零部件件检验抽样规则
工程机械零部件检验规范

检验规范1.支重轮检验:1.1支重轮总成及零件根据已批准的图纸进行检验。
1.2批量生产的支重轮总成或者零件要抽检,比例按5%抽检,但不得少于7个。
若有一个不合格则加倍抽检。
仍有一个不合格则全检或拒收。
1.3机械加工质量检验1.3.1尺寸精度用内径百分表,外径千分尺,深度尺和游标卡尺进行测定。
1.3.2形状位置公差用专用检具测定。
1.3.3表面粗糙度用粗糙度对比样块测定。
1.4热处理检验1.4.1表面硬度用里氏硬度计或洛氏硬度计测定。
1.4.2如客户需提供淬硬层硬度,则在踏面部位切片,用洛氏硬度计检测或送热处理厂用维氏硬度计检测。
1.5 外观与装配质量检验1.5.1外观用目测检验,检测支重轮总成零件的完整性,检测焊缝平整及漏焊等缺陷,检测铸锻加工件的表面平整度及裂纹、飞边、毛刺、划伤、粘砂等缺陷,检查油漆的均匀度及起皮、流痕等缺陷。
1.5.2轴向窜动量的测定:将支重轮的浮封和内外盖拆除,用百分表测定轴端的窜动量。
1.5.3漏油检测:固定轮体后,通过油孔通入0.4Mpa的压缩空气,放入水中,0.5分钟,观察有无冒泡漏气。
1.5.4转动性能测定:用手转动轮体,感觉能盘动但不很轻松。
2.引导轮检验2.1引导轮机加工质量检验2.1.1尺寸精度用内径百分表,外径千分尺,深度尺和游标卡尺进行测定.2.1.2形状位置公差用专用检具测定。
2.1.3表面粗糙度用粗糙度对比样块测定。
2.2 引导轮热处理检验2.2.1表面硬度用里氏硬度计或洛氏硬度计测定.2.2.2如客户需提供淬硬层硬度,则在淬火线部位切片,用洛氏硬度计检测或送热处理厂用维氏硬度计检测。
2.3 外观与装配质量检验2.3.1外观用目测检验,检测引导轮总成零件的完整性,检测焊缝平整及漏焊等缺陷,检测铸锻加工件的表面平整度及裂纹、飞边、毛刺、划伤、粘砂等缺陷,检查油漆的均匀度及起皮、流痕等缺陷。
2.3.2轴向窜动量的测定:将引导轮的浮封拆除,用百分表测定轴端的窜动量。
汽车零部件监督检查检验细则
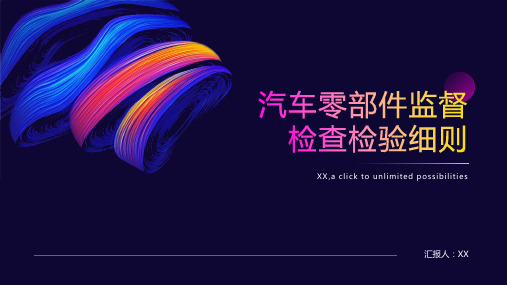
检验记录:详细 记录检验过程和 结果
报告内容:包括检 验依据、检验项目、 检验方法、检验结 果等
报告格式:统一 格式,方便阅读 和存档
报告审批:需经过 相关负责人审批, 确保报告的准确性 和可靠性
检验报告的编制与审核 检验报告的保存与备份 检验报告的调用与查阅 检验报告的更新与修订
PART SIX
持续改进:通过收集和分析质量信息,针对存在的问题和不足进行改进,提高汽车零部 件的质量水平。
质量培训:加强员工的质量意识和技能培训,提高员工对质量标准的认识和执行能力。
PART FIVE
检验员需对检验过程进行详细记录,包括检验日期、检验项目、检验方法、检验结果等。 记录应清晰、准确、完整,方便查阅和追溯。 检验记录是检验工作的重要依据,应妥善保存,避免损坏、丢失。 检验记录的格式应统一、规范,方便整理和归档。
方法:使用标识、 隔离区域或专用容 器对不合格品进行 隔离
记录:对不合格 品进行记录,以 便追踪和追溯
返修:对不合格品进行修复, 使其满足要求
返工:对不合格品进行修复 或加工,使其满足要求
报废:对无法修复的不合格 品进行报废处理
降级处理:将不合格品降低 等级,用于次要用途
PART FOUR
建立完善的质量管理体系,确保汽车零部件监督检查检验工作的有效性和可靠性。
汇报人:XX
定期检验:按照规定的周期进行检验,确保零部件性能稳定 不定期检验:在特定情况下进行检验,如发现故障、维修后等 抽检:对部分零部件进行随机检验,以评估整体性能 验收检验:对新购或维修后的零部件进行检验,确保符合质量标准
PART TWO
零部件外观应无明显缺陷,如裂纹、气泡、缩孔、夹渣等。 零部件的尺寸、形状应符合设计图纸要求,不得有明显的偏差。 零部件的表面粗糙度、硬度等机械性能应符合相关标准要求。
抽样检验标准

1.0说明1.0适用范围1)对于形成过程连续,具有自然连续性和整体均匀性的流程性材料,不能进行计数只能进行计量的物料,如没有明确规定抽样检验方式的,按本标准中的2.0有关抽检规定执行。
2)没有明确规定抽样检验方式的其他批量物料,执行本标准中的3.0、4.0、5.0有关规定,这部分物料包括:外购物料、委外加工的零部件、自制零部件等。
1.1引用标准本标准依据GB/T 2828.1-2003/ISO 2859-1:1999 计数抽样检验程序制定。
2.0流程性材料抽检规定2.1规格、型号相同,由同一个供应商供货的同批流程性材料作为一个检验批,对于塑料或树脂、钢材炉批号等相同的物料为一个检验批。
