石油化工装置管桥配管设计
石油化工装置管桥配管设计

石油化工装置管桥配管设计在石油化工装置中,管桥和配管设计是至关重要的一部分。
管桥配管设计方案的有效性和优化程度直接影响石化装置的生产效率和安全稳定运行。
管桥是指为连接厂区内各设备之间的管道而建造的桥梁状结构。
管桥的主要作用是将管道联通起来,便于维护,检修和管理,同时也方便设备之间的液体或气体传输。
管道配管是指将接在管道上的配管,用各类管件连接成一个完整的管网系统,使介质(气体或者液体)在整个制程中顺畅流动,实现石油化工过程中的生产目标。
管桥配管在石化装置中起着至关重要的作用,影响着整个装置的平稳运行和安全生产。
因此,在管桥配管设计方案的优化上,需要考虑多方面的因素,如安全性、流量与压力的匹配、配管材质的选择、管道路线布局、系统的运行易维护等。
对于管道的安全性,管桥的承重肯定是第一位考虑的问题,不仅要保证安全使用,而且也要考虑系统的防震措施及的配套保护措施。
在高温,高压,高浓度的腐蚀环境,管道使用的保温和防腐措施是必不可少的。
同时,也需要根据环境要求考虑相关的加热或降温设备,以确保管道介质处于稳定的温度及压力下运行。
在流量与压力匹配上, 支路管和主配管之间,以及不同流量介质管道交汇处的压力和流量的匹配问题,也是需要优先考虑的问题。
无论是流量过大还是过小,都有可能使得管道整体的流动压力变化不利于介质正常传输。
同时,设计者需要考虑到介质流动的方向和速度,以不同的管道材料来控制流速和流动的方向,保证介质传输畅通无阻。
管道选用材质也是一个需要仔细思考的问题,常见的管道材料有碳钢、不锈钢、镍合金等。
在建设中需要根据管道管路的特点、介质的特性、环境的特性、使用寿命等诸多因素综合考虑。
在选材过程中也需要考虑到可维护性、耐腐蚀性和密封性等问题,以确保管道的长期运行和维护成本。
管道布局对整个系统的稳定运行同样至关重要。
优良的布局可以使得管道的生产性能达到最优,减少系统的维修和运维成本。
切忌布局过于复杂或者混乱,使得整个系统难以维护、难以检修,从而影响到生产效率和安全性。
石油化工装置管桥管道设计要则

当管桥上相邻 的管道 上有法兰或 阀门时, 应尽 量交错布 置, 可 以减小管道 间距并 方便做 保 温防腐 , 同时还 应考虑 管 道 的热胀及 收缩空间 , 尤 其对 于相 邻 “ 叮 r ” 形弯, 应 充分考 虑 偏移量 , 留够变形空 间 , 避免对 相邻 管道 产生 牵扯力 。靠 近 柱子的管道 与柱 子的净距一般应 不小于 1 0 0 m m。
要求合理 易操 作检 修 , 外 观的形象设计 也会对整个装置 的美 观度影 响甚 大。 管桥部分 的管 道设 计需 要统 筹 考虑 、 协 调分 区设 计 , 从
1 . 3 管 桥 的高度
管桥第一层 的高度 由以下几个 因素的最 大高度来决定 : ( 1 ) 当跨 越 主要 道 路 时 , 梁底 与 地 面 的净 空不 宜小 于 4 . 5 m, 如果 同时作 为大型 吊车通道 , 则不宜小于 5 . 5 m; ( 2 ) 管桥下方 有小 型设 备 时 , 考 虑操 作 和检修 , 净 高宜
第7 期
杨 会林 : 石油 化工装置管桥管道设计要则
・1 6 3・
石 油 化 工 装 置 管桥 管 道 设 计 要 则
杨 会 林
( 中石化洛 阳工程有 限公 司配管室 , 广东 广州 5 1 0 6 2 0 )
摘要 : 论述 了管桥作为整个装置 的桥 梁的重要作用 , 介绍 了管桥 的柱距 、 宽度 以及 高度 的确 定、 管道 的布置 、 热力管道 的柔性设计 以及支 吊架的设置 , 最后还着重指 出了一些重要管道 的布置方案注意事项。为此部分的管道设计提供 了借鉴 。 关键词 : 管桥 ; 柔性设计 ; 支 吊架 中图分类号 : T E 9 7 3 . 1 文献标 识码 : B 文章编号 : 1 0 0 8 — 0 2 1 X ( 2 0 1 4 ) 0 7 — 0 1 6 3 — 0 2
石油化工中装置用管道设计
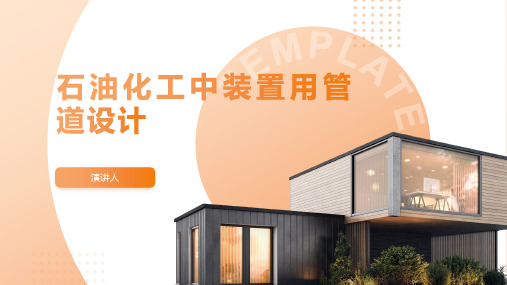
经济性
01
选用合适的材料和规格,降低成本
02
优化管道布局,减少材料消耗
03
采用先进的设计方法和技术,提高设计效率
04
考虑管道的维护和更换成本,提高使用寿命
可靠性
1
管道设计应满 足生产工艺要 求,保证生产
安全
3
管道设计应采 用成熟的技术 和材料,保证
使用寿命
2
管道设计应考 虑环境因素, 如温度、压力、
06
安全措施:设置安全阀、压 力表等安全装置,确保管道 运行安全
防泄漏措施
01
采用高质量的 管道材料和连
接件
02
设计合理的管 道布局和走向
03
安装可靠的泄 漏检测和报警
系统
04
定期进行管道检 查和维护,确保
管道安全可靠
降低能耗
1 优化管道布局:减少管道长度,降低能耗 2 采用节能材料:选择低能耗、环保的材料 3 优化管道尺寸:选择合适的管道尺寸,降低能耗 4 采用节能技术:采用节能技术,降低能耗 5 定期维护保养:定期维护保养管道,降低能耗 6 优化管道设计:优化管道设计,降低能耗
演讲人
目录
01. 管道设计的基本原则 02. 管道设计的主要内容 03. 管道设计的特殊要求 04. 管道设计的优化策略
安全性
01
材料选择:选用耐腐蚀、 耐高温、耐高压的材料
02
设计压力:根据实际需 求,合理设计管道的压 力等级
03
结构设计:确保管道的 强度和刚度,防止变形 和断裂
04
安全防护:设置安全阀、 泄压阀等安全装置,防 止事故发生
04
管道设计还需 要考虑耐高温、 耐高压等性能 要求。
石油化工装置配管设计问题探讨

