产品可追溯记录表
供应商产品质量追溯评价表
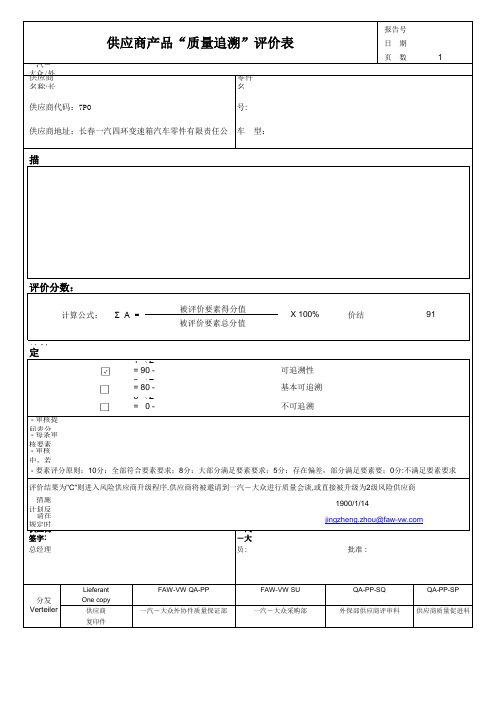
报告号
日 期页 数
1
一汽-大众/外供应商
名称:长
零件名零件号:
问题描
评价结
评价定
1 (Σ= 90 -可追溯性3 (Σ= 80 -基本可追溯6 (Σ= 0 -
不可追溯
- 审核提问表分 - 每条审核要素 - 审核中,若
措施计划反 请在规定时供应商签字:一汽-大供应商总经理
评审员:
批准 :
复印件
供应商一汽-大众外协件质量保证部
一汽-大众采购部
外保部供应商评审科
供应商质量促进科
分发
Verteiler
One copy Lieferant FAW-VW QA-PP FAW-VW SU QA-PP-SQ QA-PP-SP 91
- 要素评分原则:10分:全部符合要素要求;8分:大部分满足要素要求;5分:存在偏差,部分满足要素要;0分:不满足要素要求1900/1/14
jingzheng.zhou@
评价结果为"C"则进入风险供应商升级程序.供应商将被邀请到一汽-大众进行质量会谈,或直接被升级为2级风险供应商
供应商地址:长春一汽四环变速箱汽车零件有限责任公司
车 型:
评价分数:
供应商代码:7PO 供应商产品“质量追溯”评价表
计算公式:
Σ A =
被评价要素得分值被评价要素总分值
X 100%。
产品追溯记录(标准版)
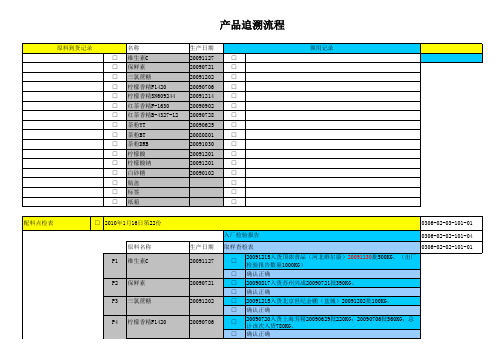
水处理开机点检表
热线制程开机点检表 热线制程品质监控表 生产配料点检表
□ 请查水线
□ 2010年1月14日夜班 正确 □ 2010年1月16日 8:30第22份 调配正确 □ 茶粉YT 20090625 茶粉BT 第7份 茶粉DRB 20091030 柠檬酸 第7份 柠檬酸钠 第7份 20091201 20091201 20080801 □ □ □ □ □ □ □ □ □ □ □ □ □ □ □ 潍坊英轩 确认正确 潍坊英轩 确认正确 北京宝德瑞 确认正确 浙江茗皇 确认正确 上海欣融 确认正确
0306-02-03-101-01 0306-02-02-101-04 0306-02-02-101-01
柠檬香精SN609244 红茶香精F-1630 红茶香精B-4327-12 配料室日报表 □ 盘点正确
20091214 20090902 20090728
□ □ □ □ □ □
20091221入货国际香料20091214批420KG。 确认正确 2009011入货上海芳精20090902批160KG;20090903批20KG。 确认正确 20090817入货厦门津美20090728批160KG。 确认正确 0306-02-03-101-02
产品追溯流程
原料到货记录 □ □ □ □ □ □ □ □ □ □ □ □ □ □ □ □ 名称 维生素C 保鲜素 三氯蔗糖 柠檬香精F1420 柠檬香精SN609244 红茶香精F-1630 红茶香精B-4327-12 茶粉YT 茶粉BT 茶粉DRB 柠檬酸 柠檬酸钠 白砂糖 瓶盖 标签 纸箱 生产日期 20091127 20090721 20091202 20090706 20091214 20090902 20090728 20090625 20080801 20091030 20091201 20091201 20090102 □ □ □ □ □ □ □ □ □ □ □ □ □ □ □ □ 领用记录
产品可追溯流程图图
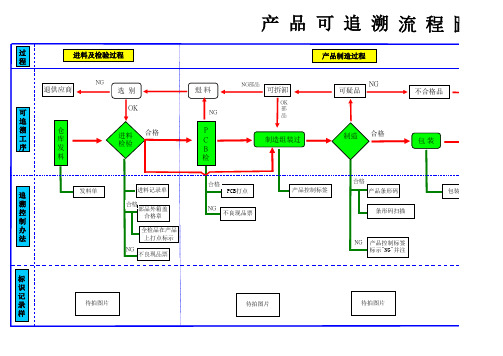
过 程 进料及检验过程 产品制造过程
NG
退供应商 可 追 溯 工 序
选 别 OK
退料
NG
NG部品
可拆卸
OK 部 品
可疑品
N
不合格品
仓库不
仓 库 发 料
合 进料
P C B 检
制造组装过
制造
合
包装
Q A 检 验
合格
合格 PCB打点
产品控制标签
追 溯 控 制 办 法
发料单
进料记录单 合格 部品外箱盖 合格章 全检品在产品 上打点标示 NG 不良现品票 NG
产品条形码 条形码扫描
包装记录表
不良现品票
NG
产品控制标签 标示"NG"并注
标 识 记 录 样待拍Βιβλιοθήκη 片待拍图片待拍图片
QA检验过程
包装交货过程
仓库不合格
Q A 检 验
合
入 库
合 OQC
装 箱 交 货
包装记录表 NG
产品盖"NG"
入库记录
出货检验
待拍图片
待拍图片
产品可追溯性评价检查表
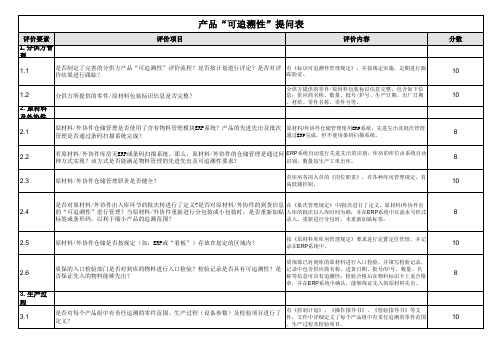
8
3.9
是否保证了“三包”及“召回”产品检验记录及供货文件的正确标识,从而确保产品生 在《标识可追溯性管理规定》中已明确在产品检验记录集供
产条件和制造时间都具有可追溯性?