2.2钢材的理化试验,每批抽检一组试样2.3不易展开的物料在端头进行常规检验,如线材类等3.0术语及符号3.1批量(N):产品生产批次数,同一个供应商采用相同材质、技术工艺、车间、人员及设备生产出的产品统称为批次.构成一个批的产品产生条件须尽可能相同采购件:规格、型号相同,由同一个供应商供货的的同批产品。
外协件:同一个外协厂按同一图纸,采用相同的工艺方法的同批产品。
自制件:同一班次按同一图纸,采用相同的材料、工艺方法和设备的产品。
3.2样本量(n):样本中产品数量3.3样本的抽取:按简单随机抽样(见GB/T 3358.1-1993的5.7)从批中抽取作为样本。
样本可在制作完成后或在制作期间抽取。
由本公司自制件的首件必须报捡。
二次或多次抽样的样本应从同一批的剩余部分抽取。
3.4正常、加严、放宽检验1)概念正常检验:在规定的时段或生产量内平均过程水平优于可允许的最差过程平均质量水平可使用正常检验方法。
•加严检验:当预先规定的连续批数检验结果表明,在规定的时段或生产量内平均过程水平比可允许的最差过程平均质量水平低劣时,采用加严检验。
•放宽检验:在预先规定连续批数的检验结构表明平均过程水平优于可接收的质量限时,可进行放宽的检验方法。
常用零部件检验标准及抽样规范

X X X X X X X X 有限公司检验标准 QP-XX-SIP-TY通用零部件检验规范(A1版)XXXXXX有限公司发布目录检验目的 (1)检验范围 (1)检验定义 (1)检验职责 (1)抽样方案 (1)检验条件 (2)塑料件检验 (2)喷涂件检验 (4)电镀件检验 (7)磷化处理(金属)检验 (10)发黑处理(金属)检验 (10)阳极氧化检验 (11)高频淬火检验 (12)磁铁类材料检验 (12)胶袋(PE袋)类检验 (13)包装彩卡类检验 (13)瓦楞箱类检验 (13)泡壳类检验 (15)印刷产品检验 (15)冲压件检验 (17)文件发放 (17)版本履历及更新内容 (18)参考资料 (19)6.6允收总则:6.1.1 可接受的缺陷不能影响该零件的装配和功能,否则,将被拒收。
6.6.2 C级面为产品底部或客户偶尔能看见的面时,如有缺陷,缺陷应不能明显可见。
6.6.3 缺陷允收定义了900平方毫米(30mmX30mm)的区域内各类缺陷的最大允收数量。
对于较大的零件表面,可允收数量和该表面所含900平方毫米区域数量成正比,但是,两个或两个以上缺陷不能相连。
6.6.4 产品表面同时存在的缺陷不能超过种、缺陷总数量不超过3个。
.塑胶件外观检验标准7.1塑胶件缺陷定义:7.1.1异色点:因塑料件内含杂质造成的不良,如黑点、白点,无固定颜色,以其最大直径为其尺寸。
7.1.2气丝:由于种种原因,气体在产品表面留下的痕迹与底面颜色不同并发亮,带有流动样。
或者部分格子被整片剥落。
13.高频淬火检验标准13.1 外观感应淬火后,经目测,不得有裂纹、烧伤、剥落等缺陷(齿轮的齿部不得有碰伤)。
13.2 硬度13.2.1 对批量产品,每批抽检3件(首件、末件及中间抽件)检验硬度。
13.2.2 对淬火的齿轮,应该附带样块,对样块进行硬度检测,按GB/T 230、GB/T 4341规定测定。
13.2.3 所测的硬度值取平均值,其最低硬度亦应符合图样要求。
原材料检验规则及抽样方法表

↑
↑
│
│
│
│
Q
1250
8
9
12
13
18
19
│
│
│
│
│
│
R
2000
12
13
18
19
↑
↑
│
│
│
│
│
│
注:↓使用箭头下面的第一个抽样方案;当样本量等于或超过批量,则执行100%检验。
↑使用箭头上面的第一个抽样方案;Ac——接收数;Re——拒收数。
3.检验程序和项目
参照具体相关的原材料检验标准。
4.产品不合格的分类与判断
4.1不合格分类
按不合格严重程度将产品分为A类不合格、B类不合格、C类不合格。
4.2 不合格的判定
4.2.1 不合格品的判断参照相关的检验标准。
4.2.2如果样本中其中一个或多于一个检验项目所含不合格数少于或等于接收数,则判定该批产
22
M
315
3
4
5
6
7
8
14
15
21
22
↑
↑
N
500
5
6
7
8
10
11
21
22
↑
↑
│
│
P
800
7
8
10
11
14
15
↑
↑
│
│
│
│
Q
1250
10
11
14
15
21
22
│
│
│
│
│
│
R
2000
14
零部件抽检方案规范

SHBJY003-2006零部件抽检方案规范1 内容与范围本规范规定了一个抽样方案及操作办法。
本规范采用术语接受质量限(AQL)来检索。
本规范的抽样方案可用于(但不限于)下述检验:——最终产品;——零部件和原材料;——操作;——在制品;——库存品;——维修操作;——数据或记录;——管理程序;本规范仅适用于本公司内部各部门。