石油化工装置配管设计问题探讨摘要:本文介绍了石油化工装置配管设计中要注意的几个问题,对无泄漏平台,附塔管道支架核算,密闭排放,不锈钢管线安装设计,管道热补偿等等进行探讨。
关键词:配管设计附塔管道支架密闭排放管道热补偿由于石油化工装置输送介质具有高温、高压、易燃易爆、有毒等特性,配管设计过程中为保证装置安全生产,需要注意的问题很多,本文结合设计工作经验,就容易忽视的配管设计方面的几个问题与大家共同探讨。
1 无泄漏平台在《石油化工企业设计防火规范》GB50160-2008第5.7.5条,“有可燃液体设备的多层建筑物或构筑物的楼板应采取防止可燃液体泄漏至下层的措施”,就是考虑到可燃液体设备泄漏或破裂时,设计要做到可燃液体不要泄漏至下层引起火灾爆炸事故。
近几年在设计过程中都实施无泄漏平台,比如某公司的1800万吨油品质量升级项目,某公司的1400万吨炼油改造项目等等。
具体设计实施时,考虑了以下几个方面:1)有可燃液体设备的多层建筑物或构筑物的平台设计为无泄漏平台,四周设150mm高的封闭挡板(围堰),楼梯口设圆滑过渡。
2)平台板管道开洞处设置套管,套管与平台封闭焊,套管高度高出平台150mm。
4)排液管收集的可燃液体或雨水接至地面围堰内,去雨污分流系统。
有毒的可燃液体应单独收集处理。
5)空冷器布置在操作温度等于或高于自燃点的可燃液体设备上方时,空冷器下方的平台设计为无泄漏平台。
6)液化烃泵、可燃液体泵上方布置甲、乙、丙类工艺设备时,泵上方的平台设计为无泄漏平台。
2 密闭排放石油化工装置生产过程中从原料到产品大多是有毒、易燃、易爆介质,近年来HSE要求越来越严格,设计过程中应将有毒及可燃介质排放至密闭回收系统,图1是某对二甲苯装置设计的密闭排放型式,主要排放介质大多是芳烃,属有毒物质。
在石油化工装置设计中,这种排放形式可用于有毒或可燃介质作参考。
3口径较大的附塔管道支架设计现在的炼油装置日益大型化,装置处理量大,处理油品的塔径较大,塔顶挥发线口径也相应增大,配管设计中要做好这些大口径附塔管线的支架设计。
海川化工论坛B石油化工装置管桥配管设计

海川化工论坛B石油化工装置管桥配管设计海川化工论坛B石油化工装置管桥配管设计随着社会的发展,石油化工装置的规模越来越大,设备和管道的数量也随之增加。
而这些设备和管道的连接起到了关键的作用,因此管桥配管设计成为了石油化工装置的重要组成部分之一。
本文将讨论海川化工公司B石油化工装置的管桥配管设计,以及在其设计过程中需要注意的问题。
海川化工公司B石油化工装置的管桥配管设计需要考虑许多因素,如油品流量、管道压力、维护的需要等等。
首先,设计师需要考虑石油化工装置的整体布局,并确定管道的走向和需要连接的设备。
在确定了这些因素后,设计师才能开始考虑具体的管道和设备的尺寸和规格。
然后,设计师需要考虑管桥的尺寸以及其与设备之间的距离。
这些因素将直接影响到管道的数量和尺寸。
在设计过程中,还需要考虑材料的选择。
由于石油化工装置的环境条件十分苛刻,因此管道和配件的材料需要具有足够的耐腐蚀性和耐压性。
同时,由于管道和配件需要经常维护和更换,因此设计师需要考虑材料的可焊性和可拆卸性。
常见的材料包括不锈钢、碳钢以及合金钢等。
在选择材料时,还需要考虑其成本和可用性等因素。
在管桥配管设计中,还需要考虑一些特殊的问题。
例如,设计师需要考虑在管道中使用的盲板、支架和附件等。
盲板可用于关闭管道和设备,而支架和附件可用于支撑管道和连接管道到设备。
在选择盲板、支架和附件时,需要考虑它们的尺寸、重量和材料等因素。
在进行管桥配管设计时,还需要考虑其与其他设备和管道之间的协调。
例如,设计师需要考虑将管道和配件安装在哪些位置以便其与其他设备和管道之间的连接。
此外,在进行设计时还需要考虑维护和检修的需要。
例如,设计师需要考虑在管道和设备之间留有足够的空间以便进行维护和检修。
综上所述,管桥配管设计是石油化工装置中的重要组成部分之一。
在进行设计时,需要考虑很多因素,如管道尺寸和规格、材料的选择、盲板和支架的使用以及与其他设备和管道的协调等。
在设计过程中,需要注意细节并做好充分的准备工作,以确保设计的效果达到预期的目标,并为石油化工装置的正常运行提供保障。
论石油化工装置夹套管的配管设计