货文件上做好标识。
8
3.10
生产过程中的批次信息、质量记录、过程数据是否被完整的记录和保存?
3.11
产品全过程文件资料的存档方式是否满足日后产品相关质量信息的快速查找?
来实现的,以保证产品“可追溯性”最小范围原则?
追溯性。
8
3.4
生产过程中,对于一汽-大众BZD系统中定义的TLD“零件”是否通过“生产管理系统”
(MES)或条码扫描系统进行精确追溯的?
NB
3.5
对于图纸或PDM图中规定的需要逐一追溯的零件,是否依靠“生产管理系统”(MES)实 现精确追溯?
NB
3.6
产品“可追溯性”提问表
评价要素 1.分供方管 理
评价项目
评价内容
1.1
是否制定了完善的分供方产品“可追溯性”评价流程?是否按计划进行评定?是否对评 有《标识可追溯性管理规定》,并按规定实施,定期进行跟
价结果进行跟踪?
踪验证。
1.2 2. 原材料 及外协件
2.1
分供方所提供的零件/原材料包装标识信息是否完整?
在《流转卡管理规定》中明确了在制品及半成品的标识卡及 流转卡的填写方法,此方法能够保证制品或半成品批次与“ 标识卡”或“流转卡”信息的一一对应。
8
3.8
是否定义了产品生产批次划分及转换方法?此方法是否能保证产品在任何情况下都能追 溯到前面的过程?
在《批次管理规定》中定义了产品生产批次划分及转换方 法,此方法能保证产品在任何情况下都能追溯到前面的过程 。
食品生产企业各种可追溯生产记录表格模板

号
产品名称
原辅料名称
使用量
产品
产量
生产批号
生产日期
检验结论
检验报告编号
备注
表4食品质量安全档案编号:质量责任人:
食品生产企业关键工艺、关键工序质量控制记录
*******编制
二〇一二年
食品生产企业关键工艺、关键工序质量控制记录
工序名称
质量控制点
质量要求
控制措施
生产班次
责任人
质量控制
运行情况
异常情况
记录
*******编制
二0一二年
食品生产企业产品销售台帐
序
号
产 品 名 称
生产批号
生产日期
执行标准
检验
结论
产量
(单位)
销量
(单位)
销售
日期
销往地区
及企业名称
单证编号
备 注
表1食品质量安全档案编号:质量责任人:
食品生产企业原辅材料供方评价登记表
*******编制
二〇一二年
食品生产企业原辅材料供方评价登记表
表6食品质量安全档案编号:质量责任人:
食品生产企业包装材料使用记录
*******编制
二〇一二年
食品生产企业包装材料使用记录
序
号
产品名称
包装材料名称
生产厂家
生产日期、生产批号
检验证书编号
检验结论
使用量
备注
表11食品质量安全档案编号:质量责任人:
食品生产企业主要负责人员、工程技术人员一览表
*******编制
二〇一二年
食品生产企业主要负责人员、工程技术人员一览表
序
号
姓名
标识和可追溯性控制程序表格格式

编写: 审核: 批准:日期: 日期: 日期:1. 目的明确规范本公司产品的标识,以及当有追溯需要时,如何执行追溯的方式。
2. 范围适用于从原材料进厂到成品出货整个产供销过程的产品标识和可追溯性作业。
3. 定义:无4. 职责4.1. 标识:各部门4.2. 追溯:品管部4.3. 检验状态标识:品管部、生产部5. 内容5.2.1. 物料进厂时,仓管员负责将其放置于待检区或标识待检,于本身未做产品标识或标识不清的物料,需用标签注明物品名称、编号、规格、数量、进货日期等(明显一眼即可辨认的可以不用予以标识,有可能造成工作人员无法辨认的须加以标识)。
5.2.2. 由仓管员检查是否有贴标签,看是否有品名、规格等标识,若当时的进货无标识,仓管员应用物料卡进行标识,以避免误用。
5.2.3. 经品管部检验合格的物料,可办理入库。
置于合格区,需要时仓管员在物料卡上标明物品的数量、进仓时间等信息,并贴于合格物料上。
5.2.4. 检验不合格的物料保持原有产品标识,放置于不合格品区或贴上不合格标签后,按《不合格品控制程序》办理。
5.3. 生产过程中的标识:5.3.1. 生产过程中的半成品、成品及其各工序的检验状态,在填写生产记录和各项检验、试验记录的相应栏目中反映。
5.3.2. 破碎料的标识:由破碎人员在塑料片上写明破碎料成分、来源、破碎时间,放在破碎料上面。
