推荐-23塑件的工艺性 精品
(完整版)塑料及加工工艺
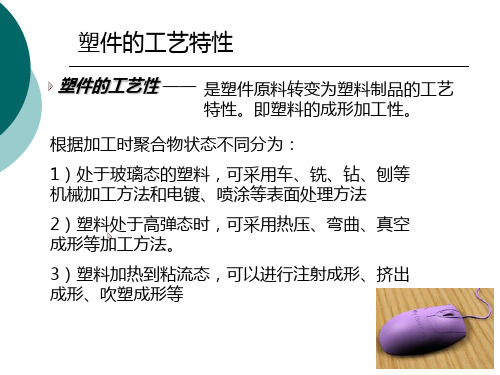
吹塑
一步法 挤—拉—吹瓶工艺流程图 1—挤出管坯;1—管坯定型;3—型坯移至拉伸吹塑模具; 4—拉伸吹塑;5—脱模
22
吹塑
吹塑成型工艺演示
23
吹塑
拉伸吹塑工艺控制 : ✓1、原材料的选择:由于拉伸制品要求具有较高的拉伸强度、 冲击强度、刚性、透明度和光泽、对氧气、二氧化碳和水蒸气 的阻隔性。主要应用的材料有:PET、PVC、PP、PC等。 ✓2、型坯成பைடு நூலகம்:透明度高,均质,内部无应变、外观无缺点 ✓3、拉伸工艺 :拉伸温度、拉伸倍率
装置、卷取装置
控制系统
3、压注成型
主要用于热固性塑料的成型方法,有模压和层压法两种。 1)模压成形:压塑成形,原理将定量的塑料原料置于金 属模具中,闭合模具,加热加压,是塑料原料塑化流动充 满模腔,同时发生化学反应固化成形。
模具闭合 热固性塑料放入加料 室 受热熔融 塑料在压力下经 浇注系统充满型腔 固化成型 开模取件
注射成型优点
1)可一次成形出外形复杂,尺寸精确和带嵌 件制品 2)可以方便的利用一套模具,成批生产尺寸、 形状、性能完全相同的产品。 3)生产性能好,成形周期短,一般制件3060秒成形。可实现自动化或半自动化作业。 4)较高的生产效率和技术经济指标。
2 挤出成型
挤出成型原理
又称挤塑成形,主要适合热塑性塑料成形,也适合一 部分流动性比较好的热固性塑料和增强塑料成形。
压注成型特点
1.加料前模具处于闭合状态。
2.塑件飞边很薄,尺寸准确,性能均匀,质量较高。 3.可以成型深孔、形状复杂、带有精细或易碎嵌件 的塑件。 4.模具结构相对复杂,制造成本较高,成型压力较 大,操作复杂,耗料比压缩模多。 5.气体难排除,一定要在模具上开设排气槽。
模具设计-塑件的结构工艺性

一般模具表面粗糙度要比塑件的要求高 1~2级。
三、塑件的几何形状
1.塑件的壁厚 (1)塑件壁厚设计原则:
①满足塑件结构和使用性能要求下取小壁厚; ②能承受推出机构等的冲击和振动; ③制品连接紧固处、嵌件埋入处等具有足够的厚度; ④保证贮存、搬运过程中强度所需的壁厚; ⑤满足成型时熔体充模所需的壁厚,见P74表3.14、3.15 ;
二、塑件的尺寸、精度和表面粗糙度
1.塑件的尺寸
(1)塑件的尺寸是指塑件的总体尺寸。 (2)塑件的尺寸受下面两个因素影响:
①塑料的流动性(大而薄的塑件充模困难) ②设备的工作能力(注射量、锁模力、工作台面)
2.塑件的精度
(1)塑件的尺寸精度是指所获得的塑件尺寸与产品图中尺寸的符合程度, 即所获塑件尺寸的准确度。 (2)影响塑件尺寸精度的因素:
塑件公差等级的选用见P70表3.10。
(3)塑件尺寸精度的确定(续)
对于塑件上孔的公差可采用基准孔,可取表中数值冠以(+)号。 对于塑件上轴的公差可采用基准轴,可取表中数值冠以(-)号。 一般配合部分尺寸精度高于非配合部分尺寸精度。
模具尺寸精度比塑件尺寸精度高2-3级。
3.塑件的表面质量
表面质量
表面粗糙度、光亮程度 色彩均匀性 表面缺陷:缩孔、凹陷 推杆痕迹 对拼缝、熔接痕、毛刺等
2.塑料原料选择方法:
使用环境: 不同的温度、湿度及介质条件、不同的受力类型选择不同的塑料;
使用对象: 使用塑料制品的国别、地区、民族和具体使用者的范围、国家不同,其
标准规格也不同。
按用途进行分类: 按应用领域分类,如汽车运输工业用、家用电气设备用、机械工业用、
建筑材料用、宇航和航空用等;按应用功能分类,如结构材料、低摩擦擦 材料、受力机械零件材料、耐热、耐腐蚀材料、电绝缘材料、透光材料等。
塑件成型工艺

塑件成型工艺一.塑件工艺分析此塑件为锥齿轮,经分析选用PC为原料,PC是一种无定型,无臭,无毒,高透明的无色或微黄色热塑性工程材料,具有优良的物理机械性能,特别是耐冲性优异;拉伸强度,弯曲强度,压缩强度高;儒变形性小,尺寸稳定,具有良好的耐热性和耐低温性,在较宽的温度范围内具有稳定的力学性能,尺寸稳定性,电性能和阳燃性,可在-6℃—12℃下长期使用,无明显熔点,在220℃—230℃虽熔融状态,由于分子键纲性大,树脂熔体粘度大,吸水率小,收缩率小,尺寸精度高,尺寸稳定性好,膜薄透气性小,属于自燃性材料;对光稳定,但不耐紫外光,耐候性好,耐油,耐酸,不耐强碱,氧化性酸及胺,酮美,溶于氧化氢类和芳香族溶剂,长期在水中易引起水解和开裂,缺点是因抗癌强度差,容易产生开裂,抗溶性差,耐磨性欠佳,用于玻璃纤维增强PC可克服上述缺点,使PC具有更好的力学性能,更好的尺寸稳定性,更小的成型收缩率,并可提高耐药性,降低成本。
1 .塑料材料成形性能使用PC注射成形塑料制品时,由于其熔体黏度较高,所需的注射成形压力较高,因此塑料对型芯的包紧力较大,故塑料应采用较大的脱模斜度。
在正常情况下,壁厚、熔料温度对收缩率的影响教小;若要求塑件精度高时,模具温度可控制在50°c ~60°c,要求塑件光泽和耐热时,应控制在60°c ~80°c;PC比热容低,速化效率高,凝固也快,固成形周期短;另外熔体黏度较高,使PC制品易产生熔接痕,所以模具设计时应注意减少浇注系统对料流的阻力。
PC的表观黏度对剪切速率的依赖性很强,因此模具设计中大都采用点浇口形式。
PC 易吸水,使塑件表面出现斑痕、云纹等。
成形加工前应进行干燥处理。
在正常的成形条件下,PC制品的尺寸稳定性较好。