论石油化工装置夹套管的配管设计1. 引言1.1 研究背景在石油化工装置中,夹套管广泛应用于各种反应釜、换热器、蒸发器等设备中,用于加热、冷却、蒸发等工艺操作。
由于夹套管的设计和配管布局直接影响着传热效果和能耗,因此对夹套管的设计原则和配管布局进行深入研究显得尤为重要。
本文旨在探讨石油化工装置夹套管的配管设计,通过对夹套管的概念、分类、设计原则、配管布局以及安装注意事项进行系统总结和分析,为石油化工装置的夹套管设计提供理论支持和实际指导。
希望通过本文的研究,能够为石油化工装置夹套管的设计与应用提供参考,提高装置的运行效率和安全性。
1.2 研究意义石油化工装置中的夹套管在工艺流程中起着至关重要的作用。
其设计合理与否直接影响到装置的运行效率和安全性。
对夹套管的配管设计进行研究具有重要的意义。
夹套管的设计可以直接影响装置的工艺参数和热效率。
通过合理设计夹套管,可以提高传热效率,减少能源消耗,降低生产成本,提高装置的生产效率。
夹套管的设计还与装置的安全性密切相关。
合理设计夹套管可以有效防止工作介质泄漏和渗漏,减少事故发生的可能性,保证装置的安全运行。
夹套管的配管设计研究对于提高石油化工行业的整体技术水平和竞争力具有重要意义。
随着石油化工行业的发展,装置规模和复杂度不断增加,对夹套管的设计要求也越来越高。
通过研究夹套管的配管设计,可以不断提升我国石油化工行业的技术水平,加强装置的设备管理和运行维护,推动行业的持续健康发展。
研究夹套管的配管设计具有重要的意义,不仅可以提高装置的工艺参数和安全性,还能促进石油化工行业的发展和技术进步。
深入开展这方面的研究对于加强我国石油化工行业的核心竞争力和可持续发展具有重要意义。
1.3 研究目的石油化工装置中,夹套管作为重要的配管设备,在工艺流程中扮演着至关重要的角色。
本文旨在对夹套管的配管设计进行深入研究,探讨其在石油化工装置中的应用及优化方法。
研究目的主要包括以下几个方面:深入了解夹套管的概念及分类,掌握其基本特性和功能;总结夹套管的设计原则,为实际工程中的设计提供指导;探讨夹套管的配管布局,优化工艺流程,提高装置运行效率;总结夹套管安装中的注意事项,确保工程施工质量及安全。
石油化工中装置用管道设计
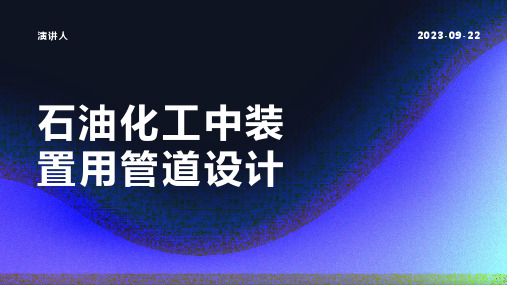
计算管道的压力 损失和流量
• 设计原则:安全、经济、环保 • 管道类型:输油管道、输气管道、输水管道等 • 管道材料:碳钢、不锈钢、合金钢等 • 管道布置:根据炼油厂工艺流程和设备布局进行合理布置 • 管道连接:采用焊接、法兰连接等方法 • 管道防腐:采用涂层、阴极保护等方法进行防腐处理 • 管道检测:采用超声波、射线等方法进行管道检测 • 管道维护:定期进行管道检查、维修和更换 • 管道安全:设置安全阀、压力表等安全装置,确保管道运行安全 • 管道优化:根据实际运行情况,不断优化管道设计和管理,提高管道运行效率
某化工厂管道设计
01
设计原则:安全、 经济、环保、可靠
05
管道连接:焊接、 法兰连接、螺纹连
接等
02
管道类型:压力管 道、真空管道、高 温管道、低温管道
等
06
管道防腐:采用涂 层、衬里、阴极保 护等方法进行防腐
处理
03
管道材料:碳钢、 不锈钢、合金钢、
塑料等
04
管道布置:根据工 艺流程、设备布局、 操作方便等因素进
施工等数据
方案设计
1
确定管道类型:根据输送介质、压力、
温度等要求选择合适的管道类型
2
确定管道尺寸:根据流量、流速、压力
损失等因素计算管道的直径和壁厚
3
确定管道布局:根据工艺流程、设备布 局等因素确定管道的走向和连接方式
4
确定管道材料:根据输送介质的腐蚀性、 温度等因素选择合适的管道材料
5
确定管道附件:根据管道类型和布局选
04 流量波动计算:根据管道
输送的介质、温度、流速 等因素,计算管道内的流 量波动,确定管道的直径 和长度。
管道设计流程
海川化工论坛- 40B212石油化工装置管桥配管设计

1 范围本标准规定了工艺装臵内常用的管桥(管廊)形式、平面布臵、立面布臵和管桥的配管设计以及相邻区关系和安全设施等的设计。
本标准适用于石油化工装臵内部管桥(管廊)的配管设计,不适用于石油化工装臵外部管带的设计。
2 管桥的平面布置2.1 一般以管桥作为全装臵的联系纽带,在管桥两侧布臵工艺设备。
管桥布臵以直通形为基本形,亦可呈L 形、T 形、U 形等组合形,如图1所示。
2.2管桥下有输送剧毒、易燃、可燃介质有机泵和储存剧毒、易燃、可燃介质的工艺设备时,机泵和设备与加热炉、变电所、配电室和仪表室的距离应符合GB50160-92《石油化工企业设计防火规范》(以下简称《防火规范》的规定。
2.3管桥柱中心线与塔器外壁或框架柱中心线间的距离,要满足管道排列和最小通道的要求,一般以4m 为宜,有往返较多的合金钢管时,经核算后,可适当减小间距,当其间布臵地下管网时应考虑地下基础与管网排列所需的最小间距。
2.4 管桥宽度第2 页共12 页40B212-19972.4.1管桥上布臵空气冷却器(以下简称“空冷器”)时,宽度应考虑空冷器构架的要求。
2.4.2管桥下布臵机泵和工艺设备时,宽度应考虑设备和通道的要求。
2.4.3管桥的宽度一般应预留10%~20%的余量;2.4.4考虑管桥宽度余量时,柱外侧一般可焊接悬臂梁,作为支撑部分工艺、仪表管道、电气仪表槽盒之用,亦可作为管桥宽度的预留余量的一部分。
2.5管桥的柱距应由管道的跨距来决定,同时还应考虑管桥上、下布臵的工艺设备等因素,一般在6~9m内取等距布臵为宜。
对于一两根极限跨距小于管桥柱间距的管道,可用临近的大管道支吊;对于多根小管道则采用加次梁的办法来支吊。
管桥在跨越道路或检修通道外,柱距应为10~15m,柱间梁宜采用桁架结构,桁架梁底距道路净空不小于4.5m。
2.6管桥下布臵机泵或工艺设备时,其地面应高出周围地面100~200mm,并分区取同一标高,电缆沟宜布臵在泵的电机端,管桥下不布臵工艺设备时,地面应作为装臵竖向地面的一部分。
石油化工装置管道设计

石油化工装置管道设计1 导言工艺管道设计是石油化工装置项目过程中的一个重要环节,因为工艺管道的设计、安装质量直接关系到石油化工装置项目总体的质量水平。
石油化工装置工艺管道的设计具有技术性强,安装内容复杂等特点,想要有效提升石油化工装置工艺管道设计的质量水平,就要在规范合理设计的同时充分掌握实际施工中的关键点。
2 石油化工装置管道设计的常见问题①仪表元件设计的常见问题,目前,在管道设计中所应用的仪表元件普遍存在着测量不够精准的问题,其测量数据难以保障,这会对于石油化工装置的运行带来负面影响;②管道支吊架设计的常见问题,管道的铺设安装离不开管道支吊架的支撑。
石油化工装置涉及到较多的安全问题,在管道支吊架的设计过程当中有时更加注重实用性而忽视了安全性;③塔和容器管线设计的常见问题,塔和容器部分的管线设计有时会出现不满足工艺流程的要求,如出现袋形及阀组位置摆放不合适,或支吊架设置不合理,如导向架的间距、承重支架的位置不合适等问题;④泵的管线设计的常见问题,泵的管线的设计是管道设计的重要环节,为了使泵正常良好运转,其管道的布置对其性能影响很大;⑤冷换设备管线设计的常见问题,冷换设备的管线设计最忌随意布置,成组的换热设备管道布置不协调,造成了后期清洗维修困难。
3 石油化工装置管道设计要点①提升仪表元件测量的准确性,进行仪表元件的安装布置时,应保障所有安装环节满足测量精准度的需求,充分考虑到介质的流向及管件的布置对测量精准性的影响,同时应避免外界环境对仪表运行的干扰;②管道布置设计的要点,对于管道布置进行设计是石油化工管道设计的重要步骤之一,相关设计人员需要对管道的施工检修和工艺过程进行全面了解。
在对安全阀出口和放空总管道进行连接设计的时候,尤其在安全阀的定压超过了7MPa时,安全阀出口管道需要以45°倾斜角沿着介质流向从上部接入放空总管,这样可以相对有效地避免逆流情况出现,除此之外,还可以降低安全阀的背压情况;③确保塔和容器管线部分设计的合理性,最典型的是对于分馏塔、汽提塔以及回馏罐之间管线的布置应进行合理的安排,使其满足工艺流程的同时,不出现袋形;④管道支架的设计要点,在管道支架设置过程中需考虑支撑点处在垂直方向位移,倘若没有垂直位移,就需要用刚性支架进行支撑;当管道垂直位移较小时,可以使用可调支吊架或者是可变弹簧支吊架;当管道垂直位移较大时,就需使用恒力弹簧支吊架;⑤科学合理的进行泵的管线设计,泵的进口管线设计,主要应做到步步低,不能出现U形,满足管道柔性需求,使管嘴受力在要求之内,做到两点的同时,应注意降低管道入口的压降;⑥正确布置换热器管道的同时注意设备的清洗检修,首先,应当满足设备之间通行的净距,确保换热器与阀门及其他设备之间可以保持安全操作通行的空间;⑦取样管道的安装设计,为了了解介质的特性和操作的状态,在某些管道上会设置取样。
论石油化工装置夹套管的配管设计