5.3.3. 对于生产过程中的合格品、废品应划分专门区域存放,并作明确标识,不得混用。
标识应注明品名数量、生产单位、生产日期、订单号码等。
5.3.4. 对于合格品,需放置于合格区,或由品管员标识合格后,方可办理入5.3.5. 对于不合格品应放置于不合格区或废品区,或由品管员加上不合格标识,并按《不合格品控制程序》执行。
5.4. 仓库中产品的标识:在仓库中的产品应利用物料卡、储位、标识牌等方式标识。
5.5. 标识的管理:5.5.1. 由品管部、生产部负责所有标识的制作,并对其有效性进行监控。
产品可追溯性模拟演练(原料-成品)记录
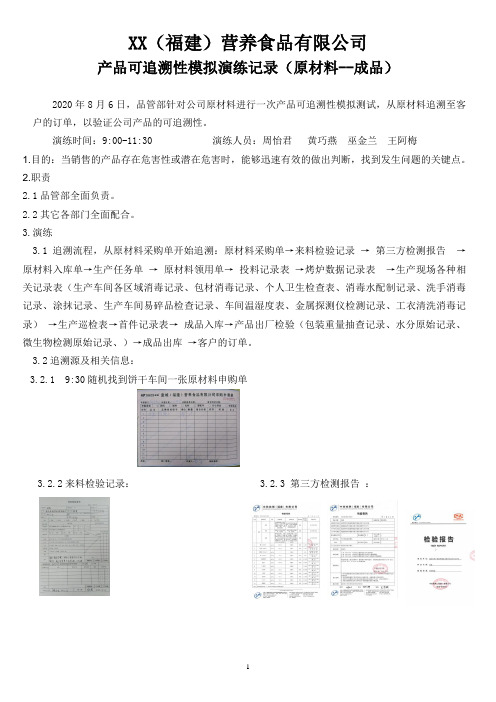
产品可追溯性模拟演练记录(原材料--成品)2020年8月6日,品管部针对公司原材料进行一次产品可追溯性模拟测试,从原材料追溯至客户的订单,以验证公司产品的可追溯性。
演练时间:9:00-11:30 演练人员:周怡君黄巧燕巫金兰王阿梅1.目的:当销售的产品存在危害性或潜在危害时,能够迅速有效的做出判断,找到发生问题的关键点。
2.职责2.1品管部全面负责。
2.2其它各部门全面配合。
3.演练3.1追溯流程,从原材料采购单开始追溯:原材料采购单→来料检验记录→第三方检测报告→原材料入库单→生产任务单→原材料领用单→投料记录表→烤炉数据记录表→生产现场各种相关记录表(生产车间各区域消毒记录、包材消毒记录、个人卫生检查表、消毒水配制记录、洗手消毒记录、涂抹记录、生产车间易碎品检查记录、车间温湿度表、金属探测仪检测记录、工衣清洗消毒记录)→生产巡检表→首件记录表→成品入库→产品出厂检验(包装重量抽查记录、水分原始记录、微生物检测原始记录、)→成品出库→客户的订单。
3.2追溯源及相关信息:3.2.1 9:30随机找到饼干车间一张原材料申购单3.2.2来料检验记录: 3.2.3 第三方检测报告:3.2.4原材料入库单: 3.2.5生产任务单: 3.2.5原材料领用单:3.23.2.7投料记录表: 3.2.7烤炉数据记录表:3.2.8生产现场的各种相关记录表:3.2.8.1生产车间各区域消毒记录: 3.2.8.2包材消毒记录:3.2.8.3个人卫生检查表: 3.2.8.4消毒水配制记录:3.2.8.5洗手消毒记录:3.2.8.6涂抹记录:3.2.8.7生产车间易碎品检查记录: 3.2.8.8生产车间温湿度表:3.2.8.9金属探测仪检测记录: 3.2.8.10 工衣清洗消毒记录表:3.2.9生产巡查记录: 3.2.10首件记录:3.2.11成品入库:3.2.12 产品出厂检验报告:3.2.12.1包装重量抽查记录: 3.2.12.2水分原始记录: 3.2.12.3微生物检测原始记录:3.2.13成品出库:3.2.14客户订单:4.从生产投料记录表投料生料合计为1250kg;成品入库单合计132件(210g*36罐)为997.92kg;追溯率核算:该批次(成品入库数997.92kg+库存数0kg)÷投料1250kg×100%=79.83%总结:这次模拟追溯是从一批原料批追溯到成品批,11:30追溯结束总共用了2小时30分钟,符合追溯的时间要求,追溯率生料79.83%,公司标准生产过程,生料25%以内;通过这次的模拟追溯,符合质量管理体系规定的追溯要求,证明追溯的有效性。
产品可追溯性评价检查表
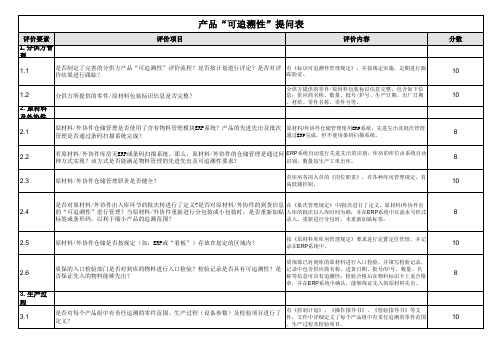
有库房各岗人员的《岗位职责》,有各种库房管理规定,有 高低储控制。
是否对原材料/外协件出入库环节的批次转进行了定义?是否对原材料/外协件的到货信息 在《批次管理规定》中/批次进行了定义,原材料/外协件出
2.4Βιβλιοθήκη 的“可追溯性”进行管理?当原材料/外协件重新进行分包装或小包装时,是否重新加贴 入库的批次以入库时间为准;并在ERP系统中以流水号形式
质保部已对到库的原材料进行入口检验,并填写检验记录, 记录中包含供应商名称、进货日期、批号/炉号、数量、名 称等信息可具有追溯性;检验合格后在物料标识卡上盖合格 章,并在ERP系统中确认,能够保证先入的原材料先出。
是否对每个产品组中有责任追溯的零件范围、生产过程(设备参数)及检验项目进行了 定义?