2 引用标准GB/T 2828.1 计数抽样检验程序Q/L1E 零部件重要度及其项目重要度分级规范3 术语、定义、符号注: 规范本部分的全部术语、定义、符号引用GB/T2828.1计数抽样检验程序第3部分, 规范未列出术语、定义、符号参考GB/T2828.1计数抽样检验程序第3部分。
3.1 检验为确定产品或服务的各特性是否合格, 测定、检查、试验或质量产品或服务的一种或多种特性, 并与规定要求进行比较的活动。
3.2 单位产品可单独描述和考察的事物。
例如:——一个有形的实体;——一定量的材料;——一项服务、一次活动或一个过程;——一个组织或个人;SHBJY003-2006 ——上述项目的任何组合。
3.3 不合格不满足规范的要求。
3.4 不合格品具有一个或一个以上不合格的产品。
3.5 缺陷不满足预期的使用要求。
3.6 不合格品百分数3.6.1 (样本)不合格品百分数样本中的不合格品数除以样本量再乘上100, 即:d/n×100式中:d——样本中的不合格品数;n——样本量。
3.6.2 (总体或批)不合格品百分数总体或批中的不合格品数除以总体量或批量再乘上100, 即:100p=100D/N式中:p——不合格品率;D——总体或批中的不合格品数;N——总体量或批量。
3.7 每百单位产品不合格数3.7.1 (样品)每百单位产品不合格数样品中不合格数除以样本量再乘上100, 即:100d/nd——样本中的不合格数;n——样本量。
3.7.2 (总体或批)每百单位产品不合格数总体或批中的不合格数除以总体量或批量再乘上100, 即:100p=100D/Np——每百单位产品不合格数;D——总体或批中不合格品数;SHBJY003-2006 N——总体量或批量。
汽车零部件抽样检验方案
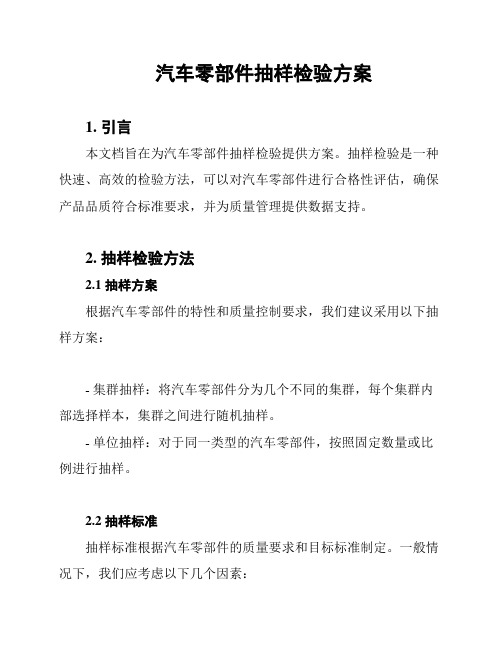
汽车零部件抽样检验方案1. 引言本文档旨在为汽车零部件抽样检验提供方案。
抽样检验是一种快速、高效的检验方法,可以对汽车零部件进行合格性评估,确保产品品质符合标准要求,并为质量管理提供数据支持。
2. 抽样检验方法2.1 抽样方案根据汽车零部件的特性和质量控制要求,我们建议采用以下抽样方案:- 集群抽样:将汽车零部件分为几个不同的集群,每个集群内部选择样本,集群之间进行随机抽样。
- 单位抽样:对于同一类型的汽车零部件,按照固定数量或比例进行抽样。
2.2 抽样标准抽样标准根据汽车零部件的质量要求和目标标准制定。
一般情况下,我们应考虑以下几个因素:- 产品特性和功能要求- 市场需求和用户满意度- 其他行业标准和法规2.3 抽样方法根据抽样方案和标准,我们可以选择以下抽样方法:- 随机抽样:通过随机方法选择样本,确保抽样结果具有代表性和可靠性。
- 系统抽样:按照一定的规则和步骤选择样本,减少偶然性因素对抽样结果的影响。
- 分层抽样:将汽车零部件按照特定的特征或属性进行分层,然后在各层内按照一定比例选择样本。
3. 抽样检验程序3.1 样本收集根据抽样方法,从生产线、仓库或供应商处收集所需样本,并确保样本的完整性和准确性。
3.2 抽样检验根据抽样方案和标准,对收集到的样本进行检验。
可以采用以下方法进行检验:- 外观检查:对汽车零部件的外观进行检查,确保外观无明显瑕疵。
- 尺寸测量:对汽车零部件的尺寸进行测量,确保尺寸符合要求。
- 功能测试:对汽车零部件的功能进行测试,确保功能正常。
3.3 检验结果评估根据抽样标准和检验结果,对汽车零部件的检验结果进行评估。
可以采用以下方法进行评估:- 合格/不合格判定:根据抽样标准,判断样本是否合格。
- 置信区间计算:通过统计学方法,计算样本抽样结果的置信区间,评估合格率的可靠性。
4. 结论通过采用本文档提供的汽车零部件抽样检验方案,可以有效评估产品品质,确保汽车零部件符合质量要求,提高质量管理水平。
零部件进货检验抽验方式及检查频率的规定111

采购产品进货检验抽样办法编制:审核:批准:分发号:河南丰收新能源车辆有限公司零部件进货检验抽样方式及检查频率的规定1、部件检验卡中“检查频率”一栏规定“抽检”的数量,凡抽检的数量超过10只以上的,除不合格项必须记录外,其余在《外购、外协件进货检验记录》可随机记录10只检验结果。
《外购、外协件进货检验记录》“抽检数量”栏填写尺寸项目的抽检数。
各项目抽检数按零部件检验卡执行。
2、对于进货数量少于或等于10只,外观、尺寸项目执行100%检验。
3、零部件检验卡凡规定破坏性检验的,检查频率每批一件,凡每批送货数量超过1500只的允许检验2只。
4、合格判定准则:如果抽检数中发现不合格品数小于或等于接收数,判定该批合格;如果抽检数中发现不合格品数大于或等于拒收数,判定该批不合格;如果抽检数中发现不合格品数介于接收数与拒收数,则加倍抽检,检验结果若不合格品数小于接收数则该批合格,大于或等于接收数则该批不合格。