2. 塑件材料的应用PC在机械工业上用来制造齿轮,泵叶轮,轴承,把手,管道,电机锥齿轮,仪表壳,仪表盘,水箱锥齿轮,蓄电池槽,冷藏库和冰箱衬里等;汽车工业上用PC制造汽车挡泥板,扶手,热空气调节管道,加热器等,还可以用PC夹层板制作小轿车车身;PC还可以用来制作水表壳,纺织器材,电器零件,文教体育用品,玩具,电子琴及收录机壳体,食品包装容器,农药喷雾器及家具等。
塑料件包装、运输工艺规范(已改)

分体机出风框:将出风框并排电机位向上竖直放入仓储笼,最上面一层平放; 分体机导风条:将覆膜后的导风条面对面放置,然后采用橡皮筋扎紧,将扎好后的导风条侧放于钙 塑箱中;对于双导风条(上、下导风条),覆膜后将上、下导风条面对面成对放置,再用用橡皮筋扎紧, 将扎好后的导风条侧放于钙塑箱中;装插销后的导风条包装方式不变。 分体机底盘后盖板:将底盘后盖板装入一个 PE 袋中后采用定枢机将袋口封住; 分体机螺丝盖:将螺丝盖装入一个 PE 袋中后采用订书机将袋口封住。 2.4 塑料件的包装注意事项 2.4.1 塑料件在包装前将产品批锋、顶白、油污等缺陷处理完好后才能包装,包装过程中需注意不要将 塑料件划伤、擦伤,严禁将不合格品包装入库; 2.4.2 不允许采用破损严重的包装袋或脏污的包装袋/布袋进行包装产品,包装后不允许将产品暴露在 外面,包装过程中必须轻拿轻放,绝对不允许有严重的摔、扔、碰撞等现象发生; 2.4.3 包装时必须保证塑料件之间以及塑料件与包装器具之间松紧适度,防止塑料件在存储、中转运输 中碰伤、变形或断裂。 2.4.4 对于喷涂塑料件,(大面积喷涂面先覆膜保护)每个单独用珍珠棉包装袋包好,再在外面加套 PE 袋或气泡袋(优先推荐使用布袋),按适度松紧的原则放入周转器具或纸箱中,每个喷涂件之间用 泡沫条或纸皮可靠隔开,外协供应商需按此方式执行; 2.4.5 采用钙塑箱或纸箱包装的塑料件,必须保证钙塑箱和纸箱完好,不变形,不破损。
Байду номын сангаас柜机
进风格栅
用布袋或珍珠棉包装袋包装后竖直放入仓储笼,喷涂件必须使 用气泡袋或珍珠棉包装袋包装
顶盖 底盘 面板
PE 袋/布袋包装后侧放入仓储笼 PE 袋/布袋包装后放入仓储笼 气泡袋/布袋包装后竖直放入仓储笼,喷涂件必须使用气泡袋或 珍珠棉包装袋包装
塑件制件结构工艺特性 3
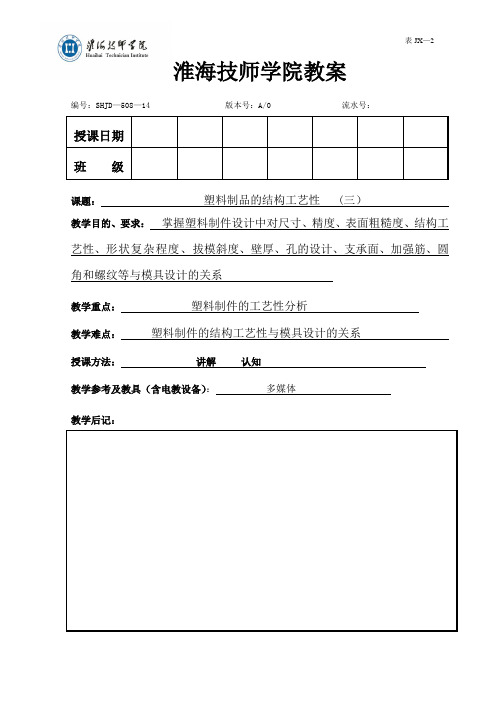
表JX—2淮海技师学院教案编号:SHJD—508—14 版本号:A/0 流水号:课题:塑料制品的结构工艺性 (三)教学重点:塑料制件的工艺性分析教学难点:塑料制件的结构工艺性与模具设计的关系授课方法:讲解认知教学参考及教具(含电教设备):多媒体教学后记:板书设计塑料制件的结构工艺性(3)【组织教学】【回顾旧课】1、塑件的形状如何设计?2、塑件的壁厚如何设计?3、什么是脱模斜度?如何设计?引言:塑料制件由于使用要求的不同,其种类繁多、形状各异,而塑料注塑成型工艺条件、注射成型设备与注射成型模具却有一定的规范要求的。
制件的结构工艺性能,是指塑料制件成型生产时对模具结构、成型工艺的适应程度。
塑料制件结构工艺性能的合理与否主要取决于制件设计。
塑料制件结构工艺性合理,即可使成型工艺稳定,保证制件质量,提高生产效率,又可使模具结构简单化,降低模具设计与制造成本。
因此,在设计制件时应充分考虑其结构工艺性能。
新课讲解:(一)塑料制品的加强肋1、目的:增加塑料制品的强度和刚度。
2、设计原则(二)塑料制品的支承面1、设计原则:(三)塑料制品的圆角(四)塑料制品上孔的设计(五)塑料制品的花纹、标记、符号及文字【课后小结】1、塑件的加强肋、支承面、圆角、孔的设计2、塑料制品的花纹、标记、符号及文字【练习与作业】1、塑件的加强肋、支承面、圆角如何设计?2、塑件的花纹、标记、符号及文字如何设计?注:要求以一块黑板的版面来进行板书设计教案纸教学过程学生活动学时分配塑料制件的结构工艺性(3)【组织教学】【回顾旧课】1、塑件的形状如何设计?2、塑件的壁厚如何设计?3、什么是脱模斜度?如何设计?引言:塑料制件由于使用要求的不同,其种类繁多、形状各异,而塑料注塑成型工艺条件、注射成型设备与注射成型模具却有一定的规范要求的。
制件的结构工艺性能,是指塑料制件成型生产时对模具结构、成型工艺的适应程度。
塑料制件结构工艺性能的合理与否主要取决于制件设计。
产品工艺性分析

新利達紋路
MT紋路
相對應出模角
#120
#MT-1100
3°
#1304
5°
#121
#MT-11010
3°
#1306
5°
#122
\
3°
#1327
7°
#124
#MT-11020
5°
#1701
2°
#125
\
6°
#1702
3°
#126
\
7°
#2207
3°
#600
\
1°
#பைடு நூலகம்224
2°
#800
\
1°
#2225
PPO+20GF
1.0035
PPS(R4)
1.002
透明ABS
1.003
GE/C1200
1.004
ULTEM 2200
1.003
軟膠
TPE
1.015
ABS+PC
1.004
RYTON R-4
1.002
SILICONE RUBBER 50%
1.015
9)另產品結構是大窗口(即多窗口碰穿)縮水率相對降低千分之二點,比如通常縮水率是
子(圖9-4所示)
3)落曲面上的孔,孔口要倒圓角,以避免出現尖銳的膠位,圖(9-5)所示,做模時,盡量前模
原裝出.