有《控制计划》、《操作指导书》、《检验指导书》等文 件,文件中详细定义了每个产品组中有责任追溯的零件范围 、生产过程及检验项目。
来实现的,以保证产品“可追溯性”最小范围原则?
追溯性。
8
3.4
生产过程中,对于一汽-大众BZD系统中定义的TLD“零件”是否通过“生产管理系统”
(MES)或条码扫描系统进行精确追溯的?
NB
3.5
对于图纸或PDM图中规定的需要逐一追溯的零件,是否依靠“生产管理系统”(MES)实 现精确追溯?
NB
3.6
10
的快速查找。
现成品、半成品及自制件的入库均录入ERP系统进行管理, 并通过条形码扫描,能够保证产品可追溯性要求。
10
4.2
一汽-大众BZD系统的TLD清单上产品或产品外包装条形码是否满足VW 01064和VW 80125 要求?
产品外包装条形码能够满足标准要求。
10
产品可追溯流程图

附 18: K3 台 账
附15:原辅料领用记录
附 8: 压 铸 车 间 生 产
)
包装
质 量 检 验
OK
入 库
OK
订单
发 OK 货 、 销 售
追 溯 控 制 办 法
报检单
来料检验 记录表
OK
合格状态 标识
NG
产品生 产计划
巡检记录 表 批次切换 标识
NG 隔离产品,
包装记 录 产品追 溯记录
OK
产品出 厂检验
OK
入库 记录
市场部发货记
更改产品质 量状态 仓库接收合 格产品 不合格标识, 等待处理
附 16: 出 厂 检 验 报
附 9: 生 产 日 报 表
附 19: 销 售 出 库 单 /K3
追 溯 记 录 ( 表 )
附13:工序衔接记录
附 14: 场 巡 检 记 录 表
附 17: 产 品 入 库 单
附 10: 产 品 标 识 牌
附20: 客户投 诉与质 量反馈 单
附 11: 产 品 合 格 证
产品追溯流程图
过 程 原辅料来料及检验过程
产品生产过程
出厂检验过程
销售过程
退供应商
NG
折扣或挑拣 使用
退料
NG
可回收半成品
可疑品
NG
不合格品
NG 可 返 工
仓库不合格 品放置区
报废
可 追 溯 工 序
OK
仓 库 报 检 仓 合格 库 发 货
OK
来料 检验
原 前辅 检料 查使 用
产品生产
在制品 检验
OK
不合格 状态标识
产品追溯报告
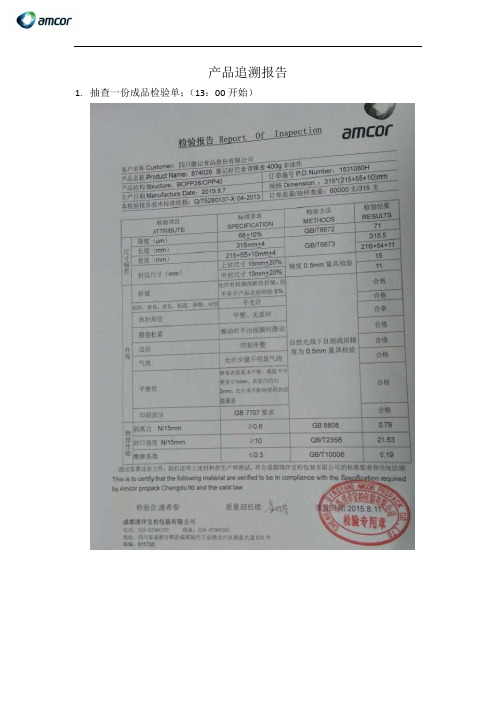
产品追溯报告1.抽查一份成品检验单;(13:00开始)2.找到对应的成品发货单,发货单上有备注订单号,且发货数量与入库数量一致;3.成品入仓截图(8月8日入库);4.制袋工序生产情况,8月7日共生产2个班组,使用2卷(卷号为8月4日复合工序生产的-1、-2卷);5.复合工序生产情况,①8月4日生产2卷计5185米,使用2卷原材料(CPP40*580),成都壮大供应,批号为1518148-2-1,7月23日生产,7月25日到货;使用胶水为3934,批号为201505111/201504221(惠州赛亚,6月23日到货);②8月11日生产4卷(还未制袋)计19934米,使用7卷原材料(CPP40*580,成都壮大供应,其中批号1518901-1-2共1卷,7月30日生产,8月3日到货,批号1519728-1-1共6卷,8月8日生产,8月10日到货;使用胶水为3934,批号为1412061/14010141(惠州赛亚,6月23日到货)。
1:对应的原材料检验报告单:2:对应的胶水粘度检测记录:3:对应的熟化记录6.印刷工序生产情况,①8月3日生产3卷,计5760米,使用1卷原材料(BOPP28*600),成都中达供应,批号为1513142-4-1,6月3日生产,6月5日到货;油墨批号为J150613A015 / J150709A017 / J150611A007 / J150610A005(洋紫荆油墨6月30日到货)②8月10日共生产2个班组,6卷半成品,计20234米,使用5卷原材料,批号为1519708-2-1,8月6日生产,8月6日到货;油墨批号为J150416A035 / J15068A070 / J150617A008 / J150729A020 / J150328A011/J150610A005/J1503310A047/J150109A049(洋紫荆油墨6月30日到货)1:对应原材料的检测数据::2:油墨的溶剂残留检测记录备注:胶水、油墨现场粘度检测数据在机台上的监控表等相关记录上体现。