合格判定对照表5、A、B类重要零部件的a类特性验收时,凡不合格既判本批不合格,不让步接收;其余项目不合格让步接收应以不影响成车外观,不影响使用性能和安全、不影响装配为原则,并由公司技术副总经理签字确认方可让步接收。
6、A类零部件每次进货附带供方出厂检验报告。
7、检验指导书中出现的长度类数值凡没注明单位的,均为毫米;未注明公差的按以下标准执行;a)凡金属切削加工、冲压加工、压铸加工及非金属材料利用模具加工的线性尺寸及焊接加工的线性未注公差按GB/T1804-C级执行;b)角度尺寸的未注公差,按GB/T1804-c级执行。
8、由于橡胶件通常是靠模具生产,所以相对稳定,一般由供货方保证。
9、整车全套贴花及标牌的尺寸、颜色、字体、材质采用对照封样办法进行检验,本零部件检验卡不做另外说明。
10、零部件检验卡中的关键性能件用(A)表示,重要性能件用(B)表示。
11、零部件检验卡中的“项目重要度”分为a、b、c三类,a类:严重影响零部件的性能、质量特性的项目;b类:影响零部件的性能、质量特性的项目;c类:对零部件的性能、质量无直接影响的项目。
零缺陷抽样规定

零缺陷抽样规定文件编号:QD8.9.1-2016
版本:C/0 页次:1/1 1. 目的
为明确本公司外购产品、自制零部件及成品的验收抽样方案及允收标准,特制定本规定。
2. 范围
本文件适用于本公司外购产品、自制零部件及成品的逐批检验。
3. 接收准则
本公司所有产品数据的接收准则为零缺陷。
4. 抽样计划
4.1 如本公司企业标准或其它三级文件未明确规定其抽样要求的,则其抽样计划按附录规定执行,其样本级别的确定原则如下:
原料入厂检验、工序巡检样本级别:10.0
成品抽样样本级别:4.0
4.2 产品抽样采取一次抽样方案,随机抽取样本,尽量在不同的包装中抽取。
4.3 根据抽取样本的检查结果,如果发现的不合格品数为Ac≤0,则判该批产品为合格批;如果发现的不合格品数Re≥1,则应有相关人员进行再次进行抽检,如果再次检验仍发现不合格品数Re≥1,则应由检验员进行100%检验,或做退货、返工、返修、换货处理。
编制/日期:
审核/日期:
批准/日期:。
工程机械零部件查验规范

査验规范1.支重轮査验:支重轮总成及零件按照已批准的图纸迸行査验。
批量生产的支重轮总成或零件要抽检,比例按5%抽检,但不得少于7个。
如有一个不合格则加倍抽检。
仍有一个不合格则全检或拒收。
机械加工质量査验131尺寸精度用内径百分表,外径千分尺,深度尺和游标卡尺迸行测定。
1.3.2形状位置公差用专用检具测定。
1.3.3表面粗糙度用粗糙度对比样块测定。
热处置査验1.4.1表面硬度用里氏硬度计或洛氏硬度计测定。
1.4.2如客户需提供淬硬层硬度,则在踏脸部位切片,用洛氏硬度计检测或送热处置厂用维氏硬度计检测。
外观与装配质量査验1.5.1外观用目测査验,检测支重轮总成零件的完整性,检测焊缝平整及漏焊等缺点,检测铸锻加工件的表面平整度及裂纹、飞边、毛刺、划伤、粘砂等缺点,检査油漆的均匀度及起皮、流痕等缺点。
1.5.2轴向窜动量的测定:将支重轮的浮封和内外盖拆除,用百分表测定轴端的窜动量。
153漏油检测:固定轮体后,通过油孔通入的紧缩空气,放入水中,分钟, 观察有无冒泡漏气。
1.5.4转动性能测定:用手转动轮体,感觉能盘动但不很轻松。
•支重轮总成不合格分类抽样方案:检査结杲汇总表注:不合格项次为每百项2.引导轮査验2.1引导轮机加工质量査验2・1.1尺寸精度用内径百分表,外径千分尺,深度尺和游标卡尺进行测定.2.1.2形状位置公差用专用检具测定。
2.1.3表面粗糙度用粗糙度对比样块测定。
引导轮热处置査验2.2.1表面硬度用里氏硬度计或洛氏硬度计测定.2.2.2如客户需提供淬硬层硬度,则在淬火线部位切片,用洛氏硬度计检测或送热处置厂用维氏硬度计检测。
外观与装配质量査验2.3.1外观用目测査验,检测引导轮总成零件的完整性,检测焊缝平整及漏焊等缺点,检测铸锻加工件的表面平整度及裂纹、飞边、毛刺、划伤、粘砂等缺点,检査油漆的均匀度及起皮、流痕等缺点。
2.3.2轴向窜动量的测定:将引导轮的浮封拆除,用百分表测定轴端的窜动* =2.3.3漏油检测:转动轮体,通过油孔通入的紧缩空气,放入水中,分钟,观察有无冒泡漏气。
零部件外观品质检验规范方案

WORD 格式整理此规范合用于我厂汽车零部件的外观品质检验。
GB/T 2828. 1-2003 第 1 部份:按接收质量限(AQL)检索的逐批检验抽样计划外观品质包含零件的颜色明艳规定等的外观特性,在规格书、图面等中指定。
外观品质基准关于零部件的外观特性 ,有是物理学的规定 ,有通过人的感觉判断 ,后者因为用人的感觉比较简单,作为外观品质基准较多的采用人的感觉评价。
