丰田-精实管理理念
丰田管理的精髓是什么
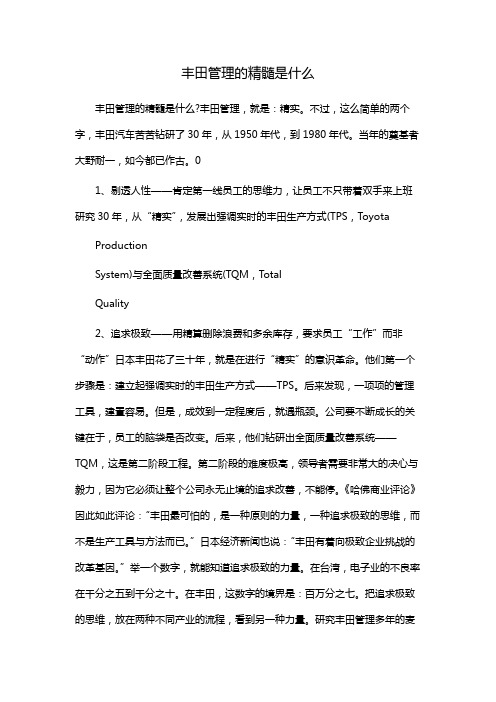
丰田管理的精髓是什么丰田管理的精髓是什么?丰田管理,就是:精实。
不过,这么简单的两个字,丰田汽车苦苦钻研了30年,从1950年代,到1980年代。
当年的奠基者大野耐一,如今都已作古。
01、剔透人性——肯定第一线员工的思维力,让员工不只带着双手来上班研究30年,从“精实”,发展出强调实时的丰田生产方式(TPS,Toyota ProductionSystem)与全面质量改善系统(TQM,TotalQuality2、追求极致——用精算删除浪费和多余库存,要求员工“工作”而非“动作”日本丰田花了三十年,就是在进行“精实”的意识革命。
他们第一个步骤是:建立起强调实时的丰田生产方式——TPS。
后来发现,一项项的管理工具,建置容易。
但是,成效到一定程度后,就遇瓶颈。
公司要不断成长的关键在于,员工的脑袋是否改变。
后来,他们钻研出全面质量改善系统——TQM,这是第二阶段工程。
第二阶段的难度极高,领导者需要非常大的决心与毅力,因为它必须让整个公司永无止境的追求改善,不能停。
《哈佛商业评论》因此如此评论:“丰田最可怕的,是一种原则的力量,一种追求极致的思维,而不是生产工具与方法而已。
”日本经济新闻也说:“丰田有着向极致企业挑战的改革基因。
”举一个数字,就能知道追求极致的力量。
在台湾,电子业的不良率在千分之五到千分之十。
在丰田,这数字的境界是:百万分之七。
把追求极致的思维,放在两种不同产业的流程,看到另一种力量。
研究丰田管理多年的麦肯锡董事柯睿明,比较丰田汽车制造流程和信用卡发卡流程。
在组件方面,汽车有30000个零件,而信用卡公司处理的消费者申请数据只有50项;在往来对象的复杂度上,车厂必须与450家企业往来零件,而信用卡公司的上下游往来只有两端(消费者、银行);虽然面对更复杂的组件与往来对象,但丰田制造一部车需要不到100个员工,但是信用卡却需要150个人。
在时间上,丰田10小时能做好一辆车,但信用卡发卡却需要4到6天。
基于丰田生产方式的4S思想概述

基于丰田生产方式的4S思想概述丰田生产方式(Toyota Production System,简称TPS)是丰田汽车公司独创的一种生产方式,也被广泛应用于全球汽车制造业和其他制造业。
TPS的核心思想是通过消除浪费和追求持续改进,实现高效率、高质量和低成本的生产过程。
丰田生产方式的核心是基于“丰田4S思想”(Toyota 4S Philosophy),这四个S分别代表“精实”(Seiri)、“整理”(Seiton)、“清洁”(Seiso)和“标准化”(Seiketsu)。
这四个S原则是丰田生产方式的基础,旨在创建一个高效、有序和高标准的工作环境。
首先,精实(Seiri)意味着消除浪费。
丰田强调通过分析生产过程并去除没有价值的活动和物品,从而提高生产效率。
例如,他们会减少库存,保持所需物品的适度数量,并通过优化布局和工艺流程来减少工人的移动和等待时间。
其次,整理(Seiton)意味着物品的有序摆放。
丰田主张将物品放置在易于取用和管理的位置,减少浪费的时间和劳动力。
通过标记和定义每个物品的存储位置,可以提高工人的效率和工作质量。
第三,清洁(Seiso)是指保持工作场所的整洁和清洁。
丰田认为一个干净的工作环境对于提高工作效率和工作品质非常重要。
工人被鼓励定期清洁和维护自己的工作区域,以及认真参与整个生产过程中的质量控制。
最后,标准化(Seiketsu)强调在生产过程中建立标准规范。
丰田认为,通过确立规范操作和标准化程序,可以稳定和优化生产过程。
员工使用相同的方法和步骤进行工作,从而提高效率和质量。
通过遵循4S思想,丰田生产方式在全球制造业享有盛誉。
这种生产方式注重消除浪费、优化工艺流程、提高质量和效率,并通过持续改进不断提高生产系统的整体性能。
这种思想的应用已经证明是一种成功的生产方式,可以为企业创建更高的价值和竞争优势。
丰田生产方式的4S思想概述丰田生产方式的核心思想是通过消除浪费、追求持续改进以及优化工艺流程来实现高效率、高质量和低成本的生产过程。
精益生产管理
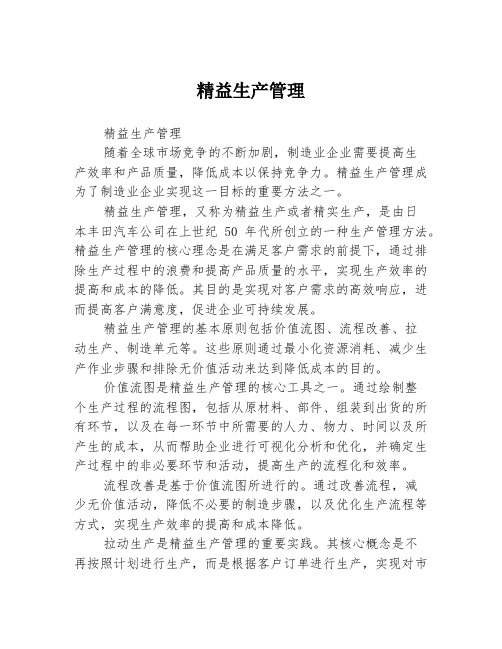
精益生产管理精益生产管理随着全球市场竞争的不断加剧,制造业企业需要提高生产效率和产品质量,降低成本以保持竞争力。
精益生产管理成为了制造业企业实现这一目标的重要方法之一。
精益生产管理,又称为精益生产或者精实生产,是由日本丰田汽车公司在上世纪50年代所创立的一种生产管理方法。
精益生产管理的核心理念是在满足客户需求的前提下,通过排除生产过程中的浪费和提高产品质量的水平,实现生产效率的提高和成本的降低。
其目的是实现对客户需求的高效响应,进而提高客户满意度,促进企业可持续发展。
精益生产管理的基本原则包括价值流图、流程改善、拉动生产、制造单元等。