产品可追溯性模拟演练(服务-客户)记录
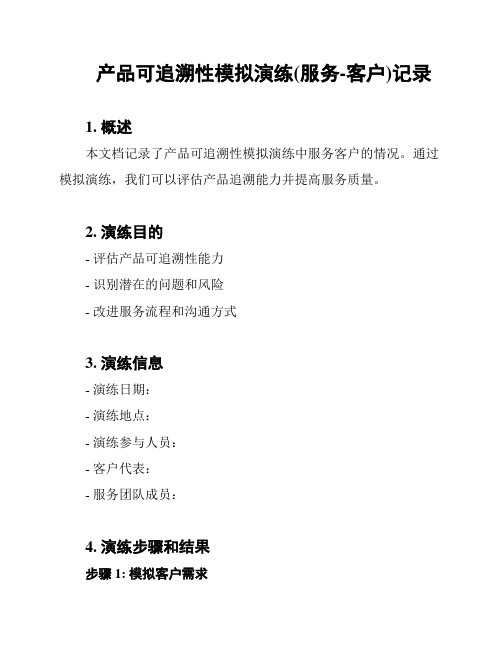
产品可追溯性模拟演练(服务-客户)记录
1. 概述
本文档记录了产品可追溯性模拟演练中服务客户的情况。
通过模拟演练,我们可以评估产品追溯能力并提高服务质量。
2. 演练目的
- 评估产品可追溯性能力
- 识别潜在的问题和风险
- 改进服务流程和沟通方式
3. 演练信息
- 演练日期:
- 演练地点:
- 演练参与人员:
- 客户代表:
- 服务团队成员:
4. 演练步骤和结果
步骤1: 模拟客户需求
- 描述客户需求并标记关键信息
步骤2: 记录和追踪产品信息
- 将模拟需求与产品相关信息关联
- 记录和跟踪产品的生产批次、供应商、交付记录等
步骤3: 演练中出现问题
- 记录演练过程中出现的问题
- 包括产品信息不明确、追溯信息缺失、与客户的沟通问题等
步骤4: 解决问题和改进
- 针对演练中出现的问题,制定解决方案
- 改进产品追溯流程和服务流程
5. 演练总结与改进
通过模拟演练,我们对产品可追溯性能力进行了评估并发现了一些问题。
我们将根据演练结果制定相应的改进措施,包括改进产品信息记录方式、加强与客户的沟通和合作等。
通过不断地进行模拟演练,我们将提升产品追溯能力,提供更高质量的服务。
产品标识与可追溯性管理程序(含表格)

产品标识与可追溯性管理程序(IATF16949-2016/ISO9001-2015)1.0目的建立和实行产品标识和记录制度,根据标识或记录对产品进行追溯,为分析产品质量和采取纠正措施提供依据。
2.0适用范围本程序适用于所有在公司范围内的原材料、半成品和成品的标识。
3.0职责3.1.生产部负责在线产品的标识方法,负责生产过程中原材料、半成品、成品状态的标识。
3.2.品质部负责检验和试验状态的标识。
3.3.仓管部负责库存品的标识4.0程序内容4.1.产品标识4.1.1.来料标识:由供方在外包装上用标签进行标识。
4.1.2.原材料存贮时标识。
4.1.2.1.原材料来料时,由IQC标明检验状态,原材料检验完成后在包装箱贴上检验标识,并注明该原材料的品名、数量、供应商及检验结果,参照《进料检验管理程序》。
4.1.2.2.原材料入库时由仓管员根据品质部检验结果标识状态办理,且在《物料标识卡》记录原材料的入库时间、品名、数量。
4.1.3.成品标识4.1.3.1.单一产品标识:在成品的指定位置贴上该成品的成品条码、QC Passed 标签,成品条码按照《产品条码编码规范》执行。
4.1.3.2.外箱标识:在外箱的指定位置贴上标签,注明产品的型号、生产日期、客户名、检验结果、检验日期、生产批号等。
4.1.4.执行状态标识。
4.1.4.1.生产状态标识为:待处理品、完成品和不良品等,生产中根据各工序的不同情况进行标识。
4.1.4.2.检验状态标识参见《成品检验管理程序》将检验情况进行标识。
4.1.4.3.具有相对独立性的各作业段半成品用“产品流程卡”作为标识,从流程卡上可追溯到生产线别,机型等特性。
4.1.4.3.1.产品流程卡标识4.1.4.3.2.作业员每天将其所用流程卡流水号记录于《条码记录表》上。
4.1.5.不良品标识:用红色的标签标识和带红色标识的防静电周转箱进行隔离,具体参照《不合格品管理程序》。
4.1.6.区域标识:现场区域采用挂牌、斑马线等方法进行标识。
产品、物料、标识可追溯性控制程序(含表格)

文件制修订记录1.0目的对产品、物料、标识等进行适当的控制,以防止不同类别、规格、批次、状态的产品、物料混淆、误用,并实现可追溯性。
2.0范围适用于本公司从原辅料、过程产品、半成品、成品、包材全过程中的标识控制。
3.0职责3.1生产管理部负责过程产品、半成品、成品的标识管理。
