危害分析与关键点控制讲解学习
HACCP危害分析与关键控点培训

艺流程图)的每一个操作步骤危害发生的可能性进行讨论。通常根据工 作经验、流行病的数据及技术资料的信息来评估其发生的可能性。危害 评估是对每一个危害的风险极其严重程度进行分析,以决定食品安全危 害的显著性。
5
三、物理危害
物理的危害和常见来源
材料
来源
玻璃
瓶子、 灯固定物、温度计
木头
水果/蔬菜/谷物、盒子、建筑物
ቤተ መጻሕፍቲ ባይዱ
石头
水果/蔬菜/谷物、建筑物
金属
机器、农田、鸟枪子弹、电线、建筑物
塑料
农田、生产区、包装材料、托盘、雇员
第三节 国际食品卫生控制发展方向 1、食品卫生控制发展方向
食品安全卫生直接涉及人类的健康,许多国家都在改进现有的食品管理 体系,并在研究制定食品安全标准的基础食品风险分析准则。 ●美国修订《HACCP原则和应用准则》 ●澳大利亚/新西兰研究制定国家食品安全体系 ●各主要进口国相继建立食品进口警告系统
●关键限值(CL):与一个CCP相联系的每个预防措施所必须满足的标准 一个关键限值(CL)用来保证一个操作生产出安全产品的界限,每个CCP必须有 一个或多个关键限值用于显著危害,当加工偏离了关键限值(CL),可能导致 产品的不安全,因此必须采取纠偏行动保证食品安全。
●操作限值(OL):比CL更严格的限度,由操作人员用以降低偏离的风险的标准 原理4 关键控制点监控
接受水平的一个点、步骤或过程。
●当危害能被预防时,这些点可以被认为是关键控制点。
●能将危害消除的点可以确定为是关键控制点。
●能将危害降低到可接受水平的点可以确定为是关键控制点。
食品生产过程中的危害分析与关键控制点

食品生产过程中的危害分析与关键控制点食品是人们生活中不可或缺的重要组成部分,而其生产过程中存在各种潜在的危害因素。
为了保障食品的质量与安全,食品生产企业必须进行全面的危害分析,并确定关键控制点来进行有效的控制。
本文将对食品生产过程中常见的危害分析与关键控制点进行详细探讨。
一、危害分析食品生产过程中的危害可以来源于多个环节,包括原料采购、加工、包装、储存等。
常见的危害包括微生物污染、化学物质残留、物理污染和饮食安全等方面。
以下将针对每一类危害进行分析和探讨。
1. 微生物污染微生物污染是食品生产过程中最常见的一种危害形式。
它包括细菌、病毒、真菌和寄生虫等。
这些微生物可以通过空气、水、原料和人员等途径进入食品生产环境,并在适宜的温度、湿度等条件下繁殖。
若未进行有效的控制,微生物污染将导致食品变质、产生有害物质,严重时还可能引发食源性疾病。
2. 化学物质残留食品生产过程中使用的化学物质包括农药、添加剂、兽药等。
过量或不当使用这些化学物质,可能导致食品中化学物质残留超标,对人体健康造成潜在的危害。
因此,在食品生产过程中需要进行严格的控制与监测,确保化学物质的使用符合相关法规,并保证食品的安全性。
3. 物理污染物理污染是指食品中存在的异物,如金属碎片、塑料颗粒、木屑等。
这些异物可能是由生产设备损坏、环境脏乱等因素引起的。
若未进行及时的检测与控制,物理污染会对食品的质量与安全产生严重影响,甚至危及消费者的生命健康。
4. 饮食安全饮食安全是指食品中存在的过敏原、异物和食源性疾病等问题。
食物过敏可引起消费者过敏反应,表现为皮肤瘙痒、呼吸困难等,甚至可能导致严重的过敏性休克。
此外,食源性疾病是由于摄入了被致病菌污染的食物而引起的疾病,如沙门氏菌、副溶血性弧菌等。
二、关键控制点在危害分析的基础上,食品生产企业需要确定关键控制点(Critical Control Points, CCPs),并建立相应的控制措施。
关键控制点是指在食品生产过程中,对危害进行控制的重要环节。
危害分析与关键控制点培训资料

1 个性化的计划
针对您的制造和加工过程制定有针对 性的计划。
2 时刻关注安全问题
尽可能多考虑食品的安全性,保持监 测和记录监测数据。
3 培训员工
向员工提供培训和信息以确保他们知道食品安全的重要性,并能够帮助维护最高标准。
为什么危害分析很重要?
每年都有数以百万计的人因为 食品中的细菌或有害物质而生 病。危害分析可以帮助您至关重要的
危害分析是一项系统性的方法, 旨在识别可能对食品安全构成 危害的生物、化学和物理因素。
在食品领域工作的人们必须时 刻关注食品安全问题,以确保 食品无害可人。
关键控制点的概念和作用
关键控制点是在食品制造和加工过程中必须严格控制的步骤。本节内容将介绍关键控制点的概念和作用, 以及如何制定和实施这些步骤。
关键控制点是什么?