缺点外观品质要求大多在规格书, 图面等要求值以外,没有量化的规定。
复合缺陷零件在单位面积内,存在 2 或者 2 个以上的缺陷.限度样件用样件表示合格品或者不合格品的品质限度, 由与供方共同商议确定。
级面(整车)依据车辆操作及装配状态,区分 1、2、3、4 级面。
1 级面:站立、蹲下或者坐在驾驶座上能很明显看到的部位(不勉强,很容易看到) 。
2 级面:站立、蹲下或者坐位上不是很明显看到的部位(勉强,不容易看到) 。
3 级面:发动机仓、货箱、车辆底部等被覆盖或者很难看到、顾客很少关注的部位。
4 级面:几乎所有顾客都不会关注的部位。
WORD 格式整理区域(零部件)依据零件在车辆上的操作及装配状态,区分 A、B、C、D 的区域。
A 区:操作状态或者正常姿式下很明显看到的部位B 区:操作状态或者正常姿式下不是很明显看到的部位C 区:需要低头、弯腰、爬下或者打开遮盖物才干看见,正常姿式看不到的部位 D 区:任何姿式都不能看见的部位(零件完整的情况下,不评价)判定等级根据质量问题在顾客心中产生的不满程度,评价出的问题分为如下等级:A 级:用户强烈不满会造成人身安全的或者会要求即将返修的不良 B 级:用户感到不满几乎所有人都不能接受,并会要求返修的不良 C 级:用户虽然会发现,但几乎所有的人都能接受的不良问题灯具类零件部位品质要求项目品质要求范围30×30mm 范围以内的缺陷数∮ 1.5mm 以上不合格气泡∮ 1.0~ ∮ 1.5m m 允许 1 个电镀麻点∮ 1.0mm 以下允许 4 个反光镜配光镜灯罩(一级面)线痕伤痕∮0.5mm 以下不评价50×100 范围内只允许 1 个W0.5 ㎜ L2.4 ㎜以下宽度< 1mm,长度> 13mmB 级宽度> 1mm,长度> 7mmB 级A 级长度>5~13mmA 级长度> 3~7mm 相互连接的伤痕要将其总数值作为尺寸大小。
抽样方案及判定准则

三、抽样及判定准则如下表所示:
关键原材料和零部件(A类
批量(N)
样本量(n)
接收数(Ac)
拒收数(Re)
IL=Ⅰ
IL=Ⅱ
IL=Ⅲ
2—8
2
2
3
0
1
9-15
2
3
5
0
1
16-25
3
5
8
0
1
26-50
5
8
13
0
1
51—90
c.品管部认为恢复正常检验是正当的其他情况。
五、特殊情况说明:
1、当样本量(n)≥批量(N)时,进行100%检验,接受准则不变。
2、当批质量判定为不合格时:公司内产品进行100%检验;外购原材料及零部件执行100%检验或退货。
德泓国际绒业股份有限公司
企业标准
0
1
26-50
5
8
13
0
1
51—90
5
13
20
0
1
91—150
8
20
32
0
1
151—280
13
32
50
1
2
281—500
20
50
80
1
2
501—1200
32
80
125
2
3
1201—3200
50
125
200
3
4
3201-10000
80
200
315
5
6
10001-35000
零部件抽样方法(I版)

HEALTH ASCEND
零部件抽样方法
《试行》
共 3 页
编制:
审核:
批准:
浙江康升实业有限公司
零部件抽样方法
按GB2828-87抽样原则结合本公司的情况,在零部件进货验收中对外观、装配尺寸及其所要求性能采取随机抽样的方法进行抽检,检验数量按下表执行,在验收中出现异常或批量质量问题时采取加大样本数的方式进行检查控制,如连续多次检验均未发现任何质量问题,可采取放宽抽查比例的检验方法。
一、抽样原则
1、外观质量
(1)、按零部件在摩托车上的装配位置区分确定外观重要度分类表
注:A、B、C见零部件外观重要度分类表
(2)、按外观重要度分类表确定检查水平和合格质量水平
(3)零部件外观重要度分类表
2 尺寸测量
按照零部件在整车上的安装要求和零部件生产工艺特点确定检查水平和合格质量水平。
3 性能检测
按照零部件的性能要求和在摩托车上的使用要求确定检查水平和判定标准。
性能检验表
二、一次抽样的检查水平及抽样方案(摘自GB2828.1-2003)
1、抽查水平(样本数量)
2、合格质量水平(AQL)
注:1、A C:接收数;
2、AQL:接收质量限(以不合格品百分数或每百单位产品不合格数表示);
3、Re:拒收数;
4、S:特殊检验水平。
零部件入厂检验抽检管理办法(新)
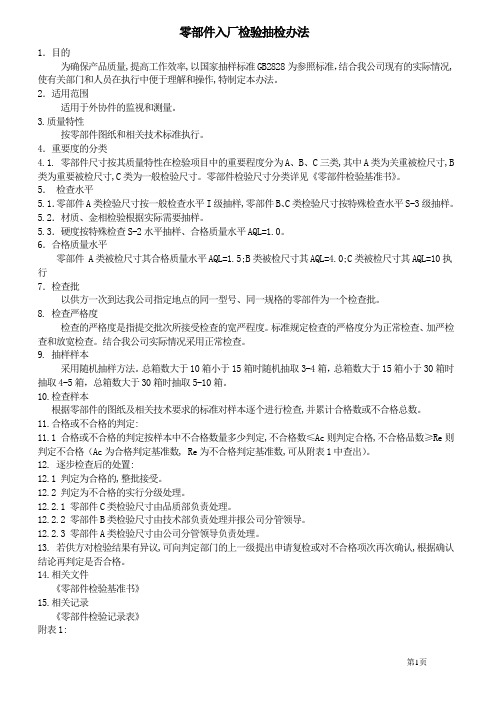
零部件入厂检验抽检办法1.目的为确保产品质量,提高工作效率,以国家抽样标准GB2828为参照标准,结合我公司现有的实际情况,使有关部门和人员在执行中便于理解和操作,特制定本办法。
2.适用范围适用于外协件的监视和测量。
3.质量特性按零部件图纸和相关技术标准执行。