4) T形面的接合面會產生凹陷,要在模呵(Core)側邊設置鍥角減薄膠位(圖9-6)所示
5)加強筋高度的預留(圖9-7)
6)要對大於基本膠厚的部分作吊空膠處理,保證基本內厚一致,並考慮冷卻問題(9-8)
2°
#1000
塑件的结构工艺性
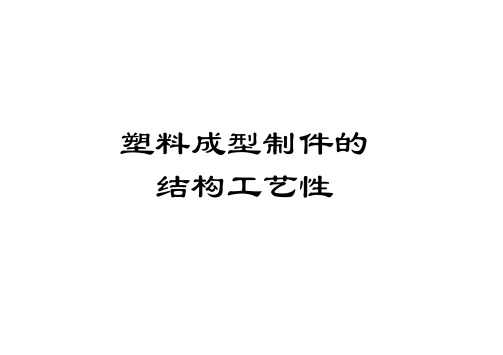
塑料成型制件的结构工艺性l塑料制件的设计是在满足使用要求的前提下,根据选用塑料的类型及其成型加工特点,确定相应而合理的成型工艺,并根据该成型工艺的特性而设计出相适应的塑料结构件。
l由于塑料有其特殊的物理机械性能,因此设计塑件时必须充分发挥其性能上的优点,避免或补偿其缺点,在满足使用要求的前提下,塑件形状应尽可能地做到简化模具结构,符合成型工艺特点。
l对于模具设计者来说,在考虑塑件的结构及有关使用要求时,还必须与成型该塑件的成型模具的相应结构结合起来考虑,既要使塑料制件能按使用要求加工出来,保证制件的质量,而又要使模具结构合理、经济。
在塑件结构工艺性设计时,应考虑以下几方面的因素:(1)塑料的各项性能特点;(2)在保证各项使用性能的前提下,塑件结构形状力求简单,且有利于充模流动、排气、补缩和高效冷却硬化(热塑性塑料制件)或快速受热固化(热固性塑料制件);(3)模具的总体结构应使模具零件易于制造,特别是抽芯和脱模机构。
一、塑料制件的选材二、塑料制件的尺寸和精度三、塑料制件的表面质量四、塑料制件的结构设计表面粗糙度表观质量形状、壁厚、斜度、加强筋、支撑面、圆角、孔、螺纹、齿轮、嵌件、铰链、标记、符号和文字等一、塑料制件的选材塑料制品的选材应考虑如下几个方面,以判断其是否能够满足使用要求。
1)塑料的力学性能,如强度、刚性、韧性、弹性、弯曲性能、冲击性能以及对应力的敏感性。
2)塑料的物理性能,如对环境温度变化的适应性、光学特性、绝热或电气绝缘的程度、精加工和外观的完满程度等。
3)塑料的化学性能,如对接触物(水、溶剂、油、药品)的耐性、卫生程度以及使用上的安全性等。
4)必要的精度,如收缩率的大小以及各向收缩率的差异。
5)成型工艺性,如塑料的流动性、结晶性、热敏性等。
对于塑料材料的这些要求往往是通过塑料的特性表进行选择和比较的。
下表列出常用塑料的特性,以供参考。
二、塑料制件的尺寸和精度1. 塑件的尺寸–总体尺寸主要取决于塑料品种的流动性Ø在一定的设备和工艺条件下,流动性好的塑料可以成型较大尺寸的塑件;反之,成型出的塑件尺寸较小。
注塑件的表面处理及工艺
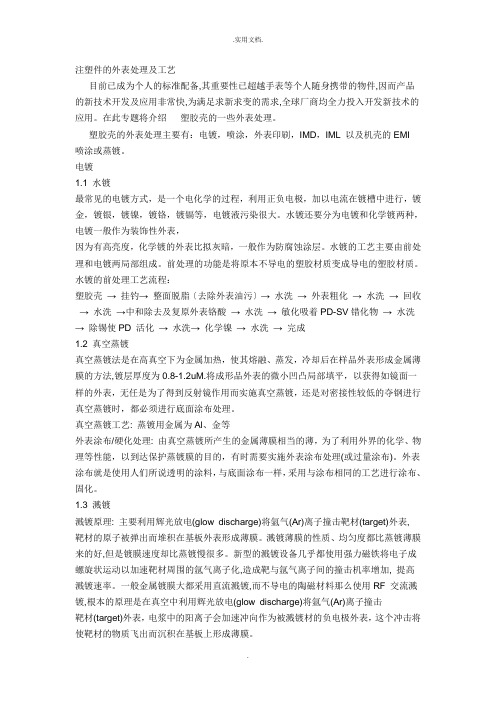
注塑件的外表处理及工艺目前已成为个人的标准配备,其重要性已超越手表等个人随身携带的物件,因而产品的新技术开发及应用非常快,为满足求新求变的需求,全球厂商均全力投入开发新技术的应用。
在此专题将介绍塑胶壳的一些外表处理。
塑胶壳的外表处理主要有:电镀,喷涂,外表印刷,IMD,IML 以及机壳的EMI喷涂或蒸镀。
电镀1.1 水镀最常见的电镀方式,是一个电化学的过程,利用正负电极,加以电流在镀槽中进行,镀金,镀银,镀镍,镀铬,镀镉等,电镀液污染很大。
水镀还要分为电镀和化学镀两种,电镀一般作为装饰性外表,因为有高亮度,化学镀的外表比拟灰暗,一般作为防腐蚀涂层。
水镀的工艺主要由前处理和电镀两局部组成。
前处理的功能是将原本不导电的塑胶材质变成导电的塑胶材质。
水镀的前处理工艺流程:塑胶壳→ 挂钓→ 整面脱脂〔去除外表油污〕→ 水洗→ 外表粗化→ 水洗→ 回收→ 水洗→中和除去及复原外表铬酸→ 水洗→ 敏化吸着PD-SV错化物→ 水洗→ 除锡使PD 活化→ 水洗→ 化学镍→ 水洗→ 完成1.2 真空蒸镀真空蒸镀法是在高真空下为金属加热,使其熔融、蒸发,冷却后在样品外表形成金属薄膜的方法,镀层厚度为0.8-1.2uM.将成形品外表的微小凹凸局部填平,以获得如镜面一样的外表,无任是为了得到反射镜作用而实施真空蒸镀,还是对密接性较低的夺钢进行真空蒸镀时,都必须进行底面涂布处理。
真空蒸镀工艺: 蒸镀用金属为Al、金等外表涂布/硬化处理: 由真空蒸镀所产生的金属薄膜相当的薄,为了利用外界的化学、物理等性能,以到达保护蒸镀膜的目的,有时需要实施外表涂布处理(或过量涂布)。
外表涂布就是使用人们所说透明的涂料,与底面涂布一样,采用与涂布相同的工艺进行涂布、固化。