这些原则通过最小化资源消耗、减少生产作业步骤和排除无价值活动来达到降低成本的目的。
价值流图是精益生产管理的核心工具之一。
通过绘制整个生产过程的流程图,包括从原材料、部件、组装到出货的所有环节,以及在每一环节中所需要的人力、物力、时间以及所产生的成本,从而帮助企业进行可视化分析和优化,并确定生产过程中的非必要环节和活动,提高生产的流程化和效率。
流程改善是基于价值流图所进行的。
通过改善流程,减少无价值活动,降低不必要的制造步骤,以及优化生产流程等方式,实现生产效率的提高和成本降低。
拉动生产是精益生产管理的重要实践。
其核心概念是不再按照计划进行生产,而是根据客户订单进行生产,实现对市场和客户需求的即时响应。
拉动生产模式也是降低生产成本的重要途径之一。
制造单元是将一个产品从输入到输出的全过程拆分为不同的制造单元,每个制造单元都负责实现一个具体的环节,从而获得更高的生产效率和质量控制。
此外,制造单元还可以更好的实现针对客户定制的生产制造。
除了上述基本原则外,精益生产管理也注重强调团队合作、员工参与和持续改进。
通过鼓励员工提出改进方案、解决生产中的问题,提高其对于生产流程的认识和参与度,加强团队精神和创新能力。
精益生产管理在实施过程中也面临一些挑战和难点。
首先,需要对整个流程进行系统的了解并持续改进。
浅谈丰田的企业文化
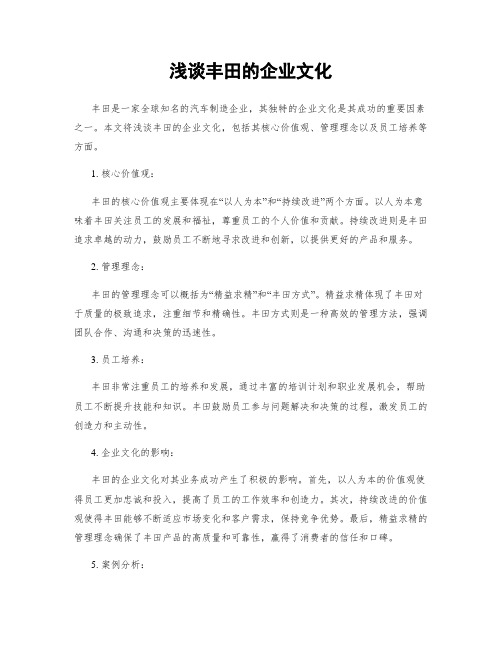
浅谈丰田的企业文化丰田是一家全球知名的汽车制造企业,其独特的企业文化是其成功的重要因素之一。
本文将浅谈丰田的企业文化,包括其核心价值观、管理理念以及员工培养等方面。
1. 核心价值观:丰田的核心价值观主要体现在“以人为本”和“持续改进”两个方面。
以人为本意味着丰田关注员工的发展和福祉,尊重员工的个人价值和贡献。
持续改进则是丰田追求卓越的动力,鼓励员工不断地寻求改进和创新,以提供更好的产品和服务。
2. 管理理念:丰田的管理理念可以概括为“精益求精”和“丰田方式”。
精益求精体现了丰田对于质量的极致追求,注重细节和精确性。
丰田方式则是一种高效的管理方法,强调团队合作、沟通和决策的迅速性。
3. 员工培养:丰田非常注重员工的培养和发展,通过丰富的培训计划和职业发展机会,帮助员工不断提升技能和知识。
丰田鼓励员工参与问题解决和决策的过程,激发员工的创造力和主动性。
4. 企业文化的影响:丰田的企业文化对其业务成功产生了积极的影响。
首先,以人为本的价值观使得员工更加忠诚和投入,提高了员工的工作效率和创造力。
其次,持续改进的价值观使得丰田能够不断适应市场变化和客户需求,保持竞争优势。
最后,精益求精的管理理念确保了丰田产品的高质量和可靠性,赢得了消费者的信任和口碑。
5. 案例分析:以丰田的生产体系为例,其“丰田生产方式”(TPS)是世界闻名的成功案例。
TPS以精益生产为基础,通过减少浪费、提高效率和质量,实现了生产成本的降低和产品质量的提升。
这一生产方式的成功得益于丰田的企业文化,即以人为本、持续改进和精益求精的价值观和管理理念。
总结:丰田的企业文化在其成功中起到了重要的作用。
以人为本和持续改进的核心价值观,精益求精和丰田方式的管理理念,以及员工培养的重视,都为丰田的发展提供了坚实的基础。
丰田的企业文化不仅影响着内部员工的行为和态度,也塑造了丰田的品牌形象和市场竞争力。
谈谈日本丰田的精益管理
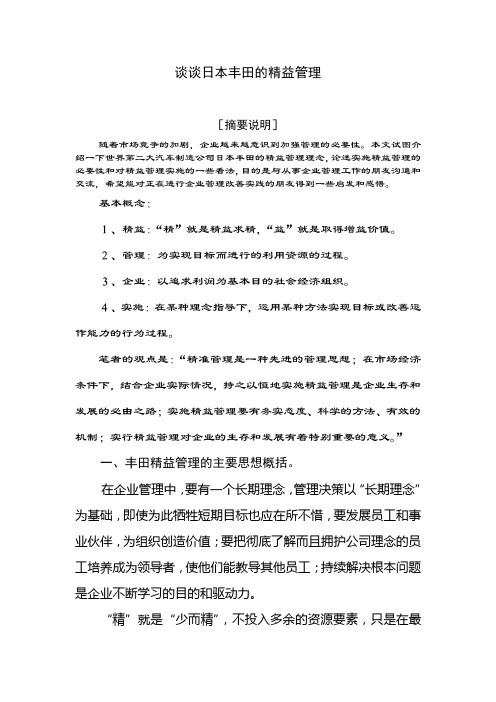
谈谈日本丰田的精益管理[摘要说明]随着市场竞争的加剧,企业越来越意识到加强管理的必要性。
本文试图介绍一下世界第二大汽车制造公司日本丰田的精益管理理念,论述实施精益管理的必要性和对精益管理实施的一些看法,目的是与从事企业管理工作的朋友沟通和交流,希望能对正在进行企业管理改善实践的朋友得到一些启发和感悟。
基本概念:1、精益:“精”就是精益求精,“益”就是取得增益价值。
2、管理:为实现目标而进行的利用资源的过程。
3、企业:以追求利润为基本目的社会经济组织。
4、实施:在某种理念指导下,运用某种方法实现目标或改善运作能力的行为过程。
笔者的观点是:“精准管理是一种先进的管理思想;在市场经济条件下,结合企业实际情况,持之以恒地实施精益管理是企业生存和发展的必由之路;实施精益管理要有务实态度、科学的方法、有效的机制;实行精益管理对企业的生存和发展有着特别重要的意义。
”一、丰田精益管理的主要思想概括。
在企业管理中,要有一个长期理念,管理决策以“长期理念”为基础,即使为此牺牲短期目标也应在所不惜,要发展员工和事业伙伴,为组织创造价值;要把彻底了解而且拥护公司理念的员工培养成为领导者,使他们能教导其他员工;持续解决根本问题是企业不断学习的目的和驱动力。
“精”就是“少而精”,不投入多余的资源要素,只是在最适当的时间生产必要数量的产品;“益”就是所有的活动都要有益有效,具有经济性。
用一句话来说就是用最小的投入按时获得满足顾客的产出,从而赢得企业利润。