论石油化工装置夹套管的配管设计石油化工装置中的夹套管是一种安装在压力容器、反应釜等设备上的管道系统。
它通常由内壳管、夹层管和外壳管组成,内壳管用来装载反应介质,夹层管用来装载加热或冷却介质,外壳管则用来装载绝热层和保护层。
夹套管的配管设计对于石油化工装置的运行安全和保持温度的稳定非常重要。
下面将从配管材料选择、压力计算、夹套管布置以及绝热层设计等方面对夹套管的配管设计进行讨论。
在选择夹套管的配管材料时,需要考虑介质的性质、温度和压力等因素。
常见的夹套管材料包括碳钢、不锈钢和合金钢等。
根据介质的特性,可以选择耐腐蚀、耐高温或耐低温材料。
对于夹套管内外壳管和夹层管之间的焊接连接,应选择具有良好焊接性能的选材,确保连接的强度和密封性。
在进行夹套管的压力计算时,需要考虑内壳管和夹层管的内压力、外壳管的外压力以及夹层管与内外壳管之间的压差。
根据工艺要求和安全标准,可以确定夹套管的安全工作压力和试验压力。
压力计算通常采用ASME压力容器标准或国内标准进行。
然后,在夹套管布置设计中,应考虑夹套管的工艺需求和操作便利性。
夹套管可以采用单管或多管布置,单管布置适用于反应釜等容器,多管布置适用于热交换器等设备。
夹套管的布置需要考虑介质流动的均匀性和传热效果,以及设备的结构强度和紧凑性。
在绝热层设计中,要根据工艺要求和介质温度确定绝热层的厚度和材料。
绝热材料可以使用石棉、玻璃棉、硅酸盐板等,同时还要考虑绝热层的保护层和固定方式。
绝热层的设计旨在降低能量损失和避免设备外壳温度过高。
石油化工装置夹套管的配管设计需要综合考虑介质性质、温度压力、工艺要求和安全标准等因素。
合理的配管设计可以确保夹套管的运行安全和性能稳定。
具体的配管设计要根据具体的工艺要求和设备特点进行调整,并充分考虑施工和维护的难易程度。
论石油化工装置夹套管的配管设计

论石油化工装置夹套管的配管设计石油化工装置夹套管是在设备装置内部容器的外壁上设置的一种管道,主要用于传热或传质等工艺需要。
夹套管的配管设计对于石油化工装置的正常运行至关重要。
以下是关于石油化工装置夹套管配管设计的一些考虑因素。
夹套管的材质选择是十分重要的。
由于夹套管的工作环境多为高温、高压下的腐蚀介质,因此夹套管的材质应具有良好的抗腐蚀性能。
常用的夹套管材质包括碳钢、不锈钢、合金钢等。
在选择夹套管材质时,需要考虑介质的性质、工作温度、压力等因素。
夹套管的布置方式也是需要考虑的因素之一。
夹套管可以采用串流布置或并流布置。
在串流布置中,介质依次经过每一条夹套管,并流布置中,介质同时经过多条夹套管。
根据实际情况,采用合适的夹套管布置方式,以提高传热或传质效果。
夹套管的配管设计还需要考虑夹套管与设备的连接方式。
常用的连接方式包括螺纹连接、法兰连接等。
在选择连接方式时,需考虑到方便拆卸、维修等因素,以确保设备的正常操作和维护。
夹套管的配管设计还需要考虑传热介质的流量、速度等参数。
流量过大可能导致热量无法充分传递,而流量过小则会影响传热效果。
建议根据实际情况,合理设计夹套管的流量,以确保传热效果的良好。
在夹套管的配管设计中,还需考虑到夹套管的绝热设计。
绝热层的设计可以有效减少传热过程中的热量损失,提高传热效率。
常用的绝热材料包括矿棉、气凝胶等,根据实际情况选择合适的绝热材料,并合理设计绝热层的厚度。
石油化工装置夹套管的配管设计需要考虑夹套管材质选择、布置方式、连接方式、传热流量和速度、绝热设计等多个因素。
只有合理设计和选择,才能确保夹套管在石油化工装置内的正常运行和工艺要求的满足。
石油化工装置工艺及管道设计

石油化工装置工艺及管道设计一、石油化工装置工艺设计1.概述石油化工装置是将石油、天然气及其化学衍生物作为原料,经过一系列化学反应、分离、精炼、加工等工艺过程,制备出石油化工产品的核心设备。
石油化工装置工艺设计的目的是根据原料特性、产品质量要求、节能、环保等要求,在保证生产经济效益的前提下,制定合理的工艺路线,优化工艺流程,提高产品质量,保障生产安全。
2.工艺路线设计工艺路线设计是指在原料特性、产品质量要求、节能、环保等方面的要求下,制定合理的工艺路线。
工艺路线的制定涉及到原料的选择、加工、分离、反应、产出等各个方面的问题。
制定工艺路线的关键是要根据原料从接收到产出的全过程的特性,确定出最佳的原料加工和输送方案,以保证生产效率,整个过程必须规范、合理,且必须符合法律和监管机构的规定。
3.工艺流程设计工艺流程设计是指在工艺路线的基础上,确定生产过程中各个工段和工序及其相应的操作工艺和设备,进一步确定产品加工的细节问题。
设计工艺流程时,应选用先进的工艺技术,使工艺流程能够简洁高效,且易于控制。
同时,在设计过程中,还必须考虑到设备的选型、设备简化、空气净化和废气处理等方面,确保石油化工生产的环境保护和安全。
4.设备选型为了设计出一套良好的石油化工装置,必须对选择的设备进行仔细的评估和选择。
设备选型的考虑因素包括:通过量、操作条件、要求的质量、使用寿命、安全性、维修及清洁要求、能源消耗等方面。
一般情况下,应选择尽量先进的设备,以达到生产率高、生产成本低、效益好的目的。
5.控制系统的设计控制系统的设计是石油化工装置设计的关键之一,其重要性在于可靠地保证生产过程的每一步的正常运行,以防止由于异常操作或缺陷导致的生产故障,同时,对于容易产生危险的操作环节,应当给予足够的关注,使工艺过程得以安全进行。
控制系统要考虑到各个设备和操作流程的相互作用,以最大限度地优化整个过程的效率和经济性。
二、管道设计1.输送介质的选择管道设计的首要任务是要选择合适的输送介质,由于不同的介质有着不同的化学、物理性质,因此需要不同的设计参数,有些介质也要求进行特殊的处理以适应输送管线的要求。
石油化工装置液化烃管道配管设计