1.3 溅镀溅镀原理: 主要利用辉光放电(glow discharge)将氩气(Ar)离子撞击靶材(target)外表,靶材的原子被弹出而堆积在基板外表形成薄膜。
溅镀薄膜的性质、均匀度都比蒸镀薄膜来的好,但是镀膜速度却比蒸镀慢很多。
塑件成型工艺性分析
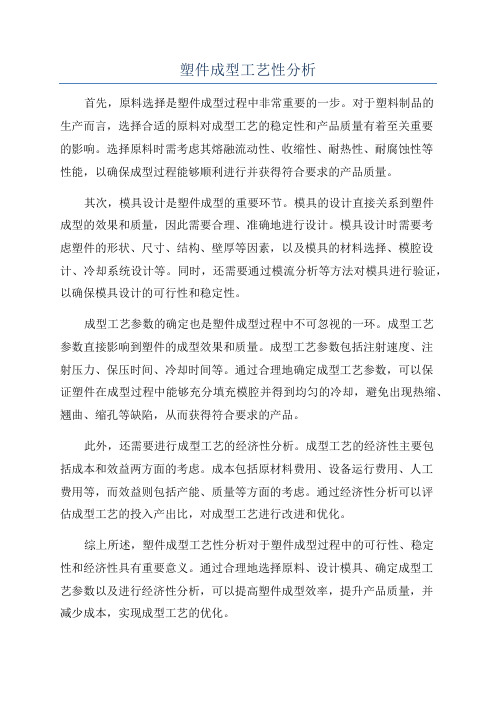
塑件成型工艺性分析首先,原料选择是塑件成型过程中非常重要的一步。
对于塑料制品的生产而言,选择合适的原料对成型工艺的稳定性和产品质量有着至关重要的影响。
选择原料时需考虑其熔融流动性、收缩性、耐热性、耐腐蚀性等性能,以确保成型过程能够顺利进行并获得符合要求的产品质量。
其次,模具设计是塑件成型的重要环节。
模具的设计直接关系到塑件成型的效果和质量,因此需要合理、准确地进行设计。
模具设计时需要考虑塑件的形状、尺寸、结构、壁厚等因素,以及模具的材料选择、模腔设计、冷却系统设计等。
同时,还需要通过模流分析等方法对模具进行验证,以确保模具设计的可行性和稳定性。
成型工艺参数的确定也是塑件成型过程中不可忽视的一环。
成型工艺参数直接影响到塑件的成型效果和质量。
成型工艺参数包括注射速度、注射压力、保压时间、冷却时间等。
通过合理地确定成型工艺参数,可以保证塑件在成型过程中能够充分填充模腔并得到均匀的冷却,避免出现热缩、翘曲、缩孔等缺陷,从而获得符合要求的产品。
此外,还需要进行成型工艺的经济性分析。
成型工艺的经济性主要包括成本和效益两方面的考虑。
成本包括原材料费用、设备运行费用、人工费用等,而效益则包括产能、质量等方面的考虑。
通过经济性分析可以评估成型工艺的投入产出比,对成型工艺进行改进和优化。
综上所述,塑件成型工艺性分析对于塑件成型过程中的可行性、稳定性和经济性具有重要意义。
通过合理地选择原料、设计模具、确定成型工艺参数以及进行经济性分析,可以提高塑件成型效率,提升产品质量,并减少成本,实现成型工艺的优化。
塑件成型工艺性分析
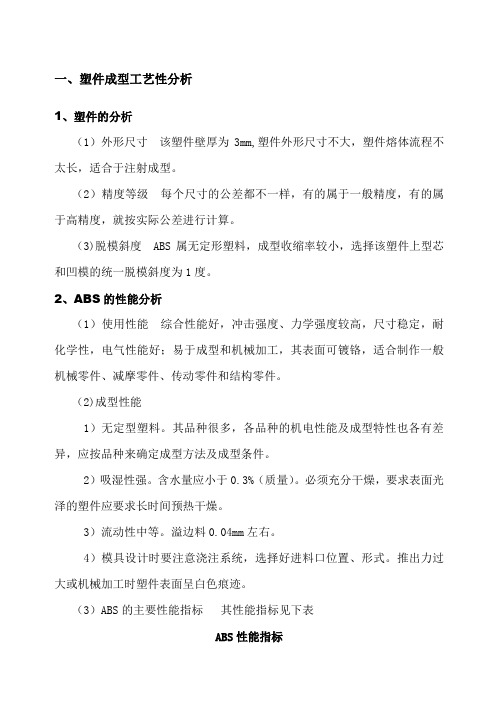
一、塑件成型工艺性分析1、塑件的分析(1)外形尺寸该塑件壁厚为3mm,塑件外形尺寸不大,塑件熔体流程不太长,适合于注射成型。
(2)精度等级每个尺寸的公差都不一样,有的属于一般精度,有的属于高精度,就按实际公差进行计算。
(3)脱模斜度 ABS属无定形塑料,成型收缩率较小,选择该塑件上型芯和凹模的统一脱模斜度为1度。
2、ABS的性能分析(1)使用性能综合性能好,冲击强度、力学强度较高,尺寸稳定,耐化学性,电气性能好;易于成型和机械加工,其表面可镀铬,适合制作一般机械零件、减摩零件、传动零件和结构零件。
(2)成型性能1)无定型塑料。
其品种很多,各品种的机电性能及成型特性也各有差异,应按品种来确定成型方法及成型条件。
2)吸湿性强。
含水量应小于0.3%(质量)。
必须充分干燥,要求表面光泽的塑件应要求长时间预热干燥。
3)流动性中等。
溢边料0.04mm左右。
4)模具设计时要注意浇注系统,选择好进料口位置、形式。
推出力过大或机械加工时塑件表面呈白色痕迹。
(3)ABS的主要性能指标其性能指标见下表ABS性能指标密度/g ·3cm 1.02~1.08 屈服强度/MPa 50 比体积/13-∙g cm0.86~0.96 拉伸强度/MPa 38 吸水率(%) 0.2~0.4 拉伸弹性模量/MPa 1.4×310熔点/C ο 130~160 抗弯强度/MPa 80 计算收缩率(%) 0.4~0.7 抗压强度/MPa 53 比热熔/1)(-∙∙C kg J ο1470弯曲弹性模量/MPa1.4310⨯3、ABS 的注射成型过程及工艺参数 (1)注射成型过程1)成型前的准备。
对ABS 的色泽、粒度和均匀度等进行检验,由于ABS 吸水性较大,成型前应进行充分的干燥。
2)注射过程。
塑件在注射机料和筒内经过加热、塑化达到流动状态后,由模具的浇注系统进入模具型腔成型,其过程可分为充模、压实、保压、倒流和冷却五个阶段。
塑件的结构工艺性
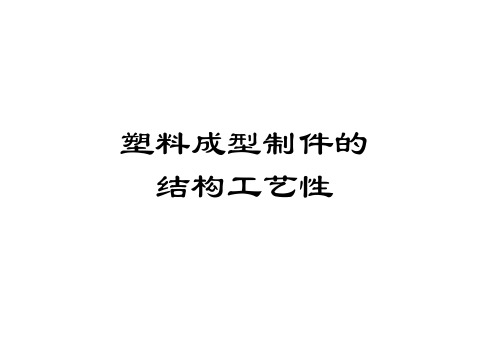
四、塑料制件的结构设计
一)成型工艺对塑件几何形状的要求
– 塑料制件的形状,首先是保证制件的使用结 构要求,并结合人们的审美观点而设计出来 的几何形状。
– 因而,随着设计者的构思方案不同,同一用 途的制件,其形状也会有不同,对此我们不 做深入讨论。