精益管理以“最大限度地减少企业所占用的资源和降低企业管理及运营成本”为主要目标,认为管理的关键是过程,包括人事组织管理的优化,大力精简中间管理层,进行组织扁平化改革,减少非直接生产人员,进行均衡化、同步化,实现零库存与柔性生产;推行全过程的质量保证体系,实现零不良;减少和降低任何环节上的资源浪费,最终实现拉动式准时化生产方式,精益求精,尽善尽美,永无止境。
这种思想是支撑职工个人与企业生命的一种精神力量,也是在永无止境的学习过程中获得自我满足的一种境界。
丰田的卓越制造文化精益求精精益求实

丰田的卓越制造文化精益求精精益求实丰田的卓越制造:精益求精,精益求实作为全球知名的汽车制造商,丰田公司以其卓越的制造文化而闻名于世。
丰田一直秉承着精益求精和精益求实的原则,不断追求卓越,致力于提供高品质的产品和优质的服务。
本文将以丰田的制造模式为例,探讨其卓越的制造文化是如何体现精益求精和精益求实的。
一、质量至上丰田公司一直坚守着质量至上的原则,将其视为制造工作的基石。
在丰田的制造流程中,质量控制被渗透到每一个环节。
从原材料的选择、生产设备的运行,到产品的组装和交付,丰田始终追求零缺陷的目标。
丰田致力于确保每一台产品都符合高质量的标准,以满足客户的需求和期望。
二、精益生产丰田的生产模式以精益生产为核心。
精益生产是指通过减少浪费,提高效率和质量,以实现更高水平的生产工作。
丰田通过优化生产流程,减少库存,精确调度和快速交付来达到精益生产的目的。
丰田采用的“Just-In-Time”(精确到时)生产系统,使得生产过程能够高效、流畅地进行,从而节约资源,提高效率。
三、精益改进丰田鼓励员工参与到持续改进的过程中。
丰田的员工被赋予改善产品和工作流程的权力和责任。
他们通过小组活动和不断的改进措施,不断寻找和解决问题,提高生产工作的效率和质量。
精益改进始终贯穿于丰田的制造过程中,使得每个员工都能够参与到持续改进的工作中,并为企业的发展作出贡献。
四、精益供应链管理丰田不仅在自身的生产过程中追求精益,还与供应商建立了紧密的合作关系,共同推进精益供应链管理。
丰田与供应商之间建立了稳定的伙伴关系,通过共享信息、提高沟通和协同工作,实现供应链的高效运作。
通过精益供应链管理,丰田可以更好地掌握物料和信息的流动,从而能够更及时地满足市场需求并降低成本。
丰田的卓越制造文化精益求精和精益求实的体现不仅仅体现在产品的制造过程中,更体现在企业的管理哲学和价值观中。
丰田通过持续不断地改进和精益的实践,不仅提高了自身的制造能力和竞争力,还为整个行业树立了榜样。
丰田模式与精实管理
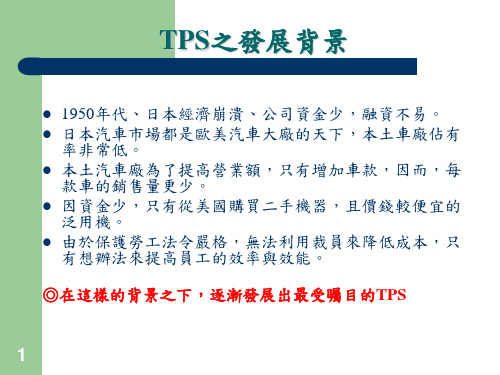
1950年代、日本經濟崩潰、公司資金少,融資不易。 日本汽車市場都是歐美汽車大廠的天下,本土車廠佔有
率非常低。 本土汽車廠為了提高營業額,只有增加車款,因而,每
款車的銷售量更少。 因資金少,只有從美國購買二手機器,且價錢較便宜的
泛用機。 由於保護勞工法令嚴格,無法利用裁員來降低成本,只
有想辦法來提高員工的效率與效能。 ◎在這樣的背景之下,逐漸發展出最受矚目的TPS
1
TPS的基本思維
徹底消除浪費(MUDA) 庫存是罪惡的 製造多餘的物品而賣不出去,等於製造廢棄物 WIP過多,會造成生產線的凌亂 應該努力做到接到訂單後才製造的「接單後生產」 善用公司有限的資源 人的潛力可以不斷的被激發出來
8
庫存的水位
顧 客 抱 怨
庫存水位
製
工
程
進作
品
料效
質
不率
不
庫存水位 良 低
良
9
設
生
備
產 線
故 障
模 具
不
出
平
問
衡
題
改善運作與手法
◎改善手法‧QCC,Six Sigma,G8D
‧改善工具
◎IE改善 ‧動作改善、作業改善、制工具使用
手法
‧製程改善、製程平準化
◎提案制度‧鼓勵員工提出改善建議
‧自工程完結
11
問題與改善
生產標準建立
員工訓練
標準化
生產現場實施 (現況掌握)
掌握問題所在 (發現浪費)
進行 改善
12
作業要求
5S
目視管理
突
顯
小批量生產
問
題
零 WIP
零不良
丰田模式精益制造的14项管理原则

丰田模式精益制造的14项管理原则丰田模式,又称精益制造,是日本汽车制造商丰田公司在生产中积累的一套管理原则和方法论。
这套管理原则起源于丰田在20世纪80年代经历的危机时期,针对生产效率低下、质量问题和滞销等困境进行和优化。
经过多年的实践,丰田模式已经在全球范围内得到推广和应用。
丰田模式的核心思想是通过消除浪费,不断提高价值创造能力和质量水平,实现制造业的持续改善和优化。
这套管理原则包括14项原则,每个原则都涉及到企业的组织结构、流程设计、团队合作、持续改进等方面。
下面是丰田模式中的14项管理原则:1.长期质量优先:丰田公司将质量放在首位,追求零缺陷和完美品质。
2.以拉动方式而非推动方式进行生产:根据需求合理制定生产计划,避免过度生产和库存积压。
3.平衡生产:通过平衡各个生产环节和工作岗位的工作量,避免产能过剩或不足。