3.2供应链部负责采购、仓储、产品运输环节原辅料、包材、成品的标识管理。
3.3生产车间的操作人员负责生产加工过程中的原辅料、半成品、成品、包材的标识。
3.4质量管理部负责标识的监督管理。
4.0控制程序4.1标识的分类a)产品标识;b)状态(包括待检、合格、不合格)标识。
各类产品标识包括产品本身标识和检验与试验状态标识。
4.2标识的原则a)对每批产品皆需有唯一性标识;b)对不同状态的产品必须标识。
4.3产品标识4.3.1原辅料标识原辅料入厂后,由库管员根据《物料验收入库管理制度》和《批号与生产日期管理规程》《物料编码管理规程》进行验收和标识。
标识包括品名、批号、数量、入库日期等内容。
4.3.2过程产品、半成品标识4.3.2.1车间操作人员根据《批号与生产日期管理规程》《物料编码管理规程》进行过程产品的标识,标识包括品名、批号、数量、生产日期、操作人等内容。
4.3.2.2从原材料领出到产品入库采用可追溯性批号标识。
a)车间领料应由管理人员填写“领料单”,并在单据上写清原辅料名称、生产批号、请领数量。
领料人持“领料单”到库房领料,库管员核对“领料单”无误后发料,并在“领料单”写清实发原辅料名称、数量。
领、发料人在“领料单”上签名。
库管员在库房台帐上登记。
b)领料人把“领料单”同原料一起交生产岗位。
生产岗位依据“领料单”上原料名称、批号填写“批生产原始记录”及“岗位操作记录”。
“批生产记录”上应写明名称、生产批号、生产日期、数量、操作人、复核人(对某些需变更或合并的物料则要求合并人详细记录)等内容。
c)操作工按工艺要求达到产品质量要求时出料,并在周转容器上粘贴标识。
制造批号及产品追溯管理程序(含表格)
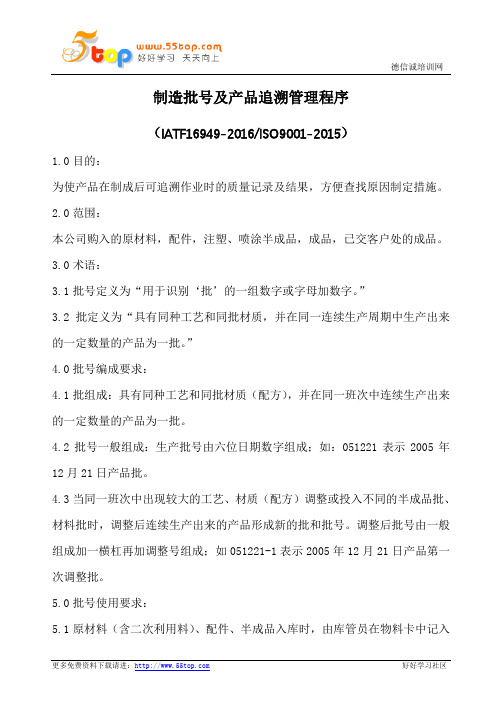
制造批号及产品追溯管理程序(IATF16949-2016/ISO9001-2015)1.0目的:为使产品在制成后可追溯作业时的质量记录及结果,方便查找原因制定措施。
2.0范围:本公司购入的原材料,配件,注塑、喷涂半成品,成品,已交客户处的成品。
3.0术语:3.1批号定义为“用于识别‘批’的一组数字或字母加数字。
”3.2批定义为“具有同种工艺和同批材质,并在同一连续生产周期中生产出来的一定数量的产品为一批。
”4.0批号编成要求:4.1批组成:具有同种工艺和同批材质(配方),并在同一班次中连续生产出来的一定数量的产品为一批。
4.2批号一般组成:生产批号由六位日期数字组成;如:051221表示2005年12月21日产品批。
4.3当同一班次中出现较大的工艺、材质(配方)调整或投入不同的半成品批、材料批时,调整后连续生产出来的产品形成新的批和批号。
调整后批号由一般组成加一横杠再加调整号组成;如051221-1表示2005年12月21日产品第一次调整批。
5.0批号使用要求:5.1原材料(含二次利用料)、配件、半成品入库时,由库管员在物料卡中记入原料、配件、半成品的批号;5.2各生产单位在领料时,由库管员在领料单上注明原料、配件、半成品的批号。
5.3注塑生产时,配料员依生产计划和物料配比表将所领物料的批号详细记录到配料记录表中,加料员将配好的物料详细记录到对应机台张贴的加料记录表中;5.4注塑产品在批量生产前由上模工人在模具日期码的对应位置或指定位置敲打印记,并在当天生产日报表中记入敲打印记的日期和加工后的产品批号;5.5注塑部每完成一个产品后,需及时在产品的背面写上开机或修边人员的工号。
每完成一个包装后,需及时将产品状态卡粘贴到产品的外包装箱/架上,生产批号统一填写在产品状态卡的生产日期栏。
产品状态卡是作为后续追溯用的重要标示,需填写清晰完整;5.0涂装小线,涂装大线生产的小产品,注塑装配在生产时,由物料员依生产计划和领料单去仓库领用相关油漆,配件或半成品,并将油漆的批号详细记录到当天的调漆记录表中,配件,半成品的批号和加工后的成品批号详细记录到当天的生产日报中。
产品识别和可追溯性程序(含表格)