– 我们所着重论述的是有关制件设计的工艺性 与经济性,即我们设计的塑件内外表面形状 要设计得易于模塑成型。
a)不合理
b)合理
图 加强筋与支撑面
2)应避免或减小塑料的局部聚积,否 则会产生缩孔、气泡。在设计时可将实心 部位改为空心结构。
缩孔或气泡
a)不合理
b)合理
图3.6 加强筋的布排应注意避免塑料局部聚积
3)筋条排列要注意排列互相错开,这样才 能防止收缩不均匀,变形较小。
a)不合理
b)合理
图3.6 加强筋的排列方向
要能满足塑件的使用要求,应将塑件设计的尽量 紧凑、尺寸小巧一些。
2. 塑件的尺寸精度 – 是指所获得的塑件尺寸与产品图纸尺寸的符 合程度,即所获塑件尺寸的准确度。 – 影响塑件精度的因素较为复杂,塑件尺寸误 差的产生是多种因素综合影响的结果,因此, 在一般情况下塑件要达到金属制件那样的精 度是非常困难的。
l 对于模具设计者来说,在考虑塑件的结构及有关使用要 求时,还必须与成型该塑件的成型模具的相应结构结合 起来考虑,既要使塑料制件能按使用要求加工出来,保 证制件的质量,而又要使模具结构合理、经济。
在塑件结构工艺性设计时,应考虑以下几方面 的因素:
(1)塑料的各项性能特点; (2)在保证各项使用性能的前提下,塑件结 构形状力求简单,且有利于充模流动、排气、补 缩和高效冷却硬化(热塑性塑料制件)或快速受 热固化(热固性塑料制件); (3)模具的总体结构应使模具零件易于制造, 特别是抽芯和脱模机构。
精选08-09-1第3章塑件的结构工艺性idr
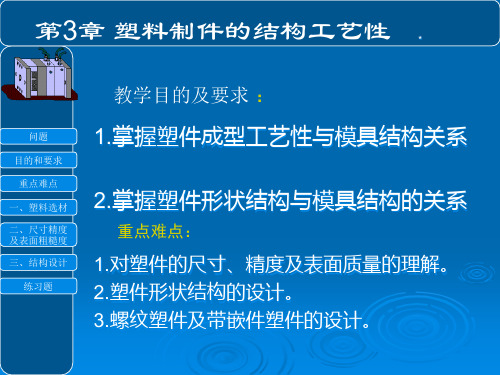
感谢您的下载观看
演讲完毕,谢谢观看!
第3章 塑料制件的结构工艺性
*
是塑件对成型加工的适应性
塑件工艺性设计的特点:满足使用性能和成形工艺的要求,力求做到结构合理、造型美观、便于制造。
第3章 塑料制件的结构工艺性
塑件的成型工艺性
*
3.1塑件的尺寸、精度
1.塑件的尺寸
第3章 塑料成型制件的结构工艺性
*
2.影响塑件尺寸精度的因素:
3.1塑件的尺寸、精度
强制脱模条件 (A-B)× 100%/ C≤5%
(A-B)×100%/C≤5%
*
*
3.4斜度设计
第3章 塑料制件的结构工艺性
当塑件成型后因塑料收缩而包紧型芯,若塑件外形较复杂时,塑件的多个面与型芯紧贴,从而脱模阻力较大。为防止脱模时塑件的表面被檫伤和推顶变形,需设脱模斜度。 一般来说,塑件高度在25mm以下者可不考虑脱模斜度。 但是,如果塑件结构复杂,即使脱模高度仅几毫米,也必须认真设计脱模斜度。
第3章 塑料制件的结构工艺性
3.13铰链
*
第3章 塑料制件的结构工艺性
3.13铰链
*
3.6 塑料制件的结构工艺性
3. 14 标记、符号、文字 塑件上的标记、符号有凸形和凹形两种。成型零件结构: 标 记、符号为凸形时,模具上就相应地为凹形,可直接在成型另件上用机械或手工雕刻或电加工等方法成型。标 记、符号为凹形时,模具上就相应地为凸形;一般尽量在有标记、符号的地方,镶上相应的镶块; 塑件上标记的凸出高度、线条宽度、两条线的间距按规范进行。
3.6加强筋
容器侧壁的增强
*
3.7支承面
第3章 塑料制件的结构工艺性
*
3.7支承面
塑料模具设计与制造

2.添加剂 ⑶稳定剂 凡能阻缓材料变质的物质称为稳定剂。 分类: 热稳定剂:它的主要作用就是抑制或防止树脂在加工或使用过程中受热而降解。 光稳定剂:它的主要作用是阻止树脂在光的作用下降解(塑料变色、力学性能下降等等)。 抗氧化剂:延缓或抑制塑料氧化速度
第二章 塑料及塑件工艺性
第二章 塑料及塑件工艺性
7.相容性(共混性) 相容性——指两种或两种以上不同品种的塑料在熔融状态下不产生相分离现象的能力。 8.塑料状态与加工性 熔融纺丝成型 注射成型 薄膜吹塑成型 挤出成型 压延成型 中空成型 真空和压力成型
第二章 塑料及塑件工艺性
二、热固性塑料的工艺性能 1.收缩性 热固性塑料收缩的表现形式、影响因素和计算方法与热塑性塑料基本相同。 2.流动性 热固性塑料流动性通常以拉西格流动性(以毫米计)来表示,数值大则流动性好。
塑料模具设计与制造
第二章 塑料及塑件工艺性
学无常师,道在则是 ——晋·潘岳 <归田赋>
第二章 塑料及塑件工艺性
问题: 1.什么是模具?什么是塑料模具? 2.塑件成型加工的三要素是什么? 3.塑料常用的成型方法有哪些?