1、石油化工装臵液化烃管道配管设计应符合GB 5 0 3 1 6 、SH 3 0 1 2 和SEPD 0 0 0 1 中的有关配管设计的规定。
2、液化烃管道,除必须采用法兰连接外,应采用焊接连接。
3、液化烃管道不得穿越与其无关的装臵、生产单元、设施和建筑物,液化烃的采样管道不应引入化验室。
4、液化烃管道应架空或沿地敷设。
如受条件限制必须在管沟内敷设时,必须采取填砂等防止气体在管沟内积聚的措施或防火措施,并在进、出装臵及厂房处密封隔断,管沟内的污水应经水封井排入生产污水管道。
5、液化烃管道布臵在多层管廊上时,应设在下层,不得与高温管道相邻布臵,与氧气管道平行敷设时宜用不燃物料管道隔开,或保持不小于2 5 0 mm 的净距。
6、液化烃管道的低点排凝和高点放气,应设两道闸阀或设一道闸阀并加丝堵、管帽或盲法兰。
7、液化烃管道横穿铁路或道路时应敷设在套管内。
套管上方最小覆盖厚度,从套管顶到轨底不应小于1 . 4 m,从套管顶到道路表面不应小于1 . 0 m,套管应伸出铁路或道路两侧边线0 . 5 m~1 . 0 m。
在套管内的管道上,不应有焊缝。
否则,应加强焊缝无损检测。
8、下列部位的液化烃管道应隔热: a ) 长时间处于太阳照射的泵入口管道; b ) 长时间处于太阳照射的泵出口管道且无安全阀保护; c ) 调节阀、安全阀后的管道; d ) 生产工艺需要的管道。
9、在两端有可能关闭且因外界影响可能导致升压的液化烃管道上,应设隔热层和安全阀,安全阀出口管应接至低压气体泄放总管。
1 0、液化烃管道的停工泄压管公称直径DN≥5 0 时,应从上方4 5 o顺流向斜接至低压气体泄放总管。
1 1、液化烃管道的停工吹扫,应连接固定氮气吹扫管。
凡考虑停工切割或焊接的,还应设蒸汽吹扫接头并加盲法兰或丝堵。
1 2、液化烃管道的热补偿,宜为自然补偿或采用“∏”型补偿器。
1 3、液化烃管道宜用氩弧焊打底,手工电弧焊盖面。
1 4、液化烃管道属SHB 类管道,但从安全考虑,其射线探伤数量宜予增加,转动口不得小于2 0 %,固定口为1 0 0 %。
论石油化工装置夹套管的配管设计

论石油化工装置夹套管的配管设计1. 引言1.1 背景介绍石油化工装置是石油化工行业中常见的设备,用于生产石油化工产品。
夹套管是石油化工装置中的重要配管部件,用于在设备内外形成一层套管,以实现对介质的加热、降温、保温或保冷。
夹套管的设计与安装直接影响到石油化工装置的运行效率与安全性。
对夹套管配管设计进行研究和优化至关重要。
本文将就夹套管的功能和作用、选材原则、布局设计、配管方法以及安装注意事项进行探讨,旨在为石油化工领域的工程师和设计师提供实用的指导和建议。
通过对夹套管配管设计的深入分析和研究,不仅可以提高石油化工装置的工作效率和安全性,还可以为未来石油化工装置的设计与改进提供参考。
1.2 研究目的本文的研究目的主要是针对石油化工装置夹套管的配管设计进行深入探讨和分析。
通过研究夹套管的功能和作用、选材原则、布局设计、配管方法以及安装注意事项,旨在为石油化工装置的夹套管设计提供参考和指导,提高装置的安全性、稳定性和效率。
通过对夹套管配管设计的研究,探讨夹套管在石油化工装置中的重要性,对其未来的发展趋势进行预测和展望。
本文旨在总结夹套管配管设计的关键技术和要点,为石油化工行业的相关工作者提供有益的参考和借鉴。
通过深入研究夹套管配管设计,为石油化工装置的运行管理和安全生产提供更有效的技术支持和指导。
2. 正文2.1 夹套管的功能和作用夹套管是石油化工装置中常用的一种管道装置,其主要功能和作用包括以下几个方面:1. 温度控制:夹套管可以用来控制管道内介质的温度,通过往夹套管中注入或排出不同温度的介质,实现对管道内介质温度的控制。
2. 冷却效果:在一些需要保持管道内介质温度恒定的情况下,夹套管可以起到冷却的作用,通过注入低温介质来达到冷却效果。
3. 加热效果:相反地,夹套管也可以用于加热管道内介质,通过注入高温介质来加热管道内介质,适用于一些需要加热的工艺。
4. 防冻保温:在寒冷环境下,夹套管还可以用来防止管道内介质结冰,通过保持管道内介质的温度,避免管道结冰导致故障。
石油化工装置管廊上管道设计的要点

若需切断一侧装置管路,应确保其他装置管线不受影响,或在安全范围内连锁切断,确保各个装置连锁顺畅。
整个装置系统设计可能较为复杂,因此在管廊管路设计之前应考虑整个厂区装置的总系统走向,结合项目实际生产要求,考虑大局面更好的完善管廊管道设计要求。
2.2 管廊上管道的安全设计对于管廊上的管道设计工作,在实践阶段会受到各类复杂因素的影响。
因此在进行管道设计之前,要对管廊有良好的统筹规划,利用合理的经验对管廊配管进行探究。
首先要对全厂性管廊上布管有良好的统筹,全厂性管廊或管墩应确保留有10%~30%的裕量,同时要考虑其荷载。
对于装置内部的管廊应保留10%~20%的裕量同时考虑荷载。
管廊上方可布置空气冷却设备,下方可布置泵换热器或者其他小型设备。
对管道线路深入分析,确定线路正确安排以及布置阶段的各项工作要求。
线路布置的好坏,会直接影响项目工程后续工作的落实情况。
因此在实践阶段,必要考虑安全设计的要求。
比方说在管道施工阶段,选择危险系数相对较小的材料,在设计阶段要尽可能地避免使用,有危害的装置材料或技术类型,利用这种技术处理方法,能够将管道应用过程中危险事故形成的概率降低。
2.3 做好管廊结构基础控制现如今我国诸多化工装置中管廊的结构形式为架空敷设。
如果有特殊的要求,也会考虑地下敷设。
管廊的主要作用为承接各装置区联通的管道,在管道设计阶段,需要考虑管廊整体结构的安全性、稳定性。
管廊的主要结构基本为混凝土材料、钢梁钢柱梁结构。
要做好管道整体系统对于结构影响的考量,比如部分管道在管廊上的占位一旦过了主装置区,就不在占据管位,那么辅助设施处的管廊结构应考虑适当压缩或取消,考虑做T 型架空单柱管廊,以节约并控制成本[2]。
1 石油化工管廊上管道设计的基本类型分析石油化工装置的特点,在管道两侧按照流程顺序,合理布置各种应用设备,管廊的形状要根据设备的平面布置要求设定。
如果系统应用小型装置,则设备数量相对较少,所以会应用一端式或直通式管廊。
石油化工装置中配管的设计与施工问题