关键控制点是制造过程中必须严格控制的步 骤。
保持食品安全
关键控制点的目的是确保食品在生产和加工 过程中保持安全。
控制食品卫生安全
制定和实施关键控制点意味着您正在控制食 品卫生安全的要素。
识别产品或过程的相关情况。
3
3.确定危害
识别可能的污染或伤害情况。
4.确定关键控制点
4
确定确保健康和安全的关键控制点。
5
5.建立监测体系
确定每个控制点的监测方法和频率。
6.建立纪录体系
6
记录监测数据和产品信息,以便追 踪任何问题发生。
危害分析与关键控制点的实例
在本节中,我们将为您介绍一些实际案例,这些案例说明了危害分析和关键控制点在食品安全中的作用。
验证控制点
对关键控制点进行定期验证可以确保您的食 品安全计划一致有效。
危害分析与关键控制点的步骤
HACCP危害分析及关键控制点
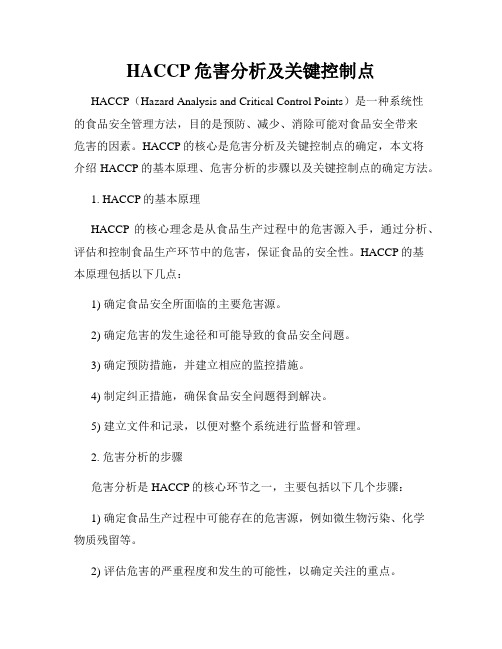
HACCP危害分析及关键控制点HACCP(Hazard Analysis and Critical Control Points)是一种系统性的食品安全管理方法,目的是预防、减少、消除可能对食品安全带来危害的因素。
HACCP的核心是危害分析及关键控制点的确定,本文将介绍HACCP的基本原理、危害分析的步骤以及关键控制点的确定方法。
1. HACCP的基本原理HACCP的核心理念是从食品生产过程中的危害源入手,通过分析、评估和控制食品生产环节中的危害,保证食品的安全性。
HACCP的基本原理包括以下几点:1) 确定食品安全所面临的主要危害源。
2) 确定危害的发生途径和可能导致的食品安全问题。
3) 确定预防措施,并建立相应的监控措施。
4) 制定纠正措施,确保食品安全问题得到解决。
5) 建立文件和记录,以便对整个系统进行监督和管理。
2. 危害分析的步骤危害分析是HACCP的核心环节之一,主要包括以下几个步骤:1) 确定食品生产过程中可能存在的危害源,例如微生物污染、化学物质残留等。
2) 评估危害的严重程度和发生的可能性,以确定关注的重点。
3) 确定危害的控制措施,包括预防控制、妥善处理等。
4) 确定监测危害的方法和频率,以及准确记录相关数据。
5) 确定纠正措施,即发生危害后应采取的措施。
3. 关键控制点的确定方法关键控制点(Critical Control Points,CCP)是指在食品生产过程中必须有效控制的环节,以确保食品的安全性。
关键控制点的确定方法主要包括下列步骤:1) 确定在整个食品生产过程中产生危害的环节。
2) 确定能够控制危害的环节,即输出与食品安全相关的关键环节。
3) 通过监测和控制这些关键环节,可以最大限度地确保食品的安全性。
4) 将关键控制点明确标记,并对其进行监测和记录。
总结:HACCP作为一种系统性的食品安全管理方法,通过危害分析及关键控制点的确定,能够有效预防和控制食品安全问题的发生。
HACCP危害分析和关键控制点
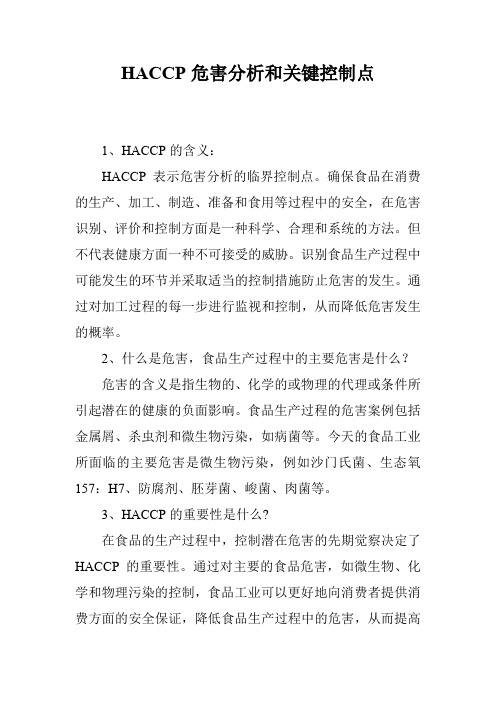
HACCP危害分析和关键控制点1、HACCP的含义:HACCP表示危害分析的临界控制点。
确保食品在消费的生产、加工、制造、准备和食用等过程中的安全,在危害识别、评价和控制方面是一种科学、合理和系统的方法。
但不代表健康方面一种不可接受的威胁。
识别食品生产过程中可能发生的环节并采取适当的控制措施防止危害的发生。
通过对加工过程的每一步进行监视和控制,从而降低危害发生的概率。
2、什么是危害,食品生产过程中的主要危害是什么?危害的含义是指生物的、化学的或物理的代理或条件所引起潜在的健康的负面影响。
食品生产过程的危害案例包括金属屑、杀虫剂和微生物污染,如病菌等。
今天的食品工业所面临的主要危害是微生物污染,例如沙门氏菌、生态氧157:H7、防腐剂、胚芽菌、峻菌、肉菌等。
3、HACCP的重要性是什么?在食品的生产过程中,控制潜在危害的先期觉察决定了HACCP的重要性。
通过对主要的食品危害,如微生物、化学和物理污染的控制,食品工业可以更好地向消费者提供消费方面的安全保证,降低食品生产过程中的危害,从而提高人民的健康水平。
4、HACCP标准是新的吗?为什么最近几年国际上那么重视HACCP?HACCP并不是新标准,它是20世纪60年代由皮尔斯伯公司联合美国国家航空航天局和美国一家军方实验室共同制定的,体系建立的初衷是为太空作业的宇航员提供食品安全方面的保障。