4.重要度的分类4.1. 零部件尺寸按其质量特性在检验项目中的重要程度分为A、B、C三类,其中A类为关重被检尺寸,B 类为重要被检尺寸,C类为一般检验尺寸。
零部件检验尺寸分类详见《零部件检验基准书》。
5.检查水平5.1.零部件A类检验尺寸按一般检查水平I级抽样,零部件B、C类检验尺寸按特殊检查水平S-3级抽样。
5.2.材质、金相检验根据实际需要抽样。
5.3.硬度按特殊检查S-2水平抽样、合格质量水平AQL=1.0。
6.合格质量水平零部件 A类被检尺寸其合格质量水平AQL=1.5;B类被检尺寸其AQL=4.0;C类被检尺寸其AQL=10执行7.检查批以供方一次到达我公司指定地点的同一型号、同一规格的零部件为一个检查批。
8. 检查严格度检查的严格度是指提交批次所接受检查的宽严程度。
标准规定检查的严格度分为正常检查、加严检查和放宽检查。
结合我公司实际情况采用正常检查。
9. 抽样样本采用随机抽样方法。
总箱数大于10箱小于15箱时随机抽取3-4箱,总箱数大于15箱小于30箱时抽取4-5箱,总箱数大于30箱时抽取5-10箱。
10.检查样本根据零部件的图纸及相关技术要求的标准对样本逐个进行检查,并累计合格数或不合格总数。
11.合格或不合格的判定:11.1 合格或不合格的判定按样本中不合格数量多少判定,不合格数≤Ac则判定合格,不合格品数≥Re则判定不合格(Ac为合格判定基准数, Re为不合格判定基准数,可从附表1中查出)。
12. 逐步检查后的处置:12.1 判定为合格的,整批接受。
12.2 判定为不合格的实行分级处理。
12.2.1 零部件C类检验尺寸由品质部负责处理。
进货检验项目及抽样标准

制定日期标准登记号PAGE 整改日期
整改次数
零部件归入正常检验程序。
相应对不良品供应商发送不良通报,要求限期提供改善措施(以 书面形式)
4-2.连续6个月内从未发生过不良的进口件,纳入免检产品。
免检周期为6个月免检期间外协件 检验员随即抽查,如发现不良或生产线反馈不良,取消免检,进行正常检验程序。
(附表) 3-2.历次检验尺寸与标准值比较,在允许公差范围内,判定为合格
3-3.检验后通知资材办理入库
4.不合格品处理
鉴于我公司的零部件大部分为进口件,当进口件发生不良时,为了不耽误生产,采取以下措施 4-1.对①批量不良、②严重影响成品尺寸、③严重影响成品性能进口件纳入100%检查并相应补 充到《进口件需100%检查零件明细表》中 (附表),如连续3个月内未发生不良,则将该 1-4-5.机加工件:尺寸、外观
2.抽样标准 注:1、若发现不良品,加倍抽查,测量后仍不合格则判定该批为不合格
2、《检查成绩书》中记录5组实测数据
3.检查
3-1.将检验后尺寸记录在《进货验证记录》或《检验成绩书》中
1-3. 环境条件:室温
1-4. 检验项目:
1-4-1.橡胶类零部件:尺寸、表面质量
1-4-2.冲压类零部件:尺寸、外观质量
1-4-3.压铸类零部件:尺寸、表面质量
1-4-4.原材料:规格尺寸、外观质量(破断拉力在产品组装时试验)
进货检验项目及抽样标准
1.进货检验项目
1-1. 目的:对零部件进行检验, 以判定是否适用于产品
1-2. 范围:所有国产、进口原材料,零部件。
零部件件检验抽样规则
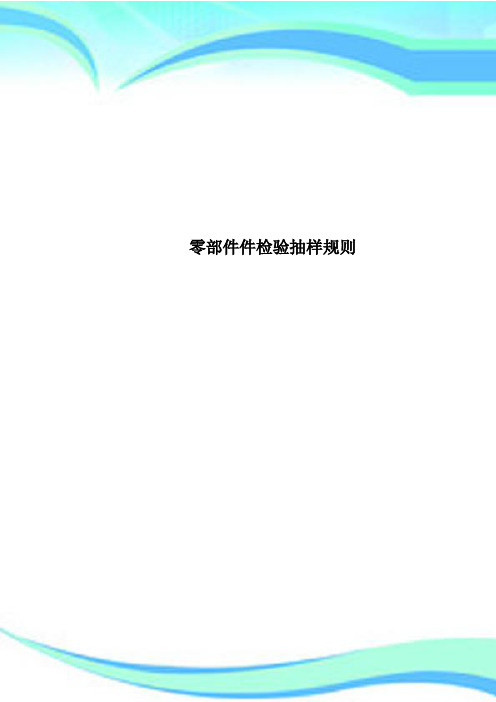
零部件件检验抽样规则————————————————————————————————作者:————————————————————————————————日期:1.目的规定本公司外协、外购件进货检验的抽样原则。
2 引用标准GB2828.1-2003 计数抽样检验程序第1部分:按接收质量限(AQL)检索的逐批检验抽样计划JB/T 5058 机械工业产品质量特征重要度分级导则。
3 术语和定义3.1 AQL—接收质量限:当一个连续系列批被提交验收抽样时,可允许的最差过程平均质量水平,以不合格品百分数表示。
3.2 Ac—接收数:是对批做出接收判定时,样本中发现的不合格品(或不合格)数的上限值,只要样本中发现的不合格品(或不合格)等于或小于Ac时,就可以接收该批。
3.3 Re—拒收数:是对批做出不接收判定时,样本中发现的不合格品(或不合格)数的下限值,即当样本中发现的不合格品(或不合格)等于或大于Rc时,则判定不接收该批。
3.4零部件重要度3.4.1关键件:构成最终产品与环保、安全有关的关键零件,直接影响最终产品的使用安全性,必然引起顾客严重投诉的产品,称A类件,用(A)表示。
3.4.2重要件:构成最终产品的重要部分,直接影响最终产品的使用性能和寿命,可能引起顾客投诉的产品,称B类件,用(B)表示。
3.4.3一般件(物资):构成最终产品的非关键部分,对最终产品的使用性能和寿命影响不大,不致引起顾客投诉的产品,称C类件。