石油化工装置中配管的设计与施工问题摘要:随着社会经济发展水平的不断提高,石油化工企业得以快速发展,并被人们应用到了日常的生产生活中,成为推动我国经济发展的重要因素,甚至会直接影响到石油化工企业的诸多生产环节。
因此,在石油化工装置的安装施工中,要做好配管的设计施工工作,保证装置结构的安全使用,促进石油化工企业的稳定化发展。
关键词:石油化工装置;配管设计施工;常见施工问题;有效解决措施一、石油化工装置中配管的设计分析(一)石油化工装置中夹套管的配管设计问题夹套管在石油化工企业中的应用,主要分为热水形式、热油形式、蒸汽形式等,而按照夹套管的结构可以将其划分为完全形式和不完全形式。
所以,在实际的设计工作中,需要结合不同形式的夹套管进行合理设计。
首先,夹套管的设计长度要控制在15m左右,并且在设计过程中需要对其实际长度进行严格控制,主要是因为其长度尺寸直接决定了管内流体的基本特征和实际流量,所以需要严格按照标准要求进行科学合理设计。
其次,要注重内外管的热应力,主要是因为其与内外管的实际温度存在密切关系。
因此,在实际的设计工作中,设计人员需要充分考虑到这点。
如果内外管之间存在较为明显的热应力,这就需要在管内设置膨胀节,并针对弯头处的外观直径进行修改,保证其在外力作用下能够满足膨胀位移需求。
(二)石油化工装置中蒸汽管道配管设计问题在石油化工企业的经营发展过程中,蒸汽是企业应用较为广泛的工程物料,根据实际的操作压力能够将蒸汽划分为不同形式,并且其实际工作温度能够达到200℃~530℃。
而这种高温环境导致实际的操作难度增加,因此,为了保证蒸汽管的安全使用,施工单位需要实际的设计过程中注意到以下几方面的内容。
第一,需要按照不同等级的压力来布置蒸汽管道,并且蒸汽管道在实际的布置过程中需要布置在距离管廊最近的位置,这样便于π形补偿器的合理设置。
而且,当蒸汽管内的热膨胀到某种程度时,能有效根据热膨胀收集所需要的蒸汽。
第二,设置管廊蒸汽排液管道,主要是因为在实际的运行中超高压蒸汽管道内部会出现大量的蒸汽凝液,这就需要在靠近主管道或者在操作便捷的位置设置阀门进行排液操作。
浅谈石化装置管廊布置及配管设计

配營技术石油化工设计Petrochemical Design2017,34(3)浅谈石化装置管廊布置及配管设计郑琦(中国石化工程建设有限公司,北京100101)摘要:以某异丁烷装置为例,从管廊的基本参数、平台布置及管道布置三方面进行经济合理性研究,阐述了管廊布置的设计要点。
通过优化管管廊布置,合理利用管廊上的空间,达到节约项目投资成本,设计美观、合理的目的。
关键词:管廊管道平台布置doi:10. 3969/j.issn. 1005 - 8168.2017.03.013随着市场竞争力加大,为了进一步提高经济 效益,对异丁烷装置的优化势在必行。
99. 9%高 浓度的异丁烷产品作为标准气体及制冷剂的使 用,对延长压缩机使用寿命、保护臭氧层、减缓全 球气候变暖、保护生态环境具有积极深远意义。
管廊是石化装置的重要组成部分,是整个装 置衔接各个部分分区管道的重要枢纽,起着承上 启下的作用。
一个好的管廊布置不仅可以使管道 设计更加合理,还能降低整个装置的投资和运行 成本。
1管廊布置及参数的确定1.1管廊布置确定管廊的基本形式因素很多,首先是装置 所处的位置、占地面积、地形地貌,其次是周围环 境,如原料罐、成品罐的位置,装置外厂区管廊的 位置,相邻装置的布置形式等等。
管廊在装置中 作为联系主要设备的核心,应布置在装置的适中 位置。
一般石油化工装置,在设备较少的情况下,通常选用一端式或直通式管廊;设备较多时可根 据情况选用“\型、“t”型或“n”型管廊。
以某厂60万t/a异丁烷装置为例,如图1所 示该装置南北长176 m,东西宽56 m,占地9 856 m2,主管廊平行于装置长边,南北方向贯穿装置,设备以工艺流程顺序布置在管廊左右两侧。
考虑 到装置外管廊的位置及物料介质走向,大部分管 道由东侧管廊进出,少部分管道由西侧管廊进出,从而避免管道在装置外绕行敷设的现象,使管道 布置更加合理。
为节省占地及空间,管廊下方通常可集中布 置泵及小型过滤器等设备。
石油化工装置中配管的设计与施工问题