基本内容: 1.理解塑料的概念、分类、成份; 2.理解热固性、热塑性塑料两个概念,二者的区别; 3.了解塑料的特性及用途。 重点难点: 1.重点:塑料的概念、成份、分类 2.难点:对概念的理解
第二章 塑料及塑件工艺性
材料变化
热固性塑料及其成型方法
热塑性树脂及其成型方法
材料在模具 内的行为
由于加热、加压、熔融或粘度下降 ↓ 流动 ↓ 赋性 ↓ 继续加热交联硬化
由于加热、加压、塑化或熔融 ↓ 流动 ↓ 赋性 ↓ 冷却固化
第二章 塑料及塑件工艺性
第三章 塑料成型制件的结构工艺性
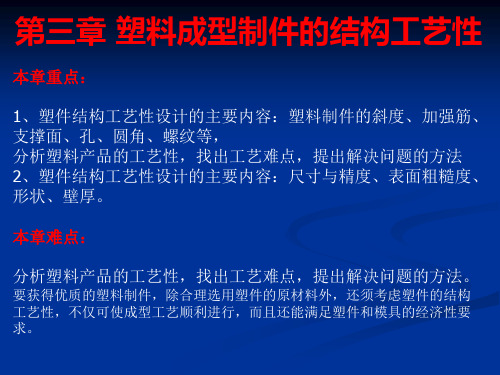
(2)塑件的表观质量 塑件的表观质量指塑件成型后的表观缺陷状态,像缺料、溢料、飞边、凹陷、 熔接痕、银纹、斑纹、翘曲与收缩、尺寸不稳定。
§3.4 脱模斜度
(1)概念:由于塑料冷却后产生收缩,在脱模前会紧紧的包住凸模(型芯) 或模腔中的凸起部分,或由于黏附作用塑件紧贴在凹模型腔内,为了便于脱 模,防止塑件表面在脱模十划伤、擦毛,在设计时塑件表面沿脱模方向应具 有合理的脱模斜度。 (2)斜度的取向原则:
内孔以小端为准,符合图纸要求,斜度由扩大方向得到; 外形以大端为准,符合图纸要求,斜度由缩小方向得到; 脱模斜度值一般不包括在塑件尺寸的公差范围。
(2)脱模斜度的确定 ☆ 塑件的脱模斜度的大小,与塑件的性质、收缩率大小、摩擦系数大小、塑件 壁厚和几何形状有关。 ☆ 在通常情况下,脱模斜度为30′~1°30′ ☆ 当塑件精度要求较高时,应选用较小的斜度,外表面斜度可小至5′,内表面可 小至10′~20′ ☆ 硬质塑料比软质塑料脱模斜度大 ☆形状较复杂、成型孔较多的塑件,引起脱模阻力较大时,取较大的脱模斜度, 可选用4°~5°塑件高度较大、孔较深,取较小的脱模斜度 ☆ 壁厚增加,应选用较大的斜度 ☆ 塑件上的加强肋单边应有4° ~5°脱模斜度 ☆ 塑件侧壁带有皮革花纹(蚀纹)时应有4° ~6°的脱模斜度
加强肋的厚度应小于塑件壁厚,并与壁用圆弧过渡,加强肋的形状尺寸如图3-2 所示:
§3.7 支承面
当塑件需要由一个面为支承面时,以整个底面作为支承面是不合理,因为塑 件稍有翘曲或变形就会造成底面不平,为了更好的起支承作用,常采用边框 (凸缘)支承或底脚(凸台)支承。
当塑件底部有加强肋时,应使加强肋与支承面相差0.5mm的高度。
一些塑件壁厚设计不合理结构与合理结构:
§3.6 加强肋
塑件的结构工艺性

塑件的结构工艺性塑件的结构工艺性是指塑件设计的结构是否符合塑料制品加工的工艺要求。
塑料制品加工过程中,考虑到成型性、冷却性、顶出性、模具等因素,设计人员需要合理地设计塑料制品的结构,以提高制品的质量和生产效率。
首先,塑件的结构应具备成型性。
成型性是指塑料在加热融化后能够在模具中形成所需形状的能力。
因此,设计人员应根据塑料材料的特性,合理选择塑胶制品的结构形式,避免在注塑过程中发生热分解、气泡和熔接线等缺陷。
其次,塑件的结构应具备良好的冷却性。
冷却性是指在塑料制品注塑过程中,塑料材料能够迅速冷却并固化。
设计人员应考虑到塑胶制品的结构形状、壁厚以及冷却系统的设置等因素,以确保塑料制品在注塑过程中能够均匀地冷却,避免出现变形和缩水等问题。
此外,塑件的结构应具备良好的顶出性。
顶出性是指塑胶制品在顶出系统的作用下,能够顺利地从模具中取出。
设计人员应注意到塑料制品的结构形状和顶出系统的设计,避免塑件在顶出过程中出现变形、折断和卡死等情况。
最后,塑件的结构应考虑到模具的制造和使用。
模具的制造和使用对塑料制品的质量和生产效率有着重要的影响。
设计人员应根据塑料制品的结构形状、尺寸和要求,合理设计模具的结构和尺寸,以便于模具的制造和使用,提高模具的寿命和生产效率。
总之,塑件的结构工艺性是塑料制品设计中需要考虑的重要因素之一。
设计人员应根据塑料材料的特性和加工工艺要求,合理设计塑料制品的结构,以提高制品的质量和生产效率。
同时,设计人员还应注意到成型性、冷却性、顶出性和模具等因素对塑料制品的影响,以确保塑料制品能够顺利地生产并符合质量要求。
塑料制品在现代工业生产中得到了广泛的应用,其轻便、耐用、成本低廉的特点使得塑料制品成为替代传统材料的理想选择。
然而,要确保塑料制品的质量和生产效率,需要充分考虑塑件的结构工艺性。
下面将继续探讨塑件的结构工艺性的相关内容。
首先,塑件的结构形式对于成型性的影响非常重要。
不同的塑件形式对于塑料材料的流动和填充具有不同的要求。
热塑性塑料(注塑成型)的工艺性能、 热固性塑塑料工艺性能-课件
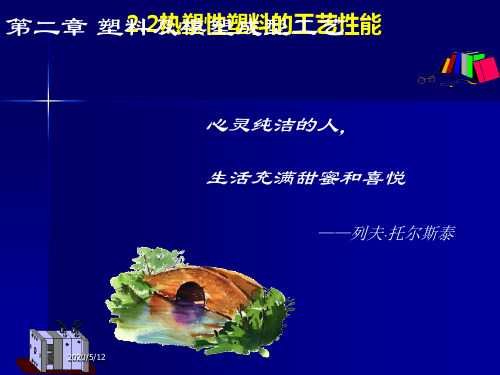
拉伸取向—由拉应力引起,取向方向与拉伸方向一致; 由拉应力引起,取向方向与拉伸方向一致; 流动取向—在切应力作用下沿着熔体流动方向形成的. 在切应力作用下沿着熔体流动方向形成的.