4.现场创新:鼓励员工提出改善建议,推动现场创新和问题解决。
5.人力积极发挥和培养:充分发挥员工的潜能,提供培训和发展机会,建立学习型组织。
6.标准化工作:制定标准化工作程序和作业指导书,提高工作质量和效率。
7.清理生产线:保持生产场地整洁有序,提高工作效率和品质水平。
8.花费创造价值的时间:减少非生产性活动,使员工的工作时间都用于创造价值。
9.使用可靠技术和设备:使用可靠的工具和设备,提高工作效率和质量。
10.组织层面的持续改进:建立改进的机制和流程,持续追求卓越和进步。
11.目标管理:设定明确的目标和标准,评估和改善绩效。
12.全员参与和团队合作:鼓励员工参与决策和管理,增强团队合作意识。
13.及时问题解决:立即解决生产中的问题,避免问题扩大化和延误。
14.指导性领导:领导者要起到激励和指导的作用,为员工提供支持和指导。
这些原则是丰田公司在生产实践中总结出来的,是一套科学且实用的管理手段。
丰田模式的核心目标是提高企业组织和流程的效率和质量,实现生产体系的优化和持续改进。
这套模式已经被广泛应用于制造业和服务业,成为现代管理的经典案例。
丰田jit管理的概念
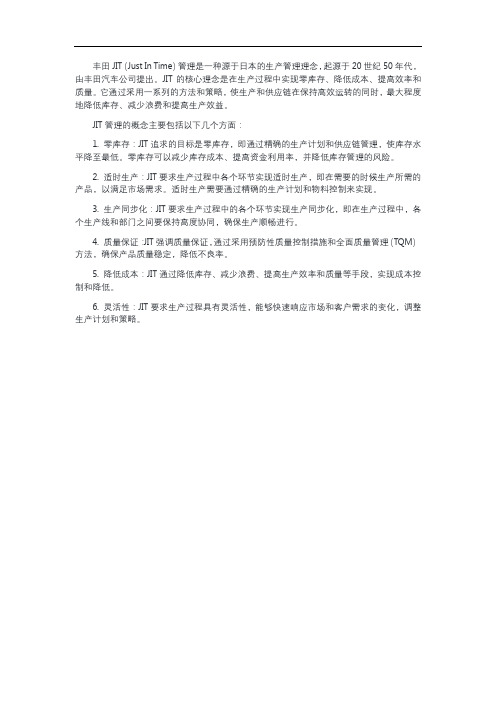
丰田JIT(Just In Time)管理是一种源于日本的生产管理理念,起源于20世纪50年代,由丰田汽车公司提出。
JIT的核心理念是在生产过程中实现零库存、降低成本、提高效率和质量。
它通过采用一系列的方法和策略,使生产和供应链在保持高效运转的同时,最大程度地降低库存、减少浪费和提高生产效益。
JIT管理的概念主要包括以下几个方面:
1. 零库存:JIT追求的目标是零库存,即通过精确的生产计划和供应链管理,使库存水平降至最低。
零库存可以减少库存成本、提高资金利用率,并降低库存管理的风险。
2. 适时生产:JIT要求生产过程中各个环节实现适时生产,即在需要的时候生产所需的产品,以满足市场需求。
适时生产需要通过精确的生产计划和物料控制来实现。
3. 生产同步化:JIT要求生产过程中的各个环节实现生产同步化,即在生产过程中,各个生产线和部门之间要保持高度协同,确保生产顺畅进行。
4. 质量保证:JIT强调质量保证,通过采用预防性质量控制措施和全面质量管理(TQM)方法,确保产品质量稳定,降低不良率。
5. 降低成本:JIT通过降低库存、减少浪费、提高生产效率和质量等手段,实现成本控制和降低。
6. 灵活性:JIT要求生产过程具有灵活性,能够快速响应市场和客户需求的变化,调整生产计划和策略。
精实管理处处讲
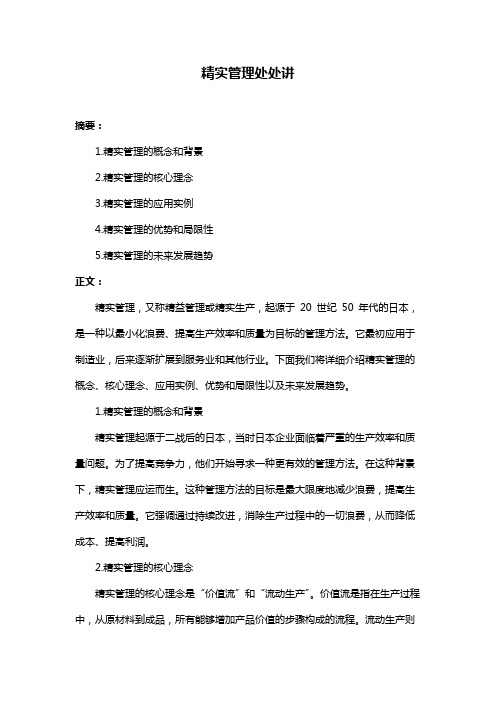
精实管理处处讲摘要:1.精实管理的概念和背景2.精实管理的核心理念3.精实管理的应用实例4.精实管理的优势和局限性5.精实管理的未来发展趋势正文:精实管理,又称精益管理或精实生产,起源于20 世纪50 年代的日本,是一种以最小化浪费、提高生产效率和质量为目标的管理方法。
它最初应用于制造业,后来逐渐扩展到服务业和其他行业。
下面我们将详细介绍精实管理的概念、核心理念、应用实例、优势和局限性以及未来发展趋势。
1.精实管理的概念和背景精实管理起源于二战后的日本,当时日本企业面临着严重的生产效率和质量问题。
为了提高竞争力,他们开始寻求一种更有效的管理方法。
在这种背景下,精实管理应运而生。
这种管理方法的目标是最大限度地减少浪费,提高生产效率和质量。
它强调通过持续改进,消除生产过程中的一切浪费,从而降低成本、提高利润。
2.精实管理的核心理念精实管理的核心理念是“价值流”和“流动生产”。
价值流是指在生产过程中,从原材料到成品,所有能够增加产品价值的步骤构成的流程。
流动生产则是指在生产过程中,产品应该像水流一样,顺畅地从一个工序流向下一个工序,避免产生停滞和浪费。
3.精实管理的应用实例精实管理在制造业中有着广泛的应用。
以丰田汽车公司为例,他们通过实施精实管理,成功地将生产周期缩短了一半,同时降低了一半的库存成本。
另一个例子是苹果公司,他们在产品设计、生产和销售环节都运用了精实管理的理念,从而取得了巨大的成功。
4.精实管理的优势和局限性精实管理的优势在于它能够帮助企业降低成本、提高效率和质量,从而增强竞争力。
此外,精实管理强调持续改进,使得企业能够不断适应市场变化,保持竞争优势。
然而,精实管理也有其局限性。
首先,实施精实管理需要投入大量的时间和精力,对企业的管理水平和员工素质都有较高的要求。
其次,精实管理强调流动生产,可能会导致生产线过于复杂,增加管理的难度。
5.精实管理的未来发展趋势随着科技的发展和市场竞争的加剧,精实管理将继续发挥重要作用。
走!去丰田,领悟精益企业管理精髓
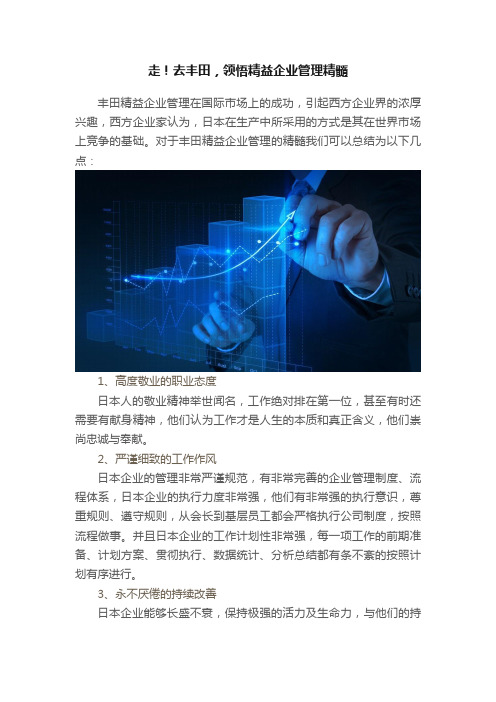
走!去丰田,领悟精益企业管理精髓丰田精益企业管理在国际市场上的成功,引起西方企业界的浓厚兴趣,西方企业家认为,日本在生产中所采用的方式是其在世界市场上竞争的基础。