石油化工装置中配管的设计与施工问题摘要:随着社会经济的快速发展,我国的石化行业也取得了史无前例的发展与突破,同时,石化行业也成为了影响我国经济发展的一个重要因素。
石油化工的高效生产离不开石油化工装置,通过对其进行全面的配管设计与施工,能够使石油化工装置不断地创新与突破,从而真正地满足多种石油化工生产的需求,从而达到可持续发展的目的。
关键词:石油化工;装置;配管设计;施工问题;引言:在石油化工企业发展中,起着至关重要的作用的就是装置,而配管是装置中的关键组成,其作用就是从工艺流程角度,按照各种生产要求,有机连接管道与设备的进出关键,这样所有设备彼此之间就可以实现有机联系,形成一个完整的系统。
在石化工业的发展过程中,为了确保装置的平稳运转,从而提高了化工的生产效率,必须采用管道。
然而,从现实的角度来看,目前的配管设计和施工还存在着一定的局限性,使得其所能发挥出来的效用无法达到最大,甚至会影响到设备的高效稳定运行。
在这种情况下,就需要通过科学的、行之有效的设计和施工方法,来保证石油化工配管设计的实际效益,从而推动石油化工行业的整体发展。
1.为保证石油化工装置泵的配管设计安全石油化工管道大多被用来输送易燃易爆和腐蚀性较强的介质,因此,在对石油化工装置泵的配管进行设计的时候,要加强对泄漏的重视,同时要加强对火灾的防范,这样才能有效地防止安全事故的发生。
在石化企业的泵站上,可设置报警装置,保证设备能在应急状态下停止运转,防止机器对操作者的安全造成危害。
与此同时,通过对国内外技术的研究,以及对我国有关法律法规的调查,可以更全面地对工艺设备进行检测,从而避免在设备和装置的使用过程中存在的违规问题。
2.石油化工装置中配管施工常见问题2.1尺寸和标准不符合要求首先,当管线在建造过程中,若管线的外径与壁厚与设计不符,将造成管线无法经受住高温、高压介质的撞击,引发泄漏、断裂等安全事故。
其次,在管道建设过程中,若管道中的弯头、三通等部件尺寸不一致,将造成管道走向与设计不符,进而影响流体流动,增大管道阻力,降低过程效率。
石油化工装置管桥配管设计
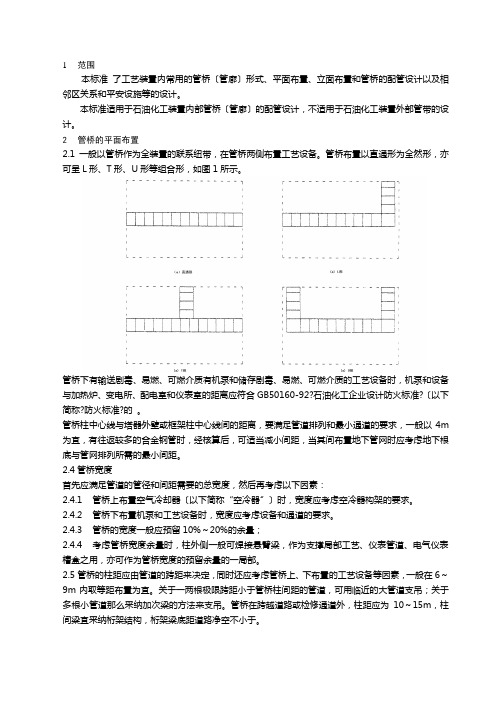
1范围本标准了工艺装置内常用的管桥〔管廊〕形式、平面布置、立面布置和管桥的配管设计以及相邻区关系和平安设施等的设计。
本标准适用于石油化工装置内部管桥〔管廊〕的配管设计,不适用于石油化工装置外部管带的设计。
2管桥的平面布置2.1一般以管桥作为全装置的联系纽带,在管桥两侧布置工艺设备。
管桥布置以直通形为全然形,亦可呈L形、T形、U形等组合形,如图1所示。
管桥下有输送剧毒、易燃、可燃介质有机泵和储存剧毒、易燃、可燃介质的工艺设备时,机泵和设备与加热炉、变电所、配电室和仪表室的距离应符合GB50160-92?石油化工企业设计防火标准?〔以下简称?防火标准?的。
管桥柱中心线与塔器外壁或框架柱中心线间的距离,要满足管道排列和最小通道的要求,一般以4m 为宜,有往返较多的合金钢管时,经核算后,可适当减小间距,当其间布置地下管网时应考虑地下根底与管网排列所需的最小间距。
2.4管桥宽度首先应满足管道的管径和间距需要的总宽度,然后再考虑以下因素:2.4.1管桥上布置空气冷却器〔以下简称“空冷器〞〕时,宽度应考虑空冷器构架的要求。
2.4.2管桥下布置机泵和工艺设备时,宽度应考虑设备和通道的要求。
2.4.3管桥的宽度一般应预留10%~20%的余量;2.4.4考虑管桥宽度余量时,柱外侧一般可焊接悬臂梁,作为支撑局部工艺、仪表管道、电气仪表槽盒之用,亦可作为管桥宽度的预留余量的一局部。
2.5管桥的柱距应由管道的跨距来决定,同时还应考虑管桥上、下布置的工艺设备等因素,一般在6~9m内取等距布置为宜。
关于一两根极限跨距小于管桥柱间距的管道,可用临近的大管道支吊;关于多根小管道那么采纳加次梁的方法来支吊。
管桥在跨越道路或检修通道外,柱距应为10~15m,柱间梁宜采纳桁架结构,桁架梁底距道路净空不小于。
2.6管桥下布置机泵或工艺设备时,其地面应高出四面地面100~200mm,并分区取同一标高,电缆沟宜布置在泵的电机端,管桥下不布置工艺设备时,地面应作为装置竖向地面的一局部。
- 1、下载文档前请自行甄别文档内容的完整性,平台不提供额外的编辑、内容补充、找答案等附加服务。
- 2、"仅部分预览"的文档,不可在线预览部分如存在完整性等问题,可反馈申请退款(可完整预览的文档不适用该条件!)。
- 3、如文档侵犯您的权益,请联系客服反馈,我们会尽快为您处理(人工客服工作时间:9:00-18:30)。
1范围
本标准规定了工艺装置内常用的管桥(管廊)形式、平面布置、立面布置和管桥的配管设计以及相邻区关系和安全设施等的设计。
本标准适用于石油化工装置内部管桥(管廊)的配管设计,不适用于石油化工装置外部管带的设计。
2管桥的平面布置
2.1 一般以管桥作为全装置的联系纽带,在管桥两侧布置工艺设备。
管桥布置以直通形为基本形,亦可呈L形、T形、U形等组合形,如图1所示。
2.2管桥下有输送剧毒、易燃、可燃介质有机泵和储存剧毒、易燃、可燃介质的工艺设备时,机泵和设备与加热炉、变电所、配电室和仪表室的距离应符合GB50160-92《石油化工企业设计防火规范》(以下简称《防火规范》的规定。
2.3管桥柱中心线与塔器外壁或框架柱中心线间的距离,要满足管道排列和最小通道的要求,一般以4m为宜,有往返较多的合金钢管时,经核算后,可适当减小间距,当其间布置地下管网时应考虑地下基础与管网排列所需的最小间距。
2.4 管桥宽度
首先应满足管道的管径和间距需要的总宽度,然后再考虑以下因素:
2.4.1管桥上布置空气冷却器(以下简称“空冷器”)时,宽度应考虑空冷器构架的要求。
2.4.2管桥下布置机泵和工艺设备时,宽度应考虑设备和通道的要求。
2.4.3管桥的宽度一般应预留10%~20%的余量;
2.4.4考虑管桥宽度余量时,柱外侧一般可焊接悬臂梁,作为支撑部分工艺、仪表管道、电气仪表槽盒之用,亦可作为管桥宽度的预留余量的一部分。
2.5管桥的柱距应由管道的跨距来决定,同时还应考虑管桥上、下布置的工艺设备等因素,一般在6~9m内取等距布置为宜。