3.4.4 零部件“项目重要度”分为a、b、c三类。
a 指对零部件的质量影响很大;b 指对零部件的质量影响较大;c 指对零部件的质量无直接影响。
4、检验项目及质量要求4.1检验项目:符合产品图样或《零部件检验基准书》的要求。
4.2质量要求:符合产品技术条件、《零部件检验基准书》、技术协议、质量协议的要求。
5、抽样规则5.1《零部件检验基准书》中“检查频率”规定的抽检数量依据GB2828.1,具体应按照本规则“抽样表”的抽样数量执行。
零部件检验规范

零部件检验标准
1.目的:
标准检验过程,使检验时做到有据可依;
1.2确保所有零件在入库前都是检验合格品,符合标准和采购使用要求的.
本标准
全检项:所有的非标零部件
抽检项:采购的批量标准件或批量生产的零件,按20%的比例抽样
3.职责
3.1品管部负责所有相关检验过程,发现不良品,不接受不良品,不流转不良品,并记录相
关数据并向生产部门及采购部门反馈问题,统计和分析不良原因并跟踪改善.
5.检验过程
确实定
5.2确认零件是否加工完成,到达图纸要求的几何形状
5.3检验过程中发现超差,检验员在不确定的情况下,可向组长反映情况,由技术部来判定,
按不合格品控制程序来处理
6.检验项目:
检具上大致由底板,型面,定位,铝柱,(铝板)标准件,车磨件销子,仓库备用标准件(夹钳,基准块,球头手柄,弹簧等)
底板检验标准
型面检验标准
定位角检验标准。
- 1、下载文档前请自行甄别文档内容的完整性,平台不提供额外的编辑、内容补充、找答案等附加服务。
- 2、"仅部分预览"的文档,不可在线预览部分如存在完整性等问题,可反馈申请退款(可完整预览的文档不适用该条件!)。
- 3、如文档侵犯您的权益,请联系客服反馈,我们会尽快为您处理(人工客服工作时间:9:00-18:30)。
14
15
12
13
表3C类零部件检验抽样表
批 量
N
样本量
n
接收质量限AQL= 6.5, 检查水平Ⅰ
正常检验一次抽样方案
加严检验一次抽样方案
Ac
Re
Ac
Re
2~8
2
0
1
0
1
9~15
2
0
1
0
1
16~25
3
0
1
0
1
26~50
5
1
2
0
1
51~90
5
1
2
0
1
91~150
8
1
2
1
2
151~280
13
2
3
1
2
281~500
20
3
4
2
3
501~1200
32
5
6
3
4
1201~3200
50
7
8
5
6
(此文档部分内容来源于网络,如有侵权请告知删除,文档可自行编辑修改内容,供参考,感谢您的配合和支持)
3)经检验抽样数中发现不合格数介于接收数与拒收数之间,则加倍抽样,检验结果若不合格品数小于接收数则该批合格,大于或等于接收数则该批不合格。
7.2供方检验证明判定:
1)《零部件检验基准书》中“检验方法”栏中要求供方提供检测报告的,在供方所提供检测报告在有效期内则此项目判定合格;
2)凡供方所提供检测报告在有效期外而没有及时提供检测报告的,此项目判定为不合格。
3
0
1
0
1
16~25
5
0
1
0
1
26~50
8
0
1
0
1
51~90
13
0
1
0
1
91~150
20
0
1
0
1
151~280
32
1
2
1
2
281~500
50
1
2
1
2
501~1200
80
2
3
1
2
1201~3200
125
3
4
2
3
3201~10000
200
5
6
3
4
表2B类零部件检验抽样表
批 量
N
样本量
n
接收质量限AQL= 4.0, 检查水平Ⅱ
5.4凡《零部件检验基准书》中规定为破坏性检验的,检查频率为每批一件,凡每批送货数量未达到300件的累计满300件后检验1件,凡批送货数量超过1500件允许检验2件。
6、抽样方案
6.1抽样方案根据零部件重要度、接收质量限AQL、检查水平IL、检查的严格性进行确定:
6.2接收质量限AQL:
A类件: AQL值为1.0;B类件:AQL值为4.0;C类件:AQL值为6.5。
6.4.批,应暂时停止检验,目的是促使供方改进提高产品质量。
7、合格判定准则
7.1接收数Ac/拒收数Re判定:
1)经检验抽样数中发现不合格数小于或等于接收数Ac,判定该批合格;
2)经检验抽样数中发现不合格品数大于或等于拒收数Re,判定该批不合格;
7.6.1未注明尺寸公差的按以下标准执行:
1) 凡金属切削加工、冲压加工、压铸加工及非金属材料利用模具加工的线性和角度尺寸的未注公差GB/T1804-m级执行。
2)焊接加工的线性和角度尺寸未注公差的,按GB/T1804-c级执行。
7.7用模具加工的塑料件和橡胶件检验,采取供方首次送检或模具更改后送检2~5套样件试装,合格后列为标准件封样,采用对照封样件办法进行检验。
9. 抽样表
表1.A类零部件检验抽样表
表2. B类零部件检验抽样表