近年来,随着全世界人们对食品安全卫生的日益关注,食品工业和其消费者已经成为企业申请HACCP体系认证的主要推动力。
世界范围内食物中毒事件的显著增加激发了经济秩序和食品卫生意识的提高,在美国、欧洲、英国、澳大利亚和加拿大等国家,越来越多的法规和消费者要求将HACCP体系的要求变为市场的准入要求。
一些组织,例如美国国家科学院、国家微生物食品标准顾问委员会、以及WHO/FAO营养法委员会,一致认为HACCP是保障食品安全最有效的管理体系。
5、与传统的食品安全控制方法相比,HACCP有什么独到之处?传统的食品安全控制流程一般建立在“集中”视察、最终产品的测试等方面,通过“望、闻、切”的方法去寻找潜在的危害,而不是采取预防的方式,因此存在一定的局限性,举例来说,在规定的时间内完成食品加工工作、靠直觉去预测潜在的食品安全问题、在最终产品的检验方面代价高昂,为获得有意义的、有代表性的信息,在搜集和分析足够的样品方面存在较大难度。
危害分析与关键点控制
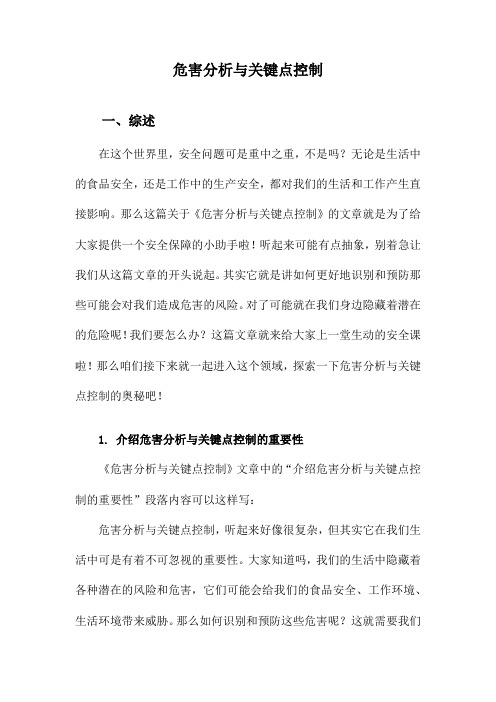
危害分析与关键点控制一、综述在这个世界里,安全问题可是重中之重,不是吗?无论是生活中的食品安全,还是工作中的生产安全,都对我们的生活和工作产生直接影响。
那么这篇关于《危害分析与关键点控制》的文章就是为了给大家提供一个安全保障的小助手啦!听起来可能有点抽象,别着急让我们从这篇文章的开头说起。
其实它就是讲如何更好地识别和预防那些可能会对我们造成危害的风险。
对了可能就在我们身边隐藏着潜在的危险呢!我们要怎么办?这篇文章就来给大家上一堂生动的安全课啦!那么咱们接下来就一起进入这个领域,探索一下危害分析与关键点控制的奥秘吧!1. 介绍危害分析与关键点控制的重要性《危害分析与关键点控制》文章中的“介绍危害分析与关键点控制的重要性”段落内容可以这样写:危害分析与关键点控制,听起来好像很复杂,但其实它在我们生活中可是有着不可忽视的重要性。
大家知道吗,我们的生活中隐藏着各种潜在的风险和危害,它们可能会给我们的食品安全、工作环境、生活环境带来威胁。
那么如何识别和预防这些危害呢?这就需要我们进行危害分析啦,通过对可能存在的危害进行深入分析,我们可以知道它们是怎么来的,对它们有更深入的了解。
同时关键点控制也是至关重要的,在某些关键的环节上采取措施,可以有效防止危害的发生或扩散。
想象一下这就像我们在生活中设置的“安全卫士”,保卫着我们的安全和生活质量。
所以危害分析与关键点控制真的是不可或缺,我们要学会重视它们,更好地保护自己和身边的人。
2. 阐述其在食品安全、工业生产等领域的应用说到危害分析与关键点控制,它在我们的日常生活里可是大有作为呢!首先得说说食品安全,大家都知道,食品安全直接关系到我们的健康,稍有疏忽就可能出问题。
这时候危害分析与关键点控制就大显身手了,通过对食品生产过程中的各个环节进行分析,找出那些容易出现问题的关键点,然后重点监控,确保食品的安全。
这样一来我们吃进嘴里的食物就更放心啦!不仅仅是在食品安全领域,危害分析与关键点控制在工业生产中也同样重要。
危害分析及关键控制点
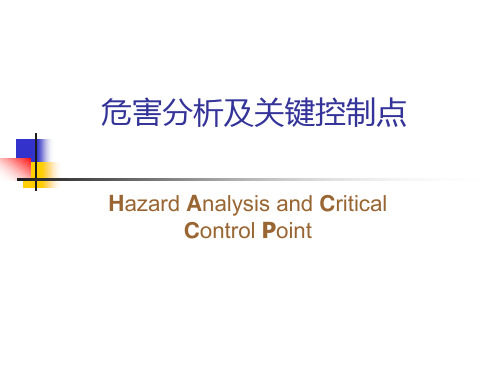
失活/去除(一些寄生虫能抵抗化学消毒,但通过 加热、干燥或冷冻可使其失活,在一些食品中, 肉眼检查可以检测寄生虫而将其去除,但不能 100%检出,应结合其他控制方法,如冷冻)
通过冷冻贮藏或冷却来预防病原微生物的生长。
常见的关键控制点2
下面的这些点可以被认为是能将危害消除 的关键控制点:
在加热过程中,病原微生物被杀死。 通过金属探测器检出产品中的金属碎片。 通过冷冻杀死寄生虫(如生吃鱼中可能带
有的寄生虫)。
常见的关键控制点3
下面的这些点可以被认为是能将危害降低 到可接受水平的关键控制点:
HACCP的意义和重要性
HACCP从生产角度来讲是安全控制系统, 是使产品从投料开始至成品保证产品安 全的体系 1、使食品生产对最终产品检验转化为控 制生产环节中的潜在危害; 2、应用最少的资源,做最有效的事情;
建立HACCP体系的好处
验证、补充和完善了传统的检验方法; 强调加工控制; 集中在影响产品安全的关键点上; 强调执法人员和企业之间的交流; 安全检验集中在预防性上; 不需要大的投资,简单有效; 可以随时与国际有关的食品法规接轨
HACCP和SSOP的关系
SSOP在对HACCP系统的支持性程序中起着十分重要的作用,有了 SSOP,HACCP才会更有效,因为它可以更好地把重点集中在与食
品或加工有关的危害上。一般来说,涉及到产品本身或某一加工 工艺、步骤的危害是由HACCP来控制,而涉及到加工环境或人员 等有关的危害通常是由SSOP来控制。在有些情况下,一个产品 加工操作可以不需要一个特定的HACCP计划,这是因为危害分析 显示没有显著危害,但是所有的加工厂必须对卫生状况和操作进 行监测,建立和维护一个良好的SSOP计划是实施HACCP计划的 基础和前提
危害分析及关键控制点介绍
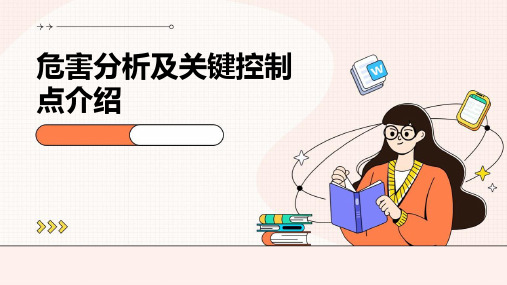
降低风险
HACCP通过对关键控制点的监控和 管理,有效降低食品生产过程中的 风险,确保食品的安全与卫生。
什么是危害分析及关键控制点(HACCP)
01
一种预防性的食品安全管理体系
使用适当的监控工具和技术,确保数据的准确性和可
靠性。
03
对监控结果进行分析,及时发现潜在问题并采取纠正
措施。
纠正措施和验证程序
制定有效的纠正措施,以应对监控过程中发现的问题。
纠正措施应具有针对性和可操作性,能够迅速解决问题并防止再次发生。 建立验证程序,定期对HACCP体系进行审核和评估,确保其持续有效性 和适用性。
危害分析及关键控制 点介绍
目录
CONTENTS
• 引言 • HACCP基本原理 • HACCP在食品行业的应用 • HACCP在其他行业的应用 • HACCP的优势和局限性 • HACCP的发展趋势和未来展望
01 引言
目的和背景
确保食品安全
HACCP作为一种有效的食品安全 管理工具,旨在识别、评估和控 制食品生产过程中的潜在危害,
食品行业中的关键控制点
原料控制
确保原料安全无害,防止有害物质和微生物 污染。
温度和时间控制
确保食品在适当的温度和时间内保存和加工, 防止细菌繁殖和毒素产生。
加工过程控制
通过合适的加工工艺和设备,杀灭有害微生 物,降低化学和物理危害。
包装和标识
确保食品包装无毒、密封性好,标识清晰准 确。
食品企业实施HACCP的步骤
HACCP强调预防措施,通过分析食品生产过程中的潜在危害,确定关
危害分析和关键控制点

危害分析和关键控制点(HACCP)体系1、HACCP的简介20世纪60年代初,美国的食品生产者与美国航天规划署合作,首次建立了HACCP系统。
1993年,国际食品法典委员会推荐HACCP系统为目前保障食品安全最经济有效的途径。
HACCP是以科学为基础,通过系统性地确定具体危害及其控制措施,以保证食品安全性的系统。
HACCP的控制系统着眼于预防而不是依靠终产品的检验来保证食品的安全。
2、制定HACCP的目的以及用途。
2.1制定危害分析和关键控制点(HACCP)的基本原则及实施指导,以帮助食品企业提高食品安全的管理水平,保证食品卫生质量,维护消费者的利益。
2.2HACCP可以应用在整个食品链——从初级(原料)到最终消费。
并且以健康危害方面的科学依据为导向进行实施。
HACCP的实施还有助于政府对食品安全的监督,并通过提高食品安全的可信度促进经济发展。
2.3HACCP的成功实施要求企业管理层及工作小组的充分支持和参与。
HACCP的实施相容于质量管理体系(列如ISO9000系列),是在质量管理体系下管理食品安全的一种系统方法。
2.4国家鼓励各类食品企业自觉实施HACCP管理,并对已实施HACCP管理的企业进行指导和评价。
(例如:出口食品)3定义3.1危害分析:指收集和评估有关的危害以及导致这些危害存在的资料,以确定哪些危害对食品安全有重要影响因而需要在HACCP计划中予以解决的过程。
3.2关键控制点:指能够实施控制措施的步骤。
该步骤对于预防和消除一个食品安全危害或将其减少到可接受水平非常关键。
3.3良好生产规范:是为保障食品安全、质量而制定的贯穿食品生产全过程一系列措施、方法和技术要求。
它要求食品生产企业应具备良好的生产设备,合理的生产过程,完善的质量管理和严格的检测系统,确保终产品的质量符合标准。
3.4卫生标准操作程序:食品企业为保障食品卫生质量,在食品加工过程中应遵守的操作规范。
具体包括以下范围:水质安全;食品接触面的条件和清洁;防止交叉污染;洗手消毒和卫生间设施的维护;防止掺杂品;有毒化学物的标记、储存和使用;雇员的健康状况;昆虫和鼠类的消灭与控制。
危害分析与关键控制点(HACCP).
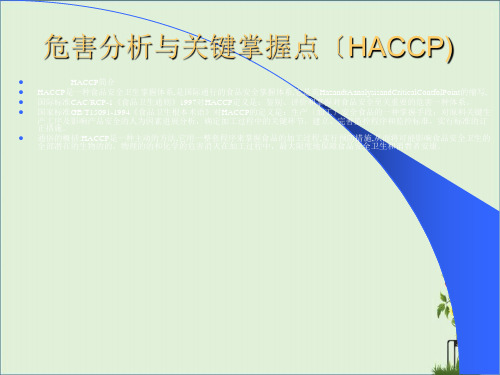
〔2023年增加的〕
12、不合格品的掌握。
良好操作标准(CMP)
G ood Manufacturing Practice
定义:良好操作标准〔简称CMP),又称食品生产标准,是政府制 定公布的强制性的食品生产、包装、存储卫生法规。GMP要求食 品企业应具备合理的生产过程、良好的生产设备、正确的生产学
三、HACCP的起源进展
1.创立阶段〔60年月至1991年〕 60年月初 美国Pillsbury公司应用于航空食品的生
产 1971年美国Pillsbury公开提出HACCP, 1972年美国FDA开头培训有关人员, 1985年美国科学院NAS评价并宣布承受H
ACCP, 1993年FAO/WHO食品法典委员会批准
国家标准GB/T15091-1994《食品卫生根本术语》对HACCP的定义是:生产〔加工〕安全食品的一种掌握手段;对原料关键生 产工序及影响产品安全的人为因素进展分析,确定加工过程中的关键环节,建立、完善监控程序和监控标准,实行标准的订 正措施。
GBT27341危害分析与关键控制点体系(HACCP)食品生产企业通用要求知识讲解
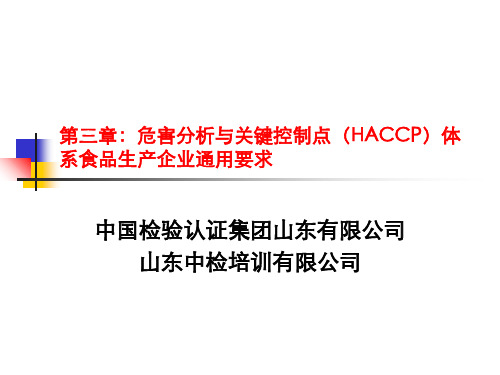
6.6维护保养计划
制定并实施厂区、厂房、设施、设备等 维护保养计划
6.7标识和追溯计划、产品召回计划
6.7.1标识和追溯计划 6.7.2产品召回程序
标识和追溯计划
最高管理者在HACCP体系中的作用: 向企业传达满足顾客和法律法规对食品
安全要求的重要性 制定食品安全方针 确保食品安全目标的制定 进行管理评审 确保资源的获得
5.2食品安全方针
最高管理者: 应以消费者食用安全为关注焦点,制定
食品安全方针和食品安全目标,确保食 品安全
5.3.1职责和权限
要 应保持管理评审的记录
6前提计划
6.1总则 6.2人力资源保障计划 6.3良好生产规范(GMP) 6.4卫生标准操作程序(SSOP) 6.5原辅料、食品包装材料安全卫生保障制度 6.6维护保养计划 6.7标识和追溯计划、产品召回计划 6.8应急预案
6.1前提计划
建立、实施、验证、保持并在必要时更 新或改进
操作限值(operation limit )
为了避免监控指数偏离关键限值而制定的操 作指标
食品防护计划 food defense plan
为了保护食品供应,免于遭受生物的、化学 的、物理的蓄意污染或人为破坏而制定并实 施的措施。
4企业HACCP体系
4.1总要求 4.2文件要求
4.1总要求
第三章:危害分析与关键控制点(HACCP)体 系食品生产企业通用要求
中国检验认证集团山东有限公司 山东中检培训有限公司
GB/T27341-2009《危害分析与关键控制 点(HACCP)体系食品生产企业通用要 求》,2009年6月01日实施
食品加工中的危害分析与关键控制点

食品加工中的危害分析与关键控制点食品加工行业在现代社会扮演着重要的角色,但随之而来的是一系列的食品安全隐患。
为了确保生产出的食品安全可靠,必须对食品加工中的危害进行深入分析,并确定关键控制点,以有效控制食品安全风险。
1. 危害分析在食品加工过程中,可能存在着多种危害,其中包括但不限于以下几种:- 生物性危害:细菌、病毒、霉菌等微生物可能引起食物中毒或感染。
- 化学性危害:食品中添加的化学物质、农药残留、重金属等可能对人体健康造成危害。
- 物理性危害:如金属片、玻璃碎片等外来物质可能混入食品中,对消费者造成伤害。
2. 关键控制点的确定为了有效控制食品加工中的危害,需要确定关键控制点,并实施相应的控制措施:- 原材料检验:在食品加工的起始阶段,对原材料进行严格的检验,确保其符合安全标准。
- 加工过程控制:在加工过程中,严格控制加工温度、湿度、时间等关键参数,避免微生物的繁殖。
- 设备清洁与消毒:定期对加工设备进行清洁与消毒,防止交叉污染。
- 成品检验:对成品进行全面检验,确保其符合食品安全标准,并及时处理不合格产品。
3. 食品安全管理体系的建立为了全面提升食品安全管理水平,建立健全的食品安全管理体系至关重要:- 制定食品安全管理制度:建立食品安全管理制度,明确责任、权限和流程。
- 培训员工:加强对员工的食品安全知识培训,提高其食品安全意识和操作技能。
- 定期审核与改进:定期对食品安全管理体系进行审核,及时发现问题并采取改进措施,不断完善管理体系。
通过对食品加工中的危害进行分析,并确定关键控制点,建立健全的食品安全管理体系,可以有效降低食品安全风险,保障消费者的健康与安全。
危害分析及关键控制点
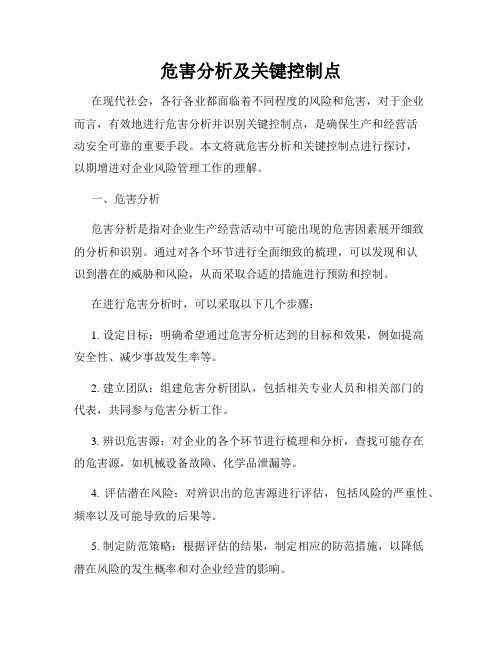
危害分析及关键控制点在现代社会,各行各业都面临着不同程度的风险和危害,对于企业而言,有效地进行危害分析并识别关键控制点,是确保生产和经营活动安全可靠的重要手段。
本文将就危害分析和关键控制点进行探讨,以期增进对企业风险管理工作的理解。
一、危害分析危害分析是指对企业生产经营活动中可能出现的危害因素展开细致的分析和识别。
通过对各个环节进行全面细致的梳理,可以发现和认识到潜在的威胁和风险,从而采取合适的措施进行预防和控制。
在进行危害分析时,可以采取以下几个步骤:1. 设定目标:明确希望通过危害分析达到的目标和效果,例如提高安全性、减少事故发生率等。
2. 建立团队:组建危害分析团队,包括相关专业人员和相关部门的代表,共同参与危害分析工作。
3. 辨识危害源:对企业的各个环节进行梳理和分析,查找可能存在的危害源,如机械设备故障、化学品泄漏等。
4. 评估潜在风险:对辨识出的危害源进行评估,包括风险的严重性、频率以及可能导致的后果等。
5. 制定防范策略:根据评估的结果,制定相应的防范措施,以降低潜在风险的发生概率和对企业经营的影响。
二、关键控制点关键控制点是指在危害分析过程中确定出的,对生产经营活动安全可靠性具有重要作用的关键环节。
通过对关键控制点的有效控制和管理,可以最大程度地减少风险的发生,并在事故发生时能够及时采取应急措施,保障员工和企业的安全。
确定关键控制点有以下几个步骤:1. 进行流程分析:对生产流程和经营过程进行全面的分析和评估,确定各个环节的重要性和关联性。
2. 识别危害产生的关键点:根据危害分析的结果,识别出可能产生危害的关键点,例如高温工作区域、危险化学品接触等。
3. 制定监控措施:对关键控制点进行监控,建立相应的监测系统和监控指标,确保可能产生的危害在可控范围内。
4. 提供培训和教育:针对关键控制点,向员工提供相应的培训和教育,加强其对相关风险和危害的认识和防范意识。
三、案例分析以一家化工企业为例进行危害分析和关键控制点的分析。
- 1、下载文档前请自行甄别文档内容的完整性,平台不提供额外的编辑、内容补充、找答案等附加服务。
- 2、"仅部分预览"的文档,不可在线预览部分如存在完整性等问题,可反馈申请退款(可完整预览的文档不适用该条件!)。
- 3、如文档侵犯您的权益,请联系客服反馈,我们会尽快为您处理(人工客服工作时间:9:00-18:30)。
危害分析与关键点控害分析关键控制点目录:第一节概述一、定义、H ACC 的产生及发展三、H ACCP体系的特点四、H ACCP体系与IS09000、GMP SSOP^的关系:第二节HACCP原理一、HACC的七个基本原理二、关键控制点三、HACC体系实施的基本步骤第三节HACCP在酸奶行业的应用一、酸奶的生产工艺流程二、危害因素三、酸奶加工全过程的危害分析四、确定生产中的关键控制点(CCP)五、CCP勺修正六、计划的评论与总结第四节参考文献第一节概述一、定义HACCP是危害分析与关键控制点(Hazard Analysis and CriticalControl Point) 的英文缩写,现已成通行全球食品特别是水产界的概念。
国家标准GB/T15091-1994《食品工业基本术语》对其规定的定义是:生产 (加工)安全食品的一种控制手段;对原料、关键生产工序及影响产品安全的人为因素进行分析,确定加工过程中的关键环节,建立、完善监控程序和监控标准,采取规范的纠正措施。
同义词:HACCP国际标准CAC/RCP-1食品卫生通则1997修订3版"对HACCP勺定义是:鉴别、评价和控制对食品安全至关重要的危害的一种体系。
二、HACCP勺产生及发展HACCP体系的建立始于1959年。
当时主要是为了满足开发航天食品的需要,即如何尽可能地保证用于太空中的食品具有100%勺安全性。
随着世界食品工业的迅速发展,消费者对食品安全、卫生的要求越来越高,各个国家特别是发达国家对食品的要求更加苛刻。
近年来部分国家或地区对我出口食品高筑技术壁垒,如对日本出口大米,农药残留、重金属与微生物指标已达到 91项之多;1996年10月,欧盟曾以中国食品企业不具备HACC体系为由,停止从中国进口肉类产品。
因此,如何提高我国出口食品卫生质量,扩大我国出口食品在国际市场的份额,已成为当务之急。
HACCP是一种确定食品的安全性,确认其中危害点并加以控制的手段。
HACCP方式与历来依靠对最终制品进行检验的品质卫生管理方法不同,而是从原料的种植、饲养开始,至最终产品到达消费者手中,对这期间各阶段可能产生的危害进行确认、防止,并加以管理的方式。
HACCF体系是建立在现代食品安全系统上的指导性的基本准则,是一种系统的、有效的、合理的食品安全预防性方案,与食品生产的全过程有关。
HACCP(Hazard An alysis and Critical Co ntrol Poi nt) 计划,是目前世界上最有权威的食品安全质量保护体系--HACCP体系的核心,是用来保护食品在整个生产过程中免受可能发生的生物、化学、物理因素的危害。
其宗旨是将这些可能发生的食品安全危害消除在生产过程中,而不是靠事后检验来保证产品的可靠性。
目前,英国、法国、比利时、荷兰、等国家已推广、应用HACCP体系,相继发布实施HACC原理的法规、办法。
我国从上世纪90年代起在一些出口食品企业推广HACC体系,取得了显著效果。
HACCP体系已成为商检确保食品安全控制的基本政策,并逐步建立了与发达国家相对等的(HACC)法规体系。
三、HACC体系的特点:HACC是—种简便易行、合理有效的食品安全保证系统,有如下特点:1 、HACCP体系建立在企业良好的食品卫生管理系统的基础上,不是一个孤立的体系。
2 、HACCP体系是预防性的食品安全控制体系,要对所有潜在的生物的、物理的、化学的危害进行分析,确定预防措施,防止危害发生。
3 、HACCP体系强调关键控制点的控制,在对所有潜在的危害进行分析的基础上确定哪些是显著危害,找出关键控制点。
4 、HACCP体系的具体内容因不同食品加工过程而异,每个HACC计划都反映了某种食品加工方法的专一特性。
5 、HACCP!一个基于科学分析而建立的体系,需要强有力的技术支持。
6 、HACC体系不是零风险体系,而是能减少或者降低食品安全风险。
7、HACCP体系需要一个实践一一认识一一再实践一一再认识的过程,企业在制定HACCP体系计划后,不是一成不变的,要不断对其有效性进行验证,在实践中加以完善和提高。
四、HACC体系与ISO9OO0 GMP SSOP可的关系:(一) HACC与 ISO9000(1)两个标准体系都是质量管理体系的一部分,有很多要素和程序可以相互兼容。
国际食品法典委员会(CAC认为,HACC刖以是ISO9000系列标准的一个部分。
(2) HACCP体系中关于危害分析、关键控制点的确定及监控等与ISO9001 的“过程控制”是相似和对应的,如果推行ISO9000的食品加工企业把过程控制这个要素突出来,就相当于抓住了 HACCP勺根本,可以收到事半功倍的效果。
(3)是否推行ISO9000是食品企业的自愿行为,而在不少国家,实行HACCP是法规规定的,如在美国,由执法机构对食品加工企业实行强制性执行HACCP(4)目前,国际贸易对食品生产实施 HACC已进入法规化阶段。
(二) HACC与 GMP SSOP(1)实施GMP可以更好地促进食品企业加强自身质量保证措施,更好地运用HACC体系,保证食品的安全卫生。
(2)SSOP侧重于卫生问题,HACCpg侧重于控制食品的安全性,良好的生产环境是食品企业得以规范运行的先决条件。
(3)HACCP必须建立在良好的GMP和SSOP的基础之上,只有与GMP ffi SSOP t 机的结合,才能更完整、更有效。
第二节 HACPP原理'、HACC的七个基本原理:1 、危害分析2 、确定关键控制点3 、建立关键限值、保证 CCP受控制4 、确定监控CCP的措施5 、确立纠偏措施6 、确立有效的记录保持程序7、建立审核程序以证明HACC系统是在正确运行中。
二、关键控制点:关键控制点是指通过实施预防或控制措施,能够消除、预防或最大限度地降低在特定的食品生产过程中的危害,使每一个CCP所产生的危害经过控制得以防止、消除或降至可接受水平。
危害分析有两个最基本的要素:第一,是鉴别可损害消费者的有害物质或引起产品腐败的致病菌或任何病源;第二,是详细了解这些危害是如何得以产生。
三、HACC体系实施的基本步骤:步骤1:成立HACC计划拟定小组步骤2:描述产品步骤3:确定最终产品用途及消费对象步骤4、编制流程图步骤5:流程图现场验证步骤6:危害分析及控制措施步骤7:确定关键控制点(CCP步骤&确定各CCP勺关键限值(CL)步骤9:建立各CCP勺监控制度步骤10:建立纠偏措施步骤11:建立验证(审核)措施步骤12:建立记录保存和文件归档制度步骤13:回顾HACC计:划第三节HACC在酸奶行业的应用由于我们所赖以生存的陆地、海洋、江湖等大环境的不断恶化,水产品受到的危害可用"四面楚歌"来形容。
这些危害既有微生物的、化学的、生物的也有寄生虫及农药污染等。
为了把好水产品的安全和质量关,当代人们惯常采用的是:监测生产设施运行与人员操作的情况,并对成品进行抽样检验(理化、微生物、感官等)。
我们常用的抽样规则本身就是有误判风险的。
再是水产品是来自单个的易变质的生物体,其样本个体的不均匀性要比机电、化工等工业产品更突出,误判风险更难预料。
大量的成品检验的费用高,周期长。
等检验结果的信息反馈到管理层再决定产品质量控制措施时,往往为时已晚。
HACCP(Hazard An alysis and Critical Co ntrol Poi nt) 计划,是目前世界上最有权威的食品安全质量保护体系--HACCP体系的核心,是用来保护食品在整个生产过程中免受可能发生的生物、化学、物理因素的危害。
其宗旨是将这些可能发生的食品安全危害消除在生产过程中,而不是靠事后检验来保证产品的可靠性。
HACCF体系是一种建立在良好操作规范(GMP和卫生标准操作规程 (SSOP基础之上的控制危害的预防性体系,它的主要控制目标是食品的安全性,因此它与其他的质量管理体系相比,可以将主要精力放在影响产品安全的关键加工点上,而不是将每一个步骤都放上很多精力,这样在预防方面显得更为有效。
HACCP 具有以下优点:食品的微生物等的危害存在于许多环节上, 但可以采取各种措施予以控制。
因此,预先采取措施来防止这些危害和确定控制 点是HACCP 的关键因素。
该体系提供一种科学逻辑的控制食品的危害的方法。
避免了单纯依靠检验进行控制的方法的许多不足。
一旦建立 HACC 体系,质量保证的主要努力将针对各关键控制点(CCP )而避免了无尽无休的成品检验,以较低 的成本保证较高的安全性。
一、酸奶的生产工艺流程①添加发酵剂卜 添加或不添加危害因素对灭菌乳制品卫生质量构成的危害主要有 3种。
(1) 微生物危害:致病微生物及其毒素,如金黄色葡萄球菌、沙门氏 菌、李斯特氏菌污染等。
(2) 化学性危害:如抗生素、农药残留,重金属、亚硝酸盐、硝酸盐残 留,蛋白质变性等。
原料奶.验收 预处理 糖、稳定剂预热 均质(18〜20MP®»杀菌 保温发酵冷藏(2C 〜5C )—后熟 成品• 检验 ②添加发酵剂或不添*罐中培养(发酵) 发酵终点 冷却(< 20C ) 加果料 搅拌.泵入包装机灌装 冷藏(2C 〜5C )冷却(40C 〜45 °c )(40 C 〜45 C ) 发酵终点岀库 销售(3)物理性危害:杂草、牛毛、乳块、碎屑等。
危害分析过程,主要是收集和确定有关的危害以及导致危害产生和存在的条件,评估危害的严重性和危险性,判定危害的性质、程度和对人体健康的潜在性影响,以确定哪些危害对灭菌乳的安全是最重要的,即识别危害、确认危害的显著性,确定采取的预防控制措施。
根据灭菌乳的生产工艺流程图,分别对原料的验收、辅料、调配等14个环节分别进行细致的危害分析,并对各种危害的显著性进行评估。
三、酸奶加工全过程的危害分析(1)原料:酸奶生产的主要原料是优质新鲜牛奶或奶粉,牛奶或奶粉的优劣直接影响酸奶产品的质量。
分析危害要因素有:抗生素残留、新鲜度、干物质含量、掺假、致病菌、杂菌、酵母菌、芽胞等。
(2)辅料:水、蔗糖、添加剂是酸奶生产的辅料,辅料的优劣也直接影响酸奶产品的质量。
如:加糖既可使产品具有一定的甜度,改善风味,又可提高粘度,也有利于酸奶的凝固。
分析危害主要因素有:水的硬度,微生物和重金属污染,糖的等级和质量,果料的标准。
如:是否含有一定数量的酵母菌,未经杀菌而加入发酵奶中,即成为污染该酸奶的主要来源。
(3)调配:调配工序中包括称料、拌料、配料,这些是酸奶生产的关键步骤,也直接影响酸奶产品的质量。
分析危害主要因素有:称料、配料不准确,拌料不均匀,加料不精细,操作过程中温度、时间控制不好,配液在机器中停留或保存的时间过长。