对于一两根极限跨距小于管桥柱间距的管道,可用临近的大管道支吊;对于多根小管道则采用加次梁的办法来支吊。
管桥在跨越道路或检修通道外,柱距应为10~15m,柱间梁宜采用桁架结构,桁架梁底距道路净空不小于4.5m。
2.6管桥下布置机泵或工艺设备时,其地面应高出周围地面100~200mm,并分区取同一标高,电缆沟宜布置在泵的电机端,管桥下不布置工艺设备时,地面应作为装置竖向地面的一部分。
2.7管桥上布置工艺设备时,应设置隔断平台并与附近的塔或框架平台相连接。
管桥顶层管道靠近塔器的外侧,可以考虑布置电气仪表槽盒(槽盒一侧也可作为走道)。
管桥上的连通平台应设操作、检修用斜梯和安全梯,具体要求应符合《防火规范》的规定。
3管桥的立面布置
3.1装置内主管桥和副管桥,按管道布置的需要,可以为一层或二层,最多三层。
一层管桥宽度最大9m,大于9m宜采用双层管桥。
双层管桥的层间标高差以1.2~1.8m为宜,管桥宜采用钢结构或以钢筋混凝土为柱的混合结构。
3.2常用的管桥结构形式,如图2所示。
3.3管桥的底层梁标高取决于下述最大高度。
a、跨越主要道路的净空,一般不小于4.5m,若需通行大型吊车时,不小于5.5m。
b、管桥下布置设备时,一般为4m以上;
c、管桥内的管道与管桥外设备相连接的管道,当在人行通道上时净空应不小于2.2m,在辅助检修通道上时净空不小于3m。
3.4装置内主管桥顶层,宜布置空冷器;中层宜布置冷却器、换热器和容器等;底层宜布置机泵、冷却器、换热器、小型容器或留作管桥两侧工艺设备的检修通道,如图3。
泵是否布置在管家桥下应根据不同的工艺过程和具体情况而定。
要综合考虑节约用地,节省投资、方便操作和符合安全要求等因素。
3.5装置内主管桥与副管桥相交时,应将副管桥的梁标高选在主管桥两层梁标高之间,高差一般取为0.6~0.9m,如图4。
3.6装置内主管桥主梁和侧梁标高需考虑与框架的塔器的接管标高要求,详见5.2条。
3.7多雨地区,当管桥下布置机泵而管桥上又无设备平台、楼板等时,可在管桥顶上设轻型防雨棚。
3.8管桥底层布置热油泵时,需考虑泄漏着火时,不致危及重要工艺设备、电缆和仪表管缆等设施。
4管桥的配管设计
4.1 装置内管道应尽量采用架空敷设。
管桥上布置的管道包括:
3 / 12
5 / 12
d. 电气、仪表的管道及槽盒。
4.2 单层管桥只在一侧布置工艺设备时,工艺管道应布置在靠设备侧。
管桥两侧布置工艺设备时,辅助管道应布置在管桥中部,两边布置工艺管道,荷载大的管道应尽可能靠近管桥柱布置,紧急放空管道应按放空坡度敷设,一般用单独的T 形支架支撑,电气仪表管道及槽盒宜布置管桥外侧悬壁梁上或柱外侧。
单层管桥的典型布置如图5。
4.3 双层管桥的工艺管道宜布置下层,公用工程管道宜布置在上层,如图6,大型装置宜将仪表和电气桥架布置在最上层,对三层管桥布置在第三层。
4.3.1下列管道应布置在管桥上层。
a. 连接两个高于管桥上层的设备管嘴的工艺管道;
b. 敷设距离较长的工艺管道;
c. 高压高温的气体管道;
d. 与管桥顶层设备有关的管道。
图5 单层管桥典型管道布置 图6 双层管橇典型管道布置
4.3.2 下列管道应布置在管桥的下层:
a. 连接泵的工艺管道和与管桥下设备联系较多的公用工程管道;
b. 输送腐蚀性介质的管道;
4.4布置多层管桥时,热油管道宜在上层,液化石油气管道宜在下层;塔底至热油泵的热油管道,可布置在管桥下层的外侧,但不宜与液化石油气管道相邻。
4.5管桥下布置有汽轮机驱动的机泵时,在汽轮机进出口上方的管桥上宜留一或二个穿管的空间,以便将蒸汽和公用工程管道由总管接至泵和汽轮机,必要时,在管桥上应设局部操作平台,如图7。
图7 管桥留穿管空间示意
4.6管桥上布置约管道,应尽量避免“袋形”和“盲肠”。
除输送腐蚀性介质外,一般宜在管道的低点设不小于DN20的排液口,在管道的高点设不小于DN15的放气口。
4.7 主蒸汽管道一般应布置在双层管桥的上层。
蒸汽支管应从主蒸汽管的上方引出,在引出点附近的水平管段上设切断阀。
4.8管桥上的饱和蒸汽管道的最低点、“盲肠”管、汽水分离器下部、伴热蒸汽管末端等均应设疏水阀。
过热蒸汽管道的最低点、流量计前、以及每隔100~150m的水平管段处,应设排液阀、疏水阀和排液阀一般用DN20或DN25。
4.9净化压缩空气、非净化压缩空气的支管应从总管的上部引出,并设切断阀,在低点应设不小于DN20的排液阀。
4.10管桥上管道除与阀门、设备管嘴连接以及需要拆卸清扫处之外,不应设法兰。
阀门、法兰活接头的位置应设在管桥的梁间1/5~1/3处,不得设在电动机的正上方。
特别是不得设在热油泵的正上方。
输送有毒、腐蚀性介质的管道其阀门、法兰管件等不应位于通道上方。
4.11管桥上的DN≥50水平管道变径时应采用偏心大小头;隔热管道应设管托,不隔热管道一般不设管托。
4.12管桥下的调节阀组宜布置在塔器侧,距管桥柱中心线0.6~1.2m为宜。
竖管上的阀门手轮应朝向操作通道,仪表箱应靠近和朝向相应的调节阀组布置。
4.13并排布置的管道间距一般要求法兰外缘与相邻管道之间的净距不小于25mm。
5管桥与相邻区的关系
7 / 12
5.1 两管桥直角相交处,当管道改变方向而其排列顺序不变时,标高不变;若管道排列顺序改变时,则应改变标高,如图8,进入管桥的大管道,若布置在边缘可不改变标高。
图8 两管桥直角相关交关系
5.2 管桥侧梁的标高应与冷换框架的层高及塔器的基础标高相配合。
一般冷换框架一层梁底标高于管桥侧梁顶标高,而塔器基础标高又低于管桥侧梁顶标高(减压塔除外)。
如图9。
5.3 管桥下采样器的布置及其配管设计按厂商提供的密闭采样器说明实施。
5.4 管桥下泵的布置及其配管设计应符合40B311-1997《石油化工装置泵配管设计技术规定》。
5.5 管桥上层冷换的布置及其配管设计应符合40B209-1997《石油化工装置冷换设备配管设计技术规定》。
5.6 管桥顶层空冷器的布置及其配管设计应符合40B210-1997《石油化工装置空冷器配管设计技术规定》。