产品识别和可追溯性程序(ISO9001-2015)1、目的确保原物料进料、制程半成品及成品完工、成品入库及出货易于标识其作业加工状况与品质状态,使产品皆有可追溯性。
2、范围原物料进料制程半成品及成品、入库、出货至售后服务各阶段的产品识别与追溯。
3、权责3.1制造单位3.1.1负责原材料、零件、半成品及成品在制程中及储存时有明确制品标识,以利掌握制程品质状况。
3.1.1负责制程所发现之不合格品及异常品、机器设备,治具的正确标识,防止误用。
3.1.3执行异常追溯处理。
3.1品保单位3.1.1负责监督相关标识的执行3.1.1主导制程中异常追溯处理及调查,以防止不合格品流入后工段或出货给客户。
3.1.3确保制程合格品、不合格品及嫌疑品被有效标识、验证。
3.3仓库单位3.3.1负责所有入库材料、成品、半成品的标识区隔。
3.3.1负责制程多余物料退回仓库后正确标识,以防止误用。
3.3.3协助异常追溯处理及调查。
4、定义4.1状态标识:用以表明产品/机器设备等所处状态特性的标识。
本办法规定主要标示产品所处的待检、合格、不合格等检验状态及机台、夹具等使用与完好,暂停使用等状态。
4.1产品标识:用以说明产品特性的标识。
本办法规定主要标示产品之名称、数量、生产日期、检验状态,批号等。
4.3可追溯性:根据记载的标识,追踪实体的历史、应用情况和所处场所的能力。
5、作业程序5.1流程说明5.1.1交货/收货供应商交货时须由送货单,且与采购单相符,所交货之包装处需贴标签,应标示有品名、规格、料号、数量、日期、重量、批号等。
仓库人员点收无误后打印《外购入库单》交给IQC,由IQC检验人员实施检验。
5.1.2IQC检验IQC检验人员根据《进料检验作业办法》和SIP中相关规定检验供方提供的产品。
5.1.3来料/产品标识物料入库时,仓管人员检查产品标识及状态标识的完整性、合理性。
根据检验状态标识在库房分区存放产品,并根据《进料搬运、包装、储存、保护程序》对产品标识及状态标识进行妥善保管。
产品可追溯流程图图

产品控制标签
合格 产品条形码
包装记录表
包装记录表
入库记录
出货检验 记录表
溯
合格
控 制
部品外箱盖 合格章
NG 不良现品票
条形码扫描
NG 产品盖"NG"章,
办
全检品在产品
法
上打点标示
NG 不良现品票
NG 产品控制标签 标示"NG"并注
标
识
记
标识图片
录
样
标识图片
标识图片
标识图片
标识图片
产品可追溯流程圖
过
进料及检验过程
程
退供应商
可
追
溯
仓
工
库
序
发
料
NG
选别
OK
进料 合格 检验
产品制造过程
退料
NG
P C B 检
NG部品
可拆卸
OK 部 品
制造组装过
NG 可疑品
制造 合
不合格品 包装
QA检验过程 仓库不合格
包装交货过程
Q
A
合格
入
检
库
验
OQC
合格
装 箱 交
货
追
发料单
进料记录单
合格 PCB打点
产品可追溯有效性测试记录表
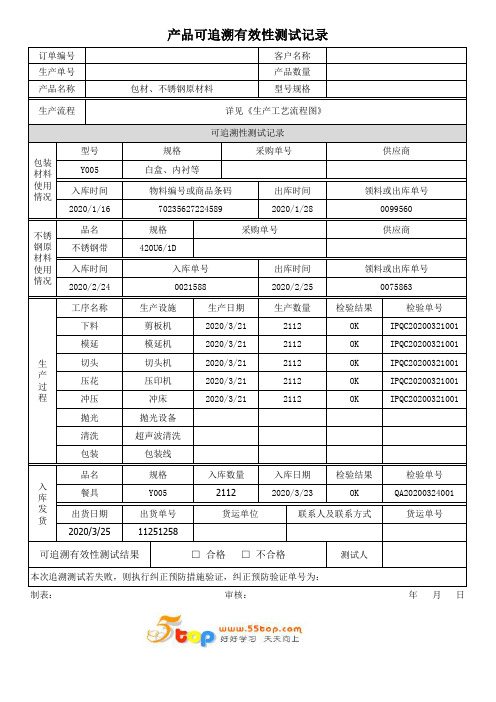
包装线
生产日期 2020/3/21 2020/3/21 2020/3/21 2020/3/21 2020/3/21
生产数量 2112 2112 2112 2112 2112
检验结果 OK OK OK OK OK
检验单号 IPQC20200321001 IPQC20200321001 IPQC20200321001 IPQC20200321001 IPQC20200321001
供应商
领料或出库单号 0099560
不锈 钢原 材料 使用 情况
品名 不锈钢带 入库时间 2020/2/24
规格 420U6/1D
入库单号 0021588
采购单号
出库时 2020/2/25
供应商
领料或出库单号 0075863
工序名称
下料
模延
生
切头
产 过
压花
程
冲压
抛光
清洗
包装
生产设施 剪板机 模延机 切头机 压印机 冲床
制表:
审核:
年月日
品名
入 库
餐具
发 货
出货日期
2020/3/25
规格 Y005 出货单号 11251258
入库数量 2112
入库日期 2020/3/23
检验结果 OK
货运单位