表3.C类零部件检验抽样表
更 改 记 录
日期
更改单编号
更改部门
标记
更改人
备注
表1A类零部件检验抽样表
批 量
N
样本量
n
接收质量限AQL=1.0, 检查水平Ⅱ
正常检验一次抽样方案
加严检验一次抽样方案
Ac
Re
Ac
Re
2~8
2
0
1
0
1
9~15
3.4零部件重要度
3.4.1关键件:构成最终产品与环保、安全有关的关键零件,直接影响最终产品的使用安全性,必然引起顾客严重投诉的产品,称A类件,用(A)表示。
3.4.2重要件:构成最终产品的重要部分,直接影响最终产品的使用性能和寿命,可能引起顾客投诉的产品,称B类件,用(B)表示。
3.4.3一般件(物资):构成最终产品的非关键部分,对最终产品的使用性能和寿命影响不大,不致引起顾客投诉的产品,称C类件。
3.2Ac—接收数:是对批做出接收判定时,样本中发现的不合格品(或不合格)数的上限值,只要样本中发现的不合格品(或不合格)等于或小于Ac时,就可以接收该批。
3.3Re—拒收数:是对批做出不接收判定时,样本中发现的不合格品(或不合格)数的下限值,即当样本中发现的不合格品(或不合格)等于或大于Rc时,则判定不接收该批。
7.5 对于A、B类关重零部件的a类特性检验验收时,凡该特性不合格即判定本批不合格,不允许让步接收;其余项目的不合格让步接收应以不影响整车外观,不影响使用性能和安全、环保特性,不影响装配为原则,并由技术、品质主管人员签字确认方可让步接收。
7.6《零部件检验基准书》中出现的长度类尺寸数值凡没注明单位的,均为毫米;
6.3检验水平IL值: A、B类零部件IL=II, C类零部件IL=I。
6.4检验的严格性:
6.4.1从正常检验到加严检验
当采用正常检验时,只要初次检验中连续5批或少于5批中有2批是不可接收的,则转移到加严检验。本程序不考虑提交批。
6.4.2从加严检验到正常检验
当采用加严检验时,如果初次检验接连5批已被认为是可接受的, 应恢复正常检验。
7.8 贴花及标牌的尺寸、颜色、字体、材质采用对照封样办法进行检验。
8. 进货检验记录填写要求:
进货检验记录必须如实填写《零部件检验基准书》中规定的检验项目及其实际检测结果,外观检验应明确填写抽样个数的每一符合或不符合,尺寸检验要逐一记录实际测量值(一般精确至小数点后两位),试验判定项目应记录参数值和判定结论,试验报告应附在检验记录表后,检验记录表中应明确做出检验合格与否的结论。
正常检验一次抽样方案
加严检验一次抽样方案
Ac
Re
Ac
Re
2~8
2
0
1
0
1
9~15
3
0
1
0
1
16~25
5
0
1
0
1
26~50
8
1
2
1
2
51~90
13
1
2
1
2
91~150
20
2
3
1
2
151~280
32
3
4
2
3
281~500
50
5
6
3
4
501~1200
80
7
8
5
6
1201~3200
125
10
11
8
9
3200~10000
3.4.4零部件“项目重要度”分为a、b、c三类。
a指对零部件的质量影响很大;
b指对零部件的质量影响较大;
c指对零部件的质量无直接影响。
4、检验项目及质量要求
4.1检验项目:符合产品图样或《零部件检验基准书》的要求。
4.2质量要求:符合产品技术条件、《零部件检验基准书》、技术协议、质量协议的要求。
5、抽样规则
7.3对于要求2件/每批进行规定项目检验的,当检验结果出现有1件不合格时,允许加倍抽样进行相同项目的检验,若加倍抽样的项目均合格,可判定该项目合格,若相同项目检验仍不合格,此项目判定为不合格。
7.4 对于形状复杂和空间尺寸不易测量的零部件可采用试装配的办法进行检验,试装配数量每批2件,当其中一件不合格时,允许加倍抽样试装,若相同项目试装仍不合格,此判定为不合格。
5.1《零部件检验基准书》中“检查频率”规定的抽检数量依据GB2828.1,具体应按照本规则“抽样表”的抽样数量执行。
5.2《零部件检验基准书》中“检查频率”规定的“抽检”数量,凡抽检的数量超过13件以上的,对不合格项目必须如实记录,合格项目允许在进货检验记录表中随机记录13件的检验结果。
5.3凡是零部件进货检验中的检验 “批”次规定为:当“检查方法”属于非破坏性检验的,每批送货数量小于10件时,外观、尺寸项目执行100%检验,大于10件的按照抽样表的规定抽样检验。
1.目的
规定本公司外协、外购件进货检验的抽样原则。
2 引用标准
GB2828.1-2003 计数抽样检验程序 第1部分:按接收质量限(AQL)检索的逐批检验抽样计划
JB/T 5058 机械工业产品质量特征重要度分级导则。
3 术语和定义
3.1AQL—接收质量限:当一个连续系列批被提交验收抽样时,可允许的最差过程平均质量水平,以不合格品百分数表示。