按流动性质不同,取向结构可分为: 按流动性质不同,取向结构可分为:
单轴取向—结构单元均沿着一个流动方向有序排列(取向); 单轴取向—结构单元均沿着一个流动方向有序排列(取向); 多轴取向—结构单元可沿两个或两个以上流动方向有序排列; 多轴取向—结构单元可沿两个或两个以上流动方向有序排列; 按结晶与非结晶聚合物分为: 按结晶与非结晶聚合物分为: 结晶取向 / 非结晶取向
a—中心层定向 最小 ; 中心层定向 b—内层定向较大; 内层定向较大; 内层定向较大 c—外层定向最大; 外层定向最大; 外层定向最大 d—表层未定向。 表层未定向。 表层未定向
20122012-2-23
定向原因: 定向原因:
2.2热塑性塑料的工艺性能 2.2热塑性塑料的工艺性能
d—未取向区 c—高度取向区 b—中等取向区 a—轻度取向区
2.2热塑性塑料的工艺性能 2.2热塑性塑料的工艺性能
定向:
在成型加工中聚合物在 某方向的压力作用下, 某方向的压力作用下,由于 剪应力造成的速度梯度的诱 导,聚合物分子在很大程度 上会顺着流动的方向整齐地 作平行的排列, 作平行的排列,这就是分子 取向的一种情况。 取向的一种情况。
d—未取向区 c—高度取向区 b—中等取向区 a—轻度取向区
2.2热塑性塑料的工艺性能 2.2热塑性塑料的工艺性能 第二章 塑料及模塑成型工艺
心灵纯洁的人, 生活充满甜蜜和喜悦
——列夫·托尔斯泰
20122012-2-23
2.2热塑性塑料的工艺性能 2.2热塑性塑料的工艺性能 2.2热塑性塑料的工艺性能
塑件结构工艺性
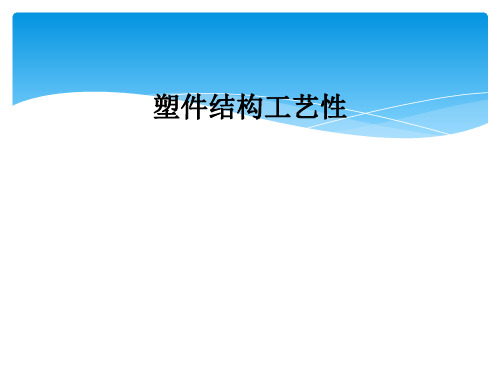
(4)塑件支承面的设计
当塑件上有一面作为支承面来使用时,将该 面设计为一个整面是不合理的,应采用如图319所示结构。
因为平板状在成型收缩后很容易翘曲变形, 稍许不平都会影响良好的支承作用,故以边框 式或底脚(三点或四点)结构设计塑件支承面。 如下图塑料盘所示。
对于细长型芯,为防止其弯曲变形,在 不影响塑件的条件下,可在塑件的下方设 支承柱来支撑。如图3-25所示。
斜孔或形状复杂的孔可采用拼合的型 芯来成型。如图7.5所示
5 带嵌件塑件的设计
在塑件内嵌入其他零件形成不可卸的连接,所嵌入 的零件即称嵌件。嵌件材料一般为金属材料,也有用 非金属材料的,例如玻璃、木材或已成型的塑件。 1、塑件中镶入嵌件的目的:
3.1 形状
当塑件的内外侧凹陷较浅,同时成 型塑件的塑料为聚乙烯、聚丙烯、聚 甲醛这类仍带有足够弹性的塑料时, 模具可采取强制脱模。
3 形状和结构设计
3.2 结构设计
为使强制脱模时的脱模阻力不要过大引 起塑件损坏和变形,塑件侧凹深度必须 在要求的合理范围内,见p222图7.2下 面的说明(公式),同时还要重视将凹凸起 伏处设计为圆角或斜面过渡结构。
增加局部强度、硬度、耐磨、导磁、导电性能,加 强塑件尺寸精度和形状的稳定性,起装饰作用等。 2、嵌件结构有柱状、针杆状、片状和框架等如图334所示。
5 带嵌件塑件的设计
3、嵌件设计的要点: ⑴ 嵌件应可靠地固定在塑件中,防止嵌
件在塑件中转动或被抽离。柱状嵌件可 在外形滚直纹并切出沟槽,或在外表面 滚菱形花纹。针杆状嵌件可切口或冲孔。 如图3-34所示。
3.5.3 模塑螺纹的结构设计
注塑指导工程塑料的成形工艺
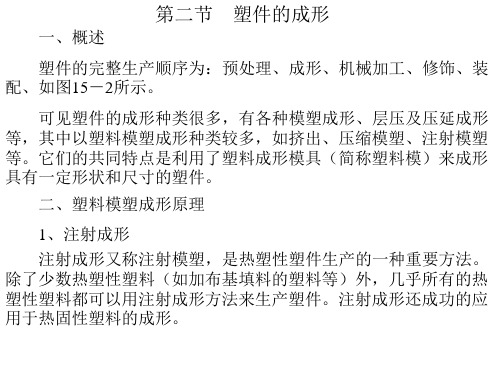
一、形状
塑件的内外表面应设计得易于模塑,尽可能不采用复杂的瓣合 分模与侧抽芯方式。
二、壁厚
塑件的壁厚首先取决于塑件的使用要求,即强度、结构、质量、 电性能、尺寸稳定性及装配要求等。从工艺性能方面考虑,应尽可 能使塑件的壁厚均匀,塑件的壁厚为1~6mm比较合适,工程上一般 为2~4mm。
三、脱模斜度
脱模斜度一般为0.5°~1.5°,对于有花纹的塑件增大到4°~5°
3、压铸(注)成形
压铸成形又称为传递模塑。它是在改进压制成形的缺点,并吸 收注射成形的优点的基础上发展起来的一种 模塑方法,其成形原 理如图所示。
压制和压铸的区别在于:前者塑料在加料腔内加热加压熔化并 成形;后者塑料在加热腔内加热熔化,并通过浇注系统而快速射入 模具型腔,也是在压力下凝固成形。
压铸成形的优点是:可以模塑成形带有深孔的及其复杂形状的 塑件,也可模塑精细的、易碎的嵌件;塑件的飞边小,尺寸准确, 性能均匀,品质较高;模具的磨损较小。其缺点也有
以及薄膜等。一条挤出生产线包括挤出成型机、挤出模具、冷却定
型装置、牵引装置、切割或卷取装置及控制系统。挤出机由挤压系
统、传动系统、加热冷却系统组成。挤压系统包括螺杆、料筒、料
斗等。
挤出过程
切割及堆放装置 牵引装置
冷却水槽
定型装置 挤出模具 挤出机
- 1、下载文档前请自行甄别文档内容的完整性,平台不提供额外的编辑、内容补充、找答案等附加服务。
- 2、"仅部分预览"的文档,不可在线预览部分如存在完整性等问题,可反馈申请退款(可完整预览的文档不适用该条件!)。
- 3、如文档侵犯您的权益,请联系客服反馈,我们会尽快为您处理(人工客服工作时间:9:00-18:30)。
君子壹教,弟子壹学,亟成!
2021/1/10
问题:
1.什么是塑料的收缩性?影响收缩率的因素有哪些? 2.什么是塑料的流动性?影响流动性的因素有哪些? 3.什么是塑料的相容性?用在什么地方? 4.热固性塑料的水分及挥发物的来源?有什么危害?怎么防止?