联系人及联系方式
检验单号 QA20200324001
货运单号
可追溯有效性测试结果
□ 合格 □ 不合格
测试人
本次追溯测试若失败,则执行纠正预防措施验证,纠正预防验证单号为:
产品可追溯有效性测试记录
订单编号 生产单号 产品名称
包材、不锈钢原材料
客户名称 产品数量 型号规格
IATF16949标识及可追溯程序(含流程表格)
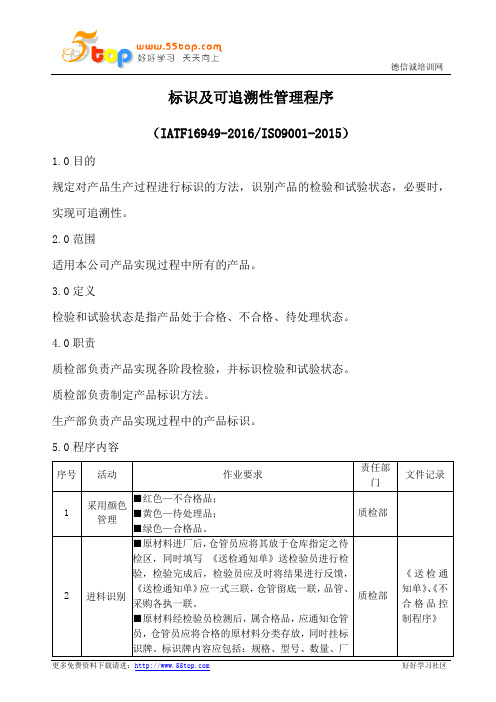
标识及可追溯性管理程序
(IATF16949-2016/ISO9001-2015)
1.0目的
规定对产品生产过程进行标识的方法,识别产品的检验和试验状态,必要时,实现可追溯性。
2.0范围
适用本公司产品实现过程中所有的产品。
3.0定义
检验和试验状态是指产品处于合格、不合格、待处理状态。
4.0职责
质检部负责产品实现各阶段检验,并标识检验和试验状态。
质检部负责制定产品标识方法。
生产部负责产品实现过程中的产品标识。
5.0程序内容
6.0相关文件
《不合格品控制程序》《检验和试验程序》《产品标识细则》《作业指导书》
《产品状态标识卡》
产品状态标识卡.xl
s
《产品异常报告书》
产品质量异常原因
及改进报告.xl s
《送检通知单》
送检通知单.d oc
《入库单》
入库单 (3).xl s。
产品追溯有效性测试记录表+召回演练记录
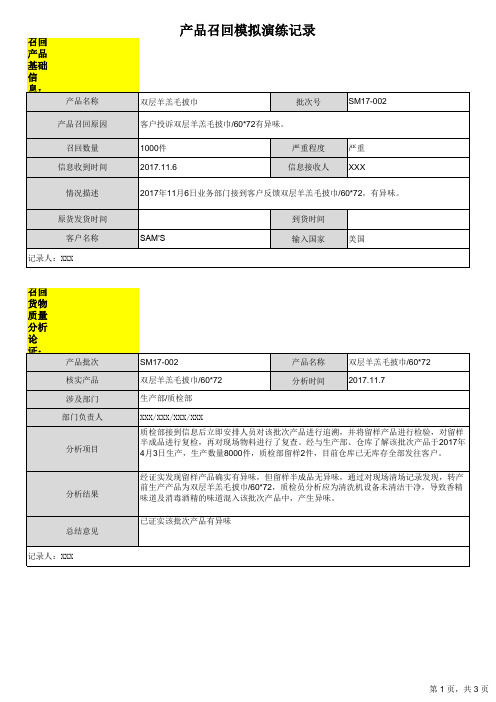
XXX/XXX/XXX/XXX
质检部接到信息后立即安排人员对该批次产品进行追溯,并将留样产品进行检验,对留样 半成品进行复检,再对现场物料进行了复查。经与生产部、仓库了解该批次产品于2017年 4月3日生产,生产数量8000件,质检部留样2件,目前仓库已无库存全部发往客户。
经证实发现留样产品确实有异味,但留样半成品无异味,通过对现场清场记录发现,转产 前生产产品为双层羊羔毛披巾/60*72,质检员分析应为清洗机设备未清洁干净,导致香精 味道及消毒酒精的味道混入该批次产品中,产生异味。
召回 产品 基础 信 息:
产品名称
产品召回原因
召回数量 信息收到时间
情况描述
原货发货时间 客户名称
记录人:XXX
召回 货物 质量 分析 论 证:
产品批次 核实产品 涉及部门 部门负责人
分析项目
分析结果
总结意见 记录人:XXX
产品召回模拟演练记录
双层羊羔毛披巾
批次号
客户投诉双层羊羔毛披巾/60*72有异味。
已证实该批次产品有异味
第 1 页,共 3 页
溯源 跟踪 文件 、记 录:
产品批次
SM17-002
召回时间
2017.11.22
溯源体系有效性评价
通过模拟演练可以追溯到原料到成品的所有记录,整个体系运行是有效事宜产计划单
所 工序生产记录
涉 及
现场生产记录
到 消毒液使用记录 的
2017.11.22
1、业务部电话通知客户停止货物流通(得知该批次产品为投入市场前抽检所得,未对外 出售) 2、船务部与客户签订退运协议,安排代理到客户端取货,通过运输方式将货物运回清 关,提货到公司。
1、仓库将召回产品单独隔离摆放。 2、质检部组织相关部门就召回产品信息进行验证,并对产品取样化验分析不合格品产生 原因。 3、行政部负责对召回的处理方法为报废的产品进行销毁。 4、业务部与顾客沟通赔偿或补偿事宜。 5、生产部负责对设备消毒员工进行教育培训加强技能学习。
产品可追溯性记录表

产品规格 产品规格及数量
产品可追溯记录表
产品名称
客户
产品数量
生产工艺流程图:来料检验→组装→焊接→整理→气密检查→喷砂→气密检查→喷涂→检验→成品出货
品名
规格 物料编号 供应商 入库时间 检验结果 附ห้องสมุดไป่ตู้据 份
原材料使 用情况
生产过程 成品入库
工序名称
组装 焊接 整理 气密检查 喷砂 气密检查 喷涂 检验
品名
成品出库
品名
生产设备
生产日期 生产数量 检验结果 附单据 份
规格
入库数量 入库日期 检验结果 附单据 份
规格
货运单位 联系人 联系方式 附单据 份
可追溯性 测试结果
合格□ 不合格□
测试人:
日
年月