对于丰田精益企业管理的精髓我们可以总结为以下几点:1、高度敬业的职业态度日本人的敬业精神举世闻名,工作绝对排在第一位,甚至有时还需要有献身精神,他们认为工作才是人生的本质和真正含义,他们崇尚忠诚与奉献。
2、严谨细致的工作作风日本企业的管理非常严谨规范,有非常完善的企业管理制度、流程体系,日本企业的执行力度非常强,他们有非常强的执行意识,尊重规则、遵守规则,从会长到基层员工都会严格执行公司制度,按照流程做事。
并且日本企业的工作计划性非常强,每一项工作的前期准备、计划方案、贯彻执行、数据统计、分析总结都有条不紊的按照计划有序进行。
3、永不厌倦的持续改善日本企业能够长盛不衰,保持极强的活力及生命力,与他们的持续改善精神是分不开的。
他们总是想尽一切办法去完善生产工艺、提高产品质量、控制成本、改善环境等并乐此不疲。
他们往往会采用成立改善小组的方式对企业的问题进行专项的持续改善,如TCM、TPM、TQM、5S等等。
4、规范系统的人才培养机制日本企业员工从入职开始公司就会根据岗位要求为其制定完善的培训计划,培训内容包括企业精神、道德教育、管理知识、专业知识、工作技能等。
在日本企业工作六个月后才敢称为正式员工,培训合格到工作现场时企业还会安排一名师傅通过“一对一”的指导员制度继续培训一年,以使其达到熟练掌握的程度。
在日后的工作中还会根据企业需要对员工的其它技能进行培训拓展,“多能工”就是日本企业人才培养的有效成果,日本企业还会对企业管理人员进行轮岗来提升管理人员的综合素质,开发管理人员的潜能,同时在轮职的过程中通过考察来挖掘人才。
日本企业绝大多数中高层管理人员都是从基层做起,一步一步提升,这就说明了日本企业人才培养机制的重要性及有效性。
丰田模式 精益制造的14项管理原则
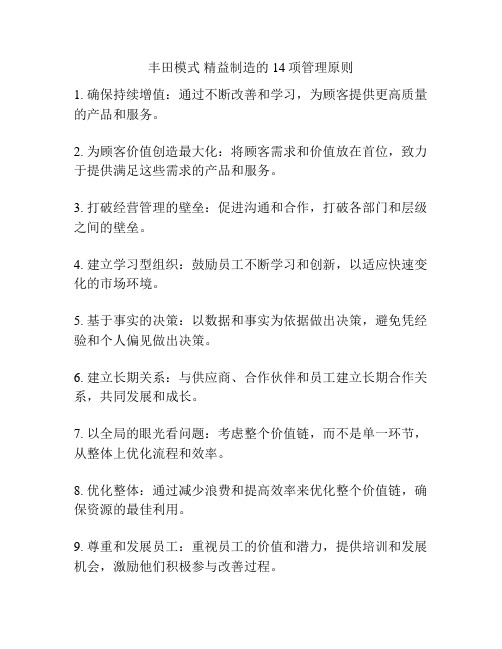
丰田模式精益制造的14项管理原则
1. 确保持续增值:通过不断改善和学习,为顾客提供更高质量的产品和服务。
2. 为顾客价值创造最大化:将顾客需求和价值放在首位,致力于提供满足这些需求的产品和服务。
3. 打破经营管理的壁垒:促进沟通和合作,打破各部门和层级之间的壁垒。
4. 建立学习型组织:鼓励员工不断学习和创新,以适应快速变化的市场环境。
5. 基于事实的决策:以数据和事实为依据做出决策,避免凭经验和个人偏见做出决策。
6. 建立长期关系:与供应商、合作伙伴和员工建立长期合作关系,共同发展和成长。
7. 以全局的眼光看问题:考虑整个价值链,而不是单一环节,从整体上优化流程和效率。
8. 优化整体:通过减少浪费和提高效率来优化整个价值链,确保资源的最佳利用。
9. 尊重和发展员工:重视员工的价值和潜力,提供培训和发展机会,激励他们积极参与改善过程。
10. 靠近现场解决问题:在现场发现和解决问题,避免问题的传导和误解。
11. 标准化工作方法:建立标准化的工作方法和流程,确保质量和效率的稳定性。
12. 反思和改进:不断反思和改进工作方式和方法,追求卓越和完美。
13. 充分利用技术和创新:利用先进的技术和创新的工具,提高生产效率和产品质量。
14. 突显领导力:培养和推崇有远见、能够激励员工并推动组织发展的领导力。
TheToyotaWay丰田模式精益企业的14大管理原则
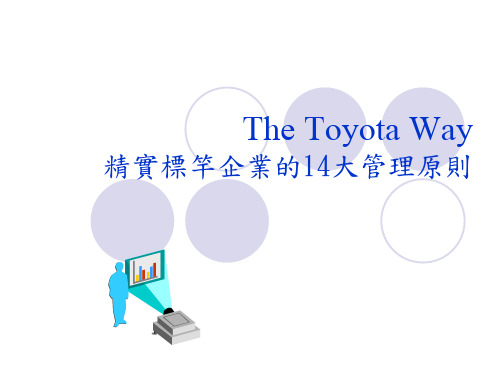
1、企業決策須以長期理念為基礎
企業理念與使命:
社會 價值
客戶 價值
經濟 價值
企業目標:
現在和將來都能賺錢
財務目標: 淨利潤(NP) 投資報酬率(ROI) 現金流量(CF)
作業目標: 有效產出(T)
存貨(I)
營運費用(OE)
製造週期
Toyota Way 的事業原則
正確的流程方能產生正確結果
Stages (4)
JUST-IN-TIME 實施後階段
INFORMATION
MATERIAL
MPS
customers
MRP
purchase reference
suppliers
JIT的成功關鍵
及時供補的理念是持續的改善和消除所有 可能的浪費,一定要組織內所有單位的每 一個人都投入心力一起來做才會成功。
並不是引進看板系統就能號稱JIT,看板其 實比較像是JIT的結果而不是JIT的原因。
JIT 暫時儲存
生產途程
需用 負荷
需用 產能
產能需求計劃
可用 產能
工作中心產能
負荷小時
平衡 負荷
工作中心平均產能
未結訂單
計劃訂單
多少負荷? 需用產能? 可用產能? 平衡負荷?
只生產下工程需要的數量
時段
排程依據最慢的那ㄧ個工作中心
三個M
Muda 浪費
Mura 不均衡
Muri 負荷過重
在客戶需求時彈性生產 降低未能售完的風險 平衡員工與機器設備使用 使上游流程及供應商面臨平順的需求
生產企業的實際情況
骰子遊戲
前後7道工序 平均産能3.5件/天(Max=6, Min=1) 7道工序一天內可以完成 每月(20天)産量多少?