2021/1/10
内容简介: 1.掌握塑件的尺寸精度和表面粗糙度; 2.掌握塑件的结构设计(脱模斜度、加强筋、圆 角设计、支承面及凸台)。
MT7级精度最低
会根据教材表2-5(常用材料模塑件公差等级 和选用)选择塑件公差等级
2.3塑件的工艺性
一、塑件的尺寸、精度和表面粗糙度
2.塑件的精度
2021/1/10
A项:不受模具活动部分影响的尺寸公差值 B项:受模具活动部分影响的尺寸公差值
2.3塑件的工艺性
一、塑件的尺寸、精度和表面粗糙度
2021/1/10
2.3塑件的工艺性
二、塑件的几何形状
2021/1/10
5.圆角 在满足使用要求的前提下,制件的所有的转角尽
可能设计成圆角,或者用圆弧过渡。
⑴圆角的作用:
圆角可避免应力集中,提 高制件强度
圆角可有利于充模和脱模
圆角有利于模具制造,提 高模具强度
2.3塑件的工艺性
二、塑件的几何形状
5.圆角
⑵圆角的确定:
2.塑件的精度 尺寸精度的确定:
对于塑件上孔的公差可采用基准孔,可取表
中数值冠以(+)号。
对于塑件上轴的公差可采用基准轴,可取表
中数值冠以(-)号。
一般配合部分尺寸精度高于非配合部分尺寸 精度。
模具尺寸精度比塑件尺寸精度高2-3级。
2.3塑件的工艺性
一、塑件的尺寸、精度和表面粗糙度
3.塑件的表面质量
一、塑料材料的选择(分析)
塑料的选材包括:选定塑料基体聚合物(树脂)
种类、塑料具体牌号、添加剂种类与用量等
塑料原料选择方法:
使用环境(不同的温度、湿度及介质条件、不同的受 力类型选择不同的塑料)
使用对象(根据国别、地区、民族和具体使用者的 不同选材 )
按用途进行分类 (按应用领域 、功能 )
2.3塑件的工艺性
2021/1/10
表面粗糙度、光亮程度
色彩均匀性
表面质量 表面缺陷:缩孔、凹陷
推杆痕迹
对拼缝、熔接痕、毛刺等
一般模具表面粗糙度要比塑件的要求高 1~2级
2.3塑件的工艺性
2021/1/10
二、塑件的几何形状
1.表面形状
塑件的内外表面形状应尽可能保证有利于成型
2.3塑件的工艺性
二、塑件的几何形状
1.表面形状
图中尺寸的符合程度,即所获塑件尺寸的准确度。
影响塑件尺寸精度的因素:
模具的制造精度、磨损程度和安装误差
塑料收缩率的波动以及成型时工艺条件的变化
塑件成型后的时效变化
2.3塑件的工艺性
二、塑件的尺寸、精度和表面粗糙度
2.塑件的精度
2021/1/10
尺寸ห้องสมุดไป่ตู้度的确定:
模塑件公差代号为MT (附录E)
MT1级精度最高(一般不采用)
二、塑件的尺寸、精度和表面粗糙度
1.塑件的尺寸
2021/1/10
塑件的尺寸 —— 指塑件的总体尺寸
塑件的尺寸受下面两个因素影响:
塑料的流动性(大而薄的塑件充模困难)
设备的工作能力(注射量、锁模力、工作台面)
2.3塑件的工艺性
二、塑件的尺寸、精度和表面粗糙度
2021/1/10
2.塑件的精度
塑件的尺寸精度是指所获得的塑件尺寸与产品
塑件精度高,采用较小脱模斜度
尺寸高的塑件,采用较小脱模斜度
塑件形状复杂不易脱模,选用较大斜度
增强塑料采用较大的脱模斜度
收缩率大,斜度加大
2.3塑件的工艺性
2021/1/10
二、塑件的几何形状
2.脱模斜度 脱模斜度设计要点:
含润滑剂的塑料采用较小脱模斜度
从留模方位考虑: 留在型芯,内表面脱模斜度﹤外表面 留在型腔,外表面脱模斜度﹤内表面
2021/1/10
2.3塑件的工艺性
2021/1/10
二、塑件的几何形状
2.脱模斜度
为了便于塑件脱模,防止脱模时擦伤塑件,必 须在塑件内外表面脱模方向上留有足够的斜度α,
在模具上称为脱模斜度。
脱模斜度取决于 塑件的形状、壁厚 及塑料的收缩率,
一般取30 ′~
1°30′。
2.3塑件的工艺性
二、塑件的几何形状
3.塑件的壁厚 壁厚过小
强度及刚度不足,塑料流动 困难
壁厚过大
原料浪费,冷却时间长,易 产生缺陷
2.3塑件的工艺性
二、塑件的几何形状
2021/1/10
3.塑件的壁厚
塑件壁厚设计原则:
满足塑件结构和使用性能要求下取小壁厚
能承受推出机构等的冲击和振动
制品连接紧固处、嵌件埋入处等具有足够的厚度
保证贮存、搬运过程中强度所需的壁厚
重点难点: 会分析产品的工艺性能
2.3塑件的工艺性
2021/1/10
塑件的工艺性 ——是塑件对成型加工的适应性
塑件工艺性设计包括 :塑料材料选择、尺寸精 度和表面粗糙度、塑件结构
塑件工艺性设计的特点:应当满足使用性能和 成形工艺的要求,力求做到结构合理、造型美 观、便于制造。
2.3塑件的工艺性
2021/1/10
它能提高制件的强度、防止 和避免塑料的变形和翘曲。
⑵加强筋设计要点:
加强筋的底部与壁连接应圆弧过渡,以防外 力作用时,产生应力集中而被破坏。
平板类零件加强筋方 向与料流方向平行
2.3塑件的工艺性
二、塑件的几何形状
4.塑件的加强筋
⑵加强筋设计要点:
加强筋厚度小 于壁厚
加强筋与支承 面间留有间隙
2021/1/10
内壁圆角半径应为壁厚的一半
2021/1/10
外壁圆角半径可为壁厚的1.5倍
一般圆角半径不应小于0.5mm 壁厚不等的两壁转角可按平均壁厚确定内、外圆 角半径
理想的内圆角半径应为壁厚的1/3以上
2.脱模斜度
脱 模 斜 度 方 向
2021/1/10
外形以大端为基准,斜度由缩小方向取得 内形以小端为基准,斜度由扩大方向取得
2.3塑件的工艺性
二、塑件的几何形状
2.脱模斜度 脱模斜度表示方法:
2021/1/10
2.3塑件的工艺性
二、塑件的几何形状
2.脱模斜度
脱模斜度设计要点:
2021/1/10
满足成型时熔体充模所需的壁厚
厚薄适中 均匀壁厚
2.3塑件的工艺性
二、塑件的几何形状
3.塑件的壁厚 改善壁厚典型实例:
2021/1/10
2.3塑件的工艺性
二、塑件的几何形状
3.塑件的壁厚 改善壁厚练习:
2021/1/10
2.3塑件的工艺性
二、塑件的几何形状
2021/1/10
4.塑件的加强筋
⑴加强筋的作用: