73.3%
C/O=40.7分
C/O=20.4分
品種=7種
品種=4種
FTT= %
3.65天
B 報廢
10 W
100-16 (補修+報廢) /100 = .84 一次合格產出
90
報廢
O9 C
90-12 (補修+報廢) /90 = .86 一次合格產出
3
R 87
5
報廢 K 2
D 87-7 (補修+報廢) /87 = .91 一次合格產出
首次合格率是根據每一工作站一次就把
工作做好的比率: .90 × .84 × .86 × .91 =
FORD精益生产体系 的衡量指标
(Lean Manufacturing)
1
精益生产的思想
只在需要的时候,按需要的量,生产需要的
产品; A Quality product or service, in the right amount at exactly the right time, based on the customer requirements….. Using the minimum of resources
MRP 系統
訂單
看板交貨
FLH
月需求量= 1878台
月計劃
日需求量= 82台
月/1趟 趟/2000台
進料 倉庫
2F
焊接 I 焊接
I
3日間交貨
天/1趟 趟/90台 混載
出貨 倉庫
裁鈑
油壓組立 油壓組立
組立封裝
總成焊接
I
I
I
I
I
I
I
550台
282台
300台
452台 96台
122台
•
C/T=0.18分 編制人數=1人 OEE=73.7% C/O=20分 品種=77種 FTT= %
BTS% = Volume% X Mix% X Sequence% BTS% = 数量完成率X 品种完成率 X 顺序完成率
18
BTS计算方法
15
精實(Lean)衡量指標
總和設備效率(OEE)
100% 85%
80% 機會 70%
$$$ 60% 55%
40%
20%
0% 現況
目標 延伸目標
$$$ OEE - 停機時間 – 主要 & 次要 - 週期時間 - 良品率 - 多餘產能
16
OEE的统计分析
OEE %
OEE (Constraint)
100
結束: 85件 “好” 的產出
59%
8
(Lean)衡量指標
仓库进料到仓库出货时间 (DTD)
• 類似於財務管理上的庫存週轉 天數, 低的DTD 天數表示順暢 的物流及現金流量愈低
9
精實(Lean)衡量指標
進料倉庫到出貨倉庫時間(DTD) 進料倉庫到出貨倉庫時間是指原料進廠至完成品 準備出貨之間所經過的時間。
• 每單位可視情況自行調整, 作为 改善的依據; 但必須前後一致.
• 為什麼要這麼定義 ? 改善的基礎,同業的標竿, 競爭優勢 的檢討
6
傳統產出的計算方式
開始 : 100 units
報廢品
A
100
B 報廢
10 90
C 報廢 3 87
D 報廢 2
100/100 = 1
產出的結果是什麼 ?
90/100 = .9
设备稼动率
稼动率=设备实际作业时间/可用时间 可用时间:指设备可以利用的时间,
设备可用时间=规定出勤时间-固定的休息/ 停机时间 设备实际作业时间=设备实际工作时间-休息时 间-设备故障时间
举例:甲班全天出勤时间为8小时,中途休息时间 为20分钟,设备故障停机修理时间为40分钟 设备稼动率=(8x60-20-40)/(8x60-20)
FTT=99.9%
6.7天
11 1.49天
精實(Lean)衡量指標 设备总效率OEE
OEE =
稼動率 x 性能(作業)效率 x 良品率 對象: 瓶頸工程/產能較不足之工程
• 換模換線 稼動率 時間
• 非預期故 障時間
性能效率 • 作業紀律
• 小的作業 等待或中 止
良品率 • 生產總數
• 良品數
• 不良12品數
5/9/96 ODEatEe
UCL X
LCL
原物料
原物料
LEAK
在製品 (DTD)
成品
10
ቤተ መጻሕፍቲ ባይዱ
■ C206- ******製造流程
協力廠
1 個月
訂單
DTD=22天 MCT=13.8天(11人) pcs C/T=15.25分
完整價值流現況圖(3. 07. 2002) 1 + (6) 個月
生管
1 + (7) 日 預示量
66 75 81 86 83 50 48
0
1
2
3
4
5
6
Month
17
Build to Schedule (BTS) 按计划制造
BTS是指在指定的生产日按照正确的生产顺序完 成生产计划的比例情况。BTS 反映了工厂能够按 照客户的要求完成生产的能力,客户需何种产品,何 时需要和客户使用产品的顺序。
Waste
貨品送達
時間〈縮短〉 4
精益生产(Lean)的衡量指标
•首次合格率
(FTT)
•仓库进货到仓库出货時間 (DTD)
•按计划制造
(BTS)
•设备总效率
(OEE)
5
精實(Lean)衡量指標 首次合格率FTT
• 如何定義首次合格率 ? 嚴格的來說任何報廢, 或經過補 修的部品皆被定義為不良品.
13
作业效率
作业效率=实际产量/标准产量; 或作业效率=总标准工时/总实际工时; 举例:设备M-01某天生产N-1产品,设备实
际工作时间为7.5小时,出勤时间为8小时, 该产品标准工时为5min/pcs,当天实际产 量为80pcs,该设备当天的作业效率是多 少?
14
良品率
良品率=合格数/总生产数