丰田-精实管理理念
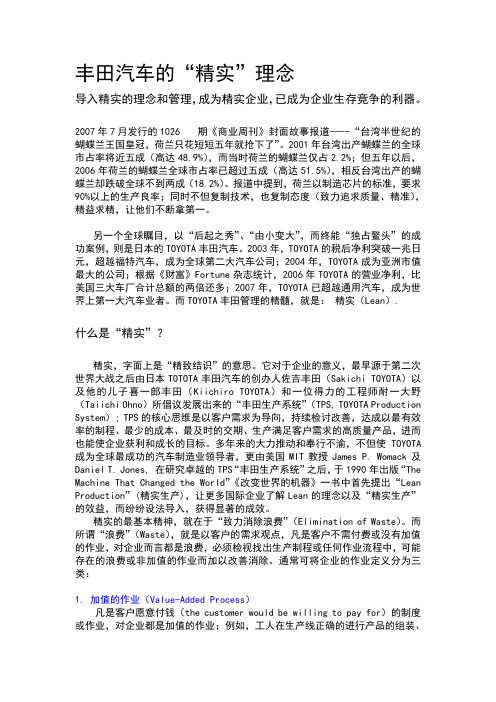
丰田汽车的“精实”理念导入精实的理念和管理,成为精实企业,已成为企业生存竞争的利器。
2007年7月发行的1026 期《商业周刊》封面故事报道----“台湾半世纪的蝴蝶兰王国皇冠,荷兰只花短短五年就抢下了”。
2001年台湾出产蝴蝶兰的全球市占率将近五成(高达48.9%),而当时荷兰的蝴蝶兰仅占2.2%;但五年以后,2006年荷兰的蝴蝶兰全球市占率已超过五成(高达51.5%),相反台湾出产的蝴蝶兰却跌破全球不到两成(18.2%)。
报道中提到,荷兰以制造芯片的标准,要求90%以上的生产良率;同时不但复制技术,也复制态度(致力追求质量、精准),精益求精,让他们不断拿第一。
另一个全球瞩目,以“后起之秀”、“由小变大”,而终能“独占鳌头”的成功案例,则是日本的TOYOTA丰田汽车。
2003年,TOYOTA的税后净利突破一兆日元,超越福特汽车,成为全球第二大汽车公司;2004年,TOYOTA成为亚洲市值最大的公司;根据《财富》Fortune杂志统计,2006年TOYOTA的营业净利,比美国三大车厂合计总额的两倍还多;2007年,TOYOTA已超越通用汽车,成为世界上第一大汽车业者。
而TOYOTA丰田管理的精髓,就是:精实(Lean).什么是“精实”?精实,字面上是“精致结识”的意思。
它对于企业的意义,最早源于第二次世界大战之后由日本TOTOTA丰田汽车的创办人佐吉丰田(Sakichi TOYOTA)以及他的儿子喜一郎丰田(Kiichiro TOYOTA)和一位得力的工程师耐一大野(Taiichi Ohno)所倡议发展出来的“丰田生产系统”(TPS, TOYOTA Production System); TPS的核心思维是以客户需求为导向,持续检讨改善,达成以最有效率的制程、最少的成本、最及时的交期、生产满足客户需求的高质量产品,进而也能使企业获利和成长的目标。
多年来的大力推动和奉行不渝,不但使TOYOTA 成为全球最成功的汽车制造业领导者,更由美国MIT教授James P. Womack及Daniel T. Jones, 在研究卓越的TPS“丰田生产系统”之后,于1990年出版“The Machine That Changed the World”《改变世界的机器》一书中首先提出“Lean Production”(精实生产),让更多国际企业了解Lean的理念以及“精实生产”的效益,而纷纷设法导入,获得显著的成效。
TheToyotaWay精实标竿企业的14大管理原则
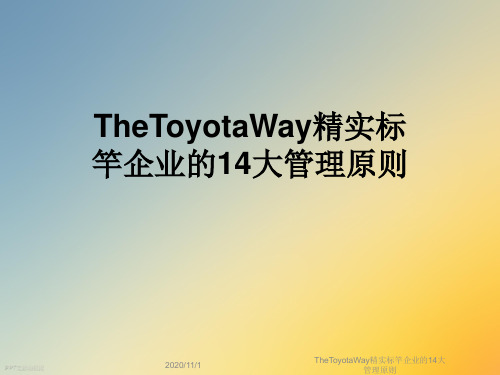
精实制造Lean Manufacturing
实时生产(JIT)
自动化
改善(Kaizen)
•Toyota •DNA •双螺旋
平准化
单件流程作业
了解与激励员工
PPT文档演模板
•企业的DNA就是企业的文化和流程
TheToyotaWay精实标竿企业的14大 管理原则
Toyota Way 14大管理原則 4P
技术体系 • 公司整体性利润增加 •经济性
•适应性
• 消除浪费降低成
•不
本
• 柔性生产提升竞争力
断 暴 露 问 题, 不
• 质量保证
• JIT生产模式 •看板管理 • 均衡化生产 •小批量生产
•尊
重
人
性
•良 好 的 外 部 协
,
作
发
• 同步化生产
挥
断
人
改 •全 面 质 量 •低成本 善 管理防错体 自动化
PPT文档演模板
TheToyotaWay精实标竿企业的14大 管理原则
游戏纪录
•WCR1 工作中心 •Ro 标准产出 •Ship 交货量
WIP 库存 Mo 真正产出
Day
WCR1
WCR2
WCR3
WCR4
Total
WIP Ro Mo WIP Ro Mo WIP Ro Mo WIP Ro Mo Ship WIP
TheToyotaWay精实标竿企业的14大 管理原则
丰田生产制度的核心:杜绝浪费
•价值系统的八大类浪费
l 生产过剩 l 在现场等候的时间 l 不必要的运输 l 过度处理或不正确的处理 l 存货过剩 l 不必要的移动搬运 l 瑕疵 l 未被使用的员工创造力 •政(决)策的浪费
企业文化——丰田企业
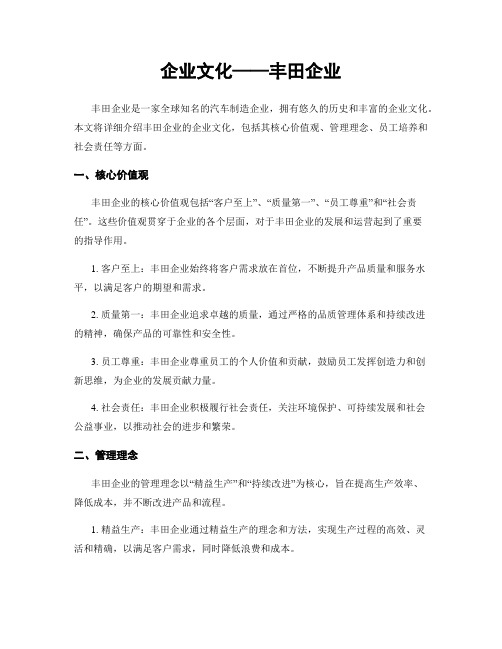
企业文化——丰田企业丰田企业是一家全球知名的汽车制造企业,拥有悠久的历史和丰富的企业文化。
本文将详细介绍丰田企业的企业文化,包括其核心价值观、管理理念、员工培养和社会责任等方面。
一、核心价值观丰田企业的核心价值观包括“客户至上”、“质量第一”、“员工尊重”和“社会责任”。
这些价值观贯穿于企业的各个层面,对于丰田企业的发展和运营起到了重要的指导作用。
1. 客户至上:丰田企业始终将客户需求放在首位,不断提升产品质量和服务水平,以满足客户的期望和需求。
2. 质量第一:丰田企业追求卓越的质量,通过严格的品质管理体系和持续改进的精神,确保产品的可靠性和安全性。
3. 员工尊重:丰田企业尊重员工的个人价值和贡献,鼓励员工发挥创造力和创新思维,为企业的发展贡献力量。
4. 社会责任:丰田企业积极履行社会责任,关注环境保护、可持续发展和社会公益事业,以推动社会的进步和繁荣。
二、管理理念丰田企业的管理理念以“精益生产”和“持续改进”为核心,旨在提高生产效率、降低成本,并不断改进产品和流程。
1. 精益生产:丰田企业通过精益生产的理念和方法,实现生产过程的高效、灵活和精确,以满足客户需求,同时降低浪费和成本。
2. 持续改进:丰田企业鼓励员工参与持续改进活动,通过不断的小改善和创新,提高产品质量、生产效率和员工满意度。
三、员工培养丰田企业注重员工的培养和发展,通过全面的培训计划和职业发展机会,激发员工的潜力和创造力。
1. 培训计划:丰田企业为员工提供全面的培训计划,包括入职培训、技术培训、管理培训等,以提升员工的专业能力和素质。
2. 职业发展:丰田企业鼓励员工在不同岗位间进行轮岗和跨部门交流,为员工提供广阔的职业发展空间和机会。
3. 激励机制:丰田企业建立了激励机制,包括薪酬激励、绩效评估和晋升机会,以激发员工的积极性和创造力。
四、社会责任丰田企业积极履行社会责任,通过环境保护、可持续发展和社会公益事业,为社会做出贡献。
1. 环境保护:丰田企业致力于减少环境污染和资源浪费,通过推广清洁能源汽车和节能技术,为环境保护做出贡献。
Toyota-精实生产心得
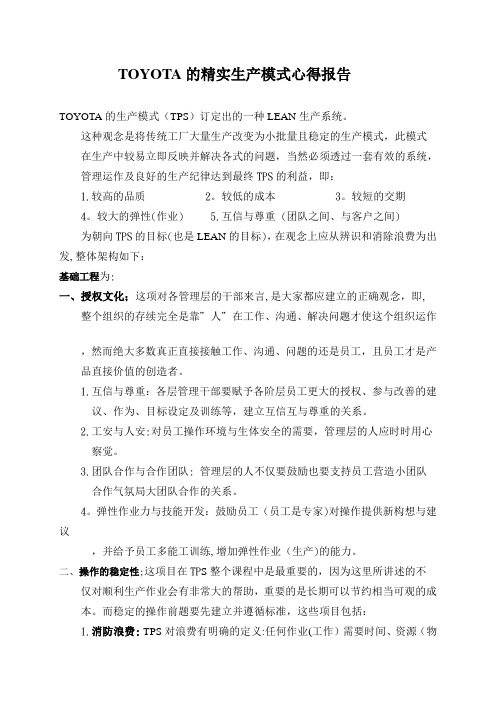
TOYOTA的精实生产模式心得报告TOYOTA的生产模式(TPS)订定出的一种LEAN生产系统。
这种观念是将传统工厂大量生产改变为小批量且稳定的生产模式,此模式在生产中较易立即反映并解决各式的问题,当然必须透过一套有效的系统,管理运作及良好的生产纪律达到最终TPS的利益,即:1.较高的品质 2。
较低的成本 3。
较短的交期4。
较大的弹性(作业) 5.互信与尊重 (团队之间、与客户之间)为朝向TPS的目标(也是LEAN的目标),在观念上应从辨识和消除浪费为出发,整体架构如下:基础工程为:一、授权文化;这项对各管理层的干部来言,是大家都应建立的正确观念,即,整个组织的存续完全是靠”人”在工作、沟通、解决问题才使这个组织运作,然而绝大多数真正直接接触工作、沟通、问题的还是员工,且员工才是产品直接价值的创造者。
1.互信与尊重:各层管理干部要赋予各阶层员工更大的授权、参与改善的建议、作为、目标设定及训练等,建立互信互与尊重的关系。
2.工安与人安:对员工操作环境与生体安全的需要,管理层的人应时时用心察觉。
3.团队合作与合作团队: 管理层的人不仅要鼓励也要支持员工营造小团队合作气氛局大团队合作的关系。
4。
弹性作业力与技能开发:鼓励员工(员工是专家)对操作提供新构想与建议,并给予员工多能工训练,增加弹性作业(生产)的能力。
二、操作的稳定性;这项目在TP S整个课程中是最重要的,因为这里所讲述的不仅对顺利生产作业会有非常大的帮助,重要的是长期可以节约相当可观的成本。
而稳定的操作前题要先建立并遵循标准,这些项目包括:1.消防浪费: TPS对浪费有明确的定义:任何作业(工作)需要时间、资源(物、空间),又无法对产品直接创造价值的都称为浪费。
这里将作业分为三类:⑴创造价值(Value Add):任何为客户需求进行改变材料的形状、结构、功能的作业。
⑵非创造价值(None—value Add):任何需要成本花费,但未能增加或创造产品价值的作业.⑶辅助价值(Incidental):任何必须但又无法直接增加或创造产品价值的作业。
- 1、下载文档前请自行甄别文档内容的完整性,平台不提供额外的编辑、内容补充、找答案等附加服务。
- 2、"仅部分预览"的文档,不可在线预览部分如存在完整性等问题,可反馈申请退款(可完整预览的文档不适用该条件!)。
- 3、如文档侵犯您的权益,请联系客服反馈,我们会尽快为您处理(人工客服工作时间:9:00-18:30)。
丰田汽车的“精实”理念导入精实的理念和管理,成为精实企业,已成为企业生存竞争的利器。
2007年7月发行的1026 期《商业周刊》封面故事报道----“台湾半世纪的蝴蝶兰王国皇冠,荷兰只花短短五年就抢下了”。
2001年台湾出产蝴蝶兰的全球市占率将近五成(高达48.9%),而当时荷兰的蝴蝶兰仅占2.2%;但五年以后,2006年荷兰的蝴蝶兰全球市占率已超过五成(高达51.5%),相反台湾出产的蝴蝶兰却跌破全球不到两成(18.2%)。
报道中提到,荷兰以制造芯片的标准,要求90%以上的生产良率;同时不但复制技术,也复制态度(致力追求质量、精准),精益求精,让他们不断拿第一。
另一个全球瞩目,以“后起之秀”、“由小变大”,而终能“独占鳌头”的成功案例,则是日本的TOYOTA丰田汽车。
2003年,TOYOTA的税后净利突破一兆日元,超越福特汽车,成为全球第二大汽车公司;2004年,TOYOTA成为亚洲市值最大的公司;根据《财富》Fortune杂志统计,2006年TOYOTA的营业净利,比美国三大车厂合计总额的两倍还多;2007年,TOYOTA已超越通用汽车,成为世界上第一大汽车业者。
而TOYOTA丰田管理的精髓,就是:精实(Lean).什么是“精实”?精实,字面上是“精致结识”的意思。
它对于企业的意义,最早源于第二次世界大战之后由日本TOTOTA丰田汽车的创办人佐吉丰田(Sakichi TOYOTA)以及他的儿子喜一郎丰田(Kiichiro TOYOTA)和一位得力的工程师耐一大野(Taiichi Ohno)所倡议发展出来的“丰田生产系统”(TPS, TOYOTA Production System); TPS的核心思维是以客户需求为导向,持续检讨改善,达成以最有效率的制程、最少的成本、最及时的交期、生产满足客户需求的高质量产品,进而也能使企业获利和成长的目标。
多年来的大力推动和奉行不渝,不但使TOYOTA 成为全球最成功的汽车制造业领导者,更由美国MIT教授James P. Womack及Daniel T. Jones, 在研究卓越的TPS“丰田生产系统”之后,于1990年出版“The Machine That Changed the World”《改变世界的机器》一书中首先提出“Lean Production”(精实生产),让更多国际企业了解Lean的理念以及“精实生产”的效益,而纷纷设法导入,获得显著的成效。
精实的最基本精神,就在于“致力消除浪费”(Elimination of Waste)。
而所谓“浪费”(Waste),就是以客户的需求观点,凡是客户不需付费或没有加值的作业,对企业而言都是浪费,必须检视找出生产制程或任何作业流程中,可能存在的浪费或非加值的作业而加以改善消除。
通常可将企业的作业定义分为三类:1.加值的作业(Value-Added Process)凡是客户愿意付钱(the customer would be willing to pay for)的制度或作业,对企业都是加值的作业;例如,工人在生产线正确的进行产品的组装、准时的将产品送达客户指定的交货地点等。
2.非加值的作业(Non-Value-Added Process)相对的,凡是客户不愿意付钱的制程或作业对企业都是非加值的作业;例如,制造业者积存太多的库存、或生产过多不是客户需要的产品等。
3.非加值,但必须的作业 (Non-Value-Added Process, But Required)有些是客户不愿意付钱,但却是当地法令或国际社会的要求而无法免除的制程或作业,则视为对企业非加值,但必须的作业;例如,愈来愈多应绿色环保或国际供应链安全要求的配合作业和措施。
虽然各个企业生产的产品或提供的服务不尽相同,但通常被认为企业常见的主要七种“浪费”为:1.过度生产(Overproduction)因未确切掌握市场和客户需求,造成生产过多滞销产品。
2.过多库存(Inventory)由于原物料交期过长,或市场需求预测(Forecast)的错估,库存过多形成呆料。
3.重新加工(Rework)因为没有再第一次就把产品作对、做好,导致必须重新加工,造成成本浪费。
4.低效能作业(Inefficient Processing)由于作业流程或制程设计不当或机器设备保养不良,造成生产效能不彰或产品不良率太高。
5.动作的浪费(Motion Waste)动作(Movement)并不等于有生产力的工作(Productive Work),浪费的动作通常发生在因为零件或工具的摆放与工人的工作桌或生产线的距离或位置不当(太远、太低、或太高),造成工人必须多走几步或将手伸的比较远才能拿到,影响生产效率。
6.等待时间的浪费(Waiting or Idle Time)由于作业设计不良或管理不当,造成前后作业或制程的衔接时间过长、或因工人训练不足动作太慢,影响下一作业或制程的顺利衔接等。
7.运输的浪费(Unnecessary Transportation)因管理不当,造成超过实际需要的运输物流的浪费,例如,因生产延误交期而只得改以空运交货。
精实的目标,就是再透过作业及流程的检视,找出对客户是加值的作业,并善用企业的资源积极从事创造客户价值的作业,同时尽量免除非加值的作业或是浪费;以达到降低成本、提升生产效率、满足客户需求,使企业获利成长的目标。
不仅是“精实生产”多年以来,精实生产(Lean Production)的应用,出了让世界各国许多企业在降低制造成本、提升生产效率上有卓越的成效之外,精实强调客户价值、持续改善、消除浪费的理念,也被国际企业广泛的运用于生产制造意外的企业其他功能和作业,绳之于职业也意外的其他产业,也都有显著的成效。
因此,精实物流(Lean Logistics)、精实供应链管理(Lean Supply Chain Management)等应用热烈的被讨论,而你公司是否是一个“精实企业”(Lean Enterprise)也成为国际间探讨衡量企业是否有效率、或具竞争力的热门话题。
以精实物流为例,就是为配合精实生产,一方面达到生产线不缺料,另一方面仅维持少量库存的严格目标;因此,必须准确掌握生产线需料的数量和时程,并与供货商、物流业者密切协调配合,将所需的物料以少量多次的配送方式,甚至一天数次配送(或称之为Milk Run),在生产线需料的时刻,正确、准时的送达,以达成少库存、低成本,提升企业竞争力。
除此之外,精实的理念和运用,亦同样有助于提升其它诸多企业重要的功能和作业的效率。
例如,产品开发周期的缩短和成本节省、提高订单处理时效、改善客户服务流程、提升客户满意度、甚至缩短公司征员并雇用适当员工的时间等等。
同时,根据Aberdeen Group 2006年3月公布的“The Lean Benchmark Report”显示驱动企业导入精实的主要动力因素为:改善营运效率的压力(67%)提升价钱或服务的竞争优势(45%)客户要求更短的订单交期(44%)因应客户降低价格的要求(34%)降低库存(29%)改善投资报酬率(26%)提升产品质量(23%)而在非制造(Non-Manufacturing)的产业,也不乏导入精实的成功案例;在零售产业为例,日本的7/11便利店以及英国的TESCO大卖场实时掌握顾客的购买需求,每天多次的快速补货(Demand-Driven Replenishment),都成功的达到仅维持少量库存,同时又避免卖场货架缺货,增加产品销售的零售产业目标。
而Eastman Kodak以精实的越仓(Lean Cross-Docking)作业方式,供货商配合生产线需求,准时适量的将原物料送达,而成功的将原料库存从一周降低为一天。
美国GE更大力推动将精实导入在非织造的业务,GE消费金融服务(GE Consumer Finance)在导入精实理念和作业改善之后,使得交易作业时间从35天减少为1~7天,大幅改善了阻碍业务成长的瓶颈,并使年营业额增加200万美元。
而2005年二月,日本中部国际机场启动,这是日本第三个国际机场,更令全球惊叹的是,透过TOTOTA丰田式的“精实管理”,其造价竟然比预期节省1,200亿日元,几乎是同规模关系机场的一半。
精实管理大师美国MIT教授詹姆斯·沃麦克(James P. Womack),曾带着美国西雅图的维吉尼亚医学中心(Virginia Mason Medical Center)改造医院管理的成功案例来台,让台湾的医院体验精实管理的效益。
当他拜访台大医院,被问到:“制造汽车和服务病患并不相同,精实管理真能一样受用吗?”沃麦克教授指出,精实管理的基本原则是将制造产品或是提供服务,都看成一连串的价值流程(Value Stream),必须不断检视这个价值流程中每个环节的附加价值,进而持续找出并切除对产品或服务没有附加价值的浪费;沃麦克教授强调:“TOYOTA 和警示管理画上等号,对TOTOTA来说是个幸运的巧合,因为它恰好是第一个采用精实管理模式的公司。
”他深信“精实管理”这一个好的管理模式,可以运用在各种产业。
如何成为“精实企业”?要成为“精实企业”,必须有下列几项认知和决心:1.以客户需求为核心(Be Customer-Driven)无论企业提供产品或是无形的服务,都是以满足客户的需求为目的。
管理大师彼得·德鲁克(Peter F. Drucker)认为:“企业经营的目标,在于满足客户的需求,获利则是结果。
”惠普公司CEO马克·赫德(Mark Hurd)说:“我们所做的一切都必须是为了客户;如果不是的话,我们必须思考为什么要做?”。
要成为:“精实企业”,必须从客户的立场了解“价值”(Value)的定义,凡是客户部需要、不愿意付钱买的,都是没有加值或是浪费;同时执行精实的第一步,就是惊醒加值流分析(Value Stream Mapping),将产品设计、制造或服务提供的作业过程,画出详细确实的流程关联图,进行部门内或跨部门的作业加值流深入检视分析,以确认并找出各项无附加价值或造成浪费的作业,并且致力改善和消除在产品制造或提供服务的过程中的各种浪费,同时集中企业资源,专注为客户创造价值;如此,才能提供满足客户需求的产品或服务,使企业达到获利和成长的目标。
2.必须订定衡量指标(Metrics! Metrics! Metrics!)德鲁克曾说:“无法衡量的,就无法管理改善”(You can’t manage what you can’t measure.).经过价值流分析(Value Stream Mapping),确认并找出各项有附加价值、无附加价值、或造成浪费的作业项目,接下来要如何确保执行的成效,很重的是必须就各项作业订定明确的绩效衡量指标(Performance Metrics);因为有明确衡量指针的项目,才能持续评量、加以改善(What gets measured get done.)。